Table of Contents
- Contents
- Figures
- Tables
- Preface
- Chapter 1
- Overview
- x950 Switches
- Features
- Ports for 1/2.5/5/10Gbps SFP/SFP+ Transceivers
- Ports 1 to 24 on the x950-28XTQm Switch
- Ports for 40Gbps QSFP+ or 100Gbps QSFP28 Transceiver, or Breakout Cables
- Management Panel
- Optional Direct Attach Cables
- PWR600 AC and DC Power Supplies
- FAN05 Cooling Fan
- Designating Ports in the Command Line Interface
- Software and Hardware Releases
- Overview
- Chapter 2
- Chapter 3
- Chapter 4
- Chapter 5
- Chapter 6
- Chapter 7
- Chapter 8
- Chapter 9
- Installing the Switch in the RKMT-SL01 Sliding Rack
- Introduction
- Rack Mount Kit Components
- Equipment Rack Requirements
- Reviewing Safety Precautions
- Installation Overview
- Unpacking the Shipping Container
- Installing the Outer Rails on the Equipment Rack
- Installing the Extension Brackets on the Inner Rails
- Installing the Inner Rails on the Switch
- Installing the Switch in the Equipment Rack
- Installing the Switch in the RKMT-SL01 Sliding Rack
- Chapter 10
- Chapter 11
- Chapter 12
- Chapter 13
- Chapter 14
- Chapter 15
- Appendix A
Allied Telesis AT-x950-52XSQ-B01 User Manual
Displayed below is the user manual for AT-x950-52XSQ-B01 by Allied Telesis which is a product in the Network Switches category. This manual has pages.
Related Manuals
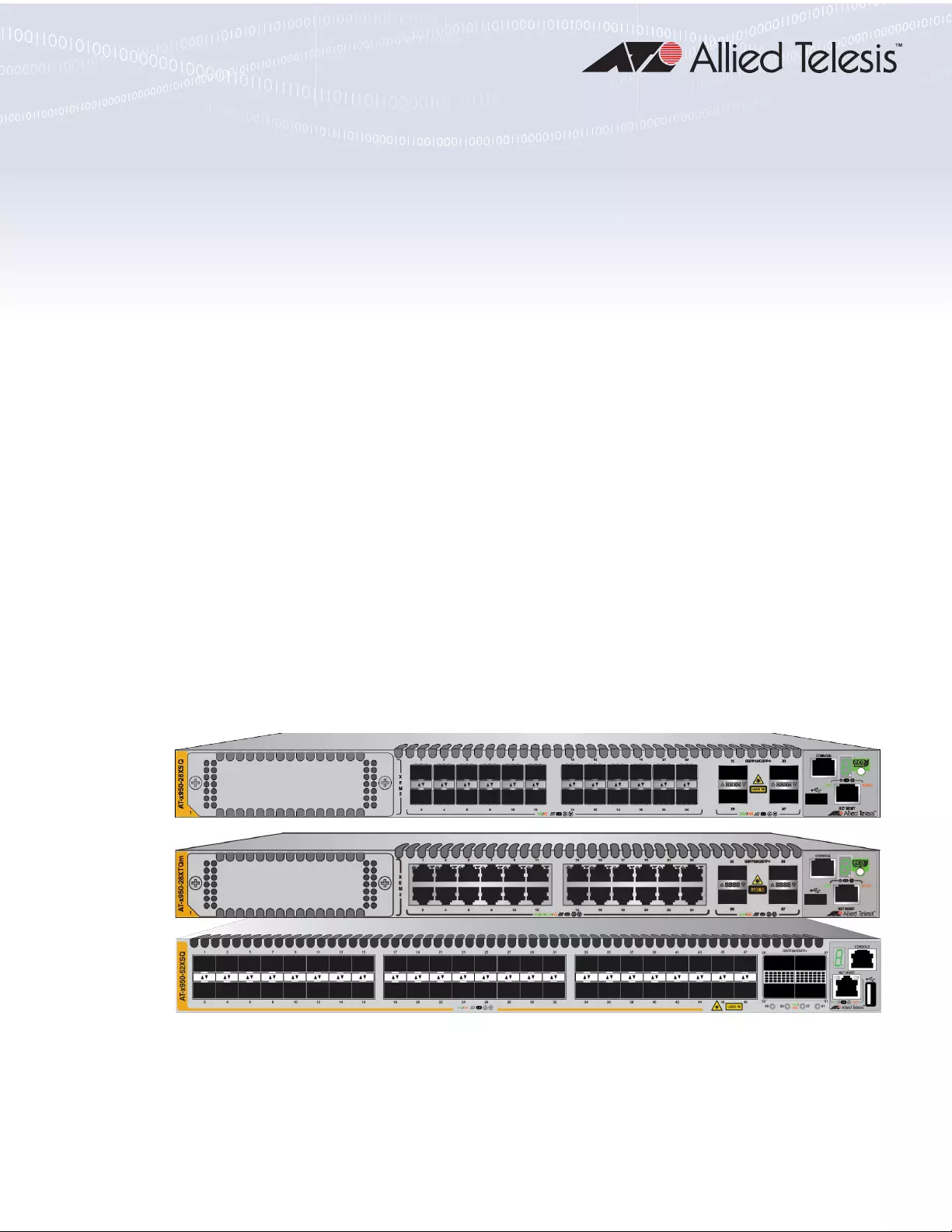
613-002643 Rev. E
x950 Series Switches
Advanced Layer 3+
AlliedWare Plus™ v5.5.0-1
x950-28XSQ Switch
x950-28XTQm Switch
x950-52XSQ Switch
XEM2-8XSTm Ethernet Line Card
XEM2-12XT Ethernet Line Card
XEM2-12XTm Ethernet Line Card
XEM2-12XS Ethernet Line Card
XEM2-12XS v2 Ethernet Line Card
XEM2-4QS Ethernet Line Card
XEM2-1CQ Ethernet Line Card
PWR600 AC Power Supply
PWR600 DC Power Supply
FAN05 Fan Module
Installation Guide for Virtual Chassis
Stacking
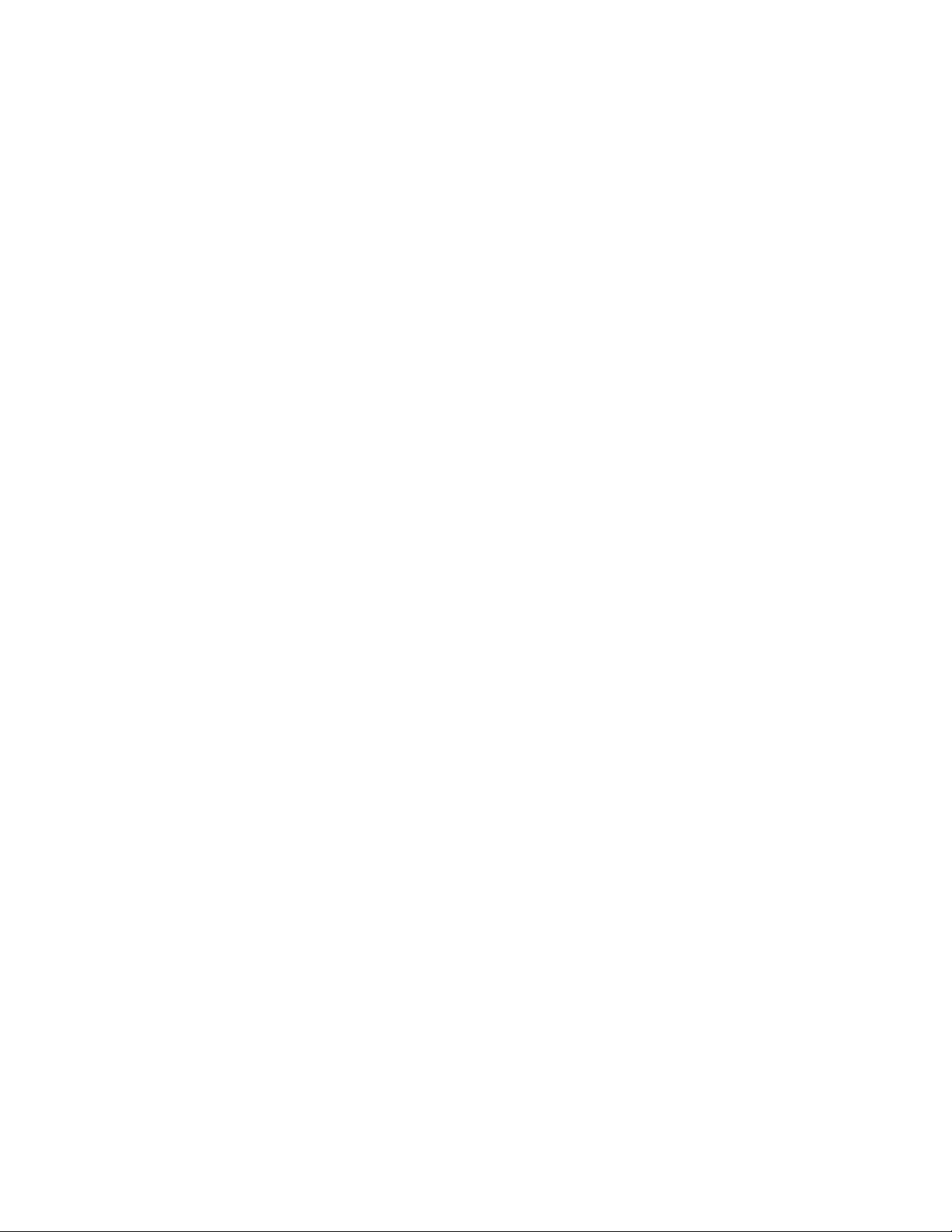
Copyright 2020 Allied Telesis, Inc.
