Table of Contents
- Contents
- Safety
- Chapter 1. Introduction
- Chapter 2. Server components
- Chapter 3. Hardware replacement procedures
- Installation guidelines
- 3.5-inch/2.5-inch drive cage replacement
- 2.5-inch/3.5-inch hot-swap drive backplane replacement
- 3.5-inch simple-swap drive backplate replacement
- CMOS battery (CR2032) replacement
- DIMM replacement
- Drive replacement
- Fan replacement
- Flash power module replacement
- Front bezel replacement
- Front door replacement
- Front panel board assembly replacement
- Heat sink and fan module replacement
- Intrusion switch replacement
- M.2 drive replacement
- Optical drive replacement
- PCIe adapter replacement
- Power distribution board replacement
- Power supply unit replacement
- Processor replacement
- Server cover replacement
- System board replacement
- Tape drive replacement
- TPM card replacement
- Complete the parts replacement
- Chapter 4. Problem determination
- Appendix A. Getting help and technical assistance
- Appendix B. Notices
- Index
Lenovo ST250 User Manual
Displayed below is the user manual for ST250 by Lenovo which is a product in the Servers category. This manual has pages.
Related Manuals

ThinkSystem ST250
Maintenance Manual
Machine Types: 7Y45 and 7Y46
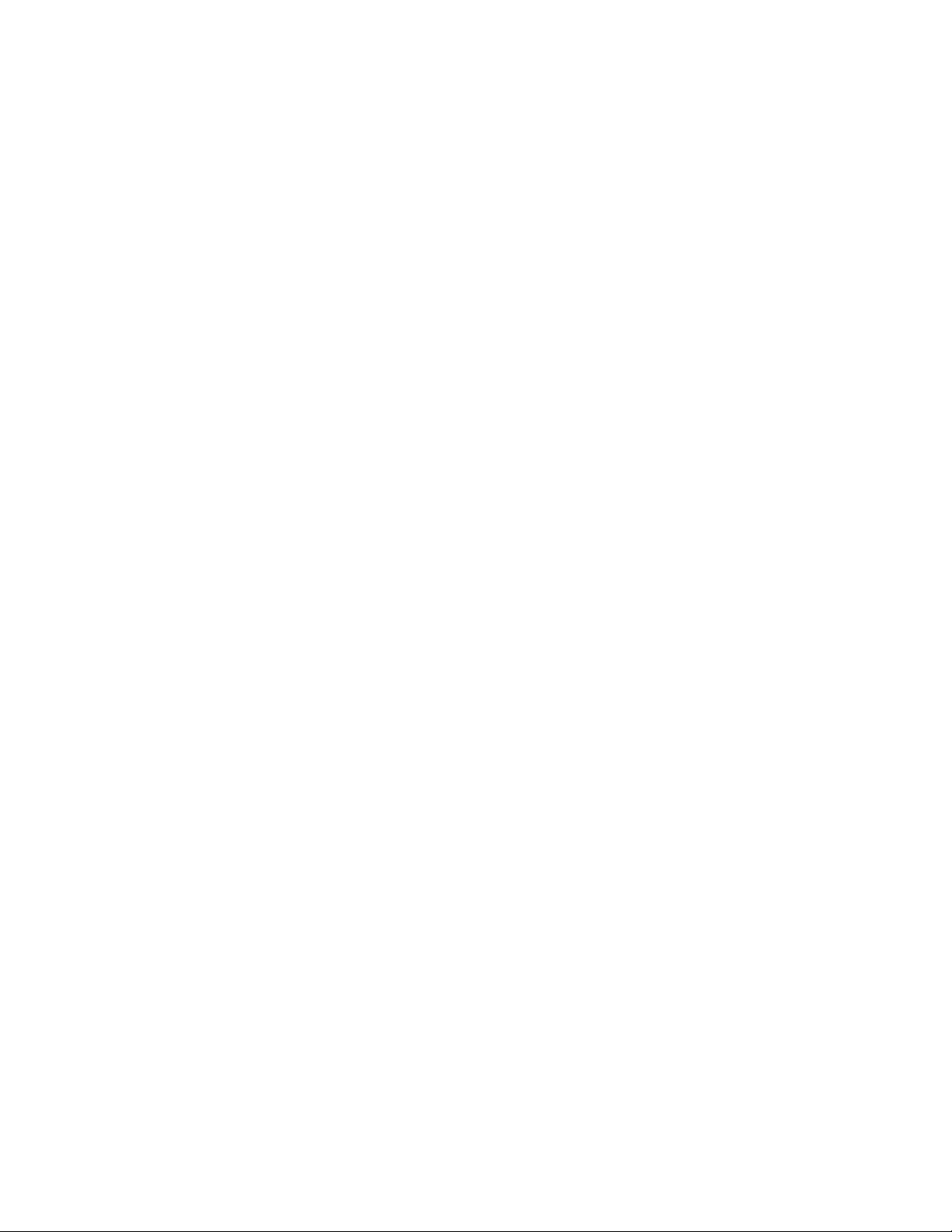
Note
Before using this information and the product it supports, be sure to read and understand the safety
information and the safety instructions, which are available at:
http://thinksystem.lenovofiles.com/help/topic/safety_documentation/pdf_files.html
In addition, ensure that you are familiar with the terms and conditions of the Lenovo warranty for your server,
which can be found at:
http://datacentersupport.lenovo.com/warrantylookup
Fifteenth Edition (May 2022)
© Copyright Lenovo 2018, 2022.
LIMITED AND RESTRICTED RIGHTS NOTICE: If data or software is delivered pursuant to a General Services
Administration (GSA) contract, use, reproduction, or disclosure is subject to restrictions set forth in Contract No. GS-35F-
05925.
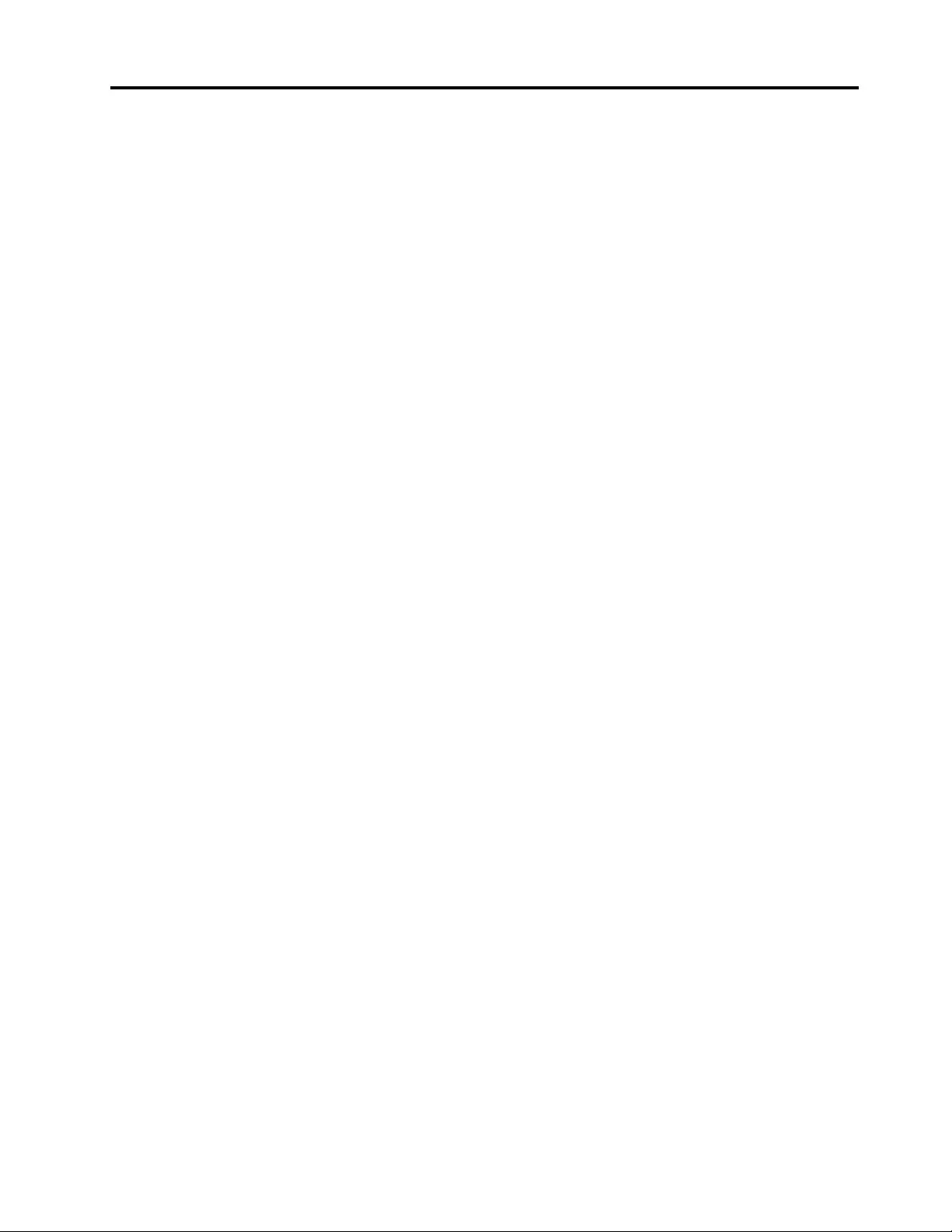
Contents
Contents . . . . . . . . . . . . . . . . . i
Safety . . . . . . . . . . . . . . . . . . iii
Safety inspection checklist . . . . . . . . . . . iv
Chapter 1. Introduction . . . . . . . . . 1
Server form factor . . . . . . . . . . . . . . . 3
Specifications . . . . . . . . . . . . . . . . 3
Particulate contamination . . . . . . . . . . 8
Firmware updates . . . . . . . . . . . . . . . 9
Tech Tips . . . . . . . . . . . . . . . . . 13
Security advisories . . . . . . . . . . . . . 13
Power on the server . . . . . . . . . . . . . 14
Power off the server . . . . . . . . . . . . . 14
Chapter 2. Server components . . . . 15
Front view . . . . . . . . . . . . . . . . . 15
Front panel . . . . . . . . . . . . . . . . 20
Server locks . . . . . . . . . . . . . . . . 22
Rear view . . . . . . . . . . . . . . . . . 24
Rear view LEDs . . . . . . . . . . . . . . . 26
System board components . . . . . . . . . . 29
System board jumpers . . . . . . . . . . . . 30
Internal cable routing. . . . . . . . . . . . . 31
Fan power cable. . . . . . . . . . . . . 31
Front panel . . . . . . . . . . . . . . . 32
Optical drive . . . . . . . . . . . . . . 34
Tape drive . . . . . . . . . . . . . . . 35
Redundant power supply . . . . . . . . . 36
Fixed power supply . . . . . . . . . . . 38
Simple-swap-drive backplate . . . . . . . 39
Hot-swap-drive backplane. . . . . . . . . 41
Parts list. . . . . . . . . . . . . . . . . . 48
Power cords . . . . . . . . . . . . . . 52
Chapter 3. Hardware replacement
procedures . . . . . . . . . . . . . . . 53
Installation guidelines . . . . . . . . . . . . 53
System reliability guidelines . . . . . . . . 54
Working inside the server with the power on . . 55
Handling static-sensitive devices . . . . . . 55
3.5-inch/2.5-inch drive cage replacement. . . . . 55
Remove the 3.5-inch/2.5-inch drive cage . . . 55
Install the 3.5-inch/2.5-inch drive cage . . . . 57
2.5-inch/3.5-inch hot-swap drive backplane
replacement . . . . . . . . . . . . . . . . 58
Remove the 3.5-inch/2.5-inch hot-swap drive
backplane . . . . . . . . . . . . . . . 58
Install the 3.5-inch/2.5-inch hot-swap drive
backplane . . . . . . . . . . . . . . . 59
3.5-inch simple-swap drive backplate
replacement . . . . . . . . . . . . . . . . 60
Remove the 3.5-inch simple-swap drive
backplate . . . . . . . . . . . . . . . 61
Install the 3.5-inch simple-swap drive
backplate . . . . . . . . . . . . . . . 62
2.5-inch SSD replacement from 3.5-inch drive
bay . . . . . . . . . . . . . . . . . . 63
CMOS battery (CR2032) replacement . . . . . . 67
Remove the CMOS battery (CR2032) . . . . 67
Install the CMOS battery (CR2032) . . . . . 68
DIMM replacement . . . . . . . . . . . . . 70
Remove a DIMM. . . . . . . . . . . . . 70
DIMM installation rules . . . . . . . . . . 71
Install a DIMM . . . . . . . . . . . . . 72
Drive replacement . . . . . . . . . . . . . . 73
Remove a simple-swap drive . . . . . . . . 74
Install a simple-swap drive. . . . . . . . . 75
Remove a hot-swap drive . . . . . . . . . 76
Install a hot-swap drive . . . . . . . . . . 78
Fan replacement . . . . . . . . . . . . . . 79
Remove the front system fan . . . . . . . . 80
Install the front system fan . . . . . . . . . 81
Remove the rear system fan . . . . . . . . 82
Install the rear system fan . . . . . . . . . 83
Flash power module replacement . . . . . . . . 85
Remove a flash power module . . . . . . . 85
Install a flash power module . . . . . . . . 87
Front bezel replacement . . . . . . . . . . . 88
Remove the front bezel . . . . . . . . . . 88
Install the front bezel . . . . . . . . . . . 89
Front door replacement. . . . . . . . . . . . 90
Remove the front door . . . . . . . . . . 90
Install the front door . . . . . . . . . . . 91
Front panel board assembly replacement. . . . . 92
Remove the front panel board assembly . . . 92
Install the front panel board assembly . . . . 93
Heat sink and fan module replacement. . . . . . 94
Remove the heat sink and fan module . . . . 95
Install the heat sink and the fan module. . . . 96
Intrusion switch replacement . . . . . . . . . 98
Remove the intrusion switch . . . . . . . . 98
Install the intrusion switch . . . . . . . . . 99
© Copyright Lenovo 2018, 2022 i
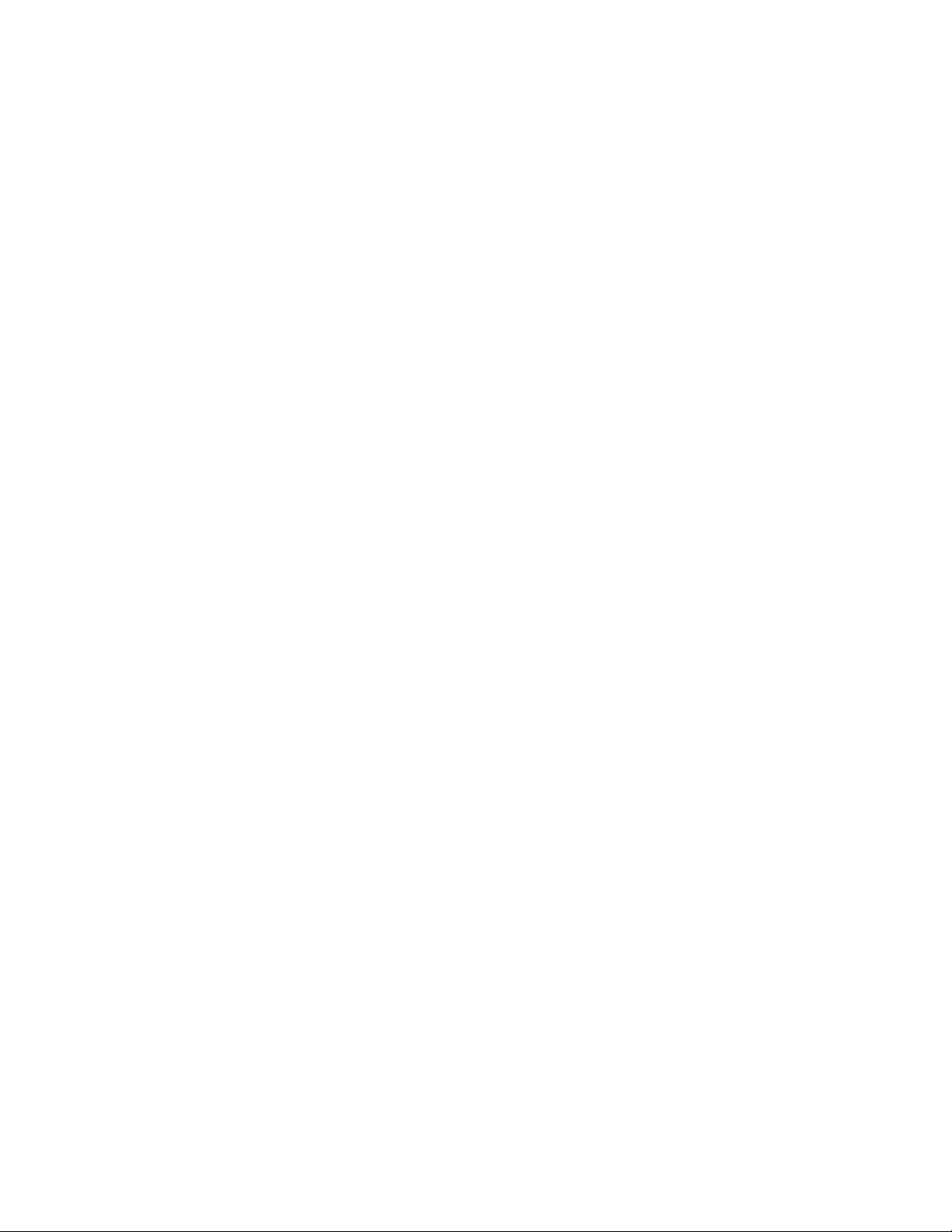
M.2 drive replacement . . . . . . . . . . . . 100
Remove the M.2 drive . . . . . . . . . . 100
Install the M.2 drive . . . . . . . . . . . 100
Optical drive replacement . . . . . . . . . . . 102
Remove an optical drive. . . . . . . . . . 103
Install an optical drive. . . . . . . . . . . 104
PCIe adapter replacement. . . . . . . . . . . 107
Remove a PCIe adapter . . . . . . . . . . 107
Install a PCIe adapter . . . . . . . . . . . 108
Power distribution board replacement . . . . . . 109
Remove the power distribution board . . . . 110
Install the power distribution board . . . . . 111
Power supply unit replacement . . . . . . . . . 114
Remove the fixed power supply. . . . . . . 114
Install the fixed power supply. . . . . . . . 118
Remove a hot-swap power supply. . . . . . 123
Install the hot-swap power supply . . . . . . 127
Processor replacement . . . . . . . . . . . . 133
Remove the processor . . . . . . . . . . 133
Install the processor . . . . . . . . . . . 134
Server cover replacement . . . . . . . . . . . 136
Remove the server cover . . . . . . . . . 136
Install the server cover . . . . . . . . . . 138
System board replacement . . . . . . . . . . 141
Remove the system board . . . . . . . . . 142
Install the system board . . . . . . . . . . 143
Update the machine type and serial
number . . . . . . . . . . . . . . . . 145
Enable TPM . . . . . . . . . . . . . . 147
Enable UEFI Secure Boot . . . . . . . . . 150
Tape drive replacement. . . . . . . . . . . . 151
Remove a tape drive . . . . . . . . . . . 151
Install a tape drive . . . . . . . . . . . . 152
TPM card replacement . . . . . . . . . . . . 153
Remove the TPM card . . . . . . . . . . 153
Install the TPM card . . . . . . . . . . . 154
Complete the parts replacement . . . . . . . . 155
Chapter 4. Problem
determination . . . . . . . . . . . . . 157
Event logs . . . . . . . . . . . . . . . . . 157
General problem determination procedures . . . . 159
Resolving suspected power problems . . . . 159
Resolving suspected Ethernet controller
problems . . . . . . . . . . . . . . . 160
Troubleshooting by symptom . . . . . . . . . 160
Power on and power off problems . . . . . . 161
Memory problems . . . . . . . . . . . . 162
Hard disk drive problems . . . . . . . . . 163
Monitor and video problems . . . . . . . . 165
Keyboard, mouse, or USB-device
problems . . . . . . . . . . . . . . . 167
Optional-device problems . . . . . . . . . 167
Serial-device problems . . . . . . . . . . 169
Intermittent problems. . . . . . . . . . . 170
Power problems . . . . . . . . . . . . . 171
Network problems . . . . . . . . . . . . 171
Observable problems. . . . . . . . . . . 171
Software problems. . . . . . . . . . . . 173
Appendix A. Getting help and
technical assistance . . . . . . . . . . 175
Before you call . . . . . . . . . . . . . . . 175
Collecting service data . . . . . . . . . . . . 176
Contacting Support . . . . . . . . . . . . . 177
Appendix B. Notices. . . . . . . . . . 179
Trademarks . . . . . . . . . . . . . . . . 180
Important notes . . . . . . . . . . . . . . . 180
Telecommunication regulatory statement. . . . . 180
Electronic emission notices . . . . . . . . . . 181
Taiwan BSMI RoHS declaration . . . . . . . 181
Taiwan import and export contact information . . . 181
Index . . . . . . . . . . . . . . . . . . 183
ii ThinkSystem ST250 Maintenance Manual

Safety
Before installing this product, read the Safety Information.
Antes de instalar este produto, leia as Informações de Segurança.
在安装本产品之前,请仔细阅读 Safety Information (安全信息)。
Læs sikkerhedsforskrifterne, før du installerer dette produkt.
Lees voordat u dit product installeert eerst de veiligheidsvoorschriften.
Ennen kuin asennat tämän tuotteen, lue turvaohjeet kohdasta Safety Information.
Avant d'installer ce produit, lisez les consignes de sécurité.
Vor der Installation dieses Produkts die Sicherheitshinweise lesen.
Prima di installare questo prodotto, leggere le Informazioni sulla Sicurezza.
Les sikkerhetsinformasjonen (Safety Information) før du installerer dette produktet.
Antes de instalar este produto, leia as Informações sobre Segurança.
© Copyright Lenovo 2018, 2022 iii
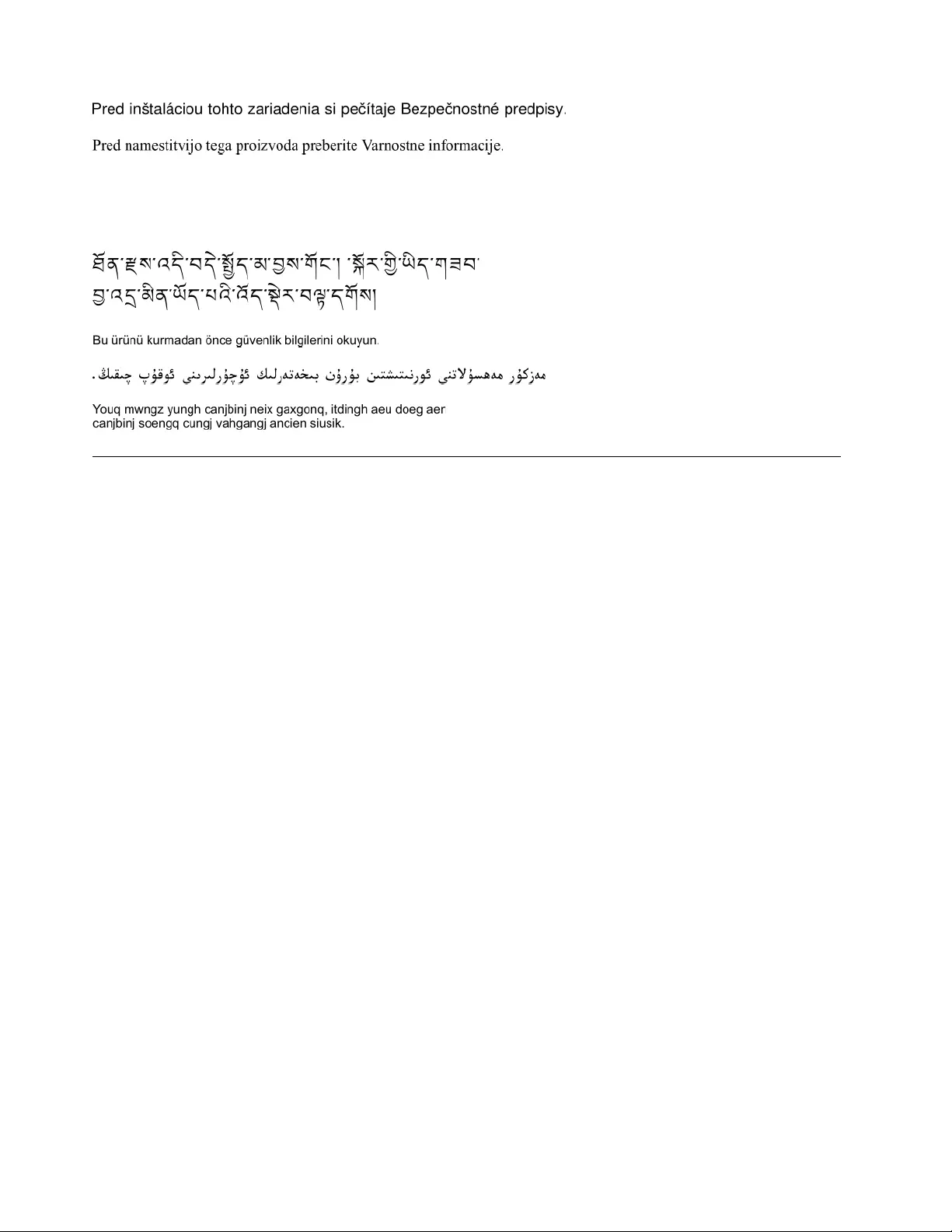
Antes de instalar este producto, lea la información de seguridad.
Läs säkerhetsinformationen innan du installerar den här produkten.
Safety inspection checklist
Use the information in this section to identify potentially unsafe conditions with your server. As each machine
was designed and built, required safety items were installed to protect users and service technicians from
injury.
Notes:
1. The product is not suitable for use at visual display workplaces according to §2 of the Workplace
Regulations.
2. The set-up of the server is made in the server room only.
CAUTION:
This equipment must be installed or serviced by trained personnel, as defined by the NEC, IEC 62368-
1 & IEC 60950-1, the standard for Safety of Electronic Equipment within the Field of Audio/Video,
Information Technology and Communication Technology. Lenovo assumes you are qualified in the
servicing of equipment and trained in recognizing hazards energy levels in products. Access to the
equipment is by the use of a tool, lock and key, or other means of security, and is controlled by the
authority responsible for the location.
Important: Electrical grounding of the server is required for operator safety and correct system function.
Proper grounding of the electrical outlet can be verified by a certified electrician.
Use the following checklist to verify that there are no potentially unsafe conditions:
1. Make sure that the power is off and the power cord is disconnected.
2. Check the power cord.
• Make sure that the third-wire ground connector is in good condition. Use a meter to measure third-
wire ground continuity for 0.1 ohm or less between the external ground pin and the frame ground.
• Make sure that the power cord is the correct type.
To view the power cords that are available for the server:
a. Go to:
http://dcsc.lenovo.com/#/
b. Click Preconfigured Model or Configure to order.
iv ThinkSystem ST250 Maintenance Manual

c. Enter the machine type and model for your server to display the configurator page.
d. Click Power ➙ Power Cables to see all line cords.
• Make sure that the insulation is not frayed or worn.
3. Check for any obvious non-Lenovo alterations. Use good judgment as to the safety of any non-Lenovo
alterations.
4. Check inside the server for any obvious unsafe conditions, such as metal filings, contamination, water or
other liquid, or signs of fire or smoke damage.
5. Check for worn, frayed, or pinched cables.
6. Make sure that the power-supply cover fasteners (screws or rivets) have not been removed or tampered
with.
© Copyright Lenovo 2018, 2022 v

vi ThinkSystem ST250 Maintenance Manual
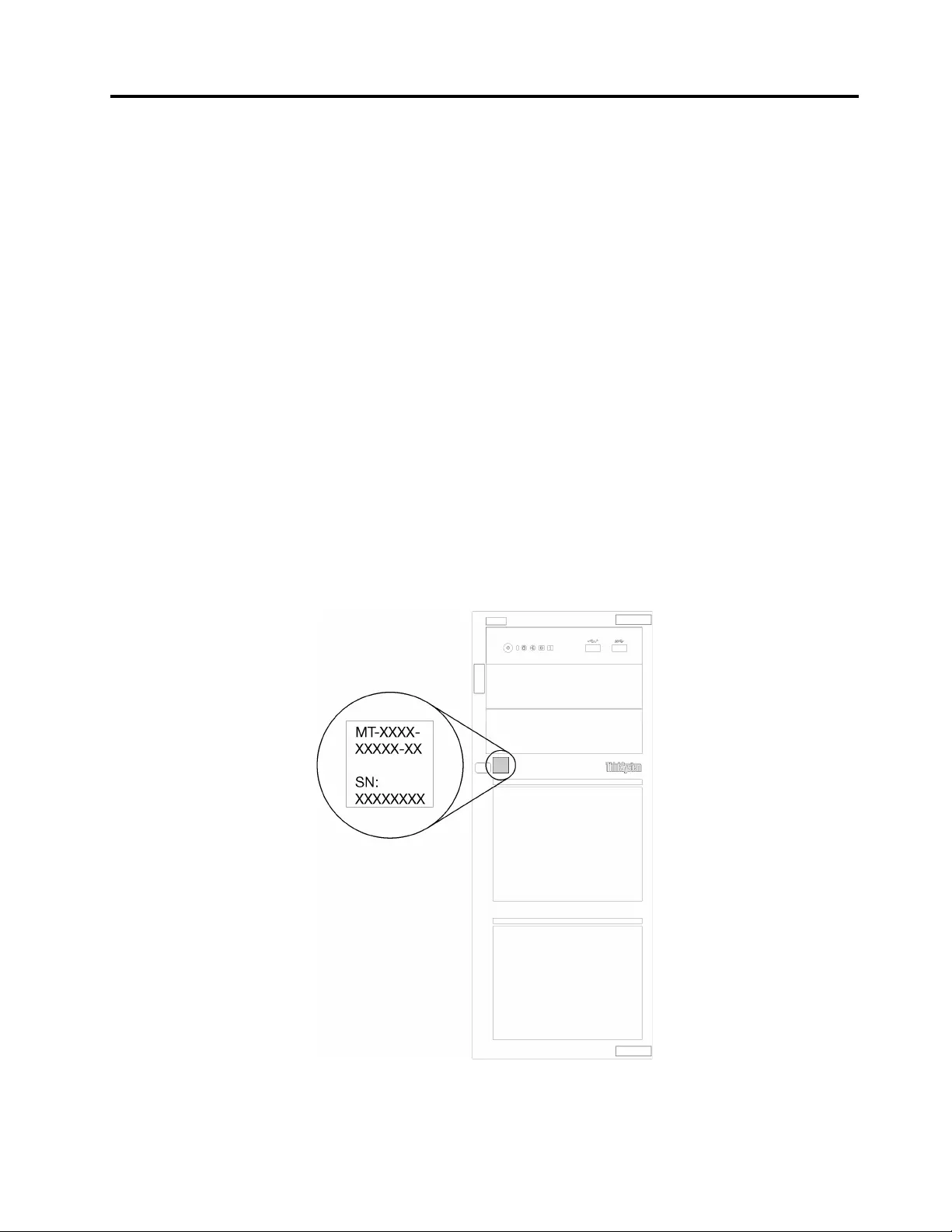
Chapter 1. Introduction
The ThinkSystem ST250 server is a 4U tower server designed for performance and expansion for various IT
workloads. With the modular design, the server is flexible to be customized for maximum storage capacity or
high storage density with selectable input/output options and tiered system management.
Performance, ease of use, reliability, and expansion capabilities were key considerations in the design of the
server. These design features make it possible for you to customize the system hardware to meet your needs
today and provide flexible expansion capabilities for the future.
The server comes with a limited warranty. For details about the warranty, see:https://support.lenovo.com/us/
en/solutions/ht503310
For details about your specific warranty, see:http://datacentersupport.lenovo.com/warrantylookup
Identifying your server
When you contact Lenovo for help, the machine type and serial number information helps support
technicians to identify your server and provide faster service.
The machine type and serial number are on the ID label on the front of the server.
The following illustration shows the location of the ID label.
Note: The illustrations in this document might differ slightly from your server.
Figure 1. Location of the ID label
© Copyright Lenovo 2018, 2022 1
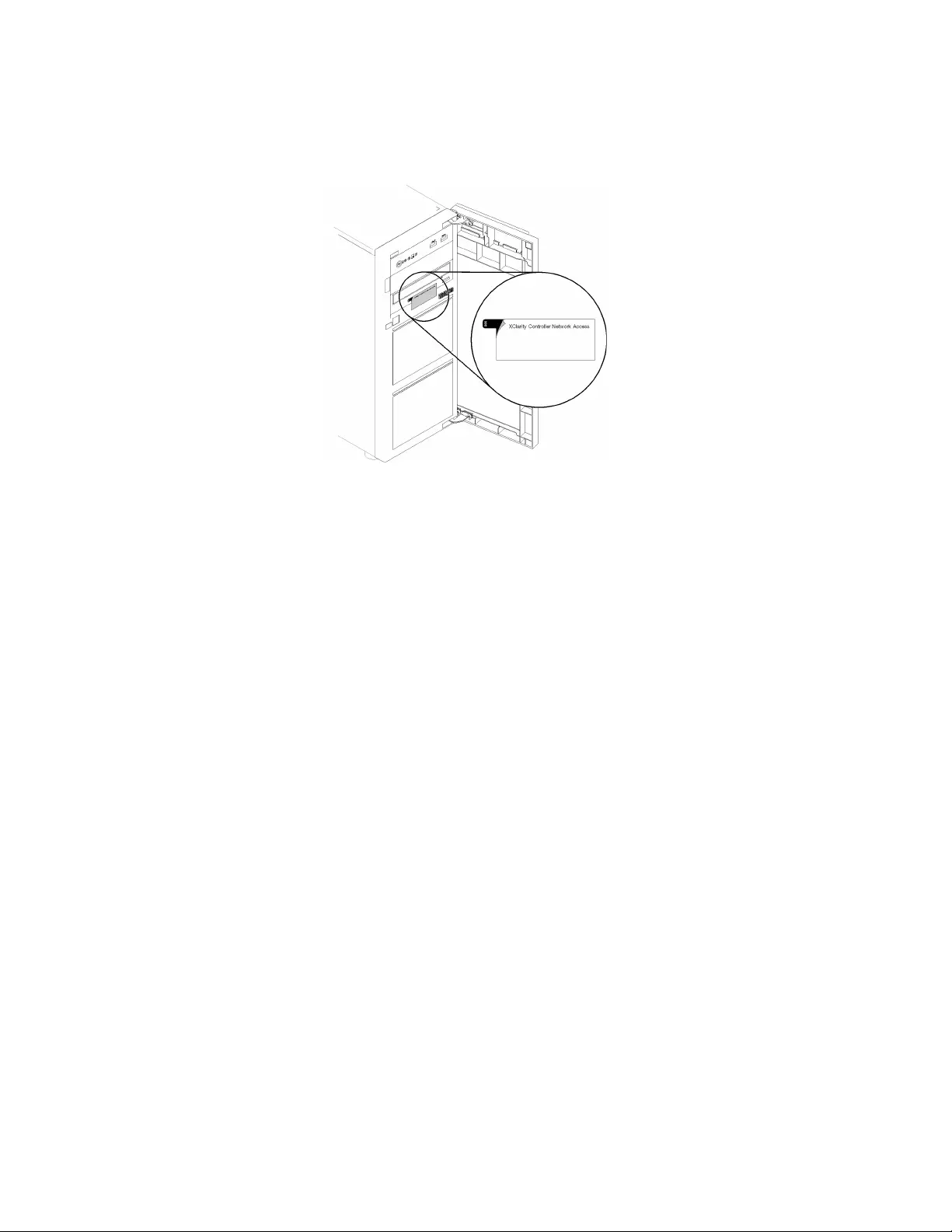
XClarity Controller network access label
The XClarity Controller network access label is attached on the front bezel as shown. After you get the
server, peel the XClarity Controller network access label away and store it in a safe place for future use.
Figure 2. Location of the XClarity Controller network access label
Quick response code
The system service label, which is on the inside of the server cover, provides a quick response (QR) code for
mobile access to service information. Scan the QR code with a mobile device and a QR code reader
application to get quick access to the Lenovo Service web site for this server. The Lenovo Service web site
provides additional information for parts installation and replacement videos, and error codes for server
support.
The following illustration shows the QR code.
2ThinkSystem ST250 Maintenance Manual

Figure 3. QR code
Server form factor
The ThinkSystem ST250 server is designed to support both tower and rack form factors.
You can change the server from tower form factor to rack form factor by installing the tower-to-rack
conversion kit. For instructions on how to install the tower-to-rack conversion kit, refer to the documentation
that comes with the conversion kit.
Specifications
The following information is a summary of the features and specifications of the server. Depending on the
model, some features might not be available, or some specifications might not apply.
Chapter 1.Introduction 3
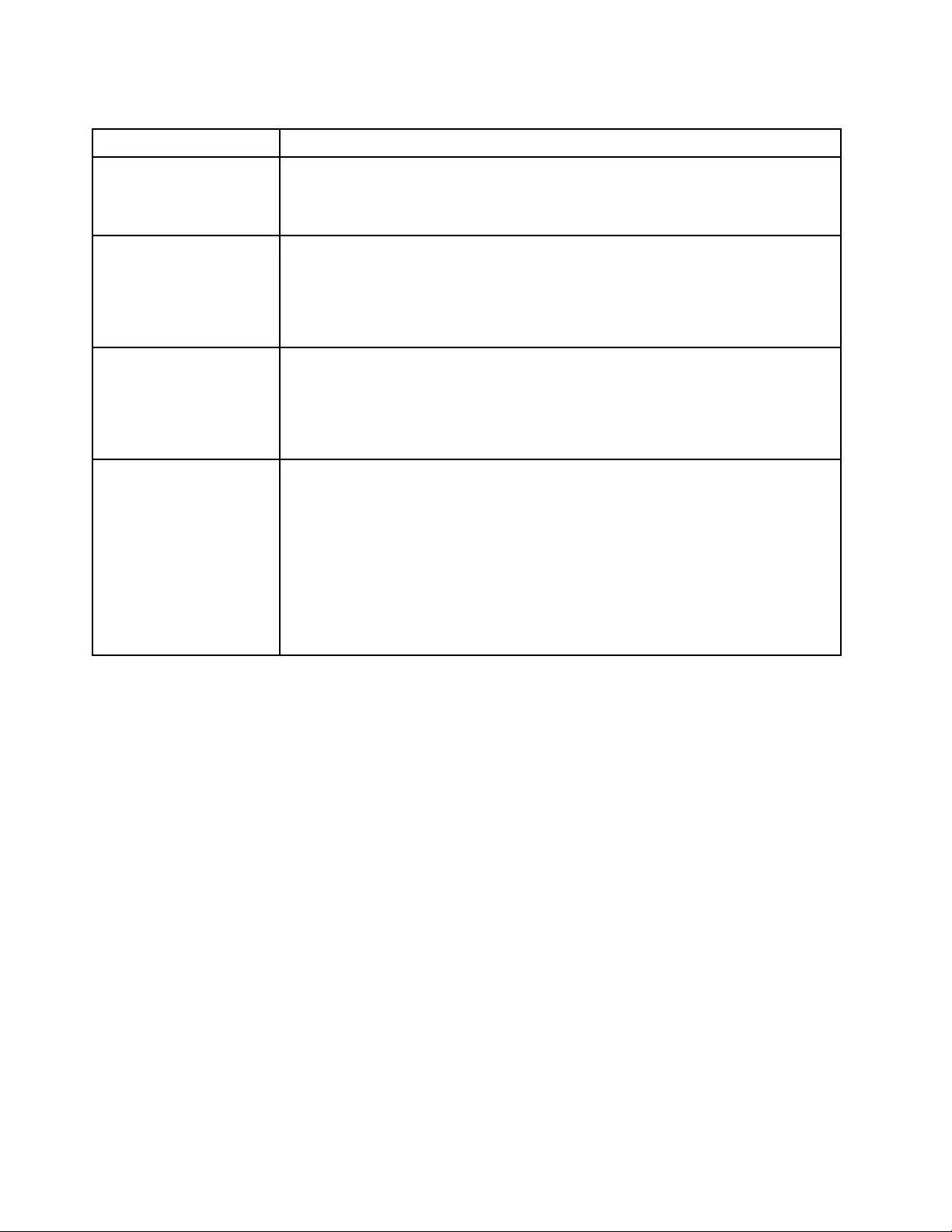
Table 1. Specifications
Specification Description
Dimension 4U server
• Height: 443.5 mm (17.46 inches)
• Width: 176 mm (6.93 inches)
• Depth: 578 mm (22.76 inches)
Weight (depending on the
configuration)
• Maximum without package:
– 2.5-inch disk drive configuration: 21.26 kg (46.87 lb)
– 3.5-inch disk drive configuration: 23.56 kg (51.94 lb)
• Minimum with package:
– 2.5-inch disk drive configuration: 17.24 kg (38.01 lb)
– 3.5-inch disk drive configuration: 19.32 kg (42.59 lb)
Processor This server supports one of the following Intel® processors:
• Xeon® E3–21XX
• Xeon® E3–22XX
• Core i3
• Pentium Gold
For a list of supported processors, see: http://datacentersupport.lenovo.com
Memory See “DIMM installation rules” on page 71 for detailed information about memory
configuration and setup.
• Minimum: 8 GB
• Maximum: 128 GB
• Slots: four DIMM slots (two channels, two DIMMs per channel)
• DIMM types:
– DDR4-2666
– 8 GB Single-rank, 16 GB dual-rank, or 32 GB dual-rank
– ECC-UDIMM
Note: Before installing 32 GB DIMMs, make sure your system has an Intel® Xeon® E
processor family installed with UEFI firmware updated to UEFI ISE114H-2.00 or later.
4ThinkSystem ST250 Maintenance Manual

Table 1. Specifications (continued)
Specification Description
Drive bays (varies by
model)
Drive bays and drives supported by your server vary by model.
• HDD storage drive bays:
– Up to four 3.5-inch simple-swap disk drives
– On board SATA ports
– Up to eight 3.5-inch simple-swap disk drives
– On board SATA ports*
– Up to four 3.5-inch hot-swap disk drives
– On board SATA ports
– RAID adapter
– Up to eight 3.5-inch hot-swap disk drives
– On board SATA ports*
– RAID adapter
– Up to eight 2.5-inch hot-swap disk drives
– On board SATA ports*
– RAID adapter
– Up to sixteen 2.5-inch hot-swap disk drives
– RAID adapter
– Up to hybrid four 3.5-inch and eight 2.5-inch hot-swap disk drives
– RAID adapter
* When M.2 or optical drive(s) are present , the on-board SATA disk drive support is
limited to six HDD.
Notes:
– Your server supports the installation of 2.5-inch SSDs in a 3.5 inch disk bay
through the use of a conversion kit. See “Installing a 2.5-inch SSD into a 3.5-inch
drive bay” on page 65 for details.
– When all eight storage drives have been installed, and the system has been set to
software RAID mode in the UEFI settings, regardless if the disks are configured as
an array or as separate disks, drives 6 and 7 cannot be used to install the Windows
operating system.
– If the M.2 drive has been installed, and the system has been set to software RAID
mode in the UEFI settings, regardless if the disks are configured as an array or as
separate disks, the M.2 drive cannot be used to install the Windows operating
system.
• Optical drive bays
– Two optical drive bays
– Supports up to two optical drives
– When the M.2 drive is present, the optical drive support is limited to one drive.
– Supports up to one tape drive (RDX or LTO)
– Can only be installed in lower optical drive bay
– Maximum support number of optical drive plus tape drive is two pieces.
Notes:
– Follow these steps to install the optical drive and tape drive when the M.2 drive is
present.
1. When the M.2 drive is installed, ensure that SATA port 7 remains
unconnected.
2. Install the optical drive into the upper media bay, Bay 1.
Chapter 1.Introduction 5

Table 1. Specifications (continued)
Specification Description
3. Install the backup drive (RDX or LTO tape) into the lower media bay, Bay 0.
4. Connect the optical drive to SATA port 6.
5. If an RDX drive is installed, connect the drive to the internal USB port adjacent
to the M.2 drive using the cable that shipped with the RDX drive (see “USB
tape drive cable routing” on page 36).
6. If an LTO tape drive is installed, install a SAS HBA into an available PCIe slot,
and connect the drive to the adapter with the cable that is shipped with the
LTO tape drive (see “SAS tape drive cable routing” on page 35).
– If your server is installed with a Windows Server operating system, you can use the
Windows Backup program to back up the data stored on tape drive media. For
detailed information, refer to the user guide of the tape drive. The user guide is
available for download at:http://www.lenovo.com/UserManuals
M.2 drive Supports 2 different physical sizes of M.2 drives:
• 42 mm (2242)
• 80 mm (2280)
Expansion slots Four PCIe expansion slots are available:
• Slot 1: PCIe3 x1, Full-height, half-length
• Slot 2: PCIe3 x16, Full-height, half-length
• Slot 3: PCIe3 x4, Full-height, half-length
• Slot 4: PCIe3 x8 (x4, x1), Full-height, half-length
Notes:
1. PCIe slot 1 and slot 2 do not support ARI and SR-IOV
2. PCIe slot 3 supports ARI and SR-IOV
3. ThinkSystem Broadcom NX-E PCIe 10Gb 2-Port Base-T Ethernet Adapter can only
be installed in the slot 2
Input/Output (I/O)
features
• Front panel
– One XClarity Controller USB 2.0 connector
– One USB 3.1 Gen 1 connector
• Rear panel
– Video Graphics Array (VGA) DB-15 connector
– Serial connector
– One USB 3.1 Gen 1 connector
– One USB 3.1 Gen 2 connector
– Two RJ-45 Ethernet connectors
– One RJ-45 Ethernet connector for BMC management
Network • Two 1Gbps RJ45 with BCM5720
• One 1Gbps Management RJ45
RAID(depending on model) The following options with RAID levels 0, 1, and 5 are available for this server. In
addition, RAID level 10 is available when four hard-disk/solid-state drives are installed in
the server.
• ThinkSystem RAID 530-8i PCIe 12Gb adapter
• ThinkSystem RAID 730-8i 1GB Cache PCIe 12Gb adapter
• ThinkSystem RAID 930-8i 2GB Flash PCIe 12Gb adapter
• ThinkSystem RAID 930-16i 4GB Flash PCIe 12Gb adapter
• ThinkSystem RAID 930-8e 4GB Flash PCIe 12Gb adapter
For a list of supported adapters, see:
http://datacentersupport.lenovo.com
6ThinkSystem ST250 Maintenance Manual

Table 1. Specifications (continued)
Specification Description
System fans Your server comes with the following fans to provide proper system cooling and airflow:
• One heat sink and fan assembly
• Two front system fans
• One rear system fan
Electrical input Universal input:
• Low range: 100 to 127 V ac
• High range: 200 to 240 V ac
• Input frequency range: 50 to 60 Hz
Note: The ThinkSystem ST250 only supports AC input power. Do not use 240VDC
input.
Power supply The server might come with one of the following power supply configurations:
• One 250W fixed power supply
• One or two 550W redundant power supply
Note: If you are using uninterruptible power supplies (UPS), ensure that you use only
pure-sine UPS with your ThinkServer server.
Acoustical noise
emissions
• Sound power, idling
– 3.7 bels, minimum
– 3.8 bels, typical
– 4.3 bels, maximum
• Sound power, operating
– 3.7 bels, minimum
– 4.0 bels, typical
– 4.4 bels, maximum
• Sound pressure level, idling (tabletop)
– 26.8 dBA, minimum
– 26.5 dBA, typical
– 39.4 dBA, maximum
• Sound pressure level, operating (tabletop)
– 27.0 dBA, minimum
– 26.7 dBA, typical
– 40.1 dBA, maximum
• Sound pressure level, idling (floor)
– 19.3 dBA, minimum
– 19.5 dBA, typical
– 29.5 dBA, maximum
• Sound pressure level, operating (floor)
– 19.4 dBA, minimum
– 21.0 dBA, typical
– 32.3 dBA, maximum
Note:
The sound levels were measured in controlled acoustical environments according to
procedures specified by ISO 7779 and are reported in accordance with ISO 9296. The
declared acoustic noise levels are based on specified configurations, which may change
slightly depending on configuration/conditions.
Approximate heat output • Minimum configuration: 221 BTU , 65 W (in BTU per hour and watts)
• Maximum configuration: 699 BTU, 205 W (in BTU per hour and watts)
Chapter 1.Introduction 7

Table 1. Specifications (continued)
Specification Description
Environment The ThinkSystem ST250 server complies with ASHRAE Class A2 specifications.
Depending on the hardware configuration, some models comply with ASHRAE Class A3
specifications. System performance may be impacted when operating temperature is
outside ASHRAE A2 specification.
• Air temperature:
– Operating
– ASHRAE Class A2: 10°C to 35°C (50°F to 95°F); the maximum ambient
temperature decreases by 1°C for every 300 m (984 ft) increase in altitude
above 900 m (2,953 ft).
– ASHRAE Class A3: 5°C to 40°C (41°F to 104°F); the maximum ambient
temperature decreases by 1°C for every 175 m (574 ft) increase in altitude
above 900 m (2,953 ft). Limited configuration as 80W processor plus eight 2.5-
inch disk drives.
– Server off: -10°C to 60°C (14°F to 140°F)
– Shipment/storage: -40°C to 60°C (-40°F to 140°F)
• Maximum altitude: 3,050 m (10,000 ft)
• Relative Humidity (non-condensing):
– Operating
– ASHRAE Class A2: 8% to 80%; maximum dew point: 21°C (70°F)
– ASHRAE Class A3: 8% to 85%; maximum dew point: 24°C (75°F)
– Shipment/storage: 8% to 90%
• Particulate contamination
Attention: Airborne particulates and reactive gases acting alone or in combination
with other environmental factors such as humidity or temperature might pose a risk to
the server. For information about the limits for particulates and gases, see
“Particulate contamination” on page 8.
Operating systems
Supported and certified operating systems:
• Microsoft Windows Server
• VMware ESXi
• Red Hat Enterprise Linux
• SUSE Linux Enterprise Server
References:
• Complete list of available operating systems: https://lenovopress.com/osig.
• OS deployment instructions: See “Deploy the operating system” in Setup Guide.
Particulate contamination
Attention: Airborne particulates (including metal flakes or particles) and reactive gases acting alone or in
combination with other environmental factors such as humidity or temperature might pose a risk to the
device that is described in this document.
Risks that are posed by the presence of excessive particulate levels or concentrations of harmful gases
include damage that might cause the device to malfunction or cease functioning altogether. This
specification sets forth limits for particulates and gases that are intended to avoid such damage. The limits
must not be viewed or used as definitive limits, because numerous other factors, such as temperature or
moisture content of the air, can influence the impact of particulates or environmental corrosives and gaseous
contaminant transfer. In the absence of specific limits that are set forth in this document, you must
implement practices that maintain particulate and gas levels that are consistent with the protection of human
health and safety. If Lenovo determines that the levels of particulates or gases in your environment have
caused damage to the device, Lenovo may condition provision of repair or replacement of devices or parts
8ThinkSystem ST250 Maintenance Manual
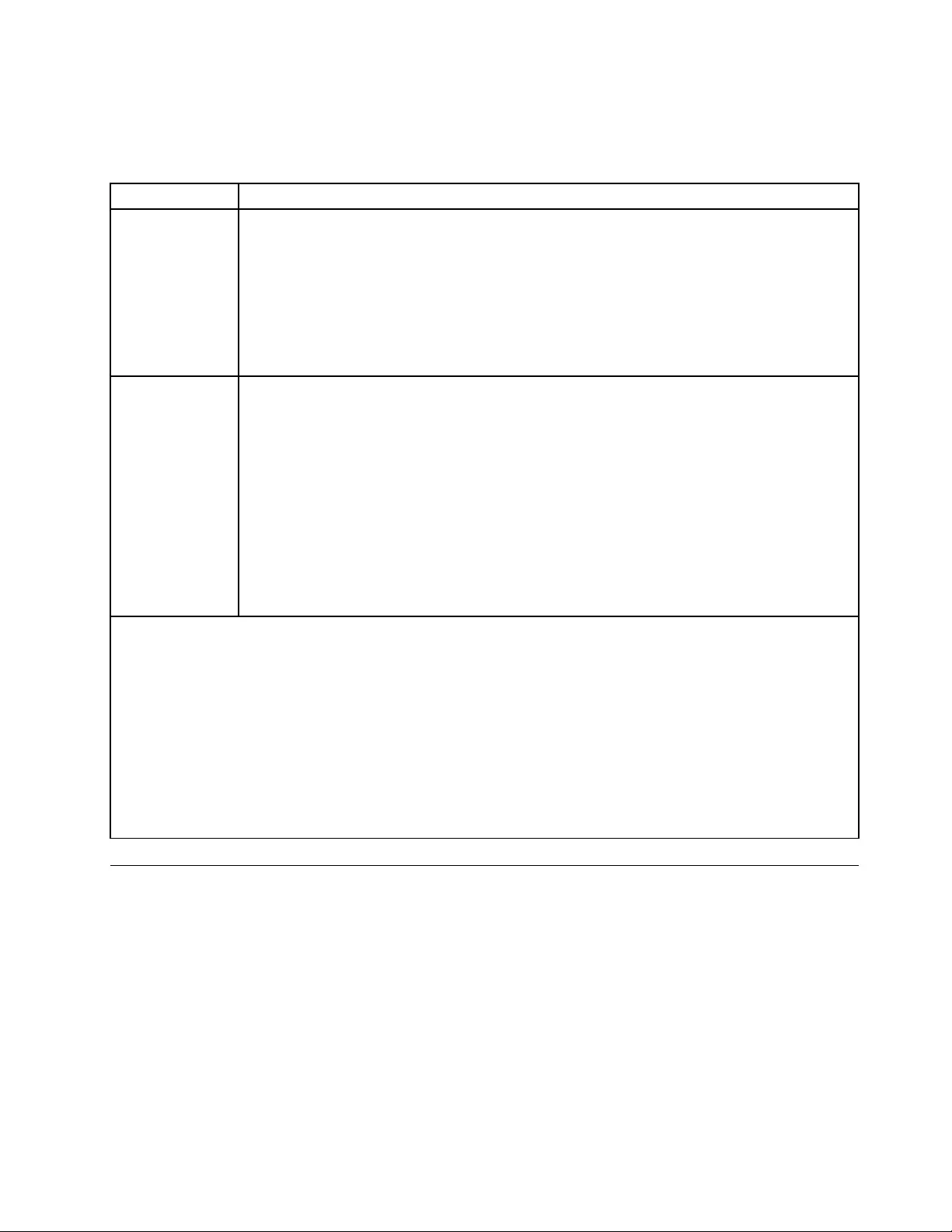
on implementation of appropriate remedial measures to mitigate such environmental contamination.
Implementation of such remedial measures is a customer responsibility.
Table 2. Limits for particulates and gases
Contaminant Limits
Reactive gases Severity level G1 as per ANSI/ISA 71.04-19851:
• The copper reactivity level shall be less than 300 Angstroms per month (Å/month ≈ 0.0039 μg/
cm2-hour weight gain).2
• The silver reactivity level shall be less than 200 Å/month (Å/month ≈ 0.0035 μg/cm2-hour
weight gain).3
• The reactive monitoring of gaseous corrosivity must be conducted approximately 5 cm (2 in.) in
front of the rack on the air inlet side at one-quarter and three-quarter frame height off the floor
or where the air velocity is much higher.
Airborne
particulates Data centers must meet the cleanliness level of ISO 14644-1 class 8.
For data centers without airside economizer, the ISO 14644-1 class 8 cleanliness might be met by
choosing one of the following filtration methods:
• The room air might be continuously filtered with MERV 8 filters.
• Air entering a data center might be filtered with MERV 11 or preferably MERV 13 filters.
For data centers with airside economizers, the choice of filters to achieve ISO class 8 cleanliness
depends on the specific conditions present at that data center.
• The deliquescent relative humidity of the particulate contamination should be more than 60%
RH.4
• Data centers must be free of zinc whiskers.5
1 ANSI/ISA-71.04-1985. Environmental conditions for process measurement and control systems: Airborne
contaminants. Instrument Society of America, Research Triangle Park, North Carolina, U.S.A.
2 The derivation of the equivalence between the rate of copper corrosion growth in the thickness of the corrosion
product in Å/month and the rate of weight gain assumes that Cu2S and Cu2O grow in equal proportions.
3 The derivation of the equivalence between the rate of silver corrosion growth in the thickness of the corrosion
product in Å/month and the rate of weight gain assumes that Ag2S is the only corrosion product.
4 The deliquescent relative humidity of particulate contamination is the relative humidity at which the dust absorbs
enough water to become wet and promote ionic conduction.
5 Surface debris is randomly collected from 10 areas of the data center on a 1.5 cm diameter disk of sticky
electrically conductive tape on a metal stub. If examination of the sticky tape in a scanning electron microscope
reveals no zinc whiskers, the data center is considered free of zinc whiskers.
Firmware updates
Several options are available to update the firmware for the server.
You can use the tools listed here to update the most current firmware for your server and the devices that are
installed in the server.
• Best practices related to updating firmware is available at the following site:
– http://lenovopress.com/LP0656
• The latest firmware can be found at the following site:
– http://datacentersupport.lenovo.com/us/en/products/servers/thinksystem/st250/7Y45/downloads
• You can subscribe to product notification to stay up to date on firmware updates:
Chapter 1.Introduction 9
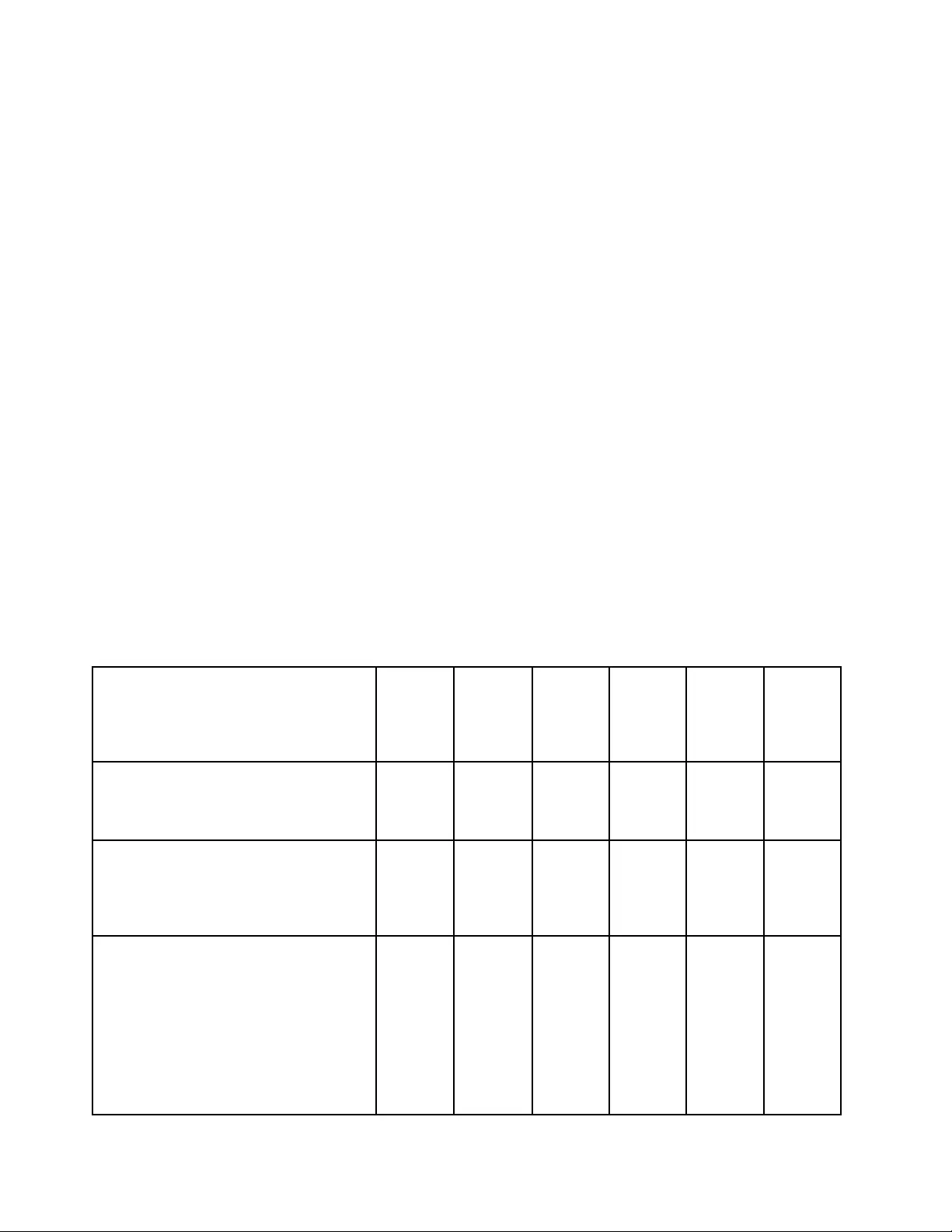
–
UpdateXpress System Packs (UXSPs)
Lenovo typically releases firmware in bundles called UpdateXpress System Packs (UXSPs). To ensure that all
of the firmware updates are compatible, you should update all firmware at the same time. If you are updating
firmware for both the Lenovo XClarity Controller and UEFI, update the firmware for Lenovo XClarity Controller
first.
Update method terminology
• In-band update. The installation or update is performed using a tool or application within an operating
system that is executing on the server’s core CPU.
• Out-of-band update. The installation or update is performed by the Lenovo XClarity Controller collecting
the update and then directing the update to the target subsystem or device. Out-of-band updates have no
dependency on an operating system executing on the core CPU. However, most out-of-band operations
do require the server to be in the S0 (Working) power state.
• On-Target update. The installation or update is initiated from an Operating System executing on the
server’s operating system.
• Off-Target update. The installation or update is initiated from a computing device interacting directly with
the server’s Lenovo XClarity Controller.
• UpdateXpress System Packs (UXSPs). UXSPs are bundled updates designed and tested to provide the
interdependent level of functionality, performance, and compatibility. UXSPs are server machine-type
specific and are built (with firmware and device driver updates) to support specific Windows Server, Red
Hat Enterprise Linux (RHEL) and SUSE Linux Enterprise Server (SLES) operating system distributions.
Machine-type-specific firmware-only UXSPs are also available.
Firmware updating tools
See the following table to determine the best Lenovo tool to use for installing and setting up the firmware:
Tool
Update
Methods
Suppor-
ted
Core
System
Firmware
Updates
I/O
Devices
Firm-
ware
Updates
Graphi-
cal user
interface
Com-
mand
line
interface
Supports
UXSPs
Lenovo XClarity Provisioning Manager
(LXPM)
In-band2
On-
Target
√ √
Lenovo XClarity Controller
(XCC)
Out-of-
band
Off-
Target
√Selected
I/O
devices
√
Lenovo XClarity Essentials OneCLI
(OneCLI)
In-band
Out-of-
band
On-
Target
Off-
Target
√All I/O
devices
√ √
10 ThinkSystem ST250 Maintenance Manual
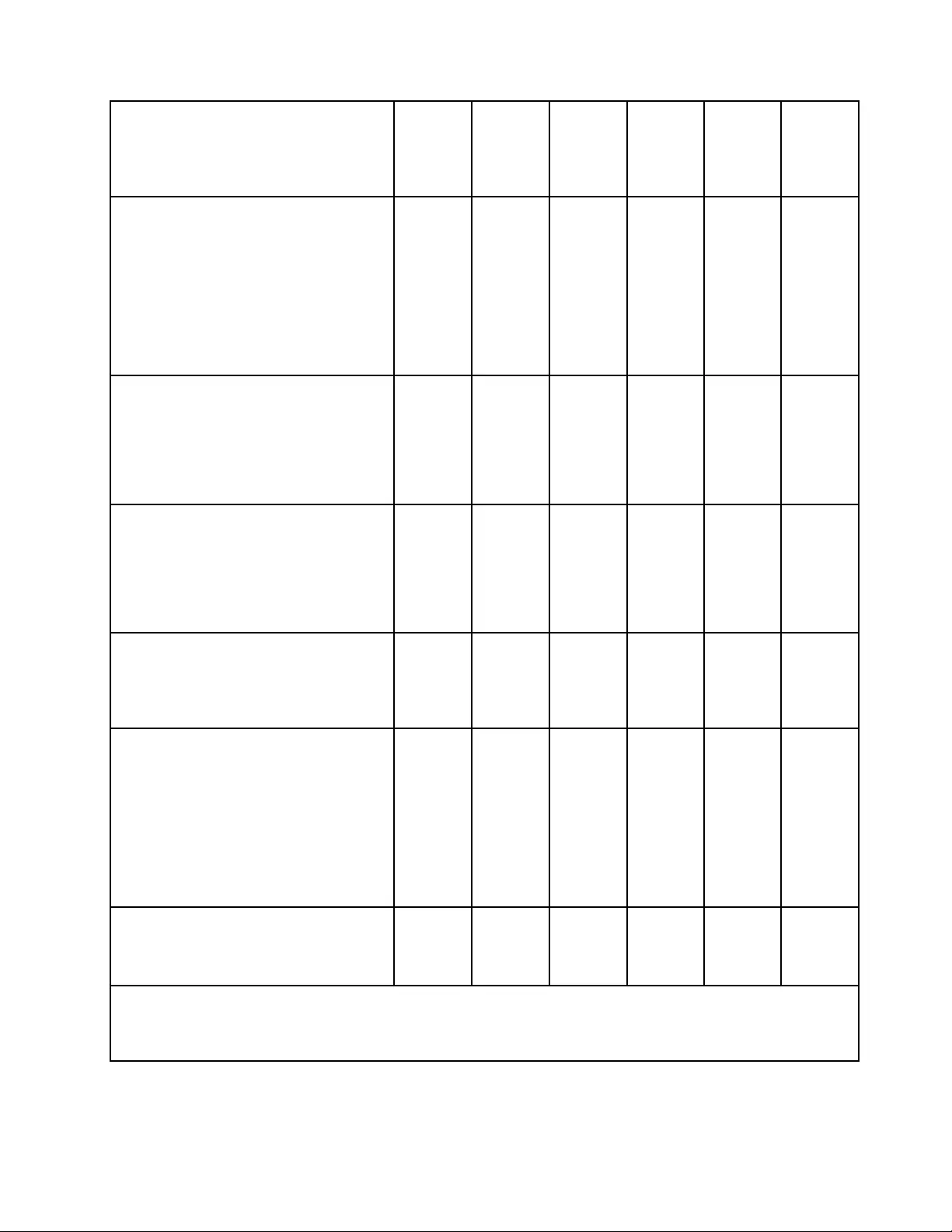
Tool
Update
Methods
Suppor-
ted
Core
System
Firmware
Updates
I/O
Devices
Firm-
ware
Updates
Graphi-
cal user
interface
Com-
mand
line
interface
Supports
UXSPs
Lenovo XClarity Essentials
UpdateXpress
(LXCE)
In-band
Out-of-
band
On-
Target
Off-
Target
√All I/O
devices
√ √
Lenovo XClarity Essentials Bootable
Media Creator3
(BoMC)
In-band
Out-of-
band
Off-
Target
√All I/O
devices
√
(BOMC
applica-
tion)
√
(BOMC
applica-
tion)
√
Lenovo XClarity Administrator
(LXCA)
In-band1
Out-of-
band2
Off-
Target
√All I/O
devices
√ √
Lenovo XClarity Integrator (LXCI) for
VMware vCenter
Out-of-
band
Off-
Target
√Selected
I/O
devices
√
Lenovo XClarity Integrator (LXCI) for
Microsoft Windows Admin Center
In-band
Out-of-
band
On-
Target
Off-
Target
√All I/O
devices
√ √
Lenovo XClarity Integrator (LXCI) for
Microsoft System Center Configuration
Manager
In-band
On-
Target
√All I/O
devices
√ √
Notes:
1. For I/O firmware updates.
2. For BMC and UEFI firmware updates.
• Lenovo XClarity Provisioning Manager
Chapter 1.Introduction 11
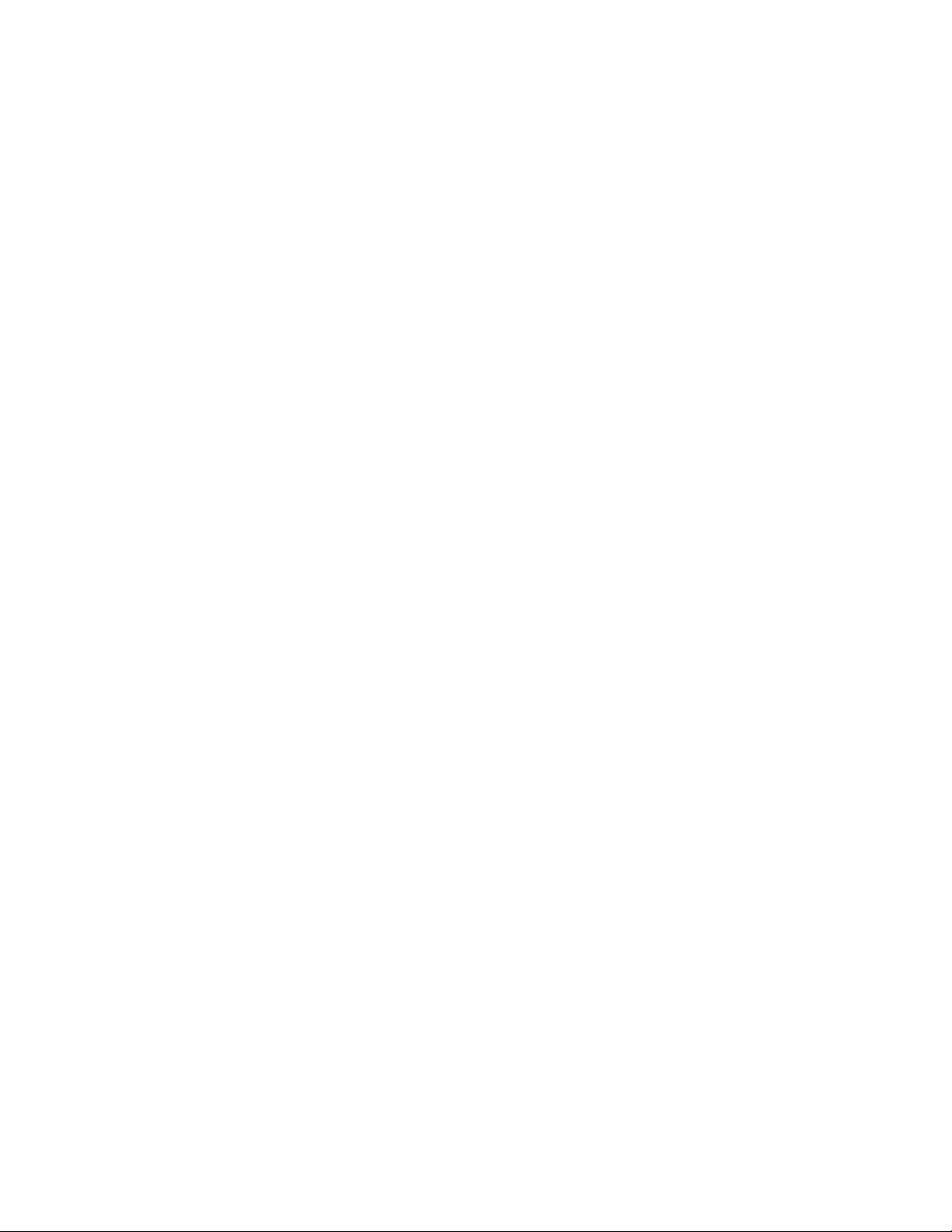
From Lenovo XClarity Provisioning Manager, you can update the Lenovo XClarity Controller firmware, the
UEFI firmware, and the Lenovo XClarity Provisioning Manager software.
Note: By default, the Lenovo XClarity Provisioning Manager Graphical User Interface is displayed when
you start the server and press the key specified in the on-screen instructions. If you have changed that
default to be the text-based system setup, you can bring up the Graphical User Interface from the text-
based system setup interface.
For additional information about using Lenovo XClarity Provisioning Manager to update firmware, see:
“Firmware Update” section in the LXPM documentation compatible with your server at https://
sysmgt.lenovofiles.com/help/topic/lxpm_frontend/lxpm_product_page.html
Important: Lenovo XClarity Provisioning Manager (LXPM) supported version varies by product. All
versions of Lenovo XClarity Provisioning Manager are referred to as Lenovo XClarity Provisioning Manager
and LXPM in this document, unless specified otherwise. To see the LXPM version supported by your
server, go to https://sysmgt.lenovofiles.com/help/topic/lxpm_frontend/lxpm_product_page.html.
• Lenovo XClarity Controller
If you need to install a specific update, you can use the Lenovo XClarity Controller interface for a specific
server.
Notes:
– To perform an in-band update through Windows or Linux, the operating system driver must be installed
and the Ethernet-over-USB (sometimes called LAN over USB) interface must be enabled.
For additional information about configuring Ethernet over USB, see:
“Configuring Ethernet over USB” section in the XCC documentation version compatible with your
server at https://sysmgt.lenovofiles.com/help/topic/lxcc_frontend/lxcc_overview.html
– If you update firmware through the Lenovo XClarity Controller, make sure that you have downloaded
and installed the latest device drivers for the operating system that is running on the server.
For additional information about using Lenovo XClarity Controller to update firmware, see:
“Updating Server Firmware” section in the XCC documentation compatible with your server at https://
sysmgt.lenovofiles.com/help/topic/lxcc_frontend/lxcc_overview.html
Important: Lenovo XClarity Controller (XCC) supported version varies by product. All versions of Lenovo
XClarity Controller are referred to as Lenovo XClarity Controller and XCC in this document, unless
specified otherwise. To see the XCC version supported by your server, go to https://
sysmgt.lenovofiles.com/help/topic/lxcc_frontend/lxcc_overview.html.
• Lenovo XClarity Essentials OneCLI
Lenovo XClarity Essentials OneCLI is a collection of command line applications that can be used to
manage Lenovo servers.Its update application can be used to update firmware and device drivers for your
servers. The update can be performed within the host operating system of the server (in-band) or remotely
through the BMC of the server (out-of-band).
For additional information about using Lenovo XClarity Essentials OneCLI to update firmware, see:
http://sysmgt.lenovofiles.com/help/topic/toolsctr_cli_lenovo/onecli_c_update.html
• Lenovo XClarity Essentials UpdateXpress
Lenovo XClarity Essentials UpdateXpress provides most of OneCLI update functions through a graphical
user interface (GUI). It can be used to acquire and deploy UpdateXpress System Pack (UXSP) update
packages and individual updates. UpdateXpress System Packs contain firmware and device driver
updates for Microsoft Windows and for Linux.
12 ThinkSystem ST250 Maintenance Manual

