Table of Contents
- 1 For your safety
- 2 General information about the Switch Blind 5800/1.0 application
- 3 General settings
- 4 Extended settings
- 4.1 Energy saving
- 4.2 Device safety
- 4.3 Device health
- 4.4 Global settings for scenes
- 4.5 Global settings for feedback
- 4.6 Sending delay after bus voltage recovery
- 4.7 Manual operation settings
- 4.8 Global settings for switching
- 4.9 Global settings for roller shutter and blind
- 4.10 PIN Code for Firmware Update
- 5 Express settings for switching
- 6 Extended settings for switching
- 7 Express settings for blind / roller shutter
- 8 Extended settings for blind / roller shutter
- 9 Express settings for roller shutter
- 10 Extended settings for roller shutter
- 11 Overview of group objects
- 12 Index
Schneider Electric MTN6705-0008 User Manual
Displayed below is the user manual for MTN6705-0008 by Schneider Electric which is a product in the Not Categorized category. This manual has pages.
Related Manuals
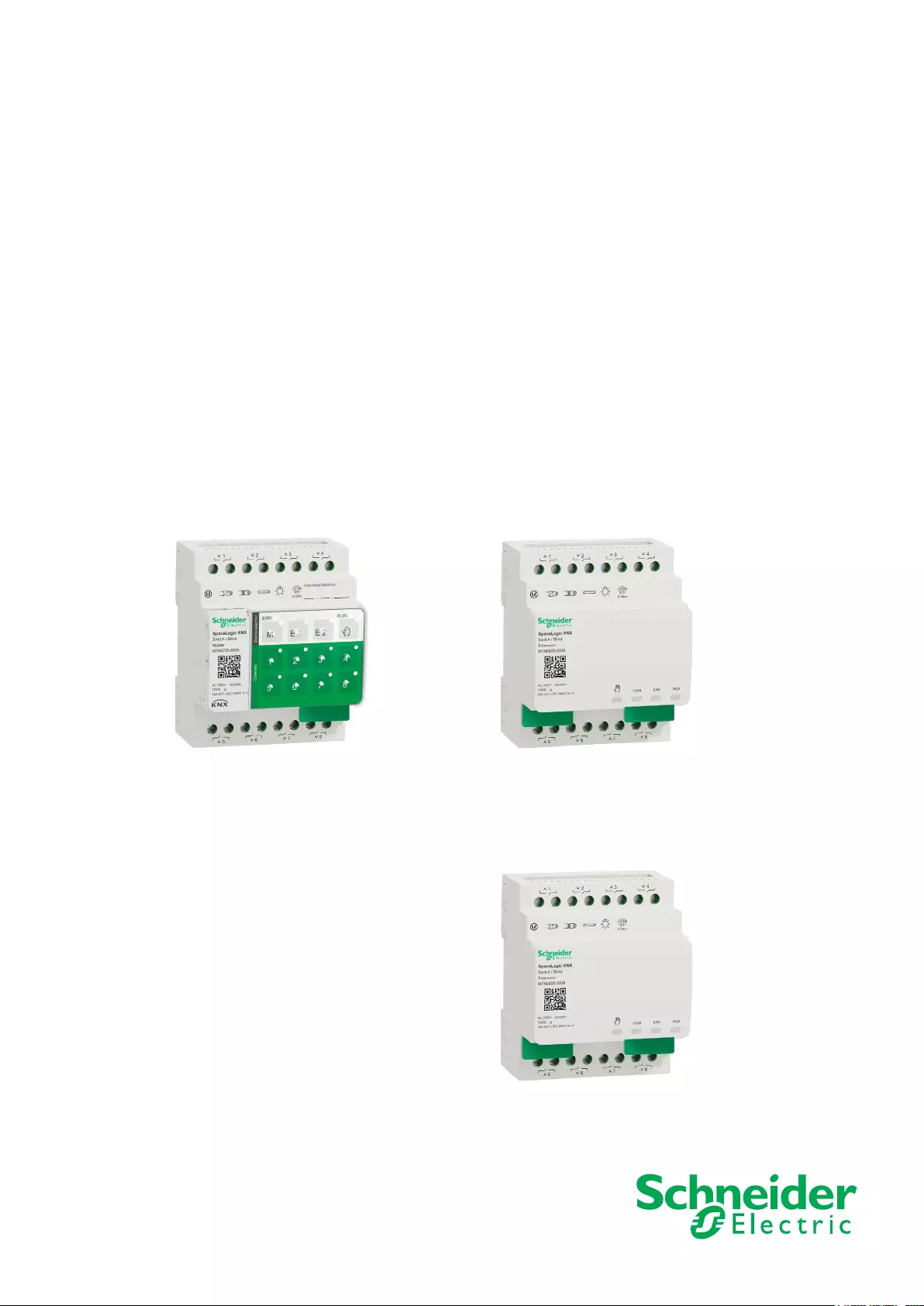
www.schneider-electric.com
SpaceLogic KNX
Switch/Blind Master
Switch Blind 5800/1.0
Application description
This document describes the software application 5800/1.0. The software application is
used to program the SpaceLogic KNX Switch/Blind Master.
MTN6705-0008 | MTN6805-0008
05/20-5800/1.0

205/20-5800/1.0MTN6705-0008 | MTN6805-0008 |
Switch Blind 5800/1.0
Legal information
The Schneider Electric brand and all registered trademarks of Schneider Electric
Industries SAS referred to in this manual are the sole property of Schneider Elec-
tric SA and its subsidiaries. They may not be used without the written approval of
the owner. This manual and its contents are protected by copyright laws for texts,
drawings and models and by the law on trademarks. You agree not to duplicate the
manual, in whole or in part, on media of any kind, without the written approval of
Schneider Electric, other than for personal, non-commercial use as dened by the
code of law. Furthermore, you agree not to create any hyperlinks to this manual or
its contents. Schneider Electric does not grant the right or permission to use the
manual or its content for personal and non-commercial use, with the sole exception
of the non-exclusive right to view the current version of the manual and its content,
at the viewer’s own risk. All other rights reserved. Electrical equipment must be
installed, operated, maintained and repaired by qualied personnel only. Schneider
Electric accepts no liability for the consequences of using this material.
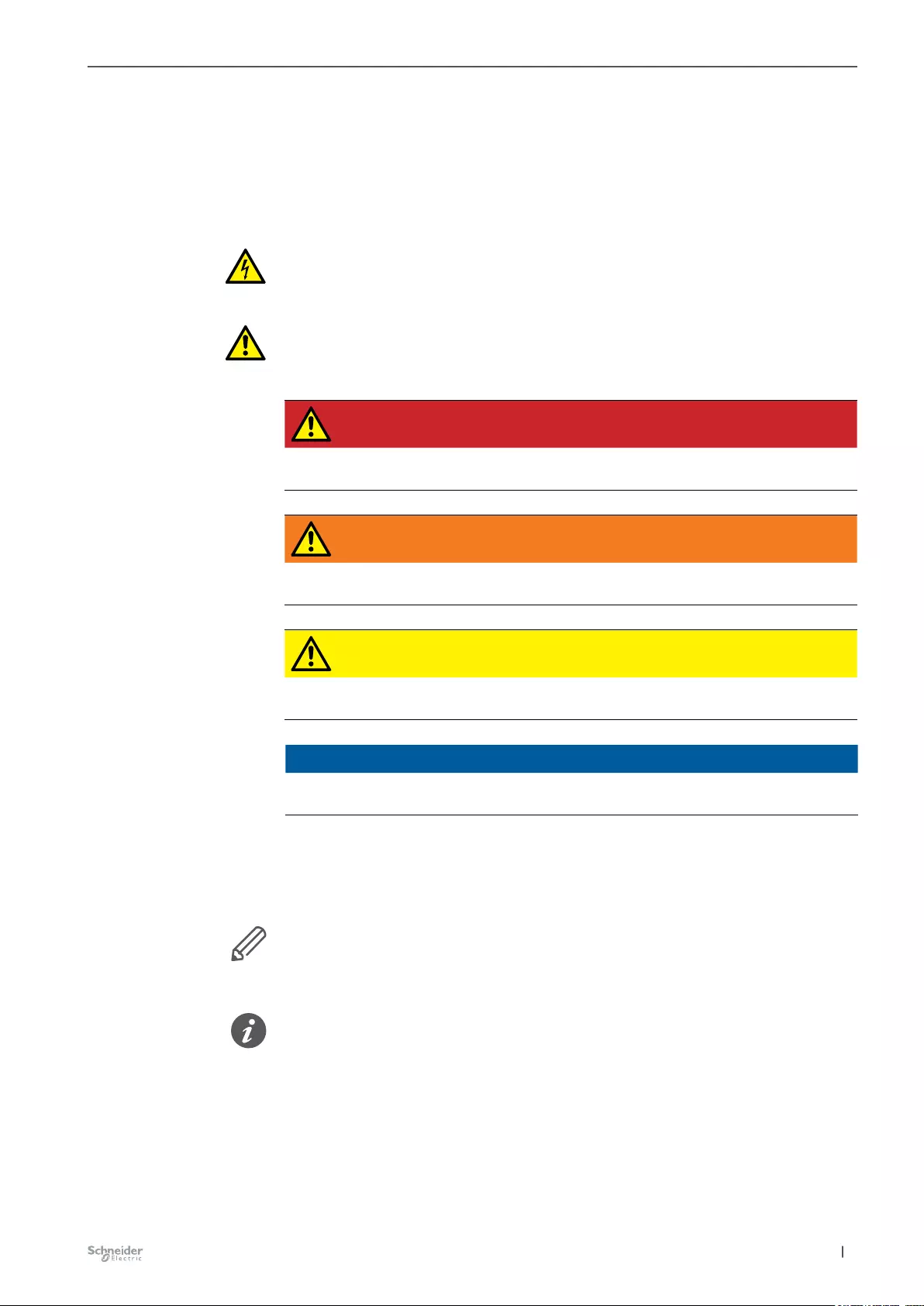
3
05/20-5800/1.0 MTN6705-0008 | MTN6805-0008 |
Switch Blind 5800/1.0
Warnings
Read through the following instructions carefully and familiarize yourself with the
device prior to installation, operation and maintenance. The warnings listed below
can be found throughout the documentation and indicate potential risks and dan-
gers, or specic information that claries or simplies a procedure.
The addition of a symbol to "Danger" or "Warning" safety instructions indicates
an electrical danger that could result in serious injuries if the instructions are not
followed.
This symbol represents a safety warning. It indicates the potential risk of personal
injury. Follow all safety instructions with this symbol to avoid serious injuries or
death.
DANGER
DANGER indicates an imminently hazardous situation that will inevitably
result in a serious or fatal accident if the instructions are not observed.
WARNING
WARNING indicates a possible danger that could result in death or seri-
ous injuries if it is not avoided.
CAUTION
CAUTION indicates a possible danger that could result in minor injuries if
it is not avoided.
NOTE
NOTE provides information about procedures that do not represent the
risk of any physical injury.
Further information
The specied information must be observed, otherwise a program or data error
may occur.
You will nd additional information here to make your work easier.
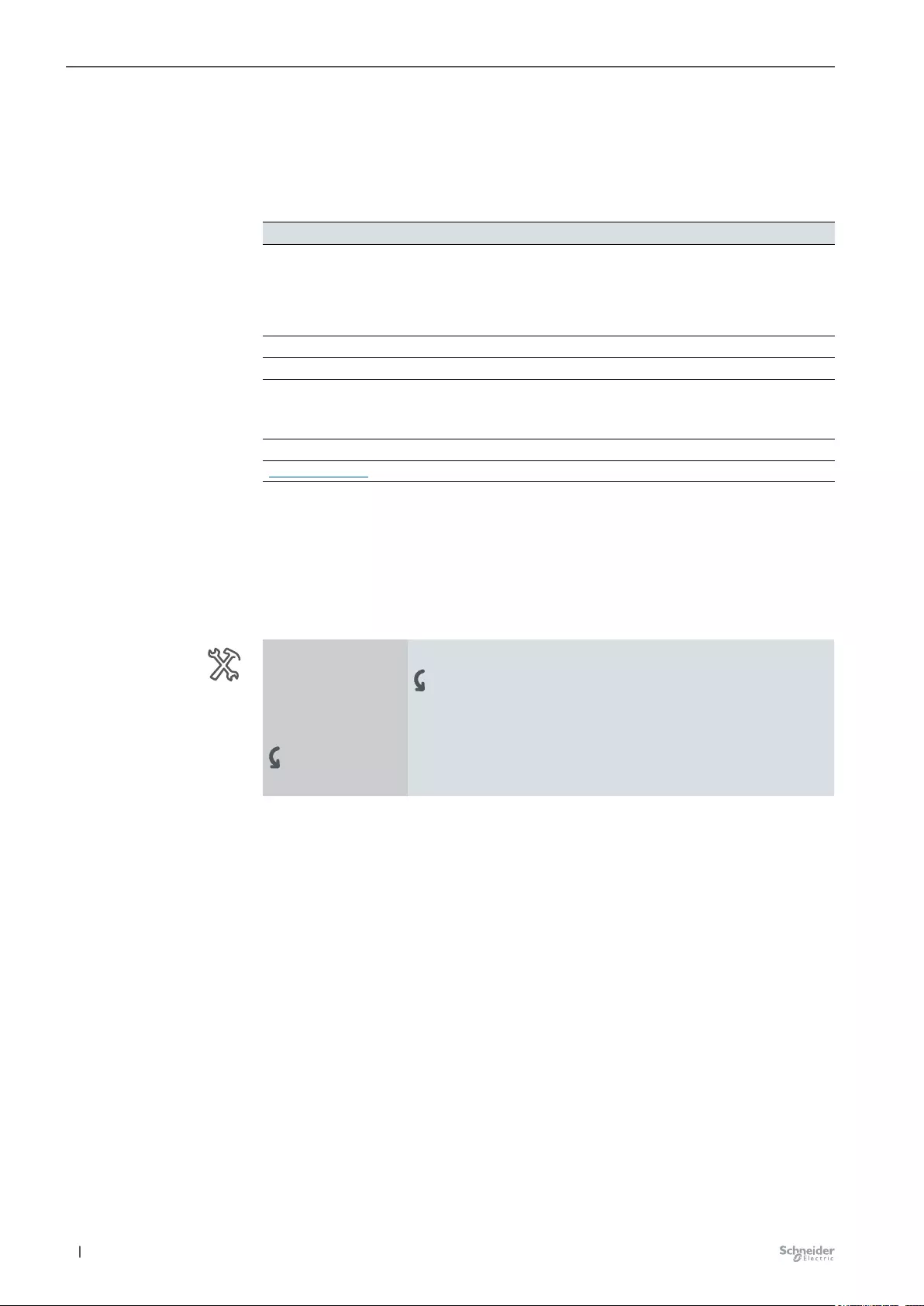
405/20-5800/1.0MTN6705-0008 | MTN6805-0008 |
Switch Blind 5800/1.0
Depictions in this document
Style and text features used
Text feature Meaning
Programming
Select the Programming button
Relay operation
– Normally opened
– Blinking
Body text contains: Service buttons, tab
name, parameter name and values.
File/Save Menu and menu sequences
Save changes? System notications
Choice:
10%/90%
...
Preset values in the ETS are highlighted in
bold in the tables.
.. works on the Switch object. Group objects
Operation chapter Cross-references
Setting tabs, parameters and values
The following overview allows you to understand the steps needed to access the
functions and settings. This overview also provides you with the correct sequence
for accessing the functions.
General settings Type of Extension 1 MTN6805-0008
Type of Extension 2 Disabled
Channel function for Extension 1
Output 1-8 Switching
Ext. 1 Output 1-8t ... ...
Meaning: Only set the parameter Type of Extension 1 to the value MTN6805-0008
on the General settings tab. Further parameters will then appear in the tab. These
can be used to change settings. New registers will also be opened.
Text features used
Overview - setting functions
Example
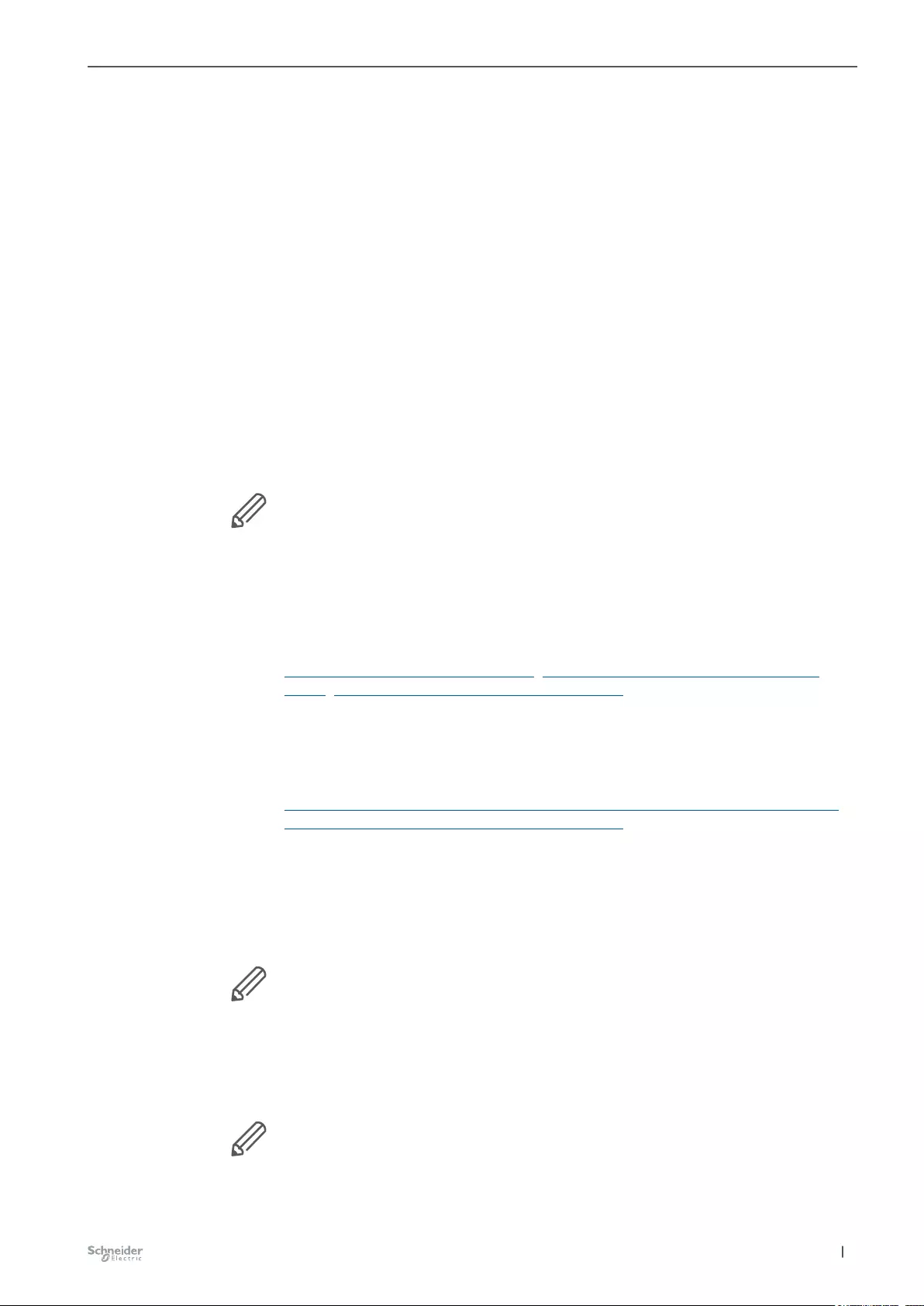
5
05/20-5800/1.0 MTN6705-0008 | MTN6805-0008 |
Switch Blind 5800/1.0
ETS operation
Requirements for safe operation
Knowledge of the basic rules for operating programs using Windows® is a prerequi-
site for operation.
The ETS is the software for the KNX system, and is not manufacturer-specic.
Knowledge of ETS operation is required. This also includes selection of the correct
sensor or actuator, transferring it to the line and commissioning it.
Special features of the ETS software
Restoring defaults
You can set the factory-specied defaults using the Default parameters service
button in the ETS5.
You can use the Default and Default parameters service buttons to switch all
parameters back to the settings on delivery (following consultation). The ETS will
then permanently delete all manual settings.
Express settings
You can use the Express settings to call up pre-set functions. Later, you simply
connect group addresses to the functions.
Express settings for switching --> 32; Express settings for blind / roller shutter
--> 67; Extended settings for roller shutter --> 117
Extended settings
With the Advanced settings, you can congure individual functions with extensive
options if required
Extended settings for switching --> 43, Extended settings for blind / roller shutter
--> 86, Extended settings for roller shutter --> 117
Dependent functions and parameters
Many functions are aected by how other functions are set. This means that de-
pendent functions can only be seen and selected in the ETS when the upstream
function is enabled.
• If you de-select functions or change parameters, previously connected group
addresses may be removed in the process.
• The values of some parameters only become active once the functions inu-
enced by these parameters are activated.
Appropriate ETS version
The application is suitable for the ETS5. You cannot use earlier versions, e.g. the
ETS3, ETS4.
Application les (knxprod) are optimised for the relevant ETS version. If you load
an ETS4 application to ETS5, time will be wasted on conversion.
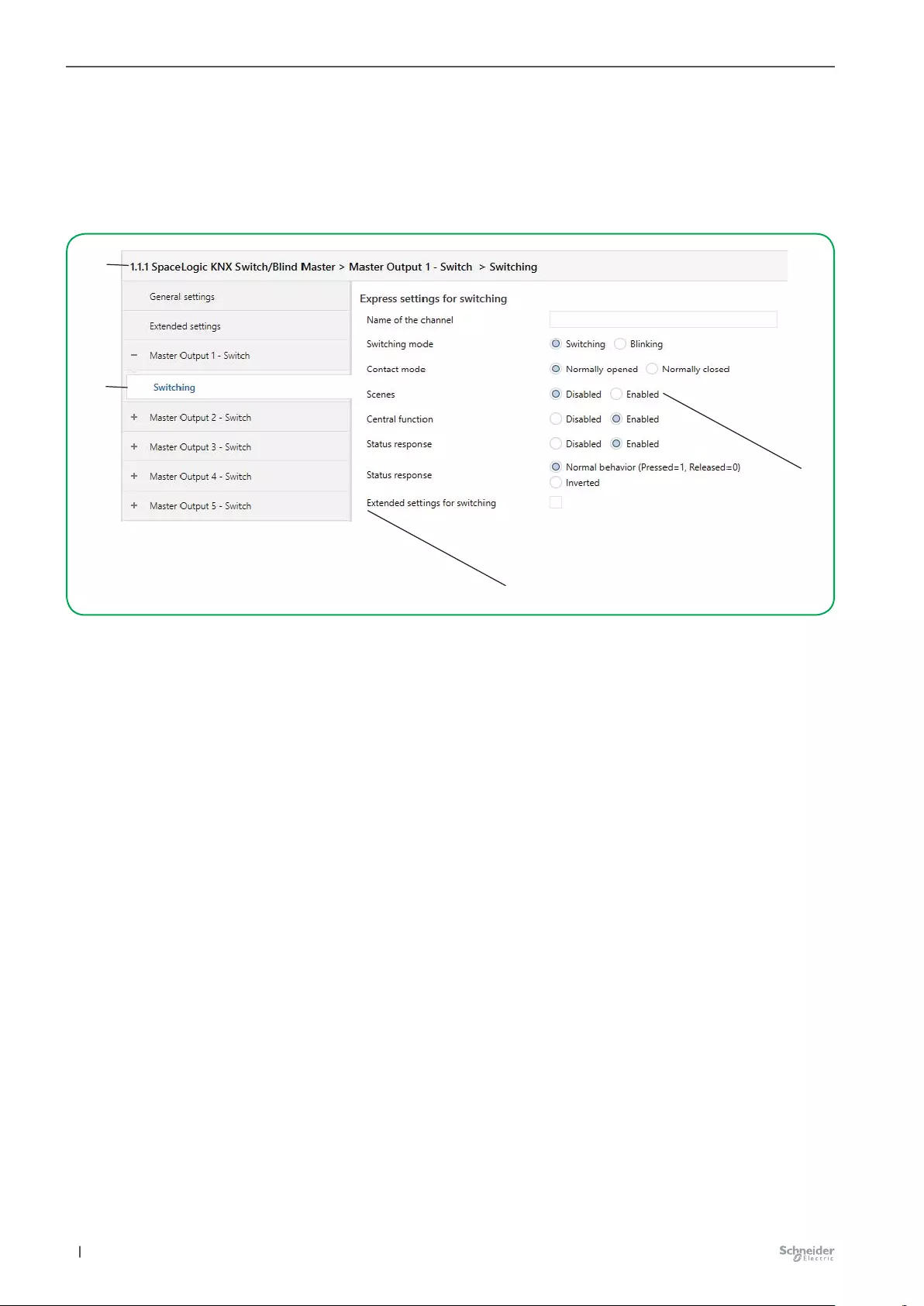
605/20-5800/1.0MTN6705-0008 | MTN6805-0008 |
Switch Blind 5800/1.0
User interface
In the ETS, the device parameters are opened using the Edit parameters service
button. The user interface is divided into 2 sections: The tabs are on the left and
the parameters on the right, together with their values.
A Name of device
B Tab
C Parameter
D Input elds for parameter values
A
B
C
D
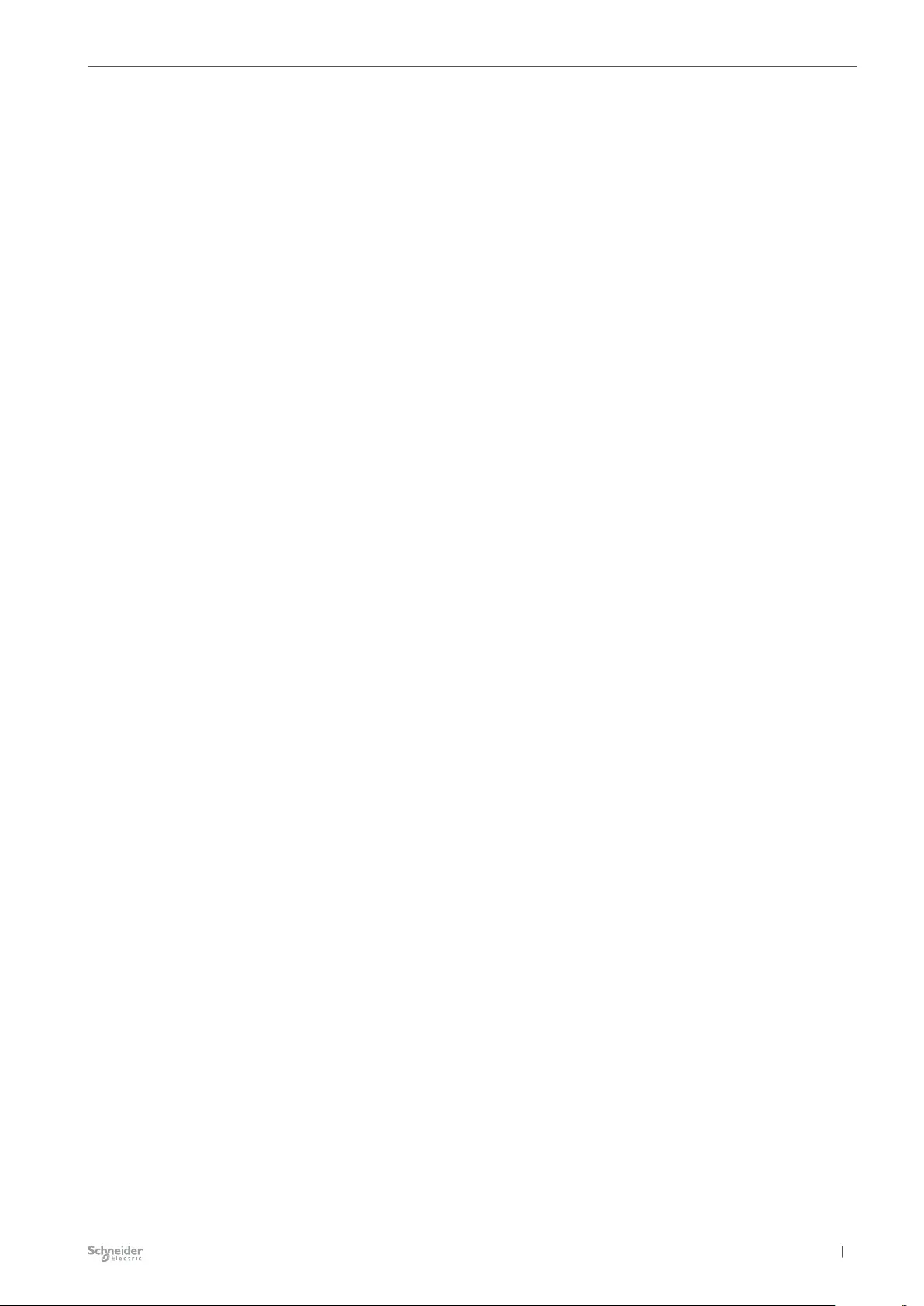
7
05/20-5800/1.0 MTN6705-0008 | MTN6805-0008 |
Switch Blind 5800/1.0
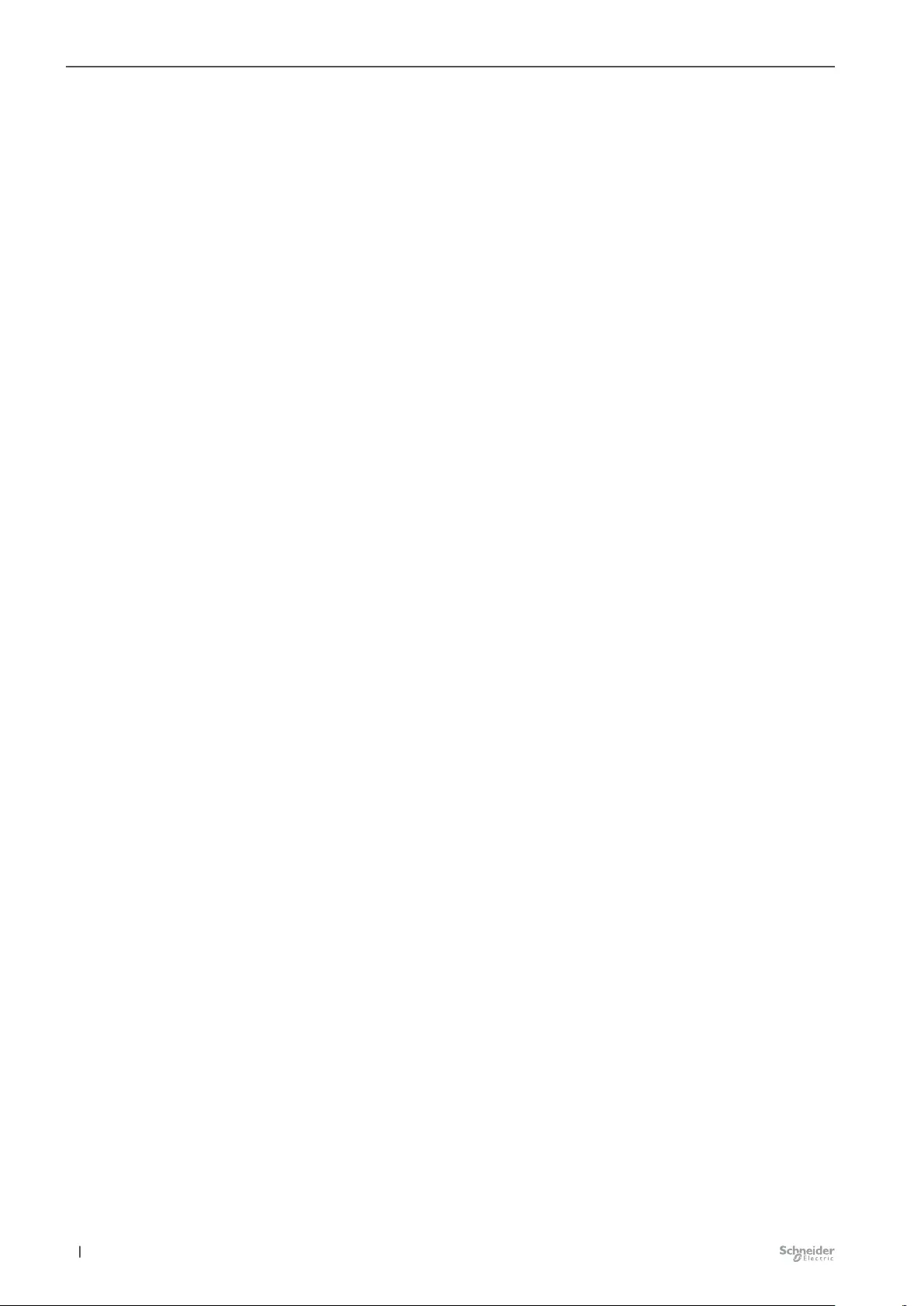
805/20-5800/1.0MTN6705-0008 | MTN6805-0008 |
Table of contents Switch Blind 5800/1.0
Table of contents
1 For your safety..................................... 11
1.1 Qualied personnel .........................................11
2 General information about the Switch Blind 5800/1.0
application ........................................ 12
2.1 Components and programming environment......................12
2.2 Overview of application functions...............................12
3 General settings ................................... 15
3.1 Device protection and Cyber Security ...........................15
3.2 Selection of the SpaceLogic KNX extensions .....................15
3.3 Dening channel functions ....................................16
Switch.................................................18
Blind ..................................................18
Roller shutter ...........................................18
3.4 Enabling central functions ....................................19
4 Extended settings . . . . . . . . . . . . . . . . . . . . . . . . . . . . . . . . . . 22
4.1 Energy saving .............................................22
4.2 Device safety ..............................................22
4.3 Device health ..............................................23
Cyclic sending live signal .................................23
Failure indicator . . . . . . . . . . . . . . . . . . . . . . . . . . . . . . . . . . . . . . . . . 23
4.4 Global settings for scenes....................................24
Scenes names .........................................24
Enable learning of scenes? ................................24
Enable description text eld for scenes . . . . . . . . . . . . . . . . . . . . . . . 24
4.5 Global settings for feedback...................................24
4.6 Sending delay after bus voltage recovery ........................25
4.7 Manual operation settings ....................................25
Activation of manual operation..............................25
Enable button for manual operation via object..................26
Suspend manual operation automatically .....................26
Send status of manual operation via object ....................27
4.8 Global settings for switching ..................................27
Activation of the collected status response ....................27
Priority of functions for switching . . . . . . . . . . . . . . . . . . . . . . . . . . . . 28
4.9 Global settings for roller shutter and blind ........................29
Weather alarm function ...................................29
Priority of functions for roller shutter and blind..................30
Calibration .............................................30
4.10 PIN Code for Firmware Update ................................31
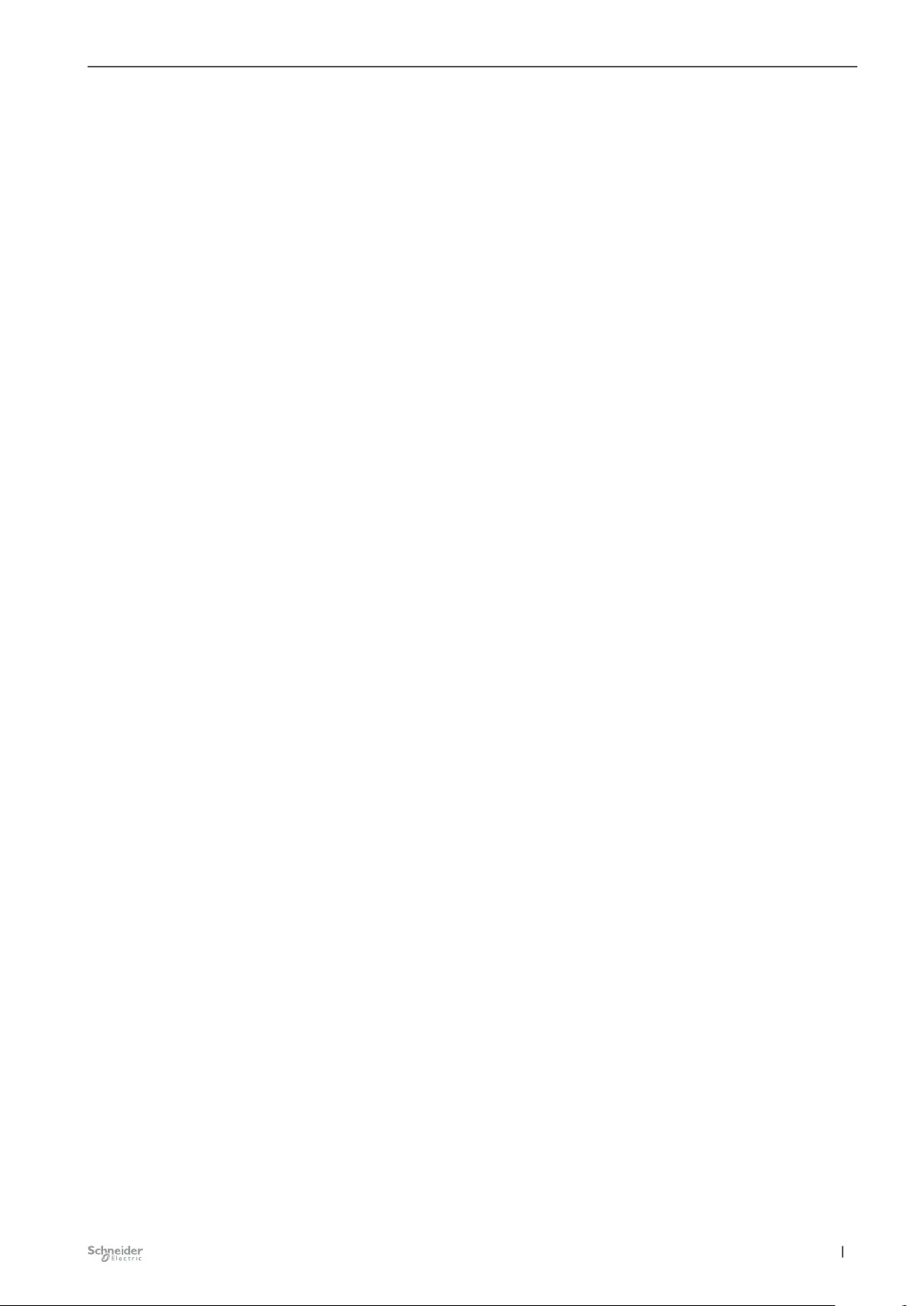
9
05/20-5800/1.0 MTN6705-0008 | MTN6805-0008 |
Table of contents Switch Blind 5800/1.0
5 Express settings for switching........................ 32
5.1 Name of the channel for switching ..............................32
5.2 Switching mode ............................................32
Switching ..............................................32
Blinking................................................34
5.3 Contact mode .............................................37
Normally opened ........................................37
Normally closed . . . . . . . . . . . . . . . . . . . . . . . . . . . . . . . . . . . . . . . . . 38
5.4 Scenes ..................................................39
Enable scenes . . . . . . . . . . . . . . . . . . . . . . . . . . . . . . . . . . . . . . . . . . 39
Number of scenes .......................................39
Time delay for scene processing ............................40
Calling and saving scene values ............................40
Overwrite scene values during download .....................41
5.5 Central function switching ....................................41
5.6 Status response ...........................................42
5.7 Activating extended settings for switching .......................42
6 Extended settings for switching ...................... 43
6.1 Time settings ..............................................43
Staircase lighting time function (staircase timer) . . . . . . . . . . . . . . . . 43
On-delay and o delay ....................................49
6.2 Logic, Locking & Priority settings ..............................53
Logic function...........................................53
Functions with higher priority ...............................57
Priority function (priority control) ............................57
Locking function .........................................59
6.3 Safety and alarm settings.....................................61
Safety function switching . . . . . . . . . . . . . . . . . . . . . . . . . . . . . . . . . . 61
Alarm function ..........................................62
Failure and download behavior .............................64
7 Express settings for blind / roller shutter ............... 67
7.1 Blind / roller shutter control ...................................68
7.2 Name of the channel ........................................70
7.3 Drive running time ..........................................70
7.4 Slat control (for blind only) ...................................72
Slat rotation time ........................................72
Setting the blind type (for blind only) .........................74
Slat position after movement . . . . . . . . . . . . . . . . . . . . . . . . . . . . . . . 78
7.5 Locking manual mode ......................................79
7.6 Scenes ..................................................80
Enabling scenes.........................................80
Number of scenes .......................................80
Time delay for scene processing ............................81
Calling and saving scene values ............................82
Overwrite scene values during download .....................83
7.7 Central function for blind .....................................83
7.8 Status response ...........................................84
7.9 Activating extended settings for blind ...........................85
7.10 Activating extended settings for roller shutter ....................85
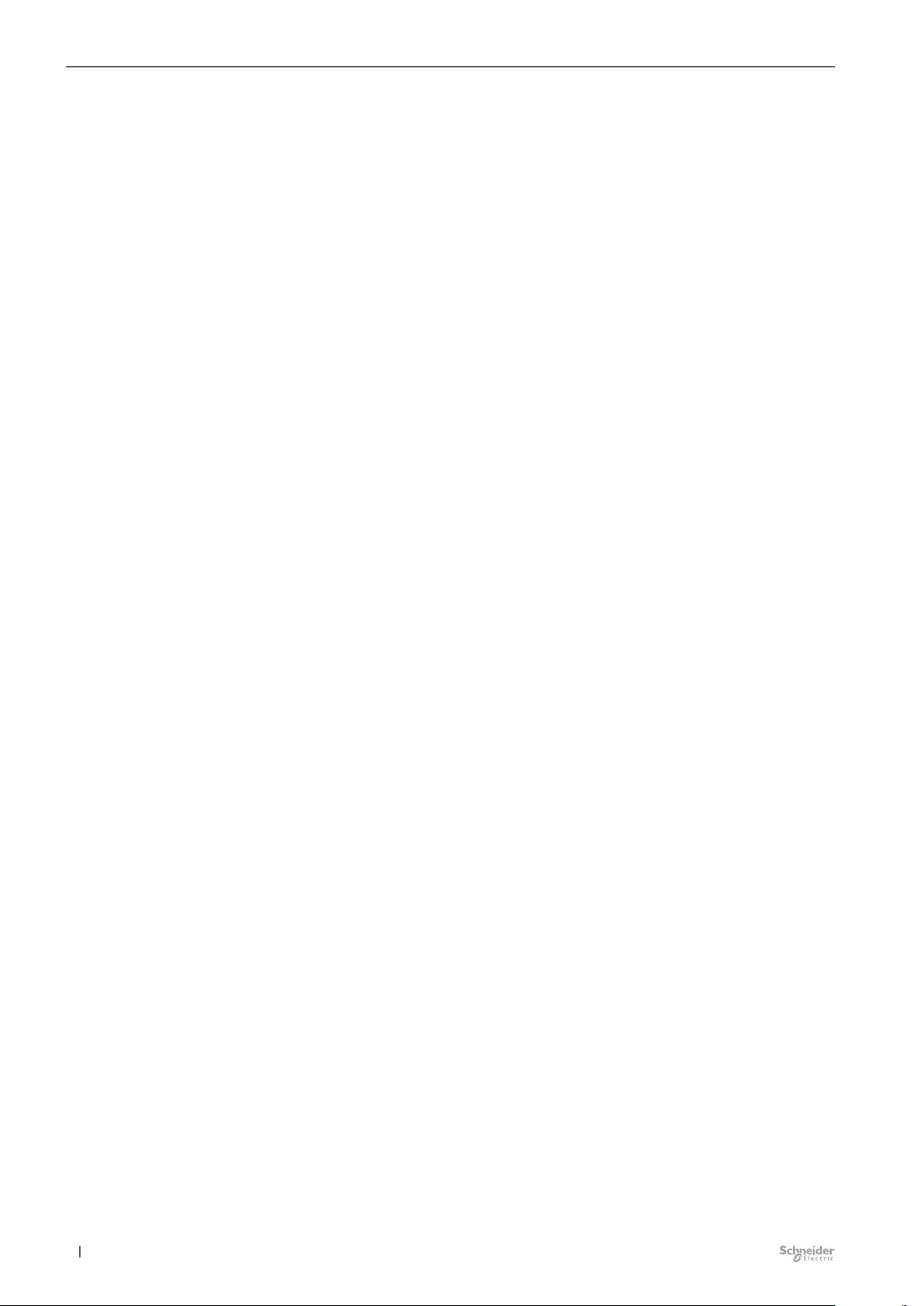
10 05/20-5800/1.0MTN6705-0008 | MTN6805-0008 |
Table of contents Switch Blind 5800/1.0
8 Extended settings for blind / roller shutter ............. 86
8.1 Extended drive timing .......................................86
Idle time until upward movement ............................87
Startup delay ...........................................87
Deceleration delay .......................................87
Additional start-up time on opening the slat
(for blind only) ..........................................88
8.2 Automatic, Locking & Calibration settings ........................88
Automatic mode .........................................88
Locking function .........................................91
Movement range limits....................................94
Calibration .............................................98
8.3 Safety and alarm settings....................................102
Safety function for blind . . . . . . . . . . . . . . . . . . . . . . . . . . . . . . . . . . 102
Alarm function .........................................104
Weather alarm function ..................................106
Failure and download behavior ............................110
9 Express settings for roller shutter ....................113
9.1 Name of the channel .......................................113
9.2 Roller shutter control drive time ..............................114
9.3 Locking manual mode ......................................114
9.4 Scenes .................................................115
9.5 Central function for roller shutter ..............................116
9.6 Status response ..........................................116
9.7 Activating extended settings for roller shutter ....................116
10 Extended settings for roller shutter ...................117
10.1 Extended drive timing.......................................117
10.2 Automatic, Locking & Calibration settings .......................118
Automatic mode ........................................118
Locking function ........................................120
Movement range limits...................................121
Calibration ............................................122
10.3 Safety and alarm settings....................................123
Safety function for roller shutter ............................123
Alarm function .........................................124
Weather alarm function ..................................125
Failure and download behavior ............................127
11 Overview of group objects ..........................128
12 Index.............................................130
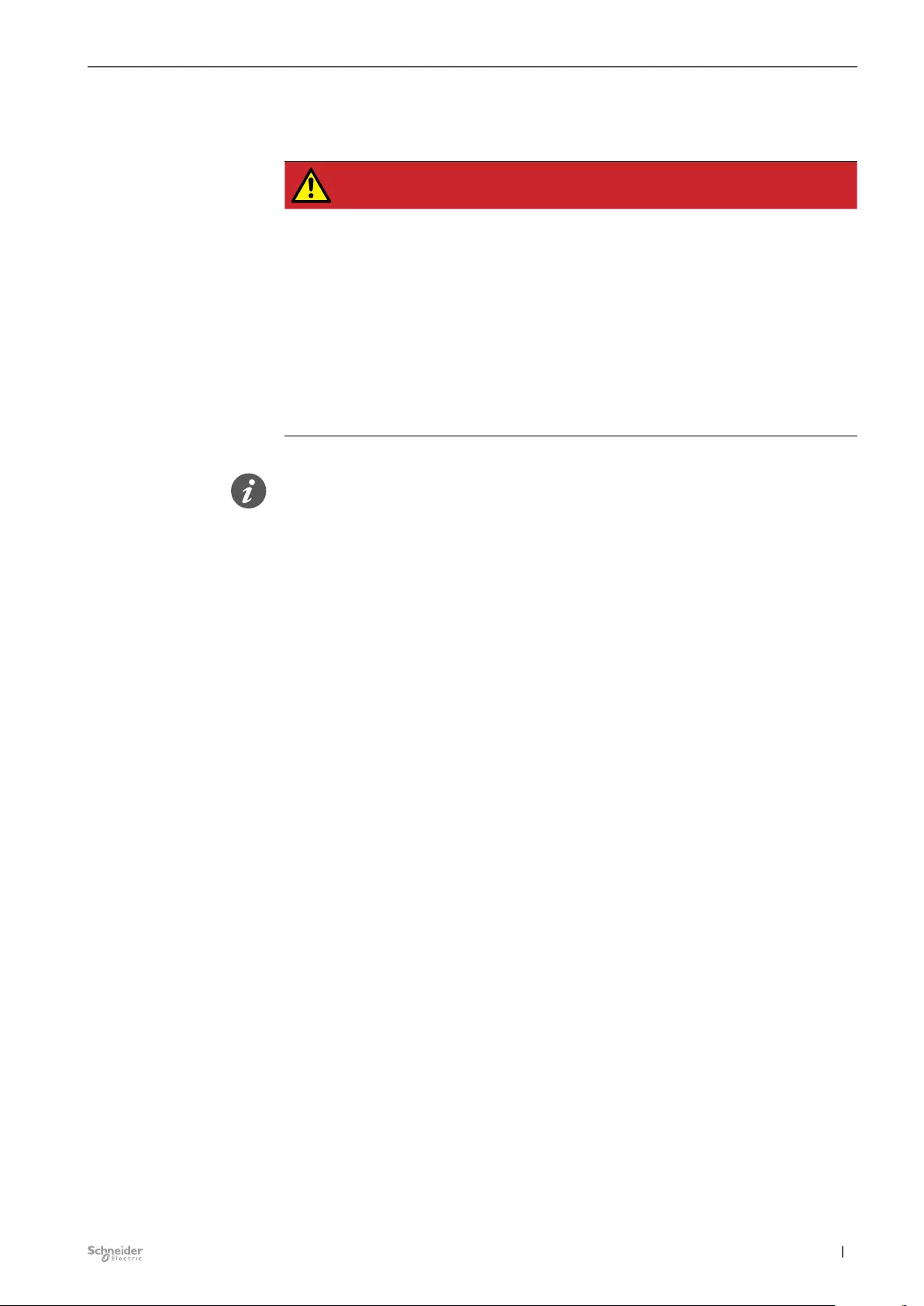
11
05/20-5800/1.0 MTN6705-0008 | MTN6805-0008 |
For your safety Switch Blind 5800/1.0
1 For your safety
DANGER
HAZARD OF ELECTRIC SHOCK, EXPLOSION, OR ARC FLASH.
Safe electrical installation must be carried out only by skilled profession-
als. Skilled professionals must prove profound knowledge in the following
areas:
• Connecting to installation networks
• Connecting several electrical devices
• Laying electric cables
• Connecting and establishing KNX networks
• Commissioning KNX installations
• Safety standards, local wiring rules and regulations
Failure to follow these instructions will result in death or serious injury.
The devices and the associated ETS application must not be used to control safe-
ty-relevant applications.
1.1 Qualified personnel
This document is aimed at personnel who are responsible for setting up, installing,
commissioning and operating the device and the system in which it is installed.
Detailed expertise gained by means of training in the KNX system is a prerequisite.
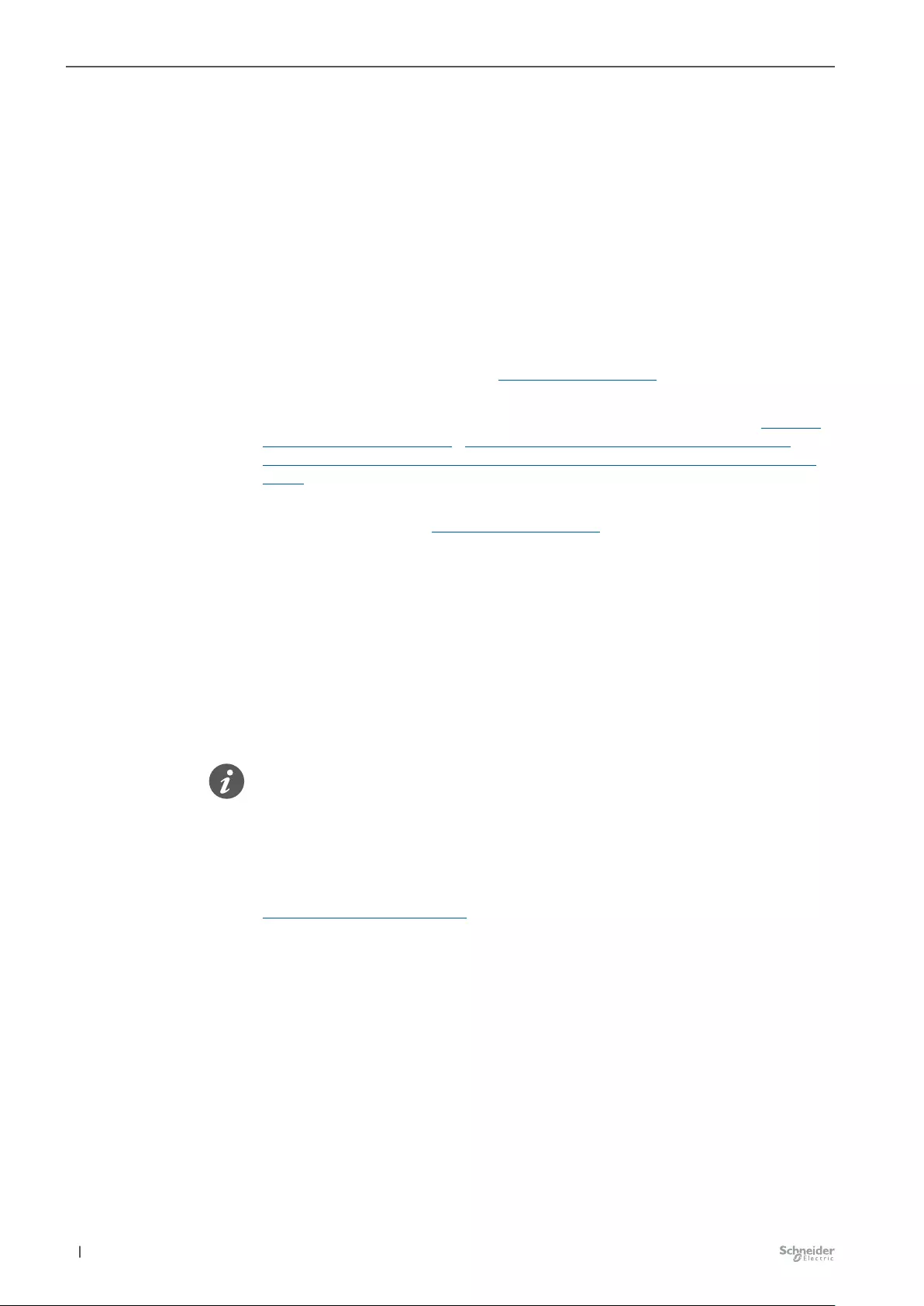
12 05/20-5800/1.0MTN6705-0008 | MTN6805-0008 |
General information about the Switch Blind 5800/1.0 application Switch Blind 5800/1.0
2 General information about
the Switch Blind 5800/1.0
application
With this application you can program the Switch/Blind Master. You can add up to
two Switch/Blind extensions to the device. Together with the two extensions, up
to 24 switching outputs are available. Two switching outputs can be congured as
blind/roller shutter outputs.
The basic settings of the device are set on the General settings tab. Here you de-
ne the device conguration from master and extensions. You can then also specify
the functions of the outputs here. (General settings --> 15).
The functions of the outputs are parameterized on the Express settings and Ex-
tended settings tabs of the outputs for switching, roller shutter and blind. Express
settings for switching --> 32., Express settings for blind / roller shutter --> 67,
Extended settings for switching --> 43, Extended settings for blind / roller shutter
--> 86
You can use the Extended settings of the device to congure the global settings of
the devices as needed. (Extended settings --> 22).
An overview of all group objects in this ETS application can be found at the end of
this document:
2.1 Components and programming environ-
ment
The device is commissioned using KNX-certied software. The application and the
technical descriptions are updated regularly and can be found on the Internet.
This application runs in conjunction with ETS software version 5 or higher.
2.2 Overview of application functions
You can set the following functions for the actuator.
General settings --> 15
•Select SpaceLogic KNX Extensions 1 and 2
–MTN6805-0008 Switch/Blind
•Select channel functions of the master for each output
–Disable
–Switch
–Roller shutter
–Blind
•Select channel functions of the extensions for each output
–Disable
–Switch
–Roller shutter
–Blind
•Enable central functions
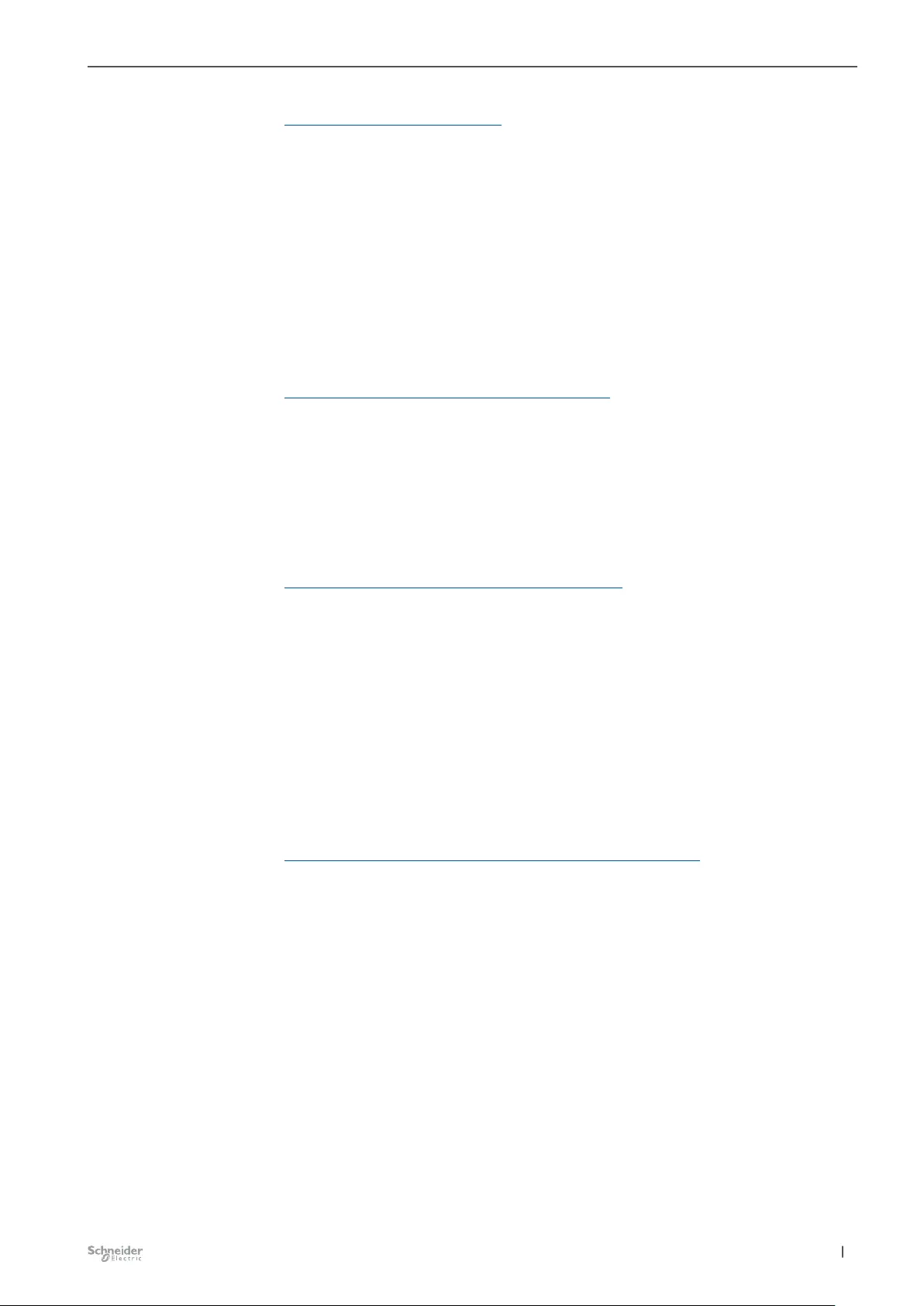
13
05/20-5800/1.0 MTN6705-0008 | MTN6805-0008 |
General information about the Switch Blind 5800/1.0 application Switch Blind 5800/1.0
Extended settings --> 22
•Energy saving
•Device safety
•Device health
•Global settings for scene
•Delay for central functions (Only if central function is enabled with delay)
•Global settings for feedback
•Sending delay
•Manual operation settings
•Global settings for switching
•Global settings for roller shutter and blind
•PIN Code for Firmware Update
Express settings for switching --> 32
•Name of the channel
•Switching mode
•Contact mode
•Scenes
•Central function
•Status response
•Extended settings for switching
Extended settings for switching --> 43
•Time settings
–Staircase lighting time
–On-delay time
–O-delay time
•Logic, Locking & Priority settings
–Priority function
–Logic function
•Safety and alarm settings
–Safety function
–Alarm function
–Failure and download behavior
Express settings for blind / roller shutter --> 67
•Name of the channel
•Blind control
–Up/Down time (same or dierent)
–Pause time before reverting
•Slat control
–Slat rotation time
–Steps that shall be executed during slat rotation
–Movement of the existing blind
–Slat position after movement
•Lock of manual mode
•Scenes
•Central function
•Status of height
•Status of slat
•Status of moving
•Extended settings for blind
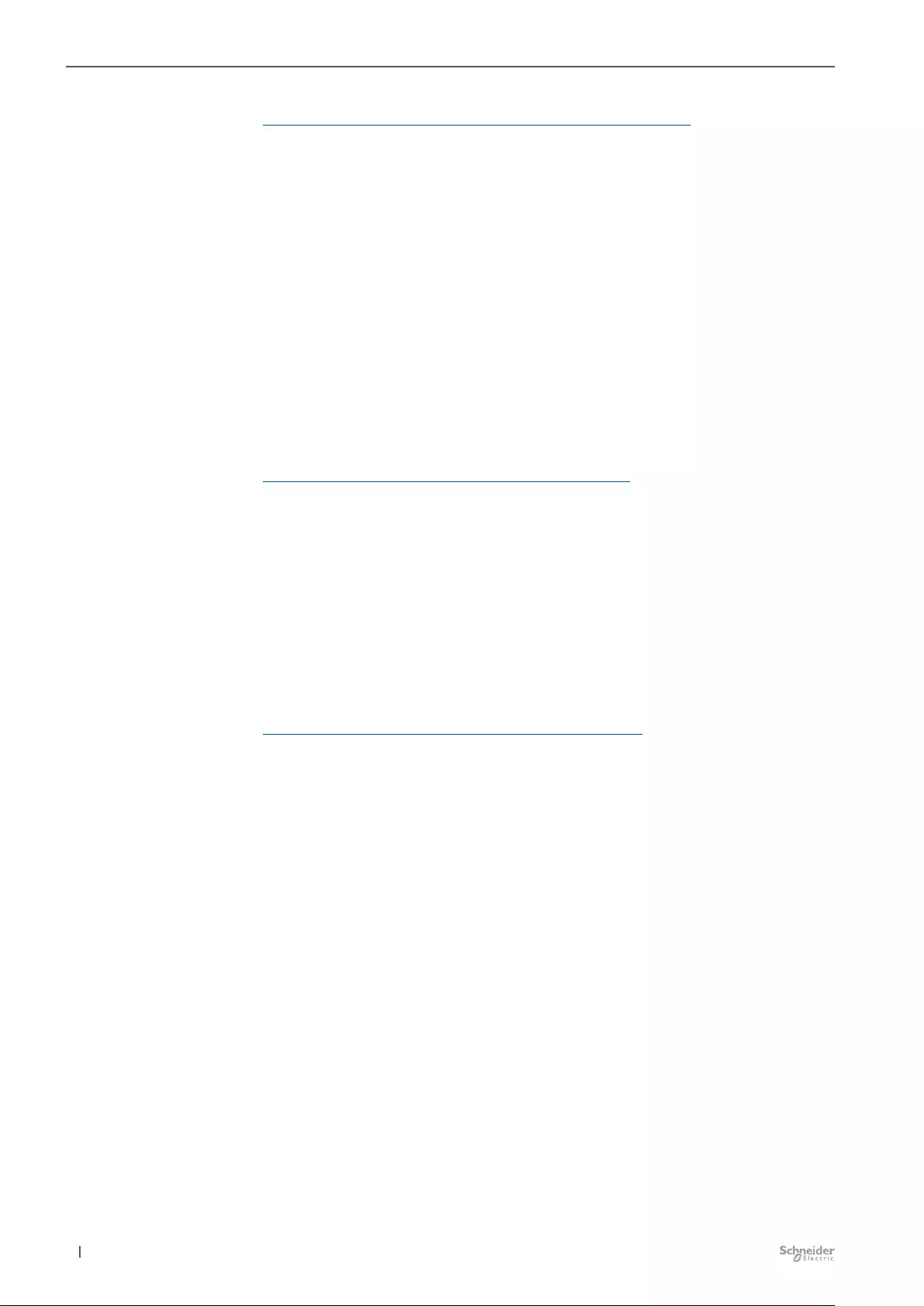
14 05/20-5800/1.0MTN6705-0008 | MTN6805-0008 |
General information about the Switch Blind 5800/1.0 application Switch Blind 5800/1.0
Extended settings for blind / roller shutter --> 86
•Extended drive timing
–Idle time until upward movement
–Startup delay
–Deceleration delay
–Additional startup time when opening slat upwards/downwards
•Automatic, Locking & Calibration settings
–Automatic mode
–Locking function
–Movement range limits
–Calibration
•Safety and alarm settings
–Safety function
–Alarm function
–Weather alarm function
–Failure and download behavior
Express settings for roller shutter --> 113
•Name of the channel
•Roller shutter control
–Up/Down time (same or dierent)
–Pause time before reverting
•Lock of manual mode
•Scenes
•Central function
•Status of height
•Status of moving
•Extended settings for roller shutter
Extended settings for roller shutter --> 117
•Extended drive timing
–Idle time until upward movement
–Startup delay
–Deceleration delay
•Automatic, Locking & Calibration settings
–Automatic mode
–Locking function
–Movement range limits
–Calibration
•Safety and alarm settings
–Safety function
–Alarm function
–Weather alarm function
–Failure and download behavior
Group addresses
•Maximum number of dierent group addresses: 1000
•Maximum assignments: 1000
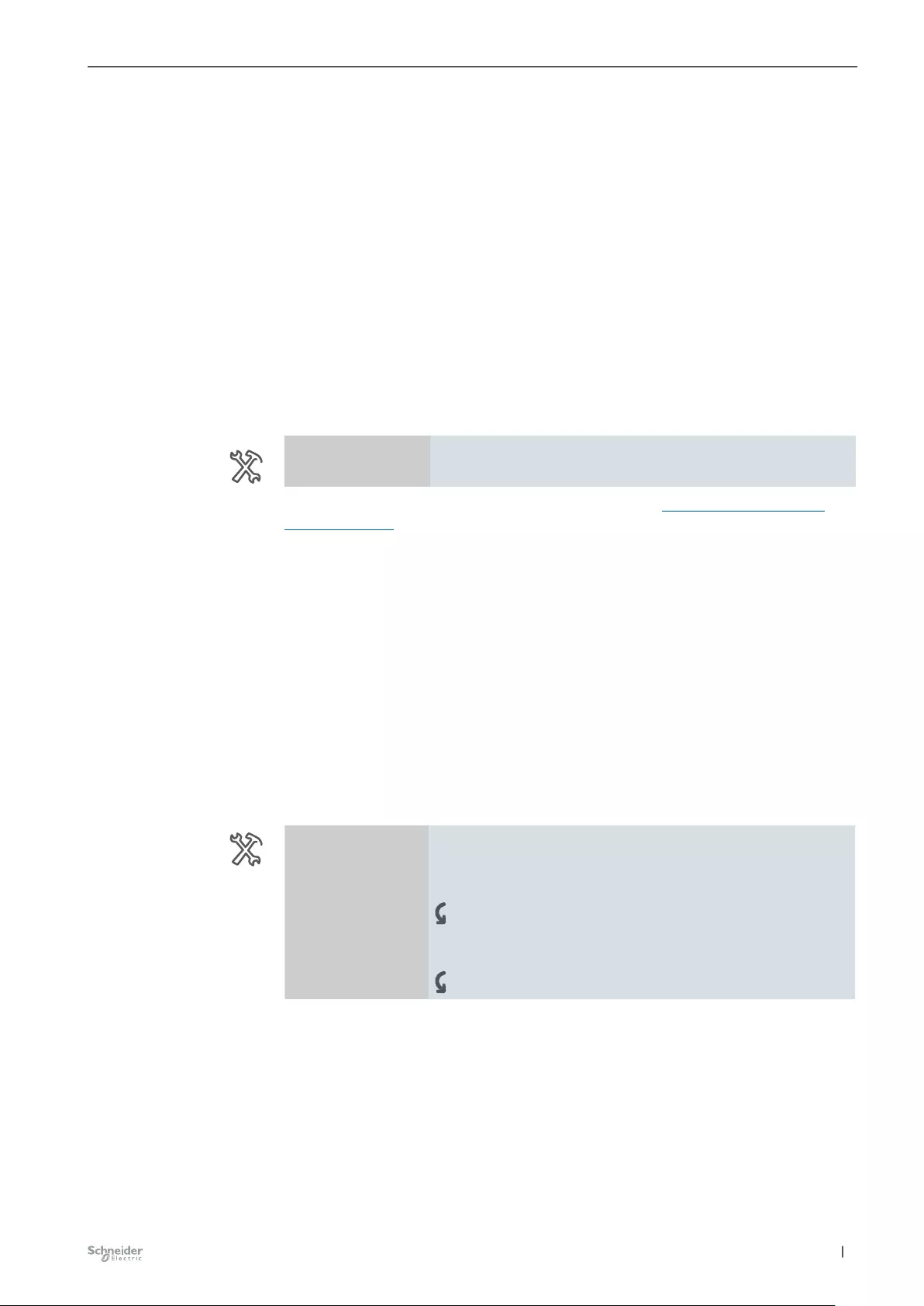
15
05/20-5800/1.0 MTN6705-0008 | MTN6805-0008 |
General settings Switch Blind 5800/1.0
3 General settings
You can dene the basic conguration of the device on the General settings tab.
3.1 Device protection and Cyber Security
The SpaceLogic KNX Switch/Blind Master has a micro USB B interface. This is
intended for diagnostic and updating the rmware of the device. A 4-digit PIN code
should be set in the ETS application to prevent unauthorized persons from manipu-
lating the rmware (Cyber Security).
This is requested before a rmware update with the Schneider Electric "Device
Firmware Update Tool". Without this PIN, an update is not possible. You have 3
attempts to enter a valid access code. If the code is not entered correctly, the ser-
vice port is disabled for 1 hour or the device needs to be restarted (power reset or
device reset).
General
settings
Device protection information:
No valid PIN Code for Firmware Update! Please enter a valid PIN code in
the extended settings before downloading your conguration!
The PIN code is entered on the Extended settings tab (PIN Code for Firmware
Update --> 31). Weak PINs are forbidden (e.g. 1234, 1111, 2222, ...)
3.2 Selection of the SpaceLogic KNX exten-
sions
The SpaceLogic KNX Switch/Blind Master is a KNX actuator that switches a max-
imum of 8 outputs (such as lamps) or controls a maximum of 4 blind motors with
end switches. The distribution of functions between channels is freely selectable
and depends on your requirements.
If you need more channels for your project, you can connect so-called SpaceLogic
KNX Switch/Blind extensions to the master. As with the master, channels can be
split into switching channels or blind channels. Since a master can control a maxi-
mum of 2 extensions, it is possible to switch a maximum of 24 outputs or control a
maximum of 12 blind motors.
General
settings
Selection of the SpaceLogic
KNX extension
Type of Extension 1 Disabled
MTN6805-0008 Switch/Blind
Type of Extension 2 Disabled
MTN6805-0008 Switch/Blind
Selecting MTN6805-0008 Switch/Blind adds Extension 1. The 8 new outputs with
tabs, parameters, channels and channel functions are now available in the applica-
tion.
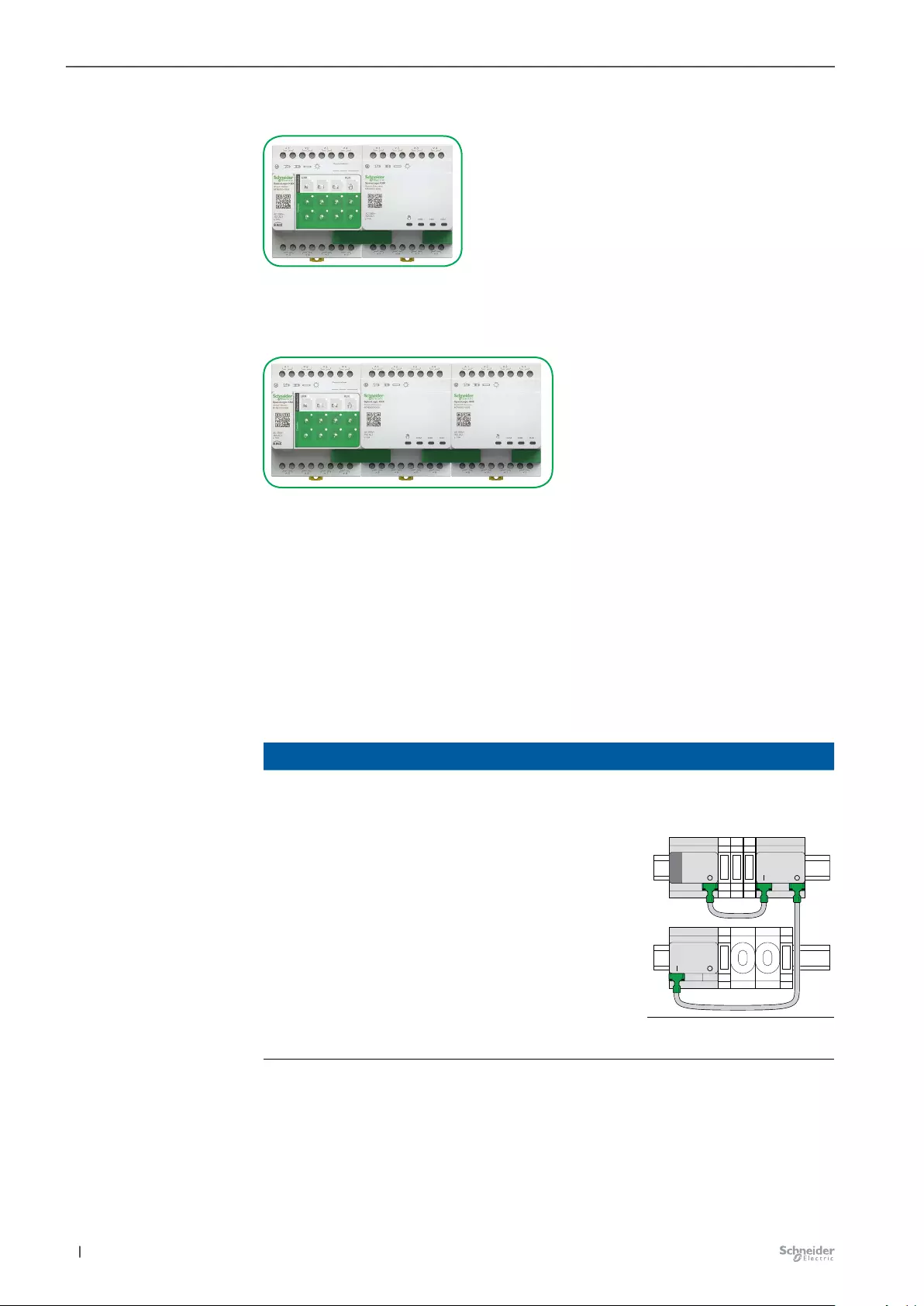
16 05/20-5800/1.0MTN6705-0008 | MTN6805-0008 |
General settings Switch Blind 5800/1.0
Extension 1 is displayed as an image to the right of the master.
Selecting MTN6805-0008 Switch/Blind as Extension 2 adds the second Switch/
Blind extension.
Extension 2 is displayed as an image to the right of Extension 1.
For Extension 2, the new outputs are now displayed with tabs, parameters, chan-
nels and channel functions.
3.3 Defining channel functions
Each output can be operated in the function disabled or switch or blind or roller
shutter. In blind and roller shutter operation, two outputs are grouped together to
form a single channel. The output contacts of the relays are then electronically in-
terlocked. This means that you cannot switch on both contacts of a motor channel
simultaneously. This applies to control via bus telegrams and to manual operation
on the device.
NOTICE
Check before commissioning: The load connections and the order of the
devices (Master -> Extension 1 -> Extension 2) must correspond to your
ETS programming.
•Connect blind motors to the blind channels
specied in the ETS.
•Connect loads to the switching channels
specied in the ETS.
•If the extension is planned as extension 1
(E1), connect it directly to the master.
•If the extension is planned as extension 2
(E2), then connect it to extension 1.
ME
1
E2
An extension cannot be put into operation if the order of the devices does
not correspond to your programming in the ETS.
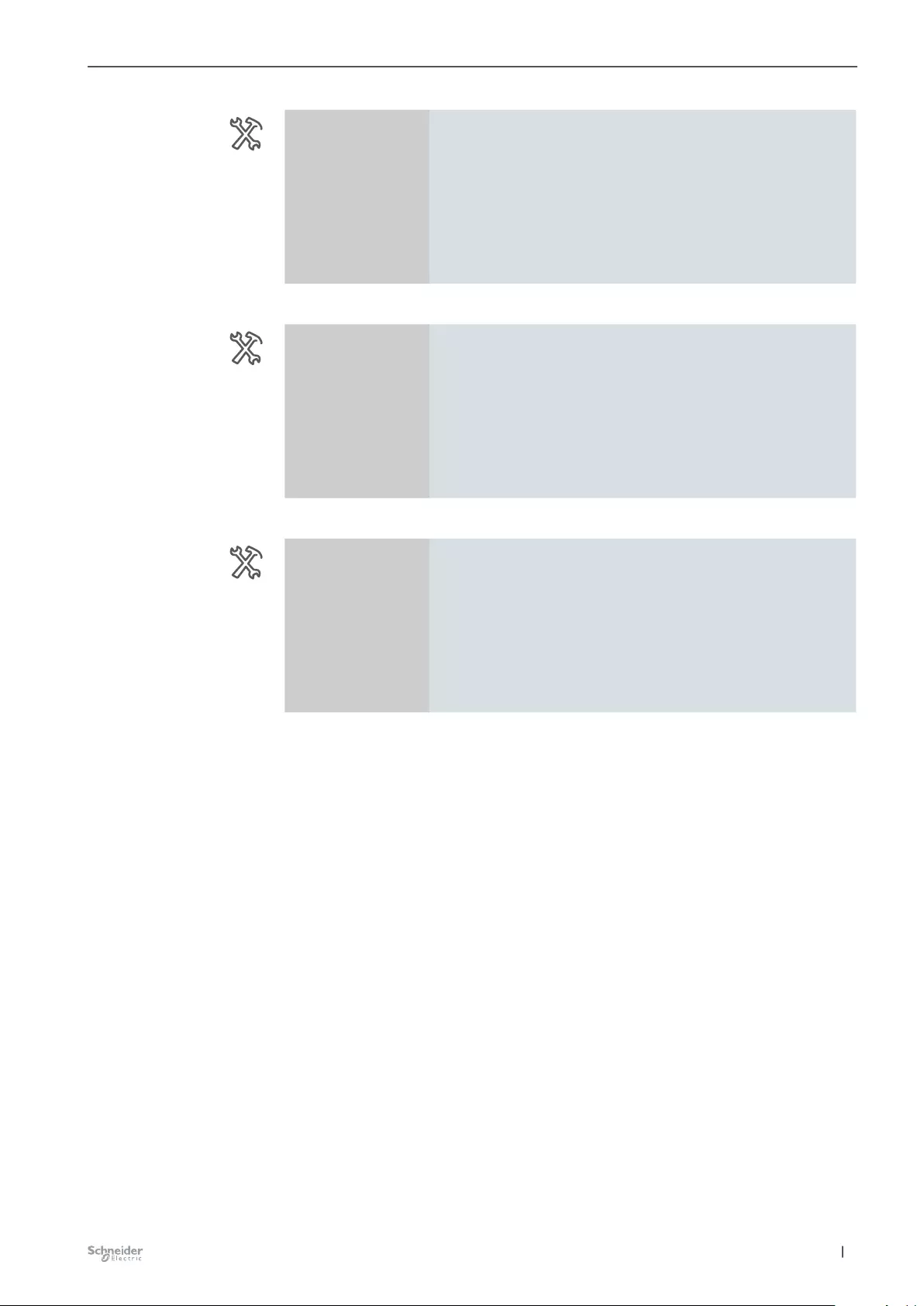
17
05/20-5800/1.0 MTN6705-0008 | MTN6805-0008 |
General settings Switch Blind 5800/1.0
General
settings Channel function for master
Output 1-8 Disable
Switch
Roller shutter
Blind
After activation of Extension 1:
General
settings Channel function for Extension 1
Output 1-8 Disable
Switch
Roller shutter
Blind
After activation of Extension 2:
General
settings Channel function for Extension 2
Output 1-8 Disable
Switch
Roller shutter
Blind
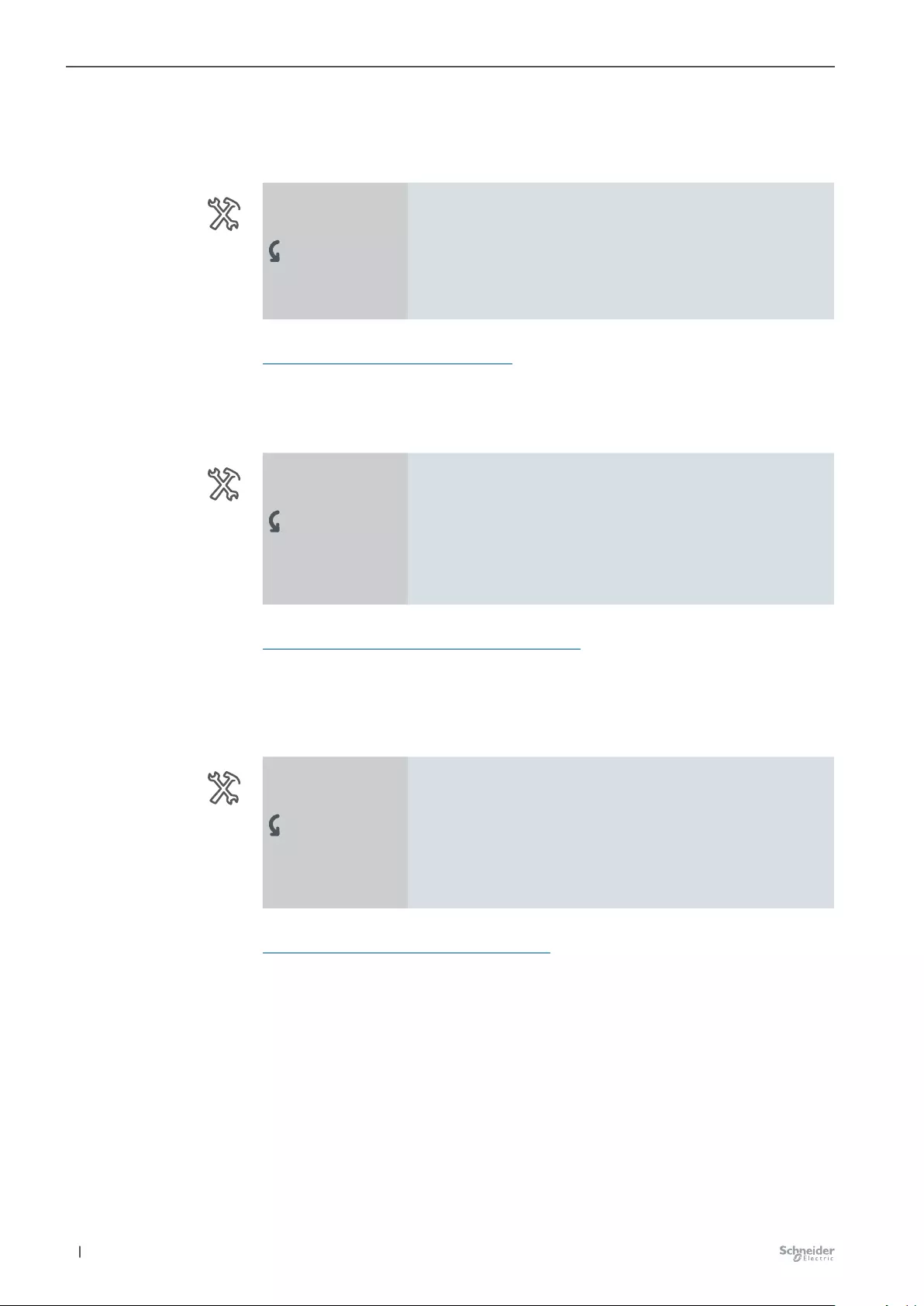
18 05/20-5800/1.0MTN6705-0008 | MTN6805-0008 |
General settings Switch Blind 5800/1.0
Switch
To switch electrical loads, you can switch the channel function of the device to
Switch mode.