All rights reserved. No part of this publication may be reproduced without prior written permission from Allied Telesis, Inc.
Allied Telesis, VCStack, and the Allied Telesis logo are trademarks of Allied Telesis, Incorporated. All other product names, company
names, logos or other designations mentioned herein are trademarks or registered trademarks of their respective owners.
Allied Telesis, Inc. reserves the right to make changes in specifications and other information contained in this document without prior
written notice. The information provided herein is subject to change without notice. In no event shall Allied Telesis, Inc. be liable for
any incidental, special, indirect, or consequential damages whatsoever, including but not limited to lost profits, arising out of or related
to this manual or the information contained herein, even if Allied Telesis, Inc. has been advised of, known, or should have known, the
possibility of such damages.
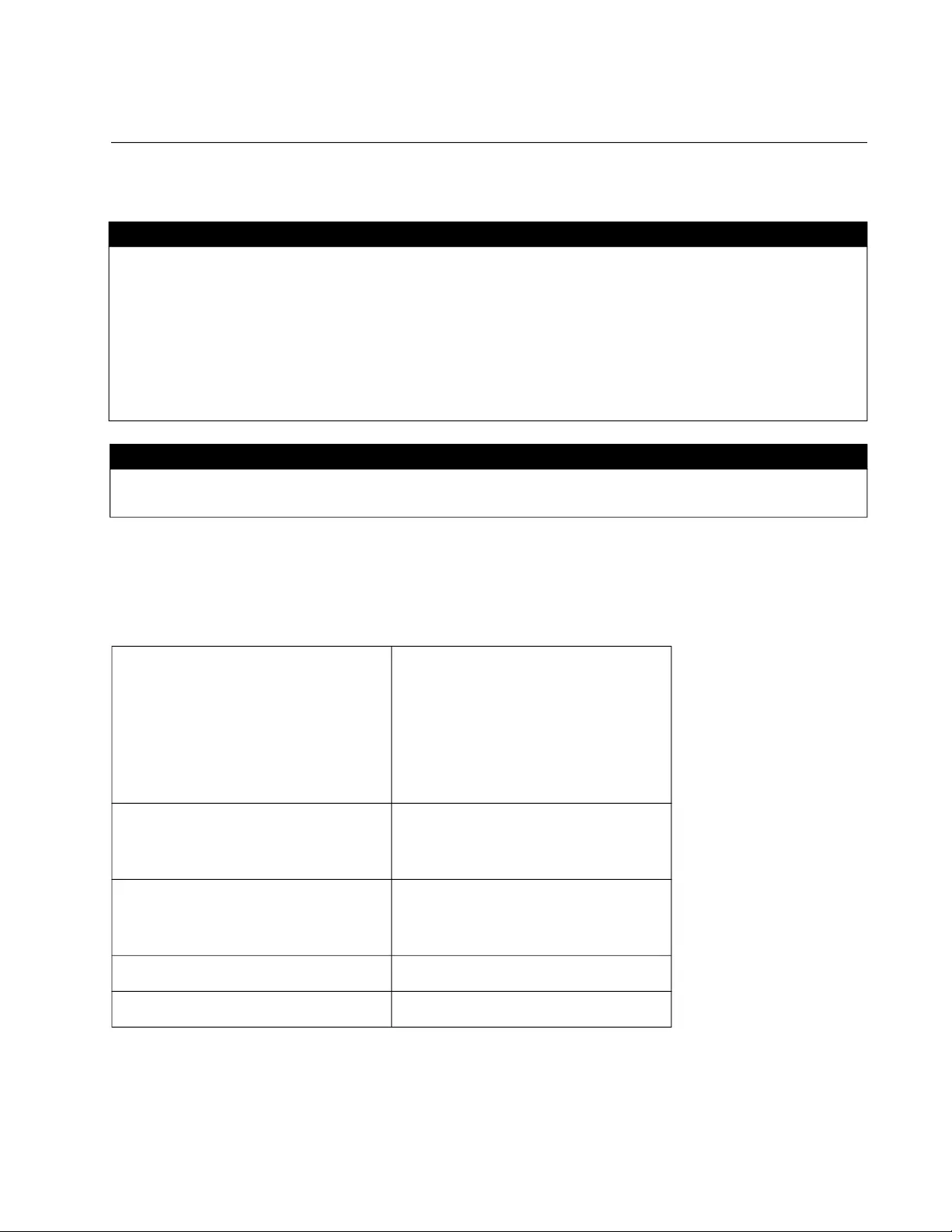
3
Electrical Safety and Emissions Standards
This product meets the following standards.
U.S. Federal Communications Commission
Radiated Energy
Note: This equipment has been tested and found to comply with the limits for a Class A digital device pursuant to Part 15
of FCC Rules. These limits are designed to provide reasonable protection against harmful interference when the
equipment is operated in a commercial environment. This equipment generates, uses, and can radiate radio frequency
energy and, if not installed and used in accordance with this instruction manual, may cause harmful interference to radio
communications. Operation of this equipment in a residential area is likely to cause harmful interference in which case
the user will be required to correct the interference at his own expense.
Note: Modifications or changes not expressly approved of by the manufacturer or the FCC, can void your right to operate
this equipment.
Industry Canada
This Class A digital apparatus complies with Canadian ICES-003.
Cet appareil numérique de la classe A est conforme à la norme NMB-003 du Canada.
Warning: In a domestic environment this product may cause radio interference in which case
the user may be required to take adequate measures.
EMI (Emissions) FCC Class A
CISPR 22 Class A
EN 55032 Class A
VCCI Class A
ICES-003 Class A
RCM
EAC Certification
EMC (Immunity) EN 55024
EN 61000-3-2
EN 61000-3-3
Electrical Safety UL 60950-1 (CULUS)
EN 62368-1 (TUV)
EN 60825-1 (TUV)
Laser Safety EN60825-1
RoHS RoHS6
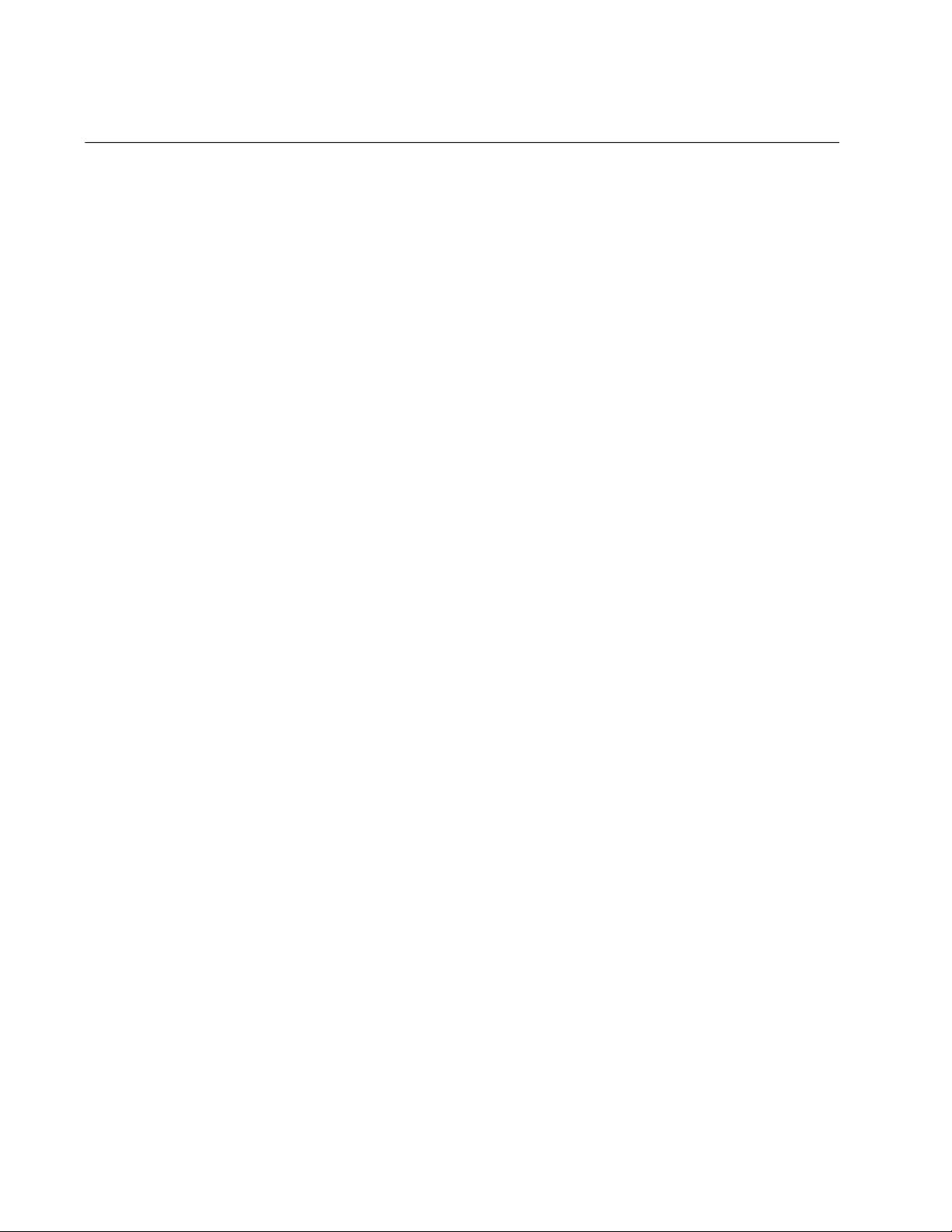
4
Translated Safety Statements
Important: Safety statements that have the symbol are translated into multiple languages in the
Translated Safety Statements document at www.alliedtelesis.com/library.