You can obtain Lenovo XClarity Essentials UpdateXpress from the following location:
https://datacentersupport.lenovo.com/solutions/lnvo-xpress
• Lenovo XClarity Essentials Bootable Media Creator
You can use Lenovo XClarity Essentials Bootable Media Creator to create bootable media that is suitable
for firmware updates, VPD updates, inventory and FFDC collection, advanced system configuration, FoD
Keys management, secure erase, RAID configuration, and diagnostics on supported servers.
You can obtain Lenovo XClarity Essentials BoMC from the following location:
https://datacentersupport.lenovo.com/solutions/lnvo-bomc
• Lenovo XClarity Administrator
If you are managing multiple servers using the Lenovo XClarity Administrator, you can update firmware for
all managed servers through that interface. Firmware management is simplified by assigning firmware-
compliance policies to managed endpoints. When you create and assign a compliance policy to managed
endpoints, Lenovo XClarity Administrator monitors changes to the inventory for those endpoints and flags
any endpoints that are out of compliance.
For additional information about using Lenovo XClarity Administrator to update firmware, see:
http://sysmgt.lenovofiles.com/help/topic/com.lenovo.lxca.doc/update_fw.html
• Lenovo XClarity Integrator offerings
Lenovo XClarity Integrator offerings can integrate management features of Lenovo XClarity Administrator
and your server with software used in a certain deployment infrastructure, such as VMware vCenter,
Microsoft Admin Center, or Microsoft System Center.
For additional information about using Lenovo XClarity Integrator to update firmware, see:
https://sysmgt.lenovofiles.com/help/topic/lxci/lxci_product_page.html
Tech Tips
Lenovo continually updates the support website with the latest tips and techniques that you can use to solve
issues that your server might encounter. These Tech Tips (also called retain tips or service bulletins) provide
procedures to work around issues or solve problems related to the operation of your server.
To find the Tech Tips available for your server:
1. Go to http://datacentersupport.lenovo.com and navigate to the support page for your server.
2. Click on the documentation icon from the navigation pane.
3. Click Documentation Type ➙ Solution from the drop-down menu.
Follow the on-screen instructions to choose the category for the problem that you are having.
Security advisories
Lenovo is committed to developing products and services that adhere to the highest security standards in
order to protect our customers and their data. When potential vulnerabilities are reported, it is the
responsibility of the Lenovo Product Security Incident Response Team (PSIRT) to investigate and provide
information to our customers so they may put mitigation plans in place as we work toward providing
solutions.
The list of current advisories is available at the following location:
https://datacentersupport.lenovo.com/product_security/home
Chapter 1.Introduction 13

Power on the server
After the server performs a short self-test (power status LED flashes quickly) when connected to input power,
it enters a standby state (power status LED flashes once per second).
The server can be turned on (power LED on) in any of the following ways:
• You can press the power button.
• The server can restart automatically after a power interruption.
• The server can respond to remote power-on requests sent to the Lenovo XClarity Controller.
For information about powering off the server, see “Power off the server” on page 14.
Power off the server
The server remains in a standby state when it is connected to a power source, allowing the Lenovo XClarity
Controller to respond to remote power-on requests. To remove all power from the server (power-on LED off),
you must disconnect all power cables.
To place the server in a standby state (power-on LED flashes once per second):
Note: The Lenovo XClarity Controller can place the server in a standby state as an automatic response to a
critical system failure.
• Start an orderly shutdown using the operating system (if supported by your operating system).
• Press the power-on button to start an orderly shutdown (if supported by your operating system).
• Press and hold the power button for more than 4 seconds to force a shutdown.
When in a standby state, the server can respond to remote power-on requests sent to the Lenovo XClarity
Controller. For information about powering on the server, see “Power on the server” on page 14.
14 ThinkSystem ST250 Maintenance Manual

Chapter 2. Server components
This section provides information that helps locate the server components.
Front view
The front view of the server varies by model.
The following illustration shows the server components that may appear on the front of your server model.
Figure 4. Front view of the server components
Table 3. Components on the front of server models
Item Description
1 Front panel See “Front panel” on page 20
2 Optical-drive bay 2 The optical drive bay 2 is for a secondary optical drive.
3 Optical-drive bay 1 The optical drive bay 1 is for an optical drive or a tape
drive.
4 Storage drive bays The number of installed drives in your server varies by
model. The vacant drive bays are occupied by drive fillers.
When you install drives, follow the order of the drive bay
numbers.
The following illustrations show the server front views based on the different supported drive configurations.
Attention: For server models that support eight drives, note the following:
© Copyright Lenovo 2018, 2022 15
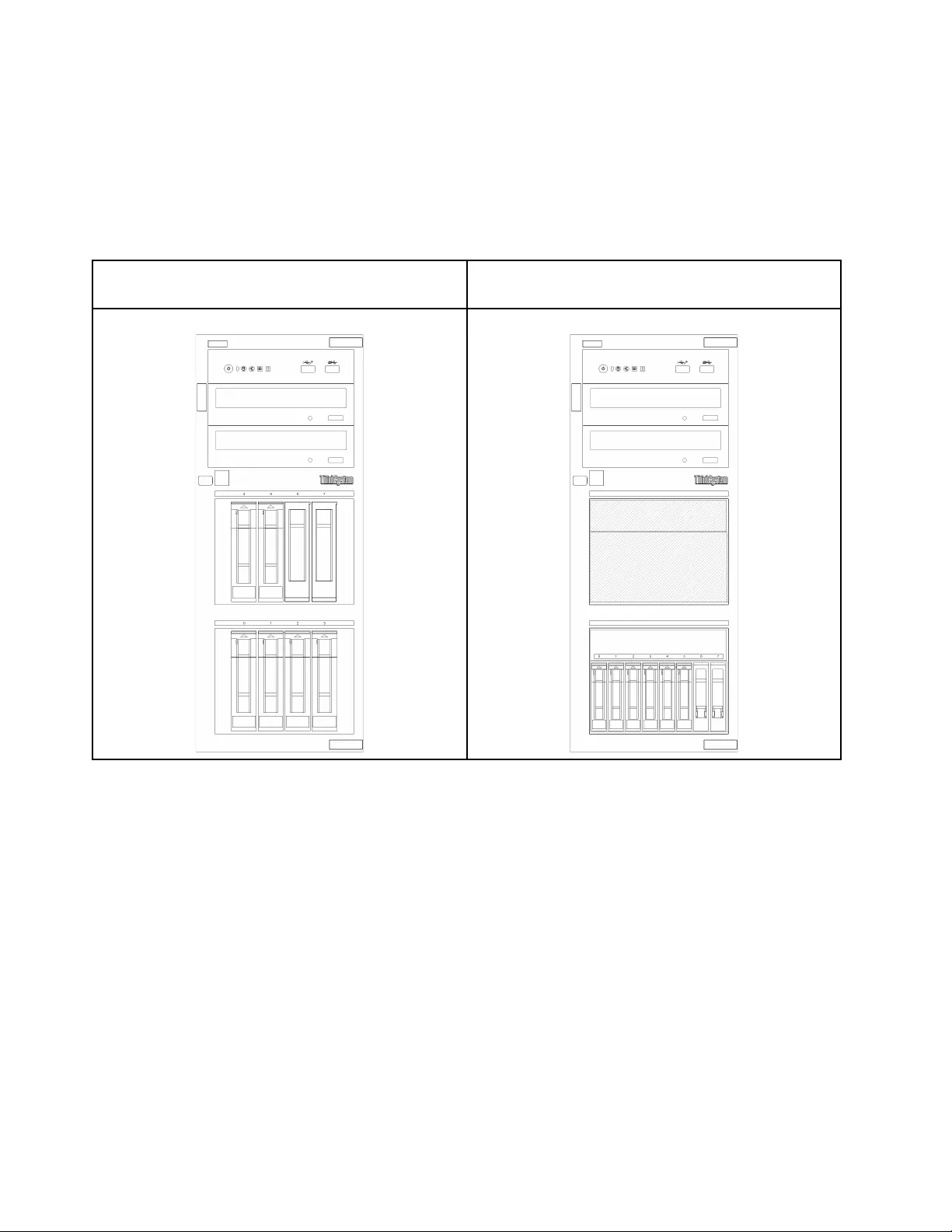
Only a maximum of six hard drives and not eight can be installed in the server if no ServeRAID SAS/SATA
controller is installed, but any of the following drives are installed:
• One optical disk drive
• Two optical disk drives
• One SATA M2 drive
• One SATA M2 drive and one optical disk drive
Front view of server models with six 3.5-inch
hot-swap drives
Front view of server models with six 2.5-inch
hot-swap drives
Figure 5. Front view of server models with six 3.5-inch or 2.5–inch hot-swap drives
16 ThinkSystem ST250 Maintenance Manual

Front view of server models with four 3.5-inch
simple-swap drives
Front view of server models with eight 3.5-inch
simple-swap drives
Figure 7. Front view of server models with four/eight 3.5-inch simple-swap drives
18 ThinkSystem ST250 Maintenance Manual
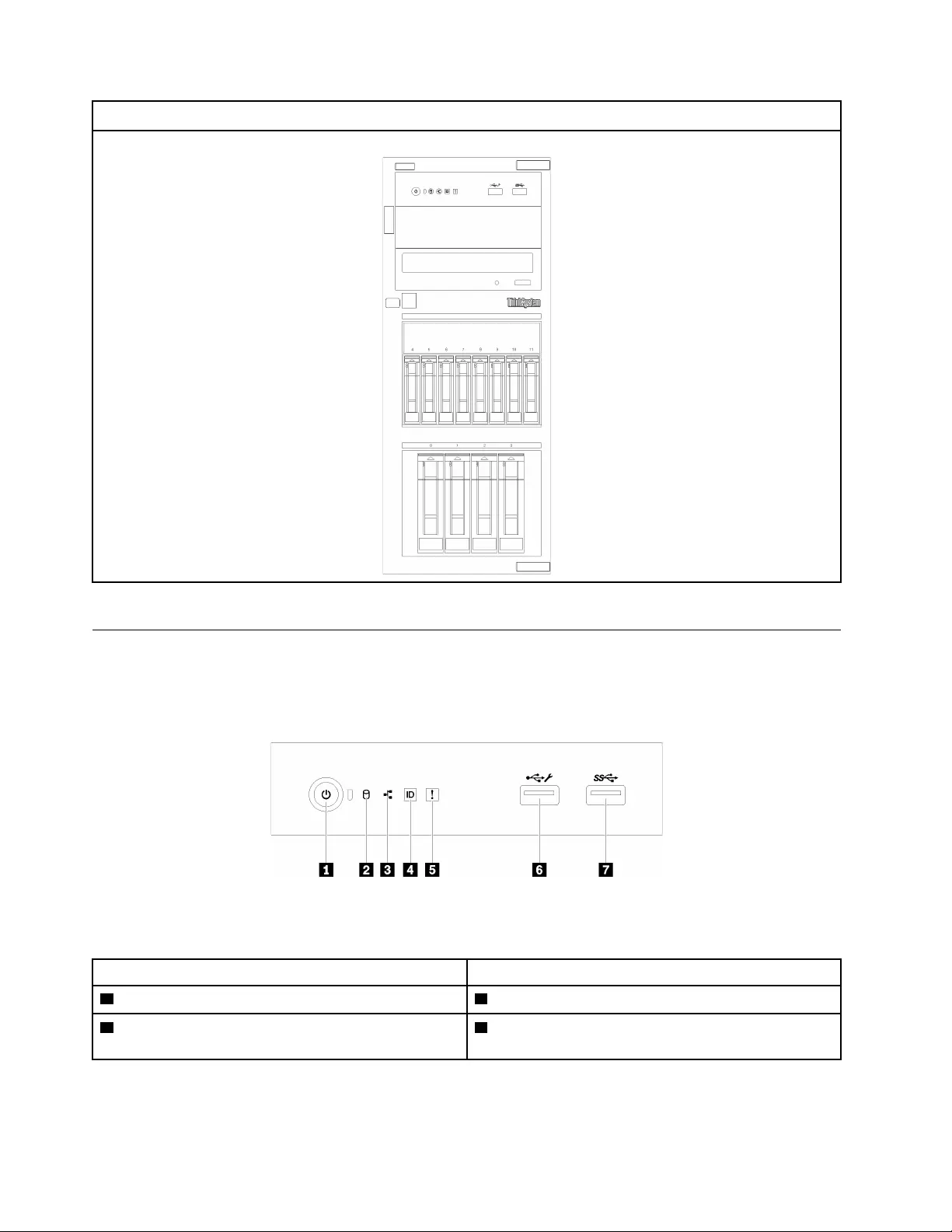
Front view of server models with four 3.5-inch hot-swap drives and eight 2.5-inch hot-swap drives
Figure 9. Front view of server models with four 3.5-inch hot-swap drives and eight 2.5-inch hot-swap drives
Front panel
The front panel of the server provides controls, connectors, and LEDs.
The following illustration shows the control, connectors, and LEDs on the front panel of the server.
Figure 10. Front panel
Table 4. Components on the front panel
Callout Callout
1 Power button with power status LED (green) 5 System error LED (yellow)
2 Drive activity LED (green)
Note: For onboard SATA indication only
6 XClarity Controller USB 2.0 connector
20 ThinkSystem ST250 Maintenance Manual

Table 4. Components on the front panel (continued)
Callout Callout
3 Network activity LED (green)
Note: For onboard LAN indication only
7 USB 3.1 Gen 1 connector
4 System ID button with system ID LED (blue)
1 Power button with power status LED
You can press the power button to turn on the server when you finish setting up the server. You also can hold
the power button for several seconds to turn off the server if you cannot turn off the server from the operating
system. The power status LED helps you determine the current power status.
Status Color Description
Solid on Green The server is on and running.
Slow blinking
(about one flash
per second)
Green The server is off and is ready to be powered on (standby state).
Fast blinking
(about four
flashes per
second)
Green The server is off, but the XClarity Controller is initializing, and the server is not ready
to be powered on.
Off None There is no ac power applied to the server.
2 Drive activity LED
The drive activity LED helps you determine the status of the drive activity.
Note: The drive activity LED only indicates the activities of drives that are connected to the SATA ports on
the system board.
Status Color Description
Solid on Green The drive is active.
Off None The drive is not active.
3 Network activity LED
The network activity LED helps you identify the network connectivity and activity.
Status Color Description
On Green The server is connected to a network.
Blinking Green The network is connected and active.
Off None The server is disconnected from the network.
4 System ID button with system ID LED
Use this system ID button and the blue system ID LED to visually locate the server. Each time you press the
system ID button, the state of the system ID LED changes. The LED can be changed to on, blinking, or off.
Chapter 2.Server components 21

You can also use the Lenovo XClarity Controller or a remote management program to change the state of the
system ID LED to assist in visually locating the server among other servers.
If the XClarity Controller USB connector is set to have both the USB 2.0 function and XClarity Controller
management function, you can press the system ID button for three seconds to switch between the two
functions.
5 System error LED
The system error LED provides basic diagnostic functions for your server.
Status Color Description Action
On Yellow An error has been detected on the server.
Causes might include one or more of the
following errors:
• The temperature of the server reached
the non-critical temperature threshold.
• The voltage of the server reached the
non-critical voltage threshold.
• A fan has been detected to be running at
low speed.
• A fan has been removed.
• The power supply has a critical error.
• The power supply is not connected to
the power.
Check the event log to determine the exact
cause of the error.
Off None The server is off or the server is on and is
working correctly.
None.
6 XClarity Controller USB connector
Depending on the setting, this connector supports USB 2.0 function, XClarity Controller management
function, or both.
• If the connector is set for USB 2.0 function, you can attach a device that requires a USB 2.0 connection,
such as a keyboard, a mouse, or a USB storage device.
• If the connector is set for XClarity Controller management function, you can attach a mobile device
installed with the application to run XClarity Controller event logs.
• If the connector is set to have both functions, you can press the system ID button for three seconds to
switch between the two functions.
7 USB 3.1 Gen 1 connector
Used to attach a device that requires a USB 2.0 or 3.0 connection, such as a keyboard, a mouse, or a USB
flash drive.
Server locks
Locking the server cover prevents unauthorized access to the inside of your server. Locking the front door
(available on some models) prevents unauthorized access to the installed drives.
Padlock
Your server comes with a padlock loop. When a padlock is installed, the server cover cannot be removed.
22 ThinkSystem ST250 Maintenance Manual
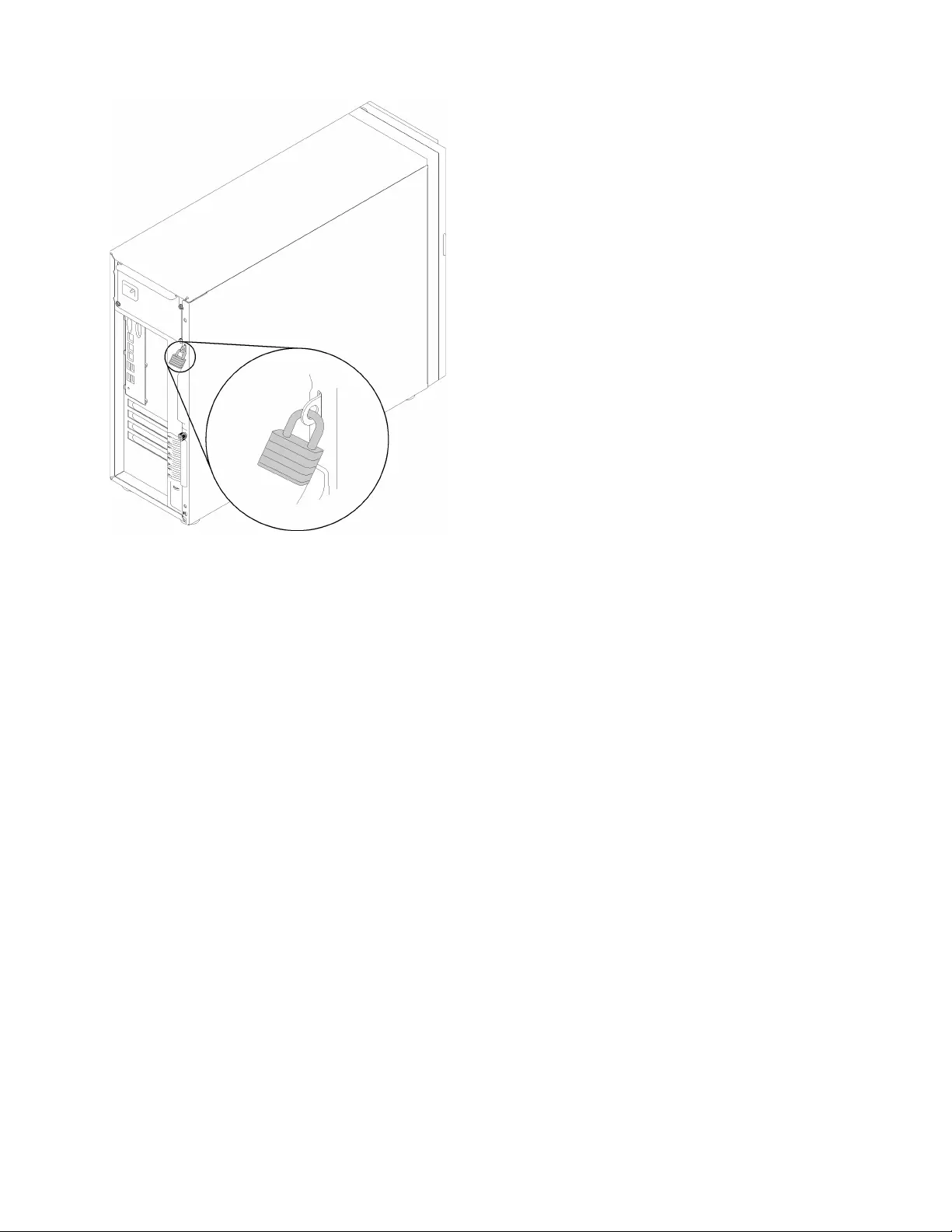
Figure 11. Padlock
Kensington-style cable lock
You can use a Kensington-style cable lock to secure your server to a desk, table, or other non-permanent
fixture. The cable lock attaches to the security-lock slot at the rear of your server and is operated with a key
or combination depending on the type selected. The cable lock also locks the server cover. This is the same
type of lock used with many notebook computers. You can order such a cable lock directly from Lenovo by
searching for Kensington at:
http://www.lenovo.com/support
Chapter 2.Server components 23

Figure 12. Kensington-style cable lock
Front door lock
You can remove the key attached on the rear of the server and use it to open or lock the front door of the
server. The front door protects the drive cage and prevents unauthorized access to the installed drives.
Figure 13. Front door lock
Rear view
Use this information to locate the connectors and components on the rear of your server. The following
illustration shows the rear view of a server with a screw-secured, fixed power supply.
24 ThinkSystem ST250 Maintenance Manual

Rear view of server models with a fixed power
supply
Rear view of server models with two hot-swap
power supplies
Figure 14. Rear view
Table 5. Components on the rear of server models with a fixed power supply or two hot-swap power supplies
1 Power cord connector 6 Ethernet 2 connector
2 VGA connector 7 USB 3.1 Gen 2 connector
3 Serial connector 8 USB 3.1 Gen 1 connector
4 Dedicated XClarity Controller (XCC) network connector 9 PCIe slots
5 Ethernet 1 connector (shared with XCC network port)
1 Power cord connector
Connect the power cord to this component.
2 VGA connector
Used to attach a VGA-compatible video device, such as a VGA monitor.
3 Serial connector
Connect a 9-pin serial device to this connector. The serial port is shared with the XCC. The XCC can take
control of the shared serial port to redirect serial traffic, using Serial over LAN (SOL).
Chapter 2.Server components 25
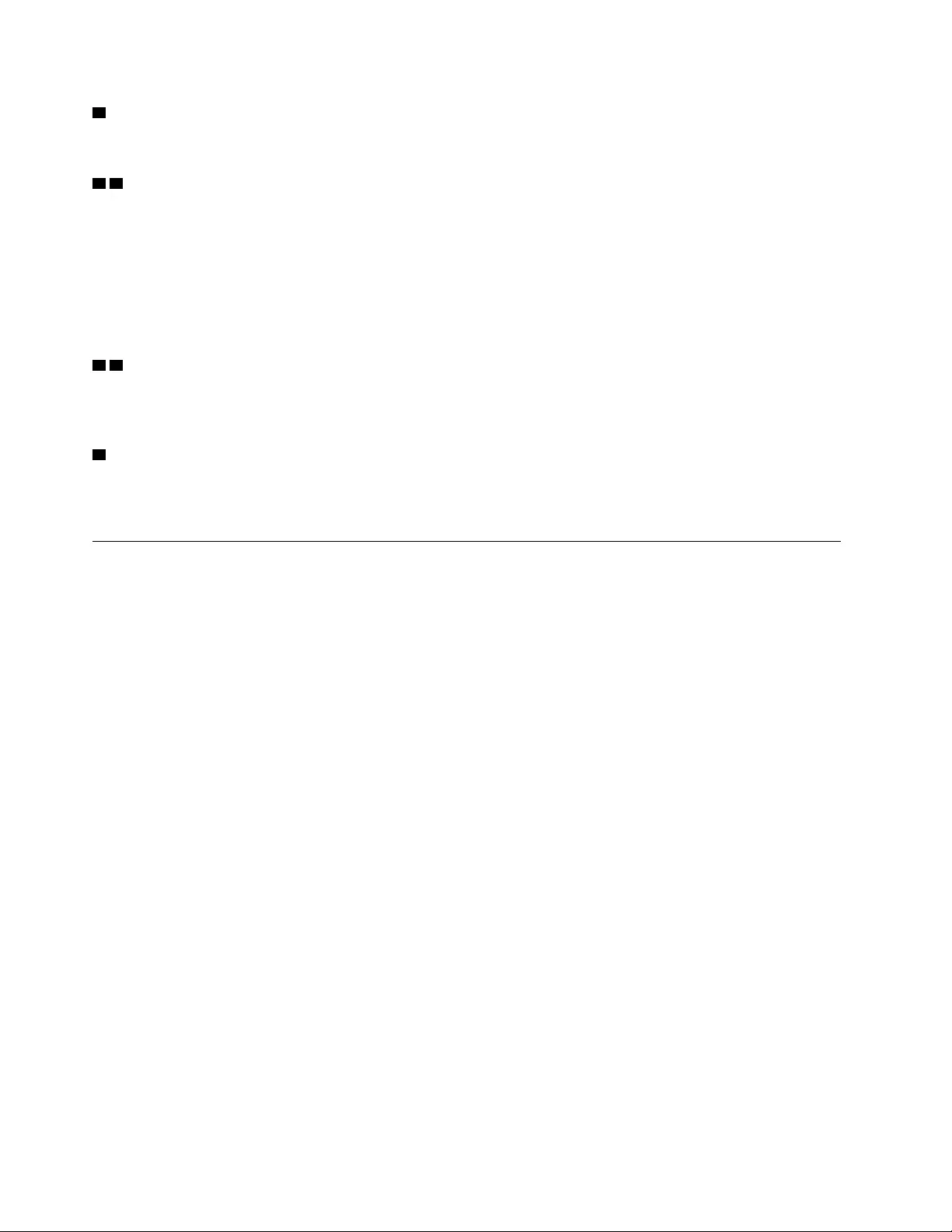
4 Dedicated XClarity Controller (XCC) network connector
Used to attach an Ethernet cable to manage the system using XClarity Controller.
5 6 Ethernet 1 and 2 connectors
Used to attach an Ethernet cable for a LAN. Each Ethernet connector has two status LEDs to help you
identify the Ethernet connectivity and activity. For more information, see “Rear view LEDs” on page 26.
Ethernet 1 connector can be set as XClarity Controller Network connector.
To set Ethernet 1 connector as XClarity Controller Network connector, start Setup Utility and select BMC
Settings ➙ Network Settings ➙ Network Settings Network Interface Port : Shared. Then, click Shared
NIC on and select Onboard Port 1.
7 8 USB 3.1 Gen1 or Gen 2 connectors
Used to attach a device that requires a USB 3.1 connection, such as a keyboard, a mouse, or a USB flash
drive.
9 PCIe slots
Your server has four PCIe slots on the system board for you to install appropriate PCIe adapters. For
information about the PCIe slots, see “Specifications” on page 3.
Rear view LEDs
The illustration in this section shows the LEDs on the rear the server.
26 ThinkSystem ST250 Maintenance Manual
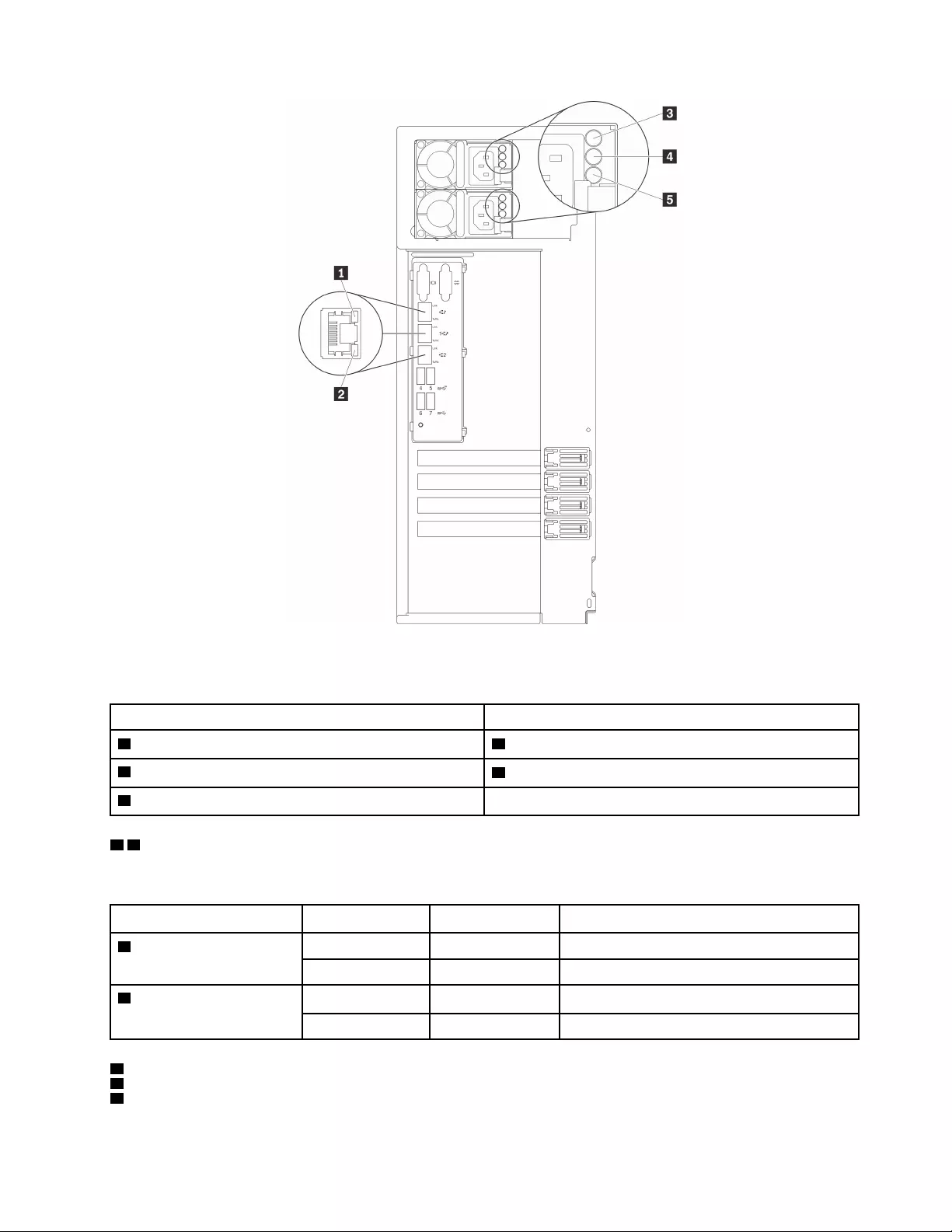
Figure 15. Rear view LEDs of the server
Table 6. LEDs on the rear of the server
Callout Callout
1 Ethernet link LED (green) 4 Power output LED (green)
2 Ethernet activity LED (green) 5 Power supply error LED (yellow)
3 Power input LED (green)
1 2 Ethernet status LEDs
Each network connector has two status LEDs.
Ethernet status LED Color Status Description
1 Ethernet link LED Green On Network link is established.
None Off Network link is disconnected.
2 Ethernet activity LED Green Blinking Network link is connected and active.
None Off The server is disconnected from a LAN.
3 Power input LED
4 Power output LED
5 Power supply error LED
Chapter 2.Server components 27

Each hot-swap power supply has three status LEDs.
LED Description
3 Power input LED • Off: The power supply is disconnected from the ac power source or a power problem
occurs.
• Green: The power supply is connected to the ac power source.
4 Power output LED • Green: The server is on and the power supply is working normally.
• Blinking green: The power supply is in zero-output mode (standby). When the server
power load is low, one of the installed power supplies enters into the standby state
while the other one delivers entire load. When the power load increases, the standby
power supply will switch to active state to provide sufficient power to the server.
To disable zero-output mode, start the Setup utility, go to System Settings ➙ Power
➙ Zero Output and select Disable. If you disable zero-output mode, both power
supplies will be in the active state.
• Off: The server is powered off, or the power supply is not working properly. If the
server is powered on but the power output LED is off, replace the power supply.
5 Power supply error LED • Off: The power supply is working normally.
• Yellow: The power supply has failed. To resolve the issue, replace the power supply.
28 ThinkSystem ST250 Maintenance Manual

System board components
The illustration in this section shows the component locations on the system board.
Figure 16. System board components
Table 7. Components on the system board
Callout Callout
1 Fan 3 connector for Rear FAN 19 Front panel connector
2 Processor power connector 20 SATA hard disk drive 6/optical disk drive connector 1
3 Processor 21 SATA hard disk drive 7/optical disk drive connector 2
4 Backplane 1 power connector 22 SATA hard disk drive 0–3 connector
5 PIB side band connector 23 SATA hard disk drive 4 connector
6 Fan 1 connector for Front FAN 1 24 SATA hard disk drive 5 connector
7 Backplane 2 power connector 25 Front USB 3.0 / 2.0 header
8 Fan 2 connector for CPU FAN 26 PCIe3 x8 slot 4
9 Optical drive power connector 27 PCIe3 x4 slot 3
10 System power connector 28 PCIe3 x16 slot 2
11 CMOS battery 29 PCIe3 x1 slot 1
12 Internal USB 3.1 Gen 1 connector 30 NMI button
13 TPM card connector 31 USB 3.1 Gen 1 connectors
14 Mounting nut for 80 mm M.2 32 USB 3.1 Gen 2 connectors
15 Mounting nut for 42 mm M.2 33 Ethernet 2 connector
Chapter 2.Server components 29

Table 7. Components on the system board (continued)
Callout Callout
16 Fan 4 connector for Front FAN 4 34 Ethernet 1 connector (shared with XCC network port)
17 M.2 module connector 35 Dedicated XClarity Controller (XCC) network
connector
18 Chassis intrusion switch connector 36 VGA + COM connector
System board jumpers
The following illustration shows the location of the jumpers on the server.
Figure 17. System board jumpers
Table 8. Jumper description
Jumper name Jumper setting
1 NCSI functional header jumper • Pins 1&2: Default
• Pins 2&3: Disable
2 Power permission override jumper • Pins 1&2: Default
• Pins 2&3: Enable
3 Clear CMOS jumper • Pins 1&2: Default
• Pins 2&3: CMOS clear
4 TPM presence header jumper • Pins 1&2: Default
• Pins 2&3: TPM presence asserted
5 IMM force update jumper • Pins 1&2: Default
• Pins 2&3: Enable
Important:
• Before you move the jumpers, turn off the server; then, disconnect all power cords and external cables.
Do not open your server or attempt any repair before reading and understanding the following information:
30 ThinkSystem ST250 Maintenance Manual

– http://thinksystem.lenovofiles.com/help/topic/safety_documentation/pdf_files.html
– “Handling static-sensitive devices” on page 55
• Any system-board switch or jumper block that is not shown in the illustrations in this document are
reserved.
Internal cable routing
Some of the components in the server come with internal cables meant for specific connectors.
Before connecting the cables, read the following guidelines carefully:
• Turn off the server before you connect or disconnect any internal cables.
• Refer to the documentation that comes with any external devices for additional cabling instructions.
• Make use of the identifiers printed on the cables to locate the proper connectors.
• Ensure that the cable is not pinched and does not cover any connectors or obstruct any components on
the system board.
Notes:
1. Disengage all latches, release tabs, or locks on cable connectors when you disconnect cables from the
system board. Failing to release them before removing the cables will damage the cable sockets on the
system board, which are fragile. Any damage to the cable sockets might require replacing the system
board.
2. When installing the front system fan into the chassis, make sure the cables do not interfere with the two
posts and the fan is firmly seated.
Fan power cable
Use the section to understand the internal routing and connectors for the fan power cables.
Chapter 2.Server components 31

Figure 18. Fan power cable routing
Table 9. Location of fan power connectors on system board
Callout Callout
1 Front fan 1 3 Rear fan
2 CPU fan 4 Front fan 4
Front panel
Use the section to understand the cable routing for the front panel.
Note: Ensure that all cables are routed through the correct cable clips.
32 ThinkSystem ST250 Maintenance Manual

Optical drive
Use the section to understand the cable routing for the optical drives.
Note: Ensure that all cables are routed through the correct cable clips.
Figure 20. Cable routing for the optical drives
Cable From To
1 Power cable Power connector on each optical drive Optical disk drive power connector on the
system board
2 Signal cable Signal connector on the optical drive 1 Optical disk drive 1 signal connector on the
system board
3 Signal cable Signal connector on the optical drive 2 Optical disk drive 2 signal connector on the
system board
34 ThinkSystem ST250 Maintenance Manual
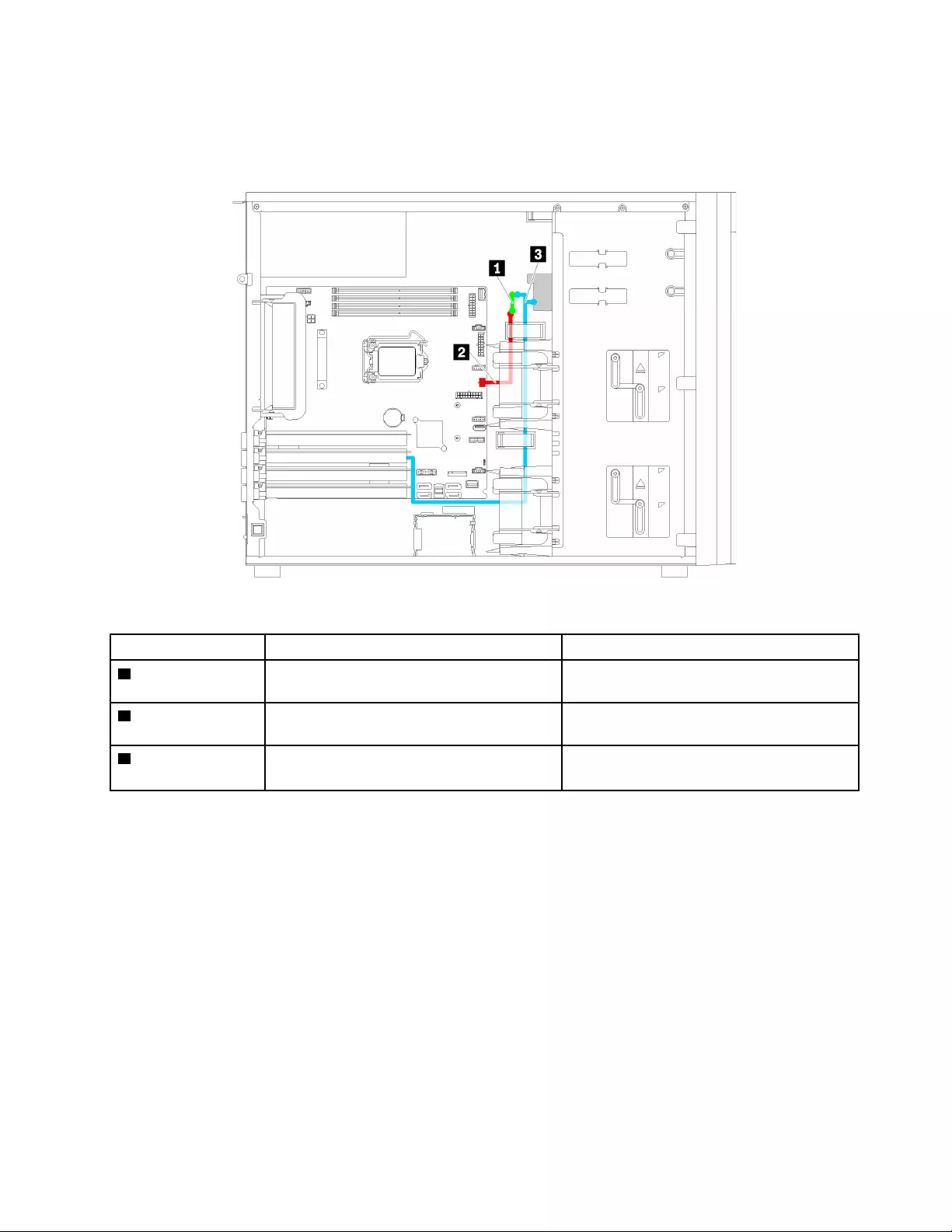
Tape drive
Use the section to understand the cable routing for the tape drive.
SAS tape drive
Figure 21. Cable routing for the SAS tape drive
Cable From To
1 Signal to power
cable
Power connector on tape drive Power connector on power cable
2 Power cable Power connector on power cable Optical drive power connector on system
board
3 Signal cable with
power
Signal connector on tape drive An available connector on the HBA adapter
Note: Ensure that all cables are routed through the correct cable clips.
Chapter 2.Server components 35

USB tape drive
Figure 22. Cable routing for the USB tape drive
Cable From To
1 Power cable Power connector on power cable Optical drive power connector on system
board
2 Signal cable Signal connector on the tape drive Internal USB 3.0 connector on the system
board
Note: Ensure that all cables are routed through the correct cable clips.
Redundant power supply
Use the section to understand the cable routing for the redundant power supply.
Notes:
• Ensure that all cables are routed through the correct cable clips.
• When installing front fan 2, the cabling highlighted by the red circle may interfere with the installation. If
this happens, push the cabling downwards and neatly tuck them under front fan 2.
36 ThinkSystem ST250 Maintenance Manual

Figure 23. Cable routing for the redundant power supply
Cable From To
1 Signal cable Signal connector on the power interface
board
Signal connector on the system board
2 CPU power cable CPU power connector on the power
interface board
CPU power connector on the system board
3 Power cable System power connector on the power
interface board
System power connector on the system
board
Chapter 2.Server components 37

Fixed power supply
Use the section to understand the cable routing for the fixed power supply.
Note: Ensure that all cables are routed through the correct cable clips.
Figure 24. Cable routing for the fixed power supply
Cable From To
1 Power supply system
power cable System power connector on paddle board System power connector on the fixed
power supply
2 Power supply CPU
power cable
CPU power connector on paddle board CPU power connector on the fixed power
supply
3 CPU power cable CPU power connector on the fixed power
supply
CPU power connector on the system board
4 System power cable System power connector on the fixed
power supply
System power connector on the system
board
38 ThinkSystem ST250 Maintenance Manual

Simple-swap-drive backplate
Use the section to understand the cable routing for the simple-swap-drive backplate.
This topic contains the following information:
• “Server models with four 3.5-inch simple-swap drives (software RAID)” on page 39
• “Server models with eight 3.5-inch simple-swap drives (software RAID)” on page 40
Server models with four 3.5-inch simple-swap drives (software RAID)
Use this section to understand the cable routing for server models with four 3.5-inch simple-swap drives
(software RAID).
Figure 25. Cable routing for server models with four 3.5-inch simple-swap drives (software RAID)
Note: Ensure that all cables are routed through the correct cable clips.
Cable From To
Simple-swap disk drive cable SAS connector on the backplate
1 Backplane 1 power connector on the
system board
2 SATA 0–3 connector on the system
board
Chapter 2.Server components 39

Server models with eight 3.5-inch simple-swap drives (software RAID)
Use this section to understand the cable routing for server models with eight 3.5-inch simple-swap drives
(software RAID).
Note: Ensure that all cables are routed through the correct cable clips.
Figure 26. Cable routing for server models with eight 3.5-inch simple-swap drives (software RAID)
Cable From To
First simple-swap disk drive cable SAS connector on the backplate
1 Backplane 1 power connector on the
system board
4 SATA 0–3 connector on the system
board
Second simple-swap disk drive
cable SAS connector on the backplate
2 SATA 4–7 connector on the system
board
3 Backplane 2 power connector on the
system board
40 ThinkSystem ST250 Maintenance Manual

Hot-swap-drive backplane
Use the section to understand the cable routing for hot-swap-drive backplanes.
This topic contains the following information:
• “Server models with eight 2.5-inch hot-swap drives (hardware RAID)” on page 43
• “Server models with sixteen 2.5-inch hot-swap drives (hardware RAID)” on page 44
• “Server models with four 3.5-inch hot-swap drives (hardware RAID)” on page 41
• “Server models with eight 3.5-inch hot-swap drives (hardware RAID)” on page 42
• “Server models with four 3.5-inch hot-swap drives and eight 2.5-inch hot-swap drives (hardware RAID)”
on page 47
Before you route cables for backplanes, observe the following guidelines when select a PCIe slot:
• The NVMe adapter can be installed only in PCIe slot 2.
• Internal RAID adapters can be installed in either PCIe slot 1 or PCIe slot 2.
Server models with four 3.5-inch hot-swap drives (hardware RAID)
Use this section to understand the cable routing for server models with four 3.5-inch hot-swap SAS/SATA
drives (hardware RAID).
Notes:
• Ensure that all cables are routed through the correct cable clips.
• Broken lines indicate the hidden parts.
Chapter 2.Server components 41
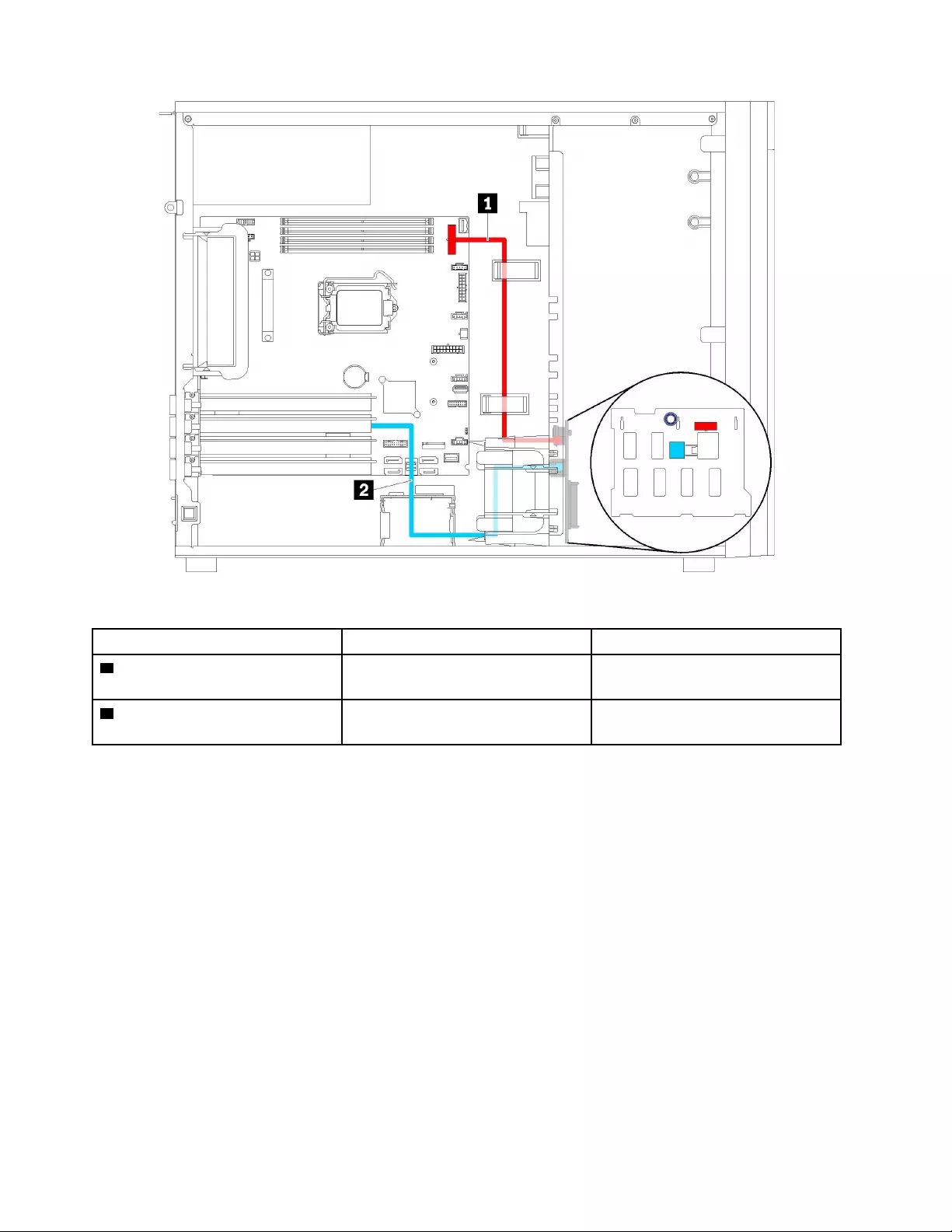
Figure 27. Cable routing for server models with four 3.5-inch hot-swap drives (hardware RAID)
Cable From To
1 Power cable for backplane 1 Power connector on backplane 1 Backplane 1 power connector on the
system board
2 SAS signal cable for backplane 1 SAS connector on backplane 1 An available connector on the RAID
adapter
Server models with eight 3.5-inch hot-swap drives (hardware RAID)
Use this section to understand the cable routing for server models with eight 3.5-inch hot-swap drives
(hardware RAID).
Note: Ensure that all cables are routed through the correct cable clips.
42 ThinkSystem ST250 Maintenance Manual
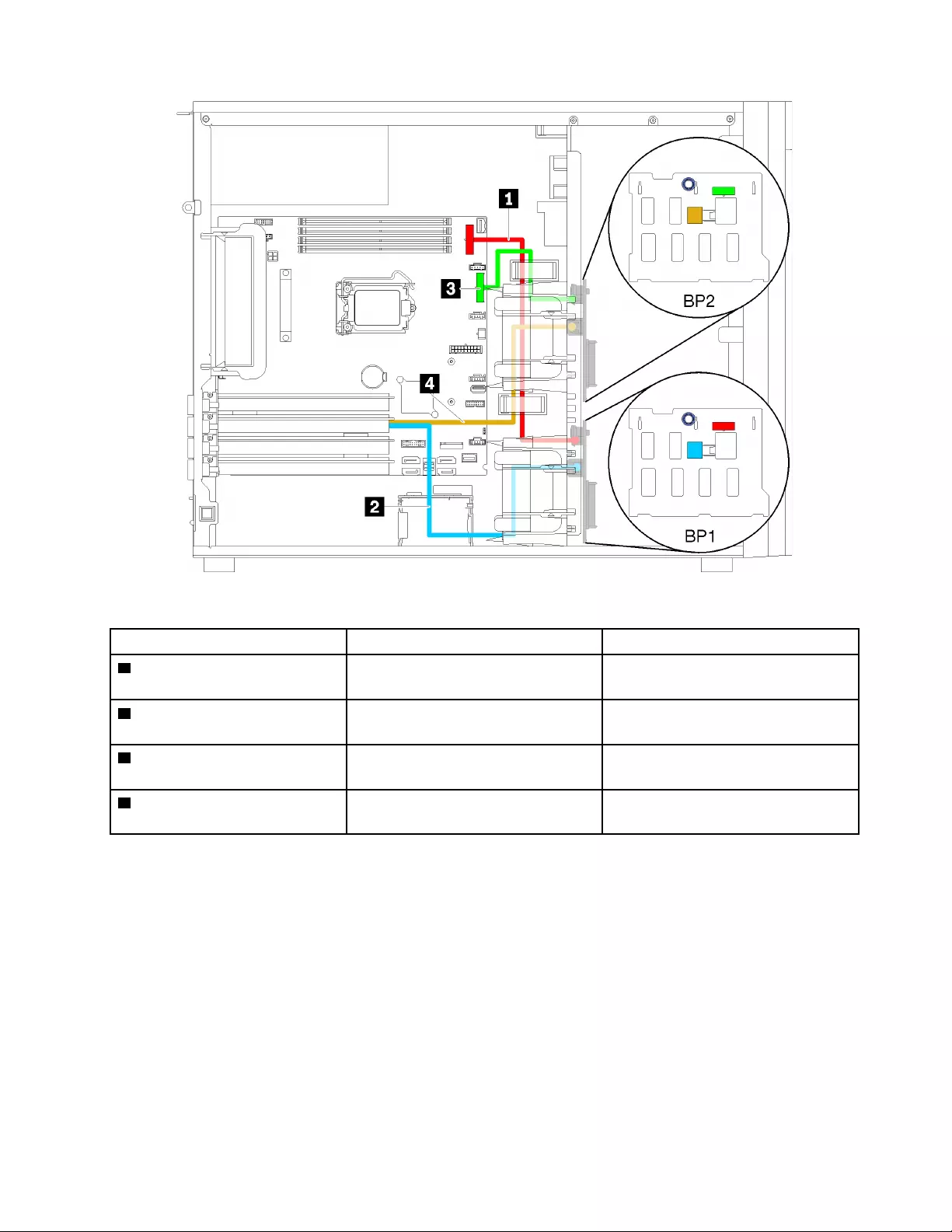
Figure 28. Cable routing for server models with eight 3.5-inch hot-swap drives (hardware RAID)
Cable From To
1 Power cable for backplane 1 Power connector on backplane 1 Backplane 1 power connector on the
system board
2 SAS signal cable for backplane 1 SAS connector on backplane 1 An available connector on the RAID
adapter
3 Power cable for backplane 2 Power connector on backplane 2 Backplane 2 power connector on the
system board
4 SAS signal cable for backplane 2 SAS connector on backplane 2 An available connector on the RAID
adapter
Server models with eight 2.5-inch hot-swap drives (hardware RAID)
Use this section to understand the cable routing for server models with eight 2.5-inch hot-swap drives
(hardware RAID).
Note: Ensure that all cables are routed through the correct cable clips.
Chapter 2.Server components 43

