Schneider Electric MTN649802 User Manual
Displayed below is the user manual for MTN649802 by Schneider Electric which is a product in the Electrical Actuators category. This manual has pages.
Related Manuals
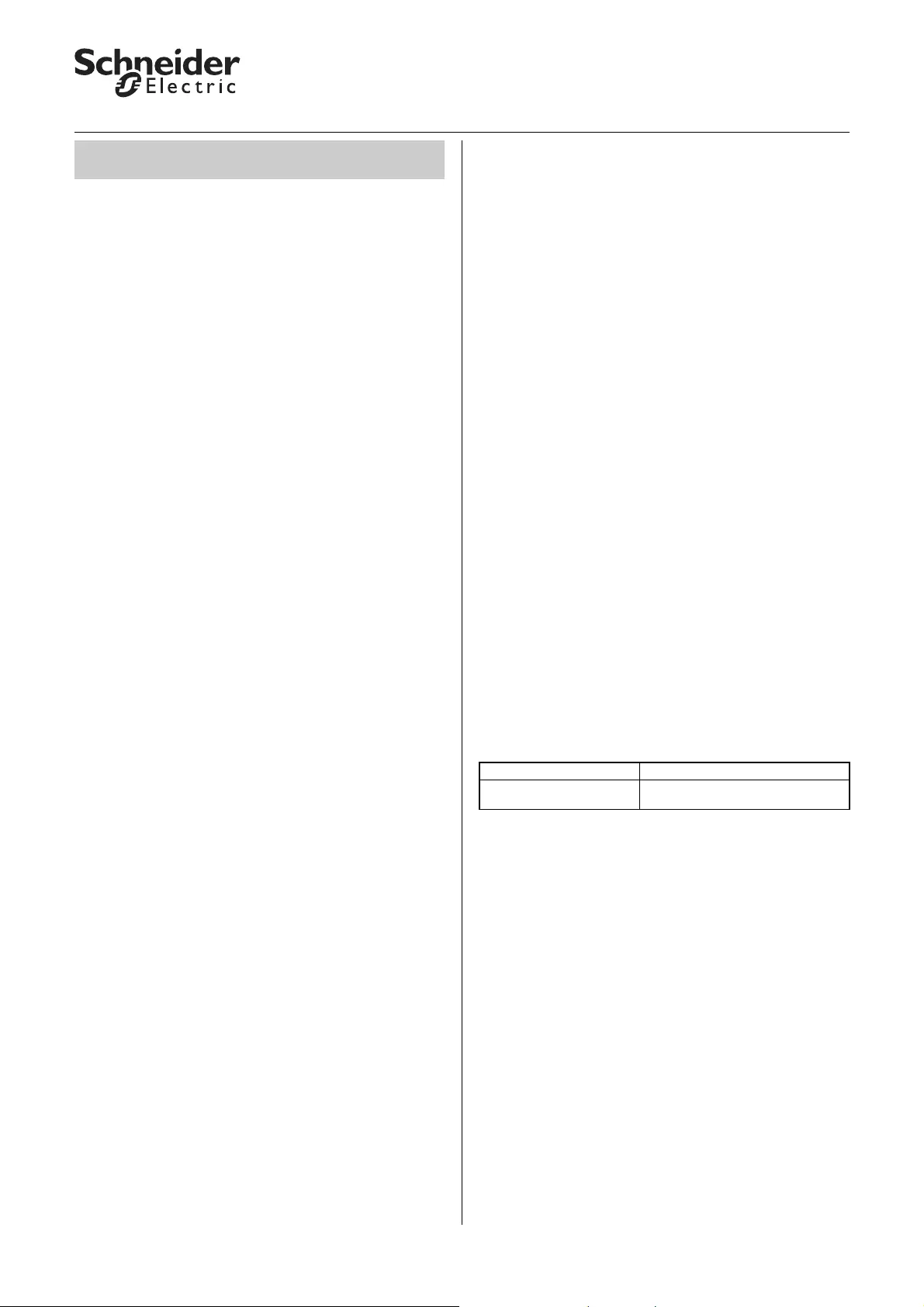
1
KNX Blind actuator REG-K/x/10 with manual mode
Art. no. MTN649802, MTN649804, MTN649808
© 2012 Schneider Electric
Application Shutter.Blind.Safety.Position.Manual 5700/1.1
●General information
This software application allows you to program series
REG K/x/10 blind actuators with manual operation,
which in turn allows you to control connected blind or
roller shutter drives. The ETS allows you to individually
set the type of connected load, as well as the
functions available to it, for each of the blind actuator's
output channels.
You can also operate the blind actuator using the push-
buttons on the front. For more information see the
section "Operation".
All the settings described refer to ETS version 3, but
you can use all the settings and functions with ETS
version 2 as well.
Maximum number of group addresses: 252
Associations: 252
½Caution!
If you switch back to the preset values in either
ETS 2 or ETS 3 (by clicking "Standard"), then all
the values that you have changed so far will be
deleted!
|Note: Due to the fact that various functions
depend on other functions, these dependant
functions are only visible and selectable in the
ETS when the preceding function has been
enabled. If you de-select functions or
parameters, group addresses that have already
been connected may be deleted.
|Note: Due to the fact that the output relays of a
channel are locked against each other, you
cannot switch on both outputs of the channel in
question at the same time.
|Note: The application files (vd2 and vd3) are
configured in such a way that the application
loading time is considerably reduced. When you
convert a ETS 2 project to ETS 3, you lose this
time saving. It therefore makes sense to load
the vd3 file when using ETS 3.
●Application functions
The software application for the blind actuator
provides you with numerous functions, which can be
broken down into three groups. The description of the
functions specifies and explains the parameters that
are relevant for these functions. You will find an
overview of all the parameters of the ETS application
for the blind actuator in the last section "Parameters
and settings“.
Basic functions
These functions allow you to commission the device
and equip it with simple functionality.
– Move height positions and slat opening angle
manually
Advanced functions
– Move height position and slat opening angle using
absolute position commands
– Automatic control
– Calibration/Reference movement
– Disable function for manual operating options
– Preset function
– Scene function
Higher-level functions
Higher-level functions are executed before the basic
function and advanced functions. There are four
higher-level functions:
– Weather alarm
– Alarm function
– Disable function
– Limit travel range
You can select the priorities freely:
A higher-level function only becomes active if there is
no other higher-level function active at the same time.
If a higher-level function is reset and there is another
higher-level function of lower priority active at the
same time, then the actions of the lower priority
function are then carried out.
0.1 Shutter.Blind.Safety.Position.Manual
5700/1.1
Tab Parameter
General Priority sequence of higher-level
functions
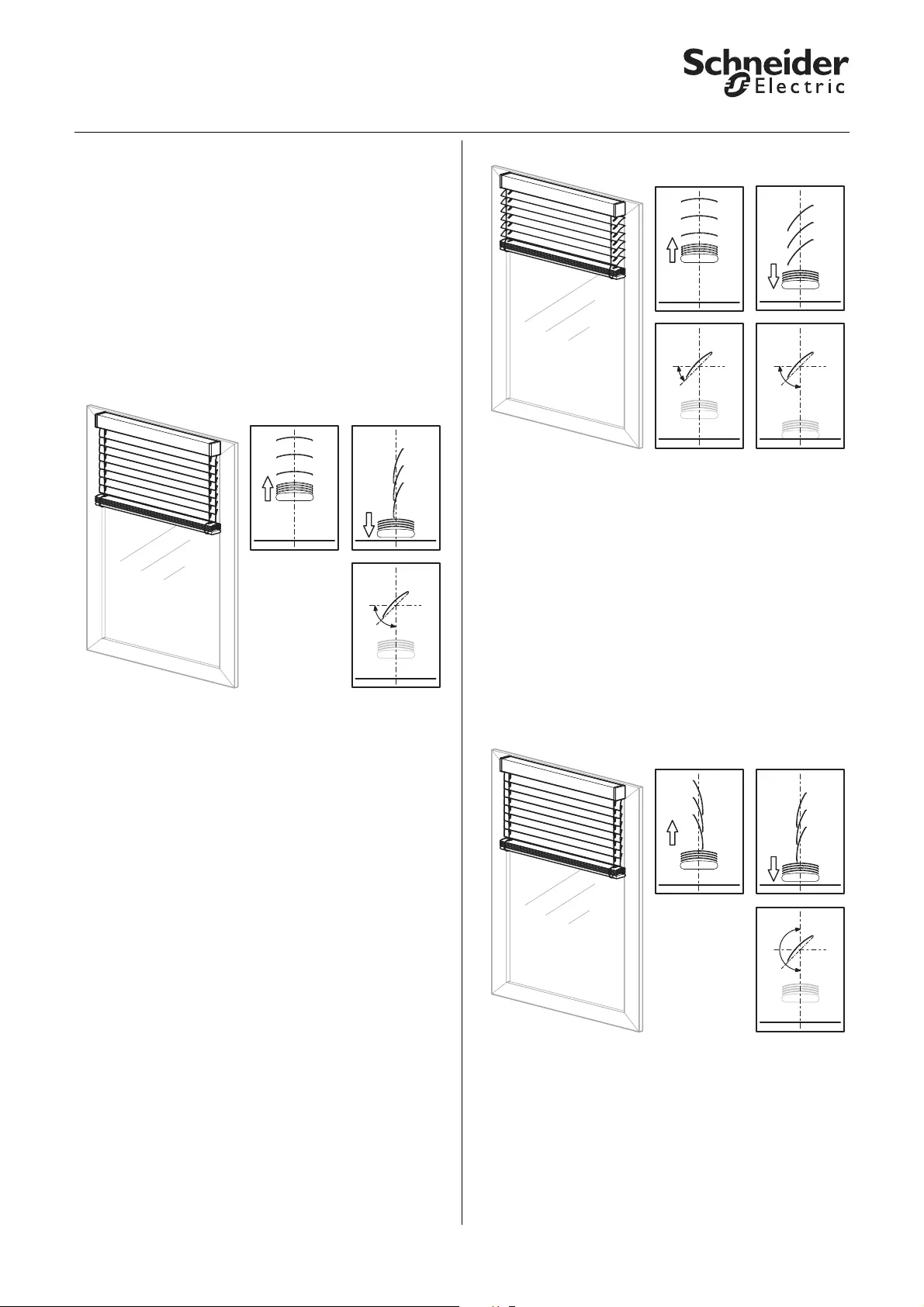
2
KNX Blind actuator REG-K/x/10 with manual mode
Art. no. MTN649802, MTN649804, MTN649808
© 2012 Schneider Electric
Application Shutter.Blind.Safety.Position.Manual 5700/1.1
●Defining blind type
If you want to define parameters for a blind, you need
to specify the type of your blind before you start
programming.
The application differentiates between four types of
blind. You can determine the blind type from the
position of its slats during movement. Two of these
types have a mechanically-determined working
position. You can recognise these by the tilted position
of the slats when moving downwards. The working
position restricts the possible opening angle of the
slats, as long as the blind has not reached its lower
end position.
Blind type 1 (without working position)
– Upward movement: Slats are in a level, opened
position (slat position 0 %)
– Downward movement: Slats are closed
downwards (slat position 100 %)
– Possible regulating range for the opening angle of
the slats: 0–100 %
For each channel, you can use the "Slat position after
movement" parameter to specify the behaviour of the
slats following a movement. If you set the parameter
to "Working position", you can configure the opening
angle that you want the slats to assume after each
downward movement. The preset value of 50 %
corresponds to a slat opening of approximately 45º.
Due to the fact that this position is time-controlled,
please note the section "Running times of the drives".
|Note: Unless stated otherwise, the examples in
the following set of instructions refer to this
type of blind.
Blind type 2 (with working position)
– Upward movement: Slats are in a level, opened
position (slat position 0 %)
– Downward movement: Slats tilted in working
position downwards (slat position in working
position)
– Possible regulating range for the opening angle of
the slats:
0 % to working position, if blind is not in lower end
position
0–100 %, if blind is in lower end position
You can use the parameter "What is the current slat
position on downward movement in %?" to configure
the opening angle for the working position.
Blind type 3 (without working position)
– Upward movement: Slats are closed upwards (slat
position100 %)
– Downward movement: Slats are closed
downwards (slat position 100 %)
– Possible regulating range for the opening angle of
the slats: 0–100 %
0 %
100 %
50 %
100 %
0 %
0 %
0 %
100 %
0 %
0 %
100 %
0 %
100 %
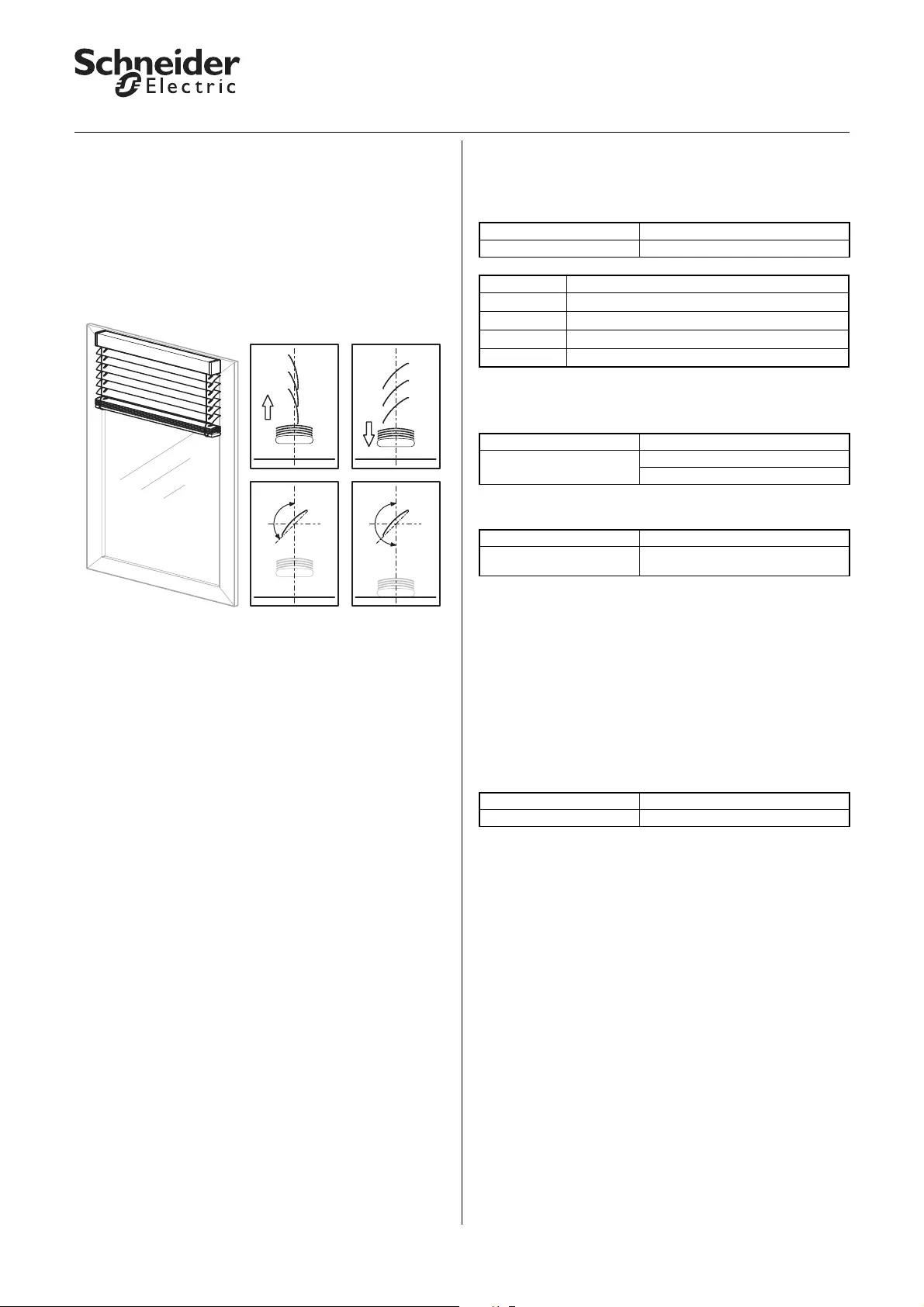
3
KNX Blind actuator REG-K/x/10 with manual mode
Art. no. MTN649802, MTN649804, MTN649808
© 2012 Schneider Electric
Application Shutter.Blind.Safety.Position.Manual 5700/1.1
For each channel, you can use the "Slat position after
movement" parameter to specify the behaviour of the
slats following a movement. If you set the parameter
to "Working position", you can configure the opening
angle that you want the slats to assume after each
downward movement. The default value of 50%
corresponds to a slat opening of approximately 45º.
Due to the fact that this position is time-controlled,
please note the section "Running times of the drives".
Blind type 4 (with working position)
– Upward movement: Slats are closed upwards (slat
position100 %)
– Downward movement: Slats tilted in working
position downwards (slat position in working
position)
– When the lower end position is reached, the slats
are closed (slat position 100 %)
– Possible regulating range for the opening angle of
the slats:
0 % to working position, if blind is not in lower end
position
0–100 %, if blind is in lower end position
You can use the parameter "What is the current slat
position on downward movement in %?" to configure
the opening angle for the working position.
What blind type to select in the ETS?
For the corresponding blind type setting, you can
configure the "How does the existing blind move?"
parameter in the "X: Blind" tab as follows:
Also configure the following parameters.
For type 1 and 3:
For type 2 and 4:
Slat adjustment function
Every time the blind moves, the position of the slats
also changes depending on the direction of
movement. After movement, the slats remain in this
new position. This application, however, allows you to
automatically adjust or reset the position of the slats
after a movement.
Use the "Slat position after movement" parameter to
specify the behaviour of the slats after a movement
for each blind channel.
The following parameters are available:
– no response (slats remain in the current position)
– working position (slats are moved into the working
position)
– last slat position (the slats resume the opening
position that they had before the movement
started)
The slat opening angle that you specify here is applied
after every positioning movement of the blind and also
after every manual movement command ended by a
stop telegram.
After a bus voltage failure or a download, the last slat
position is not clearly defined. As a result, the
corresponding working position is used as the last slat
position.
0 %
0 % 0 %
100 %
Tab Parameter
X: Blind How does the existing blind move?
Blind type Setting
1 downwards closed / upwards level
2 downwards tilted / upwards level
3 downwards closed / upwards closed
4 downwards tilted / upwards closed
Tab Parameter
X: Blind Slat position after movement
Slat working position in %
Tab Parameter
X: Blind What is the current slat position on
downward movement in %
Tab Parameter
X: Blind Slat position after movement
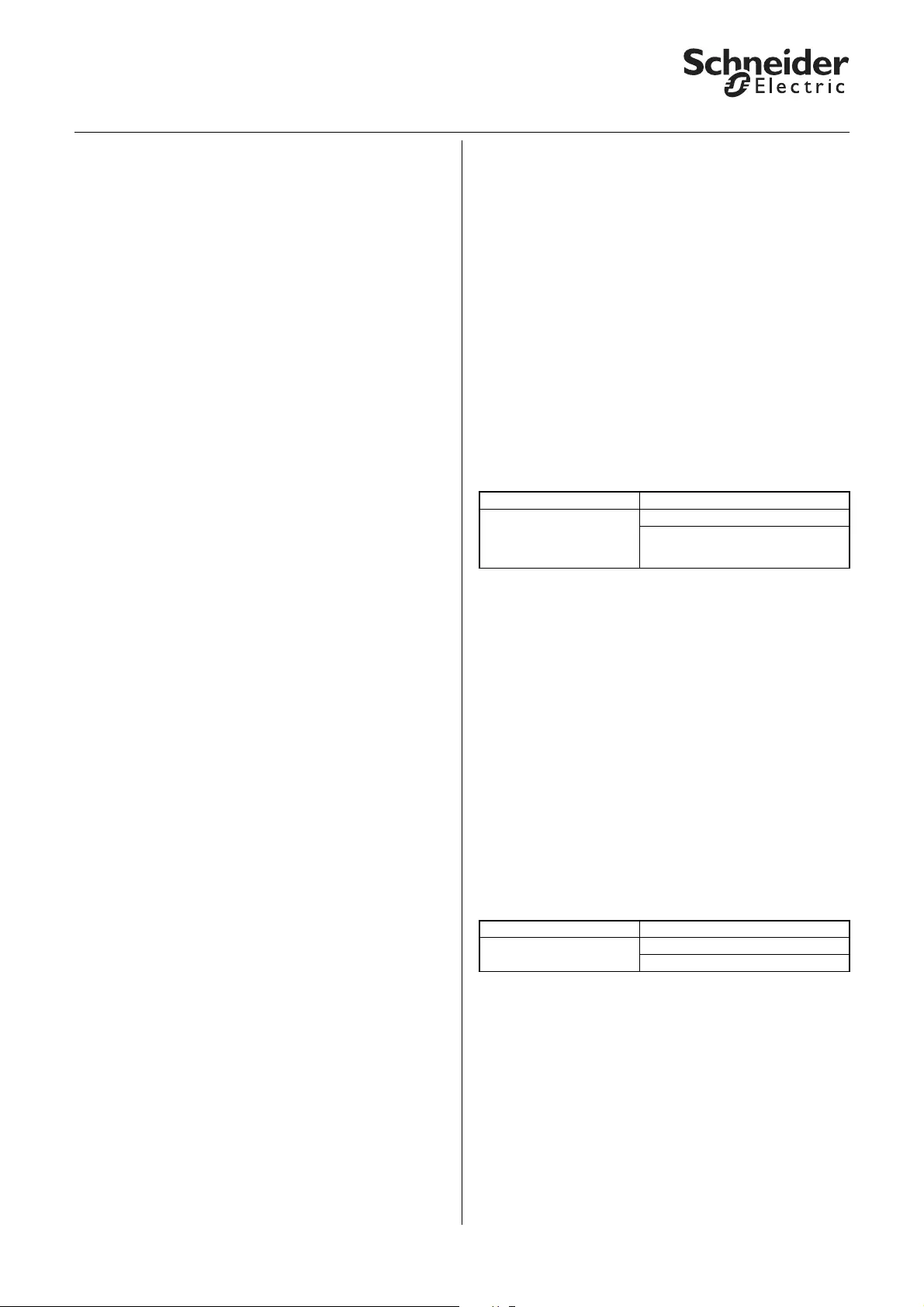
4
KNX Blind actuator REG-K/x/10 with manual mode
Art. no. MTN649802, MTN649804, MTN649808
© 2012 Schneider Electric
Application Shutter.Blind.Safety.Position.Manual 5700/1.1
Running times of the drives
|Note: Selecting the smallest possible value as
the time basis in each case allows you to
achieve the most precise results for the internal
device time setting.
The importance of the drive running times setting
depends on the desired control task for the blind or
roller shutter.
The application provides you with the following
parameters for setting running times:
– Height running time
– Slat step interval (for blind function)
– Slat running time (for blind function)
– Pause on reverse for change of direction
You also have various options for compensating small
time deviations caused by physical conditions or
technical drive properties:
– Running time upwards supplement
– Dead time until upwards movement
– Start-up delay
– Run-out delay
– Slat open up start-up supplement (for blind function)
– Slat open down start-up supplement (for blind
function)
Selecting the smallest possible value as the time basis
in each case allows you to achieve the most precise
results for the internal device time setting.
Tips for setting values
If the running times to be set are too short to measure
with the clock, then set an approximate value for the
time being. Use position commands to test the
behaviour of the drive or the slats. If the desired
positions are not fully reached, then correct the
running times upwards. If the positions are overshot,
then correct the running times downwards. Use new
position commands to check your corrections. Carry
out several tests because you will only see or detect
the small discrepancies after a few movements.
When making corrections, it makes sense to change
the value for the running time factor and to leave the
value for the running time basis the same.
In addition to the discrepancies mentioned,
environmental factors (temperature, rain etc.) also
lead to variations in the movement behaviour of the
drives. Due to the fact that the drives cannot report
their current position and the current position can't
always be calculated, the blind actuator cannot detect
these discrepancies. In order to continue to be able to
position the drive precisely, it makes sense to return
the drives to a fixed starting position by means of
regular reference movements. This allows you to
achieve satisfactory positioning precision for a long
time.
For more information, refer to the section "Calibration/
Reference movement".
Running times for basic function
You only have to measure and set the following
running times in order to configure a simple basic
function:
Height running time
The running time is always comprised of the time
basis multiplied by the factor, e.g. (default value):
100 ms * 1200 = 120 s
The drive needs this period of time to move out of one
end position (blind/roller shutter is fully open or closed)
into the opposite end position. When the set running
time expires, the relay of the corresponding channel is
automatically switched off (even if the drive with the
values set here has not fully reached its end position).
You may want to check whether the drive
manufacturer has made any specifications regarding
running times.
Slat step interval (only for blind)
Step commands allow you to turn the blind slats. You
can change the opening angle of the slats gradually, to
prevent glare when the sun changes position for
example. Time basis multiplied by factor allows you to
configure the duration of this kind of gradual rotation.
Example (default values):
10 ms * 10 = 100 ms
Depending on the total running time in one direction of
movement, the step interval allows you to provide the
user with a certain number of steps for opening or
closing the slats.
If the running time is 2.5 s for example, then the drive
needs approx. 25 steps to go through the entire slat
opening range in one direction (2.5 s / 100 ms = 25
steps).
Tab Parameter
X: Drive Time basis for height running time
Factor for height running time (10-
64000)
1 second = 1000 ms
Tab Parameter
X: Drive Time basis for slat step interval
Factor for slat step interval (5-255)
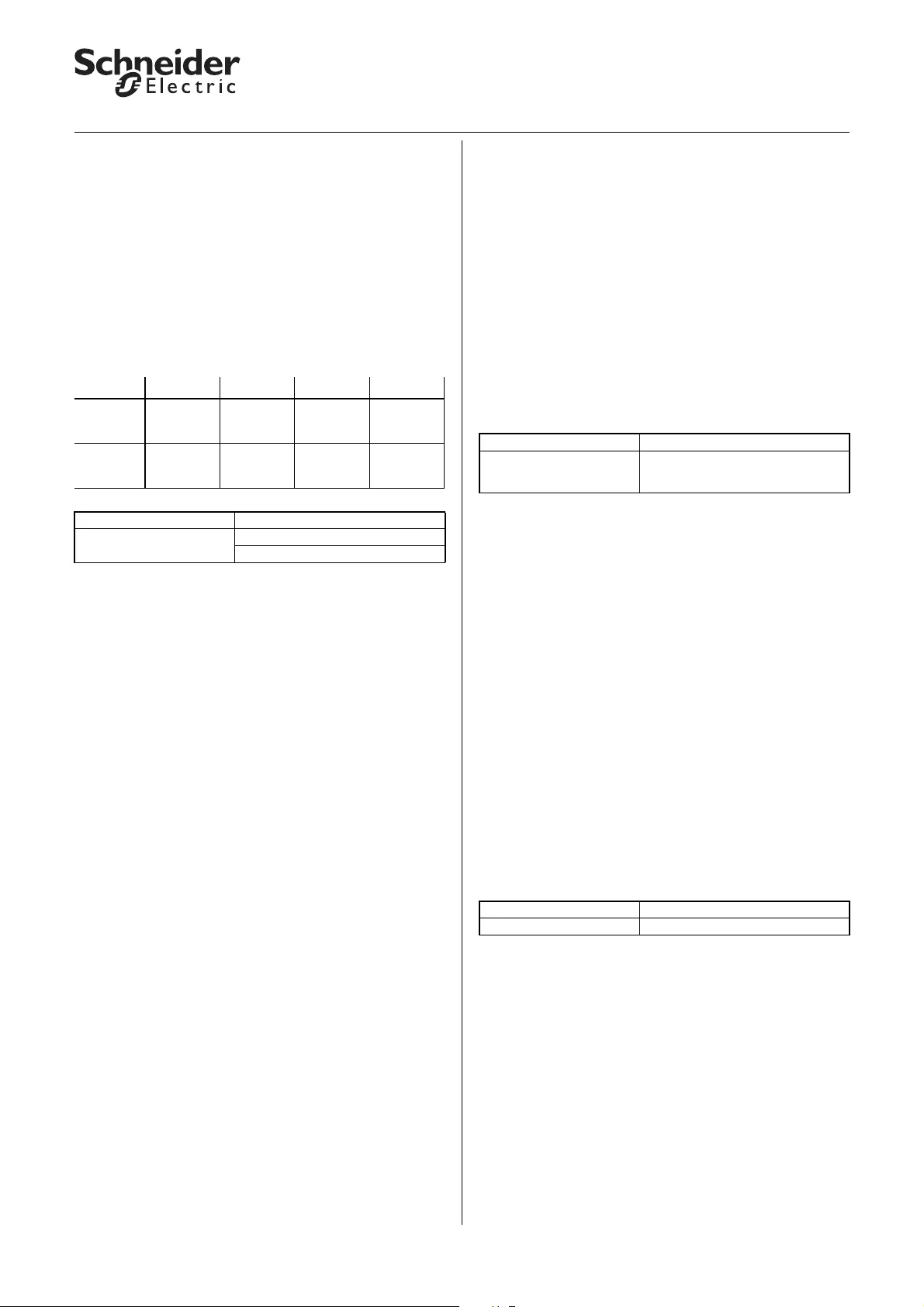
5
KNX Blind actuator REG-K/x/10 with manual mode
Art. no. MTN649802, MTN649804, MTN649808
© 2012 Schneider Electric
Application Shutter.Blind.Safety.Position.Manual 5700/1.1
Using the same example, if you only want to give the
user five slat steps:
2.5 s / 5 steps = 0.5 s step interval
Leave the time basis of the step interval at 10 ms and
set the factor of the step interval to 50:
10 ms * 50 = 0.5 s step interval
Slat running time (only for blind)
The slat running time is the period of time it takes the
slat to complete a full movement from 0% to 100% (or
vice versa). The regulating range through which the
opening angle passes depends on the type of blind in
use:
Example (default values):
10 ms * 100 = 1000 ms = 1 s
How to measure small slat running times:
– Move the slats into the closed position (slat position
100 %). This is the lower end position for blind
types with working position.
– Count step commands: Now send step commands
until the blind moves up, counting the number of
steps required.
Example: The blind requires five steps to go
through the slat regulating range. The blind moves
upwards on the sixth step.
– The step interval values set (default step interval:
100 ms) is used to calculate the slat running time:
100 ms * 5 steps = 0.5 s
How to measure large slat running times
– Move the slats into the closed position (slat position
100 %). This is the lower end position for blind
types with working position.