Remarque: Les consignes de sécurité portant le symbole sont traduites dans plusieurs langues
dans le document Translated Safety Statements, disponible à l'adresse www.alliedtelesis.com/
library.
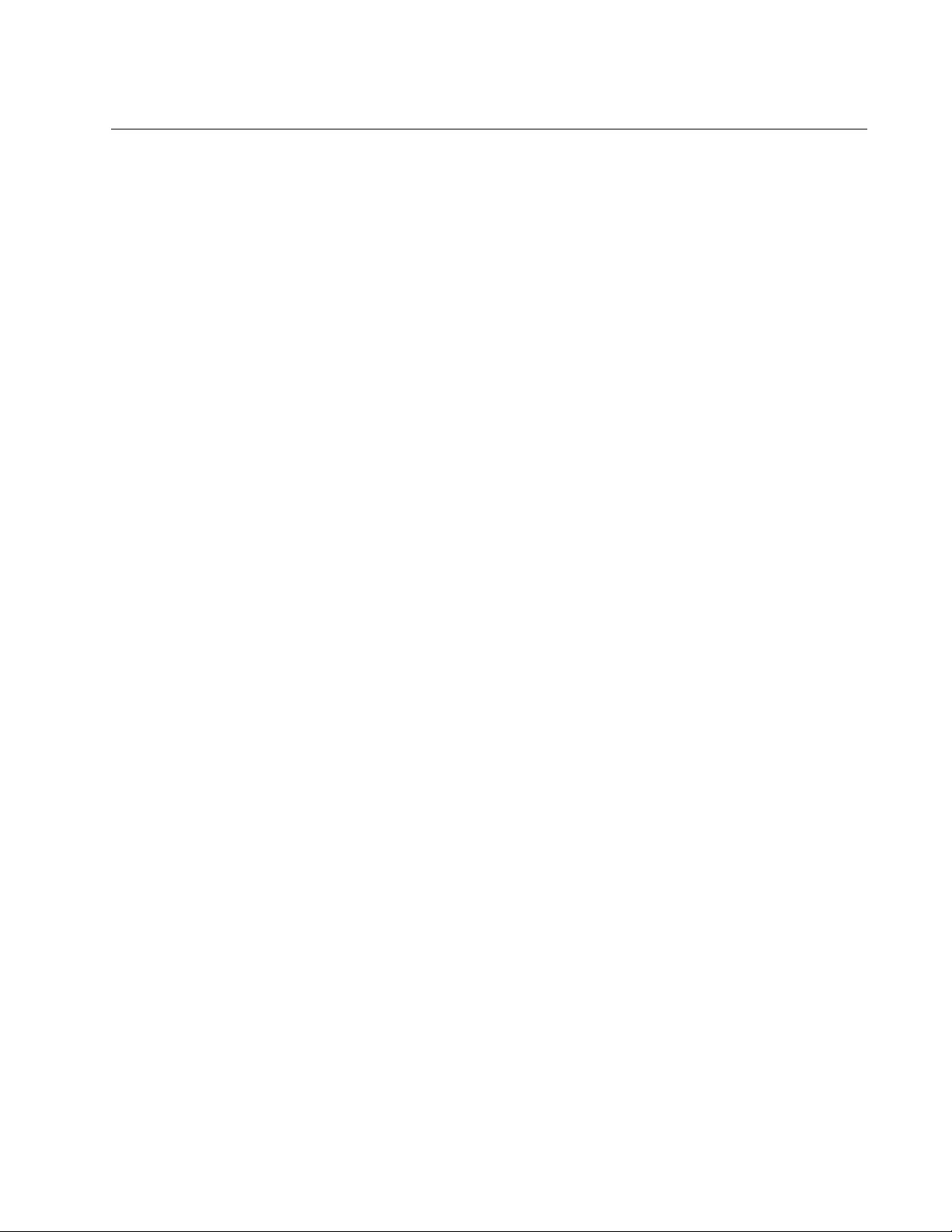
5
Preface............................................................................................................................................................................... 15
Document Conventions ................................................................................................................................................16
Contacting Allied Telesis ..............................................................................................................................................17
Chapter 1: Overview ........................................................................................................................................................ 19
x950 Switches ..............................................................................................................................................................20
Features .......................................................................................................................................................................22
Hardware Features ...............................................................................................................................................22
XEM2 Ethernet Line Cards ...................................................................................................................................22
Management Software and Interfaces ..................................................................................................................23
Management Methods ..........................................................................................................................................23
Management Panel ...............................................................................................................................................23
Power Supplies .....................................................................................................................................................24
Ports for 1/2.5/5/10Gbps SFP/SFP+ Transceivers.......................................................................................................25
SFP and SFP+ Transceivers.................................................................................................................................25
LEDs .....................................................................................................................................................................26
Ports 1 to 24 on the x950-28XTQm Switch ..................................................................................................................27
Cable Requirements .............................................................................................................................................27
LEDs .....................................................................................................................................................................28
Ports for 40Gbps QSFP+ or 100Gbps QSFP28 Transceiver, or Breakout Cables ......................................................29
QSFP28 Transceivers ...........................................................................................................................................29
QSFP+ Transceivers.............................................................................................................................................29
Breakout Cables....................................................................................................................................................29
LEDs .....................................................................................................................................................................30
Port Numbering for the x950-28XSQ and x950-28XTQm Switches......................................................................32
Port Numbering for the x950-52XSQ Switch.........................................................................................................33
Management Panel ......................................................................................................................................................34
USB Port ...............................................................................................................................................................35
NET MGMT Ethernet Management Port ...............................................................................................................35
Console (RS-232) Port ..........................................................................................................................................36
Switch ID LED .......................................................................................................................................................36
eco-friendly Button ................................................................................................................................................38
Optional Direct Attach Cables ......................................................................................................................................39
PWR600 AC and DC Power Supplies ..........................................................................................................................40
PWR600 AC Power Supply...................................................................................................................................41
LEDs .....................................................................................................................................................................42
PWR600 DC Power Supply ..................................................................................................................................43
LEDs .....................................................................................................................................................................43
..............................................................................................................................................................................43
FAN05 Cooling Fan......................................................................................................................................................45
Designating Ports in the Command Line Interface.......................................................................................................46
Examples of Port Numbering ................................................................................................................................47
Software and Hardware Releases................................................................................................................................49
Chapter 2: XEM2 Ethernet Line Cards ........................................................................................................................... 51
Overview ......................................................................................................................................................................52
XEM2-8XSTm Line Card..............................................................................................................................................55
Twisted Pair Ports .................................................................................................................................................55
Twisted Pair Port LEDs .........................................................................................................................................56
Transceivers Ports ................................................................................................................................................57
Contents
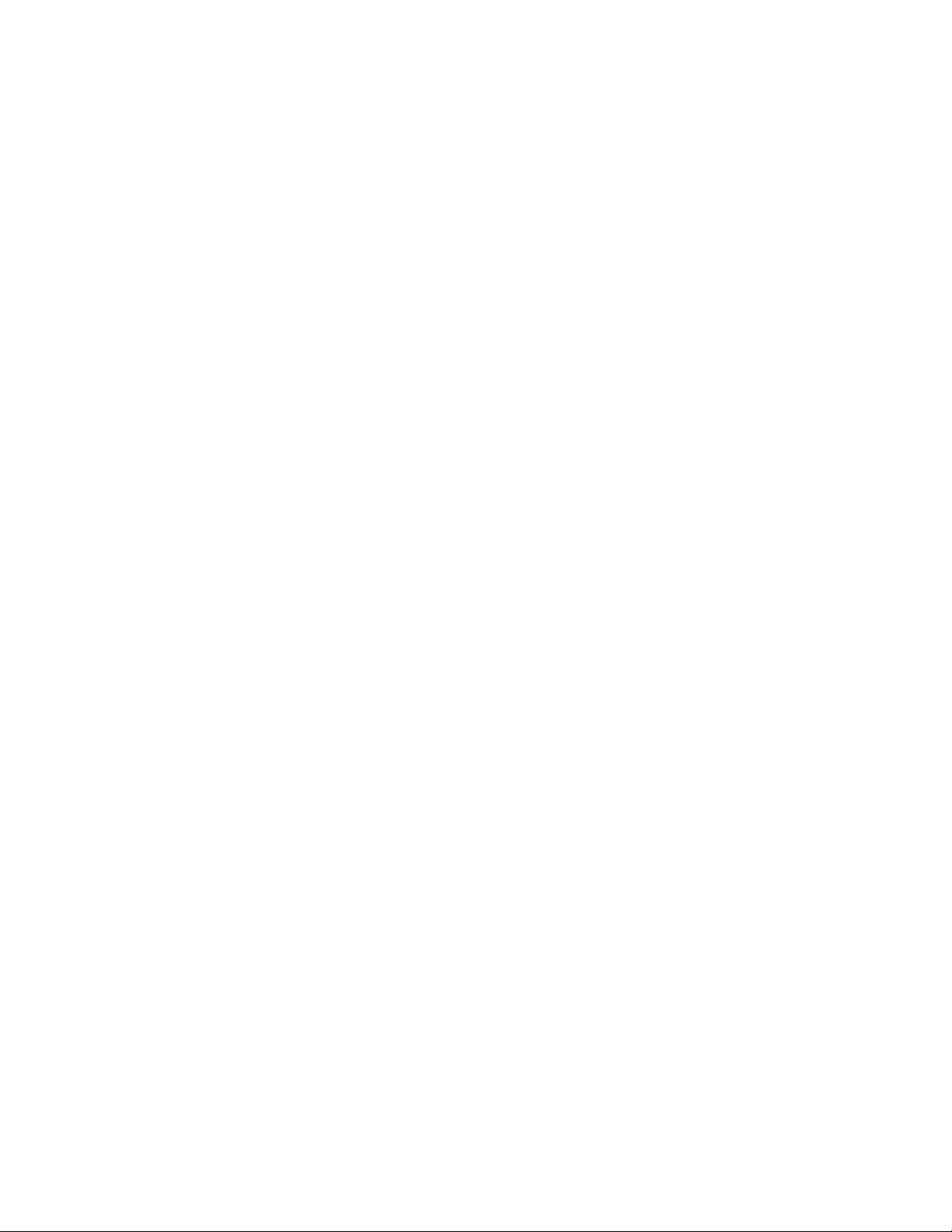
Contents
6
Transceivers Port LEDs........................................................................................................................................ 57
XEM2-12XT Line Card ................................................................................................................................................ 59
Twisted Pair Ports ................................................................................................................................................ 59
LEDs..................................................................................................................................................................... 60
XEM2-12XTm Line Card.............................................................................................................................................. 61