Figure 29. Cable routing for server models with eight 2.5-inch hot-swap drives (hardware RAID)
Cable From To
1 Power cable Power connector on the backplane Backplane 1 power connector on the system
board
2 SAS signal cable SAS 0 and SAS 1 connectors on the
backplane
Connectors on the RAID adapter
Server models with sixteen 2.5-inch hot-swap drives (hardware RAID)
Use this section to understand the cable routing for server models with sixteen 2.5-inch hot-swap drives
(hardware RAID).
Notes:
• There are two types of configurations:
– Two 8i RAID adapters
– One 16i RAID adapter
• Ensure that all cables are routed through the correct cable clips.
44 ThinkSystem ST250 Maintenance Manual
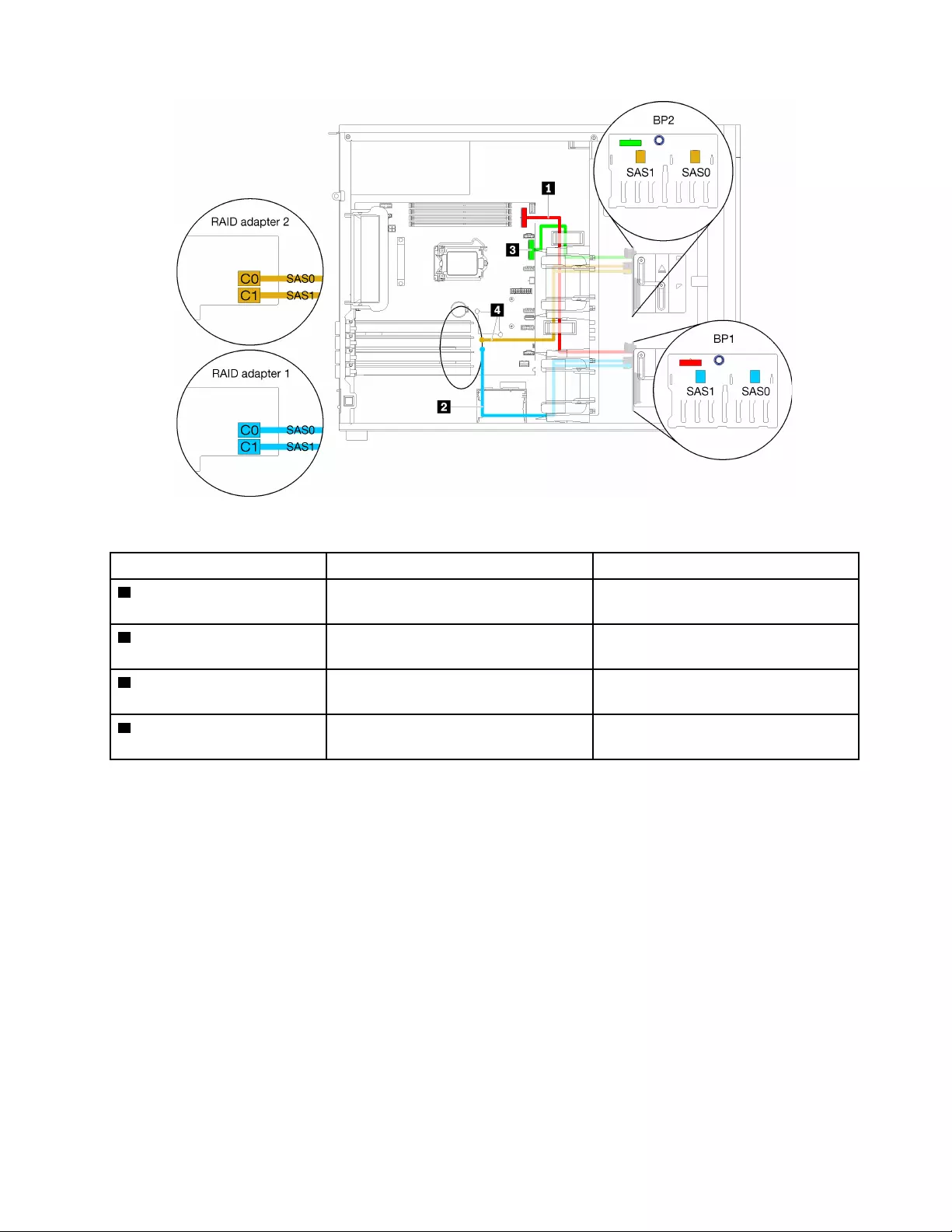
Figure 30. Cable routing server models with sixteen 2.5-inch hot-swap drives, two 8i RAID adapters (hardware RAID)
Cable From To
1 Power cable for backplane 1 Power connector on backplane 1 Backplane 1 power connector on the
system board
2 SAS signal cable for
backplane 1
SAS 0 and SAS 1 connectors on
backplane 1
Connectors on RAID adapter 1
3 Power cable for backplane 2 Power connector on backplane 2 Backplane 2 power connector on the
system board
4 SAS signal cable for
backplane 2
SAS 0 and SAS 1 connectors on
backplane 2
Connectors on RAID adapter 2
Chapter 2.Server components 45
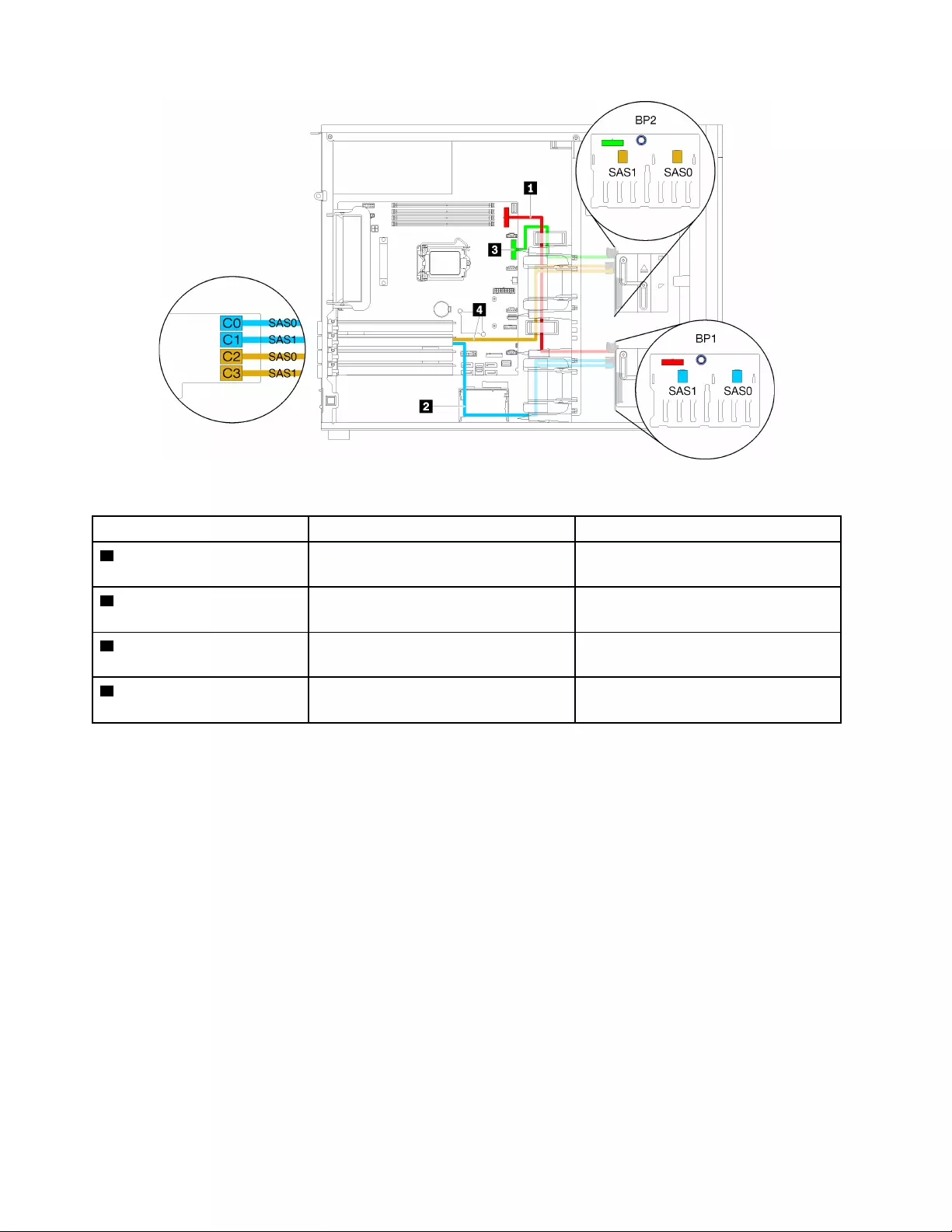
Figure 31. Cable routing server models with sixteen 2.5-inch hot-swap drives, one 16i RAID adapter (hardware RAID)
Cable From To
1 Power cable for backplane 1 Power connector on backplane 1 Backplane 1 power connector on the
system board
2 SAS signal cable for
backplane 1
SAS 0 and SAS 1 connectors on
backplane 1
C0 and C1 connectors on the 16i RAID
adapter
3 Power cable for backplane 2 Power connector on backplane 2 Backplane 2 power connector on the
system board
4 SAS signal cable for
backplane 2
SAS 0 and SAS 1 connectors on
backplane 2
C2 and C3 connectors on the 16i RAID
adapter
46 ThinkSystem ST250 Maintenance Manual

Server models with four 3.5-inch hot-swap drives and eight 2.5-inch hot-swap drives
(hardware RAID)
Use this section to understand the cable routing for server models with four 3.5-inch hot-swap drives and
eight 2.5-inch hot-swap drives (hardware RAID).
Server model: four 3.5-inch hot-swap drives and eight 2.5-inch hot-swap drives (hardware RAID)
Notes:
• There are two types of configurations:
– Two 8i RAID adapters
– One 16i RAID adapter
• Ensure that all cables are routed through the correct cable clips.
Figure 32. Cable routing for server models with four 3.5-inch hot-swap drives, eight 2.5-inch hot-swap drives, two 8i RAID
adapters (hardware RAID)
Cable From To
1 Power cable for backplane 1 Power connector on backplane 1 Backplane 1 power connector on the
system board
2 SAS signal cable for
backplane 1
SAS connector on backplane 1 C0 connector on one 8i RAID adapter 1
3 Power cable for backplane 2 Power connector on backplane 2 Backplane 2 power connector on the
system board
4 SAS signal cable for
backplane 2
SAS 1 and SAS 2 connectors on
backplane 2
C0 and C1 connectors on one 8i RAID
adapter 2
Chapter 2.Server components 47
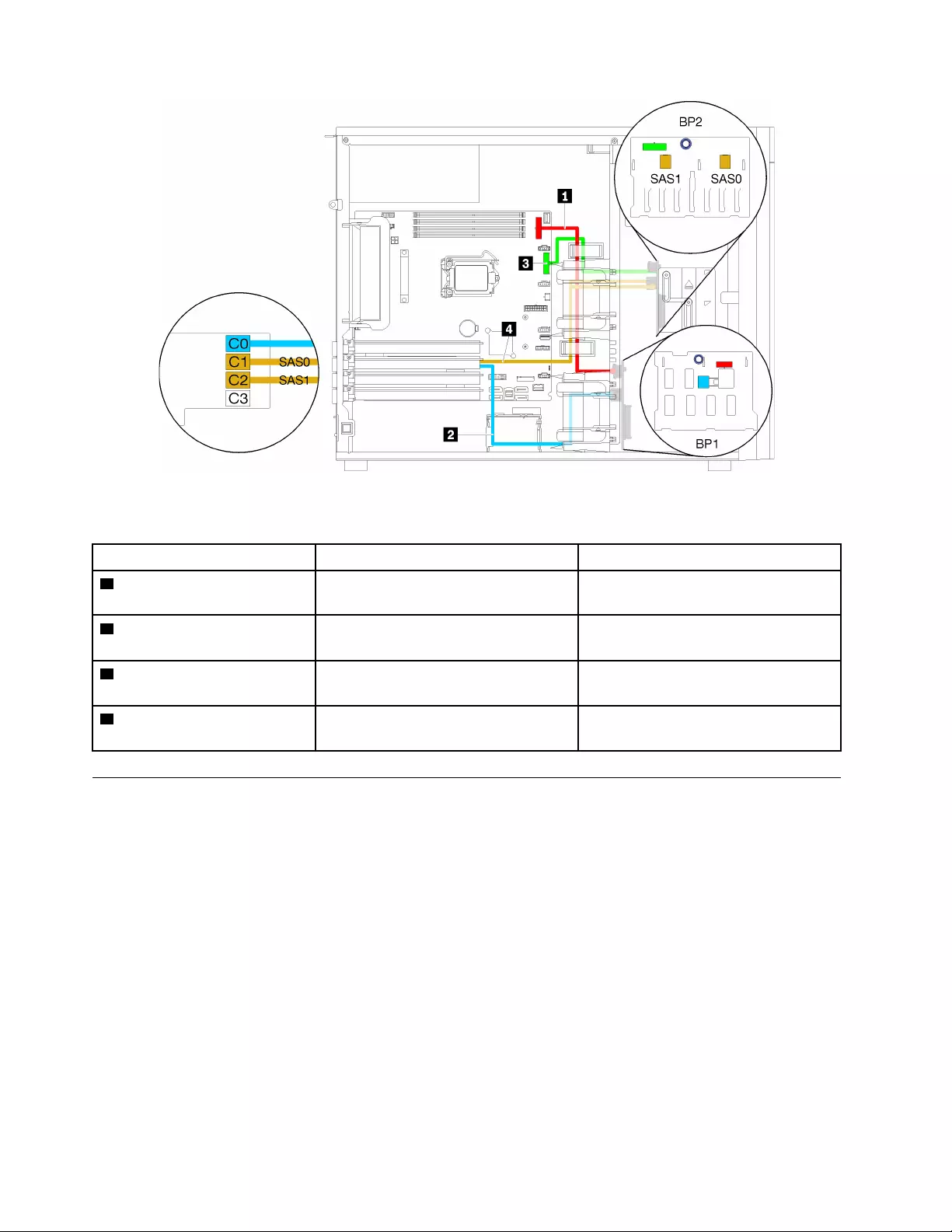
Figure 33. Cable routing for server models with four 3.5-inch hot-swap drives, eight 2.5-inch hot-swap drives, one 16i
RAID adapter (hardware RAID)
Cable From To
1 Power cable for backplane 1 Power connector on backplane 1 Backplane 1 power connector on the
system board
2 SAS signal cable for
backplane 1
SAS connector on backplane 1 C0 connector on 16i RAID adapter
3 Power cable for backplane 2 Power connector on backplane 2 Backplane 2 power connector on the
system board
4 SAS signal cable for
backplane 2
SAS 1 and SAS 2 connectors on
backplane 2
C1 and C2 connectors on 16i RAID
adapter
Parts list
Use the parts list to identify each of the components that are available for your server.
For more information about ordering the parts shown in Figure 34 “Server components” on page 49:
http://datacentersupport.lenovo.com/us/en/products/servers/thinksystem/st250/7y45/parts
Note: Depending on the model, your server might look slightly different from the illustration.
48 ThinkSystem ST250 Maintenance Manual
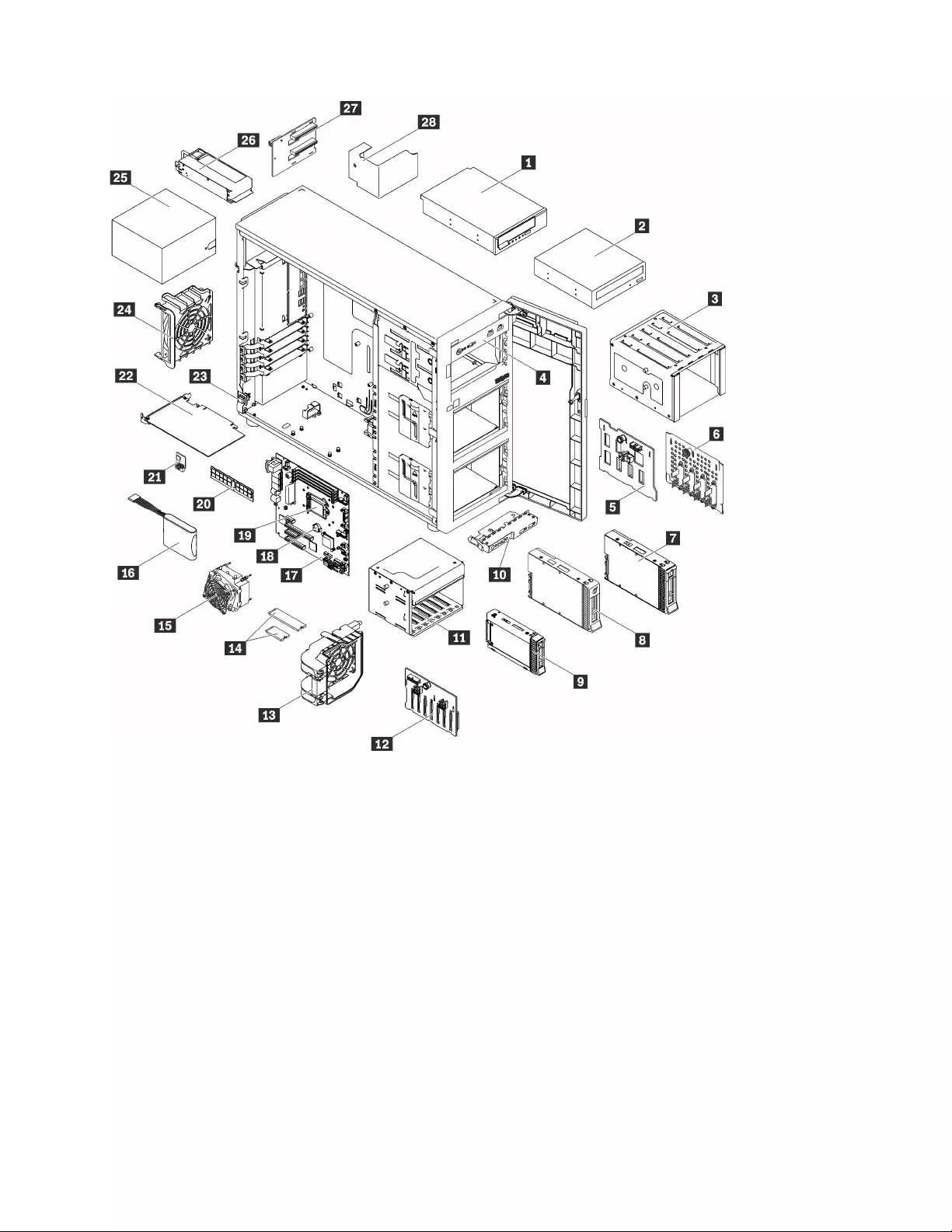
Figure 34. Server components
The parts listed in the following table are identified as one of the following:
• Tier 1 customer replaceable unit (CRU): Replacement of Tier 1 CRUs is your responsibility. If Lenovo
installs a Tier 1 CRU at your request with no service agreement, you will be charged for the installation.
• Tier 2 customer replaceable unit (CRU): You may install a Tier 2 CRU yourself or request Lenovo to
install it, at no additional charge, under the type of warranty service that is designated for your server.
• Field replaceable unit (FRU): FRUs must be installed only by trained service technicians.
• Consumable and Structural parts: Purchase and replacement of consumable and structural parts is
your responsibility. If Lenovo acquires or installs a structural component at your request, you will be
charged for the service.
Chapter 2.Server components 49
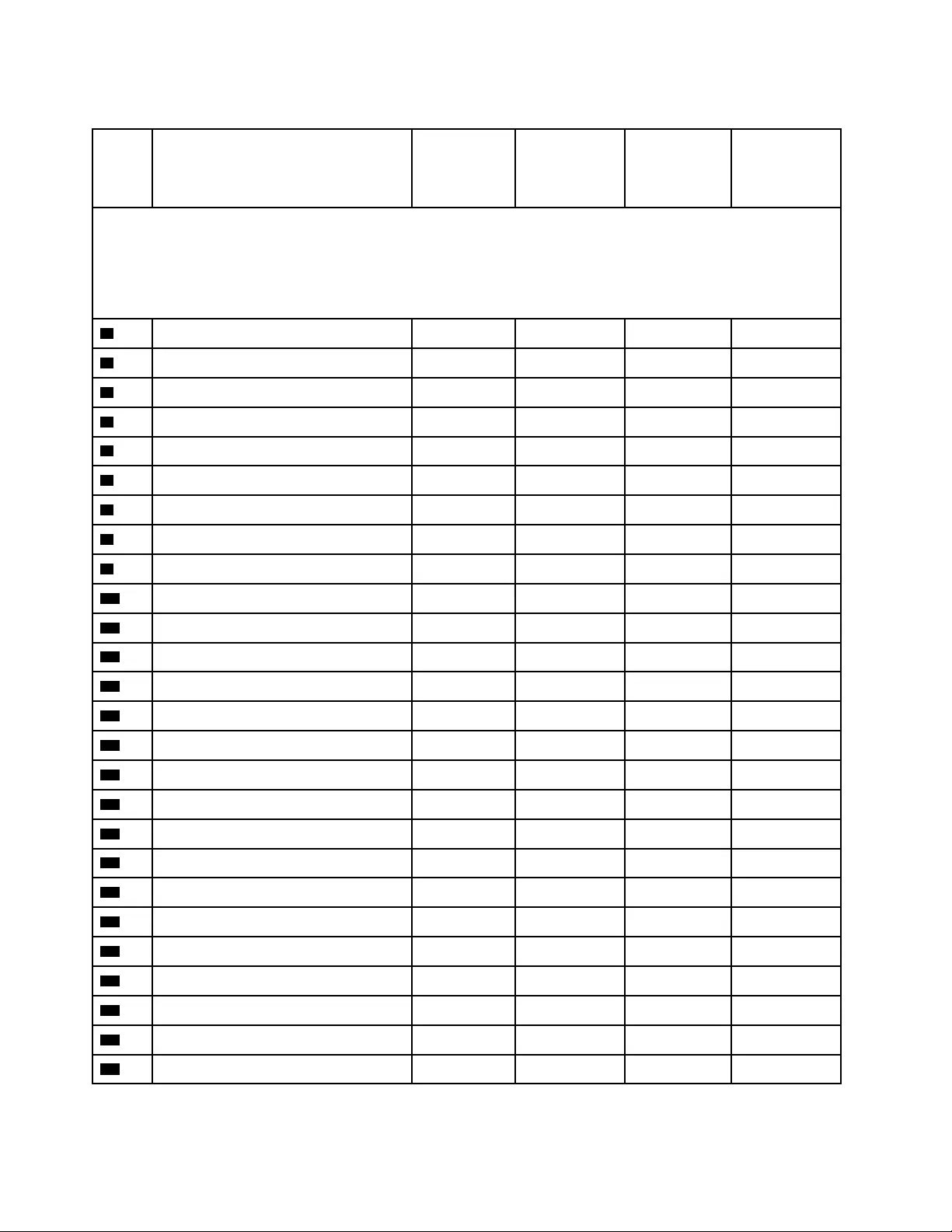
Table 10. Parts listing
Index Description Tier 1 CRU Tier 2 CRU FRU
Consumable
and
Structural
parts
For more information about ordering the parts shown in Figure 34 “Server components” on page 49:
http://datacentersupport.lenovo.com/us/en/products/servers/thinksystem/st250/7y45/parts
It is highly recommended that you check the power summary data for your server using Lenovo Capacity Planner
before purchasing any new parts.
15.25-inch LTO/RDX tape drive √
25.25-inch optical disk drive √
33.5-inch disk drive cage √
4Chassis √
53.5-inch hot-swap drive backplane √
63.5-inch simple-swap drive backplate √
73.5-inch hot-swap drive √
83.5-inch simple-swap drive √
92.5-inch hot-swap drive √
10 Front panel board assembly √
11 2.5-inch disk drive cage √
12 2.5-inch hot-swap drive backplane √
13 Front fan √
14 M.2 drive (42mm and 80mm) √
15 Heat sink fan assembly √
16 Flash power module √
17 System board √
18 CMOS battery (CR2032) √
19 Processor √
20 DIMM √
21 TPM card √
22 PCIe adapter √
23 Intrusion switch √
24 Rear fan √
25 Fixed power supply unit √
26 Redundant power supply unit √
50 ThinkSystem ST250 Maintenance Manual

Power cords
Several power cords are available, depending on the country and region where the server is installed.
To view the power cords that are available for the server:
1. Go to:
http://dcsc.lenovo.com/#/
2. Click Preconfigured Model or Configure to order.
3. Enter the machine type and model for your server to display the configurator page.
4. Click Power ➙ Power Cables to see all line cords.
Notes:
• For your safety, a power cord with a grounded attachment plug is provided to use with this product. To
avoid electrical shock, always use the power cord and plug with a properly grounded outlet.
• Power cords for this product that are used in the United States and Canada are listed by Underwriter's
Laboratories (UL) and certified by the Canadian Standards Association (CSA).
• For units intended to be operated at 115 volts: Use a UL-listed and CSA-certified cord set consisting of a
minimum 18 AWG, Type SVT or SJT, three-conductor cord, a maximum of 15 feet in length and a parallel
blade, grounding-type attachment plug rated 15 amperes, 125 volts.
• For units intended to be operated at 230 volts (U.S. use): Use a UL-listed and CSA-certified cord set
consisting of a minimum 18 AWG, Type SVT or SJT, three-conductor cord, a maximum of 15 feet in length
and a tandem blade, grounding-type attachment plug rated 15 amperes, 250 volts.
• For units intended to be operated at 230 volts (outside the U.S.): Use a cord set with a grounding-type
attachment plug. The cord set should have the appropriate safety approvals for the country in which the
equipment will be installed.
• Power cords for a specific country or region are usually available only in that country or region.
52 ThinkSystem ST250 Maintenance Manual
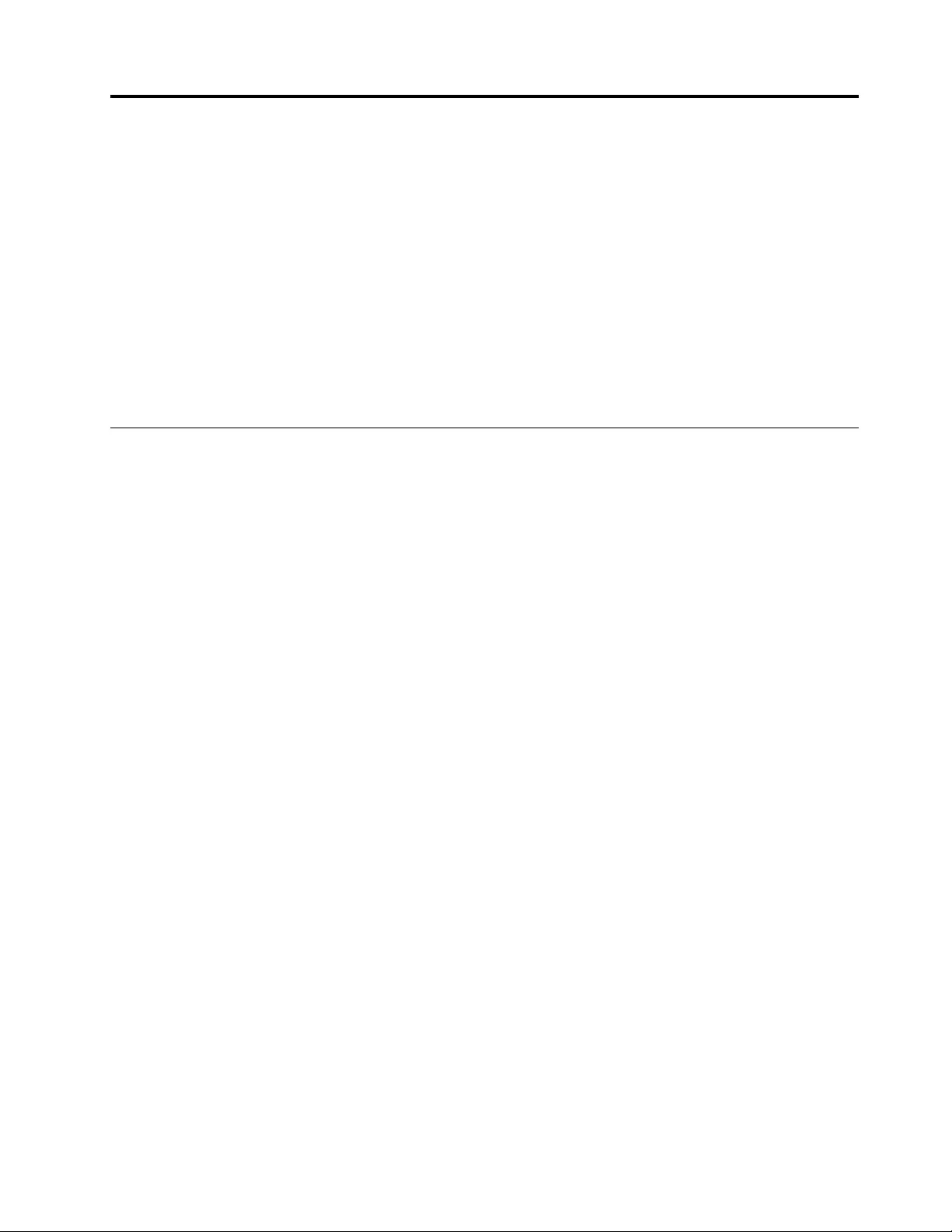
Chapter 3. Hardware replacement procedures
This section provides installation and removal procedures for all serviceable system components. Each
component replacement procedure references any tasks that need to be performed to gain access to the
component being replaced.
For more information about ordering parts:
1. Go to http://datacentersupport.lenovo.com and navigate to the support page for your server.
2. Click Service Parts.
3. Enter the serial number to view a listing of parts for your server.
Note: If you replace a part, such as an adapter, that contains firmware, you might also need to update the
firmware for that part. For more information about updating firmware, see “Firmware updates” on page 9.
Installation guidelines
Before installing components in your server, read the installation guidelines.
Before installing optional devices, read the following notices carefully:
Attention: Prevent exposure to static electricity, which might lead to system halt and loss of data, by
keeping static-sensitive components in their static-protective packages until installation, and handling these
devices with an electrostatic-discharge wrist strap or other grounding system.
• Read the safety information and guidelines to ensure your safety at work:
– A complete list of safety information for all products is available at:
http://thinksystem.lenovofiles.com/help/topic/safety_documentation/pdf_files.html
– “Handling static-sensitive devices” on page 55
• Make sure the components you are installing are supported by the server. For a list of supported optional
components for the server, see https://static.lenovo.com/us/en/serverproven/index.shtml.
• When you install a new server, download and apply the latest firmware. This will help ensure that any
known issues are addressed, and that your server is ready to work with optimal performance. Go to
ThinkSystem ST250 Drivers and Software to download firmware updates for your server.
Important: Some cluster solutions require specific code levels or coordinated code updates. If the
component is part of a cluster solution, verify that the latest level of code is supported for the cluster
solution before you update the code.
• It is good practice to make sure that the server is working correctly before you install an optional
component.
• Keep the working area clean, and place removed components on a flat and smooth surface that does not
shake or tilt.
• Do not attempt to lift an object that might be too heavy for you. If you have to lift a heavy object, read the
following precautions carefully:
– Make sure that you can stand steadily without slipping.
– Distribute the weight of the object equally between your feet.
– Use a slow lifting force. Never move suddenly or twist when you lift a heavy object.
– To avoid straining the muscles in your back, lift by standing or by pushing up with your leg muscles.
© Copyright Lenovo 2018, 2022 53

• Make sure that you have an adequate number of properly grounded electrical outlets for the server,
monitor, and other devices.
• Back up all important data before you make changes related to the disk drives.
• Have a small flat-blade screwdriver, a small Phillips screwdriver, and a T8 torx screwdriver available.
• You do not have to turn off the server to remove or install hot-swap power supplies or hot-plug USB
devices. However, you must turn off the server before you perform any steps that involve removing or
installing adapter cables, and you must disconnect the power source from the server before you perform
any steps that involve removing or installing a DIMM.
• Blue on a component indicates touch points, where you can grip to remove a component from or install it
in the server, open or close a latch, and so on.
• Terra-cotta on a component or an orange label on or near a component indicates that the component can
be hot-swapped if the server and operating system support hot-swap capability, which means that you
can remove or install the component while the server is still running. (Orange can also indicate touch
points on hot-swap components.) See the instructions for removing or installing a specific hot-swap
component for any additional procedures that you might have to perform before you remove or install the
component.
• The Red strip on the drives, adjacent to the release latch, indicates that the drive can be hot-swapped if
the server and operating system support hot-swap capability. This means that you can remove or install
the drive while the server is still running.
Note: See the system specific instructions for removing or installing a hot-swap drive for any additional
procedures that you might need to perform before you remove or install the drive.
• After finishing working on the server, make sure you reinstall all safety shields, guards, labels, and ground
wires.
System reliability guidelines
Review the system reliability guidelines to ensure proper system cooling and reliability.
Make sure the following requirements are met:
• When the server comes with redundant power, a power supply must be installed in each power-supply
bay.
• Adequate space around the server must be spared to allow server cooling system to work properly. Leave
approximately 50 mm (2.0 in.) of open space around the front and rear of the server. Do not place any
object in front of the fans.
• For proper cooling and airflow, refit the server cover before you turn the power on. Do not operate the
server for more than 30 minutes with the server cover removed, for it might damage server components.
• Cabling instructions that come with optional components must be followed.
• A failed fan must be replaced within 48 hours since malfunction.
• A removed hot-swap drive must be replaced within two minutes after removal.
• A removed hot-swap power supply must be replaced within two minutes after removal.
• Every air baffle that comes with the server must be installed when the server starts (some servers might
come with more than one air baffle). Operating the server with a missing air baffle might damage the
processor.
• All processor sockets must contain either a socket cover or a processor with heat sink.
• When more than one processor is installed, fan population rules for each server must be strictly followed.
54 ThinkSystem ST250 Maintenance Manual

Working inside the server with the power on
You might need to keep the power on with the server cover removed to look at system information on the
display panel or to replace hot-swap components. Review these guidelines before doing so.
Attention: The server might stop and loss of data might occur when internal server components are
exposed to static electricity. To avoid this potential problem, always use an electrostatic-discharge wrist
strap or other grounding systems when working inside the server with the power on.
• Avoid loose-fitting clothing, particularly around your forearms. Button or roll up long sleeves before
working inside the server.
• Prevent your necktie, scarf, badge rope, or long hair from dangling into the server.
• Remove jewelry, such as bracelets, necklaces, rings, cuff links, and wrist watches.
• Remove items from your shirt pocket, such as pens and pencils, in case they fall into the server as you
lean over it.
• Avoid dropping any metallic objects, such as paper clips, hairpins, and screws, into the server.
Handling static-sensitive devices
Review these guidelines before you handle static-sensitive devices to reduce the possibility of damage from
electrostatic discharge.
Attention: Prevent exposure to static electricity, which might lead to system halt and loss of data, by
keeping static-sensitive components in their static-protective packages until installation, and handling these
devices with an electrostatic-discharge wrist strap or other grounding system.
• Limit your movement to prevent building up static electricity around you.
• Take additional care when handling devices during cold weather, for heating would reduce indoor
humidity and increase static electricity.
• Always use an electrostatic-discharge wrist strap or other grounding system.
• While the device is still in its static-protective package, touch it to an unpainted metal surface on the
outside of the server for at least two seconds. This drains static electricity from the package and from your
body.
• Remove the device from the package and install it directly into the server without putting it down. If it is
necessary to put the device down, put it back into the static-protective package. Never place the device
on the server or on any metal surface.
• When handling a device, carefully hold it by the edges or the frame.
• Do not touch solder joints, pins, or exposed circuitry.
• Keep the device from others’ reach to prevent possible damages.
3.5-inch/2.5-inch drive cage replacement
Use this information to remove and install the 3.5-inch/2.5-inch drive cage.
Remove the 3.5-inch/2.5-inch drive cage
Use this information to remove the 3.5-inch/2.5-inch drive drive cage.
“Read the
installation
Guidelines” on
page 53
“Power off
the server for
this task” on
page 14
“ATTENTION:
Static Sensitive Device
Ground package before opening”
on page 55
Chapter 3.Hardware replacement procedures 55

Before removing the drive cage:
1. Watch the procedure
A video of this procedure is available at YouTube: https://www.youtube.com/playlist?list=
PLYV5R7hVcs-Dy5N2dPXFx5Pht-FljAi6S.
2. If the server is in a rack, remove it from the rack.
3. Remove any locking device that secures the server cover, such as a Kensington lock or a pad lock.
4. Remove the server cover (see “Remove the server cover” on page 136).
To remove the drive cage, complete the following steps:
Step 1. Remove the front door (see “Remove the front door” on page 90).
Step 2. Remove the front bezel (see “Remove the front bezel” on page 88).
Figure 35. Drive cage removal
Step 3. Remove any drives or drive bay fillers and set them aside on a static-protective surface (see
“Remove a hot-swap drive” on page 76 or “Remove a simple-swap drive” on page 74).
Step 4. Remove the system fan. See “Remove the front system fan” on page 80.
Step 5. Disconnect the cables from the backplane or backplate.
Step 6. Press and hold the drive cage release latch; then, carefully pull the drive cage out of the opening in
the chassis.
Step 7. Remove the backplane or backplate (see “Remove the 3.5-inch/2.5-inch hot-swap drive
backplane” on page 58 or “Remove the 3.5-inch simple-swap drive backplate” on page 61).
After removing the drive cage:
If you are instructed to return the defective component, please package the part to prevent any shipping
damage. Reuse the packaging the new part arrived in and follow all packaging instructions.
56 ThinkSystem ST250 Maintenance Manual
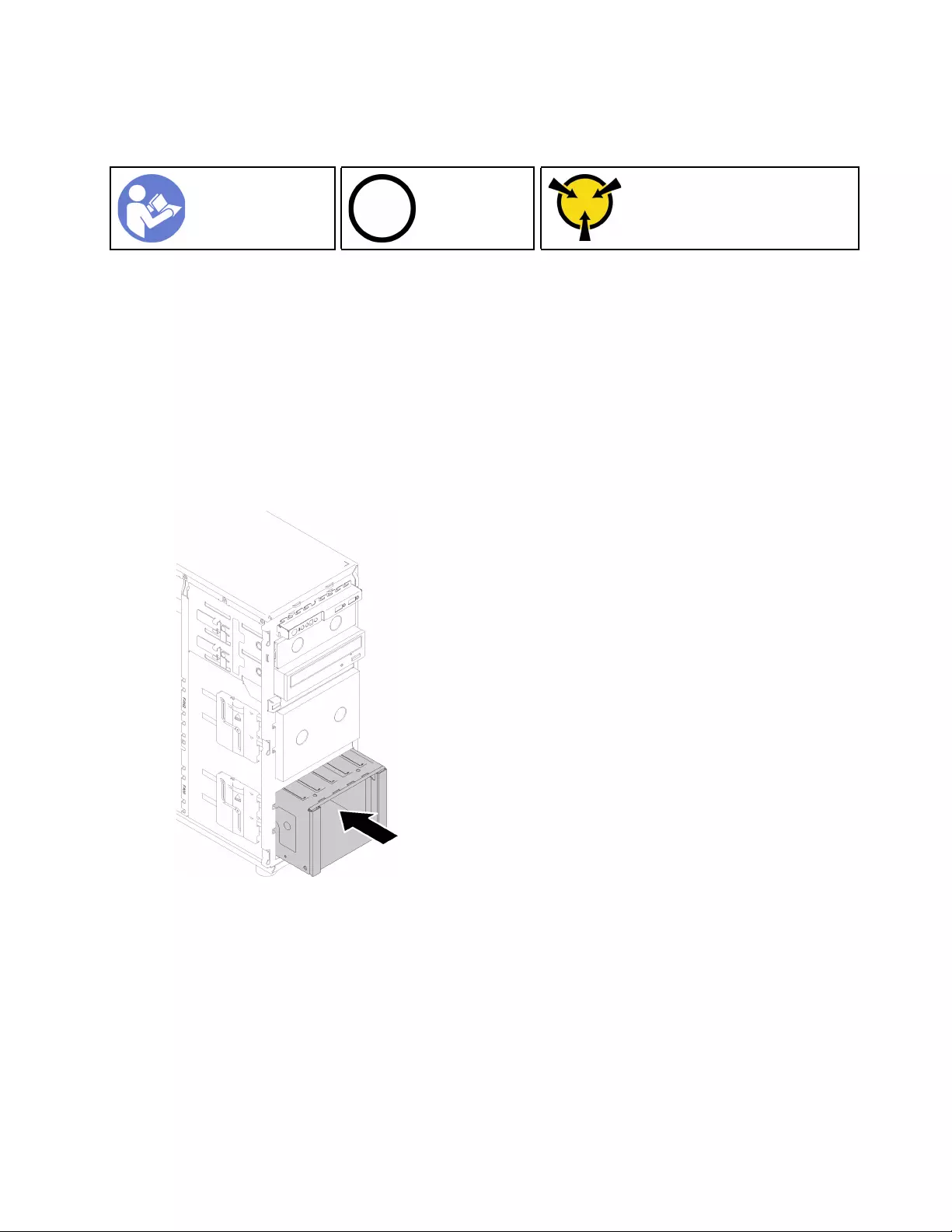
Install the 3.5-inch/2.5-inch drive cage
Use this information to install the 3.5-inch/2.5-inch drive cage.
“Read the
installation
Guidelines” on
page 53
“Power off
the server for
this task” on
page 14
“ATTENTION:
Static Sensitive Device
Ground package before opening”
on page 55
Before installing the drive cage:
1. Watch the procedure
A video of this procedure is available at YouTube: https://www.youtube.com/playlist?list=
PLYV5R7hVcs-Dy5N2dPXFx5Pht-FljAi6S.
To install the drive cage, complete the following steps:
Step 1. Install the backplane or backplate (see “Install the 3.5-inch/2.5-inch hot-swap drive backplane” on
page 59 or “Install the 3.5-inch simple-swap drive backplate” on page 62 ).
Step 2. Press the drive cage in until the release latch clicks into place.
Figure 36. Drive cage installation
After installing the drive cage:
1. Install the system fan (see “Install the front system fan” on page 81).
2. Reinstall all the drives and drive bay fillers (if any) into the drive cage (see “Install a hot-swap drive” on
page 78 or “Installing a 2.5-inch SSD into a 3.5-inch drive bay” on page 65).
3. Reconnect the cables to the backplane or backplate.
4. Complete the parts replacement. See “Complete the parts replacement” on page 155
Chapter 3.Hardware replacement procedures 57
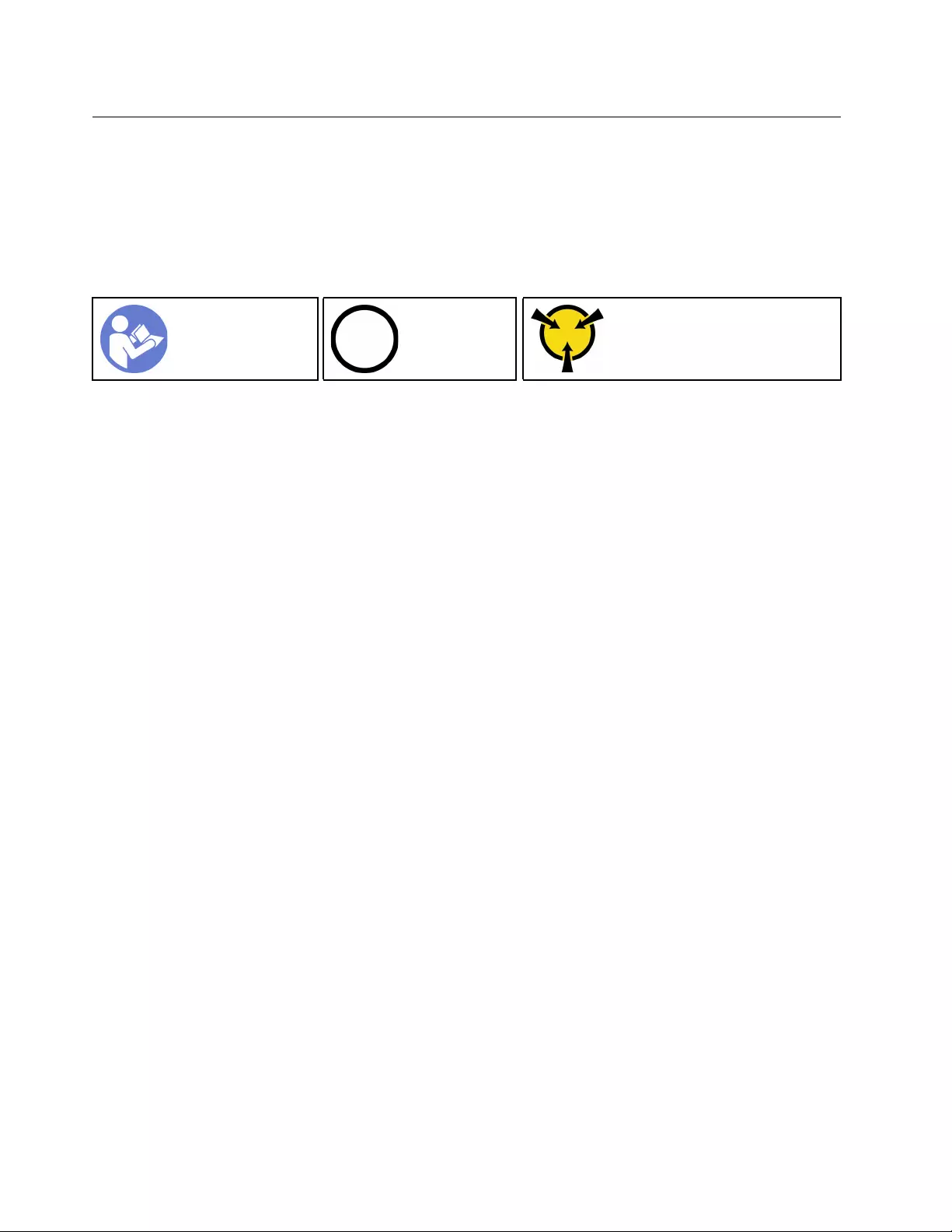
2.5-inch/3.5-inch hot-swap drive backplane replacement
Use this information to remove and install a 2.5-inch/3.5-inch hot-swap drive backplane.
This topic applies only to server models that have hot-swap drives installed.
Remove the 3.5-inch/2.5-inch hot-swap drive backplane
Use this information to remove the 3.5-inch/2.5-inch hot-swap drive backplane.
“Read the
installation
Guidelines” on
page 53
“Power off
the server for
this task” on
page 14
“ATTENTION:
Static Sensitive Device
Ground package before opening”
on page 55
Before removing the hot-swap drive backplane:
1. Watch the procedure
A video of this procedure is available at YouTube: https://www.youtube.com/playlist?list=
PLYV5R7hVcs-Dy5N2dPXFx5Pht-FljAi6S.
2. If the server is in a rack, remove it from the rack.
3. Remove any locking device that secures the server cover, such as a Kensington lock or a pad lock.
4. Remove the server cover (see “Remove the server cover” on page 136).
To remove the hot-swap drive backplane, complete the following steps:
Step 1. Remove the front door (see “Remove the front door” on page 90).
Step 2. Remove the front bezel (see “Remove the front bezel” on page 88).
Step 3. Remove all installed drives and drive bay fillers (if any) from the drive cage. See “Remove a hot-
swap drive” on page 76 or “Removing a 2.5-inch SSD from a 3.5-inch drive bay” on page 64.
Step 4. Remove the system fan. (see “Remove the front system fan” on page 80).
Step 5. Disconnect all the cables from the backplane.
Step 6. Lift the release latch and slide the drive cage out of the chassis.
58 ThinkSystem ST250 Maintenance Manual
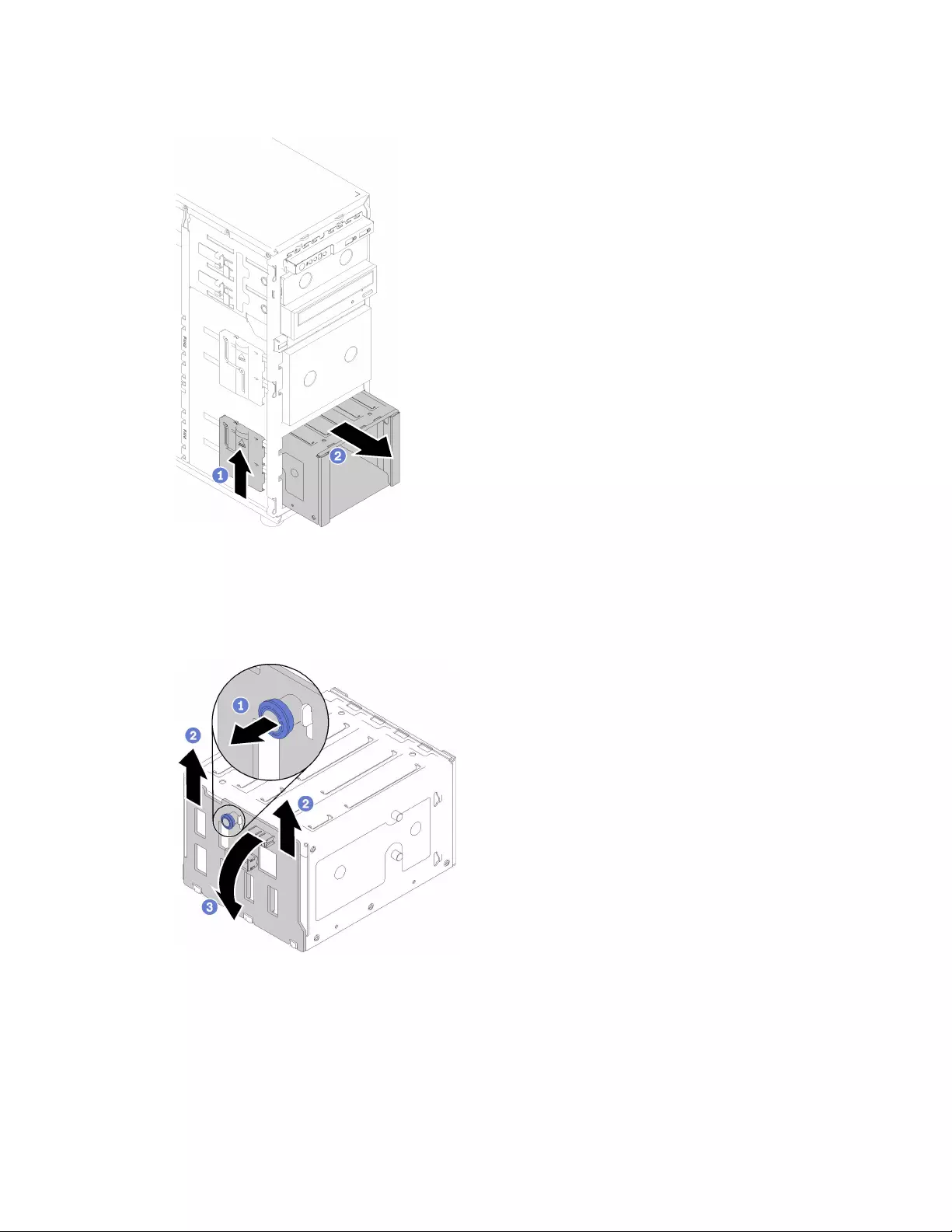
Figure 37. Drive cage removal
Step 7. Open the plunger that secures the backplane
Step 8. Slightly lift the backplane to disengage it from the drive cage; then, remove the backplane from the
drive cage.
Figure 38. Hot-swap drive backplane removal
After removing the hot-swap drive backplane:
If you are instructed to return the defective component, please package the part to prevent any shipping
damage. Reuse the packaging the new part arrived in and follow all packaging instructions.
Install the 3.5-inch/2.5-inch hot-swap drive backplane
Use this information to install the 3.5-inch/2.5-inch hot-swap drive backplane.
Chapter 3.Hardware replacement procedures 59
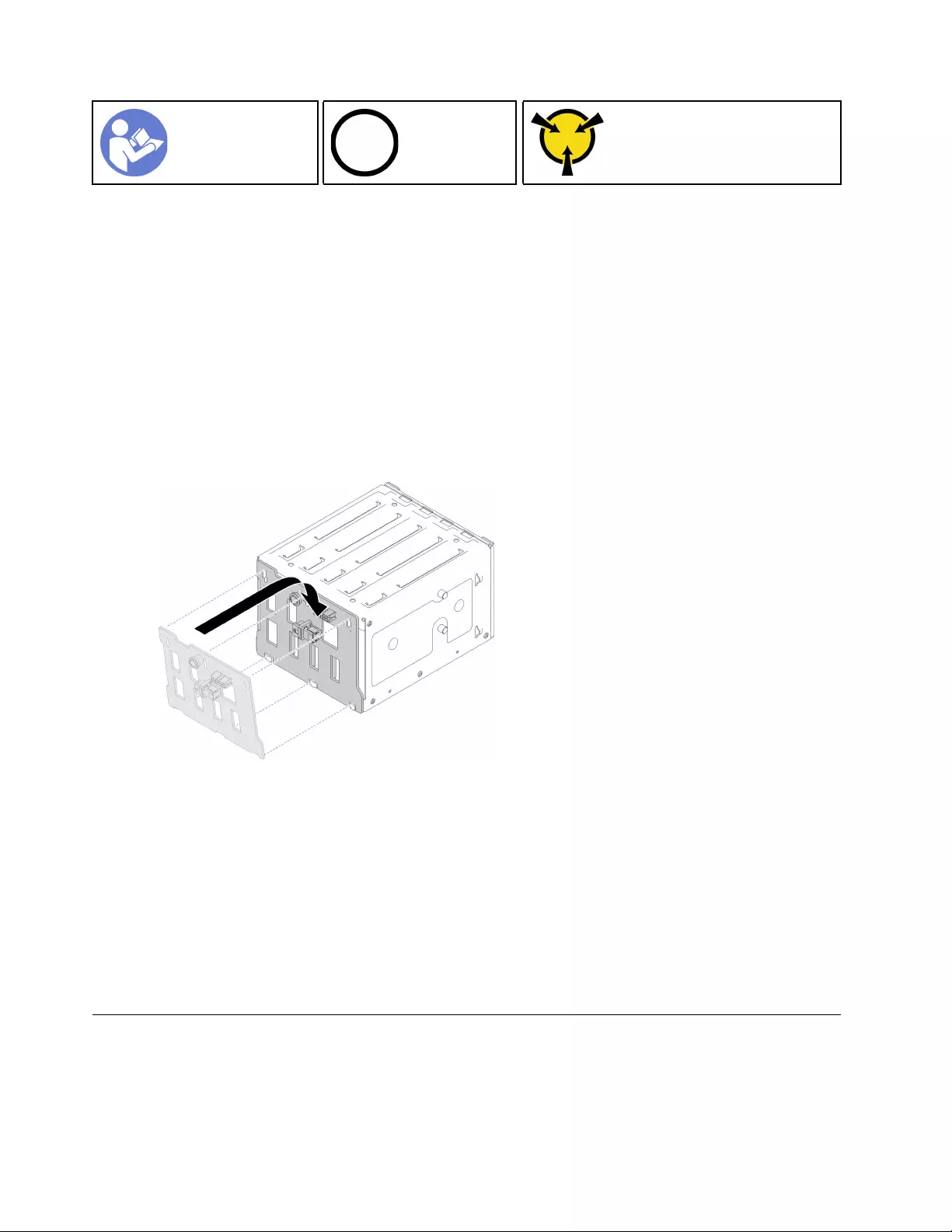
“Read the
installation
Guidelines” on
page 53
“Power off
the server for
this task” on
page 14
“ATTENTION:
Static Sensitive Device
Ground package before opening”
on page 55
Before installing a hot-swap drive backplane:
1. Watch the procedure
A video of this procedure is available at YouTube: https://www.youtube.com/playlist?list=
PLYV5R7hVcs-Dy5N2dPXFx5Pht-FljAi6S.
To install a hot-swap drive backplane, complete the following steps:
Step 1. Position the backplane on the drive cage so that the tabs on the drive cage are inserted into the
corresponding holes in the backplane; then, align bottom of backplane inside the bottom tabs of
the drive cage.
Step 2. While pulling the plunger, slide down the backplane until it is seated at the bottom of the drive
cage; then, close the plunger to secure the backplane into position.
Figure 39. Hot-swap drive backplane installation
Step 3. Install the drive cage into the chassis (see “Install the 3.5-inch/2.5-inch drive cage” on page 57 ).
After installing the backplane:
1. Reinstall all the hot-swap drives and drive bay fillers (if any) into the drive cage (see “Install a hot-swap
drive” on page 78 or “Installing a 2.5-inch SSD into a 3.5-inch drive bay” on page 65).
2. Reconnect the cables to the backplane.
3. Reinstall the system fan (see “Install the front system fan” on page 81).
4. Complete the parts replacement. See “Complete the parts replacement” on page 155
3.5-inch simple-swap drive backplate replacement
Use this information to remove and install a 3.5-inch simple-swap drive backplate.
Note: This section applies only to server models that have 3.5-inch simple-swap drive backplates installed.
60 ThinkSystem ST250 Maintenance Manual

Remove the 3.5-inch simple-swap drive backplate
Use this information to remove the 3.5-inch simple-swap drive backplate.
“Read the
installation
Guidelines” on
page 53
“Power off
the server for
this task” on
page 14
“ATTENTION:
Static Sensitive Device
Ground package before opening”
on page 55
Before removing the simple-swap drive backplate:
1. Watch the procedure
A video of this procedure is available at YouTube: https://www.youtube.com/playlist?list=
PLYV5R7hVcs-Dy5N2dPXFx5Pht-FljAi6S.
2. If the server is in a rack, remove it from the rack.
3. Remove any locking device that secures the server cover, such as a Kensington lock or a pad lock.
4. Remove the server cover (see “Remove the server cover” on page 136).
To remove the simple-swap drive backplate, complete the following steps:
Step 1. Remove the front door (see “Remove the front door” on page 90).
Step 2. Remove the front bezel. (see “Remove the front bezel” on page 88).
Step 3. Remove the front system fan. (see “Remove the front system fan” on page 80).
Step 4. Remove all the installed simple-swap drives and drive bay fillers (if any) from the drive cage, then
disconnect all the cables from the backplate. See “Remove a simple-swap drive” on page 74 or
“Removing a 2.5-inch SSD from a 3.5-inch drive bay” on page 64.
Step 5. Lift the release latch and slide the drive cage out of the chassis.
Note: Depending on the model, your drive cage might look slightly different from the illustration.
Chapter 3.Hardware replacement procedures 61
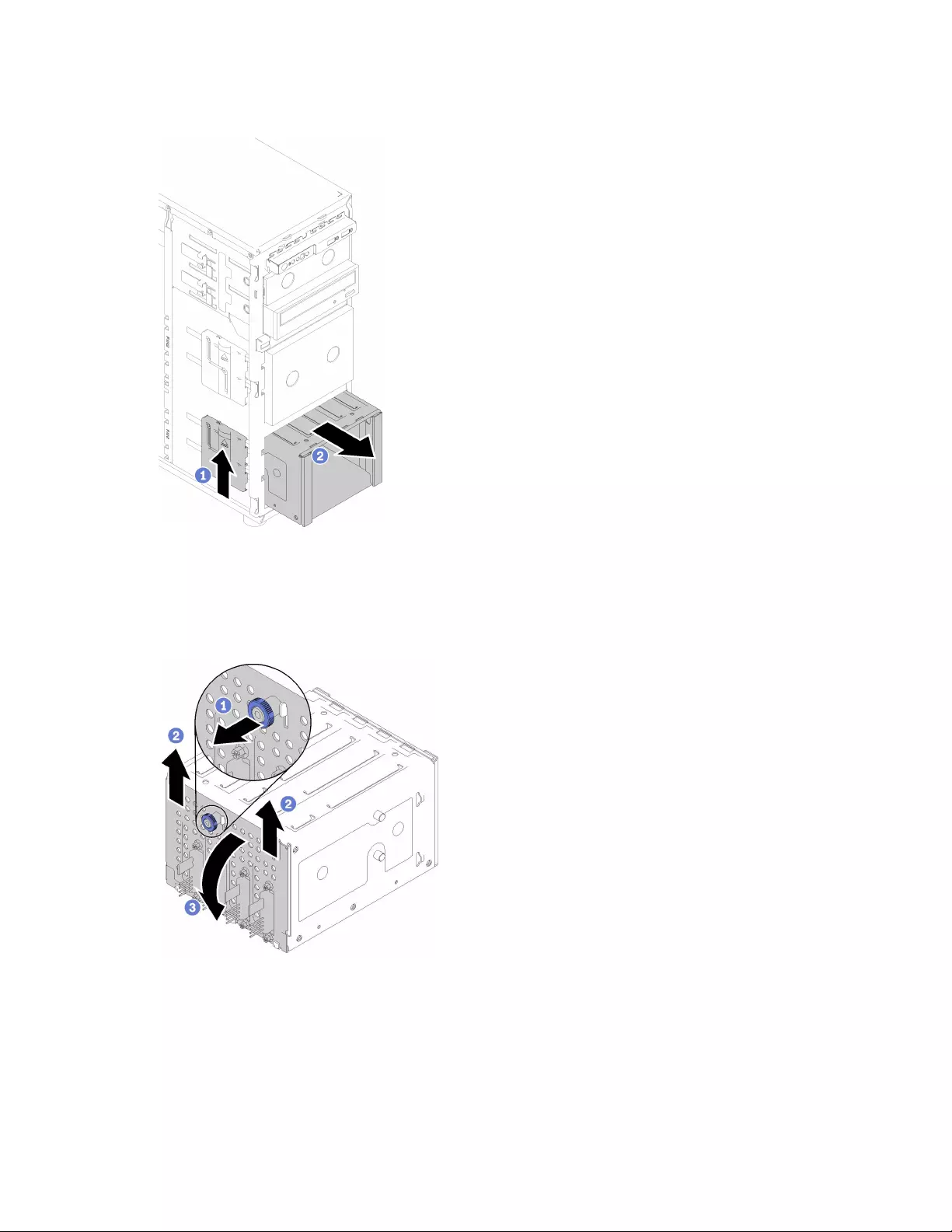
Figure 40. Drive cage removal
Step 6. Open the plunger that secures the backplate
Step 7. Slightly lift the backplate to disengage it from the drive cage; then, remove the backplate from the
drive cage.
Figure 41. Simple-swap drive backplate removal
After removing the simple-swap drive backplate:
If you are instructed to return the defective component, please package the part to prevent any shipping
damage. Reuse the packaging the new part arrived in and follow all packaging instructions.
Install the 3.5-inch simple-swap drive backplate
Use this information to install the 3.5-inch simple-swap drive backplate.
62 ThinkSystem ST250 Maintenance Manual

“Read the
installation
Guidelines” on
page 53
“Power off
the server for
this task” on
page 14
“ATTENTION:
Static Sensitive Device
Ground package before opening”
on page 55
Before installing a simple-swap drive backplate:
1. Watch the procedure
A video of this procedure is available at YouTube: https://www.youtube.com/playlist?list=
PLYV5R7hVcs-Dy5N2dPXFx5Pht-FljAi6S.
To install a simple-swap drive backplate, complete the following steps:
Step 1. Position the backplate on the drive cage so that the tabs on the drive cage are inserted into the
corresponding holes in the backplate.
Step 2. Close the plunger to secure the backplate into position.
Figure 42. Simple-swap drive backplate installation
Step 3. Press the drive cage in until the release latch clicks into place (see “Install the 3.5-inch/2.5-inch
drive cage” on page 57 ).
After installing the backplate:
1. Reinstall all the simple-swap drives and drive bay fillers (if any) into the drive cage (see “Install a simple-
swap drive” on page 75 or “Installing a 2.5-inch SSD into a 3.5-inch drive bay” on page 65).
2. Reconnect the cables to the backplate.
3. Reinstall the system fan (see “Install the front system fan” on page 81).
4. Complete the parts replacement. See “Complete the parts replacement” on page 155
2.5-inch SSD replacement from 3.5-inch drive bay
Use this information to remove and install a 2.5-inch SSD from a 3.5-inch drive bay.
The EMI integrity and cooling of the server are protected by having all drive bays covered or occupied. The
number of the installed simple-swap disk drives in your server varies depending on the server model. The
Chapter 3.Hardware replacement procedures 63

vacant bays are occupied by dummy trays. When you install a drive, save the removed dummy tray from the
drive bay in case you later remove the drive and need the dummy tray to cover the place.
Attention: An unoccupied drive bay without any other protection might impact the EMI integrity and cooling
of the server, which might result in overheating or component damage. To maintain the EMI integrity and
cooling of the server, install a new SSD as soon as you remove the failing one or the dummy tray.
Before you begin, review the following drive installation rules:
• Follow the order of the disk drive bays when installing a SSD. See Chapter 2 “Server components” on
page 15 to locate the disk drive bays in your server.
• For SSDs with different capacities, install the drive by following the order of the disk drive bays as well as
the order from the lowest capacity to the highest capacity.
Removing a 2.5-inch SSD from a 3.5-inch drive bay
Use this information to remove 2.5-inch SSD from a 3.5-inch drive bay.
“Read the
installation
Guidelines” on
page 53
“ATTENTION:
Static Sensitive Device
Ground package before opening”
on page 55
Before removing a 2.5-inch SSD from a 3.5-inch drive bay:
1. Watch the procedure
A video of this procedure is available at YouTube: https://www.youtube.com/playlist?list=
PLYV5R7hVcs-Dy5N2dPXFx5Pht-FljAi6S.
2. Use the front door key to unlock the front door (available on some models), and then open the front
door.
To remove a 2.5-inch SSD from a 3.5-inch drive bay, complete the following steps:
Step 1. Locate the drive you want to remove.
Step 2. Remove the 3.5-inch drive tray with the 2.5-inch SSD (see “Remove a simple-swap drive” on page
74).
Step 3. Remove the five screws that secure the 2.5-inch SSD and the drive adapter; then, remove the 2.5-
inch SSD and the drive adapter from the tray.
Figure 43. Removing the screws that secure the 2.5-inch SSD and the drive adapter
64 ThinkSystem ST250 Maintenance Manual

Step 4. Remove the two screws that secure the 2.5-inch SSD; then, lift the drive up to remove it from the
drive adapter.
Figure 44. 2.5-inch SSD removal from the drive adapter
After removing the 2.5-inch SSD from a 3.5-inch drive bay:
If you are instructed to return the defective component, please package the part to prevent any shipping
damage. Reuse the packaging the new part arrived in and follow all packaging instructions.
Installing a 2.5-inch SSD into a 3.5-inch drive bay
Use this information to install a 2.5-inch SSD into a 3.5-inch drive bay.
“Read the
installation
Guidelines” on
page 53
“ATTENTION:
Static Sensitive Device
Ground package before opening”
on page 55
Before installing a 2.5-inch SSD into a 3.5-inch drive bay:
1. Watch the procedure
A video of this procedure is available at YouTube: https://www.youtube.com/playlist?list=
PLYV5R7hVcs-Dy5N2dPXFx5Pht-FljAi6S.
To install a 2.5-inch SSD into a 3.5-inch drive bay, complete the following steps:
Step 1. Locate the appropriate drive bay.
Step 2. If necessary, remove the 3.5-inch drive tray.
Step 3. Position the 2.5-inch SSD into the 2.5-inch to 3.5-inch drive adapter.
Chapter 3.Hardware replacement procedures 65

Figure 45. Positioning the 2.5-inch SSD into the drive adapter
Step 4. Align the two screw holes in the SSD with the corresponding holes in the drive adapter; then, install
the two screws to secure the drive to the drive adapter.
Figure 46. Screw installation to secure the SSD to the drive adapter
Step 5. Position the drive adapter with the SSD into the 3.5-inch drive tray. Align the screw holes in the
drive adapter and the SSD with the corresponding holes in the tray; then, install the five screws to
secure the drive adapter and the SSD into the tray.
Figure 47. Screw installation to secure the drive adapter and the SSD to the drive tray
66 ThinkSystem ST250 Maintenance Manual

Step 6. Slide the tray with the SSD into the drive bay from the front until it snaps into position and then
completely close the handle. See “Install a hot-swap drive” on page 78 .
After installing the SSD:
1. Install other drives if necessary.
2. Complete the parts replacement. See “Complete the parts replacement” on page 155
CMOS battery (CR2032) replacement
Use this information to remove and install the CMOS battery (CR2032).
Remove the CMOS battery (CR2032)
Use this information to remove the CMOS battery (CR2032).
“Read the
installation
Guidelines” on
page 53
“Power off
the server for
this task” on
page 14
“ATTENTION:
Static Sensitive Device
Ground package before opening”
on page 55
S004
CAUTION:
When replacing the lithium battery, use only Lenovo specified part number or an equivalent type
battery recommended by the manufacturer. If your system has a module containing a lithium battery,
replace it only with the same module type made by the same manufacturer. The battery contains
lithium and can explode if not properly used, handled, or disposed of.
Do not:
• Throw or immerse into water
• Heat to more than 100°C (212°F)
• Repair or disassemble
Dispose of the battery as required by local ordinances or regulations.
S002
CAUTION:
The power-control button on the device and the power switch on the power supply do not turn off the
electrical current supplied to the device. The device also might have more than one power cord. To
remove all electrical current from the device, ensure that all power cords are disconnected from the
power source.
Chapter 3.Hardware replacement procedures 67