General
settings
Channel function Master /
Extension 1 / Extension 2
Output 1-8 Switch
Master/Ext. 1/2
Output 1-8 -Switch:
-Switching
Express settings for switching ...
Express settings for switching --> 32.,
Blind
To control blinds, you can switch the channel function of the device to Blind mode.
General
settings
Channel function Master /
Extension 1 / Extension 2
Output 1-8 Blind
Master/Ext. 1/2
Output 1+2; 3+4; 5+6;
7+8 -Blind
-Blind
Express settings for blind ...
Express settings for blind / roller shutter --> 67
Roller shutter
To control roller shutter, you can switch the channel function of the device to Roller
shutter mode.
General
settings
Channel function Master /
Extension 1 / Extension 2
Output 1-8 Roller shutter
Master/Ext. 1/2
Output 1+2; 3+4; 5+6;
7+8 -Roller shutter
-Roller shutter
Express settings for Roller shutter ...
Express settings for roller shutter --> 113,
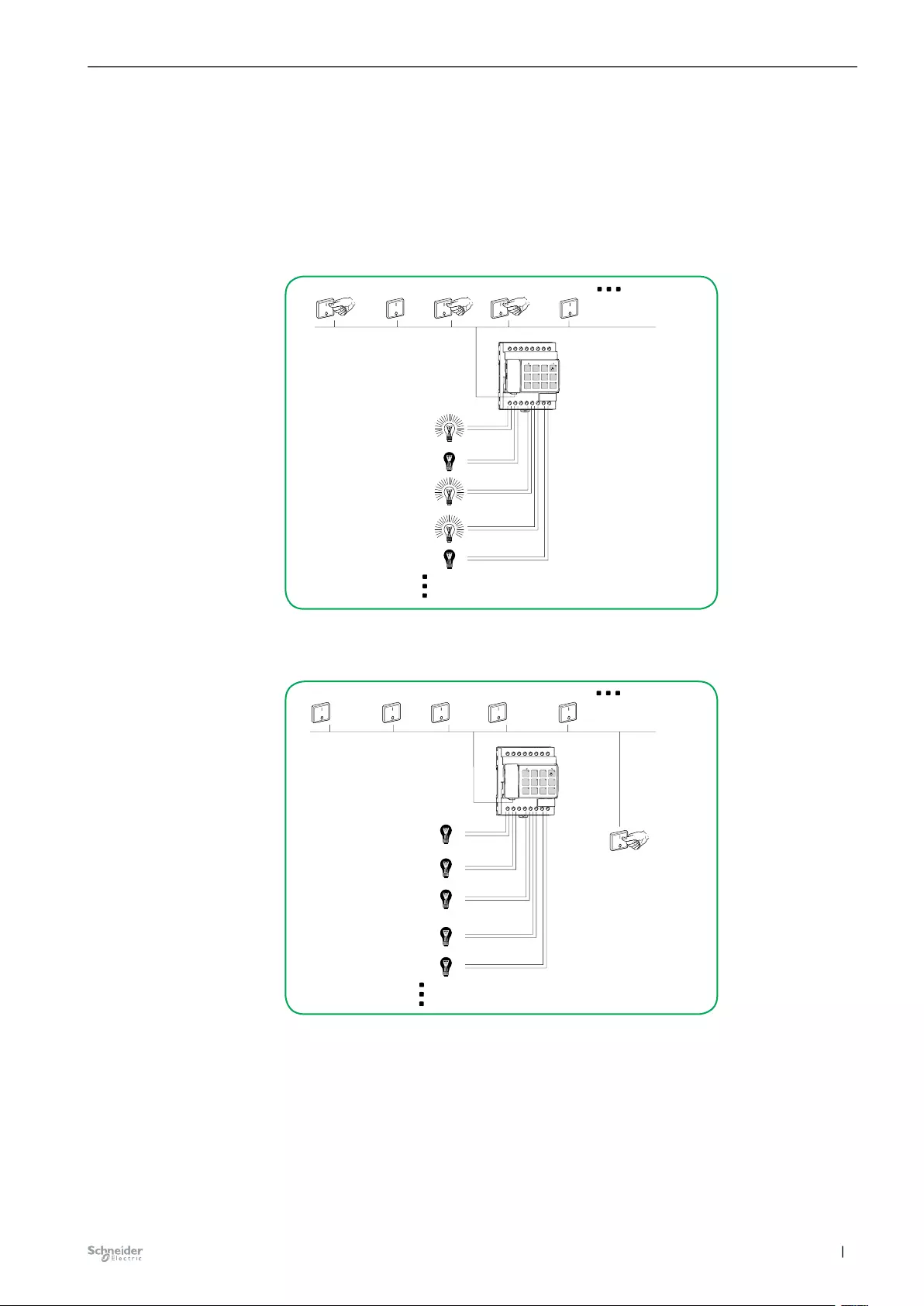
19
05/20-5800/1.0 MTN6705-0008 | MTN6805-0008 |
General settings Switch Blind 5800/1.0
3.4 Enabling central functions
The central function allows you to switch multiple output switching channels simul-
taneously with a telegram via the Central - Switch object. This functionality is avail-
able, for example, if you want to switch o all lamps at the press of a button when
leaving the house and switch on all lamps at the press of a button when cleaning
the house or in the event of an alarm.
Decentralized control without central function
NURRRE
Channels Device selection
ME 1 E 2
5678
1234
Office
Kitchen
Toilet
Hall
Cellar
Office
Cellar
Hall
ToiletKitchen
Centralized control with central function
NURRRE
Channels Device selection
ME 1 E 2
5678
1234
Office
Kitchen
Toilet
Hall
Cellar
Office
Cellar
Hall
ToiletKitchen
Central
switch
For blinds and roller shutters, there is a separate central object with a correspond-
ing central object.
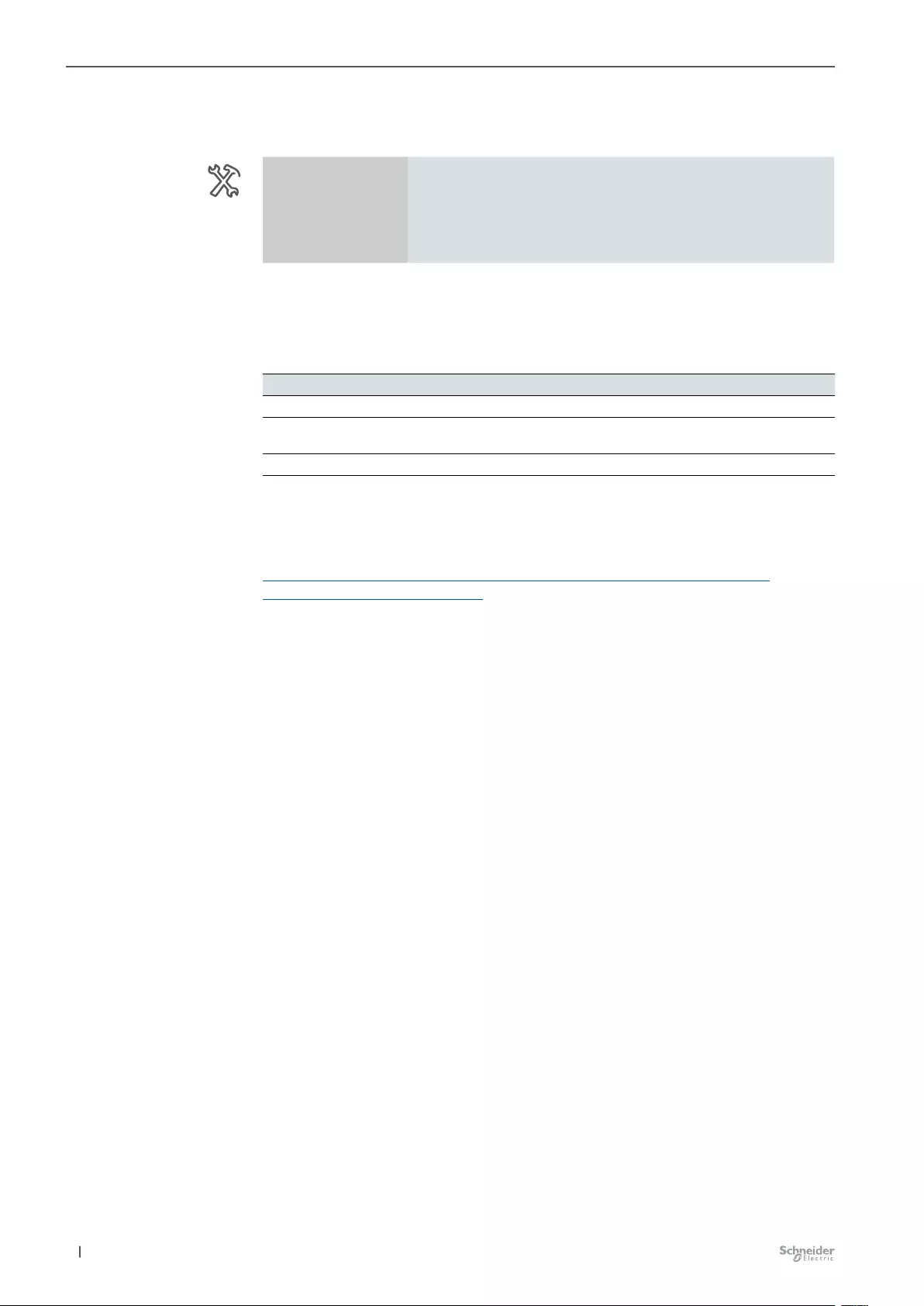
20 05/20-5800/1.0MTN6705-0008 | MTN6805-0008 |
General settings Switch Blind 5800/1.0
In order to use the central function for the individual switch/blind/roller shutter chan-
nels, you must rst enable the global function on the General settings tab.
General
settings Central functions Disabled
Enabled
Enabled / Delayed
Following enabling, the group objects appear and all outputs are enabled for the
central function.
Group objects
No. Name Object function Length Behavior Data Type
1 Central Switch 1 bit Received 1.001 Switching
2 Central Move up/down roller
shutter
1 bit Received 1.008 Up/Down
3 Central Move up/down blind 1 bit Received 1.008 Up/Down
Enabling a central function for each output
The central function for each output/drive is enabled or disabled on the Express
settings for Switching/Roller shutter/Blind tabs.
Central function switching --> 41; Central function for blind --> 83; Central
function for roller shutter --> 116
Group objects of the central
function
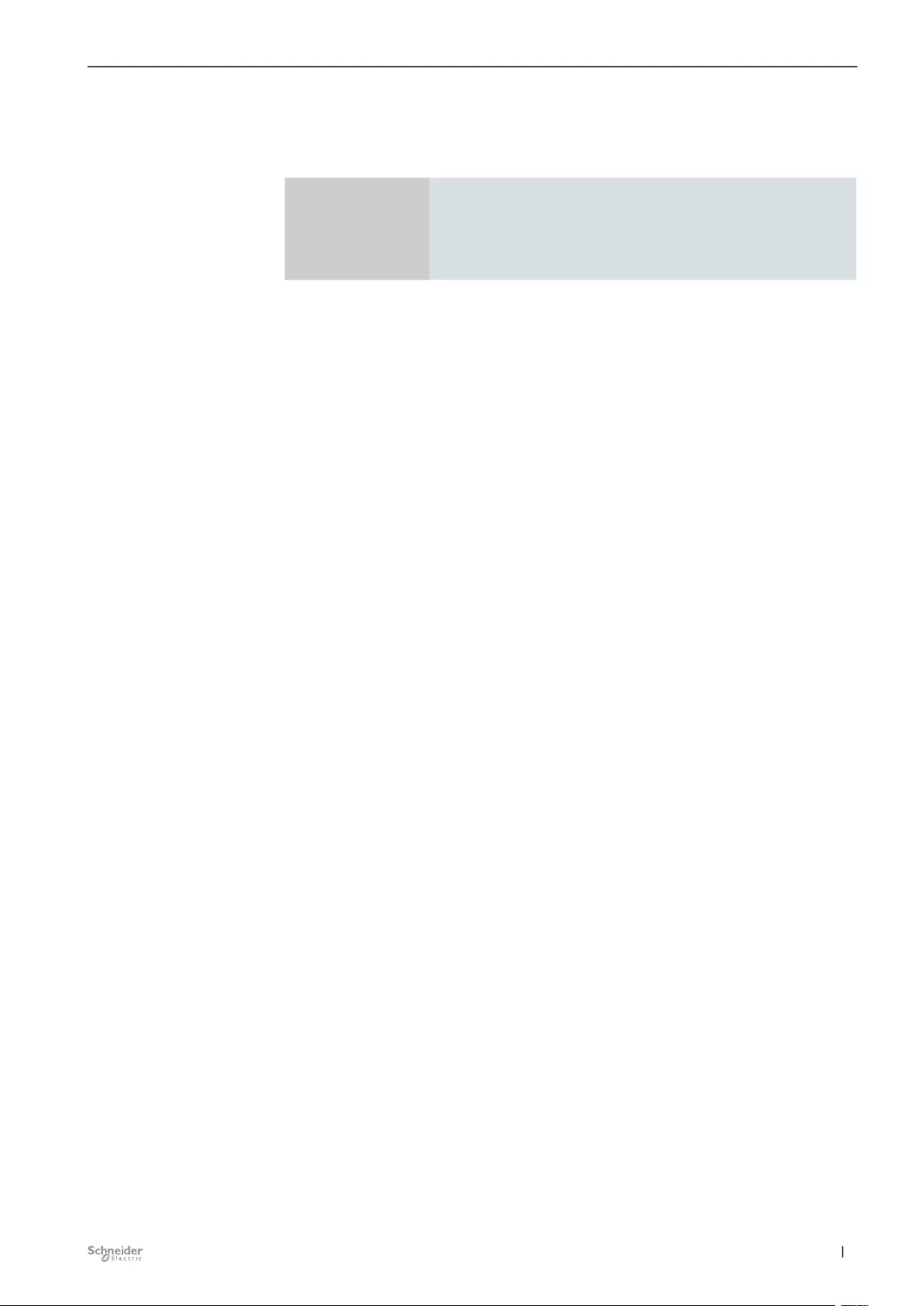
21
05/20-5800/1.0 MTN6705-0008 | MTN6805-0008 |
General settings Switch Blind 5800/1.0
Central function delay times
The delay times for all channels together are parameterized on the Extended set-
tings tab.
Extended settings
Delay of central functions
all channels (0...255, unit =
100ms)
0
Time between central func-
tions per channel (2...255, unit
= 100 ms)
5
The central function has the same priority as the normal switching function. Receiv-
ing a new object value via the central object has the same eect as receiving a new
object value for the switch object of the output.
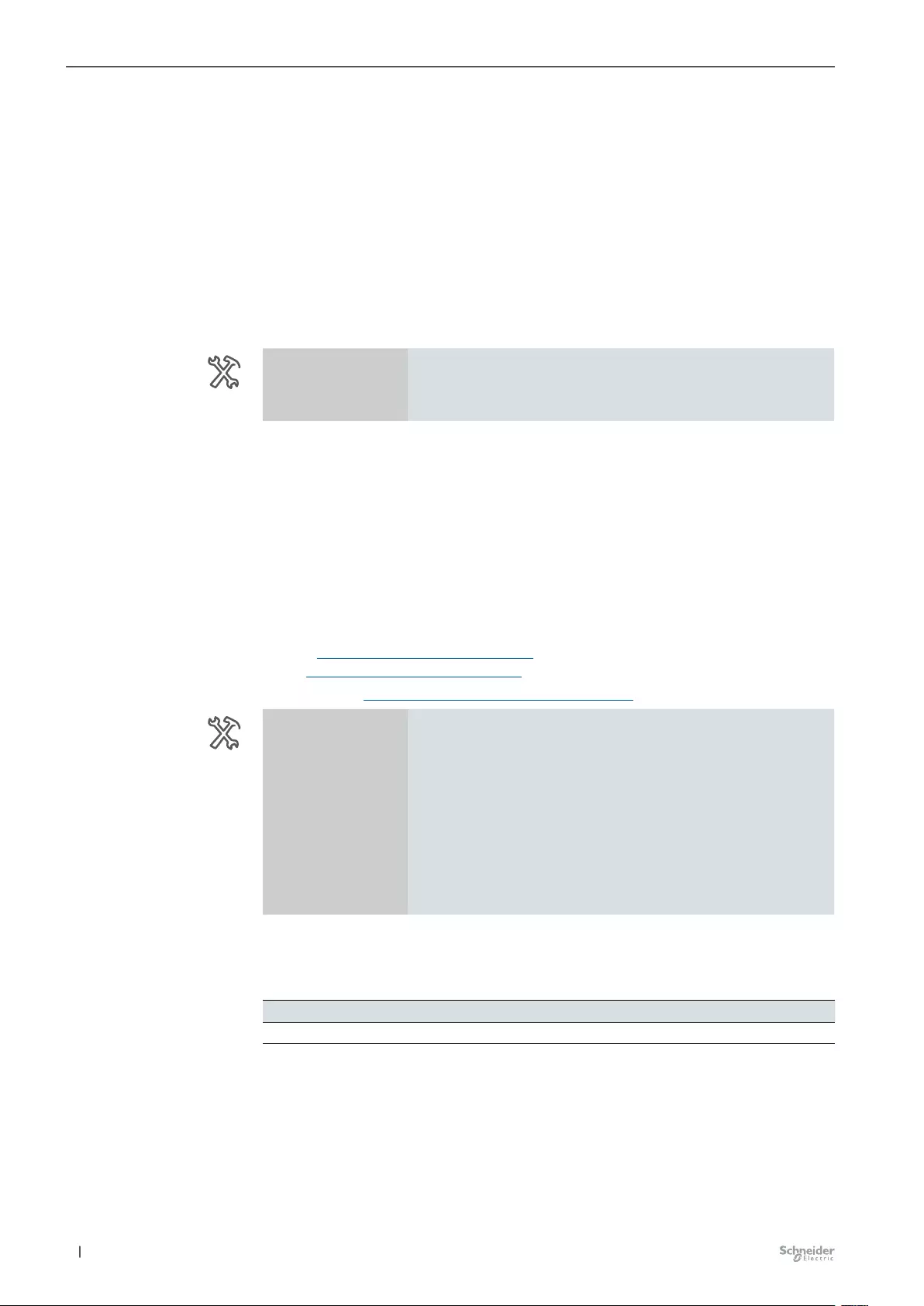
22 05/20-5800/1.0MTN6705-0008 | MTN6805-0008 |
Extended settings Switch Blind 5800/1.0
4 Extended settings
In the Extended settings, you can congure global device functions for the master
and the extensions.
4.1 Energy saving
The status LEDs of the channels on the master can be switched o automatically
after a period of between 1 minute and 255 minutes. In this way, you do not illumi-
nate the switch cabinet unnecessarily. Pressing a button reactivates the LEDs for
the preset time.
Extended settings Energy saving
LEDs on the device can be
set to standby after (0...255,
unit = 1 min, 0 = always on)
0
4.2 Device safety
This parameter activates the central safety object.
For each channel, a channel parameter can be used to determine whether and how
this channel should respond to the safety object. The object value for the device
safety function can also be set.
The device then waits for a telegram from an external sender within the set cycle
time. If such a telegram is not received within the monitoring time, it is then possi-
ble to decide for each channel what should happen.
Switch: Safety function switching --> 61
Blind: Safety function for blind --> 102
Roller shutter: Safety function for roller shutter --> 123
Extended
settings Device safety
Device safety At object value "1"
At object value "0"
Disabled
Cycle time surveillance for
Safety object
(0 ... 255, unit = 1 s,
0 = inactive)
0
Following enabling, the group object appears.
Group objects
No. Name Object function Length Behavior Data Type
23 Central Safety 1 bit Received 1.005 Alarm
Safety function priority
The safety function has the highest priority.
Group object for
central safety
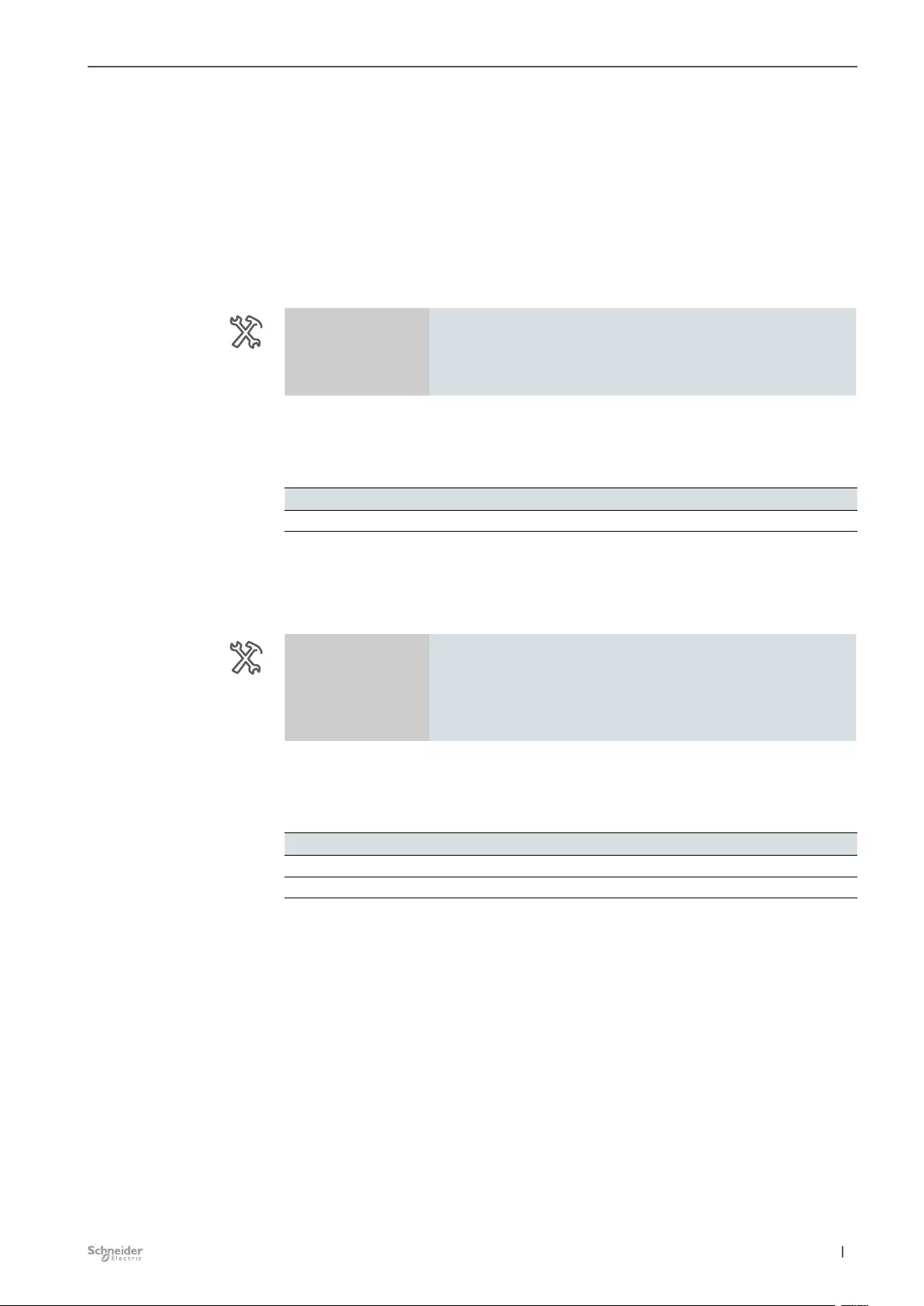
23
05/20-5800/1.0 MTN6705-0008 | MTN6805-0008 |
Extended settings Switch Blind 5800/1.0
4.3 Device health
Cyclic sending live signal
With the setting Cyclic sending live signal > 0, the central sign of life object is acti-
vated (live signal).
If activated, the device cyclically sends the value "1" with the cycle time set. This
information is only a sign of life from the KNX master. Here, for example, the device
can be monitored in a visualization.
Extended
settings Device health
Cyclic sending live signal
(0...255, unit = 1 s,
0 = inactive)
0
Following enabling, the group object appears.
Group objects
No. Name Object function Length Behavior Data Type
26 Central Life signal 1 bit Sending 1.017 Triggers
Failure indicator
The failure indicator of the device can be activated in the ETS. Failure indication is
carried out using two group objects.
Extended
settings Device health
Enable outputs for failure
indication Disabled
Enabled
Following enabling, these group objects appear.
Group objects
No. Name Object function Length Behavior Data Type
27 Master Fault - Internal 1 bit Sending 1.001 Switching
28 Master Fault - External 1 bit Sending 1.001 Switching
The Fault - Internal object signals internal device faults detected during the self-
test. The Schneider-Electric Device Firmware Update Tool can be used to diagnose
the fault with the integrated diagnostics function.
The Fault - External object signals external installation faults. The Schneider-Elec-
tric Device Firmware Update Tool can be used to diagnose the fault with the inte-
grated diagnostics function.
Group object for
live signal
Group object for
failure indicator
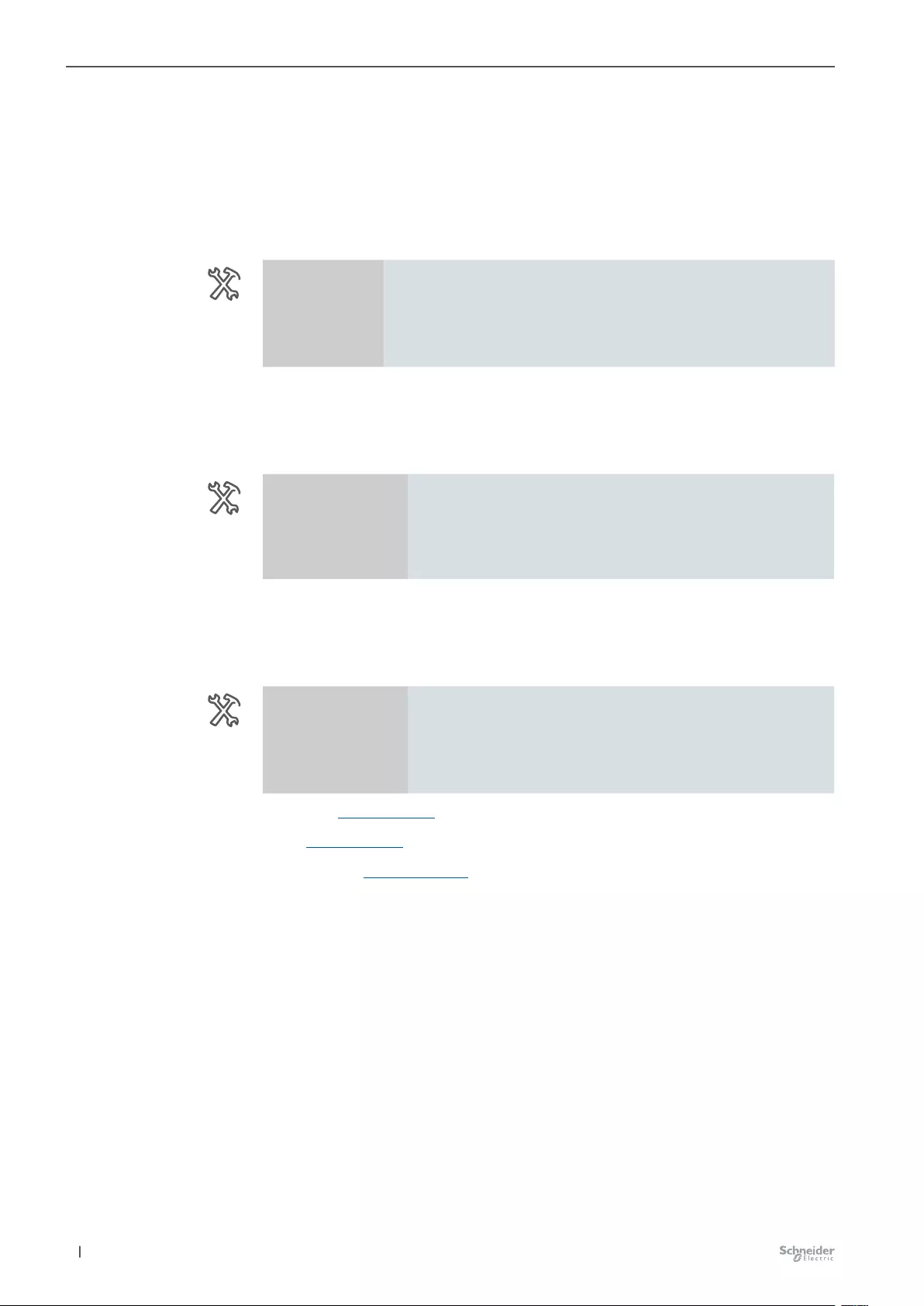
24 05/20-5800/1.0MTN6705-0008 | MTN6805-0008 |
Extended settings Switch Blind 5800/1.0
4.4 Global settings for scenes
Scenes names
This parameter is used to dene the scene numbering view for the user in the ETS.
Either Scene address 1 - 64 or Scene address 0 - 63. The values on the bus are
always 0-63
Extended
settings Global settings for scene
Naming of the scenes
(The values on the bus are always 0-63) Scene address 0 - 63
Scene address 1 - 64
Enable learning of scenes?
The parameter Enable learning of scenes? is activated as standard and the learn-
ing of scenes is thus allowed. This can be disabled globally.
Extended
settings Global settings for scene
Enable learning of scenes? Yes
No
Enable description text field for scenes
A description text can be stored for each scene. This provides clarity for the dier-
ent scenes. This function can be switched o globally here.
Extended
settings Global settings for scene
Enable description text eld
for scenes Yes
No
Switching: Scenes --> 39
Blind: Scenes --> 80
Roller shutter: Scenes --> 115
4.5 Global settings for feedback
Here you can set the delay of the feedback of this device and the time interval
between multiple feedback telegrams.
If there is only one telegram to be sent, it is sent as set in the parameter Delay of
status response for all channels. If more than one response is active, the other re-
sponses will be sent at the delay time intervals set by the parameter Time between
responses per channel.
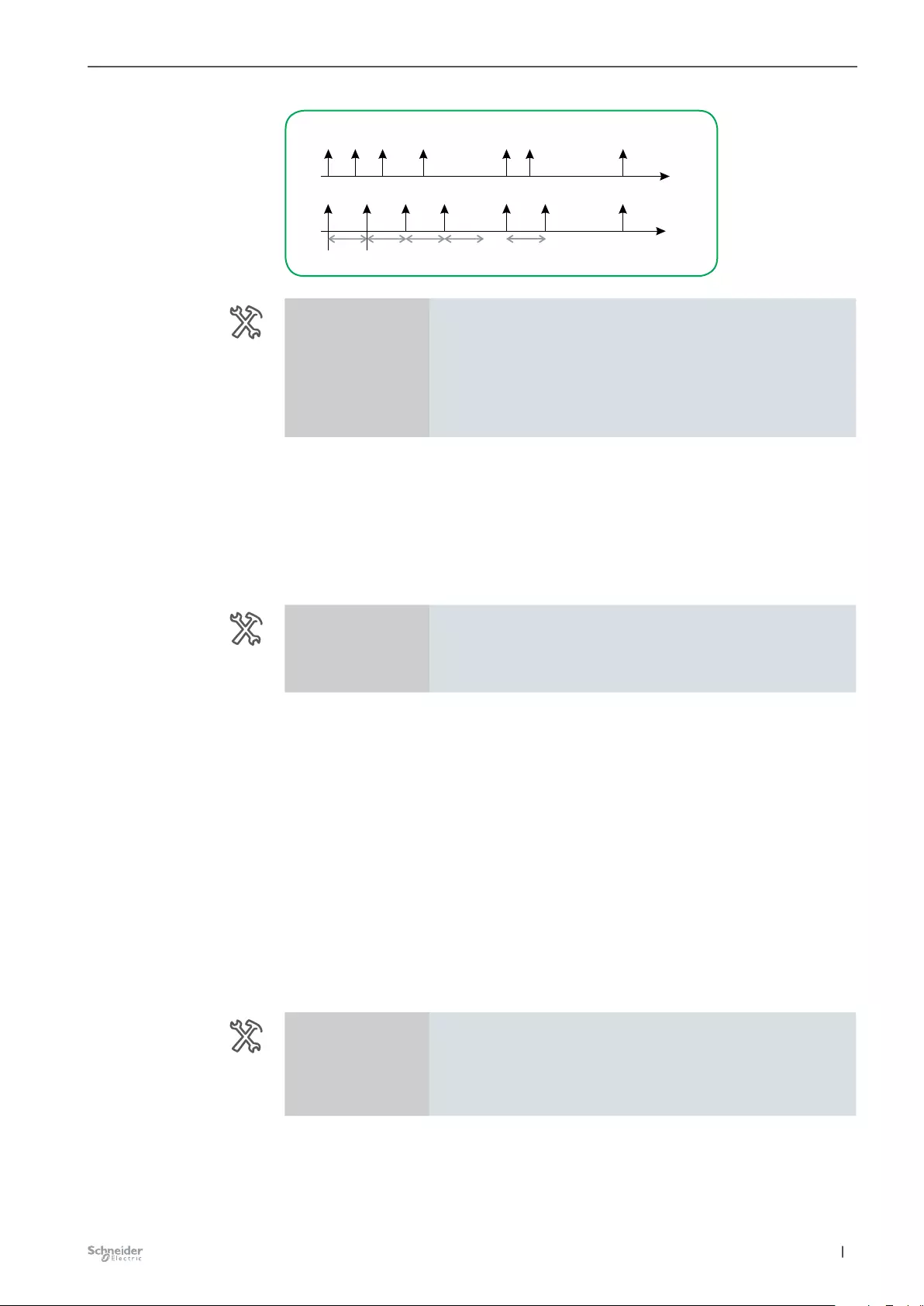
25
05/20-5800/1.0 MTN6705-0008 | MTN6805-0008 |
Extended settings Switch Blind 5800/1.0
Feedback messages
Telegrams
Time between
feedback messages
R1 R2 R3 R4 R5 R6 R7
R1 R2 R3 R4 R5 R6 R7
Extended
settings Global settings for feedback
Delay of status response for
all channels
(0...255, unit = 100 ms)
0
Time between status re-
sponse per channel.
(0...50, unit = 100 ms)
0
4.6 Sending delay after bus voltage recovery
It is possible to set a global sending delay for all telegrams after bus voltage recov-
ery.
Once the bus voltage has been recovered, all send activities of the device are
delayed.
Extended
settings Sending delay
Sending delay after bus volt-
age recovery
(0...255, unit = 1 s)
0
4.7 Manual operation settings
On the front side of the master, there is a channel button for each channel and a
corresponding yellow LED for indicating the channel status (channel status LED).
In addition to the channel buttons, the device also has device selection buttons (M
for the master; E1 for Extension 1; E2 for Extension 2). With these buttons, you
rst select the device (Master/Extension 1/Extension 2) whose status you want to
display or which you want to operate. Manual operation is performed after pressing
the Manual pushbutton and then a channel button.
Activation of manual operation
Manual operation can be disabled on the device in the ETS. This means that oper-
ation on the device is no longer possible.
Extended
settings Manual operation settings
Activation of manual operation
on the device is Not allowed
Allowed
Manual operation is allowed as standard.
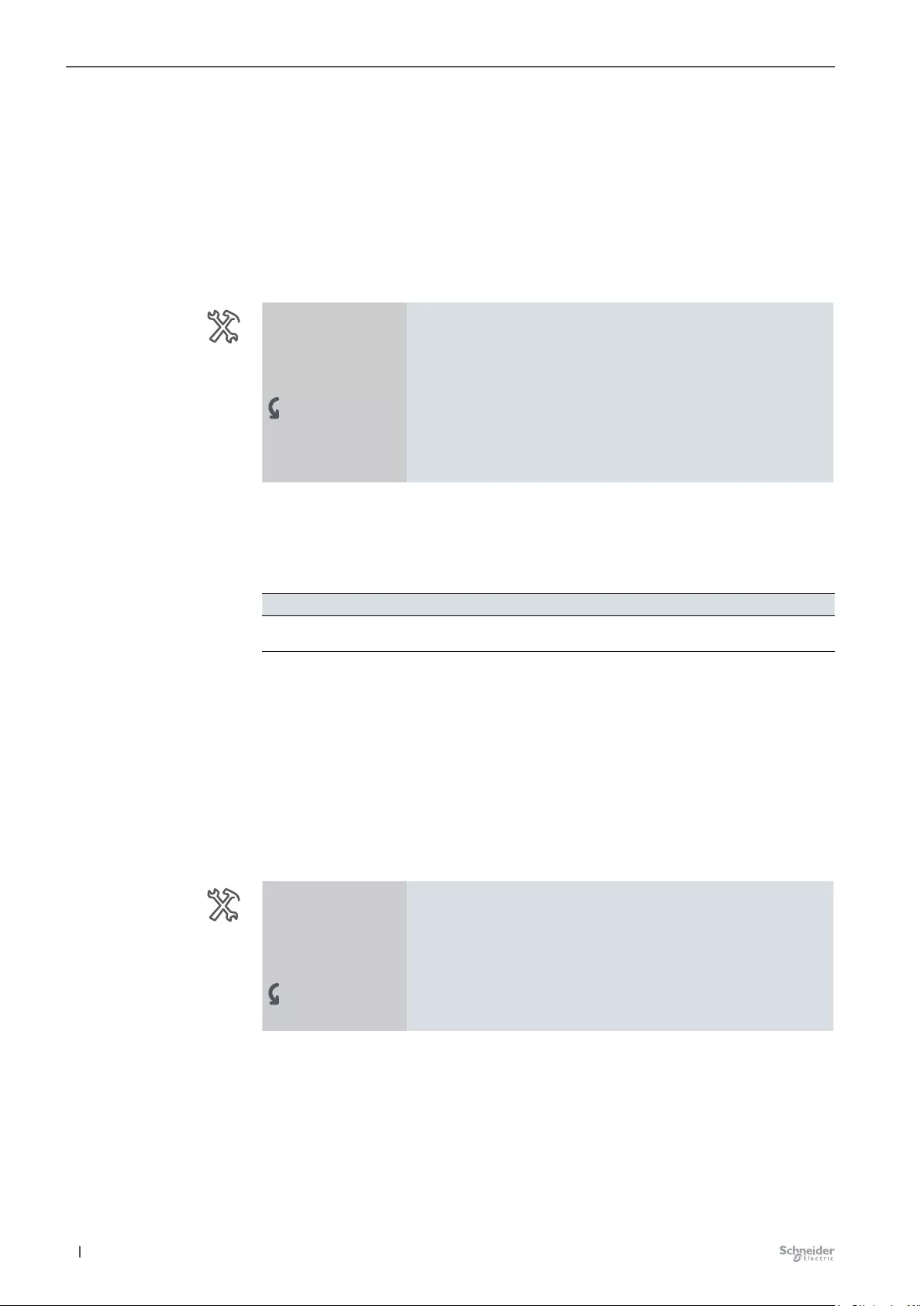
26 05/20-5800/1.0MTN6705-0008 | MTN6805-0008 |
Extended settings Switch Blind 5800/1.0
Enable button for manual operation via object
Switching to manual operation control via the Manual pushbutton is only possible
if the object Enable button for manual operation via object has the value "1". If the
object has the value "0", toggling to manual operation is disabled. If toggling is dis-
abled by a telegram, the device also automatically deactivates manual operation.
The value of the object Enable button for manual operation via object can be pa-
rameterized after bus voltage recovery. The value "1" enables the Manual push-
button and the outputs can be operated on the device. The value "0" disables the
Manual pushbutton after bus voltage recovery.
Extended
settings Manual operation settings
Enable button for manual
operation via object No
Yes
Object value after bus voltage
recovery 0 (Manual pushbutton disabled)
1 (Manual pushbutton enabled)
As before bus voltage failure
Following "Enable button for manual operation via object", the group object ap-
pears.
Group objects
No. Name Object function Length Behavior Data Type
15 Master keypad Enable button for
manual operation
1 bit Received 1.003 Enabled
Suspend manual operation automatically
You can set a time limit for manual operation when toggling to it. To do so, set the
parameter Suspend manual operation automatically to Yes
Then set the parameter Suspend manual operation after 1...48 in hours to the
desired time after which the device automatically resets manual operation. You
can read the current operating status from the manual operation LED and you will
receive feedback via the "Status of manual operation" object if you have enabled
this function.
Extended
settings Manual operation settings
Suspend manual operation
automatically No
Yes
Suspend manual operation
after
(1...48, unit = 1 hour)
2
Group object for
enable button for manual
operation
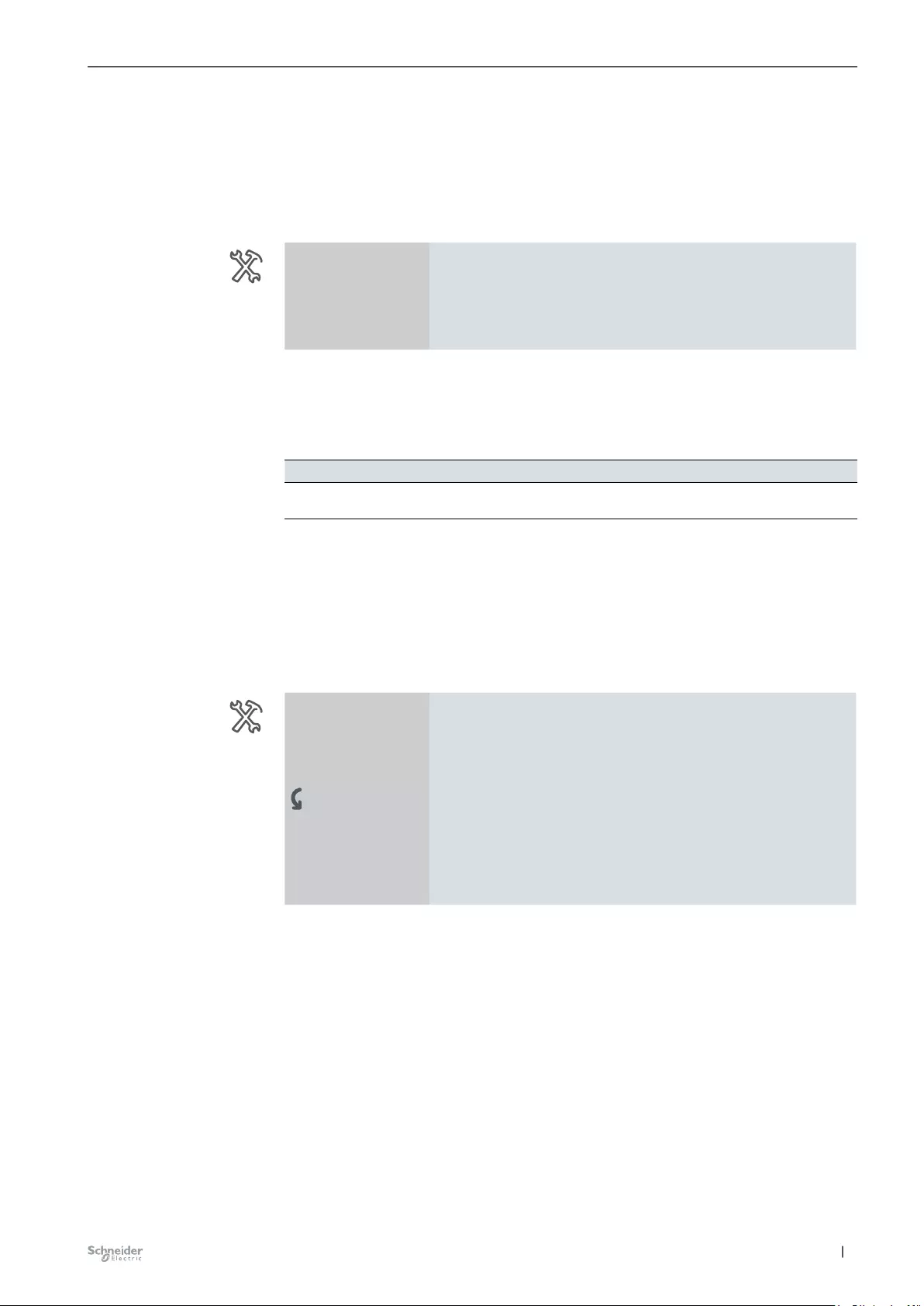
27
05/20-5800/1.0 MTN6705-0008 | MTN6805-0008 |
Extended settings Switch Blind 5800/1.0
Send status of manual operation via object
In addition to the possibility of enabling manual operation via the "Enable manual
operation" object, it is also possible to send the status of the manual operation via
the "Status of manual operation" object. You can read the current operating status
from the manual operation LED and you will receive feedback via the "Status of
manual operation" object if you have enabled this function.
Extended
settings Manual operation settings
Send status of manual opera-
tion via object No
Yes
Once Send status of manual operation via object has been enabled, the group
object appears.
Group objects
No. Name Object function Length Behavior Data Type
16 Master keypad Status of manual
operation
1 bit Send/Read 1.001 Switching
4.8 Global settings for switching
The global settings for the switching functions are dened here.
Activation of the collected status response
The collected status response can be activated on the device in the ETS.
Extended
settings Global settings for switching
Collected status response No
Yes
Assign channel status to 1bit
value
Normal behavior (Pressed=1, Re-
leased=0)
Inverted
Delay time sending
(0...255, unit = 1 s) 60
With the collected status response object, you can send the status responses cod-
ed bit-by-bit via a 4-byte telegram with a time delay.
Each device (Master / Extension 1 / Extension 2) has its own collected status re-
sponse object.
The collected status response is intended to save group addresses and to reduce
the bus load, e.g. in the case of a Central O telegram, the 8 channels are grouped
together to form a single collected status response.
Group object for
status of manual operation
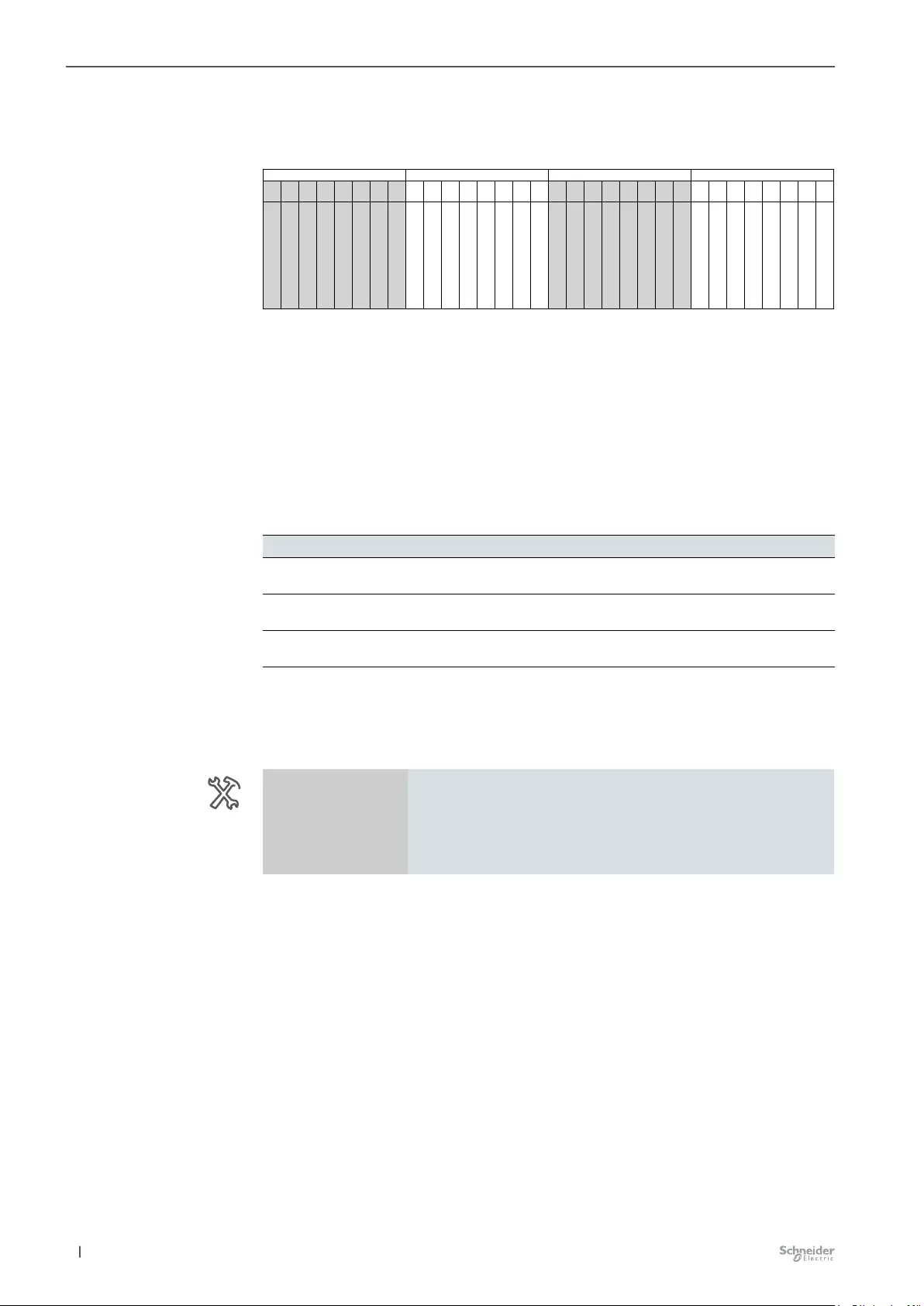
28 05/20-5800/1.0MTN6705-0008 | MTN6805-0008 |
Extended settings Switch Blind 5800/1.0
The four-byte object has the following structure. The upper two bytes indicate
which status bit is valid ("1" = valid, "0" = invalid). The lower two bytes indicate the
statuses (pressed or released) of the channels.
Byte 4 Byte 3 Byte 2 Byte 1
76543210765432107654321076543210
Not used
Not used
Not used
Not used
Not used
Not used
Not used
Not used
Valid output 8
Valid output 7
Valid output 6
Valid output 5
Valid output 4
Valid output 3
Valid output 2
Valid output 1
Not used
Not used
Not used
Not used
Not used
Not used
Not used
Not used
Status output 8
Status output 7
Status output 6
Status output 5
Status output 4
Status output 3
Status output 2
Status output 1
Example: Master with 8 switching channels, channels 2 and 6 are pressed
00000000 11111111 00000000 00100010
You can dene or invert the value of the collected status response (pressed=1,
released=0 or pressed=0, released=1) via the parameter Assign channel status to
1bit value.
Once the set sending delay has expired, the current status of the output channels
is sent to the bus.
Group objects
No. Name Object function Length Behavior Data Type
10 Master Collected status 4 bytes Send/Read 27.001 bit-combined info
On/O
11 Extension 1 Collected status 4 bytes Send/Read 27.001 bit-combined info
On/O
11 Extension 2 Collected status 4 bytes Send/Read 27.001 bit-combined info
On/O
Priority of functions for switching
The global priorities for switching are dened here. The safety function has the
highest priority. The other priorities can be selected here.
Extended
settings Global settings for switching
Priority of functions Safety->Alarm->Lock/Prio->all other
Safety->Lock/Prio->Alarm->all other
Group object for
collected status
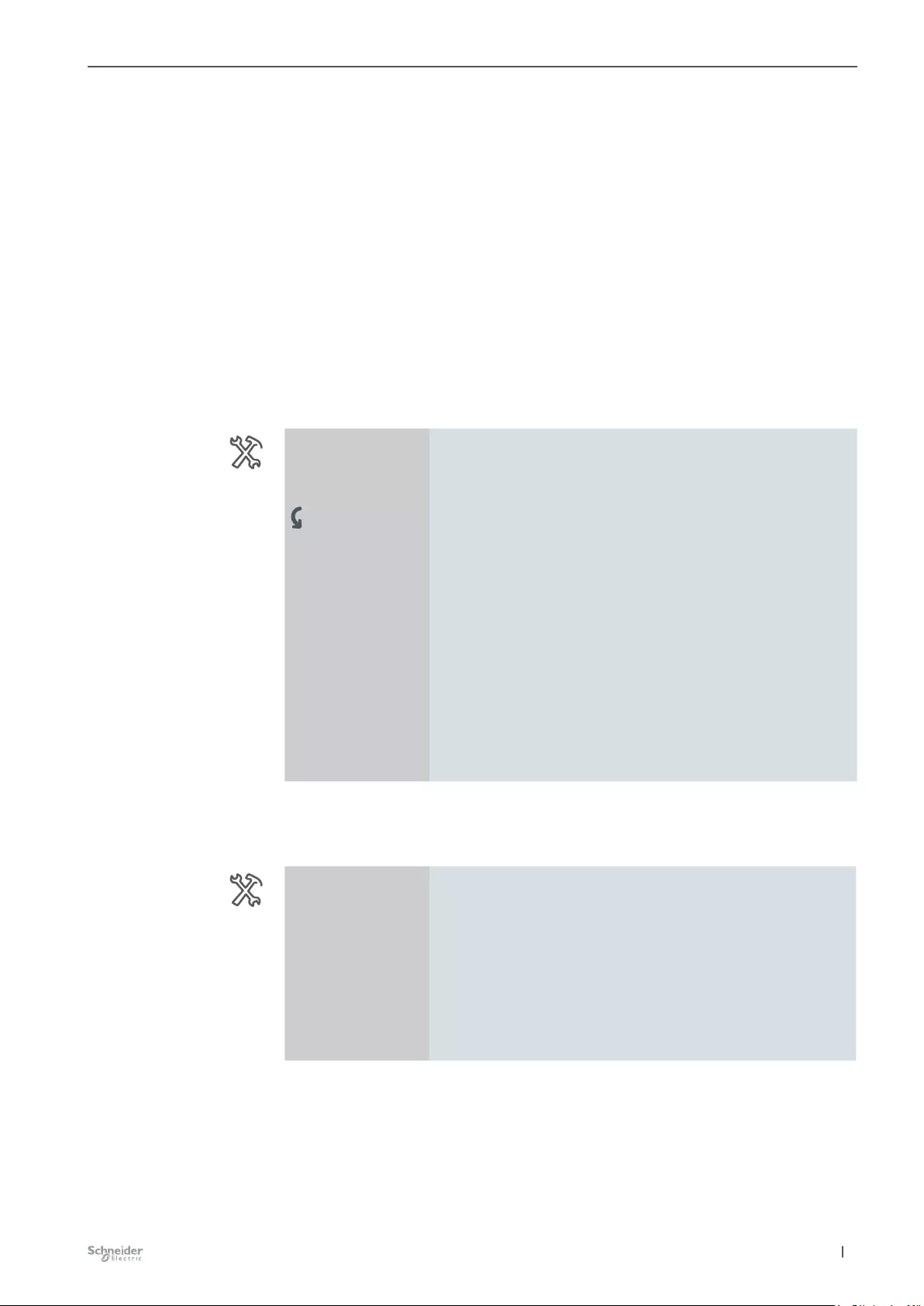
29
05/20-5800/1.0 MTN6705-0008 | MTN6805-0008 |
Extended settings Switch Blind 5800/1.0
4.9 Global settings for roller shutter and blind
The global settings for roller shutter and blind are dened here.
Weather alarm function
The weather alarm function can be activated for all roller shutter/blind channels in
the ETS.
There are now 5 dierent weather alarms available, together with their group ob-
jects.
The monitoring of the signals of the activated weather sensors can be carried out
cyclically. The device then expects a telegram from the relevant sensor within the
cycle time set. If such a telegram is not received within the monitoring time, the as-
sociated weather alarm is nevertheless triggered for safety reasons (if, for example,
the sensor or the cable connection between sensor and blind channel is defective
and no message would be sent in the event of a genuine alarm).
Extended
settings Global settings for roller shutter and blind
Weather alarm function Disabled
Enabled
Monitoring time for wind alarm 1 Disabled
1 s ... 12 h
Monitoring time for wind alarm 2 Disabled
1 s ... 12 h
Monitoring time for wind alarm 3 Disabled
1 s ... 12 h
Monitoring time for rain alarm Disabled
1 s ... 12 h
Monitoring time for frost alarm Disabled
1 s ... 12 h
Priority of weather alarms
The global priorities for the weather alarms are dened here.
Extended
settings Global settings for roller shutter and blind
Priority of weather alarms Wind alarm->Rain alarm->Frost alarm
Wind alarm->Frost alarm->Rain alarm
Rain alarm->Wind alarm->Frost alarm
Rain alarm->Frost alarm->Wind alarm
Frost alarm->Rain alarm->Wind alarm
Frost alarm->Wind alarm->Rain alarm
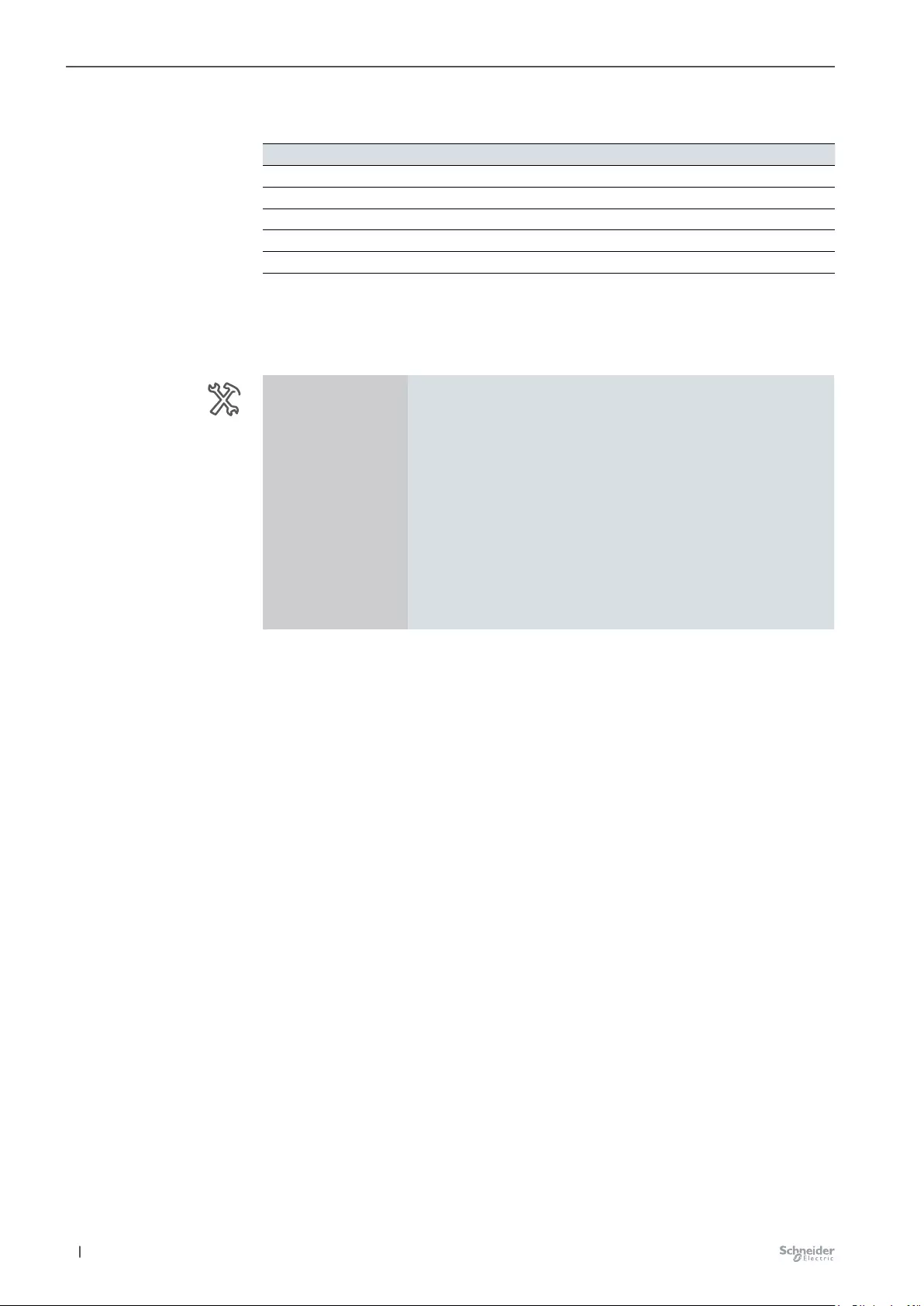
30 05/20-5800/1.0MTN6705-0008 | MTN6805-0008 |
Extended settings Switch Blind 5800/1.0
Group objects
No. Name Object function Length Behavior Data Type
18 Central Wind alarm 1 1 bit Received 1.005 Alarm
19 Central Wind alarm 2 1 bit Received 1.005 Alarm
20 Central Wind alarm 3 1 bit Received 1.005 Alarm
21 Central Rain alarm 1 bit Received 1.005 Alarm
22 Central Frost alarm 1 bit Received 1.005 Alarm
Priority of functions for roller shutter and blind
The global priorities for roller shutter and blind are dened here. The safety function
has the highest priority. The other priorities can be selected here.
Extended
settings Global settings for roller shutter and blind
Priority of functions Safety ->Alarm ->Weather alarms
->Lock ->All other
Safety ->Alarm ->Lock
->Weather alarms ->All other
Safety ->Weather alarms ->Alarm ->Lock
->All other
Safety ->Weather alarms ->Lock ->Alarm
->All other
Safety ->Lock ->Alarm
->Weather alarms ->All other
Safety ->Lock ->Weather alarms ->Alarm
->All other
Calibration
The device calculates the current position of a drive from the running times you
have set for the drive and from the control commands it executes. This calculation
must be performed because there is no feedback from the drive regarding its posi-
tion. Even if you have set the running times very precisely, the internally calculated
height position will deviate slightly from the actual height position after a number of
movements. This is due to mechanical tolerances and weather conditions (tem-
perature uctuations, frost, rain, etc.).
The device can reset these deviations by means of reference runs. For this pur-
pose, it moves the drives to the upper or lower end position. After the reference
run, the internal position calculation starts again from a xed value. Any deviations
that have arisen in the meantime are thus eliminated.
Note: The calibration function is especially important if you work a lot with position
commands and high positioning accuracy is required. If the drives are controlled
exclusively using the basic functions and position commands do not matter, then
you do not need this function.
Group object for
weather alarms
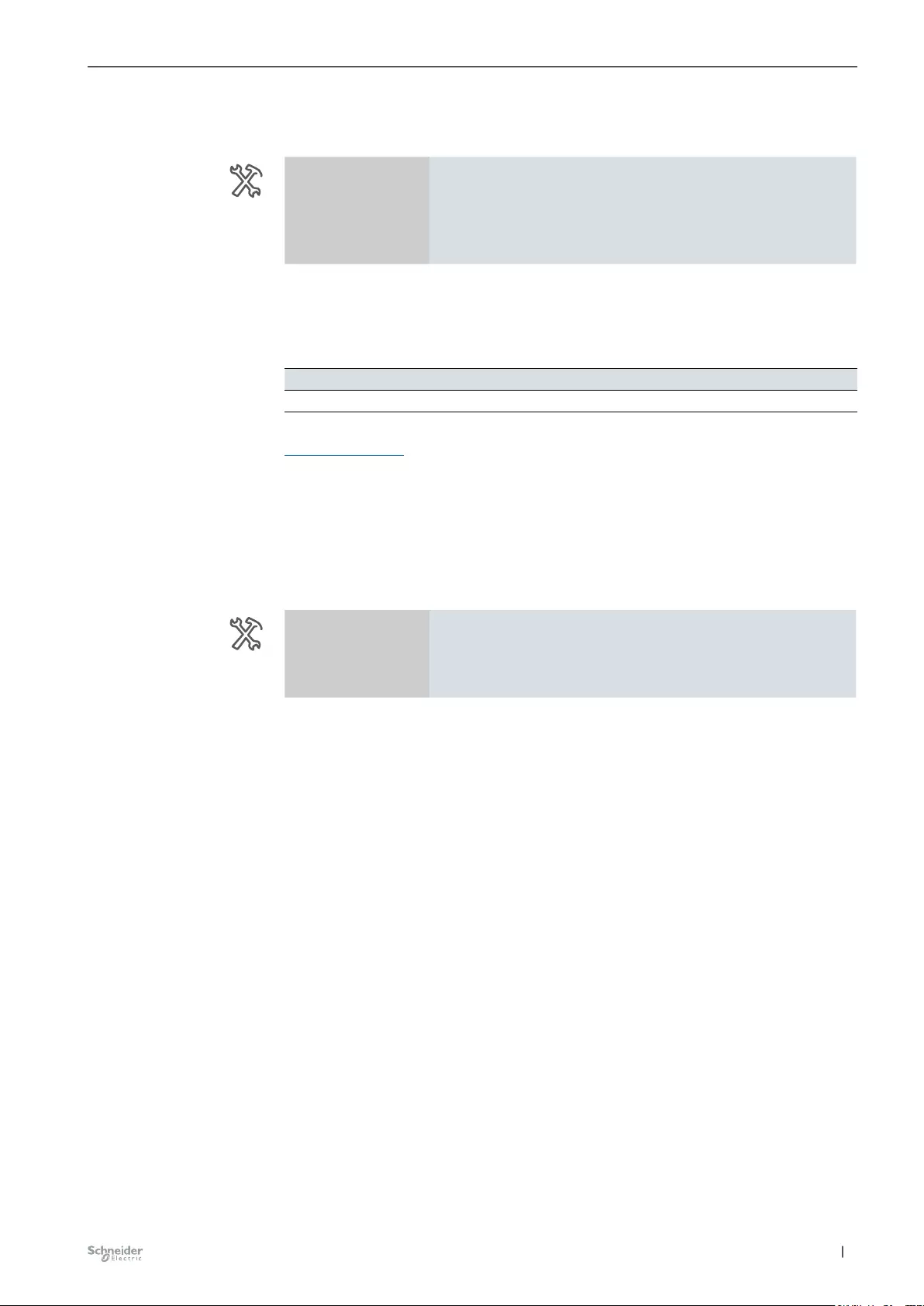
31
05/20-5800/1.0 MTN6705-0008 | MTN6805-0008 |
Extended settings Switch Blind 5800/1.0
The calibration function can be activated here in the ETS for all roller shutter/blind
channels.
Extended
settings Global settings for roller shutter and blind
Calibration Disabled
Enabled
A reference run can be triggered by a group object or after a certain number of
movements.
Group objects
No. Name Object function Length Behavior Data Type
17 Central Calibration 1 bit Received 1.010 Start/Stop
The channel-specic settings for the calibrating function can be found in the:
Calibration --> 98
4.10 PIN Code for Firmware Update
For security reasons, you must set a valid 4-digit PIN code to block unauthorized
updates of the device rmware. The PIN code dened in the ETS must be entered
in the Schneider-Electric Firmware Update Tool before downloading the rmware.
This prevents unauthorized rmware update of the device via the USB interface.
Extended
settings PIN Code for Firmware Update
Please enter PIN Code for
Firmware Update
(4 digits, 0 ... 9)
1234
PIN codes that are insecure or too simple cannot be selected.
You will receive the following message:
No valid PIN Code for Firmware Update! Please enter a valid PIN Code before you
download your conguration!
Group object for
calibration
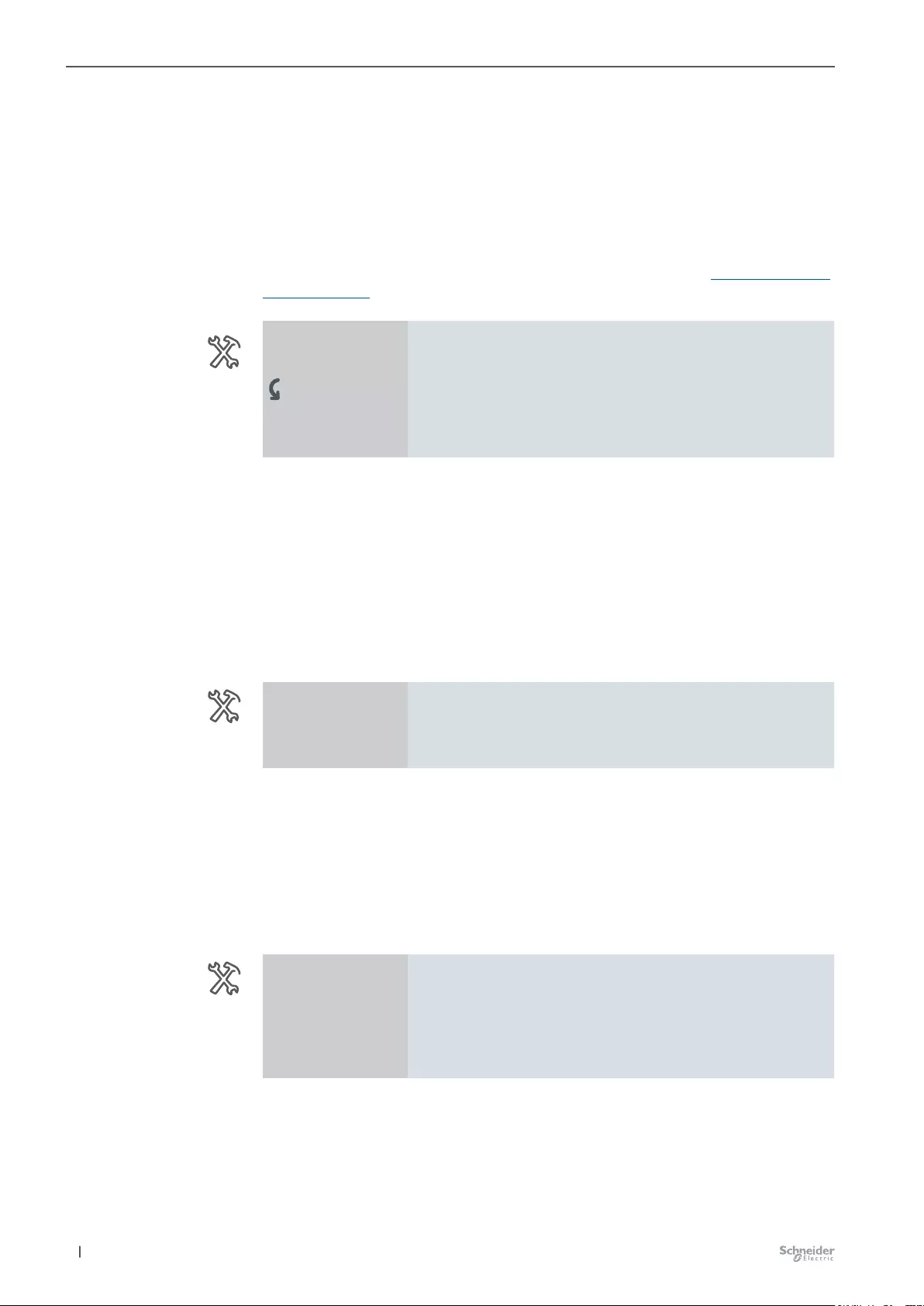
32 05/20-5800/1.0MTN6705-0008 | MTN6805-0008 |
Express settings for switching Switch Blind 5800/1.0
5 Express settings for switch-
ing
On the Express settings for switching tab, dene basic settings and activate or
deactivate other functions.
To switch electrical loads, you can set the channel function of the device to Switch-
ing mode. The operating mode is selected for each output on the Dening channel
functions --> 16 tab:
General
settings
Channel function Master /
Extension 1 / Extension 2
Output 1-8 Switching
Master/Ext. 1/2
Output 1-8 -Switch
-Switching
Express settings for switching ...
5.1 Name of the channel for switching
You can assign a separate name for each channel, e.g. "Light Hall Ground Floor".
This individual name is appended to the xed channel name, e.g. "Master Output 1
- Switch". The full name of the channel is then, e.g. "Master Output 1 - Switch Light
Hall Ground Floor".
The name of the channel now appears on the parameters, channels and associ-
ated group objects.
Master/Ext. 1/2
Output 1-8 -Switch
-Switching
Express settings for switching
Name of the channel Light Hall Ground Floor
5.2 Switching mode
Switching
You can choose between the switching modes Switching and Blinking. In Switching
mode, the relay opens and closes depending on the KNX telegram and the setting
for the contact mode.
Master/Ext. 1/2
Output 1-8 -Switch
-Switching
Express settings for switching
Switching mode Switching
Blinking
Contact mode Normally opened
Normally closed
The settings for Output 1 are described below, but apply equally to all outputs.
If you select switching mode Switching for output 1 on the master, an ETS channel
with the name Master Output 1 - Switch +Name of the channel will be created. All
the group objects for this output are located here.
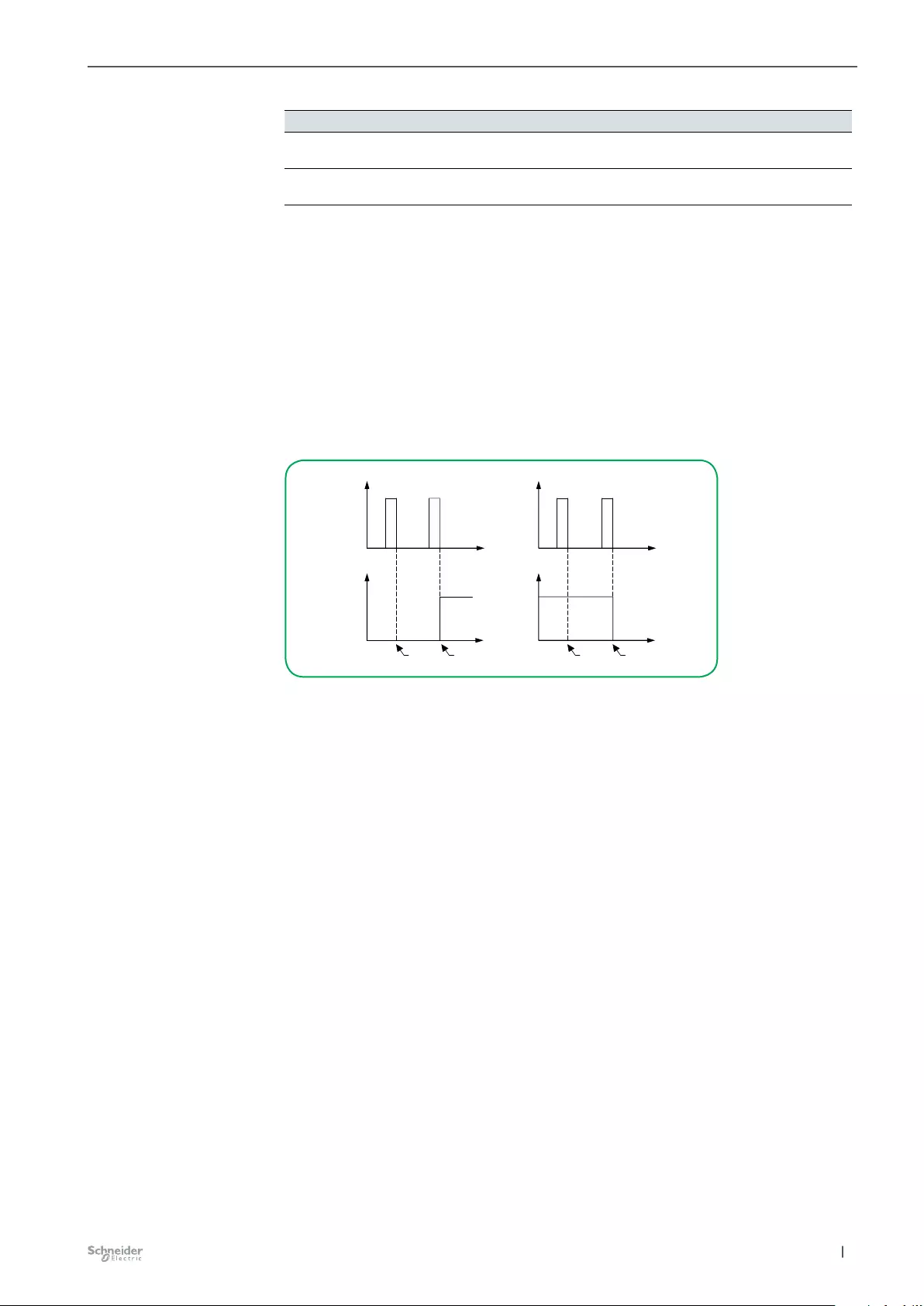
33
05/20-5800/1.0 MTN6705-0008 | MTN6805-0008 |
Express settings for switching Switch Blind 5800/1.0
No. Name Object function Length Behavior Data Type
31 Master Output 1 &
(name of the channel)
Switching 1 bit Received 1.001 Switching
37 Master Output 1 &
(name of the channel)
Status feedback 1 bit Sending 1.001 Switching
Contact mode normally opened
If the switch object receives a telegram with the value "0", the contact is opened. If
a telegram value of "1" is received, the contact is closed.
The settings "Pressed" and "Released" are used for the dierent switching states of
the output contacts.
In relay mode "Normally opened":
•Pressed = contact closed
•Released = contact opened
Switching ("Normally opened" mode)
Open
t
t
10
Remains
Open
Becomes
Closed
KNX
telegram
Relay status
Closed
Relay status
Closed
t
Remains
Closed
Becomes
Opened
Open
t
10
KNX
telegram
Switch on Switch off
Status response
Depending on the parameterization, each channel can return a status response.
The following parameter settings are available for this:
Normal behavior (Pressed = 1; Released = 0)
Inverted (Pressed = 0; Released = 1)
Contact mode normally closed
If the switch object receives a telegram with the value "0", the contact is closed. If a
telegram value of "1" is received, the contact is opened.
The settings "Pressed" and "Released" are used for the dierent switching states of
the output contacts.
In relay mode "Normally closed":
•Pressed = contact opened
•Released = contact closed
Group objects for “Switching”
express setting
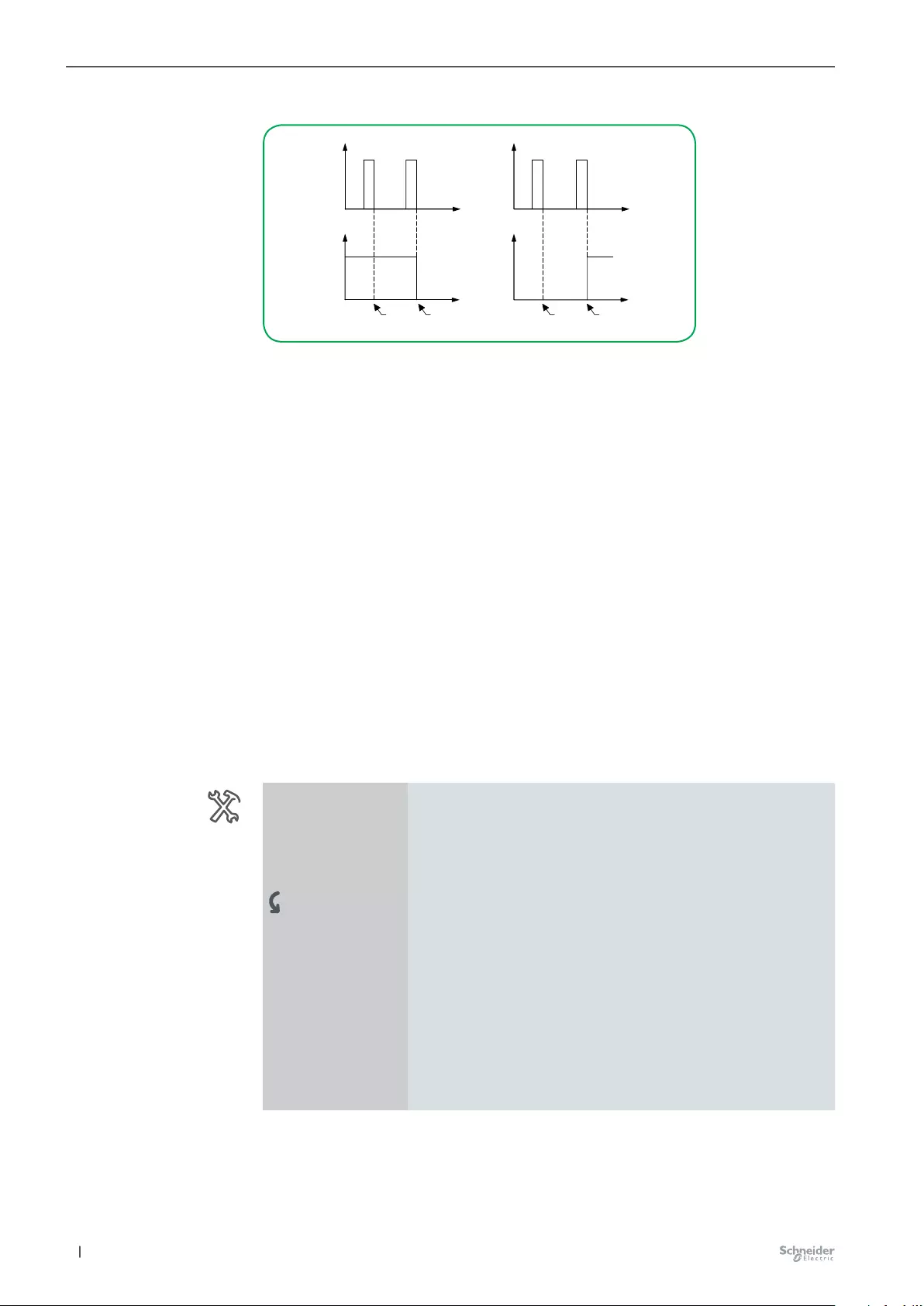
34 05/20-5800/1.0MTN6705-0008 | MTN6805-0008 |
Express settings for switching Switch Blind 5800/1.0
Switching ("Normally closed" mode)
Open
t
t
10
RemainsBecomes
Closed
KNX
telegram
Relay status
Closed
Relay status
Closed
t
RemainsBecomes
Open
t
10
KNX
telegram
ClosedOpenedOpen
Switch on Switch off
Status response
Depending on the parameterization, each channel can return a status response.