Twisted Pair Ports ................................................................................................................................................ 61
LEDs..................................................................................................................................................................... 62
XEM2-12XS and XEM2-12XS v2 Line Cards.............................................................................................................. 63
Transceiver Ports ................................................................................................................................................. 63
Card Versions....................................................................................................................................................... 64
LEDs..................................................................................................................................................................... 64
XEM2-4QS Line Card.................................................................................................................................................. 66
Transceiver Ports ................................................................................................................................................. 66
LEDs..................................................................................................................................................................... 67
XEM2-1CQ Line Card.................................................................................................................................................. 68
Transceiver Port ................................................................................................................................................... 68
LED ...................................................................................................................................................................... 68
Chapter 3: Virtual Chassis Stacking .............................................................................................................................. 71
Overview...................................................................................................................................................................... 72
Stacking Guidelines..................................................................................................................................................... 73
Stack Trunks................................................................................................................................................................ 74
Ports 1 to 24 and Ports 1 to 48............................................................................................................................. 74
Ports 25 to 37 and Ports 49 to 61 with 40Gbps Transceivers .............................................................................. 79
Ports 25 to 37 and Ports 49 to 61 with 100Gbps Transceivers ............................................................................ 80
XEM2 Line Cards ................................................................................................................................................. 82
Unsupported Trunks............................................................................................................................................. 84
Master and Member Switches ..................................................................................................................................... 89
Selection of the Master Switch ............................................................................................................................. 89
Switch ID Numbers ...................................................................................................................................................... 90
Optional Feature Licenses........................................................................................................................................... 91
Planning a Stack.......................................................................................................................................................... 92
Stacking Worksheet..................................................................................................................................................... 93
Chapter 4: Beginning the Installation ............................................................................................................................ 97
Reviewing Safety Precautions ..................................................................................................................................... 98
Installation Options .................................................................................................................................................... 103
Choosing a Site for the Chassis ................................................................................................................................ 104
Unpacking the Switch ................................................................................................................................................ 105
Verifying the Accessory Kit ........................................................................................................................................ 109
Unpacking the PWR600 AC Power Supply ............................................................................................................... 111
Unpacking the PWR600 DC Power Supply ............................................................................................................... 114
Chapter 5: Installing Power Supplies and Optional XEM2 Line Card ....................................................................... 115
Installing PWR600 AC Power Supplies ..................................................................................................................... 116
Installing PWR600 DC Power Supplies ..................................................................................................................... 120
Connecting the Grounding Wire ................................................................................................................................ 123
Connecting the DC Power Wires ............................................................................................................................... 126
Installing an Optional XEM2 Ethernet Line Card ....................................................................................................... 130
Chapter 6: Installing the Switch on a Table ................................................................................................................. 135
Chapter 7: Installing the Switch in an Equipment Rack ............................................................................................. 139
Beginning the Installation .......................................................................................................................................... 140
Required Items ................................................................................................................................................... 140
Switch Orientations in the Equipment Rack ....................................................................................................... 140
Removing the Bumper Feet....................................................................................................................................... 142
Installing the Switch................................................................................................................................................... 143
Chapter 8: Installing the Switch on a Wall ................................................................................................................... 147
Switch Orientations on a Wall.................................................................................................................................... 148
Recommended Minimum Wall Area Dimensions ...................................................................................................... 149
Plywood Base for a Wall with Wooden Studs............................................................................................................ 151
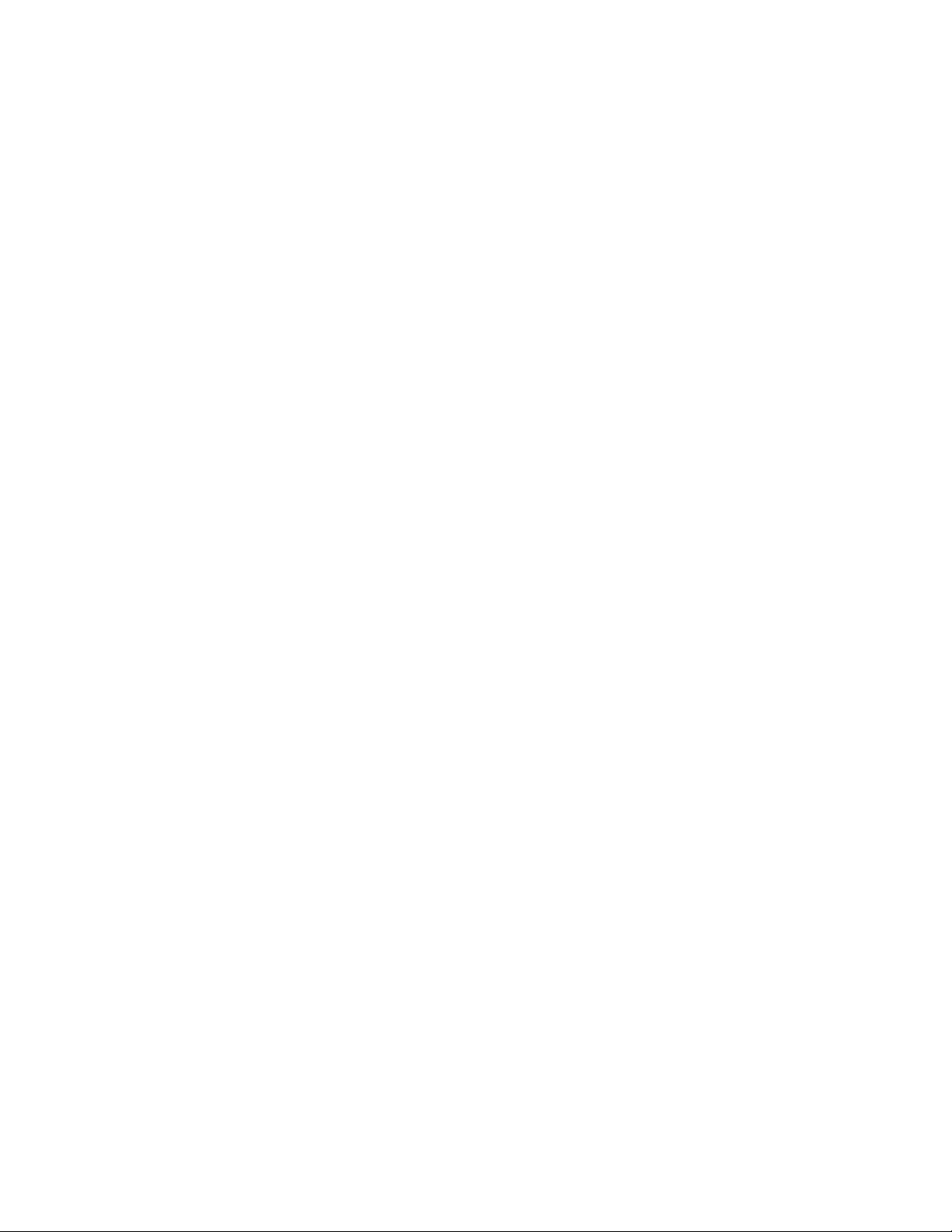
x950-28XSQ Switch and VCStack Installation Guide
7
Installation Guidelines ................................................................................................................................................153
Tools and Material...............................................................................................................................................153