Before removing the CMOS battery:
1. Watch the procedure
A video of this procedure is available at YouTube: https://www.youtube.com/playlist?list=
PLYV5R7hVcs-Dy5N2dPXFx5Pht-FljAi6S.
2. If the server is in a rack, remove it from the rack.
3. Remove any locking device that secures the server cover, such as a Kensington lock or a pad lock.
4. Remove the server cover (see “Remove the server cover” on page 136).
Step 1. Locate the CMOS battery on the system board (see “System board components” on page 29).
Step 2. Press on the nub on the side of the CMOS battery; then, pivot the battery away from the socket to
remove it.
Attention: Do not apply excessive force on the CMOS battery. Failing to remove the CMOS
battery properly might damage the socket on the system board. Any damage to the socket might
require replacing the system board.
Figure 48. Removing the CMOS battery
After removing the CMOS battery:
1. Install a new CMOS battery. See “Install the CMOS battery (CR2032)” on page 68.
2. If you are instructed to return the defective component, please package the part to prevent any shipping
damage. Reuse the packaging the new part arrived in and follow all packaging instructions.
Install the CMOS battery (CR2032)
Use this information to install the CMOS battery (CR2032).
“Read the
installation
Guidelines” on
page 53
“Power off
the server for
this task” on
page 14
“ATTENTION:
Static Sensitive Device
Ground package before opening”
on page 55
Consider the following when replacing the CMOS battery in the server:
• When replacing the CMOS battery, you must replace it with another CMOS battery of the same type from
the same manufacturer.
• After replacing the CMOS battery, make sure to reconfigure the server and reset system date and time.
• To avoid possible danger, read and follow the following safety statement carefully.
• Lenovo has designed this product with your safety in mind. The lithium battery must be handled correctly
to avoid possible danger. If you install the CMOS battery, you must adhere to the following instructions.
Note: In the U. S., call 1-800-IBM-4333 for information about battery disposal.
• If you replace the original lithium battery with a heavy-metal battery or a battery with heavy-metal
components, be aware of the following environmental consideration. Batteries and accumulators that
contain heavy metals must not be disposed of with normal domestic waste. They will be taken back free
68 ThinkSystem ST250 Maintenance Manual

of charge by the manufacturer, distributor, or representative, to be recycled or disposed of in a proper
manner.
S004
CAUTION:
When replacing the lithium battery, use only Lenovo specified part number or an equivalent type
battery recommended by the manufacturer. If your system has a module containing a lithium battery,
replace it only with the same module type made by the same manufacturer. The battery contains
lithium and can explode if not properly used, handled, or disposed of.
Do not:
• Throw or immerse into water
• Heat to more than 100°C (212°F)
• Repair or disassemble
Dispose of the battery as required by local ordinances or regulations.
S002
CAUTION:
The power-control button on the device and the power switch on the power supply do not turn off the
electrical current supplied to the device. The device also might have more than one power cord. To
remove all electrical current from the device, ensure that all power cords are disconnected from the
power source.
Before install the CMOS battery:
1. Watch the procedure
A video of this procedure is available at YouTube: https://www.youtube.com/playlist?list=
PLYV5R7hVcs-Dy5N2dPXFx5Pht-FljAi6S.
2. Touch the static-protective package that contains the component to any unpainted metal surface on the
server; then, remove it from the package and place it on a static-protective surface.
To install the CMOS battery, complete the following steps:
Chapter 3.Hardware replacement procedures 69

Step 1. Place the CMOS battery on top of the socket with the positive (+) symbol facing up; then, push the
battery into the socket until it clicks in place.
Figure 49. Installing the CMOS battery
After installing the CMOS battery:
1. Complete the parts replacement. See “Complete the parts replacement” on page 155
2. Reset date, time, and all the passwords.
DIMM replacement
Use this information to remove and install a DIMM.
Remove a DIMM
Use this information to remove a DIMM.
“Read the
installation
Guidelines” on
page 53
“Power off
the server for
this task” on
page 14
“ATTENTION:
Static Sensitive Device
Ground package before opening”
on page 55
Attention: DIMMs are sensitive to static discharge and require special handling. In addition to the standard
guidelines for “Handling static-sensitive devices” on page 55:
• Always wear an electrostatic-discharge strap when removing or installing DIMMs. Electrostatic-discharge
gloves can also be used.
• Never hold two or more DIMMs together so that they touch. Do not stack DIMMs directly on top of each
other during storage.
• Never touch the gold DIMM connector contacts or allow these contacts to touch the outside of the DIMM
connector housing.
• Handle DIMMs with care: never bend, twist, or drop a DIMM.
Before removing a DIMM:
1. Watch the procedure
A video of this procedure is available at YouTube: https://www.youtube.com/playlist?list=
PLYV5R7hVcs-Dy5N2dPXFx5Pht-FljAi6S.
2. If the server is in a rack, remove it from the rack.
3. Remove any locking device that secures the server cover, such as a Kensington lock or a pad lock.
4. Remove the server cover (see “Remove the server cover” on page 136).
To remove a DIMM, complete the following steps:
Step 1. Carefully open the retaining clips on each end of the DIMM slot.
70 ThinkSystem ST250 Maintenance Manual
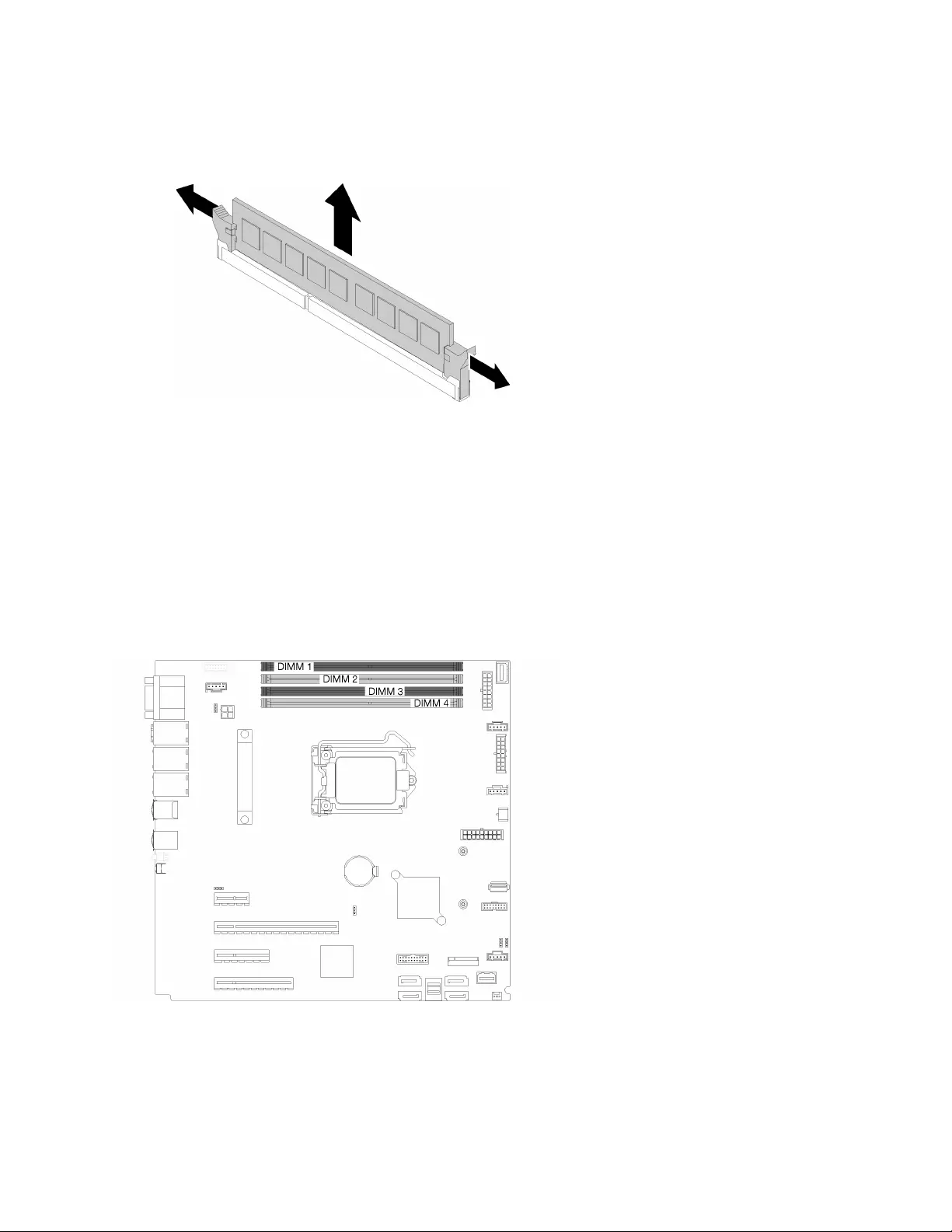
Attention: To avoid breaking the retaining clips or damaging the DIMM slots, handle the clips
gently.
Step 2. Remove the DIMM.
Figure 50. DIMM removal
After removing the DIMM:
If you are instructed to return the defective component, please package the part to prevent any shipping
damage. Reuse the packaging the new part arrived in and follow all packaging instructions.
DIMM installation rules
DIMMs must be installed in a specific order based on the memory configuration of the server.
The following illustration shows the location of the DIMM connectors on the system board.
Figure 51. DIMM slots
This server comes with four DIMM slots with the following features:
For a list of supported DIMM options, see: https://static.lenovo.com/us/en/serverproven/index.shtml
Chapter 3.Hardware replacement procedures 71

Before installing a DIMM, ensure that all DIMMs to be installed must be the same type. This server supports
the following types of DIMMs:
• DDR4 UDIMM with ECC technology
Your server supports the following memory modes:
• Independent mode
Independent mode
Independent mode provides high performance memory capability. You can populate all channels with no
matching requirements. Individual channels can run at different DIMM timings, but all channels must run at
the same interface frequency.
Notes:
• All DIMMs to be installed must be the same type.
• When you install DIMMs with same rank and different capacity, install the DIMM that has the highest
capacity first.
The following table shows the DIMM installation order.
Table 11. DIMM installation order
Number of DIMMs
DIMM Slot Number
1 2 34
One DIMM X
Two DIMMs X X
Three DIMMs X X X
Four DIMMs X X X X
Install a DIMM
Use this information to install a DIMM.
“Read the
installation
Guidelines” on
page 53
“Power off
the server for
this task” on
page 14
“ATTENTION:
Static Sensitive Device
Ground package before opening”
on page 55
See “DIMM installation rules” on page 71 for detailed information about memory configuration and setup.
Attention:
• Disconnect all power cords for this task.
• DIMMs are sensitive to static discharge and require special handling. In addition to the standard
guidelines for “Handling static-sensitive devices” on page 55:
– Always wear an electrostatic-discharge strap when removing or installing DIMMs. Electrostatic-
discharge gloves can also be used.
– Never hold two or more DIMMs together so that they touch. Do not stack DIMMs directly on top of
each other during storage.
– Never touch the gold DIMM connector contacts or allow these contacts to touch the outside of the
DIMM connector housing.
72 ThinkSystem ST250 Maintenance Manual

– Handle DIMMs with care: never bend, twist, or drop a DIMM.
Before installing a DIMM:
1. Watch the procedure
A video of this procedure is available at YouTube: https://www.youtube.com/playlist?list=
PLYV5R7hVcs-Dy5N2dPXFx5Pht-FljAi6S.
2. Touch the static-protective package that contains the component to any unpainted metal surface on the
server; then, remove it from the package and place it on a static-protective surface.
3. Ensure that you consider and follow the DIMM installation rules when performing the operation. See
“DIMM installation rules” on page 71.
To install a DIMM, complete the following steps:
Step 1. Open the retaining clips on each end of the DIMM slot; then, install the DIMM into the slot.
Attention: To avoid breaking the retaining clips or damaging the DIMM slots, open and close the
clips gently.
Step 2. Firmly press the DIMM straight down into the slot by applying pressure on both ends of the DIMM
simultaneously. The retaining clips snap into the locked position when the DIMM is firmly seated in
the slot.
Note: If there is a gap between the DIMM and the retaining clips, the DIMM has not been correctly
inserted; open the retaining clips, remove the DIMM, and then reinsert it.
Figure 52. DIMM installation
After installing a DIMM:
Complete the parts replacement. See “Complete the parts replacement” on page 155
Drive replacement
Use the following information to remove and install drives.
Chapter 3.Hardware replacement procedures 73
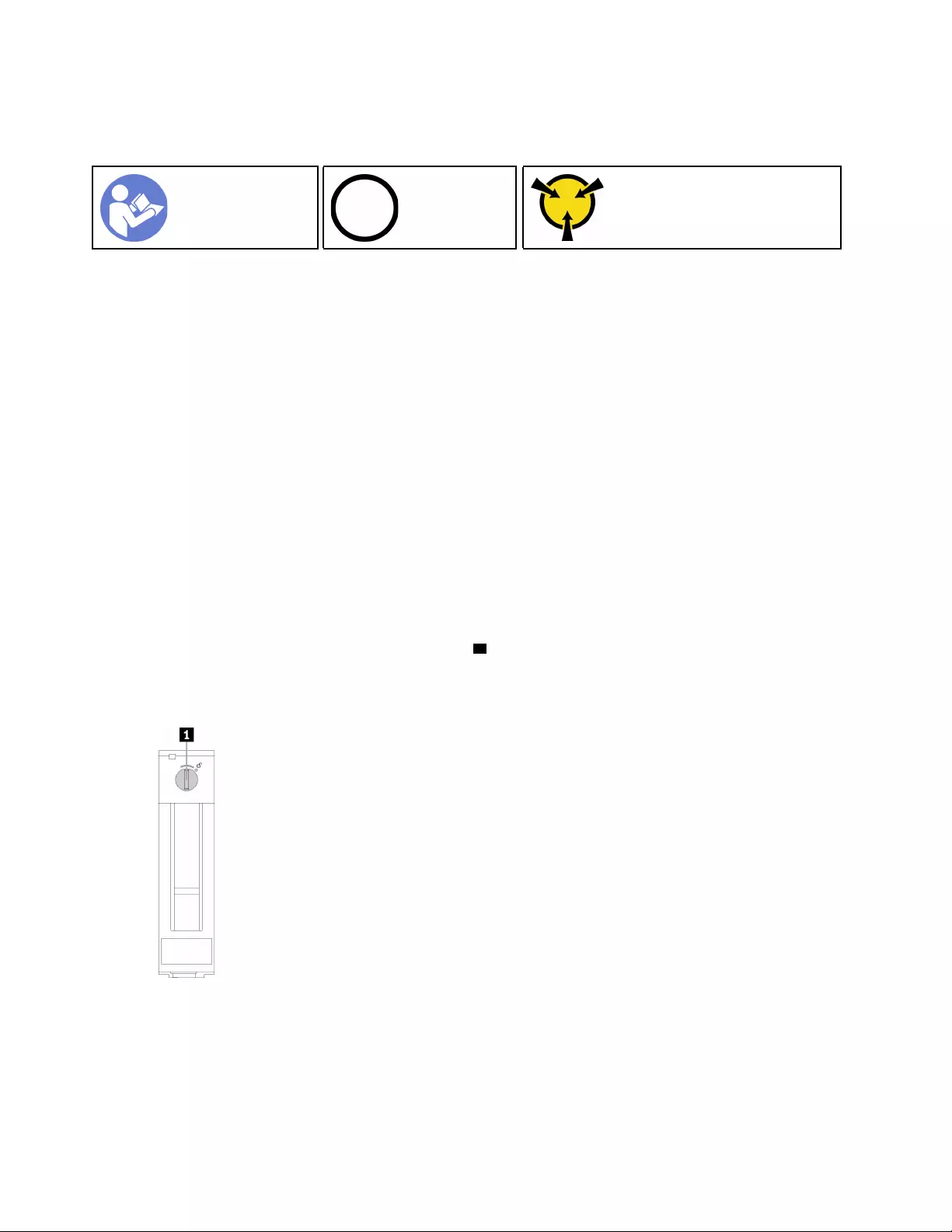
Remove a simple-swap drive
Use this information to remove a simple-swap drive.
“Read the
installation
Guidelines” on
page 53
“Power off
the server for
this task” on
page 14
“ATTENTION:
Static Sensitive Device
Ground package before opening”
on page 55
Before removing a simple-swap drive:
1. Watch the procedure
A video of this procedure is available at YouTube: https://www.youtube.com/playlist?list=
PLYV5R7hVcs-Dy5N2dPXFx5Pht-FljAi6S.
2. Ensure that you have back up data on your drive, especially if it is part of a RAID array.
• Before you make changes to drives, drive backplanes, or drive cables, back up all important data that
is stored on the drives.
• Before you remove any component of a RAID array, back up all RAID configuration information.
3. Use the front door key to unlock the front door (available on some models), and then open the front
door.
To remove a simple-swap drive, complete the following steps:
Step 1. Locate the simple-swap drive you wish to remove. lower drive bay.
Step 2. Disconnect the SATA signal cable and the power cable from the rear of the simple-swap drive. See
“Front view” on page 15.
Step 3. Use a screwdriver to turn the tray handle lock 1 to the unlocked position. The tray handle opens
automatically.
Figure 53. Opening the tray handle of the simple-swap drive
Step 4. Pull the handle and carefully slide the simple-swap drive out of the chassis.
74 ThinkSystem ST250 Maintenance Manual
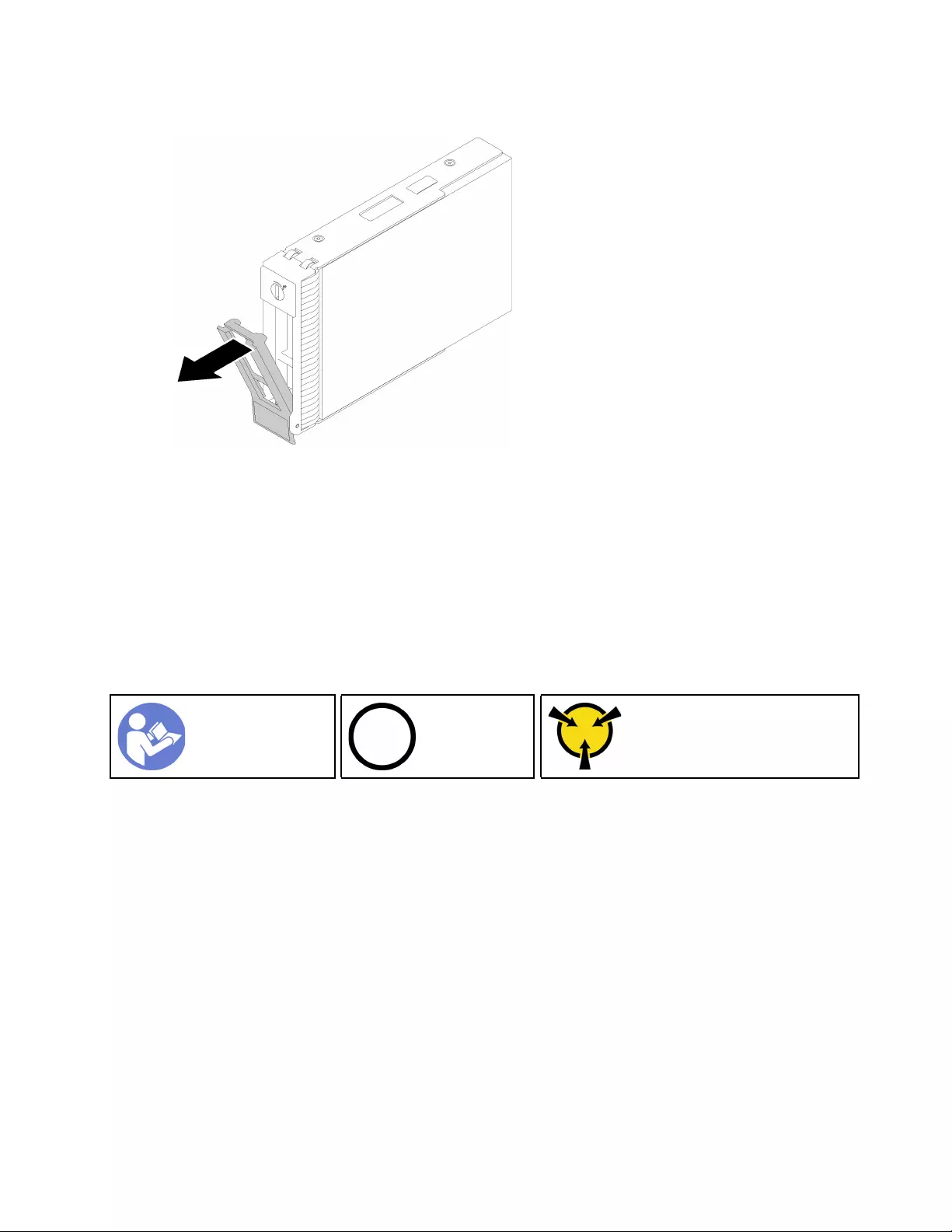
Figure 54. Simple-swap drive removal
After removing the simple-swap drive:
1. Install a new drive or drive filler into the vacant drive bay (see “Install a simple-swap drive” on page 75).
Note: To ensure that there is adequate system cooling, do not operate the server for more than two
minutes without either a drive or a drive filler installed in each bay.
2. If you are instructed to return the defective component, please package the part to prevent any shipping
damage. Reuse the packaging the new part arrived in and follow all packaging instructions.
Install a simple-swap drive
Use this information to install a simple-swap drive.
“Read the
installation
Guidelines” on
page 53
“Power off
the server for
this task” on
page 14
“ATTENTION:
Static Sensitive Device
Ground package before opening”
on page 55
The following notes describe the type of drives that your server supports and other information that you must
consider when you install a drive.
• For a complete list of supported optional devices for the server, see:https://static.lenovo.com/us/en/
serverproven/index.shtml
• The drive bays are numbered to indicate the installation order (starting from number “0”). Follow the
installation order when you install a drive. See “Front view” on page 15.
• The drives in a single RAID array must be the same type, same size, and same capacity.
Before installing a simple-swap drive:
1. Watch the procedure
A video of this procedure is available at YouTube: https://www.youtube.com/playlist?list=
PLYV5R7hVcs-Dy5N2dPXFx5Pht-FljAi6S.
2. If the drive bay has a drive filler installed, remove it. Keep the drive filler in a safe place for future use.
Chapter 3.Hardware replacement procedures 75

To install a simple-swap drive, complete the following steps:
Step 1. Ensure that the tray handle is in the open position. Align the drive with the guide rails in the bay;
then, gently push the drive into the bay until the drive stops.
Step 2. Close the tray handle to lock the drive in place.
Figure 55. Simple-swap drive installation into drive bay
Step 3. Connect signal and power cable to the system board. See “Internal cable routing” on page 31 for
details.
After installing the simple-swap drive:
1. Install other drives if necessary.
2. Complete the parts replacement. See “Complete the parts replacement” on page 155
3. Check the drive activity LED on the front panel to verify if the drives are operating correctly.
4. Use the Lenovo XClarity Provisioning Manager to configure the RAID if necessary. For more information,
see:
http://sysmgt.lenovofiles.com/help/index.jsp?topic=%2FLXPM%2FRAID_setup.html
Remove a hot-swap drive
Use this information to remove a hot-swap drive.
“Read the
installation
Guidelines” on
page 53
“ATTENTION:
Static Sensitive Device
Ground package before opening”
on page 55
Before removing a hot-swap drive:
1. Watch the procedure
76 ThinkSystem ST250 Maintenance Manual

A video of this procedure is available at YouTube: https://www.youtube.com/playlist?list=
PLYV5R7hVcs-Dy5N2dPXFx5Pht-FljAi6S.
2. Ensure that you have back up data on your drive, especially if it is part of a RAID array.
• Before you make changes to drives, RAID adapters, drive backplanes, or drive cables, back up all
important data that is stored on the drives.
• Before you remove any component of a RAID array, back up all RAID configuration information.
3. If the server is installed in a rack, extend the server from the rack.
4. Use the front door key to unlock the front door (available on some models), and then open the front
door.
To remove a hot-swap drive, complete the following steps:
Step 1. Locate the drive you want to remove and press the release button 1 to open the handle of the
drive.
Figure 56. Opening the tray handle
Step 2. Grasp the tray handle and carefully slide the drive out of the drive bay.
Step 3. Remove the four screws; then, remove the drive from the drive tray.
Chapter 3.Hardware replacement procedures 77
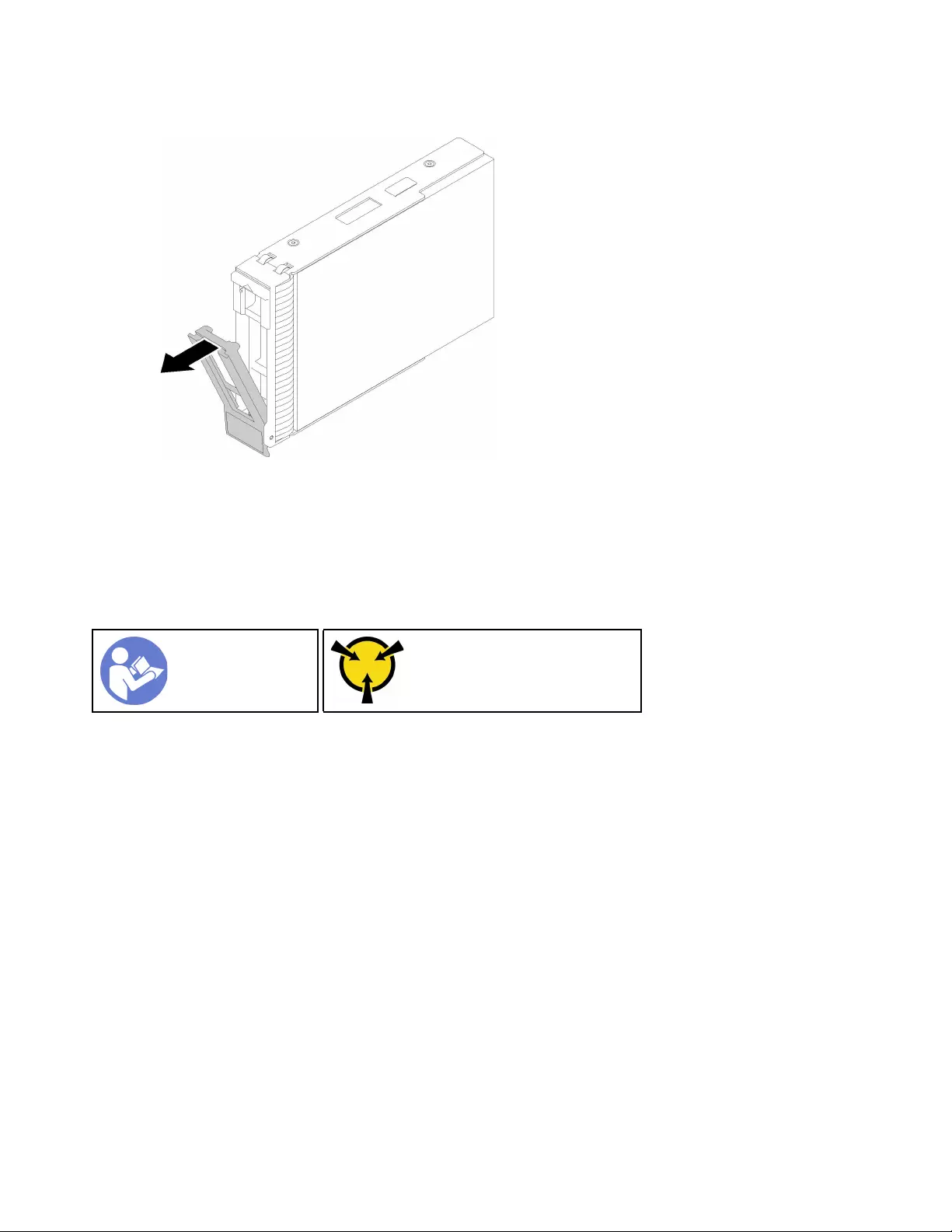
Figure 57. Hot-swap drive removal from drive tray
After removing the hot-swap drive:
1. If you are instructed to return the defective component, please package the part to prevent any shipping
damage. Reuse the packaging the new part arrived in and follow all packaging instructions.
Install a hot-swap drive
Use this information to install a hot-swap drive.
“Read the
installation
Guidelines” on
page 53
“ATTENTION:
Static Sensitive Device
Ground package before opening”
on page 55
The following notes describe the type of drives that your server supports and other information that you must
consider when you install a drive.
• Depending on your server models, your server supports the following drive types:
– Solid-state drives
– SAS/SATA drives
For a complete list of supported optional devices for the server, see:https://static.lenovo.com/us/en/
serverproven/index.shtml
• The drive bays are numbered to indicate the installation order (starting from number “0”). Follow the
installation order when you install a drive. See “Front view” on page 15.
• The drives in a single RAID array must be the same type, same size, and same capacity.
Before installing a hot-swap drive:
1. Watch the procedure
A video of this procedure is available at YouTube: https://www.youtube.com/playlist?list=
PLYV5R7hVcs-Dy5N2dPXFx5Pht-FljAi6S.
2. If the drive bay has a drive filler installed, remove it. Keep the drive filler in a safe place for future use.
78 ThinkSystem ST250 Maintenance Manual

3. Touch the static-protective package that contains the new hot-swap drive to any unpainted surface on
the outside of the server. Then, take the new hot-swap drive out of the package and place it on a static-
protective surface.
To install a hot-swap drive, complete the following steps:
Step 1. Ensure that the tray handle is in the open position. Slide the drive into the drive bay until it snaps
into position.
Step 2. Close the tray handle to lock the drive in place.
Figure 58. Hot-swap drive installation
Step 3. The hot-swap drive should be powered up and begin initialization. Check the drive LEDs to verify
that the drive is operating correctly.
After installing the hot-swap drive:
1. Continue to install additional hot-swap drives if necessary.
2. Complete the parts replacement. See “Complete the parts replacement” on page 155.
3. Use the Lenovo XClarity Provisioning Manager to configure the RAID if necessary. For more information,
see:
http://sysmgt.lenovofiles.com/help/index.jsp?topic=%2FLXPM%2FRAID_setup.html
Fan replacement
Use this information to remove and install the front or rear fan.
S033
Chapter 3.Hardware replacement procedures 79

CAUTION:
Hazardous energy present. Voltages with hazardous energy might cause heating when shorted with
metal, which might result in spattered metal, burns, or both.
S009
CAUTION:
To avoid personal injury, disconnect the fan cables before removing the fan from the device.
S002
CAUTION:
The power-control button on the device and the power switch on the power supply do not turn off the
electrical current supplied to the device. The device also might have more than one power cord. To
remove all electrical current from the device, ensure that all power cords are disconnected from the
power source.
Note: For processor fan replacement, see “Heat sink and fan module replacement” on page 94.
Remove the front system fan
Use this information to remove the front system fan.
“Read the
installation
Guidelines” on
page 53
“Power off
the server for
this task” on
page 14
“ATTENTION:
Static Sensitive Device
Ground package before opening”
on page 55
Before removing the front system fan:
1. Watch the procedure
A video of this procedure is available at YouTube: https://www.youtube.com/playlist?list=
PLYV5R7hVcs-Dy5N2dPXFx5Pht-FljAi6S.
2. If the server is in a rack, remove it from the rack.
3. Remove any locking device that secures the server cover, such as a Kensington lock or a pad lock.
4. Remove the server cover (see “Remove the server cover” on page 136).
To remove the front system fan, complete the following steps:
Step 1. Disconnect the fan cable from the system board (see “System board components” on page 29).
Step 2. Press the two tabs of the front system fan towards each other and carefully slide the fan out of the
chassis.
80 ThinkSystem ST250 Maintenance Manual

Figure 59. Front system fan removal
After removing the front system fan:
If you are instructed to return the defective component, please package the part to prevent any shipping
damage. Reuse the packaging the new part arrived in and follow all packaging instructions.
Install the front system fan
Use this information to install the front system fan.
“Read the
installation
Guidelines” on
page 53
“Power off
the server for
this task” on
page 14
“ATTENTION:
Static Sensitive Device
Ground package before opening”
on page 55
Before installing the front system fan:
1. Watch the procedure
A video of this procedure is available at YouTube: https://www.youtube.com/playlist?list=
PLYV5R7hVcs-Dy5N2dPXFx5Pht-FljAi6S.
2. Touch the static-protective package that contains the component to any unpainted metal surface on the
server; then, remove it from the package and place it on a static-protective surface.
To install the front system fan, complete the following steps:
Chapter 3.Hardware replacement procedures 81

Step 1. Position the front system fan where the four tabs are aligned with the corresponding holes in the
mounting area. In addition, ensure that the two posts of the front system fan are aligned with the
corresponding holes in the inner side of the chassis; then, carefully slide the front system fan into
the chassis until it snaps into position.
Note: When installing the front system fan into the chassis, make sure the cables do not interfere
with the two posts and the fan is firmly seated.
Figure 60. Front system fan installation
Step 2. Connect the front system fan power cable to the Fan 1 or Fan 4 connector on the system board.
See “System board components” on page 29 and “Fan power cable” on page 31.
After installing the front system fan:
Complete the parts replacement. See “Complete the parts replacement” on page 155
Remove the rear system fan
Use this information to remove the rear system fan.
“Read the
installation
Guidelines” on
page 53
“Power off
the server for
this task” on
page 14
“ATTENTION:
Static Sensitive Device
Ground package before opening”
on page 55
82 ThinkSystem ST250 Maintenance Manual

Before removing the rear system fan:
1. Watch the procedure
A video of this procedure is available at YouTube: https://www.youtube.com/playlist?list=
PLYV5R7hVcs-Dy5N2dPXFx5Pht-FljAi6S.
2. If the server is in a rack, remove it from the rack.
3. Remove any locking device that secures the server cover, such as a Kensington lock or a pad lock.
4. Remove the server cover (see “Remove the server cover” on page 136).
To remove the rear system fan, complete the following steps:
Step 1. Disconnect the fan cable from the system board. See “System board components” on page 29.
Step 2. Press the two tabs of the rear system fan towards each other and carefully slide the fan out of the
chassis.
Figure 61. Rear system fan removal
After removing the rear system fan:
If you are instructed to return the defective component, please package the part to prevent any shipping
damage. Reuse the packaging the new part arrived in and follow all packaging instructions.
Install the rear system fan
Use this information to install the rear system fan.
“Read the
installation
Guidelines” on
page 53
“Power off
the server for
this task” on
page 14
“ATTENTION:
Static Sensitive Device
Ground package before opening”
on page 55
Before installing the rear system fan
1. Watch the procedure
Chapter 3.Hardware replacement procedures 83

A video of this procedure is available at YouTube: https://www.youtube.com/playlist?list=
PLYV5R7hVcs-Dy5N2dPXFx5Pht-FljAi6S.
2. Touch the static-protective package that contains the component to any unpainted metal surface on the
server; then, remove it from the package and place it on a static-protective surface.
To install the rear system fan, complete the following steps:
Step 1. Position the new rear system fan where the four tips on the fan are closely aligned with the
corresponding holes in the mounting area.
Figure 62. Positioning the rear system fan into the chassis
Step 2. Carefully push the rear system fan until it snaps into position. Ensure that all four tips on the fan are
inserted into the corresponding holes as shown.
84 ThinkSystem ST250 Maintenance Manual

Figure 63. Rear system fan installation
Step 3. Connect the fan power cable to the Fan 3 connector on the system board. See “System board
components” on page 29 and “Fan power cable” on page 31.
After installing the rear system fan:
Complete the parts replacement. See “Complete the parts replacement” on page 155
Flash power module replacement
Use this information to remove and install the flash power module.
Note: This topic applies only to server models that have flash power modules installed.
The flash power module protects the cache memory on the installed RAID adapter. You can purchase a flash
power module from Lenovo.
For a list of supported options, see:
https://static.lenovo.com/us/en/serverproven/index.shtml
Remove a flash power module
Use this information to remove a flash power module.
“Read the
installation
Guidelines” on
page 53
“Power off
the server for
this task” on
page 14
“ATTENTION:
Static Sensitive Device
Ground package before opening”
on page 55
Before removing a flash power module:
1. Watch the procedure
A video of this procedure is available at YouTube: https://www.youtube.com/playlist?list=
PLYV5R7hVcs-Dy5N2dPXFx5Pht-FljAi6S.
2. If the server is in a rack, remove it from the rack.
Chapter 3.Hardware replacement procedures 85

3. Remove any locking device that secures the server cover, such as a Kensington lock or a pad lock.
4. Remove the server cover (see “Remove the server cover” on page 136).
To remove a flash power module, complete the following steps:
Step 1. Disconnect the cable of the flash power module from the RAID card.
Step 2. Press the tab on the flash power module bracket and remove the flash power module and bracket
assembly from the chassis.
Figure 64. Flash power module and bracket assembly removal from chassis
Step 3. If you are going to remove the flash power module from the bracket, gently pull the tab on the
bracket to remove the module from the bracket.
Figure 65. Flash power module removal from bracket
After removing the flash power module:
If you are instructed to return the defective component, please package the part to prevent any shipping
damage. Reuse the packaging the new part arrived in and follow all packaging instructions.
86 ThinkSystem ST250 Maintenance Manual
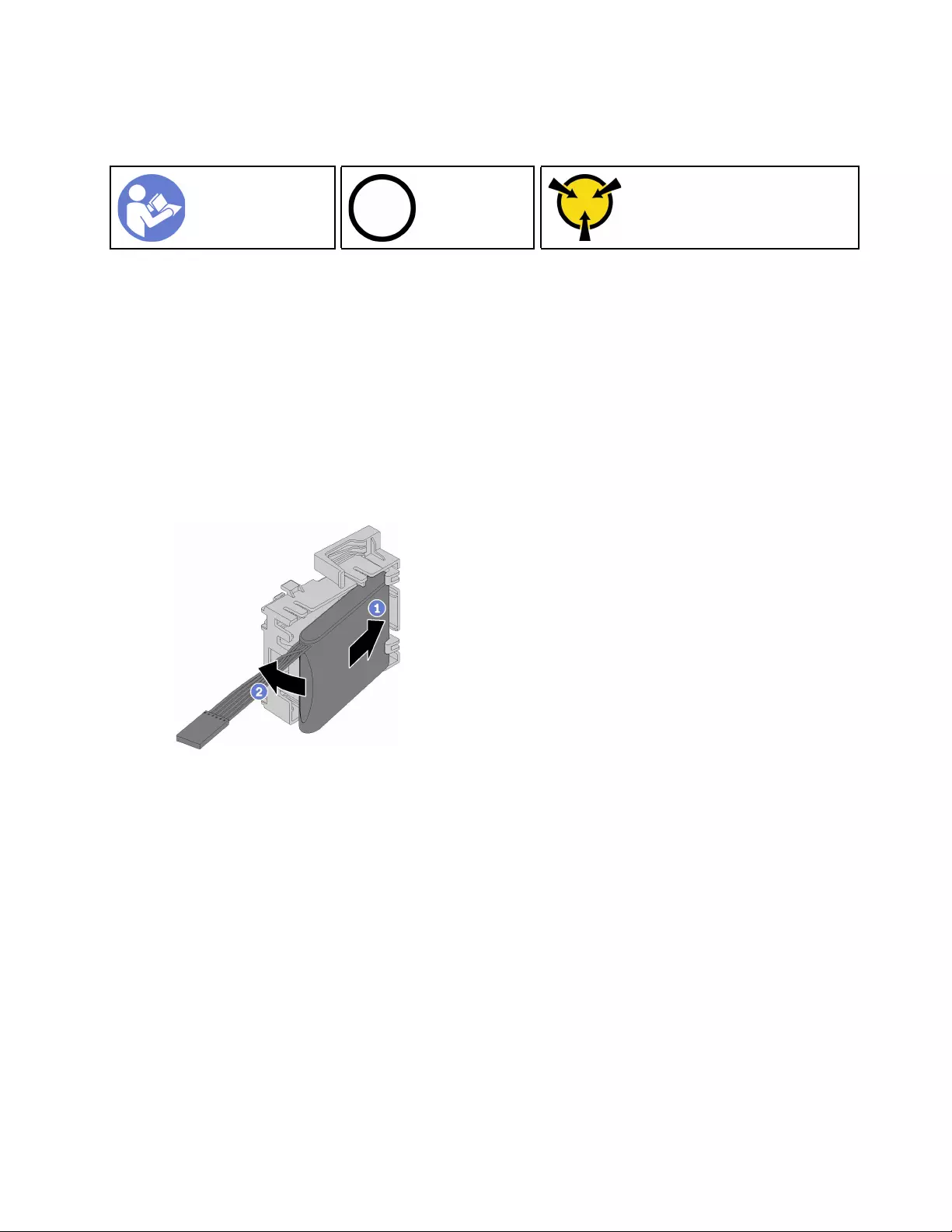
Install a flash power module
Use this information to install a flash power module.
“Read the
installation
Guidelines” on
page 53
“Power off
the server for
this task” on
page 14
“ATTENTION:
Static Sensitive Device
Ground package before opening”
on page 55
Before installing a flash power module:
1. Watch the procedure
A video of this procedure is available at YouTube: https://www.youtube.com/playlist?list=
PLYV5R7hVcs-Dy5N2dPXFx5Pht-FljAi6S.
2. Touch the static-protective package that contains the component to any unpainted metal surface on the
server; then, remove it from the package and place it on a static-protective surface.
To install a flash power module, complete the following steps:
Step 1. Note the orientation of the flash power module; then, gently insert the flash power module into the
bracket.
Figure 66. Flash power module installation into bracket
Step 2. Position the flash power module and bracket assembly onto the chassis, where the tabs on the
bracket pass through the corresponding holes in the chassis. Move the assembly as shown until it
is secured onto the chassis.
Chapter 3.Hardware replacement procedures 87

Figure 67. Flash power module and bracket assembly installation onto chassis
Step 3. Connect the flash power module cable to the RAID adapter.
After installing the flash power module:
Complete the parts replacement. See “Complete the parts replacement” on page 155
Front bezel replacement
Use this information to remove and install the front bezel.
Remove the front bezel
Use this information to remove the front bezel.
“Read the
installation
Guidelines” on
page 53
“Power off the
server for this
task” on page
14
Before removing the front bezel:
1. Watch the procedure
A video of this procedure is available at YouTube: https://www.youtube.com/playlist?list=
PLYV5R7hVcs-Dy5N2dPXFx5Pht-FljAi6S.
2. If the server is in a rack, remove it from the rack.
3. Remove any locking device that secures the server cover, such as a Kensington lock or a pad lock.
4. Remove the server cover (see “Remove the server cover” on page 136).
To remove the front bezel, complete the following step:
88 ThinkSystem ST250 Maintenance Manual

Step 1. Remove the front door (see “Remove the front door” on page 90).
Step 2. Lift the three plastic tabs to release left side of the bezel from the chassis; then, pivot the bezel as
shown to remove it from the chassis.
Figure 68. Front bezel removal
After removing the front bezel:
If you are instructed to return the defective component, please package the part to prevent any shipping
damage. Reuse the packaging the new part arrived in and follow all packaging instructions.
Install the front bezel
Use this information to install the front bezel.
“Read the
installation
Guidelines” on
page 53
“Power off the
server for this
task” on page
14
Before installing the front bezel:
1. Watch the procedure
A video of this procedure is available at YouTube: https://www.youtube.com/playlist?list=
PLYV5R7hVcs-Dy5N2dPXFx5Pht-FljAi6S.
To install the front bezel, complete the following step:
Chapter 3.Hardware replacement procedures 89

Step 1. Align the three plastic tabs on the right side of the front bezel with the corresponding holes in the
chassis; then, pivot the front bezel and front door (available on some models) inward until the front
bezel snaps into position on the left side.
Figure 69. Front bezel installation
After installing the front bezel:
Complete the parts replacement. See “Complete the parts replacement” on page 155
Front door replacement
Use this information to remove and install the front door.
Note: This section applies only to server models that have a front door installed.
Remove the front door
Use this information to remove the front door.
“Read the
installation
Guidelines” on
page 53
Before removing the front door:
1. Watch the procedure
A video of this procedure is available at YouTube: https://www.youtube.com/playlist?list=
PLYV5R7hVcs-Dy5N2dPXFx5Pht-FljAi6S.
2. If the server is in a rack, remove it from the rack.
3. Remove any locking device that secures the server cover, such as a Kensington lock or a pad lock.
To remove the front door, complete the following steps:
90 ThinkSystem ST250 Maintenance Manual
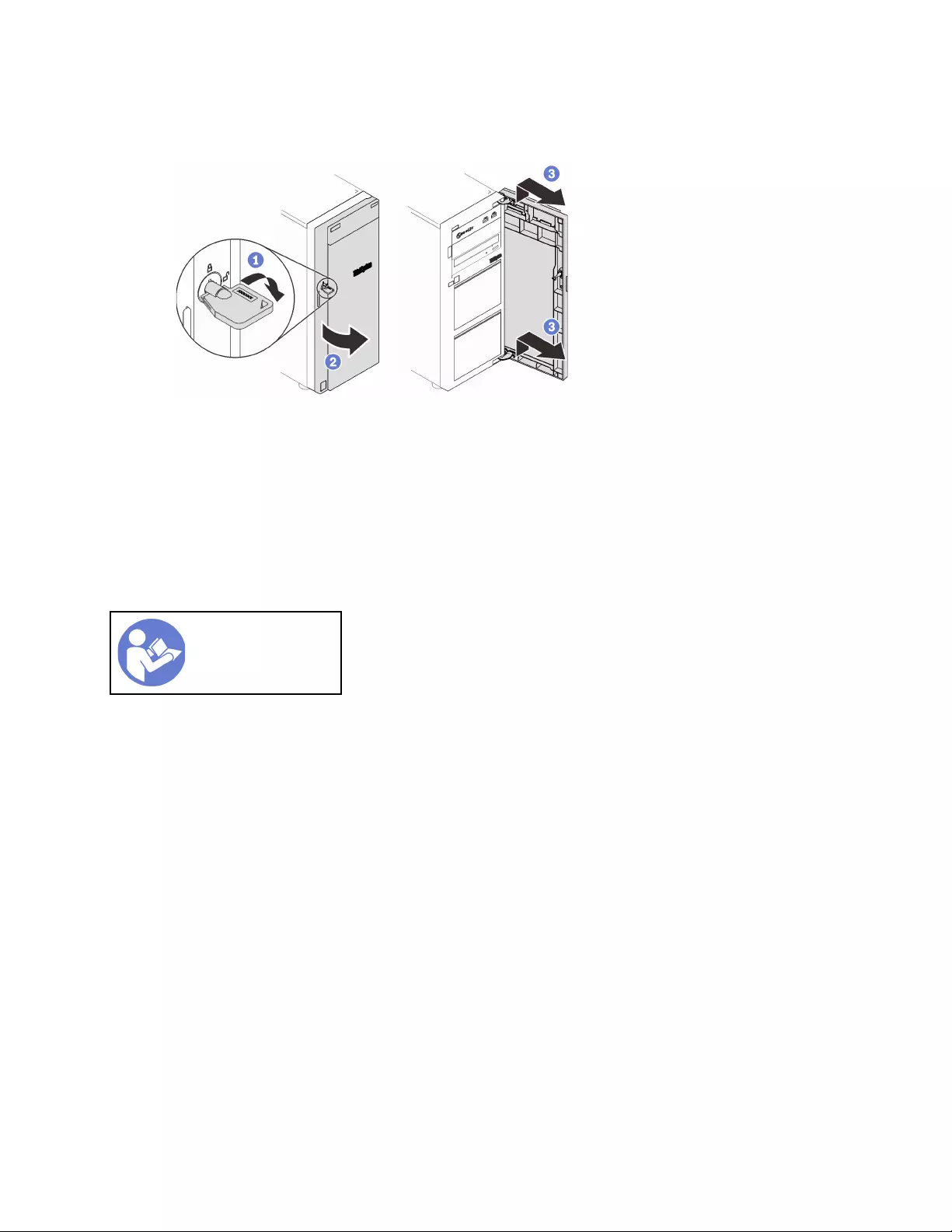
Step 1. Open the front door.
Step 2. Lift the front door slightly upward until you can completely remove it.
Figure 70. Front door removal
After removing the front door:
If you are instructed to return the defective component, please package the part to prevent any shipping
damage. Reuse the packaging the new part arrived in and follow all packaging instructions.
Install the front door
Use this information to install the front door.
“Read the
installation
Guidelines” on
page 53
Before installing the front door:
1. Watch the procedure
A video of this procedure is available at YouTube: https://www.youtube.com/playlist?list=
PLYV5R7hVcs-Dy5N2dPXFx5Pht-FljAi6S.
2. Before installing the front door, if the server comes with rubber blocks to cover the holes for installing the
front door, remove the rubber blocks first. Store the rubber blocks in case that you later remove the front
door and need the rubber blocks to cover the holes in the front bezel.
To install the front door, complete the following steps:
Step 1. Align the two hooks on the front door with the corresponding holes in the front bezel; then, move
the front door inward and then pull it slightly downward until it is secured in place by the hooks.
Chapter 3.Hardware replacement procedures 91
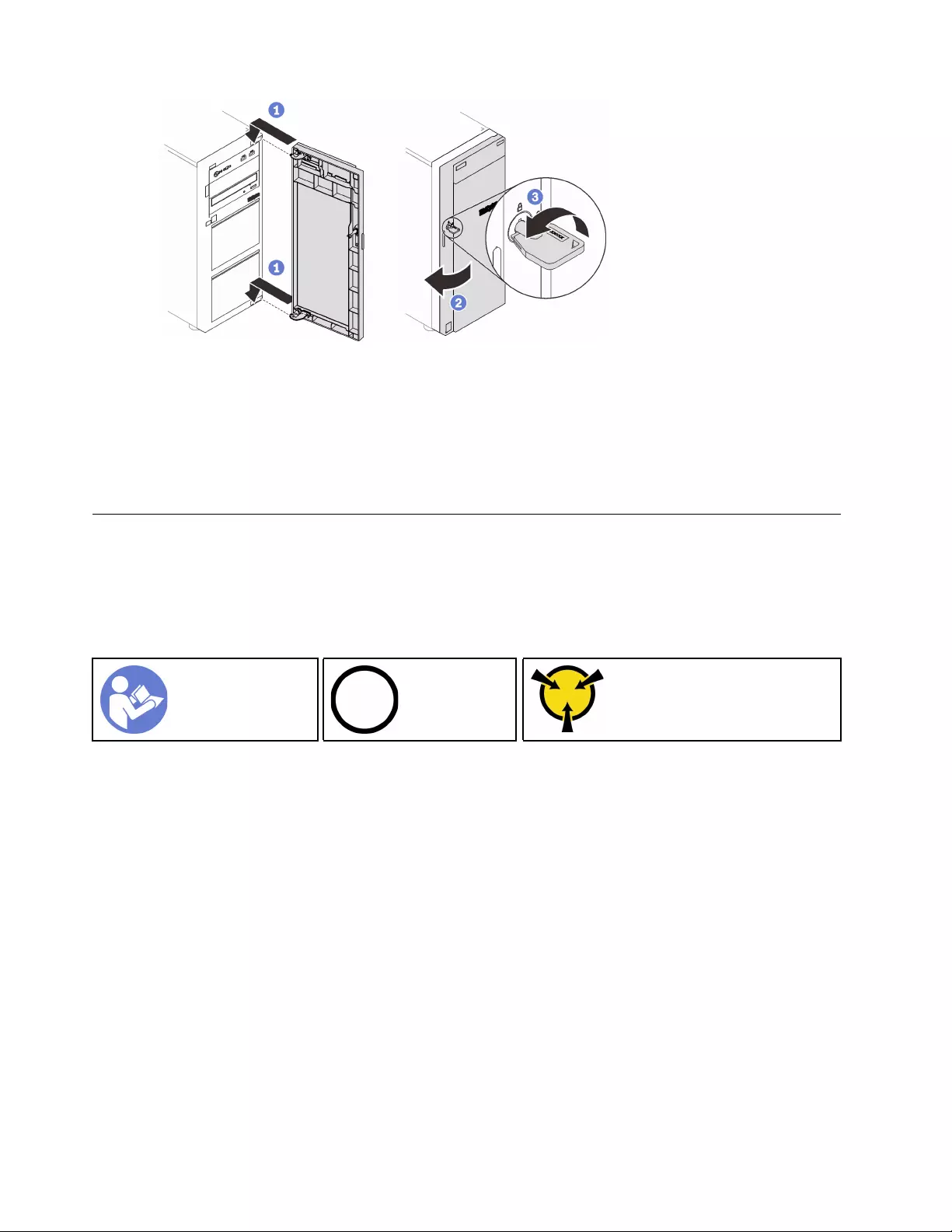
Figure 71. Front door installation
Step 2. Close the front door.
After installing the front door:
Complete the parts replacement. See “Complete the parts replacement” on page 155
Front panel board assembly replacement
Use this information to remove and install the front panel board assembly.
Remove the front panel board assembly
Use this information to remove the front panel board assembly.
“Read the
installation
Guidelines” on
page 53
“Power off
the server for
this task” on
page 14
“ATTENTION:
Static Sensitive Device
Ground package before opening”
on page 55
Before removing the front bezel:
1. Watch the procedure
A video of this procedure is available at YouTube: https://www.youtube.com/playlist?list=
PLYV5R7hVcs-Dy5N2dPXFx5Pht-FljAi6S.
2. If the server is in a rack, remove it from the rack.
3. Remove any locking device that secures the server cover, such as a Kensington lock or a pad lock.
4. Remove the server cover (see “Remove the server cover” on page 136).
To remove the front panel board assembly, complete the following steps:
Step 1. Remove the front door (see “Remove the front door” on page 90).
Step 2. Remove the front bezel (see “Remove the front bezel” on page 88).
Step 3. Locate the front panel board assembly and disconnect the cables from the system board. See
“System board components” on page 29
92 ThinkSystem ST250 Maintenance Manual

Step 4. Press the release tab in the direction as shown in the illustration and pivot the front panel board
assembly outward. Pull the cables out to completely remove the front panel board assembly from
the chassis.
Figure 72. Front panel board assembly removal
Step 5. Disconnect cables from the front panel board assembly.
After removing the front panel board assembly:
If you are instructed to return the defective component, please package the part to prevent any shipping
damage. Reuse the packaging the new part arrived in and follow all packaging instructions.
Install the front panel board assembly
Use this information to install the front panel board assembly.
“Read the
installation
Guidelines” on
page 53
“Power off
the server for
this task” on
page 14
“ATTENTION:
Static Sensitive Device
Ground package before opening”
on page 55
Before installing the front panel:
1. Watch the procedure
A video of this procedure is available at YouTube: https://www.youtube.com/playlist?list=
PLYV5R7hVcs-Dy5N2dPXFx5Pht-FljAi6S.
2. Touch the static-protective package that contains the component to any unpainted metal surface on the
server; then, remove it from the package and place it on a static-protective surface.
Chapter 3.Hardware replacement procedures 93
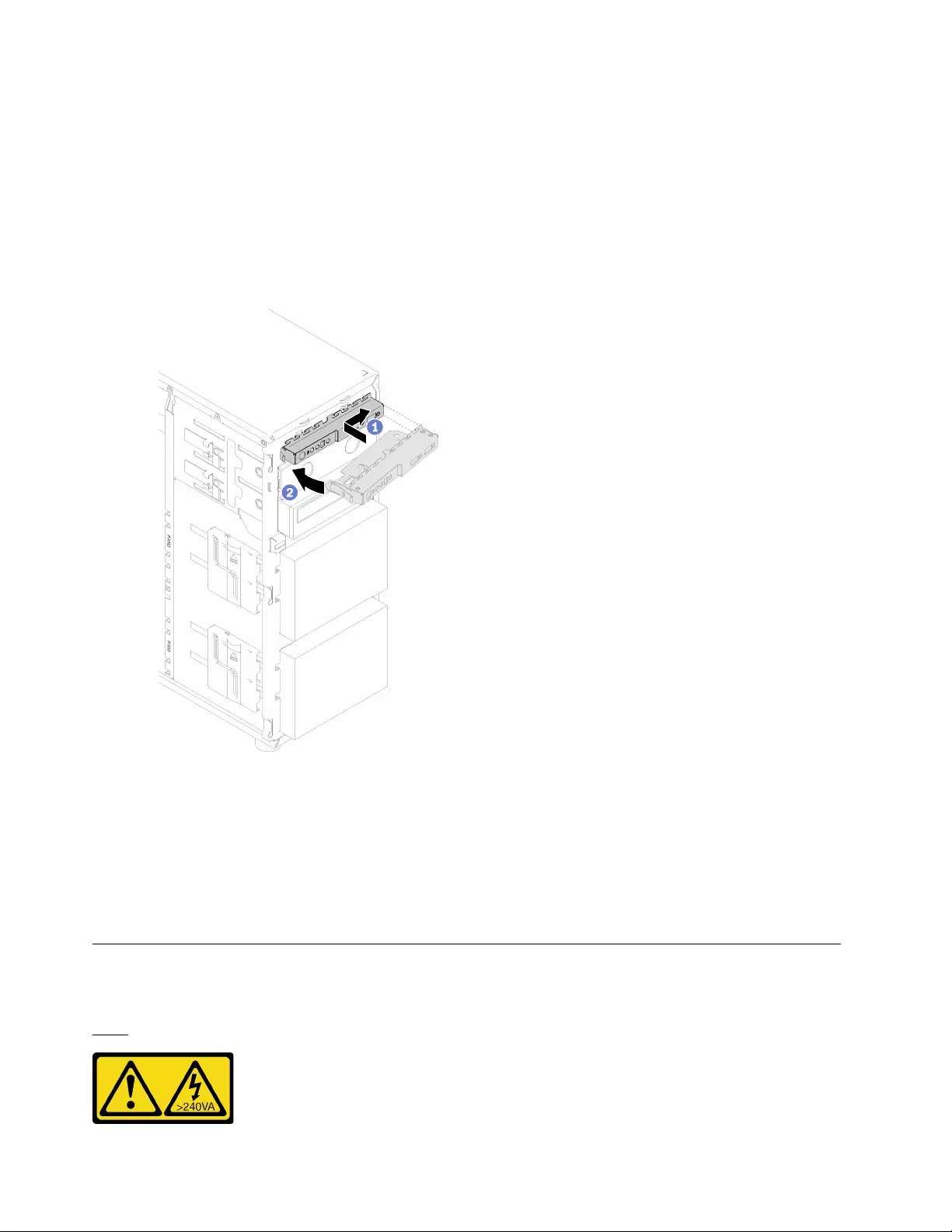
To install the front panel, complete the following steps:
Step 1. Connect cables to the new front panel board assembly and route the cables through the
corresponding hole in the chassis.
Step 2. Align the tab on the right side of the front panel board assembly with the side of the corresponding
hole in the chassis.
Step 3. Align the tab on the top of the front panel board assembly with the side of the corresponding hole in
the chassis.
Step 4. Pivot the front panel board assembly in until it snaps into position.
Figure 73. Front panel board assembly installation
Step 5. Connect the respective cables to the front panel connectors 1 and 2 and the front USB 3.0
connector on the system board. See “System board components” on page 29.
After installing the front panel board assembly:
Complete the parts replacement. See “Complete the parts replacement” on page 155
Heat sink and fan module replacement
Use this information to remove and install the heat sink and fan module.
S033
94 ThinkSystem ST250 Maintenance Manual

CAUTION:
Hazardous energy present. Voltages with hazardous energy might cause heating when shorted with
metal, which might result in spattered metal, burns, or both.
S014
CAUTION:
Hazardous voltage, current, and energy levels might be present. Only a qualified service technician is
authorized to remove the covers where the label is attached.
Remove the heat sink and fan module
Use this information to remove the heat sink and fan module. This procedure must be executed by a trained
technician
“Read the
installation
Guidelines” on
page 53
“Power off
the server for
this task” on
page 14
“ATTENTION:
Static Sensitive Device
Ground package before opening”
on page 55
Before removing the heat sink and fan module:
1. Watch the procedure
A video of this procedure is available at YouTube: https://www.youtube.com/playlist?list=
PLYV5R7hVcs-Dy5N2dPXFx5Pht-FljAi6S.
2. If the server is in a rack, remove it from the rack.
3. Remove any locking device that secures the server cover, such as a Kensington lock or a pad lock.
4. Remove the server cover (see “Remove the server cover” on page 136).
CAUTION:
The heat sinks and processor could be very hot. To avoid from burning yourself, wait for a few
minutes before removing the server cover after turning off the server.
5. Disconnect the heat sink and fan module cable from the system board.
To remove the heat sink and fan module, complete the following steps:
Step 1. Disconnect the fan cable from the system board.
Step 2. Loosen screw 1 and 2:
Notes:
1. Gently remove the four screws to avoid any possible damage to the system board.
2. Always keep the four screws attached to the heat sink and fan module.
3. Do not touch the thermal grease while handling the heat sink and fan module.
a. Partially loosen screw 1.
b. Fully loosen screw 2.
c. Fully loosen screw 1.
Chapter 3.Hardware replacement procedures 95

Step 3. Loosen screw 3 and 4:
a. Partially loosen screw 3.
b. Fully loosen screw 4.
c. Fully loosen screw 3.
Figure 74. Removing the heat sink and fan module
Step 4. Lift evenly and remove the heat sink and fan module from the server.
After removing the heat sink and fan module:
If you are instructed to return the defective component, please package the part to prevent any shipping
damage. Reuse the packaging the new part arrived in and follow all packaging instructions.
Install the heat sink and the fan module
Use this information to install the heat sink and the fan module. This procedure must be executed by a
trained technician.
“Read the
installation
Guidelines” on
page 53
“Power off
the server for
this task” on
page 14
“ATTENTION:
Static Sensitive Device
Ground package before opening”
on page 55
Before installing the heat sink and the fan module:
1. Watch the procedure
96 ThinkSystem ST250 Maintenance Manual