– Now send a movement command upwards.
Before the drive opens the blind, the slats turn into
the open position (0 %).
Measure the time it takes them to turn.
– Stop the drive after turning.
– For blind type 2 and 4 (with working position),
ensure that the closed slat position is not engaged
until in the lower end position. Then also add on the
time it takes to turn from the working position to the
closed position.
|Note: For blind types 1 and 3 (without working
position) your setting for the slat running time
influences the opening angle after a movement.
This is because the selected opening angle
(percentage of automatic slat position) is
converted into a percentage turning time for the
slats. The same applies for the slat adjustment
function after a movement.
Pause on reverse for change of direction
When the blind actuator of a drive that is currently
moving receives a command to move in the opposite
direction, then it first switches off both output relays
for this channel. Before it switches on the relay for the
new direction, it waits for the pause on reverse
interval to pass. Set the length of the pause on reverse
using the factor:
100 ms is the underlying time basis. Example (default
values):
5 * 100 ms (fixed value) = 500 ms
The blind actuator also observes the pause on reverse
if, when executing two step commands, it has to turn
the slats in different directions.
½Caution!
Pauses on reverse that are too short could
cause damage to the drive.
When setting values, observe the
manufacturer's specifications for the drive
under all circumstances.
Running times for advanced functions and
positioning commands
The advanced functions and direct positioning
commands allow you to move the connected blinds or
roller shutters into the desired position directly and, in
the case of blinds, configure the opening angle of the
slats also.
Due to the fact that the actuated drive cannot provide
any status feedback on its position, these positioning
movements are time controlled. Here it is important to
set the running time parameter as precisely as
possible because the more precisely you set this
parameter, the more precisely the desired position can
be determined and engaged. This is particularly the
case for buildings that demand sophisticated blind
control.
Positioning will be more precise the slower and longer
a drive moves.
Type 1 Type 2 Type 3 Type 4
Slat
position
0%
level open level open up closed up closed
Slat
position
100 %
down
closed down
closed down
closed down
closed
Tab Parameter
X: Drive Time basis for slat running time
Factor for slat running time (5-255)
Tab Parameter
X: Drive Pause on reverse for change of
direction (1-255) factor * 100 ms,
manufacturer data!
Tab Parameter
X: Drive Advanced drive parameter
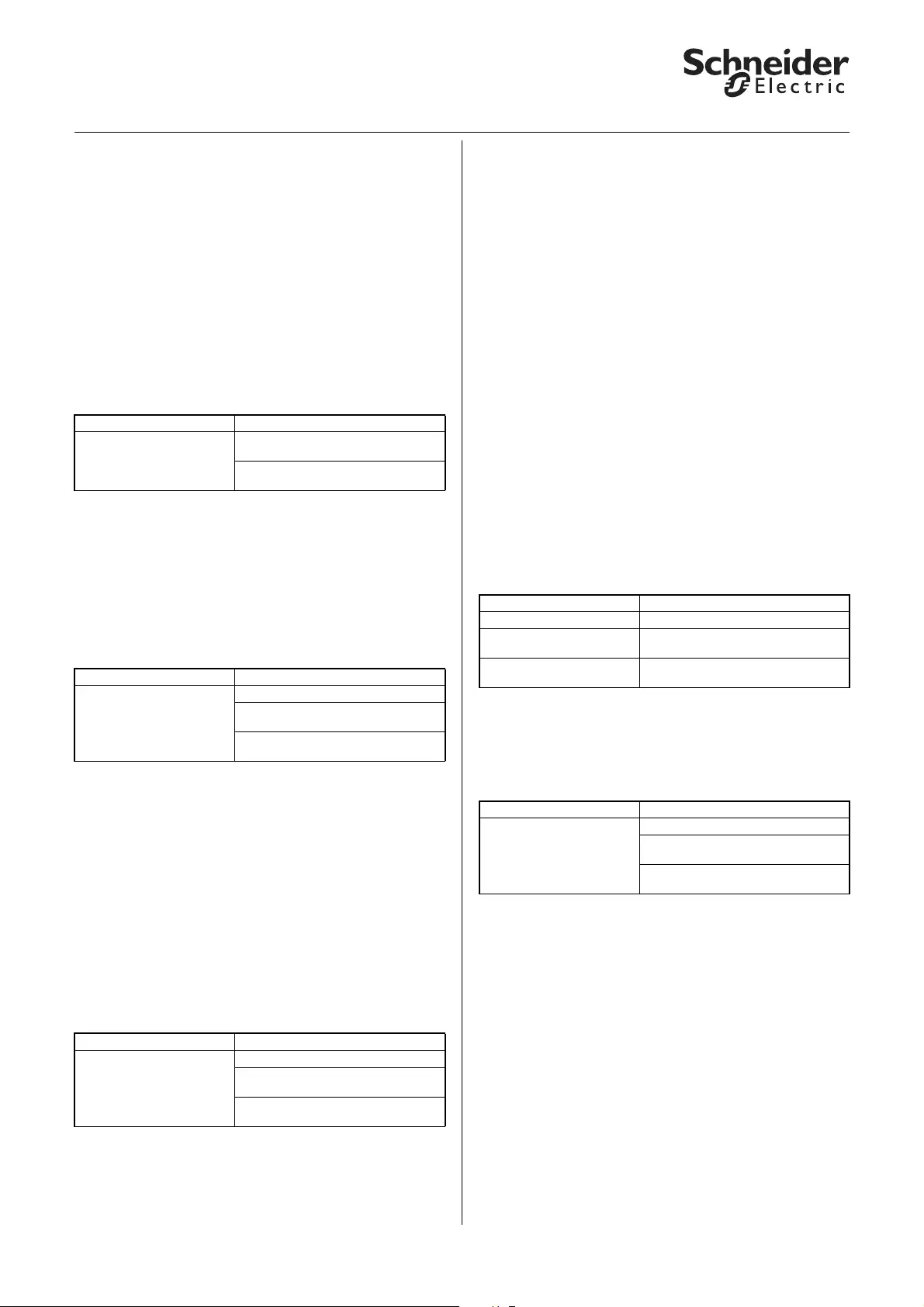
6
KNX Blind actuator REG-K/x/10 with manual mode
Art. no. MTN649802, MTN649804, MTN649808
© 2012 Schneider Electric
Application Shutter.Blind.Safety.Position.Manual 5700/1.1
The settings for the height running time have already
been explained. You can also set the following
parameters contingent upon physical circumstances
and the drive.
Running time upwards supplement
The running time supplement only applies for upward
drive movements. This is due to the physical fact of
gravity: it takes drives longer to move up than down.
Due to the fact that this time variation can be very
short, you need to carry out a few movements in order
to become aware of this behaviour. It's a good idea to
move the drive from 10% to 90% and back to 10%
again a few times. If, after these movements, you
observe that the drive doesn't quite reach the top end
position any more, you can compensate as follows:
Example (default values):
10 ms * 20 = 200 ms
Dead time until upwards movement
If, when in the closed lower end position, the used
blind experiences dead time between the time when
the main band is activated and the first upward
movement, then you can compensate for this delay as
follows:
Example:
10 ms * 10 = 100 ms
You can also use the dead time to compensate for the
roller shutter opening when using a roller shutter.
Start-up delay / Run-out delay
Some motors do not achieve maximum output
immediately when they are switched on, but a few
milliseconds later. You can compensate for this using
the start-up delay time setting.
Some motors continue to run for a few milliseconds
after they have been switched off. If you observe this
behaviour, then you can compensate with the settings
for run-out delay.
Start-up delay example:
10 ms * 2 = 20 ms (with a time basis of 10 ms)
Slat running time with time-controlled positioning
In addition to the specifications already described for
the slat running times, the following values apply in
the case of time-control positioning:
– 0 %: Slats open or in the top closed position
– 100 %: Slats closed or in the bottom closed position
The resulting opening angle depends on the type of
blind in use.
The device converts the set slat running time to a
value between 0% and 100% accordingly and
calculates the resulting travel times for the desired
position commands.
Start-up supplement
When opening the slats, some blind types need an
extra start-up supplement until the slats start to
respond depending on the tightening and loosening of
the slat cords. This depends on the current position of
the slats. You can use the following parameter to set a
start-up supplement for both the top and bottom slat
position.
These parameters allow you to set the start-up delay
for an upwards movement until the slat turns when
the slats are in the open position (0%) (the previous
blind movement was an upwards movement):
The start-up delay until the slat turns that you specify
here is always considered when the blind is opened if
the slats are in the closed position (100 %) (the
previous blind movement was a downwards
movement):
|Note: For every slat movement, it is assumed
that the drive is switched on for a minimum
running time. This minimum running time of the
slat results from the switching capacity of the
blind actuator's relay and is approx. 20 ms. Slat
movements that are mathematically less than
20 ms are not carried out.
Tab Parameter
X: Drive Shared time basis for running time
supplements/dead time
Factor for running time upwards
supplement
Tab Parameter
X: Drive Advanced drive parameter
Shared time basis for running time
supplements/dead time
Factor for dead time to upward
movement (1-255)
Tab Parameter
X: Drive Advanced drive parameter
Factor for start-up delay
Factor * 10 ms
Factor for run-out delay
Factor * 10 ms
Tab Parameter
X: Drive Advanced drive parameter
Shared time basis for running time
supplements/dead time
Factor for slat open up start-up
supplement
Tab Parameter
X: Drive Advanced drive parameter
Shared time basis for running time
supplements/dead time
Factor for slat open down start-up
supplement
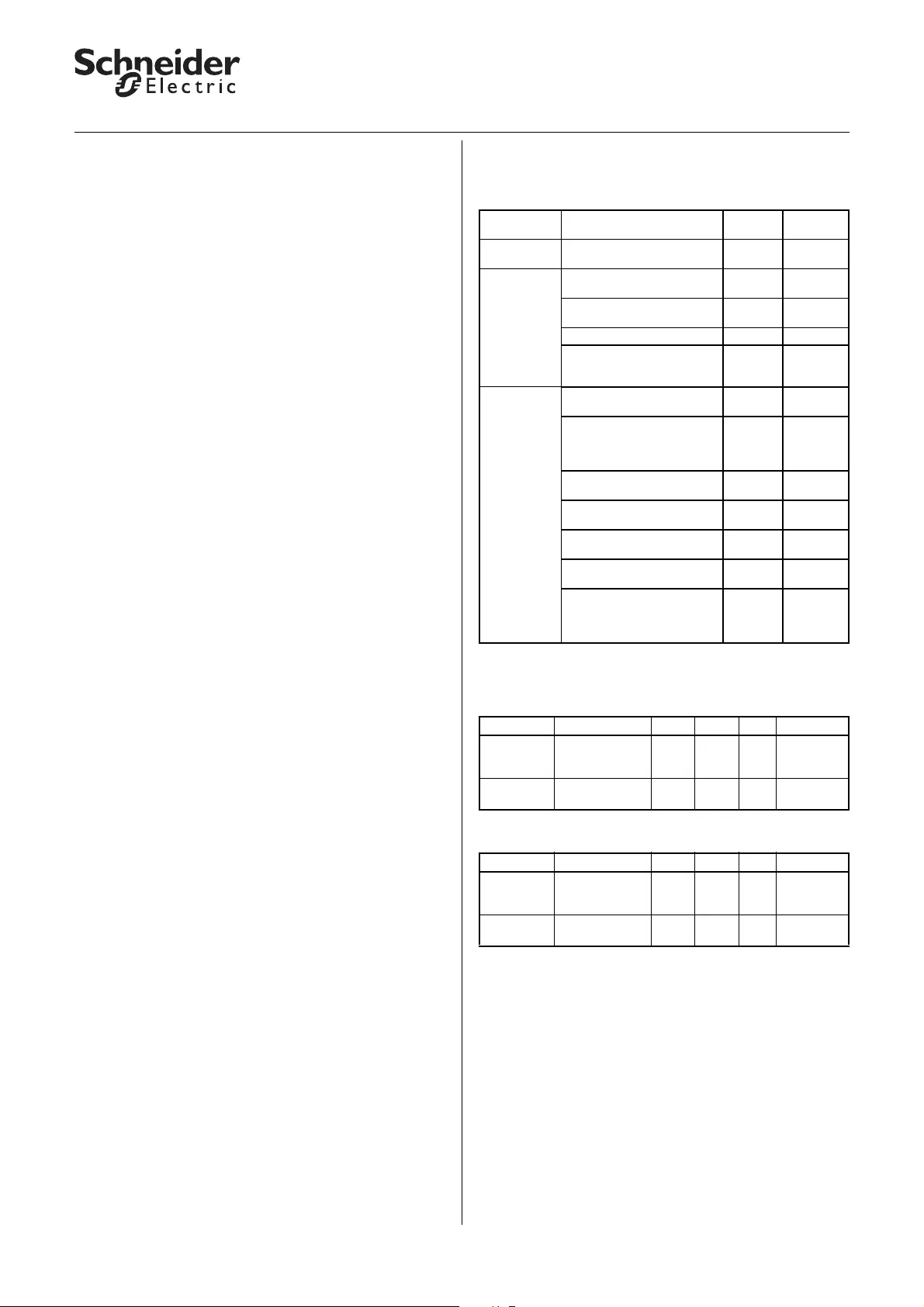
7
KNX Blind actuator REG-K/x/10 with manual mode
Art. no. MTN649802, MTN649804, MTN649808
© 2012 Schneider Electric
Application Shutter.Blind.Safety.Position.Manual 5700/1.1
●Basic functions: Moving height position and slat
opening angle manually
The basic function allows you to move the connected
drive into the desired position manually. You have two
communication objects to do this: "Manual movement
object" and "Manual stop/step object" (for roller
shutters: "Manual stop/step object").
– Move drive
The "Manual movement object" is responsible for
opening and closing the blind or the roller shutter.
When the value "1" is received, the drive moves
down; "0" moves it up.
– Running time
The active output remains active until the set
running time expires. If a new movement command
in the same direction is received, then the drive
continues moving.
– Pause on reverse for change of direction
If, during a drive movement, a control command in
the opposite direction is received, then the drive
stops and waits for the defined pause on reverse
time before moving in the new direction of
movement.
– Stop drive
When a drive that is currently moving receives a bus
telegram for the "Manual stop/step object" (for roller
shutters: "Manual stop/step object"), it stops. The
object value received is irrelevant.
– Slat adjustment
If the drive has been stopped, then the slats are
turned into the desired position depending on the
settings for the "Slat position after movement"
parameter.
– Turn blind slats
The "Manual stop/step object" allows you to adjust
the opening angle of the slats gradually for blinds.
The drive must be idle. If the communication object
receives the object value "1", then the slats are
closed by one increment; if "0" is received, they
open by one (type 1).
Note the following special cases:
1. If a step command is executed and the slats
subsequently reach the limit of their possible
movement range or if they are already in a
maximum position, then the drive moves briefly in
the desired direction. The duration of this
movement also corresponds to the set step time.
2. If the direction changes from one step command to
the next, then the device waits the pause on
reverse time between steps in this case also.
Parameter settings in the ETS:
Set the following parameters for this function in the
ETS:
Communication objects
Communication objects for blind:
Communication objects for roller shutters:
Tab Parameter Blind Roller
shutter
Channel
configuration Channel X operating mode X X
X: Blind How does the existing blind
move? X
Slat position after
movement X
Slat working position in % X
What is the current slat
position on downward
movement in %
X
X: Drive Time basis for height
running time XX
Factor for height running
time
(10-64000)
1 second = 1000 ms
XX
Time basis for slat step
interval X
Factor for slat step interval
(5-255) X
Time basis for slat running
time X
Factor for slat running time
(5-255) X
Pause on reverse for
change of direction (1-255)
factor * 100 ms,
manufacturer data!
XX
Function Object name Type Prio Flags Behaviour
Blind Manual
movement
object
1 bit Low WC Receive
Blind Manual stop/
step object 1 bit Low WC Receive
Function Object name Type Prio Flags Behaviour
Roller
shutter Manual
movement
object
1 bit Low WC Receive
Roller
shutter Manual stop
object 1 bit Low WC Receive
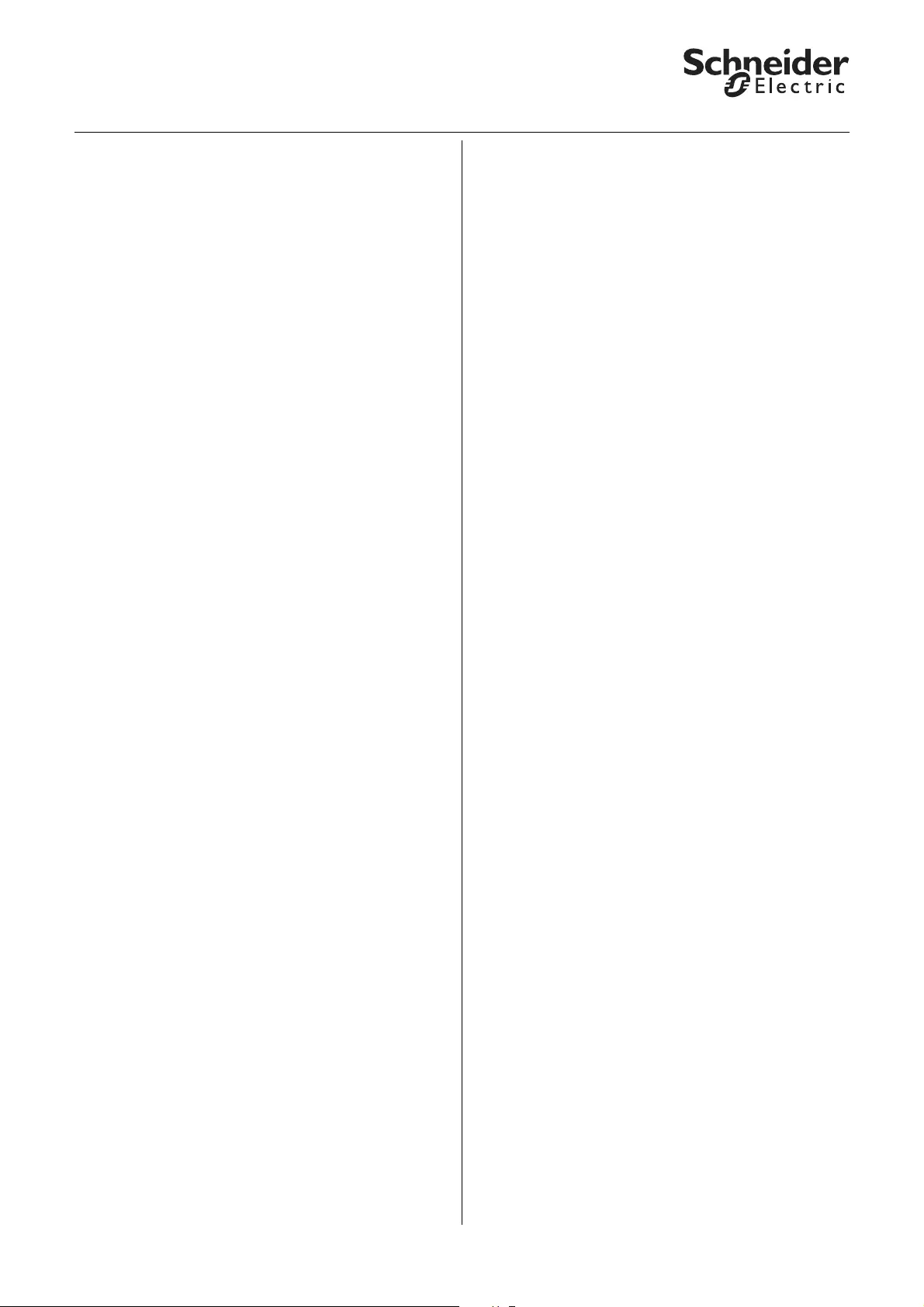
8
KNX Blind actuator REG-K/x/10 with manual mode
Art. no. MTN649802, MTN649804, MTN649808
© 2012 Schneider Electric
Application Shutter.Blind.Safety.Position.Manual 5700/1.1
Settings for this function:
– "Manual movement object" = "0": Blind/Roller
shutter open
– "Manual movement object" = "1": Blind/Roller
shutter close
– Drive is moving and "Manual stop/step object" or
"Manual stop object" = "0" or "1": Stop drive
Extra for blinds:
– Drive is idle and "Manual stop/step object" = "0“:
Slats one step upwards
– Drive is idle and "Manual stop/step object" = "1“:
Slats one step downwards.
Special cases:
– Slats in top end position (slat position 0 %) and
"Manual stop/step object" = "0": Drive moves one
step upwards
– Slats in bottom end position (slat position 100 %)
and "Manual stop/step object" = "1": Drive moves
one step downwards.
●Advanced functions: Move height position and
slat opening angle using absolute position
commands
This function allows you to manually set a height
position, and in the case of blinds the opening angle of
the slats, directly using a percentage value. The
desired percentage value always relates to the
possible movement range of 0–100 % that you set by
specifying the running times. You therefore set an
absolute height position for the entire movement
range.
After receiving a new positon value, the blind actuator
calculates a proportional movement time from the
current position and the new desired position and then
moves the drive in the corresponding direction of
movement for this period of time. The new position is
buffered. The precision of the position settings
depends on the precision of your settings for the drive
running times.
After a few position movements, there will be minimal
deviations between the actual position and the
calculated position for physical and mechanical
reasons. You can reset these deviations with
reference movements.
If a reference movement is necessary before a new
position movement, then the blind actuator allows this
to be carried out before moving into the new setpoint
position (see the section "Calibration/Reference
movement").
The communication objects "Manual height position"
and "Manual slat position" (for blinds) allow you to set
the absolute position values.
– Set height position
The "Manual height position" object is responsible
for the height position of the blind or roller shutter.
The limit position 0 % means that the blind/roller
shutter is fully up. If 100% is set, then the blind/
roller shutter is fully down.
– Turn slats into opening position
The "Manual slat position" object allows you to set
the slat opening angle directly. In slat position 0 %
the slats are horizontally open or closed up. At
100 % they are closed down. The actual opening
angle of the slats depends on the type of blind in
use.
When it receives a new position value, the blind
actuator calculates the running time necessary to
reach the new position from the current position. Then
the drive is moved to the new position for the
calculated period of time. The calculation also
determines the direction of travel. If, during a
positioning movement, the device receives a new
position value and the calculation results in the same
direction of travel, then the drive continues moving
until it reaches the new setpoint postion.
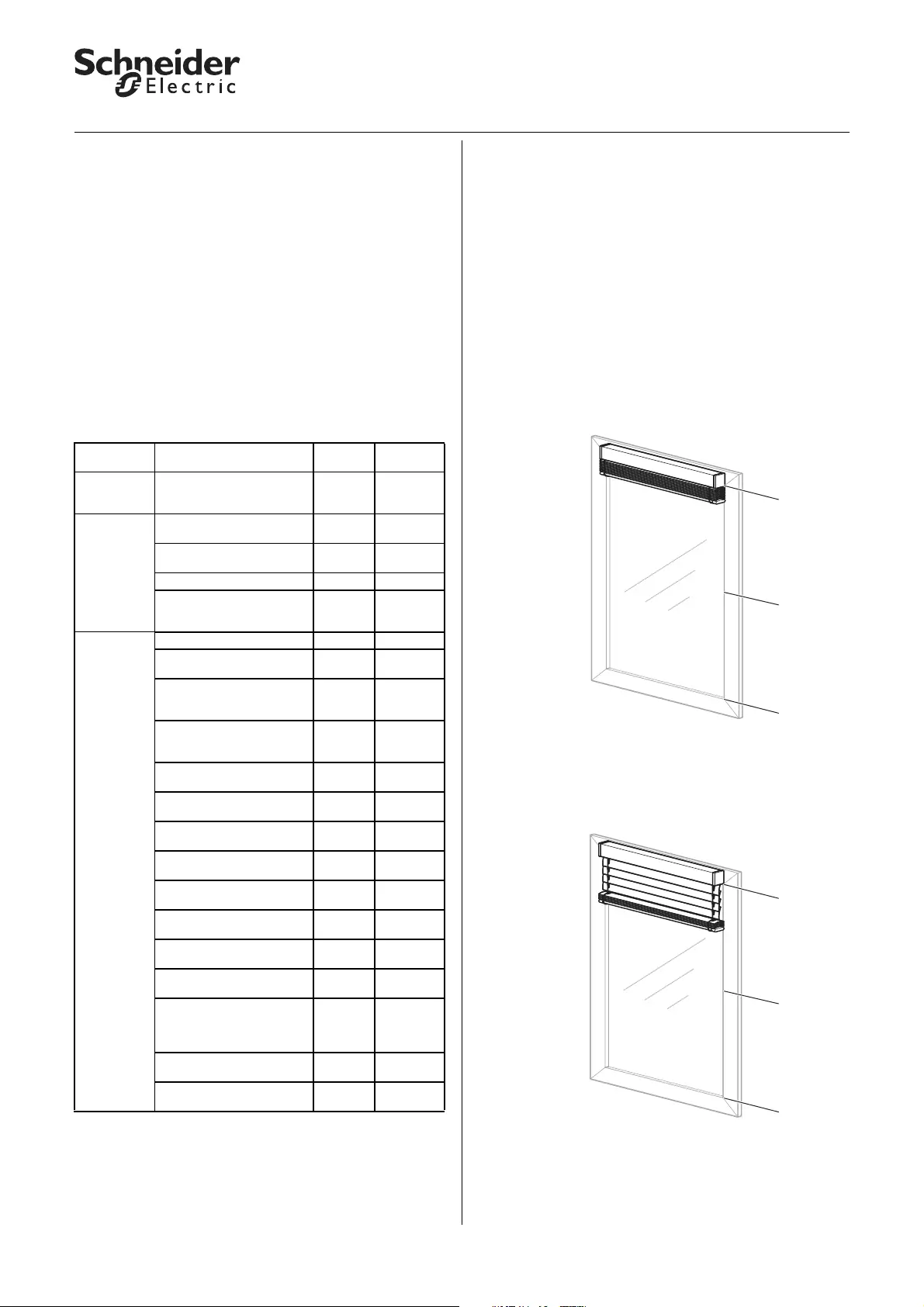
9
KNX Blind actuator REG-K/x/10 with manual mode
Art. no. MTN649802, MTN649804, MTN649808
© 2012 Schneider Electric
Application Shutter.Blind.Safety.Position.Manual 5700/1.1
– Pause on reverse for change of direction
If, during a drive movement or slat adjustment, a
new position command is recieved and the
calculation results in the opposite direction of travel,
then the drive stops and waits for the defined pause
on reverse time before starting the new position
movement.
– Slat adjustment
When the height position of the blind is changed
and the blind reaches the desired position, then the
slat adjustment function is carried out and the slats
are moved into the desired position.
Parameter settings in the ETS:
Set the following parameters for this function in the
ETS:
Application examples
The following examples show the running times that
result in order to reach certain positions.
Starting position and set values:
– Blind type 1, working position 50 %, slat
adjustment = working position
– Running times:
Start-up delay disabled
Run-out delay disabled
Slat open up/down start-up supplement disabled
Height running time 120 s
Running time supplement upwards 0.2 s
Slat running time 2.5 s
– Current height position 0 % (blind up)
– Current slat position 0 % (slats open)
New height position: 50 %
Step 1:
Close slats for downwards movement = 2.5 s
(Slat running time from 0 % to 100 %)
Tab Parameter Blind Roller
shutter
Channel
configuratio
n
Channel X operating mode X X
X: Blind How does the existing
blind move? X
Slat position after
movement X
Slat working position in % X
What is the current slat
position on downward
movement in %
X
X: Drive Advanced drive parameter X X
Time basis for height
running time XX
Factor for height running
time (10-64000)
1 second = 1000 ms
XX
Shared time basis for
running time supplements/
dead time
XX
Factor for running time
upwards supplement XX
Factor for dead time until
upwards movement XX
Factor for slat open up
start-up supplement X
Factor for slat open down
start-up supplement X
Time basis for slat step
interval X
Factor for slat step interval
(5-255) X
Time basis for slat running
time X
Factor for slat running time
(5-255) X
Pause on reverse for
change of direction (1-255)
Factor * 100 ms,
manufacturer data!