Installing the Plywood Base .......................................................................................................................................155
Installing the Switch on the Plywood Base.................................................................................................................156
Installing the Switch on a Concrete Wall ....................................................................................................................159
Chapter 9: Installing the Switch in the RKMT-SL01 Sliding Rack ............................................................................. 163
Introduction.................................................................................................................................................................164
Rack Mount Kit Components......................................................................................................................................165
Adjustable Outer Rails ........................................................................................................................................165
Inner Rails ...........................................................................................................................................................165
Extension Brackets .............................................................................................................................................165
Equipment Rack Requirements..................................................................................................................................167
Reviewing Safety Precautions....................................................................................................................................168
Installation Overview ..................................................................................................................................................171
Unpacking the Shipping Container .............................................................................................................................172
Installing the Outer Rails on the Equipment Rack......................................................................................................174
Installing the Extension Brackets on the Inner Rails ..................................................................................................176
Measuring the Extension Bracket Lengths..........................................................................................................176
Assembling the Extension Brackets ....................................................................................................................178
Installing the Inner Rails on the Switch.......................................................................................................................182
Installing the Switch in the Equipment Rack...............................................................................................................184
Chapter 10: Configuring the Master Switch ................................................................................................................ 187
Command Summary...................................................................................................................................................188
PLATFORM PORTMODE INTERFACE..............................................................................................................188
STACKPORT ......................................................................................................................................................189
STACK ENABLE .................................................................................................................................................189
STACK PRIORITY ..............................................................................................................................................190
STACK RENUMBER...........................................................................................................................................190
SWITCH PROVISION .........................................................................................................................................190
Powering On a Switch ................................................................................................................................................192
Powering on the PWR600 AC Power Supply......................................................................................................192
Powering on the PWR600 DC Power Supply......................................................................................................194
Starting a Local Management Session.......................................................................................................................196
General Steps for the Master Switch..........................................................................................................................198
Configuring the Master Switch - Part I........................................................................................................................200
Configuring the Master Switch - Part II.......................................................................................................................203
Verifying the Master Switch ........................................................................................................................................206
What to Do Next .........................................................................................................................................................208
Chapter 11: Configuring Member Switches ................................................................................................................ 209
General Steps for Member Switches..........................................................................................................................210
Configuring a Member Switch - Part I.........................................................................................................................212
Configuring a Member Switch - Part II........................................................................................................................215
Verifying a Member Switch.........................................................................................................................................218
What to Do Next .........................................................................................................................................................220
Chapter 12: Powering On and Verifying the Stack ..................................................................................................... 221
Powering on the Stack ...............................................................................................................................................222
Verifying the Stack .....................................................................................................................................................223
Chapter 13: Cabling the Networking Ports .................................................................................................................. 225
Cabling Twisted Pair Ports .........................................................................................................................................226
Guidelines to Handling Twisted Pair or Fiber Optic Transceivers ..............................................................................227
Installing Transceivers................................................................................................................................................228
Installing Direct Attach Cables....................................................................................................................................235
Chapter 14: Replacing Modules ................................................................................................................................... 237
Replacing XEM2 Ethernet Line Cards........................................................................................................................238
Replacing PWR600 AC Power Supplies ....................................................................................................................243
Replacing PWR600 DC Power Supplies ....................................................................................................................248
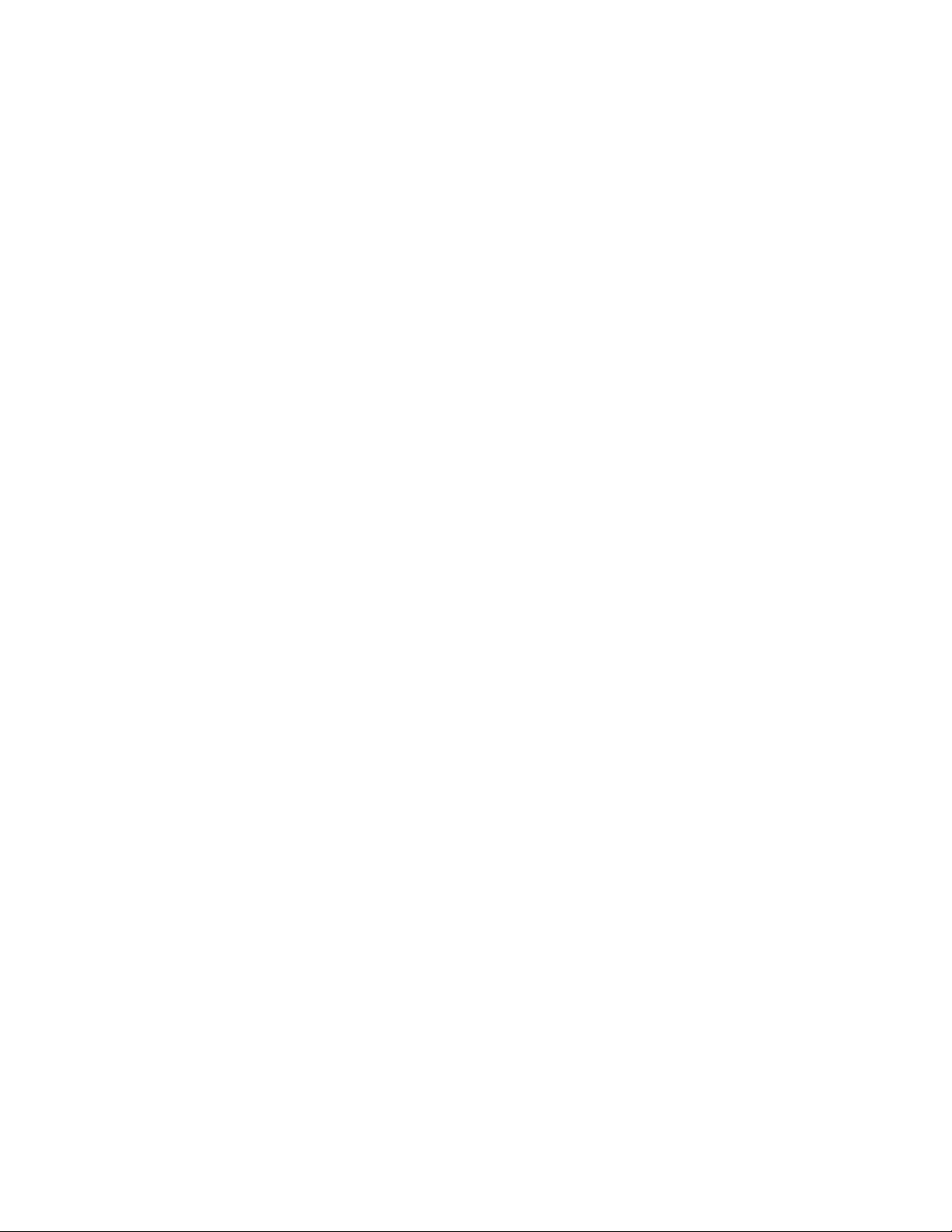
Contents
8
Replacing FAN05 Modules ........................................................................................................................................ 251