A video of this procedure is available at YouTube: https://www.youtube.com/playlist?list=
PLYV5R7hVcs-Dy5N2dPXFx5Pht-FljAi6S.
2. Install the processor if one is not yet installed (see “Install the processor ” on page 134).
To install the heat sink and the fan module, complete the following steps:
Step 1. Align the four screws on the heat sink and fan assembly with the corresponding screw holes on the
system board. Make sure that the “Front” label is facing the front of the server.
Step 2. Tighten screw 1 and 2:
a. Partially tighten screw 1.
b. Fully tighten screw 2.
c. Fully tighten screw 1.
Figure 75. Installing the heat sink and the fan module
Step 3. Tighten screw 3 and 4:
a. Partially tighten screw 3.
b. Fully tighten screw 4.
c. Fully tighten screw 3.
Chapter 3.Hardware replacement procedures 97
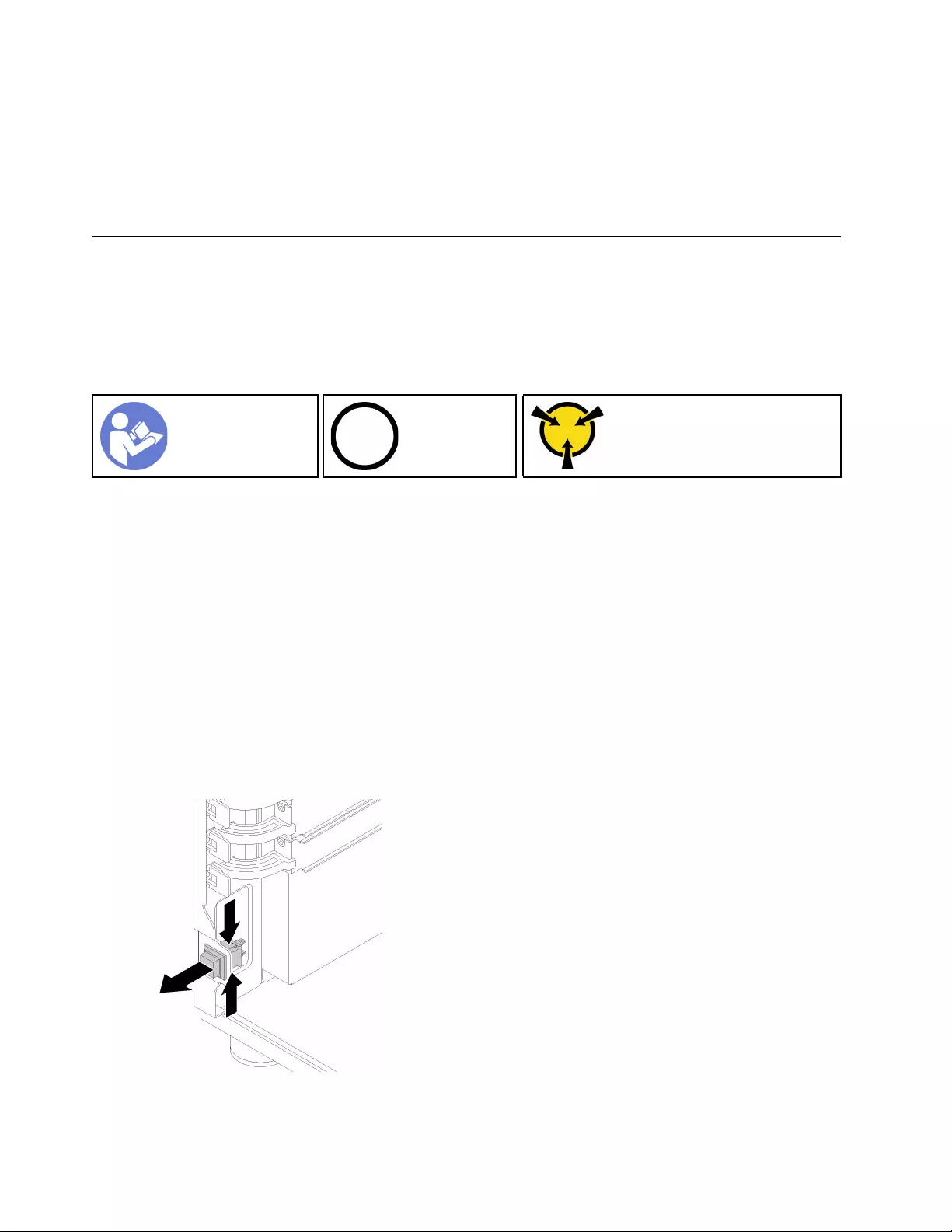
Step 4. Connect the fan power cable to the Fan 2 connector on the system board. See “System board
components” on page 29 and “Fan power cable” on page 31
After installing the heat sink and the fan module:
Complete the parts replacement. See “Complete the parts replacement” on page 155.
Intrusion switch replacement
Use this information to remove and install the intrusion switch. The intrusion switch informs you that the
server cover is not properly installed or closed by creating an event in the system event log (SEL).
Remove the intrusion switch
Use this information to remove the intrusion switch.
“Read the
installation
Guidelines” on
page 53
“Power off
the server for
this task” on
page 14
“ATTENTION:
Static Sensitive Device
Ground package before opening”
on page 55
Before removing the intrusion switch:
1. Watch the procedure
A video of this procedure is available at YouTube: https://www.youtube.com/playlist?list=
PLYV5R7hVcs-Dy5N2dPXFx5Pht-FljAi6S.
2. If the server is in a rack, remove it from the rack.
3. Remove any locking device that secures the server cover, such as a Kensington lock or a pad lock.
4. Remove the server cover (see “Remove the server cover” on page 136).
To remove the intrusion switch, complete the following steps:
Step 1. Disconnect the cable of the intrusion switch from the system board.
Step 2. Press the two tabs on the intrusion switch towards each other and carefully pull out the intrusion
switch at the same time to remove it from the frame.
Figure 76. Intrusion switch removal
98 ThinkSystem ST250 Maintenance Manual
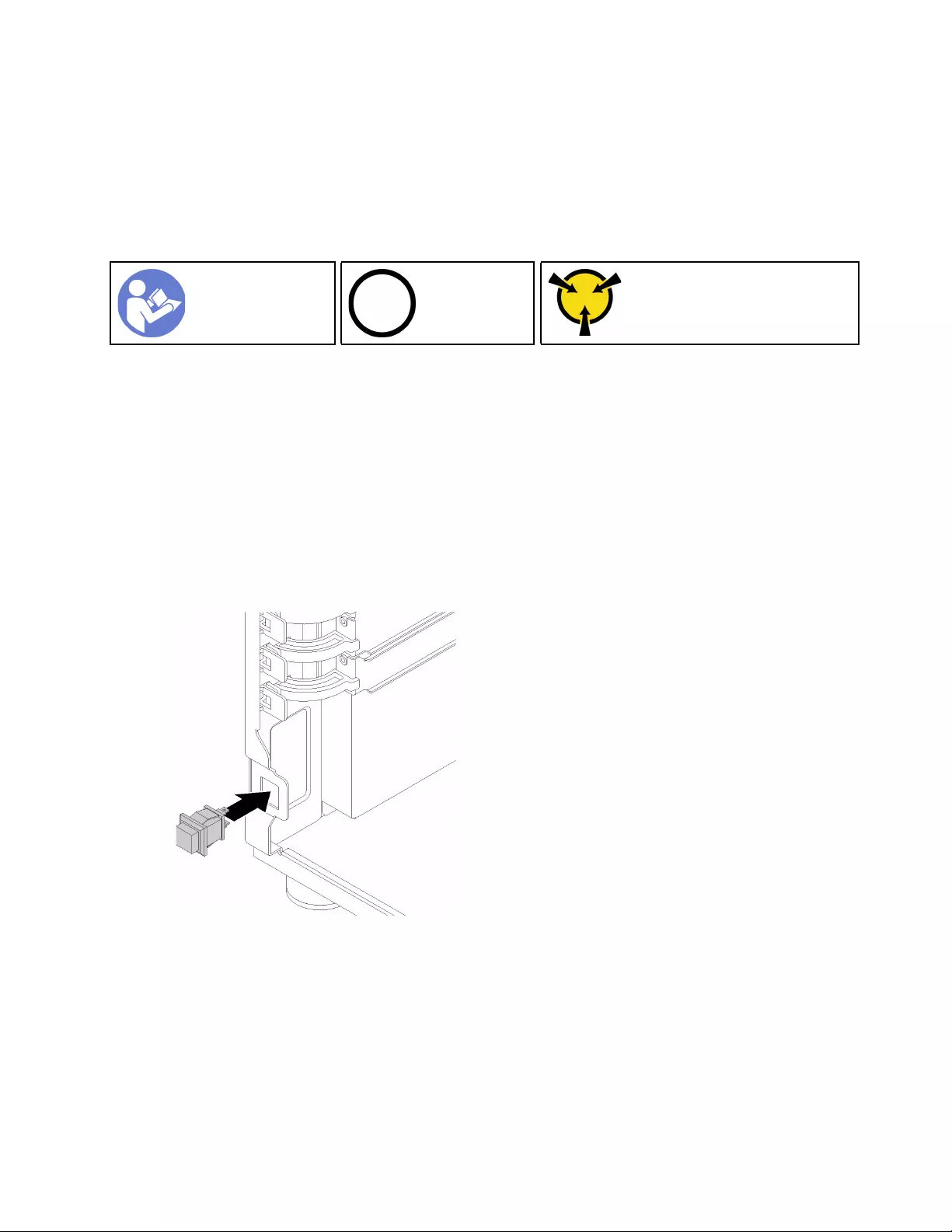
After removing the intrusion switch:
If you are instructed to return the defective component, please package the part to prevent any shipping
damage. Reuse the packaging the new part arrived in and follow all packaging instructions.
Install the intrusion switch
Use this information to install the intrusion switch.
“Read the
installation
Guidelines” on
page 53
“Power off
the server for
this task” on
page 14
“ATTENTION:
Static Sensitive Device
Ground package before opening”
on page 55
Before installing the intrusion switch:
1. Watch the procedure
A video of this procedure is available at YouTube: https://www.youtube.com/playlist?list=
PLYV5R7hVcs-Dy5N2dPXFx5Pht-FljAi6S.
2. Touch the static-protective package that contains the component to any unpainted metal surface on the
server; then, remove it from the package and place it on a static-protective surface.
To install the intrusion switch, complete the following steps:
Step 1. Insert the cable of the new intrusion switch and then the tab on the intrusion switch frame into the
corresponding hole in the chassis. Then, push the intrusion switch in until it is securely seated.
Figure 77. Installing the intrusion switch
Step 2. Connect the cable of the new intrusion switch to Chassis intrusion switch connector on the system
board. See “System board components” on page 29.
After installing the intrusion switch:
Complete the parts replacement. See “Complete the parts replacement” on page 155
Chapter 3.Hardware replacement procedures 99

M.2 drive replacement
Use this information to remove and install the M.2 drive.
Remove the M.2 drive
Use this information to remove the M.2 drive.
“Read the
installation
Guidelines” on
page 53
“Power off
the server for
this task” on
page 14
“ATTENTION:
Static Sensitive Device
Ground package before opening”
on page 55
Before removing the M.2 drive:
1. Watch the procedure
A video of this procedure is available at YouTube: https://www.youtube.com/playlist?list=
PLYV5R7hVcs-Dy5N2dPXFx5Pht-FljAi6S.
2. If the server is in a rack, remove it from the rack.
3. Remove any locking device that secures the server cover, such as a Kensington lock or a pad lock.
4. Remove the server cover (see “Remove the server cover” on page 136).
5. Obtain a #1 Phillips screwdriver
To remove the M.2 drive, complete the following steps:
Step 1. Using a #1 Phillips screwdriver, remove the screw that secures the M.2 drive to the system board.
Step 2. Pull the M.2 drive away from the connector at an angle of approximately 30 degrees.
Figure 78. M.2 drive removal
After removing the M.2 drive:
If you are instructed to return the defective component, please package the part to prevent any shipping
damage. Reuse the packaging the new part arrived in and follow all packaging instructions.
Install the M.2 drive
Use this information to install the M.2 drive.
100 ThinkSystem ST250 Maintenance Manual

“Read the
installation
Guidelines” on
page 53
“Power off
the server for
this task” on
page 14
“ATTENTION:
Static Sensitive Device
Ground package before opening”
on page 55
Before installing the M.2 drive:
1. Watch the procedure
A video of this procedure is available at YouTube: https://www.youtube.com/playlist?list=
PLYV5R7hVcs-Dy5N2dPXFx5Pht-FljAi6S.
2. Touch the static-protective package that contains the component to any unpainted metal surface on the
server; then, remove it from the package and place it on a static-protective surface.
3. Obtain a #1 Phillips screwdriver and a 4.5mm hex socket screwdriver
To install the M.2 drive, complete the following steps:
Two different M.2 drive lengths are supported by the server - 42mm and 80mm drives. If necessary, by using
a 4.5mm hex socket screwdriver, remove the standoff and screw it to the appropriate mounting point to
accommodate the specific drive.
Figure 79. Moving standoff to appropriate mounting point
Table 12. Standoff location on system board
Callout Callout
1 Standoff for 42 mm M.2 drive 2 Standoff for 80 mm M.2 drive
Step 1. Insert the M.2 drive at an angle into the connector; then, rotate it.
Step 2. Using a #1 Phillips screwdriver, tighten the screw that you saved earlier to secure the drive to the
system board.
Chapter 3.Hardware replacement procedures 101

Figure 80. M.2 drive installation
After installing the M.2 drive:
Complete the parts replacement. See “Complete the parts replacement” on page 155
Optical drive replacement
Use this information to remove and install the optical drive.
Note: This section applies only to server models that have an optical drive installed.
S006
CAUTION:
When laser products (such as CD-ROMs, DVD drives, fiber optic devices, or transmitters) are
installed, note the following:
• Do not remove the covers. Removing the covers of the laser product could result in exposure to
hazardous laser radiation. There are no serviceable parts inside the device.
• Use of controls or adjustments or performance of procedures other than those specified herein
might result in hazardous radiation exposure.
S007
CAUTION:
This product contains a Class 1M laser. Do not view directly with optical instruments.
S008
102 ThinkSystem ST250 Maintenance Manual
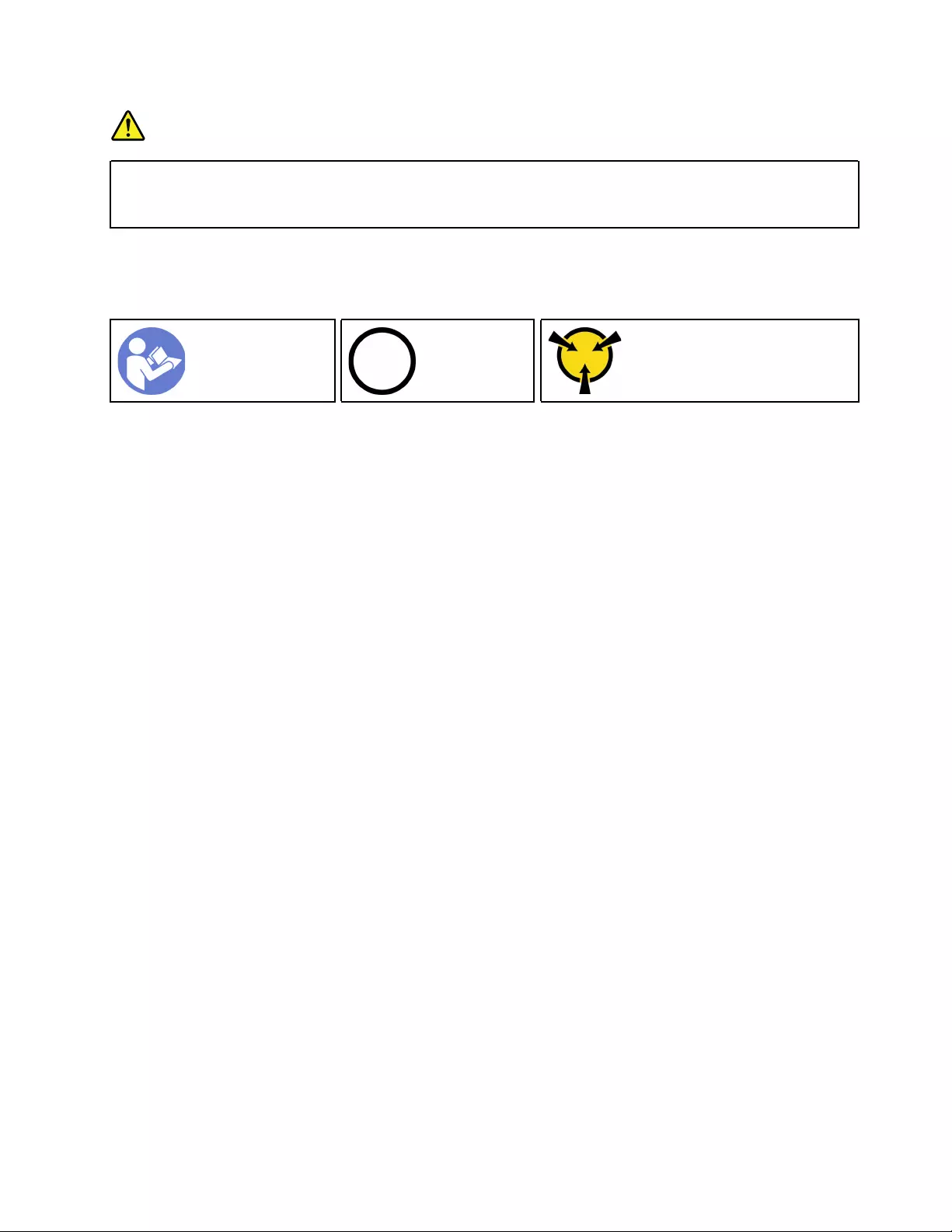
DANGER
Some laser products contain an embedded Class 3A or Class 3B laser diode. Note the following:
Laser radiation when open. Do not stare into the beam, do not view directly with optical
instruments, and avoid direct exposure to the beam.
Remove an optical drive
Use this information to remove an optical drive.
“Read the
installation
Guidelines” on
page 53
“Power off
the server for
this task” on
page 14
“ATTENTION:
Static Sensitive Device
Ground package before opening”
on page 55
Before removing an optical or tape drive:
1. Watch the procedure
A video of this procedure is available at YouTube: https://www.youtube.com/playlist?list=
PLYV5R7hVcs-Dy5N2dPXFx5Pht-FljAi6S.
2. If the server is in a rack, remove it from the rack.
3. Remove any locking device that secures the server cover, such as a Kensington lock or a pad lock.
4. Use the front door key to unlock the front door (available on some models), and then open the front
door.
5. Remove the server cover (see “Remove the server cover” on page 136).
To remove an optical drive, complete the following steps:
Step 1. Disconnect the cables from the rear of the optical drive.
Chapter 3.Hardware replacement procedures 103
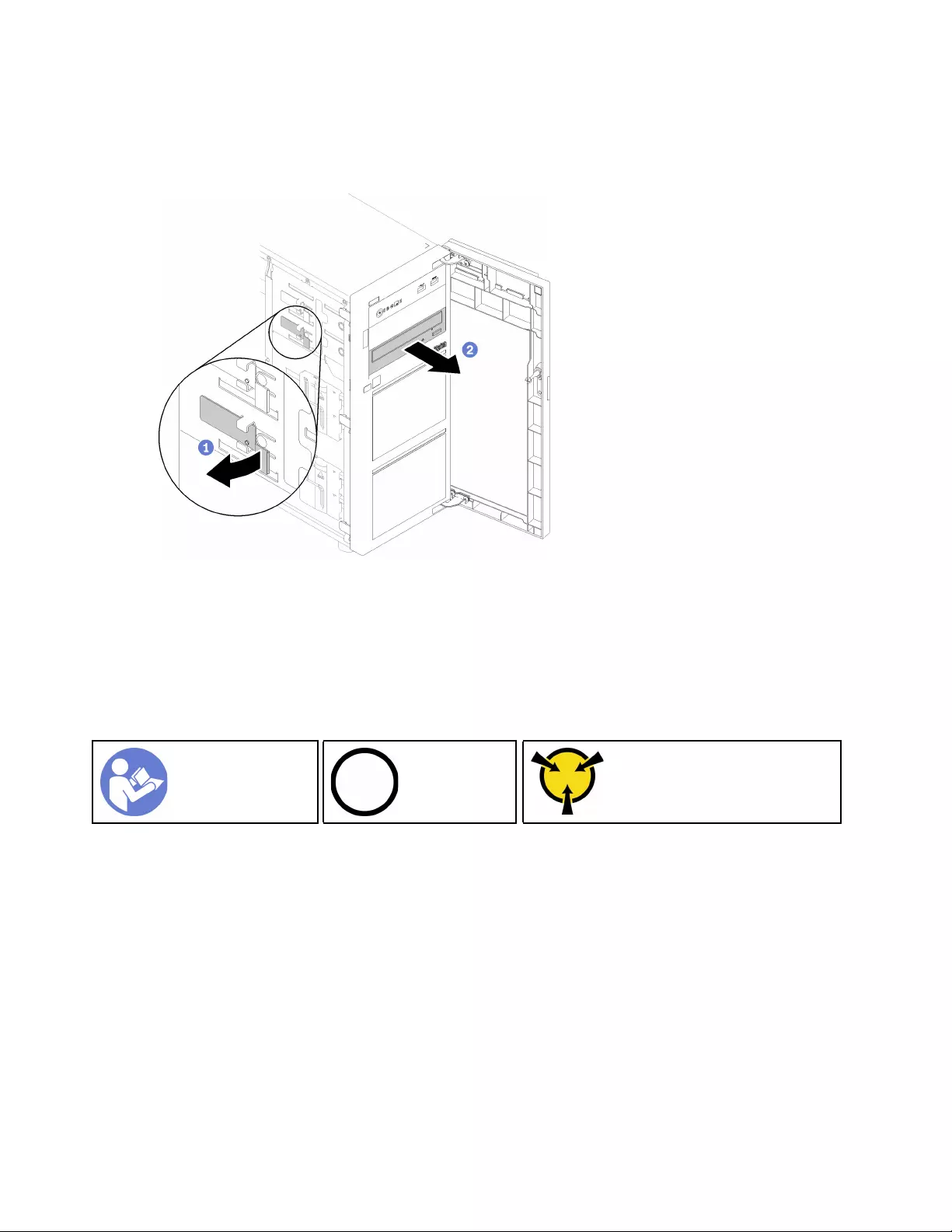
Step 2. Gently pull the metal tab on the side of the chassis and push the optical drive outward from the
rear; then, draw the optical drive out of the chassis.
Figure 81. Optical drive removal
After removing the optical drive:
If you are instructed to return the defective component, please package the part to prevent any shipping
damage. Reuse the packaging the new part arrived in and follow all packaging instructions.
Install an optical drive
Use this information to install an optical drive.
“Read the
installation
Guidelines” on
page 53
“Power off
the server for
this task” on
page 14
“ATTENTION:
Static Sensitive Device
Ground package before opening”
on page 55
Before installing an optical drive:
1. Watch the procedure
A video of this procedure is available at YouTube: https://www.youtube.com/playlist?list=
PLYV5R7hVcs-Dy5N2dPXFx5Pht-FljAi6S.
2. Touch the static-protective package that contains the component to any unpainted metal surface on the
server; then, remove it from the package and place it on a static-protective surface.
To install an optical drive, complete the following steps:
Step 1. Remove the front door (see “Remove the front door” on page 90).
Step 2. Remove the front bezel (see “Remove the front bezel” on page 88).
Step 3. If necessary, press the tabs on the side of the plastic bay filler of the optical drive bay and push the
plastic bay filler as shown to remove it.
104 ThinkSystem ST250 Maintenance Manual

Figure 83. EMI shield removal in optical drive bay
Step 5. Insert the optical drive into the optical drive bay and slide it in until it is obstructed.
Step 6. Gently pull the metal tab on the slide of the chassis and slide the optical drive slightly. Release the
tab and keep sliding the optical drive until it snaps into position.
Figure 84. Optical drive installation
Step 7. Connect the power cable and the signal cable to the rear of the optical drive. See “Cable routing:
optical drive” on page 34.
106 ThinkSystem ST250 Maintenance Manual

Step 8. Save the removed EMI-protective shield from the chassis and the plastic bay filler from the front
bezel in case you later remove the drive and need the shields to cover the drive bay.
After installing the optical drive:
Complete the parts replacement. See “Complete the parts replacement” on page 155
PCIe adapter replacement
Use this information to remove and install a PCIe adapter.
Your server comes with four PCIe slots. Depending on your needs, you can install a PCIe adapter to obtain
the corresponding function or remove the adapter if necessary. The PCIe adapter can be an Ethernet
adapter, a host bus adapter, a RAID adapter, a graphics adapter, or any other supported PCIe adapters.
PCIe adapters vary by type, but the installation and removal procedures are the same.
Note: For a list of the supported PCIe adapters, see:
https://static.lenovo.com/us/en/serverproven/index.shtml
Remove a PCIe adapter
Use this information to remove a PCIe adapter.
“Read the
installation
Guidelines” on
page 53
“Power off
the server for
this task” on
page 14
“ATTENTION:
Static Sensitive Device
Ground package before opening”
on page 55
Before removing a PCIe adapter:
1. Watch the procedure
A video of this procedure is available at YouTube: https://www.youtube.com/playlist?list=
PLYV5R7hVcs-Dy5N2dPXFx5Pht-FljAi6S.
2. If the server is in a rack, remove it from the rack.
3. Remove any locking device that secures the server cover, such as a Kensington lock or a pad lock.
4. Remove the server cover (see “Remove the server cover” on page 136).
5. Remove the processor and the heat sink if necessary (see “Remove the processor” on page 133).
Notes:
• Depending on the specific type, your PCIe adapter might look different from the illustration in this topic.
• Use any documentation that comes with the PCIe adapter and follow those instructions in addition to the
instructions in this topic.
To remove a PCIe adapter, complete the following steps:
Step 1. Lay the server on its side for easier operation.
Step 2. Locate the PCIe adapter you want to remove. Depending on the type of a PCIe card, you might also
need to disconnect all cables from a PCIe card, the system board, or the hot-swap drive
backplane.
Step 3. If the PCIe adapter is secured by a retaining clip, disengage the adapter from the retaining clip first.
Chapter 3.Hardware replacement procedures 107

Step 4. Open the adapter latch as shown; then, grasp the PCIe adapter by its edges and carefully pull it out
of the slot.
Figure 85. PCIe adapter removal
After removing the PCIe adapter:
1. Install another PCIe adapter if necessary (see “Install a PCIe adapter” on page 108). Otherwise, install a
bracket to cover the vacancy.
2. If you are instructed to return the defective component, please package the part to prevent any shipping
damage. Reuse the packaging the new part arrived in and follow all packaging instructions.
Install a PCIe adapter
Use this information to install a PCIe adapter.
“Read the
installation
Guidelines” on
page 53
“Power off
the server for
this task” on
page 14
“ATTENTION:
Static Sensitive Device
Ground package before opening”
on page 55
Notes:
• Depending on the specific type, your PCIe adapter might look different from the illustration in this topic.
• Use any documentation that comes with the PCIe adapter and follow those instructions in addition to the
instructions in this topic.
• ThinkSystem Broadcom NX-E PCIe 10Gb 2-Port Base-T Ethernet Adapter can only be installed in the slot
2.
Before installing a PCIe adapter:
108 ThinkSystem ST250 Maintenance Manual

1. Watch the procedure
A video of this procedure is available at YouTube: https://www.youtube.com/playlist?list=
PLYV5R7hVcs-Dy5N2dPXFx5Pht-FljAi6S.
2. If a bracket is installed in the PCIe slot, remove it. Store the bracket for the PCIe slot in case that you
later remove the PCIe adapter and need the bracket to cover the place.
3. Touch the static-protective package that contains the component to any unpainted metal surface on the
server; then, remove it from the package and place it on a static-protective surface.
To install a PCIe adapter, complete the following steps:
Step 1. Lay the server on its side for easier operation.
Step 2. Locate the applicable PCIe slot. See “Specifications” on page 3 to identify the different types of
PCIe slots in your server.
Step 3. Open the card latch. Position the new PCIe adapter over the PCIe slot; then, carefully press the
PCIe card straight down until it is securely seated in the slot. Close the card latch to secure the
PCIe adapter in place.
Figure 86. PCIe adapter installation
Step 4. Depending on the type of the PCIe adapter, you might need to connect any required cables. Refer
to “Internal cable routing” on page 31 or the documentation that comes with the PCIe adapter for
specific information.
After installing the PCIe adapter:
Complete the parts replacement. See “Complete the parts replacement” on page 155
Power distribution board replacement
Use this information to remove and install the power distribution board.
Chapter 3.Hardware replacement procedures 109

Remove the power distribution board
Use this information to remove the power distribution board.
“Read the
installation
Guidelines” on
page 53
“Power off
the server for
this task” on
page 14
“ATTENTION:
Static Sensitive Device
Ground package before opening”
on page 55
S001
DANGER
Electrical current from power, telephone, and communication cables is hazardous.
To avoid a shock hazard:
• Connect all power cords to a properly wired and grounded electrical outlet/source.
• Connect any equipment that will be attached to this product to properly wired outlets/sources.
• When possible, use one hand only to connect or disconnect signal cables.
• Never turn on any equipment when there is evidence of fire, water, or structural damage.
• The device might have more than one power cord, to remove all electrical current from the
device, ensure that all power cords are disconnected from the power source.
Before removing the power distribution board:
1. Watch the procedure
A video of this procedure is available at YouTube: https://www.youtube.com/playlist?list=
PLYV5R7hVcs-Dy5N2dPXFx5Pht-FljAi6S.
2. If the server is in a rack, remove it from the rack.
3. Remove any locking device that secures the server cover, such as a Kensington lock or a pad lock.
4. Remove the server cover (see “Remove the server cover” on page 136).
To remove the power distribution board, complete the following steps:
Step 1. Remove the hot-swap redundant power supply. See “Remove a hot-swap power supply” on page
123.
Step 2. Remove the power distribution board cover by removing the screw.
Step 3. Disconnect the power cables from the power distribution board.
Step 4. Pull the power distribution board outward to release it from the power supply cage; then, remove
the power distribution board out of the chassis.
Note: Carefully handle the power distribution board by its edges.
110 ThinkSystem ST250 Maintenance Manual

Figure 87. Power distribution board removal
After removing the power distribution board:
If you are instructed to return the defective component, please package the part to prevent any shipping
damage. Reuse the packaging the new part arrived in and follow all packaging instructions.
Install the power distribution board
Use this information to install the power distribution board.
“Read the
installation
Guidelines” on
page 53
“Power off
the server for
this task” on
page 14
“ATTENTION:
Static Sensitive Device
Ground package before opening”
on page 55
S001
Chapter 3.Hardware replacement procedures 111
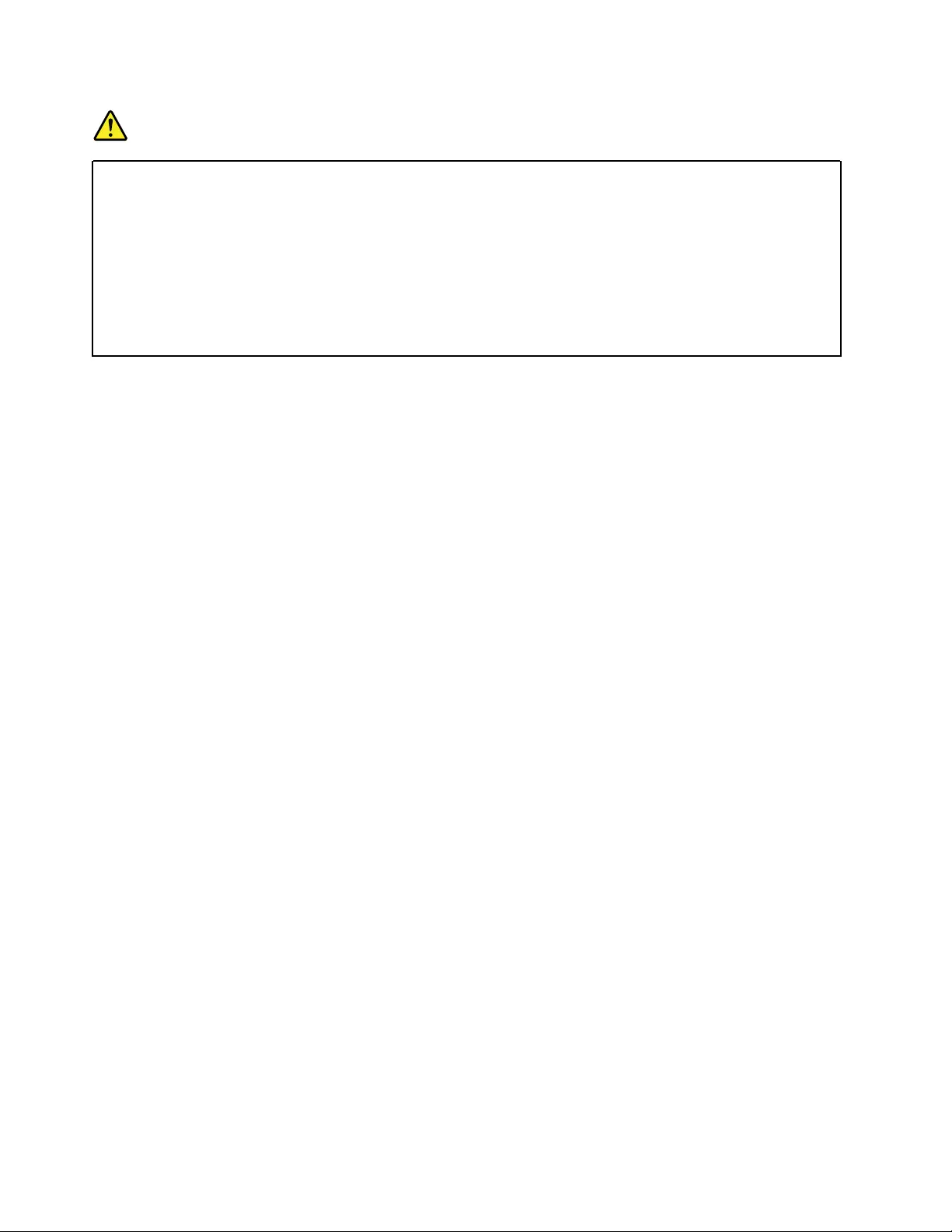
DANGER
Electrical current from power, telephone, and communication cables is hazardous.
To avoid a shock hazard:
• Connect all power cords to a properly wired and grounded electrical outlet/source.
• Connect any equipment that will be attached to this product to properly wired outlets/sources.
• When possible, use one hand only to connect or disconnect signal cables.
• Never turn on any equipment when there is evidence of fire, water, or structural damage.
• The device might have more than one power cord, to remove all electrical current from the
device, ensure that all power cords are disconnected from the power source.
Before installing the power distribution board,
1. Watch the procedure
A video of this procedure is available at YouTube: https://www.youtube.com/playlist?list=
PLYV5R7hVcs-Dy5N2dPXFx5Pht-FljAi6S.
2. Touch the static-protective package that contains the component to any unpainted metal surface on the
server; then, remove it from the package and place it on a static-protective surface.
To install the power distribution board, complete the following steps:
Step 1. Lay the server on its side for easier operation.
Step 2. Hold the power distribution board by its edges and position it to the power supply cage. Ensure
that the four tabs on the power supply cage are inserted into the corresponding holes in the power
distribution board; then, push the power distribution board inward.
112 ThinkSystem ST250 Maintenance Manual

Figure 88. Power distribution board installation
Step 3. Connect the power cables to the new power distribution board; then, properly route the cables and
secure the cables with the cable clips and ties in the chassis.
Step 4. Ensure that the hole in the power distribution board cover is aligned with the one in the power
supply cage; then, install the screw to secure the power distribution board cover.
Chapter 3.Hardware replacement procedures 113

Figure 89. Power distribution board cover installation
After installing the power distribution board:
Complete the parts replacement. See “Complete the parts replacement” on page 155
Power supply unit replacement
Use this information to remove and install the fixed or redundant power supply unit.
Remove the fixed power supply
Use this information to remove the fixed power supply.
“Read the
installation
Guidelines” on
page 53
“Power off
the server for
this task” on
page 14
“ATTENTION:
Static Sensitive Device
Ground package before opening”
on page 55
114 ThinkSystem ST250 Maintenance Manual
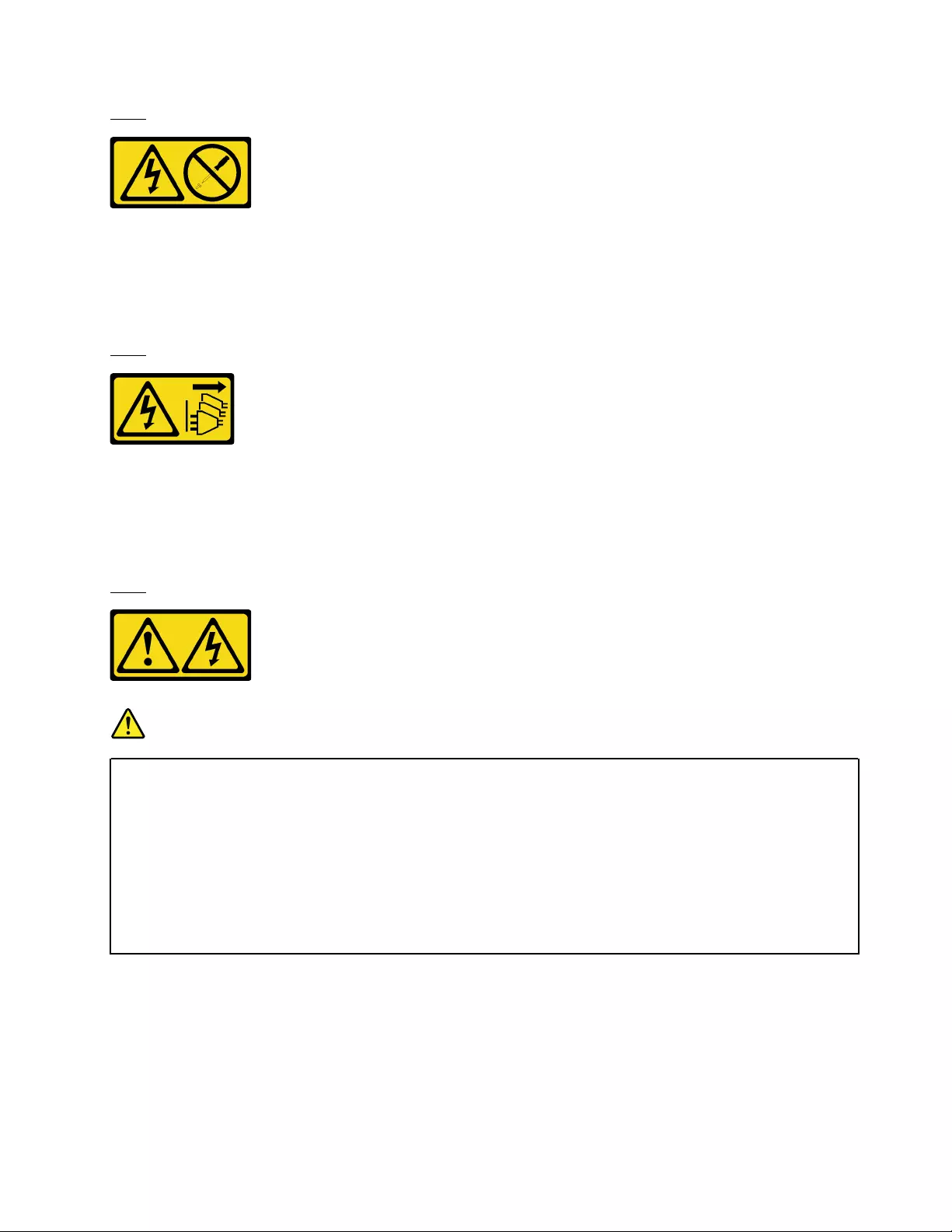
S035
CAUTION:
Never remove the cover on a power supply or any part that has this label attached. Hazardous voltage,
current, and energy levels are present inside any component that has this label attached. There are no
serviceable parts inside these components. If you suspect a problem with one of these parts, contact
a service technician.
S002
CAUTION:
The power-control button on the device and the power switch on the power supply do not turn off the
electrical current supplied to the device. The device also might have more than one power cord. To
remove all electrical current from the device, ensure that all power cords are disconnected from the
power source.
S001
DANGER
Electrical current from power, telephone, and communication cables is hazardous.
To avoid a shock hazard:
• Connect all power cords to a properly wired and grounded electrical outlet/source.
• Connect any equipment that will be attached to this product to properly wired outlets/sources.
• When possible, use one hand only to connect or disconnect signal cables.
• Never turn on any equipment when there is evidence of fire, water, or structural damage.
• The device might have more than one power cord, to remove all electrical current from the
device, ensure that all power cords are disconnected from the power source.
Chapter 3.Hardware replacement procedures 115

Figure 90. Fixed power supply label on the cover
NEVER CONNECT AND DISCONNECT THE POWER SUPPLY CABLE AND EQUIPMENT WHILE YOUR
EQUIPMENT IS POWERED ON WITH DC SUPPLY (hot-plugging). Otherwise you may damage the
equipment and result in data loss, the damages and losses result from incorrect operation of the equipment
will not be covered by the manufacturers’ warranty.
S035
CAUTION:
Never remove the cover on a power supply or any part that has this label attached. Hazardous voltage,
current, and energy levels are present inside any component that has this label attached. There are no
serviceable parts inside these components. If you suspect a problem with one of these parts, contact
a service technician.
S019
CAUTION:
The power-control button on the device does not turn off the electrical current supplied to the device.
The device also might have more than one connection to dc power. To remove all electrical current
from the device, ensure that all connections to dc power are disconnected at the dc power input
terminals.
S029
116 ThinkSystem ST250 Maintenance Manual

DANGER
Electrical current from power, telephone, and communication cables is hazardous.
To avoid a shock hazard:
• Do not connect or disconnect any cables or perform installation, maintenance, or reconfiguration
of this product during an electrical storm.
• Connect all power cords to a properly wired and grounded power source.
• Connect to properly wired power sources any equipment that will be attached to this product.
• When possible, use one hand only to connect or disconnect signal cables.
• Never turn on any equipment when there is evidence of fire, water, or structural damage.
• Disconnect the attached ac power cords, dc power sources, network connections,
telecommunications systems, and serial cables before you open the device covers, unless you
are instructed otherwise in the installation and configuration procedures.
• Connect and disconnect cables as described in the following table when installing, moving, or
opening covers on this product or attached devices.
To Connect: To Disconnect:
1. Turn OFF all power sources and equipment that is to
be attached to this product.
2. Attach signal cables to the product.
3. Attach power cords to the product.
• For ac systems, use appliance inlets.
• For dc systems, ensure correct polarity of -48 V dc
connections: RTN is + and -48 V dc is -. Earth
ground should use a two-hole lug for safety.
4. Attach signal cables to other devices.
5. Connect power cords to their sources.
6. Turn ON all the power sources.
1. Turn OFF all power sources and equipment that is to
be attached to this product.
• For ac systems, remove all power cords from the
chassis power receptacles or interrupt power at
the ac power distribution unit.
• For dc systems, disconnect dc power sources at
the breaker panel or by turning off the power
source. Then, remove the dc cables.
2. Remove the signal cables from the connectors.
3. Remove all cables from the devices.
Before removing the fixed power supply:
1. Watch the procedure
A video of this procedure is available at YouTube: https://www.youtube.com/playlist?list=
PLYV5R7hVcs-Dy5N2dPXFx5Pht-FljAi6S.
2. If the server is in a rack, remove it from the rack.
3. Remove any locking device that secures the server cover, such as a Kensington lock or a pad lock.
4. Remove the server cover (see “Remove the server cover” on page 136).
To remove the fixed power supply, complete the following steps:
Step 1. Remove all cables on the fixed power supply from the power interface board (PIB).
Step 2. Remove the four screws at the rear of the chassis that secure the power supply; then, push the
power supply from the rear until it is released from the metal retaining tab.
Step 3. Carefully lift the fixed power supply out of the chassis.
Chapter 3.Hardware replacement procedures 117
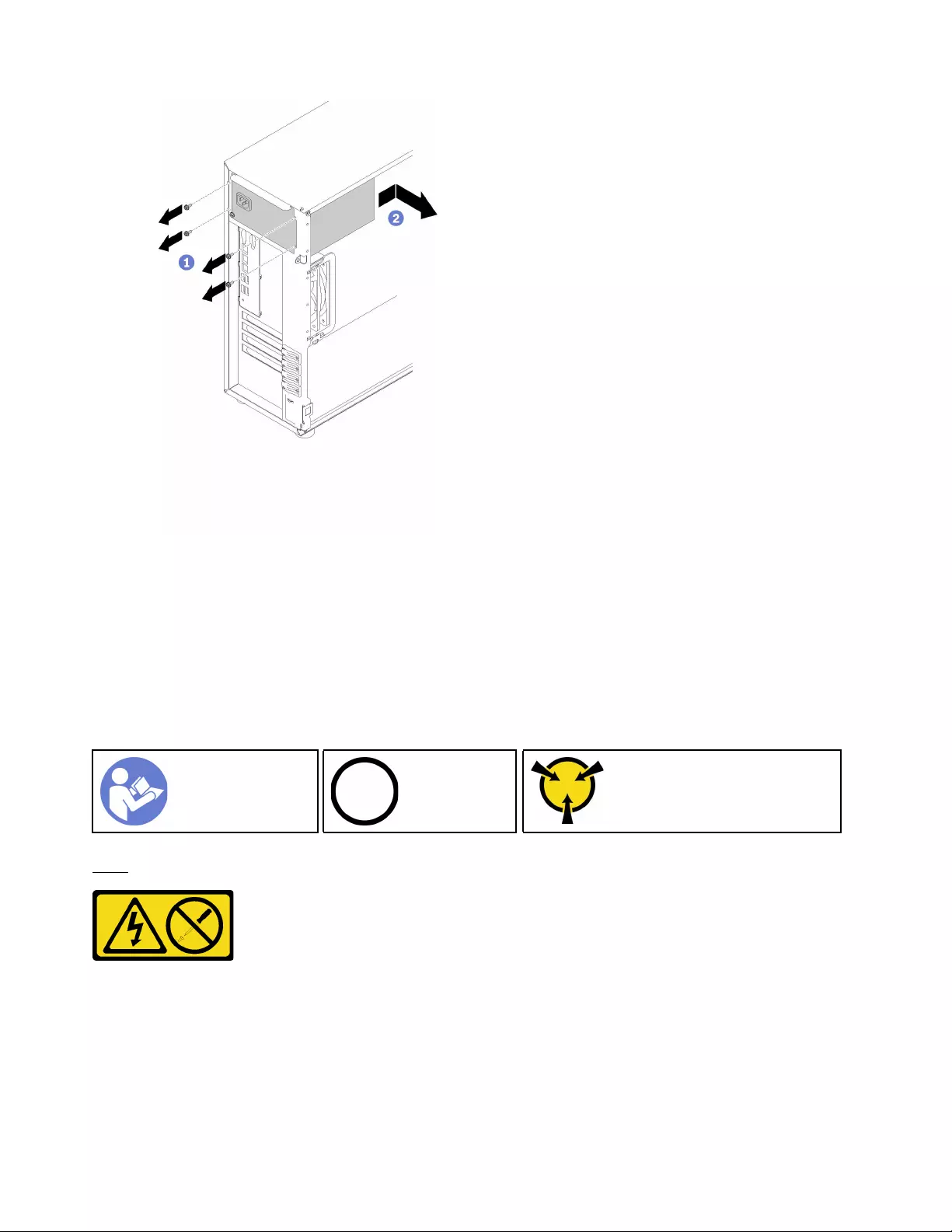
Figure 91. Fixed power supply removal
After removing the fixed power supply:
If you are instructed to return the defective component, please package the part to prevent any shipping
damage. Reuse the packaging the new part arrived in and follow all packaging instructions.
Install the fixed power supply
Use this information to install the fixed power supply.
“Read the
installation
Guidelines” on
page 53
“Power off
the server for
this task” on
page 14
“ATTENTION:
Static Sensitive Device
Ground package before opening”
on page 55
S035
CAUTION:
Never remove the cover on a power supply or any part that has this label attached. Hazardous voltage,
current, and energy levels are present inside any component that has this label attached. There are no
serviceable parts inside these components. If you suspect a problem with one of these parts, contact
a service technician.
118 ThinkSystem ST250 Maintenance Manual

S002
CAUTION:
The power-control button on the device and the power switch on the power supply do not turn off the
electrical current supplied to the device. The device also might have more than one power cord. To
remove all electrical current from the device, ensure that all power cords are disconnected from the
power source.
S001
DANGER
Electrical current from power, telephone, and communication cables is hazardous.
To avoid a shock hazard:
• Connect all power cords to a properly wired and grounded electrical outlet/source.
• Connect any equipment that will be attached to this product to properly wired outlets/sources.
• When possible, use one hand only to connect or disconnect signal cables.
• Never turn on any equipment when there is evidence of fire, water, or structural damage.
• The device might have more than one power cord, to remove all electrical current from the
device, ensure that all power cords are disconnected from the power source.
Figure 92. Power supply unit label on the cover
The following tips describe the information that you must consider when you install a power supply with dc
input.
NEVER CONNECT AND DISCONNECT THE POWER SUPPLY CABLE AND EQUIPMENT WHILE YOUR
EQUIPMENT IS POWERED ON WITH DC SUPPLY (hot-plugging). Otherwise you may damage the
equipment and result in data loss, the damages and losses result from incorrect operation of the equipment
will not be covered by the manufacturers’ warranty.
Chapter 3.Hardware replacement procedures 119
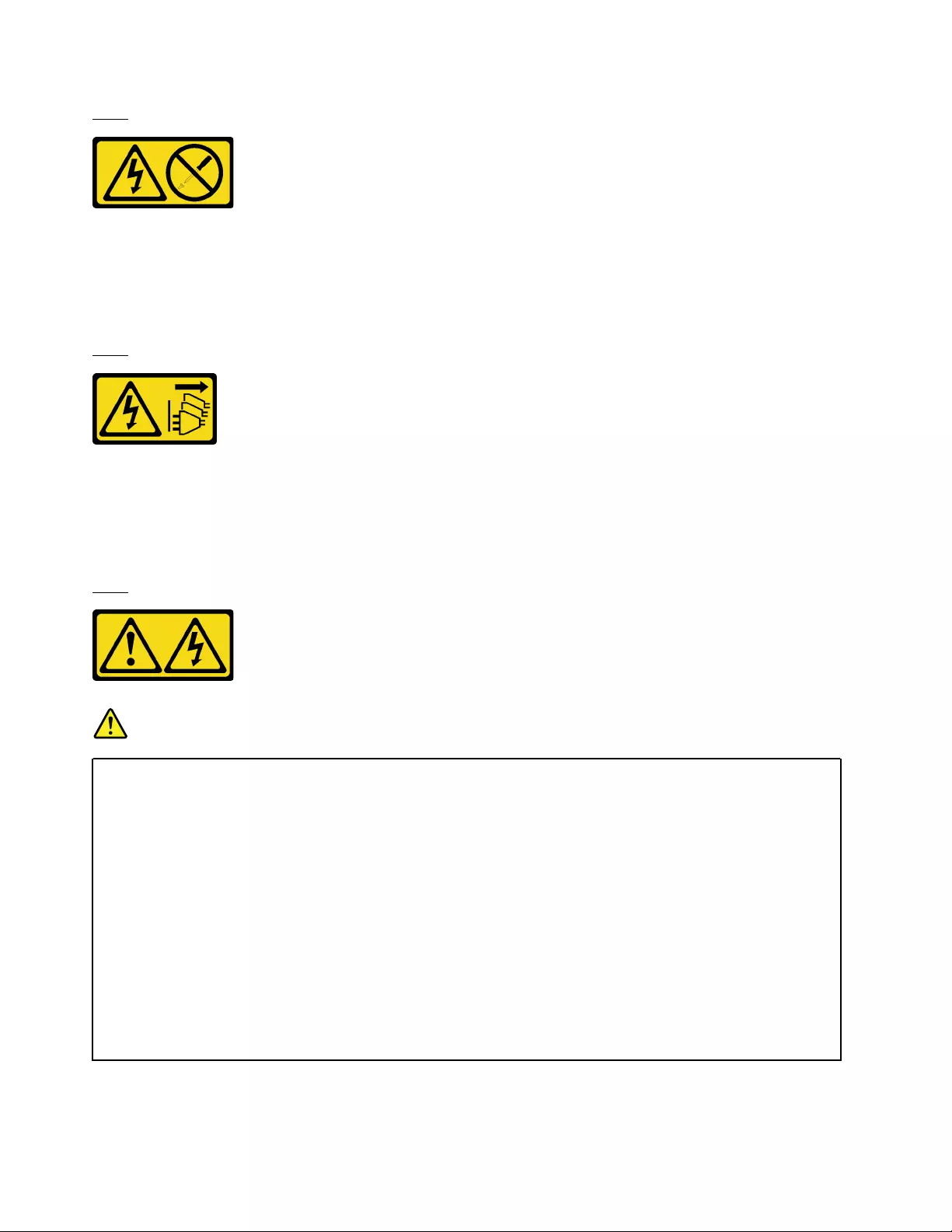
S035
CAUTION:
Never remove the cover on a power supply or any part that has this label attached. Hazardous voltage,
current, and energy levels are present inside any component that has this label attached. There are no
serviceable parts inside these components. If you suspect a problem with one of these parts, contact
a service technician.
S019
CAUTION:
The power-control button on the device does not turn off the electrical current supplied to the device.
The device also might have more than one connection to dc power. To remove all electrical current
from the device, ensure that all connections to dc power are disconnected at the dc power input
terminals.
S029
DANGER
Electrical current from power, telephone, and communication cables is hazardous.
To avoid a shock hazard:
• Do not connect or disconnect any cables or perform installation, maintenance, or reconfiguration
of this product during an electrical storm.
• Connect all power cords to a properly wired and grounded power source.
• Connect to properly wired power sources any equipment that will be attached to this product.
• When possible, use one hand only to connect or disconnect signal cables.
• Never turn on any equipment when there is evidence of fire, water, or structural damage.
• Disconnect the attached ac power cords, dc power sources, network connections,
telecommunications systems, and serial cables before you open the device covers, unless you
are instructed otherwise in the installation and configuration procedures.
• Connect and disconnect cables as described in the following table when installing, moving, or
opening covers on this product or attached devices.
120 ThinkSystem ST250 Maintenance Manual

To Connect: To Disconnect:
1. Turn OFF all power sources and equipment that is to
be attached to this product.
2. Attach signal cables to the product.
3. Attach power cords to the product.
• For ac systems, use appliance inlets.
• For dc systems, ensure correct polarity of -48 V dc
connections: RTN is + and -48 V dc is -. Earth
ground should use a two-hole lug for safety.
4. Attach signal cables to other devices.
5. Connect power cords to their sources.
6. Turn ON all the power sources.
1. Turn OFF all power sources and equipment that is to
be attached to this product.
• For ac systems, remove all power cords from the
chassis power receptacles or interrupt power at
the ac power distribution unit.
• For dc systems, disconnect dc power sources at
the breaker panel or by turning off the power
source. Then, remove the dc cables.
2. Remove the signal cables from the connectors.
3. Remove all cables from the devices.
Before installing the fixed power supply,
1. Watch the procedure
A video of this procedure is available at YouTube: https://www.youtube.com/playlist?list=
PLYV5R7hVcs-Dy5N2dPXFx5Pht-FljAi6S.
2. Touch the static-protective package that contains the component to any unpainted metal surface on the
server; then, remove it from the package and place it on a static-protective surface.
To install the fixed power supply, complete the following steps:
Step 1. Align the tabs on the fixed power supply bracket with the corresponding holes on the chassis.
Step 2. Pivot the fixed power supply bracket in until it snaps into position.
Chapter 3.Hardware replacement procedures 121
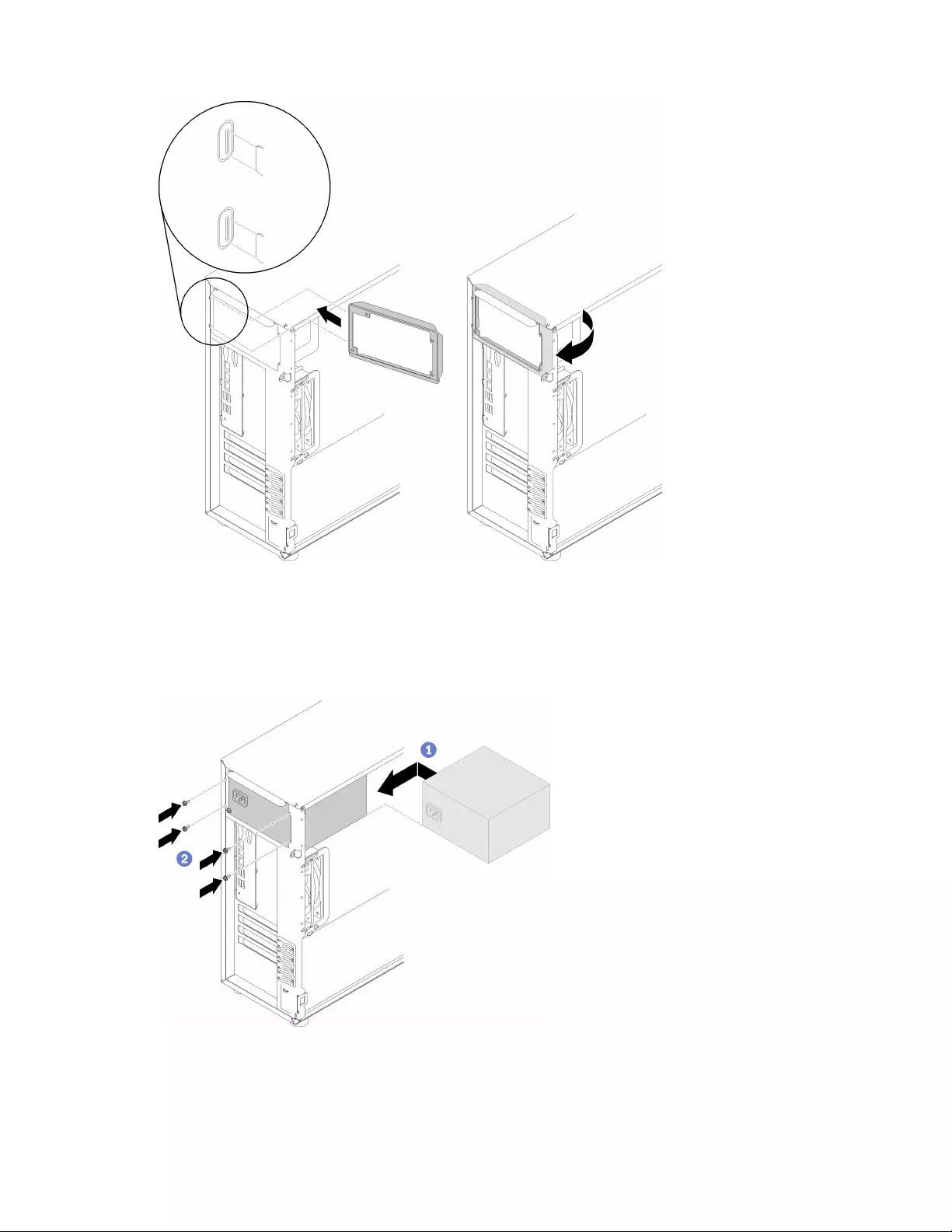
Figure 93. Fixed power supply bracket installation
Step 3. Slide the fixed power supply into the bay until it snaps into position. Make sure the four screw holes
in the fixed power supply are aligned with the corresponding holes in the rear of the chassis
Step 4. Install the four screws to secure the fixed power supply in place.
Figure 94. Fixed power supply installation
After installing the fixed power supply:
122 ThinkSystem ST250 Maintenance Manual

1. Connect all cables on the fixed power supply to corresponding connectors on the system board. See
“Fixed power supply” on page 38.
2. Connect the power cable to the power supply and a properly grounded electrical outlet.
3. Power on the server. Ensure that both the power input LED and the power output LED on the power
supply are lit, indicating that the power supply is operating properly.
4. Complete the parts replacement. See “Complete the parts replacement” on page 155
Remove a hot-swap power supply
Use this information to remove a hot-swap power supply.
“Read the
installation
Guidelines” on
page 53
“ATTENTION:
Static Sensitive Device
Ground package before opening”
on page 55
S035
CAUTION:
Never remove the cover on a power supply or any part that has this label attached. Hazardous voltage,
current, and energy levels are present inside any component that has this label attached. There are no
serviceable parts inside these components. If you suspect a problem with one of these parts, contact
a service technician.
S002
CAUTION:
The power-control button on the device and the power switch on the power supply do not turn off the
electrical current supplied to the device. The device also might have more than one power cord. To
remove all electrical current from the device, ensure that all power cords are disconnected from the
power source.
S001
Chapter 3.Hardware replacement procedures 123
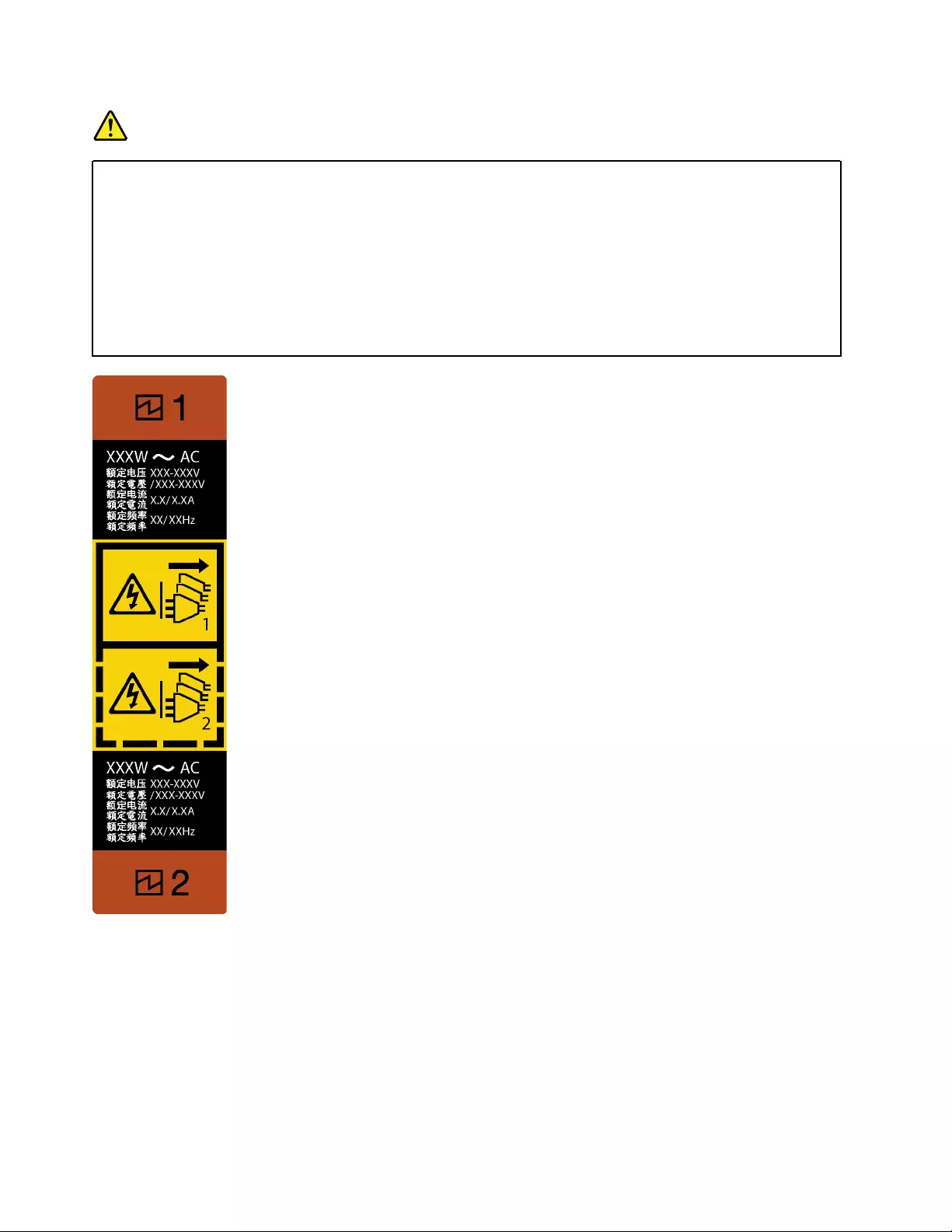
DANGER
Electrical current from power, telephone, and communication cables is hazardous.
To avoid a shock hazard:
• Connect all power cords to a properly wired and grounded electrical outlet/source.
• Connect any equipment that will be attached to this product to properly wired outlets/sources.
• When possible, use one hand only to connect or disconnect signal cables.
• Never turn on any equipment when there is evidence of fire, water, or structural damage.
• The device might have more than one power cord, to remove all electrical current from the
device, ensure that all power cords are disconnected from the power source.
Figure 95. Hot-swap power supply label
Attention: This type of power supply is hot-swap only when two power supplies are installed for
redundancy. If only one power supply is installed, you must power off the server first before removing the
power supply.
The following tips describe the information that you must consider when you remove a power supply with dc
input.
124 ThinkSystem ST250 Maintenance Manual
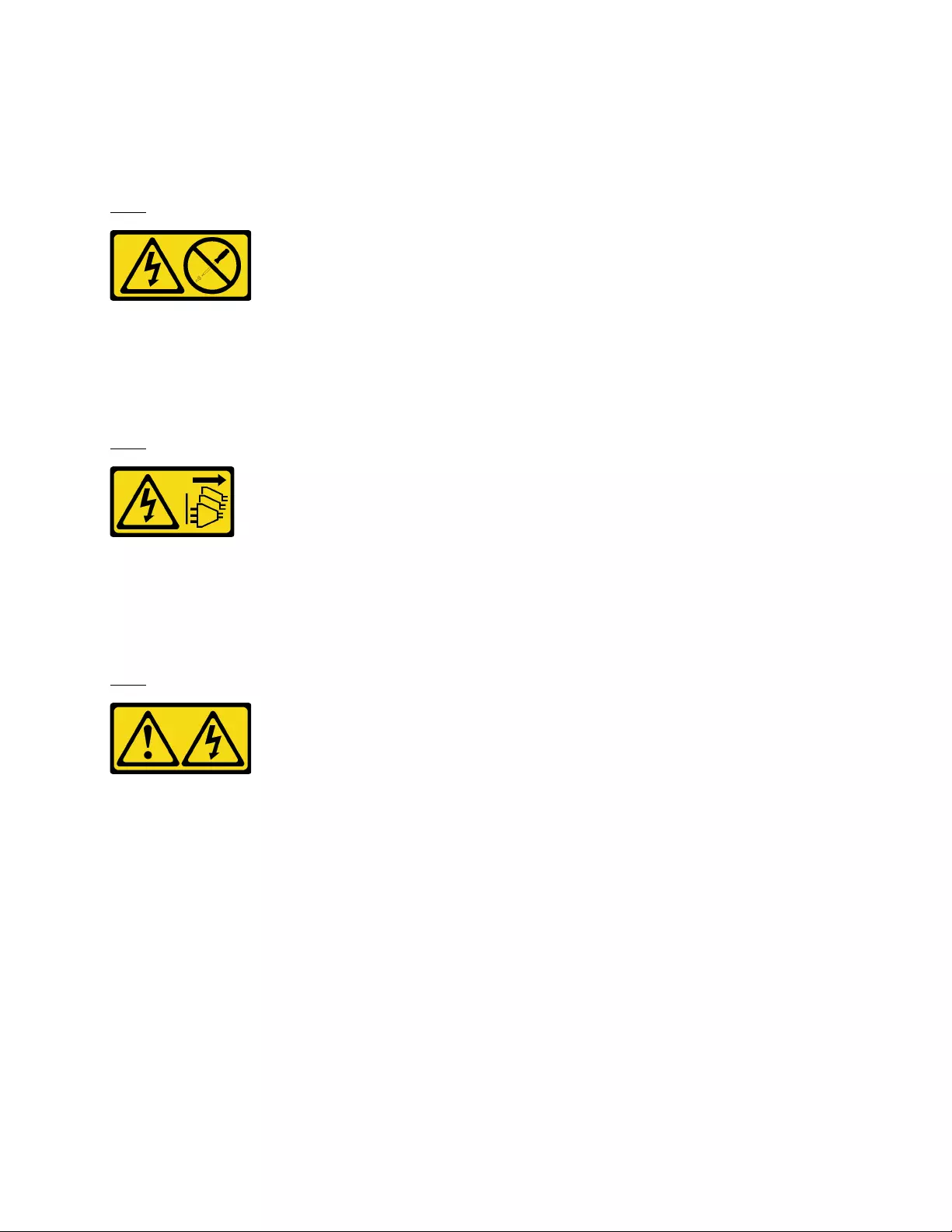
NEVER CONNECT AND DISCONNECT THE POWER SUPPLY CABLE AND EQUIPMENT WHILE YOUR
EQUIPMENT IS POWERED ON WITH DC SUPPLY (hot-plugging). Otherwise you may damage the
equipment and result in data loss, the damages and losses result from incorrect operation of the equipment
will not be covered by the manufacturers’ warranty.
S035
CAUTION:
Never remove the cover on a power supply or any part that has this label attached. Hazardous voltage,
current, and energy levels are present inside any component that has this label attached. There are no
serviceable parts inside these components. If you suspect a problem with one of these parts, contact
a service technician.
S019
CAUTION:
The power-control button on the device does not turn off the electrical current supplied to the device.
The device also might have more than one connection to dc power. To remove all electrical current
from the device, ensure that all connections to dc power are disconnected at the dc power input
terminals.
S029
Chapter 3.Hardware replacement procedures 125