The following parameter settings are available for this:
Normal behavior (Pressed = 1; Released = 0)
Inverted (Pressed = 0; Released = 1)
Blinking
The switching mode Blinking alternately opens and closes the relay. You can dene
the blinking behavior for each channel. The blinking speed is dened using the
parameter Blinking interval. The blinking cycle starts with a closed relay. Further-
more, you can set the ratio between closed and open relay during a blinking time
in 3 steps. You can reduce the blinking intervals to a dened number to protect the
relay. Additionally, you can specify the state to which the relay will be switched after
the dened number of blinking intervals.
Important
Short switching times must not be parameterized under load (see technical data of
the switching output).
Master/Ext. 1/2
Output 1-8 -Switch
-Switching
Express settings for
switching
Switching mode Blinking
Behavior at pressed/re-
leased
Blinking / relay opened
Blinking / relay closed
Relay opened / blinking
Relay closed / blinking
Blinking interval 5 s
(5 s - 60 s)
Proportion open/closed
Equal (50/50%)
Short open / long closed (20/80%)
Long open / short closed (80/20%)
Dened number of blinking
intervals (0...255, 0 = per-
manent blinking)
20
Behavior after dened num-
ber of blinking intervals
Relay is closed
Relay is opened
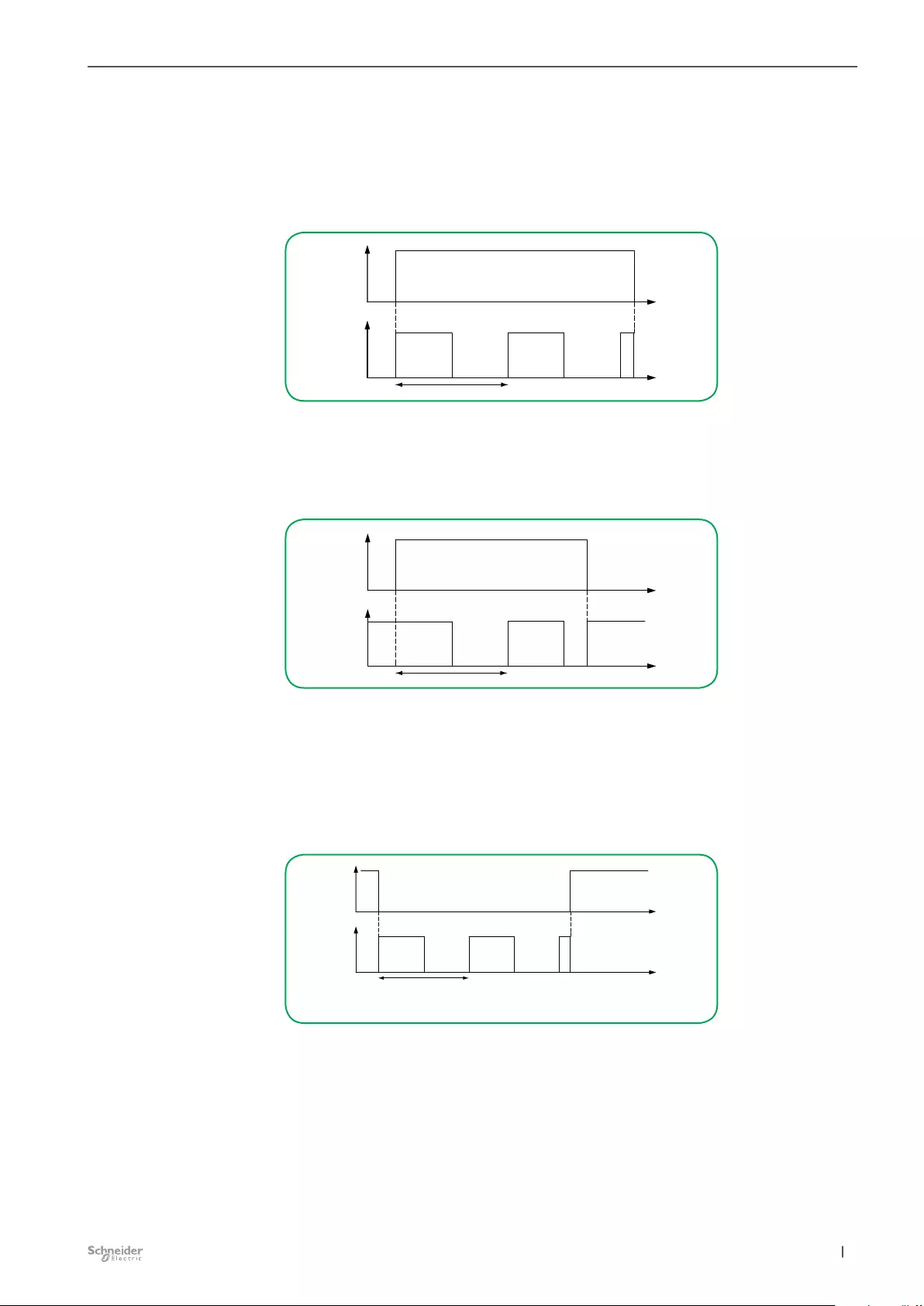
35
05/20-5800/1.0 MTN6705-0008 | MTN6805-0008 |
Express settings for switching Switch Blind 5800/1.0
Behavior at pressed/released
•Blinking / relay opened
With pressed (telegram value "1"), the relay starts blinking. With released (telegram
value "0" during blinking), the relay stops blinking and the relay is opened.
Blinking / relay opened
Open
Closed
Relay
State
Actuated
Not actuated
Flashing interval
•Blinking / relay closed
With pressed (telegram value "1"), the relay starts blinking. With released (telegram
value "0" during blinking), the relay stops blinking and the relay is closed.
Blinking / relay closed
Open
Closed
Relay
State
Actuated
Not actuated
Flashing interval
•Relay opened / blinking
With pressed (telegram value "1"), the relay stops blinking and the relay is opened.
With released (telegram value "0" during blinking), the relay starts blinking.
The blinking cycle starts with a closed relay immediately after the download. Fol-
lowing the download, the switch object is released.
Relay closed / blinking
Open
Closed
Relay
State
Actuated
Not actuated
Flashing interval
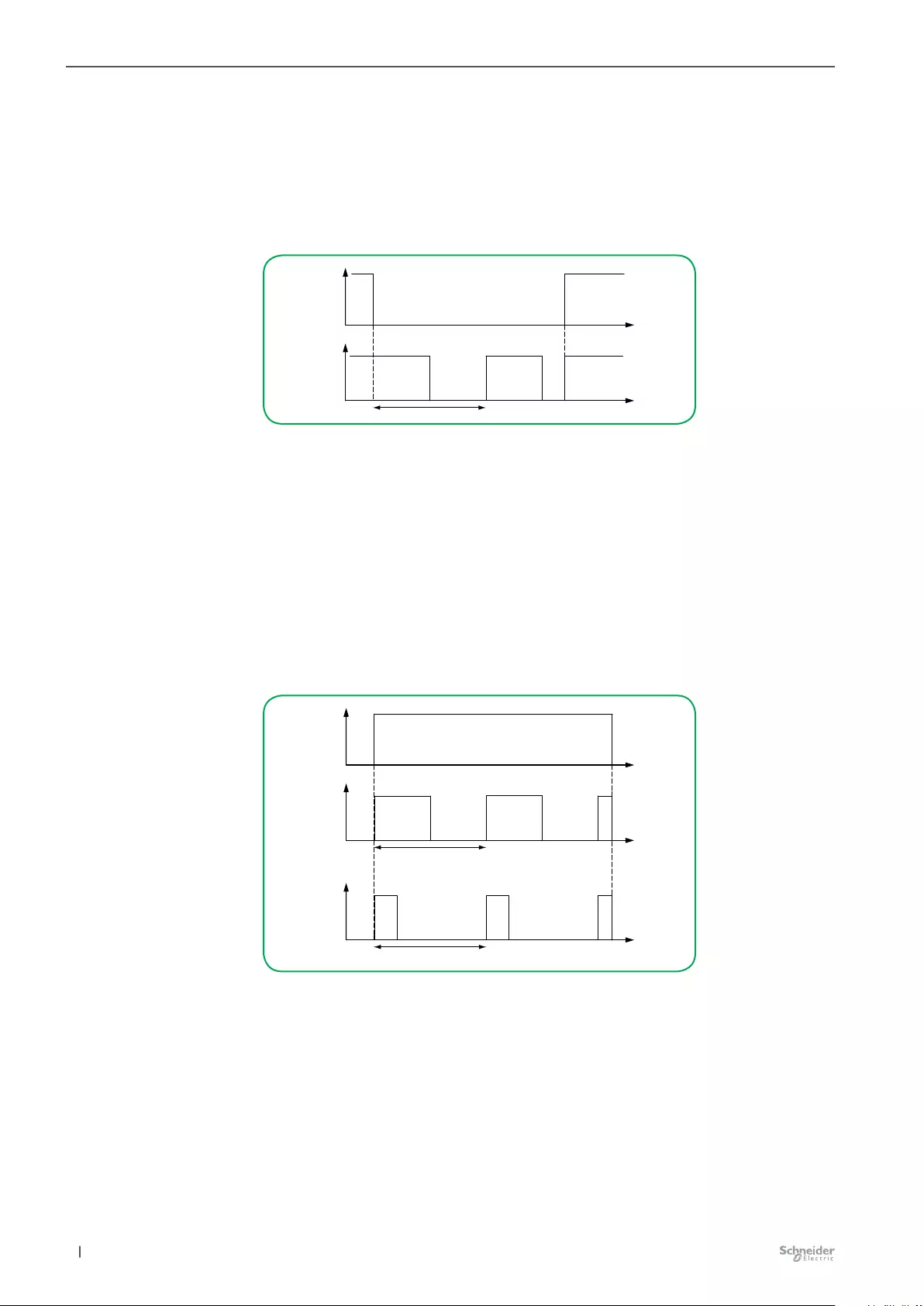
36 05/20-5800/1.0MTN6705-0008 | MTN6805-0008 |
Express settings for switching Switch Blind 5800/1.0
•Relay closed / blinking
With pressed (telegram value "1"), the relay stops blinking and the relay is closed.
With released (telegram value "0" during blinking), the relay starts blinking.
The blinking cycle starts with a closed relay immediately after the download. Fol-
lowing the download, the switch object is released.
Relay closed / blinking
Open
Closed
Relay
State
Actuated
Not actuated
Flashing interval
Blinking interval
The blinking speed is set here. A blinking interval (on / o) can be set between 5
and 60 seconds.
Proportion open/closed
You can parameterize the ratio between closed and open relay during a blinking
time. You can select whether the relay is to be open/closed equally (Equal) during a
blinking interval (50% / 50%) or short open / long closed (20% / 80%) or long open
/ short closed (80% / 20%).
Proportion open/closed
Open
Closed
Relay
State
Actuated
Not actuated
Flashing interval
50%50%
Open
Closed
Relay
Flashing interval
80%20%
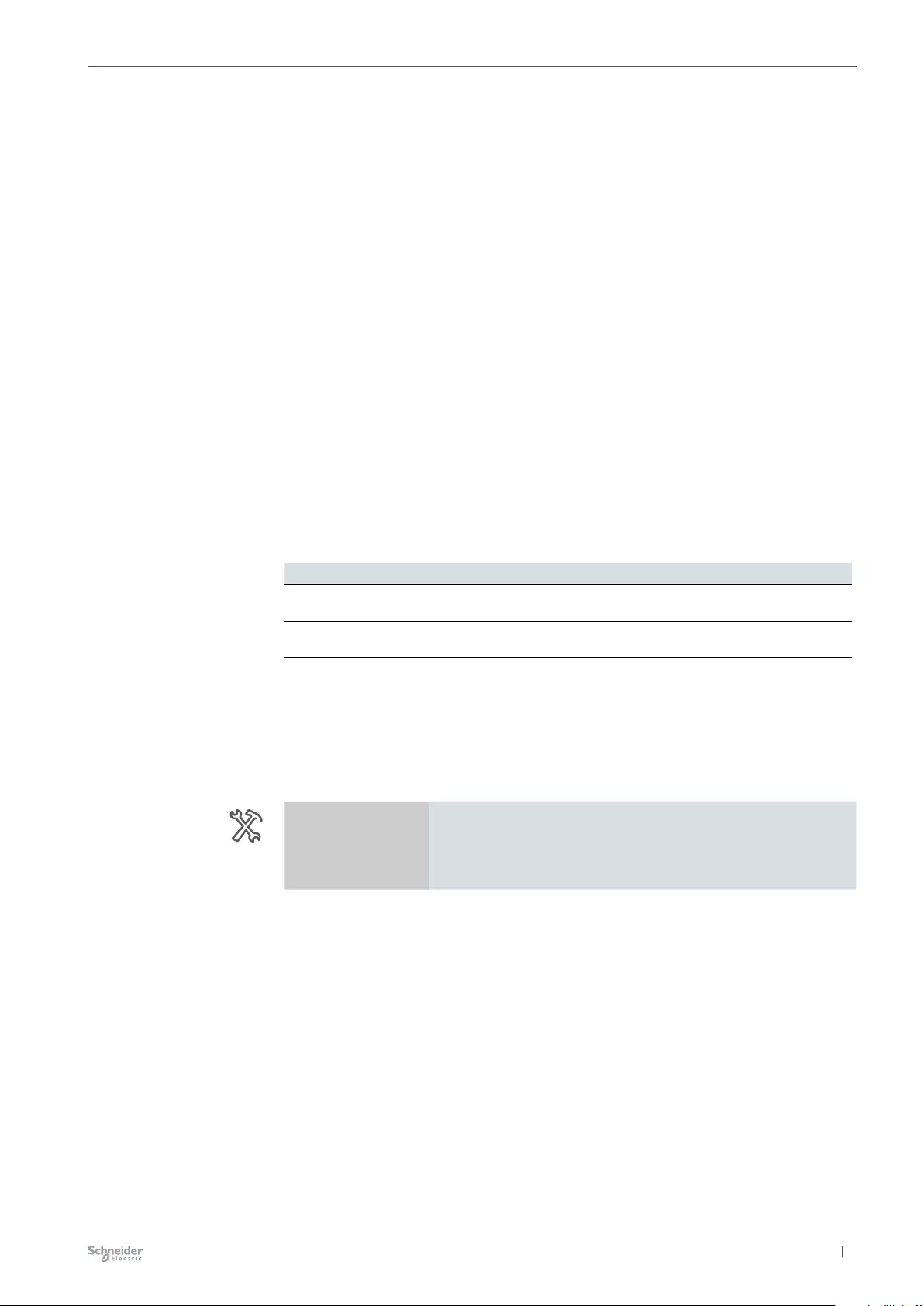
37
05/20-5800/1.0 MTN6705-0008 | MTN6805-0008 |
Express settings for switching Switch Blind 5800/1.0
Defined number of blinking intervals
You can reduce the blinking intervals to a dened number (0...255) to protect the
relay. With "0", the number of blinking intervals is unlimited, so the relay blinks
permanently.
Behavior after defined number of blinking intervals
You can specify the state to which the relay will be switched after the dened num-
ber of blinking intervals. Either Relay is closed or Relay is opened.
Status response
Depending on the parameterization, each channel can return a status response.
The following parameter settings are available for this:
Normal behavior (Pressed = 1; Released = 0)
Inverted (Pressed = 0; Released = 1)
Note:
At the beginning of the blinking interval, a one-o "1" signal is sent as feedback to
the bus. After the end of the blinking interval, a one-o "0" telegram is sent to the
bus. Or inverted.
No. Name Object function Length Behavior Data Type
31 Master Output 1 &
(name of the channel)
Switching 1 bit Received 1.001 Switching
37 Master Output 1 &
(name of the channel)
Status feedback 1 bit Sending 1.001 Switching
5.3 Contact mode
Normally opened
The settings for Output 1 are described below, but apply equally to all outputs.
Master/Ext. 1/2
Output 1-8 -Switch
-Switching
Express settings for switching
Contact mode Normally opened
Normally closed
If the switch object receives a telegram with the value "0", the contact is opened. If
a telegram value of "1" is received, the contact is closed.
The settings "Pressed" and "Released" are used for the dierent switching states of
the output contacts.
In relay mode "Normally opened":
•Pressed = contact closed
•Released = contact opened
Group objects for “Switching”
express setting
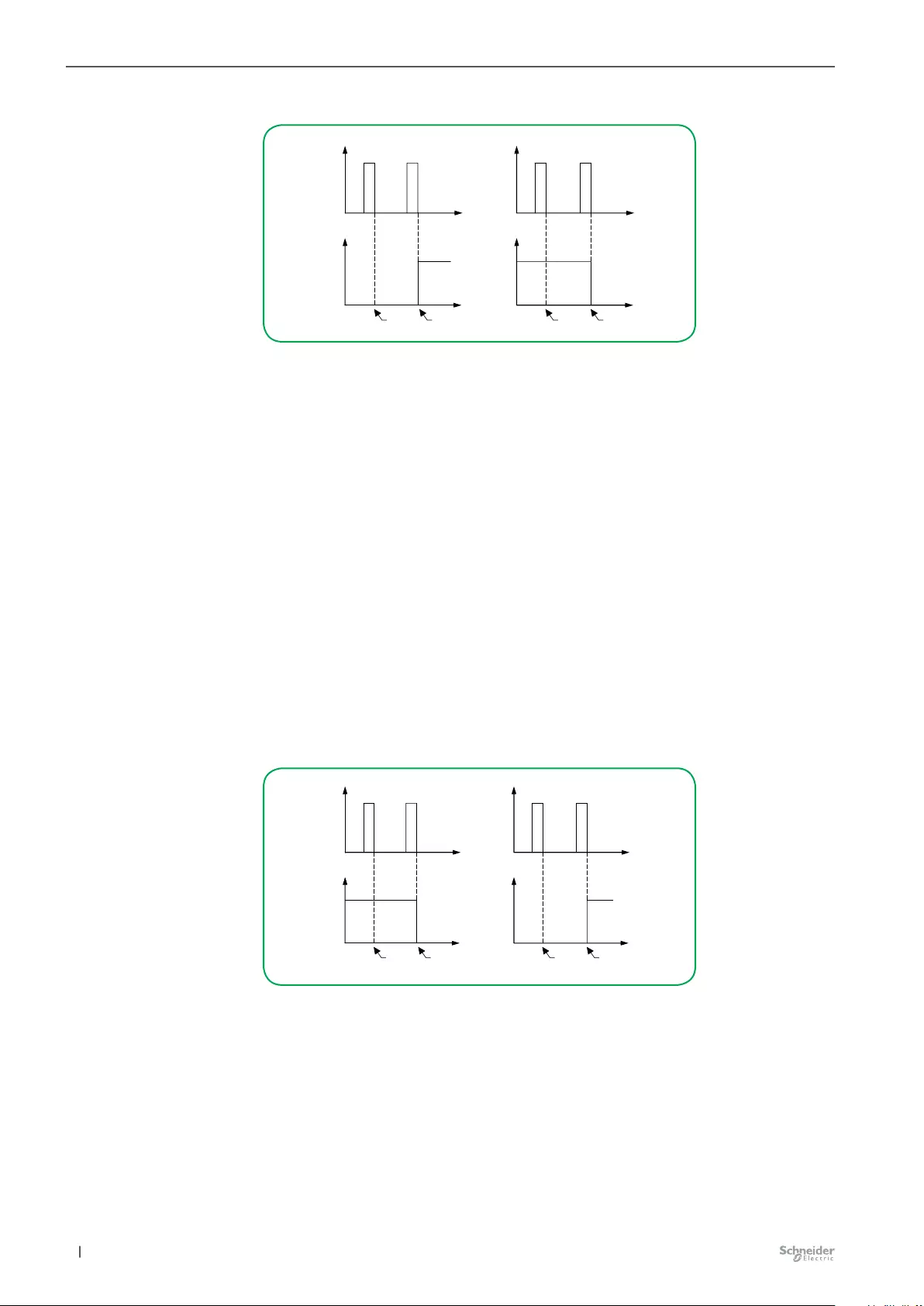
38 05/20-5800/1.0MTN6705-0008 | MTN6805-0008 |
Express settings for switching Switch Blind 5800/1.0
Switching ("Normally opened" mode)
Open
t
t
10
Remains
Open
Becomes
Closed
KNX
telegram
Relay status
Closed
Relay status
Closed
t
Remains
Closed
Becomes
Opened
Open
t
10
KNX
telegram
Switch on Switch off
Status response
Depending on the parameterization, each channel can return a status response.
The following parameter settings are available for this:
Normal behavior (Pressed = 1; Released = 0)
Inverted (Pressed = 0; Released = 1)
Normally closed
If the switch object receives a telegram with the value "0", the contact is closed. If a
telegram value of "1" is received, the contact is opened.
The settings "Pressed" and "Released" are used for the dierent switching states of
the output contacts.
In relay mode "Normally closed":
•Pressed = contact opened
•Released = contact closed
Switching ("Normally closed" mode)
Open
t
t
10
RemainsBecomes
Closed
KNX
telegram
Relay status
Closed
Relay status
Closed
t
RemainsBecomes
Open
t
10
KNX
telegram
ClosedOpenedOpen
Switch on Switch off
Status response
Depending on the parameterization, each channel can return a status response.
The following parameter settings are available for this:
Normal behavior (Pressed = 1; Released = 0)
Inverted (Pressed = 0; Released = 1)
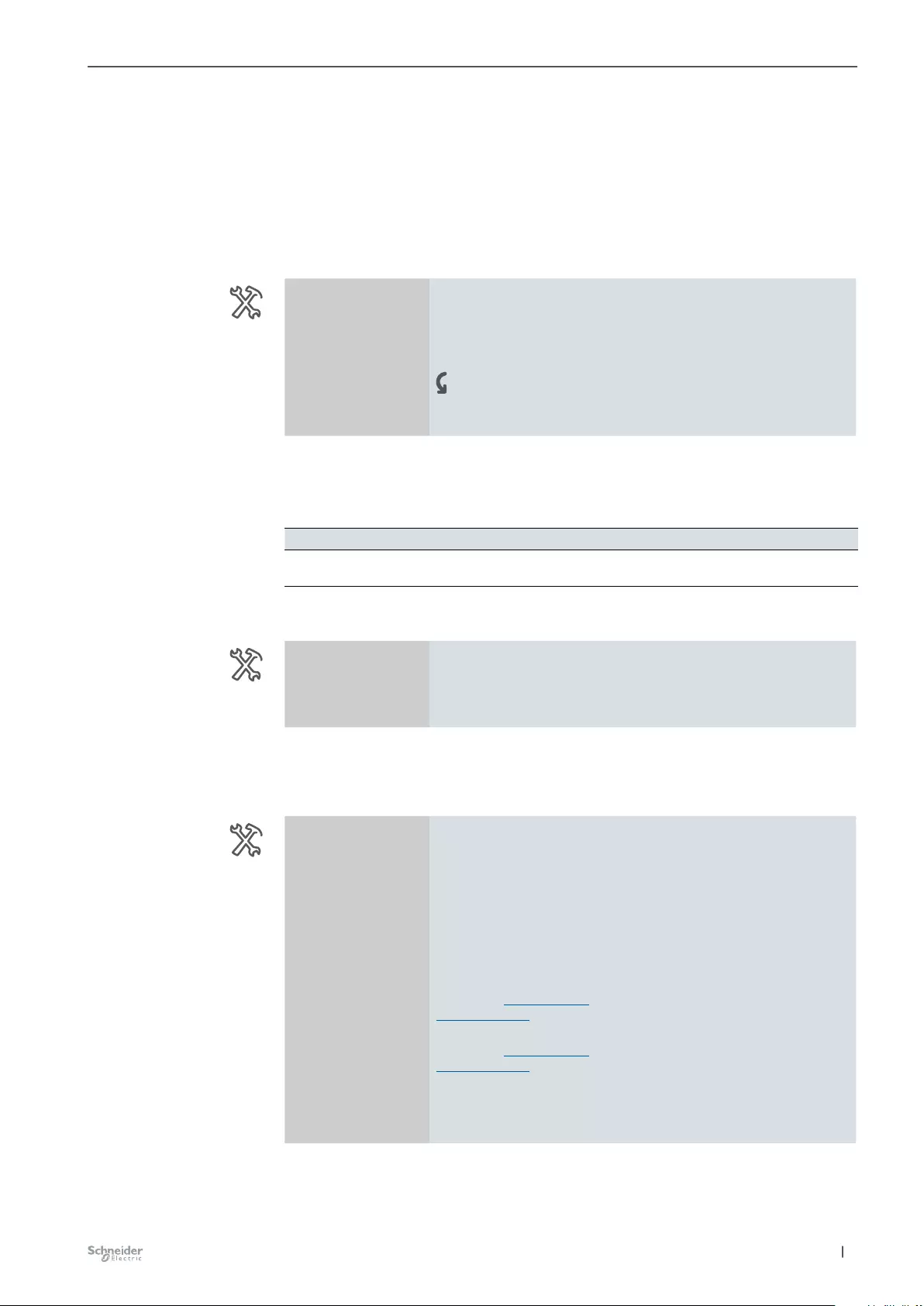
39
05/20-5800/1.0 MTN6705-0008 | MTN6805-0008 |
Express settings for switching Switch Blind 5800/1.0
5.4 Scenes
If you want to change multiple room functions simultaneously at the press of a
button or with a command, you can do so using the scene function. You can use a
scene, for example, to switch on the room lighting, set the heating control to day-
time operation and turn on the power supply for the sockets of a room.
Enable scenes
Master/Ext. 1/2
Output 1-8 -Switch
-Switching
Express settings for switching
Scenes Disabled
Enabled
-Scenes settings Scene settings
Following enabling of the scenes, the group object appears.
Group objects
No. Name Object function Length Behavior Data Type
36 Master Output 1 &
(name of the channel)
Scene 1 byte Received 18.001 Scene
control
Number of scenes
Master/Ext. 1/2
Output 1-8 -Switch
-Switching
Scene settings
-Scenes settings Required number of scenes 1 (1-16)
You can use the scene function to include multiple channels in a scene control. Up
to 16 dierent scenes are available for each output channel.
Each of the up to 16 scenes can be disabled again.
Master/Ext. 1/2
Output 1-8 -Switch
-Switching
Scene settings
-Scenes settings Scene 1 (1-16) Disabled
Enabled
Scene 1 Description
Scene 1 Address (0-63)
Dependent: Global settings
for scenes --> 24
Scene address 0 - 63
Scene 1 Address (1-64)
Dependent: Global settings
for scenes --> 24
Scene address 1 - 64
Scene 1 switching state Released
Pressed
For clarity, a short description can be stored for each scene.
Group object for
scene
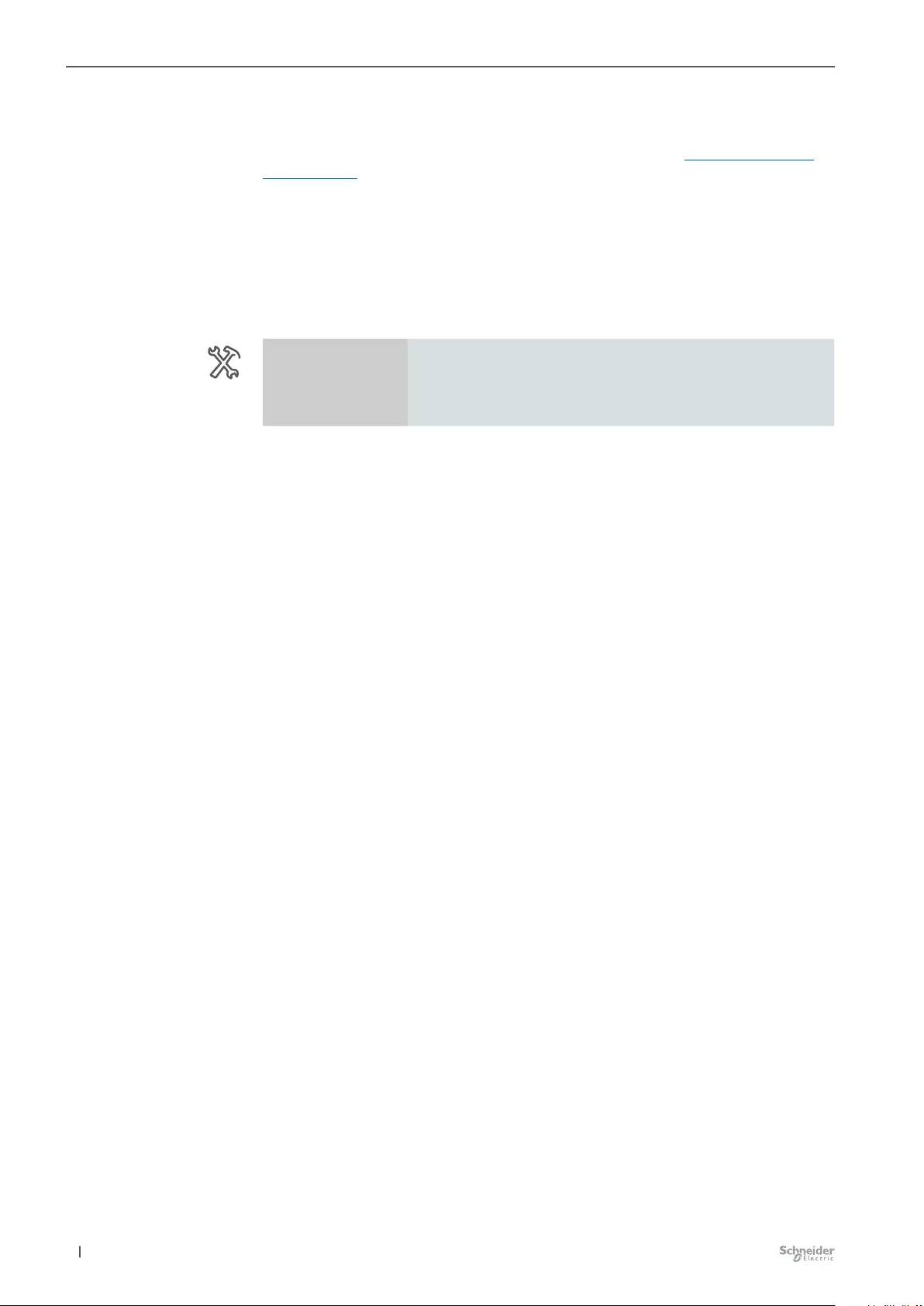
40 05/20-5800/1.0MTN6705-0008 | MTN6805-0008 |
Express settings for switching Switch Blind 5800/1.0
Each of these scenes can be assigned one of 64 possible scene addresses 0 to
63 (corresponding to telegram values 0-63) or 1 to 64 (corresponding to telegram
values 0-63). This depends on the global settings for scenes. Global settings for
scenes --> 24
You can store the switching states (pressed, released) as scene values for each
output channel.
Time delay for scene processing
To avoid high power-on currents when switching to a complex scene, you can pa-
rameterize a time delay for each output channel.
Master/Ext. 1/2
Output 1-8 -Switch
-Switching
Scene settings
-Scenes settings Time delay for scene process-
ing (0...255, unit = 100 ms) 0
Calling and saving scene values
The scene values for the output relays are called using the "Scene object" object.
After receiving a scene telegram, the device evaluates the sent scene address and
switches the outputs to the saved scene values.
If the "scene object" receives a scene telegram with learning bit "1", then for all
scenes assigned to the received scene address, the current switching state is
saved as the new scene value.
Note: If a scene address within a channel is assigned to multiple scenes (incorrect
parameterization), only the last scene found with this scene address is called or
saved. You can avoid this by assigning dierent scene addresses within a channel.
Telegram format
Telegrams for the scene function have the data format: L X D D D D D D.
L = learning bit
X = not used
DDDDDD = called scene address
If the learning bit in a telegram has the value "0", then the relay states saved for the
scene address are called and set.
If the learning bit receives the value "1", then the current output states are saved as
new scene values for the received scene address.
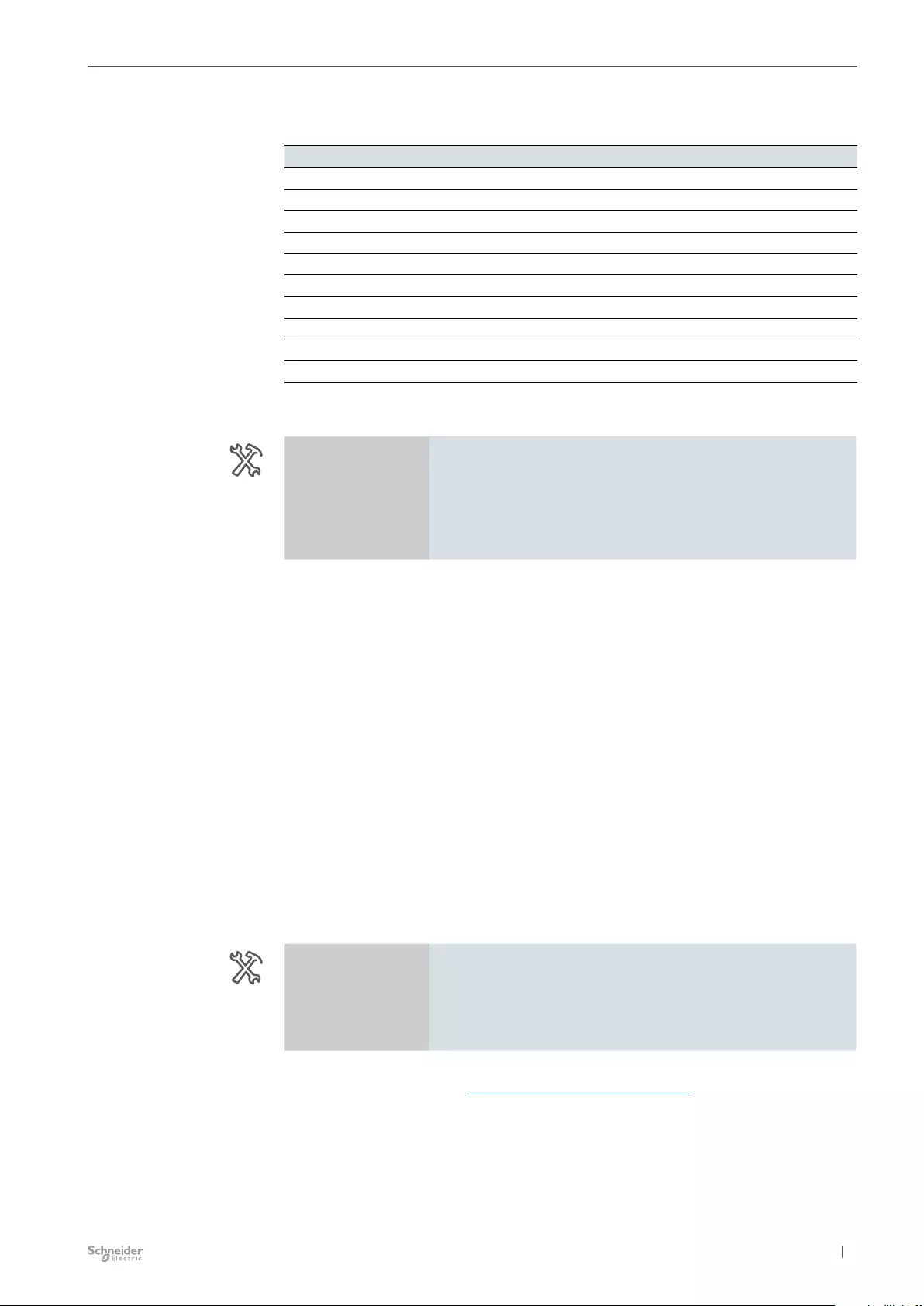
41
05/20-5800/1.0 MTN6705-0008 | MTN6805-0008 |
Express settings for switching Switch Blind 5800/1.0
Examples:
Telegram value Binary Hexadecimal Scene address
0 0000 0000 0 Call scene address 0
1 0000 0001 1 Call scene address 1
29 0001 1101 1D Call scene address 29
57 0011 1001 39 Call scene address 57
63 0011 1111 3F Call scene address 63
128 1000 0001 80 Learning scene address 0
129 1000 0001 81 Learning scene address 1 (129-128)
157 1001 1101 9D Learning scene address 29 (157-128)
185 1011 1001 B9 Learning scene address 57 (185-128)
191 1011 1111 BF Learning scene address 63 (191-128)
Overwrite scene values during download
Master/Ext. 1/2
Output 1-8 -Switch
-Switching
Scene settings
-Scenes settings Overwrite scene values of
actuator during download Disabled
Enabled
If you have enabled the parameter "Overwrite scene values in actuator during
download", the scene values saved in the device will be overwritten with your pre-
set values on downloading. If you do not want to overwrite the values in the device
when downloading, you must disable the parameter. In this case, the parameter-
ized scene values are only written to the device memory during the rst download.
If an application download is then carried out, the scene values in the device mem-
ory are retained.
Priority
The scene function has the same priority as the normal switching function via the
"switch object". This should be taken into account with regard to the priority of the
higher-level functions.
5.5 Central function switching
Enabling a central function for switching output
The central function is enabled or disabled here for each switch output.
Master/Ext. 1/2
Output 1-8 -Switch
-Switching
Express settings for switching
Central function Enabled
Disabled
The global settings and explanations of the central function can be found in the
chapter General settings. (Enabling central functions --> 19)
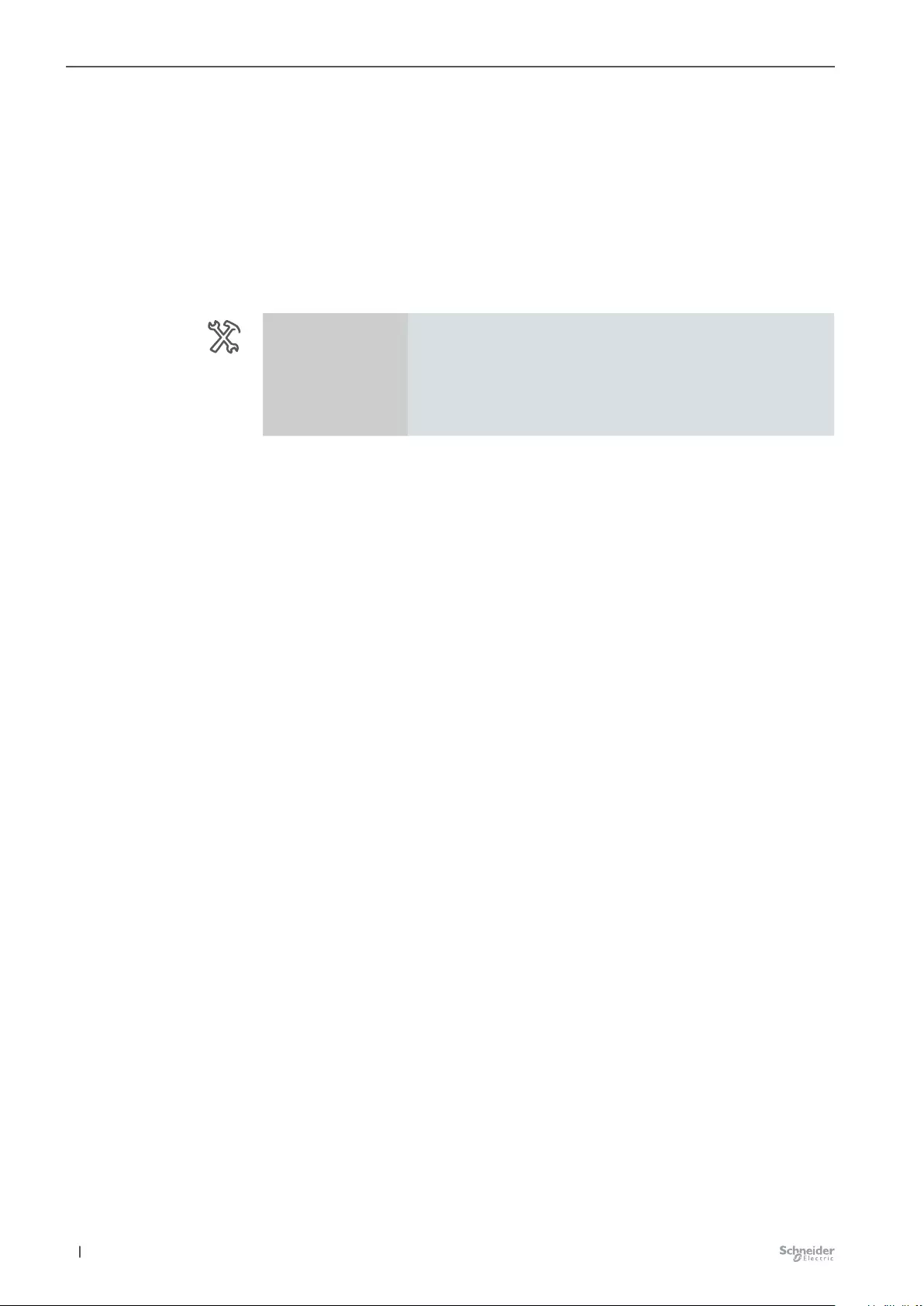
42 05/20-5800/1.0MTN6705-0008 | MTN6805-0008 |
Express settings for switching Switch Blind 5800/1.0
5.6 Status response
Depending on the parameterization, each channel can return a status response.
The following parameter settings are available for this:
Normal behavior (Pressed = 1; Released = 0)
Inverted (Pressed = 0; Released = 1)
5.7 Activating extended settings for switching
Master/Ext. 1/2
Output 1-8 -Switch
-Switching
Express settings for switching
Extended settings for switch-
ing No
Yes
To activate the advanced settings for switching, you must enable them here.
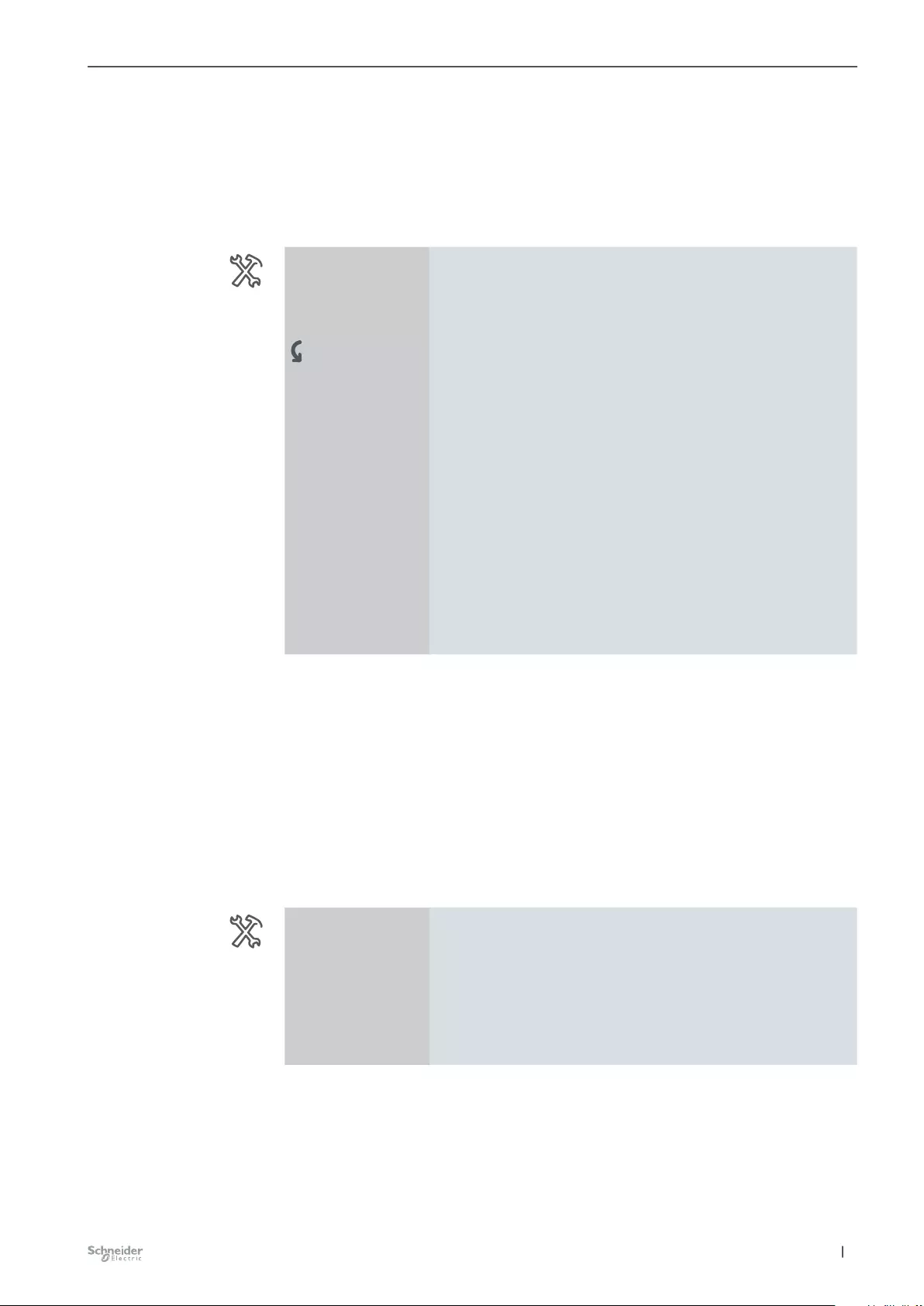
43
05/20-5800/1.0 MTN6705-0008 | MTN6805-0008 |
Extended settings for switching Switch Blind 5800/1.0
6 Extended settings for
switching
On the Express settings for switching tab, activate the Extended settings for switch-
ing.
Master/Ext. 1/2
Output 1-8 -Switch
-Switching
Express settings for switching
Extended settings for switching No
Yes
-Time settings Staircase lighting time
On-delay time
O-delay time
-Logic, Locking & Prior-
ity settings Priority function
Logic function
-Safety and alarm
settings Safety function
Alarm function
Failure and download behavior
6.1 Time settings
Staircase lighting time function (staircase timer)
This function is used to switch on an appliance, e.g. the light in a staircase, via a
bus telegram and automatically switch it o again after a set duration. Therefore,
no manually or automatically generated bus telegram is required for switching o.
The actuator carries out the switching o operation independently and under time
control.
Two types of staircase lighting time function are available:
Master/Ext. 1/2
Output 1-8 -Switch
-Switching
Staircase lighting time
-Time settings Staircase lighting time Disabled
Fix
Variable
Following enabling of the corresponding staircase lighting time function, the rele-
vant group object appears.
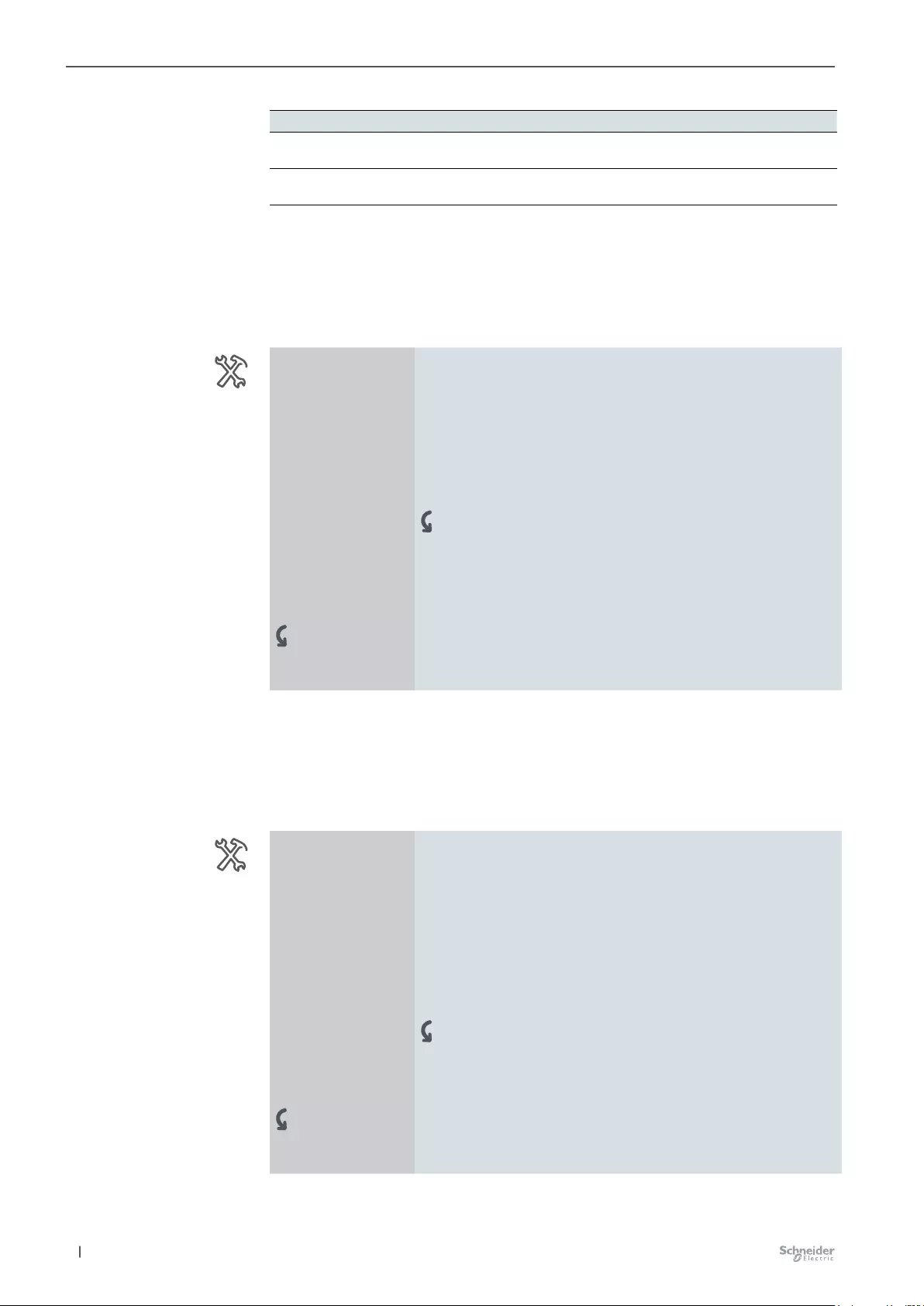
44 05/20-5800/1.0MTN6705-0008 | MTN6805-0008 |
Extended settings for switching Switch Blind 5800/1.0
No. Name Object function Length Behavior Data Type
35 Master Output 1 &
(name of the channel)
Staircase x 1 bit Received 1.010 Start/Stop
35 Master Output 1 &
(name of the channel)
Staircase vari-
able
2 bytes Received 7.005 Time (s)
Staircase lighting time fix
With Staircase lighting time x, you can parameterize a xed staircase lighting
time for each channel. The staircase lighting time can be parameterized between 5
seconds and 1 hour. This function makes the Staircase x object (1 bit) available to
you.
Master/Ext. 1/2
Output 1-8 -Switch
-Switching
Staircase lighting time x
-Time settings Manual switching o Active
Not active
Time extension Not retriggerable
Retriggerable
Retriggerable and adding
Max. number of additions 2 (2 - 5)
Duration time 2 min (5 s - 1 h)
Number of prewarnings 0 (0 - 5)
Warning starts (5...255, unit = 1s)
before end 20 (5 - 255)
Hint: Staircase duration time must be longer or equal than prewarning
start time.
Staircase lighting time variable
With Staircase lighting time variable, a time between 0 s and 65 535 s is dened
via the object Staircase variable (2 bytes DPT 7.005 time (s)), e.g. using a button.
This enables you to specify the length of the staircase lighting time from dierent
places depending on the desired situation.
Master/Ext. 1/2
Output 1-8 -Switch
-Switching
Staircase lighting time variable
-Time settings Manual switching o Active
Not active
Time extension Not retriggerable
Retriggerable
Retriggerable to the higher value
Retriggerable and adding
Max. number of additions 2 (2-5)
Number of prewarnings 0 (0-5)
Warning starts (5...255, unit = 1s)
before end 20 (5-255)
Hint: Staircase duration time must be longer or equal than prewarning
start time.
Group objects of staircase
lighting time
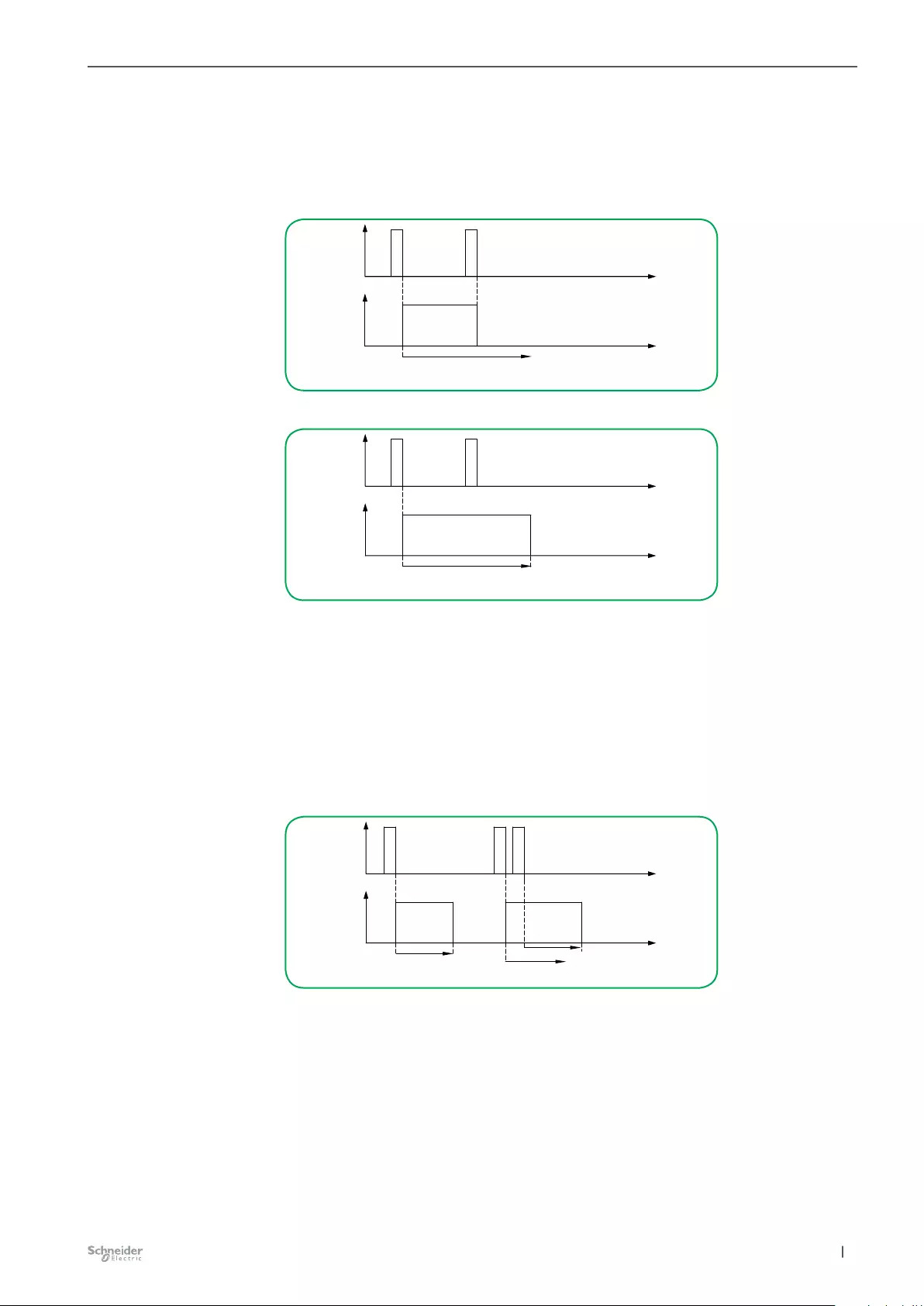
45
05/20-5800/1.0 MTN6705-0008 | MTN6805-0008 |
Extended settings for switching Switch Blind 5800/1.0
Manual switching off
Both staircase lighting time functions enable you to switch o the staircase lighting
time prematurely. After receiving the object value 0, the output is switched to the
released position.
Manual switching o = Active ("0" telegram)
t
t
10
t staircase
KNX
telegram
State
Actuated
Not actuated
Manual switching o = Not active ("0" telegram)
t
t
10
t staircase
KNX
telegram
State
Actuated
Not actuated
A telegram with the object value 0 has no eect. The set staircase light time contin-
ues to run normally until the end.
Time extension
If you want to restart the staircase lighting time before it has elapsed or add up the
staircase lighting time, you must select the staircase lighting time Retriggerable or
Retriggerable and adding or Retriggerable to the higher value. The staircase light-
ing time is then restarted or added using another "1" telegram.
Time extension = Retriggerable
t
t
111
t staircase
t staircase
t staircase
KNX
telegram
State
Actuated
Not actuated
Once a new telegram with the object value "1" has been received, the staircase
lighting time is restarted.

46 05/20-5800/1.0MTN6705-0008 | MTN6805-0008 |
Extended settings for switching Switch Blind 5800/1.0
Time extension = Retriggerable and adding
t
t
111
t staircase
KNX
telegram
State
Actuated
Not actuated
t staircase t staircase
++
1
Max.
5 x
Once one or more new telegrams with the object value "1" have been received, the
staircase lighting time is added to the previous staircase lighting time. The number
of additions can be set. You can parameterize a maximum of 5 additions of the
staircase lighting time. For example, you can add up the staircase lighting time by
pressing a separate button several times.
Time extension = Retriggerable to the higher value
(only for staircase lighting time = variable)
t
t
Value
t staircase = 200 s
t staircase = 100 s
t staircase = 100 s
KNX
telegram
State
Actuated
Not actuated
Value
Value
t staircase = 50 s
Value
t = 20 s
Once a new telegram has been received, the staircase lighting time is restarted
with the higher value.
Time extension = Not retriggerable
t
t
111
t staircase
t staircase
t staircase
KNX
telegram
State
Actuated
Not actuated
However, if the staircase lighting time is not retriggerable, the relay will switch o at
exactly the moment the time elapses. If the Manual switching o function is activat-
ed, the staircase timer can be ended with a “0” telegram.
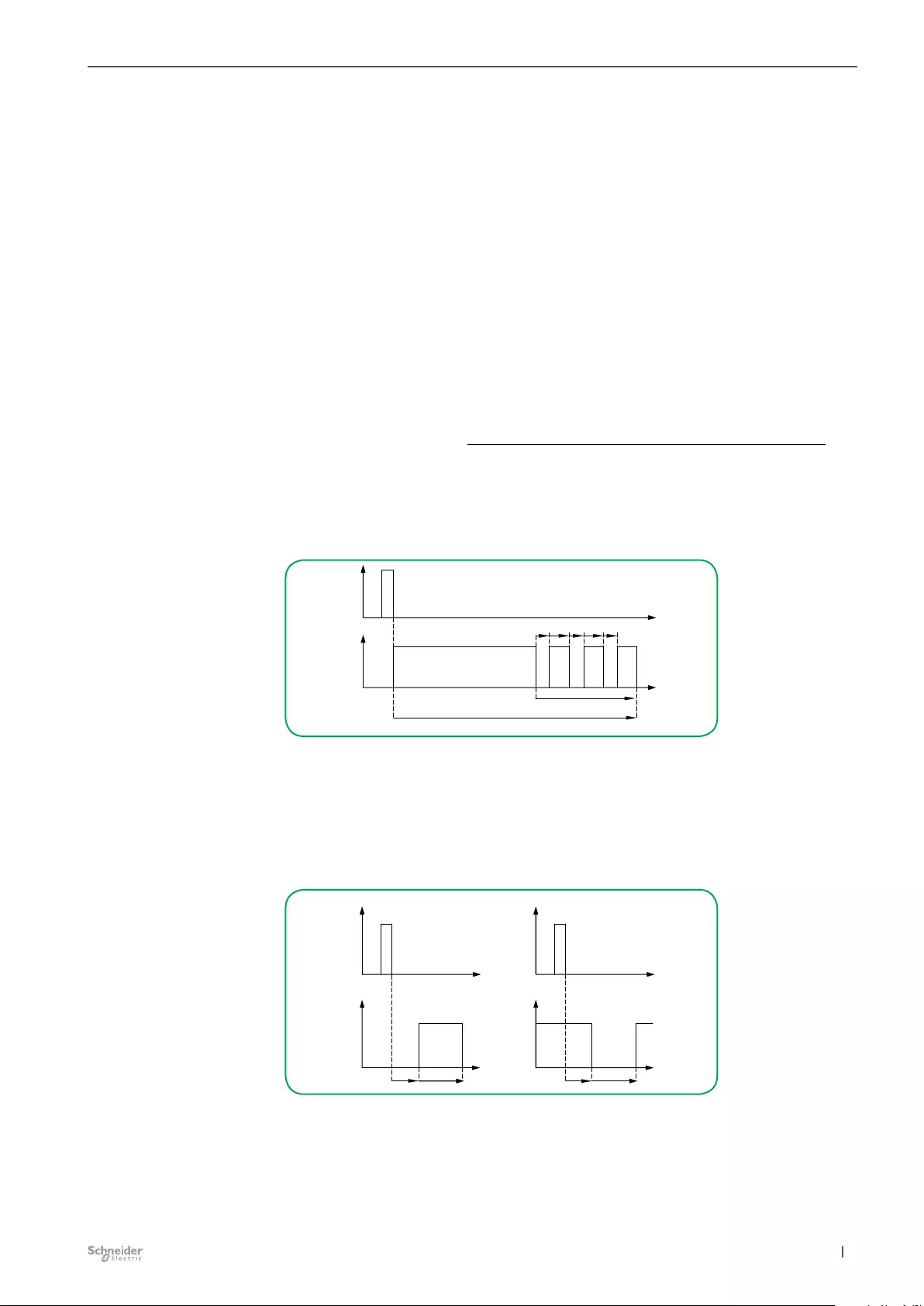
47
05/20-5800/1.0 MTN6705-0008 | MTN6805-0008 |
Extended settings for switching Switch Blind 5800/1.0
Prewarnings
To ensure that you are warned before the end of the staircase lighting time, you
can parameterize a dened number (0-5) of prewarnings.
With the prewarnings, the user can be informed about the imminent end of the
function by briey switching o the lighting system shortly before the end of a stair-
case lighting time. He can then restart the staircase lighting by pressing a button
(retriggering). If he does nothing, the function continues normally.
You can set this using the parameter Number of prewarnings. With the value "0",
the warning function is disabled. To enable the prewarnings, select the number
of warning pulses. The rst warning starts at the remaining staircase lighting time
(tWarning) set via the parameter Warning starts before end.
With every prewarning, the output contact is switched to "released" state for the
xed duration of 500 ms (tu). If you have activated more than one warning, the wait-
ing time (tzv) between the warning pulses is calculated using the following formula:
Wait time between
prewarnings (tzv)=
Remaining staircase lighting time (twarning) -
(number of prewarnings x 500 ms (tu))
Number of prewarnings
If a continuous staircase lighting time function is interrupted by premature termina-
tion, no prewarning is given
Prewarning (number of prewarnings=3)
t
t
1
t staircase
KNX
telegram
State
Actuated
Not actuated
t Warning
t u t int t u t int t u
123
Staircase lighting time function in combination
with on-delay and off-delay
Combining a staircase lighting time function with an on-delay results in a delayed
start of the staircase lighting function.
Staircase lighting time function with on-delay
Open
t
t
KNX
Relay status
Closed
Relay status
Closed
t
Open
t
KNX
1
t staircase
telegram telegram
1
t staircase
t on t on
Make-contact function Break-contact function
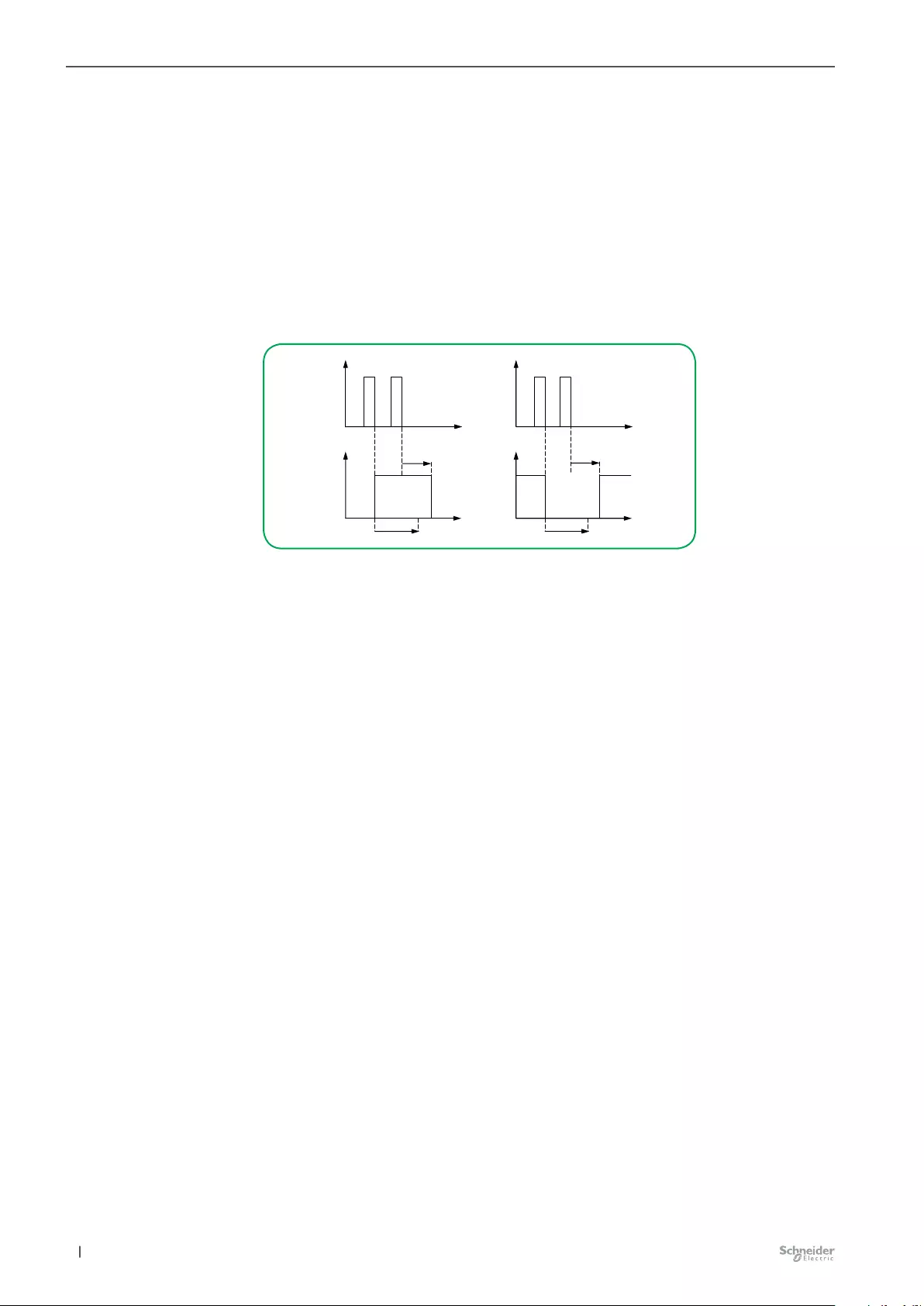
48 05/20-5800/1.0MTN6705-0008 | MTN6805-0008 |
Extended settings for switching Switch Blind 5800/1.0
The result of combining a staircase lighting time function with an o-delay depends
on how you have dened the staircase lighting time function:
In the case of the staircase lighting time function with manual switching o ("0"
telegram), the o-delay is started if a premature switch-o telegram is received on
the "staircase lighting time object". Once the o-delay time has elapsed, the output
is switched o (released).
In the case of the staircase lighting time function without manual switching o,
receipt of a switch-o telegram on the "staircase lighting time object" has no eect.
The staircase lighting time function continues to the end and then switches the
output relay directly to the "released" state. An o-delay cannot be set.
Staircase lighting time function with o-delay
Open
t
t
KNX
Relay status
Closed
Relay status
Closed
t
Open
t
KNX
1
t staircase
telegram telegram
1
0 0
t staircase
t off t off
Make-contact function Break-contact function
For staircase lighting time functions with manual switching o and warnings acti-
vated, the staircase lighting time function is immediately deactivated with a warning
when an "O" telegram is received. The o-delay elapses. No warning is gener-
ated.
Priority
If the output of the actuator is switched to a new switch position by a higher priority
function during an ongoing staircase lighting time, the relay switches to the new
position immediately. The most recent switching telegram is saved and delay times
and staircase lighting times continue.
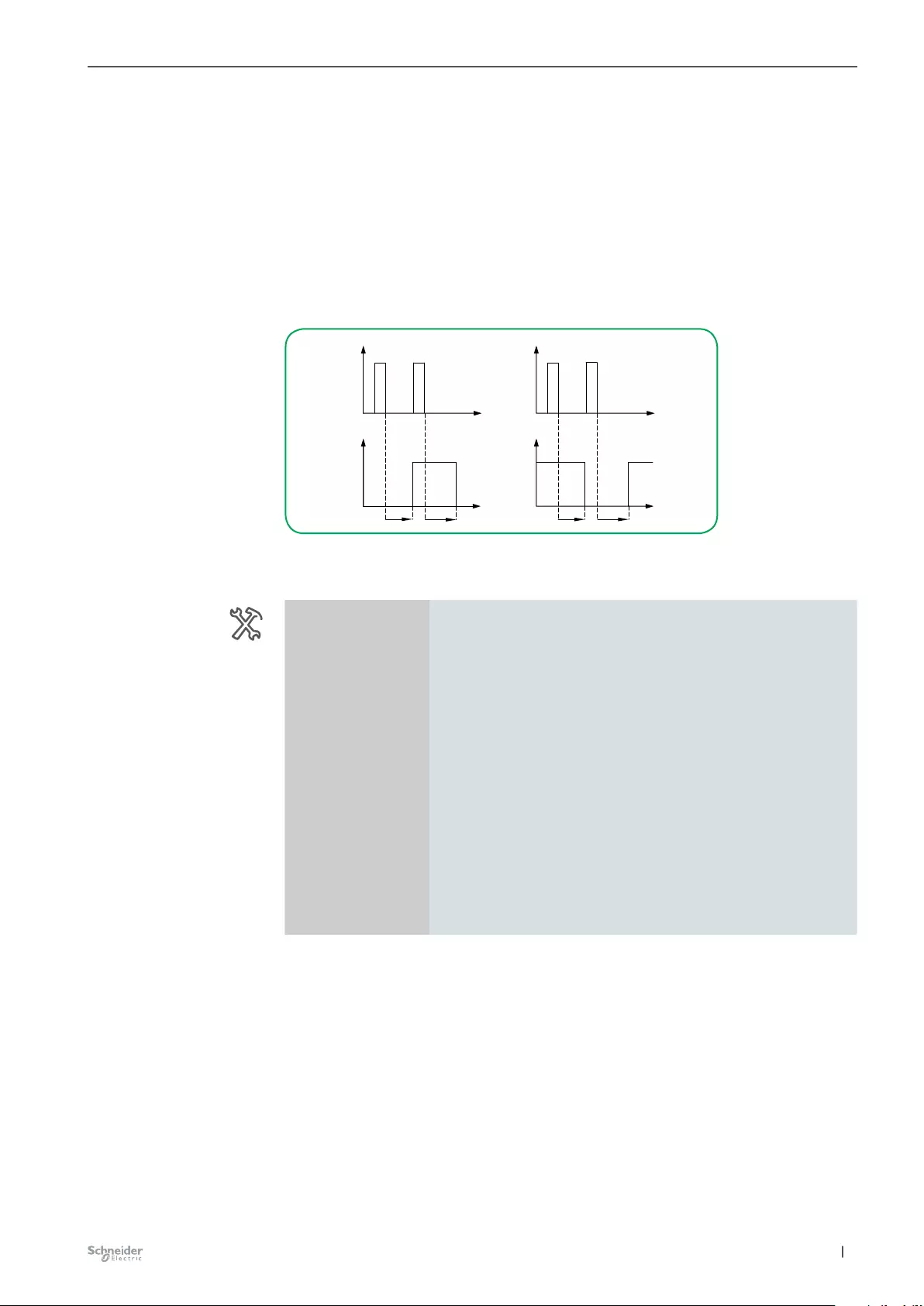
49
05/20-5800/1.0 MTN6705-0008 | MTN6805-0008 |
Extended settings for switching Switch Blind 5800/1.0
On-delay and off delay
Due to the delay functions, the change of relay states is not carried out immediately
after receipt of a telegram, but only after the set delay time has elapsed:
After the object value "1" has been received, the on-delay delays the switching of
the relay contact from the released state to the pressed state.
After the object value "0" has been received, the o-delay delays the switching of
the relay contact from the pressed state to the released state.
You can also use both functions together with a single channel.
On-delay and o-delay (normally opened/normally closed)
Open
t
t
KNX
Relay status
Closed
Relay status
Closed
t
Open
t
KNX
1
telegram
Switching
telegram
Switching
1
t on t on
t off t off
0
0
Make-contact function Break-contact function
On-delay
Master/Ext. 1/2
Output 1-8 -Switch
-Switching
On-delay time
-Time settings On-delay time Enabled
Disabled
Works on Switch object Yes (Yes/No)
Works on Staircase object No (Yes/No)
Works on Scene object No (Yes/No)
On-delay mode Not retriggerable
Retriggerable
On-delay time 1 s (0 ms-1 h)
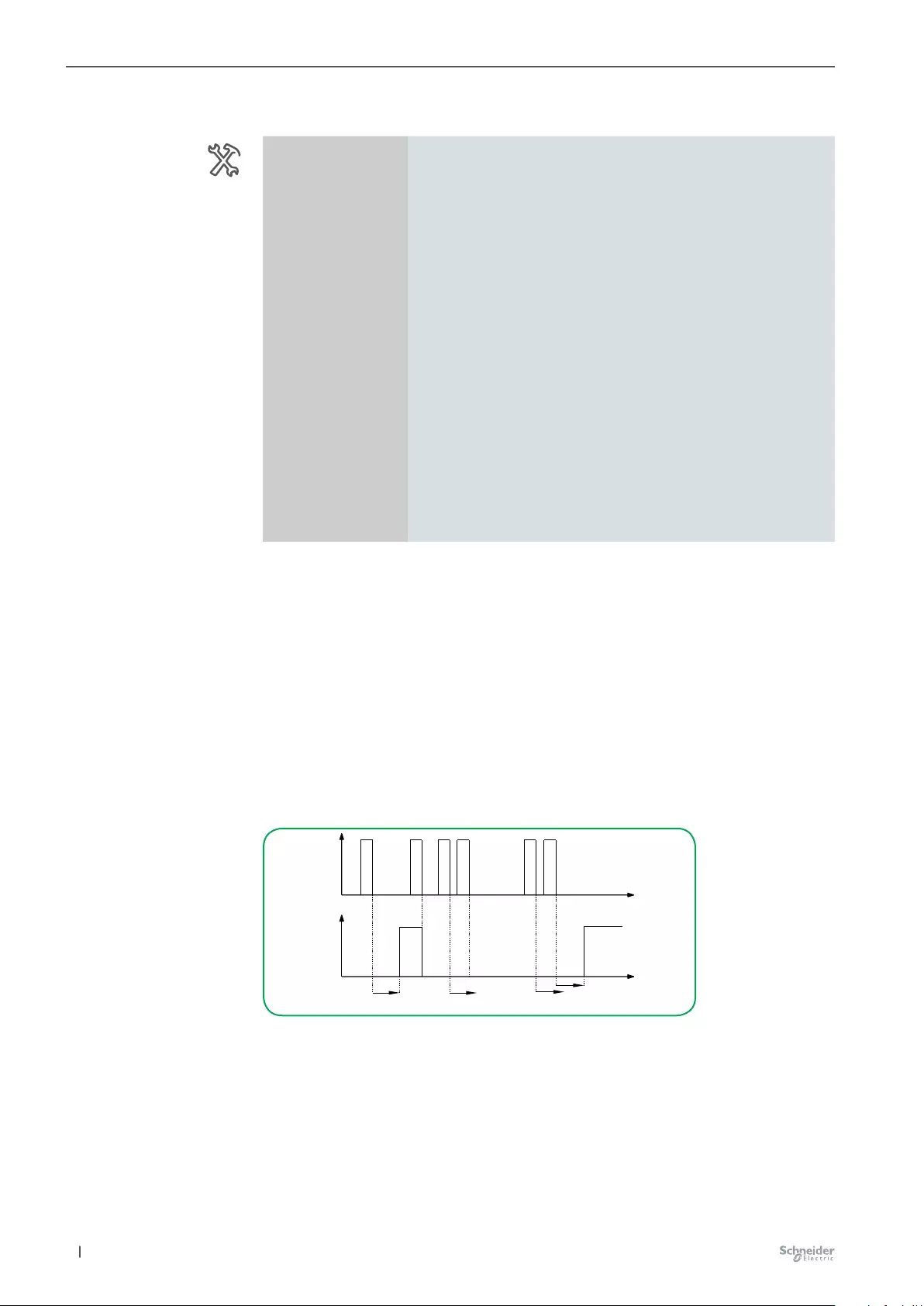
50 05/20-5800/1.0MTN6705-0008 | MTN6805-0008 |
Extended settings for switching Switch Blind 5800/1.0
Off-delay
Master/Ext. 1/2
Output 1-8 -Switch
-Switching
O-delay time
-Time settings O-delay time Enabled
Disabled
Works on Switch object Yes (Yes/No)
Works on Staircase object No (Yes/No)
Works on Scene object No (Yes/No)
O-delay mode Not retriggerable
Retriggerable
Retriggerable and adding
Max. number of additions 2 (2-5)
O-delay time 1 s (0 ms-1 h)
Works on object
For each channel, you can parameterize whether the delay aects the switch
object, staircase lighting time object or scene object, or multiple objects in combina-
tion.
Type of delay
Delay times can be parameterized for each channel. You can use parameters to
dene the set delays as Retriggerable or Not retriggerable. In the case of a retrig-
gerable on-delay, the delay time is restarted when a "1" telegram is received. In the
case of retriggerable o-delays, the delay time is restarted when a "0" telegram is
received.
Retriggerable on-delay ("1" telegram)
t
t
1
t on
01011
t on t on t on
KNX
telegram
State
Actuated
Not actuated
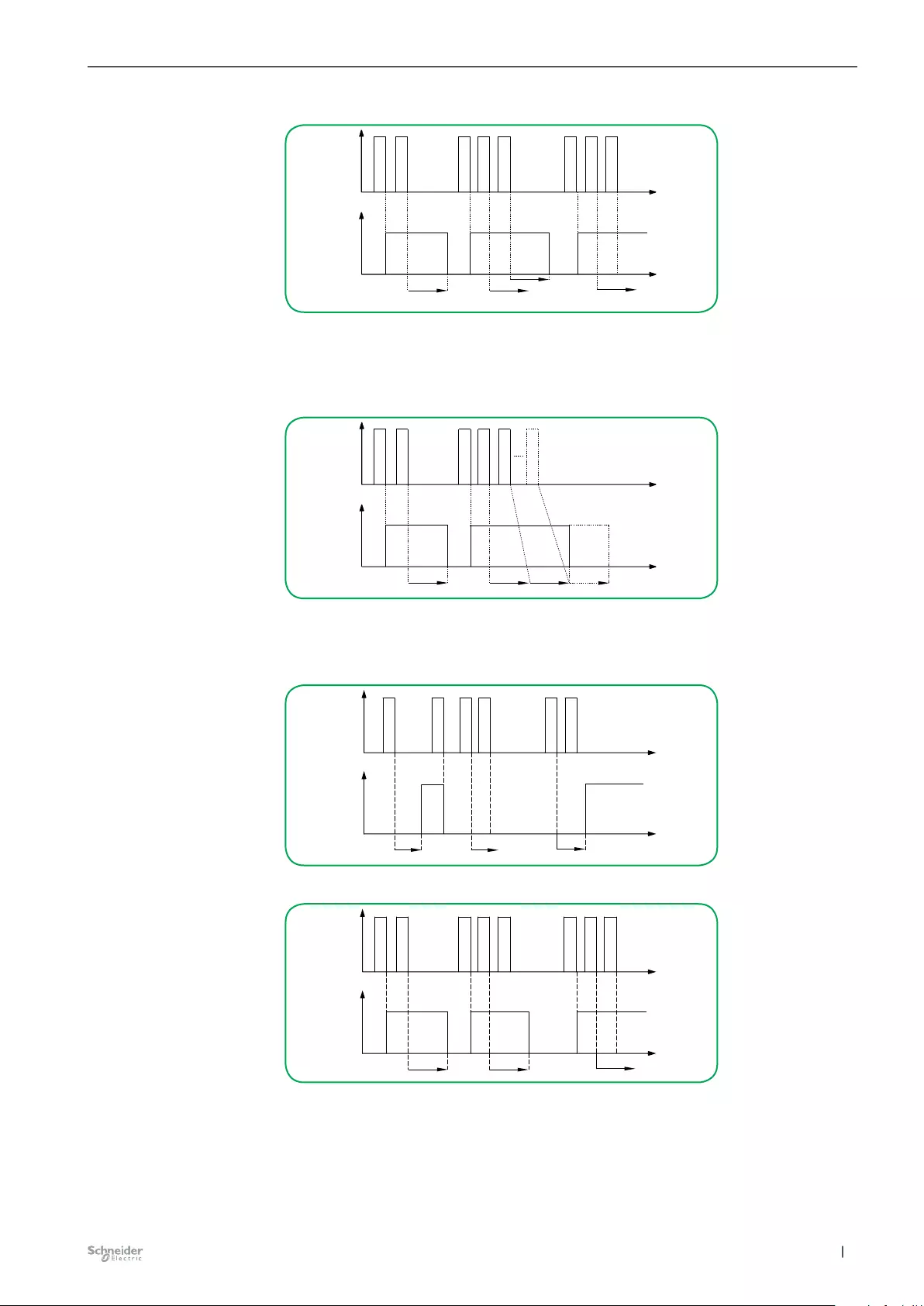
51
05/20-5800/1.0 MTN6705-0008 | MTN6805-0008 |
Extended settings for switching Switch Blind 5800/1.0
Retriggerable o-delay ("0" telegram)
t
t
1
t off
10 010
t off
10
t offt off
KNX
telegram
State
Actuated
Not actuated
Moreover, for the o-delay, you can also select Retriggerable and adding. The de-
lay time is added when the same telegram value is received, e.g. using a separate
button. You can dene the maximum number of additions.