Removing Fan Modules ..................................................................................................................................... 251
Installing Fan Modules ....................................................................................................................................... 253
Chapter 15: Troubleshooting ........................................................................................................................................ 257
Appendix A: Technical Specifications ......................................................................................................................... 263
Physical Specifications .............................................................................................................................................. 264
Environmental Specifications..................................................................................................................................... 267
Power Specifications ................................................................................................................................................. 268
Certifications .............................................................................................................................................................. 277
RJ-45 Twisted Pair Port Pinouts................................................................................................................................ 278
RJ-45 Style Serial Console Port Pinouts ................................................................................................................... 280
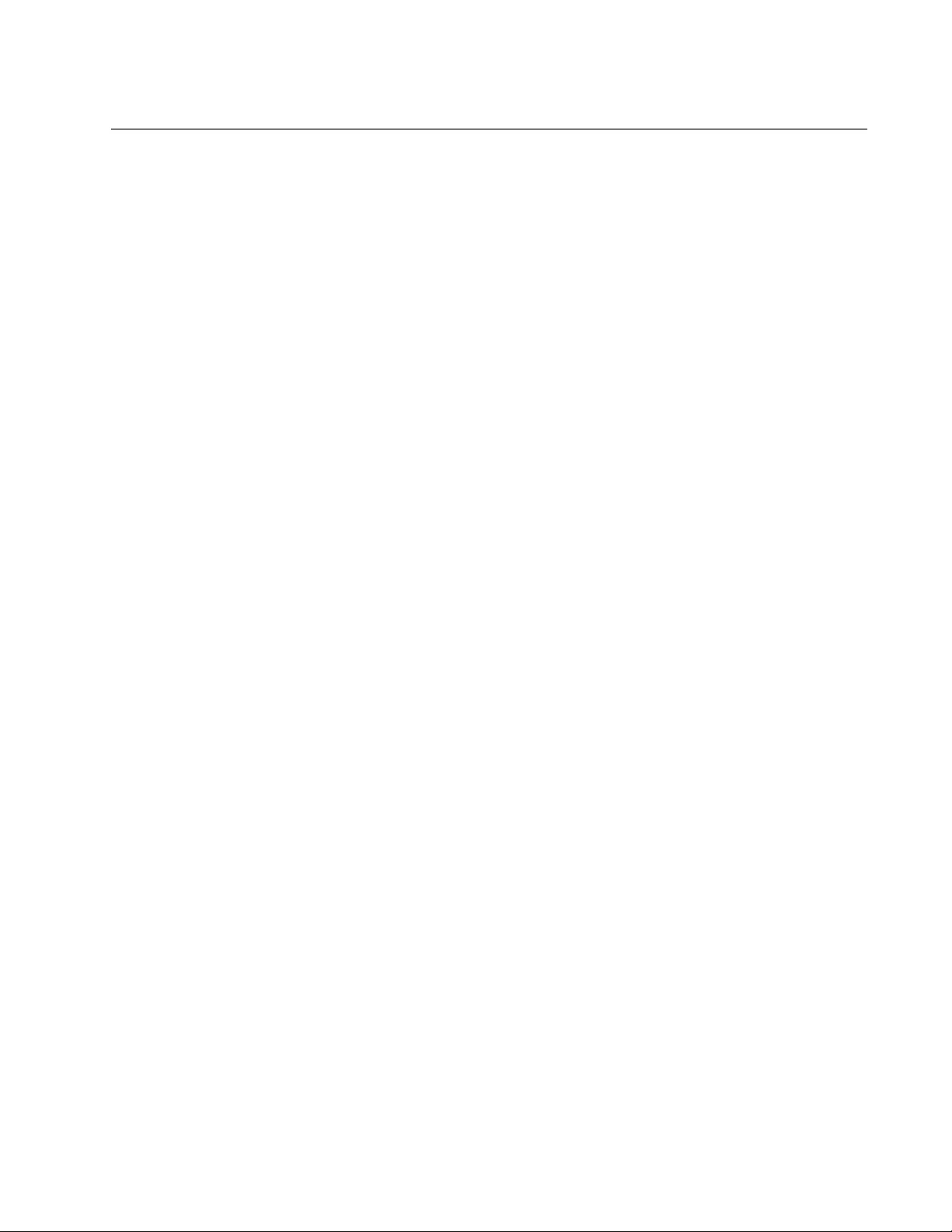
9
Figure 1: Front Panels of the x950 Switches........................................................................................................................20
Figure 2: Rear Panel of the x950 Switches ..........................................................................................................................21
Figure 3: Link and Activity LEDs for Ports for 1/2.5/5/10Gbps SFP/SFP+ Transceivers...................................................... 26
Figure 4: Link and Activity LEDs for Ports 1 to 24 on the x950-28XTQm Switch .................................................................28
Figure 5: QSFP-4SFP10G-3CU or QSFP-4SFP10G-5CU Copper Breakout Cable ............................................................30
Figure 6: ET3-MPO08-4LC-5 or ET3-MPO08-4LC-10 Fiber Optic Breakout Cable.............................................................30
Figure 7: LEDs for Ports 25, 29, 33, 37 on the x950-28XSQ and x950-28XTQm Switches.................................................30
Figure 8: LEDs for Ports 49, 53, 57, 61 on x950-52XSQ Switch..........................................................................................31
Figure 9: Management Panel for the x950-28XSQ and x950-28XTQm Switches................................................................34
Figure 10: Management Panel for the x950-52XSQ Switch.................................................................................................34
Figure 11: Switch ID LED with the eco-friendly Mode Disabled ...........................................................................................37
Figure 12: Switch ID LED with the eco-friendly Mode Enabled ............................................................................................37
Figure 13: PWR600 AC Power Supply .................................................................................................................................41
Figure 14: PWR600 DC Power Supply.................................................................................................................................43
Figure 15: LEDs for PWR600 DC Power Supply..................................................................................................................43
Figure 16: FAN05 Fan Module .............................................................................................................................................45
Figure 17: PORT Parameter in the Command Line Interface...............................................................................................46
Figure 18: Slot Numbers for Port Numbering .......................................................................................................................47
Figure 19: XEM2 Ethernet Line Cards..................................................................................................................................52
Figure 20: XEM2-8XSTm Line Card .....................................................................................................................................55
Figure 21: XEM2-12XT Line Card ........................................................................................................................................59
Figure 22: XEM2-12XTm Line Card .....................................................................................................................................61
Figure 23: XEM2-12XS Line Card ........................................................................................................................................63
Figure 24: XEM2-12XS and XEM2-12XS v2 Line Cards......................................................................................................64
Figure 25: XEM2-4QS Line Card..........................................................................................................................................66
Figure 26: XEM2-1CQ Line Card..........................................................................................................................................68
Figure 27: Example Stacks of x950-28XSQ Switches with Trunks of 10Gbps Ports ...........................................................76
Figure 28: Example Stacks of x950-28XTQm Switches with Trunks of 10Gbps Ports.........................................................77
Figure 29: Example Stack Trunks of 10Gbps Links on x950-28XSQ and x950-52XSQ Switches .......................................78
Figure 30: Stack Trunk Examples of Two Switches with Trunk 40Gbps Links.....................................................................79
Figure 31: Stack Trunk Examples of Three or Four Switches with 40Gbps Links................................................................80
Figure 32: Stack Trunk Examples with 100Gbps Links ........................................................................................................81
Figure 33: Example Trunk Using XEM2-12XT Line Cards ...................................................................................................83
Figure 34: Example Trunk Using XEM2-12XS Line Cards...................................................................................................83
Figure 35: Example Trunk Using XEM2-4QS Line Cards.....................................................................................................84
Figure 36: Unsupported Trunk with Different Numbers of Links Between Switches ............................................................84
Figure 37: Unsupported Trunk with Mixed Cables................................................................................................................85
Figure 38: Unsupported Trunk with Both Base and XEM2 Line Card Ports.........................................................................85
Figure 39: Unsupported Trunk of Connected Base and Line Card Ports .............................................................................85
Figure 40: Unsupported Trunk with Only One Link Between Switches ................................................................................86
Figure 41: Unsupported Trunk with Different Port Speeds...................................................................................................86
Figure 42: Not Recommended Stack Trunk of XEM2-1CQ Line Cards................................................................................87
Figure 43: Unsupported Trunk with a 10Gbps Breakout Cable............................................................................................87
Figure 44: Unsupported Trunk with Intermediary Network Devices .....................................................................................88
Figure 45: Installation Options ............................................................................................................................................103
Figure 46: Removing Accessories ......................................................................................................................................105
Figure 47: Removing the Shipping Partition .......................................................................................................................106