DANGER
Electrical current from power, telephone, and communication cables is hazardous.
To avoid a shock hazard:
• Do not connect or disconnect any cables or perform installation, maintenance, or reconfiguration
of this product during an electrical storm.
• Connect all power cords to a properly wired and grounded power source.
• Connect to properly wired power sources any equipment that will be attached to this product.
• When possible, use one hand only to connect or disconnect signal cables.
• Never turn on any equipment when there is evidence of fire, water, or structural damage.
• Disconnect the attached ac power cords, dc power sources, network connections,
telecommunications systems, and serial cables before you open the device covers, unless you
are instructed otherwise in the installation and configuration procedures.
• Connect and disconnect cables as described in the following table when installing, moving, or
opening covers on this product or attached devices.
To Connect: To Disconnect:
1. Turn OFF all power sources and equipment that is to
be attached to this product.
2. Attach signal cables to the product.
3. Attach power cords to the product.
• For ac systems, use appliance inlets.
• For dc systems, ensure correct polarity of -48 V dc
connections: RTN is + and -48 V dc is -. Earth
ground should use a two-hole lug for safety.
4. Attach signal cables to other devices.
5. Connect power cords to their sources.
6. Turn ON all the power sources.
1. Turn OFF all power sources and equipment that is to
be attached to this product.
• For ac systems, remove all power cords from the
chassis power receptacles or interrupt power at
the ac power distribution unit.
• For dc systems, disconnect dc power sources at
the breaker panel or by turning off the power
source. Then, remove the dc cables.
2. Remove the signal cables from the connectors.
3. Remove all cables from the devices.
Before removing the hot-swap power supply:
1. Watch the procedure
A video of this procedure is available at YouTube: https://www.youtube.com/playlist?list=
PLYV5R7hVcs-Dy5N2dPXFx5Pht-FljAi6S.
2. If the server is in a rack, pull back the cable management arm to gain access to the rear of the server and
the power supply.
To remove the hot-swap power supply, complete the following steps:
Step 1. Locate the hot-swap power supply in the rear of your server and disconnect the power cord from
the power supply.
Step 2. Press the release tab in the direction as shown and carefully pull the handle at the same time to
slide the hot-swap power supply out of the chassis.
126 ThinkSystem ST250 Maintenance Manual
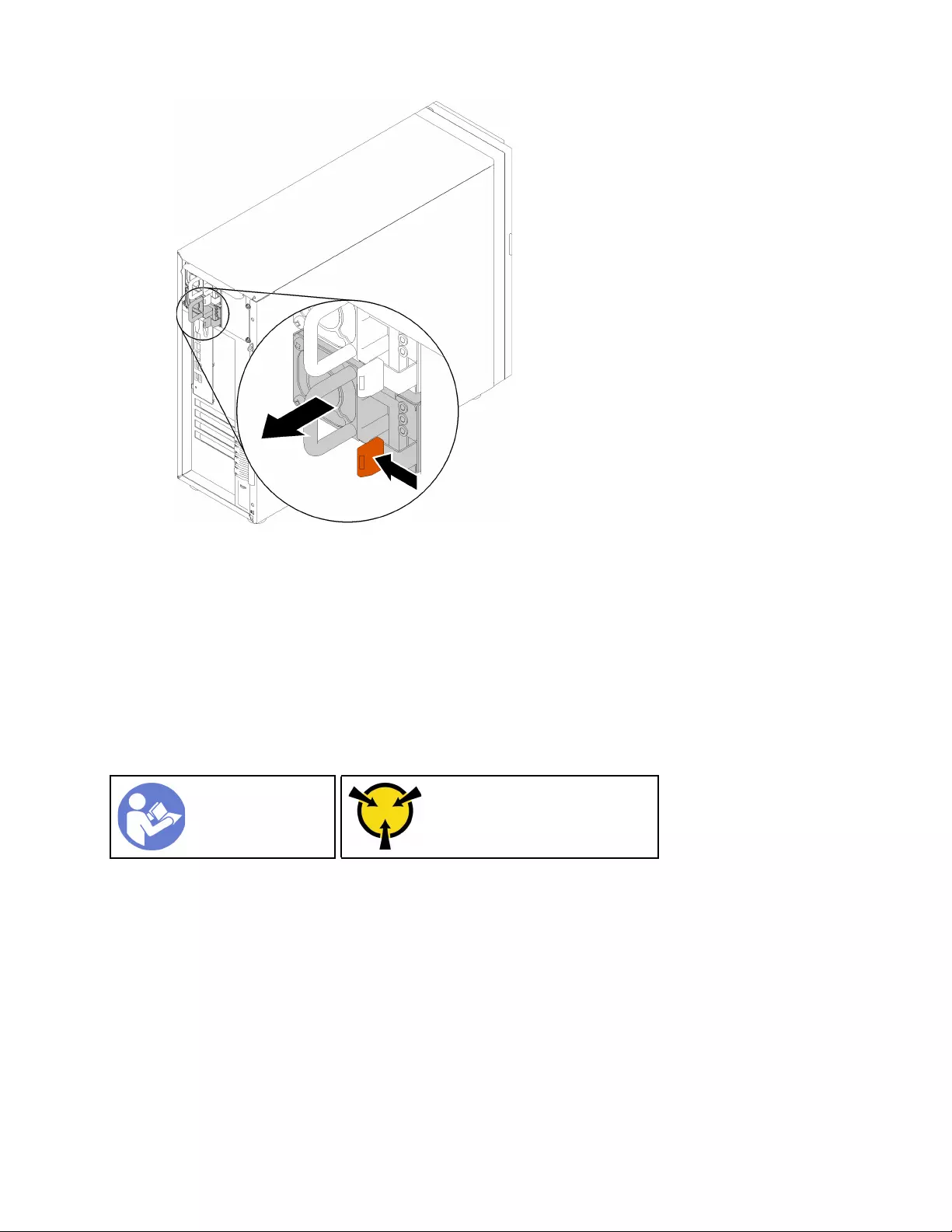
Figure 96. Hot-swap power supply removal
After removing the hot-swap power supply:
1. Install a new power supply or install the power-supply filler to cover the power supply bay. See “Install
the hot-swap power supply” on page 127.
2. If you are instructed to return the defective component, please package the part to prevent any shipping
damage. Reuse the packaging the new part arrived in and follow all packaging instructions.
Install the hot-swap power supply
Use this information to install the hot-swap power supply.
“Read the
installation
Guidelines” on
page 53
“ATTENTION:
Static Sensitive Device
Ground package before opening”
on page 55
The following tips describe the type of power supply that the server supports and other information that you
must consider when you install a power supply:
• The standard shipping has only one power supply installed in the server. For redundancy and hot-swap
support, you must install an additional hot-swap power supply. Certain customized models might be
shipped with two power supplies installed.
• Ensure that the devices that you are installing are supported. For a list of supported optional devices for
the server, go to:
https://static.lenovo.com/us/en/serverproven/index.shtml
Notes:
– Ensure that the two power supplies installed on the server have the same wattage.
Chapter 3.Hardware replacement procedures 127

– If you are replacing the existing power supply with a new power supply of different wattage, attach the
power information label that comes with this option onto the existing label near the power supply.
Figure 97. Hot-swap power supply label
S035
CAUTION:
Never remove the cover on a power supply or any part that has this label attached. Hazardous voltage,
current, and energy levels are present inside any component that has this label attached. There are no
serviceable parts inside these components. If you suspect a problem with one of these parts, contact
a service technician.
128 ThinkSystem ST250 Maintenance Manual
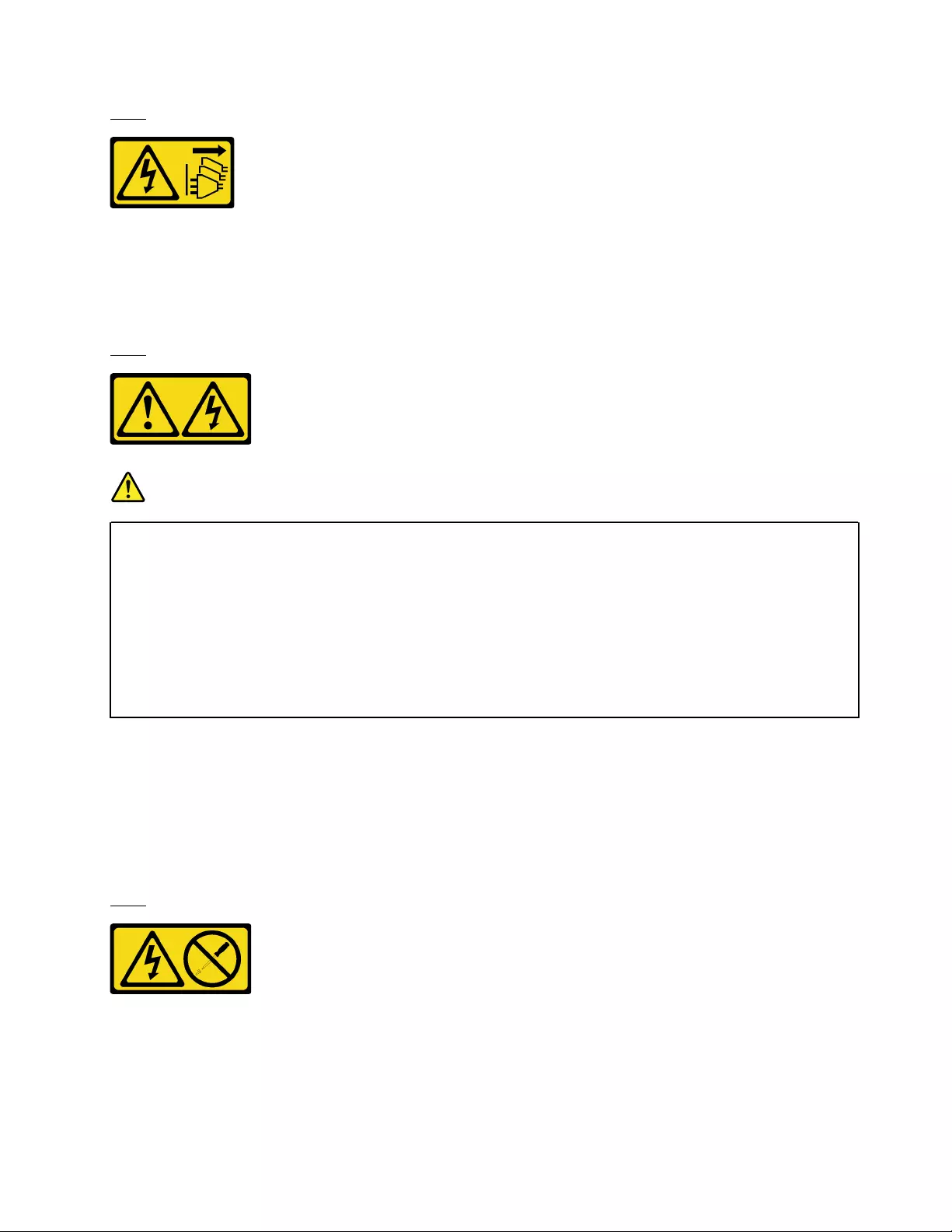
S002
CAUTION:
The power-control button on the device and the power switch on the power supply do not turn off the
electrical current supplied to the device. The device also might have more than one power cord. To
remove all electrical current from the device, ensure that all power cords are disconnected from the
power source.
S001
DANGER
Electrical current from power, telephone, and communication cables is hazardous.
To avoid a shock hazard:
• Connect all power cords to a properly wired and grounded electrical outlet/source.
• Connect any equipment that will be attached to this product to properly wired outlets/sources.
• When possible, use one hand only to connect or disconnect signal cables.
• Never turn on any equipment when there is evidence of fire, water, or structural damage.
• The device might have more than one power cord, to remove all electrical current from the
device, ensure that all power cords are disconnected from the power source.
The following tips describe the information that you must consider when you install a power supply with dc
input.
NEVER CONNECT AND DISCONNECT THE POWER SUPPLY CABLE AND EQUIPMENT WHILE YOUR
EQUIPMENT IS POWERED ON WITH DC SUPPLY (hot-plugging). Otherwise you may damage the
equipment and result in data loss, the damages and losses result from incorrect operation of the equipment
will not be covered by the manufacturers’ warranty.
S035
CAUTION:
Never remove the cover on a power supply or any part that has this label attached. Hazardous voltage,
current, and energy levels are present inside any component that has this label attached. There are no
serviceable parts inside these components. If you suspect a problem with one of these parts, contact
a service technician.
Chapter 3.Hardware replacement procedures 129

S019
CAUTION:
The power-control button on the device does not turn off the electrical current supplied to the device.
The device also might have more than one connection to dc power. To remove all electrical current
from the device, ensure that all connections to dc power are disconnected at the dc power input
terminals.
S029
DANGER
Electrical current from power, telephone, and communication cables is hazardous.
To avoid a shock hazard:
• Do not connect or disconnect any cables or perform installation, maintenance, or reconfiguration
of this product during an electrical storm.
• Connect all power cords to a properly wired and grounded power source.
• Connect to properly wired power sources any equipment that will be attached to this product.
• When possible, use one hand only to connect or disconnect signal cables.
• Never turn on any equipment when there is evidence of fire, water, or structural damage.
• Disconnect the attached ac power cords, dc power sources, network connections,
telecommunications systems, and serial cables before you open the device covers, unless you
are instructed otherwise in the installation and configuration procedures.
• Connect and disconnect cables as described in the following table when installing, moving, or
opening covers on this product or attached devices.
To Connect: To Disconnect:
1. Turn OFF all power sources and equipment that is to
be attached to this product.
2. Attach signal cables to the product.
3. Attach power cords to the product.
• For ac systems, use appliance inlets.
• For dc systems, ensure correct polarity of -48 V dc
connections: RTN is + and -48 V dc is -. Earth
ground should use a two-hole lug for safety.
4. Attach signal cables to other devices.
5. Connect power cords to their sources.
6. Turn ON all the power sources.
1. Turn OFF all power sources and equipment that is to
be attached to this product.
• For ac systems, remove all power cords from the
chassis power receptacles or interrupt power at
the ac power distribution unit.
• For dc systems, disconnect dc power sources at
the breaker panel or by turning off the power
source. Then, remove the dc cables.
2. Remove the signal cables from the connectors.
3. Remove all cables from the devices.
130 ThinkSystem ST250 Maintenance Manual

Before installing the hot -swap power supply,
1. Watch the procedure
A video of this procedure is available at YouTube: https://www.youtube.com/playlist?list=
PLYV5R7hVcs-Dy5N2dPXFx5Pht-FljAi6S.
2. Touch the static-protective package that contains the component to any unpainted metal surface on the
server; then, remove it from the package and place it on a static-protective surface.
To install the hot-swap power supply, complete the following steps:
Step 1. If there is a power-supply-bay filler installed, remove it.
Important: To ensure proper cooling during normal server operation, both of the power supply
bays must be occupied. This means that each bay must have a power supply installed; or one has
a power supply installed and the other has a power-supply filler installed.
Figure 98. Hot-swap power supply filler removal
Step 2. Note the orientation of the hot-swap power supply, and then slide it into the chassis until it snaps
into position.
Chapter 3.Hardware replacement procedures 131
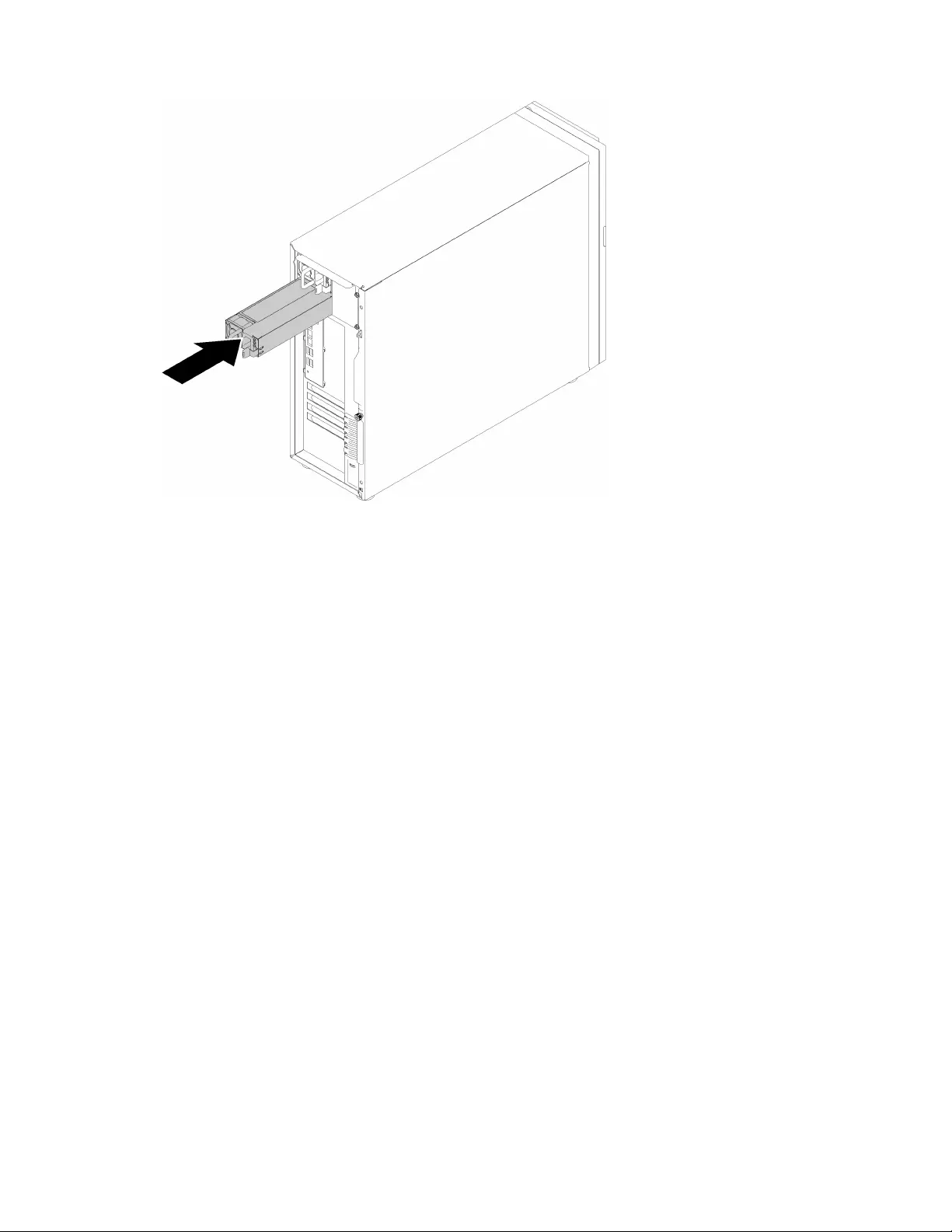
Figure 99. Hot-swap power supply installation
After installing the hot-swap power supply:
1. Connect the power cable to the power supply and a properly grounded electrical outlet.
2. If the server is powered off, power on the server. Ensure that both the power input LED and the power
output LED on the power supply are lit, indicating that the power supply is operating properly.
3. Complete the parts replacement. See “Complete the parts replacement” on page 155
132 ThinkSystem ST250 Maintenance Manual
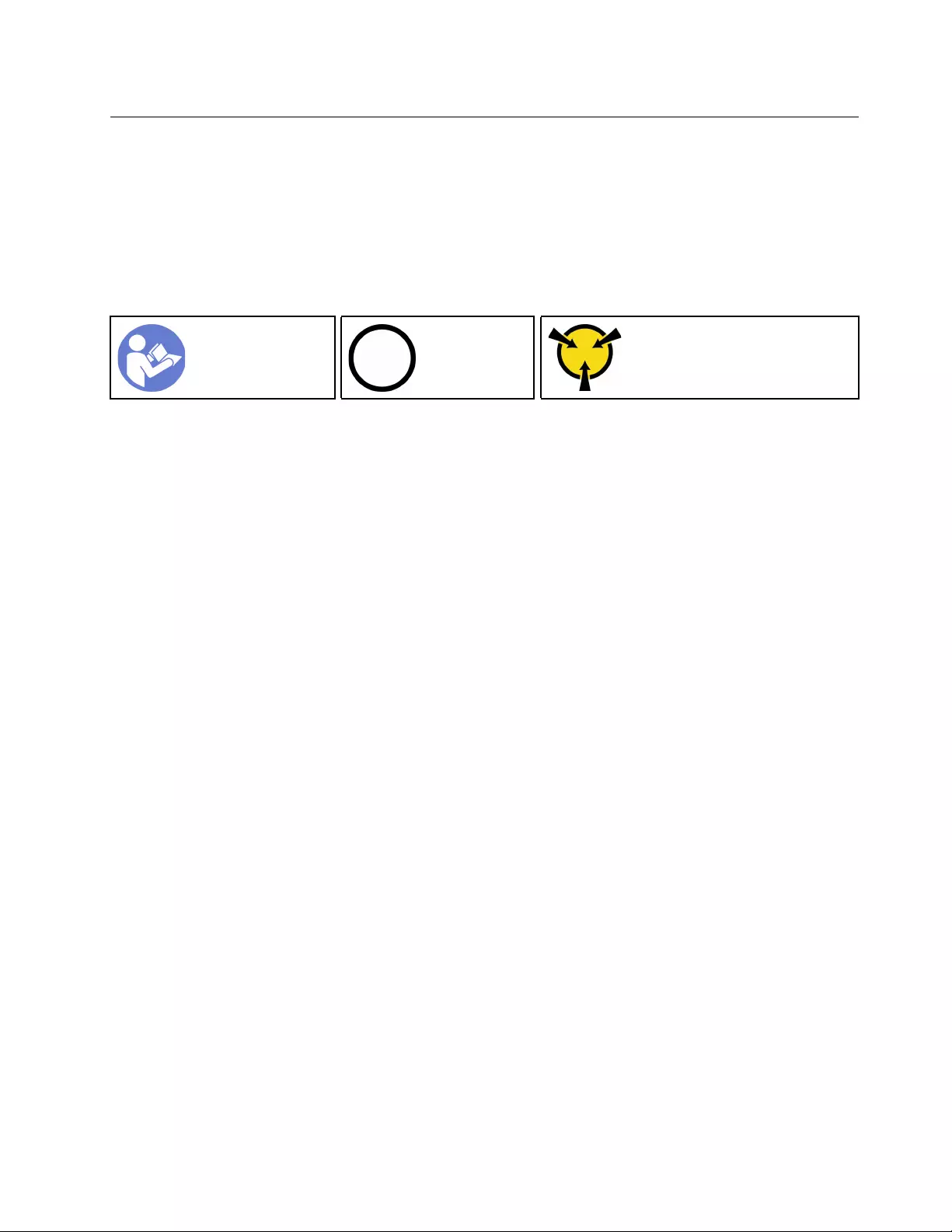
Processor replacement
Use this information to remove and install a processor.
Attention: Before you begin replacing a processor, make sure that you have an alcohol cleaning pad (part
number 00MP352) and gray thermal grease (part number 41Y9292).
Remove the processor
Use this information to remove the processor. This procedure must be executed by a trained technician.
“Read the
installation
Guidelines” on
page 53
“Power off
the server for
this task” on
page 14
“ATTENTION:
Static Sensitive Device
Ground package before opening”
on page 55
Before removing the processor:
1. Watch the procedure
A video of this procedure is available at YouTube: https://www.youtube.com/playlist?list=
PLYV5R7hVcs-Dy5N2dPXFx5Pht-FljAi6S.
2. If the server is in a rack, remove it from the rack.
3. Remove any locking device that secures the server cover, such as a Kensington lock or a pad lock.
4. Remove the server cover (see “Remove the server cover” on page 136).
5. Remove the heat sink and fan module if necessary (see “Remove the heat sink and fan module” on page
95)
To remove the processor, complete the following steps:
Step 1. Gently pull the handle away from the processor retainer.
Chapter 3.Hardware replacement procedures 133
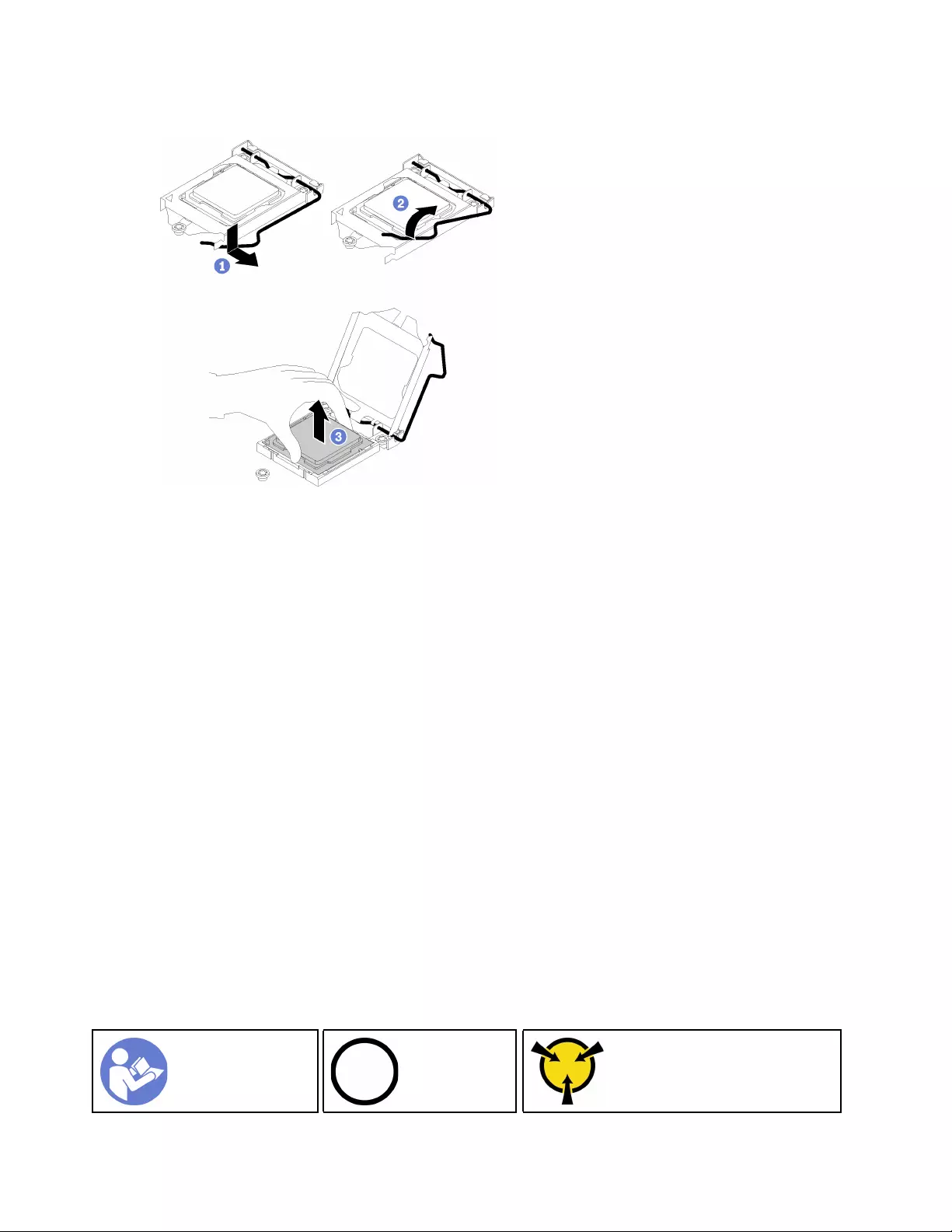
Step 2. Lift the handle along with the retainer to the fully open position.
Figure 100. Opening the processor retainer
Step 3. Hold the processor by both sides and gently lift it away from the processor socket.
Notes:
1. Do not touch the gold contacts on the bottom of the processor.
2. Keep the processor socket clean from any object to prevent possible damages.
After removing the processor, perform one of the following tasks immediately:
• Install the replacement processor.
1. Install the replacement processor to the system board (see “Install the processor ” on page 134).
2. Package the defective processor that was removed, and return it to Lenovo. To prevent any shipping
damage, reuse the packaging of the new processor, and follow all available packaging instructions.
or
• Install the processor that you removed to the replacement system board.
1. Install the removed processor to the replacement system board (see “Install the processor ” on page
134).
2. Package the defective system board, and return it to Lenovo. To prevent any shipping damage, reuse
the packaging of the new system board, and follow all available packaging instructions.
Install the processor
Use this information to install the processor. This procedure must be executed by a trained technician.
“Read the
installation
Guidelines” on
page 53
“Power off
the server for
this task” on
page 14
“ATTENTION:
Static Sensitive Device
Ground package before opening”
on page 55
134 ThinkSystem ST250 Maintenance Manual

Before installing the processor:
1. Watch the procedure
A video of this procedure is available at YouTube: https://www.youtube.com/playlist?list=
PLYV5R7hVcs-Dy5N2dPXFx5Pht-FljAi6S.
2. Before reusing a processor that was removed from another system board, wipe the thermal grease from
the processor with an alcohol cleaning pad, and dispose of the cleaning pad after all of the thermal
grease is removed.
Note: If you are applying new thermal grease on the top of the processor, make sure to do it after the
alcohol has fully evaporated.
3. Apply the thermal grease on the top of the processor with syringe by forming four uniformly spaced
dots, while each dot consists of about 0.1 ml of thermal grease.
Figure 101. Proper shape of the thermal grease
4. Touch the static-protective package that contains the component to any unpainted metal surface on the
server; then, remove it from the package and place it on a static-protective surface.
To install the processor, complete the following steps:
Step 1. Hold the processor by both sides, and align the following:
1. Align 1 the small notches on the processor to 2 the tabs on the socket.
2. Align 3 the small triangle of the processor to 4 the beveled corner on the socket.
Then, gently lower the processor evenly into the socket.
Chapter 3.Hardware replacement procedures 135
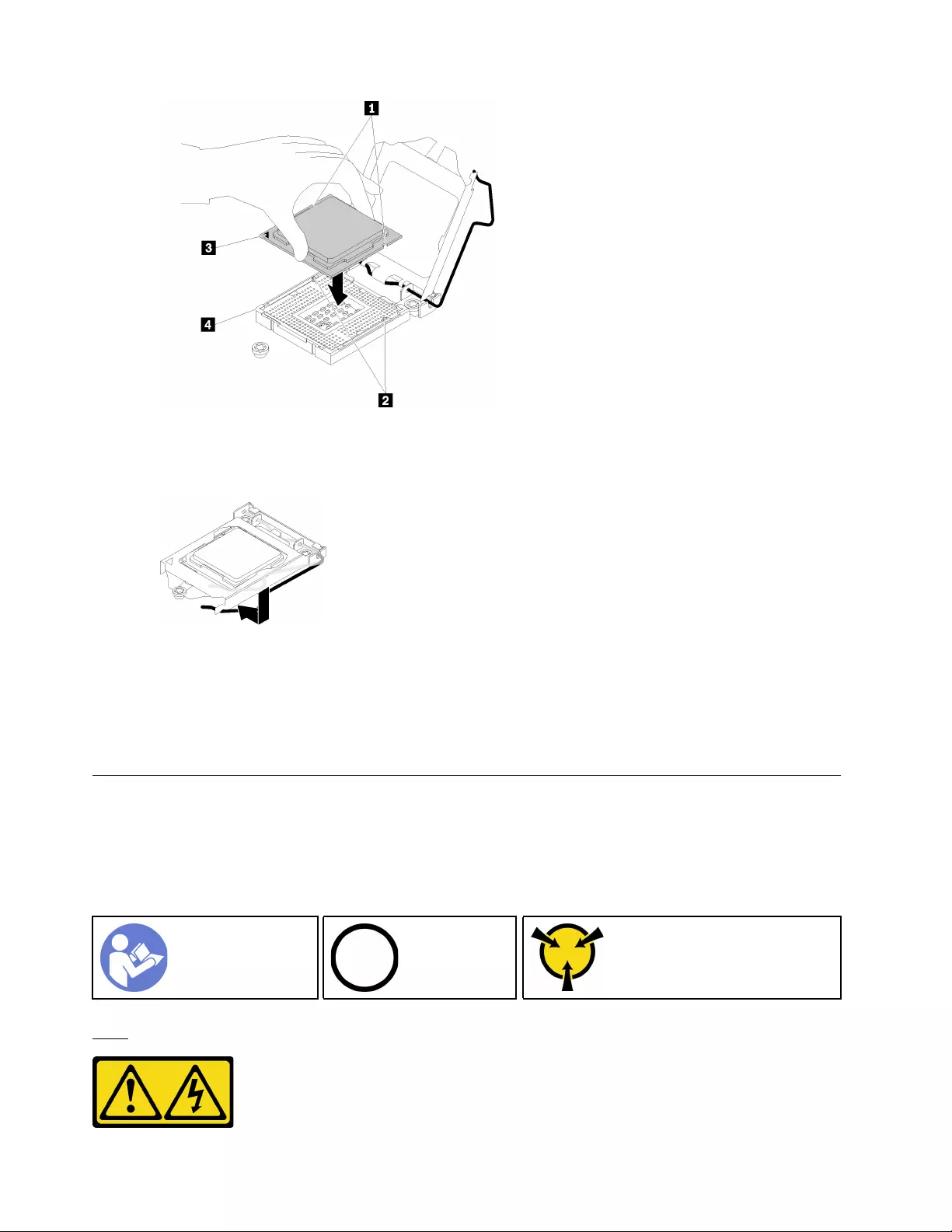
Figure 102. Installing the processor
Step 2. Close the processor retainer, and push the handle to the locked position.
Figure 103. Closing the processor retainer
After installing the processor:
1. Reinstall the heat sink and fan assembly (see “Install the heat sink and the fan module” on page 96).
2. Complete the parts replacement. See “Complete the parts replacement” on page 155
Server cover replacement
Use this information to remove and install the server cover.
Remove the server cover
Use this information to remove the server cover.
“Read the
installation
Guidelines” on
page 53
“Power off
the server for
this task” on
page 14
“ATTENTION:
Static Sensitive Device
Ground package before opening”
on page 55
S014
136 ThinkSystem ST250 Maintenance Manual

CAUTION:
Hazardous voltage, current, and energy levels might be present. Only a qualified service technician is
authorized to remove the covers where the label is attached.
S033
CAUTION:
Hazardous energy present. Voltages with hazardous energy might cause heating when shorted with
metal, which might result in spattered metal, burns, or both.
Before removing the server cover:
1. Watch the procedure
A video of this procedure is available at YouTube: https://www.youtube.com/playlist?list=
PLYV5R7hVcs-Dy5N2dPXFx5Pht-FljAi6S.
2. If the server is in a rack, remove it from the rack.
3. Remove any locking device that secures the server cover, such as a Kensington lock or a pad lock.
Complete the following steps to remove the server cover:
Step 1. Use a screwdriver to loosen the thumbscrew that secures the server cover. The thumbscrew is an
integrated part of the server cover. Do not try to remove the thumbscrew from the server cover
Step 2. Slide the server cover to the rear until it stops.
Step 3. Pivot the server cover outward to remove it.
Chapter 3.Hardware replacement procedures 137
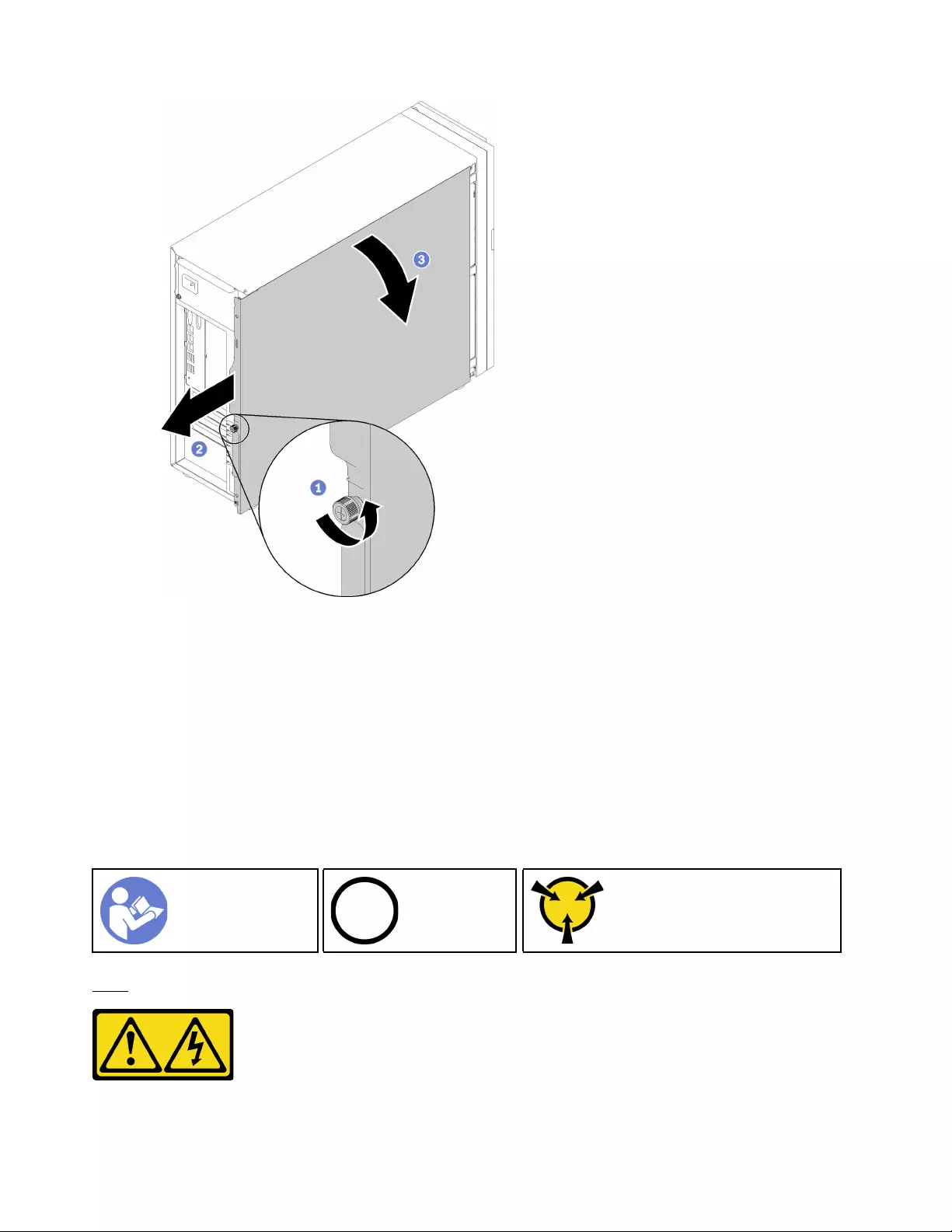
Figure 104. Server cover removal
Attention: For proper cooling, always install the server cover before powering on the server.
Operating the server without the cover properly installed might result in server component damage.
After removing the server cover:
If you are instructed to return the defective component, please package the part to prevent any shipping
damage. Reuse the packaging the new part arrived in and follow all packaging instructions.
Install the server cover
Use this information to install the server cover.
“Read the
installation
Guidelines” on
page 53
“Power off
the server for
this task” on
page 14
“ATTENTION:
Static Sensitive Device
Ground package before opening”
on page 55
S014
CAUTION:
138 ThinkSystem ST250 Maintenance Manual
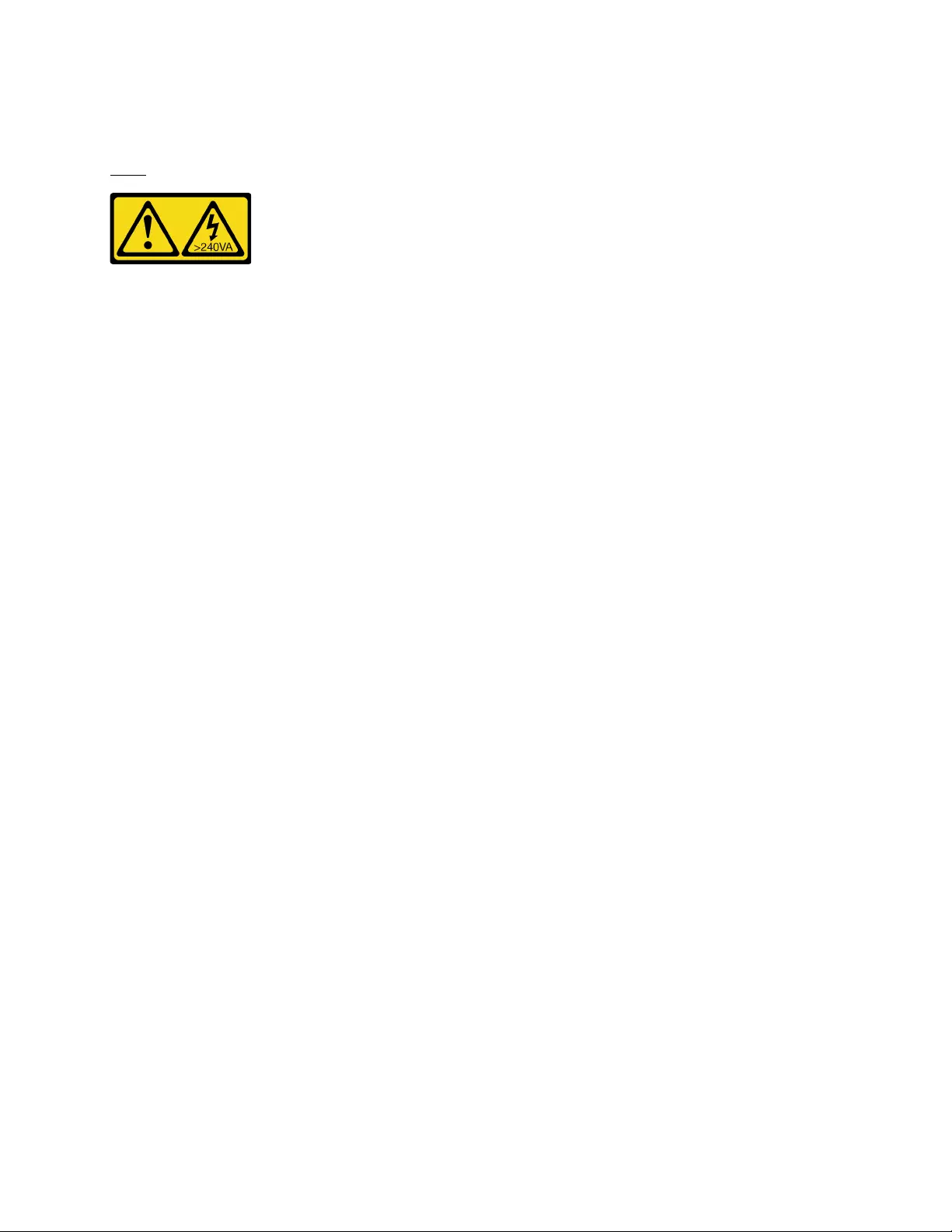
Hazardous voltage, current, and energy levels might be present. Only a qualified service technician is
authorized to remove the covers where the label is attached.
S033
CAUTION:
Hazardous energy present. Voltages with hazardous energy might cause heating when shorted with
metal, which might result in spattered metal, burns, or both.
Before installing the server cover:
1. Watch the procedure
A video of this procedure is available at YouTube: https://www.youtube.com/playlist?list=
PLYV5R7hVcs-Dy5N2dPXFx5Pht-FljAi6S.
2. Ensure that all adapters and other components are installed and seated correctly and that you have not
left loose tools or parts inside the server.
3. Ensure that all internal cables are correctly routed. See “Internal cable routing” on page 31.
4. If you are installing a new server cover, attach the service label to the inside of the new server cover first
if necessary.
Note: A new server cover comes without a service label attached. If you need a service label, order it
together with the new server cover. The service label is free of charge.
To install the server cover, complete the following steps:
Chapter 3.Hardware replacement procedures 139
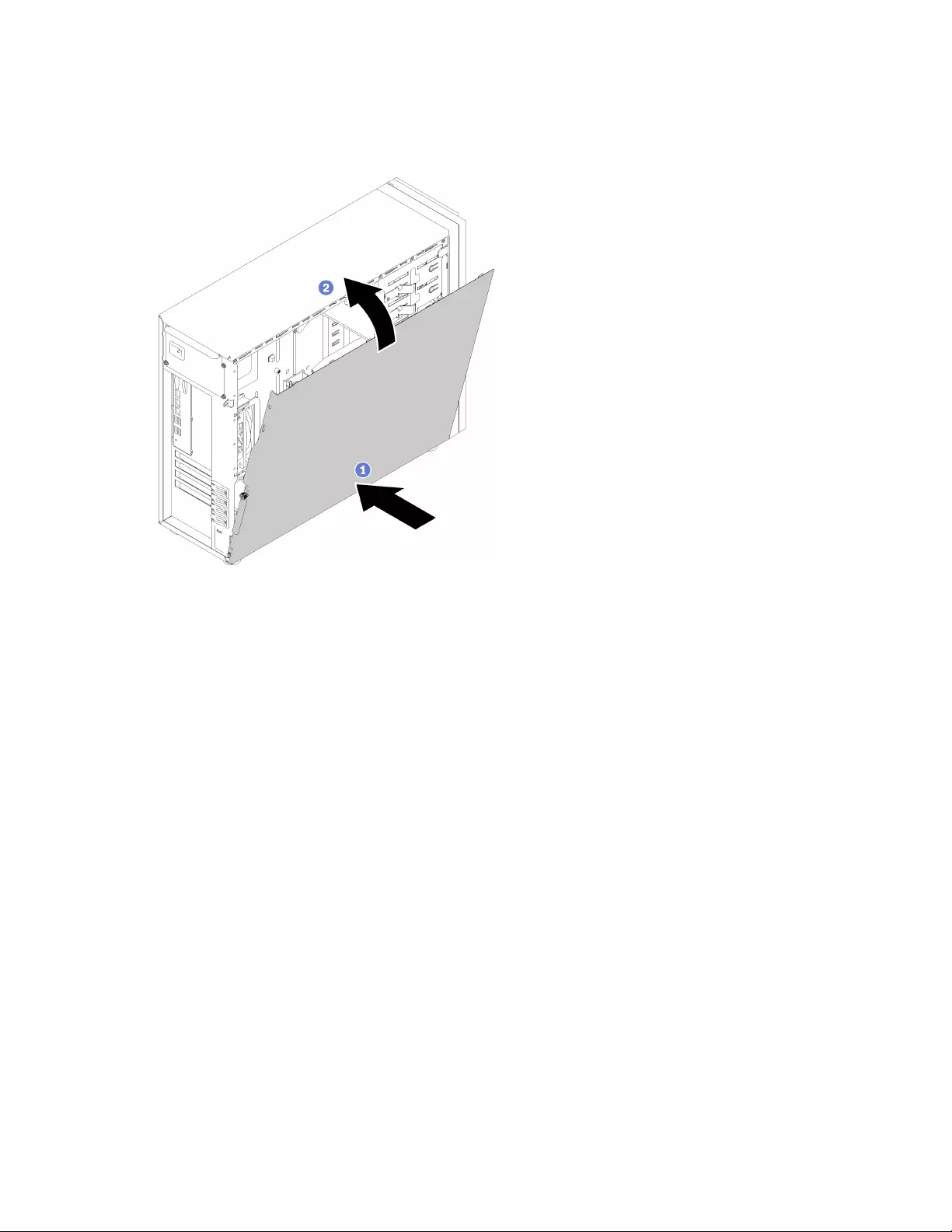
Step 1. Position the server cover on the chassis so that the rail on the bottom of the server cover engages
the bottom rail on the chassis. Align the tabs on the server cover with the corresponding holes in
the top edge of the chassis; then, pivot the server cover to close it.
Figure 105. Server cover installation (1)
Note: Before you slide the cover forward, ensure that all the tabs of the cover engage the chassis
correctly. If all the tabs do not engage the chassis correctly, it will be very difficult to remove the
cover later.
Step 2. Slide the server cover to the front of the chassis until it snaps into position.
140 ThinkSystem ST250 Maintenance Manual

Figure 106. Server cover installation (2)
Step 3. Use a screwdriver to tighten the thumbscrew on the server cover to secure the server cover in
place.
After installing the server cover
Complete the parts replacement. See “Complete the parts replacement” on page 155
System board replacement
Use this information to remove and install the system board.
Important: Before you return the system board, make sure that you install the CPU socket dust covers from
the new system board. To replace a CPU socket dust cover:
1. Take a dust cover from the CPU socket assembly on the new system board and orient it correctly above
the CPU socket assembly on the removed system board.
2. Gently press down the dust cover legs to the CPU socket assembly, pressing on the edges to avoid
damage to the socket pins. You might hear a click on the dust cover is securely attached.
3. Make sure that the dust cover is securely attached to the CPU socket assembly.
S017
Chapter 3.Hardware replacement procedures 141
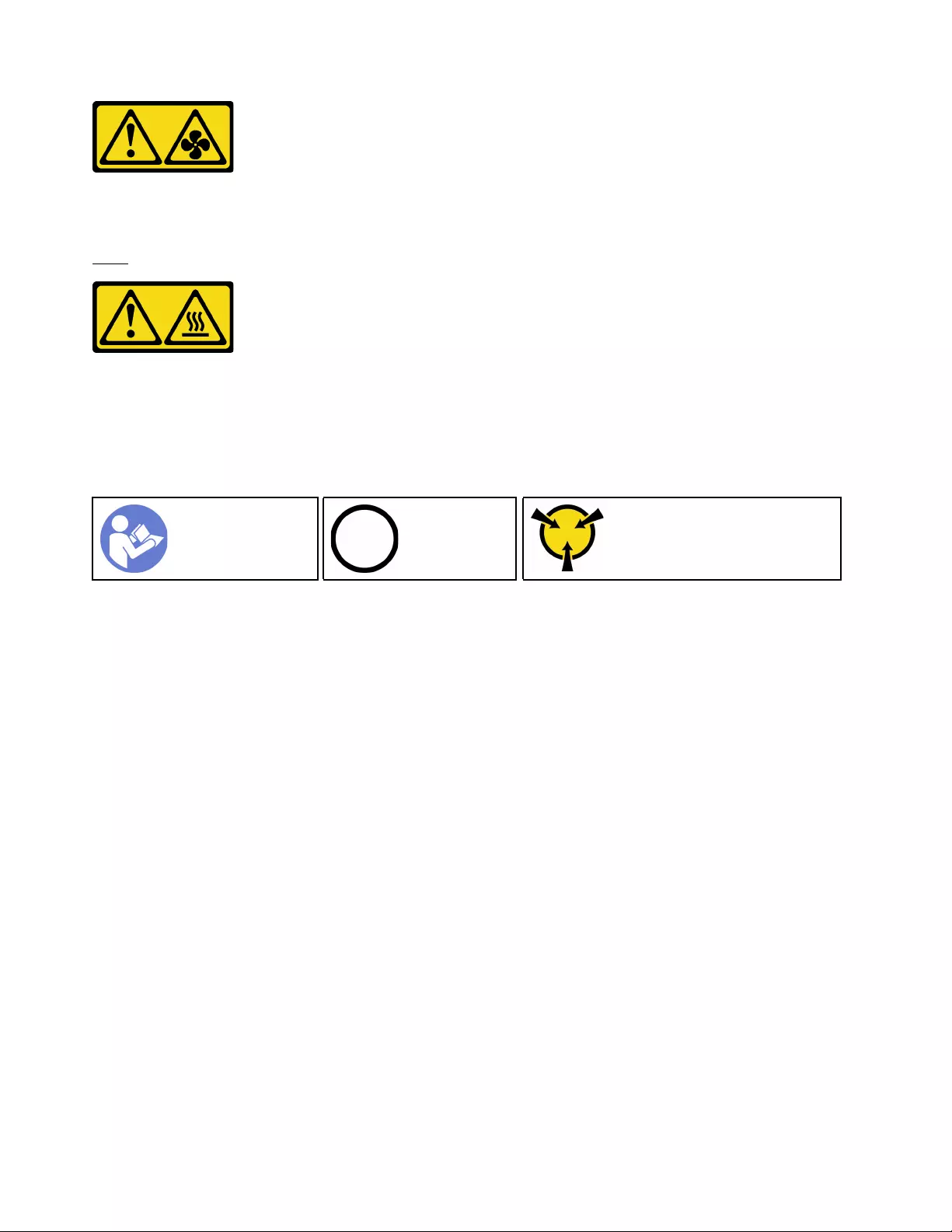
CAUTION:
Hazardous moving fan blades nearby. Keep fingers and other body parts away.
S012
CAUTION:
Hot surface nearby.
Remove the system board
Use this information to remove the system board.
“Read the
installation
Guidelines” on
page 53
“Power off
the server for
this task” on
page 14
“ATTENTION:
Static Sensitive Device
Ground package before opening”
on page 55
Before removing the system board:
1. Watch the procedure
A video of this procedure is available at YouTube: https://www.youtube.com/playlist?list=
PLYV5R7hVcs-Dy5N2dPXFx5Pht-FljAi6S.
2. If the server is in a rack, remove it from the rack.
3. Remove any locking device that secures the server cover, such as a Kensington lock or a pad lock.
4. Remove the server cover (see “Remove the server cover” on page 136).
5. Make note of where the cables are connected to the system board; then, disconnect all the cables.
Attention: Disengage all latches, cable clips, release tabs, or locks on cable connectors beforehand.
Failing to release them before removing the cables will damage the cable connectors on the system
board. Any damage to the cable connectors may require replacing the system board.
6. Remove any of the following components that are installed on the system board and put them in a safe,
static-protective place. See the related topics in Chapter 3 “Hardware replacement procedures” on page
53.
• Front and rear system fans
• PCIe adapters
• DIMMs
• Heat sink and fan assembly
• Processor
• CMOS battery
• M.2 backplane
• TPM card (for Chinese Mainland only)
142 ThinkSystem ST250 Maintenance Manual

To remove the system board, complete the following steps:
Step 1. Place the server on the side with the system board facing up.
Step 2. Remove the eight screws that secure the system board following the recommended numerical
sequence as shown; then , carefully remove the system board out of the chassis.
Figure 107. Screw removal that secures the system board
Step 3. Place the old system board on a clean, flat, and static-protective surface.
After removing the system board:
If you are instructed to return the defective component, please package the part to prevent any shipping
damage. Reuse the packaging the new part arrived in and follow all packaging instructions.
Important: Before you return the system board, make sure that you install the processor socket dust covers
from the new system board. To replace a processor socket dust cover:
1. Take a dust cover from the processor socket assembly on the new system board and orient it correctly
above the processor socket assembly on the removed system board.
2. Gently press down the dust cover legs to the processor socket assembly, pressing on the edges to
avoid damage to the socket pins. You might hear a click on the dust cover is securely attached.
3. Make sure that the dust cover is securely attached to the processor socket assembly.
Install the system board
Use this information to install the system board.
“Read the
installation
Guidelines” on
page 53
“Power off
the server for
this task” on
page 14
“ATTENTION:
Static Sensitive Device
Ground package before opening”
on page 55
Before installing the system board:
1. Watch the procedure
Chapter 3.Hardware replacement procedures 143

A video of this procedure is available at YouTube: https://www.youtube.com/playlist?list=
PLYV5R7hVcs-Dy5N2dPXFx5Pht-FljAi6S.
2. Touch the static-protective package that contains the component to any unpainted metal surface on the
server; then, remove it from the package and place it on a static-protective surface.
To install the system board, complete the following steps:
Step 1. Note the orientation of the new system board and carefully place it into the chassis. Ensure that the
serial port on the new system board is inserted into the corresponding hole in the chassis and the
eight screw holes in the new system board are aligned with the corresponding mounting studs on
the chassis.
Step 2. Tighten the eight screws to secure the system board in place.
Figure 108. System board installation (1)
Figure 109. System board installation (2)
144 ThinkSystem ST250 Maintenance Manual
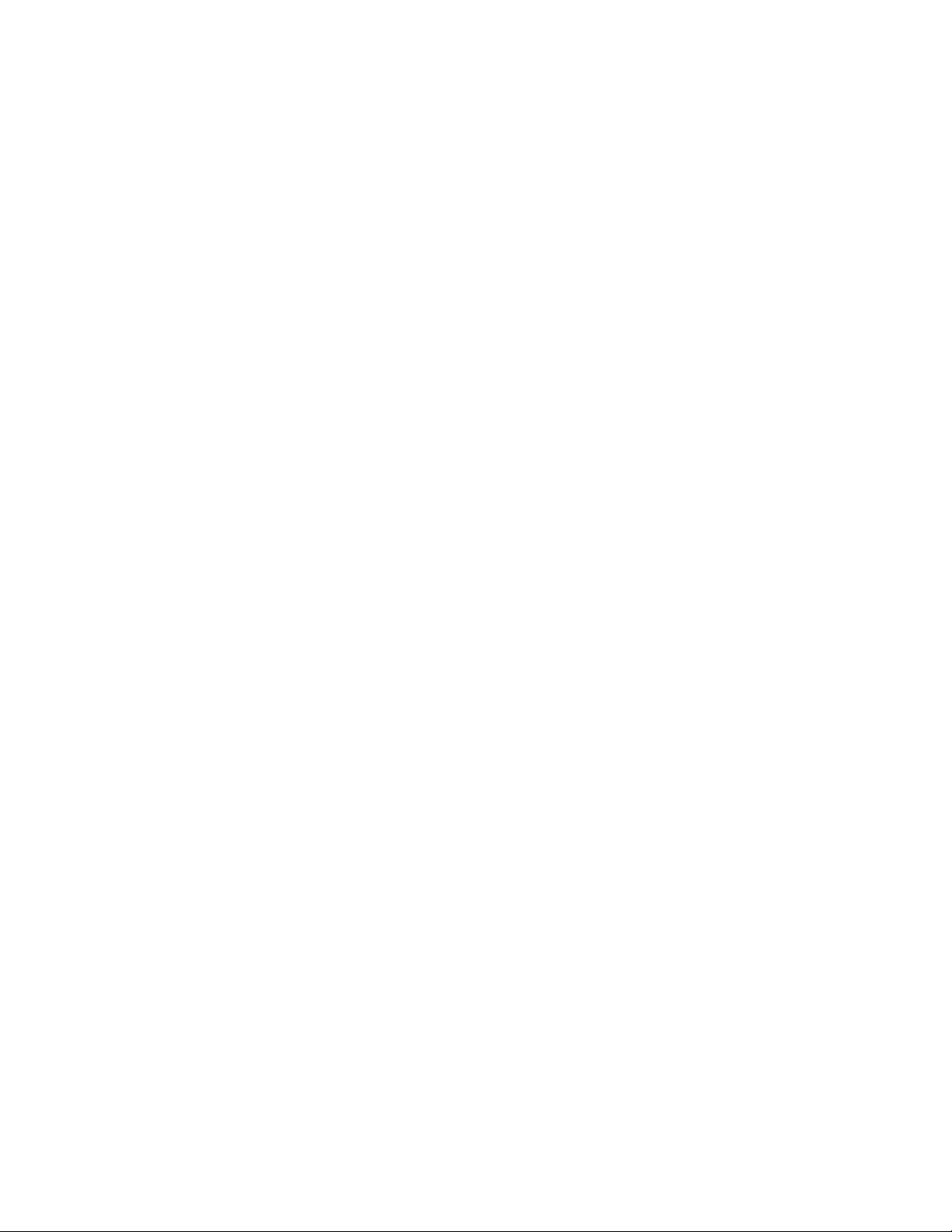
After installing the system board:
1. Install any components that you removed from the failing system board. See the related topics in
Chapter 3 “Hardware replacement procedures” on page 53.
2. Complete the parts replacement. See “Complete the parts replacement” on page 155
3. Update the machine type and serial number with new vital product data (VPD). Use the Lenovo XClarity
Provisioning Manager to update the machine type and serial number. See “Update the machine type
and serial number” on page 145.
4. Enable TPM/TCM. See “Enable TPM” on page 147
5. Optionally, enable Secure Boot. See “Enable UEFI Secure Boot” on page 150.
Update the machine type and serial number
After the system board is replaced by trained service technicians, the machine type and serial number must
be updated.
There are two methods available to update the machine type and serial number:
• From Lenovo XClarity Provisioning Manager
To update the machine type and serial number from Lenovo XClarity Provisioning Manager:
1. Start the server and press the key according to the on-screen instructions to display the Lenovo
XClarity Provisioning Manager interface.
2. If the power-on Administrator password is required, enter the password.
3. From the System Summary page, click Update VPD.
4. Update the machine type and serial number.
• From Lenovo XClarity Essentials OneCLI
Lenovo XClarity Essentials OneCLI sets the machine type and serial number in the Lenovo XClarity
Controller. Select one of the following methods to access the Lenovo XClarity Controller and set the
machine type and serial number:
– Operate from the target system, such as LAN or keyboard console style (KCS) access
– Remote access to the target system (TCP/IP based)
To update the machine type and serial number from Lenovo XClarity Essentials OneCLI:
1. Download and install Lenovo XClarity Essentials OneCLI.
To download Lenovo XClarity Essentials OneCLI, go to the following site:
https://datacentersupport.lenovo.com/solutions/HT116433
2. Copy and unpack the OneCLI package, which also includes other required files, to the server. Make
sure that you unpack the OneCLI and the required files to the same directory.
3. After you have Lenovo XClarity Essentials OneCLI in place, type the following commands to set the
machine type and serial number:
onecli config set SYSTEM_PROD_DATA.SysInfoProdName <m/t_model> [access_method]
onecli config set SYSTEM_PROD_DATA.SysInfoSerialNum <s/n> [access_method]
Where:
<m/t_model>
The server machine type and model number. Type mtm xxxxyyy, where xxxx is the machine type
and yyy is the server model number.
Chapter 3.Hardware replacement procedures 145

<s/n>
The serial number on the server. Type sn zzzzzzz, where zzzzzzz is the serial number.
[access_method]
The access method that you select to use from the following methods:
– Online authenticated LAN access, type the command:
[--bmc-username xcc_user_id --bmc-password xcc_password]
Where:
xcc_user_id
The BMC/IMM/XCC account name (1 of 12 accounts). The default value is USERID.
xcc_password
The BMC/IMM/XCC account password (1 of 12 accounts).
Example commands are as follows:
onecli config set SYSTEM_PROD_DATA.SysInfoProdName <m/t_model> --bmc-username xcc_user_id
--bmc-password xcc_password
onecli config set SYSTEM_PROD_DATA.SysInfoSerialNum <s/n> --bmc-username xcc_user_id
--bmc-password xcc_password
– Online KCS access (unauthenticated and user restricted):
You do not need to specify a value for access_method when you use this access method.
Example commands are as follows:
onecli config set SYSTEM_PROD_DATA.SysInfoProdName <m/t_model>
onecli config set SYSTEM_PROD_DATA.SysInfoSerialNum <s/n>
Note: The KCS access method uses the IPMI/KCS interface, which requires that the IPMI
driver be installed.
– Remote LAN access, type the command:
[−−bmc xcc_user_id:xcc_password@xcc_external_ip]
Where:
xcc_external_ip
The BMC/IMM/XCC IP address. There is no default value. This parameter is required.
xcc_user_id
The BMC/IMM/XCC account (1 of 12 accounts). The default value is USERID.
xcc_password
The BMC/IMM/XCC account password (1 of 12 accounts).
Note: BMC, IMM, or XCC internal LAN/USB IP address, account name, and password are all
valid for this command.
Example commands are as follows:
onecli config set SYSTEM_PROD_DATA.SysInfoProdName <m/t_model>
−−bmc xcc_user_id:xcc_password@xcc_external_ip
onecli config set SYSTEM_PROD_DATA.SysInfoSerialNum <s/n>
−−bmc xcc_user_id:xcc_password@xcc_external_ip
146 ThinkSystem ST250 Maintenance Manual