XX
Factor for start-up delay
Factor * 10 ms XX
Factor for run-out delay
Factor * 10 ms XX
0 %
50 %
100 %
0 %
50 %
100 %
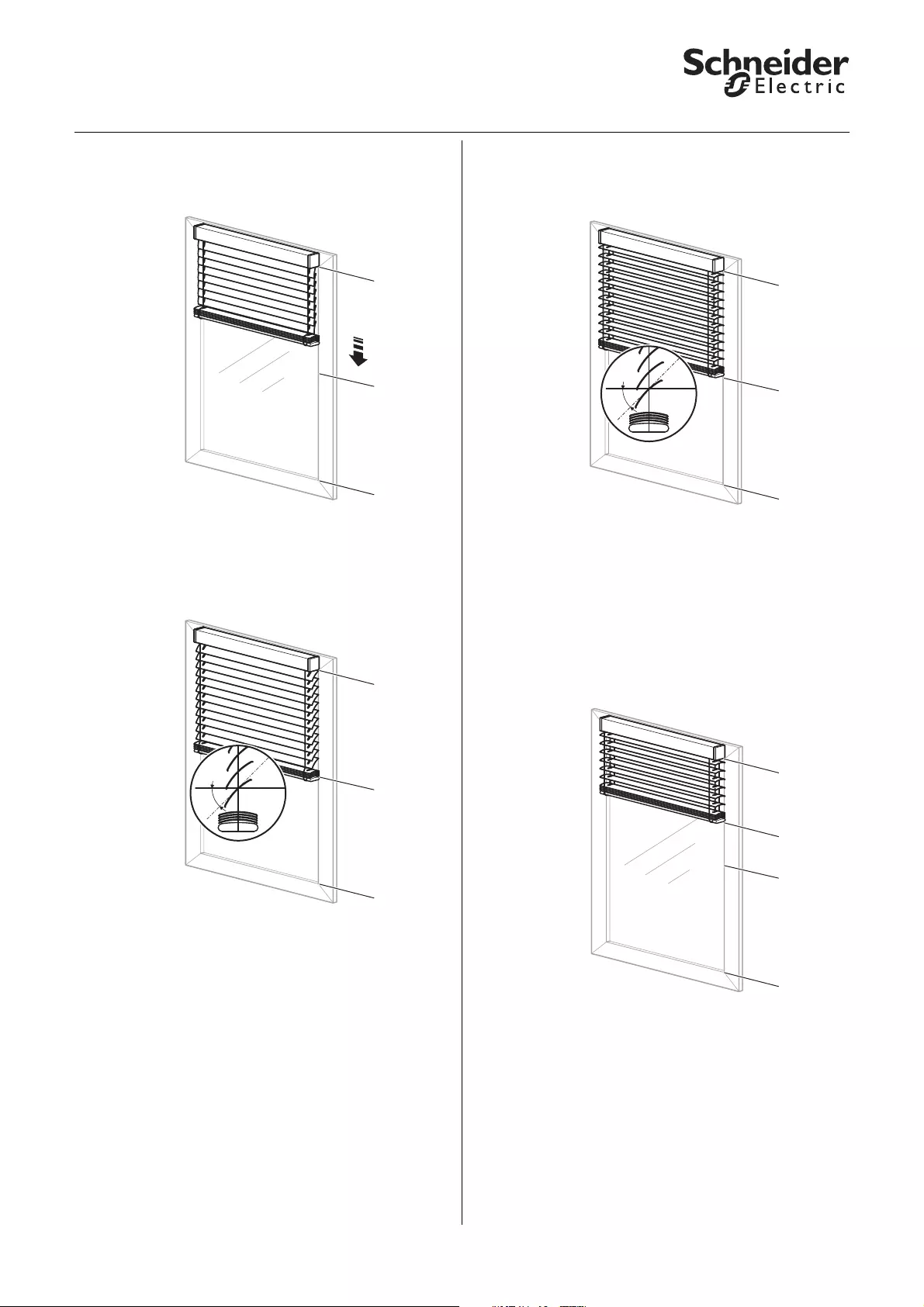
10
KNX Blind actuator REG-K/x/10 with manual mode
Art. no. MTN649802, MTN649804, MTN649808
© 2012 Schneider Electric
Application Shutter.Blind.Safety.Position.Manual 5700/1.1
Step 2:
Height running time = 60 s, downwards direction
(Difference between current 0 % and new position 50
% = 50 % of height running time)
Step 3:
Slat adjustment into the working position after
downwards movement = 1.25 s
(Slat running time from 100 % to 50 %)
Total movement time therefore:
2.5 s + 60 s + 1.25 s = 63.75 s
New height position: 30 %
Step 1:
Open slats for the upwards movement = 1.25 s
(Slat running time from 50 % to 0 %)
Step 2:
Height running time = 24 s, upwards direction
(Difference between current position 50 % and new
position 30 % = 20 % of height running time)
plus
Running time supplement upwards = 0.04 s
(Difference between current position 50 % and new
position 30 % = 20% of running time supplement)
0 %
50 %
100 %
50 %
0 %
50 %
100 %
50 %
0 %
50 %
100 %
0 %
30 %
50 %
100 %
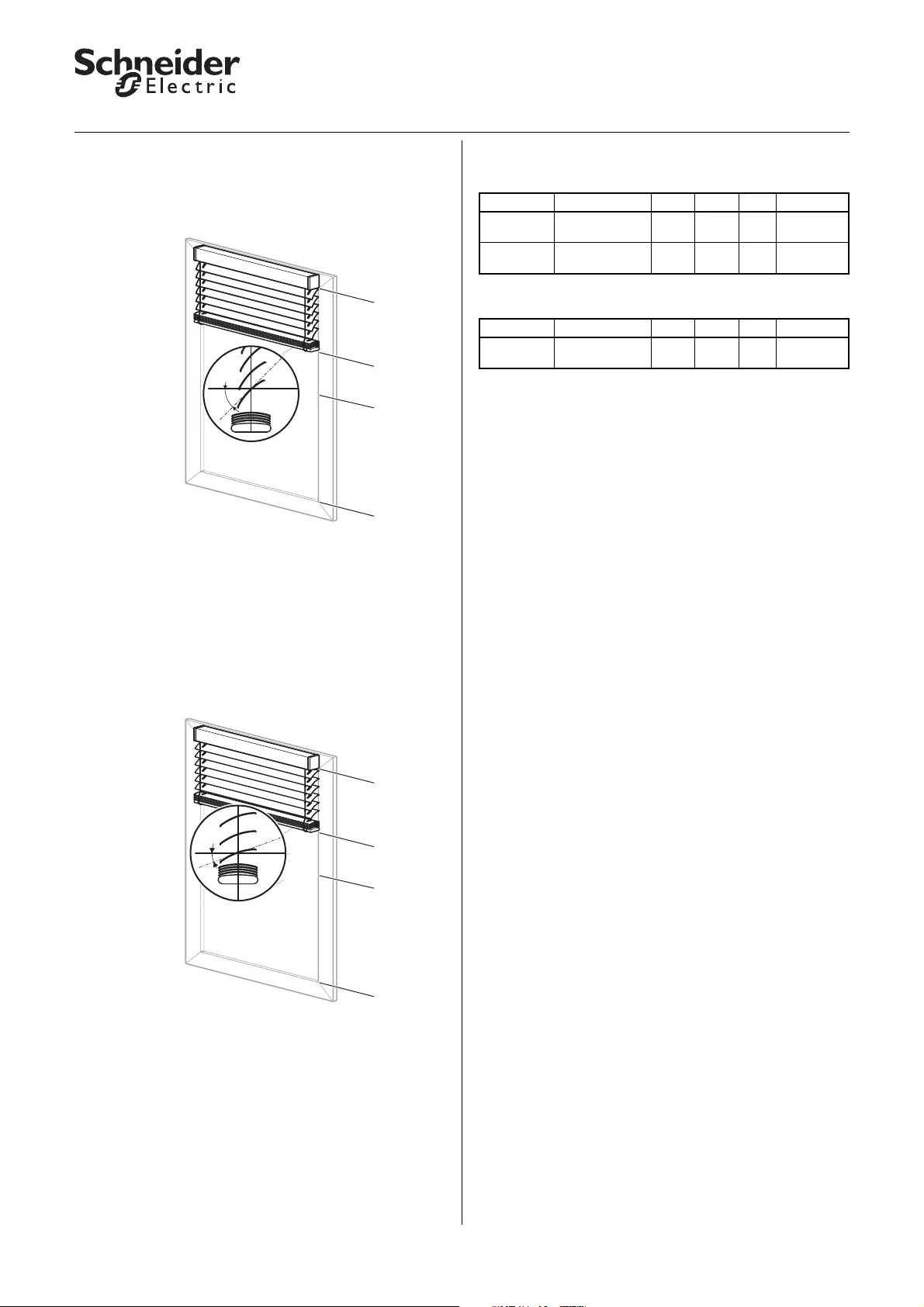
11
KNX Blind actuator REG-K/x/10 with manual mode
Art. no. MTN649802, MTN649804, MTN649808
© 2012 Schneider Electric
Application Shutter.Blind.Safety.Position.Manual 5700/1.1
Step 3:
Slat adjustment into the working position after
upwards movement = 1.25 s
(Slat running time from 0 % to 50 %)
Total movement time therefore:
1.25 s + 24 s + 0.04 s + 1.25 s = 26.54 s
New slat postion: 20 %
Step 1:
Slat running time = 750 ms
(Difference between current position 50 % and new
position 20 % = 30 % of slat running time)
Communication objects
Communication objects for blind:
Communication objects for roller shutters:
50 %
0 %
30 %
50 %
100 %
20 %
0 %
30 %
50 %
100 %
Function Object name Type Prio Flags Behaviour
Channel X Manual height
position 1 byte Low WC Receive
Channel X Manual slat
position 1 byte Low WC Receive
Function Object name Type Prio Flags Behaviour
Channel X Manual height
position 1 byte Low WC Receive
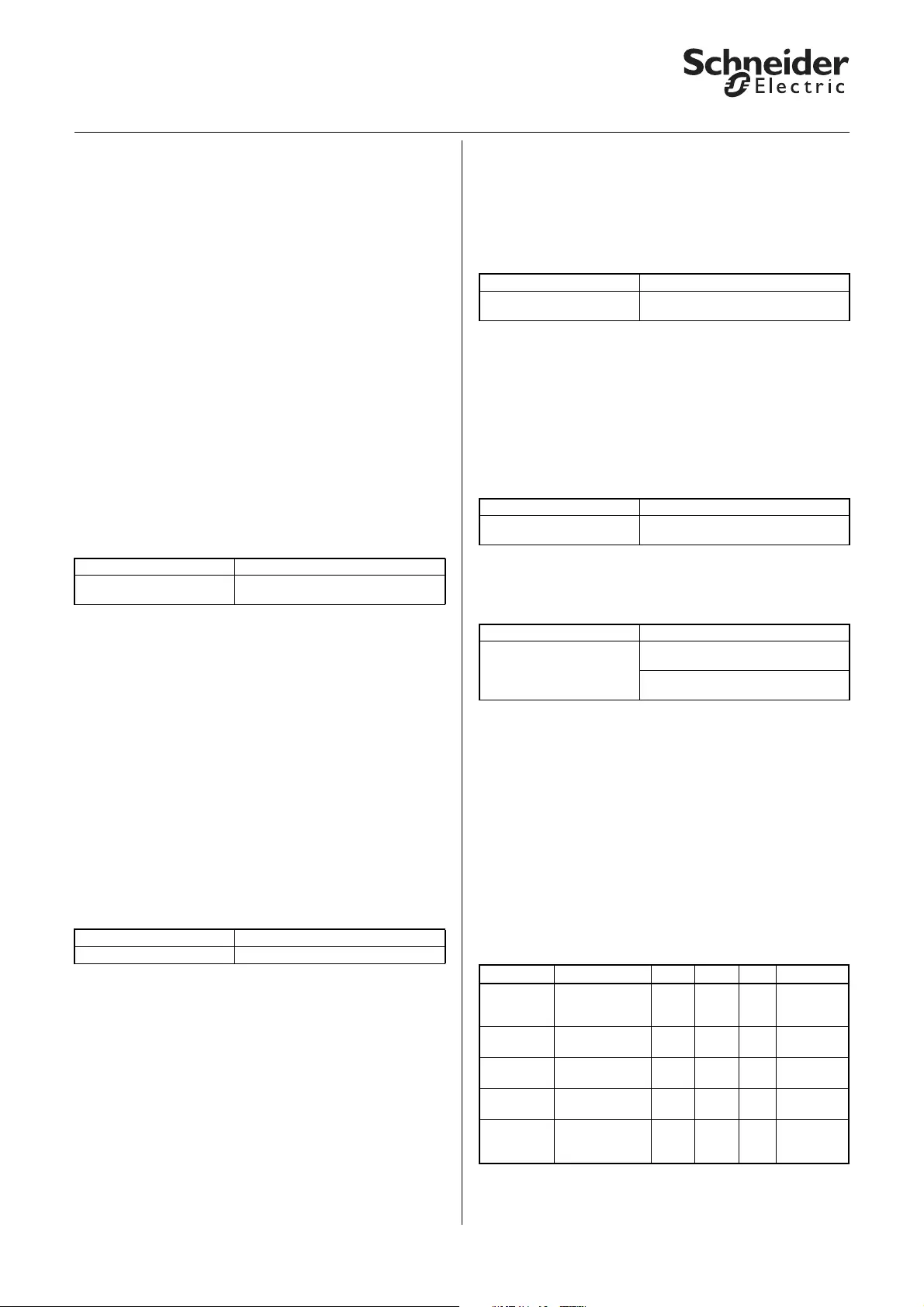
12
KNX Blind actuator REG-K/x/10 with manual mode
Art. no. MTN649802, MTN649804, MTN649808
© 2012 Schneider Electric
Application Shutter.Blind.Safety.Position.Manual 5700/1.1
●Advanced functions: Automatic control
In addition to manual control of the blind/roller shutter
drives (using the communication objects for the
manual operation options), the software application
also provides you with another group of
communication objects for automatic control.
Automatic control can take place from other bus
devices, e.g., presence detectors, light controllers or
through a building control centre. When you have
activated automatic control for a channel, then initially
you can position the connected drive equally using
manual or automatic control. The drive responds
identically to control telegrams received from both
types of control.
Using parameter settings and objects you can change
the operating principle of both control options. You can
also configure manual and automatic control to
influence each other.
Activating automatic control
In order to be able to use automatic control, you have
to activate the function in the ETS first:
When automatic control is active, the extra tab "X:
Automatic" appears. Here you can make more
settings.
The communication objects for manual operation and
automatic control have the same effects. The drive
carries out the last command it received to one of the
objects.
Deactivating/Disabling automatic control
If manual control and automatic control operating on
an equal basis doesn't always suit your application,
then you can disable the automatic function using
another object if necessary, and then enable it again
later.
In addition, you can specify how automatic control
responds to a manual operating telegram.
If you set "Automatic lock" to the value "on object value
0" or "on object value 1", then the communication
object "Automatic lock" also appears.
Depending on how it is set, the automatic function is
either enabled or disabled when it receives a new
telegram value.
– "Automatic lock" = "on object value 0"
If "Automatic lock" = "0": Automatic function
disabled (automatic lock active)
If "Automatic lock" = "1": Automatic function
enabled (automatic lock inactive)
– "Automatic lock" = "on object value 1"
If "Automatic lock" = "0": Automatic function
enabled (automatic lock inactive)
If "Automatic lock" = "1": Automatic function
disabled (automatic lock active)
You can also specify the behaviour of the drive at the
end of an automatic lock.
Specifying dependency between automatic
function and manual control
The following parameter allows you to define the
response of the automatic function to the receipt of a
control telegram from the manual control options
(manual movement object, manual stop/step object,
manual height position, manual slat position and scene
retrieval):
If this parameter is set to "Automatic control
temporarily disabled", two additional parameters
appear:
The deactivation time period results from the time
basis x factor.
The only way to cancel a continuous deactivation of
the automatic function is with a telegram to end an
automatic lock via the automatic lock object. The
action that you set in the parameter "Behaviour on
deactivation of the automatic lock via object value" is
executed.
After a time-limited deactivation has expired, the drive
remains in its current position until it receives the next
control telegram.
Communication objects
Tab Parameter
X: Blind
X: Roller shutter Automatic control/Presets
Tab Parameter
X: Automatic Automatic lock
Tab Parameter
X: Automatic Behaviour on deactivation of the
automatic lock via object value
Tab Parameter
X: Automatic Response in automatic operation on
receipt of a manual object value
Tab Parameter
X: Automatic Time basis for automatic function
deactivation time
Factor for automatic function
deactivation time (1-255)
Function Object name Type Prio Flags Behaviour
Channel X Automatic
movement
object
1 bit Low WC Receive
Channel X Stop/step object
automatic 1 bit Low WC Receive
Channel X Height position
automatic 1 byte Low WC Receive
Channel X Slat position
automatic 1 byte Low WC Receive
Channel X Automatic lock 1 bit Low CRW
TSend/
Receive/
Read out
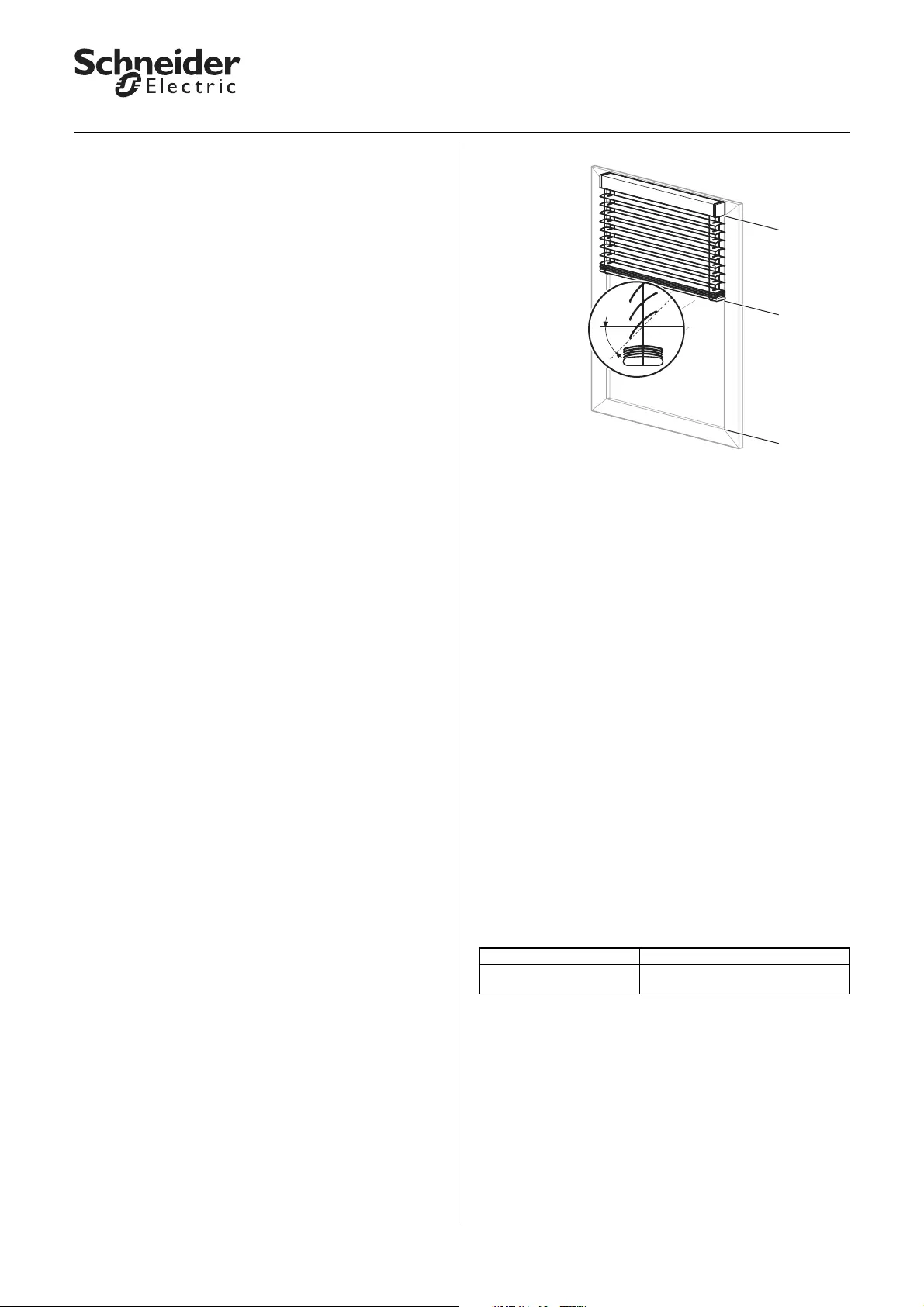
13
KNX Blind actuator REG-K/x/10 with manual mode
Art. no. MTN649802, MTN649804, MTN649808
© 2012 Schneider Electric
Application Shutter.Blind.Safety.Position.Manual 5700/1.1
●Advanced functions: Calibration/Reference
movement
The blind actuator calculates the current position of a
drive from the running times that you set for the drive
and also from the control commands that it executes.
This calculation has to be performed because the drive
cannot provide any status feedback on its position.
Even if you set the running times very precisely, small
variations occur between the internally calculated
height position and the actual height position after a
few movements. These are due to mechanical
tolerances and weather influences (temperature
fluctuations, frost, rain etc.).
The blind actuator can reset these deviations with
reference movements. To do this, it moves the drives
specifically into the top or lower end position. After the
reference movement, the internal position calculation
re-starts from a fixed value. This means that any
deviations that have occurred in the meantime are
deleted.
|Note: The calibration function is primarily
important if you are working with a lot of
position commands and require a high level of
positioning precision. If you are controlling the
blind with the basic function only and position
commands are irrelevant, then you don't need
this function.
Operation
A reference movement can be triggered by a
communication object or after a certain number of
movements. When a reference movement is
triggered, the drive moves into the desired reference
position (end position). If you have set both end
positions as reference positions, then the drive moves
into the nearest end position, depending on its current
position. In order to ensure that the drive reaches the
end position fully, the actuator adds a running time
supplement of 5% of the total running time to the
calculated movement time for every reference
movement.
Application example
– Blind type 1, automatic slat position after
downwards movement (working position) 50 %
– Start-up delay: disabled
Run-out delay: disabled
Slat up start-up supplement: disabled
– Height running time 120 s
Running time supplement upwards 0.2 s
Slat running time 2.5 s
– Current height position 40 %
Current slat position 50 % (work position)
Calculated movement time for reference movement
to top end position:
– Open slats fully for the upwards movement = 1.25s
– plus height running time (40 % of total movement
range) 48 s, upwards direction
– plus running time supplement upwards (40 % of 0.2
s) 0.08 s
– Calculated movement time: 49.33 s
– plus supplement for reference movement (5 % of
total running time) 6 s
–Total movement time of the reference
movement 55.33 s
Calibration is also automatically carried out when the
drive moves into an end position following a "normal"
positioning command. The running time supplement
of 5% also applies in the case of automatic calibration.
|Note: If during a calibration function a weather
alarm or any other higher-level function is
activated, then the calibrating function is
cancelled and the higher-level function is
executed.
You can activate the calibration function for every
channel individually: Enable the "Calibration"
parameter.
Tab Parameter
X: Blind
X: Roller shutter Calibration
50 %
0 %
40 %
100 %
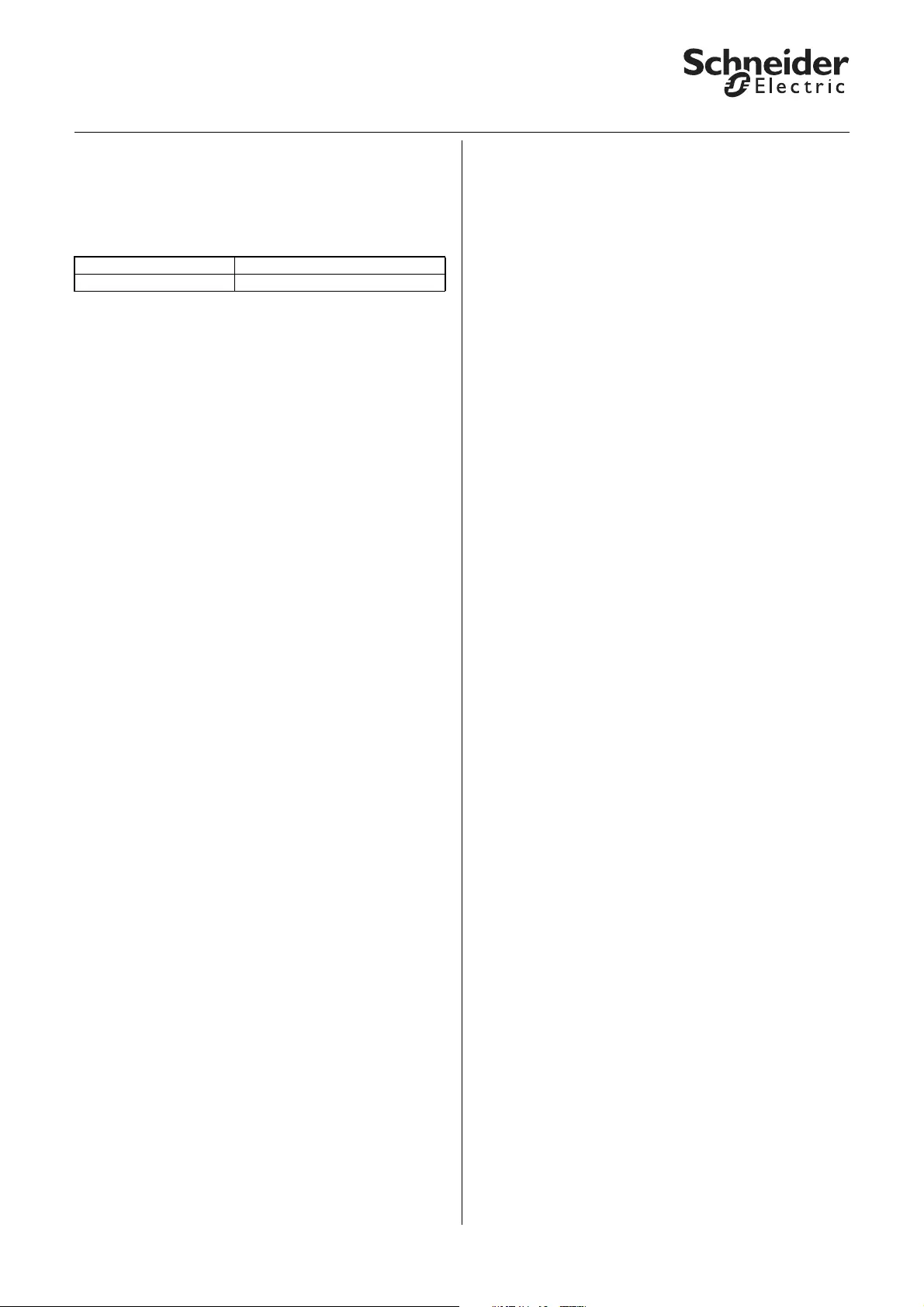
14
KNX Blind actuator REG-K/x/10 with manual mode
Art. no. MTN649802, MTN649804, MTN649808
© 2012 Schneider Electric
Application Shutter.Blind.Safety.Position.Manual 5700/1.1
A new tab "X:Calibration" appears for those channels
for which you activated the calibration function. Here
you can make the desired settings for each channel.
Using the "Reference position" parameter, first select
the end position that you want to use as the reference
position.
Then you can specify what triggers a reference
movement:
Trigger reference movement after a certain
number of movements
The actuator adds the number of all movements
regardless of which control command triggered the
movements. Once the defined number of movements
has been reached, the drive carries out a reference
movement before the next positioning command.
Then it moves into the required position. After the
reference movement, the movement counter is reset.
Trigger reference movement by communication
object
When the "Trigger reference movement" object
receives the value "1", a reference movement is
started on all associated channels. So as not to
overload the power supply of the blind system, you
can stagger the reference movements by specifying a
delay time for each individual channel. If during this
delay time, the object receives a new value of "1", the
delay time is restarted. The object value "0" has no
meaning.
You can define the height position after the reference
movement with the "Position after reference
movement via object". If you want the drive to move
into a new position, then set the height, and in the
case of blinds the opening angle of the slats also, to a
value in the movement range between 0% and 100%.
If the blind actuator receives an absolute positioning
command during the reference movement, it moves
into the desired position after the reference
movement. The settings in the "Position after
reference movement via object“ parameter have no
effect in this case. All other control commands
interrupt the calibration function. The drive responds
to the control commands received.
Automatic calibration
Every time the drive moves into the defined end
position following a positioning command, the
calibration function is carried out. This means that a
running time supplement of 5% of the total running
time is added to the calculated movement time
needed by the drive, so that the drive can reach the
desired end position fully. When the end position is
reached, the movement counter is reset.
Reference movement after initialisation
The aim of the reference movement after a download
or recovered bus voltage is to have an exact starting
position for subsequent position movements.
|Note: The reference movement after
initialisation is always carried out, even if the
"General reference movement" function is
disabled.
The reference movement is triggered by an absolute
positioning command. These are, for example, the
receipt of a value on the "Manual height position" or
"Automatic height position" objects, retrieval of scenes
or pre-set values, or if an absolute position is assumed
in the event of a weather alarm, alarm or lock. If after
initialisation the "Manual movement object" object
receives a value that moves the blind/roller shutter
into the top end position, then the actuator
automatically assesses this movement as a reference
movement.
In general, the reference movement after initialisation
is towards the top end position. If you enabled
transmission of the status messages "Height status"
and/or "Slat status" (active status feedback object), the
current status is automatically transmitted via this
object.
Reference movement in the event of movement
range limitation
½Caution!
Blinds/roller shutters could be damaged. The
blinds/roller shutter may move beyond the
limits of the movement range into windows that
may be open. Pay attention therefore to where
you want the reference movement to go.
A reference movement also takes place after
initialisation even if the "Limit movement range"
function is active. The blinds/roller shutter may move
beyond the limits of the movement range into
windows that may be open. Pay attention therefore to
where you want the reference movement to go. In
general, the reference movement after initialisation is
towards the top end position. Only when the
"Reference position" is set to "down" does a reference
movement take place towards the lower end position.
In the case of a reference movement, the "Movement
range limit status feedback" object receives the value
"0". The blind/roller shutter only moves in the travel
range after the reference movement has completed.
Tab Parameter
X: Calibration Reference position
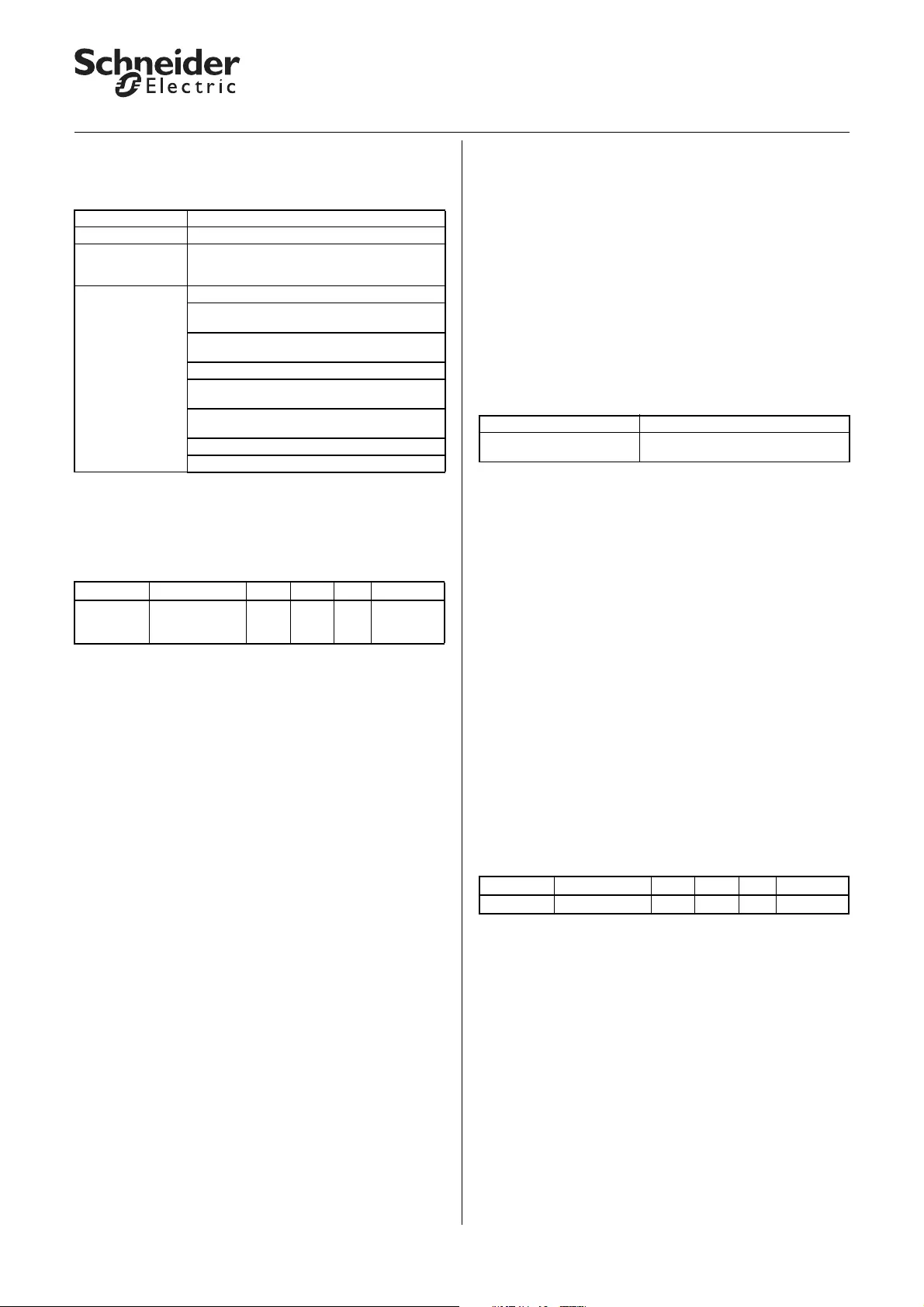
15
KNX Blind actuator REG-K/x/10 with manual mode
Art. no. MTN649802, MTN649804, MTN649808
© 2012 Schneider Electric
Application Shutter.Blind.Safety.Position.Manual 5700/1.1
Parameter settings in the ETS:
Set the following parameters for this function in the
ETS:
Communication objects
If the "General reference movement" parameter is
enabled in the "General" tab, the "Trigger reference
movement" object appears.