Retriggerable o-delay and adding ("0" telegram)
t
t
1100
t off
0
t off
KNX
telegram
State
Actuated
Not actuated
t offt off++
0
Max.
5 x
In the case of not retriggerable delays, by contrast, the relay will switch o at ex-
actly the moment the time elapses.
Not retriggerable on-delay
KNX
telegram
t
t
State
Actu ated
1
t on
Not actu ated
01011
t on t on
Not retriggerable o-delay
t
t
1
t off
10 010
t off
10
t off
KNX
telegram
State
Actuated
Not actuated
Interrupting a delay function
If a delay function is started by receiving a new object value and the output channel
receives a telegram with the opposite object value during the current delay time,
the delay function is canceled. The relay is not switched:
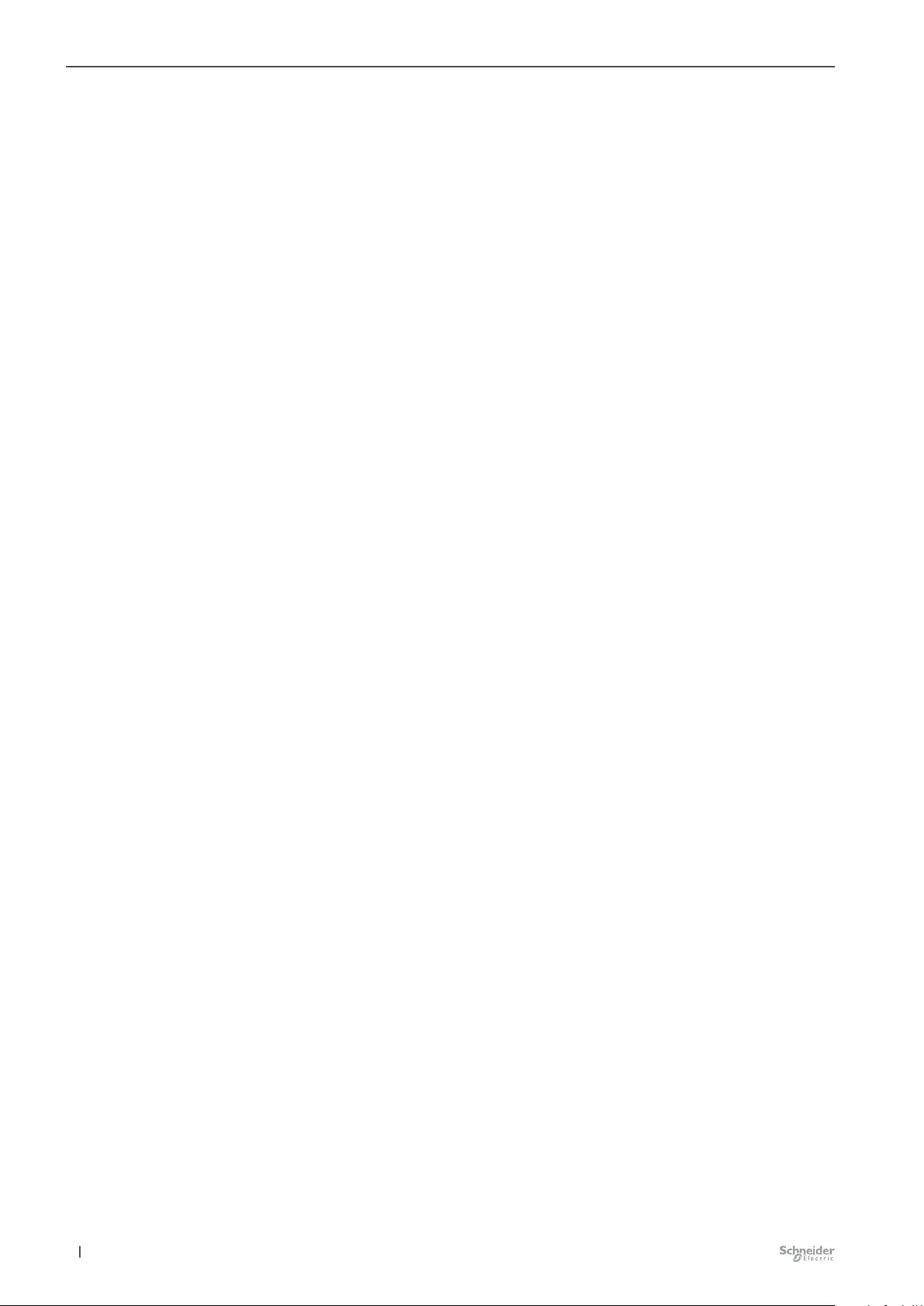
52 05/20-5800/1.0MTN6705-0008 | MTN6805-0008 |
Extended settings for switching Switch Blind 5800/1.0
Receipt of the object value "0" interrupts an active on-delay.
Receipt of the object value "1" interrupts an active o-delay.
Priority
If the output of the actuator is switched to a new switch position by a higher-level
function during an active delay time, the relay switches immediately.
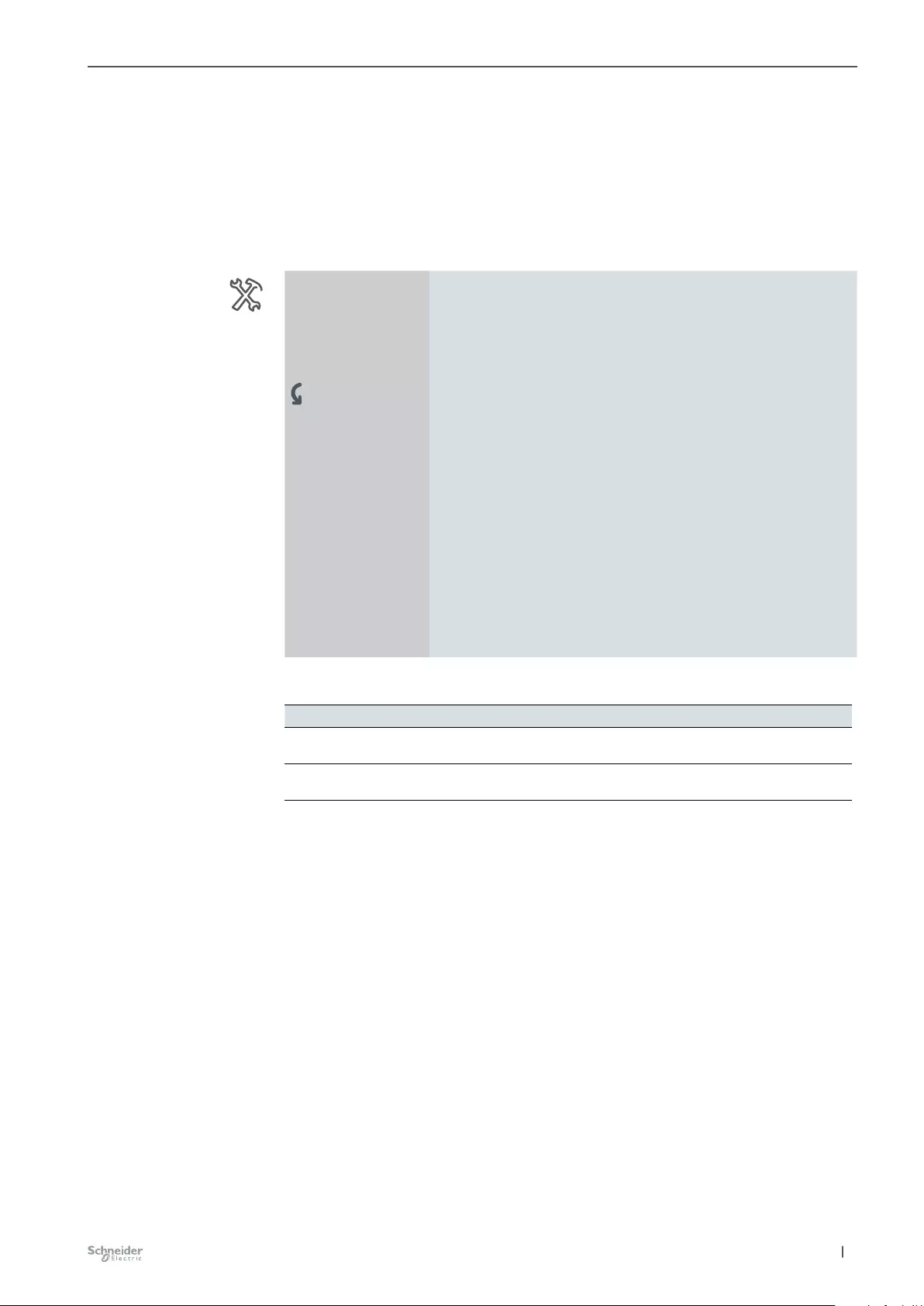
53
05/20-5800/1.0 MTN6705-0008 | MTN6805-0008 |
Extended settings for switching Switch Blind 5800/1.0
6.2 Logic, Locking & Priority settings
Logic function
With this functionality, the Switching object and the Logical input object can be
logically linked to one another.
The logic function can be activated (enabled) in the ETS.
Master/Ext. 1/2
Output 1-8 -Switch
-Switching
Logic function
-Logic, Locking & Prior-
ity settings Logic function Disabled
Enabled
Type of logic operation OR
AND
XOR
Value of logic operation object
after bus voltage recovery or
download
0
1
Value of logic object Normal
Inverted
Following enabling, these group objects appear.
No. Name Object function Length Behavior Data Type
31 Master Output 1 &
(name of the channel)
Switching 1 bit Received 1.001 Switching
32 Master Output 1 &
(name of the channel)
Logical input 1 bit Received 1.002 Boolean
An AND, OR or XOR logic operation can be set. A parameter is used to dene the
preset value of the logic object after bus voltage recovery and download.
For example, in the case of an OR logic object preset with the value "1" after bus
voltage recovery, the output remains activated until a "0" telegram is received on
the "logic object". A parameterized behavior after bus voltage recovery is only
adopted after the logic operation has been terminated.
Group objects of logic function

54 05/20-5800/1.0MTN6705-0008 | MTN6805-0008 |
Extended settings for switching Switch Blind 5800/1.0
AND logic operation
As long as the "logic operation input object" has the value "1", switching can be
carried out as usual using the address of the "switch object". Set staircase lighting
times will continue to be observed. Switching o via the "logic object" takes eect
immediately.
Object
Logical input
Object
Switching
Result
000
010
100
111
Example:
An AND logic operation can be used to create a power-on lock. This means that
as long as the value of the "logic object" is "0", the "switch object" cannot be used
for switching on. If the value of the "switch object" is "1", switching on is carried out
automatically if the value of the logic object changes from 0 to 1.
AND logic operation;
Value of logic object after bus voltage recovery: 1
telegram
logic
operation
telegram
switching
Status
actuated
not actuated
KNX-
KNX-
t
01
t
t
0101
RESET
The logic object is preset with the value "1" after a RESET (bus voltage recovery
and download). This enables switching to be carried out as usual using the switch
object. The power-on lock is not active until a "0" telegram has been received via
the logic object.
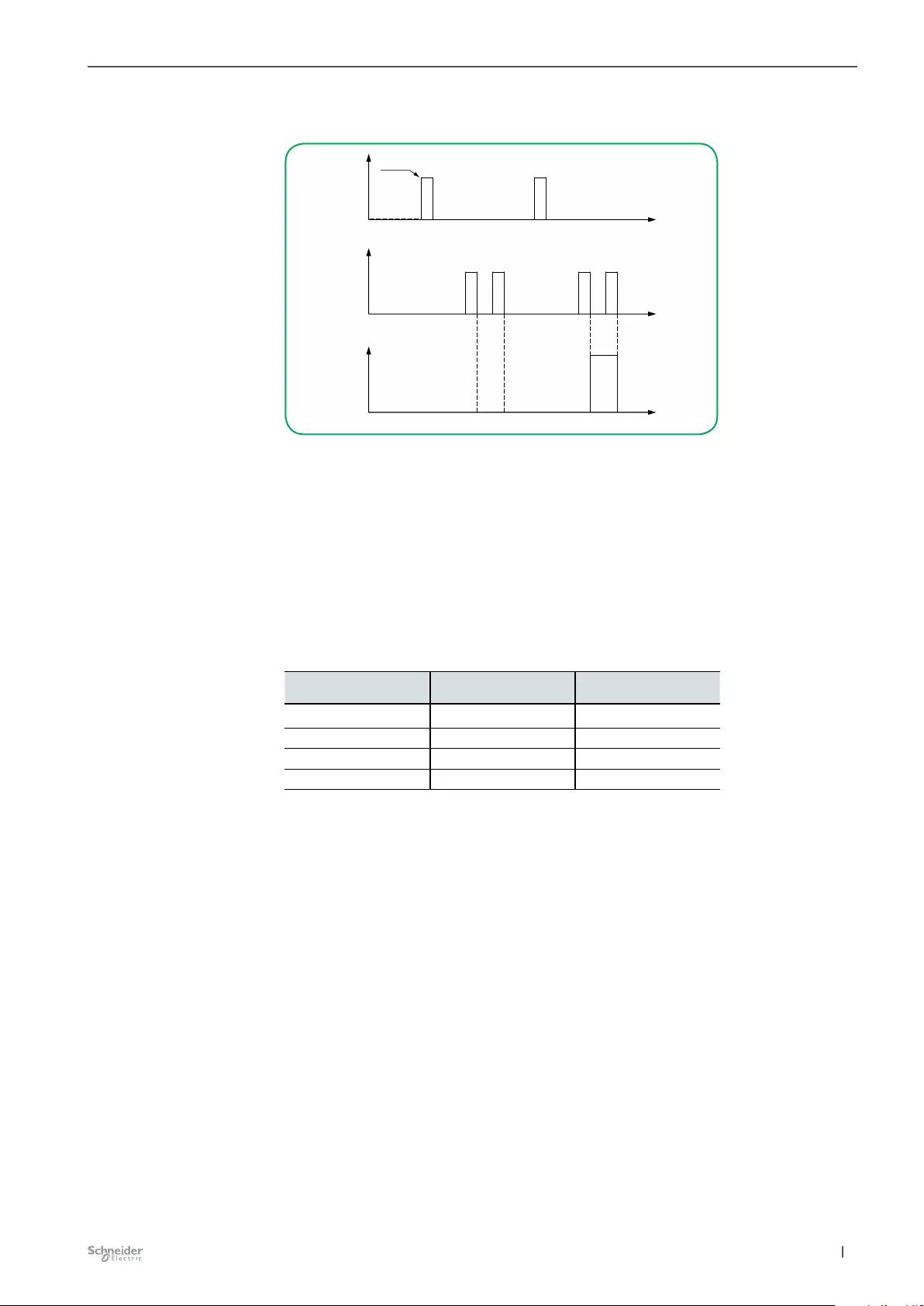
55
05/20-5800/1.0 MTN6705-0008 | MTN6805-0008 |
Extended settings for switching Switch Blind 5800/1.0
AND logic operation;
Value of logic object after bus voltage recovery: 0
telegram
logic
operation
telegram
switching
Status
actuated
not actuated
KNX-
KNX-
t
10
t
t
0101
RESET
The parameter setting causes the "logic object" to be set to the value "0". After
a RESET, the actuator does not switch the output until a "1" telegram has been
received on the "logic object".
OR logic operation
As long as the "logic object" has the value "0", switching can be carried out as
usual using the address of the "switch object". Set staircase times continue to be
observed. Switching on via the "logic object" takes eect immediately.
Object
Logical input
Object
Switching
Result
000
011
101
111
Example:
An OR logic operation can be used to implement a power-o lock or Central ON
function (e.g. light for cleaning buildings). If the value of the "switch object" is also
set to "1" locally, the relay remains switched on when the power-o lock is with-
drawn (value change of logic object from 1 to 0).

56 05/20-5800/1.0MTN6705-0008 | MTN6805-0008 |
Extended settings for switching Switch Blind 5800/1.0
OR logic operation;
Value of logic object after bus voltage recovery: 0
telegram
logic
operation
telegram
switching
Status
actuated
not actuated
KNX-
KNX-
t
10
t
t
0101
RESET
0
The relay can only be switched via the "switch object" if a "0" telegram has been
received via the "logic object".
OR logic operation;
Value of logic object after bus voltage recovery: 1
telegram
logic
operation
telegram
switching
Status
actuated
not actuated
KNX-
KNX-
t
01
t
t
0101
RESET
1
The logic object is preset to the value "1" after a RESET. The actuator will switch
on the output immediately. The OR logic function is only reset by a "0" telegram on
the logic object.
XOR logic operation
As soon as the values of the "logic object" and the "switch object" dier from one
another, the output is switched to Pressed. If the values are the same, the output is
Released.
Object
Logical input
Object
Switching
Result
000
011
101
110
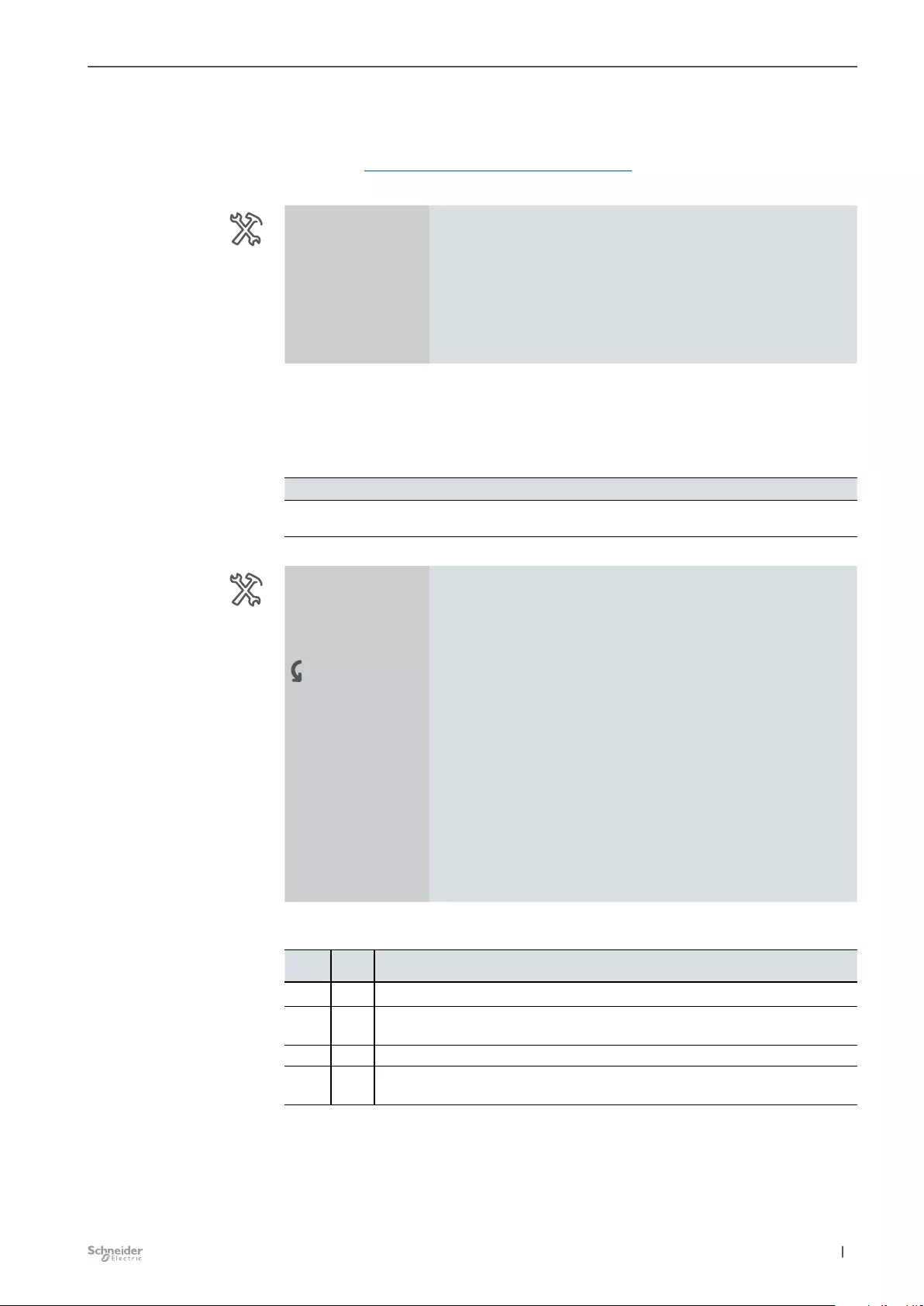
57
05/20-5800/1.0 MTN6705-0008 | MTN6805-0008 |
Extended settings for switching Switch Blind 5800/1.0
Functions with higher priority
The order of priority of the various functions is set on the Extended settings tab of
the device. Priority of functions for switching --> 28
In the ETS, the higher priority function can be activated.
Master/Ext. 1/2
Output 1-8 -Switch
-Switching
Priority function
-Logic, Locking & Prior-
ity settings Higher priority function Disabled
Priority function
Locking function
Priority function (priority control)
If you have chosen the priority function (known in other devices as priority control),
a new group object called Priority is available for this channel.
No. Name Object function Length Behavior Data Type
33 Master Output 1 &
(name of the channel)
Priority 2 bit Received 2.001 Prio. switching
Master/Ext. 1/2
Output 1-8 -Switch
-Switching
Priority function
-Logic, Locking & Prior-
ity settings Higher priority function Priority function
Behavior at end of priority Follows current value
Pressed
Released
Behavior after bus voltage
recovery Disabled
Enabled, released
Enabled, pressed
As before bus voltage failure
The object values of the priority object have the following meaning:
Value
bit 1
Value
bit 2
Behavior of output
1 1 Activate priority, switching state "Pressed"
0 1 Deactivate priority, switching state dependent on the parameter Be-
havior at end of priority
1 0 Activate priority, switching state "Released"
0 0 End of priority, switching state dependent on parameter Behavior at
end of priority
Group objects of priority function
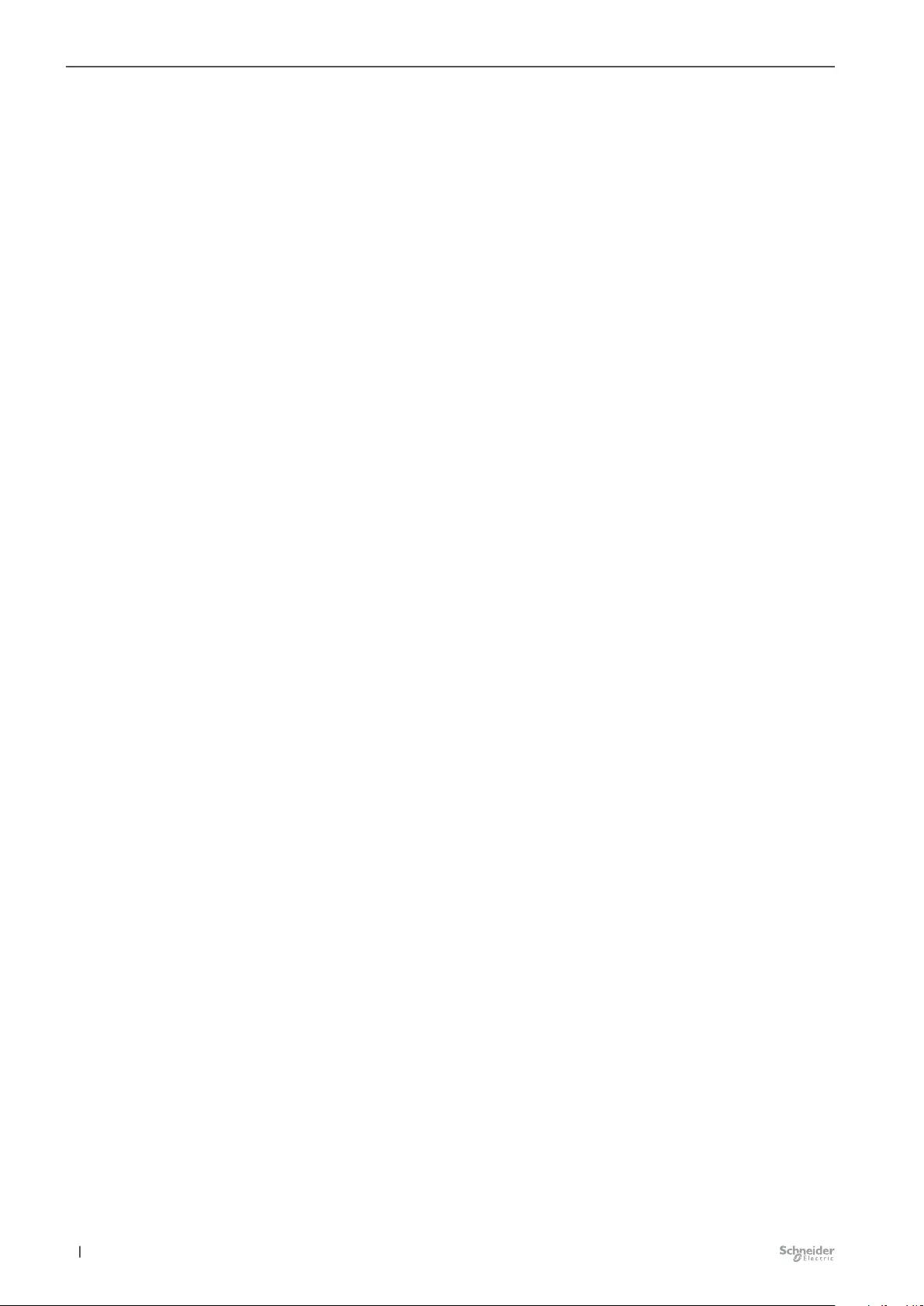
58 05/20-5800/1.0MTN6705-0008 | MTN6805-0008 |
Extended settings for switching Switch Blind 5800/1.0
The priority is activated if the value "1" is received on bit 1. The assigned output
relay is then switched, depending on bit 2, to "Pressed" (bit 2 = "1") or "Released"
(bit 2 = "0") .
An active priority is deactivated by a new telegram with the value "0" on bit 1. As
long as a priority function is active, the channel concerned cannot be controlled by
the "switch object" and the advanced functions (central function, time functions,
scene function).
After the end of a priority, the behavior of the output relay is determined by the
parameter Behavior at end of priority.
The setting Follows currently valid state has the following eect:
During the active priority, all switching commands of subordinate functions are
tracked by the application and the switching state is tracked internally. In this way,
at the end of the priority, the switching state can be set that would currently have
been set without the priority.
Behavior after bus voltage recovery
Using the parameter Behavior after bus voltage recovery, you can dene the reac-
tion of the channel to bus voltage recovery and the switching state:
•Disabled
Priority remains deactivated. The switching state of the channel results from the
other higher-level functions or from the set switching behavior after bus voltage
recovery.
•Enabled, released
The priority is automatically activated on bus voltage recovery and the switching
state is switched to Released.
•Enabled, pressed
The priority is automatically activated on bus voltage recovery and the switching
state is switched to Pressed.
•As before bus voltage failure
The priority is brought to the state it had before the bus voltage failure. If the
priority was previously active, the output relay is switched to the state it had
previously.
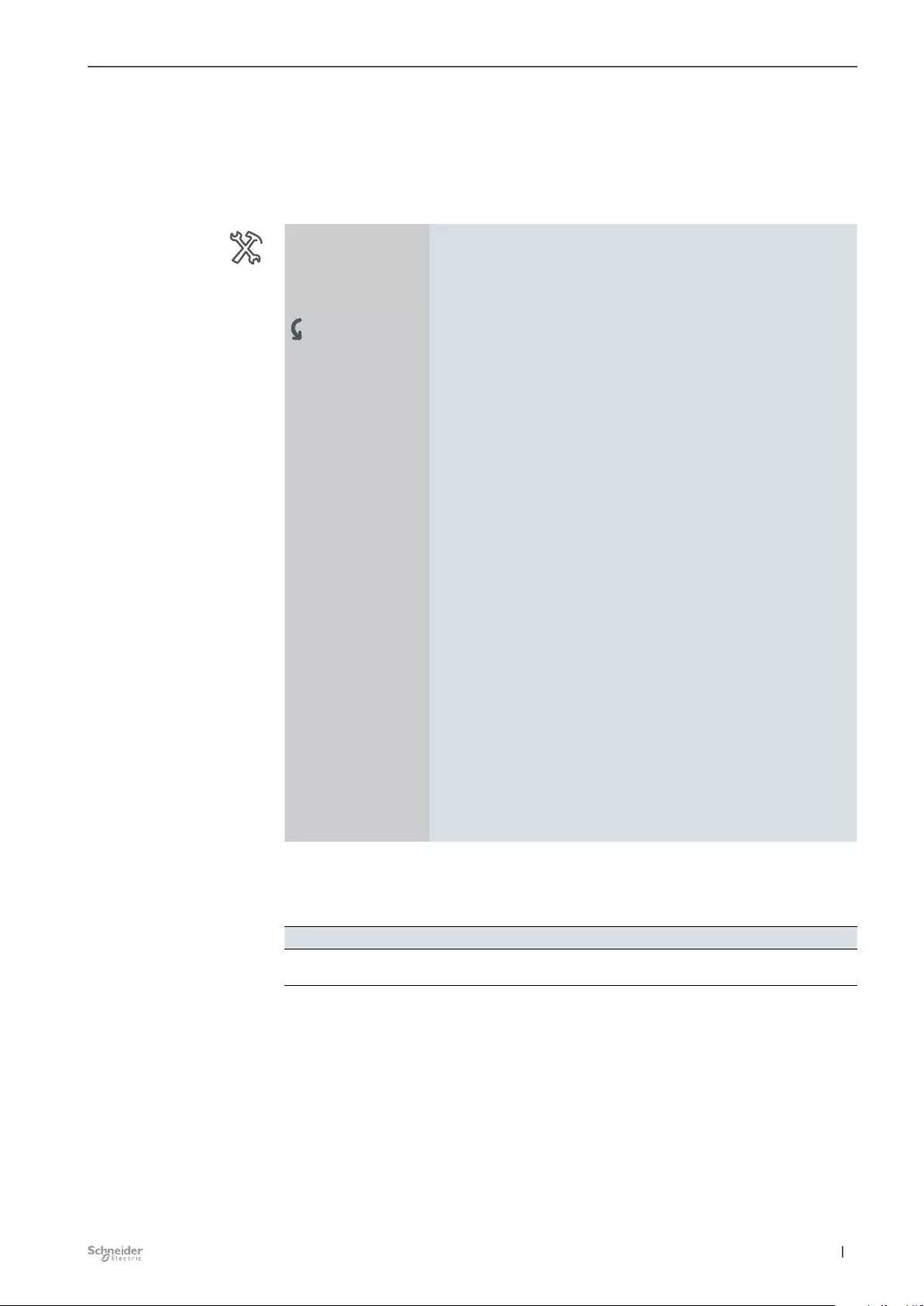
59
05/20-5800/1.0 MTN6705-0008 | MTN6805-0008 |
Extended settings for switching Switch Blind 5800/1.0
Locking function
You can use the locking function to set a specic channel to pressed/released and
lock it in this position. The state of the output channel cannot be changed by other
control commands as long as the lock is active. You can enable the locking function
individually for each switching channel.
Master/Ext. 1/2
Output 1-8 -Switch
-Switching
Locking function
-Logic, Locking & Prior-
ity settings Higher priority function Locking function
Locking at object value "1"
At object value "0"
Behavior at start of locking No reaction
Pressed
Released
Behavior at end of locking No reaction
Pressed
Released
Follows current value
Behavior after download Disabled
Enabled
As before download
Behavior after bus voltage
recovery Disabled
Enabled
As before bus voltage failure
Once the locking function has been enabled, a new group object called Lock is
available for the switching channel. You can activate and deactivate a channel lock
using the locking object.
No. Name Object function Length Behavior Data Type
33 Master Output 1 &
(name of the channel)
Locking 1 bit Received 1.003 Enable
If the locking object receives a telegram with the object value that you set for the
parameter Lock, all other channel functions are disabled. You can dene the reac-
tion using the parameter Behavior at start of locking.
If the locking object receives a telegram with the object value opposite of that for
activation, the lock is canceled and the output relay adopts the state that you de-
ned in the parameter Behavior at end of locking.
The locking function always switches without a delay. During a lock, the most
recent switching telegram is saved and delay times and staircase lighting times
continue.
Group objects of locking func-
tion
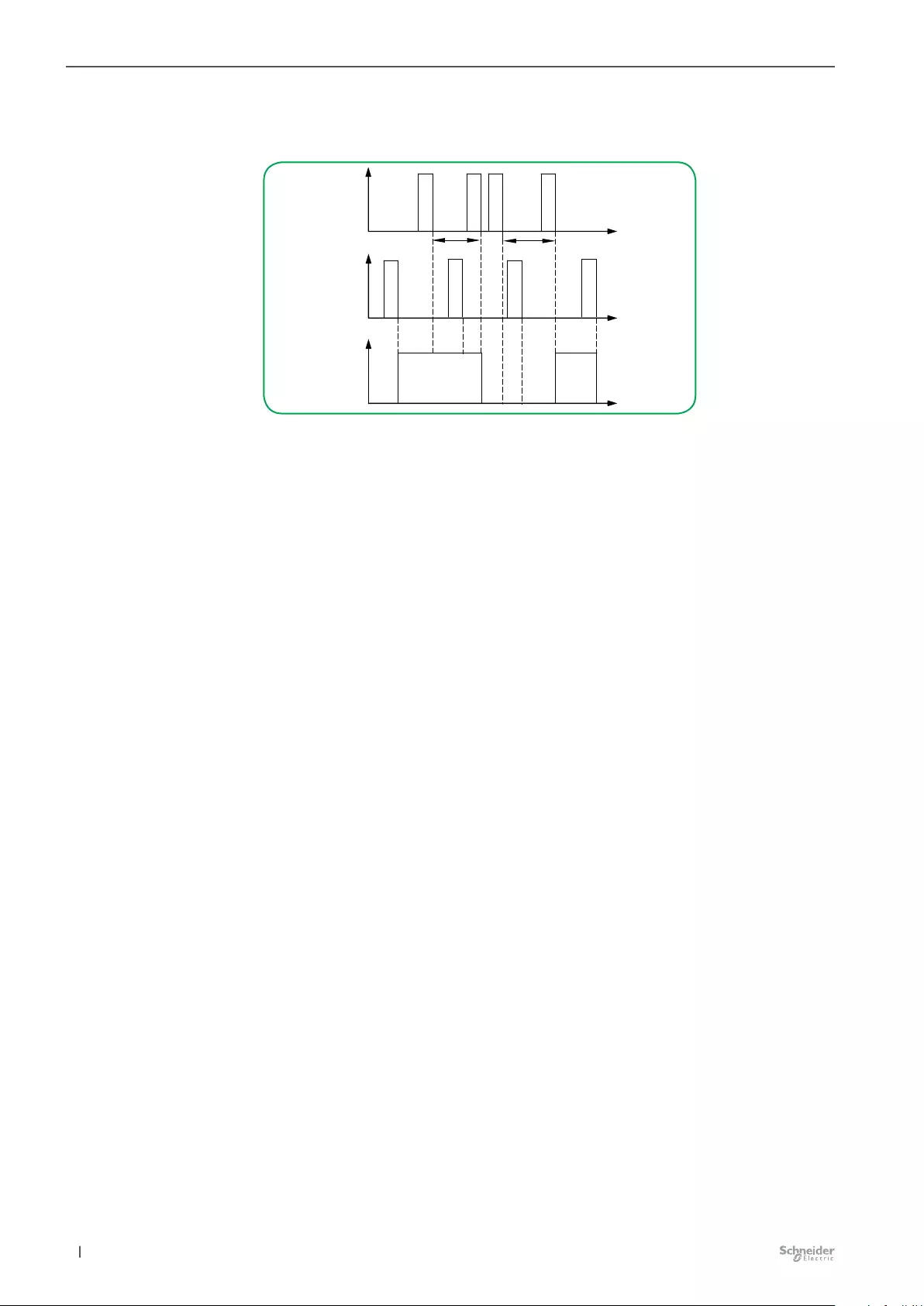
60 05/20-5800/1.0MTN6705-0008 | MTN6805-0008 |
Extended settings for switching Switch Blind 5800/1.0
Lock at object value "1"; Behavior at start of locking = no reaction;
Behavior at end of locking = Follows current value; relay operation: Normally
opened
KNX
telegram
Switch object
t
t
switching state
1
Not actuated
1
KNX
telegram
Disable object
t
1010
Disabled Disabled
Actuated
00
Lock behavior after download
After a download, the lock function is also set as in the case of bus voltage recov-
ery. The parameter Behavior after download determines which state is set.
If the parameter Behavior after download is set to the value As before download,
the locking function is activated as before and the relay is switched accordingly.
Lock behavior after bus voltage recovery
•Disabled
The locking function is not activated after a bus voltage recovery, regardless of
the state it had before the bus voltage failure.
•Enabled
After a bus voltage recovery, the locking function becomes active and the output
is switched to the state that you dened via the parameter Behavior at start of
locking. If you have set the value No reaction here, the output is locked in its
current state.
•As before bus voltage failure
The locking function is brought to the state that was active before the bus
voltage failure. If the locking function was active, the output is controlled by its
settings in the parameter Behavior at start of locking.
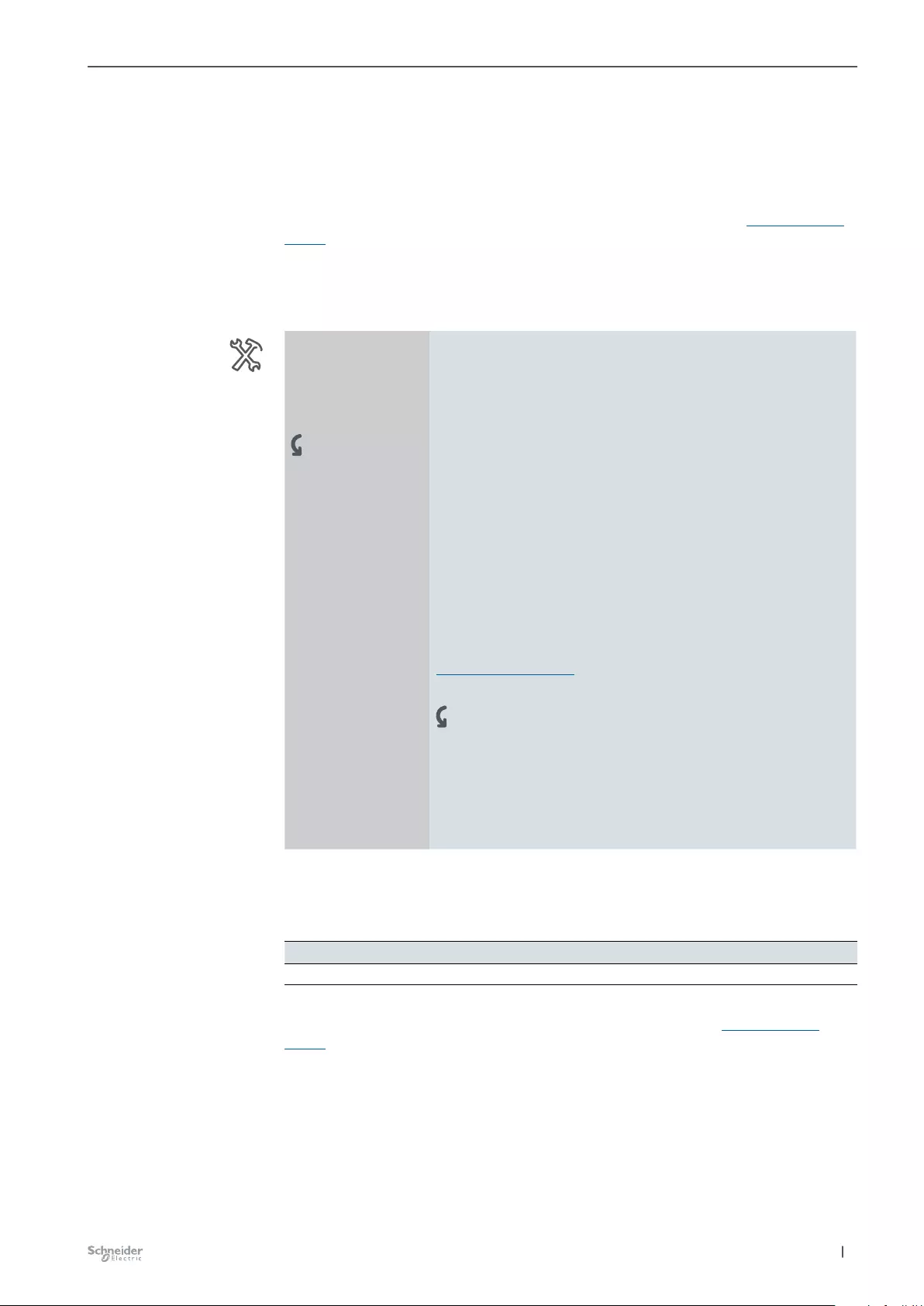
61
05/20-5800/1.0 MTN6705-0008 | MTN6805-0008 |
Extended settings for switching Switch Blind 5800/1.0
6.3 Safety and alarm settings
Safety function switching
The global safety function is activated on the Extended settings tab with the param-
eter Device safety and the global settings are parameterized there. Device safety
--> 22
The eect of the safety function can be parameterized here for each channel. You
can enable the safety function individually for each switching channel.
Master/Ext. 1/2
Output 1-8 -Switch
-Switching
Safety function
-Safety and alarm
settings Safety function Disabled
Enabled
Behavior at start of safety No reaction
Pressed
Released
Blinking (5s cycle)
Behavior at end of safety No reaction
Pressed
Released
Follows current value
Device safety --> 22
(Cycle time surveillance for
Safety object” > 0
Behavior at exceeding cycle
time No reaction
Pressed
Released
Blinking (5s cycle)
Following global enabling of the device safety, the group object appears.
Group objects
No. Name Object function Length Behavior Data Type
23 Central Safety 1 bit Received 1.005 Alarm
The safety function is activated if the safety object receives a telegram with the
object value that you dened with the parameter Device safety (Device safety
--> 22 ). The reaction is dened by the parameter Behavior at start of safety.
If the safety object receives a telegram with the object value opposite of that for
activation, the safety function is canceled and the output relay adopts the state that
you dened in the parameter Behavior at end of safety.
The device then waits for a telegram from an external sender within the globally set
cycle time. If such a telegram is not received within the monitoring time, the param-
eter Behavior at exceeding cycle time is used to determine what is to happen.
Group object for
central safety
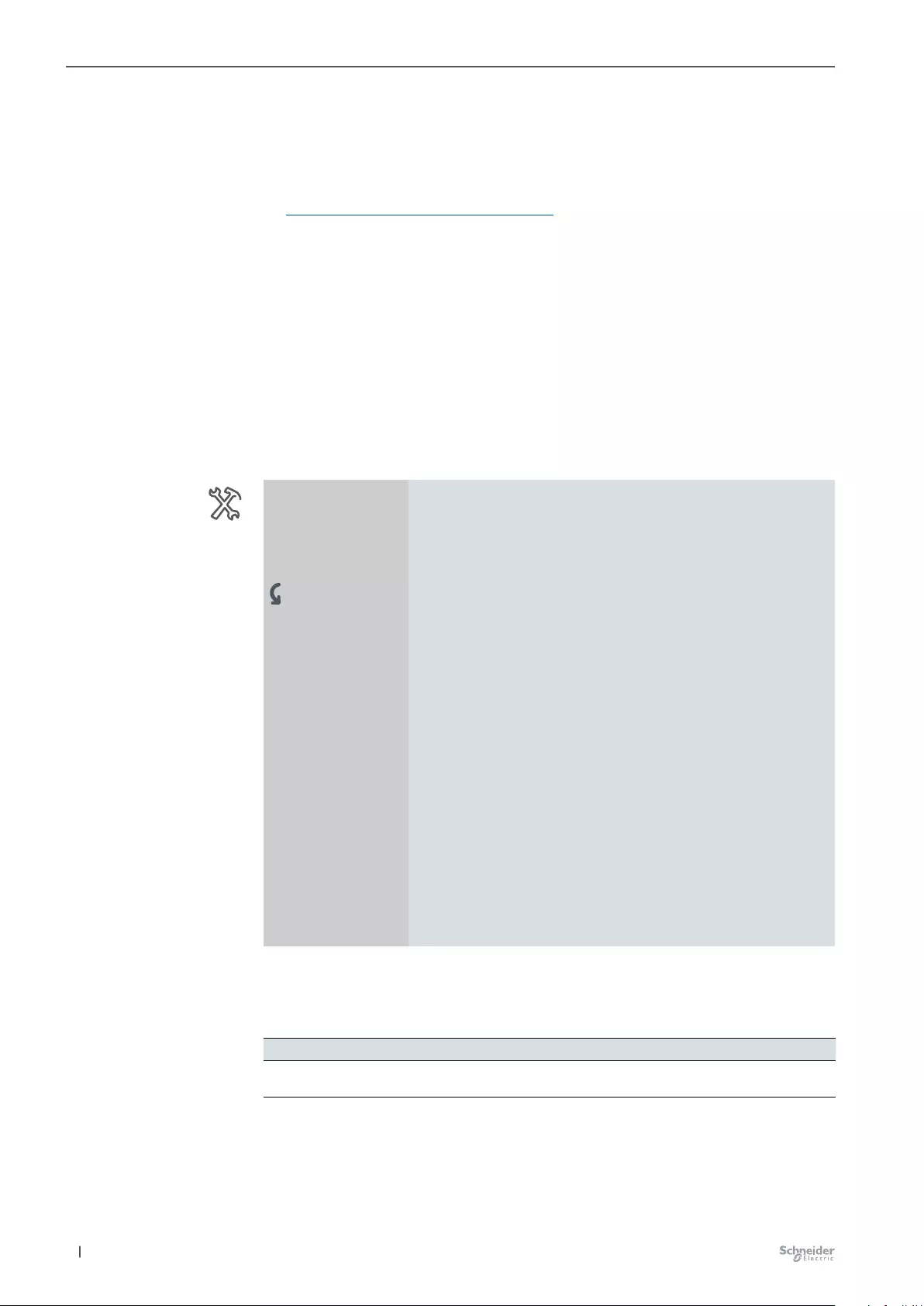
62 05/20-5800/1.0MTN6705-0008 | MTN6805-0008 |
Extended settings for switching Switch Blind 5800/1.0
Priority
The safety function is a 1-bit group object with the highest priority. This means that
this object takes precedence over the following group objects:
•Alarm object / Lock object / Priority object
Priority of functions for switching --> 28
•Logical input object
•Scene object
•Central switch object
•Staircase x / Staircase variable object
•Switch object
Alarm function
In the case of an alarm, the alarm function can be used to set each output to a
desired alarm state. The output is disabled for further operation. Only a higher-level
function with a higher priority can still be used to switch the output to a dierent
state. You can activate the alarm function individually for each output channel. The
alarm function can be parameterized here for each channel.
Master/Ext. 1/2
Output 1-8 -Switch
-Switching
Alarm function
-Safety and alarm
settings Alarm function Disabled
Enabled
Alarm At object value "1"
At object value "0"
Behavior at start of alarm No reaction
Pressed
Released
Blinking (5s cycle)
Behavior at end of alarm No reaction
Pressed
Released
Follows current value
Behavior after bus voltage
recovery Disabled
Enabled
As before bus voltage failure
Following enabling, the group object for this channel appears.
Group objects
No. Name Object function Length Behavior Data Type
34 Master Output 1 &
(name of the channel)
Alarm 1 bit Received 1.005 Alarm
Group objects of the alarm
function
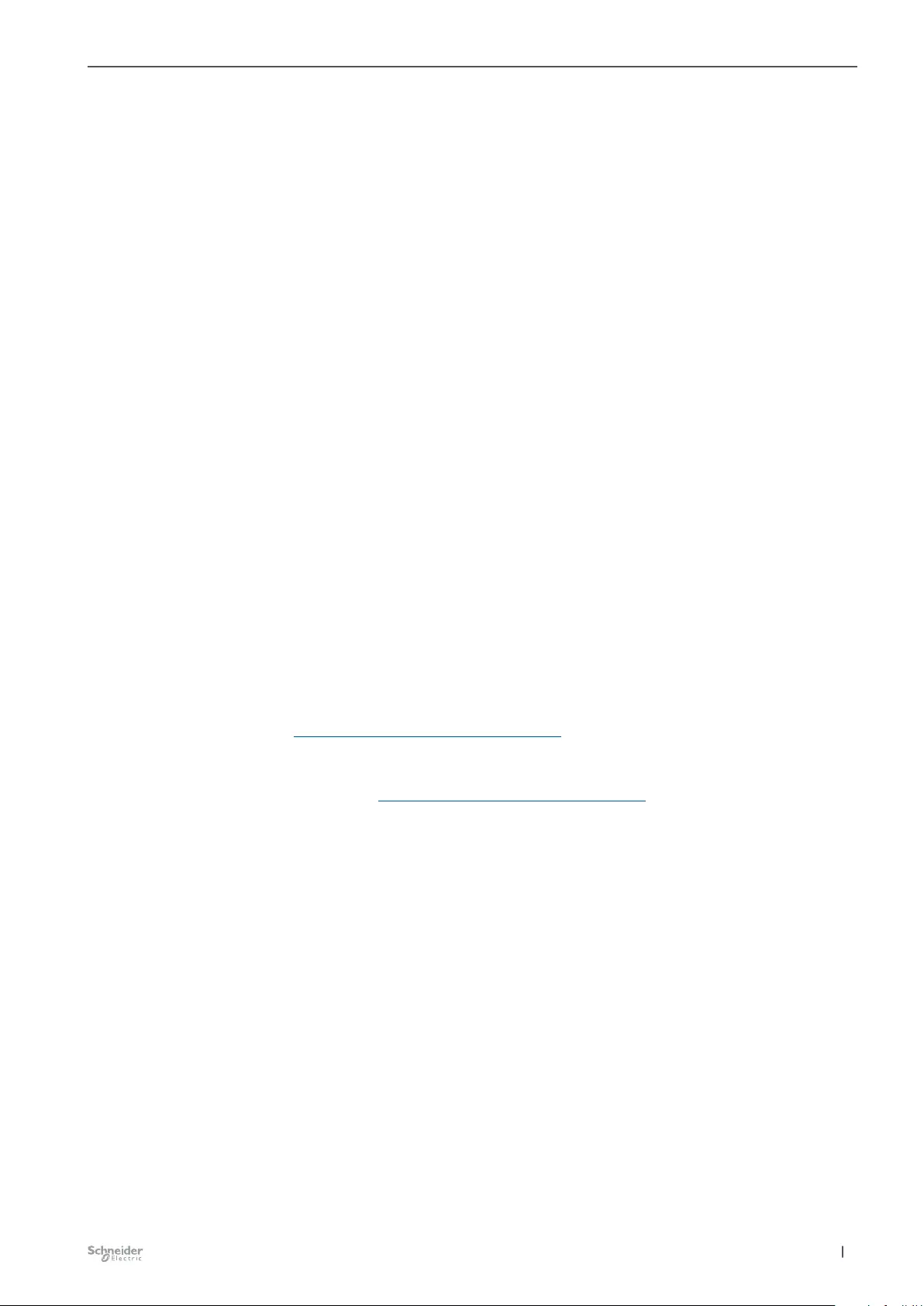
63
05/20-5800/1.0 MTN6705-0008 | MTN6805-0008 |
Extended settings for switching Switch Blind 5800/1.0
Object values for alarm
The alarm function is activated if the alarm object receives a telegram with the ob-
ject value that you dened with the parameter Alarm. The reaction is dened by the
parameter Behavior at start of alarm.
If the alarm object receives a telegram with the object value opposite of that for
activation, the alarm function is canceled and the output relay adopts the state that
you dened in the parameter Behavior at end of alarm.
•At object value "1":
The object value "1" switches on the alarm function. If the object value "0" is
received, the alarm function is switched o again.
•At object value "0":
The object value "0" switches on the alarm function. A telegram with the object
value "1" deactivates the function again.
Behavior of the alarm after bus voltage recovery
•Disabled
The alarm function is not activated after a bus voltage recovery, regardless of
the state it had before the bus voltage failure.
•Enabled
After a bus voltage recovery, the alarm function becomes active and the output
is switched to the state that you dened via the parameter Behavior at start of
alarm.
•As before bus voltage failure
The alarm function is brought to the state that was active before the bus voltage
failure. If the alarm function was active, the output is controlled by its settings in
the parameter Behavior at start of alarm.
Priority
The alarm function is a 1-bit group object with high priority. The device safety func-
tion has the highest priority. The priority order for switching can be dened globally
( Priority of functions for switching --> 28 ). The alarm object takes precedence
over the following group objects:
•The priority relative to the locking object / priority object is dened centrally for
switching: Priority of functions for switching --> 28
•Logical input object
•Scene object
•Central switch object
•Staircase x / Staircase variable object
•Switch object
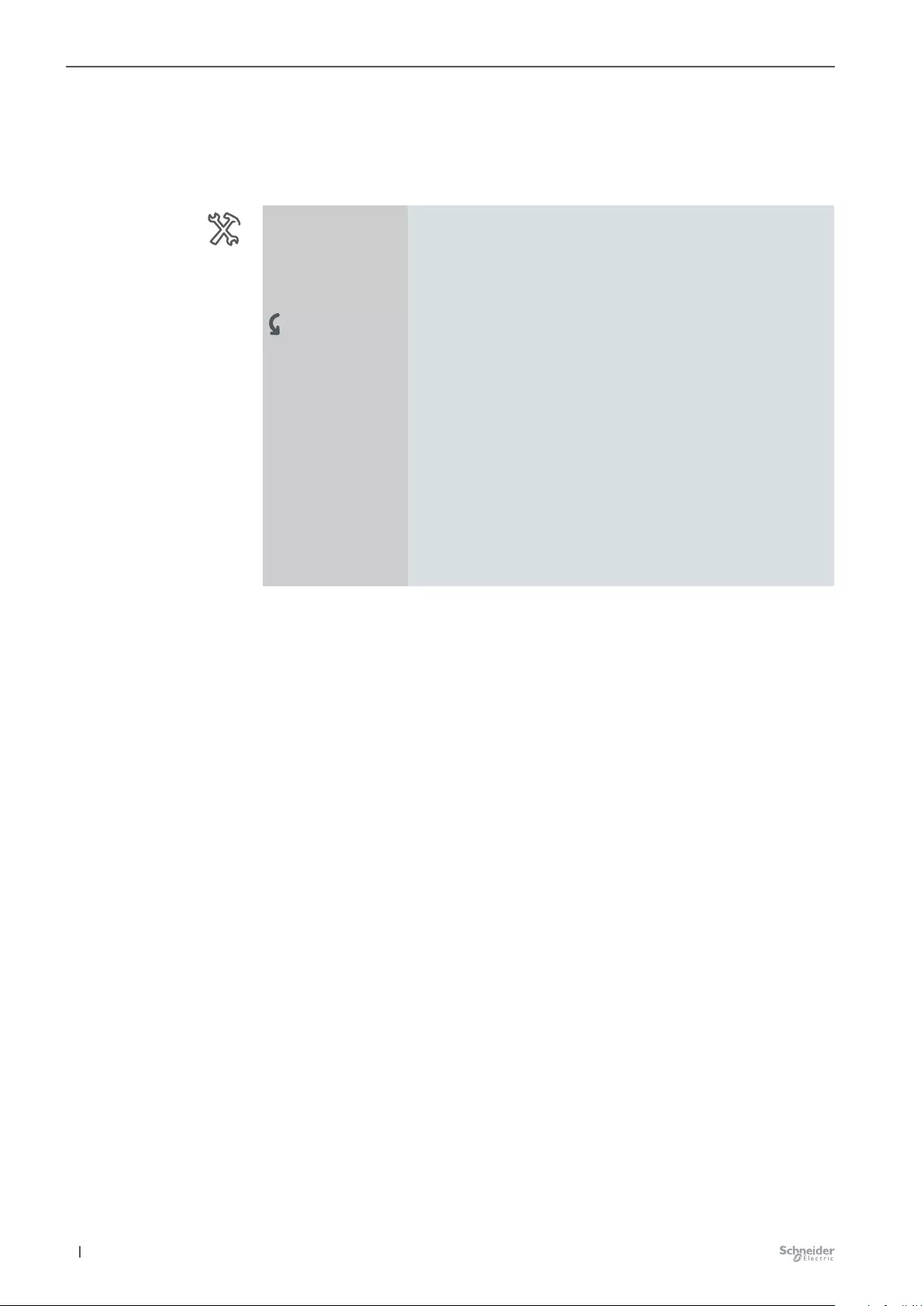
64 05/20-5800/1.0MTN6705-0008 | MTN6805-0008 |
Extended settings for switching Switch Blind 5800/1.0
Failure and download behavior
You can enable this function individually for each switching channel. The behavior
of the switch output in the case of a bus voltage failure / bus voltage recovery and
application download is dened.
Master/Ext. 1/2
Output 1-8 -Switch
-Switching
Failure and download behavior
-Safety and alarm
settings
Failure and download be-
havior Disabled
Enabled
Relay state after bus voltage
failure No reaction
Pressed
Released
Relay state after bus voltage
recovery As before bus voltage failure
Pressed
Released
Relay state at end of down-
load As before download
Pressed
Released
Relay behavior after bus voltage failure
If the bus voltage falls below 18 V, the relay can be switched to a parameterized
state. The relay state can be dened as either pressed or released or remain in the
state it had before the failure (No reaction). At the same time, the current switching
position of the relay is saved in the device.
Possible settings:
•No reaction
The relay contact remains unchanged in its current position. If time functions
(staircase lighting time function, on-delay, o-delay) are currently active, they
are canceled.
•Pressed
In the case of a normally opened contact, the relay is closed; in the case of a
normally closed contact, the relay is opened. Running time functions are deacti-
vated.
•Released
In the case of a normally opened contact, the relay is opened; in the case of a
normally closed contact, the relay is closed. Running time functions are deacti-
vated.
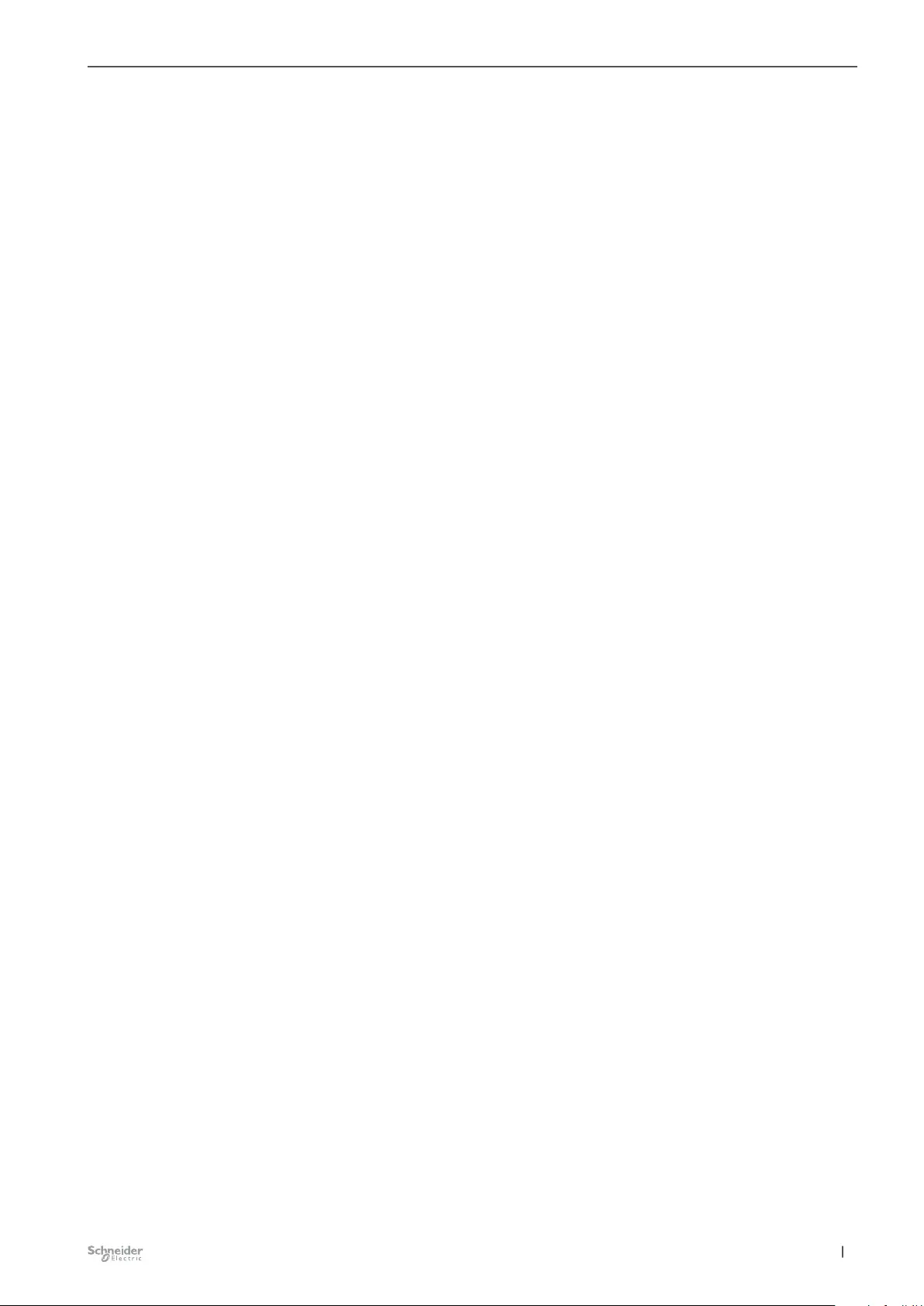
65
05/20-5800/1.0 MTN6705-0008 | MTN6805-0008 |
Extended settings for switching Switch Blind 5800/1.0
Relay behavior after bus voltage recovery
In the case of bus voltage recovery, the relay can adopt a parameterized state.
Possible settings:
•Pressed
In the case of a normally opened contact, the relay is closed; in the case of a
normally closed contact, the relay is opened.
•Released
In the case of a normally opened contact, the relay is opened; in the case of a
normally closed contact, the relay is closed.
•As before bus voltage failure
With the parameter "As before bus voltage failure", the relay adopts the state
that was saved in the device at the time of the bus voltage failure. Any subse-
quent manual switchings are overwritten.
Priority:
The reaction to the behavior set here for bus voltage recovery has a low priority. If a
function with a higher priority is activated for the switching channel directly after bus
voltage recovery, the settings described below apply to these functions.
Relay states caused by higher-priority functions (higher-level function) take prece-
dence over behavior after bus voltage recovery.
Example: OR logic operation with parameterized value of the logic object after bus
voltage recovery = 1, prevails and switches the output.
Behavior after download
After the ETS download, the relay can adopt a parameterized state.
If an internal defect or a faulty download results in a state in which the application
is not operational, the device will not react. The output relays remain in their last
position.
If you wish to activate the behavior after ETS download for an output channel, you
must select a "relay state at end of download" for each channel.
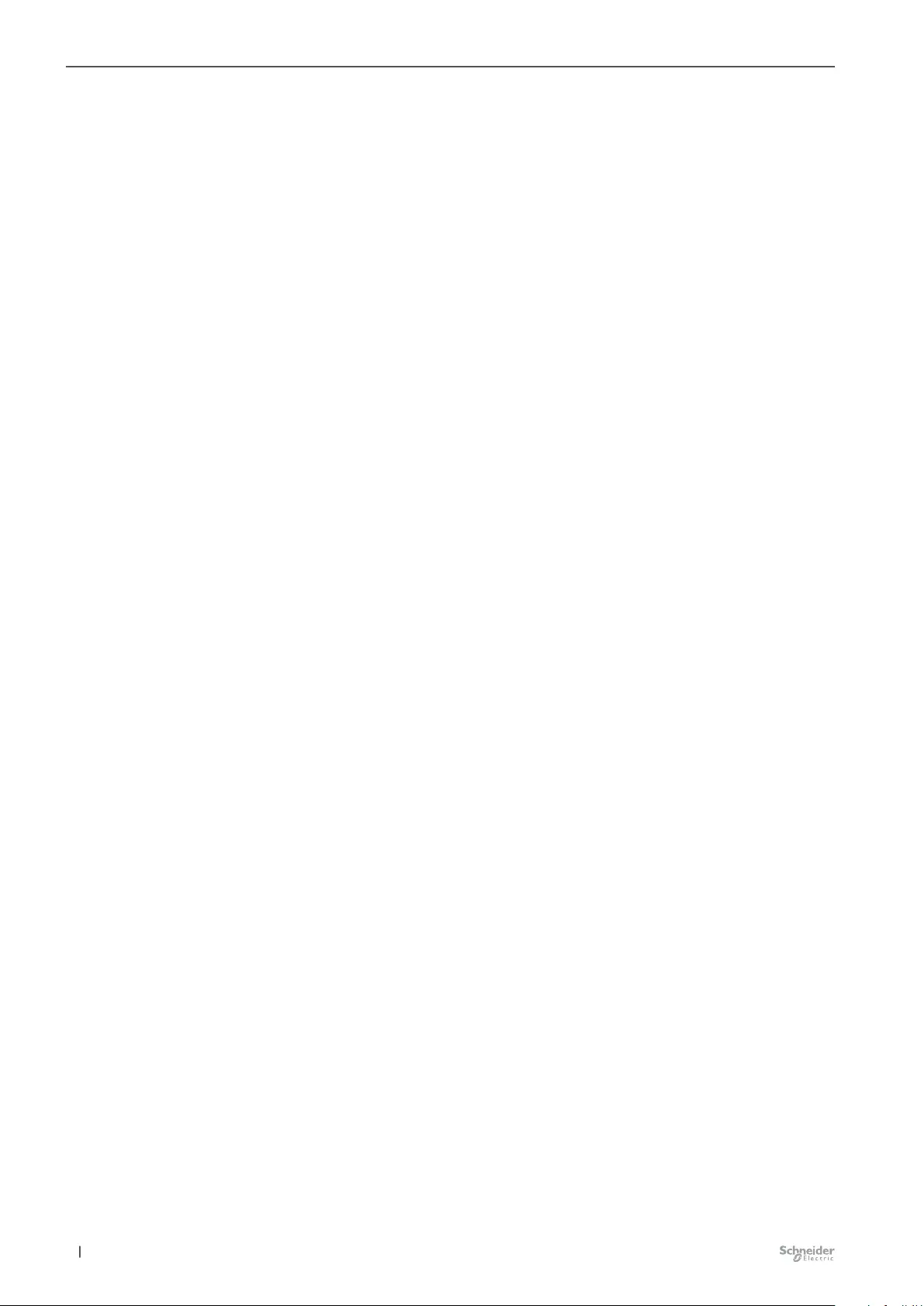
66 05/20-5800/1.0MTN6705-0008 | MTN6805-0008 |
Extended settings for switching Switch Blind 5800/1.0
Possible settings:
•As before download
The relays execute the behavior set before the download. Any subsequent man-
ual switching is overwritten. If a higher-level function (logic operation, priority
control or lock) is active, the behavior you dened for these functions will be
executed.
•Pressed
In the case of a normally opened contact, the relay is closed; in the case of a
normally closed contact, the relay is opened.
•Released
In the case of a normally opened contact, the relay is opened; in the case of a
normally closed contact, the relay is closed.
Priority
Relay states caused by higher-priority functions take precedence over behavior
after ETS download.
Example: OR logic operation with parameterized value of the logic object after bus
voltage recovery = 1, prevails and switches the output.
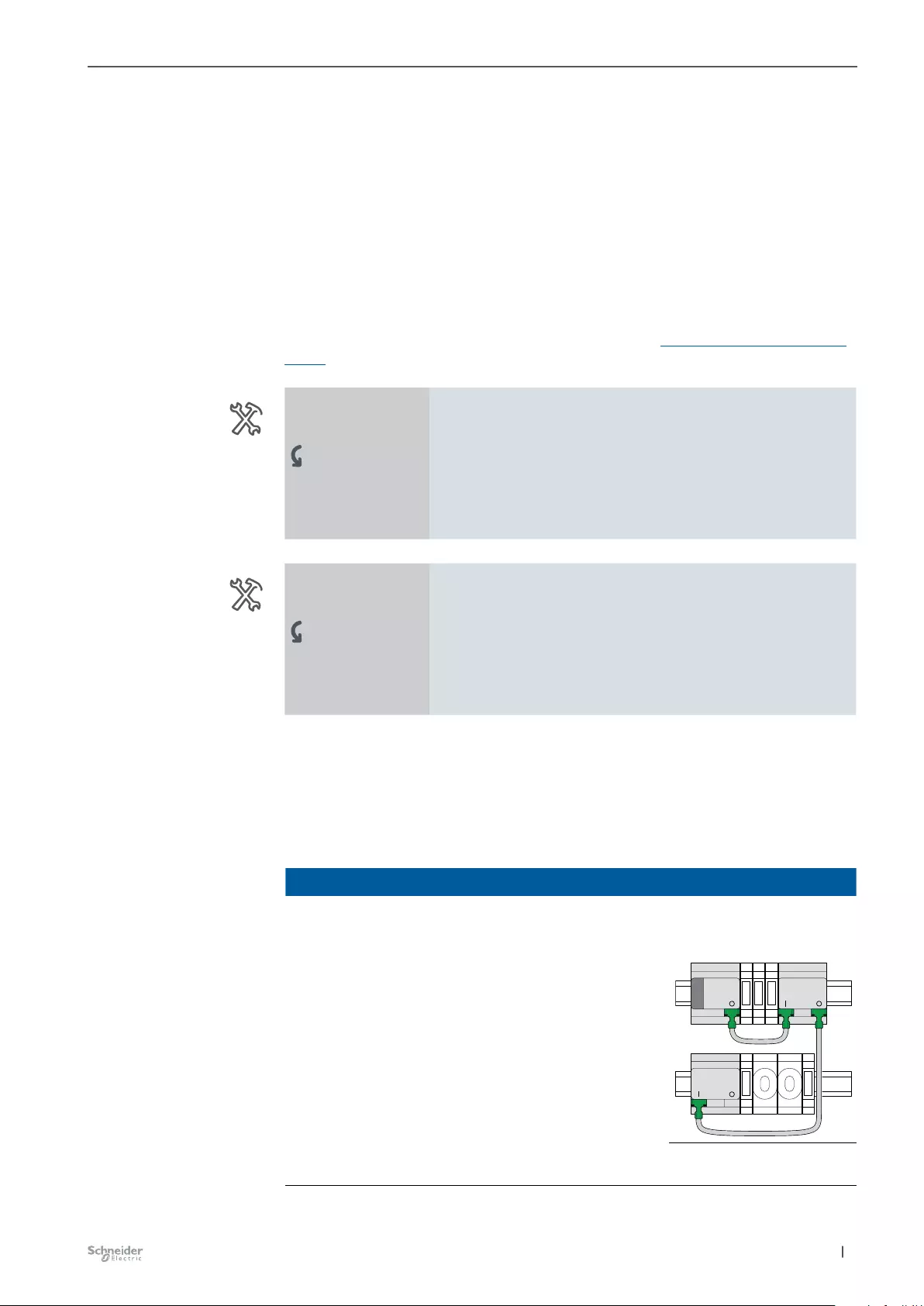
67
05/20-5800/1.0 MTN6705-0008 | MTN6805-0008 |
Express settings for blind / roller shutter Switch Blind 5800/1.0
7 Express settings for blind /
roller shutter
On the Express settings for blind / roller shutter tab, you can set basic settings and
enable or disable other functions.
To control blinds/roller shutters, you can set the channel function of the device to
the operating mode Blind or roller shutter. Now, two outputs will always be merged
into a single blind / roller shutter channel. Please install the drives according to the
installation instructions.
The operating mode is selected for each output on the Dening channel functions
--> 16 tab:
General
settings
Channel function for Master /
Extension 1 / Extension 2
Output 1+2 / 3+4 / 5+6 / 7+8 Blind
Master / Ext. 1/2
Output 1+2 / 3+4 / 5+6
/ 7+8
-Blind
Express settings for blind ...
General
settings
Channel function for Master /
Extension 1 / Extension 2
Output 1+2 / 3+4 / 5+6 / 7+8 Roller shutter
Master / Ext. 1/2
Output 1+2 / 3+4 / 5+6
/ 7+8
-Roller shutter
Express settings for roller shutter ...
Please install the drives according to the installation instructions. When connecting
the motor, note the correct direction of rotation for movement up/down.
There are many dierent blind variants for indoor and outdoor use. The channel en-
ables the control of a blind / roller shutter motor with max. 1000 VA. Only one motor
may be connected per channel. The motor must have an end position switch.
NOTICE
Check before commissioning: The load connections and the order of the
devices (Master -> Extension 1 -> Extension 2) must correspond to your
ETS programming.
•Connect blind motors to the blind channels
specied in the ETS.
•Connect loads to the switching channels
specied in the ETS.
•If the extension is planned as extension 1
(E1), connect it directly to the master.
•If the extension is planned as extension 2
(E2), then connect it to extension 1.
ME
1
E2
An extension cannot be put into operation if the order of the devices does
not correspond to your programming in the ETS.
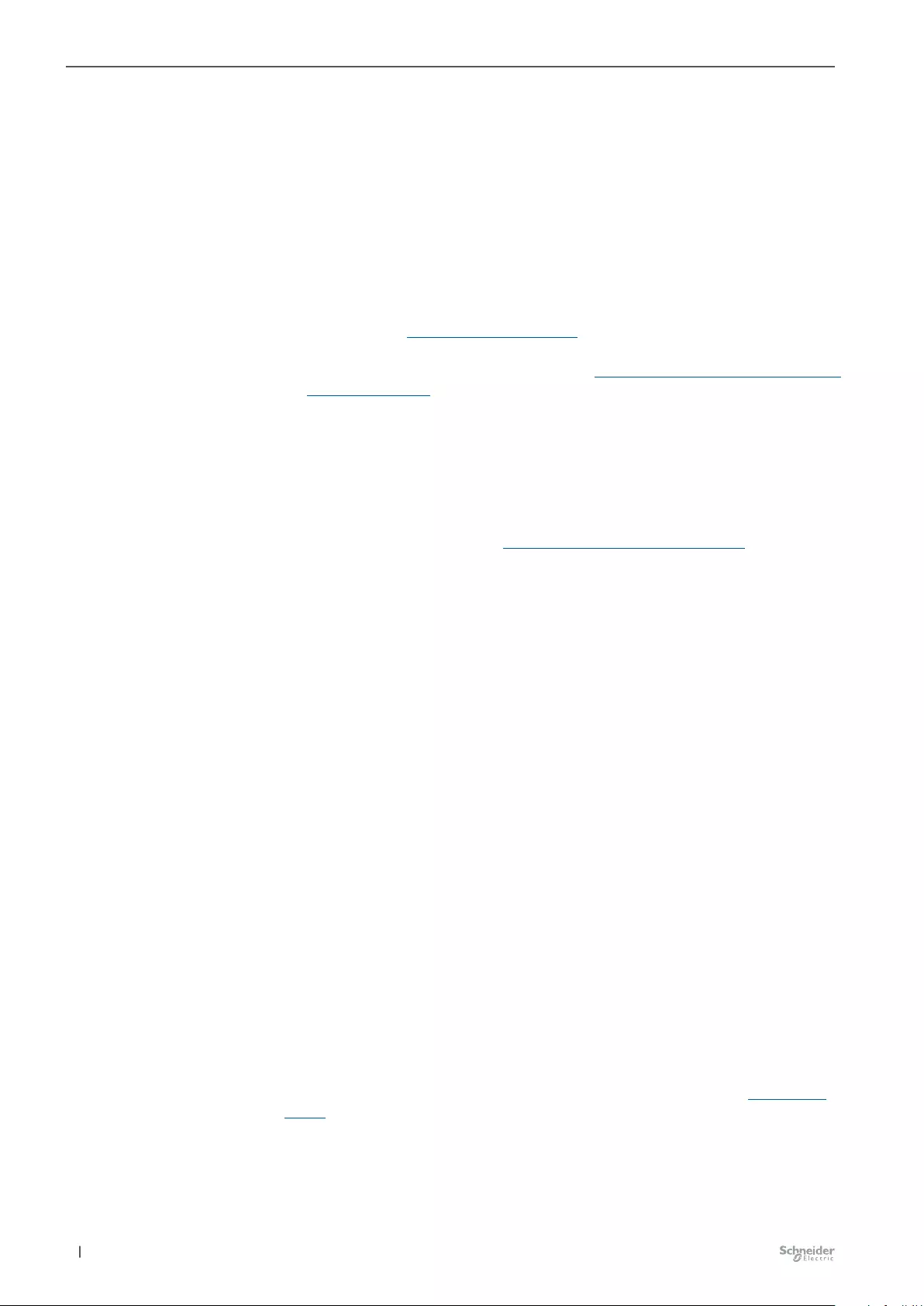
68 05/20-5800/1.0MTN6705-0008 | MTN6805-0008 |
Express settings for blind / roller shutter Switch Blind 5800/1.0
7.1 Blind / roller shutter control
The Express settings can be used to move the connected drive manually to the
desired position. Four group objects are available for this purpose: “Movement in
manual mode” and “Stop/step in manual mode” (for roller shutters: “Stop in manual
mode”). For positioning: “Height position in manual mode” and for blind only “Slat
position in manual mode”.
•Move drive
The object “Movement in manual mode” is responsible for moving the blind or
roller shutter up and down. The drive moves down if the value “1” is received
and up if the value is “0”.
•Running time: Drive running time --> 70
The activated output remains active until the set running time has expired.
•Pause on reverse for change of direction: Pause time before reverting (pause
on reverse) --> 72
If a control command in the opposite direction of motion is received while the
drive is moving, the drive stops and waits for the dened pause on reverse time
before starting to move in the new direction of motion.
•Stop drive
A drive that is in motion is stopped on receiving a bus telegram for the object
Stop/step in manual mode (for roller shutters: “Stop in manual mode”). The val-
ue received for the object is irrelevant here.
•Slat tracking (for blind only): Slat position after movement --> 78
Once the drive has been stopped, the slats will be rotated to the desired posi-
tion according to the settings for the parameter “Slat position after movement”.
•Rotate blind slats (for blind only)
In the case of blinds, the opening angle of the slats can be adjusted gradually
using the object “Stop/step in manual mode”. For this, the drive must be at rest.
If the group object receives the object value “1”, the slats are closed by one
step; if the value “0” is received, they are opened.
If a step command is executed and the slats reach one of their movement range
limits or are already in a limit position, the drive will briey move in the desired
direction. The duration of this motion also corresponds to the set step time.
If the direction is changed from one step command to the next, the device will
once again observe the pause on reverse as the wait time between the steps.
Manually moving to the height position and slat opening angle (blind) using
absolute position commands
With this function, you can set a height position for blinds / roller shutters and the
slat opening angle for blinds directly and manually using a percentage value. The
desired percentage value always refers to the possible movement range 0-100%
that you have set by dening the running times. You thus set an absolute height
position for the entire movement range.
After receiving a new positional value, the device calculates a proportional travel
time from the current position and the new desired position and moves the drive in
the corresponding direction of motion for the duration of this travel time. The new
position is buered again. The accuracy of the position settings depends on the
accuracy of your drive running time settings.
After a number of positioning movements, there are slight deviations between the
actual position and the calculated position for physical and mechanical reasons.
You can reset these deviations by means of reference movements “Calibration
--> 98”.
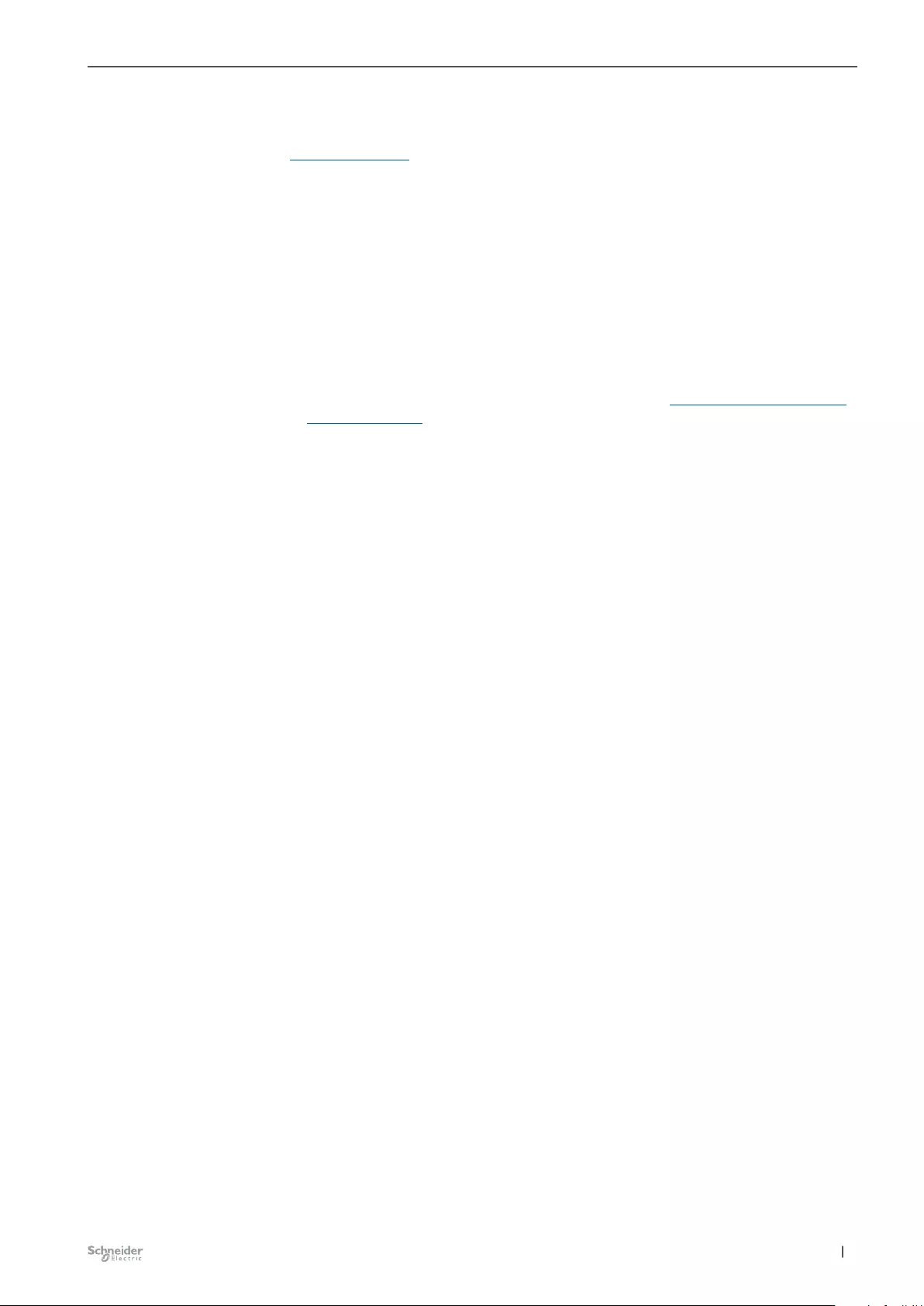
69
05/20-5800/1.0 MTN6705-0008 | MTN6805-0008 |
Express settings for blind / roller shutter Switch Blind 5800/1.0
If a reference movement is required before a new positioning movement, the
device initiates it before the movement to the new command position (see section
“Calibration --> 98”).