4. Reset the Lenovo XClarity Controller to the factory defaults. See “Resetting the BMC to Factory
Default” section in the XCC documentation compatible with your server at https://
sysmgt.lenovofiles.com/help/topic/lxcc_frontend/lxcc_overview.html.
Enable TPM
The server supports Trusted Platform Module (TPM), Version 1.2 or Version 2.0.
Note: For customers in Chinese Mainland, TPM is not supported. However, customers in Chinese Mainland
can install a TPM card (sometimes called a daughter card).
When a system board is replaced, you must make sure that the TPM policy is set correctly.
CAUTION:
Take special care when setting the TPM policy. If it is not set correctly, the system board can become
unusable.
Set the TPM policy
By default, a replacement system board is shipped with the TPM policy set to undefined. You must modify
this setting to match the setting that was in place for the system board that is being replaced.
There are two methods available to set the TPM policy:
• From Lenovo XClarity Provisioning Manager
To set the TPM policy from Lenovo XClarity Provisioning Manager:
1. Start the server and press the key according to the on-screen instructions to display the Lenovo
XClarity Provisioning Manager interface.
2. If the power-on Administrator password is required, enter the password.
3. From the System Summary page, click Update VPD.
4. Set the policy to one of the following settings.
– TPM 2.0 enabled - Chinese Mainland only. Customers in the Chinese Mainland should choose
this setting if a NationZ TPM 2.0 adapter is installed.
– TPM enabled - ROW. Customers outside of the Chinese Mainland should choose this setting.
– Permanently disabled. Customers in the Chinese Mainland should use this setting if no TPM
adapter is installed.
Note: Although the setting undefined is available as a policy setting, it should not be used.
• From Lenovo XClarity Essentials OneCLI
Note: Please note that a Local IPMI user and password must be setup in Lenovo XClarity Controller for
remote accessing to the target system.
To set the TPM policy from Lenovo XClarity Essentials OneCLI:
1. Read TpmTcmPolicyLock to check whether the TPM_TCM_POLICY has been locked:OneCli.exe config
show imm.TpmTcmPolicyLock --override --imm <userid>:<password>@<ip_address>
OneCli.exe config show imm.TpmTcmPolicyLock --override --imm <userid>:<password>@<ip_address>
Note: The imm.TpmTcmPolicyLock value must be 'Disabled', which means TPM_TCM_POLICY is
NOT locked and changes to the TPM_TCM_POLICY are permitted. If the return code is ‘Enabled’
then no changes to the policy are permitted. The planar may still be used if the desired setting is
correct for the system being replaced.
2. Configure the TPM_TCM_POLICY into XCC:
Chapter 3.Hardware replacement procedures 147

– For the customer in Chinese Mainland with no TCM/TPM:
OneCli.exe config set imm.TpmTcmPolicy "NeitherTpmNorTcm" --override --imm <userid>:<password>@<ip_
address>
– For the customer in Chinese Mainland that has installed TCM/TPM module on the original system
(TCM/TPM module should be moved to the FRU prior to changing policy)
OneCli.exe config set imm.TpmTcmPolicy "TcmOnly" --override --imm <userid>:<password>@<ip_address>
– For the customer outside of Chinese Mainland:
OneCli.exe config set imm.TpmTcmPolicy "TpmOnly" --override --imm <userid>:<password>@<ip_address>
3. Issue reset command to reset system:
OneCli.exe misc ospower reboot --imm <userid>:<password>@<ip_address>
4. Read back the value to check whether the change has been accepted:
OneCli.exe config show imm.TpmTcmPolicy --override --imm <userid>:<password>@<ip_address>
Notes:
– If the read back value is matched it means the TPM_TCM_POLICY has been set correctly.
imm.TpmTcmPolicy is defined as below:
– Value 0 use string “Undefined” , which means UNDEFINED policy.
– Value 1 use string “NeitherTpmNorTcm”, which means TPM_PERM_DISABLED.
– Value 2 use string “TpmOnly”, which means TPM_ALLOWED.
– Value 4 use string “TcmOnly”, which means TCM_ALLOWED.
– Below 4 steps must also be used to ‘lock’ the TPM_TCM_POLICY when using OneCli/ASU
commands:
5. Read TpmTcmPolicyLock to check whether the TPM_TCM_POLICY has been locked , command as
below:
OneCli.exe config show imm.TpmTcmPolicyLock --override --imm <userid>:<password>@<ip_address>
The value must be 'Disabled', it means TPM_TCM_POLICY is NOT locked and must be set.
6. Lock the TPM_TCM_POLICY:
OneCli.exe config set imm.TpmTcmPolicyLock "Enabled"--override --imm <userid>:<password>@<ip_address>
7. Issue reset command to reset system, command as below:
OneCli.exe misc ospower reboot --imm <userid>:<password>@<ip_address>
During the reset, UEFI will read the value from imm.TpmTcmPolicyLock, if the value is 'Enabled' and
the imm.TpmTcmPolicy value is valid, UEFI will lock the TPM_TCM_POLICY setting.
Note: The valid value for imm.TpmTcmPolicy includes 'NeitherTpmNorTcm', 'TpmOnly' and
'TpmOnly'.
If the imm.TpmTcmPolicy is set as 'Enabled' but imm.TpmTcmPolicy value is invalid, UEFI will reject
the 'lock' request and change imm.TpmTcmPolicy back to 'Disabled'.
8. Read back the value to check whether the ‘Lock’ is accepted or rejected. command as below:
OneCli.exe config show imm.TpmTcmPolicy --override --imm <userid>:<password>@<ip_address>
Note: If the read back value is changed from 'Disabled' to 'Enabled' that means the TPM_TCM_
POLICY has been locked successfully. There is no method to unlock a policy once it has been set
other than replacing system board.
148 ThinkSystem ST250 Maintenance Manual

imm.TpmTcmPolicyLock is defined as below:
Value 1 use string “Enabled" , which means lock the policy. Other values are not accepted.
Procedure also requires that Physical Presence is enabled. The Default value for FRU will be
enabled.PhysicalPresencePolicyConfiguration.PhysicalPresencePolicy=Enable
Assert Physical Presence
Before you can assert Physical Presence, the Physical Presence Policy must be enabled. By default, the
Physical Presence Policy is enabled with a timeout of 30 minutes.
There are two ways to assert the Physical Presence:
1. If the Physical Presence Policy is enabled, you can assert Physical Presence through the Lenovo
XClarity Provisioning Manager or through the Lenovo XClarity Controller.
2. Switch the hardware jumpers on the system board.
Notes: If the Physical Presence Policy has been disabled:
1. Set the hardware Physical Presence jumper on the system board to assert Physical Presence.
2. Enable the Physical Presence Policy using either F1 (UEFI Settings) or Lenovo XClarity Essentials
OneCLI.
Assert Physical Presence through the Lenovo XClarity Controller
Complete the following steps to assert Physical Presence through the Lenovo XClarity Controller:
1. Log in to the Lenovo XClarity Controller interface.
For information about logging in to the Lenovo XClarity Controller, see the “Opening and Using the
XClarity Controller Web Interface” section in the XCC documentation version compatible with your
server at https://sysmgt.lenovofiles.com/help/topic/lxcc_frontend/lxcc_overview.html.
2. Click BMC Configuration ➙ Security and verify that Physical Presence is set to assert.
Assert Physical Presence through the hardware
You can also assert hardware Physical Presence through the use of a jumper on the system board. For more
information about asserting hardware Physical Presence through the use of a jumper, see:
“System board jumpers” on page 30.
Set the TPM version
To be able to set the TPM version, Physical Presence must be asserted.
The Lenovo XClarity Provisioning Manager or the Lenovo XClarity Essentials OneCLI can be used to set the
TPM version.
To set the TPM version:
1. Download and install Lenovo XClarity Essentials OneCLI.
a. Go to http://datacentersupport.lenovo.com and navigate to the support page for your server.
b. Click Drivers & Software.
c. Navigate to the version of Lenovo XClarity Essentials OneCLI for your operating system and
download the package.
2. Run the following command to set the TPM version:
Chapter 3.Hardware replacement procedures 149
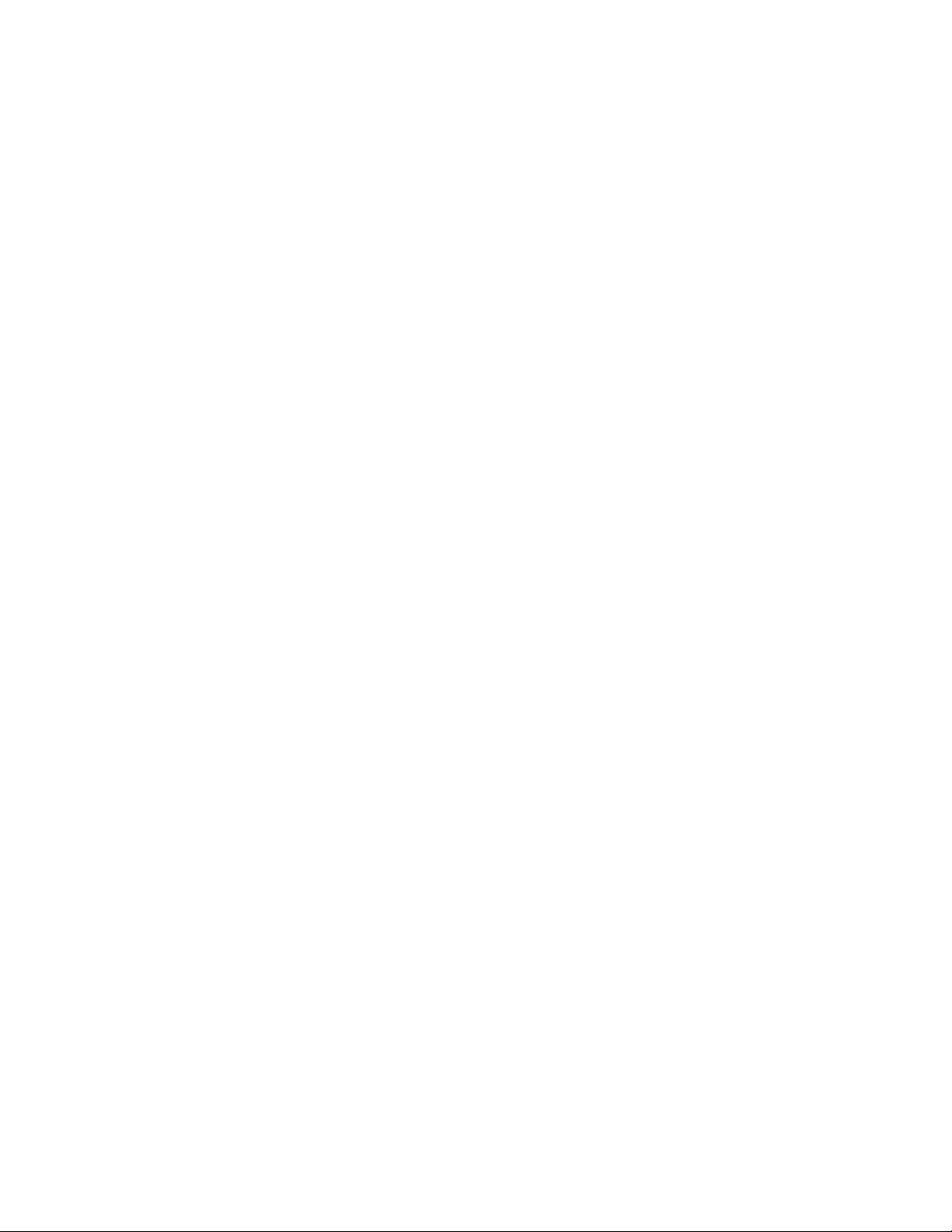
Note: You can change the TPM version from 1.2 to 2.0 and back again. However, you can toggle
between versions a maximum of 128 times.
To set the TPM version to version 2.0:OneCli.exe config set TrustedComputingGroup.DeviceOperation "Update
to TPM2.0 compliant" -–bmc userid:password@ip_address
To set the TPM version to version 1.2:OneCli.exe config set TrustedComputingGroup.DeviceOperation "Update
to TPM1.2 compliant" -–bmc userid:password@ip_address
where:
• <userid>:<password> are the credentials used to access the BMC (Lenovo XClarity Controller
interface) of your server. The default user ID is USERID, and the default password is PASSW0RD
(zero, not an uppercase o)
• <ip_address> is the IP address of the BMC.
For more information about the Lenovo XClarity Essentials OneCLI set command, see:
http://sysmgt.lenovofiles.com/help/topic/toolsctr_cli_lenovo/onecli_r_set_command.html
3. Alternatively, you can use the following Advanced Settings Utility (ASU) commands:
To set the TPM version to version 2.0:asu64 set TPMVersion.TPMVersion "Update to TPM2.0 compliant" --host
<ip_address> --user <userid> --password <password> --override
To set the TPM version to version 1.2:asu64 set TPMVersion.TPMVersion "Update to TPM1.2 compliant" --host
<ip_address> --user <userid> --password <password> --override
where:
• <userid> and <password> are the credentials used to the BMC (Lenovo XClarity Controller interface)
of your server. The default user ID is USERID, and the default password is PASSW0RD (zero, not an
uppercase o)
• <ip_address> is the IP address of the BMC.
Enable UEFI Secure Boot
Optionally, you can enable UEFI Secure Boot.
There are two methods available to enable UEFI Secure Boot:
• From Lenovo XClarity Provisioning Manager
To enable UEFI Secure Boot from Lenovo XClarity Provisioning Manager:
1. Start the server and press the key specified in the on-screen instructions to display the Lenovo
XClarity Provisioning Manager interface. (For more information, see the “Startup” section in the LXPM
documentation compatible with your server at https://sysmgt.lenovofiles.com/help/topic/lxpm_frontend/
lxpm_product_page.html.)
2. If the power-on Administrator password is required, enter the password.
3. From the UEFI Setup page, click System Settings ➙ Security ➙ Secure Boot.
4. Enable Secure Boot and save the settings.
• From Lenovo XClarity Essentials OneCLI
To enable UEFI Secure Boot from Lenovo XClarity Essentials OneCLI:
1. Download and install Lenovo XClarity Essentials OneCLI.
To download Lenovo XClarity Essentials OneCLI, go to the following site:
https://datacentersupport.lenovo.com/solutions/HT116433
150 ThinkSystem ST250 Maintenance Manual

2. Run the following command to enable Secure Boot:
OneCli.exe config set SecureBootConfiguration.SecureBootSetting Enabled
--bmc <userid>:<password>@<ip_address>
where:
– <userid>:<password> are the credentials used to access the BMC (Lenovo XClarity Controller
interface) of your server. The default user ID is USERID, and the default password is PASSW0RD
(zero, not an uppercase o)
– <ip_address> is the IP address of the BMC.
For more information about the Lenovo XClarity Essentials OneCLI set command, see:
http://sysmgt.lenovofiles.com/help/topic/toolsctr_cli_lenovo/onecli_r_set_command.html
Tape drive replacement
Use this information to remove and install the tape drive.
Your server supports RDX and LTO tape drives.
Remove a tape drive
Use this information to remove a tape drive.
“Read the
installation
Guidelines” on
page 53
“Power off
the server for
this task” on
page 14
“ATTENTION:
Static Sensitive Device
Ground package before opening”
on page 55
Before removing a tape drive:
1. Watch the procedure
A video of this procedure is available at YouTube: https://www.youtube.com/playlist?list=
PLYV5R7hVcs-Dy5N2dPXFx5Pht-FljAi6S.
2. If the server is in a rack, remove it from the rack.
3. Remove any locking device that secures the server cover, such as a Kensington lock or a pad lock.
4. Use the front door key to unlock the front door (available on some models), and then open the front
door.
5. Remove the server cover (see “Remove the server cover” on page 136).
To remove a tape drive, complete the following steps:
Step 1. Disconnect the cables from the rear of the tape drive.
Chapter 3.Hardware replacement procedures 151
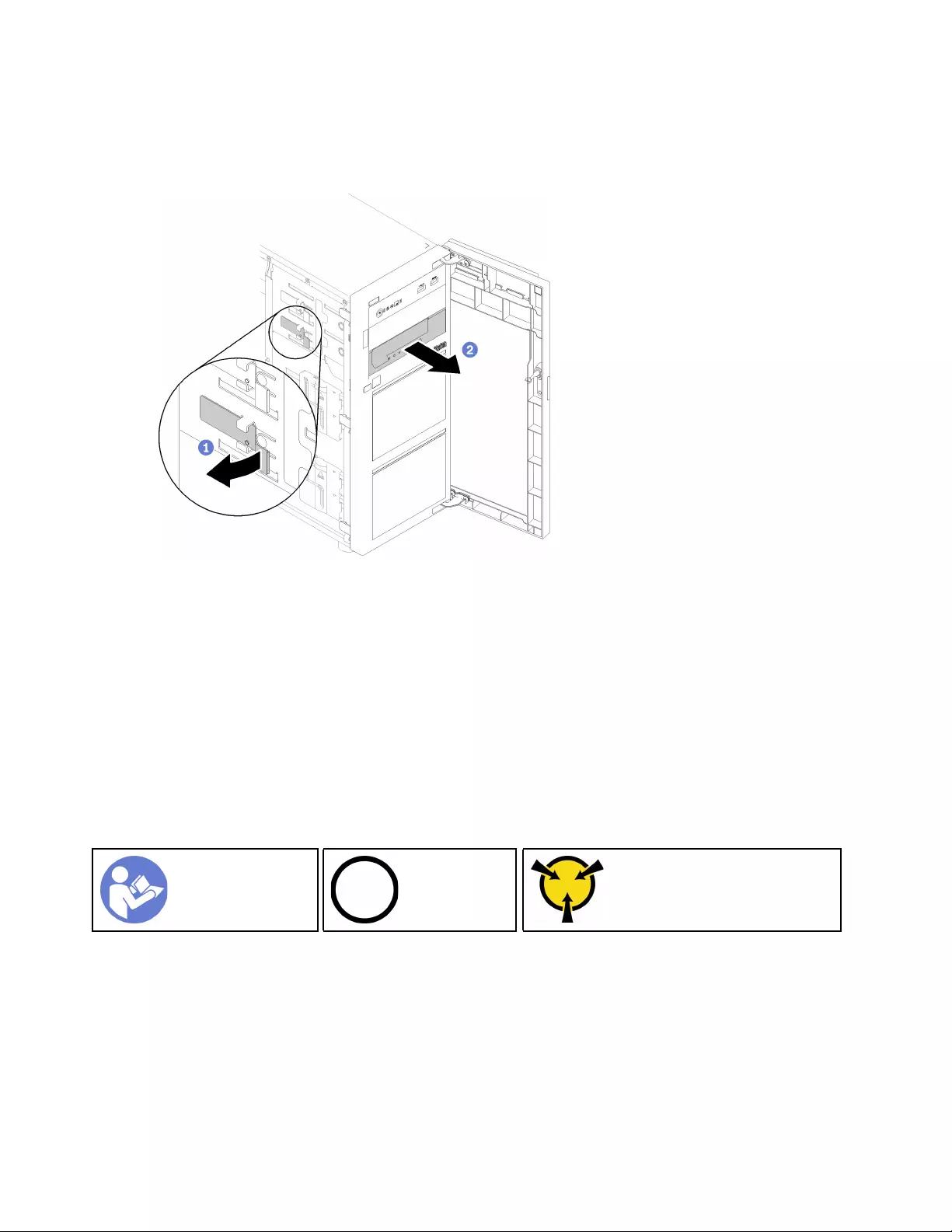
Step 2. Gently pull the metal tab on the side of the chassis and push the tape drive outward from the rear;
then, draw the tape drive out of the chassis.
Figure 110. Tape drive removal
After removing the tape drive:
1. Install one of the following:
• Another tape drive or optical drive.
See “Install a tape drive” on page 152 or “Install an optical drive” on page 104.
• A drive filler in the vacant drive bay.
2. If you are instructed to return the defective component, please package the part to prevent any shipping
damage. Reuse the packaging the new part arrived in and follow all packaging instructions.
Install a tape drive
Use this information to install a tape drive.
“Read the
installation
Guidelines” on
page 53
“Power off
the server for
this task” on
page 14
“ATTENTION:
Static Sensitive Device
Ground package before opening”
on page 55
Before installing a tape drive:
1. Watch the procedure
A video of this procedure is available at YouTube: https://www.youtube.com/playlist?list=
PLYV5R7hVcs-Dy5N2dPXFx5Pht-FljAi6S.
2. Touch the static-protective package that contains the component to any unpainted metal surface on the
server; then, remove it from the package and place it on a static-protective surface.
To install a tape drive, complete the following steps:
152 ThinkSystem ST250 Maintenance Manual
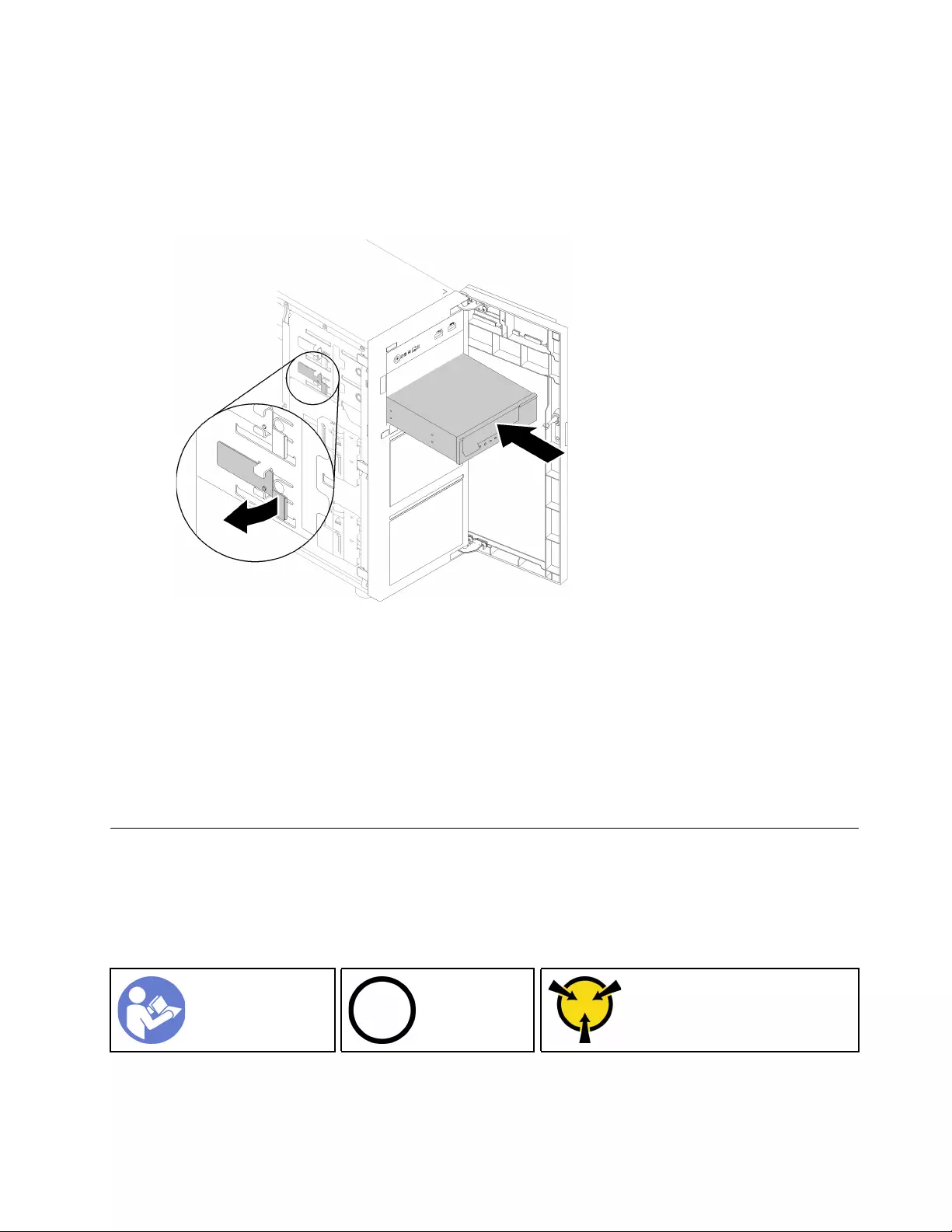
Step 1. The tape drive must be installed into the lower optical drive bay. If the drive bay is covered by a
filler, remove it first. Store the filler in case that you later remove the tape drive and need the filler to
cover the place.
Step 2. Insert the tape drive into the lower drive bay and slide it in until it is obstructed. Gently pull the
metal tab on the side of the chassis, and then continue to slide the tape drive in until it snaps into
position.
Figure 111. Tape drive installation
Step 3. Connect the power and signal cables to the rear of the tape drive. See “Tape drive” on page 35.
Note: For the LTO tape drive, connect one end of the signal cable to the LTO tape drive; then,
connect the other end of the signal cable to the RAID adapter.
After installing the tape drive:
Complete the parts replacement. See “Complete the parts replacement” on page 155
TPM card replacement
Use this information to remove and install the TPM card.
Remove the TPM card
Use this information to remove the TPM card.
“Read the
installation
Guidelines” on
page 53
“Power off
the server for
this task” on
page 14
“ATTENTION:
Static Sensitive Device
Ground package before opening”
on page 55
Chapter 3.Hardware replacement procedures 153
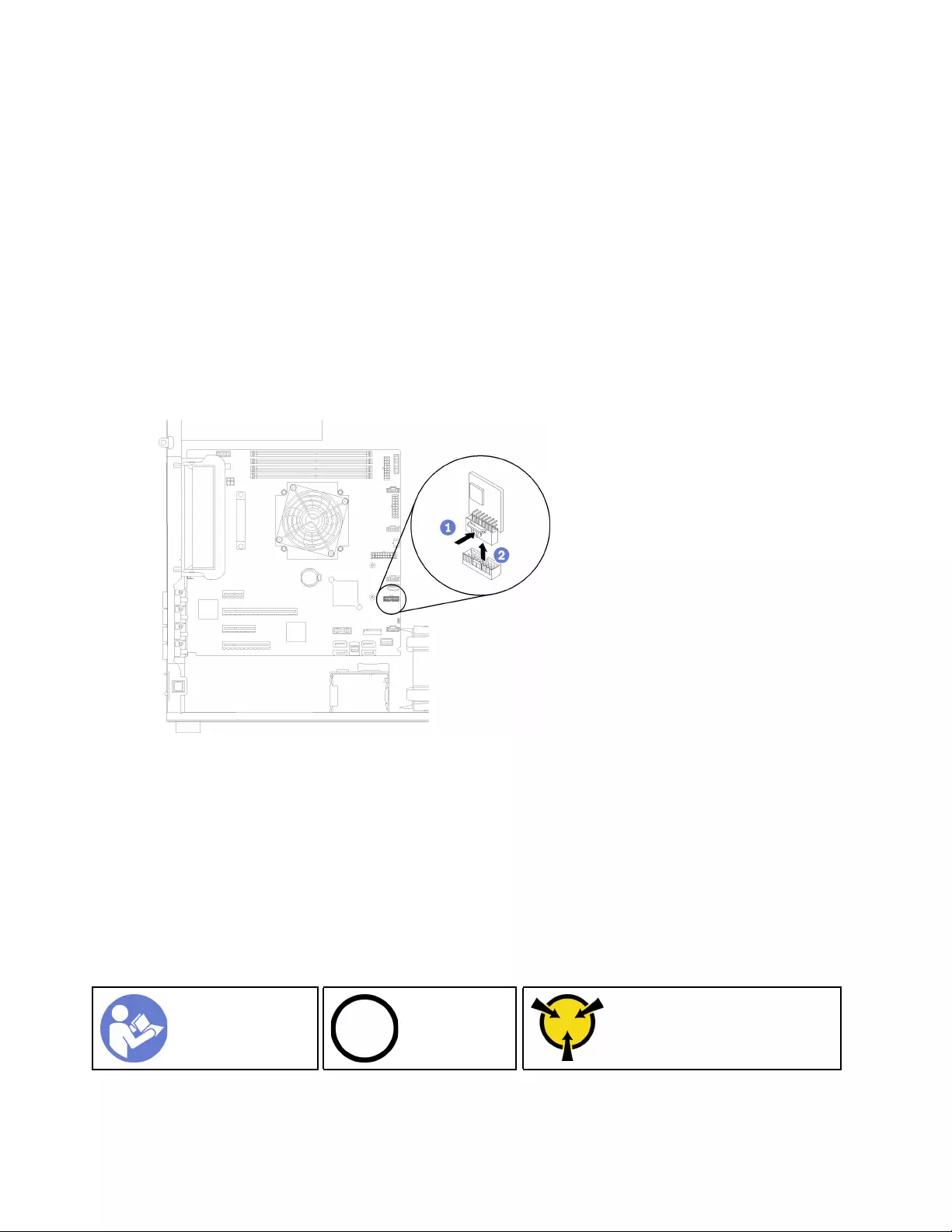
Before removing the TPM card:
1. Watch the procedure
A video of this procedure is available at YouTube: https://www.youtube.com/playlist?list=
PLYV5R7hVcs-Dy5N2dPXFx5Pht-FljAi6S.
2. If the server is in a rack, remove it from the rack.
3. Remove any locking device that secures the server cover, such as a Kensington lock or a pad lock.
4. Remove the server cover (see “Remove the server cover” on page 136).
To remove the TPM card, complete the following step:
Step 1. Locate the TPM card connector on the system board (see “System board components” on page
29).
Step 2. Carefully hold the TPM card by its edges; then, gently press on the latch, and lift it from the system
board.
Figure 112. TPM card removal
Note: Your TPM card might look slightly different from the illustration.
After removing the TPM card:
If you are instructed to return the defective component, please package the part to prevent any shipping
damage. Reuse the packaging the new part arrived in and follow all packaging instructions.
Install the TPM card
Use this information to install the TPM card.
“Read the
installation
Guidelines” on
page 53
“Power off
the server for
this task” on
page 14
“ATTENTION:
Static Sensitive Device
Ground package before opening”
on page 55
Before installing the TPM card:
154 ThinkSystem ST250 Maintenance Manual
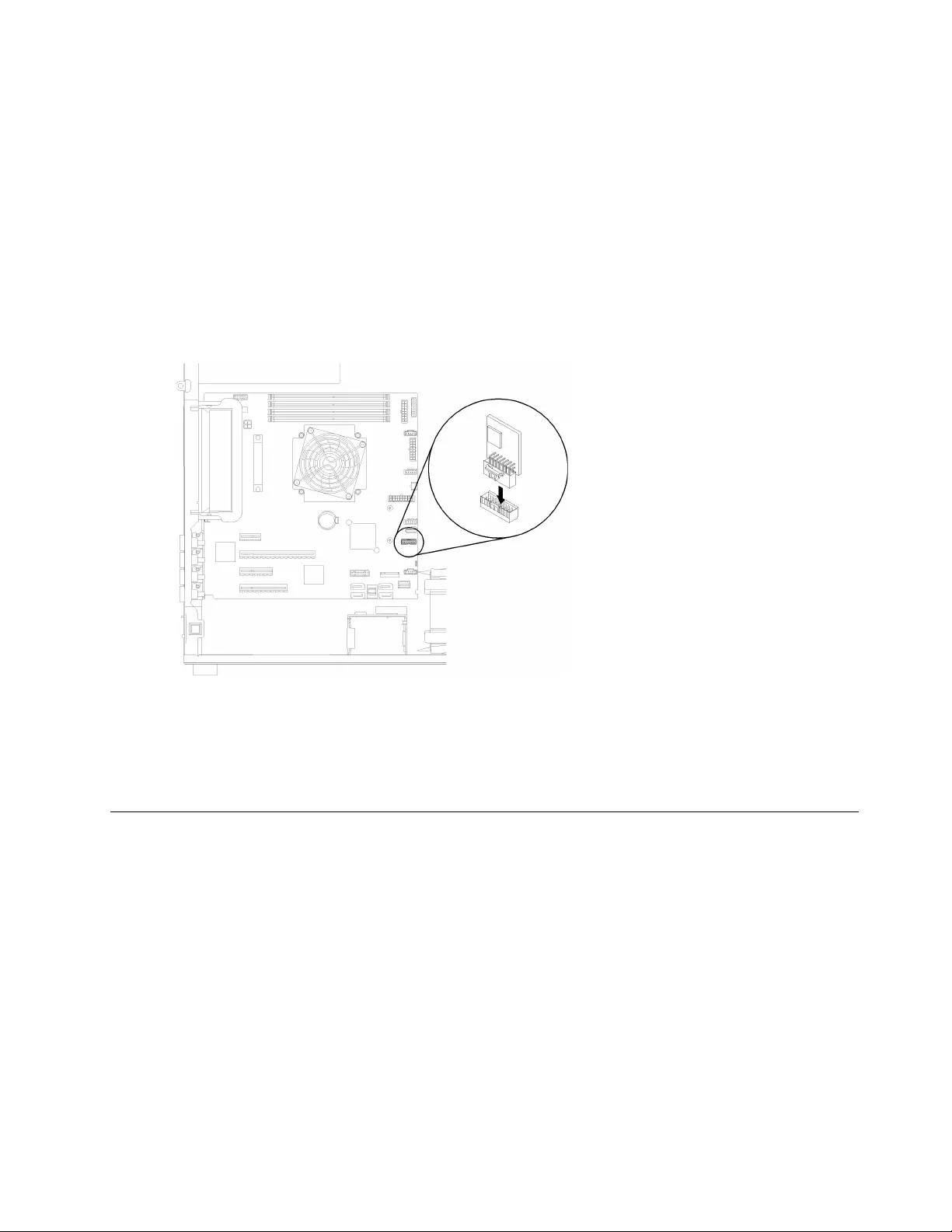
1. Watch the procedure
A video of this procedure is available at YouTube: https://www.youtube.com/playlist?list=
PLYV5R7hVcs-Dy5N2dPXFx5Pht-FljAi6S.
2. Touch the static-protective package that contains the component to any unpainted metal surface on the
server; then, remove it from the package and place it on a static-protective surface.
To install the TPM card, complete the following step:
Step 1. Locate the TPM card connector on the system board (see “System board components” on page
29).
Step 2. Carefully hold the TPM card by its edges and insert it into the TPM card connector on the system
board.
Figure 113. TPM card installation
After installing the TPM card:
Complete the parts replacement. See “Complete the parts replacement” on page 155
Complete the parts replacement
Use this information to complete the parts replacement.
To complete the parts replacement, do the following:
1. Ensure that all components have been reassembled correctly and that no tools or loose screws are left
inside your server.
2. Properly route and secure the cables in the server. Refer to the cable connecting and routing information
for each component.
3. If you have removed the front bezel, reinstall it. See “Install the front bezel” on page 89
4. If you have removed the front door, reinstall it. See “Install the front door” on page 91.
5. If you have removed the top cover, reinstall it. See “Install the server cover” on page 138.
6. Lock the server cover and server front door (available on some models) to ensure the security. See
“Server locks” on page 22.
Chapter 3.Hardware replacement procedures 155

7. Reconnect external cables and power cords to the server.
Attention: To avoid component damage, connect the power cords last.
8. If necessary, install the server in the rack.
9. Update the server configuration if necessary.
• Download and install the latest device drivers: http://datacentersupport.lenovo.com
• Update the system firmware. See “Firmware updates” on page 9.
• Use the Lenovo XClarity Provisioning Manager to update the UEFI configuration. For more
information, see: http://sysmgt.lenovofiles.com/help/topic/LXPM/UEFI_setup.html
• Use the Lenovo XClarity Provisioning Manager to configure the RAID if you have installed or removed
a hot-swap drive, a RAID adapter, or the M.2 backplane and M.2 drive. For more information, see:
http://sysmgt.lenovofiles.com/help/topic/LXPM/RAID_setup.html
156 ThinkSystem ST250 Maintenance Manual

Chapter 4. Problem determination
Use the information in this section to isolate and resolve issues that you might encounter while using your
server.
Lenovo servers can be configured to automatically notify Lenovo Support if certain events are generated.
You can configure automatic notification, also known as Call Home, from management applications, such as
the Lenovo XClarity Administrator. If you configure automatic problem notification, Lenovo Support is
automatically alerted whenever a server encounters a potentially significant event.
To isolate a problem, you should typically begin with the event log of the application that is managing the
server:
• If you are managing the server from the Lenovo XClarity Administrator, begin with the Lenovo XClarity
Administrator event log.
• If you are using some other management application, begin with the Lenovo XClarity Controller event log.
Notes:
• For your server, the Lenovo XClarity Controller web page or command-line interface does not support the
display of system utilization information for the following:
– Processor
– DIMM
– I/O
Event logs
An alert is a message or other indication that signals an event or an impending event. Alerts are generated by
the Lenovo XClarity Controller or by UEFI in the servers. These alerts are stored in the Lenovo XClarity
Controller Event Log. If the server is managed by the Chassis Management Module 2 or by the Lenovo
XClarity Administrator, alerts are automatically forwarded to those management applications.
Note: For a listing of events, including user actions that might need to be performed to recover from an
event, see the Messages and Codes Reference, which is available at:http://thinksystem.lenovofiles.com/
help/topic/7X09/pdf_files.html
Lenovo XClarity Administrator event log
If you are using Lenovo XClarity Administrator to manage server, network, and storage hardware, you can
view the events from all managed devices through the XClarity Administrator.
© Copyright Lenovo 2018, 2022 157
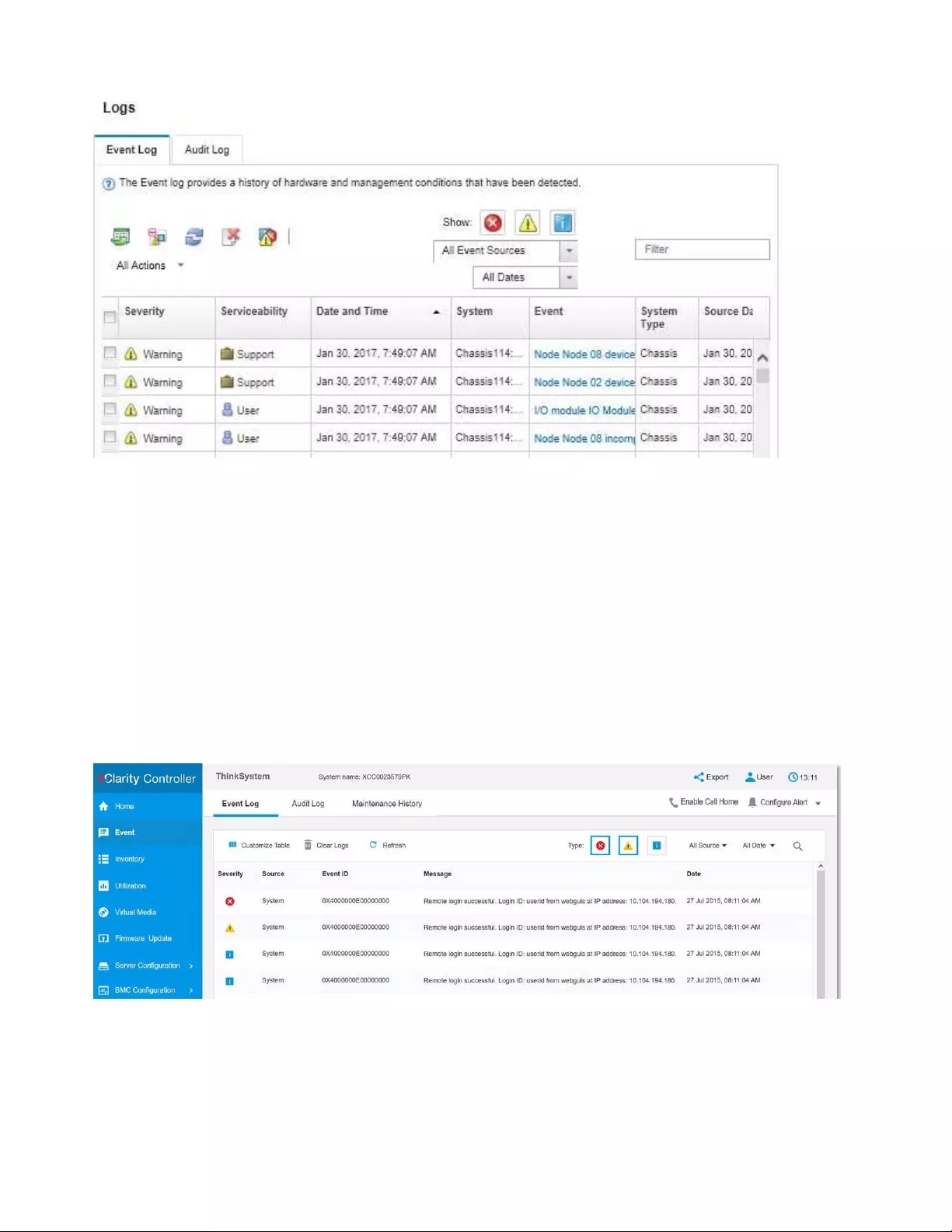
Figure 114. Lenovo XClarity Administrator event log
For more information about working with events from XClarity Administrator, see:
http://sysmgt.lenovofiles.com/help/topic/com.lenovo.lxca.doc/events_vieweventlog.html
Lenovo XClarity Controller event log
The Lenovo XClarity Controller monitors the physical state of the server and its components using sensors
that measure internal physical variables such as temperature, power-supply voltages, fan speeds, and
component status. The Lenovo XClarity Controller provides various interfaces to systems management
software and to system administrators and users to enable remote management and control of a server.
The Lenovo XClarity Controller monitors all components of the server and posts events in the Lenovo
XClarity Controller event log.
Figure 115. Lenovo XClarity Controller event log
For more information about accessing the Lenovo XClarity Controller event log, see:
158 ThinkSystem ST250 Maintenance Manual

“Viewing Event Logs” section in the XCC documentation compatible with your server at https://
sysmgt.lenovofiles.com/help/topic/lxcc_frontend/lxcc_overview.html
General problem determination procedures
Use the information in this section to resolve problems if the event log does not contain specific errors or the
server is inoperative.
If you are not sure about the cause of a problem and the power supplies are working correctly, complete the
following steps to attempt to resolve the problem:
1. Power off the server.
2. Make sure that the server is cabled correctly.
3. Remove or disconnect the following devices if applicable, one at a time, until you find the failure. Power
on and configure the server each time you remove or disconnect a device.
• Any external devices.
• Surge-suppressor device (on the server).
• Printer, mouse, and non-Lenovo devices.
• Each adapter.
• Hard disk drives.
• Memory modules until you reach the minimum configuration that is supported for the server.
See “Specifications” on page 3 to determine the minimum configuration for your server.
4. Power on the server.
If the problem is solved when you remove an adapter from the server, but the problem recurs when you
install the same adapter again, suspect the adapter. If the problem recurs when you replace the adapter with
a different one, try a different PCIe slot.
If the problem appears to be a networking problem and the server passes all system tests, suspect a network
cabling problem that is external to the server.
Resolving suspected power problems
Power problems can be difficult to solve. For example, a short circuit can exist anywhere on any of the power
distribution buses. Usually, a short circuit will cause the power subsystem to shut down because of an
overcurrent condition.
Complete the following steps to diagnose and resolve a suspected power problem.
Step 1. Check the event log and resolve any errors related to the power.
Note: Start with the event log of the application that is managing the server. For more information
about event logs, see “Event logs” on page 157.
Step 2. Check for short circuits, for example, if a loose screw is causing a short circuit on a circuit board.
Step 3. Remove the adapters and disconnect the cables and power cords to all internal and external
devices until the server is at the minimum configuration that is required for the server to start. See
“Specifications” on page 3 to determine the minimum configuration for your server.
Step 4. Reconnect all ac power cords and turn on the server. If the server starts successfully, reseat the
adapters and devices one at a time until the problem is isolated.
If the server does not start from the minimum configuration, replace the components in the minimum
configuration one at a time until the problem is isolated.
Chapter 4.Problem determination 159

Resolving suspected Ethernet controller problems
The method that you use to test the Ethernet controller depends on which operating system you are using.
See the operating-system documentation for information about Ethernet controllers, and see the Ethernet
controller device-driver readme file.
Complete the following steps to attempt to resolve suspected problems with the Ethernet controller.
Step 1. Make sure that the correct device drivers, which come with the server are installed and that they
are at the latest level.
Step 2. Make sure that the Ethernet cable is installed correctly.
• The cable must be securely attached at all connections. If the cable is attached but the problem
remains, try a different cable.
• If you set the Ethernet controller to operate at 100 Mbps or 1000 Mbps, you must use Category
5 cabling.
Step 3. Determine whether the hub supports auto-negotiation. If it does not, try configuring the integrated
Ethernet controller manually to match the speed and duplex mode of the hub.
Step 4. Check the Ethernet controller LEDs on the rear panel of the server. These LEDs indicate whether
there is a problem with the connector, cable, or hub.
• The Ethernet link status LED is lit when the Ethernet controller receives a link pulse from the hub.
If the LED is off, there might be a defective connector or cable or a problem with the hub.
• The Ethernet transmit/receive activity LED is lit when the Ethernet controller sends or receives
data over the Ethernet network. If the Ethernet transmit/receive activity is off, make sure that the
hub and network are operating and that the correct device drivers are installed.
Step 5. Check the Network activity LED on the rear of the server. The Network activity LED is lit when data
is active on the Ethernet network. If the Network activity LED is off, make sure that the hub and
network are operating and that the correct device drivers are installed.
Step 6. Check for operating-system-specific causes of the problem, and also make sure that the operating
system drivers are installed correctly.
Step 7. Make sure that the device drivers on the client and server are using the same protocol.
If the Ethernet controller still cannot connect to the network but the hardware appears to be working, the
network administrator must investigate other possible causes of the error.
Troubleshooting by symptom
Follow this procedure to find solutions to problems that have identifiable symptoms.
To use the symptom-based troubleshooting information in this section, complete the following steps:
1. Check the event log of the application that is managing the server and follow the suggested actions to
resolve any event codes.
• If you are managing the server from the Lenovo XClarity Administrator, begin with the Lenovo XClarity
Administrator event log.
• If you are using some other management application, begin with the Lenovo XClarity Controller event
log.
For more information about event logs, see “Event logs” on page 157.
2. Review this section to find the symptoms that you are experiencing and follow the suggested actions to
resolve the issue.
3. If the problem persists, contact support (see “Contacting Support” on page 177).
160 ThinkSystem ST250 Maintenance Manual

Power on and power off problems
Follow this procedure to resolve issues when powering on or powering off the server.
• “Embedded hypervisor is not in the boot list” on page 161
• “The power button does not work (server does not start)” on page 161
• “Server does not power on” on page 162
• “Server does not power off” on page 162
Embedded hypervisor is not in the boot list
Complete the following steps until the problem is solved.
1. If the server has been installed, moved, or serviced recently, or if this is the first time the embedded
hypervisor is being used, make sure that the device is connected properly and that there is no physical
damage to the connectors.
2. See the documentation that comes with the optional embedded hypervisor flash device for setup and
configuration information.
3. Check https://static.lenovo.com/us/en/serverproven/index.shtml to validate that the embedded hypervisor
device is supported for the server.
4. Make sure that the embedded hypervisor device is listed in the list of available boot options. From the
management controller user interface, click Server Configuration ➙ Boot Options.
For information about accessing the management controller user interface, see the XClarity Controller
product documentation:
5. Check http://datacentersupport.lenovo.com for any tech tips (service bulletins) related to the embedded
hypervisor and the server.
6. Make sure that other software works on the server to ensure that it is working properly.
The power button does not work (server does not start)
Note: The power button will not function until approximately 1 to 3 minutes after the server has been
connected to ac power.
Complete the following steps until the problem is resolved:
1. Make sure that the power button on the server is working correctly:
a. Disconnect the server power cords.
b. Reconnect the server power cords.
c. Reseat the operator information panel cable, and then repeat steps a and b.
• If the server starts, reseat the operator information panel.
• If the problem remains, replace the operator information panel.
2. Make sure that:
• The power cords are correctly connected to the server and to a working electrical outlet.
• The LEDs on the power supply do not indicate a problem.
3. Reseat the power supplies.
4. Replace each power supply, restarting the server each time:
• DIMMs
• Power supplies
Chapter 4.Problem determination 161

5. If you just installed an optional device, remove it, and restart the server. If the server starts, you might
have installed more devices than the power supply supports.
Server does not power on
Complete the following steps until the problem is resolved:
1. Check the event log for any events related to the server not powering on.
2. Check for any LEDs that are flashing amber.
3. Check the power LED on the system board.
4. Reseat the power supply.
5. Replace the power supply.
Server does not power off
Complete the following steps until the problem is resolved:
1. Determine whether you are using an Advanced Configuration and Power Interface (ACPI) or a non-ACPI
operating system. If you are using a non-ACPI operating system, complete the following steps:
a. Press Ctrl+Alt+Delete.
b. Turn off the server by pressing the power button and holding it down for 5 seconds.
c. Restart the server.
d. If the server fails POST and the power button does not work, disconnect the power cord for 20
seconds; then, reconnect the power cord and restart the server.
2. If the problem remains or if you are using an ACPI-aware operating system, suspect the system board.
Memory problems
Follow this procedure to resolve issues related to memory.
• “Displayed system memory less than installed physical memory” on page 162
• “Multiple rows of DIMMs in a branch identified as failing” on page 163
Displayed system memory less than installed physical memory
Complete the following steps until the problem is resolved:
Note: Each time you install or remove a DIMM, you must disconnect the server from the power source; then,
wait 10 seconds before restarting the server.
1. Make sure that:
• No error LEDs are lit on the operator information panel.
• No DIMM error LEDs are lit on the system board.
• Memory mirrored channel does not account for the discrepancy.
• The memory modules are seated correctly.
• You have installed the correct type of memory.
• If you changed the memory, you updated the memory configuration in the Setup utility.
• All banks of memory are enabled. The server might have automatically disabled a memory bank when
it detected a problem, or a memory bank might have been manually disabled.
• There is no memory mismatch when the server is at the minimum memory configuration.
2. Reseat the DIMMs, and then restart the server.
162 ThinkSystem ST250 Maintenance Manual

3. Run memory diagnostics. When you start a solution and press the key according to the on-screen
instructions, the LXPM interface is displayed by default. (For more information, see the “Startup” section
in the LXPM documentation compatible with your server at https://sysmgt.lenovofiles.com/help/topic/
lxpm_frontend/lxpm_product_page.html.) You can perform memory diagnostics from this interface. From
the Diagnostic page, click Run Diagnostic ➙ Memory test.
4. Check the POST error log:
• If a DIMM was disabled by a systems-management interrupt (SMI), replace the DIMM.
• If a DIMM was disabled by the user or by POST, reseat the DIMM; then, run the Setup utility and
enable the DIMM.
5. Reseat the DIMM.
6. Restart the server.
Multiple rows of DIMMs in a branch identified as failing
1. Reseat the DIMMs; then, restart the server.
2. Remove the lowest-numbered DIMM pair of those that are identified and replace it with an identical
known good DIMM; then, restart the server. Repeat as necessary. If the failures continue after all
identified DIMMs are replaced, go to step 4.
3. Return the removed DIMMs, one at a time, to their original connectors, restarting the server after each
DIMM, until a DIMM fails. Replace each failing DIMM with an identical known good DIMM, restarting the
server after each DIMM replacement. Repeat step 3 until you have tested all removed DIMMs.
4. Replace the lowest-numbered DIMM of those identified; then, restart the server. Repeat as necessary.
5. Reverse the DIMMs between the channels (of the same processor), and then restart the server. If the
problem is related to a DIMM, replace the failing DIMM.
6. (Trained technician only) Replace the system board.
Hard disk drive problems
Follow this procedure to resolve issues related to the hard disk drives.
• “Server cannot recognize a hard drive” on page 163
• “Multiple hard drives fail” on page 164
• “Multiple hard drives are offline” on page 164
• “A replacement hard disk drive does not rebuild” on page 164
• “Green hard disk drive activity LED does not represent actual state of associated drive” on page 165
• “Yellow hard disk drive status LED does not represent actual state of associated drive” on page 165
Server cannot recognize a hard drive
Complete the following steps until the problem is solved.
1. Observe the associated yellow hard disk drive status LED. If the LED is lit, it indicates a drive fault.
2. If the LED is lit, remove the drive from the bay, wait 45 seconds, and reinsert the drive, making sure that
the drive assembly connects to the hard disk drive backplane.
3. Observe the associated green hard disk drive activity LED and the yellow status LED:
• If the green activity LED is flashing and the yellow status LED is not lit, the drive is recognized by the
controller and is working correctly. Run the diagnostics tests for the hard disk drives. When you start
a server and press the key according to the on-screen instructions, the LXPM is displayed by default.
(For more information, see the “Startup” section in the LXPM documentation compatible with your
server at https://sysmgt.lenovofiles.com/help/topic/lxpm_frontend/lxpm_product_page.html.) You can
Chapter 4.Problem determination 163
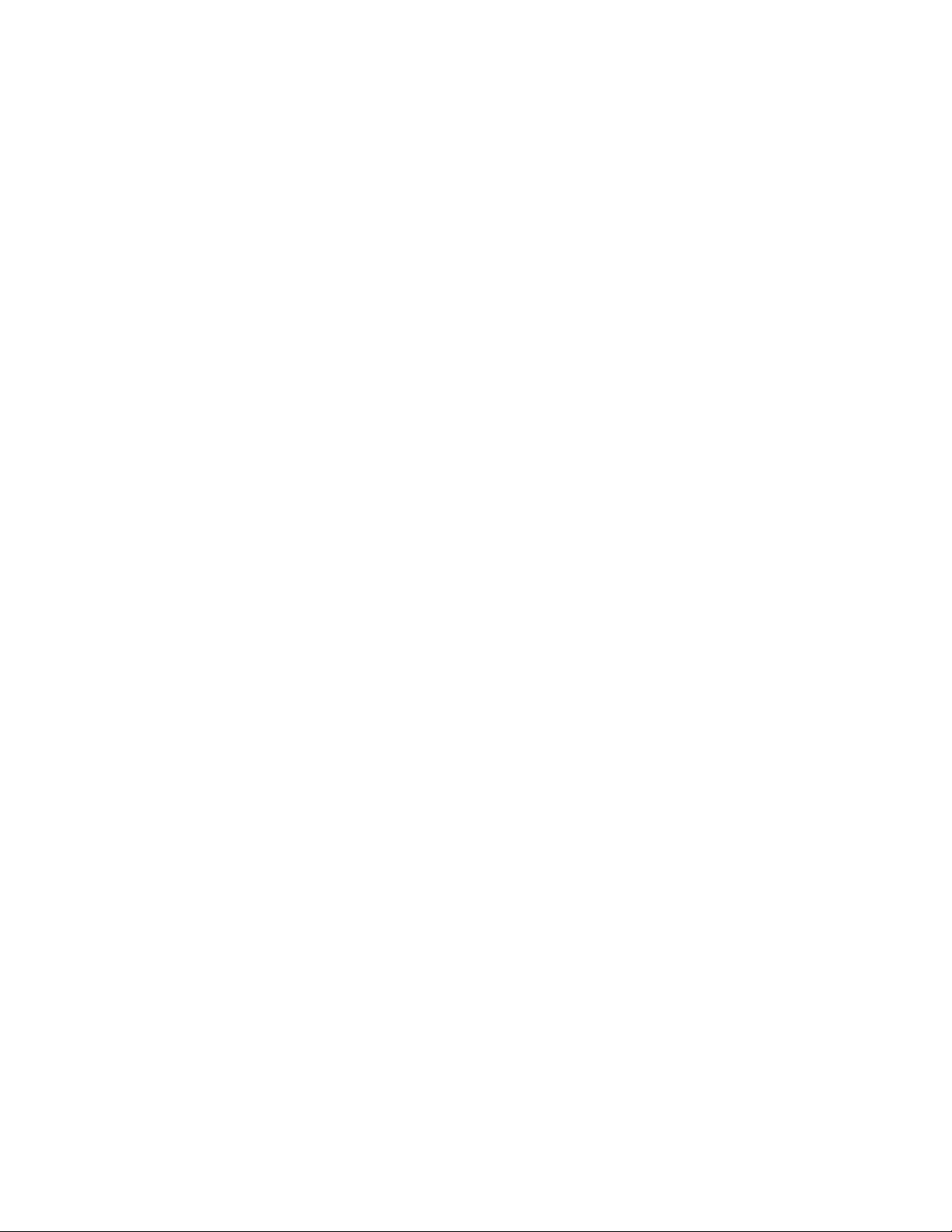
perform hard drive diagnostics from this interface. From the Diagnostic page, click Run Diagnostic
➙ HDD test.
• If the green activity LED is flashing and the yellow status LED is flashing slowly, the drive is
recognized by the controller and is rebuilding.
• If neither LED is lit or flashing, check the hard disk drive backplane.
• If the green activity LED is flashing and the yellow status LED is lit, replace the drive. If the activity of
the LEDs remains the same, go to step Hard disk drive problems. If the activity of the LEDs changes,
return to step 1.
4. Make sure that the hard disk drive backplane is correctly seated. When it is correctly seated, the drive
assemblies correctly connect to the backplane without bowing or causing movement of the backplane.
5. Reseat the backplane power cable and repeat steps 1 through 3.
6. Reseat the backplane signal cable and repeat steps 1 through 3.
7. Suspect the backplane signal cable or the backplane:
• Replace the affected backplane signal cable.
• Replace the affected backplane.
8. Run the diagnostics tests for the hard disk drives. When you start a server and press the key according
to the on-screen instructions, the LXPM is displayed by default. (For more information, see the “Startup”
section in the LXPM documentation compatible with your server at https://sysmgt.lenovofiles.com/help/
topic/lxpm_frontend/lxpm_product_page.html.) You can perform hard drive diagnostics from this interface.
From the Diagnostic page, click Run Diagnostic ➙ HDD test.
Based on those tests:
• If the adapter passes the test but the drives are not recognized, replace the backplane signal cable
and run the tests again.
• Replace the backplane.
• If the adapter fails the test, disconnect the backplane signal cable from the adapter and run the tests
again.
• If the adapter fails the test, replace the adapter.
Multiple hard drives fail
Complete the following steps until the problem is solved:
• View the Lenovo XClarity Controller event log for events related to power supplies or vibration issues and
resolve those events.
• Make sure that the device drivers and firmware for the hard disk drive and server are at the latest level
Important: Some cluster solutions require specific code levels or coordinated code updates. If the device is
part of a cluster solution, verify that the latest level of code is supported for the cluster solution before you
update the code.
Multiple hard drives are offline
Complete the following steps until the problem is solved:
• View the Lenovo XClarity Controller event log for events related to power supplies or vibration issues and
resolve those events.
• View the storage subsystem log for events related to the storage subsystem and resolve those events.
A replacement hard disk drive does not rebuild
Complete the following steps until the problem is solved:
164 ThinkSystem ST250 Maintenance Manual

1. Make sure that the hard disk drive is recognized by the adapter (the green hard disk drive activity LED is
flashing).
2. Review the SAS/SATA RAID adapter documentation to determine the correct configuration parameters
and settings.
Green hard disk drive activity LED does not represent actual state of associated drive
Complete the following steps until the problem is solved:
1. If the green hard disk drive activity LED does not flash when the drive is in use, run the diagnostics tests
for the hard disk drives. When you start a server and press the key according to the on-screen
instructions, the LXPM is displayed by default. (For more information, see the “Startup” section in the
LXPM documentation compatible with your server at https://sysmgt.lenovofiles.com/help/topic/lxpm_
frontend/lxpm_product_page.html.) You can perform hard drive diagnostics from this interface. From the
Diagnostic page, click Run Diagnostic ➙ HDD test.
2. If the drive passes the test, replace the backplane.
3. If the drive fails the test, replace the drive.
Yellow hard disk drive status LED does not represent actual state of associated drive
Complete the following steps until the problem is solved:
1. Turn off the server.
2. Reseat the SAS/SATA adapter.
3. Reseat the backplane signal cable and backplane power cable.
4. Reseat the hard disk drive.
5. Power on the server and observe the activity of the hard disk drive LEDs.
Monitor and video problems
Follow this procedure to solve problems related to a monitor or video.
• “Incorrect characters are displayed” on page 165
• “Screen is blank” on page 165
• “Screen goes blank when you start some application programs” on page 166
• “The monitor has screen jitter, or the screen image is wavy, unreadable, rolling, or distorted.” on page 166
• “The wrong characters appear on the screen” on page 166
• “Management controller remote presence cannot work” on page 167
Incorrect characters are displayed
Complete the following steps:
1. Verify that the language and locality settings are correct for the keyboard and operating system.
2. If the wrong language is displayed, update the server firmware to the latest level. See “Firmware
updates” on page 9.
Screen is blank
1. If the server is attached to a KVM switch, bypass the KVM switch to eliminate it as a possible cause of
the problem: connect the monitor cable directly to the correct connector on the rear of the server.
2. If the server installed with the graphical adapters while turning on the server, the Lenovo logo displays
on the screen after approximately 3 minutes. This is normal operation while the system loads.
3. Make sure that:
Chapter 4.Problem determination 165
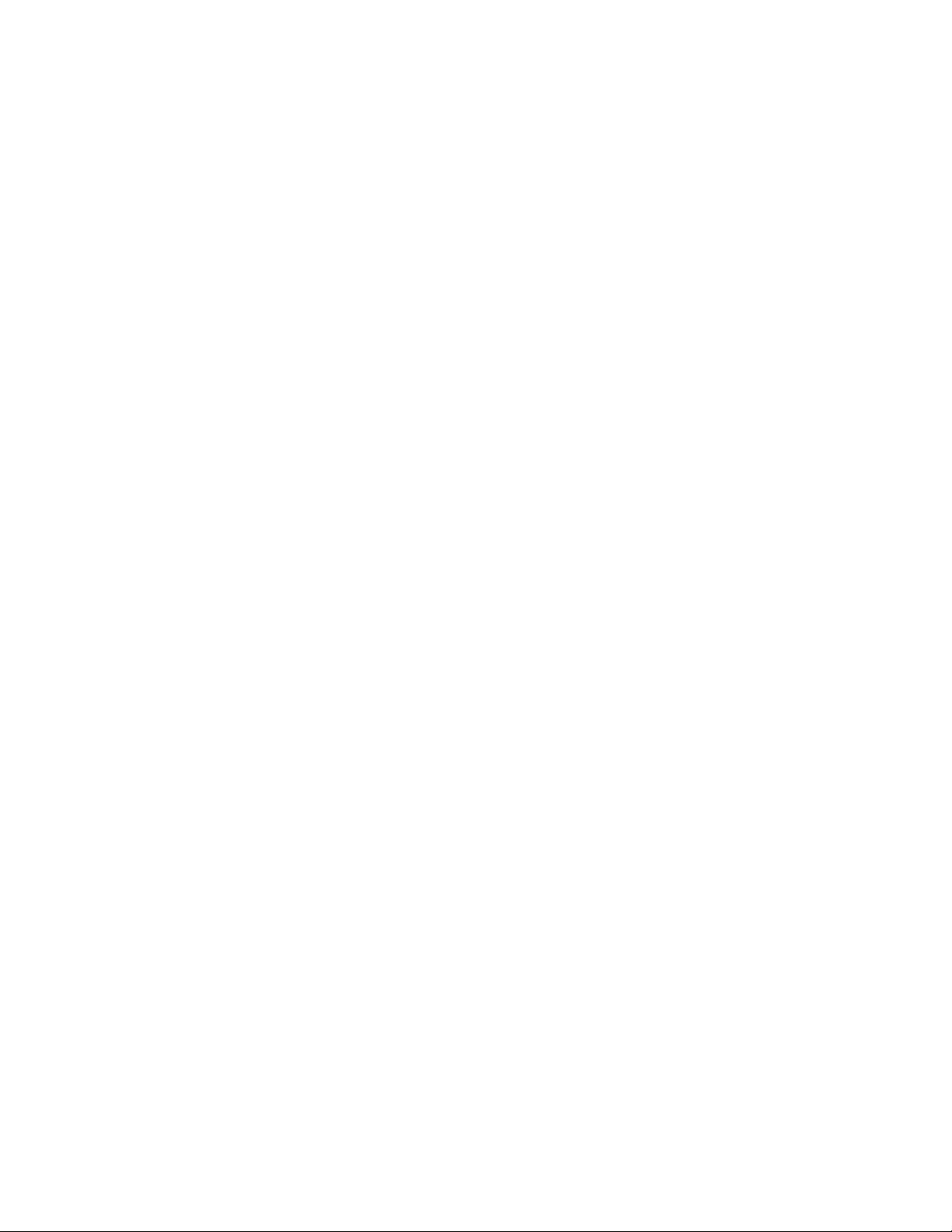
• The server is turned on. If there is no power to the server.
• The monitor cables are connected correctly.
• The monitor is turned on and the brightness and contrast controls are adjusted correctly.
4. Make sure that the correct server is controlling the monitor, if applicable.
5. Make sure that corrupted server firmware is not affecting the video; see “Firmware updates” on page 9.
6. Observe the LEDs on the system board; if the codes are changing, go to step 6.
7. Replace the following components one at a time, in the order shown, restarting the server each time:
a. Monitor
b. Video adapter (if one is installed)
c. (Trained technician only) System board
Screen goes blank when you start some application programs
1. Make sure that:
• The application program is not setting a display mode that is higher than the capability of the monitor.
• You installed the necessary device drivers for the application.
The monitor has screen jitter, or the screen image is wavy, unreadable, rolling, or distorted.
1. If the monitor self-tests show that the monitor is working correctly, consider the location of the monitor.
Magnetic fields around other devices (such as transformers, appliances, fluorescents, and other
monitors) can cause screen jitter or wavy, unreadable, rolling, or distorted screen images. If this
happens, turn off the monitor.
Attention: Moving a color monitor while it is turned on might cause screen discoloration.
Move the device and the monitor at least 305 mm (12 in.) apart, and turn on the monitor.
Notes:
a. To prevent diskette drive read/write errors, make sure that the distance between the monitor and any
external diskette drive is at least 76 mm (3 in.).
b. Non-Lenovo monitor cables might cause unpredictable problems.
2. Reseat the monitor cable.
3. Replace the components listed in step 2 one at a time, in the order shown, restarting the server each
time:
a. Monitor cable
b. Video adapter (if one is installed)
c. Monitor
d. (Trained technician only) System board
The wrong characters appear on the screen
Complete the following steps until the problem is solved:
1. Verify that the language and locality settings are correct for the keyboard and operating system.
2. If the wrong language is displayed, update the server firmware to the latest level. See “Firmware
updates” on page 9.
166 ThinkSystem ST250 Maintenance Manual