●Advanced functions: Disable function for
manual operating options
You can control the connected drives using the
communication objects for manual operation or by
automatic control. There are two manual operation
options available:
– Manually move height position and slat opening
angle with up/down/step/stop commands
– Move height position and slat opening angle using
absolute position commands
Disable manual operation
If you want to disable manual operation for a time,
then you can activate a disable function for every
output channel.
Depending on how it is set, manual operation is either
enabled or disabled when it receives a new telegram
value.
– "Manual lock" = on object value "0"
If "Manual lock" = "0": manual operation disabled
(manual lock active)
If "Manual lock" = "1": manual operation enabled
(manual lock inactive)
– "Manual lock" = on object value "1"
If "Manual lock" = "0": manual operation enabled
(manual lock inactive)
If "Manual lock" = "1": manual operation disabled
(manual lock active)
Alarm functions or other higher-level functions (e.g.,
wind alarm, rain alarm) also disable drive operation
(see the section "Higher-level functions").
Communication objects
If you set "Manual lock" to the value "on object value 0"
or "on object value 1", then the communication object
"Manual lock" appears.
Tab Parameter
General General reference movement
X: Blind
or
X: Roller shutter
Calibration
X: Calibration Reference movement after
number of movements until a reference
movement is executed (1-20)
Reference movement delay time via object in
seconds
Position after reference movement via object
Height position after reference movement in
%
(for blind) slat position after reference
movement in %
Reference position
Automatic calibration
Function Object name Type Prio Flags Behaviour
Calibration Trigger
reference
movement
1 bit Low WC Receive
Tab Parameter
X: Blind
X: Roller shutter Manual lock
Function Object name Type Prio Flags Behaviour
Channel X Manual lock 1 bit Low WC Receive
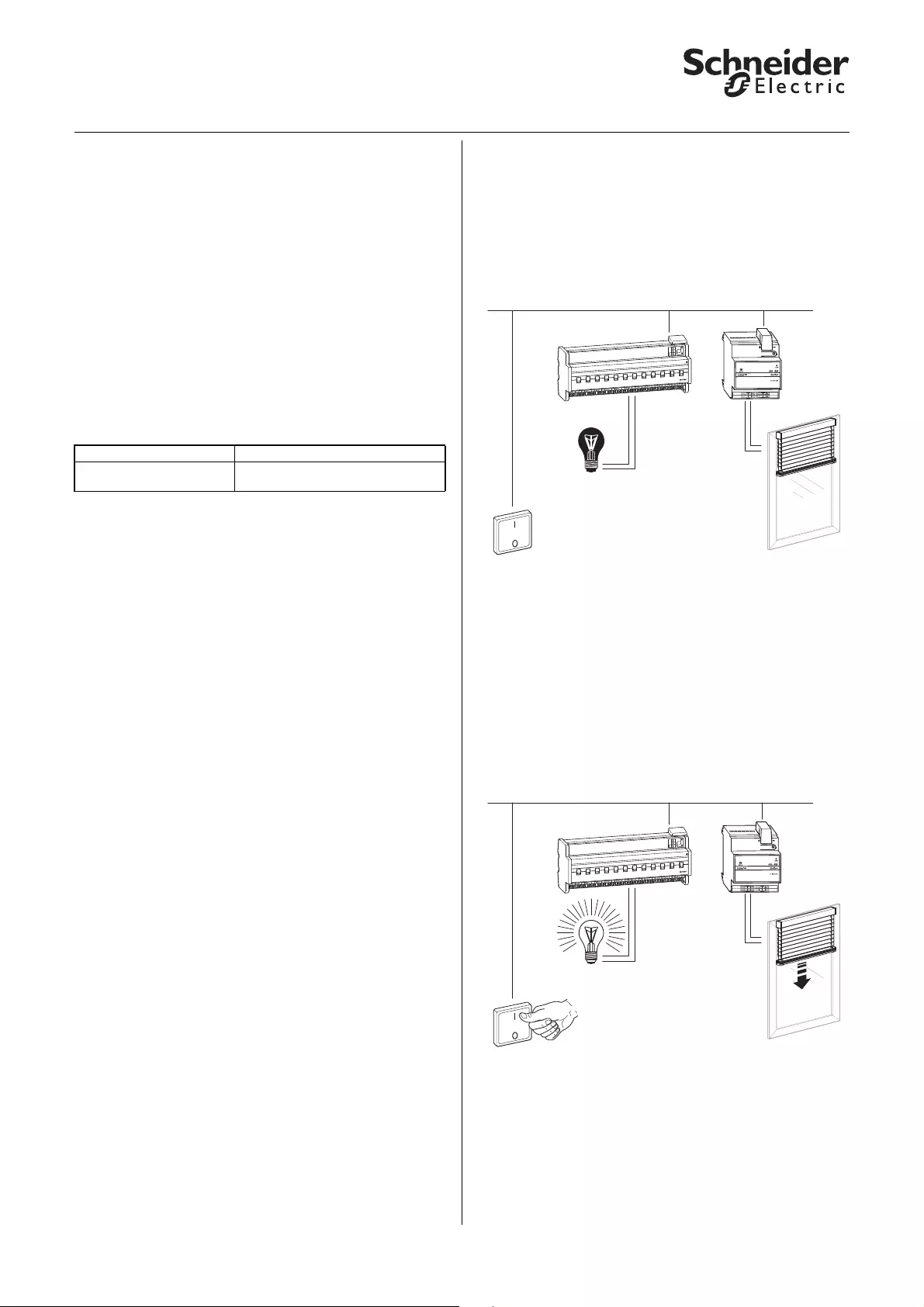
16
KNX Blind actuator REG-K/x/10 with manual mode
Art. no. MTN649802, MTN649804, MTN649808
© 2012 Schneider Electric
Application Shutter.Blind.Safety.Position.Manual 5700/1.1
●Advanced functions: Preset function
The preset function allows you to save up to four
height positions and slat opening angles (for blind
drives) per blind or roller shutter channel and to
activate these preset positions later by telegram. You
can save current height positions as preset positions
by telegram control. The difference between this
function and the scene function is in terms of the data
format of the allocated communication objects. In the
case of the preset function, all communication objects
are 1-bit objects.
You can activate the preset function as an alternative
to the automatic function.
Activating the preset function
You can activate the preset function for each channel
individually:
After you have activated the function, the "X: Presets“
tab opens. Here you can specify the four preset
positions. You can change these positions later during
operation using telegrams.
Retrieving preset positions
You can retrieve the preset positions with the
communication objects "Preset 1/2" or "Preset 3/4".
Following receipt of a telegram on either of the two
objects, the drive moves into the saved pre-set
position.
– "Retrieve preset 1/2" = "0": Preset position 1 is
activated
– "Retrieve preset 1/2" = "1": Preset position 2 is
activated
– "Retrieve preset 3/4" = "0": Preset position 3 is
activated
– "Retrieve preset 3/4" = "1": Preset position 4 is
activated
If a reference movement is necessary before moving
into the preset position, the reference movement is
carried out first and then the drive moves into the
requested preset position.
Saving a preset position
You can replace the preset positions during operation
with the communication objects "Preset 1/2" or "Preset
3/4".
Following receipt of a telegram on either of the two
objects, the current position of the drive is saved as
the new preset position.
– "Set preset 1/2" = "0": Saves current position as
preset position 1
– "Set preset 1/2" = "1": Saves current position as
preset position 2
– "Set preset 3/4" = "0": Saves current position as
preset position 3
– "Set preset 3/4" = "1": Saves current position as
preset position 4
If you enabled the parameter "Replace preset values in
the actuator on download", then the preset values
saved in the device are replaced with your default
values on download. If you don't want to replace the
values in the device, then you must disable this
parameter.
Application example 1
The preset function allows you, for example, to switch
on the lighting and move the roller shutter at the same
time by pressing one push-button. If you enter the
value 0 % (roller shutter open) for preset function 1
and the value 100 % (roller shutter closed) for preset
value 2, then pressing one push-button gives you the
following control:
Push-button action to ON => telegram value "1" =>
light ON and retrieve preset position 2 = close roller
shutter:
Tab Parameter
X: Blind
X: Roller shutter Automatic control/Presets
KNX
B
L
T
+-
-
ON
Bus
Prog.
LLL
LL
LL
LL
LL
LL
K
OFF
L
OFF
RUN
OFF
OFF
OFF
OFFOFF
J
I
HG
F
E
OFF
OFF
OFFOFF
D
C
B
A
LLL
LL
LL
LL
LL
Jalousieaktor REG-K/4x/6
Blind actuator REG-K/4x/6
LL
LL
LL
646704
1
2
3
4
KNX
1
B
L
T
+-
-
ON
Bus
Prog.
LLLLL
LL
LL
LL
LL
K
OFF
L
OFF
RUN
OFF
OFF
OFF
OFF
OFF
J
I
HG
F
E
OFF
OFF
OFF
OFF
D
C
B
A
LLL
LL
LL
LL
LL
Jalousieaktor REG-K/4x/6
Blind actuator REG-K/4x/6
LL
LL
LL
646704
1
2
3
4
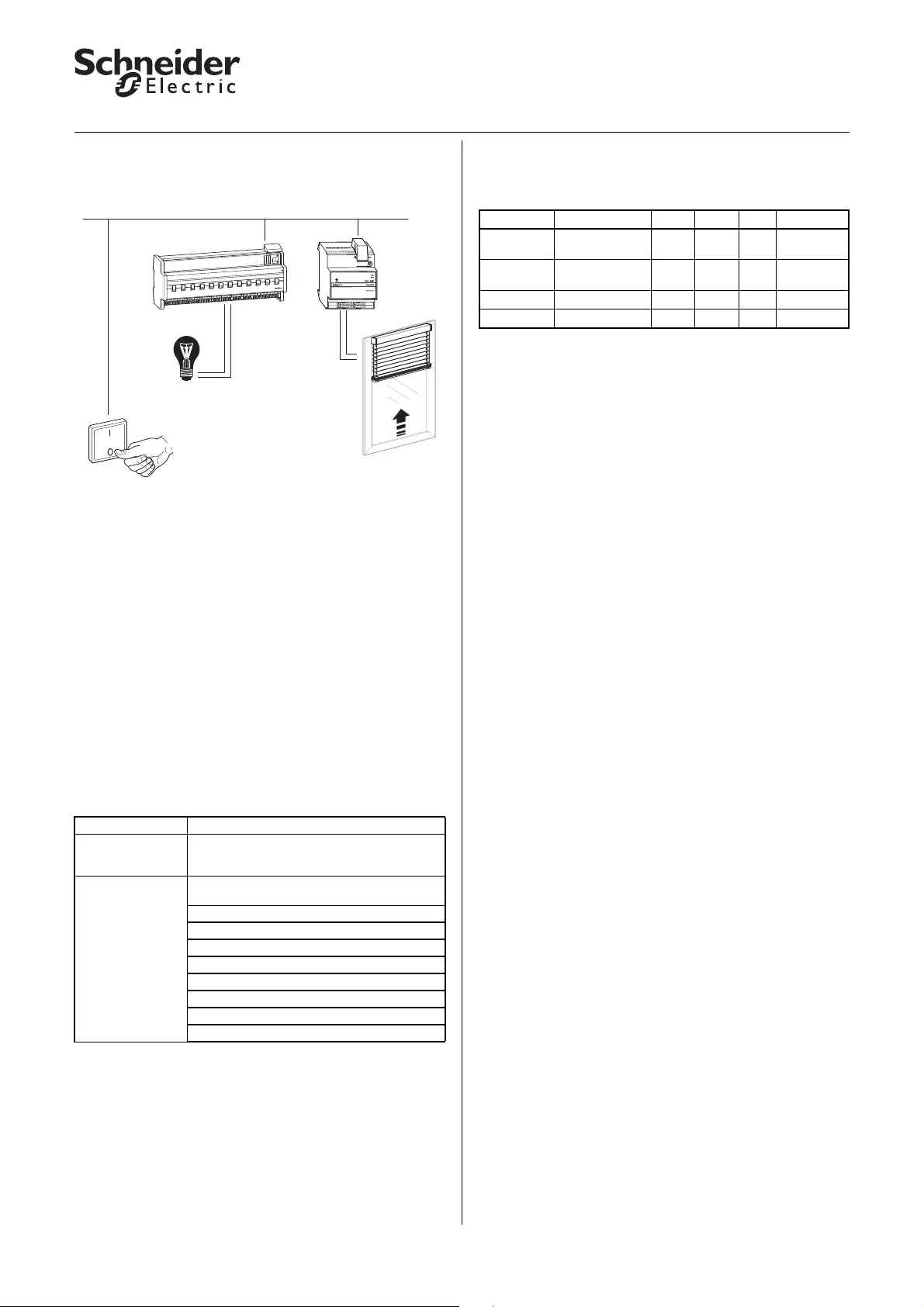
17
KNX Blind actuator REG-K/x/10 with manual mode
Art. no. MTN649802, MTN649804, MTN649808
© 2012 Schneider Electric
Application Shutter.Blind.Safety.Position.Manual 5700/1.1
Push-button action to OFF=> telegram value "0" =>
light OFF and retrieve preset position 1 = open roller
shutter:
In this case, due to the fact that the roller shutter
requires a certain running time to open, the light needs
to be swiched off with a switch-off delay so that it
doesn't suddenly become dark prematurely.
Application example 2
You can also use a 1-bit light sensor to retrieve a
preset. The following devices can be used as a light
sensor: INSTABUS-ARGUS 220 Connect Art. No.
6315., light-sensitive switch REG-S/DS1 Art. No.
670601, weather station REG-K/4-gang Art. No.
682991.
Parameter settings in the ETS:
Set the following parameters for this function in the
ETS:
Communication objects
Use the following objects to retrieve the preset
functions:
Tab Parameter
X: Blind
or
X: Roller shutter
Automatic control/Presets
X: Presets Replace preset values in the actuator on
download
Preset 1 height pos. in %
Preset 1 slat pos. in %
Preset 2 height pos. in %
Preset 2 slat pos. in %
Preset 3 height pos. in %
Preset 3 slat pos. in %
Preset 4 height pos. in %
Preset 4 slat pos. in %
KNX
0
B
L
T
+-
-
ON
Bus
Prog.
LL L
LL
LL
LL
LL
LL
K
OFF
L
OFF
RUN
OFF
OFFOFF
OFF
OFF
J
I
H
G
F
E
OFF
OFF
OFF
OFF
D
C
B
A
LLL
LL
LL
LL
LL
Jalousieaktor REG-K/4x/6
Blind actuator REG-K/4x/6
LL
LL
LL
646704
1
2
3
4
Function Object name Type Prio Flags Behaviour
Channel X Retrieve preset
1/2 1 bit Low WC Receive
Channel X Retrieve preset
3/4 1 bit Low WC Receive
Channel X Set preset 1/2 1 bit Low WC Receive
Channel X Set preset 3/4 1 bit Low WC Receive
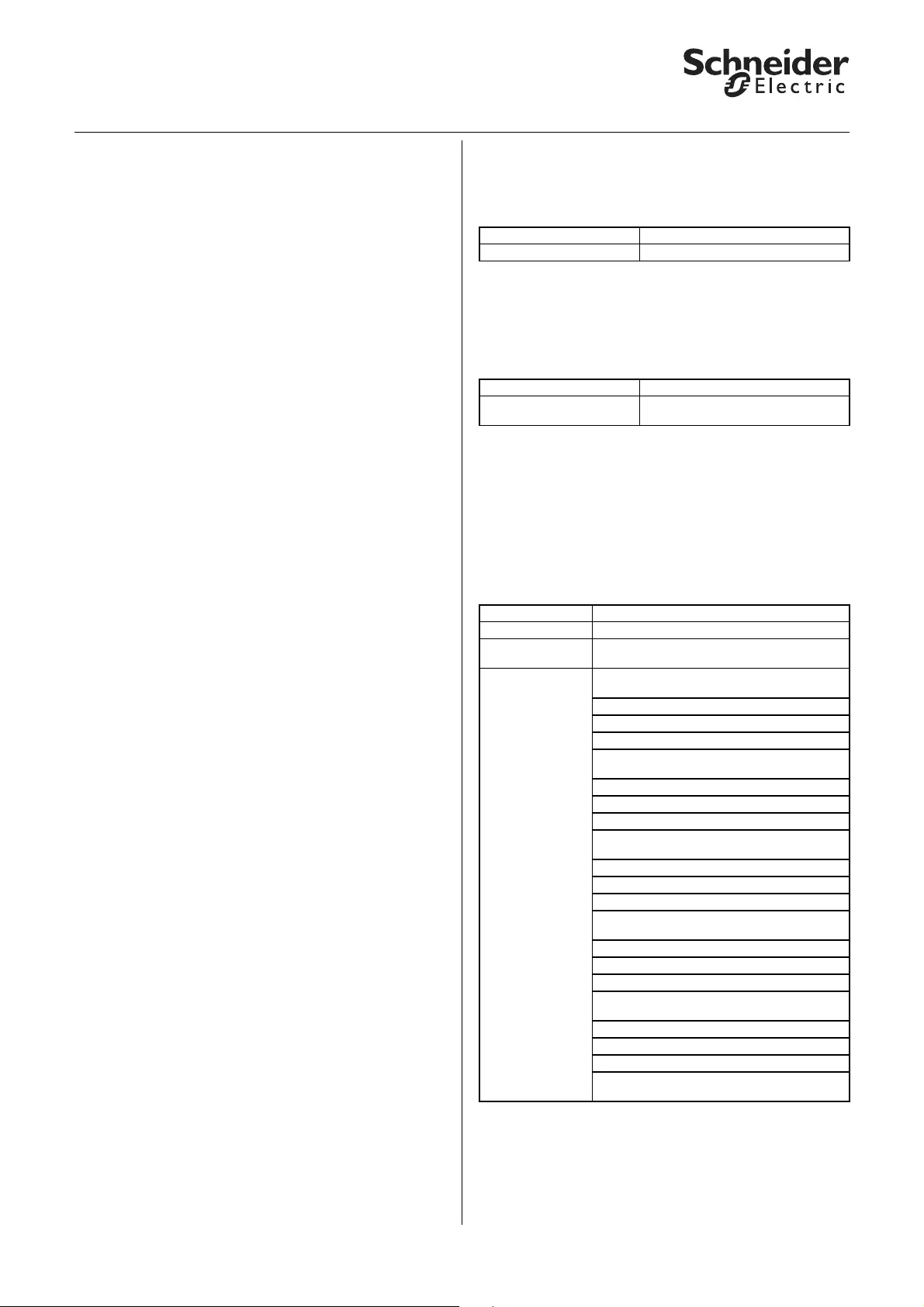
18
KNX Blind actuator REG-K/x/10 with manual mode
Art. no. MTN649802, MTN649804, MTN649808
© 2012 Schneider Electric
Application Shutter.Blind.Safety.Position.Manual 5700/1.1
●Advanced functions: Scene function
If you want to change various room functions at the
same time using a bus telegram, then the scene
function is ideal. Retrieving a scene allows you, for
example, to dim the room lighting to a desired value,
move the blinds into a desired position and turn the
slats, switch heating control to daytime operation and
switch on the power to the socket-outlets in a room.
Due to the fact that these functions can have different
telegram formats and moreover, the telegram values
have different meanings (e.g., for lighting value "0"
means OFF and for blinds OPEN), without the scene
function you would have to send a separate telegram
to each actuator to achieve the same result.
The scene function allows you to integrate the blind
actuator into scene control. There are memory slots
for up to five different scene values for each output
channel. Each of these scene memory slots can be
assigned one of 64 possible scene numbers (scene
numbers 0 to 63 correspond to telegram values 0 to
63). You can save height positions, and for blinds also
slat opening angles, as scene values. When the
actuator receives a telegram that retrieves a scene
number, the drive is moved into the saved position and
the slats are turned. The scene numbers that you save
on commissioning can be replaced later by users if
they want.
Telegram format
Telegrams for the scene function have the data format
LXDDDDDD.
L: Learn bit
X: is not used
DDDDDD: retrieved scene number
If the learn bit in a telegram has the value "0", the
position values saved for this scene number are
retrieved and engaged.
If the learn bit has the value "1", then the current drive
and slat positions are saved as new position values for
the scene number.
Examples:
– Telegram value 2
Binary 0000 0010
Hexadecimal 02
Retrieve scene number 2
– Telegram value 45
Binary 0010 1101
Hexadecimal 2D
Retrieve scene number 45
– Telegram value 173
Binary 1010 1101
Hexadecimal AD
Learn scene number 45
– Telegram value 190
Binary 1011 1110
Hexadecimal BE
Learn scene number 62
Activating the scene function
In order to be able to use the scene function for the
individual channels, you first have to enable the
function for the device once:
After you enable the function, the communication
object "Scene object" appears. This object receives the
scene telegrams.
Now you can activate the function for each channel
individually:
After you enable the "Scenes" parameter, the "X:
Scenes" tab appears. Here you can assign the scene
position. You can activate each of the scene memory
slots independently of each other.
Parameter settings in the ETS:
Set the following parameters for this function in the
ETS:
Tab Parameter
General Scenes general
Tab Parameter
X: Blind
X: Roller shutter Scenes
Tab Parameter
General Scenes general
X: Blind
X: Roller shutter Scenes
X: Scenes Replace scene values in the actuator on
download
Scene 1
Scene 1: Scene number (0-63)
Scene 1: Height pos. in %
Scene 1: Slat pos. in %
(only for blind)
Scene 2
Scene 2: Scene number (0-63)
Scene 2: Height pos. in %
Scene 2: Slat pos. in %
(only for blind)
Scene 3
Scene 3: Scene number (0-63)
Scene 3: Height pos. in %
Scene 3: Slat pos. in %
(only for blind)
Scene 4
Scene 4: Scene number (0-63)
Scene 4: Height pos. in %
Scene 4: Slat pos. in %
(only for blind)
Scene 5
Scene 5: Scene number (0-63)
Scene 5: Height pos. in %
Scene 5: Slat pos. in %
(only for blind)
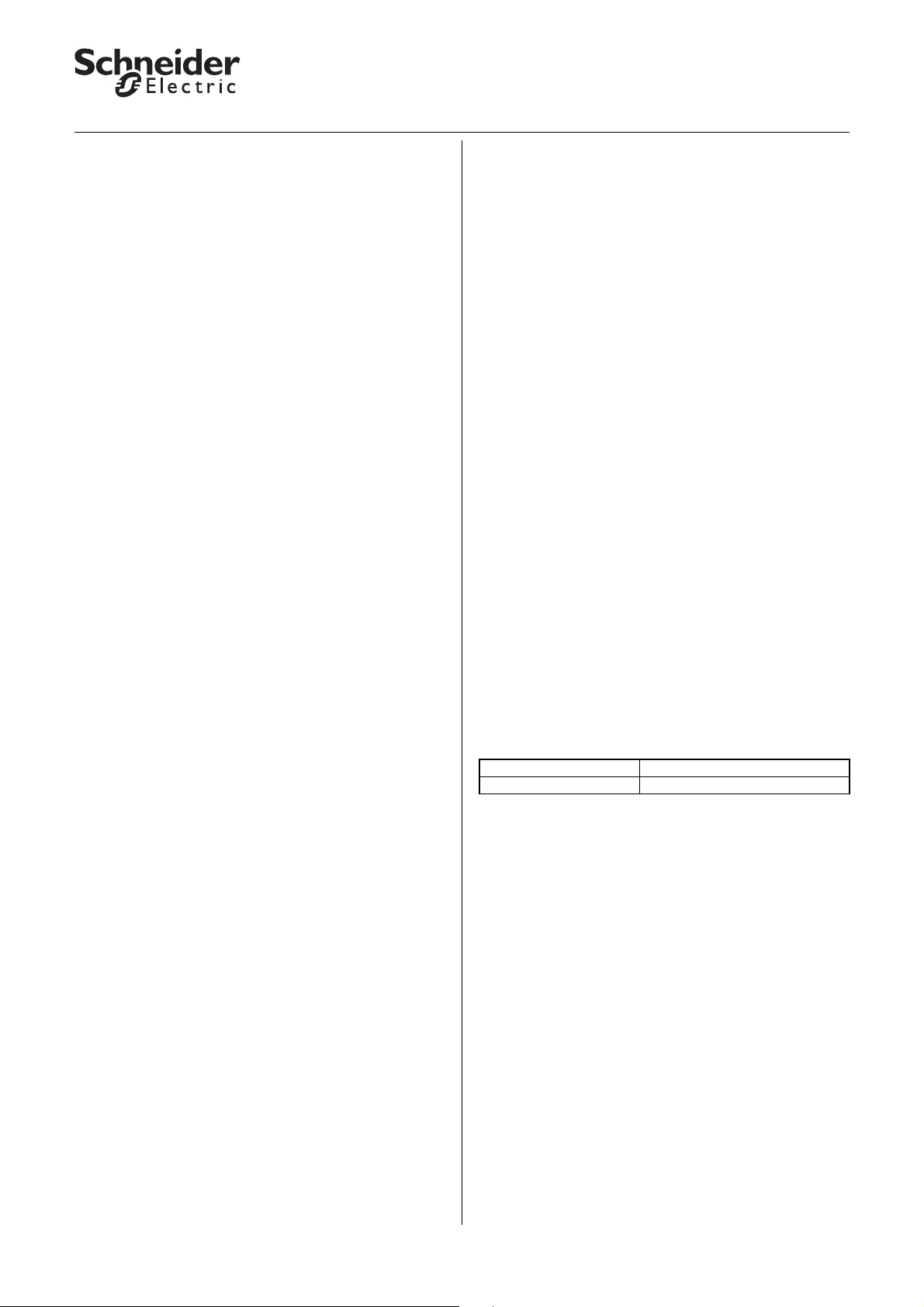
19
KNX Blind actuator REG-K/x/10 with manual mode
Art. no. MTN649802, MTN649804, MTN649808
© 2012 Schneider Electric
Application Shutter.Blind.Safety.Position.Manual 5700/1.1
Retrieving and saving a scene position
The "Scene object" object allows you to retrieve scene
positions. When a scene telegram is received, the
blind actuator evaluates the scene number sent.
If a reference movement is necessary before moving
into the scene position, the reference movement is
carried out first and then the drive moves into the
requested scene position.
If the "Scene object" object receives a scene telegram
with learn bit "1", then the current position, and in the
case of blinds the current slat position, is saved as the
new scene value in all those scene memory slots
allocated the scene number received.
|Note: If a scene number has been allocated to
more then one scene within a channel, then the
first scene that has this scene number and is
found will be activated (only this scene
number). Or it will be saved in the memory. To
avoid this, you should allocate different scene
numbers to every scene within a channel.
Example:
–Output channel 1
Scene 1 activated to scene number 13
(Scene 1 Height position = 50 %,
(Scene 1 Slat position = 75 %,
Scene 2 activated to scene number 7
(Scene 2 Height position = 0 %,
(Scene 2 Slat position = 0 %,
Scene 3, 4, 5 deactivated
–Output channel 5
Scene 1 activated to scene number 7
(Scene 1 Height position = 100 %,
(Scene 1 Slat position = 0 %,
Scene 3 activated to scene number 21
(Scene 3 Height position = 50 %,
(Scene 3 Slat position = 50 %,
Scene 2, 4, 5 deactivated
"Scene object" object receives "Retrieve scene
number 13" telegram:
– Output channel 1 moves into position 50 % height,
75 % slat
– Output channel 5 does not respond
"Scene object" object receives "Retrieve scene
number 1" telegram:
– Actuator does not respond because scene number
1 is not assigned.
"Scene object" object receives "Retrieve scene
number 7" telegram
– Output channel 1 moves into position 0 % height,
0 % slat
– Output channel 5 moves into position 100 %
height, 0 % slat
"Scene object" object receives "Retrieve scene
number 21" telegram
– Output channel 1 does not respond
– Output channel 5 moves into position 50 % height,
50 % slat
Drives are moved into the following positions either
manually or automatically:
– Output channel 1: Height position = 30 %, Slat
position = 70 %
– Output channel 5: Height position = 20 %, Slat
position = 10 %
The "Scene object" object now receives a learning
telegram for scene number 13
– Output channel 1: Scene 1 Height position = 30 %,
Scene 1 Slat position = 70 %
– Output channel 5 does not respond
"Scene object" object receives "Retrieve scene
number 13" telegram:
– Output channel 1 moves into position 30 % height,
70 % slat
– Output channel 5 does not respond
Note the difference with the first retrieval of scene
number 13!