The group objects “Height position in manual mode” and “Slat position in manual
mode” (for blind only) are available for setting the absolute positional values.
•Set height position
The object Height position in manual mode is responsible for the height posi-
tion of the blind or roller shutter. Limit position 0% means that the blind / roller
shutter is at the top. Limit position 100% means that the blind / roller shutter is
at the bottom.
•Rotate slats to opening position (for blind only)
You can use the object “Slat position in manual mode” to set the slat opening
angle directly. In slat position 0%, the slats are horizontally open, or closed at
the top, while 100% means they are closed at the bottom. The actual opening
angle of the slats depends on the type of blind used. Setting the blind type (for
blind only) --> 74
When a new positional value is received, the channel calculates a running time
needed to reach the new position from the current position. The drive is then
moved to the new position for the calculated duration. The direction of motion is
derived from the calculation. If the device receives a new positional value during a
positioning movement and the calculation results in the same direction of motion,
the drive continues moving to the new command position.
•Pause on reverse for change of direction
If a new positioning command is received during a drive motion or slat adjust-
ment and the calculation results in the opposite direction of motion, the drive
stops and waits for the dened pause on reverse time before starting the new
positioning movement.
•Slat tracking (for blind only)
If the height position of the blind is changed and the blind reaches the desired
position, the slat tracking function is executed and the slats are rotated to the
desired position.
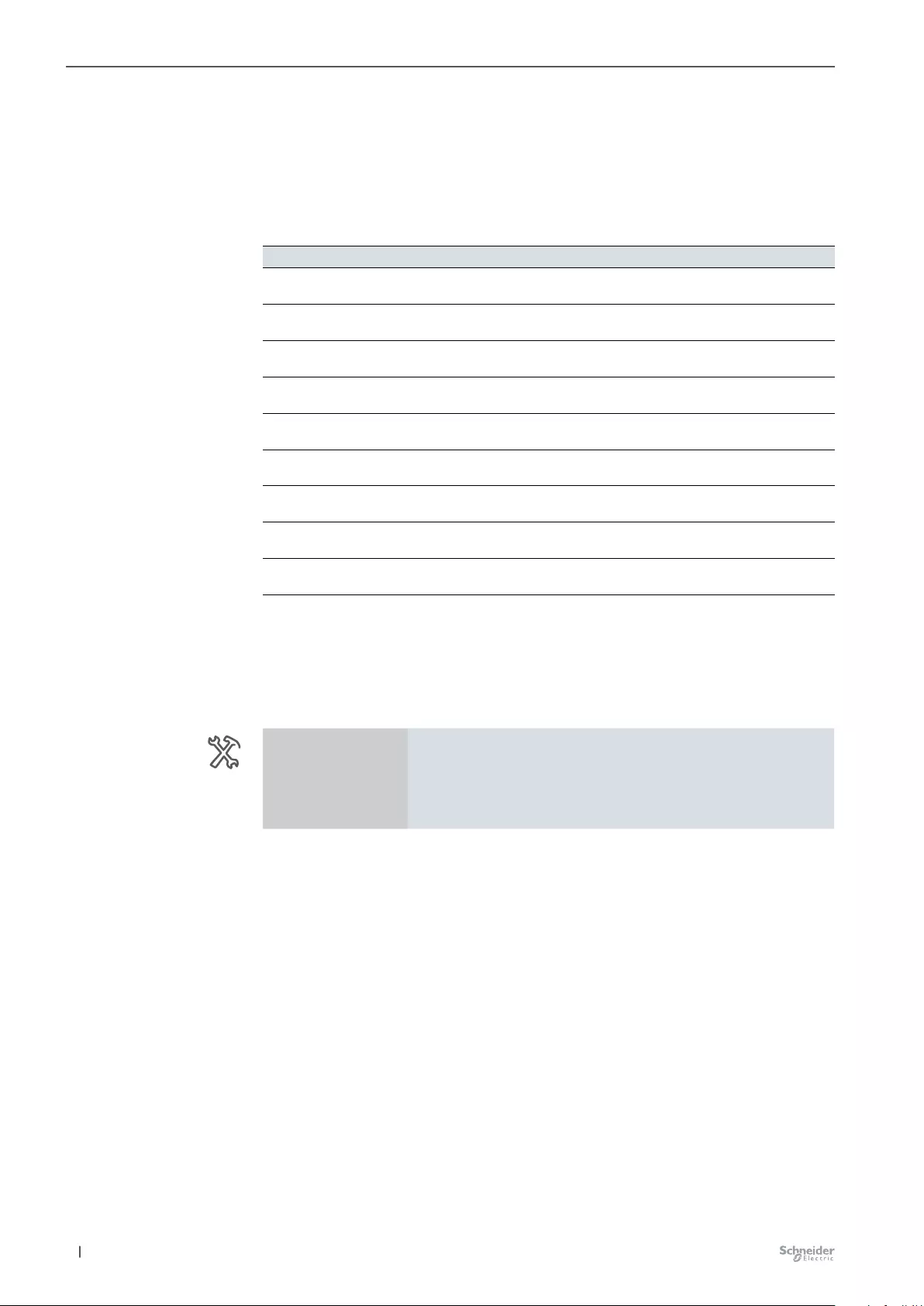
70 05/20-5800/1.0MTN6705-0008 | MTN6805-0008 |
Express settings for blind / roller shutter Switch Blind 5800/1.0
If, for example, you select the channel function Blind / roller shutter for output 1+2
on the master, an ETS channel with the name Master Output 1+2 - blind / roller
shutter + name of the channel is generated. All the group objects for this channel
are located here.
Group objects
No. Name Object function Length Behavior Data Type
31 Master Output 1+2
name of the channel
Movement in manual
mode
1 bit Received 1.008 Up/DOWN
32 Master Output 1+2
name of the channel
Stop/step in manual
mode (blind)
1 bit Received 1.007 Step
32 Master Output 1+2
name of the channel
Stop in manual mode
(roller shutter)
1 bit Received 1.007 Step
33 Master Output 1+2
name of the channel
Height position in
manual mode
1 byte Received 5.001 Percent
(0...100%)
34 Master Output 1+2
name of the channel
Slat position in manual
mode (blind)
1 byte Received 5.001 Percent
(0...100%)
46 Master Output 1+2
name of the channel
Feedback for height 1 byte Sending 5.001 Percent
(0...100%)
47 Master Output 1+2
name of the channel
Feedback for slat
(blind)
1 byte Sending 5.001 Percent
(0...100%)
51 Master Output 1+2
name of the channel
Feedback for moving 1 bit Sending 1.010 Start/Stop
52 Master Output 1+2
name of the channel
Feedback for last
direction
1 bit Sending 1.008 Up/DOWN
7.2 Name of the channel
You can assign a separate name for each channel, e.g. “Blind Kitchen”. The name
of the channel now appears on the parameters, channels and associated group
objects.
Master / Ext. 1/2
Output 1+2 / 3+4 / 5+6
/ 7+8
-Blind / roller shutter
Express settings for blind / roller shutter
Name of the channel Blind Kitchen
7.3 Drive running time
The individual running times for the blind / roller shutter can be determined very
well with a stopwatch.
If the running times to be set are too short to be measured with the stopwatch, rst
set an approximate value. Test the behavior of the drive or of the slats by means of
positioning commands (for blind only). If the desired positions are not fully reached,
correct the running times upwards. If the positions are overshot, correct the running
times downwards. Check your corrections with new positioning commands. Per-
form multiple tests, as the small deviations only become visible or detectable after
several motions.
In addition to the aforementioned deviations, environmental factors (temperature,
rain, etc.) also cause deviations in the motion behavior of the drives. Since the
drives cannot signal their current position and the current position is always calcu-
lated, the channel cannot detect these deviations. In order to be able to continue
to position the drive accurately, it is helpful to return the drives to a xed starting
position by means of regular reference movements. In this way you can achieve
satisfactory positional accuracy for a long time.
Group objects for express set-
ting for blind
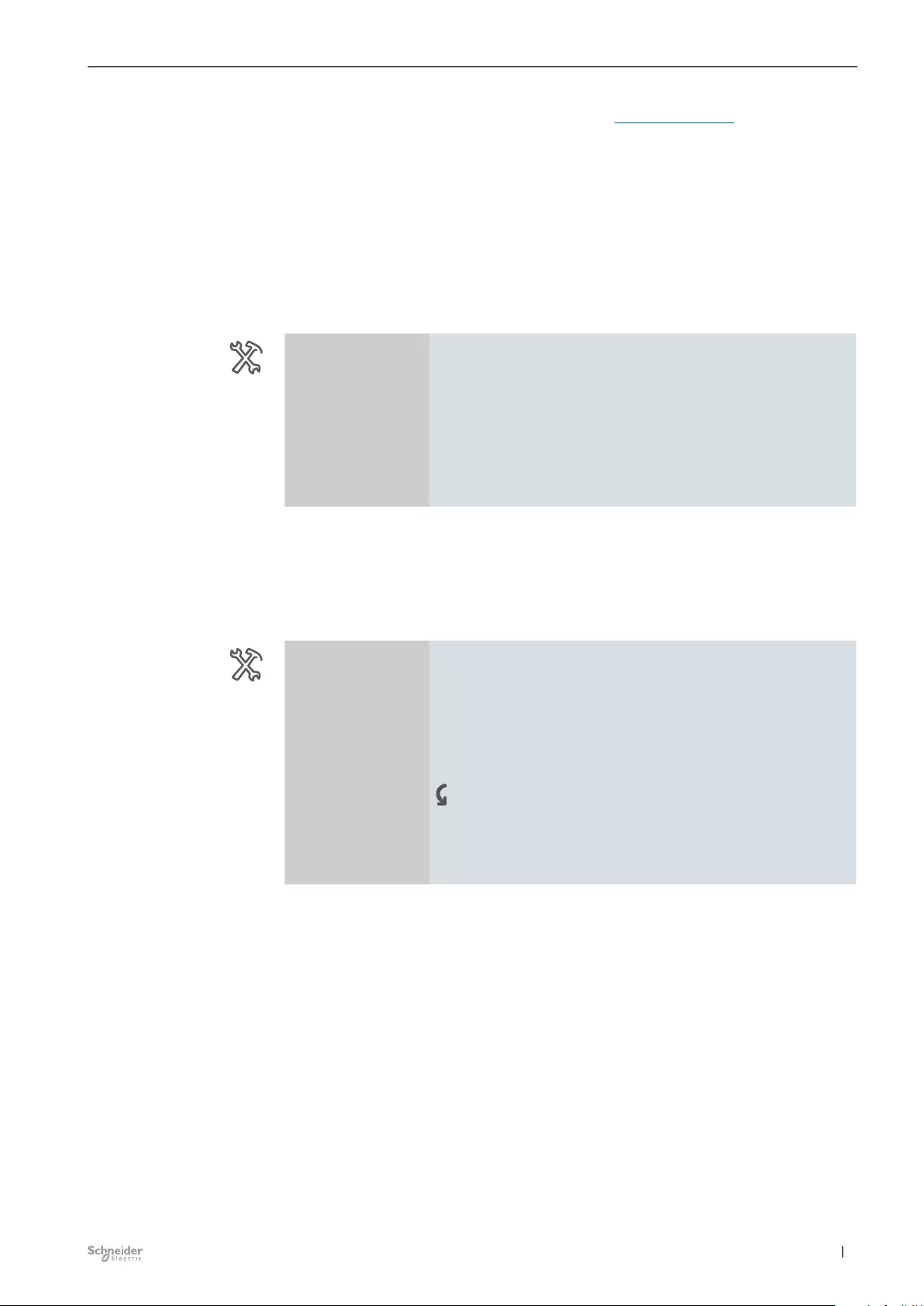
71
05/20-5800/1.0 MTN6705-0008 | MTN6805-0008 |
Express settings for blind / roller shutter Switch Blind 5800/1.0
Further information can be found in the section “Calibration --> 98”.
The factory setting for the running time is 2 minutes, with up and down movement
parameterized the same.
This duration is required for the drive to move from one end position (blind / roll-
er shutter is fully open or fully closed) to the opposite end position. After the set
running time, the relay of the corresponding channel is automatically switched o
(even if the drive has not yet reached its end position with the values set here). If
necessary, check whether the drive manufacturer has provided information about
running times.
Same running times for up and down
Master / Ext. 1/2
Output 1+2 / 3+4 / 5+6
/ 7+8
-Blind / roller shutter
Express settings for blind / roller shutter
Blind control / roller shutter control
Use same time for up and
down Yes
Up/Down time
(5s...99:59.9 min) 02:00.0
Different running times for up and down
If the parameter Use same time for up and down is deactivated, dierent running
times can be set for up and down. The Running time: Up should be parameterized
slightly longer so that the end stops are always reached, even in the case of low
temperatures or a heavy blind / roller shutter.
Master / Ext. 1/2
Output 1+2 / 3+4 / 5+6
/ 7+8
-Blind / roller shutter
Express settings for blind / roller shutter
Blind control / roller shutter control
Use same time for up and
down No
Up time
(5s...99:59.9 min) 02:00.0
Down time
(5s...99:59.9 min) 02:00.0
The Running time: Up should be parameterized slightly longer so that the end
stops are always reached, even in the case of low temperatures or a heavy blind /
roller shutter.
This type of running time allowance should be taken into account due to the
physical fact that drives take longer for upward movements than for downward
movements due to the eect of gravity on the blind / roller shutter. Since this time
deviation can be very short, you have to execute multiple movements to become
aware of this behavior. It is useful to move the drive from 10% to 90% and back to
10% several times. If you notice that the drive does not completely reach the upper
end position after these movements, you can increase the “Running time: Up”.
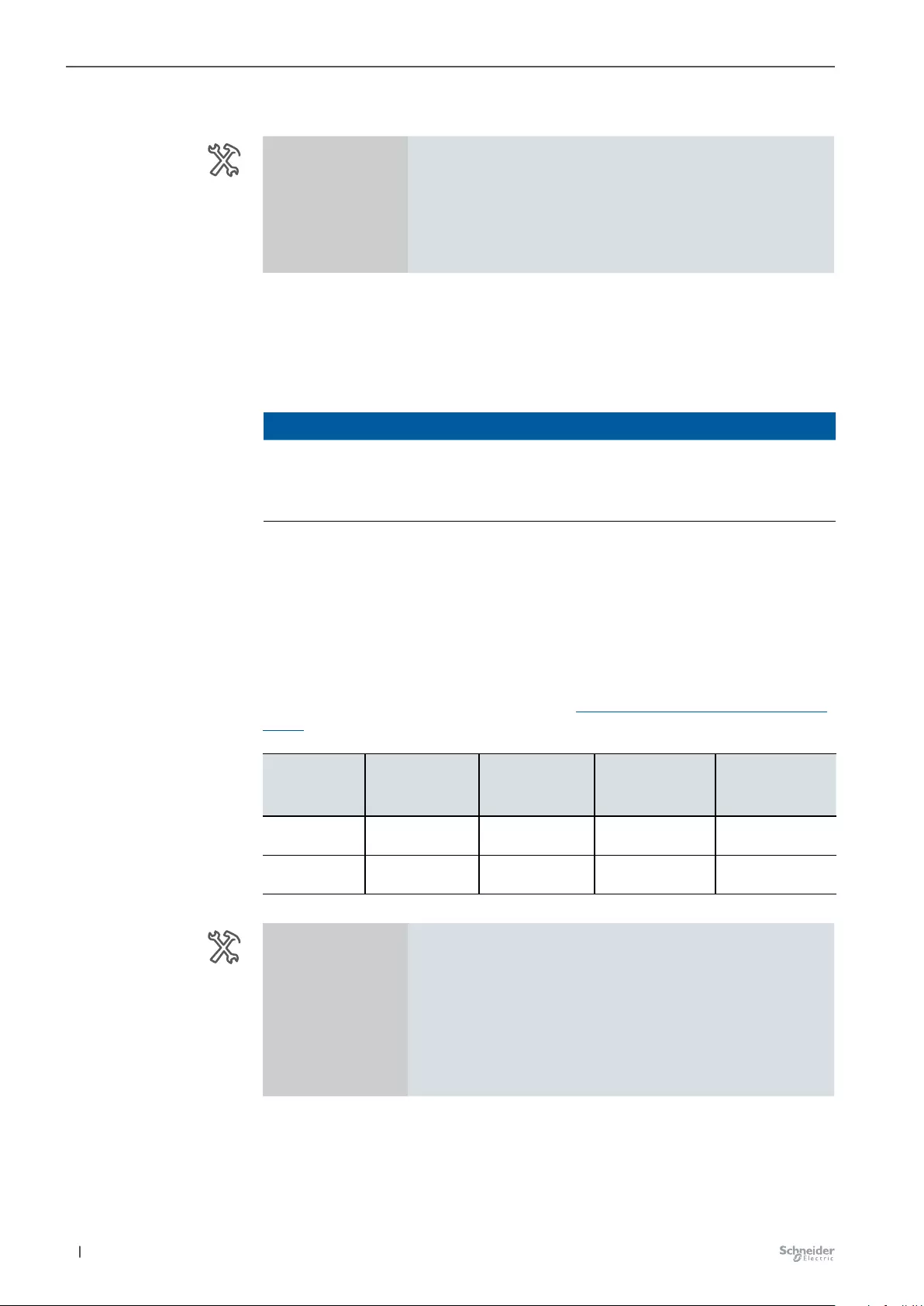
72 05/20-5800/1.0MTN6705-0008 | MTN6805-0008 |
Express settings for blind / roller shutter Switch Blind 5800/1.0
Pause time before reverting (pause on reverse)
Master / Ext. 1/2
Output 1+2 / 3+4 / 5+6
/ 7+8
-Blind / roller shutter
Express settings for blind / roller shutter
Blind control / roller shutter control
Pause time before reverting
(2...255, unit = 100 ms) 5
If the channel for a drive that is currently in motion receives a motion command in
the opposite direction, it rst turns o both output relays for this channel. Before
turning on the relay for the new direction of motion, it waits for the set Pause time
before reverting.
The channel observes the pause on reverse even if it is to rotate the slats in dier-
ent directions when executing two step commands (for blind only).
NOTE
The drive may be damaged.
•The drive may be damaged if the pause times are too short. Be sure to
refer to the specications in the data sheet of the drive manufacturer
when setting the values.
7.4 Slat control (for blind only)
Slat rotation time
The Slat rotation time is the time during which the slat performs a complete move-
ment from 0% to 100% (or vice versa). The adjustment range for the opening
angle is dependent on the type of blind used. Setting the blind type (for blind only)
--> 74
Blind type:
Downwards
closed / upwards
horizontal
Blind type: Down-
wards tilted / up-
wards horizontal
Blind type: Down-
wards closed /
upwards closed
Blind type:
Downwards tilted /
upwards closed
Slat position
0 %
Horizontal
open
Horizontal
open
Top
closed
Top
closed
Slat position
100 %
Bottom
closed
Bottom
closed
Bottom
closed
Bottom
closed
Master / Ext. 1/2
Output 1+2 / 3+4 / 5+6
/ 7+8
-Blind
Express settings for blind
Slat control
Slat rotation time (open/
closed) (0.1 s...25 s) 01:00
Steps that shall be executed
during slat rotation (1...10) 10
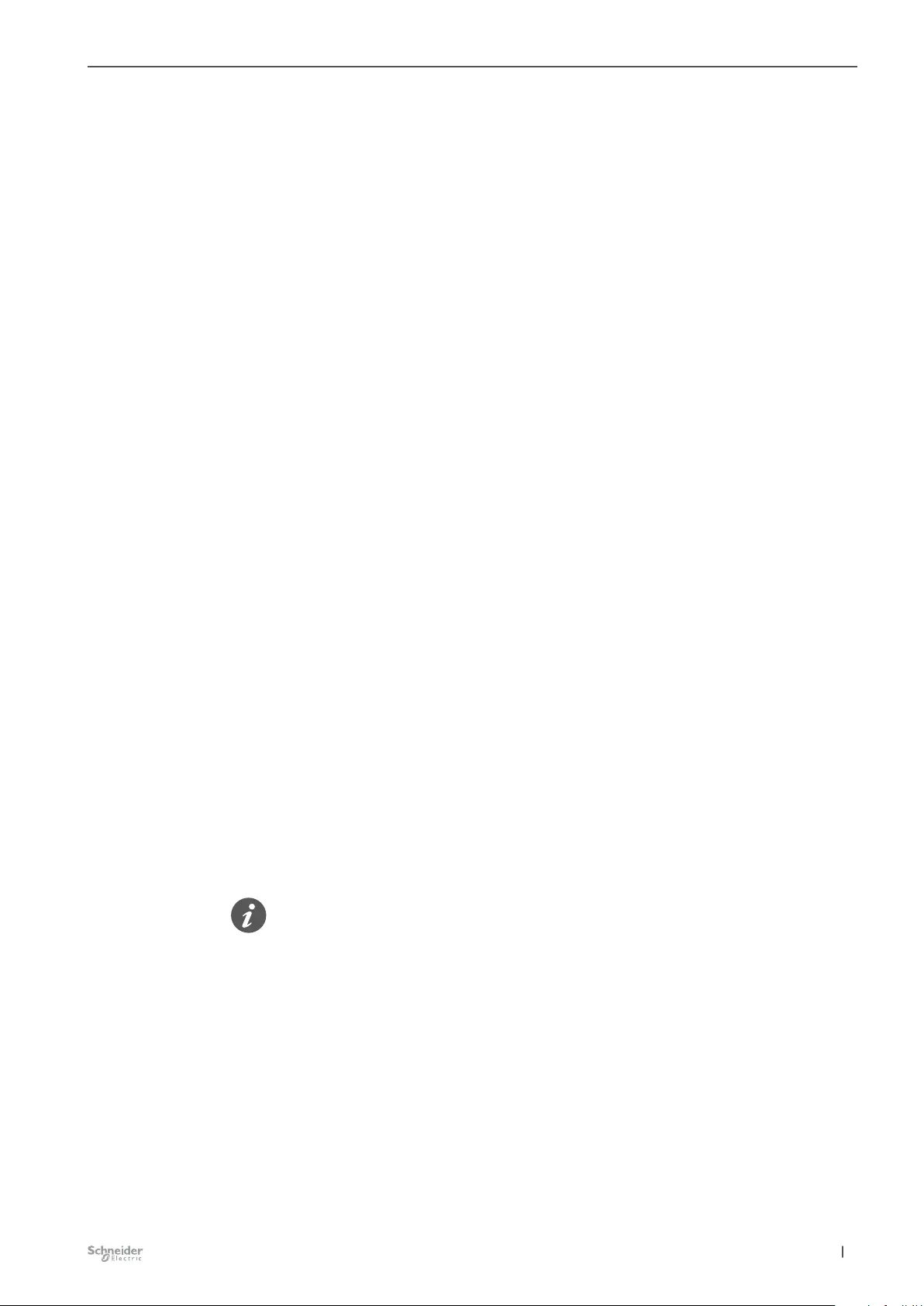
73
05/20-5800/1.0 MTN6705-0008 | MTN6805-0008 |
Express settings for blind / roller shutter Switch Blind 5800/1.0
If the slat rotation time to be set is too short to be measured with the stopwatch,
rst set an approximate value. Test it by sending step telegrams.
Step commands can be used to rotate the blind slats. The opening angle of the
slats can be changed in small steps, e.g. to prevent dazzle caused by a change in
the position of the sun.
Depending on the Slat rotation time in one direction of motion, you can use the step
time to provide the user with a certain number of steps for opening or closing the
slats. The number of possible steps varies with the slat running time.
If the slat running time is 2.5 s, for example, you have a maximum of 15 steps
available for moving through the entire slat opening range in one direction (2.5 s /
166 ms = 15 steps).
If you only wish to provide the user with 5 slat steps in this case:
2.5 s / 5 steps = 0.5 s step time
Procedure for measuring short slat running times:
•Set an approximate time and select a large number of steps. This results in the
step time. Example: Slat running time = 1 s;
Number of steps = 10; => Step time = 100 ms.
•Move the slats to the closed position (slat position 100%). For blind types with
operating position, this is the lower end position.
•Count step commands: now send step commands until the blind moves up-
wards, and count the steps required.
•Example: The blind requires 5 steps to move through the slat adjustment range.
With the sixth step, the blind moves upwards.
•With the set values for the step time (default step time: 100 ms), the following
slat running time is calculated: 100 ms x 5 steps = 0.5 s.
•You can now enter this value as the slat running time.
Procedure for measuring long slat running times:
•Move the slats to the closed position (slat position 100%). For blind types with
operating position, this is the lower end position.
•Now send an “Up” motion command.
•Before opening the blind, the drive rotates the slats into the open position (0%).
•Measure the time for this rotation.
•Stop the drive after the rotation.
•For blind type: Downwards tilted / upwards horizontal and blind type: Down-
wards tilted / upwards closed (with operating position), note that the closed slat
position is only set in the lower end position. You must then also add the time for
the rotation from the operating position to the closed position.
Note:
For blinds types 1 and 3 (without operating position), your setting for the slat run-
ning time aects the opening angle after a movement, since the selected opening
angle (percentage value for the automatic slat position) is converted into a propor-
tional rotation time for the slats. The same applies to the slat tracking function after
a movement.
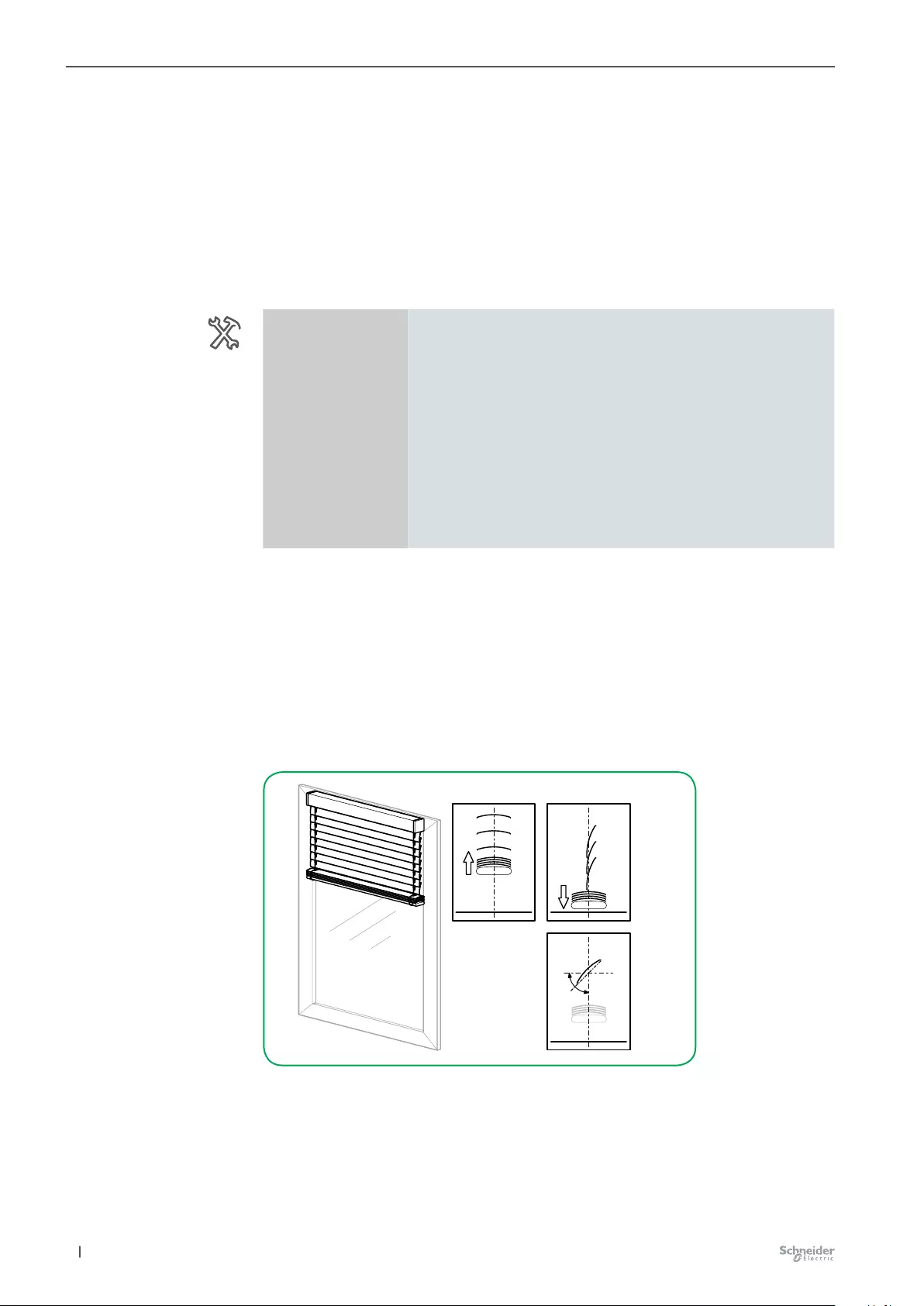
74 05/20-5800/1.0MTN6705-0008 | MTN6805-0008 |
Express settings for blind / roller shutter Switch Blind 5800/1.0
Setting the blind type (for blind only)
If you wish to program the slat control for a blind, you should dene your blind type
before starting the parameterization.
The application distinguishes between four dierent types of blinds, which you can
recognize by the position of their slats during the movement. Two of these types
have a mechanically dened operating position. They can be recognized seen from
the tilted slat position during a downward movement. The operating position limits
the possible opening angle of the slats, unless the blind is in its lower end position.
This is done using the parameter Movement of the existing blind.
Master / Ext. 1/2
Output 1+2 / 3+4 / 5+6
/ 7+8
-Blind
Express settings for blind
Slat control
Movement of the existing
blind
Downwards closed / upwards horizon-
tal
Downwards tilted / upwards horizontal
Downwards closed / upwards closed
Downwards tilted / upwards closed
Blind type: Downwards closed / upwards horizontal
(Without operating position)
•Upward movement: Slats in horizontal open position
(slat position 0%)
•Downward movement: Slats closed downwards
(slat position 100%)
•Possible adjustment range for the opening angle of the slats: 0-100%
Downwards closed / upwards horizontal
0 %
100 %
50 %
100 %
0 %
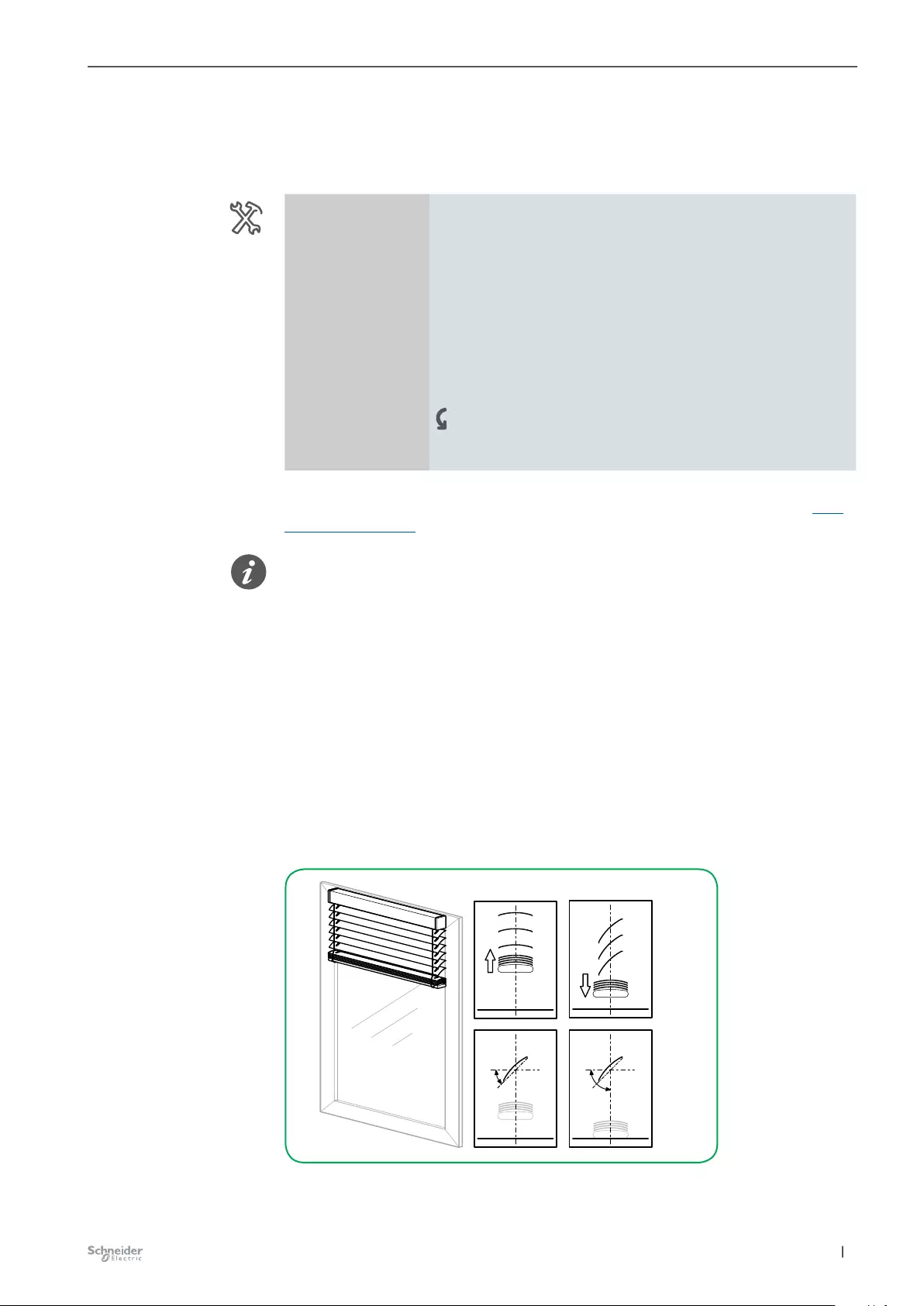
75
05/20-5800/1.0 MTN6705-0008 | MTN6805-0008 |
Express settings for blind / roller shutter Switch Blind 5800/1.0
The parameter Slat position after movement in % allows you to dene the behavior
of the slats after a movement for the channel. If you set the parameter to Operat-
ing position, you can set an opening angle to be adopted by the slats after every
downward movement.
Master / Ext. 1/2
Output 1+2 / 3+4 / 5+6
/ 7+8
-Blind
Express settings for blind
Slat control
Movement of the existing
blind
Downwards closed / upwards horizon-
tal
Slat position after movement
in % Last slat position
No reaction
Operating position
Operating position of slat in % 50
The preset value of 50% corresponds to a slat opening angle of about 45°. Since
this position is set on a time-controlled basis, please refer also to the section Slat
rotation time --> 72
Note:
Unless otherwise indicated in the following instructions, the examples refer to this
type of blind.
Blind type: Downwards tilted / upwards horizontal
(with operating position)
•Upward movement: Slats in horizontal open position
(slat position 0%)
•Downward movement: Slats tilted down in the operating position
(slat position in operating position)
•Possible adjustment range for the opening angle of the slats:
0% to the operating position if blind not in lower end position
0-100% if blind in lower end position
Downwards tilted / upwards horizontal
0 %
0 %
100 %
0 %
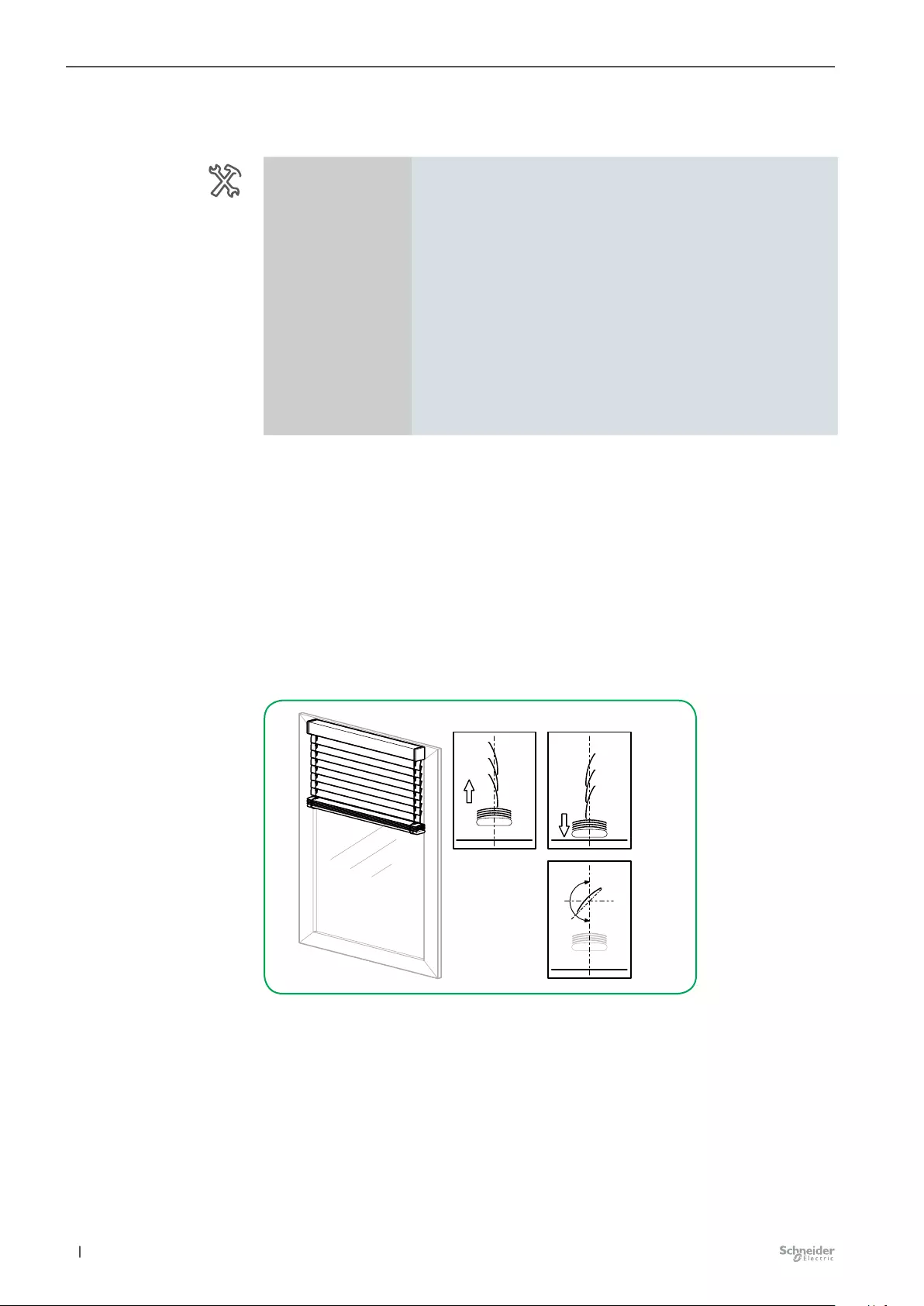
76 05/20-5800/1.0MTN6705-0008 | MTN6805-0008 |
Express settings for blind / roller shutter Switch Blind 5800/1.0
The parameter Slat position after movement in % allows you to dene the behavior
of the slats after a movement for the channel.
Master / Ext. 1/2
Output 1+2 / 3+4 / 5+6
/ 7+8
-Blind
Express settings for blind
Slat control
Movement of the existing
blind Downwards tilted / upwards horizontal
Slat position after movement
in % Last slat position
No reaction
Operating position
Existing slat position during
downwards movement in % 50
You can use the parameter Existing slat position during downwards movement in
% to set the opening angle for the operating position.
Blind type: Downwards closed / upwards closed
(without operating position)
•Upward movement: Slats closed upwards
(slat position 0%)
•Downward movement: Slats closed downwards
(slat position 100%)
•Possible adjustment range for the opening angle of the slats 0-100%
Downwards closed / upwards closed
0 %
100 %
0 %
100 %
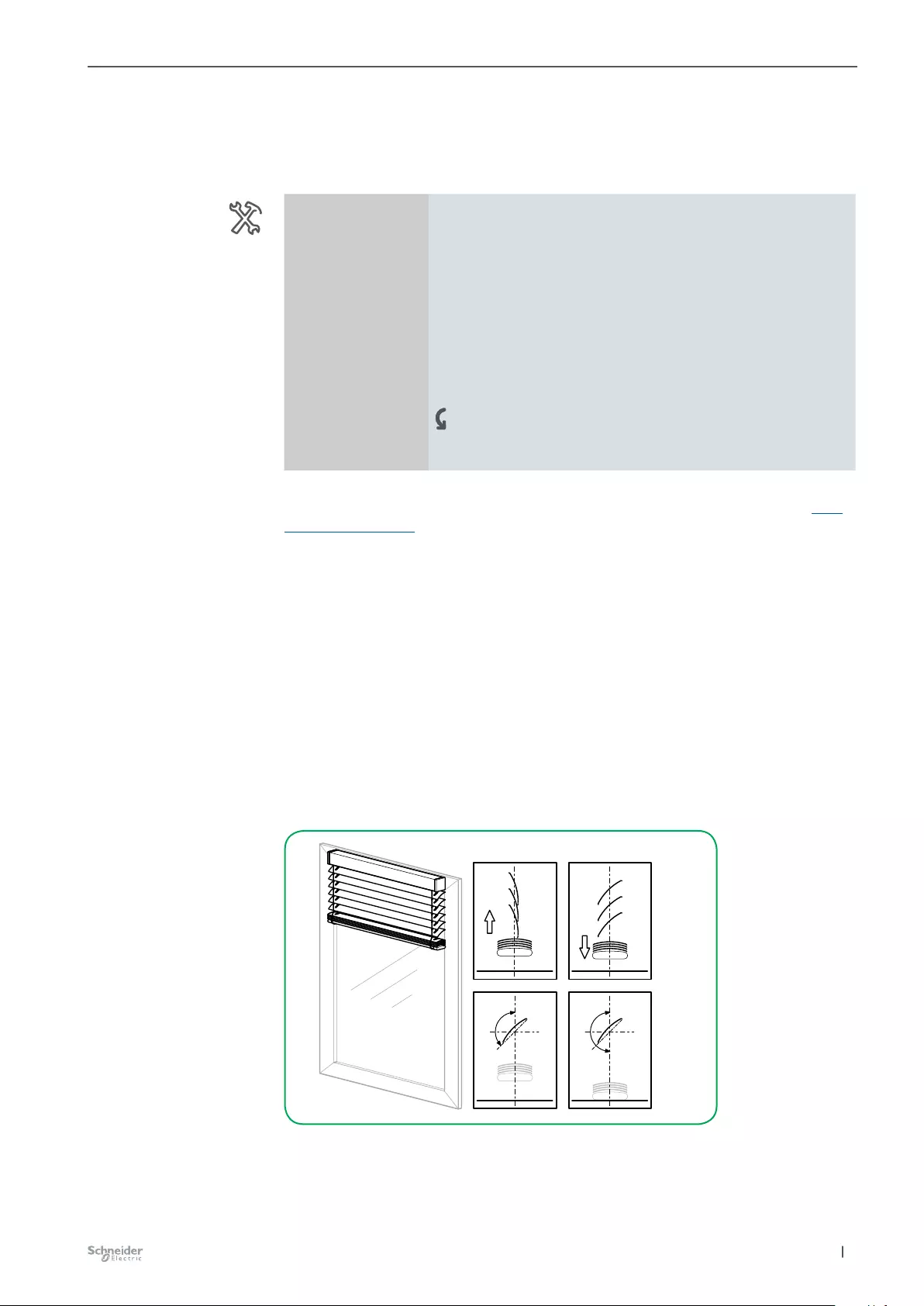
77
05/20-5800/1.0 MTN6705-0008 | MTN6805-0008 |
Express settings for blind / roller shutter Switch Blind 5800/1.0
The parameter Slat position after movement in % allows you to dene the behavior
of the slats after a movement for the channel. If you set the parameter to Operat-
ing position, you can set an opening angle to be adopted by the slats after every
downward movement.
Master / Ext. 1/2
Output 1+2 / 3+4 / 5+6
/ 7+8
-Blind
Express settings for blind
Slat control
Movement of the existing
blind Downwards closed / upwards closed
Slat position after movement
in % Last slat position
No reaction
Operating position
Operating position of slat in % 75
The preset value of 75% corresponds to a slat opening angle of about 45°. Since
this position is set on a time-controlled basis, please refer also to the section Slat
rotation time --> 72
Blind type: Downwards tilted / upwards closed
(with operating position)
•Upward movement: Slats closed upwards
(slat position 0%)
•Downward movement: Slats tilted down in the operating position
(slat position in operating position)
•The slats are closed on reaching the lower end position
(slat position 100%)
•Possible adjustment range for the opening angle of the slats:
0% to the operating position if blind not in lower end position
0-100% if blind in lower end position
Downwards tilted / upwards closed
0 %
0 % 0 %
100 %
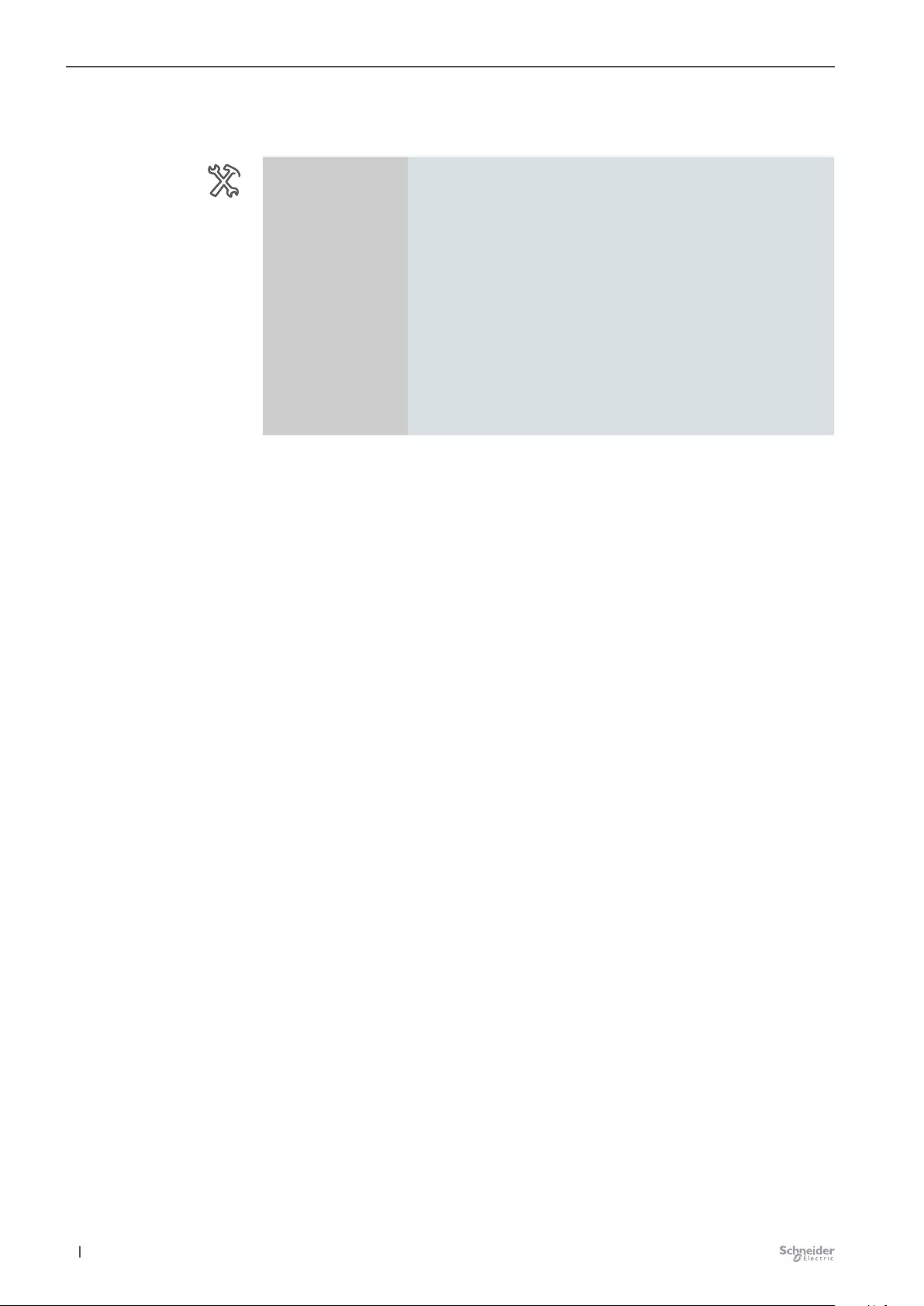
78 05/20-5800/1.0MTN6705-0008 | MTN6805-0008 |
Express settings for blind / roller shutter Switch Blind 5800/1.0
The parameter Slat position after movement in % allows you to dene the behavior
of the slats after a movement for the channel.
Master / Ext. 1/2
Output 1+2 / 3+4 / 5+6
/ 7+8
-Blind
Express settings for blind
Slat control
Movement of the existing
blind Downwards tilted / upwards closed
Slat position after movement
in % Last slat position
No reaction
Operating position
Existing slat position during
downwards movement in % 75
You can use the parameter Existing slat position during downwards movement in %
to set the opening angle for the operating position.
Slat position after movement
With every blind movement, the position of the slats also changes, depending on
the direction of motion. After the movement, the slats stay in this new position.
With this application, however, you can automatically move or reset the slats to a
desired position after a movement.
Using the parameter “Slat position after movement”, you can dene the behavior of
the slats after a movement for each blind channel.
The following parameters are available for this:
•No reaction (stay in the current position)
•Operating position (move to operating position)
•Last slat position (move to the slat opening angle that the blind had before the
start of the movement)
The slat opening angle you have dened is set after each positioning movement of
the blind or after a manual motion command terminated by a stop telegram.
After a bus voltage failure or a download, the last slat position is not clearly dened,
so the last slat position is assumed to be the operating position.
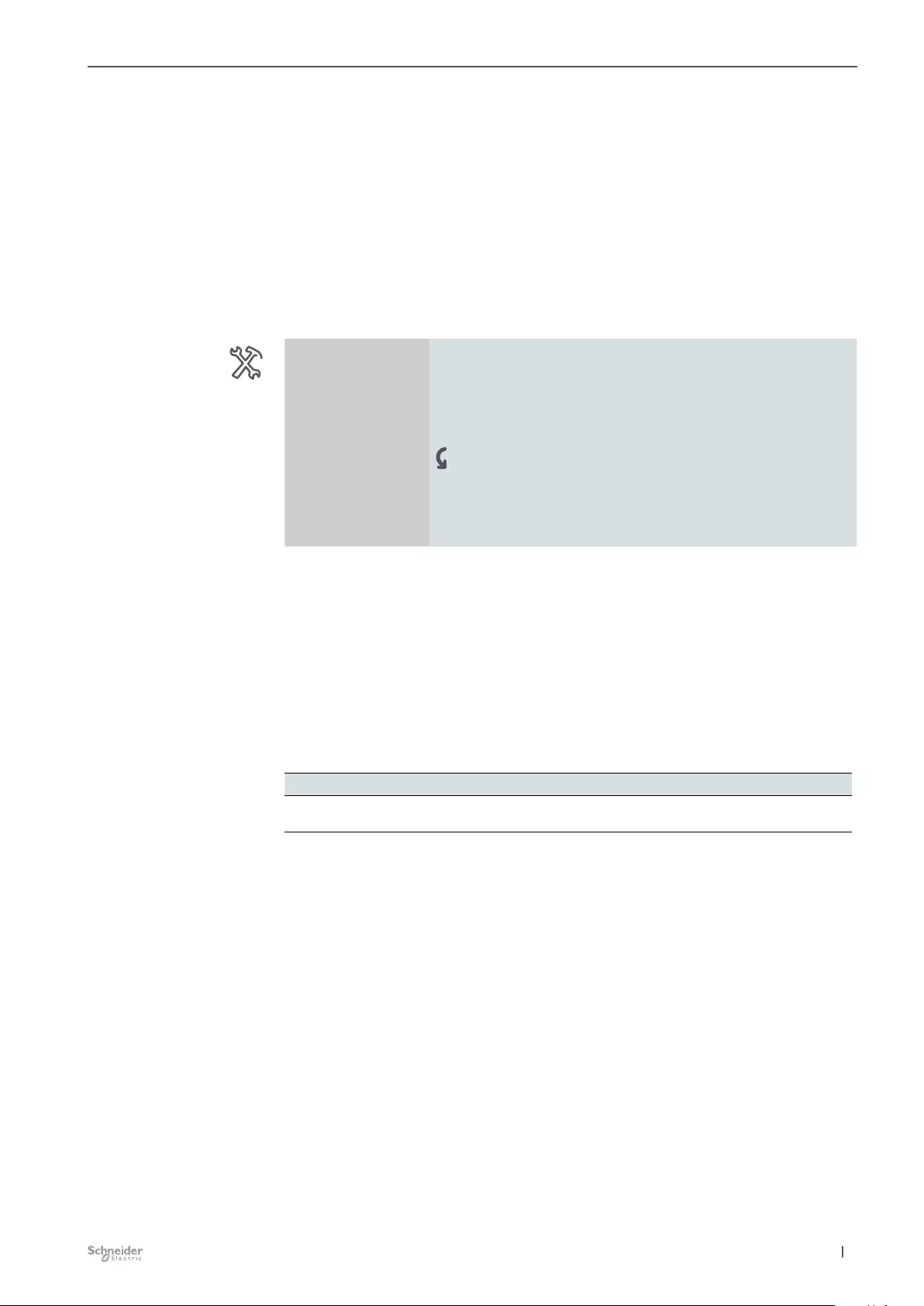
79
05/20-5800/1.0 MTN6705-0008 | MTN6805-0008 |
Express settings for blind / roller shutter Switch Blind 5800/1.0
7.5 Locking manual mode
You can control the connected drives via the group objects the for manual operat-
ing options or via automatic control. There are two options available for the manual
operating options:
•Move manually to height position and slat opening angle (for blind only) via Up/
Down/Step/Stop commands
•Move manually to height position and slat opening angle (for blind only) using
absolute position commands
If you want to stop manual operation temporarily, you can enable lock of manual
mode for each output channel:
Master / Ext. 1/2
Output 1+2 / 3+4 / 5+6
/ 7+8
-Blind / roller shutter
Express settings for blind / roller shutter
Locking manual mode Disabled
Enabled
Manual locking At object value "1"
At object value "0"
Depending on the setting, manual operation is disabled or enabled when a new
telegram value is received:
•“Manual locking” = “at object value “0”
If “Manual locking” = “0”: manual operation disabled (manual locking active)
If Manual locking = “1”: manual operation enabled (manual locking inactive)
•“Manual locking” = “at object value “1”
If “Manual locking” = “0”: manual operation enabled (manual locking inactive)
If “Manual locking” = “1”: manual operation disabled (manual locking active)
Group objects
No. Name Object function Length Behavior Data Type
35 Master Output 1+2
name of the channel
Locking manual
mode
1 bit Received 1.003 Enable
Group objects for lock of manual
mode
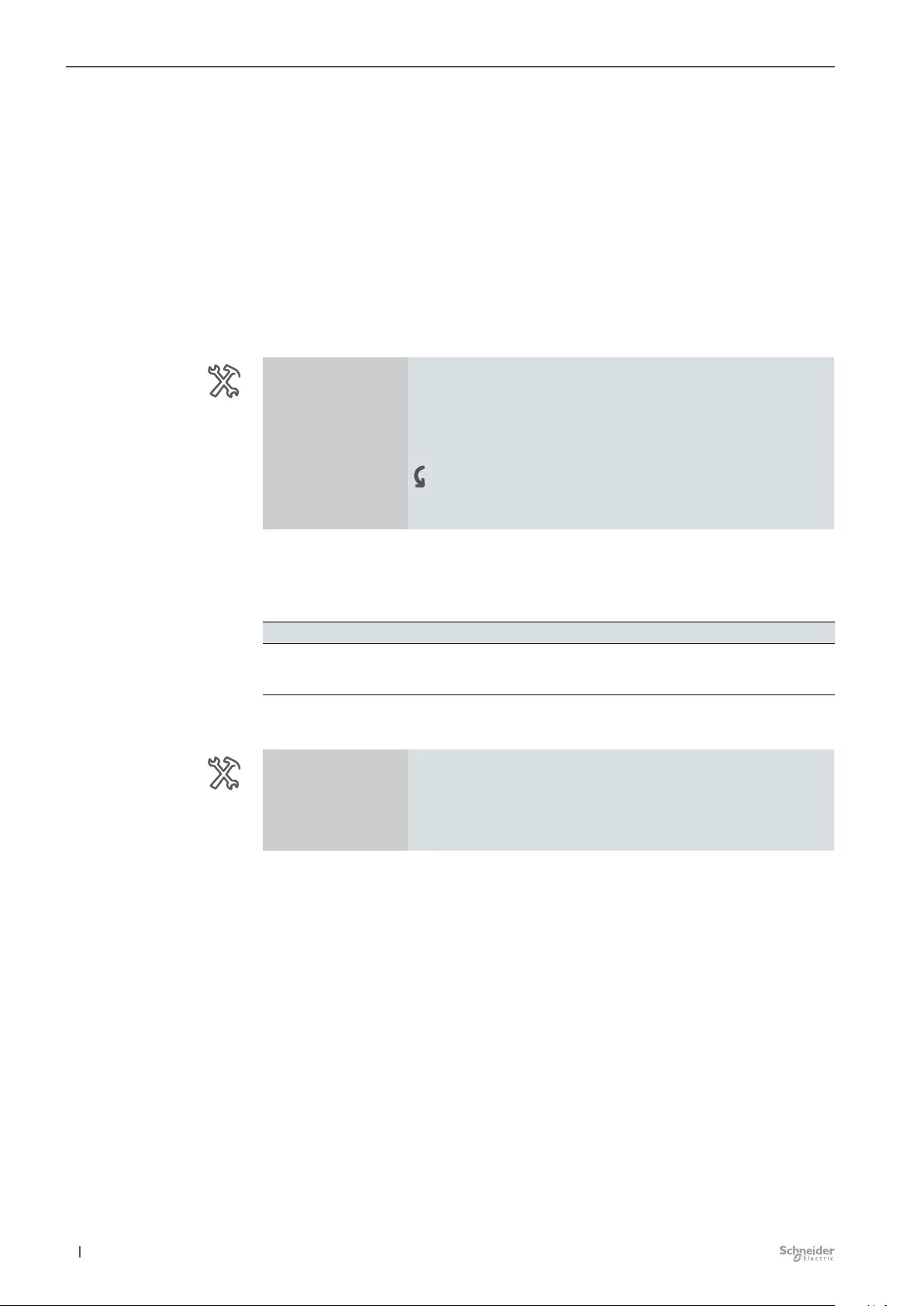
80 05/20-5800/1.0MTN6705-0008 | MTN6805-0008 |
Express settings for blind / roller shutter Switch Blind 5800/1.0
7.6 Scenes
If you want to change multiple room functions simultaneously at the press of a
button or with a command, you can do so using the scene function. You can use a
scene, for example, to switch on the room lighting, set the heating control to day-
time operation and control the blinds.
Without the scene function, you would have to send a separate telegram to each
actuator to get the same setting, since these functions can not only have dierent
telegram formats, but also the telegram values have dierent meanings (e.g. value
“0” for lighting OFF and for OPEN blind).
Enabling scenes
Master / Ext. 1/2
Output 1+2 / 3+4 / 5+6
/ 7+8
-Blind / roller shutter
Express settings for blind / roller shutter
Scenes Disabled
Enabled
-Scenes settings Scene settings
Following enabling of the scenes, the group object appears.
Group objects
No. Name Object function Length Behavior Data Type
43 Master Output
1+2 name of
the channel
Scene 1 byte Received 18.001 Scene
control
Number of scenes
Master / Ext. 1/2
Output 1+2 / 3+4 / 5+6
/ 7+8
-Blind / roller shutter
Scene settings
-Scenes settings Required number of scenes 1 (1-16)
You can use the scene function to include multiple channels in a scene control. Up
to 16 dierent scenes are available for each output channel.
Group object for
scene
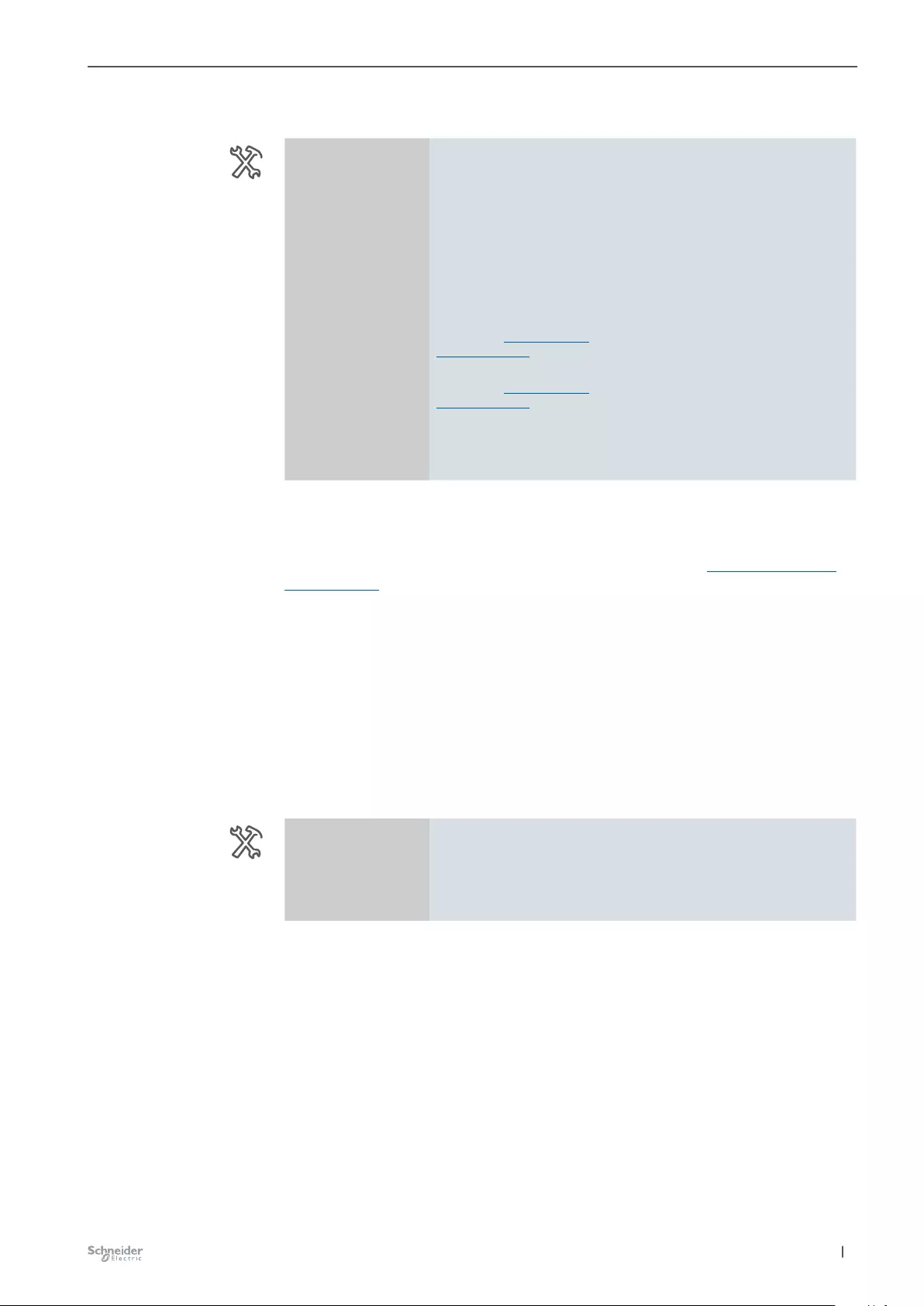
81
05/20-5800/1.0 MTN6705-0008 | MTN6805-0008 |
Express settings for blind / roller shutter Switch Blind 5800/1.0
Each of the up to 16 scenes can in turn be disabled or enabled.
Master / Ext. 1/2
Output 1+2 / 3+4 / 5+6
/ 7+8
-Blind / roller shutter
Scene settings
-Scenes settings Scene 1 (1-16) Disabled
Enabled
Scene 1 Description
Scene 1 Address (0-63)
Dependent: Global settings
for scenes --> 24
Scene address 0 - 63
Scene 1 Address (1-64)
Dependent: Global settings
for scenes --> 24
Scene address 1 - 64
Scene 1 height in % 0 (0-100)
Scene 1 slat position in % 0 (0-100)
For clarity, a short description can be stored for each scene.
Each of these scenes can be assigned one of 64 possible scene addresses 0 to
63 (corresponding to telegram values 0-63) or 1 to 64 (corresponding to telegram
values 0-63). This depends on the global settings for scenes. Global settings for
scenes --> 24
You can store height positions and also, for blinds, slat opening angles as scene
values. When the actuator receives a telegram calling a scene number, the drive
is moved to the saved position and the slats are rotated. The scene positions you
store during start-up can be overwritten later by the user if he wants to change
them.
Time delay for scene processing
To avoid high power-on currents when switching to a complex scene, you can
parameterize a time delay for each output channel. (Especially in the case of many
motors)
Master / Ext. 1/2
Output 1+2 / 3+4 / 5+6
/ 7+8
-Blind / roller shutter
Scene settings
-Scenes settings Time delay for scene process-
ing (0...255, unit = 100 ms) 0
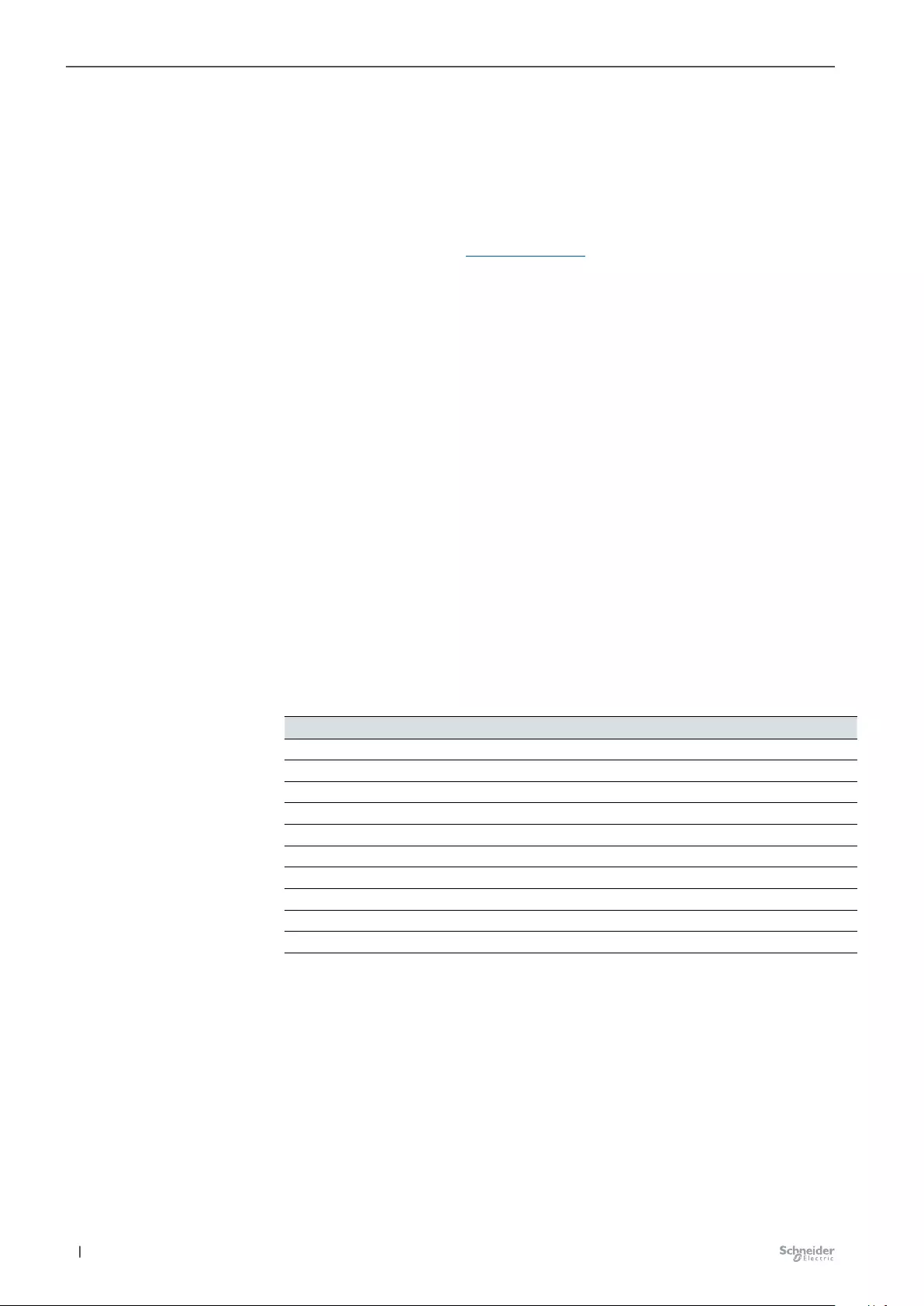
82 05/20-5800/1.0MTN6705-0008 | MTN6805-0008 |
Express settings for blind / roller shutter Switch Blind 5800/1.0
Calling and saving scene values
Scene values for the output relays are called using the object “Scene”. After receiv-
ing a scene telegram, the device evaluates the sent scene address and controls
the channels to the saved scene values.
If a reference movement is required before the drive is moved to the scene po-
sition, the reference movement is executed rst and the drive then moves to the
requested scene position. Calibration --> 98
If the “scene object” receives a scene telegram with learning bit “1”, then for all
scenes assigned to the received scene address, the current height position and, in
the case of blind drives, the current slat position are saved as the new scene value.
Note: If a scene address within a channel is assigned to multiple scenes (incorrect
parameterization), only the last scene found with this scene address is called or
saved. You can avoid this by assigning dierent scene addresses within a channel.
Telegram format
Telegrams for the scene function have the data format: L X D D D D D D.
L = learning bit
X = not used
DDDDDD = called scene address
If the learning bit in a telegram has the value “0”, then the relay states saved for the
scene address are called and set.
If the learning bit receives the value “1”, then the current output states are saved as
new scene values for the received scene address.
Take the scene address (0-63) and add 128 to get the value for learning the scene.
Examples:
Telegram value Binary Hexadecimal Scene address
0 0000 0000 00 Call scene address 0
1 0000 0001 01 Call scene address 1
29 0001 1101 1D Call scene address 29
57 0011 1001 39 Call scene address 57
63 0011 1111 3F Call scene address 63
128 (0+128) 1000 0000 80 Learning scene address 0
129 (1+128) 1000 0001 81 Learning scene address 1
157 (29+128) 1001 1101 9D Learning scene address 29
185 (57+128) 1011 1001 B9 Learning scene address 57
191 (63+128) 1011 1111 BF Learning scene address 63
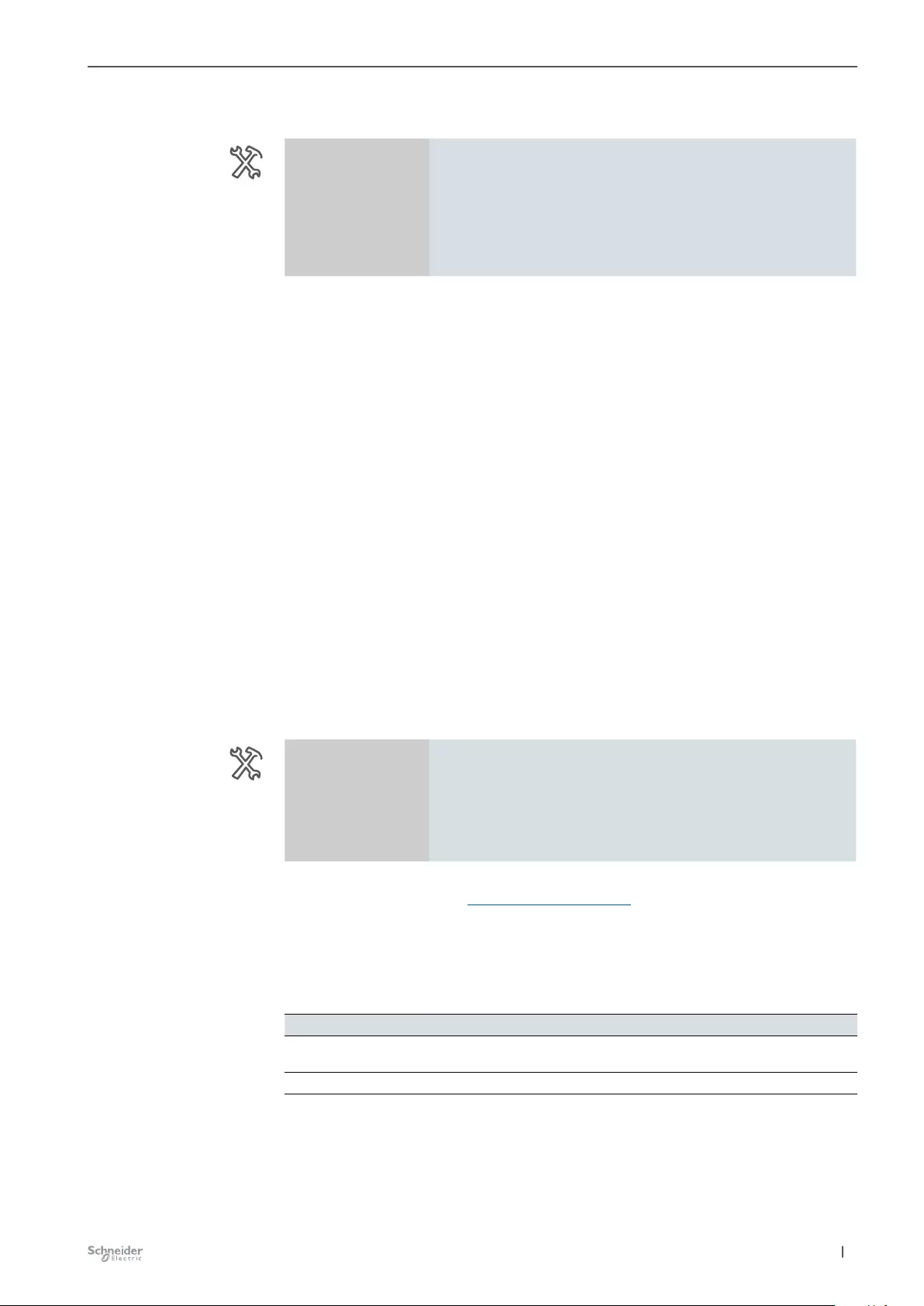
83
05/20-5800/1.0 MTN6705-0008 | MTN6805-0008 |
Express settings for blind / roller shutter Switch Blind 5800/1.0
Overwrite scene values during download
Master / Ext. 1/2
Output 1+2 / 3+4 / 5+6
/ 7+8
-Blind / roller shutter
Scene settings
-Scenes settings Overwrite scene values of
actuator during download Disabled
Enabled
If you have enabled the parameter “Overwrite scene values in actuator during
download”, the scene values saved in the device will be overwritten with your pre-
set values on downloading. If you do not want to overwrite the values in the device
when downloading, you must disable the parameter. In this case, the parameter-
ized scene values are only written to the device memory during the rst download.
If an application download is then carried out, the scene values in the device mem-
ory are retained.
Priority
The scene function has the same priority as the normal blind / roller shutter func-
tion with control over the 4 group objects: “Movement in manual mode” and “Stop/
step in manual mode” (for roller shutters: “Stop in manual mode”) For positioning:
“Height position in manual mode” and “Slat position in manual mode” (for blind
only).
This should be taken into account with regard to the priority of the higher-level func-
tions.
7.7 Central function for blind
Enable central function for each drive
The central function is enabled or disabled here for each drive.
Master / Ext. 1/2
Output 1+2 / 3+4 / 5+6
/ 7+8
-Blind / roller shutter
Express settings for blind / roller shutter
Central function Enabled
Disabled
The global settings and explanations of the central function can be found in the
chapter General settings. (General settings --> 15)
Using the central function, you can simultaneously open or close multiple blind
channels with a telegram via the object Central - Move up/down blind.
Group objects
No. Name Object function Length Behavior Data Type
2 Central Move up/down roller
shutter
1 bit Received 1.008 Up/Down
3 Central Move up/down blind 1 bit Received 1.008 Up/Down
Group objects of the central
function
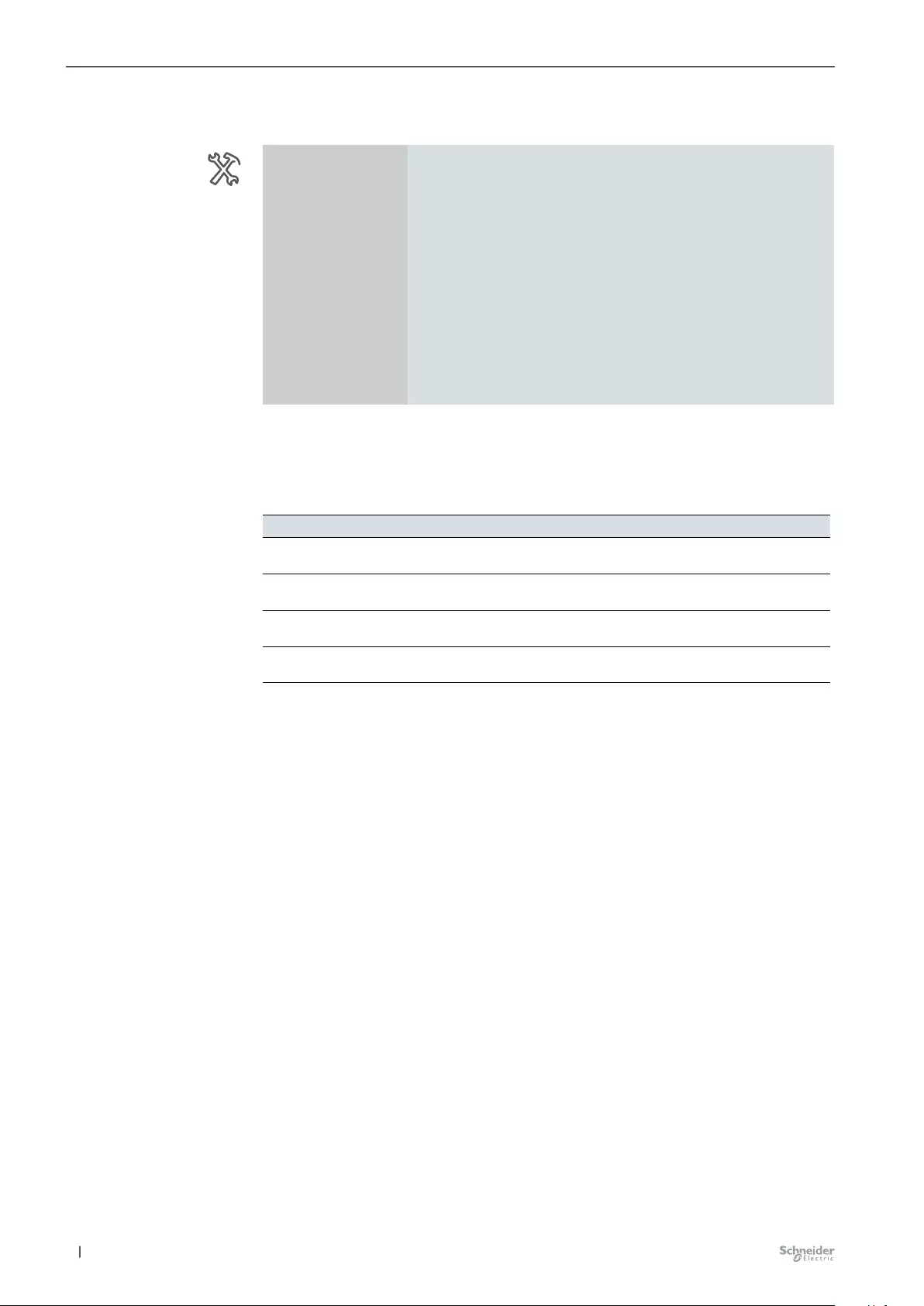
84 05/20-5800/1.0MTN6705-0008 | MTN6805-0008 |
Express settings for blind / roller shutter Switch Blind 5800/1.0
7.8 Status response
Master / Ext. 1/2
Output 1+2 / 3+4 / 5+6
/ 7+8
-Blind / roller shutter
Express settings for blind / roller shutter
Status of height Enabled
Disabled
Status of slat (for blind only) Enabled
Disabled
Status of moving Enabled
Disabled
Each blind channel can provide dierent status responses, depending on how it is
enabled. The following group objects are available and can be disabled:
Group objects
No. Name Object function Length Behavior Data Type
46 Master Output 1+2
name of the channel
Feedback for
height
1 byte Sending 5.001 Percent
(0...100%)
47 Master Output 1+2
name of the channel
Feedback for
slat (blind)
1 byte Sending 5.001 Percent
(0...100%)
51 Master Output 1+2
name of the channel
Feedback for
moving
1 bit Sending 1.010 Start/Stop
52 Master Output 1+2
name of the channel
Feedback for
last direction
1 bit Sending 1.008 Up/DOWN
Status of height
The current position of the drive is provided as a value between 0-100%. The
corresponding status object “Feedback for height” sends the value on the bus if the
drive has reached a xed position after a movement.
Status of slat (for blind only)
The current angle of rotation of the blind slats is provided as a value between
0-100%. The corresponding status object “Feedback for slat” sends the value on
the bus if the drive/slat has reached a xed position after a movement.
Status of moving
The status object “Feedback for moving” sends the movement status of the drive.