Figure 48: Lifting the Switch from the Shipping Box...........................................................................................................107
Figure 49: Removing the Switch from the Shipping End-caps and Protective Bag............................................................107
Figures
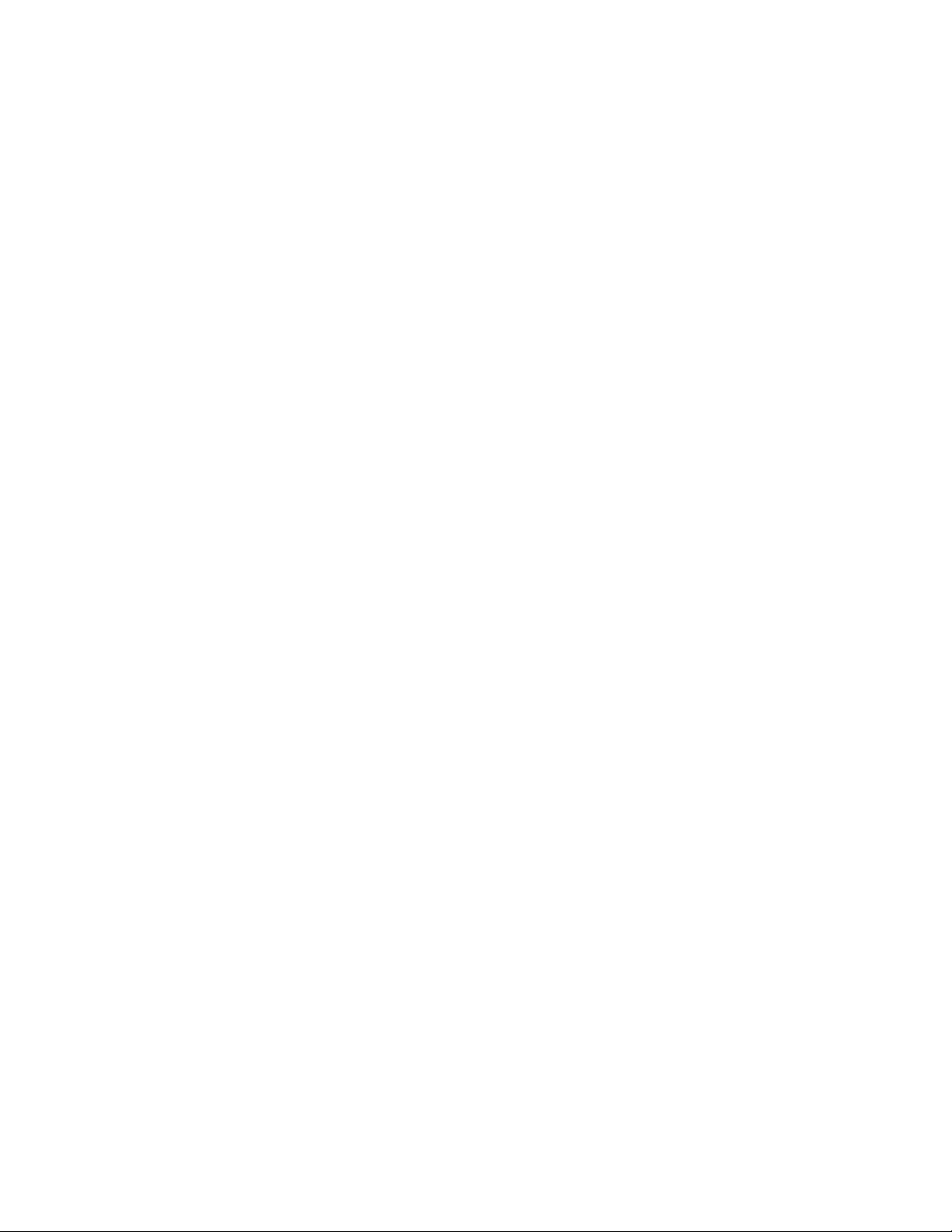
Figures
10
Figure 50: Accessory Kit .....................................................................................................................................................109
Figure 51: Removing the Power Cord and Documents from the PWR600 AC Power Supply............................................111
Figure 52: Removing the Partition from the PWR600 AC Power Supply Shipping Box .....................................................112
Figure 53: Removing the Power Supply from the Shipping Box.........................................................................................113
Figure 54: Removing the Power Supply from the Shipping End-caps and Protective Bag.................................................113
Figure 55: Removing the Blank Power Supply Panel from Slot PSU B..............................................................................117
Figure 56: Sliding the PWR600 AC Power Supply into the Switch.....................................................................................118
Figure 57: Seating the Power Supply on the Internal Connector........................................................................................119
Figure 58: Sliding the PWR600 DC Power Supply into the Chassis...................................................................................121
Figure 59: Stripping the Grounding Wire ............................................................................................................................123
Figure 60: Loosening the Screw for the Panel....................................................................................................................124
Figure 61: Accessing the Connectors .................................................................................................................................124
Figure 62: Loosening the Ground Screw ............................................................................................................................125
Figure 63: Wrapping the Grounding Wire and Tightening the Screw .................................................................................125
Figure 64: Stripping the Power Wire ...................................................................................................................................126
Figure 65: Wrapping the Wire Strands................................................................................................................................126
Figure 66: Loosening the Screw for the Negative (-) ..........................................................................................................127
Figure 67: Tightening the Screw for the Negative (-)..........................................................................................................127
Figure 68: Loosening the Screw for the Negative (+) .........................................................................................................128
Figure 69: Tightening the Screw for the Negative (+) .........................................................................................................128
Figure 70: Placing the Cover Panel ....................................................................................................................................129
Figure 71: Tightening the Screw for the Cover Panel.........................................................................................................129
Figure 72: Removing the Blank Line Card Cover ...............................................................................................................130
Figure 73: Removing the Ethernet Line Card from the Anti-static Bag ...............................................................................131
Figure 74: Sliding the Ethernet Line Card into the Slot.......................................................................................................131
Figure 75: Seating the Ethernet Line Card in the Expansion Slot.......................................................................................132
Figure 76: Tightening the Two Captive Screws on the Ethernet Line Card ........................................................................133
Figure 77: Parts of the Bumper Feet...................................................................................................................................135
Figure 78: Holes for Bumper Feet.......................................................................................................................................136
Figure 79: Inserting the Rivet Housing into the Bumper Foot.............................................................................................136
Figure 80: Placing the Bumper Foot on a Base Corner Hole..............................................................................................137
Figure 81: Inserting the Rivet into the Bumper Foot ...........................................................................................................137
Figure 82: Bracket Holes on the Switch..............................................................................................................................140
Figure 83: Switch Orientations in an Equipment Rack........................................................................................................141
Figure 84: Removing the Bumper Feet...............................................................................................................................142
Figure 85: Attaching the Equipment Rack Brackets ...........................................................................................................144
Figure 86: Installing the Switch in an Equipment Rack.......................................................................................................144
Figure 87: Positions of the Switch on the Wall....................................................................................................................148
Figure 88: Minimum Wall Area Dimensions with the Front Panel on the Left.....................................................................149
Figure 89: Minimum Wall Area Dimensions with the Front Panel on the Right ..................................................................150
Figure 90: Switch on the Wall with a Plywood Base...........................................................................................................151
Figure 91: Steps to Installing the Switch with a Plywood Base...........................................................................................152
Figure 92: Installing the Brackets to the Switch for Wall Installation...................................................................................156
Figure 93: Attaching the Switch to the Plywood Base ........................................................................................................157
Figure 94: Marking the Locations of the Bracket Holes on a Concrete Wall.......................................................................160
Figure 95: Installing the Switch on a Concrete Wall ...........................................................................................................161
Figure 96: Outer Rails.........................................................................................................................................................165
Figure 97: Inner Rails..........................................................................................................................................................165
Figure 98: Extension Brackets ............................................................................................................................................166
Figure 99: Shipping Container Contents.............................................................................................................................172
Figure 100: FRONT and REAR Labels on the Outer Rails.................................................................................................174
Figure 101: Installing the Outer Rails on the Equipment Rack ...........................................................................................175
Figure 102: Extension Brackets ..........................................................................................................................................176
Figure 103: Example of a Switch Recessed in an Equipment Rack...................................................................................176