If you enabled the parameter "Replace scene values in
the actuator on download", then the scene values
saved in the device are replaced with your default
values on download. If you don't want to replace the
values in the device, then you must disable this
parameter.
Extension function for scenes
This function allows you to activate or re-program the
scene values for scene numbers 0–3 also using 1-bit
telegrams. Activate the extension function for the
device:
After you enable this function, two communication
objects appear to activate a scene number:
– "Retrieve scene 1/2"“ = "0": Scene number 0 is
activated
– "Retrieve scene 1/2"“ = "1": Scene number 1 is
activated
– "Retrieve scene 3/4"“ = "0": Scene number 2 is
activated
– "Retrieve scene 3/4"“ = "1": Scene number 3 is
activated
Two communication objects to set a scene number
also appear:
– "Set scene 1/2" = "0": Scene number 0 is
programmed
– "Set scene 1/2" = "1": Scene number 1 is
programmed
– "Set scene 3/4" = "0": Scene number 2 is
programmed
– "Set scene 3/4" = "1": Scene number 3 is
programmed
Tab Parameter
General Extension scenes
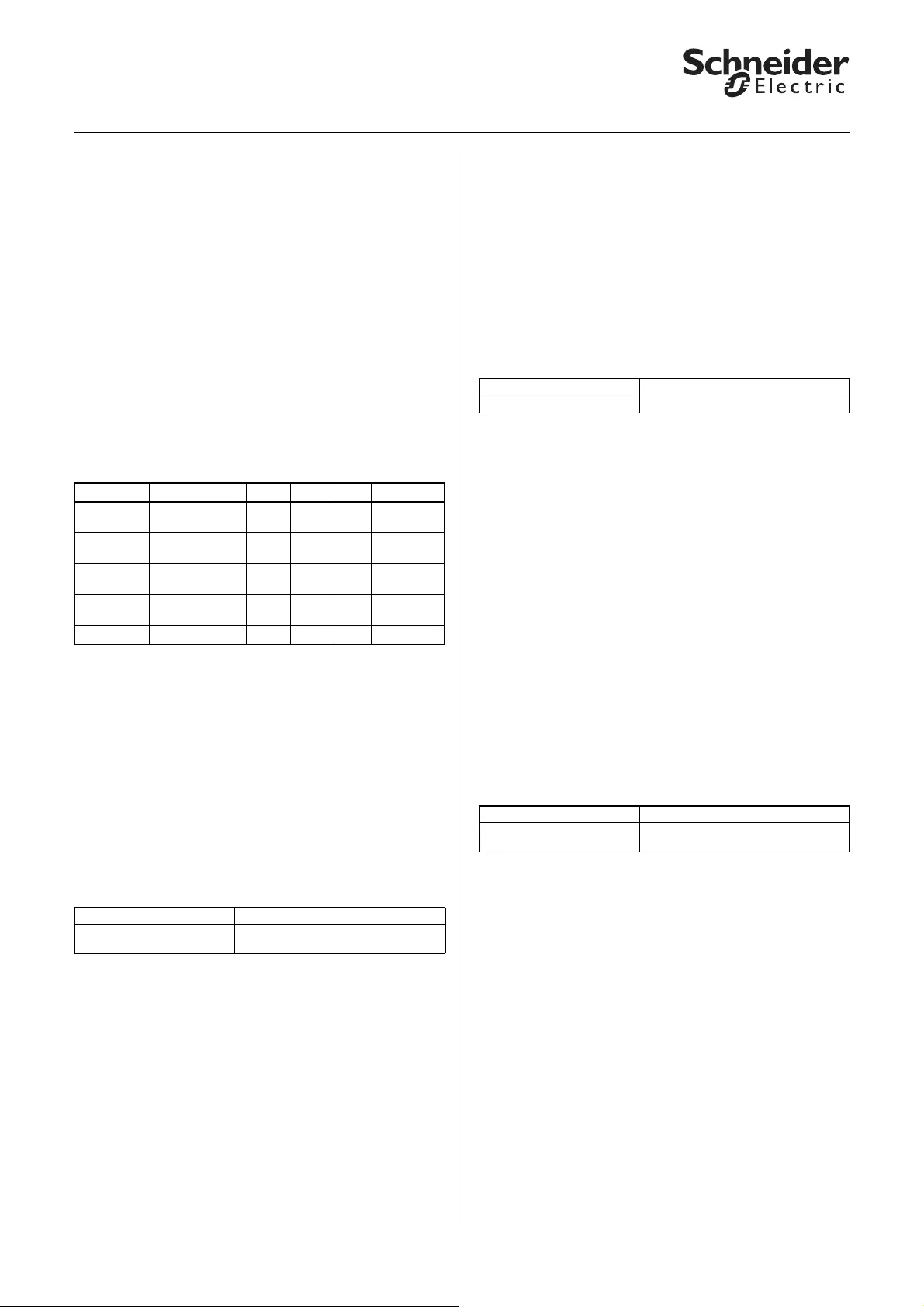
20
KNX Blind actuator REG-K/x/10 with manual mode
Art. no. MTN649802, MTN649804, MTN649808
© 2012 Schneider Electric
Application Shutter.Blind.Safety.Position.Manual 5700/1.1
|Note: The actions correspond to a normal
retrieval or learn command for scene numbers
0, 1, 2, or 3 or using the "Scene object" object.
The extension function is not available for scene
numbers 4 to 63. You can only address these
scene numbers using the "Scene object" object.
By using this extension function for scenes, you can
also avail of a preset function (retrieving saved position
values using 1-bit telegrams) if you want to use
automatic control instead of the actual preset function.
If you use the preset function and the extension
function for scenes together, you have up to eight
different positions available for each channel, which
you can retrieve using 1-bit telegrams.
Communication objects
Use the following objects to retrieve the preset
functions:
●Higher-level functions: General information
You can use four higher-level functions with the blind
actuator:
– Weather alarm
– Alarm function
– Disable function
– Limit travel range
Higher-level functions are executed before the basic
function and advanced functions.
You can prioritise the higher-level functions among
each other as you wish with the following parameter:
A higher-level function only becomes active if there is
no other higher-level function active at the same time.
If a higher-level function has been reset and there is
another higher-level function of lower priority active at
the same time, then the actions of the function of
lower priority are carried out.
●Higher-level functions: Weather alarm
The weather alarm functions allow you to protect the
blinds or roller shutters from weather damage such as
wind, rain and frost.. If an alarm is triggered for one of
these three weather events, the drives move into a
safe position and stay there until the event has passed
(depending on the priorities of the higher-level
functions).
Enabling the weather alarm function
Enable the weather alarm function for the blind
actuator as a higher-level function:
Once you have enabled the function, the new "General
weather alarm" tab appears. Here you can configure
the alarm function in detail for three wind alarms, one
rain alarm and one frost protection alarm.
You can enable and disable the individual alarm
functions separately. For each function you enable, a
communication object appears through which the
sensor signals are received.
Cyclical monitoring of sensor signals
The signals of the active weather sensors can be
monitored cyclically. The device then expects a
telegram from the sensor in question within the set
cycle time. If it doesn't receive this telegram within
the monitoring period, the associated weather alarm is
still triggered for security reasons (if for example the
sensor or the cable connection between the sensor
and the blind actuator is defective and no signalling
takes place in the event of a real alarm).
First define the time basis for the monitoring time:
Function Object name Type Prio Flags Behaviour
Scene
extension Retrieve scene
1/2 1 bit Low WC Receive
Scene
extension Retrieve scene
3/4 1 bit Low WC Receive
Scene
extension Set scene 1/2 1 bit Low WC Receive
Scene
extension Set scene 3/4 1 bit Low WC Receive
Scenes Scene object 1 byte Low WC Receive
Tab Parameter
General Priority sequence of higher-level
functions
Tab Parameter
General General weather alarm function
Tab Parameter
General weather alarm Time basis for monitoring time of
weather alarms
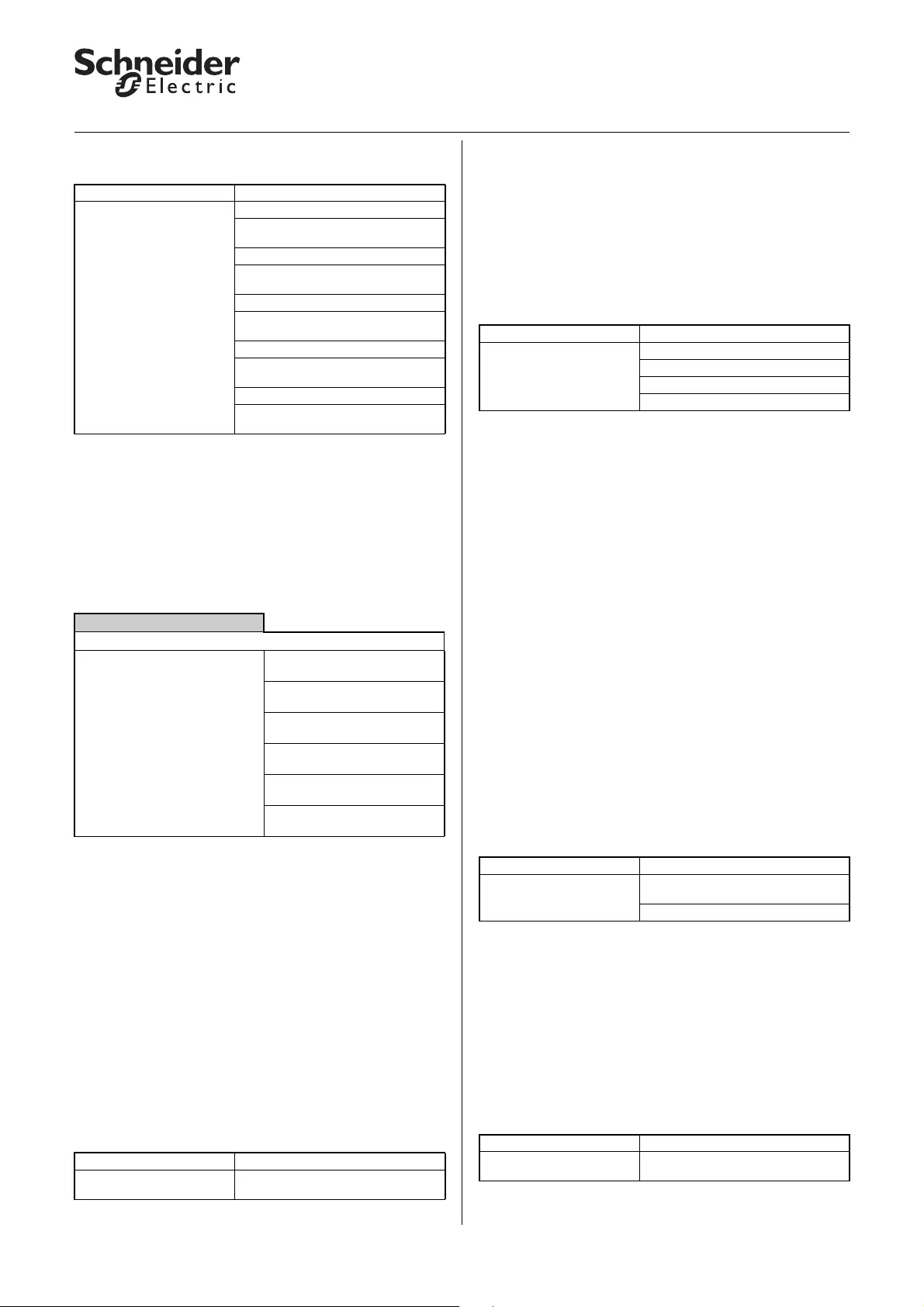
21
KNX Blind actuator REG-K/x/10 with manual mode
Art. no. MTN649802, MTN649804, MTN649808
© 2012 Schneider Electric
Application Shutter.Blind.Safety.Position.Manual 5700/1.1
Now you can set the relevant monitoring time for each
active sensor by specifying a factor:
The monitoring time is calculated by multiplying the
time basis by the factor. If you have disabled the value
of a factor, then cyclical measured value monitoring
will not take place for this sensor value. In this case 1-
bit telegrams trigger the alarm.
Weather alarm priorities
You can prioritise the weather alarms as you wish.
This prioritisation applies for all blind and roller-shutter
channels for which you have enabled the weather
protection function. Responses to a weather alarm
only become active if there is no other higher-level
weather alarm active at the same time. If a weather
alarm is reset and there is another lower-priority
weather alarm active at the same time, then the
responses of the lower-priority alarm are carried out.
Response of the individual drives in the event of a
weather alarm
After you have prioritised the weather alarm functions,
you can specify the behaviour of the drive in the event
of a weather alarm for each output channel. First you
must enable the weather alarm function for each
output channel:
When you have enabled the weather alarm function
for an output chanel, a new tab appears: "X: Weather
alarm"
First select how you want the drive to respond to an
active weather alarm. To protect against damage in the
event of high wind speeds, you can individually assign
each channel to one of the three wind sensor
categories, 1, 2 or 3. Alternatively, you can choose to
connect the three signals logically with the OR and
AND operators.
If a wind alarm becomes active, the drive has one of
the following responses depending on its settings:
– No response: The alarm function is inactive.
The weather alarm function is switched off. In case
of a wind alarm the channel is not disabled.
– Up: The drive moves into the top end position. The
weather alarm function is switched on and the
alarm function is active.
– Down: The drive moves into the lower end position.
The weather alarm function is switched on and the
alarm function is active.
– Move to position: The drive moves into the
specified safety position. The weather alarm
function is switched on and the alarm function is
active.
When the drive has responded accordingly, it remains
in this position and cannot be operated as long as the
weather alarm is active. Only when a higher-level
function becomes active will the response defined for
this function be carried out.
If you want the drive to move into a special safety
position, you can define this position using the
following parameters:
This safety position applies for all three weather
alarms if you selected the "Move to position"
parameter value as the response to a weather alarm.
Drive behaviour after weather alarm ends
When the sensor values of the weather sensors return
to within the normal measurement range, the weather
alarms are deactivated again. You can specify how you
want the drive to respond when the weather alarm
ceases to be active.
Tab Parameter
General weather alarm Wind alarm no. 1
(if wind alarm no. 1 is enabled) Factor
for wind alarm no. 1 monitoring time
Wind alarm no. 2
(if wind alarm no. 2 is enabled) Factor
for wind alarm no. 2 monitoring time
Wind alarm no. 3
(if wind alarm no. 3 is enabled) Factor
for wind alarm no. 3 monitoring time
Rain alarm
(if rain alarm enabled) Factor for rain
alarm monitoring time
Frost alarm
(if frost alarm enabled) Factor for
frost alarm monitoring time
General weather alarm
Parameter Setting
Priority sequence of weather
alarms 1. wind alarm, 2. rain alarm, 3.
frost alarm
1. wind alarm, 2. frost alarm,
3. rain alarm
1. rain alarm, 2. wind alarm,
3. frost alarm
1. rain alarm, 2. frost alarm,
3. wind alarm
1. frost alarm, 2. wind alarm,
3. rain alarm
1. frost alarm, 2. rain alarm,
3. wind alarm
Tab Parameter
X: Blind
X: Roller shutter Weather alarm
Tab Parameter
X: Weather alarm Responds to wind alarm no.
Response to wind alarms
Response to rain alarm
Response to frost alarm
Tab Parameter
X: Weather alarm Height position on weather alarm in
%
Slat position on weather alarm in %
Tab Parameter
X: Weather alarm Behaviour on end of all weather
alarm functions
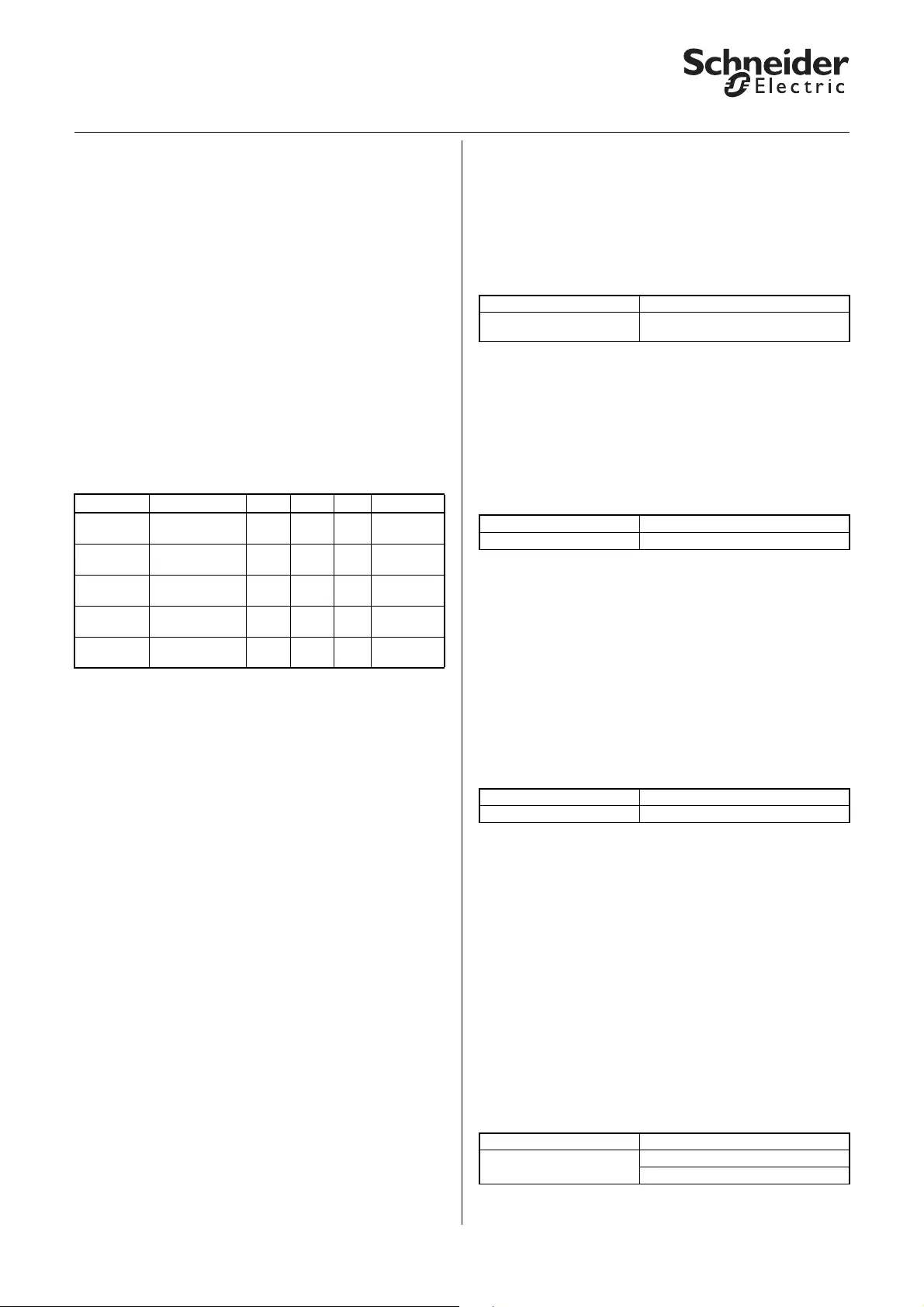
22
KNX Blind actuator REG-K/x/10 with manual mode
Art. no. MTN649802, MTN649804, MTN649808
© 2012 Schneider Electric
Application Shutter.Blind.Safety.Position.Manual 5700/1.1
The drive then carries out the following functions:
– No response: The drive remains in its current
position. The alarm function is terminated.
– Up: The drive moves into the top end position. The
alarm function is terminated.
– Down: The drives moves into the lower end
position. The alarm function is terminated.
– Move into position prior to weather alarm: The drive
returns to the same position it was in before the
weather alarm.The alarm function is terminated.
– Assume current automatic position: This setting
only makes sense if the automatic function is
active. The drive moves into the last requested
automatic position. The alarm function is
terminated.
Communication objects
The following communication objects are available:
●Higher-level functions: Alarm function
In the event of an alarm situation, the drive can be
moved into a specified alarm position. When the drive
reaches the alarm postion, further operation is
disabled. Now only a higher-level function of higher
priority can move the drive into another position. You
can activate the alarm function for each output
channel individually:
After you activate the alarm function, the
communication object "Alarm object" appears for this
channel. This object allows you to switch the function
on and off.
You can make the other function settings in the
additional "X: Alarm function" tab.
First select the object value that you want to switch on
the alarm function:
Values to be set:
– For object value "1": Object value "1" switches the
alarm function on. If the object value "0" is received,
the alarm function is switched off again.
– For object value "0": Object value "0" switches the
alarm function on. A telegram with the object value
"1" deactivates the function again.
Drive behaviour when alarm function is activated
Here you specify how you want the blind actuator to
behave when the alarm function is enabled:
Values to be set:
– No response: The drive remains in its current
position.
– Up: The drive moves into the top end position.
– Down: The drives moves into the lower end
position.
– Move to position: The drives moves into the
specified safety position.
After the drive has carried out the desired action, it
remains in this position and cannot be operated as
long as the alarm function is active. Only when a
higher-level function becomes active will the response
defined for this function be carried out.
You can define a special safety position for the alarm
function:
Function Object name Type Prio Flags Behaviour
Weather
alarm Wind alarm 1 1 bit Low WC Receive
Weather
alarm Wind alarm 2 1 bit Low WC Receive
Weather
alarm Wind alarm 3 1 bit Low WC Receive
Weather
alarm Rain alarm 1 bit Low WC Receive
Weather
alarm Frost alarm 1 bit Low WC Receive
Tab Parameter
X: Blind
X: Roller shutter Alarm function
Tab Parameter
X: Alarm function Alarm
Tab Parameter
X: Alarm function Behaviour on alarm start
Tab Parameter
X: Alarm function Height position on alarm start in %
Slat position on alarm start in %
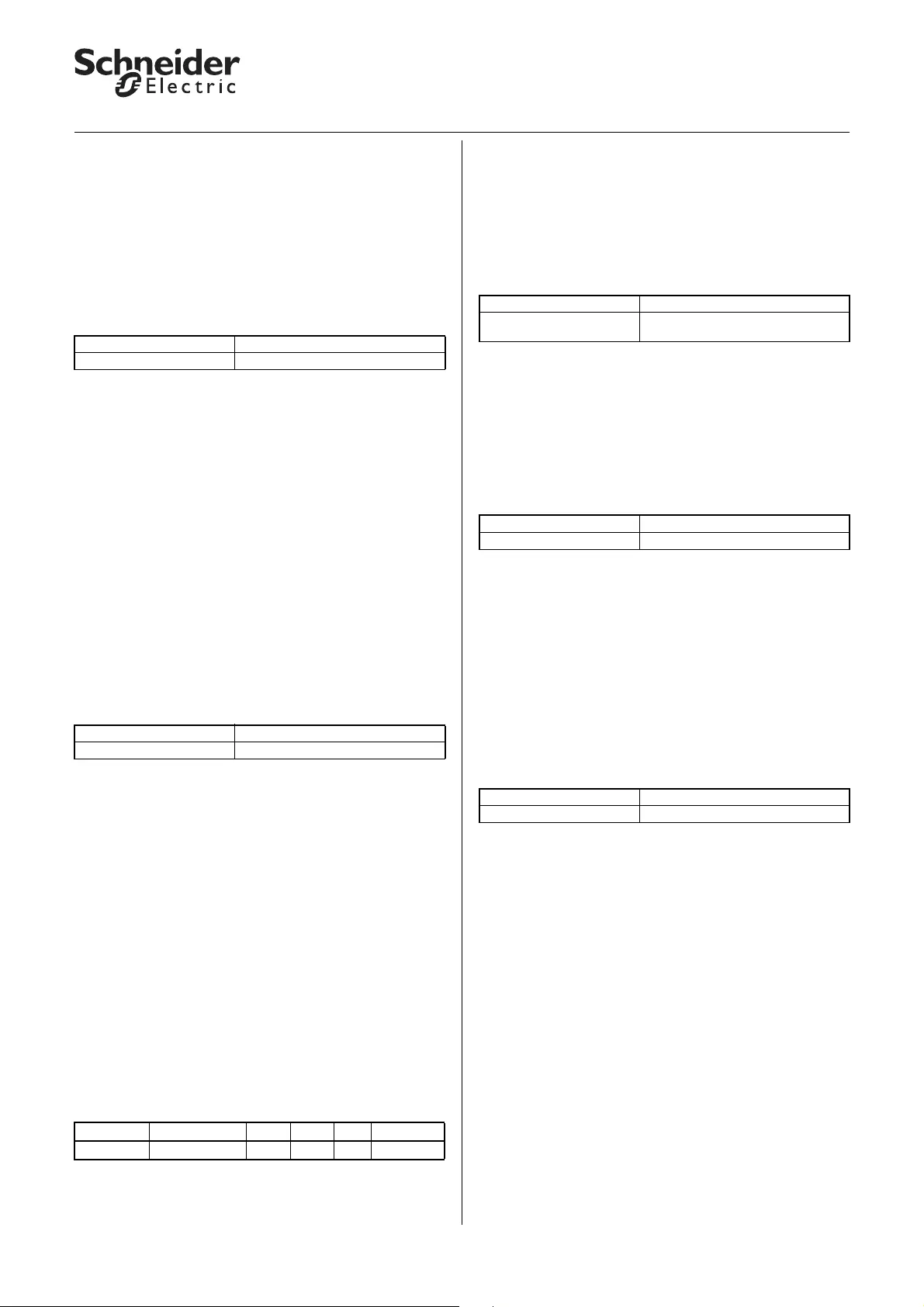
23
KNX Blind actuator REG-K/x/10 with manual mode
Art. no. MTN649802, MTN649804, MTN649808
© 2012 Schneider Electric
Application Shutter.Blind.Safety.Position.Manual 5700/1.1
The drive moves into this safety position if you
selected the "Move into position" parameter value as
the behaviour when the alarm function begins.
Drive behaviour when alarm function has finished
When a new object value has switched the alarm
function off, you can operate the drive as normal
again. If you want the drive to carry out an automatic
action when the alarm function ends, you can define
this action using the following parameter:
Values to be set:
– No response: The drive remains in its current
position.
– Up: The drive moves into the top end position.
– Down: The drives moves into the lower end
position.
– Move into position prior to alarm: The drive returns
to the same position it was in before the alarm.
– Assume current automatic position: This setting
only makes sense if the automatic function is
active. The drive moves into the last requested
automatic position.
Alarm function on bus voltage recovery
This parameter allows you to specify how you want
the alarm function to respond when bus voltage is
recovered:
Values to be set:
– Inactive: After bus voltage has been recovered, the
alarm function is deactivated, regardless of its
status prior to bus voltage failure.
– Active: The alarm function is activated when bus
voltage has recovered. The output relay responds in
line with your settings for behaviour following bus
voltage recovery (see the section "Operating
behaviour on failure and recovery of supply
voltage").
– As before bus voltage failure: The alarm function
resumes the status it had before bus voltage failure.
Your settings regarding behaviour following bus
voltage recovery determine the output relay's
response in this case also.
Communication objects
The following communication objects are available:
●Higher-level functions: Disable function
In the event of a special operating status, the drive can
move into a specified disable position. When the drive
has reached the disable position, operation is no
longer possible. Now only a higher-level function of
higher priority can move the drive into another
position. You can activate the disable function for each
output channel individually:
After you activate the disable function, the "Disable
object" communication object appears for this
channel. This object allows you to switch the function
on and off.
You can make the other function settings in the
additional "X: Disable function" tab.
First select the object value that you want to switch on
the disable function:
Values to be set:
– For object value "1": Object value "1" switches the
disable function on. If the object value "0" is
received, the disable function is switched off again.
– For object value "0": Object value "0" switches the
disable function on. A telegram with the object
value "1" deactivates the function again.
Drive behaviour when disable function is activated
Here you specify how you want the blind actuator to
behave when the disable function is enabled::
Values to be set:
– No response: The drive remains in its current
position.
– Up: The drive moves into the top end position.
– Down: The drives moves into the lower end
position.
– Move to position: The drives moves into the
specified safety position.
After the drive has carried out the desired action, it
remains in this position and cannot be operated as
long as the disable function is active. Only when a
higher-level function becomes active will the response
defined for this function be carried out.