This information is sent directly.
•Sends a “1” when the movement/drive is started
•Sends a “0” when the movement/drive is stopped
Group objects of status re-
sponse of blind
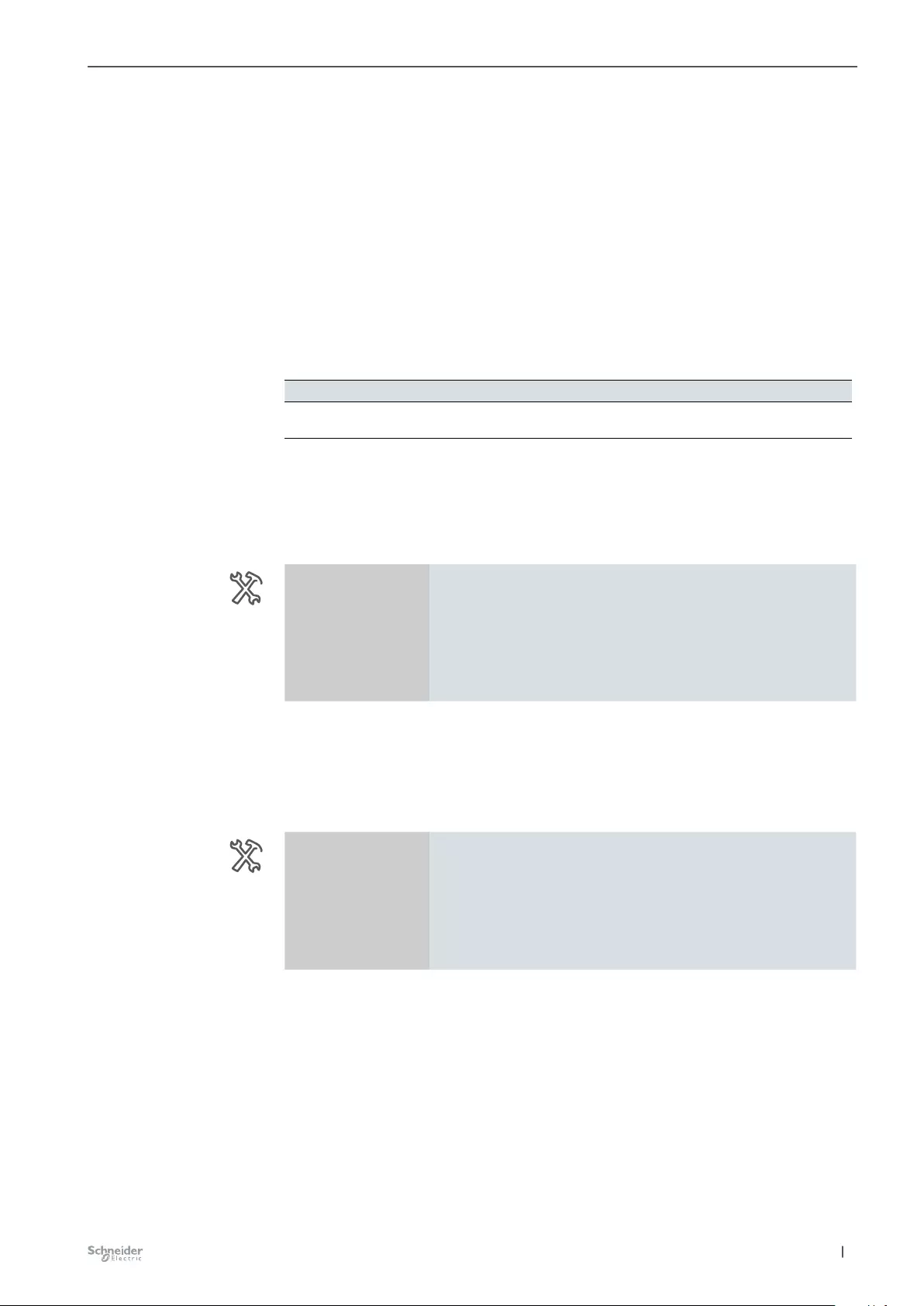
85
05/20-5800/1.0 MTN6705-0008 | MTN6805-0008 |
Express settings for blind / roller shutter Switch Blind 5800/1.0
The status object “Feedback for last direction” sends the value for the last direction
of movement of the drive.
•Sends a “1” if the drive has been moved down or the slat has been closed by
one step.
•Sends a “0” if the drive has been moved up or the slat has been opened by one
step.
Automatic status
Once the function “Status of automatic locking” has been enabled, a new group
object is available for the channel.
Group objects
No. Name Object function Length Behavior Data Type
48 Master Output 1+2
name of the channel
Feedback for
automatic mode
1 bit Sending 1.003 Enable
The feedback object sends a “1” if automatic locking is active.
The feedback object sends a “0” if automatic locking is inactive.
7.9 Activating extended settings for blind
Master / Ext. 1/2
Output 1+2 / 3+4 / 5+6
/ 7+8
-Blind
Express settings for blind
Extended settings for blind No
Yes
To activate the extended settings for blind, you must enable them here.
7.10 Activating extended settings for roller
shutter
Master / Ext. 1/2
Output 1+2 / 3+4 / 5+6
/ 7+8
-Roller shutter
Express settings for roller shutter
Extended settings for roller
shutter No
Yes
To activate the extended settings for roller shutter, you must enable them here.
Group objects of status re-
sponse of automatic mode
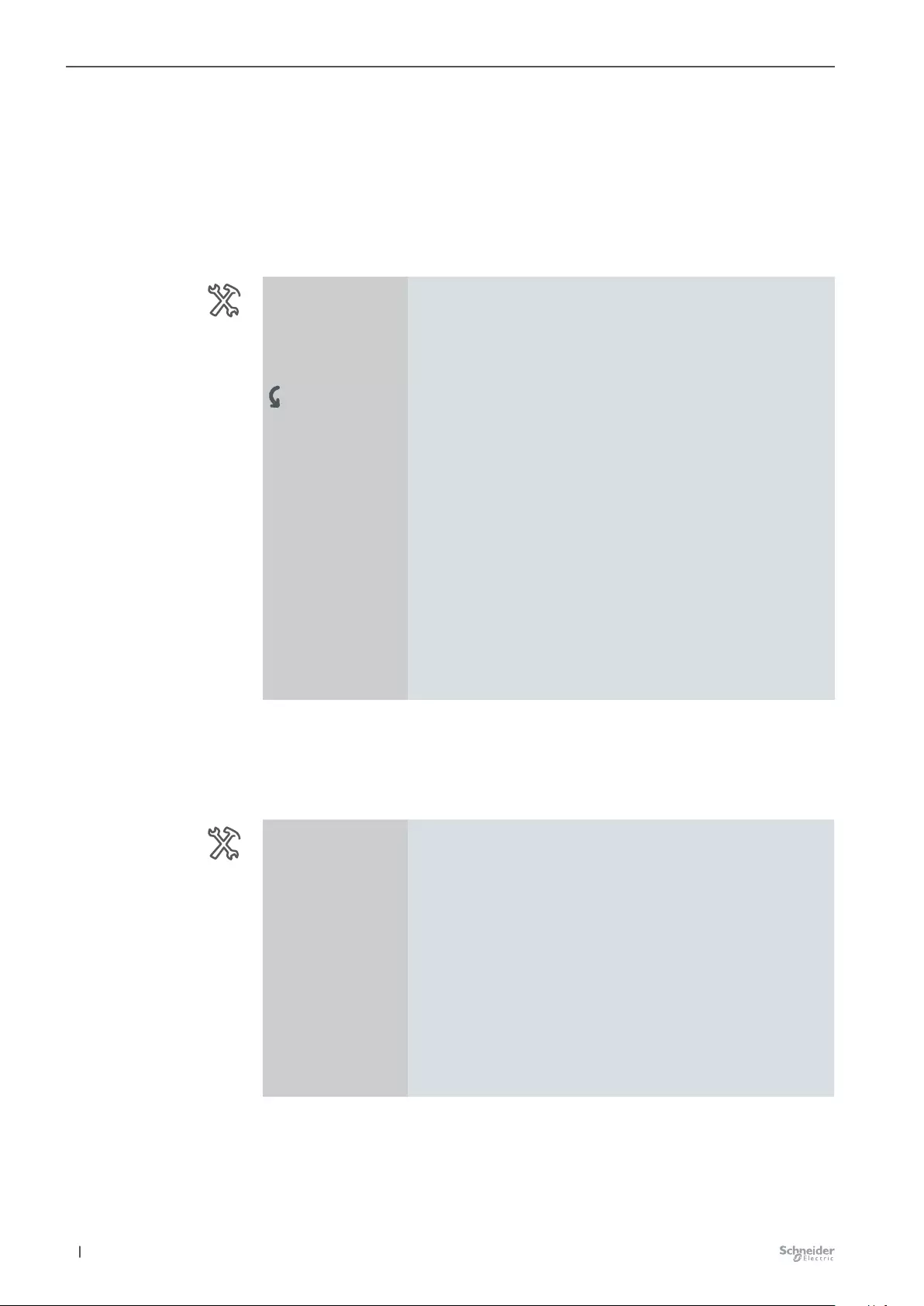
86 05/20-5800/1.0MTN6705-0008 | MTN6805-0008 |
Extended settings for blind / roller shutter Switch Blind 5800/1.0
8 Extended settings for blind /
roller shutter
On the Extended settings for blind tab, you can dened additional settings and
enable or disable additional functions.
On the Express settings for blind tab, activate the Extended settings for blind.
Master / Ext. 1/2
Output 1+2 / 3+4 / 5+6
/ 7+8
-Blind / roller shutter
Express settings for blind / roller shutter
Extended settings for blind /
roller shutter No
Yes
-Extended drive timing Idle time until upward movement
Startup delay
Additional startup time
-Automatic, Locking &
Calibration settings Priority function
Logic function
-Safety and alarm
settings Safety function
Alarm function
Failure and download behavior
8.1 Extended drive timing
For special drives and blinds, you can adjust the drive times by means of additional
parameters.
Master / Ext. 1/2
Output 1+2 / 3+4 / 5+6
/ 7+8
-Blind / roller shutter
Extended drive timing
-Extended drive timing Idle time until upward move-
ment (0...255, unit = 10 ms) 0
Startup delay (0...255, unit =
10 ms) 0
Deceleration delay (0...255,
unit = 10 ms) 0
Additional startup time when
opening slat downwards
(0...255, unit = 10 ms)
0
Additional startup time when
opening slat upwards (0...255,
unit = 10 ms)
0
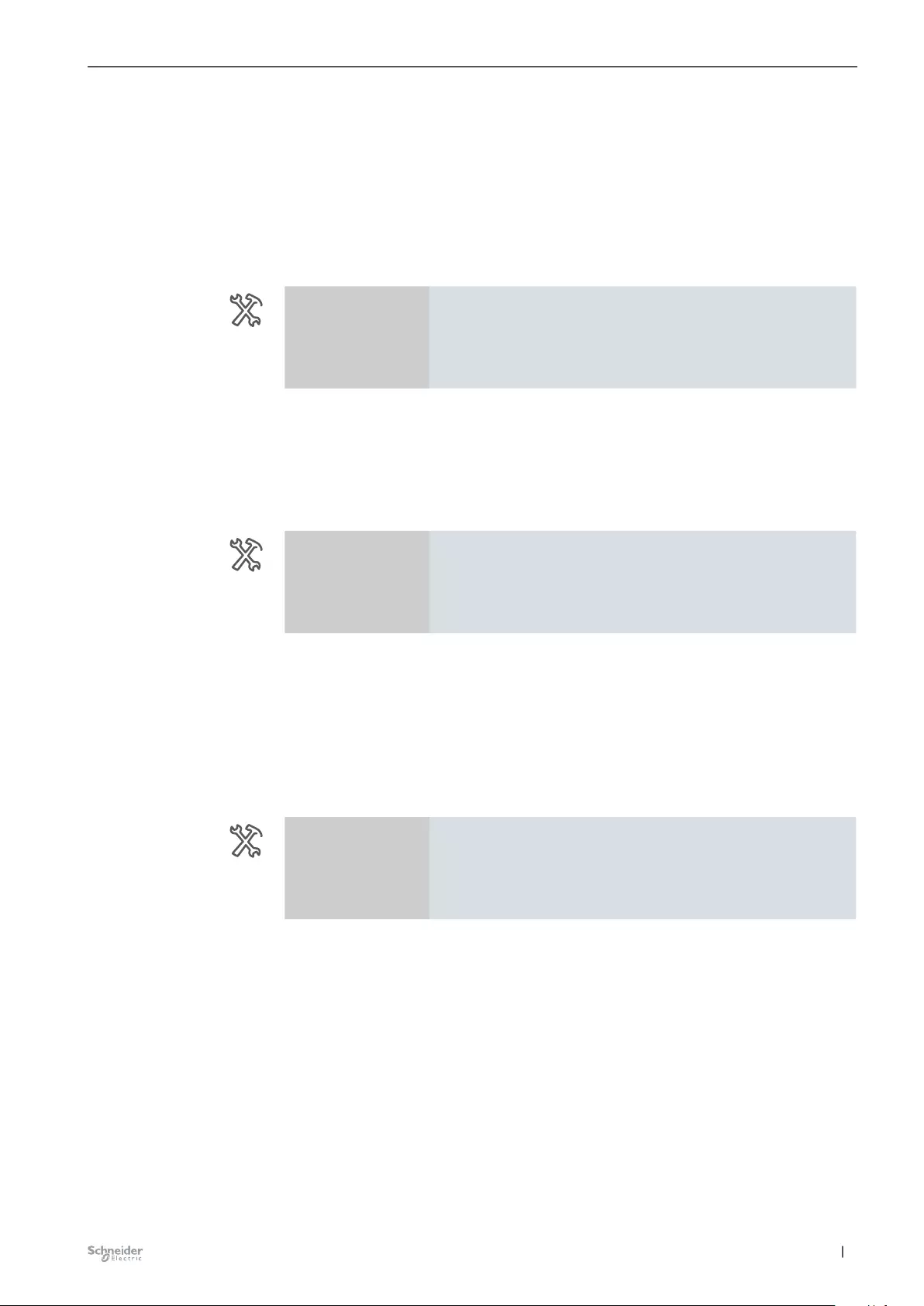
87
05/20-5800/1.0 MTN6705-0008 | MTN6805-0008 |
Extended settings for blind / roller shutter Switch Blind 5800/1.0
Idle time until upward movement
If the blind used has an idle time in the closed lower position between pulling on
the main strap and the rst upward movement, you can compensate for this delay
in this way.
The idle time can also be used when using a roller shutter to compensate for the
roller shutter opening.
Example:
A value = 10 gives an idle time of 10 x 10 ms = 100 ms
Master / Ext. 1/2
Output 1+2 / 3+4 / 5+6
/ 7+8
-Blind / roller shutter
Extended drive timing
-Extended drive timing Idle time until upward move-
ment (0...255, unit = 10 ms) 0
Startup delay
Some motors do not bring full power directly when switched on, but only after a few
milliseconds. You can use the time setting for the start-up delay to compensate for
this.
A value = 10 gives a start-up delay of 2 x 10 ms = 20 ms
Master / Ext. 1/2
Output 1+2 / 3+4 / 5+6
/ 7+8
-Blind / roller shutter
Extended drive timing
-Extended drive timing Startup delay (0...255, unit =
10 ms) 0
Deceleration delay
There are some motors that continue running for several milliseconds after they are
switched o. This can also be caused by large and heavy blinds/roller shutters. If
you notice this behavior, you can compensate for it using the setting for the decel-
eration delay.
A value = 6 gives a deceleration delay of 6 x 10 ms = 60 ms.
In this way, the motor will be switched o 60 ms earlier.
Master / Ext. 1/2
Output 1+2 / 3+4 / 5+6
/ 7+8
-Blind / roller shutter
Extended drive timing
-Extended drive timing Deceleration delay (0...255,
unit = 10 ms) 0
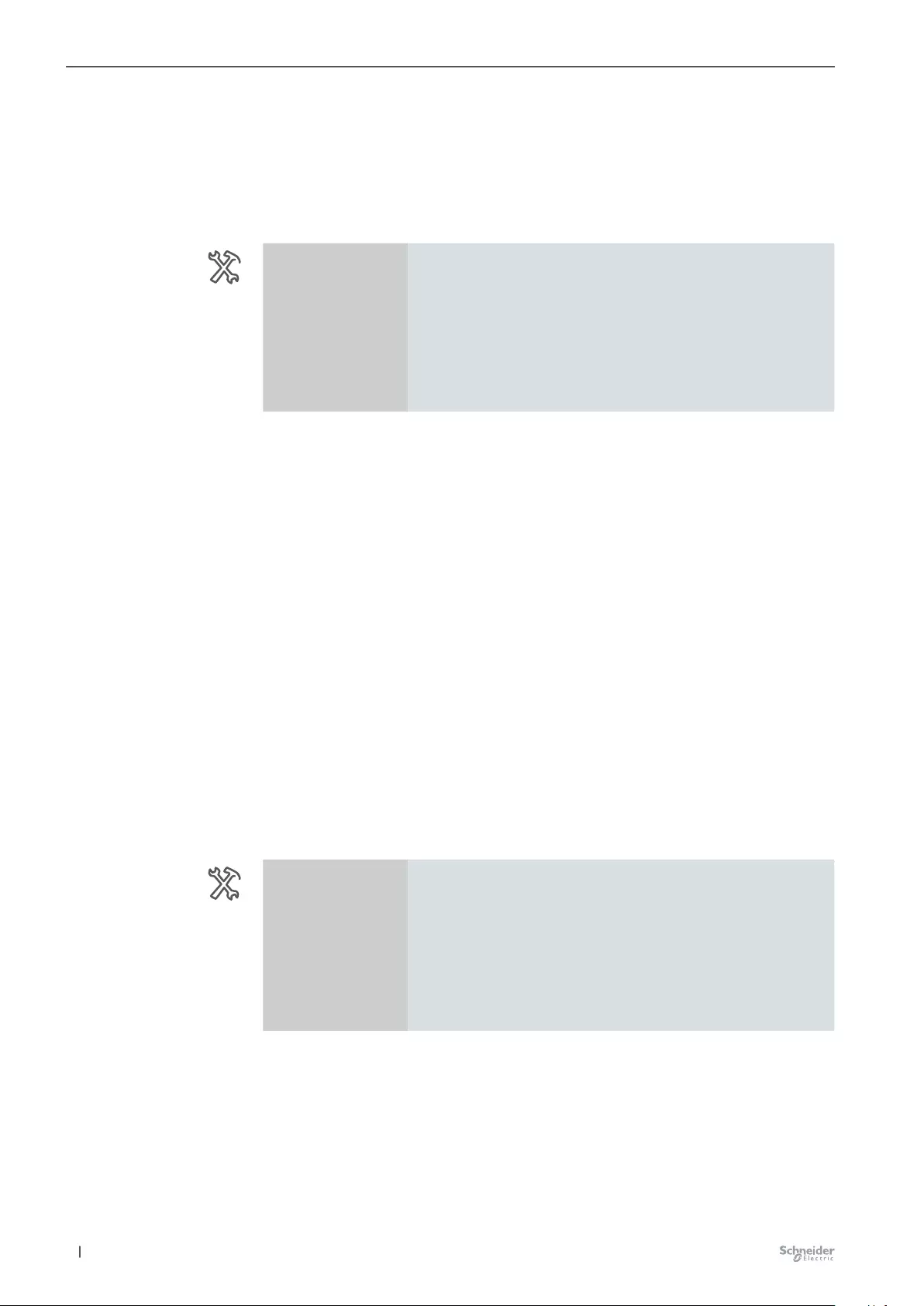
88 05/20-5800/1.0MTN6705-0008 | MTN6805-0008 |
Extended settings for blind / roller shutter Switch Blind 5800/1.0
Additional start-up time on opening the slat
(for blind only)
Some types of blinds require an additional start-up supplement before the rst
reaction of the slats when opening the slats due to the tensioning and releasing of
the slat straps. This depends on the current slat position. The following parameters
can be used to set a start-up supplement for the upper and lower slat positions.
Master / Ext. 1/2
Output 1+2 / 3+4 / 5+6
/ 7+8
-Blind / roller shutter
Extended drive timing
-Extended drive timing
Additional startup time when
opening slat downwards
(0...255, unit = 10 ms)
0
Additional startup time when
opening slat upwards (0...255,
unit = 10 ms)
0
With these parameters for Additional startup time when opening slat downwards,
set the start-up delay for an upward movement until the slat is rotated when the
slats are in the open position (0%) (the previous blind movement was an upward
motion):
Additional startup time when opening slat upwards: the start-up delay until the slat
is rotated, which you dene here, is always taken into account when opening the
blind if the slat is in the closed position (100%) (the previous blind movement was a
downward movement):
8.2 Automatic, Locking & Calibration settings
Automatic mode
In addition to manual control of the blind / roller shutter drives (via the group objects
for the manual operating options), the software application also provides you with
another set of group objects for automatic control.
Automatic control can be performed by other bus devices, e.g. presence detectors
or light controllers, or via a building control system. Once you have activated auto-
matic control for a channel, you can initially position the connected drive with equal
priority using manual control or automatic control. The drive reacts identically on
receiving control telegrams from one of the two types of control.
Master / Ext. 1/2
Output 1+2 / 3+4 / 5+6
/ 7+8
-Blind / roller shutter
Automatic, Locking & Calibration settings
-Automatic, Locking &
Calibration settings Automatic mode
Automatic mode Disabled
Enabled
In order to use the automatic mode, you must rst activate the function in the ETS.
Once automatic mode has been enabled, new group objects are available for the
channel.
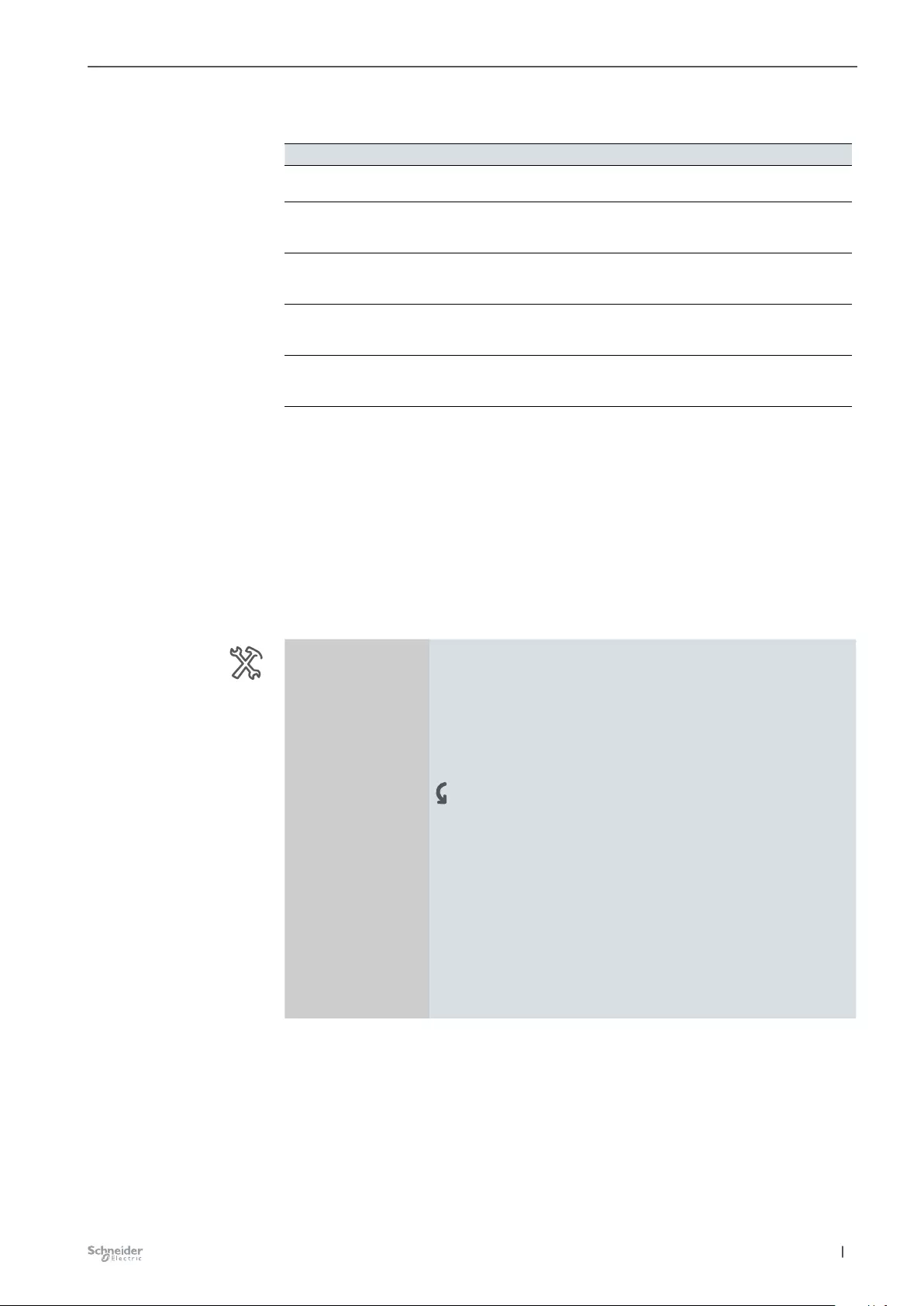
89
05/20-5800/1.0 MTN6705-0008 | MTN6805-0008 |
Extended settings for blind / roller shutter Switch Blind 5800/1.0
Group objects
No. Name Object function Length Behavior Data Type
36 Master Output 1+2
name of the channel
Movement in au-
tomatic mode
1 bit Received 1.008 Up/DOWN
37 Master Output 1+2
name of the channel
Stop/step in
automatic mode
(blind)
1 bit Received 1.007 Step
37 Master Output 1+2
name of the channel
Stop in automat-
ic mode (roller
shutter)
1 bit Received 1.007 Step
38 Master Output 1+2
name of the channel
Height position
in automatic
mode
1 byte Received 5.001 Percent
(0...100%)
39 Master Output 1+2
name of the channel
Slat position in
automatic mode
(blind)
1 byte Received 5.001 Percent
(0...100%)
The group objects for manual operation and automatic mode have equal priority.
The drive always executes the command it received last on one of the objects.
Using parameter settings and objects, you can modify the operation of the two
control options. You also have the possibility of dening the reciprocal inuence of
manual control and automatic control.
Enabling/disabling automatic mode
If operation with equal priorities for manual operation and automatic mode is not
always suitable for your application, you can disable and re-enable automatic mode
using an additional object as required:
Master / Ext. 1/2
Output 1+2 / 3+4 / 5+6
/ 7+8
-Blind / roller shutter
Automatic, Locking & Calibration settings
-Automatic, Locking &
Calibration settings Automatic mode
Lock of automatic mode Disabled
Enabled
Automatic locking At object value "1"
At object value "0"
Status of automatic locking Disabled
Enabled
Behavior on deactivating
automatic locking via object No reaction
Accept current automatic position
Once the function “Lock of automatic mode” and “Status of automatic locking” has
been enabled, new group objects are available for the channel.
The feedback object sends a “1” if automatic locking is active.
The feedback object sends a “0” if automatic locking is inactive.
Group objects of automatic
mode "Blind"
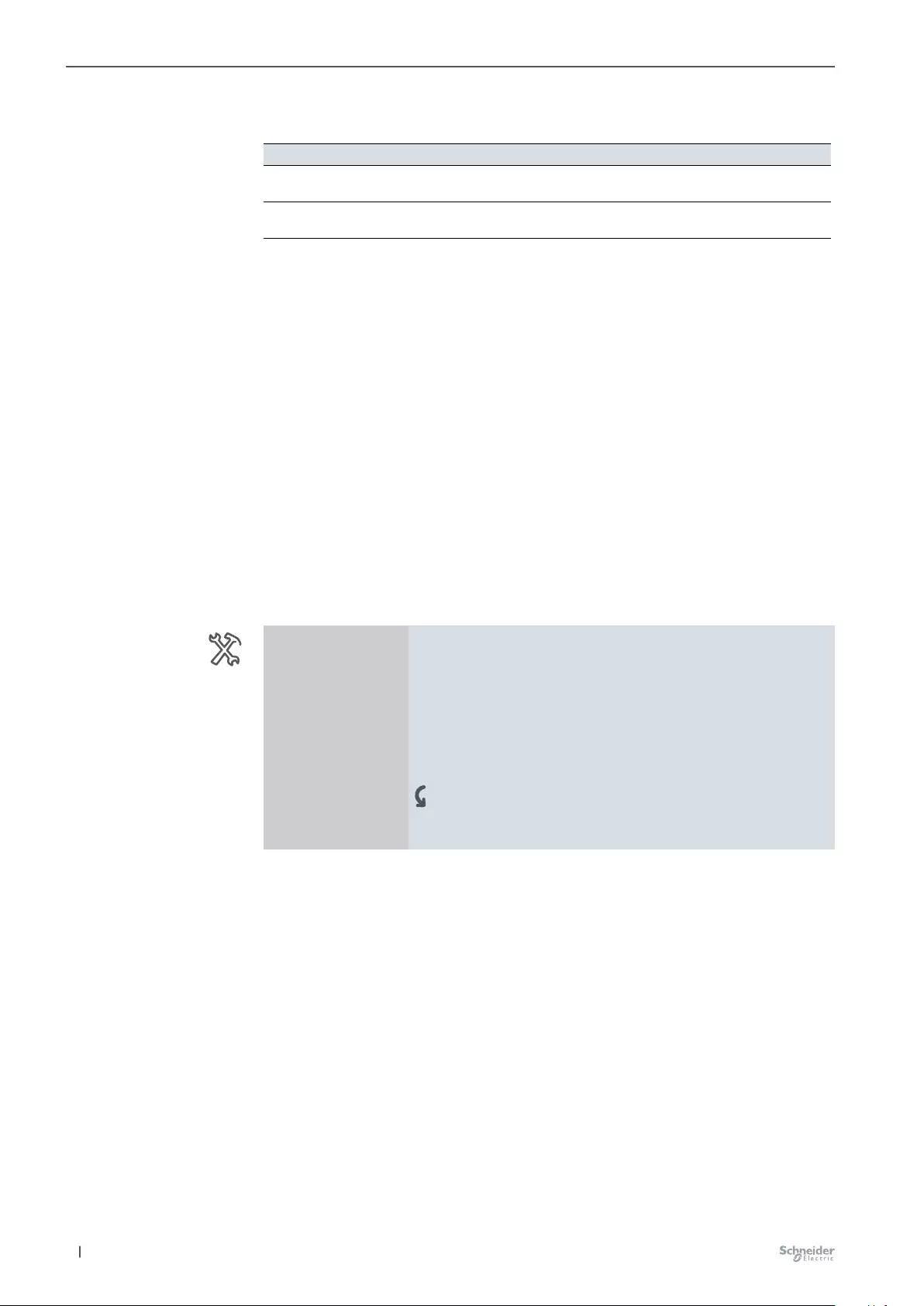
90 05/20-5800/1.0MTN6705-0008 | MTN6805-0008 |
Extended settings for blind / roller shutter Switch Blind 5800/1.0
Group objects
No. Name Object function Length Behavior Data Type
40 Master Output 1+2
name of the channel
Lock of automat-
ic mode
1 bit Received 1.003 Enable
48 Master Output 1+2
name of the channel
Feedback for
automatic mode
1 bit Sending 1.003 Enable
Depending on the setting, the automatic locking is activated or deactivated when a
new telegram value is received:
•“Automatic locking” = “at object value 0”
If “Automatic locking” = “0”: automatic locking is active.
If “Automatic locking” = “1”: automatic locking is inactive.
•“Automatic locking”= “at object value 1”
If “Automatic locking” = “0”: automatic locking is inactive.
If “Automatic locking” = “1”: automatic locking is active.
In addition, you can set the behavior of the drive to the end of automatic locking.
Furthermore, you can separately dene the response of automatic control on re-
ceiving a manual control telegram.
Defining dependency between automatic function and manual
control
You can use the following parameter to dene the reaction of the automatic func-
tion on receiving a control telegram from the manual operating options (Movement
in manual mode, Stop/step in manual mode, Height position in manual mode, Slat
position in manual mode, and calling up scenes):
Master / Ext. 1/2
Output 1+2 / 3+4 / 5+6
/ 7+8
-Blind / roller shutter
Automatic, Locking & Calibration settings
-Automatic, Locking &
Calibration settings Automatic mode
Reaction in automatic mode
on receipt of a manual object
value
Automatic mode remains enabled
Automatic mode temporarily disabled
Deactivation time for automat-
ic mode 1 min (1 min - 24 h)
Permanent deactivation of the automatic function can only be canceled by a tele-
gram terminating automatic locking via the automatic locking object. The action you
set in the parameter “Behavior on deactivating automatic locking via object” will be
executed.
Once a temporary deactivation has elapsed, the drive remains in its current posi-
tion until the next control telegram.
Group objects of automatic
mode "Lock"
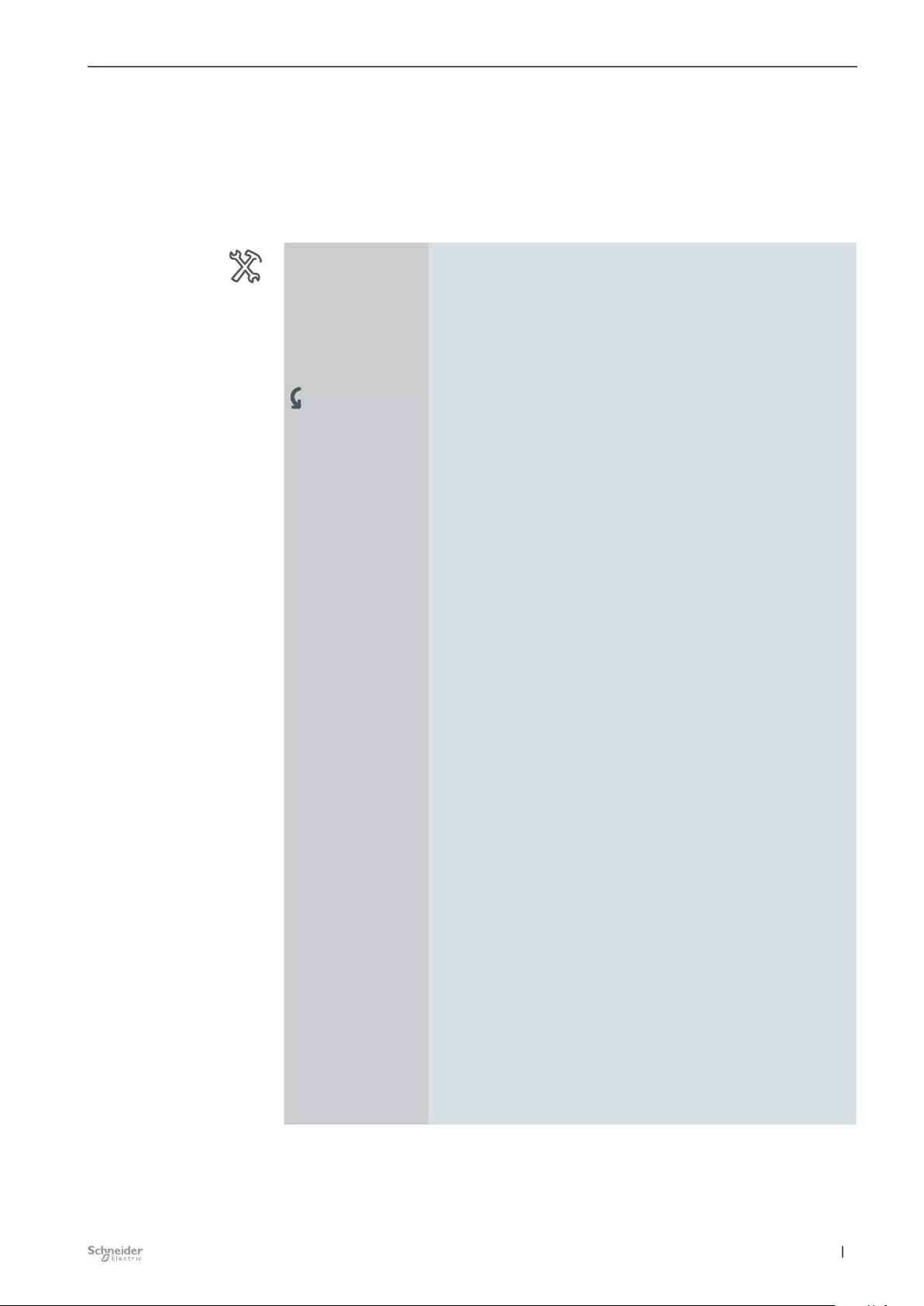
91
05/20-5800/1.0 MTN6705-0008 | MTN6805-0008 |
Extended settings for blind / roller shutter Switch Blind 5800/1.0
Locking function
Using the locking function, you can move a blind / roller shutter to a desired lock-
ing position. The state of the output channel cannot be changed by other control
commands as long as the lock is active. Only a higher-level function with a higher
priority can still be used to move the drive to a dierent position. You can enable
the locking function individually for each output channel.
Master / Ext. 1/2
Output 1+2 / 3+4 / 5+6
/ 7+8
-Blind / roller shutter
Locking function
-Automatic, Locking &
Calibration settings Locking function Disabled
Enabled
Locking At object value "1"
At object value "0"
Status of locking signal Disabled
Enabled
Behavior at start of locking No reaction
Up
Down
Move to position
Height position at start of locking
in % 0 (0-100)
Slat position at start of locking
in % 0 (0-100)
Behavior at end of locking No reaction
Up
Down
Move to position prior locking
Accept current automatic position
Behavior after download Disabled
Enabled
As before download
Behavior after bus voltage
recovery Disabled
Enabled
As before bus voltage failure
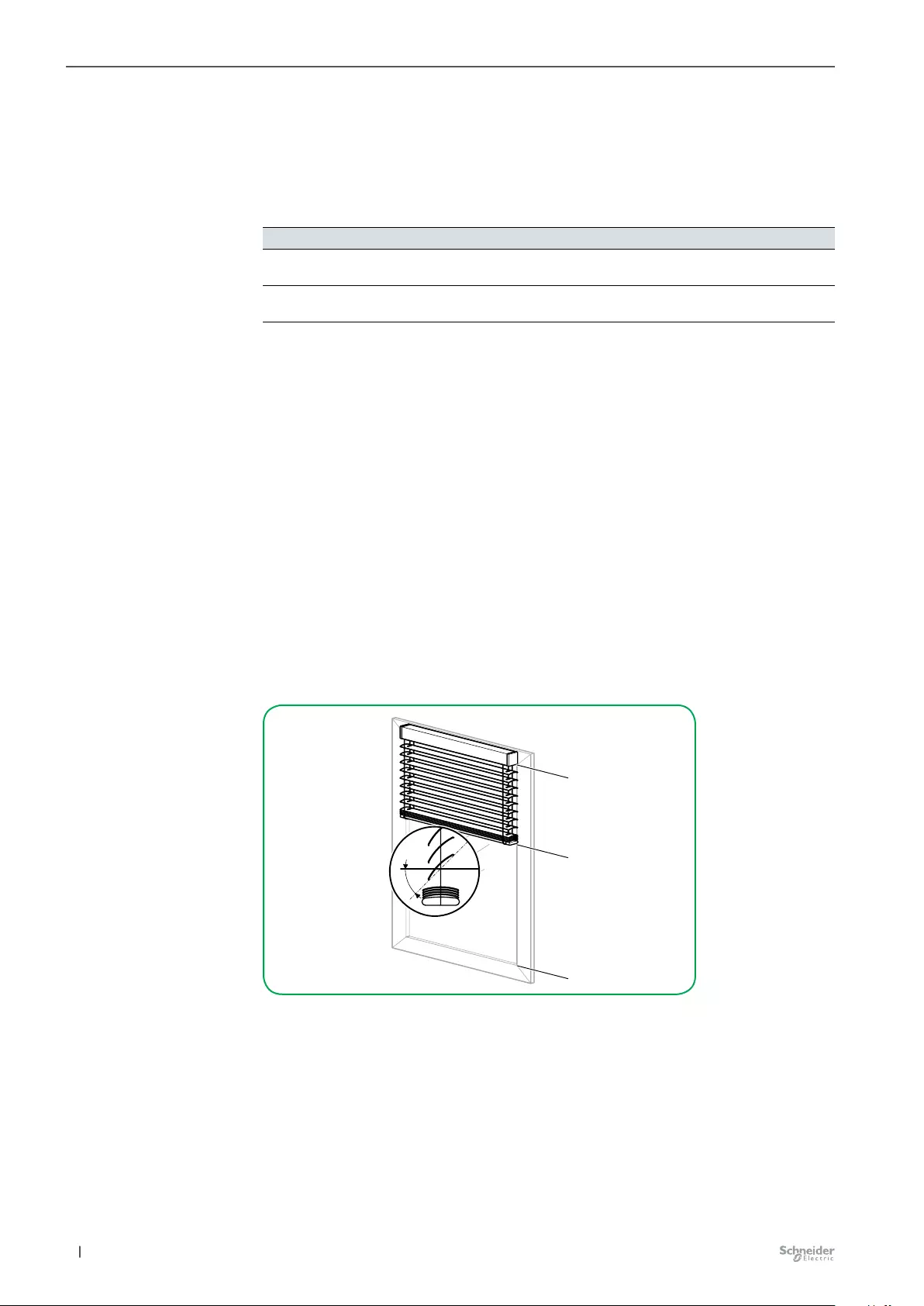
92 05/20-5800/1.0MTN6705-0008 | MTN6805-0008 |
Extended settings for blind / roller shutter Switch Blind 5800/1.0
Once the “Locking function” and “Status of locking signal” have been enabled,
new group objects are available for the channel. You can activate and deactivate a
channel lock using the locking object.
Group objects
No. Name Object function Length Behavior Data Type
41 Master Output 1+2
name of the channel
Locking 1 bit Received 1.003 Enable
49 Master Output 1+2
name of the channel
Feedback for
drive locking
1 bit Sending 1.003 Enable
If the locking object receives a telegram with the object value that you set for the
parameter Lock, all other functions for the channel are disabled. You can dene the
reaction using the parameter Behavior at start of locking.
If the locking object receives a telegram with the object value opposite of that for
activation, the lock is canceled and the drive adopts the state that you dened in
the parameter Behavior at end of locking.
The Feedback for drive locking object sends a “1” if the lock is active.
The Feedback for drive locking object sends a “0” if the lock is inactive.
Behavior of the drive at start of locking
Set how the drive is to behave when the locking function becomes active:
•No reaction: the drive remains in its current position.
•Up: the drive moves to the upper end position.
•Down: the drive moves to the lower end position.
•Move to position: the drive moves to the dened position for height and slat (for
blind only).
Behavior at start of locking = move to position; height position
at start of locking = 40%; slat position at start of locking = 50%
50 %
0 %
40 %
100 %
Once the drive has performed the desired action, it remains in this position and
cannot be operated while the locking function is active. Only when a function with a
higher priority becomes active will the reaction dened there be executed.
The locking function always switches without a delay. During locking, the telegram
received most recently is saved and delay times and staircase lighting times contin-
ue.
Group objects of locking func-
tion
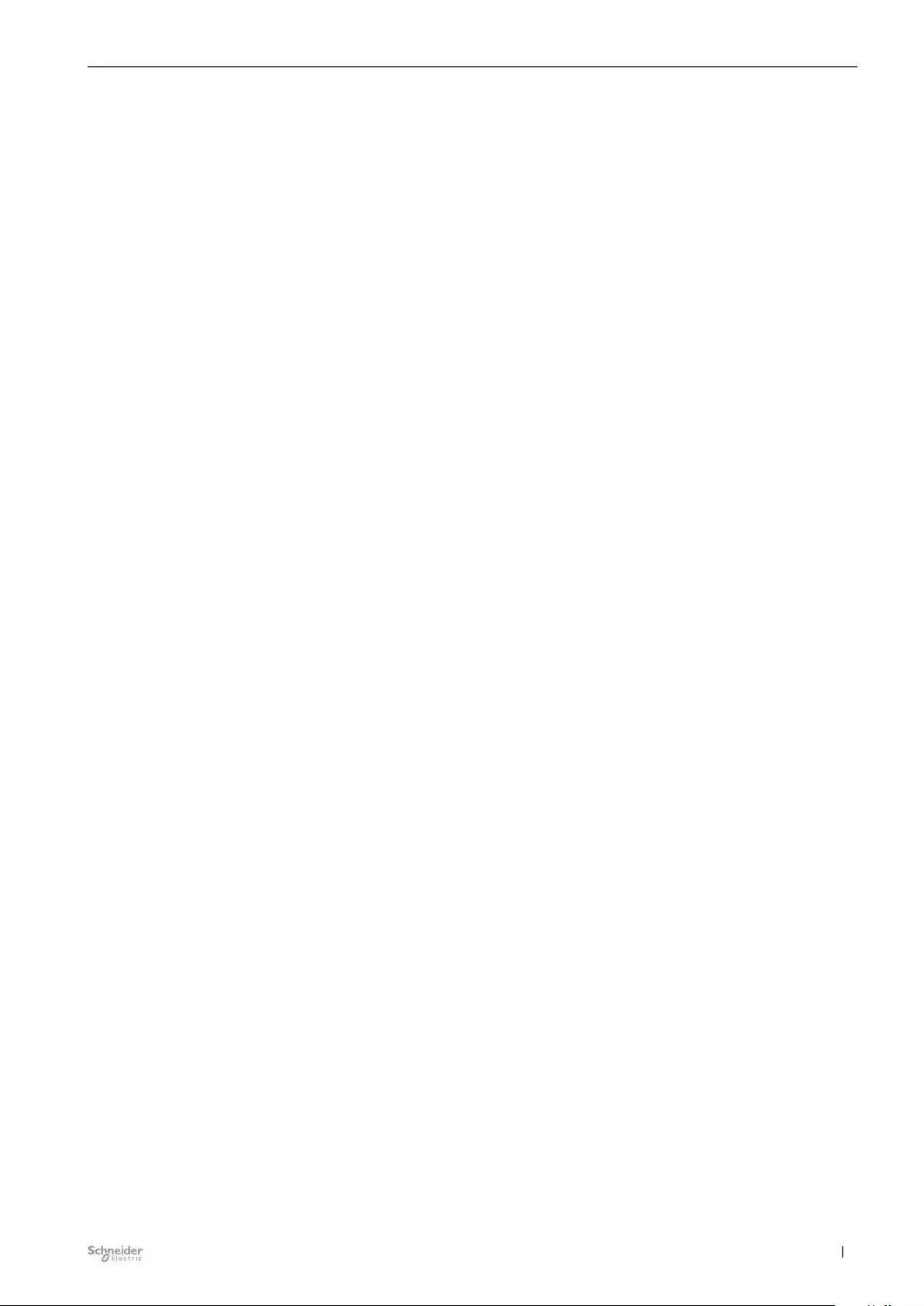
93
05/20-5800/1.0 MTN6705-0008 | MTN6805-0008 |
Extended settings for blind / roller shutter Switch Blind 5800/1.0
Behavior at end of locking
If the locking function has been switched o again by a new object value, you can
operate the drive normally again. If the drive is to perform an automatic action after
the locking function has been terminated, you can dene it with this parameter:
•No reaction: the drive remains in its current position.
•Up: the drive moves to the upper end position.
•Down: the drive moves to the lower end position.
•Move to position prior locking: the drive returns to the position it had before the
locking.
•Accept current automatic position: this setting is only useful if the automatic
function is active. The drive moves to the last automatic position requested.
Lock behavior after download
After a download, the lock function is also set as in the case of bus voltage recov-
ery. The parameter “Behavior after download” determines which state is set.
If the “Behavior after download” parameter is set to “As before download”, the lock-
ing function is activated as previously set and the relay is switched accordingly.
Lock behavior after bus voltage recovery
•Disabled
The locking function is not activated after a bus voltage recovery, regardless of
the state it had before the bus voltage failure.
•Enabled
After a bus voltage recovery, the locking function becomes active and the output
is switched to the state that you dened via the parameter Behavior at start of
locking. If you have set the value “No reaction” here, the output is locked in its
current state.
•As before bus voltage failure
The locking function is brought to the state that was active before the bus
voltage failure. If the locking function was active, the output is controlled by its
settings in the parameter Behavior at start of locking.
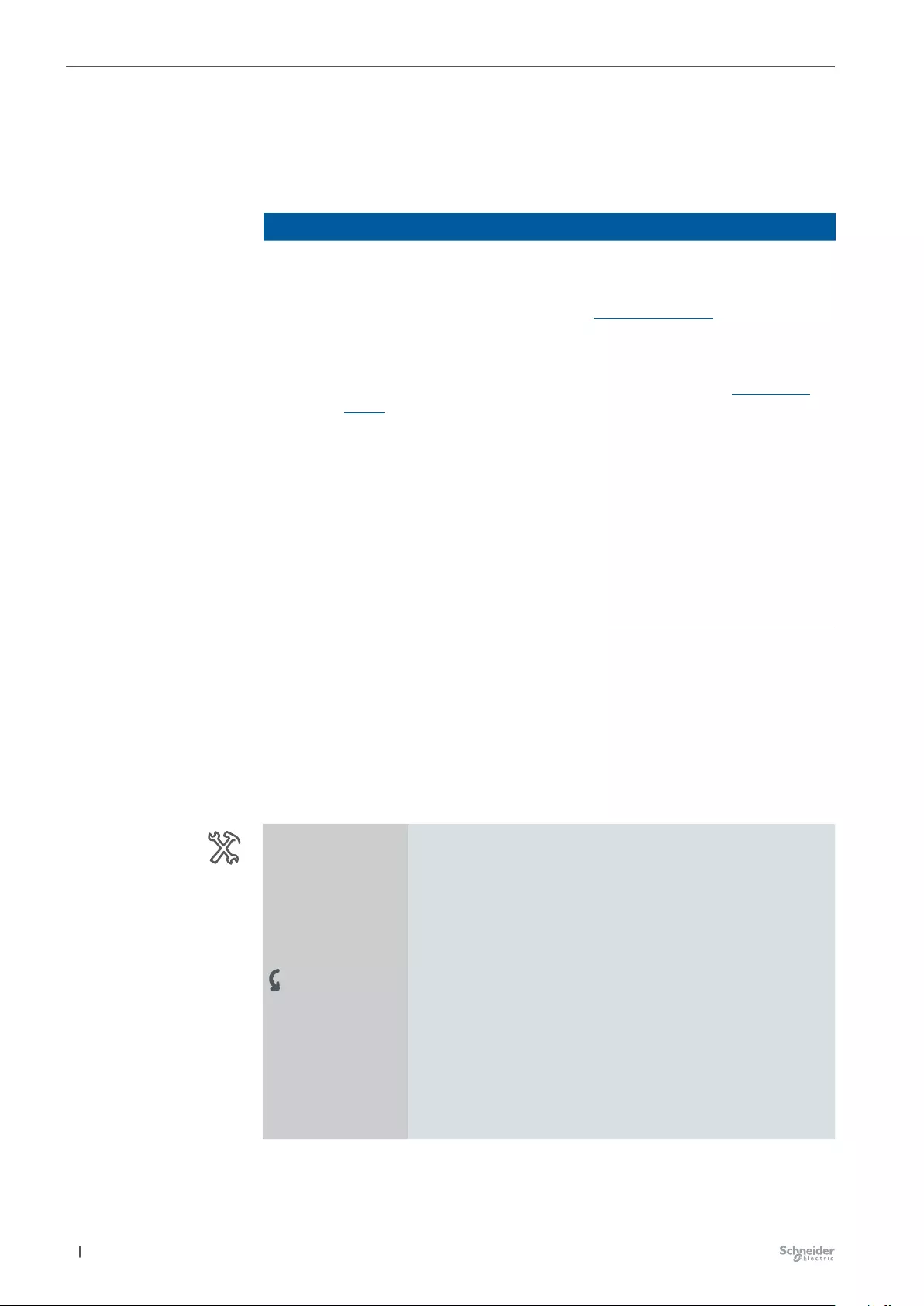
94 05/20-5800/1.0MTN6705-0008 | MTN6805-0008 |
Extended settings for blind / roller shutter Switch Blind 5800/1.0
Movement range limits
For certain applications, e.g. in the case of open tilting windows or window boxes
for owers in the summer, it may be helpful or necessary to limit the possible move-
ment range of a drive temporarily or permanently.
NOTE
Blinds / roller shutters can be damaged.
•The blinds / roller shutters may move outside the movement range
limits and into any open windows. For this reason, consider where the
reference movement is to be made (Calibration --> 98).
•After a download or bus voltage recovery, a reference movement is
made after initialization, even if the "General reference movement"
function is disabled. The blinds / roller shutters may move outside
the movement range limits and into any open windows. (Calibration
--> 98)
•After a download or bus voltage recovery, the movement range
limitation may be disabled because no activation telegram has been
received.
•For this reason, consider where the reference movement is to be
made: The reference movement after initialization is generally carried
out towards the upper end position. A reference movement to the low-
er end position is only carried out if the parameter "Reference position"
is set to "lower".
•Functions with a higher priority, such as safety function or alarm
function, can also control blinds / roller shutters outside the movement
range limitation.
If movement range limitation is active, manual operation, automatic functions or
scene calls can only move the drive within the dened limit. The limitation also
applies to motion commands from functions a lower priority. Only a higher-level
function with a higher priority can still be used to move the drive to a dierent posi-
tion outside the limit. This must be taken into account if the movement range is to
be limited due to an obstacle. Obstacles in operation must be avoided.
You can activate the limits of the movement range individually for each output
channel (enabled).
Master / Ext. 1/2
Output 1+2 / 3+4 / 5+6
/ 7+8
-Blind / roller shutter
Movement range limits
-Automatic, Locking &
Calibration settings Movement range limits Disabled
Enabled
Limit movement range Immediately after bus voltage
recovery
At object value "1"
At object value "0"
Feedback for range limitation Disabled
Enabled
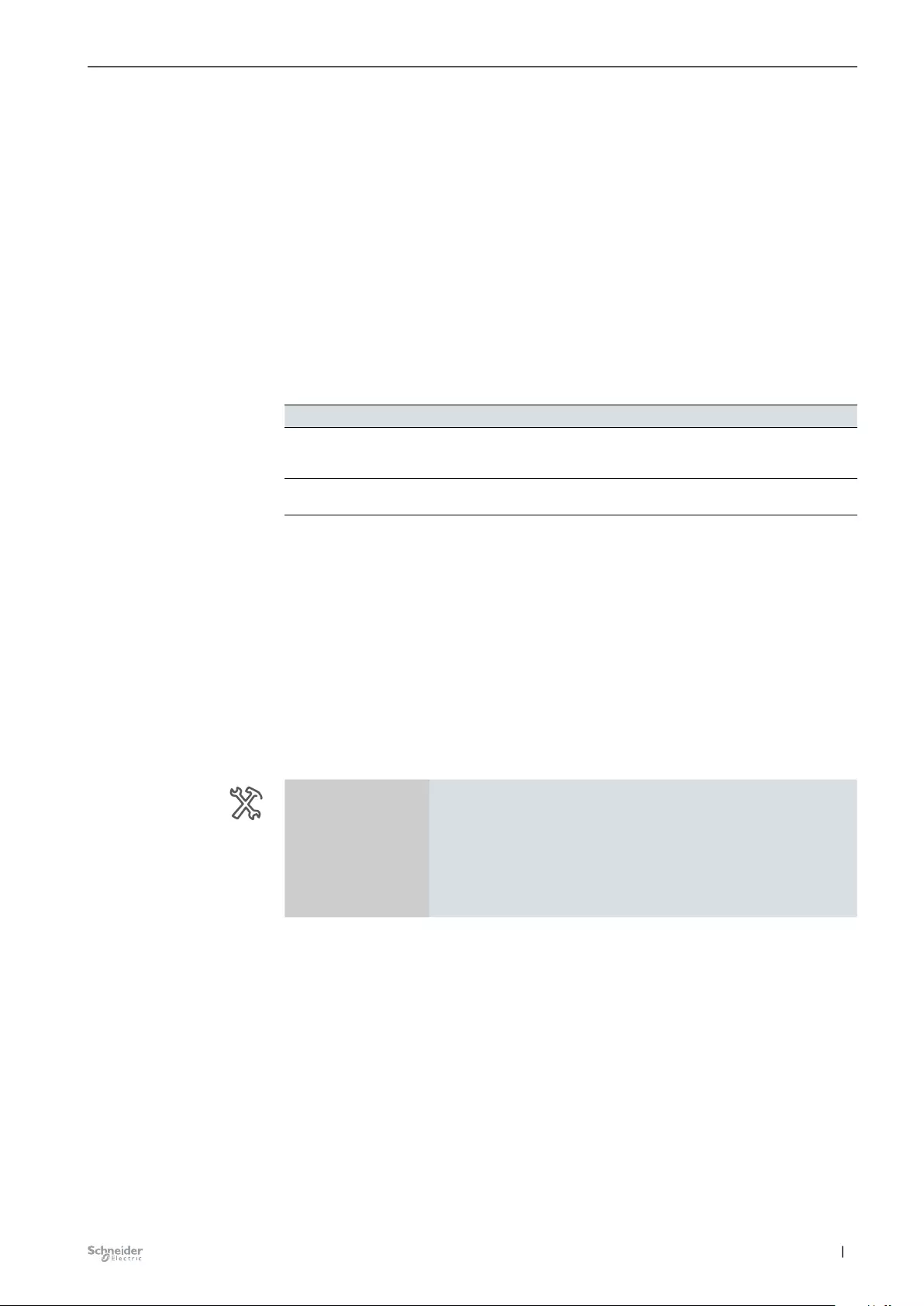
95
05/20-5800/1.0 MTN6705-0008 | MTN6805-0008 |
Extended settings for blind / roller shutter Switch Blind 5800/1.0
After the function “Movement range limits” has been enabled, the parameter “Limit
movement range” appears. Here you can dene when and how the function is
activated for the channel.
•Immediately after bus voltage recovery: the function becomes active immedi-
ately after bus voltage recovery or after a download. The drive can only move
between the limits. Only a function with a higher priority can move the drive to a
position outside the limit.
•At object value “1”: the object value “1” activates the limit. If the object value “0”
is received, the entire movement range is enabled again.
•At object value “0”: the object value “0” activates the limit. A telegram with the
object value “1” deactivates the limit.
In the case of activation by an object value, an additional group object “Activate
movement range limits”, which can be used to switch the limit on and o, appears
for this channel.
No. Name Object function Length Behavior Data Type
44 Master Output 1+2
name of the channel
Activate move-
ment range
limits
1 bit Received 1.003 Enable
50 Master Output 1+2
name of the channel
Feedback for
range limitation
1 bit Sending 1.003 Enable
In addition, a status feedback object can be enabled that sends the status of the
movement range limits function to the bus.
The value of the status feedback object receives the object value “1” as soon as
the movement range limitation becomes active and the drive reaches the specied
limit.
•If the drive is already within the specied limit when the movement range limita-
tion is activated, the status feedback object immediately sends the object value
“1”.
•If the movement range is left or the limit is canceled due to a function with a
higher priority, the object value changes to “0”.
You can set the limits of the movement range using other parameters:
Master / Ext. 1/2
Output 1+2 / 3+4 / 5+6
/ 7+8
-Blind / roller shutter
Movement range limits
-Automatic, Locking &
Calibration settings Limit movement position Limit range at upper position
Limit range at lower position
If limitation is active, the drive will only move between the limits. The limitation ap-
plies to all motion commands from manual operation, automatic functions, scenes,
and motion commands from functions with a lower priority. It is possible to limit
either the upper position or the lower position.
Group objects of the function
"Movement range limits"
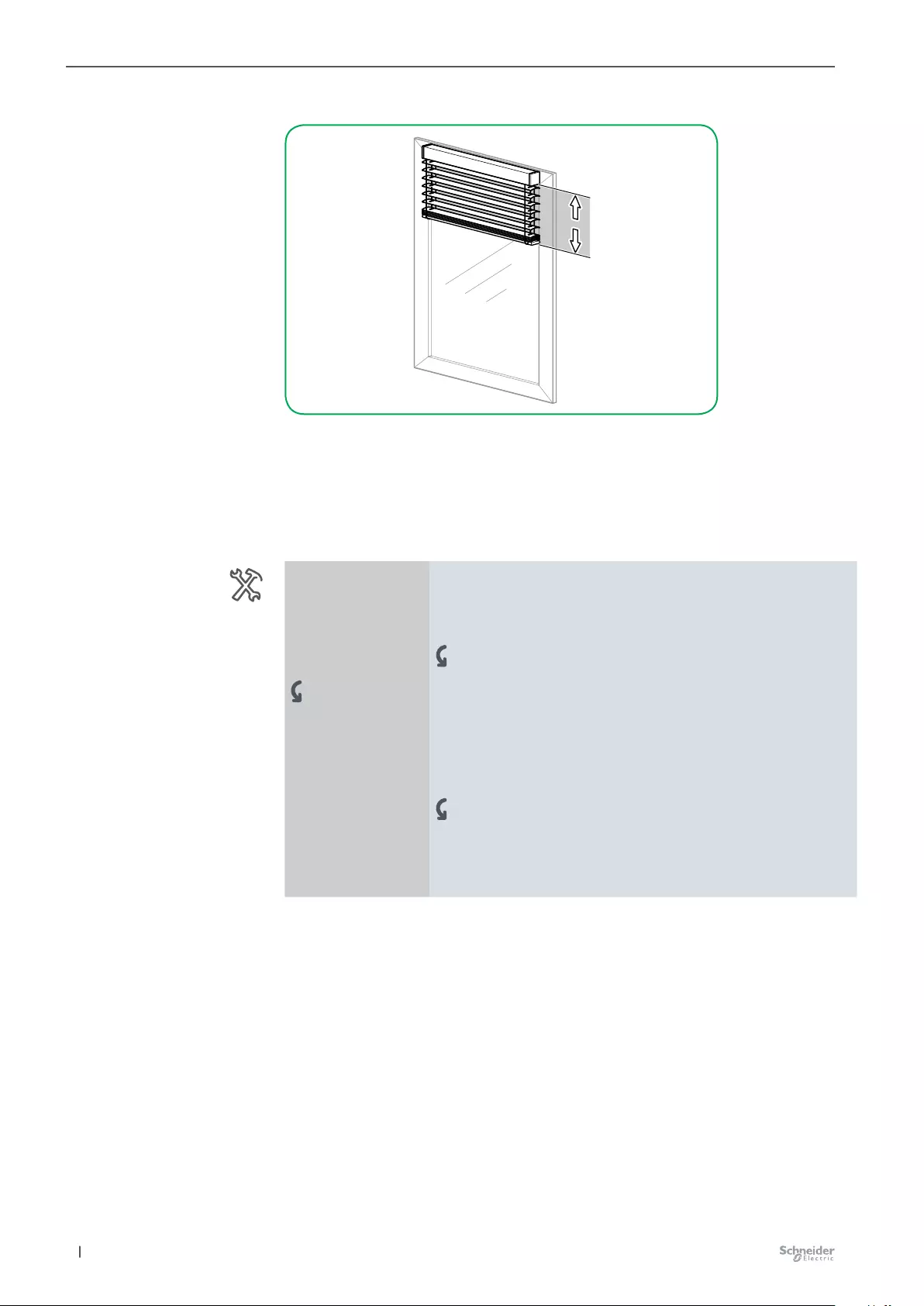
96 05/20-5800/1.0MTN6705-0008 | MTN6805-0008 |
Extended settings for blind / roller shutter Switch Blind 5800/1.0
Limit range at lower position with upper limit = 0% (x) and lower limit = 25%
If limitation is active, the drive will only move between the limits.
If the drive is outside the limits when movement range limitation is activated, it is
automatically moved to the nearest limit and stops there.
If a drive reaches its movement range limits, this can be signaled to the bus via a
status feedback object. Functions that depend on it, e.g. opening a window, can
now be executed.
Master / Ext. 1/2
Output 1+2 / 3+4 / 5+6
/ 7+8
-Blind / roller shutter
Movement range limits
-Automatic, Locking &
Calibration settings
Limit movement position Limit range at lower position
Upper limit value in % (x) 0
Lower limit value in % 100 (0-100)
Limit movement position
Limit range at upper position
Upper limit value in % 100 (0-100)
Lower limit in % (x) 0
The movement range limitation function is often selected in summer when solar
radiation is strong, so that it does not heat up rooms or dazzle people. The drive
can no longer be moved manually all the way up, but in the event of a storm the
weather alarm will move the blind to the safe position.
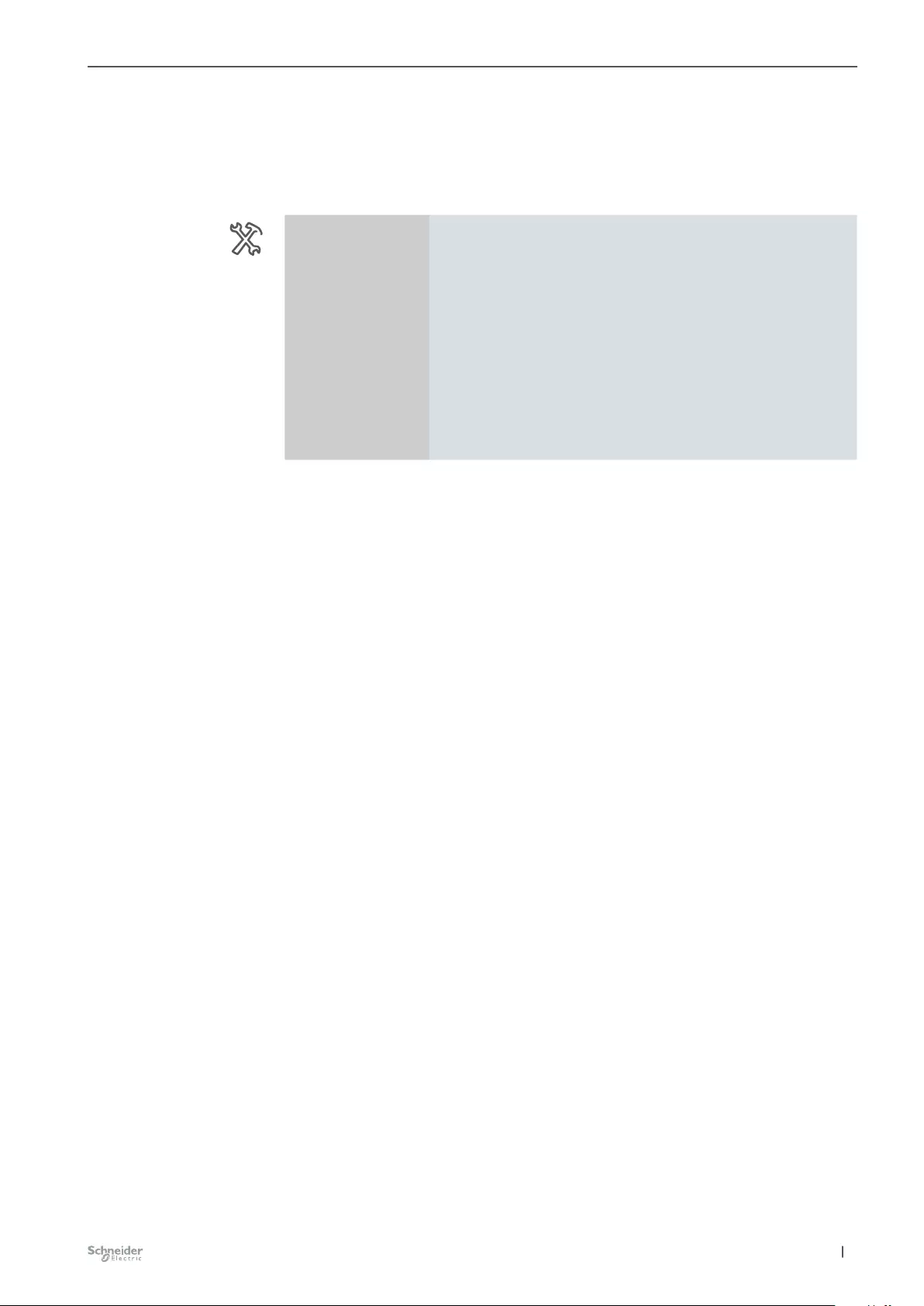
97
05/20-5800/1.0 MTN6705-0008 | MTN6805-0008 |
Extended settings for blind / roller shutter Switch Blind 5800/1.0
Drive behavior after end of movement restriction
If the limitation of the movement range is determined by object values and a new
object value cancels an active limitation, then you can operate the drive normally
again. If the drive is to perform an automatic action in this case, you can dene it
with the following parameter:
Master / Ext. 1/2
Output 1+2 / 3+4 / 5+6
/ 7+8
-Blind / roller shutter
Movement range limits
-Automatic, Locking &
Calibration settings
Behavior at the end of movement
restriction No reaction
Up
Down
Move to position prior to movement
restriction
Accept current automatic position
Values to be set:
•No reaction: the drive remains in its current position.
•Up: the drive moves to the upper end position.
•Down: the drive moves to the lower end position.
•Move to position prior to movement restriction: the drive returns to the position it
had before the movement restriction.
•Accept current automatic position: this setting is only useful if the automatic
function is active. The drive moves to the last automatic position requested.
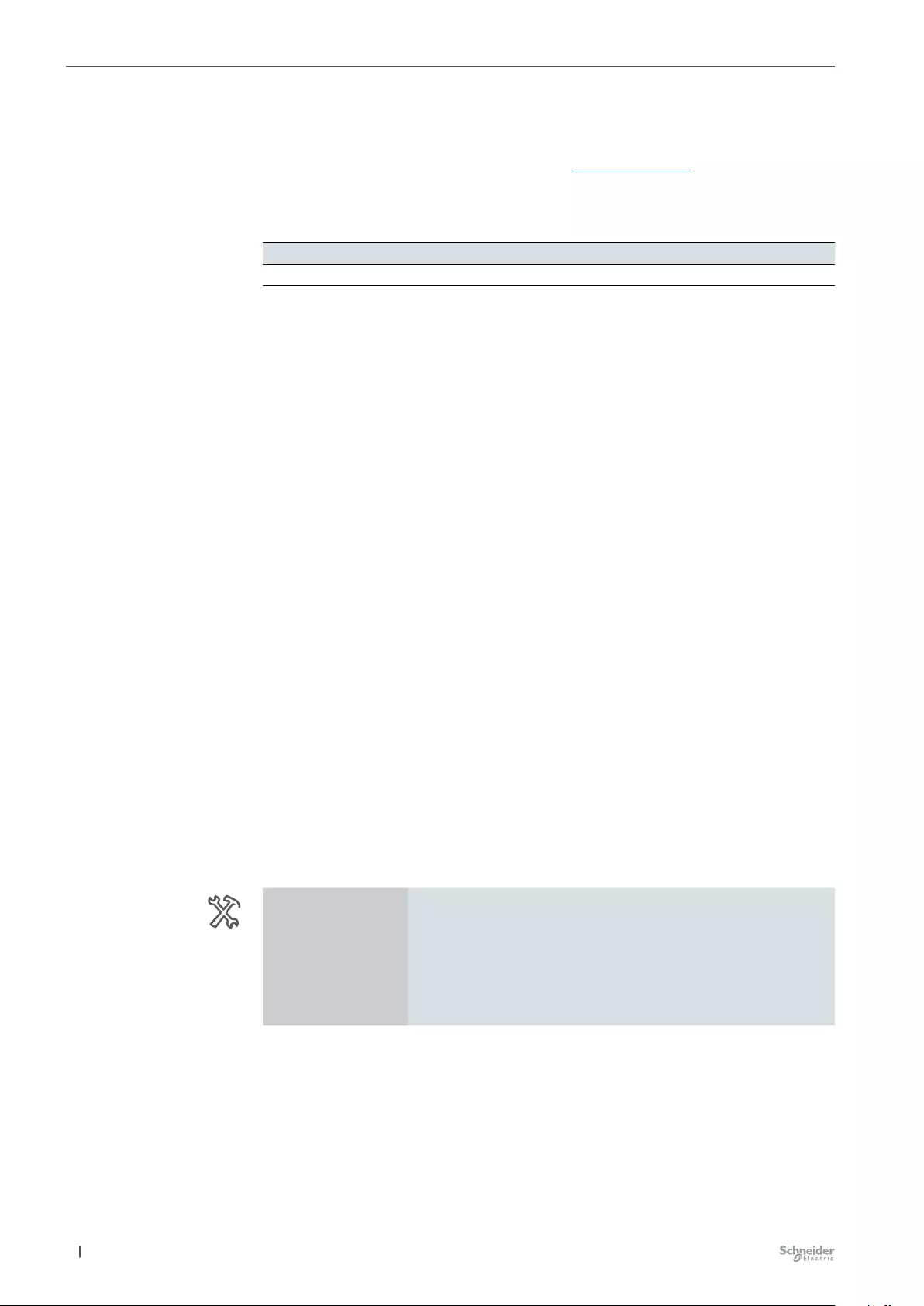
98 05/20-5800/1.0MTN6705-0008 | MTN6805-0008 |
Extended settings for blind / roller shutter Switch Blind 5800/1.0
Calibration
The calibrating function is activated centrally on the Global settings for roller shutter
and blind tab with the parameter Calibration. Calibration --> 32
If the function has been activated globally, the following group object is available for
all channels and each channel can use the calibrating function:
No. Name Object function Length Behavior Data Type
17 Central Calibration 1 bit Received 1.010 Start/Stop
The device calculates the current position of a drive from the running times you
have set for the drive and from the control commands it executes. This calculation
must be performed because there is no feedback from the drive regarding its posi-
tion. Even if you have set the running times very precisely, the internally calculated
height position will deviate slightly from the actual height position after a number of
movements. This is due to mechanical tolerances and weather conditions (tem-
perature uctuations, frost, rain, etc.).
The blind channel can reset these deviations by means of reference runs. For this
purpose, it moves the drives to the upper or lower end position. After the reference
run, the internal position calculation starts again from a xed value. Any deviations
that have arisen in the meantime are thus eliminated.
Note: The calibration function is especially important if you work a lot with position
commands and high positioning accuracy is required. If the blind is controlled ex-
clusively using the basic functions and position commands do not matter, then you
do not need this function.
Operating principle
A reference movement can be triggered by a telegram on the central calibration
object or after a certain number of movements. After a reference movement has
been triggered, the drive moves to the desired reference position (end position). If
you have set both end positions as reference positions, the drive will move to the
nearest end position, depending on its current position. In order to ensure that the
drive reliably reaches the desired end position, the actuator adds a running time
allowance of 5% of the total running time to the calculated travel time for each
reference movement.
Note: If a weather alarm or other higher-level function is activated during a cali-
brating function, the calibrating function is canceled and the higher-level function is
executed.
Per channel:
Master / Ext. 1/2
Output 1+2 / 3+4 / 5+6
/ 7+8
-Blind / roller shutter
Calibration
-Automatic, Locking &
Calibration settings Calibration Disabled
Enabled
Group object for
calibration
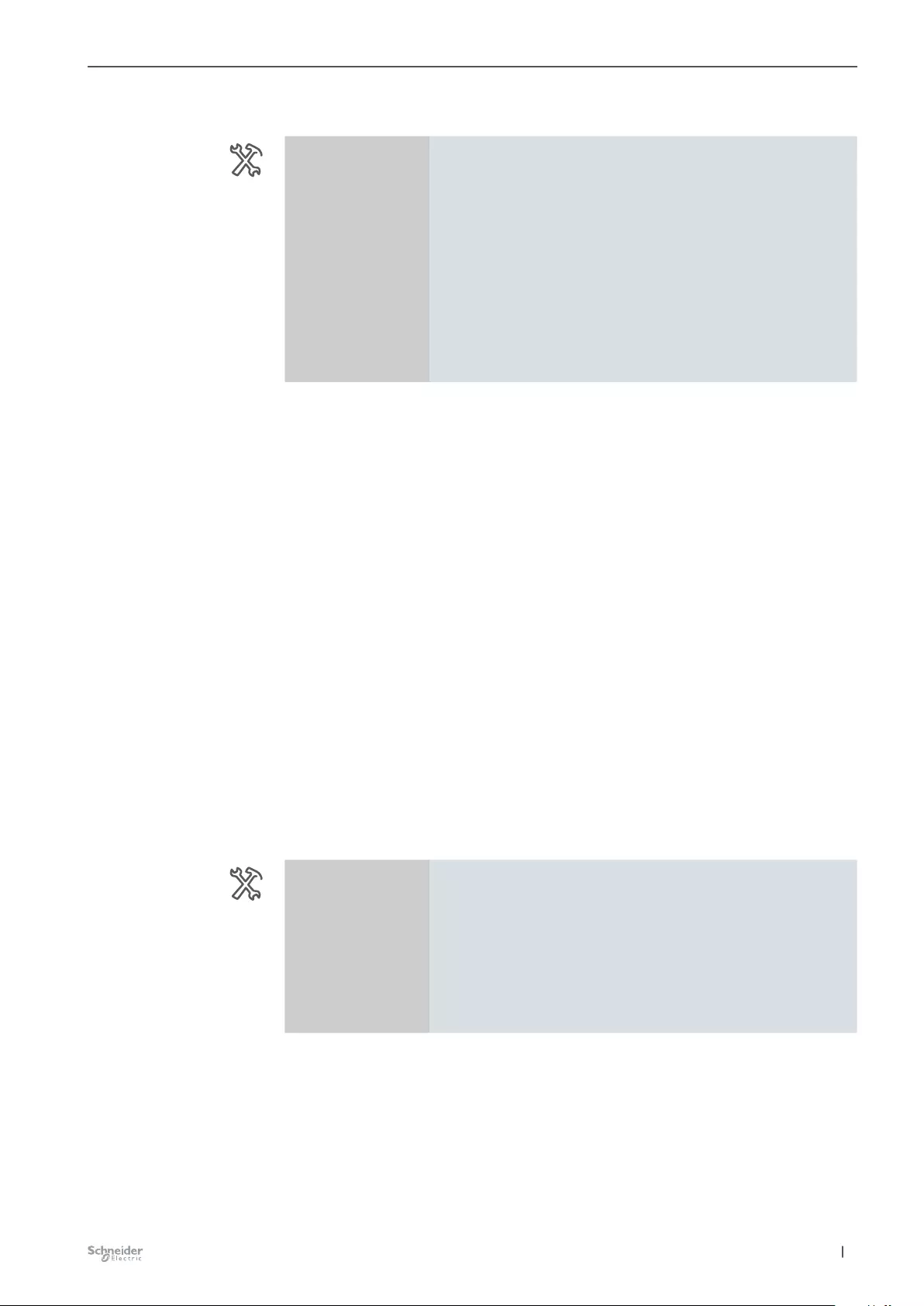
99
05/20-5800/1.0 MTN6705-0008 | MTN6805-0008 |
Extended settings for blind / roller shutter Switch Blind 5800/1.0
Trigger of calibration
Master / Ext. 1/2
Output 1+2 / 3+4 / 5+6
/ 7+8
-Blind / roller shutter
Calibration
-Automatic, Locking &
Calibration settings Trigger of calibration Number of movements
Value "1" on calibration object
No. of movements or calibration object
Delay of calibration via object
(0...255, unit = 1 s) 0
Number of movements until
calibration 7 (1-20)
Triggering a reference movement after a number of movements
The channel adds up the total number of movements, irrespective of the control
command that triggered the movements. Once the dened number of movements
has been reached, the drive rst performs a reference movement before the next
positioning command. It then moves to the requested position. After the reference
movement, the movement counter is reset.
Trigger reference movement via group object
If the object “Calibration” receives the value “1”, a reference movement is started
for all assigned channels. In order not to overload the power supply of the blind
system, you can select a “Delay of calibration” for each channel. If a new value
“1” is received on the object during this delay time, the delay time is restarted. The
object value “0” has no meaning.
Trigger reference movement after a number of movements or via group ob-
ject
It is also possible to select a logic operation from the number of movements or the
calibration telegram.
Reference position
After a reference movement has been triggered, the drive moves to the desired pa-
rameterizable reference position (end position). If you have set both end positions
as reference positions, the drive will move to the nearest end position, depending
on its current position.
Master / Ext. 1/2
Output 1+2 / 3+4 / 5+6
/ 7+8
-Blind / roller shutter
Calibration
-Automatic, Locking &
Calibration settings Reference position upper
lower
upper and lower
Automatic calibration
Each time the drive moves to the dened end position due to a positioning com-
mand, the calibrating function is performed. This means that a running time allow-
ance of 5% of the total running time is added to the calculated travel time required
by the drive to ensure that the drive reliably reaches the desired end position. Once
the end position has been reached, the movement counter is also reset.
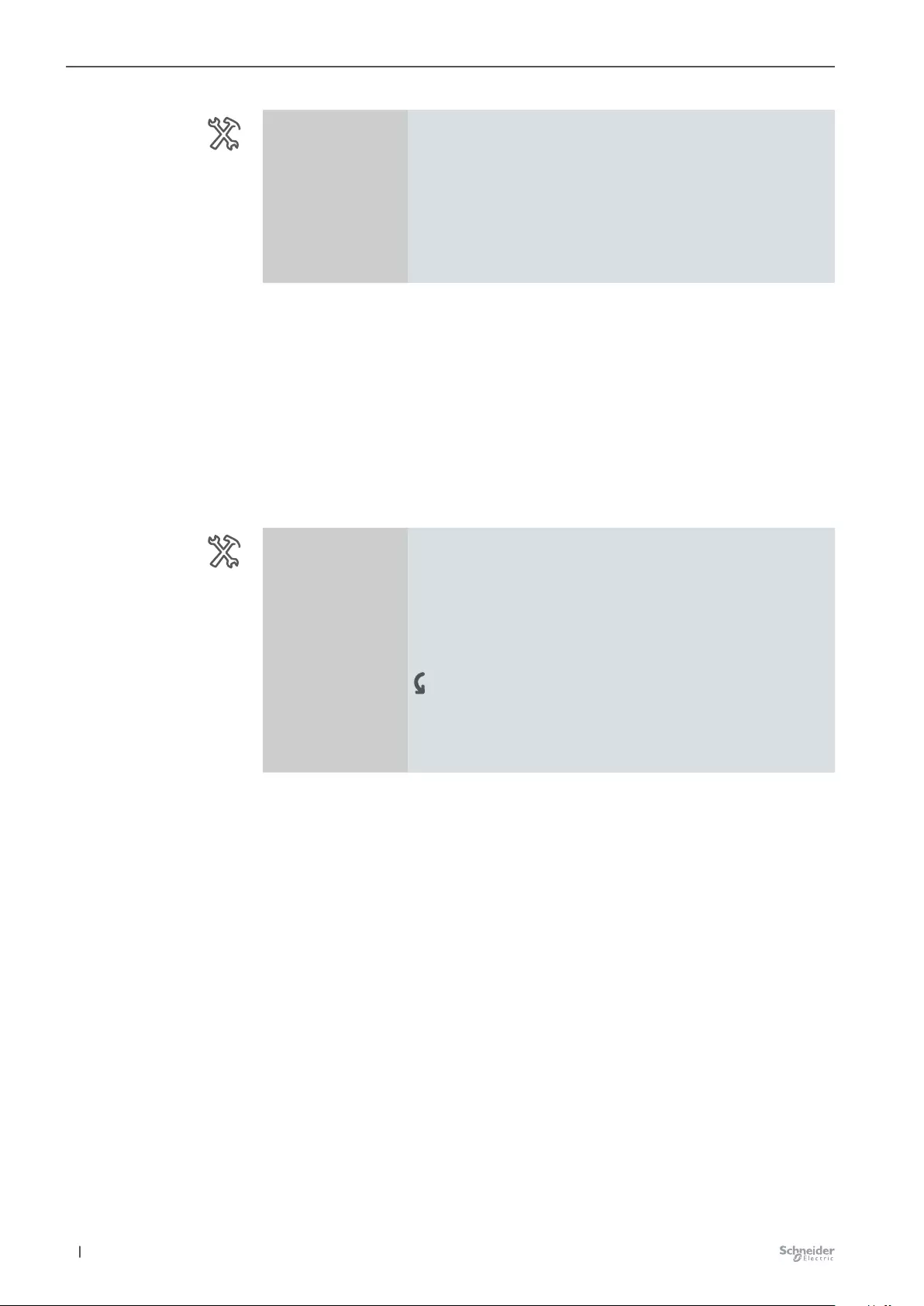
100 05/20-5800/1.0MTN6705-0008 | MTN6805-0008 |
Extended settings for blind / roller shutter Switch Blind 5800/1.0
Master / Ext. 1/2
Output 1+2 / 3+4 / 5+6
/ 7+8
-Blind / roller shutter
Calibration
-Automatic, Locking &
Calibration settings Automatic calibration upper
lower
upper and lower
Position after calibration via object
The height position after the reference movement can be dened using the param-
eter “Position after calibration via object”. If a movement is to be made to a “new
position”, set the height and, in the case of blinds, also the opening angle of the
slats, in the movement range form 0% to 100%.