Management controller remote presence cannot work
The management controller remote presence function is unable to display the system screen when an
optional video adapter is present. To use the management controller remote presence function, remove the
optional video adapter or use the onboard VGA as the display device.
Keyboard, mouse, or USB-device problems
Follow this procedure to solve problems related to a keyboard, mouse, or USB device.
• “All or some keys on the keyboard do not work.” on page 167
• “Mouse does not work.” on page 167
• “USB-device does not work.” on page 167
All or some keys on the keyboard do not work.
1. Make sure that:
• The keyboard cable is securely connected.
• The server and the monitor are turned on.
2. If you are using a USB keyboard, run the Setup utility and enable keyboardless operation.
3. If you are using a USB keyboard and it is connected to a USB hub, disconnect the keyboard from the
hub and connect it directly to the server.
4. Replace the keyboard.
Mouse does not work.
1. Make sure that:
• The mouse cable is securely connected to the server.
• The mouse device drivers are installed correctly.
• The server and the monitor are turned on.
• The mouse option is enabled in the Setup utility.
2. If you are using a USB mouse and it is connected to a USB hub, disconnect the mouse from the hub and
connect it directly to the server.
3. Replace the mouse.
USB-device does not work.
1. Make sure that:
• The correct USB device driver is installed.
• The operating system supports USB devices.
2. Make sure that the USB configuration options are set correctly in system setup.
Restart the server and press key according to the on-screen instructions to display the LXPM system
setup interface. (For more information, see the “Startup” section in the LXPM documentation compatible
with your server at https://sysmgt.lenovofiles.com/help/topic/lxpm_frontend/lxpm_product_page.html.)
Then, click System Settings ➙ Devices and I/O Ports ➙ USB Configuration.
3. If you are using a USB hub, disconnect the USB device from the hub and connect it directly to the
server.
Optional-device problems
Follow this procedure to solve problems related to optional devices.
Chapter 4.Problem determination 167

• “External USB device not recognized” on page 168
• “PCIe adapter is not recognized or is not functioning” on page 168
• “A Lenovo optional device that worked previously does not work now. ” on page 169
• “A Lenovo optional device that was just installed does not work.” on page 168
• “A Lenovo optional device that worked previously does not work now. ” on page 169
External USB device not recognized
Complete the following steps until the problem is resolved:
1. Make sure that the proper drivers are installed on the compute node. See the product documentation for
the USB device for information about device drivers.
2. Use the Setup utility to make sure that the device is configured correctly.
3. If the USB device is plugged into a hub or the console breakout cable, unplug the device and plug it
directly into the USB port on the front of the compute node.
PCIe adapter is not recognized or is not functioning
Complete the following steps until the problem is resolved:
1. Check the event log and resolve any issues related to the device.
2. Validate that the device is supported for the server (see https://static.lenovo.com/us/en/serverproven/
index.shtml).
3. Make sure that the adapter is installed in a correct slot.
4. Make sure that the proper device drivers are installed for the device.
5. Resolve any resource conflicts if running legacy mode (UEFI).
6. Check http://datacentersupport.lenovo.com for any tech tips (also known as retain tips or service
bulletins) that might be related to the adapter.
7. Ensure any adapter external connections are correct and that the connectors are not physically
damaged.
Insufficient PCIe resources are detected.
If you see an error message stating “Insufficient PCI Resources Detected,” complete the following steps until
the problem is resolved:
1. Remove one of the PCIe adapters.
2. Restart the system and press F1 to display the Lenovo XClarity Provisioning Manager system setup
interface.
3. Click UEFI Setup ➙ System Settings ➙ Devices and I/O Ports ➙ MM Config Base; then, modify the
setting to the lower memory capacity. For example, modify 3 GB to 2 GB or modify 2 GB to 1 GB.
4. Save the settings and restart the system.
5. The action for this step will differ based on whether or not the reboot is successful.
• If the reboot is successful, shut down the solution and reinstall the PCIe card you removed.
• If the reboot failed, repeat step 2 to step 5.
A Lenovo optional device that was just installed does not work.
1. Make sure that:
• The device is supported for the server (see https://static.lenovo.com/us/en/serverproven/index.shtml).
• You followed the installation instructions that came with the device and the device is installed
correctly.
• You have not loosened any other installed devices or cables.
168 ThinkSystem ST250 Maintenance Manual

• You updated the configuration information in system setup. When you start a server and press the
key according to the on-screen instructions to display the Setup Utility. (For more information, see the
“Startup” section in the LXPM documentation compatible with your server at https://
sysmgt.lenovofiles.com/help/topic/lxpm_frontend/lxpm_product_page.html.) Whenever memory or any
other device is changed, you must update the configuration.
2. Reseat the device that you just installed.
3. Replace the device that you just installed.
A Lenovo optional device that worked previously does not work now.
1. Make sure that all of the cable connections for the device are secure.
2. If the device comes with test instructions, use those instructions to test the device.
3. If the failing device is a SCSI device, make sure that:
• The cables for all external SCSI devices are connected correctly.
• The last device in each SCSI chain, or the end of the SCSI cable, is terminated correctly.
• Any external SCSI device is turned on. You must turn on an external SCSI device before you turn on
the server.
4. Reseat the failing device.
5. Replace the failing device.
Serial-device problems
Follow this procedure to solve problems with serial ports or devices.
• “Number of displayed serial ports is less than the number of installed serial ports” on page 169
• “Serial device does not work” on page 169
Number of displayed serial ports is less than the number of installed serial ports
Complete the following steps until the problem is solved.
1. Make sure that:
• Each port is assigned a unique address in the Setup utility and none of the serial ports is disabled.
• The serial-port adapter (if one is present) is seated correctly.
2. Reseat the serial port adapter.
3. Replace the serial port adapter.
Serial device does not work
1. Make sure that:
• The device is compatible with the server.
• The serial port is enabled and is assigned a unique address.
• The device is connected to the correct connector.
2. Reseat the following components:
a. Failing serial device.
b. Serial cable.
3. Replace the following components:
a. Failing serial device.
b. Serial cable.
4. (Trained technician only) Replace the system board.
Chapter 4.Problem determination 169

Intermittent problems
Follow this procedure to solve intermittent problems.
• “Intermittent external device problems” on page 170
• “Intermittent KVM problems” on page 170
• “Intermittent unexpected reboots” on page 170
Intermittent external device problems
Complete the following steps until the problem is solved.
1. Make sure that the correct device drivers are installed. See the manufacturer's website for
documentation.
2. For a USB device:
a. Make sure that the device is configured correctly.
Restart the server and press the key according to the on-screen instructions to display the LXPM
system setup interface. (For more information, see the “Startup” section in the LXPM documentation
compatible with your server at https://sysmgt.lenovofiles.com/help/topic/lxpm_frontend/lxpm_product_
page.html.) Then, click System Settings ➙ Devices and I/O Ports ➙ USB Configuration.
b. Connect the device to another port. If using a USB hub, remove the hub and connect the device
directly to the compute node. Make sure that the device is configured correctly for the port.
Intermittent KVM problems
Complete the following steps until the problem is solved.
Video problems:
1. Make sure that all cables and the console breakout cable are properly connected and secure.
2. Make sure that the monitor is working properly by testing it on another compute node.
3. Test the console breakout cable on a working compute node to ensure that it is operating properly.
Replace the console breakout cable if it is defective.
Keyboard problems:
Make sure that all cables and the console breakout cable are properly connected and secure.
Mouse problems:
Make sure that all cables and the console breakout cable are properly connected and secure.
Intermittent unexpected reboots
Note: Some correctable errors require that the server reboot so that it can disable a device, such as a
memory DIMM or a processor to allow the machine to boot up properly.
1. If the reset occurs during POST and the POST watchdog timer is enabled, make sure that sufficient time
is allowed in the watchdog timeout value (POST Watchdog Timer).
To check the POST watchdog time, restart the server and press the key according to the on-screen
instructions to display the LXPM system setup interface. (For more information, see the “Startup”
section in the LXPM documentation compatible with your server at https://sysmgt.lenovofiles.com/help/
topic/lxpm_frontend/lxpm_product_page.html.) Then, click BMC Settings ➙ POST Watchdog Timer.
170 ThinkSystem ST250 Maintenance Manual

2. If the reset occurs after the operating system starts, disable any automatic server restart (ASR) utilities,
such as the Automatic Server Restart IPMI Application for Windows, or any ASR devices that are
installed.
3. See the management controller event log to check for an event code that indicates a reboot. See “Event
logs” on page 157 for information about viewing the event log.
Power problems
Follow this procedure to resolve issues related to power.
System error LED is on and event log "Power supply has lost input" is displayed
To resolve the problem, ensure that:
1. The power supply is properly connected to a power cord.
2. The power cord is connected to a properly grounded electrical outlet for the server.
Network problems
Follow this procedure to resolve issues related to networking.
• “Cannot wake server using Wake on LAN” on page 171
• “Could not log in using LDAP account with SSL enabled” on page 171
Cannot wake server using Wake on LAN
Complete the following steps until the problem is resolved:
1. If you are using the dual-port network adapter and the server is connected to the network using Ethernet
5 connector, check the system-error log or IMM2 system event log (see “Event logs” on page 157),
make sure:
a. Fan 3 is running in standby mode, if Emulex dual port 10GBase-T embedded adapter is installed.
b. The room temperature is not too high (see “Specifications” on page 3).
c. The air vents are not blocked.
d. The air baffle is installed securely.
2. Reseat the dual-port network adapter.
3. Turn off the server and disconnect it from the power source; then, wait 10 seconds before restarting the
server.
4. If the problem still remains, replace the dual-port network adapter.
Could not log in using LDAP account with SSL enabled
Complete the following steps until the problem is resolved:
1. Make sure that the license key is valid.
2. Generate a new license key and log in again.
Observable problems
Follow this procedure to solve observable problems.
• “The server immediately displays the POST Event Viewer when it is turned on” on page 172
• “Server is unresponsive (POST is complete and operating system is running)” on page 172
• “Server is unresponsive (POST failed and cannot start System Setup)” on page 173
Chapter 4.Problem determination 171
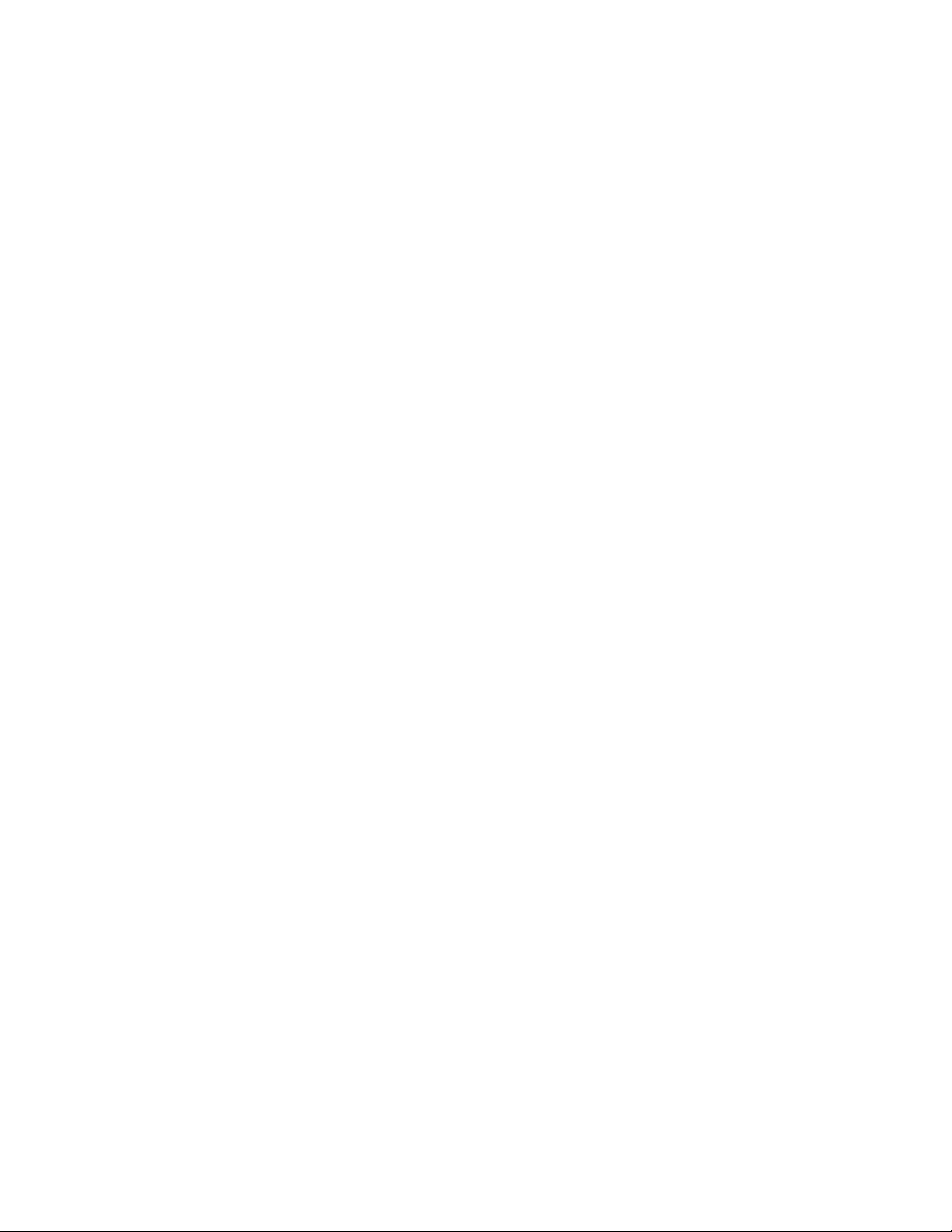
• “Voltage planar fault is displayed in the event log” on page 173
• “Unusual smell” on page 173
• “Server seems to be running hot” on page 173
• “Cracked parts or cracked chassis” on page 173
The server immediately displays the POST Event Viewer when it is turned on
Complete the following steps until the problem is solved.
1. Correct any errors that are indicated by the light path diagnostics LEDs.
2. Make sure that the server supports all the processors and that the processors match in speed and
cache size.
You can view processor details from system setup.
To determine if the processor is supported for the server, see https://static.lenovo.com/us/en/
serverproven/index.shtml.
3. (Trained technician only) Make sure that processor 1 is seated correctly.
4. (Trained technician only) Remove processor 2 and restart the server.
5. Replace the following components one at a time, in the order shown, restarting the server each time:
a. (Trained technician only) Processor
b. (Trained technician only) System board
Server is unresponsive (POST is complete and operating system is running)
Complete the following steps until the problem is solved.
• If you are in the same location as the compute node, complete the following steps:
1. If you are using a KVM connection, make sure that the connection is operating correctly. Otherwise,
make sure that the keyboard and mouse are operating correctly.
2. If possible, log in to the compute node and verify that all applications are running (no applications are
hung).
3. Restart the compute node.
4. If the problem remains, make sure that any new software has been installed and configured correctly.
5. Contact your place of purchase of the software or your software provider.
• If you are accessing the compute node from a remote location, complete the following steps:
1. Make sure that all applications are running (no applications are hung).
2. Attempt to log out of the system and log back in.
3. Validate the network access by pinging or running a trace route to the compute node from a
command line.
a. If you are unable to get a response during a ping test, attempt to ping another compute node in
the enclosure to determine whether it is a connection problem or compute node problem.
b. Run a trace route to determine where the connection breaks down. Attempt to resolve a
connection issue with either the VPN or the point at which the connection breaks down.
4. Restart the compute node remotely through the management interface.
5. If the problem remains, verify that any new software has been installed and configured correctly.
6. Contact your place of purchase of the software or your software provider.
172 ThinkSystem ST250 Maintenance Manual
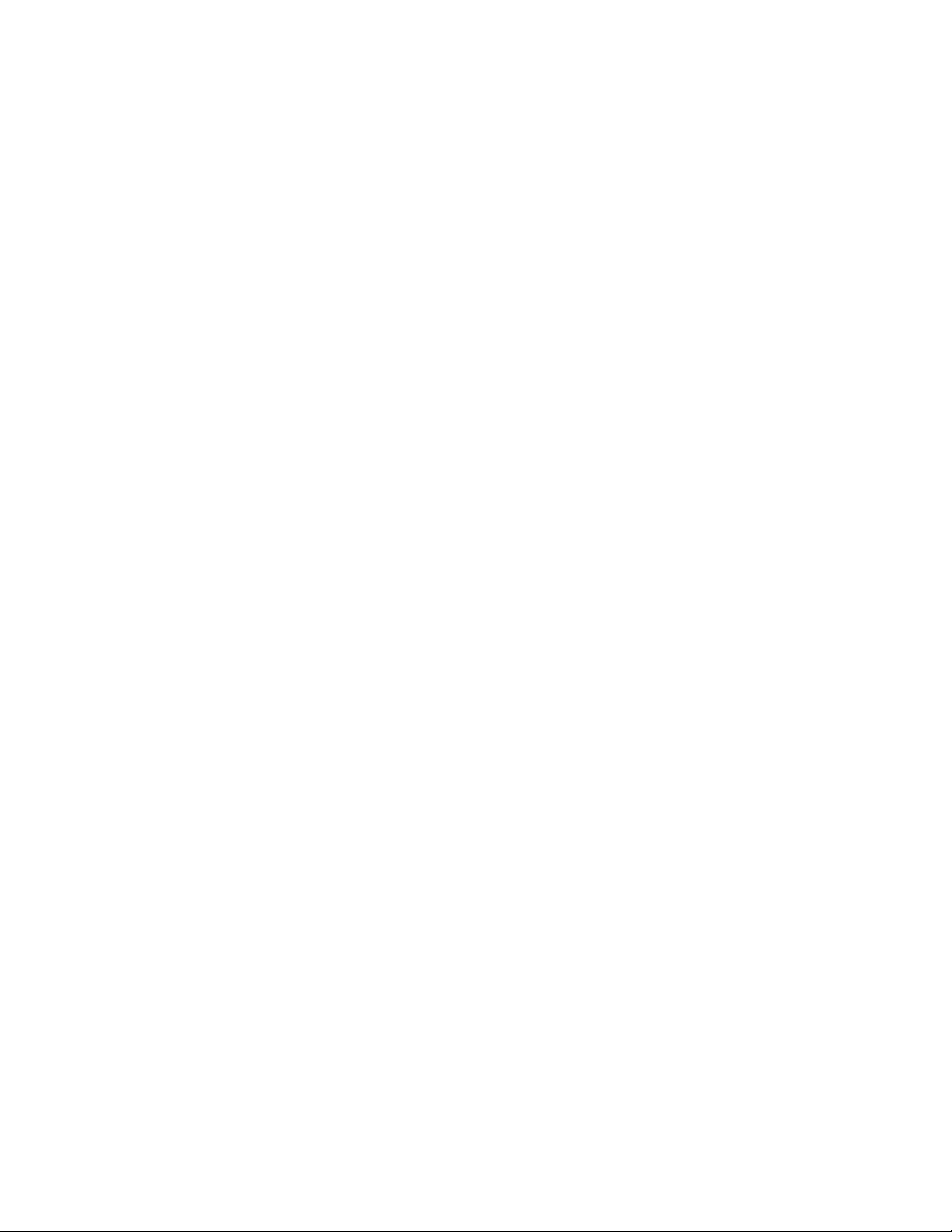
Server is unresponsive (POST failed and cannot start System Setup)
Configuration changes, such as added devices or adapter firmware updates, and firmware or application
code problems can cause the server to fail POST (the power-on self-test).
If this occurs, the server responds in either of the following ways:
• The server restarts automatically and attempts POST again.
• The server hangs, and you must manually restart the server for the server to attempt POST again.
After a specified number of consecutive attempts (automatic or manual), the server to reverts to the default
UEFI configuration and starts System Setup so that you can make the necessary corrections to the
configuration and restart the server. If the server is unable to successfully complete POST with the default
configuration, there might be a problem with the system board.
You can specify the number of consecutive restart attempts in System Setup. Restart the server and press
the key according to the on-screen instructions to display the LXPM system setup interface. (For more
information, see the “Startup” section in the LXPM documentation compatible with your server at https://
sysmgt.lenovofiles.com/help/topic/lxpm_frontend/lxpm_product_page.html.) Then, click System Settings ➙
Recovery and RAS ➙ POST Attempts ➙ POST Attempts Limit. Available options are 3, 6, 9, and disable.
Voltage planar fault is displayed in the event log
Complete the following steps until the problem is solved.
1. Revert the system to the minimum configuration. See “Specifications” on page 3 for the minimally
required number of processors and DIMMs.
2. Restart the system.
• If the system restarts, add each of the items that you removed one at a time, restarting the system
each time, until the error occurs. Replace the item for which the error occurs.
• If the system does not restart, suspect the system board.
Unusual smell
Complete the following steps until the problem is solved.
1. An unusual smell might be coming from newly installed equipment.
2. If the problem remains, contact Lenovo Support.
Server seems to be running hot
Complete the following steps until the problem is solved.
Multiple compute nodes or chassis:
1. Make sure that the room temperature is within the specified range (see “Specifications” on page 3).
2. Check the management processor event log for rising temperature events. If there are no events, the
compute node is running within normal operating temperatures. Note that you can expect some
variation in temperature.
Cracked parts or cracked chassis
Contact Lenovo Support.
Software problems
Follow this procedure to solve software problems.
1. To determine whether the problem is caused by the software, make sure that:
Chapter 4.Problem determination 173
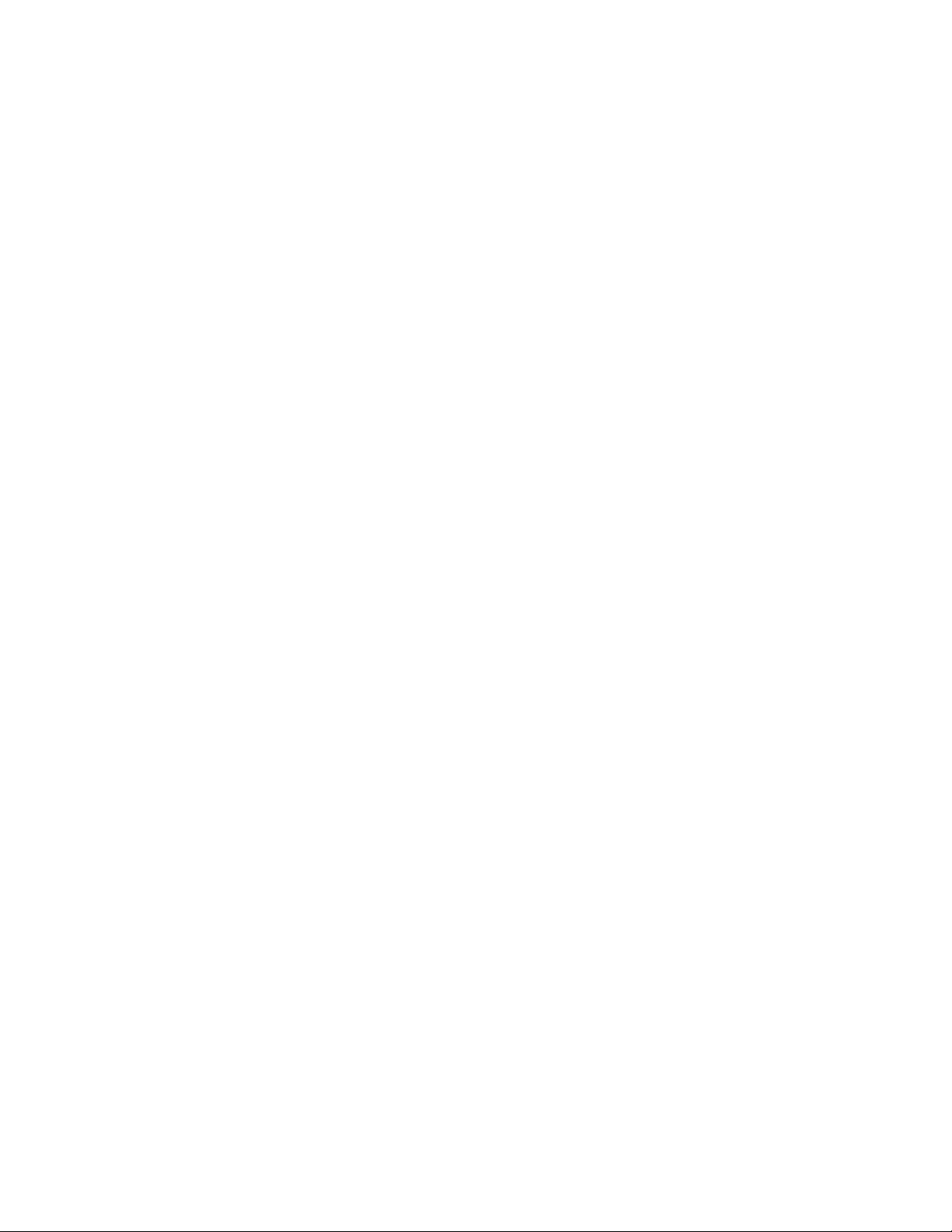
• The server has the minimum memory that is needed to use the software. For memory requirements,
see the information that comes with the software.
Note: If you have just installed an adapter or memory, the server might have a memory-address
conflict.
• The software is designed to operate on the server.
• Other software works on the server.
• The software works on another server.
2. If you receive any error messages while you use the software, see the information that comes with the
software for a description of the messages and suggested solutions to the problem.
3. Contact your place of purchase of the software.
174 ThinkSystem ST250 Maintenance Manual

Appendix A. Getting help and technical assistance
If you need help, service, or technical assistance or just want more information about Lenovo products, you
will find a wide variety of sources available from Lenovo to assist you.
On the World Wide Web, up-to-date information about Lenovo systems, optional devices, services, and
support are available at:
http://datacentersupport.lenovo.com
Note: IBM is Lenovo's preferred service provider for ThinkSystem.
Before you call
Before you call, there are several steps that you can take to try and solve the problem yourself. If you decide
that you do need to call for assistance, gather the information that will be needed by the service technician to
more quickly resolve your problem.
Attempt to resolve the problem yourself
You can solve many problems without outside assistance by following the troubleshooting procedures that
Lenovo provides in the online help or in the Lenovo product documentation. The Lenovo product
documentation also describes the diagnostic tests that you can perform. The documentation for most
systems, operating systems, and programs contains troubleshooting procedures and explanations of error
messages and error codes. If you suspect a software problem, see the documentation for the operating
system or program.
You can find the product documentation for your ThinkSystem products at the following location:
http://thinksystem.lenovofiles.com/help/index.jsp
You can take these steps to try to solve the problem yourself:
• Check all cables to make sure that they are connected.
• Check the power switches to make sure that the system and any optional devices are turned on.
• Check for updated software, firmware, and operating-system device drivers for your Lenovo product. The
Lenovo Warranty terms and conditions state that you, the owner of the Lenovo product, are responsible
for maintaining and updating all software and firmware for the product (unless it is covered by an
additional maintenance contract). Your service technician will request that you upgrade your software and
firmware if the problem has a documented solution within a software upgrade.
• If you have installed new hardware or software in your environment, check https://static.lenovo.com/us/en/
serverproven/index.shtml to make sure that the hardware and software is supported by your product.
• Go to http://datacentersupport.lenovo.com and check for information to help you solve the problem.
– Check the Lenovo forums at https://forums.lenovo.com/t5/Datacenter-Systems/ct-p/sv_eg to see if
someone else has encountered a similar problem.
You can solve many problems without outside assistance by following the troubleshooting procedures that
Lenovo provides in the online help or in the Lenovo product documentation. The Lenovo product
documentation also describes the diagnostic tests that you can perform. The documentation for most
systems, operating systems, and programs contains troubleshooting procedures and explanations of error
messages and error codes. If you suspect a software problem, see the documentation for the operating
system or program.
© Copyright Lenovo 2018, 2022 175

Gathering information needed to call Support
If you believe that you require warranty service for your Lenovo product, the service technicians will be able
to assist you more efficiently if you prepare before you call. You can also see http://
datacentersupport.lenovo.com/warrantylookup for more information about your product warranty.
Gather the following information to provide to the service technician. This data will help the service
technician quickly provide a solution to your problem and ensure that you receive the level of service for
which you might have contracted.
• Hardware and Software Maintenance agreement contract numbers, if applicable
• Machine type number (Lenovo 4-digit machine identifier)
• Model number
• Serial number
• Current system UEFI and firmware levels
• Other pertinent information such as error messages and logs
As an alternative to calling Lenovo Support, you can go to https://support.lenovo.com/servicerequest to
submit an Electronic Service Request. Submitting an Electronic Service Request will start the process of
determining a solution to your problem by making the pertinent information available to the service
technicians. The Lenovo service technicians can start working on your solution as soon as you have
completed and submitted an Electronic Service Request.
Collecting service data
To clearly identify the root cause of a server issue or at the request of Lenovo Support, you might need
collect service data that can be used for further analysis. Service data includes information such as event
logs and hardware inventory.
Service data can be collected through the following tools:
• Lenovo XClarity Provisioning Manager
Use the Collect Service Data function of Lenovo XClarity Provisioning Manager to collect system service
data. You can collect existing system log data or run a new diagnostic to collect new data.
• Lenovo XClarity Controller
You can use the Lenovo XClarity Controller web interface or the CLI to collect service data for the server.
The file can be saved and sent to Lenovo Support.
– For more information about using the web interface to collect service data, see the “Downloading
service data” section in the XCC documentation version compatible with your server at https://
sysmgt.lenovofiles.com/help/topic/lxcc_frontend/lxcc_overview.html.
– For more information about using the CLI to collect service data, see the “ffdc command” section in the
XCC documentation version compatible with your server at https://sysmgt.lenovofiles.com/help/topic/
lxcc_frontend/lxcc_overview.html.
• Lenovo XClarity Administrator
Lenovo XClarity Administrator can be set up to collect and send diagnostic files automatically to Lenovo
Support when certain serviceable events occur in Lenovo XClarity Administrator and the managed
endpoints. You can choose to send diagnostic files to Lenovo Support using Call Home or to another
service provider using SFTP. You can also manually collect diagnostic files, open a problem record, and
send diagnostic files to the Lenovo Support Center.
You can find more information about setting up automatic problem notification within the Lenovo XClarity
Administrator at http://sysmgt.lenovofiles.com/help/topic/com.lenovo.lxca.doc/admin_setupcallhome.html.
176 ThinkSystem ST250 Maintenance Manual
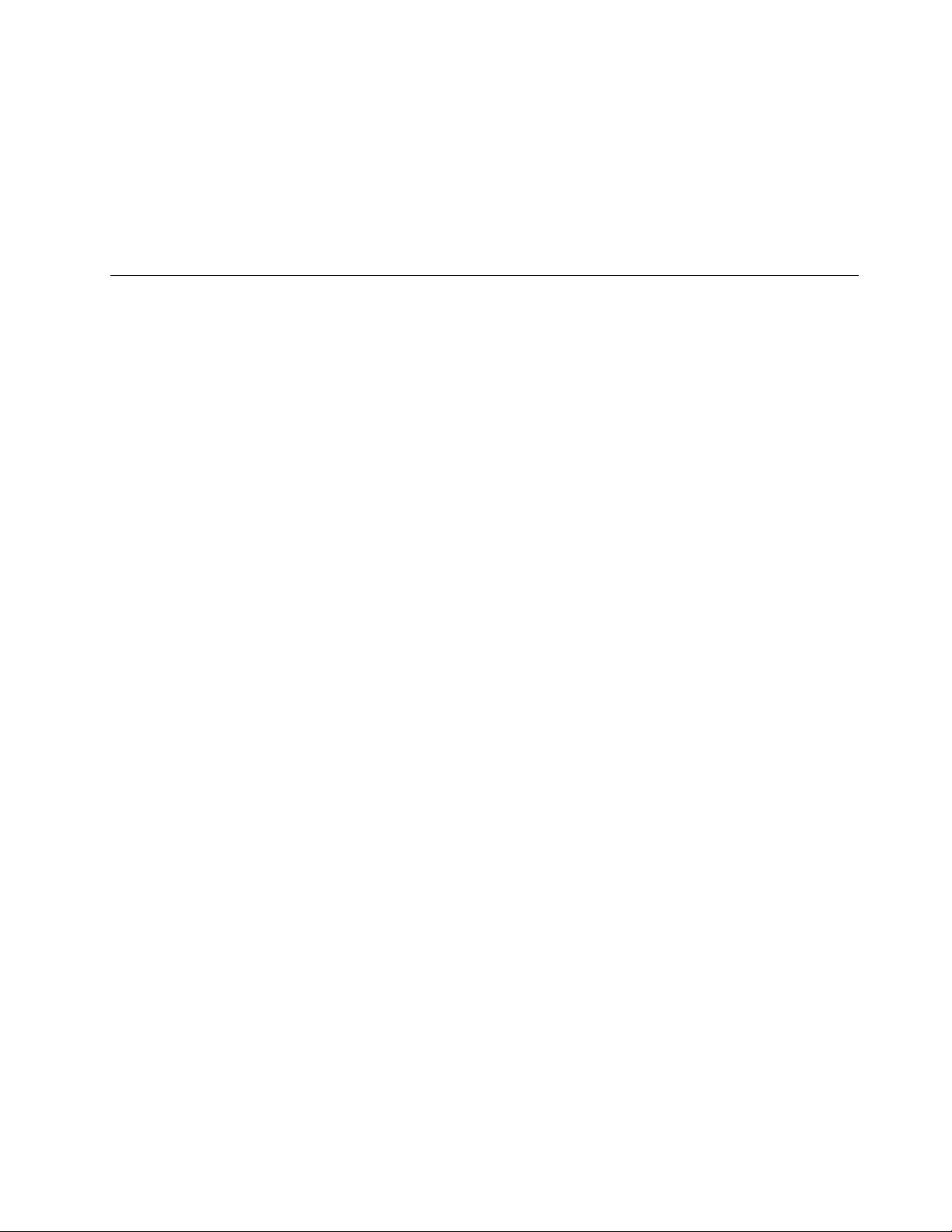
• Lenovo XClarity Essentials OneCLI
Lenovo XClarity Essentials OneCLI has inventory application to collect service data. It can run both in-
band and out-of-band. When running in-band within the host operating system on the server, OneCLI can
collect information about the operating system, such as the operating system event log, in addition to the
hardware service data.
To obtain service data, you can run the getinfor command. For more information about running the
getinfor, see http://sysmgt.lenovofiles.com/help/topic/toolsctr_cli_lenovo/onecli_r_getinfor_command.html.
Contacting Support
You can contact Support to obtain help for your issue.
You can receive hardware service through a Lenovo Authorized Service Provider. To locate a service
provider authorized by Lenovo to provide warranty service, go to https://datacentersupport.lenovo.com/
serviceprovider and use filter searching for different countries. For Lenovo support telephone numbers, see
https://datacentersupport.lenovo.com/supportphonelist for your region support details.
Appendix A. Getting help and technical assistance 177

178 ThinkSystem ST250 Maintenance Manual

Appendix B. Notices
Lenovo may not offer the products, services, or features discussed in this document in all countries. Consult
your local Lenovo representative for information on the products and services currently available in your
area.
Any reference to a Lenovo product, program, or service is not intended to state or imply that only that
Lenovo product, program, or service may be used. Any functionally equivalent product, program, or service
that does not infringe any Lenovo intellectual property right may be used instead. However, it is the user's
responsibility to evaluate and verify the operation of any other product, program, or service.
Lenovo may have patents or pending patent applications covering subject matter described in this
document. The furnishing of this document is not an offer and does not provide a license under any patents
or patent applications. You can send inquiries in writing to the following:
Lenovo (United States), Inc.
8001 Development Drive
Morrisville, NC 27560
U.S.A.
Attention: Lenovo Director of Licensing
LENOVO PROVIDES THIS PUBLICATION “AS IS” WITHOUT WARRANTY OF ANY KIND, EITHER EXPRESS
OR IMPLIED, INCLUDING, BUT NOT LIMITED TO, THE IMPLIED WARRANTIES OF NON-INFRINGEMENT,
MERCHANTABILITY OR FITNESS FOR A PARTICULAR PURPOSE. Some jurisdictions do not allow
disclaimer of express or implied warranties in certain transactions, therefore, this statement may not apply to
you.
This information could include technical inaccuracies or typographical errors. Changes are periodically made
to the information herein; these changes will be incorporated in new editions of the publication. Lenovo may
make improvements and/or changes in the product(s) and/or the program(s) described in this publication at
any time without notice.
The products described in this document are not intended for use in implantation or other life support
applications where malfunction may result in injury or death to persons. The information contained in this
document does not affect or change Lenovo product specifications or warranties. Nothing in this document
shall operate as an express or implied license or indemnity under the intellectual property rights of Lenovo or
third parties. All information contained in this document was obtained in specific environments and is
presented as an illustration. The result obtained in other operating environments may vary.
Lenovo may use or distribute any of the information you supply in any way it believes appropriate without
incurring any obligation to you.
Any references in this publication to non-Lenovo Web sites are provided for convenience only and do not in
any manner serve as an endorsement of those Web sites. The materials at those Web sites are not part of the
materials for this Lenovo product, and use of those Web sites is at your own risk.
Any performance data contained herein was determined in a controlled environment. Therefore, the result
obtained in other operating environments may vary significantly. Some measurements may have been made
on development-level systems and there is no guarantee that these measurements will be the same on
generally available systems. Furthermore, some measurements may have been estimated through
extrapolation. Actual results may vary. Users of this document should verify the applicable data for their
specific environment.
© Copyright Lenovo 2018, 2022 179

Trademarks
LENOVO, THINKSYSTEM, Flex System, System x, NeXtScale System, and x Architecture are trademarks of
Lenovo.
Intel and Intel Xeon are trademarks of Intel Corporation in the United States, other countries, or both.
Internet Explorer, Microsoft, and Windows are trademarks of the Microsoft group of companies.
Linux is a registered trademark of Linus Torvalds.
All other trademarks are the property of their respective owners.
Important notes
Processor speed indicates the internal clock speed of the microprocessor; other factors also affect
application performance.
CD or DVD drive speed is the variable read rate. Actual speeds vary and are often less than the possible
maximum.
When referring to processor storage, real and virtual storage, or channel volume, KB stands for 1 024 bytes,
MB stands for 1 048 576 bytes, and GB stands for 1 073 741 824 bytes.
When referring to hard disk drive capacity or communications volume, MB stands for 1 000 000 bytes, and
GB stands for 1 000 000 000 bytes. Total user-accessible capacity can vary depending on operating
environments.
Maximum internal hard disk drive capacities assume the replacement of any standard hard disk drives and
population of all hard-disk-drive bays with the largest currently supported drives that are available from
Lenovo.
Maximum memory might require replacement of the standard memory with an optional memory module.
Each solid-state memory cell has an intrinsic, finite number of write cycles that the cell can incur. Therefore, a
solid-state device has a maximum number of write cycles that it can be subjected to, expressed as total
bytes written (TBW). A device that has exceeded this limit might fail to respond to system-generated
commands or might be incapable of being written to. Lenovo is not responsible for replacement of a device
that has exceeded its maximum guaranteed number of program/erase cycles, as documented in the Official
Published Specifications for the device.
Lenovo makes no representations or warranties with respect to non-Lenovo products. Support (if any) for the
non-Lenovo products is provided by the third party, not Lenovo.
Some software might differ from its retail version (if available) and might not include user manuals or all
program functionality.
Telecommunication regulatory statement
This product may not be certified in your country for connection by any means whatsoever to interfaces of
public telecommunications networks. Further certification may be required by law prior to making any such
connection. Contact a Lenovo representative or reseller for any questions.
180 ThinkSystem ST250 Maintenance Manual
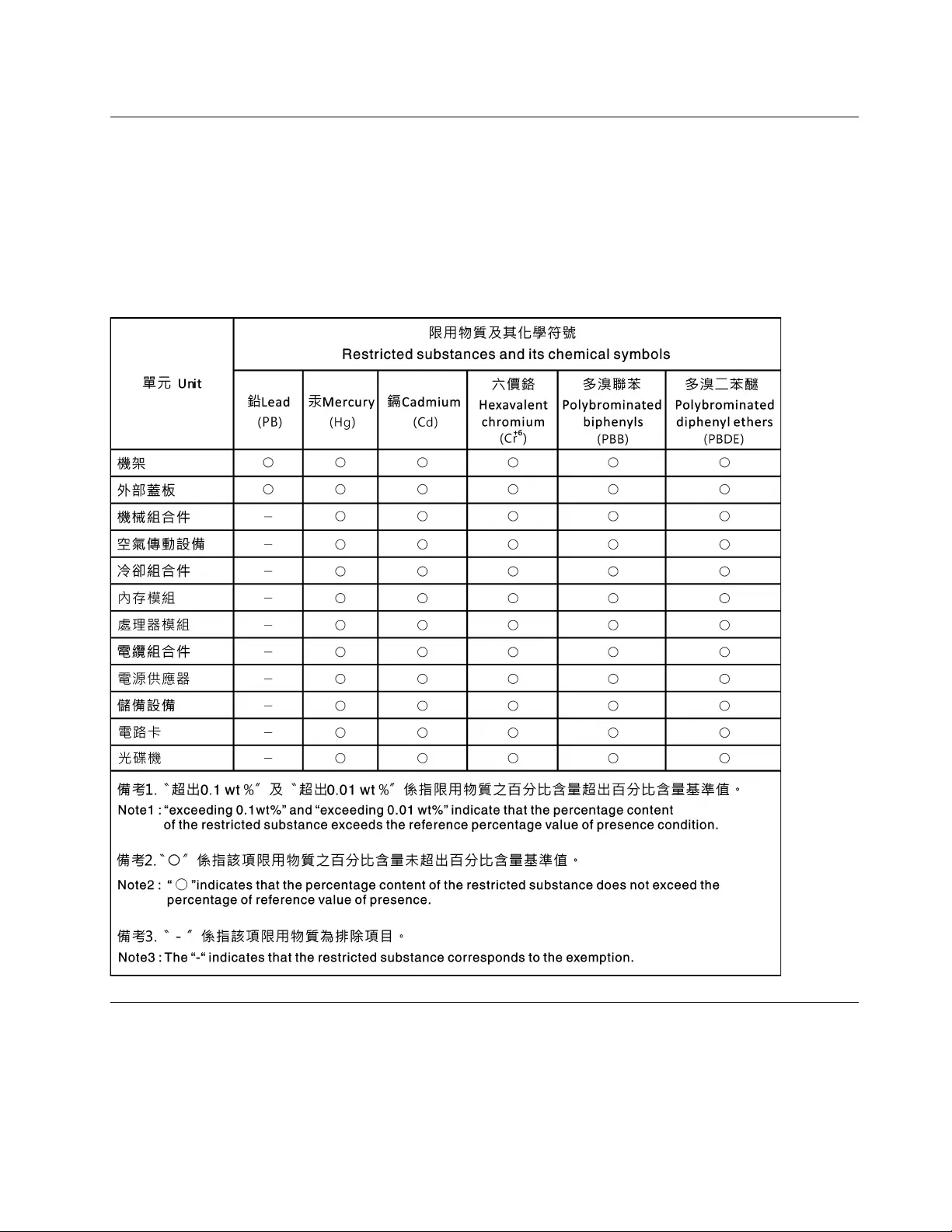
Electronic emission notices
When you attach a monitor to the equipment, you must use the designated monitor cable and any
interference suppression devices that are supplied with the monitor.
Additional electronic emissions notices are available at:
http://thinksystem.lenovofiles.com/help/index.jsp
Taiwan BSMI RoHS declaration
Taiwan import and export contact information
Contacts are available for Taiwan import and export information.
Appendix B. Notices 181

182 ThinkSystem ST250 Maintenance Manual
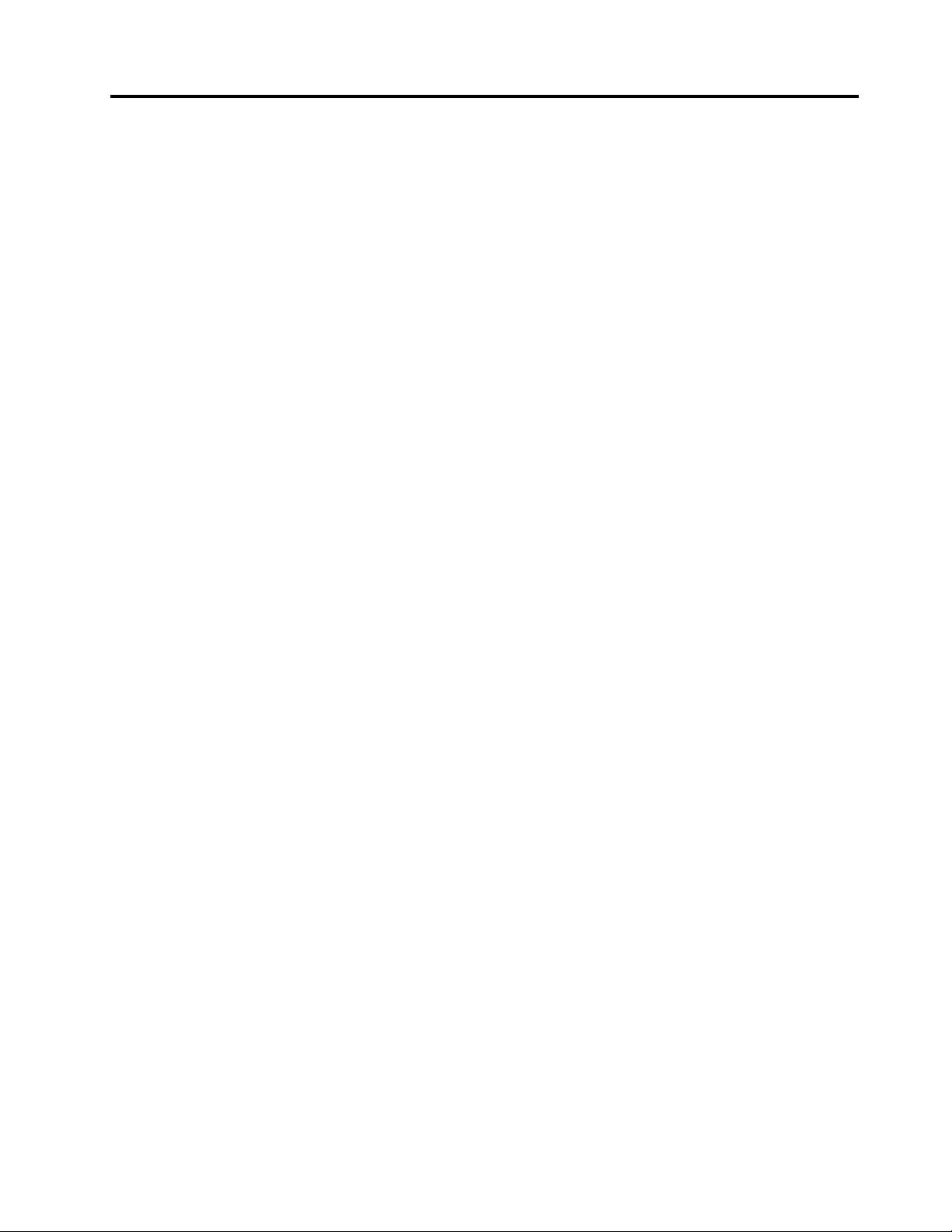
Index
2.5-inch SSD from 3.5-inch drive bay
replacing 63
2.5-inch SSD from a 3.5-inch drive bay
removing 64
2.5-inch SSD into a 3.5-inch drive bay
installing 65
A
assert
physical presence 149
B
backplane
replacing 58
C
cable routing
eight 2.5-inch hot-swap drives 43
eight 3.5-inch hot-swap drives and four 2.5-inch hot-swap
drives 47
eight 3.5-inch hot-swap SAS/SATA drives 42
eight 3.5-inch simple-swap drives 40
fixed power supply 38
four 3.5-inch hot-swap SAS/SATA drives 41
four 3.5-inch simple-swap drives 39
front panel 32
hot-swap-drive backplane 41
optical drive 34
redundant power supply 36
simple-swap-drive backplate 39
sixteen 2.5-inch hot-swap drives 44
tape drive 35
CMOS battery
install 68
remove 67
replacing 67
collecting service data 176
completing
parts replacement 155
contamination, particulate and gaseous 8
CR2032 67
creating a personalized support web page 175
custom support web page 175
D
devices, static-sensitive
handling 55
DIMM
installing 72
removing 70
replacing 70
DIMM installation rules 71
drive
replacing 73
drive cage
installing 57
removing 55
replacing 55
E
enable
TPM 147
Ethernet
controller
troubleshooting 160
Ethernet controller problems
solving 160
F
fan
replacing 79
fan power cable routing 31
firmware
update 9
firmware updates 9
fixed power supply
installing 118
removing 114
fixed power supply unit
replacing 114
flash power module
installing 87
removing 85
replacing 85
form factor 3
front bezel
installing 89
removing 88
replacing 88
front door
installing 91
removing 90
replacing 90
front panel 20
front panel board assembly
installing 93
removing 92
replacing 92
front system fan
installing 81
removing 80
front view 15
front view of the server 15
G
gaseous contamination 8
Getting help 175
guidelines
options installation 53
system reliability 54
H
handling static-sensitive devices 55
hard disk drive problems 163
hardware service and support telephone numbers 177
heat sink
installing 96
removing 95
help 175
hot-swap drive
© Copyright Lenovo 2018, 2022 183
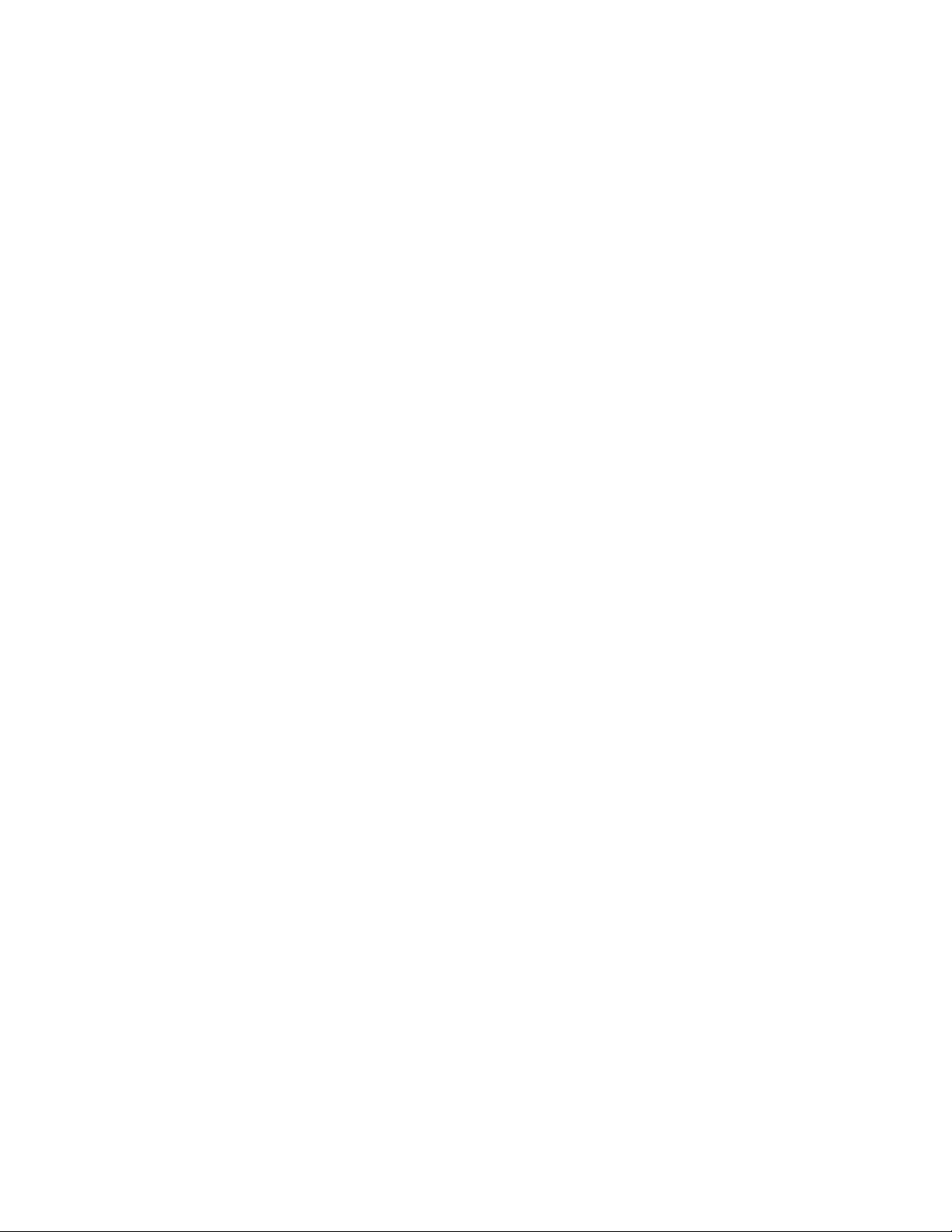
installing 78
removing 76
hot-swap drive backplane
installing 59
removing 58
replacing 58
hot-swap power supply
installing 127
removing 123
I
ID label 1
important notices 180
install
CMOS battery 68
processor 134
installation
guidelines 53
installation guidelines 53
installing
2.5-inch SSD into a 3.5-inch drive bay 65
DIMM 72
drive cage 57
fixed power supply 118
flash power module 87
front bezel 89
front door 91
front panel board assembly 93
front system fan 81
heat sink 96
hot-swap drive 78
hot-swap drive backplane 59
hot-swap power supply 127
intrusion switch 99
M.2 drive 100
optical drive 104
power distribution board 111
processor fan 96
rear system fan 83
server cover 138
simple-swap drive 75
simple-swap drive backplate 62
system board 143
tape drive 152
TPM card 154
insufficient PCIe resource
solving 167
intermittent problems 170
internal cable routing 31
introduction 1
intrusion switch
installing 99
removing 98
replacing 98
J
jumper 30
K
keyboard problems 167
M
M.2 drive
installing 100
removing 100
replacing 100
memory
problems 162
monitor problems 165
mouse problems 167
N
network
problems 171
network access label 1
network activity LED 20
notes, important 180
notices 179
O
observable problems 171
optical drive
installing 104
removing 103
replacing 102
optional-device problems 167
P
particulate contamination 8
parts list 48
parts replacement, completing 155
PCIe
troubleshooting 167
PCIe adapter
replacing 107
physical presence 149
power
problems 171
power button 20
power cords 52
power distribution board
installing 111
removing 110
replacing 109
power off the server 14
power on the server 14
power problems 159
power status LED 20
problem determination 157
problems
Ethernet controller 160
hard disk drive 163
intermittent 170
keyboard 167
memory 162
monitor 165
mouse 167
network 171
observable 171
optional devices 167
PCIe 167
power 159, 171
power on and power off 161
serial-device 169
software 173
USB device 167
video 165
processor
install 134
removing 133
replacing 133
processor fan
184 ThinkSystem ST250 Maintenance Manual
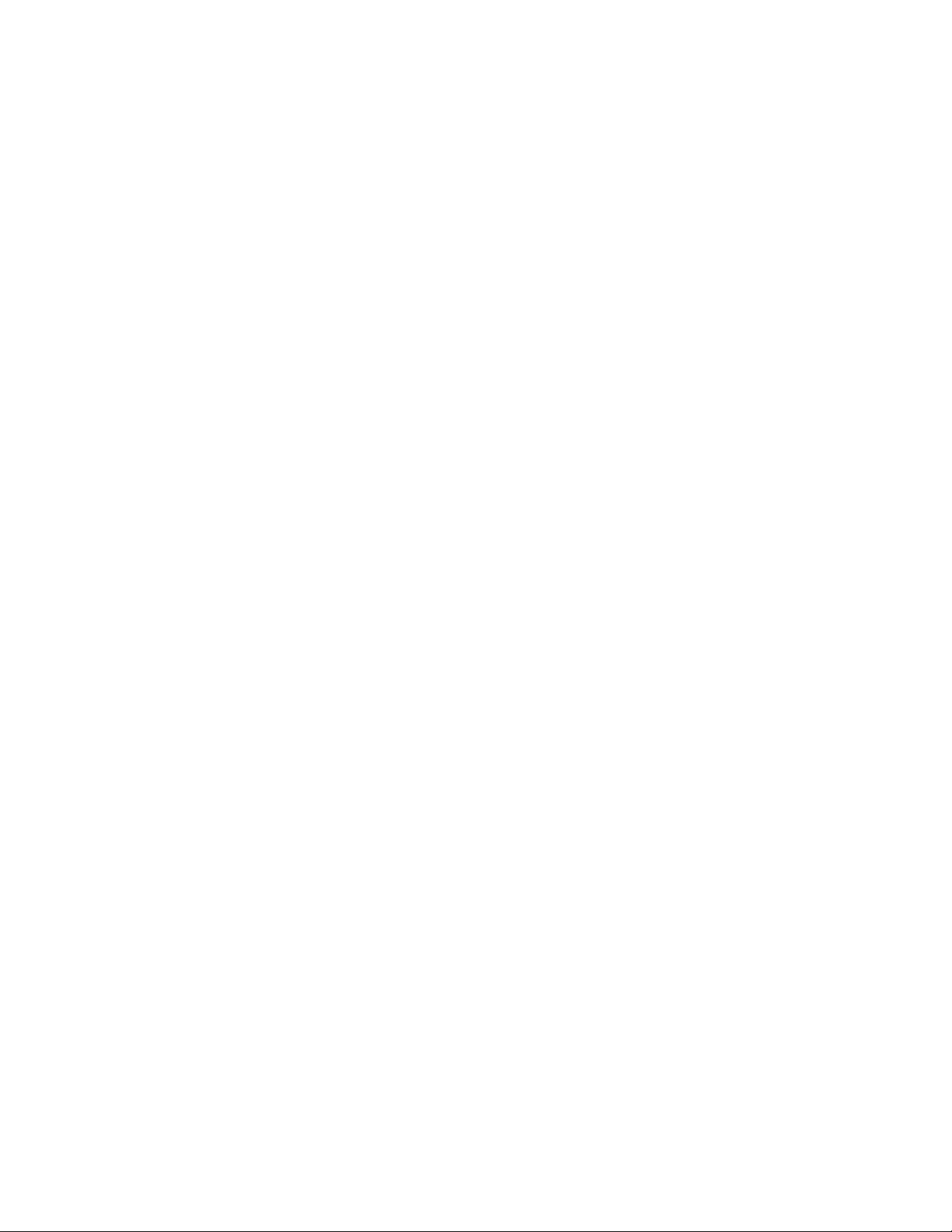
installing 96
removing 95
R
rear system fan
installing 83
removing 82
rear view 24
rear view LED 26
redundant power supply unit
replacing 114
remove
CMOS battery 67
removing
2.5-inch SSD from a 3.5-inch drive bay 64
DIMM 70
drive cage 55
fixed power supply 114
flash power module 85
front bezel 88
front door 90
front panel board assembly 92
front system fan 80
heat sink 95
hot-swap drive 76
hot-swap drive backplane 58
hot-swap power supply 123
intrusion switch 98
M.2 drive 100
optical drive 103
power distribution board 110
processor 133
processor fan 95
rear system fan 82
server cover 136
simple-swap drive 74
simple-swap drive backplate 61
system board 142
tape drive 151
TPM card 153
replacing
2.5-inch SSD from 3.5-inch drive bay 63
backplane 58
CMOS battery 67
DIMM 70
drive 73
drive cage 55
fan 79
fixed power supply unit 114
flash power module 85
front bezel 88
front door 90
front panel board assembly 92
hot-swap drive backplane 58
intrusion switch 98
M.2 drive 100
optical drive 102
PCIe adapter 107
power distribution board 109
processor 133
redundant power supply unit 114
server cover 94, 136
simple-swap-drive backplate 60
system board 141
tape drive 151
TPM card 153
S
safety iii
safety inspection checklist iv
Secure Boot 150
security
integrated cable lock 22
padlock 22
security
front door lock 22
security advisories 13
serial number 145
serial-device problems 169
server components 15
server cover
installing 138
removing 136
replacing 94, 136
server locks
locations 22
server power on or power off problems 161
server, front view 15
service and support
before you call 175
hardware 177
software 177
service data 176
simple-swap drive
installing 75
simple-swap drive backplate
installing 62
removing 61
simple-swap drives
removing 74
simple-swap-drive backplate
replacing 60
software problems 173
software service and support telephone numbers 177
solving
Ethernet controller problems 160
insufficient PCIe resource 167
solving power problems 159
Specifications 3
static-sensitive devices
handling 55
support web page, custom 175
system board
installing 143
removing 142
replacing 141
system board components 29
system error LED 20
system ID button 20
system ID LED 20
system reliability guidelines 54
T
Taiwan BSMI RoHS declaration 181
Taiwan import and export contact information 181
tape drive
installing 152
removing 151
replacing 151
Tech Tips 13
telecommunication regulatory statement 180
telephone numbers 177
TPM 147
TPM 1.2 149
TPM 2.0 149
TPM card 147
installing 154
removing 153
replacing 153
TPM policy 147
TPM version 149
trademarks 180
© Copyright Lenovo 2018, 2022 185

troubleshooting 165, 167, 173
by symptom 160
hard disk drive problems 163
intermittent problems 170
keyboard problems 167
memory problems 162
mouse problems 167
network problems 171
observable problems 171
power on and power off problems 161
power problems 171
serial-device problems 169
symptoms-based troubleshooting 160
USB-device problems 167
video 165
Trusted Platform Module 147
U
UEFI Secure Boot 150
updating,
machine type 145
USB-device problems 167
V
video problems 165
W
warranty 1
working inside the server
power on 55
186 ThinkSystem ST250 Maintenance Manual
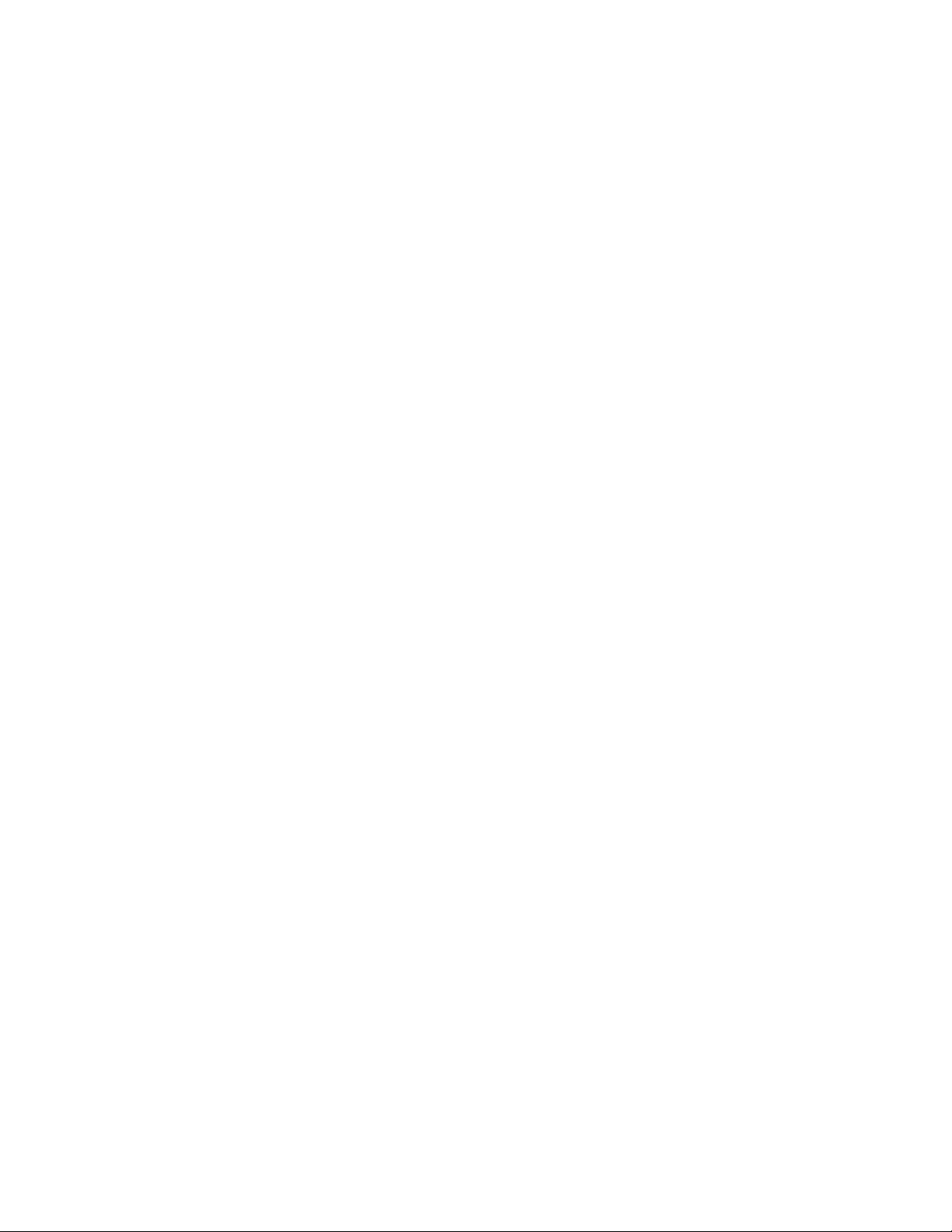

Part Number: SP47A37775
Printed in China
(1P) P/N: SP47A37775
*1PSP47A37775*