Tab Parameter
X: Alarm function Behaviour on alarm end
Tab Parameter
X: Alarm function Alarm status on bus voltage recovery
Function Object name Type Prio Flags Behaviour
Channel X Alarm object 1 bit Low WC Receive
Tab Parameter
X: Blind
X: Roller shutter Disable function
Tab Parameter
X: Disable function Lock
Tab Parameter
X: Disable function Behaviour on lock start
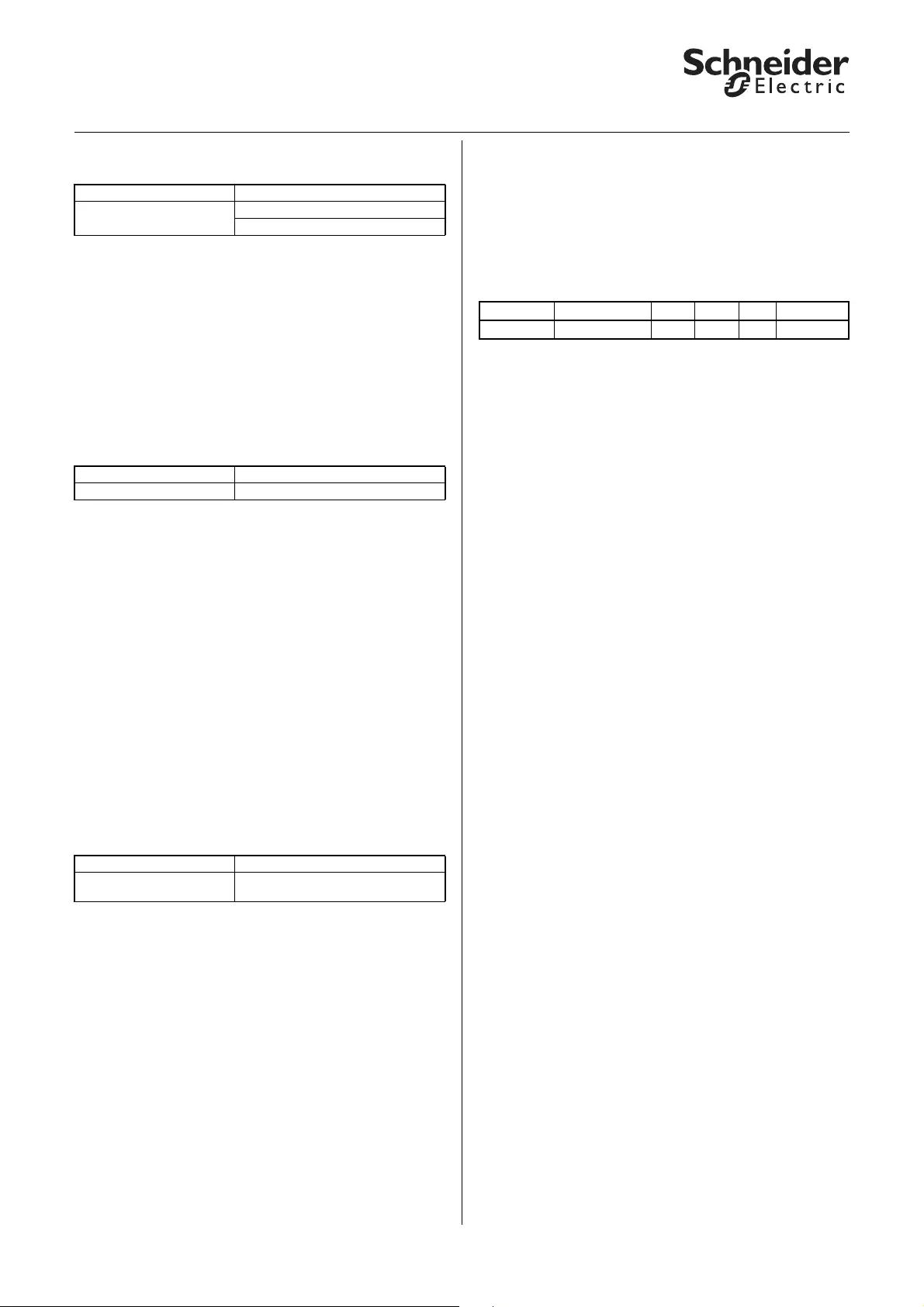
24
KNX Blind actuator REG-K/x/10 with manual mode
Art. no. MTN649802, MTN649804, MTN649808
© 2012 Schneider Electric
Application Shutter.Blind.Safety.Position.Manual 5700/1.1
You can define a special safety position for the disable
function:
The drive moves into this safety position if you
selected the "Move into position" parameter value as
the behaviour when the disable function begins.
Drive behaviour when disable function has
finished
When a new object value has switched the disable
function off, you can operate the drive as normal
again. If you want the drive to carry out an automatic
action when the disable function ends, you can define
this action using the following parameter:
Values to be set:
– No response: The drive remains in its current
position.
– Up: The drive moves into the top end position.
– Down: The drives moves into the lower end
position.
– Move into position prior to disable: The drive returns
to the same position it was in before the disable
function.
– Assume current automatic position: This setting
only makes sense if the automatic function is
active. The drive moves into the last requested
automatic position.
Disable function on bus voltage recovery
This parameter allows you to specify how you want
the disable function to respond when bus voltage fails:
Values to be set:
– Inactive: After bus voltage has been recovered, the
disable function is deactivated, regardless of its
status prior to bus voltage failure.
– Active: The disable function is activated when bus
voltage has been recovered. The output relay
responds in line with your settings for behaviour
following bus voltage recovery (see the section
"Operating behaviour on failure and recovery of
supply voltage").
– As before bus voltage failure: The disable function
resumes the status it had before bus voltage failure.
Your settings regarding behaviour following bus
voltage recovery determine the output relay's
response in this case also.
Communication objects
The following communication objects are available:
Tab Parameter
X: Disable function Height position on lock start in %
Slat position on lock start in %
Tab Parameter
X: Disable function Behaviour on lock end
Tab Parameter
X: Disable function Behaviour of disable function on bus
voltage recovery
Function Object name Type Prio Flags Behaviour
Channel X Disable object 1 bit Low WC Receive
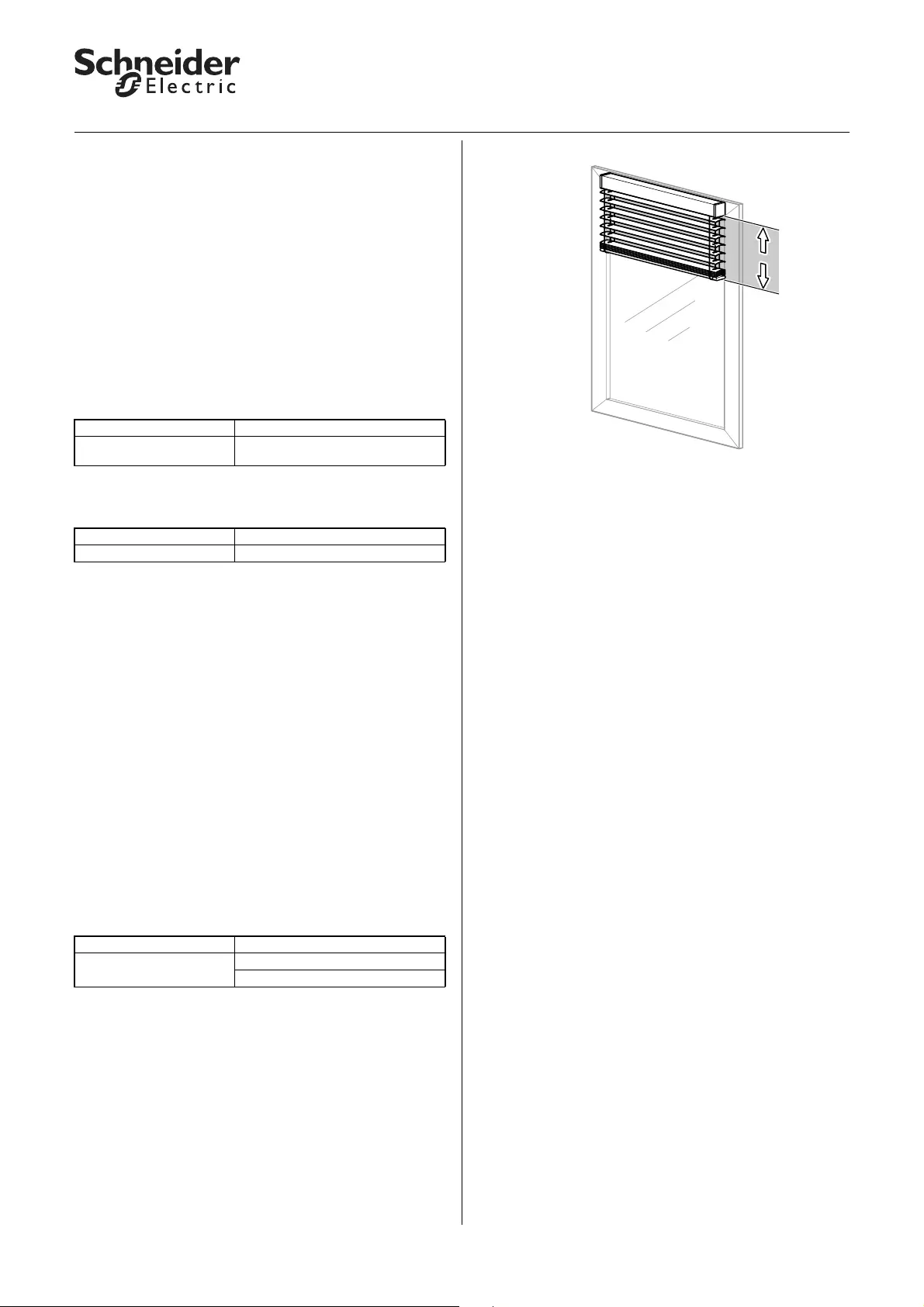
25
KNX Blind actuator REG-K/x/10 with manual mode
Art. no. MTN649802, MTN649804, MTN649808
© 2012 Schneider Electric
Application Shutter.Blind.Safety.Position.Manual 5700/1.1
●Higher-level functions: Limitation of the
movement range
For certain applications, e.g. open pivot-hung
windows, it can be helpful or necessary to limit the
possible movement range of a drive temporarily or
permanently. If the movement range has been limited,
then during manual operation, automatic functions,
scene retrievals or presets, the drive can only move
within the defined limits. The limit also applies for
movement commands from functions of lower
priority. Only a higher-level function of higher priority
can move the drive into another position beyond the
limit.
You can activate the movement range limitation for
each output channel individually:
After you have activated the movement range limits,
the additional "X: Movement range limits" tab appears:
Values to be set:
– Immediately after bus voltage recovery: The
function becomes active immediately after bus
voltage recovery or a download. The drive can only
move between the limit values. Only a function of
higher priority can move the drive into a position
beyond the limit.
– For object value "1": Object value "1" switches the
limit on. If the object value "0" is received, the entire
movement range is enabled again.
– For object value "0": Object value "0" switches the
limit on. A telegram with the object value "1"
deactivates the limit again.
When activated by an object value, an additional
communication object "Activate movement limits"
appears for this channel. This object allows you to
switch the limit on and off.
You can set the limits of the movement range using
additional parameters:
When the limit function is active, the drive only moves
between the limit values. The limit applies for all
movement commands from manual operation,
automatic functions, scenes, presets and for
movements from functions of lower priority.
If the drive is outside the limits when the movement
range limitation is activated, then it is automatically
moved to the nearest limit and remains there.
|Note: Remember to set the lower limit value
higher than the top limit value because
otherwise the drive can't move.
When a drive reaches its movement range limits, this
is reported by a status object on the bus. Dependent
functions, for example opening a window, can now be
carried out. The next section on "Status responses"
has more information on this.
Reference movement after initialisation
½Caution!
Blinds/roller shutters could be damaged.
The blinds/roller shutter may move beyond the
movement range limits into windows that may
be open. Pay attention therefore to where you
want the reference movement to go.
After a download or bus voltage recovery, a reference
movement takes place following initialisation, even if
the "General reference movement" function is
disabled. The blinds/roller shutter may move beyond
the limits of the movement range into windows that
may be open.
Pay attention therefore to where you want the
reference movement to go. In general, the reference
movement after initialisation is towards the top end
position. Only when the "Reference position" is set to
"down" does a reference movement take place
towards the lower end position.
Tab Parameter
X: Blind
X: Roller shutter Movement range limits
Tab Parameter
X: Movement range limits Limit movement range
Tab Parameter
X: Movement range limits upper limit value in %
lower limit value in %
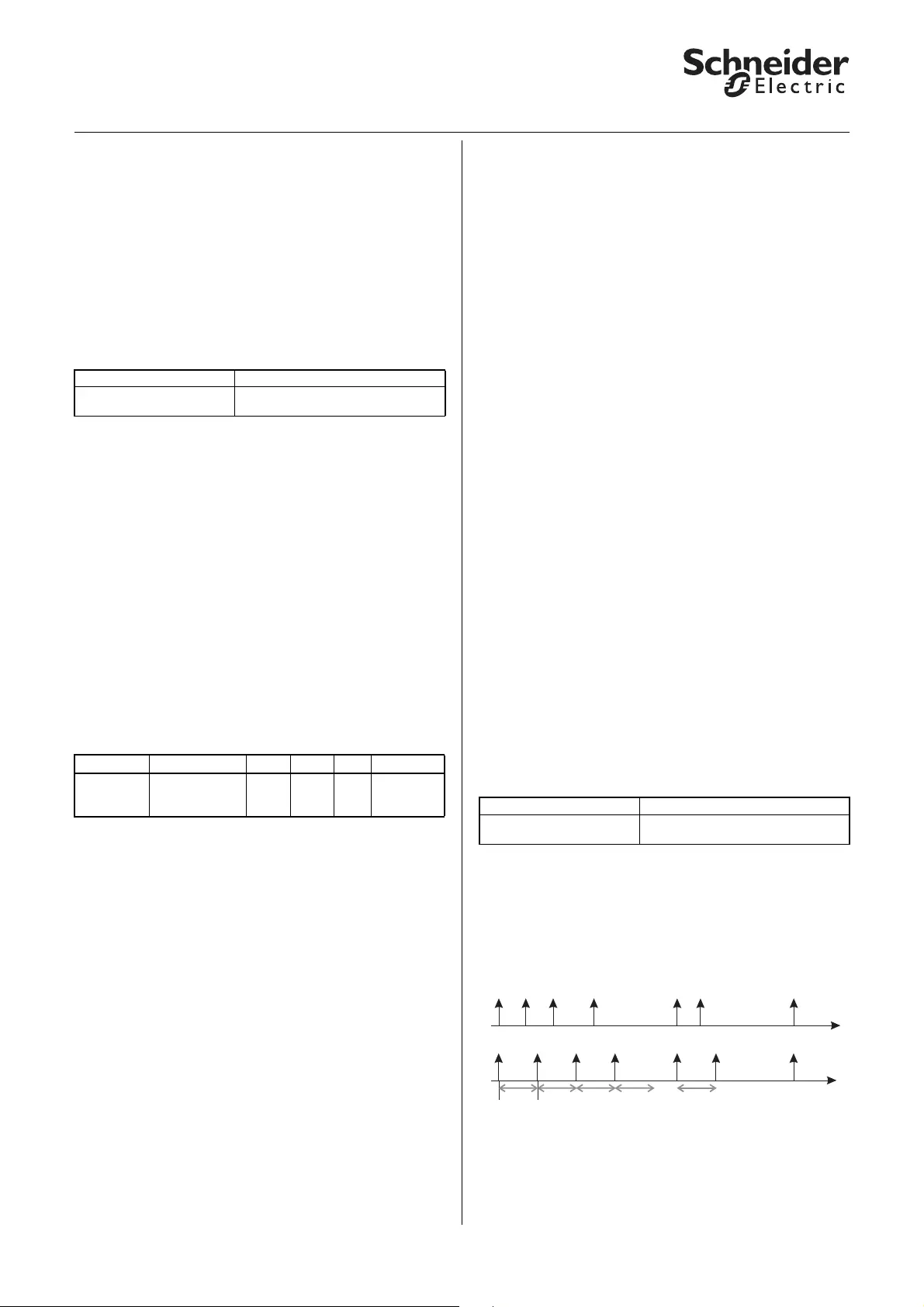
26
KNX Blind actuator REG-K/x/10 with manual mode
Art. no. MTN649802, MTN649804, MTN649808
© 2012 Schneider Electric
Application Shutter.Blind.Safety.Position.Manual 5700/1.1
In the case of a reference movement, the "Movement
range limit status feedback" object receives the value
"0". The blind/roller shutter only moves in the travel
range after the reference movement has completed.
Drive behaviour after movement limitation ends
If object values are responsible for limiting the
movement range and a new object value disables the
limitation, then you can operate the drive as normal
again. If you want the drive to carry out an automatic
action in this case, you can define this action using the
following parameter:
Values to be set:
– No response: The drive remains in its current
position.
– Up: The drive moves into the top end position.
– Down: The drives moves into the lower end
position.
– Move into position prior to movement limitation:
The drive returns to the same position it was in
before movement limitation.
– Assume current automatic position: This setting
only makes sense if the automatic function is
active. The drive moves into the last requested
automatic position.
Communication objects
The following communication objects are available:
●Status messages/status feedback
The software application provides you with numerous
options to report the current device status and the
status of output channels via communication objects.
Depending on these status messages, you can trigger
certain control processes or enable and disable
functions in the system.
So for example, opening a window is permitted if a
blind drive reports that it has reached the height
position within a movement range limitation. The
window status in turn can be used to deactivate an
active movement range limitation.
In addition, status messages are also suitable for
displaying current operating statuses by means of
visualisation software.
The status messages of the output channels are made
available through communication objects. You can set
the transmission characteristics of these status
objects to one of the following values using
parameters:
– disabled
The status object is not active.
– active status feedback object
When the status changes, the new status is
automatically transmitted.
– passive status object
The status object does not transmit its values. But
the current status is available and can be read out by
other bus devices.
Transmission behaviour of the status messages in
time
You can prioritise the interval between two status
telegrams for the device. This setting applies for the
transmission behaviour of all status messages.
If there is only one pending transmission job, then the
message is sent immediately. If there are several
status messages pending, then the first one is sent
immediately and the remainder are staggered
according to the delay time specified in the "Minimum
interval between status messages" parameter.
Tab Parameter
X: Movement range limits Behaviour at end of movement
limitation
Function Object name Type Prio Flags Behaviour
Channel X Activate
movement
limits
1 bit Low WC Receive
Tab Parameter
General Minimum interval between status
messages
Status reports
Telegrams
Minimum interval
S1 S2 S3 S4 S5 S6 S7
S1 S2 S3 S4 S5 S6 S7
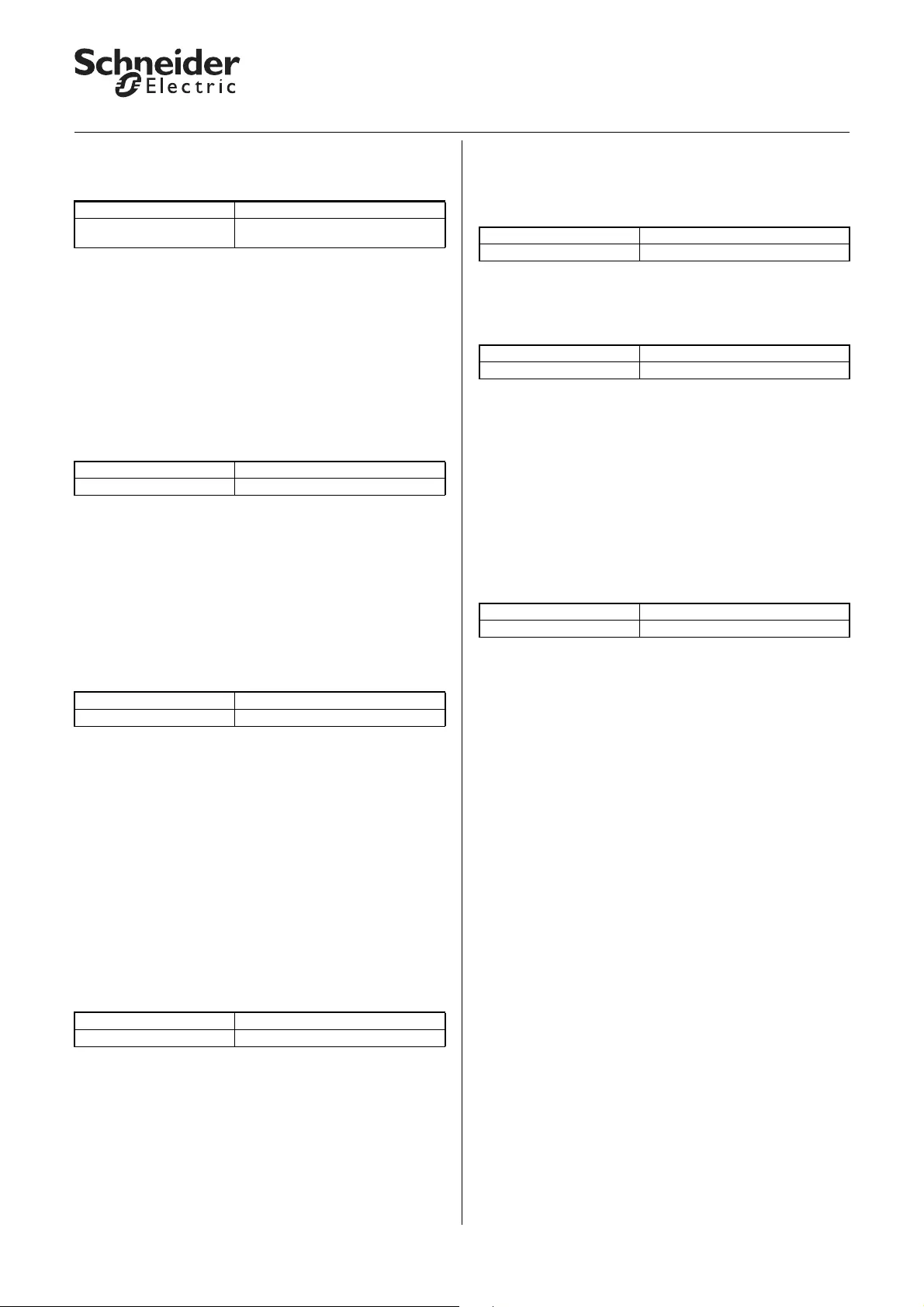
27
KNX Blind actuator REG-K/x/10 with manual mode
Art. no. MTN649802, MTN649804, MTN649808
© 2012 Schneider Electric
Application Shutter.Blind.Safety.Position.Manual 5700/1.1
If you want to activate the status messages for an
output channel, then you have to enable the "Status
messages" parameter:
A new tab "X: Status messages" then appears for this
output channel. Here you make settings for the
possible status messages.
Height status
The current position of the drive is available as a value
between 0 –100 %. The associated status objects
change name depending on whether the status is to
be transmitted (Height status feedback) or read out
(Height status).
The height status object is only updated when the
drive has reached a fixed position after a movement.
Slat status
The current angle of rotation of the blind slats is
available as a value between 0 –100 %. The
associated status objects change name depending on
whether the status is to be transmitted (Slat status
feedback) or read out (Slat status).
The slat status object is only updated when the drive
has reached a fixed position after a movement.
Automatic status
The status message of the automatic function takes
place via the "Automatic lock" object of the output
channels (see the section "Automatic control"). This is
a bidirectional object. In addition to its status function,
it also serves to enable and disable the automatic
function directly using bus telegrams.
If you want to display an activation and lock of the
automatic function via operating telegrams as a status
function, then set the "Automatic status" to the
desired value:
The current object value of the "Automatic lock" object
is simultaneously the status value.
Disable message status
There are two types of disable messages you can
activate as the status message: a drive lock or a
movement range limitation.
Disable message type = Drive lock
A drive lock is triggered by the higher-level functions
weather alarm, alarm function and disable function.
If one of the higher-level functions is active and the
drive has reached its defined safety position, the
status object receives the value "1". When the drive is
enabled again, the object value of the status message
changes to "0".
Disable message type = Movement range limit
If you are using the higher-level function movement
range limitation and other control functions depend on
whether the drive has reached its limit if movement
range limitation is active, then you can report this
using this status type:
The value of the status object receives the object
value "1" if movement range limitation is active and the
drive has reached one of the specified limits.
– If, when movement range limitation is activated, the
drive is already within the specified limits, then the
status object receives the object value "1"
immediately.
– If a function of higher priority causes the drive to
leave the movement range or if the limitation is
cancelled, then object value switches to "0".
Tab Parameter
X: Blind
X: Roller shutter Status messages
Tab Parameter
X: Status messages Height status
Tab Parameter
X: Status messages Slat status
Tab Parameter
X: Status messages Automatic status
Tab Parameter
X: Status messages Disable message type
Tab Parameter
X: Status messages Drive lock status
Tab Parameter
X: Status messages Movement range limit status
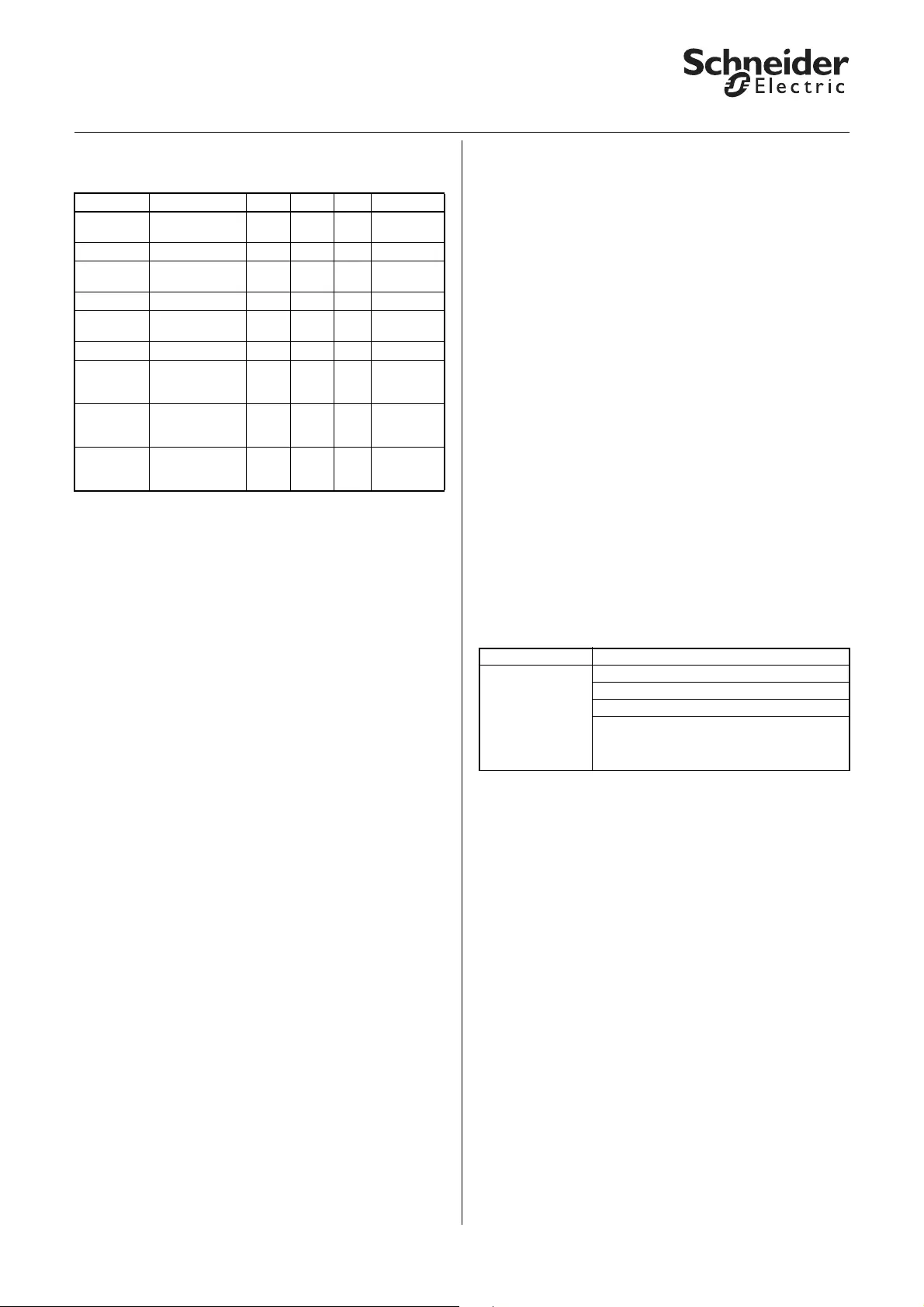
28
KNX Blind actuator REG-K/x/10 with manual mode
Art. no. MTN649802, MTN649804, MTN649808
© 2012 Schneider Electric
Application Shutter.Blind.Safety.Position.Manual 5700/1.1
Communication objects
The following communication objects are available:
●Manual operation and status displays
On the front of the device there is a channel key and a
yellow LED for each channel to display the operating
statuses of the channel (channel status LED).
In addition to the channel keys for the output channels
and the channel status LED, the device also has a
toggle switch and a red LED labelled "Manual" (manual
operation LED). The toggle switch allows you to
activate and deactivate manual operation. Another
green operation LED labelled "RUN" (RUN LED)
indicates that the device is ready for operation.
The programming key for programming the physical
address of the device and an associated red
programming LED are located under the cover of the
bus connection.
|Note: For more information see the chapter
"Operation".
After the mains or bus voltage has been connected,
you can move the connected drives using the
operating keys, if you have activated manual
operation. The status LEDs allocated to the channels
indicates the current switching status.
Setting manual operation
You can set the blind actuator in such a way that it can
be operated using the channel keys:
If "Manual operation type" = "Manual operation only"
and you press the manual key, the device is in pure
manual operation (manual LED lights up). It does not
evaluate any bus telegrams. The connected drives can
only be moved manually using the channel keys. Due
to the fact that bus telegrams are suppressed, the
drives can also be moved if higher-level functions are
active.
½Caution!
When operating blinds or roller shutters in
"Manual operation only" using the channel keys,
safety functions such as weather alarm
position, alarm position, disable position or
travel range no longer work. To prevent damage
to the blind/roller shutter, you should therefore
be very careful when operating manually!