If the channel receives an absolute positioning command during the reference
movement, it sets the desired position after the reference movement. In this case,
the settings in the parameter “Position after reference movement via object” have
no eect. All other control commands interrupt the calibrating function. The drive
reacts to the received control commands.
Master / Ext. 1/2
Output 1+2 / 3+4 / 5+6
/ 7+8
-Blind / roller shutter
Calibration
-Automatic, Locking &
Calibration settings
Position after calibration via
object Position prior reference movement
remain in reference position
new position
Height position after calibration
in % 0 (0-100)
Slat position after calibration in % 0 (0-100)
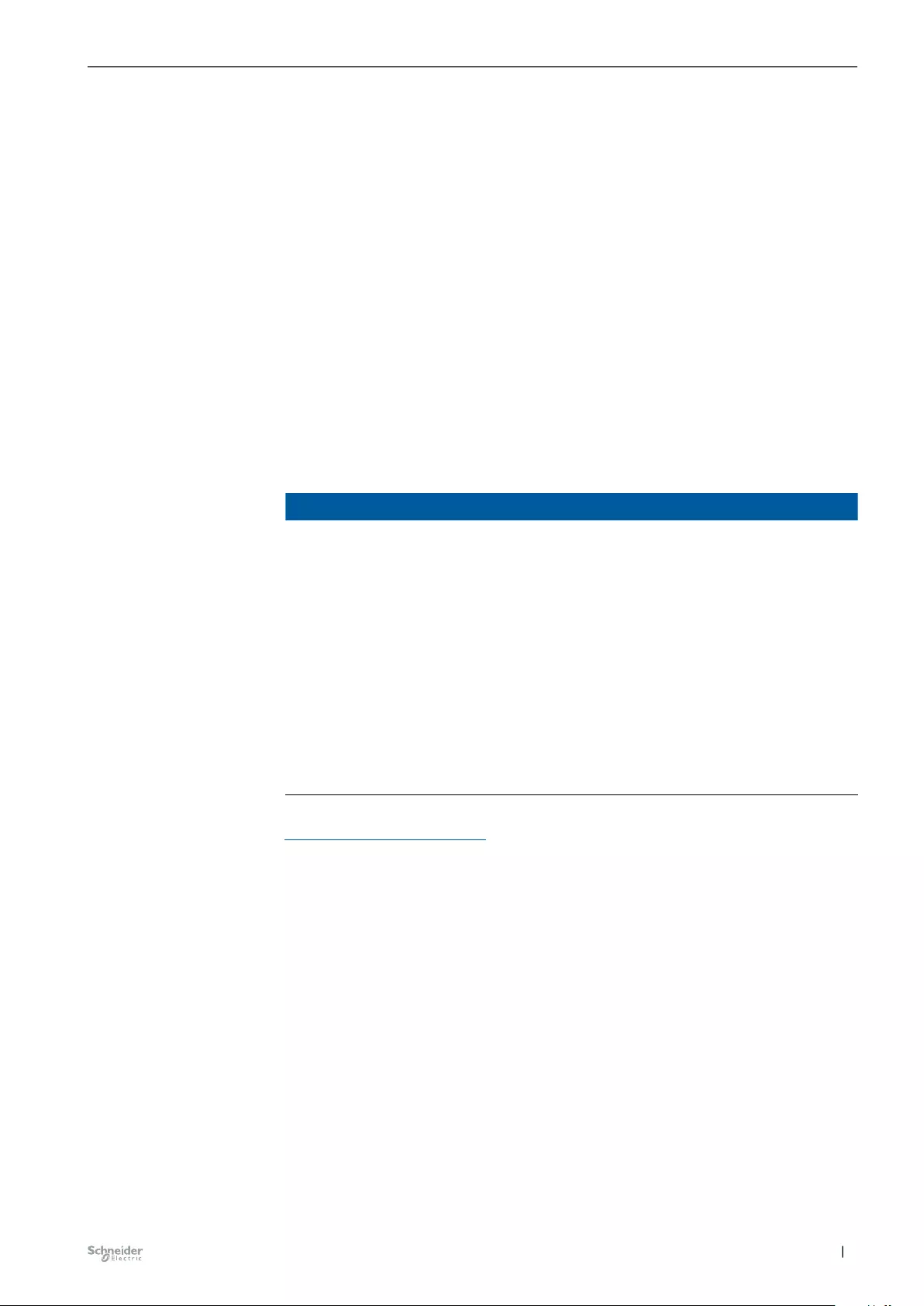
101
05/20-5800/1.0 MTN6705-0008 | MTN6805-0008 |
Extended settings for blind / roller shutter Switch Blind 5800/1.0
Reference movement after initialization
The reference movement after a download or bus voltage recovery serves to obtain
an exact starting position for further positioning movements.
Note: The reference movement after initialization is always carried out, even if the
function “General reference movement” is disabled.
The reference movement is triggered by an absolute positioning command. These
include, for example, receiving a value on the objects “Height position in manual
mode” or “Height position in automatic mode”, the calling of scenes, or movement
to an absolute position in the case of weather alarm, alarm or lock. If, after initial-
ization, the object “Move object in manual mode” receives a value that moves the
blind / roller shutter to the upper end position, the actuator automatically evaluates
this movement as a reference movement.
The reference movement after initialization is generally carried out towards the
upper end position. If you have enabled sending of the status messages “Feedback
for height” and/or “Feedback for slat” , this automatically sends the current status.
Reference movement with movement range limitation:
NOTE
Blinds / roller shutters can be damaged.
•The blinds / roller shutters may move outside the movement range
limits and into any open windows. For this reason, consider where the
reference movement is to be made.
•After a download or bus voltage recovery, a reference movement is
made after initialization, even if the "General reference movement"
function is disabled. The blinds / roller shutters may move outside the
movement range limits and into any open windows.
•For this reason, consider where the reference movement is to be
made: The reference movement after initialization is generally carried
out towards the upper end position. A reference movement to the low-
er end position is only carried out if the parameter "Reference position"
is set to "lower".
Movement range limits --> 94
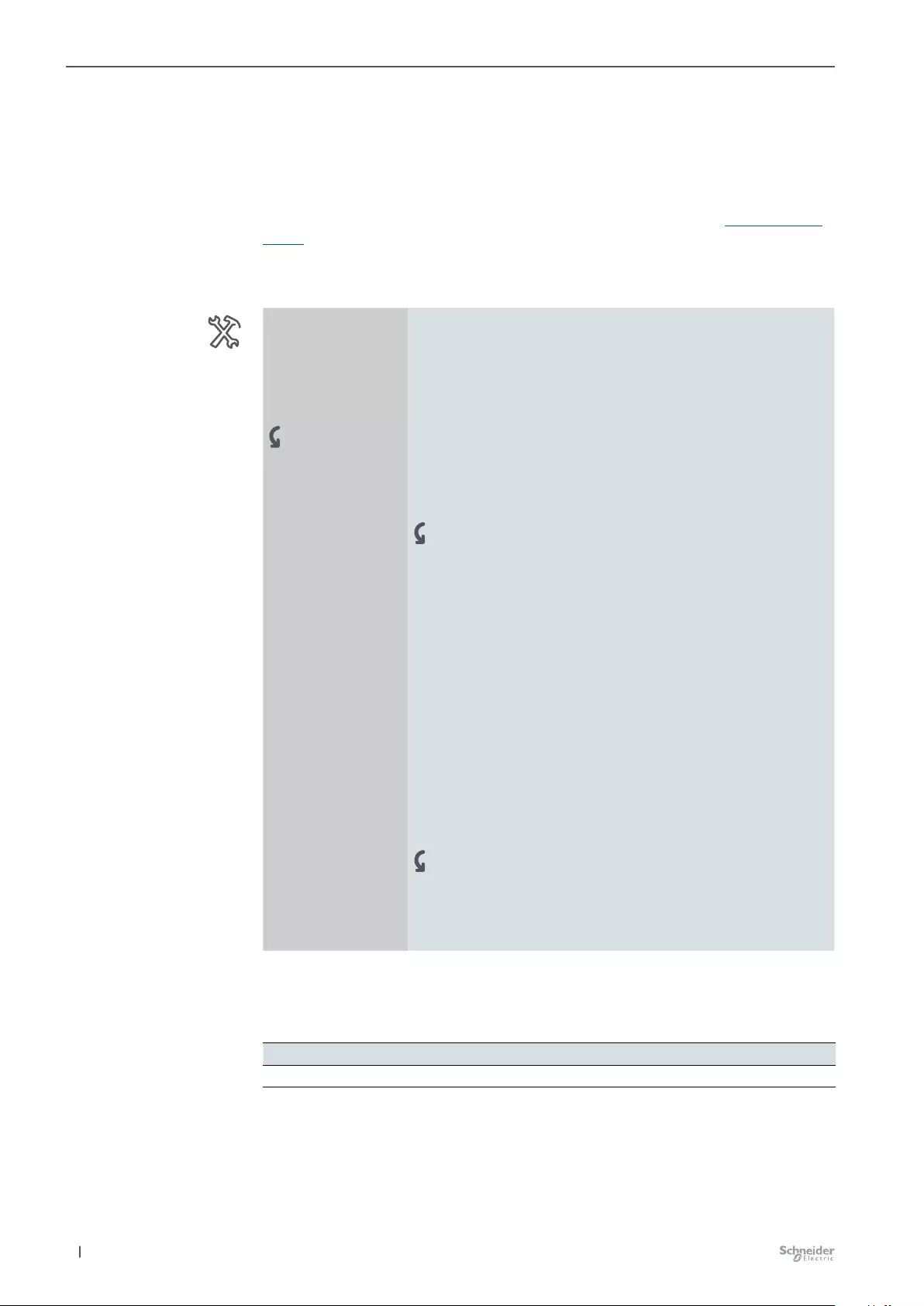
102 05/20-5800/1.0MTN6705-0008 | MTN6805-0008 |
Extended settings for blind / roller shutter Switch Blind 5800/1.0
8.3 Safety and alarm settings
Safety function for blind
The global safety function is activated on the Extended settings tab with the param-
eter Device safety and the global settings are parameterized there. Device safety
--> 22
The eect of the safety function can be parameterized here for each channel. You
can enable the safety function individually for each drive.
Master / Ext. 1/2
Output 1+2 / 3+4 / 5+6
/ 7+8
-Blind / roller shutter
Safety function
-Safety and alarm
settings Safety function Disabled
Enabled
Behavior at start of safety No reaction
Up
Down
Move to position
Height position at start of
safety in % 0 (0-100)
Slat position at start of safety
in % 0 (0-100)
Behavior at end of safety No reaction
Up
Down
Move to position prior safety
Accept current automatic position
Behavior at exceeding cycle
time No reaction
Up
Down
Move to position
Height position on exceeding
cycle time in % 0 (0-100)
Slat position on exceeding
cycle time in % 0 (0-100)
Following global enabling of the device safety, the group object appears.
Group objects
No. Name Object function Length Behavior Data Type
23 Central Safety 1 bit Received 1.005 Alarm
Group object for
central safety
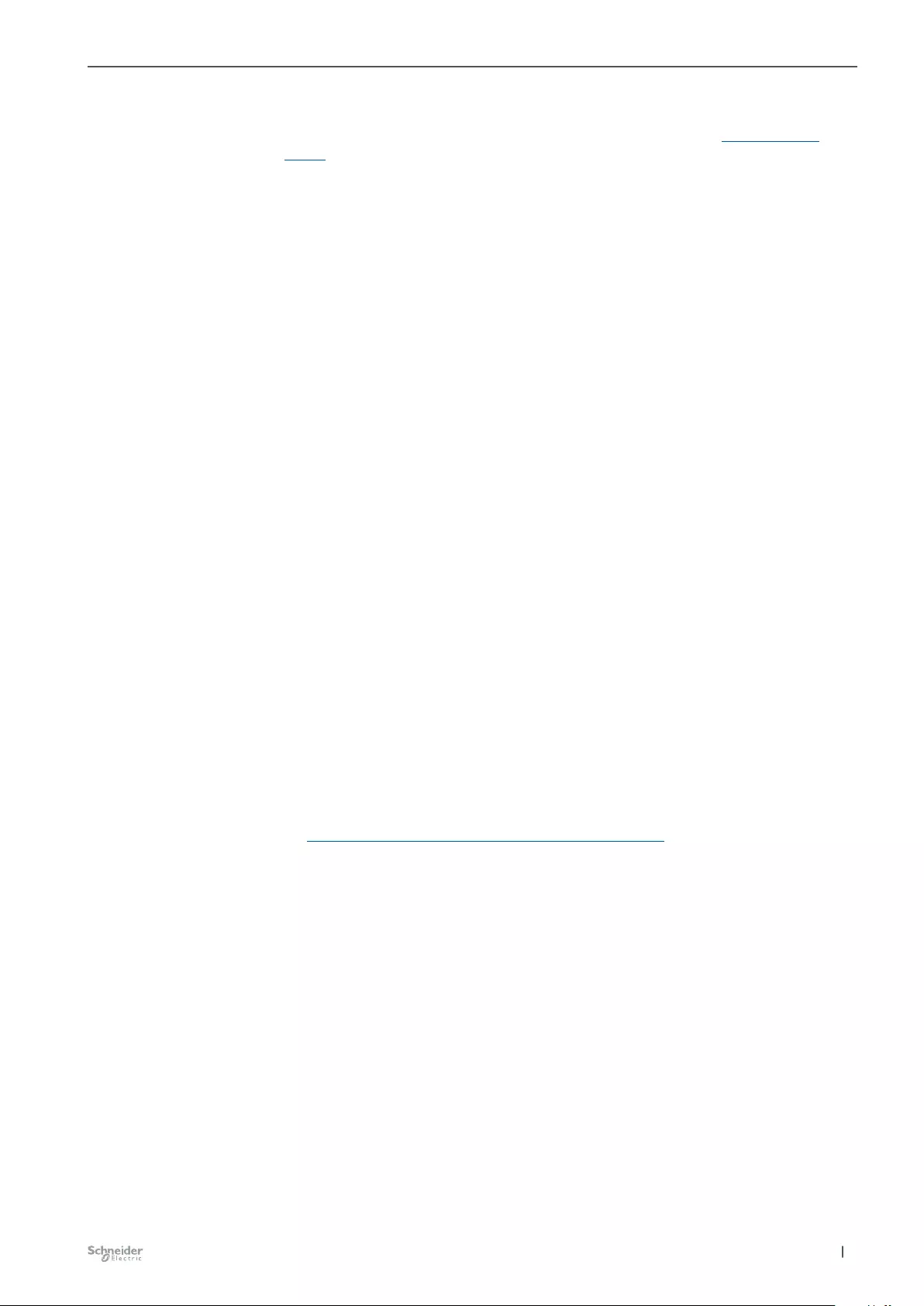
103
05/20-5800/1.0 MTN6705-0008 | MTN6805-0008 |
Extended settings for blind / roller shutter Switch Blind 5800/1.0
The safety function is activated if the safety object receives a telegram with the
object value that you dened with the parameter Device safety (Device safety
--> 22 ). You can dene the reaction using the parameter Behavior at start of
safety.
•No reaction: the drive remains in its current position.
•Up: the drive moves to the upper end position.
•Down: the drive moves to the lower end position.
•Move to position: the drive moves to the dened position for height and slat (for
blind only).
If the safety object receives a telegram with the object value opposite of that for
activation, the safety function is canceled and the output relay adopts the state that
you dened in the parameter Behavior at end of safety.
•No reaction: the drive remains in its current position.
•Up: the drive moves to the upper end position.
•Down: the drive moves to the lower end position.
•Move to position prior safety: the drive returns to the position it had before the
safety telegram.
•Accept current automatic position: this setting is only useful if the automatic
function is active. The drive moves to the last automatic position requested.
The device then waits for a telegram from an external sender within the globally set
cycle time. If such a telegram is not received within the monitoring time, the param-
eter Behavior at exceeding cycle time is used to determine what is to happen.
•No reaction: the drive remains in its current position.
•Up: the drive moves to the upper end position.
•Down: the drive moves to the lower end position.
•Move to position: the drive moves to the dened position for height and slat (for
blind only).
Priority
The safety function is a 1-bit group object with the highest priority. This means that
this object takes precedence over the following group objects:
•Alarm object / Weather alarm objects / Lock object
Priority of functions for roller shutter and blind --> 30
•Scene object
•Central Move up/down blind / roller shutter objects
•Blind / roller shutter automatic objects
•Blind / roller shutter manual objects
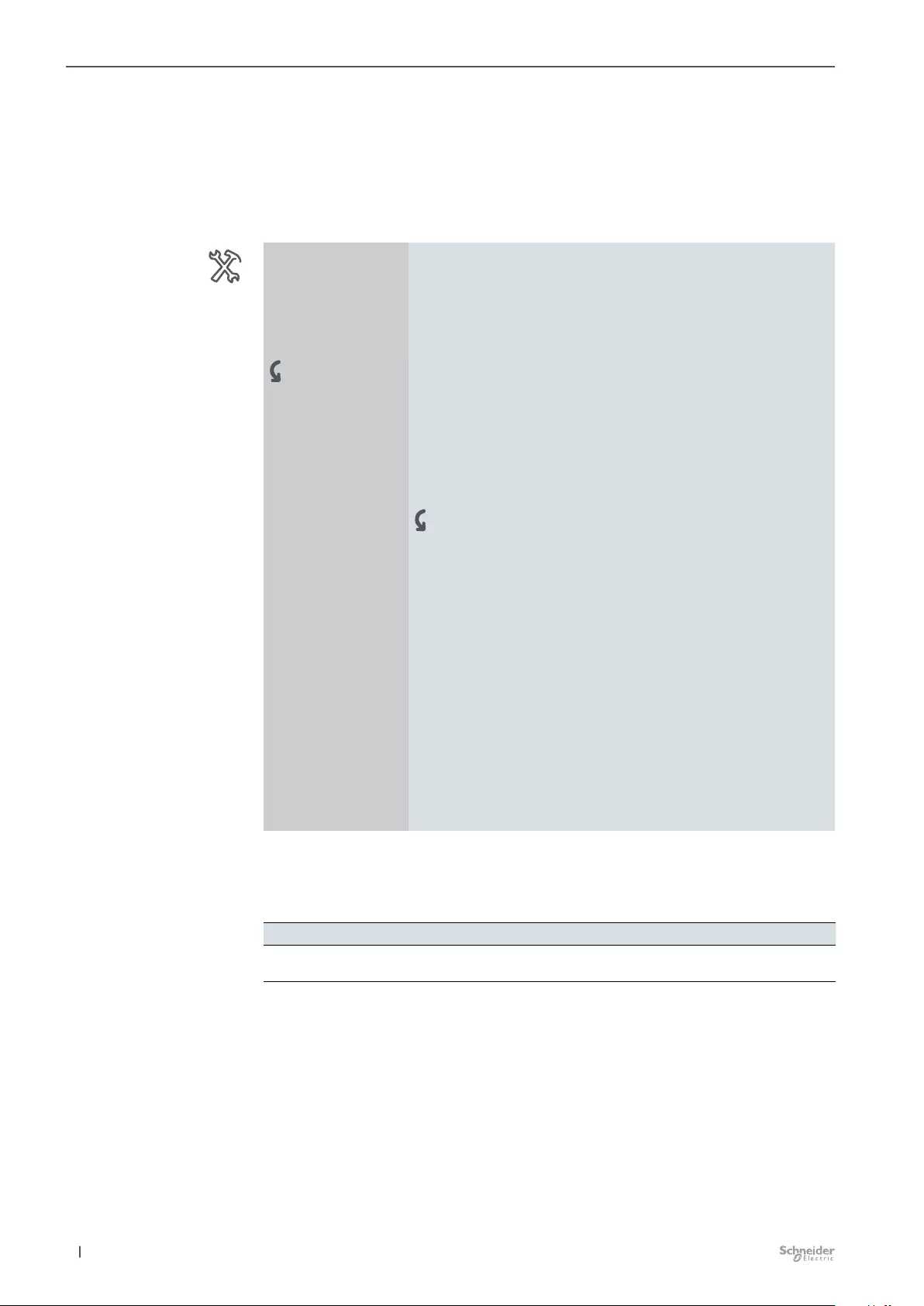
104 05/20-5800/1.0MTN6705-0008 | MTN6805-0008 |
Extended settings for blind / roller shutter Switch Blind 5800/1.0
Alarm function
In the case of an alarm, the alarm function can be used to set each channel to a
desired alarm state. The output is disabled for further operation. Only a higher-level
function with a higher priority can still be used to switch the output to a dierent
state. You can activate the alarm function individually for each output channel. The
alarm function can be parameterized here for each channel.
Master / Ext. 1/2
Output 1+2 / 3+4 / 5+6
/ 7+8
-Blind / roller shutter
Alarm function
-Safety and alarm
settings Alarm function Disabled
Enabled
Alarm At object value "1"
At object value "0"
Behavior at start of alarm No reaction
Up
Down
Move to position
Height position at start of
alarm in % 0 (0-100)
Slat position at start of alarm
in % 0 (0-100)
Behavior at end of alarm No reaction
Up
Down
Move to position prior alarm
Accept current automatic position
Behavior after bus voltage
recovery Disabled
Enabled
As before bus voltage failure
Following enabling, the group object for this channel appears.
Group objects
No. Name Object function Length Behavior Data Type
42 Master Output 1+2
name of the channel
Alarm 1 bit Received 1.005 Alarm
Group objects of the alarm
function
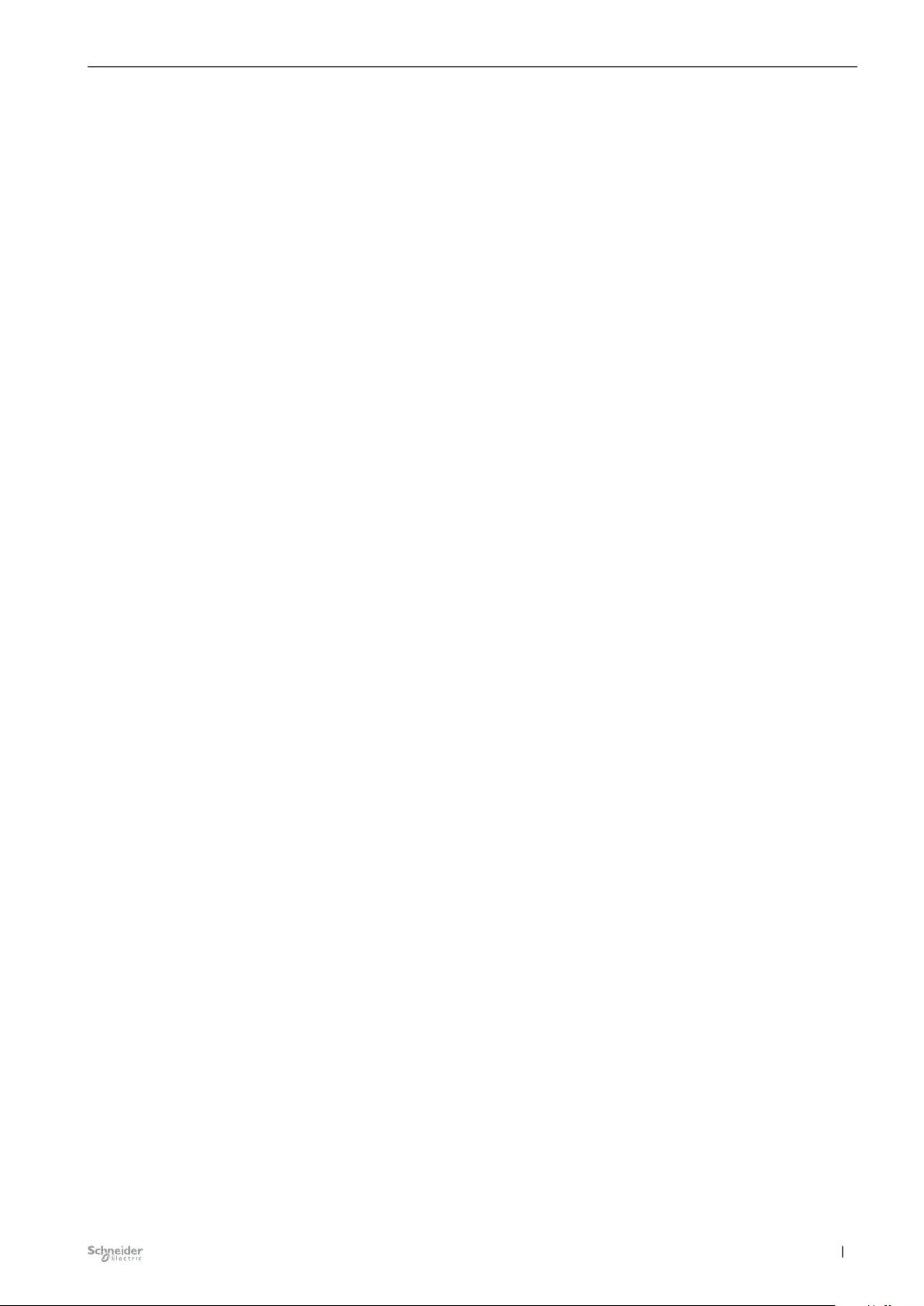
105
05/20-5800/1.0 MTN6705-0008 | MTN6805-0008 |
Extended settings for blind / roller shutter Switch Blind 5800/1.0
Object values for alarm
First select the object value that is to switch on the alarm function:
•At object value “1”: object value “1” switches on the alarm function. If the object
value “0” is received, the alarm function is switched o again.
•At object value “0”: object value “0” switches on the alarm function. A telegram
with the object value “1” deactivates the function again.
The alarm function is activated if the alarm object receives a telegram with the ob-
ject value that you dened with the parameter Alarm. The reaction is dened by the
parameter Behavior at start of alarm.
•No reaction: the drive remains in its current position.
•Up: the drive moves to the upper end position.
•Down: the drive moves to the lower end position.
•Move to position: the drive moves to the dened position for height and slat (for
blind only).
Once the drive has performed the desired action, it remains in this position and
cannot be operated while the alarm function is active. Only when a function with a
higher priority becomes active will the reaction dened there be executed.
If the alarm object receives a telegram with the object value opposite of that for
activation, the alarm function is canceled and the output relay adopts the state that
you dened in the parameter Behavior at end of alarm.
•No reaction: the drive remains in its current position.
•Up: the drive moves to the upper end position.
•Down: the drive moves to the lower end position.
•Move to position prior alarm: the drive returns to the position it had before the
alarm telegram.
•Accept current automatic position: this setting is only useful if the automatic
function is active. The drive moves to the last automatic position requested.
Behavior of the alarm after bus voltage recovery
•Disabled: the alarm function is not activated after a bus voltage recovery, re-
gardless of the state it had before the bus voltage failure.
•Enabled: after a bus voltage recovery, the alarm function becomes active and
the output is switched to the state that you dened via the parameter Behavior
at start of alarm.
•As before bus voltage failure: the alarm function is brought to the state that was
active before the bus voltage failure. If the alarm function was active, the output
is controlled by its settings in the parameter Behavior at start of alarm.
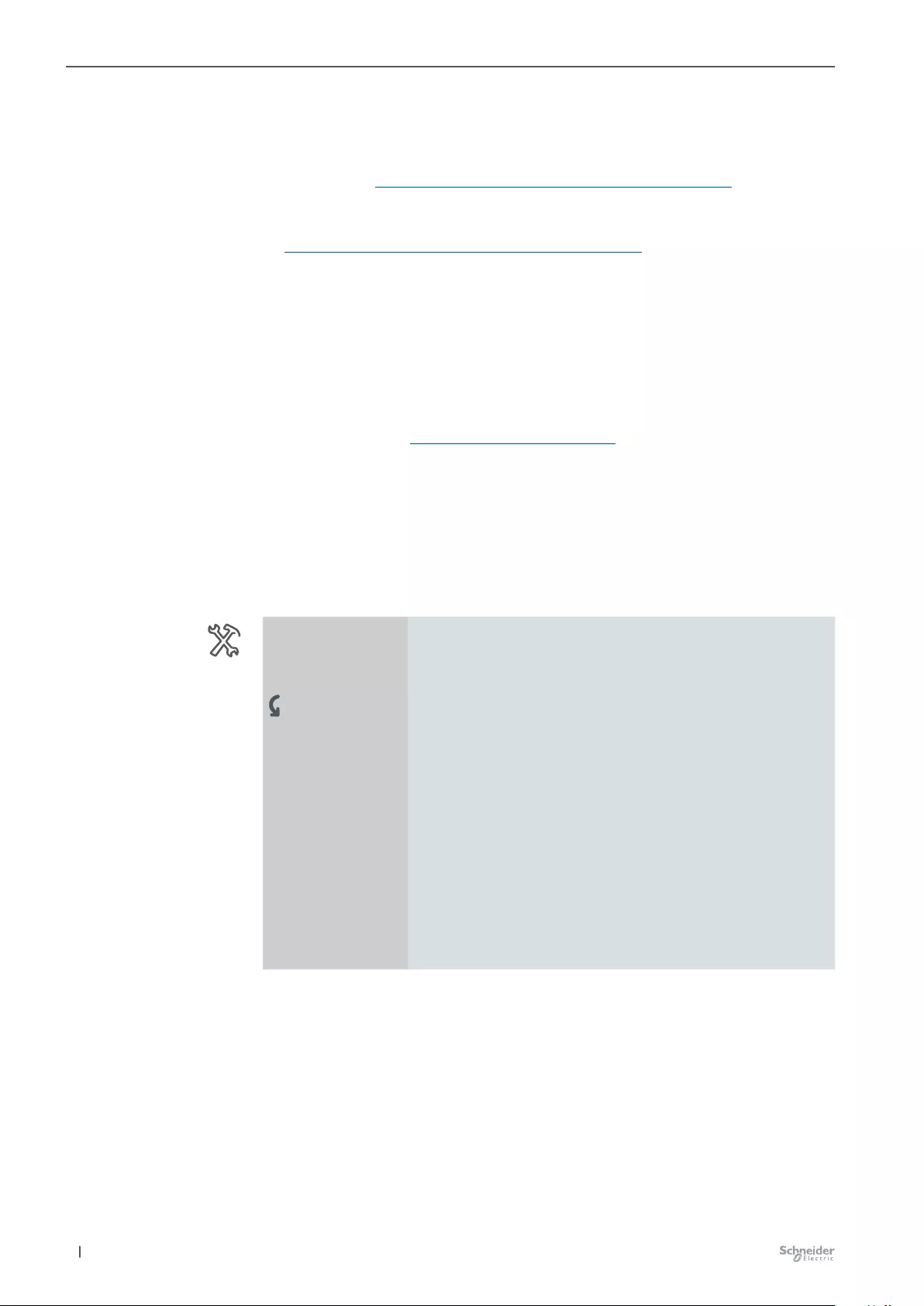
106 05/20-5800/1.0MTN6705-0008 | MTN6805-0008 |
Extended settings for blind / roller shutter Switch Blind 5800/1.0
Priority
The alarm function is a 1-bit group object with high priority. The device safety
function has the highest priority. The priority order for blind / roller shutter can be
dened globally Priority of functions for roller shutter and blind --> 30. The alarm
object takes precedence over the following group objects:
•Weather alarm objects / Lock object
Priority of functions for roller shutter and blind --> 30
•Scene object
•Central Move up/down blind / roller shutter objects
•Blind / roller shutter automatic objects
•Blind / roller shutter manual objects
Weather alarm function
The weather alarms are activated globally on the Extended settings tab with the
parameter Global settings for roller shutter and blind, and the global settings are
parameterized there. Weather alarm function --> 29
There are now 5 dierent weather alarms available, together with their group ob-
jects.
The monitoring of the signals of the activated weather sensors can be carried out
cyclically. The device then expects a telegram from the relevant sensor within the
cycle time set. If such a telegram is not received within the monitoring time, the as-
sociated weather alarm is nevertheless triggered for safety reasons (if, for example,
the sensor or the cable connection between sensor and blind channel is defective
and no message would be sent in the event of a genuine alarm).
Extended
settings Global settings for roller shutter and blind
Weather alarm function Disabled
Enabled
Monitoring time for wind alarm 1 Disabled
1 s ... 12 h
Monitoring time for wind alarm 2 Disabled
1 s ... 12 h
Monitoring time for wind alarm 3 Disabled
1 s ... 12 h
Monitoring time for rain alarm Disabled
1 s ... 12 h
Monitoring time for frost alarm Disabled
1 s ... 12 h
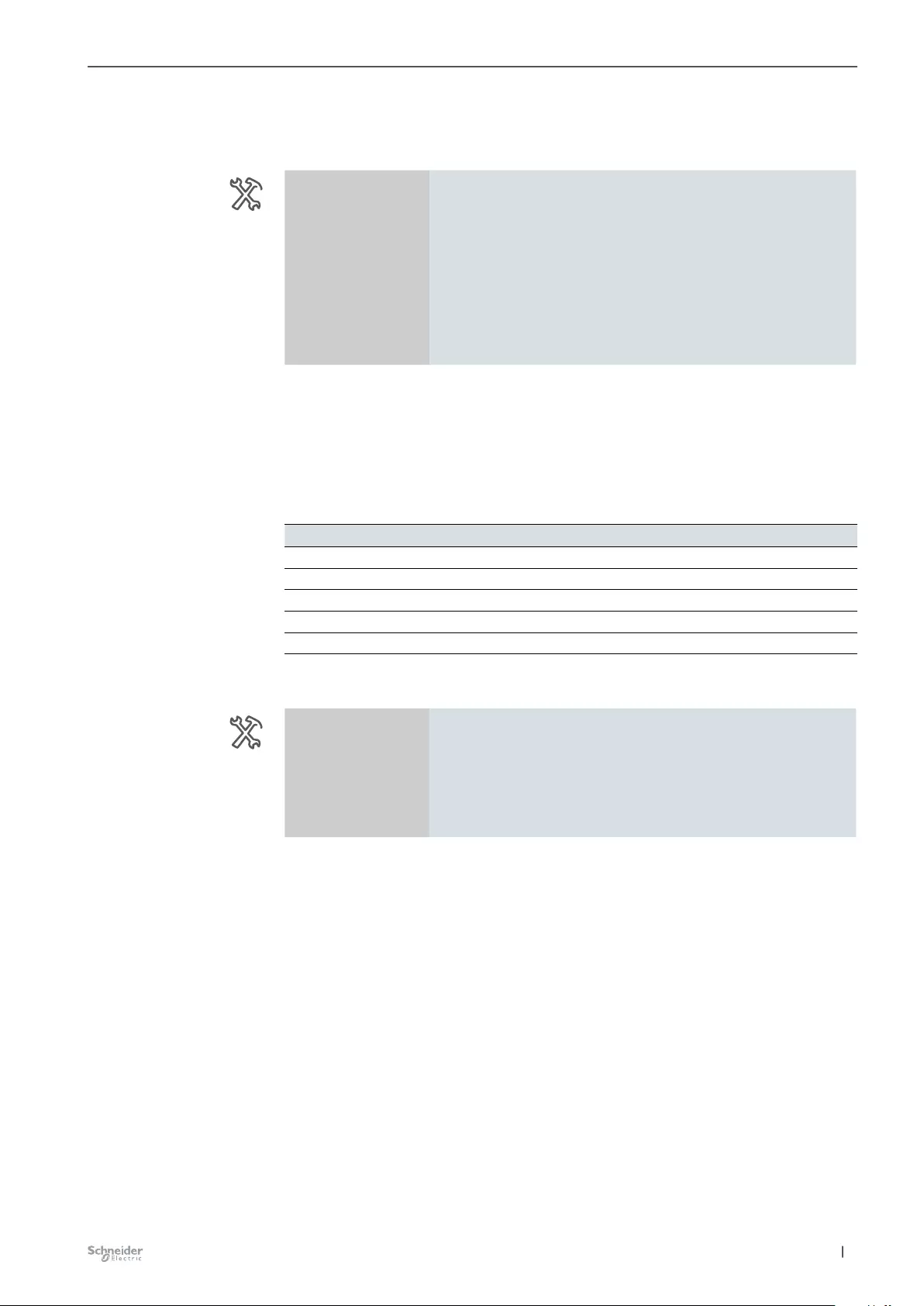
107
05/20-5800/1.0 MTN6705-0008 | MTN6805-0008 |
Extended settings for blind / roller shutter Switch Blind 5800/1.0
Priority of weather alarms
The global priorities for the weather alarms are dened here.
Extended
settings Global settings for roller shutter and blind
Priority of weather alarms Wind alarm->Rain alarm->Frost alarm
Wind alarm->Frost alarm->Rain alarm
Rain alarm->Wind alarm->Frost alarm
Rain alarm->Frost alarm->Wind alarm
Frost alarm->Rain alarm->Wind alarm
Frost alarm->Wind alarm->Rain alarm
This priority setting applies to all blind and roller shutter channels for which the
weather alarm function is enabled. The reactions to a weather alarm only become
active if no weather alarm with a higher priority is already active. If a weather alarm
is reset and another weather alarm with a lower priority is active at that time, the
reactions of the alarm with the lower priority are now executed.
Group objects
No. Name Object function Length Behavior Data Type
18 Central Wind alarm 1 1 bit Received 1.005 Alarm
19 Central Wind alarm 2 1 bit Received 1.005 Alarm
20 Central Wind alarm 3 1 bit Received 1.005 Alarm
21 Central Rain alarm 1 bit Received 1.005 Alarm
22 Central Frost alarm 1 bit Received 1.005 Alarm
The eect of the weather alarm functions can be parameterized here for each
channel. You can enable the weather alarm function individually for each drive.
Master / Ext. 1/2
Output 1+2 / 3+4 / 5+6
/ 7+8
-Blind / roller shutter
Weather alarm function
-Safety and alarm
settings Weather alarm function Disabled
Enabled
With the weather alarms functions, you can protect the blinds or roller shutters
against adverse weather eects such as wind, rain and frost. In the event of an
alarm for one of these 5 possible weather events, the drives move into a safe posi-
tion and stay there for the duration of the event (depending on the priorities of the
other higher-level functions).
Group object for
weather alarms
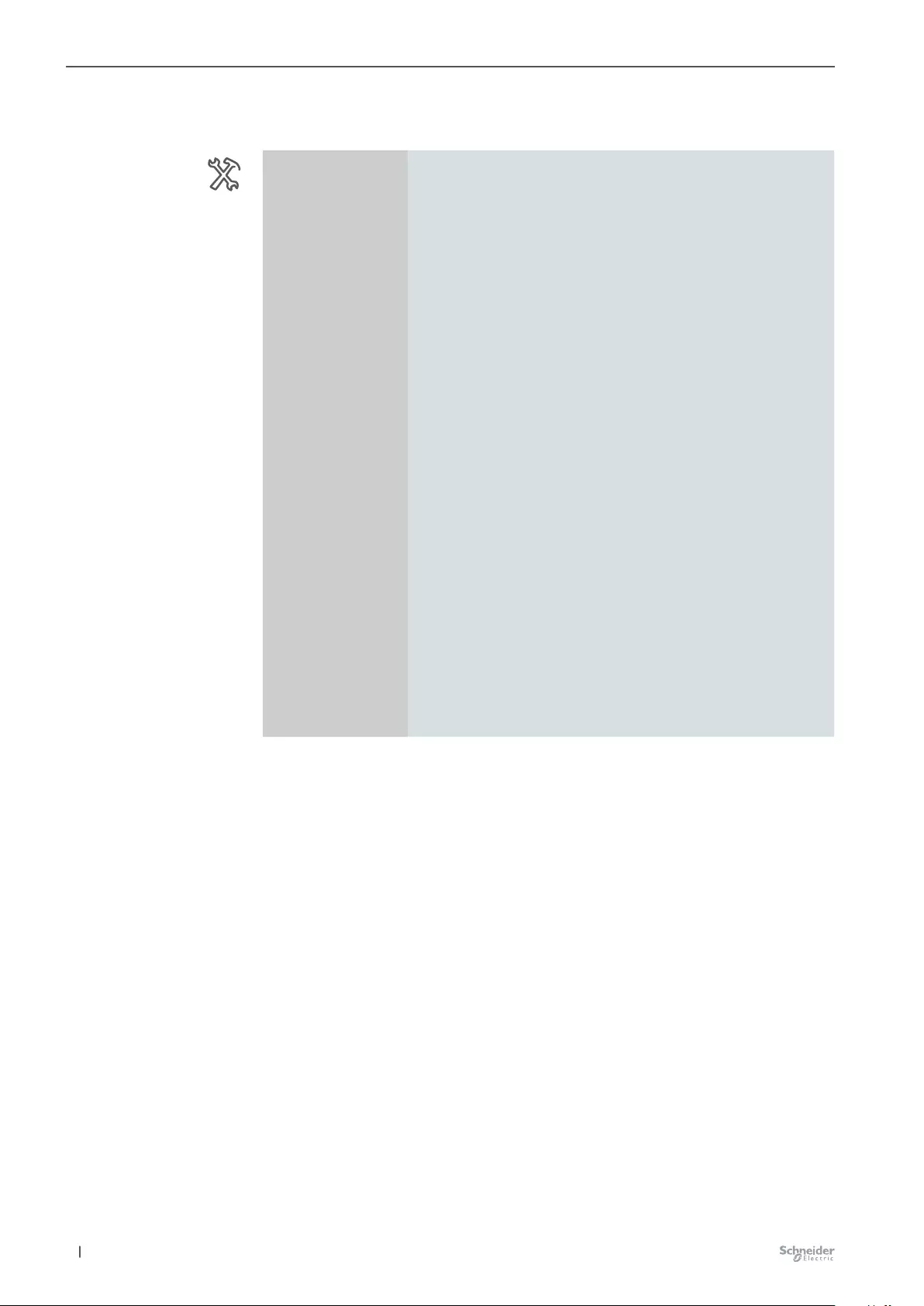
108 05/20-5800/1.0MTN6705-0008 | MTN6805-0008 |
Extended settings for blind / roller shutter Switch Blind 5800/1.0
New parameters appear for the detailed setting of the alarm functions for three
wind alarms, one rain alarm and one frost protection alarm.
Master / Ext.Ext. 1/2
Output 1+2 / 3+4 / 5+6
/ 7+8
-Blind / roller shutter
Weather alarm function
-Safety and alarm
settings Reacts on wind alarm 1 No
Yes
Reacts on wind alarm 2 No
Yes
Reacts on wind alarm 3 No
Yes
Use AND logic for wind
alarms No
Yes
Reaction on wind alarm(s) Up
Down
Move to position
Reaction on rain alarm No reaction
Up
Down
Move to position
Reaction on frost alarm No reaction
Up
Down
Move to position
First select how the drive is to react to an active weather alarm. To protect against
damage in the case of excessive wind speeds, you can individually assign one of
the three wind sensor signals 1, 2 or 3 to each channel. With the respective acti-
vation, the three signals of the wind alarms are logically “OR” linked or linked by
means of the AND parameter.
When a weather alarm becomes active, the drive performs one of the following
reactions according to your settings:
•No reaction: the alarm function is inactive.
The weather alarm function is switched o. In the case of an alarm, the chan-
nel is not disabled.
•Up: the drive moves to the upper end position. The weather alarm function is
switched on and the alarm function is active.
•Down: the drive moves to the lower end position. The weather alarm function is
switched on and the alarm function is active.
•Move to position: the drive moves to the dened safety position. The weather
alarm function is switched on and the alarm function is active.
Once the drive has performed the desired reaction, it remains in this position and
cannot be operated while the weather alarm is active. Only when a function with a
higher priority becomes active will the reaction dened there be executed.
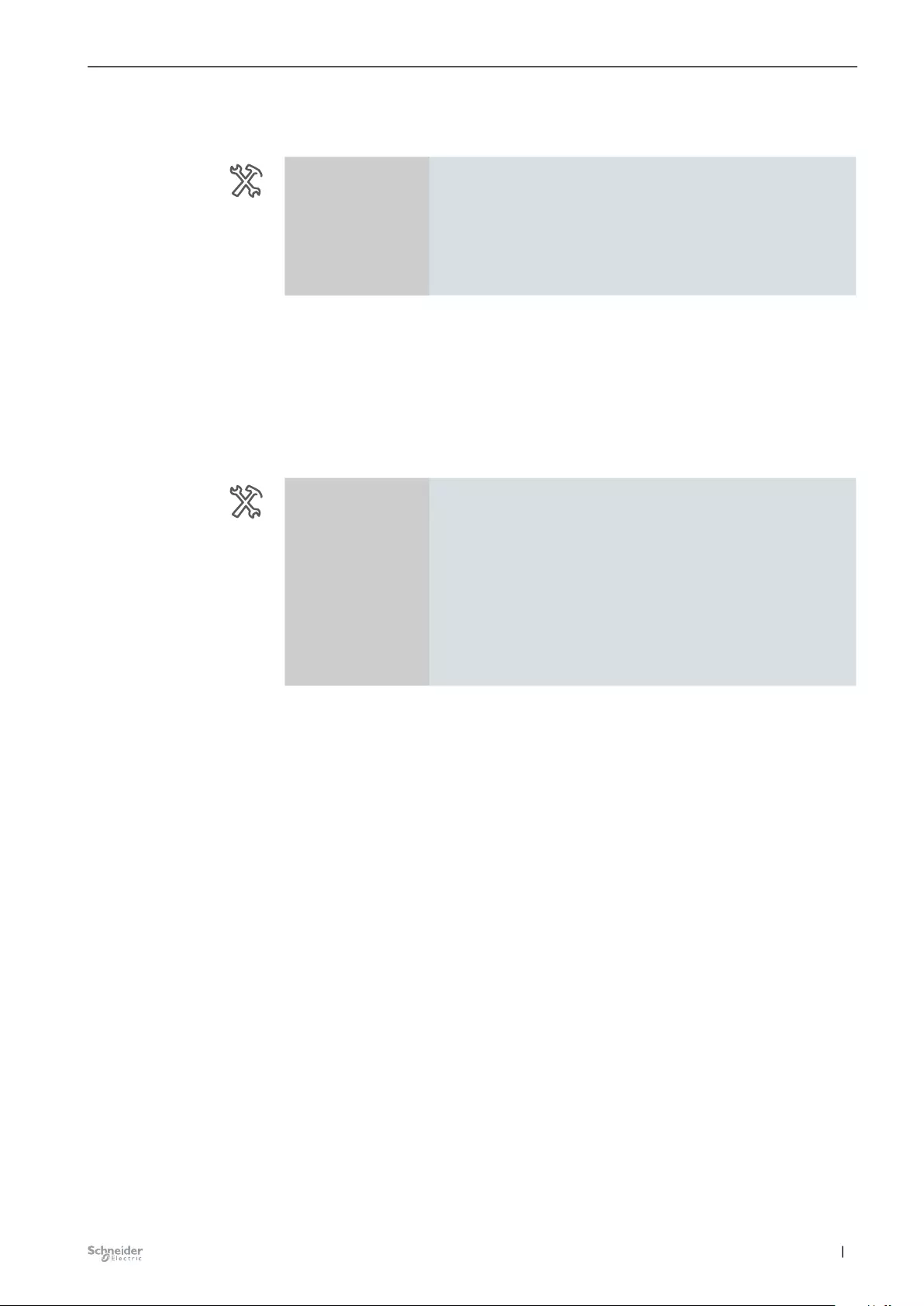
109
05/20-5800/1.0 MTN6705-0008 | MTN6805-0008 |
Extended settings for blind / roller shutter Switch Blind 5800/1.0
If the drive is to move to a specic safety position, you can dene this position
using parameters:
Master / Ext.Ext. 1/2
Output 1+2 / 3+4 / 5+6
/ 7+8
-Blind / roller shutter
Weather alarm function
-Safety and alarm
settings
Height position at weather
alarm in % 0 (0-100)
Slat position at weather alarm
in % 0 (0-100)
This safety position is valid for all three weather alarms if you have selected the
parameter value “Move to position” as the reaction to a weather alarm.
Drive behavior after end of weather alarm
Once the sensor values of the weather sensors have returned to the normal mea-
suring range, the weather alarms are deactivated again. You can dene a reaction
to be performed by the drive as soon as there is no longer any weather alarm
active:
Master / Ext.Ext. 1/2
Output 1+2 / 3+4 / 5+6
/ 7+8
-Blind / roller shutter
Weather alarm function
-Safety and alarm
settings
Behavior at end of all weather
alarms No reaction
Up
Down
Move to position prior weather alarm
Accept current automatic position
The drive then performs the following functions:
•No reaction: the drive remains in its current position. The alarm function is termi-
nated.
•Up: the drive moves to the upper end position. The alarm function is terminated.
•Down: the drive moves to the lower end position. The alarm function is terminat-
ed.
•Move to position prior weather alarm: the drive returns to the position it had
before the weather alarm. The alarm function is terminated.
•Accept current automatic position: this setting is only useful if the automatic
function is active. The drive moves to the last automatic position requested. The
alarm function is terminated.
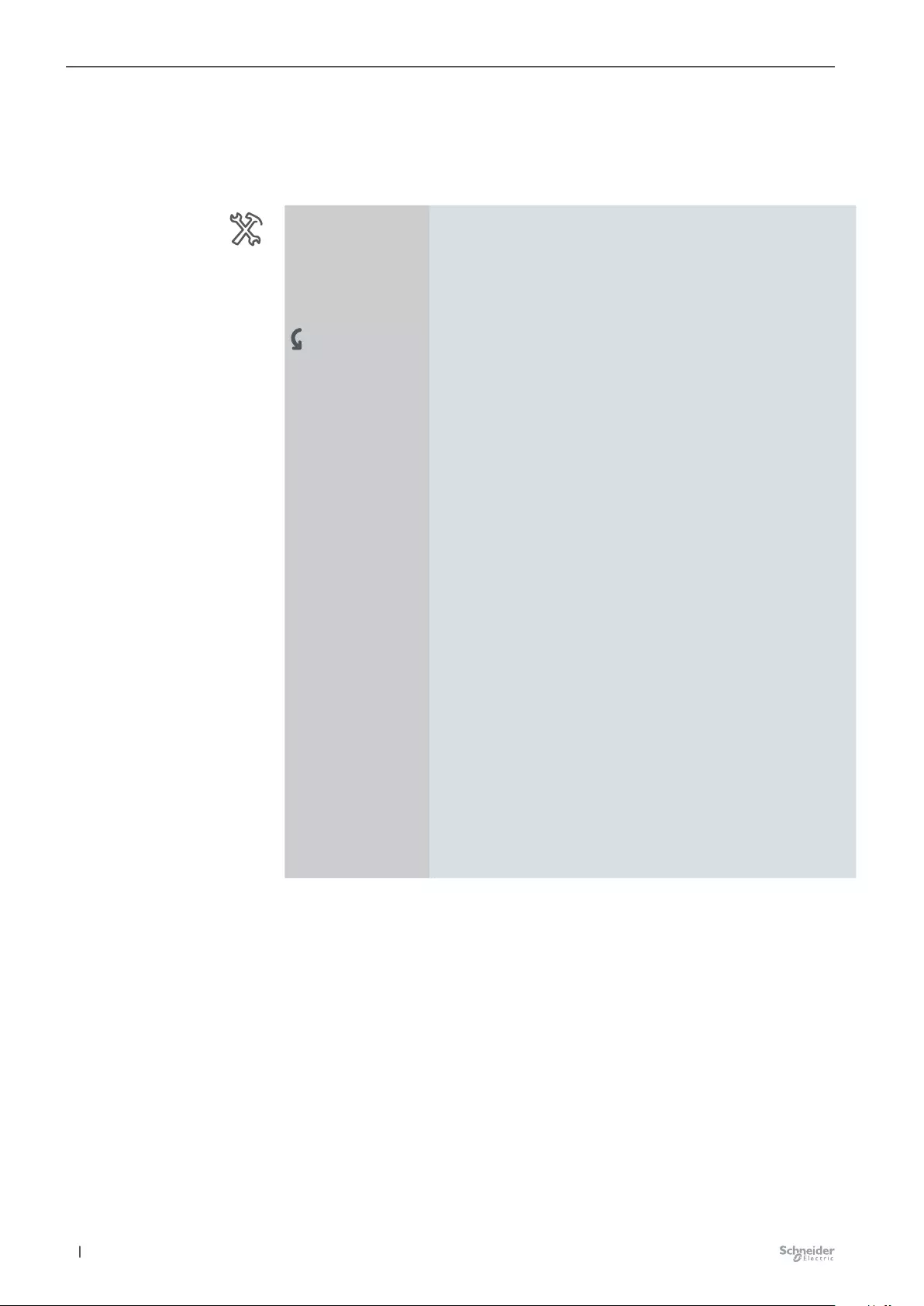
110 05/20-5800/1.0MTN6705-0008 | MTN6805-0008 |
Extended settings for blind / roller shutter Switch Blind 5800/1.0
Failure and download behavior
You can enable this function individually for each drive. The behavior of the drive in
the case of a bus voltage failure / bus voltage recovery and application download is
dened.
Master / Ext. 1/2
Output 1+2 / 3+4 / 5+6
/ 7+8
-Blind / roller shutter
Failure and download behavior
-Safety and alarm
settings
Failure and download be-
havior Disabled
Enabled
Relay state after bus voltage
failure No reaction
Stop
Up
Down
Relay state after bus voltage
recovery Stop
Up
Down
Move to position
As before bus voltage failure
Height position at bus voltage
recovery in % 0 (0-100)
Slat position at bus voltage
recovery in % 0 (0-100)
Relay state at end of down-
load Stop
Up
Down
Move to position
As before download
Height position at end of
download in % 0 (0-100)
Slat position at end of down-
load in % 0 (0-100)
Relay behavior after bus voltage failure
If the bus voltage falls below 18 V, the drive can be switched to a parameterized
state. The drive can either be dened as moving Up or Down or stopped (Stop),
remain in the state it had before the failure (No reaction). At the same time, the
current position of the relay is saved in the device.
Possible settings:
•No reaction: the drive remains in its current state, i.e. it remains stationary or it
continues to execute a current movement until the running times have elapsed.
•Stop: the drive stops immediately.
•Up: the drive moves up. If it was in the process of moving downwards, it stops
and waits for a preset pause on reverse time of 300 ms before starting the up-
ward movement.
•Down: the drive moves down. If it was in the process of moving upwards, it
stops and waits for a preset pause on reverse time of 300 ms before starting the
downward movement.
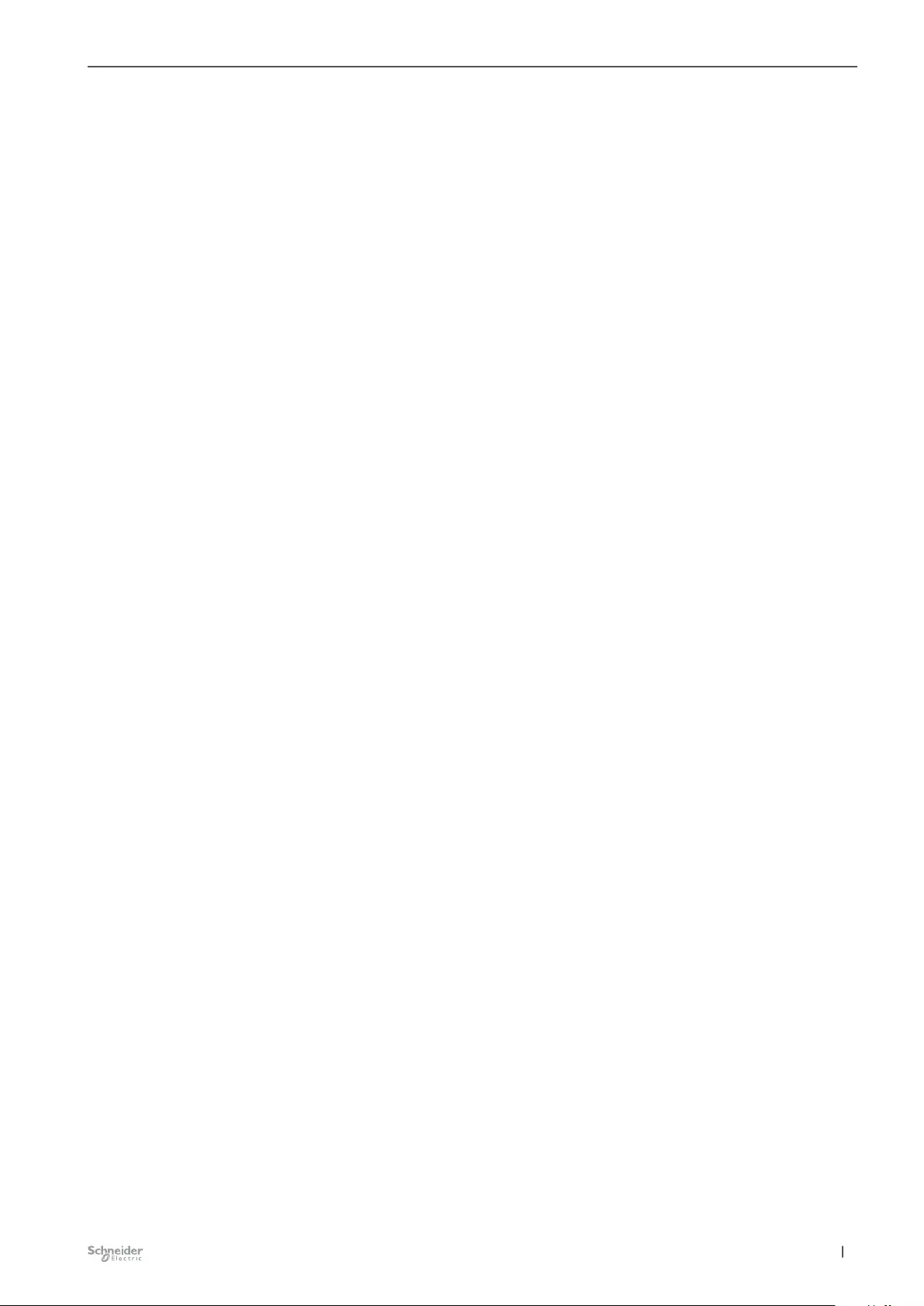
111
05/20-5800/1.0 MTN6705-0008 | MTN6805-0008 |
Extended settings for blind / roller shutter Switch Blind 5800/1.0
Caution!
If your settings may cause a change in direction in the event of a bus voltage failure
(Up or Down settings), be sure to take the pause on reverse into account. This is
preset to 300 ms for a bus voltage failure. The parameterized value for the drive
is not active in this case. If the drive used requires a longer pause on reverse (see
manufacturer specications), then you must not use the settings Up or Down in
order to avoid damage to the drive.
When making settings, note that the higher-level safety functions are not active
during the bus voltage failure. In order to prevent this from resulting in damage, it
is useful to make the settings in such a way that the drives are in a safe position
during a bus voltage failure.
Relay behavior after bus voltage recovery
In the case of bus voltage recovery, the relay can adopt a parameterized state.
Possible settings:
•Stop: the drive stops immediately.
•Up: the drive moves to the upper end position.
•Down: the drive moves to the lower end position.
•Move to position: the drive moves to the dened position for height and slat (for
blind only).
•As before bus voltage failure
With the parameter “As before bus voltage failure”, the relay adopts the state
that was saved in the device at the time of the bus voltage failure. Any subse-
quent manual switchings are overwritten.
Priority:
The reaction to the behavior set here for bus voltage recovery has a low priority. If
a function with a higher priority is activated for the drive directly after bus voltage
recovery, the settings described below apply to these functions.
Relay states caused by higher-priority functions (higher-level function) take prece-
dence over behavior after bus voltage recovery.
Behavior after download
After the ETS download, the channel can adopt a parameterized state.
If an internal defect or a faulty download results in a state in which the application
is not operational, the device will not react. The output relays remain in their last
position.
If you wish to activate the behavior after ETS download for a drive, you must pa-
rameterize a “relay state at end of download” for each channel.
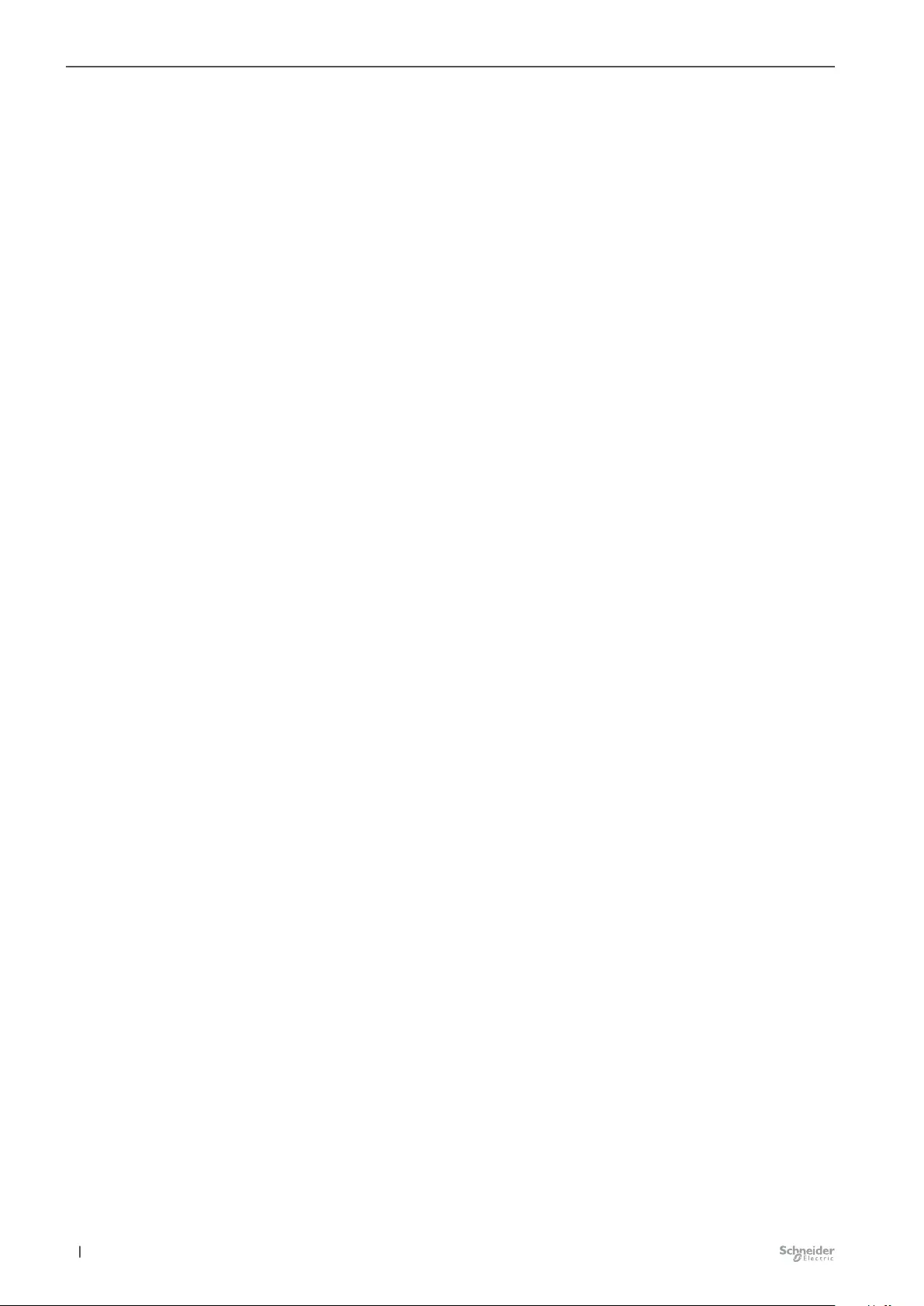
112 05/20-5800/1.0MTN6705-0008 | MTN6805-0008 |
Extended settings for blind / roller shutter Switch Blind 5800/1.0
Possible settings:
•Stop: the drive stops immediately.
•Up: the drive moves to the upper end position.
•Down: the drive moves to the lower end position.
•Move to position: the drive moves to the dened position for height and slat (for
blind only).
•As before download: the drive remains in its current state after a download.
Priority
Relay states caused by higher-priority functions take precedence over behavior
after ETS download.
Example: OR logic operation with parameterized value of the logic object after bus
voltage recovery = 1, prevails and switches the output.
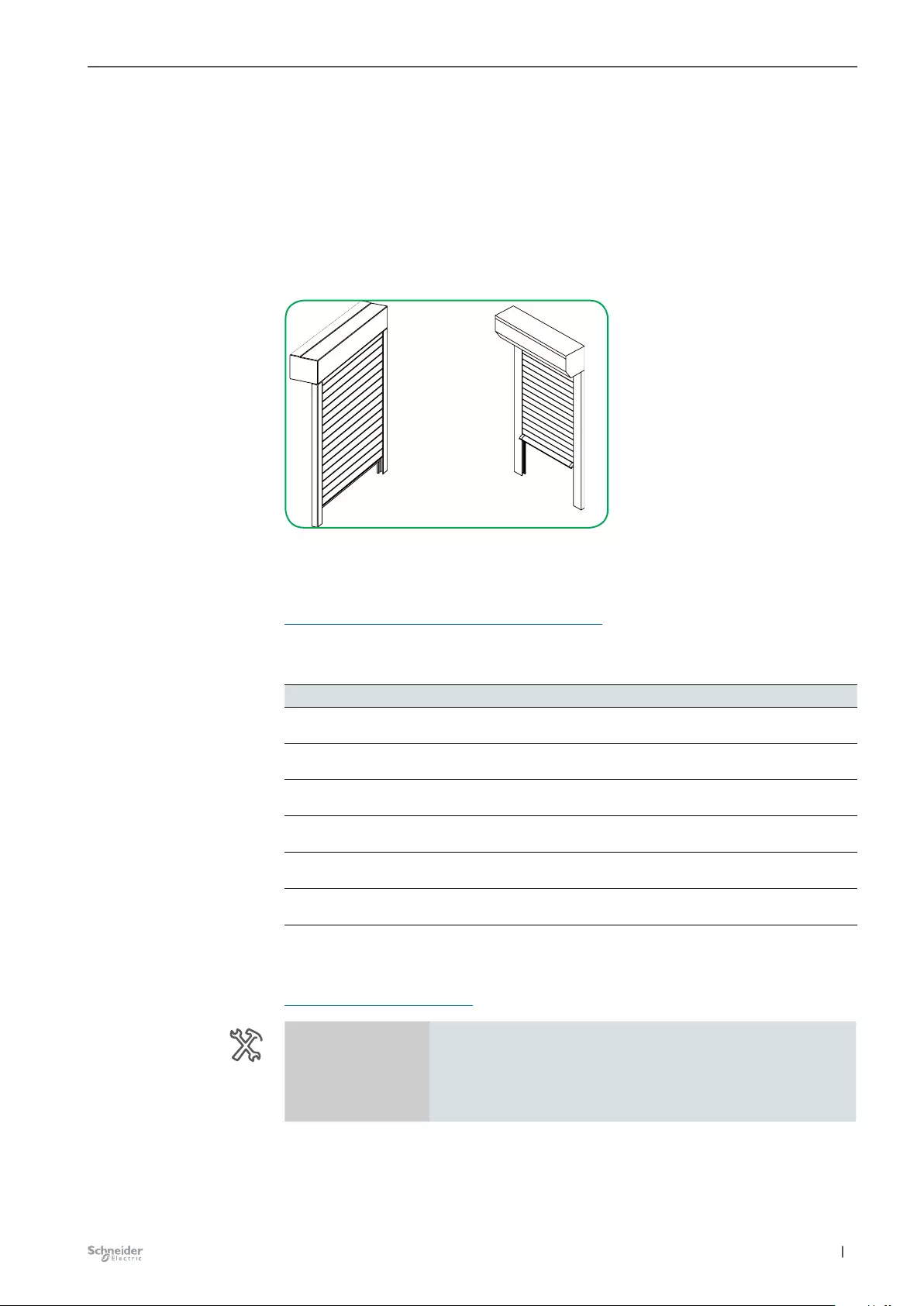
113
05/20-5800/1.0 MTN6705-0008 | MTN6805-0008 |
Express settings for roller shutter Switch Blind 5800/1.0
9 Express settings for roller
shutter
Roller shutters protect residents, furnishings and plants against too much sun and
UV radiation. The roller shutter prevents the excessive heating of rooms from expo-
sure to sunlight. The protection oered by roller shutters against external noise is
also not to be underestimated. In the cold season, the layer of air between window
and shutter has an insulating eect. This can additionally save heating costs.
Roller shutters behave in a similar manner to blinds. They lack the slat control func-
tions. For this reason, we refer to the description of the individual functions in the
chapter “Blind / roller shutter”.
Express settings for blind / roller shutter --> 67
Group objects
No. Name Object function Length Behavior Data Type
31 Master Output 1+2
name of the channel
Movement in manual
mode
1 bit Received 1.008 Up/DOWN
32 Master Output 1+2
name of the channel
Stop in manual mode
(roller shutter)
1 bit Received 1.007 Step
33 Master Output 1+2
name of the channel
Height position in
manual mode
1 byte Received 5.001 Percent
(0...100%)
46 Master Output 1+2
name of the channel
Feedback for height 1 byte Sending 5.001 Percent
(0...100%)
51 Master Output 1+2
name of the channel
Feedback for moving 1 bit Sending 1.010 Start/Stop
52 Master Output 1+2
name of the channel
Feedback for last
direction
1 bit Sending 1.008 Up/DOWN
9.1 Name of the channel
Name of the channel --> 70
Master / Ext. 1/2
Output 1+2 / 3+4 / 5+6
/ 7+8
-Roller shutter
Express settings for roller shutter
Name of the channel Roller shutter Kitchen
Group objects for express set-
ting for roller shutter
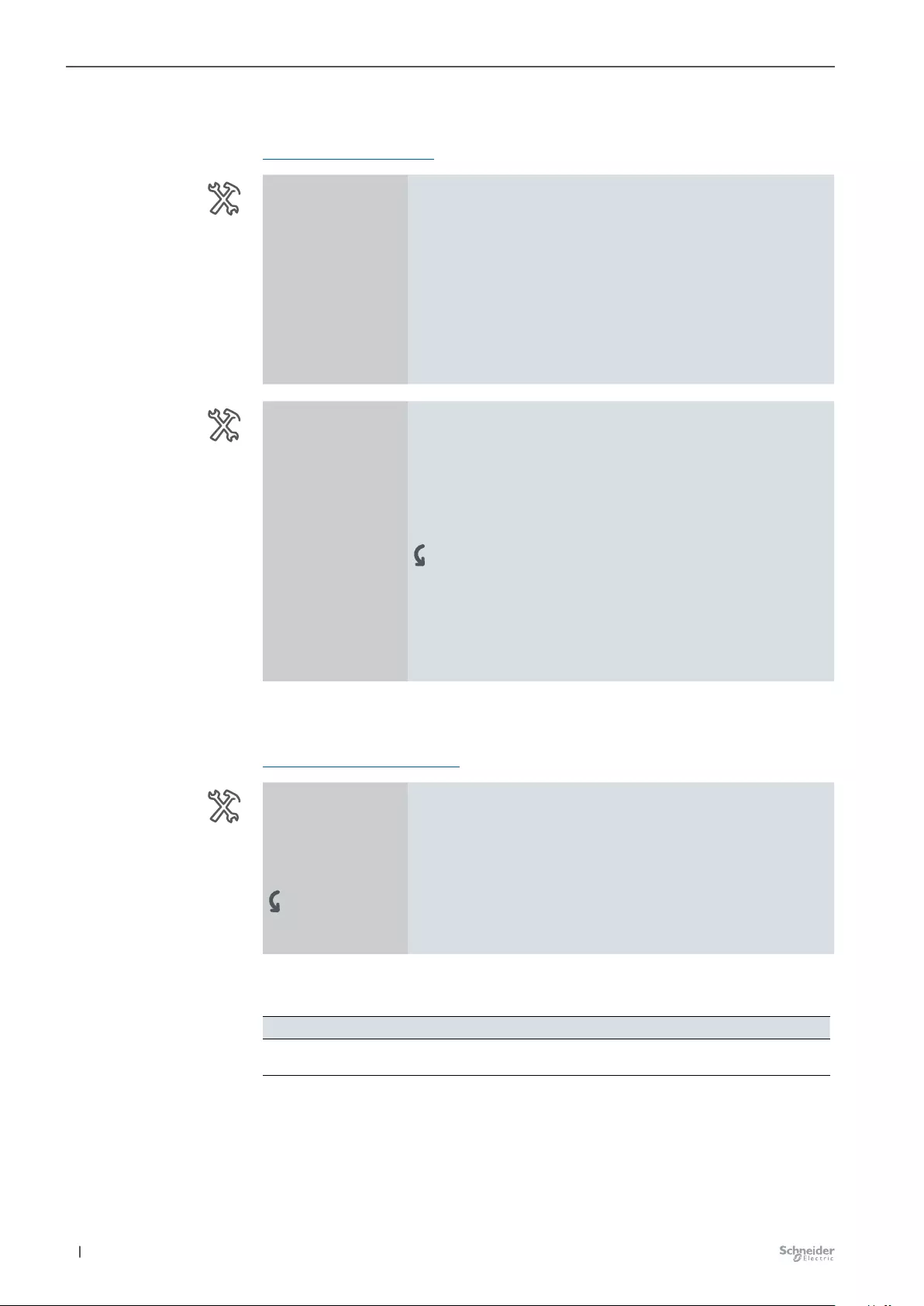
114 05/20-5800/1.0MTN6705-0008 | MTN6805-0008 |
Express settings for roller shutter Switch Blind 5800/1.0
9.2 Roller shutter control drive time
Drive running time --> 70
Master / Ext. 1/2
Output 1+2 / 3+4 / 5+6
/ 7+8
-Roller shutter
Express settings for roller shutter
Roller shutter control
Use same time for up and
down Yes
Running time: Up/Down
(5s...99:59.9 min) 02:00.0
Pause time before reverting
(2...255, unit = 100 ms) 5
Master / Ext. 1/2
Output 1+2 / 3+4 / 5+6
/ 7+8
-Roller shutter
Express settings for roller shutter
Roller shutter control
Use same time for up and
down No
Running time: Up
(5s...99:59.9 min) 02:00.0
Running time: Down
(5s...99:59.9 min) 02:00.0
Pause time before reverting
(2...255, unit = 100 ms) 5
9.3 Locking manual mode
Locking manual mode --> 79
Master / Ext. 1/2
Output 1+2 / 3+4 / 5+6
/ 7+8
-Roller shutter
Express settings for roller shutter
Locking manual mode Disabled
Enabled
Manual locking At object value "1"
At object value "0"
Group objects
No. Name Object function Length Behavior Data Type
35 Master Output 1+2
name of the channel
Locking manual
mode
1 bit Received 1.003 Enable
Group objects for lock of manual
mode
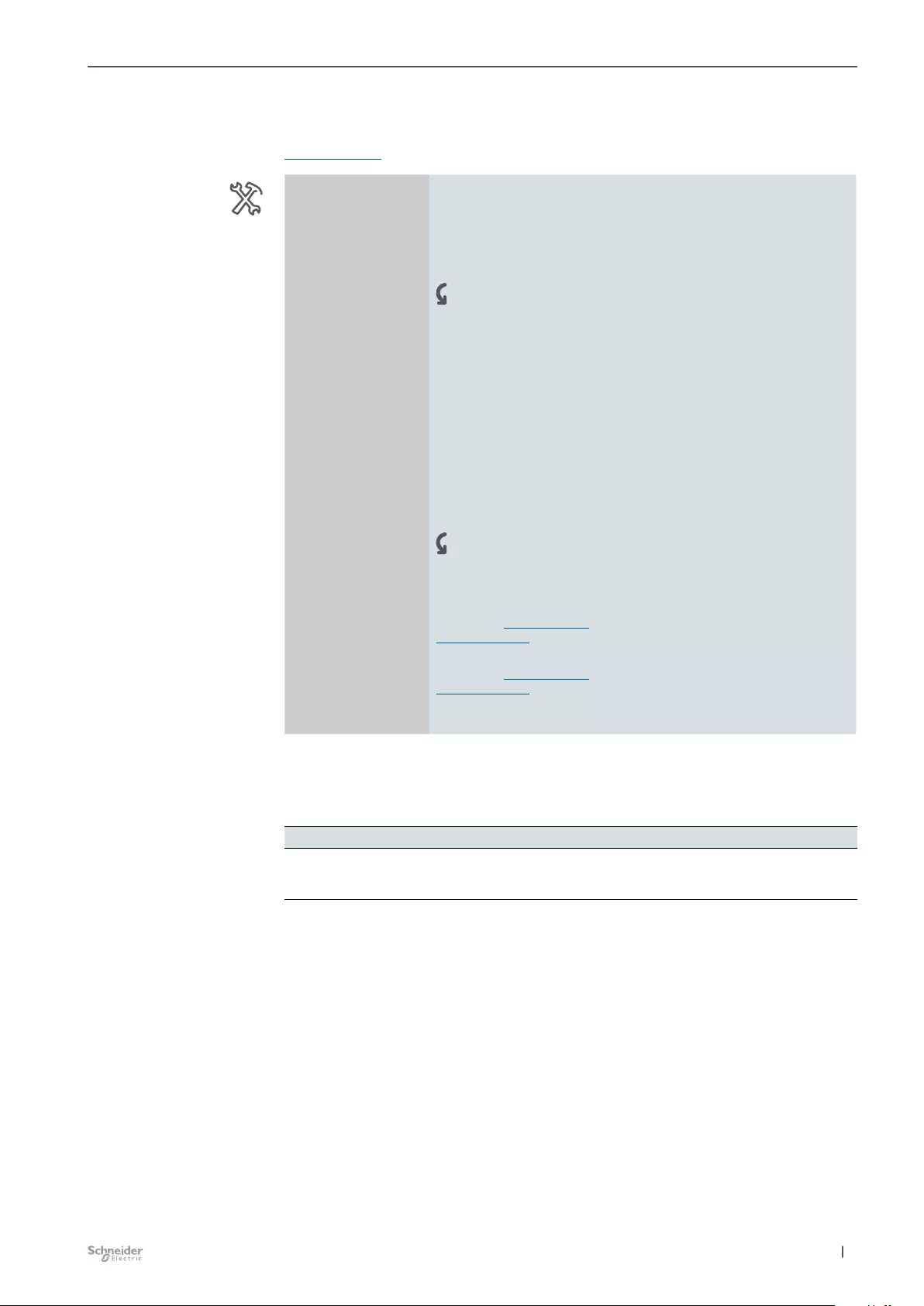
115
05/20-5800/1.0 MTN6705-0008 | MTN6805-0008 |
Express settings for roller shutter Switch Blind 5800/1.0
9.4 Scenes
Scenes --> 80
Master / Ext. 1/2
Output 1+2 / 3+4 / 5+6
/ 7+8
-Roller shutter
Express settings for roller shutter
Scenes Disabled
Enabled
-Scenes settings Scene settings
Required number of scenes 1 (1-16)
Overwrite scene values of
actuator during download Disabled
Enabled
Time delay for scene process-
ing (0...255, unit = 100 ms) 0
Scene 1 (1-16) Disabled
Enabled
Scene 1 Description
Scene 1 Address (0-63)
Dependent: Global settings
for scenes --> 24
Scene address 0 - 63
Scene 1 Address (1-64)
Dependent: Global settings
for scenes --> 24
Scene address 1 - 64
Scene 1 height in % 0 (0-100)
Following enabling of the scenes, the group object appears.
Group objects
No. Name Object function Length Behavior Data Type
43 Master Output
1+2 name of
the channel
Scene 1 byte Received 18.001 Scene
control
Group object for
scene
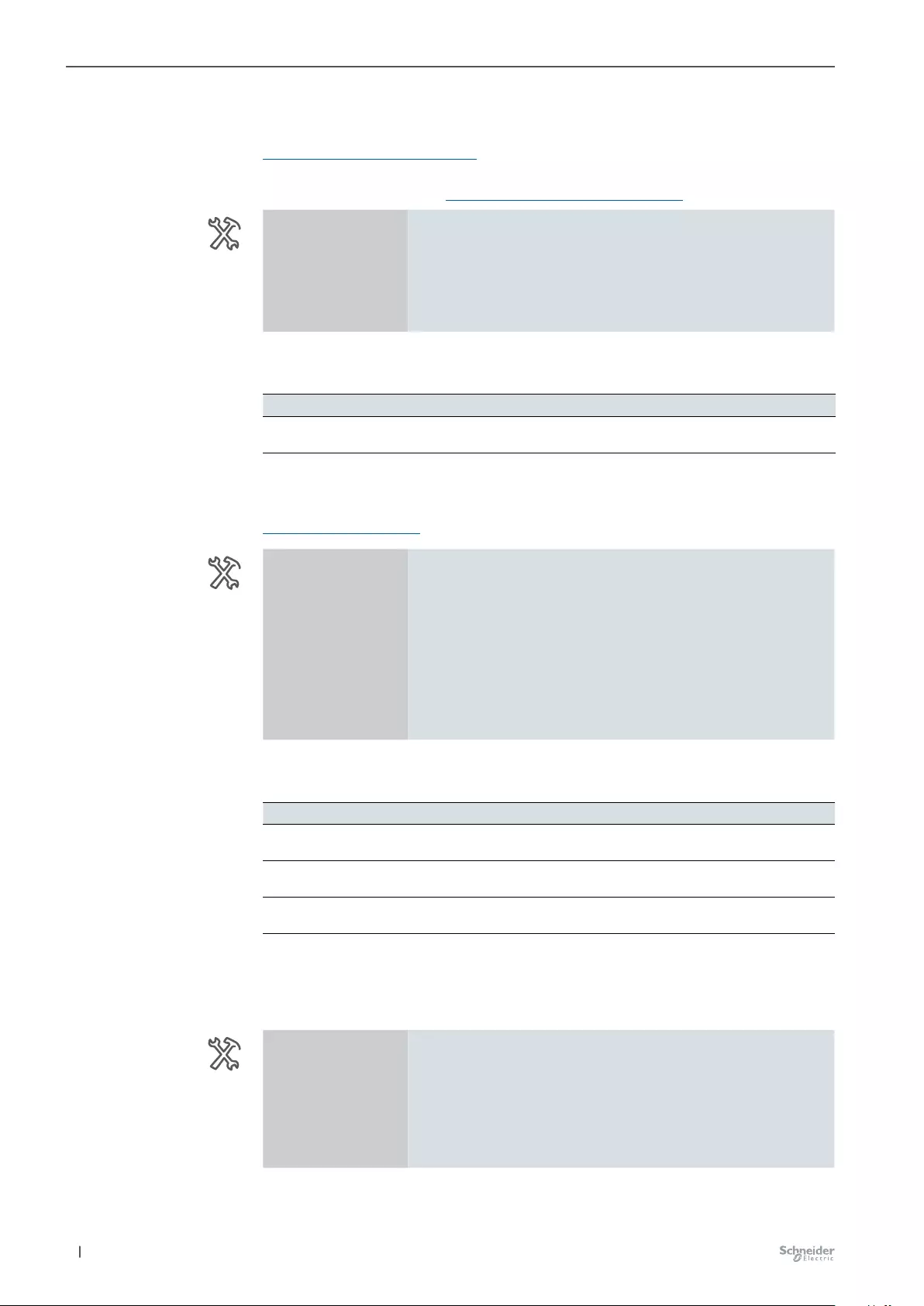
116 05/20-5800/1.0MTN6705-0008 | MTN6805-0008 |
Express settings for roller shutter Switch Blind 5800/1.0
9.5 Central function for roller shutter
Central function for blind --> 83
The global settings and explanations of the central function can be found in the
chapter General settings. (Enabling central functions --> 19)=
Master / Ext. 1/2
Output 1+2 / 3+4 / 5+6
/ 7+8
-Roller shutter
Express settings for roller shutter
Central function Enabled
Disabled
Group objects
No. Name Object function Length Behavior Data Type
2 Central Move up/down roller
shutter
1 bit Received 1.008 Up/Down
9.6 Status response
Status response --> 84
Master / Ext. 1/2
Output 1+2 / 3+4 / 5+6
/ 7+8
-Blind
Express settings for roller shutter
Status of height Enabled
Disabled
Status of moving Enabled
Disabled
Group objects
No. Name Object function Length Behavior Data Type
46 Master Output 1+2
name of the channel
Feedback for height 1 byte Sending 5.001 Percent
(0...100%)
51 Master Output 1+2
name of the channel
Feedback for moving 1 bit Sending 1.010 Start/Stop
52 Master Output 1+2
name of the channel
Feedback for last
direction
1 bit Sending 1.008 Up/DOWN
9.7 Activating extended settings for roller
shutter
Master / Ext. 1/2
Output 1+2 / 3+4 / 5+6
/ 7+8
-Roller shutter
Express settings for roller shutter
Extended settings for roller
shutter No
Yes
To activate the extended settings for roller shutter, you must enable them here.
Group objects of the central
function
Group objects of status re-
sponse of roller shutter
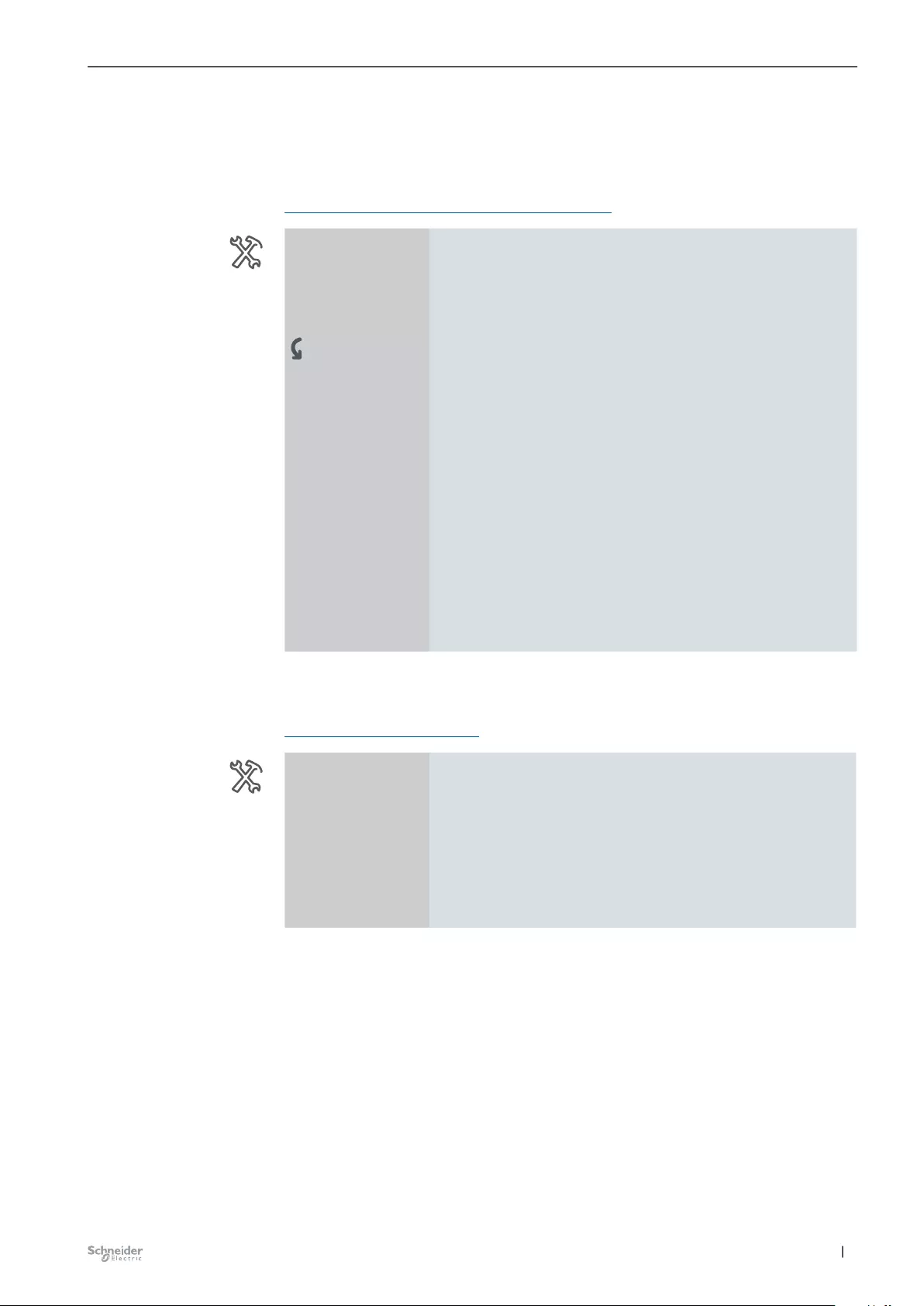
117
05/20-5800/1.0 MTN6705-0008 | MTN6805-0008 |
Extended settings for roller shutter Switch Blind 5800/1.0
10 Extended settings for roller
shutter
Extended settings for blind / roller shutter --> 86
Master / Ext. 1/2
Output 1+2 / 3+4 / 5+6
/ 7+8
-Blind / roller shutter
Express settings for blind / roller shutter
Extended settings for blind /
roller shutter No
Yes
-Extended drive timing Idle time until upward movement
Startup delay
Additional startup time
-Automatic, Locking &
Calibration settings Priority function
Logic function
-Safety and alarm
settings Safety function
Alarm function
Failure and download behavior
10.1 Extended drive timing
Extended drive timing --> 86
Master / Ext. 1/2
Output 1+2 / 3+4 / 5+6
/ 7+8
-Blind / roller shutter
Extended drive timing
-Extended drive timing Idle time until upward move-
ment (0...255, unit = 10 ms) 0
Startup delay (0...255, unit =
10 ms) 0
Deceleration delay (0...255,
unit = 10 ms) 0
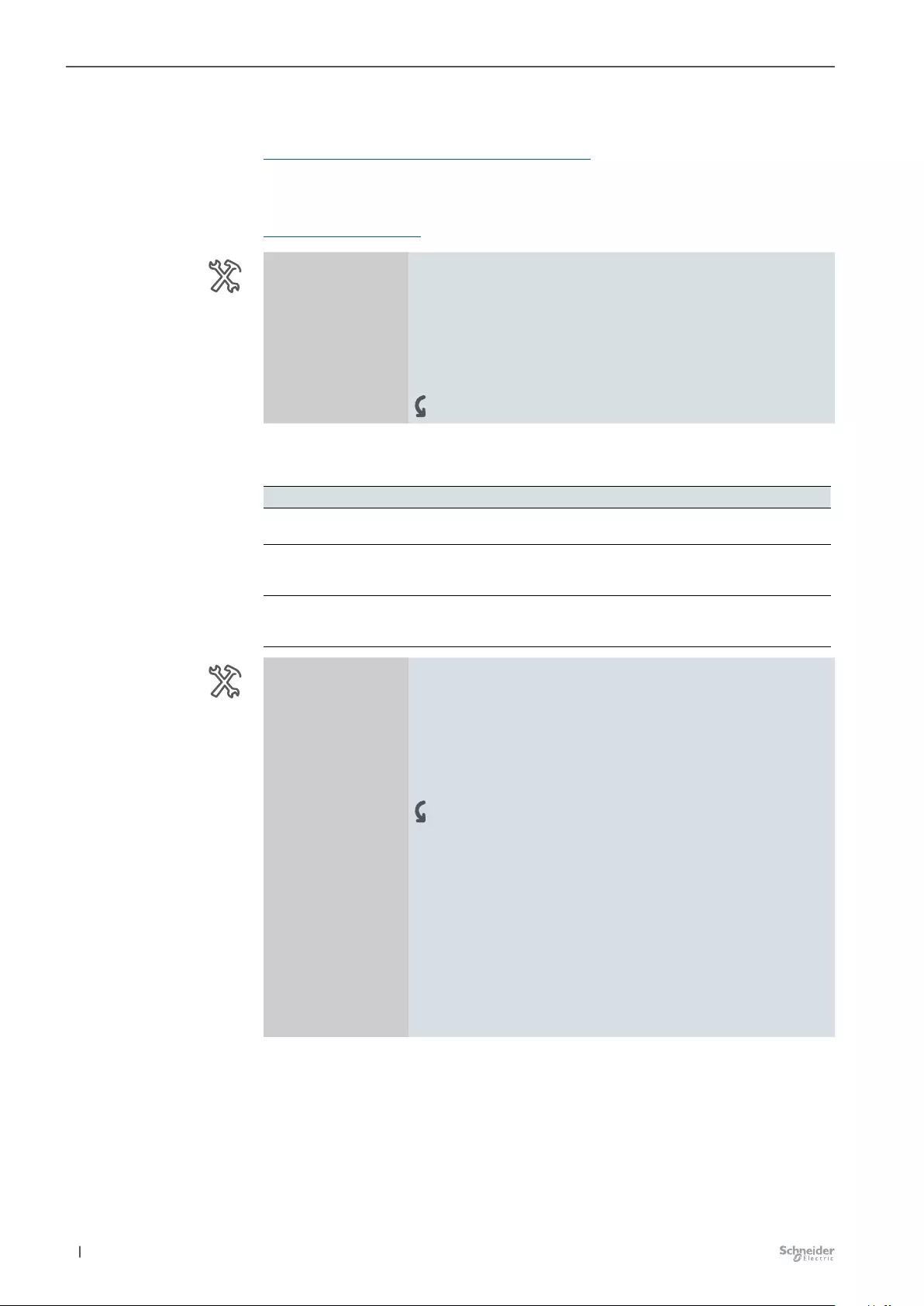
118 05/20-5800/1.0MTN6705-0008 | MTN6805-0008 |
Extended settings for roller shutter Switch Blind 5800/1.0
10.2 Automatic, Locking & Calibration settings
Automatic, Locking & Calibration settings --> 88
Automatic mode
Automatic mode --> 88
Master / Ext. 1/2
Output 1+2 / 3+4 / 5+6
/ 7+8
-Blind / roller shutter
Automatic, Locking & Calibration settings
-Automatic, Locking &
Calibration settings Automatic mode
Automatic mode Disabled
Enabled
Group objects
No. Name Object function Length Behavior Data Type
36 Master Output 1+2
name of the channel
Movement in au-
tomatic mode
1 bit Received 1.008 Up/DOWN
37 Master Output 1+2
name of the channel
Stop in automat-
ic mode (roller
shutter)
1 bit Received 1.007 Step
38 Master Output 1+2
name of the channel
Height position
in automatic
mode
1 byte Received 5.001 Percent
(0...100%)
Master / Ext. 1/2
Output 1+2 / 3+4 / 5+6
/ 7+8
-Blind / roller shutter
Automatic, Locking & Calibration settings
-Automatic, Locking &
Calibration settings Automatic mode
Lock of automatic mode Disabled
Enabled
Automatic locking At object value "1"
At object value "0"
Status of automatic locking Disabled
Enabled
Behavior on deactivating
automatic locking via object No reaction
Accept current automatic position
Group objects of automatic
mode "Roller shutter"
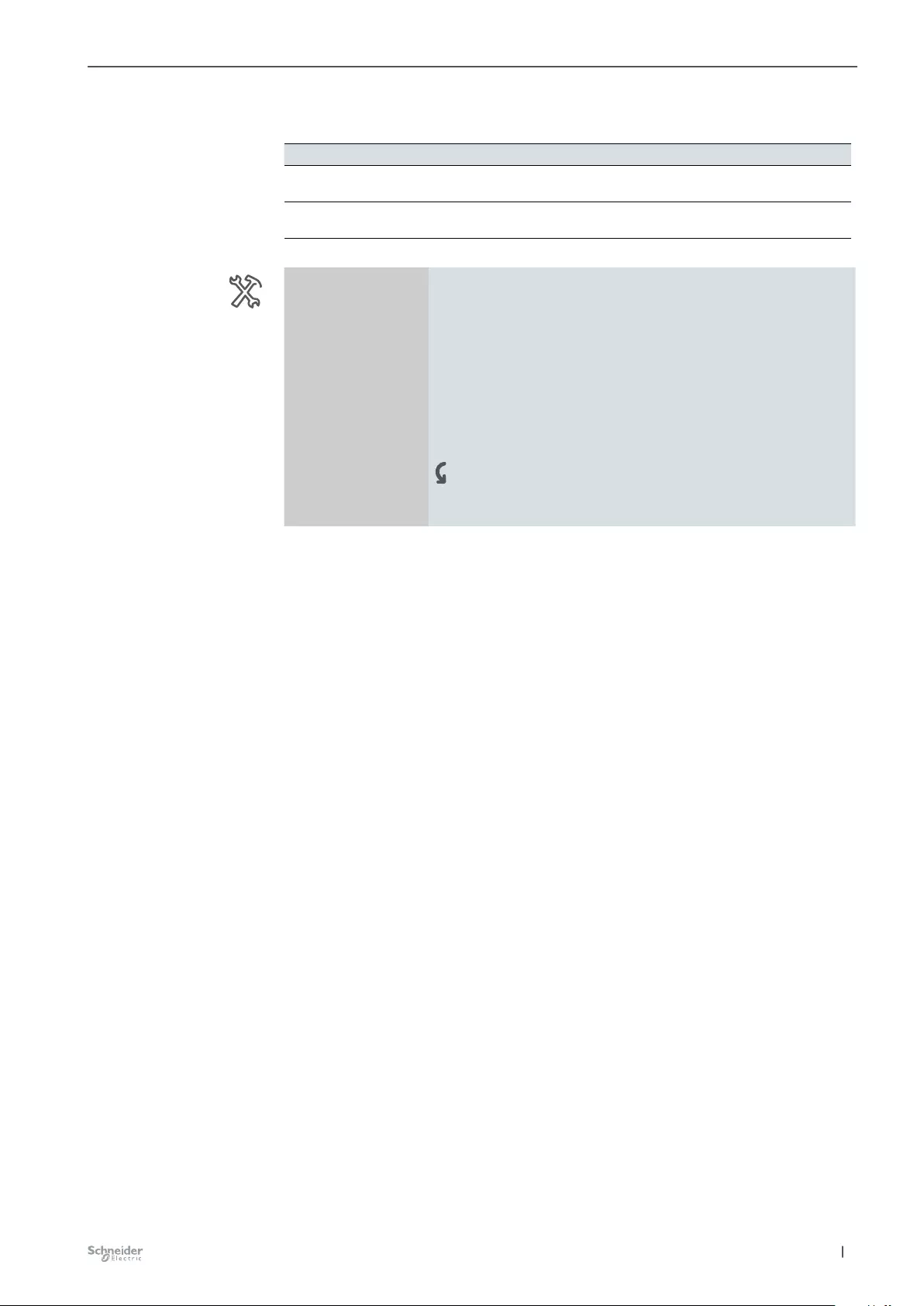
119
05/20-5800/1.0 MTN6705-0008 | MTN6805-0008 |
Extended settings for roller shutter Switch Blind 5800/1.0
Group objects
No. Name Object function Length Behavior Data Type
40 Master Output 1+2
name of the channel
Lock of automat-
ic mode
1 bit Received 1.003 Enable
48 Master Output 1+2
name of the channel
Feedback for
automatic mode
1 bit Sending 1.003 Enable
Master / Ext. 1/2
Output 1+2 / 3+4 / 5+6
/ 7+8
-Blind / roller shutter
Automatic, Locking & Calibration settings
-Automatic, Locking &
Calibration settings Automatic mode
Reaction in automatic mode
on receipt of a manual object
value
Automatic mode remains enabled
Automatic mode disabled
Automatic mode temporarily disabled
Deactivation time for automat-
ic mode 1 min (1 min - 24 h)
Group objects of automatic
mode "Lock"
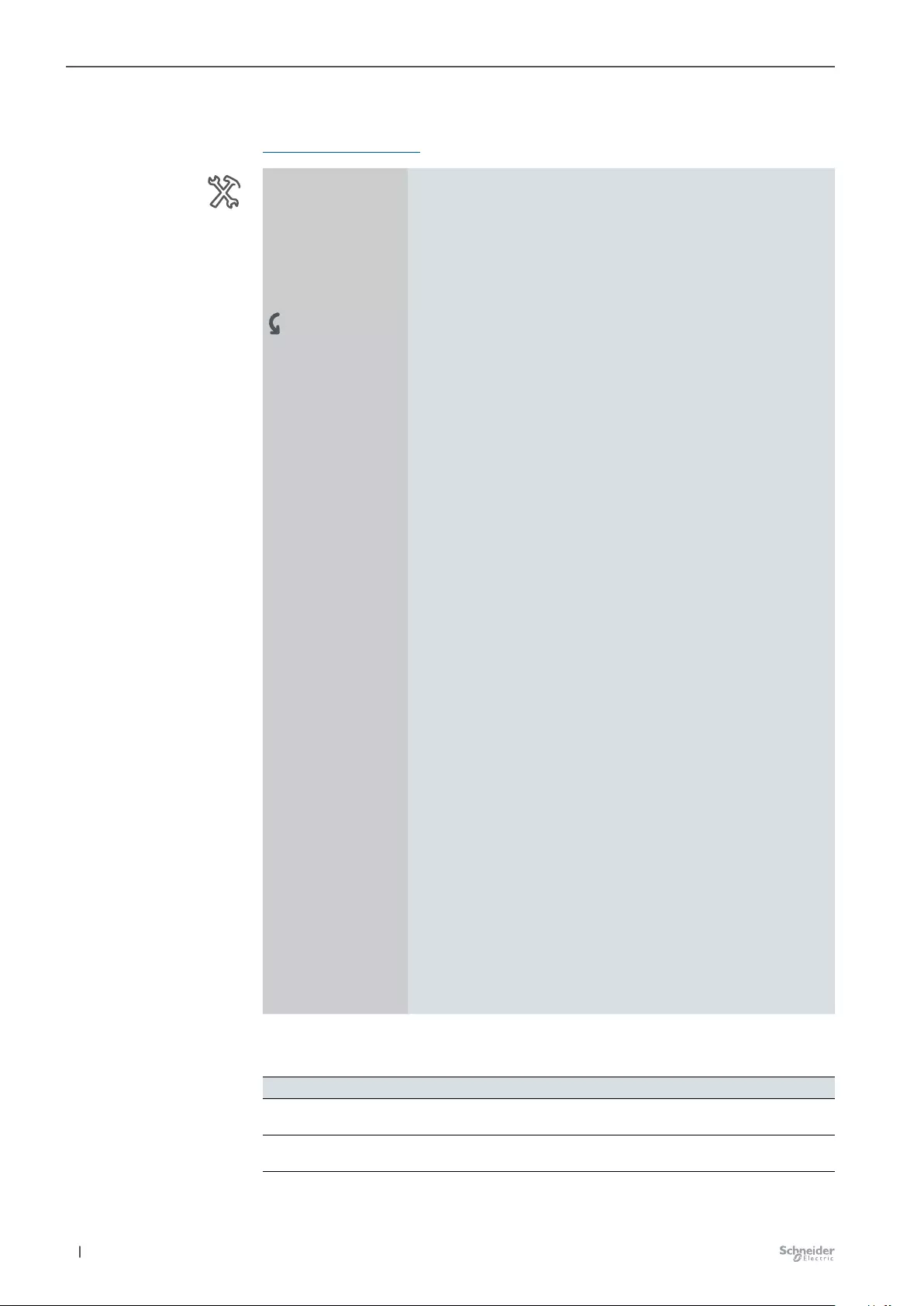
120 05/20-5800/1.0MTN6705-0008 | MTN6805-0008 |
Extended settings for roller shutter Switch Blind 5800/1.0
Locking function
Locking function --> 91
Master / Ext. 1/2
Output 1+2 / 3+4 / 5+6
/ 7+8
-Blind / roller shutter
Locking function
-Automatic, Locking &
Calibration settings Locking function Disabled
Enabled
Locking At object value "1"
At object value "0"
Status of locking signal Disabled
Enabled
Behavior at start of locking No reaction
Up
Down
Move to position
Height position at start of locking
in % 0 (0-100)
Behavior at end of locking No reaction
Up
Down
Move to position prior locking
Accept current automatic position
Behavior after download Disabled
Enabled
As before download
Behavior after bus voltage
recovery Disabled
Enabled
As before bus voltage failure
Group objects
No. Name Object function Length Behavior Data Type
41 Master Output 1+2
name of the channel
Locking 1 bit Received 1.003 Enable
49 Master Output 1+2
name of the channel
Feedback for
drive locking
1 bit Sending 1.003 Enable
Group objects of locking func-
tion
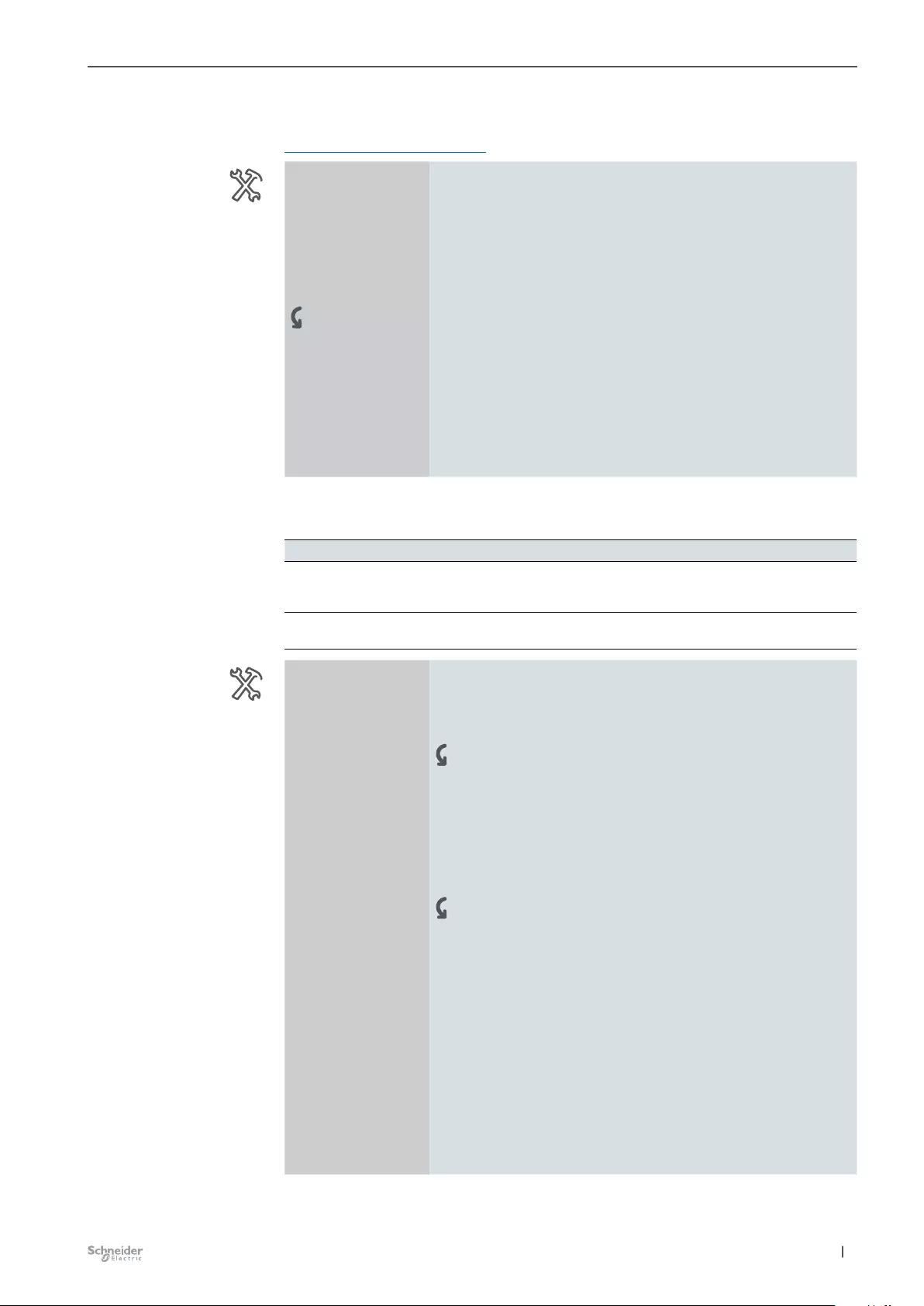
121
05/20-5800/1.0 MTN6705-0008 | MTN6805-0008 |
Extended settings for roller shutter Switch Blind 5800/1.0
Movement range limits
Movement range limits --> 94
Master / Ext. 1/2
Output 1+2 / 3+4 / 5+6
/ 7+8
-Blind / roller shutter
Movement range limits
-Automatic, Locking &
Calibration settings Movement range limits Disabled
Enabled
Limit movement range Immediately after bus voltage
recovery
At object value "1"
At object value "0"
Feedback for range limitation Disabled
Enabled
Group objects
No. Name Object function Length Behavior Data Type
44 Master Output 1+2
name of the channel
Activate move-
ment range
limits
1 bit Received 1.003 Enable
50 Master Output 1+2
name of the channel
Feedback for
range limitation
1 bit Sending 1.003 Enable
Master / Ext. 1/2
Output 1+2 / 3+4 / 5+6
/ 7+8
-Blind / roller shutter
Movement range limits
-Automatic, Locking &
Calibration settings
Limit movement position Limit range at lower position
Upper limit value in % (x) 0
Lower limit value in % 100 (0-100)
Limit movement position
Limit range at upper position
Upper limit value in % 100 (0-100)
Lower limit in % (x) 0
Behavior at the end of movement
restriction No reaction
Up
Down
Move to position prior to movement
restriction
Accept current automatic position
Group objects of the function
"Movement range limits"
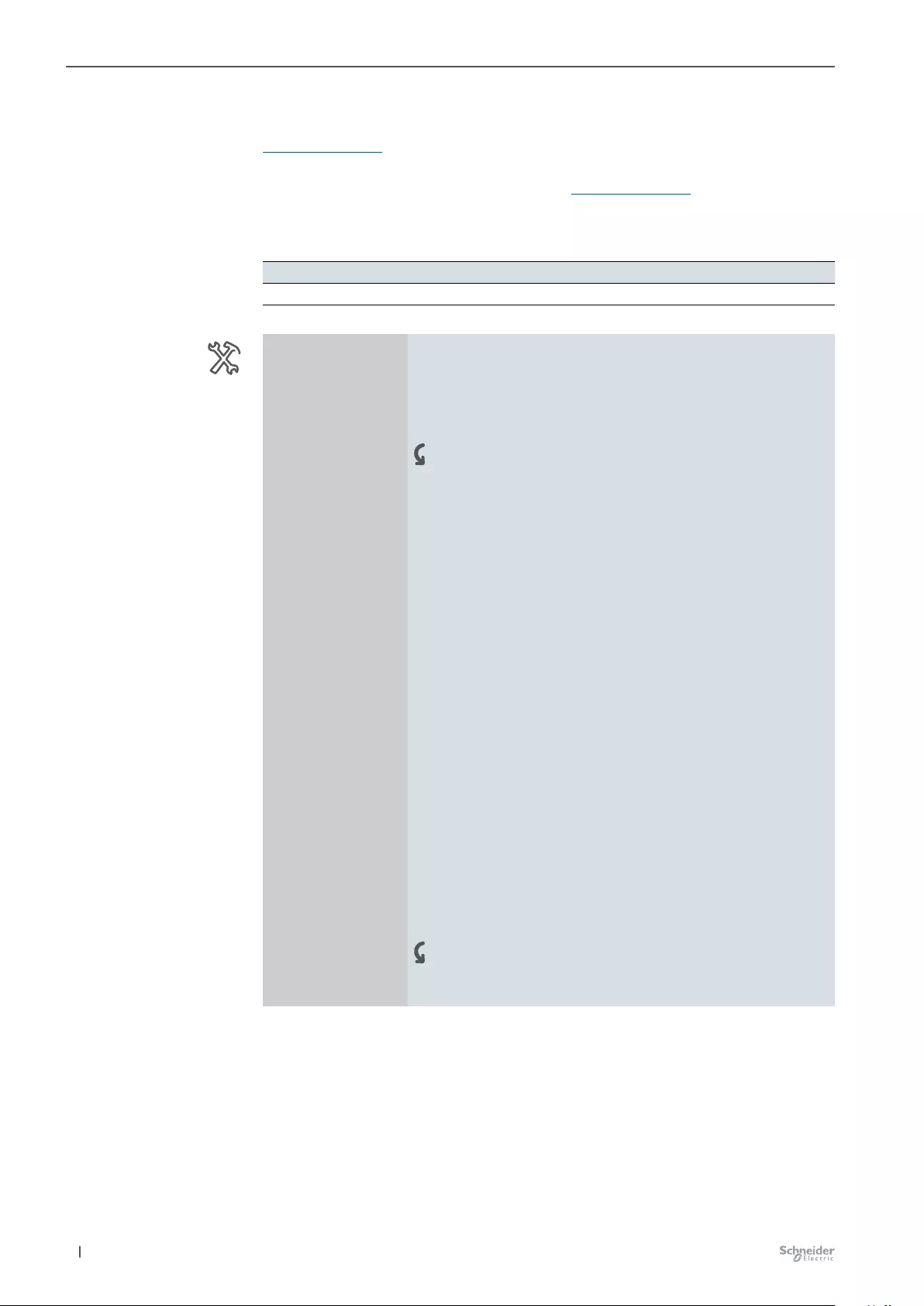
122 05/20-5800/1.0MTN6705-0008 | MTN6805-0008 |
Extended settings for roller shutter Switch Blind 5800/1.0
Calibration
Calibration --> 98
The calibrating function is activated centrally on the Global settings for roller shutter
and blind tab with the parameter Calibration. Calibration --> 30
Group objects
No. Name Object function Length Behavior Data Type
17 Central Calibration 1 bit Received 1.010 Start/Stop
Master / Ext. 1/2
Output 1+2 / 3+4 / 5+6
/ 7+8
-Blind / roller shutter
Calibration
-Automatic, Locking &
Calibration settings Calibration Disabled
Enabled
Trigger of calibration Number of movements
Value "1" on calibration object
No. of movements or calibration object
Delay of calibration via object
(0...255, unit = 1 s) 0
Number of movements until
calibration 7 (1-20)
Reference position upper
lower
upper and lower
Automatic calibration upper
lower
upper and lower
Position after calibration via
object Position prior reference movement
remain in reference position
new position
Height position after calibration
in % 0 (0-100)
Group object for
calibration
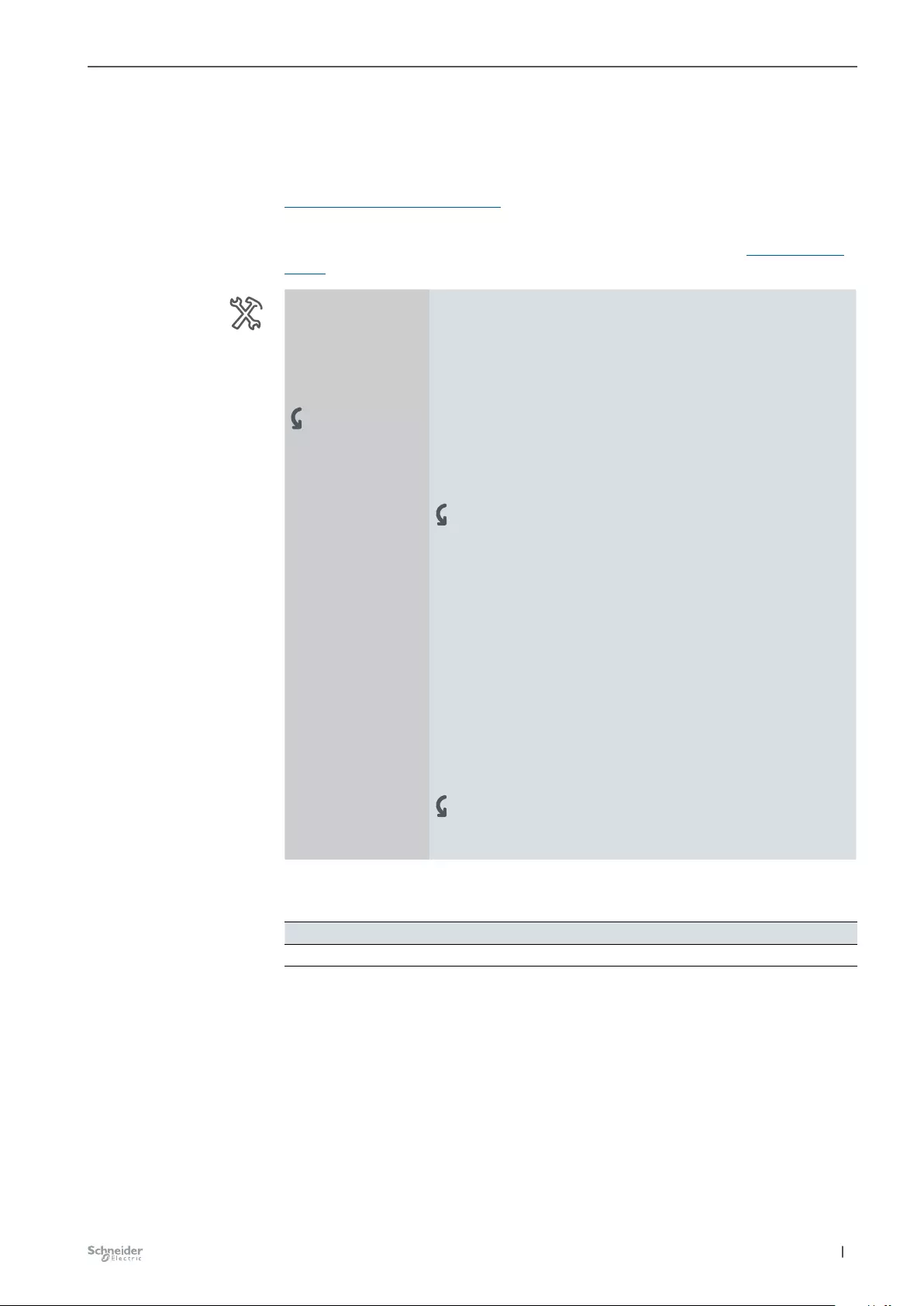
123
05/20-5800/1.0 MTN6705-0008 | MTN6805-0008 |
Extended settings for roller shutter Switch Blind 5800/1.0
10.3 Safety and alarm settings
Safety function for roller shutter
Safety function for blind --> 102
The global safety function is activated on the Extended settings tab with the param-
eter Device safety and the global settings are parameterized there. Device safety
--> 22
Master / Ext. 1/2
Output 1+2 / 3+4 / 5+6
/ 7+8
-Blind / roller shutter
Safety function
-Safety and alarm
settings Safety function Disabled
Enabled
Behavior at start of safety No reaction
Up
Down
Move to position
Height position at start of
safety in % 0 (0-100)
Behavior at end of safety No reaction
Up
Down
Move to position prior safety
Accept current automatic position
Behavior at exceeding cycle
time No reaction
Up
Down
Move to position
Height position on exceeding
cycle time in % 0 (0-100)
Group objects
No. Name Object function Length Behavior Data Type
23 Central Safety 1 bit Received 1.005 Alarm
Group object for
central safety
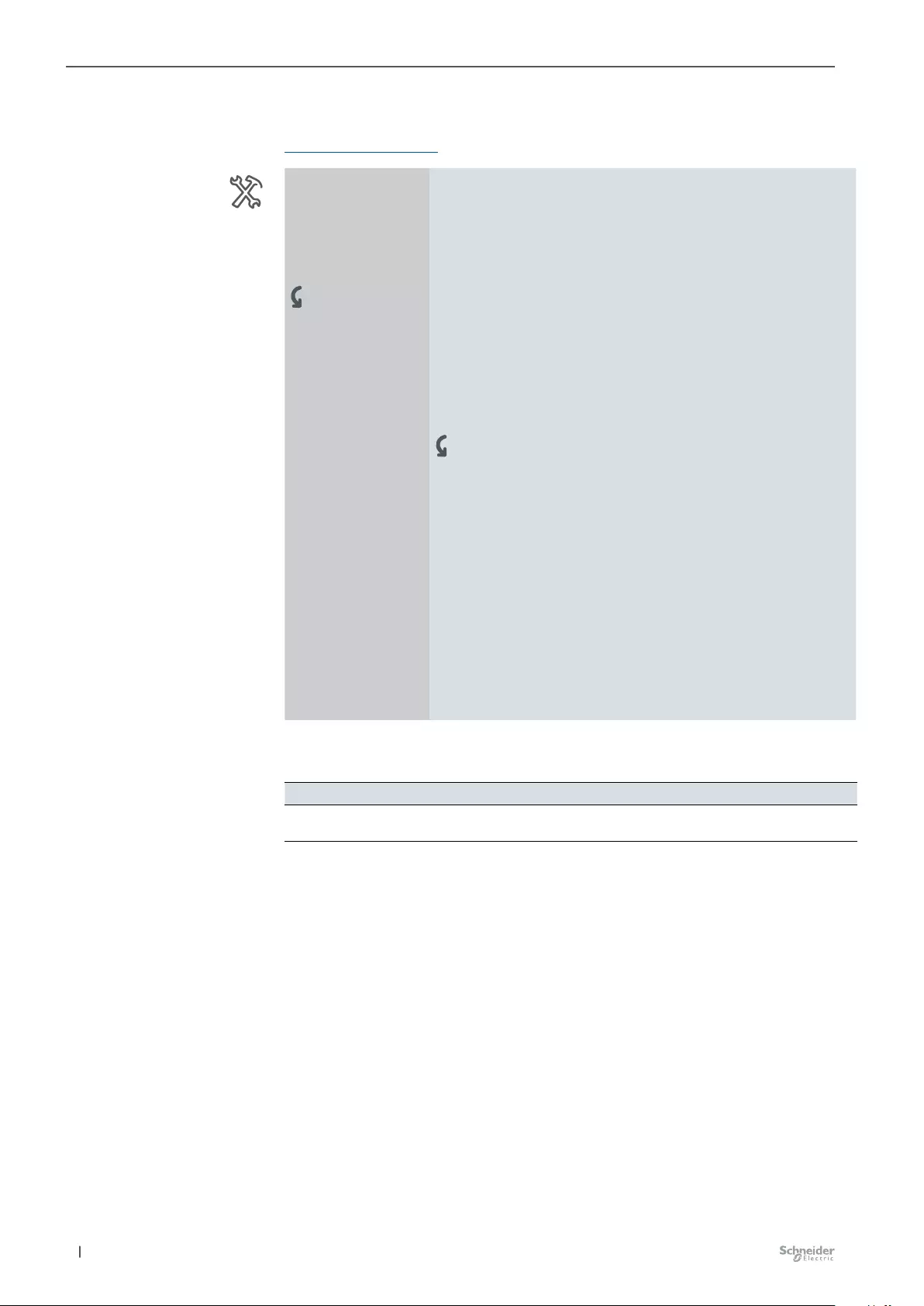
124 05/20-5800/1.0MTN6705-0008 | MTN6805-0008 |
Extended settings for roller shutter Switch Blind 5800/1.0
Alarm function
Alarm function --> 104
Master / Ext. 1/2
Output 1+2 / 3+4 / 5+6
/ 7+8
-Blind / roller shutter
Alarm function
-Safety and alarm
settings Alarm function Disabled
Enabled
Alarm At object value "1"
At object value "0"
Behavior at start of alarm No reaction
Up
Down
Move to position
Height position at start of
alarm in % 0 (0-100)
Behavior at end of alarm No reaction
Up
Down
Move to position prior alarm
Accept current automatic position
Behavior after bus voltage
recovery Disabled
Enabled
As before bus voltage failure
Group objects
No. Name Object function Length Behavior Data Type
42 Master Output 1+2
name of the channel
Alarm 1 bit Received 1.005 Alarm
Group objects of the alarm
function
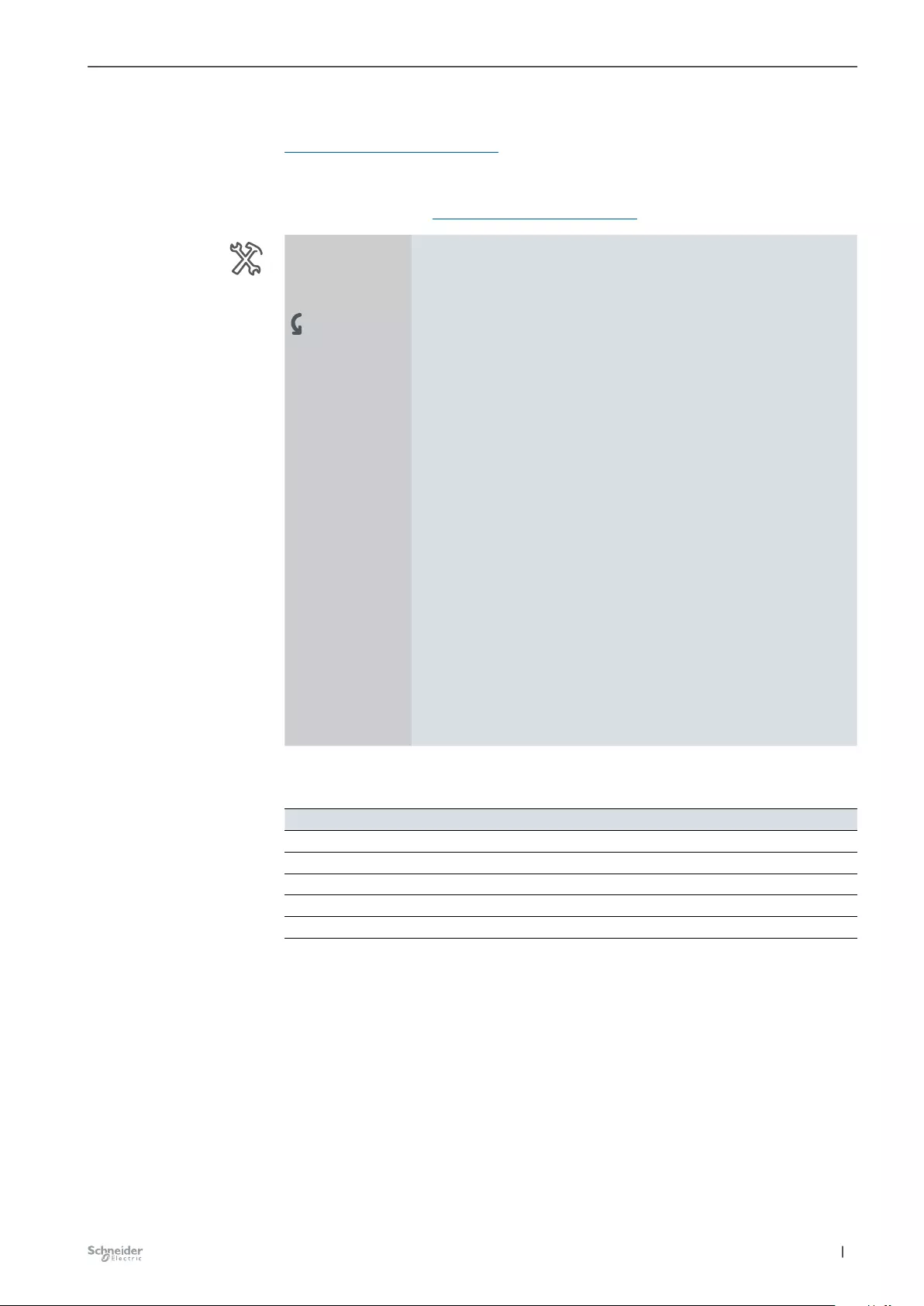
125
05/20-5800/1.0 MTN6705-0008 | MTN6805-0008 |
Extended settings for roller shutter Switch Blind 5800/1.0
Weather alarm function
Weather alarm function --> 106
The weather alarms are activated globally on the Extended settings tab with the
parameter Global settings for roller shutter and blind, and the global settings are
parameterized there. Weather alarm function --> 29
Extended
settings Global settings for roller shutter and blind
Weather alarm function Disabled
Enabled
Monitoring time for wind alarm 1 Disabled
1 s ... 12 h
Monitoring time for wind alarm 2 Disabled
1 s ... 12 h
Monitoring time for wind alarm 3 Disabled
1 s ... 12 h
Monitoring time for rain alarm Disabled
1 s ... 12 h
Monitoring time for frost alarm Disabled
1 s ... 12 h
Priority of weather alarms Wind alarm->Rain alarm->Frost alarm
Wind alarm->Frost alarm->Rain alarm
Rain alarm->Wind alarm->Frost alarm
Rain alarm->Frost alarm->Wind alarm
Frost alarm->Rain alarm->Wind alarm
Frost alarm->Wind alarm->Rain alarm
Group objects
No. Name Object function Length Behavior Data Type
18 Central Wind alarm 1 1 bit Received 1.005 Alarm
19 Central Wind alarm 2 1 bit Received 1.005 Alarm
20 Central Wind alarm 3 1 bit Received 1.005 Alarm
21 Central Rain alarm 1 bit Received 1.005 Alarm
22 Central Frost alarm 1 bit Received 1.005 Alarm
Group object for
weather alarms
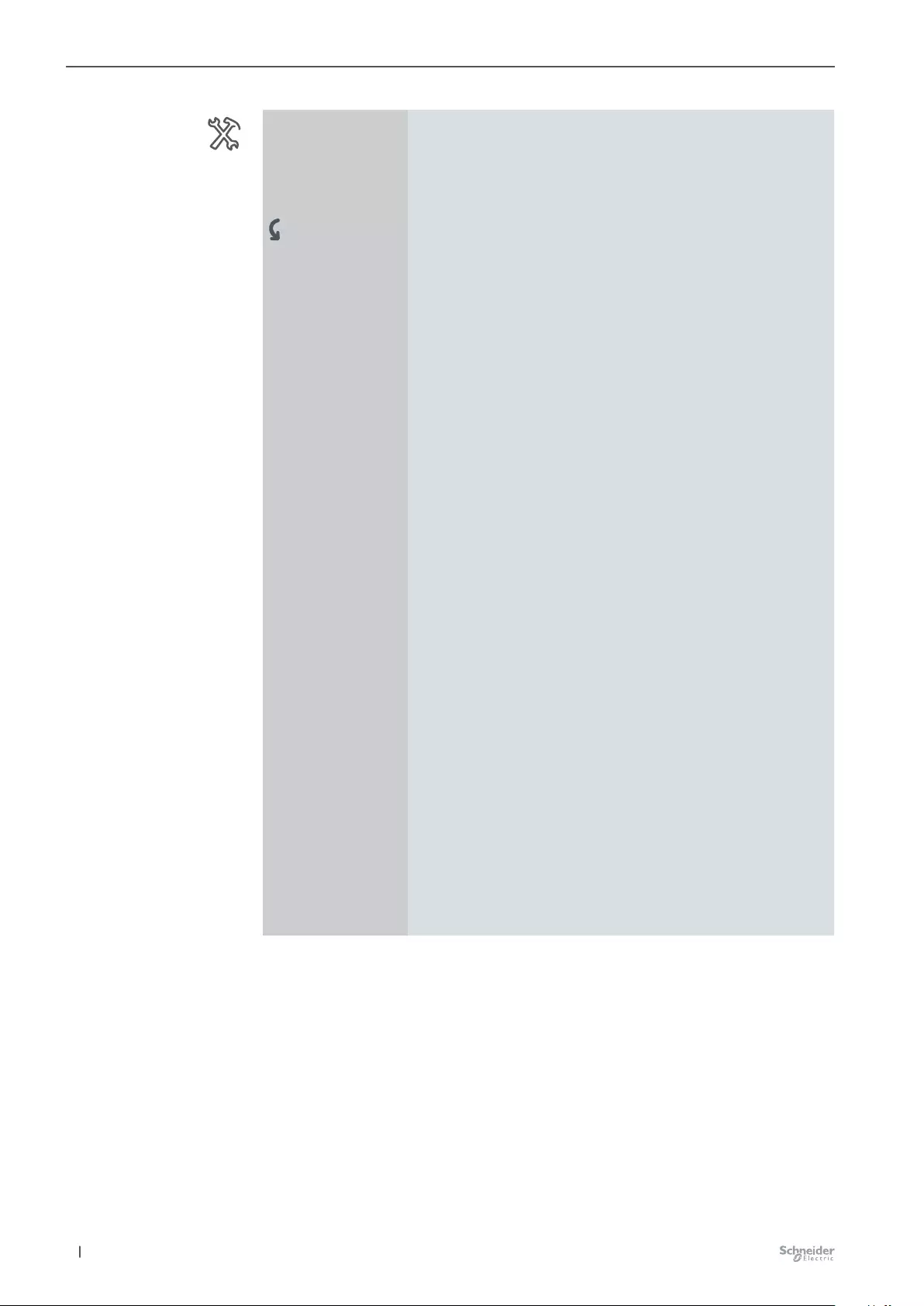
126 05/20-5800/1.0MTN6705-0008 | MTN6805-0008 |
Extended settings for roller shutter Switch Blind 5800/1.0
Master / Ext. 1/2
Output 1+2 / 3+4 / 5+6
/ 7+8
-Blind / roller shutter
Weather alarm function
-Safety and alarm
settings Weather alarm function Disabled
Enabled
Reacts on wind alarm 1 No
Yes
Reacts on wind alarm 2 No
Yes
Reacts on wind alarm 3 No
Yes
Use AND logic for wind
alarms No
Yes
Reaction on wind alarm(s) Up
Down
Move to position
Reaction on rain alarm No reaction
Up
Down
Move to position
Reaction on frost alarm No reaction
Up
Down
Move to position
Height position at weather
alarm in % 0 (0-100)
Behavior at end of all weather
alarms No reaction
Up
Down
Move to position prior weather alarm
Accept current automatic position
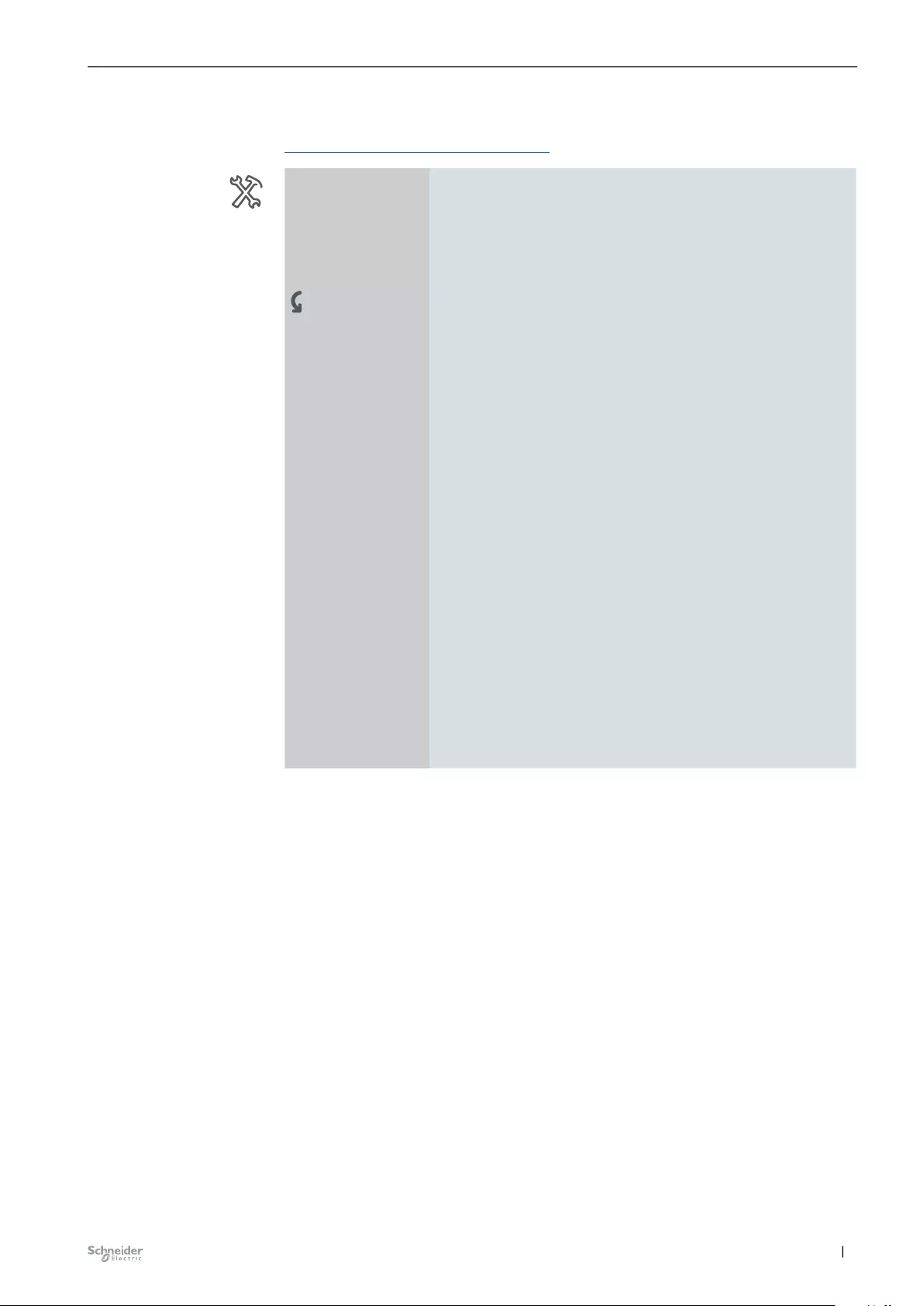
127
05/20-5800/1.0 MTN6705-0008 | MTN6805-0008 |
Extended settings for roller shutter Switch Blind 5800/1.0
Failure and download behavior
Failure and download behavior --> 110
Master / Ext. 1/2
Output 1+2 / 3+4 / 5+6
/ 7+8
-Blind / roller shutter
Failure and download behavior
-Safety and alarm
settings
Failure and download be-
havior Disabled
Enabled
Relay state after bus voltage
failure No reaction
Stop
Up
Down
Relay state after bus voltage
recovery Stop
Up
Down
Move to position
As before bus voltage failure
Height position at bus voltage
recovery in % 0 (0-100)
Relay state at end of down-
load Stop
Up
Down
Move to position
As before download
Height position at end of
download in % 0 (0-100)
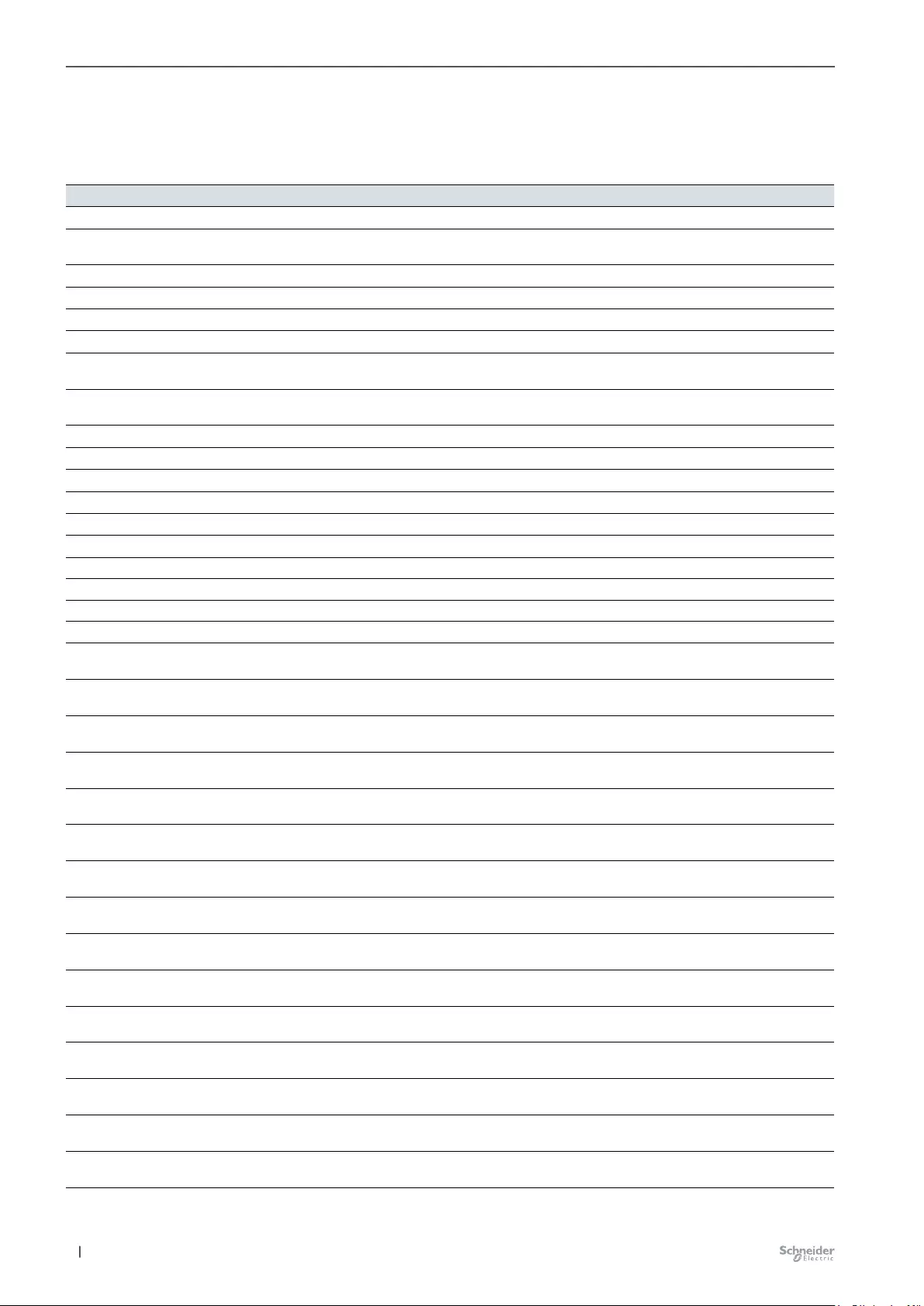
128 05/20-5800/1.0MTN6705-0008 | MTN6805-0008 |
Overview of group objects Switch Blind 5800/1.0
11 Overview of group objects
Group objects:
No. Name Object function Length Behavior Data Type
1 Central Switching 1 bit Received 1.001 switching
2 Central Move up/down roller
shutter
1 bit Received 1.008 Up/Down
3 Central Move up/down blind 1 bit Received 1.008 Up/Down
10 Master Collected status 4 bytes Send/Read 27.001 Bit-combined info On/O
11 Extension 1 Collected status 4 bytes Send/Read 27.001 Bit-combined info On/O
12 Extension 2 Collected status 4 bytes Send/Read 27.001 Bit-combined info On/O
15 Master keypad Enable button for man-
ual operation
1 bit Received 1.003 Enabled
16 Master keypad Status of manual
operation
1 bit Send/Read 1.001 switching
17 Central Calibration 1 bit Received 1.010 Start/Stop
18 Central Wind alarm 1 1 bit Received 1.005 Alarm
19 Central Wind alarm 2 1 bit Received 1.005 Alarm
20 Central Wind alarm 3 1 bit Received 1.005 Alarm
21 Central Rain alarm 1 bit Received 1.005 Alarm
22 Central Frost alarm 1 bit Received 1.005 Alarm
23 Central Safety 1 bit Received 1.005 Alarm
26 Central Life signal 1 bit Sending 1.017 Triggers
27 Master Fault - Internal 1 bit Sending 1.001 Switching
28 Master Fault - External 1 bit Sending 1.001 Switching
31 Master Output 1 name of the
channel
Switching 1 bit Received 1.001 Switching
31 Master Output 1+2 name of the
channel
Movement in manual
mode
1 bit Received 1.008 Up/DOWN
32 Master Output 1 name of the
channel
Logical input 1 bit Received 1.002 Boolean
32 Master Output 1+2 name of the
channel
Stop/step in manual
mode (blind)
1 bit Received 1.007 Step
32 Master Output 1+2 name of the
channel
Stop in manual mode
(roller shutter)
1 bit Received 1.007 Step
33 Master Output 1+2 name of the
channel
Height position in man-
ual mode
1 byte Received 5.001 Percent (0...100%)
33 Master Output 1 name of the
channel
Locking 1 bit Received 1.003 Enable
33 Master Output 1 name of the
channel
Priority 2 bit Received 2.001 Prio. switching
34 Master Output 1+2 name of the
channel
Slat position in manual
mode (blind)
1 byte Received 5.001 Percent (0...100%)
34 Master Output 1 name of the
channel
Alarm 1 bit Received 1.005 Alarm
35 Master Output 1 name of the
channel
Staircase x 1 bit Received 1.010 Start/Stop
35 Master Output 1 name of the
channel
Staircase variable 2 bytes Received 7.005 Time (s)
35 Master Output 1+2 name of the
channel
Locking manual mode 1 bit Received 1.003 Enable
36 Master Output 1 name of the
channel
Scene 1 byte Received 18.001 Scene control
36 Master Output 1+2 name of the
channel
Movement in automatic
mode
1 bit Received 1.008 Up/DOWN
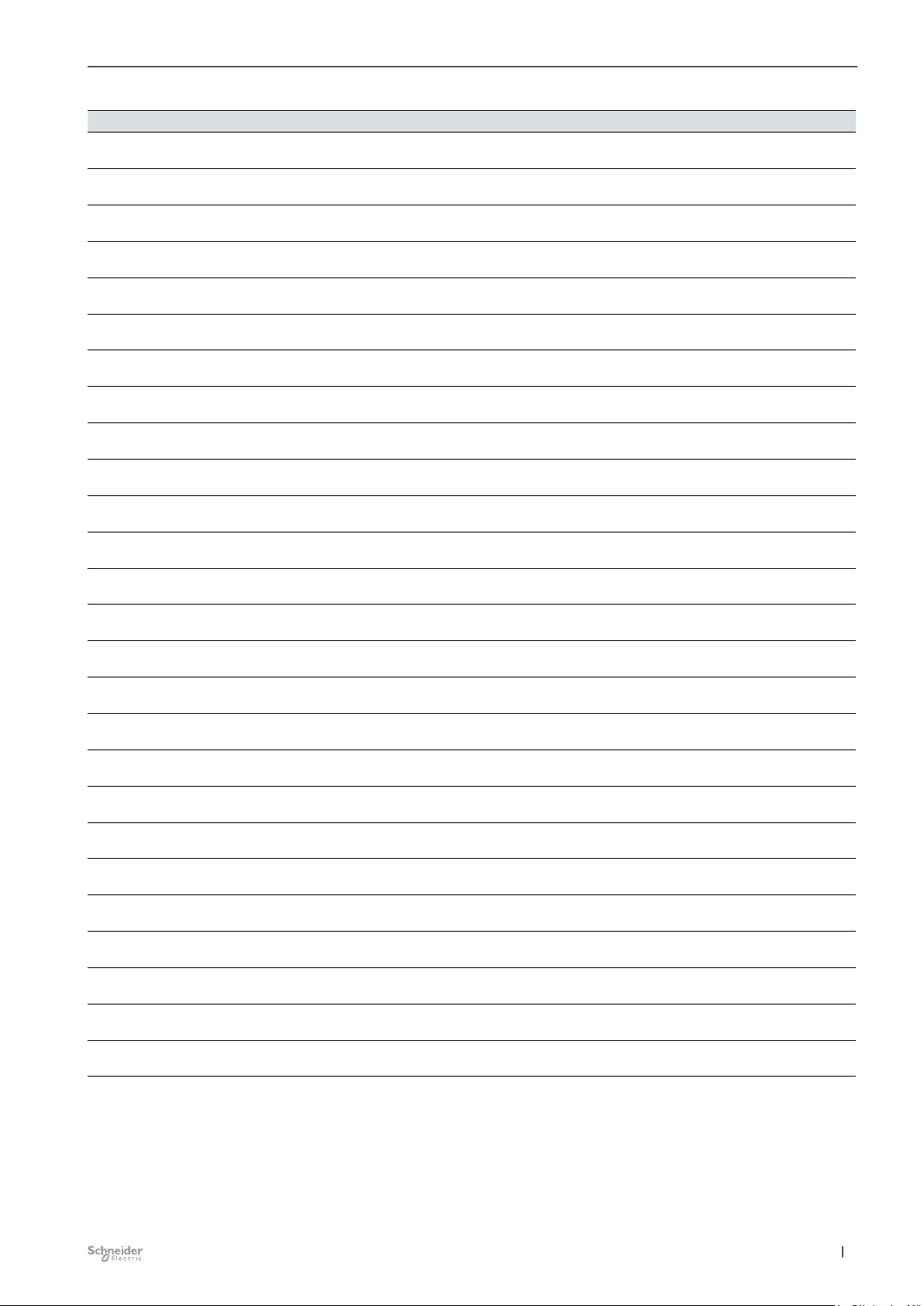
129
05/20-5800/1.0 MTN6705-0008 | MTN6805-0008 |
Overview of group objects Switch Blind 5800/1.0
No. Name Object function Length Behavior Data Type
37 Master Output 1 name of the
channel
Status feedback 1 bit Sending 1.001 Switching
37 Master Output 1+2 name of the
channel
Stop/step in automatic
mode (blind)
1 bit Received 1.007 Step
37 Master Output 1+2 name of the
channel
Stop in automatic mode
(roller shutter)
1 bit Received 1.007 Step
38 Master Output 1+2 name of the
channel
Height position in auto-
matic mode
1 byte Received 5.001 Percent (0...100%)
39 Master Output 1+2 name of the
channel
Slat position in auto-
matic mode (blind)
1 byte Received 5.001 Percent (0...100%)
40 Master Output 1+2 name of the
channel
Lock of automatic mode 1 bit Received 1.003 Enable
41 Master Output 1+2 name of the
channel
Locking 1 bit Received 1.003 Enable
42 Master Output 1+2 name of the
channel
Alarm 1 bit Received 1.005 Alarm
42 Master Output 2 name of the
channel
Switching 1 bit Received 1.001 Switching
43 Master Output 1+2 name of the
channel
Scene 1 byte Received 18.001 Scene control
43 Master Output 2 name of the
channel
Logical input 1 bit Received 1.002 Boolean
44 Master Output 1+2 name of the
channel
Activate movement
range limits
1 bit Received 1.003 Enable
44 Master Output 2 name of the
channel
Locking 1 bit Received 1.003 Enable
44 Master Output 2 name of the
channel
Priority 2 bit Received 2.001 Prio. switching
45 Master Output 1 name of the
channel
Alarm 1 bit Received 1.005 Alarm
46 Master Output 1+2 name of the
channel
Feedback for height 1 byte Sending 5.001 Percent (0...100%)
46 Master Output 2 name of the
channel
Staircase x 1 bit Received 1.010 Start/Stop
46 Master Output 2 name of the
channel
Staircase variable 2 bytes Received 7.005 Time (s)
47 Master Output 1+2 name of the
channel
Feedback for slat
(blind)
1 byte Sending 5.001 Percent (0...100%)
47 Master Output 2 name of the
channel
Scene 1 byte Received 18.001 Scene control
48 Master Output 1+2 name of the
channel
Feedback for automatic
mode
1 bit Sending 1.003 Enable
48 Master Output 2 name of the
channel
Status feedback 1 bit Sending 1.001 Switching
49 Master Output 1+2 name of the
channel
Feedback for drive
locking
1 bit Sending 1.003 Enable
50 Master Output 1+2 name of the
channel
Feedback for range
limitation
1 bit Sending 1.003 Enable
51 Master Output 1+2 name of the
channel
Feedback for moving 1 bit Sending 1.010 Start/Stop
52 Master Output 1+2 name of the
channel
Feedback for last
direction
1 bit Sending 1.008 Up/DOWN
This list contains the numbers of all group objects for outputs 1 and 2 on the master and all central objects.
All other outputs (3-8) at the master and all outputs 1-8 of extension 1 and all outputs 1-8 of extension 2 have
the same group objects.
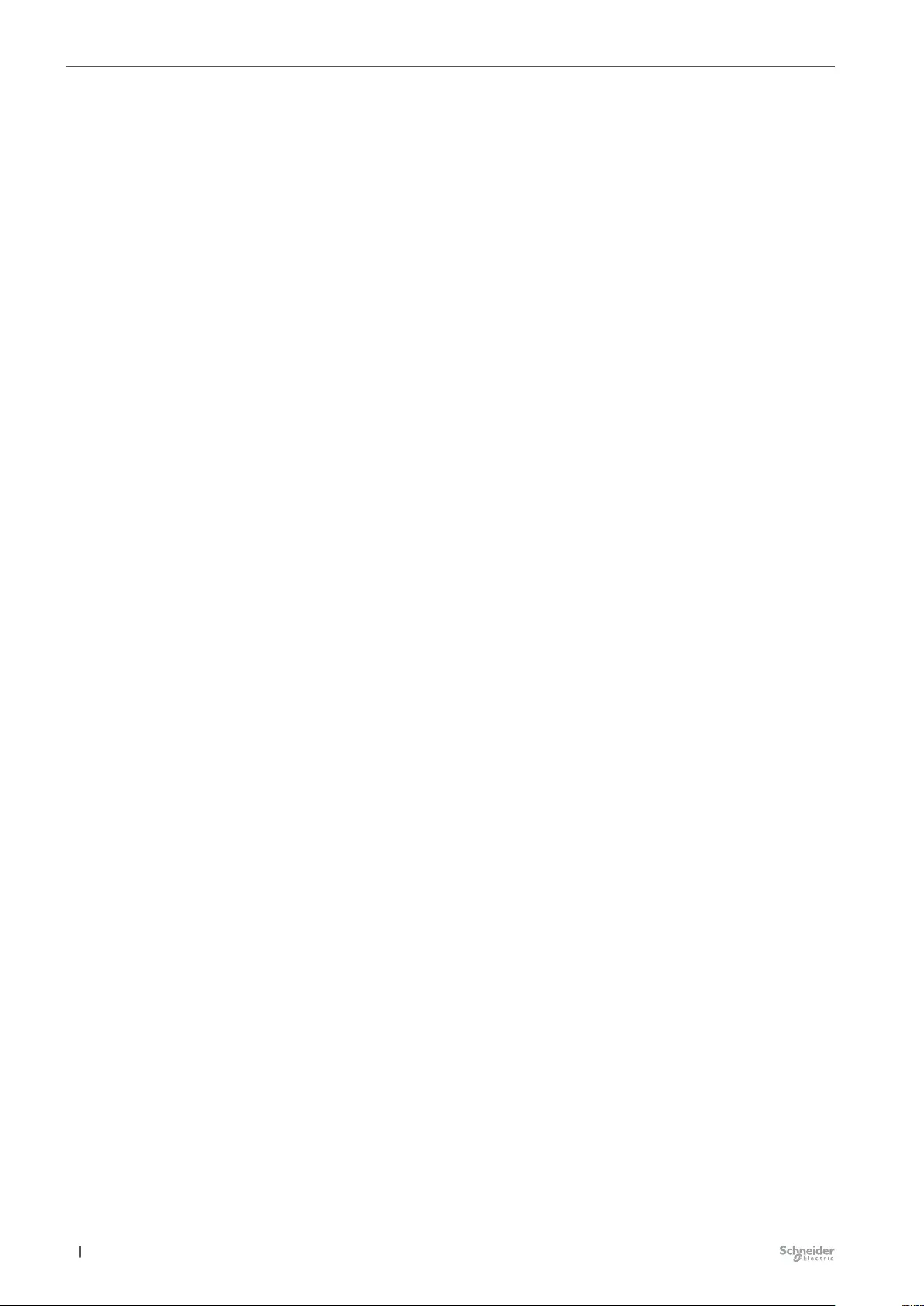
130 05/20-5800/1.0MTN6705-0008 | MTN6805-0008 |
Index Switch Blind 5800/1.0
Extension → 15
F
Failure and download behavior → 64, 110
Failure indicator → 23
feedback → 24
Functions with higher priority → 57
G
General settings → 15
global settings for roller shutter and blind → 29
global settings for the switching → 27
Group object for calibration → 31, 98, 122
Group object for central safety → 22, 61, 102, 123
Group object for collected status → 28
Group object for enable button for manual operation → 26
Group object for failure indicator → 23
Group object for live signal → 23
Group object for scene → 39, 80, 115
Group object for status of manual operation → 27
Group object for weather alarms → 30, 107, 125
Group objects → 128
Group objects for express setting for blind → 70
Group objects for express setting for roller shutter → 113
Group objects for lock of manual mode → 79, 114
Group objects for “Switching” express setting → 33
Group objects of automatic mode “Blind” → 89
Group objects of automatic mode “Lock” → 90, 119
Group objects of automatic mode “Roller shutter” → 118
Group objects of locking function → 59, 92, 120
Group objects of logic function → 53
Group objects of priority function → 57
Group objects of staircase lighting time → 44
Group objects of status response of automatic mode → 85
Group objects of status response of blind → 84
Group objects of status response of roller shutter → 116
Group objects of the alarm function → 62, 104, 124
Group objects of the central function → 20, 83, 116
Group objects of the function “Movement range limits” →
95, 121
I
Idle time → 87
L
live signal → 23
Locking function → 59, 91
Locking manual mode → 79
Logic function → 53
M
Manual operation settings → 25
Movement range limits → 94
MTN6805-0008 Switch/Blind → 15
12 Index
A
Activating extended settings for blind → 85
Activating extended settings for switching → 42
Additional start-up time → 88
Alarm function → 62, 104
AND logic operation → 54
Appropriate ETS version → 5
Automatic calibration → 99
Automatic mode → 88
B
Blind → 18
Blind / roller shutter control → 68
Blind type → 74
Blinking → 34
Blinking interval → 36
C
Calibration → 30, 98
Central function for blind → 83
central function for switching output → 41
central functions → 19
collected status response → 27
Contact mode → 37
Contact mode normally closed → 33
Contact mode normally opened → 33
Cyber Security → 15
D
Deceleration delay → 87
Dening channel functions → 16
Depictions in this document → 4
Device health → 23
Device protection → 15
Device safety → 22
Downwards closed / upwards closed → 76
Downwards closed / upwards horizontal → 74
Downwards tilted / upwards closed → 77
Downwards tilted / upwards horizontal → 75
Drive running time → 70
E
Energy saving → 22
ETS operation → 5
ETS soware → 12
Express settings → 5
Express settings for blind / roller shutter → 67
Express settings for roller shutter → 113
Express settings for switching → 32
Extended drive timing → 86
Extended settings → 22
Extended settings for blind / roller shutter → 86
Extended settings for roller shutter → 117
Extended settings for switching → 43
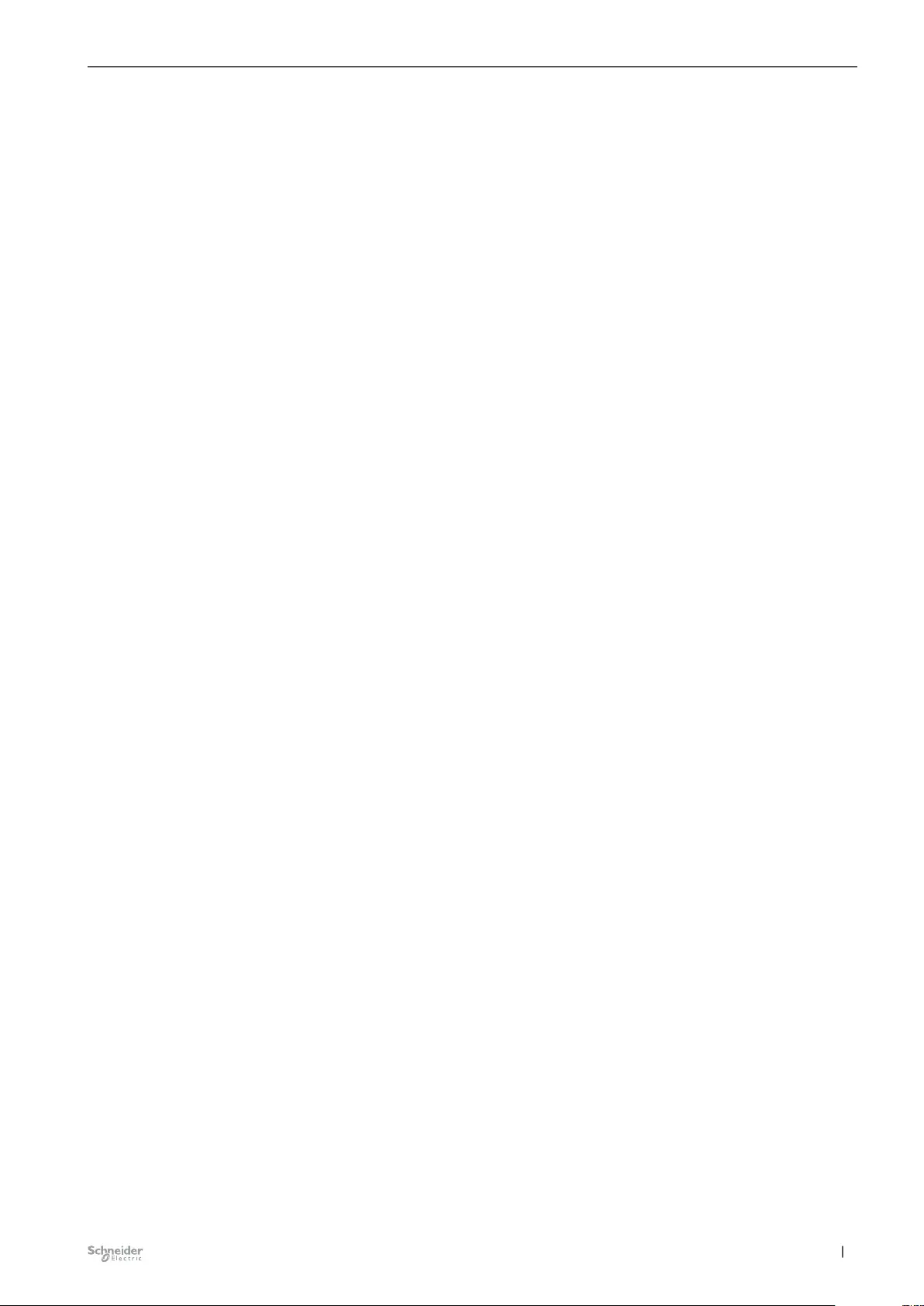
131
05/20-5800/1.0 MTN6705-0008 | MTN6805-0008 |
Index Switch Blind 5800/1.0
N
Name of the channel → 32, 70
Normally closed → 38
Normally opened → 37
O
O-delay → 50
On-delay → 49
On-delay and o delay → 49
OR logic operation → 55
Overview of application functions → 12
Overview of group objects → 128
P
pause on reverse → 72
Pause time before reverting → 72
PIN Code for Firmware Update → 31
Prewarnings → 47
Priority → 41, 62, 63, 83, 103, 106
priority control → 57
Priority function → 57
Priority of functions for roller shutter and blind → 30
Priority of functions for switching → 28
Priority of weather alarms → 29, 107
R
Reference position → 99
Roller shutter → 18
Roller shutters → 113
S
Safety and alarm settings → 61
Safety function for blind → 102
Safety function priority → 22
Safety function switching → 61
scene address → 40, 82
scenes → 24
Scenes → 39, 80, 115
scene values → 40, 82
Selection of the SpaceLogic KNX extensions → 15
Setting the blind type → 74
Slat control → 72
Slat position aer movement → 78
Slat rotation time → 72
SpaceLogic KNX Switch/Blind extensions → 15
Staircase lighting time x → 44
Staircase lighting time function → 43
Staircase lighting time variable → 44
staircase timer → 43
Startup delay → 87
Status of height → 84
Status of moving → 84
Status of slat → 84
status response → 42
Status response → 33, 34, 37, 38, 84
Switch → 18
Switching → 32
Switching mode → 32
T
Time delay for scene → 40
Time settings → 43
Type of Extension → 15
U
User interface → 6
W
Weather alarm function → 29, 106
X
XOR logic operation → 56