Function Object name Type Prio Flags Behaviour
Channel X Height status
feedback 1 bit Low CRT Transmit/
Read out
Channel X Height status 1 bit Low CR Read out
Channel X Slat status
feedback 1 bit Low CRT Transmit/
Read out
Channel X Slat status 1 bit Low CR Read out
Channel X Drive lock status
feedback 1 bit Low CRT Transmit/
Read out
Channel X Drive lock status 1 bit Low CR Read out
Channel X Movement
range limit
status feedback
1 bit Low CRT Transmit/
Read out
Channel X Movement
range limit
status
1 bit Low CR Read out
Channel X Automatic lock 1 bit Low CRW
TTransmit/
Receive/
Read out
Tab Parameter
General Manual operation type
Manual operation activation
Time-dependent reset of manual operation
(if "Time-dependent reset of manual
operation" is enabled):
Time in minutes when hand operation will be
automatically reset (5-255)
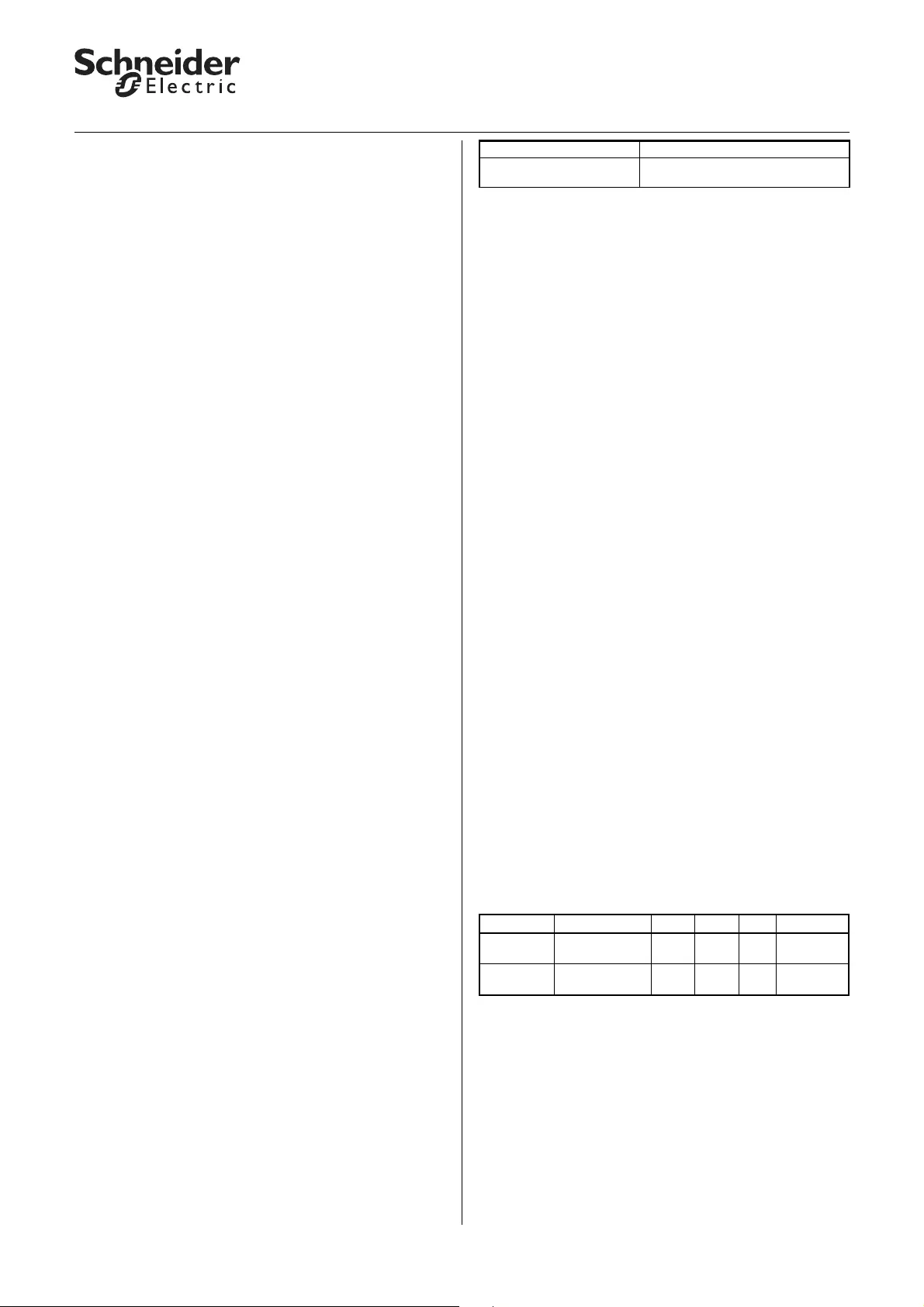
29
KNX Blind actuator REG-K/x/10 with manual mode
Art. no. MTN649802, MTN649804, MTN649808
© 2012 Schneider Electric
Application Shutter.Blind.Safety.Position.Manual 5700/1.1
If the "Manual operation type" parameter has the value
"Bus and manual operation", you can operate the
connected drives manually with the channel keys and
with bus telegrams. This has the same effect as
receiving a bus telegram. If however during this mode
one of the higher-level functions (weather alarm, alarm
function, disable function or limit travel range) is
active, then manual operation is disabled.
First select the desired operation mode for manual
operation, as described above. Then you can select
the settings for enabling manual operation:
– disabled
Switching to manual operation using the manual
key is not possible.
– enabled
Switching to manual operation using the manual
key is possible. The manual LED indicates the
current manual operation mode.
– enabled with status message
Switching to manual operation using the manual
key is possible. The manual LED indicates the
current manual operation mode. When you switch
to manual operation mode, a telegram with the
value "1" is sent via the "Manual operation status"
object. When manual operation is reset, a telegram
with the value "0" is sent.
– Enable via object
The "Enable manual operation" object allows you to
enable and disable the switching option for manual
operation. Manual operation is enabled on receipt of
a telegram with the value "1" and disabled on receipt
of a telegram with the value "0".
– Enable via object with status message
In addition to enabling manual operation with the
"Enable manual operation" object, the "Manual
operation status" object reports the switching
status.
|Note: To switch the blind actuator to manual
operation, press the manual key before
pressing a channel key.
Resetting manual operation dependent on time
You can limit the switch to manual operation on a time
basis. To do this, set the "Time-dependent reset of
manual operation" parameter to "enabled".
Then set the "Time for automatic reset of manual
operation in minutes" parameter. When the time you
specify here expires, the device automatically resets
manual operation. The manual LED indicates the
current operating status.
Enabling manual operation on bus voltage failure
If bus voltage fails, then you can provide users with an
additional control option for the connected loads:
manual operation. Mains voltage must still be present
however. You can enable manual operation on bus
voltage failure for each channel individually. Enable or
disable the following parameter:
"Manual operation on bus voltage failure"
disabled
If bus voltage has failed and you press a channel key,
the blind/roller shutter drive does not respond.
"Manual operation on bus voltage failure" enabled
You can continue to operate the connected drive using
the channel keys in the event of bus voltage failure
(press manual key). Manual operation during bus
voltage failure is possible independently of the
settings for manual operation activation. The status
LEDs indicate the current output status. When bus
voltage is recovered, manual operation is
automatically reset.
½Caution!
Risk of damage!
When using the channel keys to manually
operate blinds or roller shutters during a bus
failure, safety functions such as the weather
alarm position, alarm position, disable position
and travel range no longer have any effect.
To prevent damage to the blind/roller shutter,
you should therefore be very careful when
operating manually!
Manual operation for blind/roller shutter
When manual operation is enabled, you can move
connected drives using the channel keys (see section
"Operation").
The running time of the drive is preset to 2 min and the
switching time to 500 ms. Please observe the
specifications of the drive manufacturer.
If you press a channel key when manual operation is
not active or has been temporarily disabled by a
higher-level function, nothing happens.
Communication objects
The following communication objects are available:
Tab Parameter
X: Blind
X: Roller shutter Manual operation on bus voltage
failure (mains voltage present)
Function Object name Type Prio Flags Behaviour
Manual
operation Enable manual
operation 1 bit Low CW Receive
Manual
operation Manual
operation status 1 bit Low CRT Transmit/
Read out
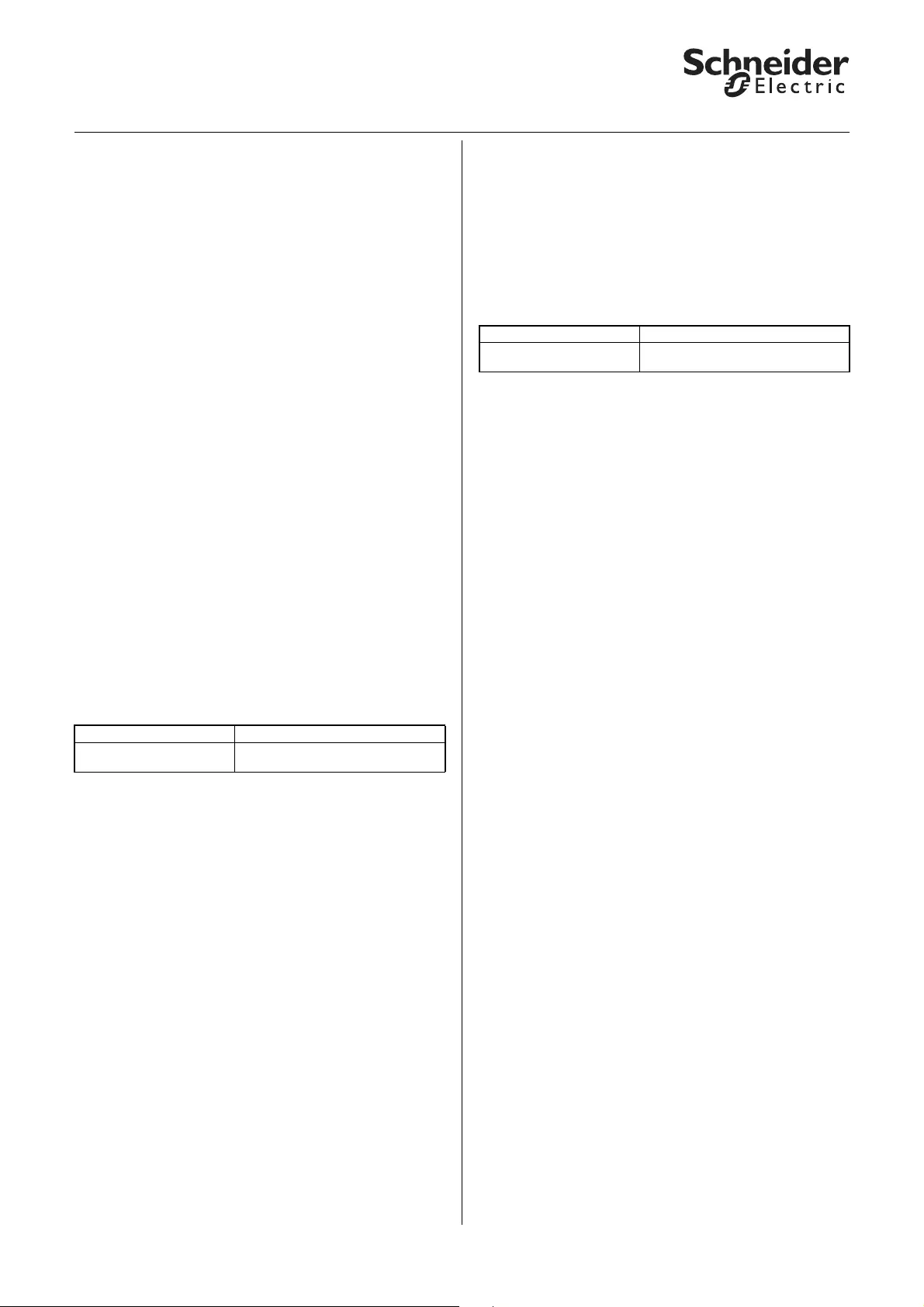
30
KNX Blind actuator REG-K/x/10 with manual mode
Art. no. MTN649802, MTN649804, MTN649808
© 2012 Schneider Electric
Application Shutter.Blind.Safety.Position.Manual 5700/1.1
●Behaviour after failure and recovery of supply
voltage
|Note: Normally, the device is connected to both
bus and mains voltage. All device functions can
only be fully guaranteed if the device is
receiving both supply voltages correctly.
If the engine supply voltage for the loads fails or is
recovered, the blind actuator itself doesn't carry out
any action. Please note the following however:
½Caution!
Switching on the engine can cause the drives to
move if the output relay is switched on at the
time.
In order to avoid bodily injury or material
damage, ensure that before switching the
supply voltage on again that all connected blinds
and roller shutters can move freely.
|Note: If only bus voltage is available, the blind
actuator can generally carry out all functions,
possibly with a short time delay however (e.g.,
switching relays, slat adjustment). Manual
operation is possible.
Without bus voltage (mains voltage only), the blind
actuator may only work in manual operation without
bus communication. You can operate the blind or roller
shutter directly using the channel keys.
If you want the blind actuator to respond in a certain
way when supply voltage fails unexpectedly during
operation, then you can configure failure behaviour for
each channel.
When you have enabled the failure behaviour for a
channel, the additional tab "X: Failure behaviour"
appears. Here you can set more parameters. These
depend on the type of voltage failure:
– Possibility 1:
Bus voltage failure/recovery
Mains voltage present
– Possibility 2:
Bus voltage present
Mains voltage failure/recovery
– Possibility 3:
Bus voltage failure/recovery
Mains voltage failure/recovery
The setting options in the "X: Failure behaviour" tab
vary according to the type of voltage failure.
Possibility 1: Bus voltage failure/recovery, mains
voltage present
Bus voltage has failed
The RUN LED is not lit when bus voltage fails. If the
output channels for manual operation are enabled in
the event of bus voltage failure, you can operate the
connected drives using the channel keys.
Behaviour of channels for blind/roller shutters
You can set failure behaviour as follows:
Possible settings:
– no response
The drive remains in its current status, in other
words, it doesn't move or it completes its current
movement until the running times have expired.
–Stop
The drive stops immediately.
–Up
The drive moves upwards. If it was in the middle of
an downwards movement, then it stops and waits
the default pause on reverse time of 300 ms before
beginning the upwards movement.
–Down
The drive moves downwards. If it was in the middle
of an upwards movement, then it stops and waits
the default pause on reverse time of 300 ms before
beginning the downwards movement.
½Caution!
If it is possible that your settings may result in a
change of direction in the event of bus voltage
failure (up or down settings), it is important to
remember the pause on reverse. This is pre-set
to a fixed value of 300 ms for bus voltage failure.
The parameterised value for the drive is not
active in this case. If the drive in use requires a
longer pause on reverse (see manufacturer
specifications), then you may not use the "up" or
"down" settings in order to avoid damaging the
drive.
When making your settings, ensure that the higher-
level safety functions are not acitve during bus voltage
failure. So that this doesn't cause damage, it makes
sense to make the settings in such a way that the
drive assumes a safe position during bus voltage
failure.
Tab Parameter
X: Blind
X: Roller shutter Failure behaviour
Tab Parameter
X: Failure behaviour Behaviour on bus voltage failure
(fixed pause on reverse = 300 ms)
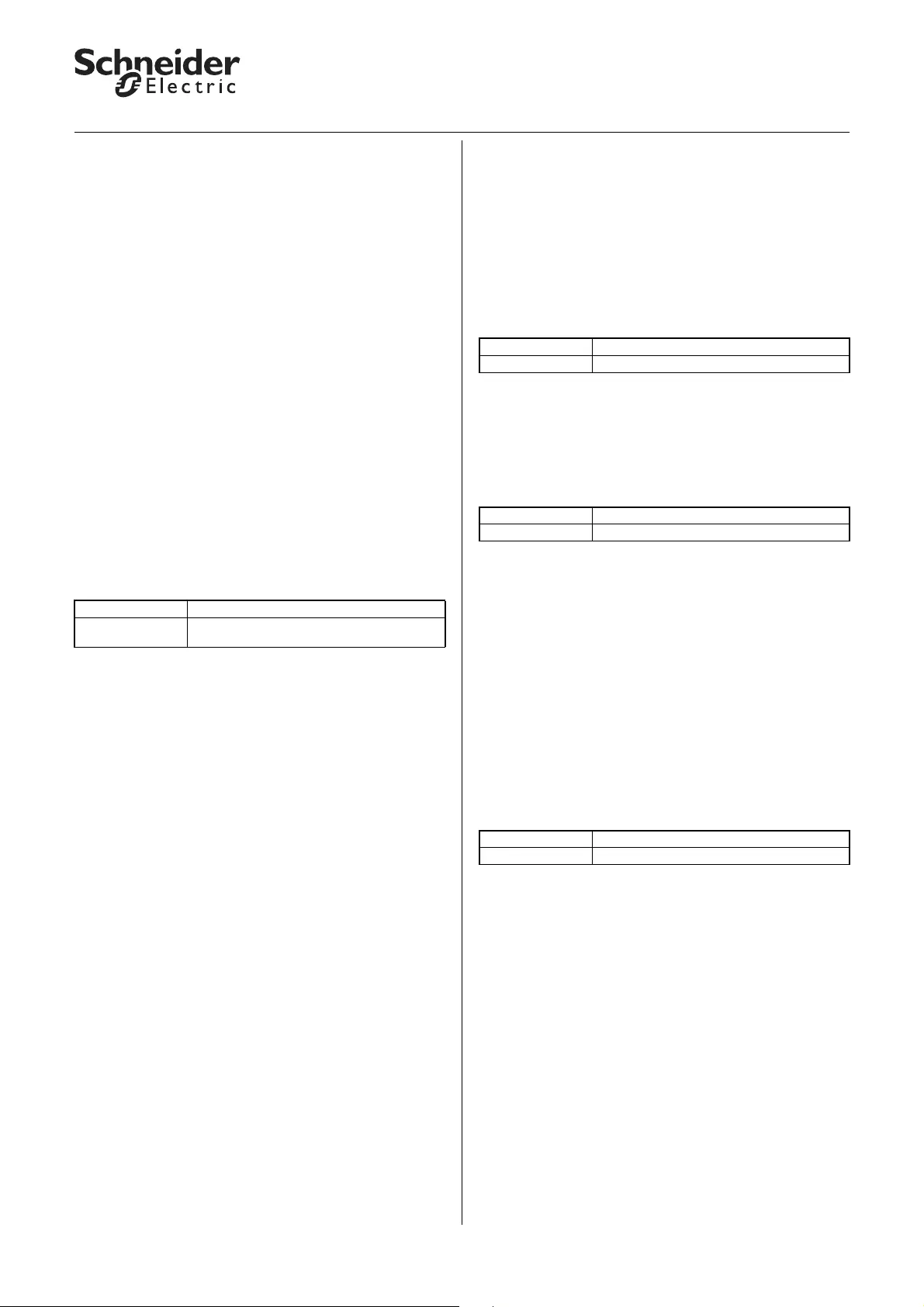
31
KNX Blind actuator REG-K/x/10 with manual mode
Art. no. MTN649802, MTN649804, MTN649808
© 2012 Schneider Electric
Application Shutter.Blind.Safety.Position.Manual 5700/1.1
Bus voltage is recovered
The RUN LED is lit, thus indicating that bus voltage is
present again. The behaviour that you specified for
bus voltage recovery is also carried out if the device
receives a restart instruction (management function)
through a bus.
Thirty seconds after bus voltage is once again stably
present, the device starts transmitting the activated
status messages of all the channels one after another.
However, only those status messages that you did not
define as passive status objects are transmitted, in
other messages defined for read out only. The object
value of the status objects valid at the time of
transmission is always sent as the status message,
even if it has changed once or several times since bus
voltage has been recovered. For more information,
refer to the section "Status messages".
Behaviour of channels for blind/roller shutters
After bus voltage has been recovered, all output relays
are opened (all drives stop) and the pause on reverse
specified by the parameters is started. Only after the
pause on reverse time has expired will the behaviour
that you set with the following parameter be carried
out:
Possible values:
–Stop
The drive stays in its current idle state.
–Up
The drive moves upwards. If it was in the middle of
an downwards movement, then it stops and waits
the pause on reverse time before beginning the
upwards movement.
–Down
The drive moves downwards. If it was in the middle
of an upwards movement, then it stops and waits
the pause on reverse time before beginning the
downwards movement.
– Move to position
The blind moves into a position defined by you. The
new parameter "Height position on bus voltage
recovery in %" appears to allow you to set this
position.
Set the desired height position in the possible travel
range of 0 –100 %.
In the case of blind drives, the additional parameter
"Slat position on bus voltage recovery in %" allows
you to define the opening angle of the slats in the
regulating range of 0 –100 %.
If there is no weather alarm present, the positin
movement begins. If there is a weather alarm present,
then the device responds in line with your settings for
this weather alarm, and the position movement is no
longer carried out.
Behaviour of higher-level functions
In addition to the behaviour of the channels, you can
also specify the behaviour of higher-level functions
following bus voltage recovery.
Alarm function
Following bus voltage recovery, the alarm function of
the channel responds in line with your settings. It
remains either inactive (deactivated) or active, or it
reverts to the status prior to bus voltage failure (see
the section "Alarm function" also).
Disable function
Following bus voltage recovery, the disable function of
the channel responds in line with you settings. It
remains either inactive (deactivated) or active, or it
reverts to the status prior to bus voltage failure (see
the section "Disable function" also).
Possibility 2: Bus voltage present, mains voltage
failure/recovery
Mains voltage has failed
The blind actuator can still carry out all functions if
supplied by bus voltage only. The power supply for
switching the relays, however, is provided primarily by
the mains voltage. If the mains voltage fails, it can still
carry out all functions, but there may be a slight time
delay (e.g. switching of the relays, slat adjustment).
Manual operation is possible.
You can transmit the status of the mains voltage to the
to bus via a communications object. You can set the
transmission behaviour of this status object with a
parameter:
Possible settings:
– disabled
The current status of the mains voltage is not
transmitted to the bus and cannot be read out
either. No communication object is available.
– active status feedback object
If it changes, the current status of the mains voltage
is transmitted to the bus via the "Mains voltage
status feedback" communication object. If mains
voltage is present, the object value is "1", if there is
no mains voltage "0".
– passive status object
You can export the current status of the mains
voltage using the "Main voltage status"
communication object. The object value is not sent
in the case of changes.
For more information see the section "Status
messages".
Tab Parameter
X: Failure
behaviour Behaviour on bus voltage recovery
Tab Parameter
X: Alarm function Alarm status on bus voltage recovery
Tab Parameter
X: Disable function Lock status on bus voltage recovery
Tab Parameter
General Mains voltage status
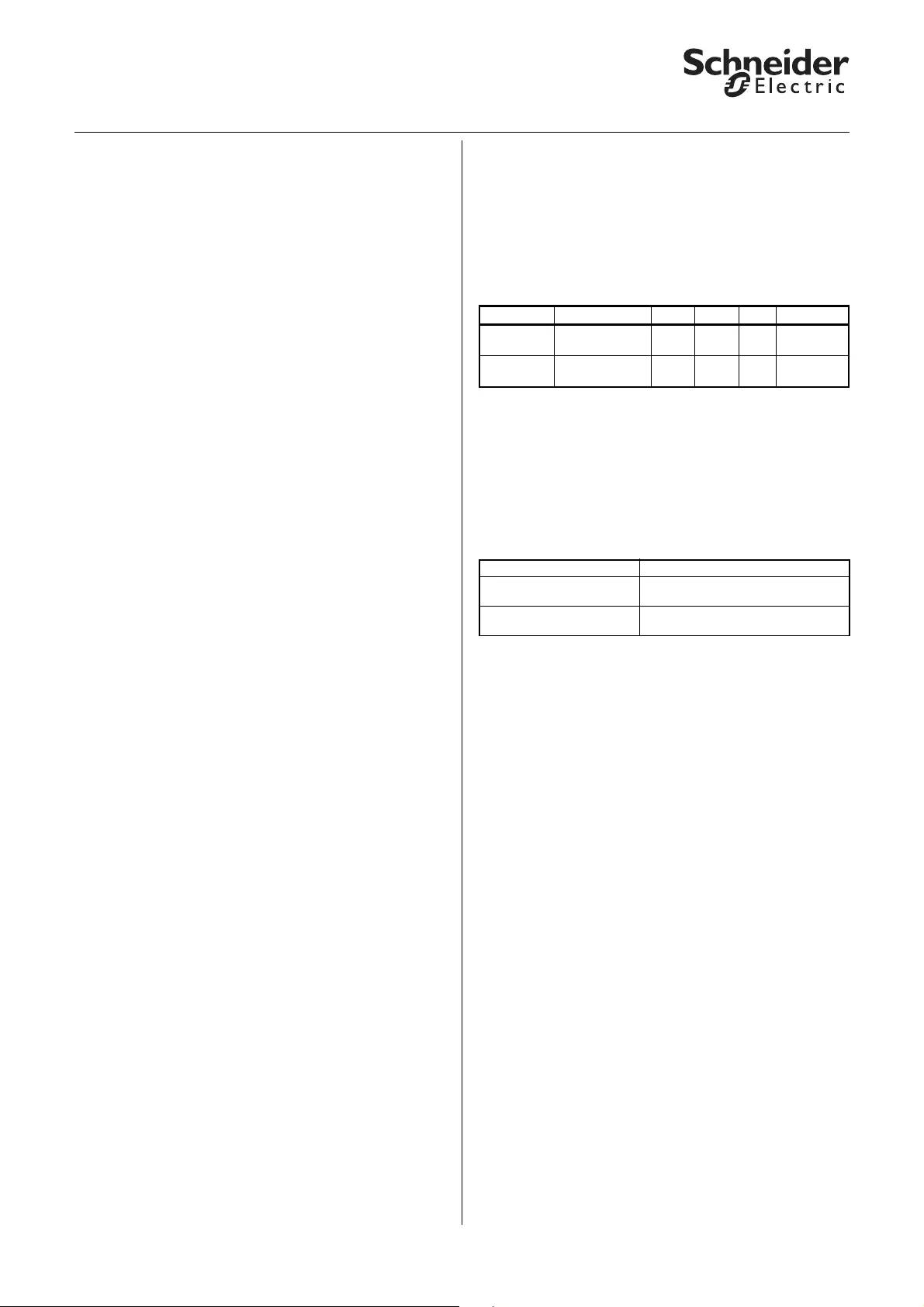
32
KNX Blind actuator REG-K/x/10 with manual mode
Art. no. MTN649802, MTN649804, MTN649808
© 2012 Schneider Electric
Application Shutter.Blind.Safety.Position.Manual 5700/1.1
Mains voltage is recovered
When the mains voltage is present again, then the
device is once again in normal operation and the
switching processes can be carried out as normal. You
can transmit the status of the mains voltage to the bus
or make it available for readout. In this case the status
object has the value "1".
Possibility 3: Bus and mains voltage failure/
recovery
Bus and mains voltage fail
If the power supply for switching the relays fails in
addition to the bus functions, the blind actuator cannot
carry out any more switching actions. Status displays,
the manual LED and the RUN LED all go out. Manual
operation using the channel keys is no longer possible.
Behaviour of channels for blind/roller shutters
The relays remain permanently in their current
switching position. The switching status of the relays
can only be changed when bus voltage is recovered.
Behaviour when bus voltage fails after mains
voltage failure
If the bus voltage fails after the main voltage has
previously failed, then the relays remain in their
current switching position permanently. The switching
status of the relays can only be changed when bus
voltage is recovered.
Behaviour when mains voltage fails after bus
voltage failure
If the mains voltage fails after the bus voltage has
previously failed, there is no additonal response. The
relays remain in their current switching position. The
status displays, the manual LED and the RUN LED all
go out.
Bus and mains voltage are recovered
The RUN LED is lit, thus indicating that bus voltage is
present again. The status LEDs of the channels
indicate the current output statuses. The manual LED
is switched off, thus indicating that manual operation
is deactivated.
The output channels behave in line with your settings
following the failure of bus voltage only (see option 1).
The relays are not switched until there is enough
power to do so safely.
Status messages
The device can transmit status messages again. For
more information see "Behaviour after bus voltage
recovery" (option 1).
Behaviour of higher-level functions
The settings and behaviour of higher-level functions
correspond to those described under bus voltage
recovery (option 1).
Behaviour on recovery of bus voltage without
mains voltage
In this case, the device behaves as described under
"Bus and mains voltage are recovered". It transmits the
status of the mains voltage with the value "0".
Behaviour on recovery of mains voltage without
bus voltage
If mains voltage is recovered without bus voltage, the
device behaves as described under bus voltage failure
with mains voltage present (option 1).
Communication objects
The following communication objects are available:
●Behaviour after application download
Before the first download after commissioning, all
relays are switched off (default setting). Manual
operation is deactivated; the manual LED is switched
off.
You can specify the download behaviour of the output
channels:
Possible settings:
– no response
After a download, the relays remain in their current
status.
– as for bus voltage recovery
The relays behave in line with your settings for a
return of bus voltage for this channel.
If an internal error or a defective download results in a
status in which the application is no longer operational,
the device does not respond. The drives remain in
their last position. All relays are switched off.
Function Object name Type Prio Flags Behaviour
Status Mains voltage
status 1 bit Low CR Send
Status Mains voltage
status feedback 1 bit Low CR Transmit/
Read out
Tab Parameter
X: Blind
X: Roller shutter Failure behaviour
X: Failure behaviour(if
failure behaviour enabled) Relay status after download
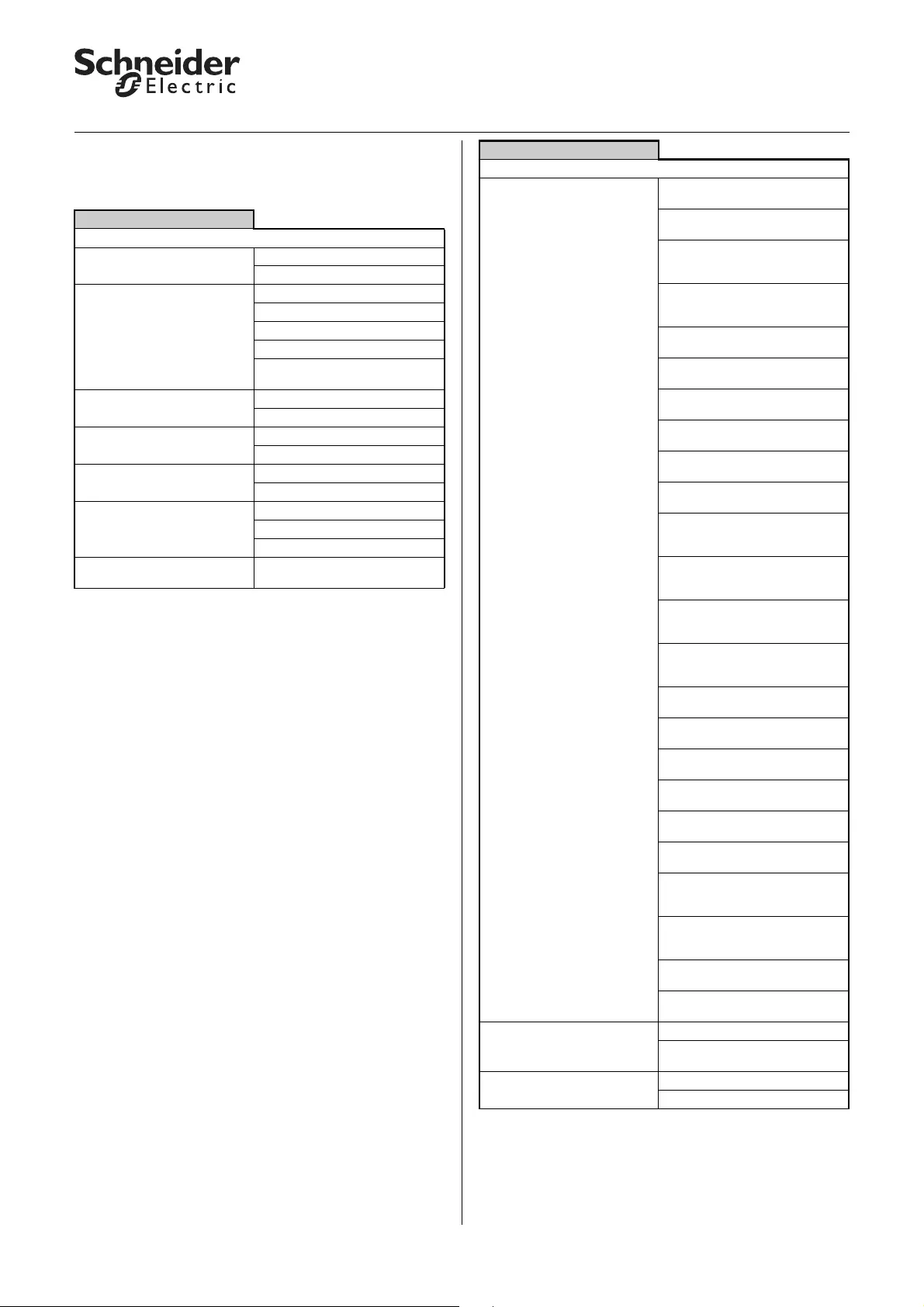
33
KNX Blind actuator REG-K/x/10 with manual mode
Art. no. MTN649802, MTN649804, MTN649808
© 2012 Schneider Electric
Application Shutter.Blind.Safety.Position.Manual 5700/1.1
●Parameters and settings
This section lists all the parameters of the ETS
application with their settings and default settings.
General
Parameter Setting
Manual operation type Bus and manual operation
Manual operation only
Manual operation activation disabled
enabled
enabled with status message
Enable via object
Enable via object with status
message
Time-dependent reset of
manual operation disabled
enabled
Scenes general disabled
enabled
Extension scenes disabled
enabled
Mains voltage status disabled
active status feedback object
passive status object
Minimum interval between
status messages 100 ms, 200 ms, 500 ms, 1 sec,
1.5 sec, 2 sec
Priority sequence of higher-level
functions 1. alarm, 2. weather alarm,
3. lock. 4. movement range
1. alarm, 2. weather alarm,
3. movement range, 4. lock
1. alarm, 2. lock,
3. weather alarm. 4. movement
range
1. alarm, 2. lock,
3. movement range, 4. weather
alarm
1. alarm, 2. movement range,
3. weather alarm, 4. lock
1. alarm, 2. movement range,
3. lock, 4. weather alarm
1. weather alarm, 2. alarm
3. lock. 4. movement range
1. weather alarm, 2. alarm,
3. movement range, 4. lock
1. weather alarm, 2. lock,
3. alarm. 4. movement range
1. weather alarm, lock,
3. movement range, 4. alarm
1. weather alarm, 2. movement
range,
3. alarm. 4. lock
1. weather alarm, 3. movement
range,
3. lock. 4. alarm
1. lock, 2. alarm,
3. weather alarm. 4. movement
range
1. lock, 2. alarm,
3. movement range, 4. weather
alarm
1. lock, 2. weather alarm,
3. alarm. 4. movement range
1. lock, 2. weather alarm,
3. movement range, 4. alarm
1. lock, 2. movement range,
3. weather alarm. 4. alarm
1. lock, 2. movement range,
3. alarm, 4. weather alarm
1. movement range, 2. alarm
3. weather alarm, 4. lock
1. movement range, 2. alarm
3. lock, 4. weather alarm
1. movement range, 2. weather
alarm,
3. alarm. 4. lock
1. movement range, 2. weather
alarm,
3. lock. 4. alarm
1. movement range, 2. lock,
3. weather alarm. 4. alarm
1. movement range, 2. lock,
3. alarm, 4. weather alarm
General weather alarm function disabled
enabled
(=> "General weather alarm" tab)
General reference movement disabled
enabled
General
Parameter Setting
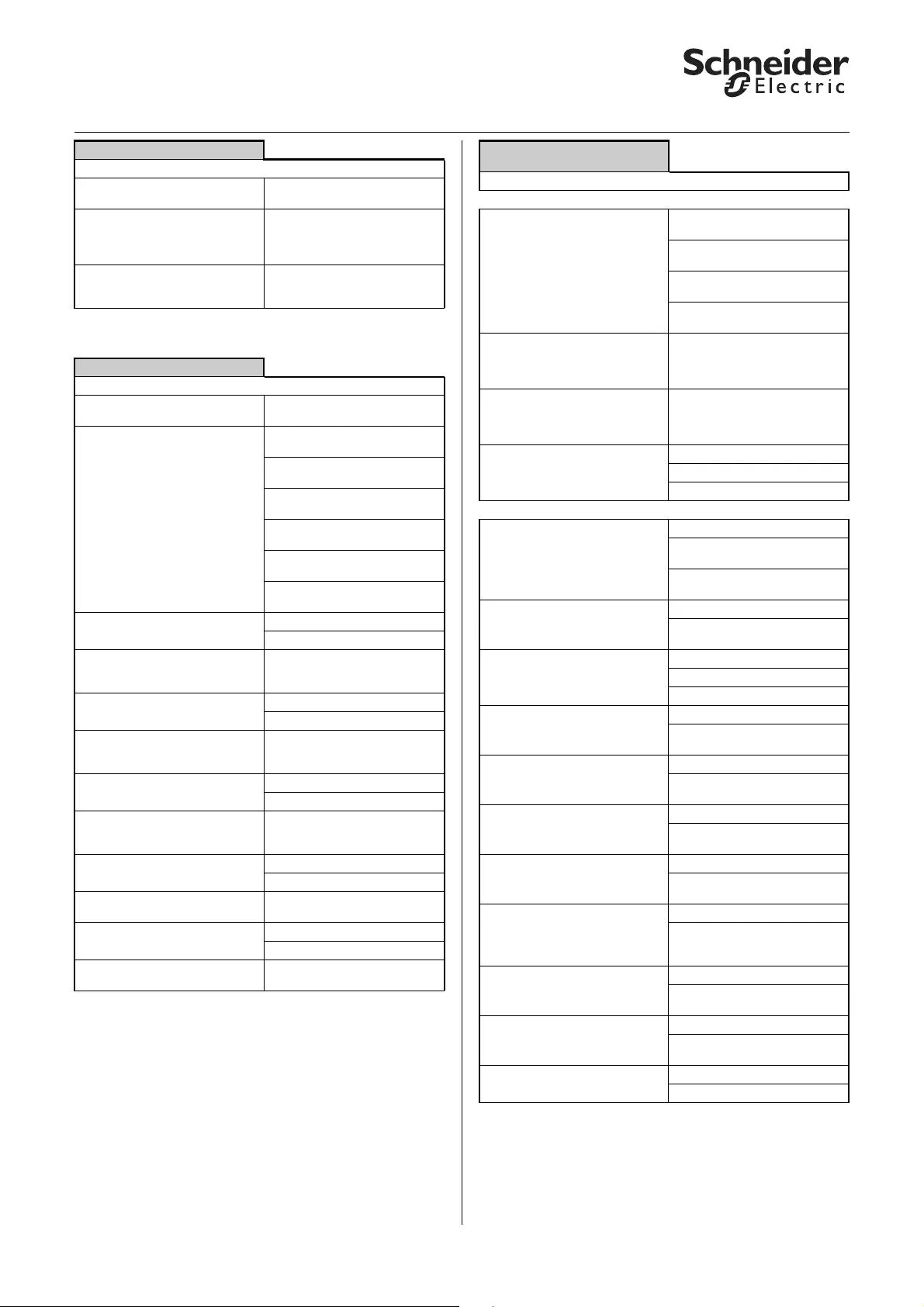
34
KNX Blind actuator REG-K/x/10 with manual mode
Art. no. MTN649802, MTN649804, MTN649808
© 2012 Schneider Electric
Application Shutter.Blind.Safety.Position.Manual 5700/1.1
If weather alarm is enabled in the "General" tab:
Channel_config._X
Parameter Setting
Channel X operating mode disabled (default setting for all
channels except 1)
Blind (default setting for channel
1)
(=> "X:_Blind" tab
=> "X:_Drive" tab)
Roller shutter
(=> "X:_Roller shutter" tab
=> "X_Drive" tab)
General weather alarm
Parameter Setting
Time basis for monitoring time of
weather alarms 1 sec, 1 min, 1 hr
Priority sequence of weather
alarms 1. wind alarm, 2. rain alarm, 3.
frost alarm
1. wind alarm, 2. frost alarm,
3. rain alarm
1. rain alarm, 2. wind alarm,
3. frost alarm
1. rain alarm, 2. frost alarm,
3. wind alarm
1. frost alarm, 2. wind alarm,
3. rain alarm
1. frost alarm, 2. rain alarm,
3. wind alarm
Wind alarm no. 1 disabled
enabled
Factor for wind alarm no. 1
monitoring time(if wind alarm no.
1 enabled)
disabled, 1 to 255
Wind alarm no. 2 disabled
enabled
Factor for wind alarm no. 2
monitoring time(if wind alarm no.
2 enabled)
disabled, 1 to 255
Wind alarm no. 3 disabled
enabled
Factor for wind alarm no. 3
monitoring time(if wind alarm no.
3 enabled)
disabled, 1 to 255
Rain alarm disabled
enabled
Factor for rain alarm monitoring
time (if rain alarm enabled) disabled, 1 to 255
Frost alarm disabled
enabled
Factor for frost alarm monitoring
time (if rain alarm enabled) disabled, 1 to 255
X_Blind
X_Roller shutter
Parameter Setting
Only for operation type "blind"
How does the existing blind
move? downwards closed / upwards
level (= blind type 1)
downwards tilted / upwards
level (= blind type 2)
downwards closed / upwards
closed (= blind type 3)
downwards tilted / upwards
closed (= blind type 4)
Slat working position in %
(for blind type 1 and 3 - if working
position)
0–100
Default settings:
Blind type 1: 50%
Blind type 3: 75%
What is the current slat position
on downward movement in %?
(for blind type 2 and 4)
0–100
Default settings:
Blind type 2: 50%
Blind type 4: 75%
Slat position after movement no response
Working position
last slat position
"Blind" operation type / "Roller shutter" operation type
Automatic control/Presets disabled
Automatic control
(=> "X_Automatic" tab)
Presets
(=> "X_Presets" tab)
Scenes disabled
enabled
(=> "X_Scenes" tab)
Manual lock inactive
For object value "0"
For object value "1"
Calibration disabled
enabled
(=> "X_Calibration" tab)
Weather alarm disabled
enabled
(=> "X_Weather alarm")
Alarm function disabled
enabled
(=> "X_Alarm function" tab)
Disable function disabled
enabled
(=> "X_Disable function" tab)
Movement range limits disabled
enabled
(=> "X_Movement range limits"
tab)
Failure behaviour disabled
enabled
(=> "X_Failure behaviour" tab)
Status messages disabled
enabled
(=> "X_Status messages" tab)
Manual operation on bus voltage
failure (mains voltage present) disabled
enabled
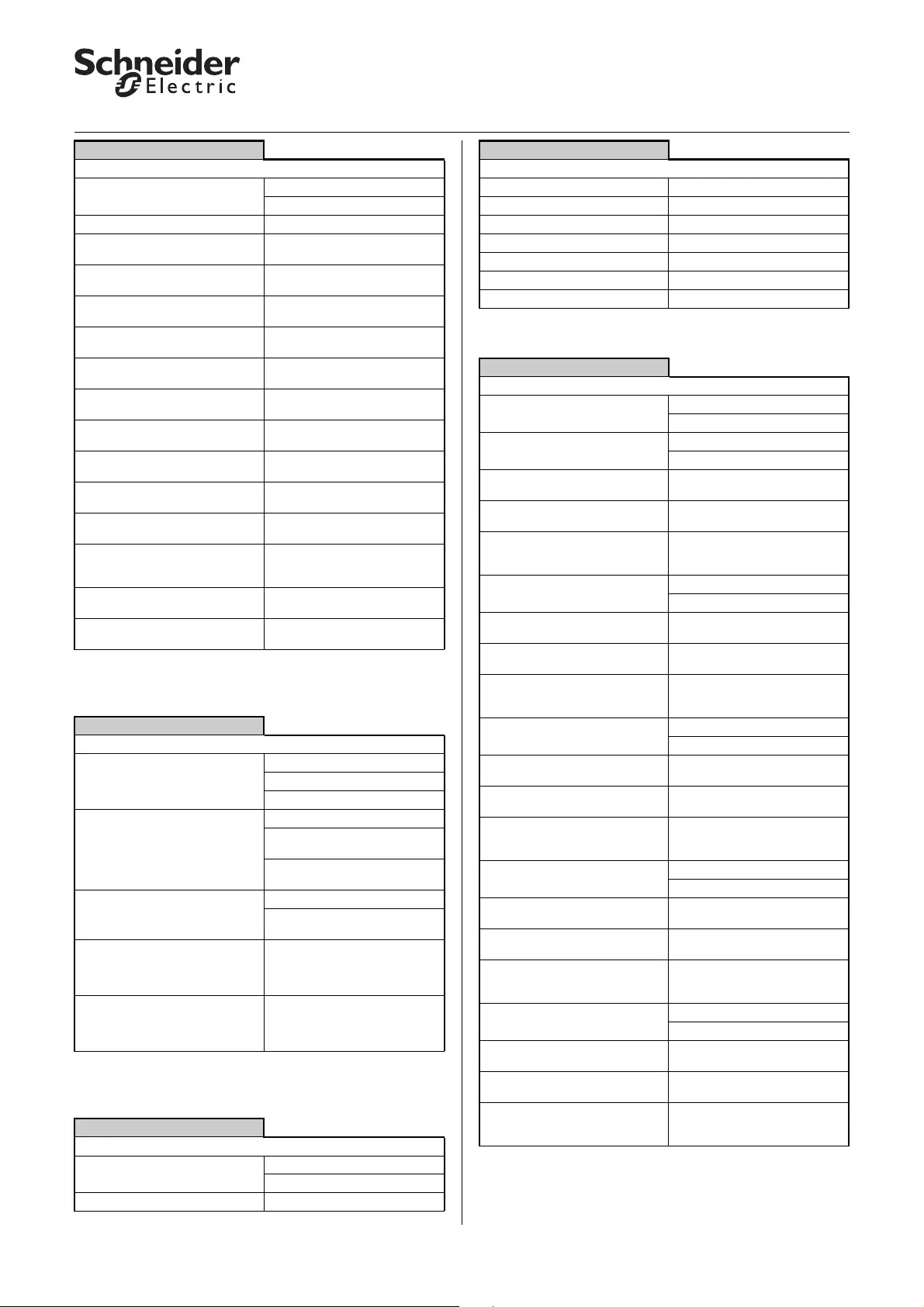
35
KNX Blind actuator REG-K/x/10 with manual mode
Art. no. MTN649802, MTN649804, MTN649808
© 2012 Schneider Electric
Application Shutter.Blind.Safety.Position.Manual 5700/1.1
If "Automatic control/Presets" in the "X_Blind" tab set
to "Automatic control":
If "Automatic control/Presets" in the "X_Blind" tab set
to "Presets":
If "Scenes" in the "X_Blind" tab is "enabled":
X:_Drive
Parameter Setting
Advanced drive parameter enabled
disabled
Time basis for height running time 10 ms, 100 ms
Factor for height running time (10-
64000) 1 second = 1000 ms 10–64000, 1200 default setting
Shared time basis for running
time supplements/dead time 10 ms, 100 ms
Factor for running time upwards
supplement disabled, 1–255, 20 default
setting
Factor for dead time until
upwards movement disabled, 1–255
Factor for slat open up start-up
supplement ("Blind" only) disabled, 1–255
Factor for slat open down start-up
supplement ("Blind" only) disabled, 1–255
Time basis for slat step
time("Blind" only) 10 ms, 100 ms
Factor for slat step time (5-255)
("Blind" only) 5–255, 10 default setting
Time basis for slat running
time("Blind" only) 10 ms, 100 ms
Factor for slat running time (5-
255) ("Blind" only) 5–255, 100 default setting
Pause on change for change of
direction (1-255), factor * 100 ms,
manufacturer data!
1–255, 5 default setting
Factor for start-up delay
Factor * 10 ms disabled, 1–255
Factor for run-out delay
Factor * 10 ms disabled, 1–255
X:_Automatic
Parameter Setting
Automatic lock inactive
For object value "0"
For object value "1"
Response in automatic operation
on receipt of a manual object
value
Automatic control disabled
Automatic control remains
enabled
Automatic control disabled
temporarily
Behaviour on deactivation of
automatic lock via object value
(only if automatic lock enabled)
no response
Assume current automatic
position
Time basis for automatic control
deactivation time (only if
automatic control disabled
temporarily)
1 sec, 1 min, 1 hr
Factor for automatic control
deactivation time (only if
automatic control disabled
temporarily)
1–255, 1 default setting
X: Presets
Parameter Setting
Replace preset values in the
actuator on download disabled
enabled
Preset 1: Height pos. in % 0–100, 0 default setting
Preset 1: Slat pos. in % 0–100, 0 default setting
Preset 2: Height pos. in % 0–100, 0 default setting
Preset 2: Slat pos. in % 0–100, 0 default setting
Preset 3: Height pos. in % 0–100, 0 default setting
Preset 3: Slat pos. in % 0–100, 0 default setting
Preset 4: Height pos. in % 0–100, 0 default setting
Preset 4: Slat pos. in % 0–100, 0 default setting
X: Scenes
Parameter Setting
Replace scene values in the
actuator on download? disabled
enabled
Scene 1 disabled
enabled
Scene 1: Scene number (0-63)
(only if scene 1 enabled) 0-63, 0 default setting
Scene 1: Pos. height (1-64) (only if
scene 1 enabled) 0–100, 0 default setting
Scene 1: Pos. height in % (blind
operation only and only if scene 1
enabled)
0–100, 0 default setting
Scene 2 disabled
enabled
Scene 2: Scene number (0-63)
(only if scene 2 enabled) 0-63, 1 default setting
Scene 2: Pos. height (2-64) (only if
scene 1 enabled) 0–100, 0 default setting
Scene 2: Pos. height in % (blind
operation only and only if scene 2
enabled)
0–100, 0 default setting
Scene 3 disabled
enabled
Scene 3: Scene number (0-63)
(only if scene 3 enabled) 0-63, 2 default setting
Scene 3: Pos. height (3-64) (only if
scene 1 enabled) 0–100, 0 default setting
Scene 3: Pos. height in % (blind
operation only and only if scene 3
enabled)
0–100, 0 default setting
Scene 4 disabled
enabled
Scene 4: Scene number (0-63)
(only if scene 4 enabled) 0-63, 3 default setting
Scene 4: Pos. height (4-64) (only if
scene 1 enabled) 0–100, 0 default setting
Scene 1: Pos. height in % (blind
operation only and only if scene 4
enabled)
0–100, 0 default setting
Scene 5 disabled
enabled
Scene 5: Scene number (0-63)
(only if scene 5 enabled) 0–63, 4 default setting
Scene 5: Pos. height (5-64) (only if
scene 1 enabled) 0–100, 0 default setting
Scene 5: Pos. height in % (blind
operation only and only if scene 5
enabled)
0–100, 0 default setting
X: Presets
Parameter Setting
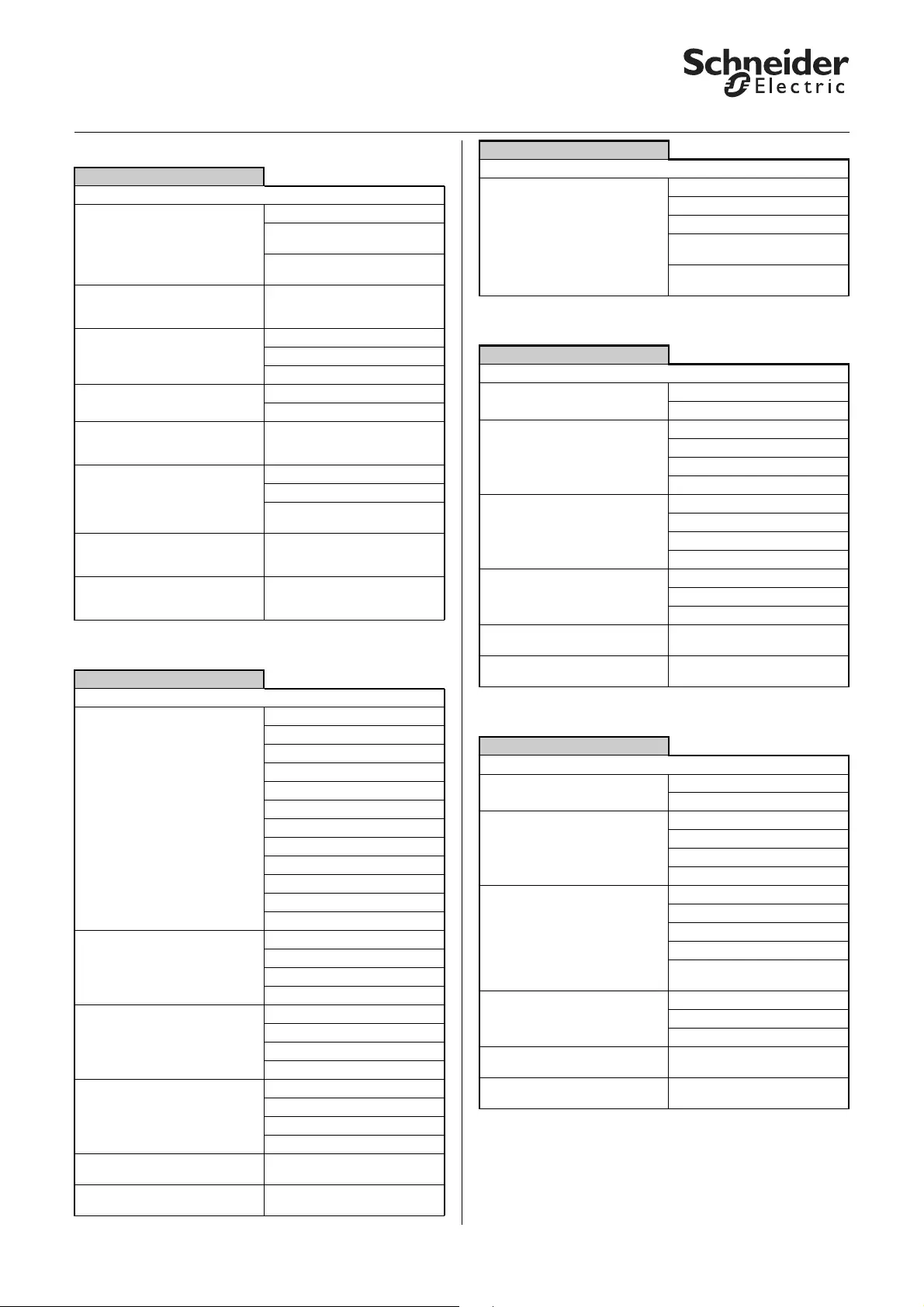
36
KNX Blind actuator REG-K/x/10 with manual mode
Art. no. MTN649802, MTN649804, MTN649808
© 2012 Schneider Electric
Application Shutter.Blind.Safety.Position.Manual 5700/1.1
If "Calibration" in the "X_Blind" tab is "enabled":
If "Weather alarm" in the "X_Blind" tab is "enabled":
If "Alarm function" in the "X_Blind" tab is "enabled":
If "Disable function" in the "X_Blind" tab is "enabled":
X: Calibration
Parameter Setting
Reference movement after No. of movements
Value "1" to object trigger
reference movement
No. of movements and trigger
reference movement
Number of movements until a
reference movement is executed
(1-20)
1–20, 7 default setting
Reference position up
down
up and down
Automatic calibration top end position
top and lower end position
Reference movement delay time
via object in seconds (only for
"Reference movement object")
disabled, 1–255
Position after reference
movement via object (only for
"Reference movement object")
New position
Stay in reference position
Same position as before
reference movement
Height position after reference
movement in % (only for "new
position")
0–100, 0 default setting
Slat position after reference
movement in % (only for "new
position")
0–100, 0 default setting
X: Weather alarm
Parameter Setting
Responds to wind alarm no. no response
1
2
3
1 OR 2
1 OR 3
2 OR 3
1 OR 2 OR 3
1 AND 2
1 AND 3
2 AND 3
1 AND 2 AND 3
Response to wind alarm(s)
(no response=alarm funktion
inactive)
no response
Up
Down
Move to position
Response to rain alarm
(no response=alarm funktion
inactive
no response
Up
Down
Move to position
Response to frost alarm
(no response=alarm funktion
inactive
no response
Up
Down
Move to position
Height position on weather alarm
in % 0–100, 0 default setting
Slat position on weather alarm in
%0–100, 0 default setting
Behaviour on end of all weather
alarm functions no response
Up
Down
Move into position prior to
weather alarm
Assume current automatic
position
X: Alarm function
Parameter Setting
Alarm For object value "0"
For object value "1"
Behaviour on alarm start no response
Up
Down
Move to position
Behaviour on alarm end no response
Up
Down
Move to position
Alarm status on bus voltage
recovery inactive
active
as before bus voltage failure
Height position on alarm start in
% (only for "Move to position") 0–100, 0 default setting
Slat position on alarm start in %
(only for "Move to position") 0–100, 0 default setting
X: Disable function
Parameter Setting
Lock For object value "0"
For object value "1"
Behaviour on lock start no response
Up
Down
Move to position
Behaviour on lock end no response
Up
Down
Move into position prior to lock
Assume current automatic
position
Lock status on bus voltage
recovery inactive
active
as before bus voltage failure
Height position on lock start in %
(only for "Move to position") 0–100, 0 default setting
Slat position on lock start in %
(only for "Move to position") 0–100, 100 default setting
X: Weather alarm
Parameter Setting
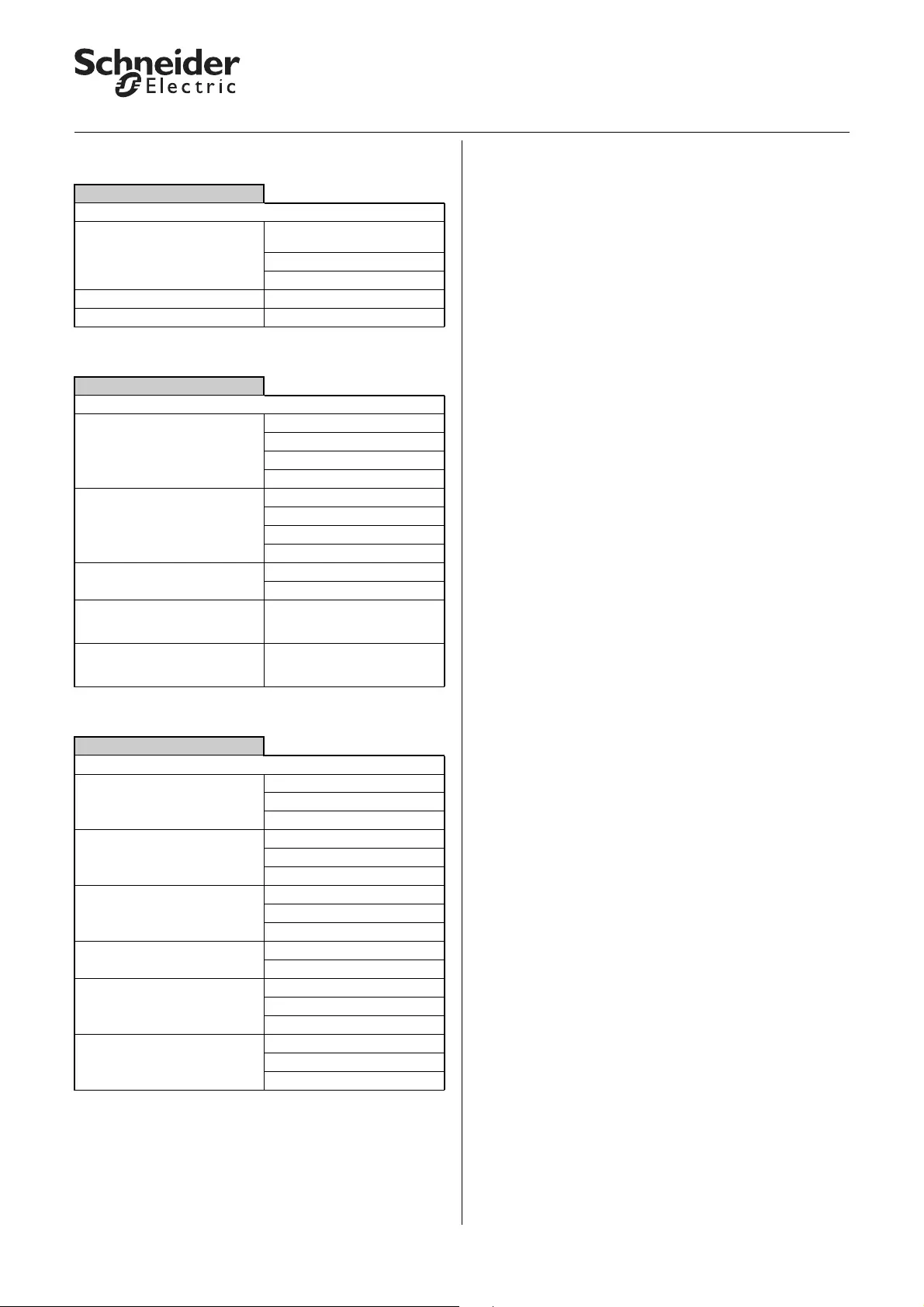
37
KNX Blind actuator REG-K/x/10 with manual mode
Art. no. MTN649802, MTN649804, MTN649808
© 2012 Schneider Electric
Application Shutter.Blind.Safety.Position.Manual 5700/1.1
If "Movement range limits" in the "X_Blind" tab is
"enabled":
If "Failure behaviour" in the "X_Blind" tab is "enabled":
If "Status messages" in the "X_Blind" tab is "enabled":
X: Movement range limits
Parameter Setting
Limit movement range Immediately after bus voltage
recovery
For object value "0"
For object value "1"
upper limit value in % 0–100, 0 default setting
lower limit value in % 0–100, 0 default setting
X: Failure behaviour
Parameter Setting
Behaviour on bus voltage failure
(fixed pause on reverse = 300 ms) no response
Stop
Up
Down
Behaviour on bus voltage
recovery Stop
Up
Down
Move to position
Relay status after download Stop
as for bus voltage recovery
Height position on bus voltage
recovery in % (only for "Move to
position")
0–100, 0 default setting
Slat position on bus voltage
recovery in % (only for "Move to
position")
0–100, 0 default setting
X: Status messages
Parameter Setting
Height status disabled
active status feedback object
passive status object
Slat status disabled
active status feedback object
passive status object
Automatic status disabled
active status feedback object
passive status object
Disable message type Drive lock
Movement range limit
Drive lock status (if disable
message type = drive lock) disabled
active status feedback object
passive status object
Movement range limit status (if
disable message type =
movement range limit)
disabled
active status feedback object
passive status object