Figure 104: Inserting an Inner Rail into an Outer Rail.........................................................................................................177
Figure 105: Example of Positioning the Inner Rail..............................................................................................................177
Figure 106: Measuring for the Extension Brackets.............................................................................................................177
Figure 107: Removing the Inner Rail ..................................................................................................................................178
Figure 108: Extension Bracket Parts ..................................................................................................................................178
Figure 109: Extension Bracket Configurations....................................................................................................................179
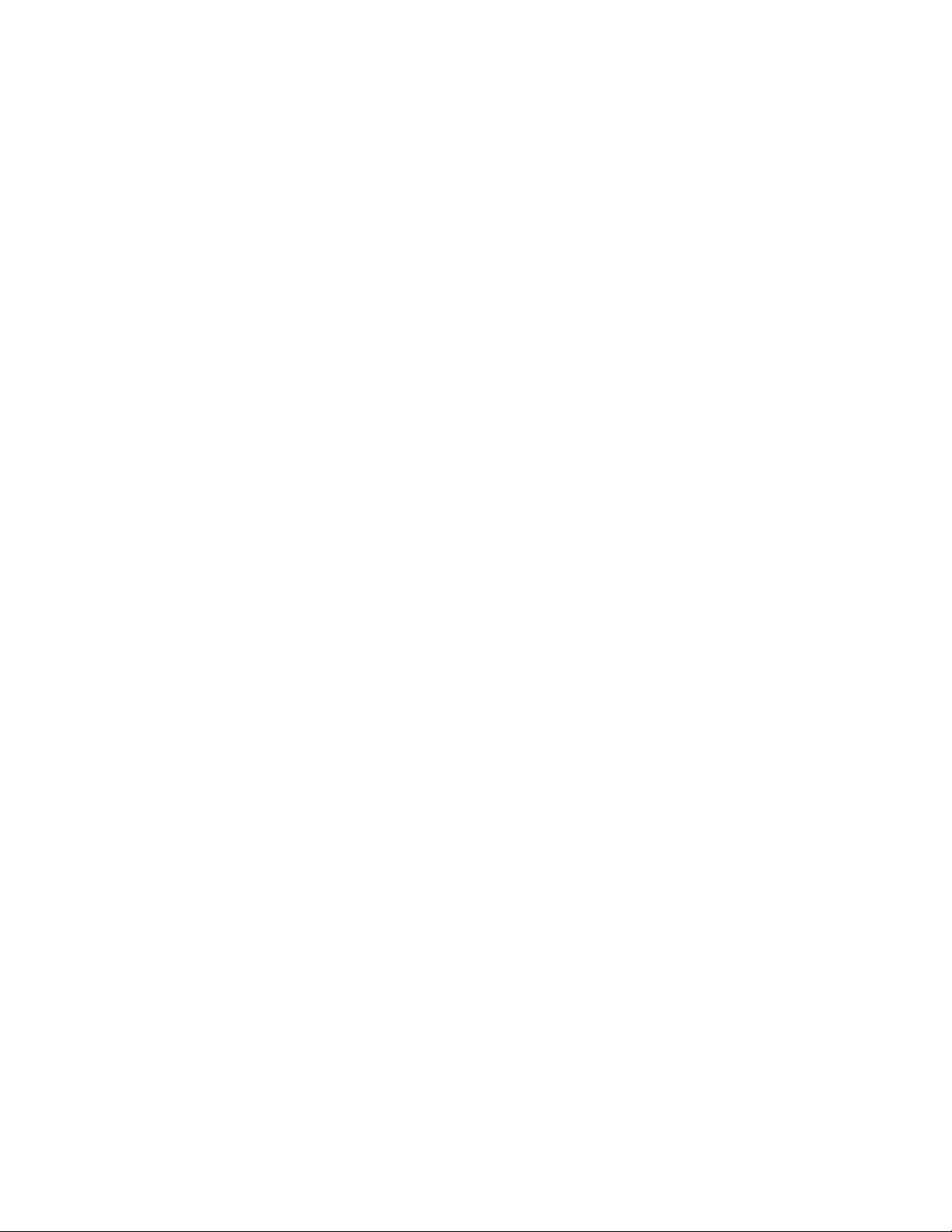
x950 Installation Guide for Virtual Chassis Stacking
11
Figure 110: Example of Attaching the Extension Brackets to the Inner Rails.....................................................................180
Figure 111: Testing the Inner Rails with the Extension Brackets .......................................................................................181
Figure 112: Verifying the Length of the Extension Bracket.................................................................................................181
Figure 113: Inner Rail Screw Holes for the x950-28XSQ and x950-28XTQm Switches ....................................................182
Figure 114: Inner Rail Screw Holes for the x950 Switch ....................................................................................................182
Figure 115: Attaching the Inner Rails to the x950 Switch...................................................................................................183
Figure 116: Sliding the Inner Rails on the Switch into the Outer Rails ...............................................................................184
Figure 117: Affixing the Warning Labels.............................................................................................................................185
Figure 118: Tightening the Two Screws on the Fixed Brackets .........................................................................................185
Figure 119: Tightening the Screws on the Outer Rails.......................................................................................................186
Figure 120: Connecting the AC Power Cord ......................................................................................................................192
Figure 121: Securing the Power Cord with the Restraining Strap ......................................................................................193
Figure 122: Connecting the Power Cord to an AC Power Source......................................................................................194
Figure 123: Connecting the Management Cable to the Console RS-232 Port ...................................................................196
Figure 124: User Exec Mode Prompt .................................................................................................................................197
Figure 125: Powering Off the AC Power Supply.................................................................................................................208
Figure 126: SHOW STACK Command...............................................................................................................................223
Figure 127: Handle on 100Gbps Transceivers for XEM2-1CQ Line Cards ........................................................................227
Figure 128: SP10T Transceivers ........................................................................................................................................229
Figure 129: Installing an SFP or SFP+ Transceiver ...........................................................................................................232
Figure 130: Installing 40Gbps Fiber Optic Transceivers in XEM2-4QS Line Cards ...........................................................232
Figure 131: Installing 100Gbps QSFP28 Transceivers in Base Ports 25, 29, 33, 37 .........................................................233
Figure 132: Installing 100Gbps QSFP28 Transceivers in XEM2-1CQ Line Cards.............................................................233
Figure 133: Installing SP10TW Direct Attach Cables .........................................................................................................235
Figure 134: Attaching QSFPCU Cables .............................................................................................................................236
Figure 135: Loosening the Screws on the Ethernet Line Card...........................................................................................239
Figure 136: Disconnecting an Ethernet Line Card from the Switch ....................................................................................240
Figure 137: Sliding an Ethernet Line Card from the Switch................................................................................................240
Figure 138: Placing the Ethernet Line Card in its Anti-static Bag.......................................................................................241
Figure 139: Installing the Line Card Blank Cover ...............................................................................................................241
Figure 140: Tightening the Two Screws on the Line Card Blank Panel .............................................................................242
Figure 141: Disconnecting the AC Power Cord from the Power Source ............................................................................243
Figure 142: Opening the Restraining Strap on the Power Supply......................................................................................244
Figure 143: Disconnecting the Power Cord from the Power Supply...................................................................................244
Figure 144: Removing the Power Supply ...........................................................................................................................245
Figure 145: Removing a Power Supply ..............................................................................................................................246
Figure 146: Installing the Blank Power Supply Cover.........................................................................................................247
Figure 147: Loosening the Screw for the Panel..................................................................................................................248
Figure 148: Accessing the Connecting Screws ..................................................................................................................249
Figure 149: Front Panel of the PWR600 DC Power Supply ...............................................................................................249
Figure 150: Front Panel of the PWR600 DC Power Supply ...............................................................................................250
Figure 151: Loosening the Screws on the Fan Module ......................................................................................................251
Figure 152: Disconnecting the FAN05 Module from the Switch .........................................................................................252
Figure 153: Sliding the Fan Module from the Switch..........................................................................................................252
Figure 154: Removing the Fan Module from the Shipping Container.................................................................................253
Figure 155: Aligning the FAN05 Module in the Switch Slot ................................................................................................254
Figure 156: Seating the FAN05 Module on the Internal Connector....................................................................................254
Figure 157: Tightening the Two Captive Screws on the FAN05 Module ............................................................................255
Figure 158: Switch Width and Height .................................................................................................................................264
Figure 159: Switch Depth and Locations of Bracket Holes.................................................................................................265
Figure 160: Pin Layout (Front View) of Twisted Pair Ports.................................................................................................278
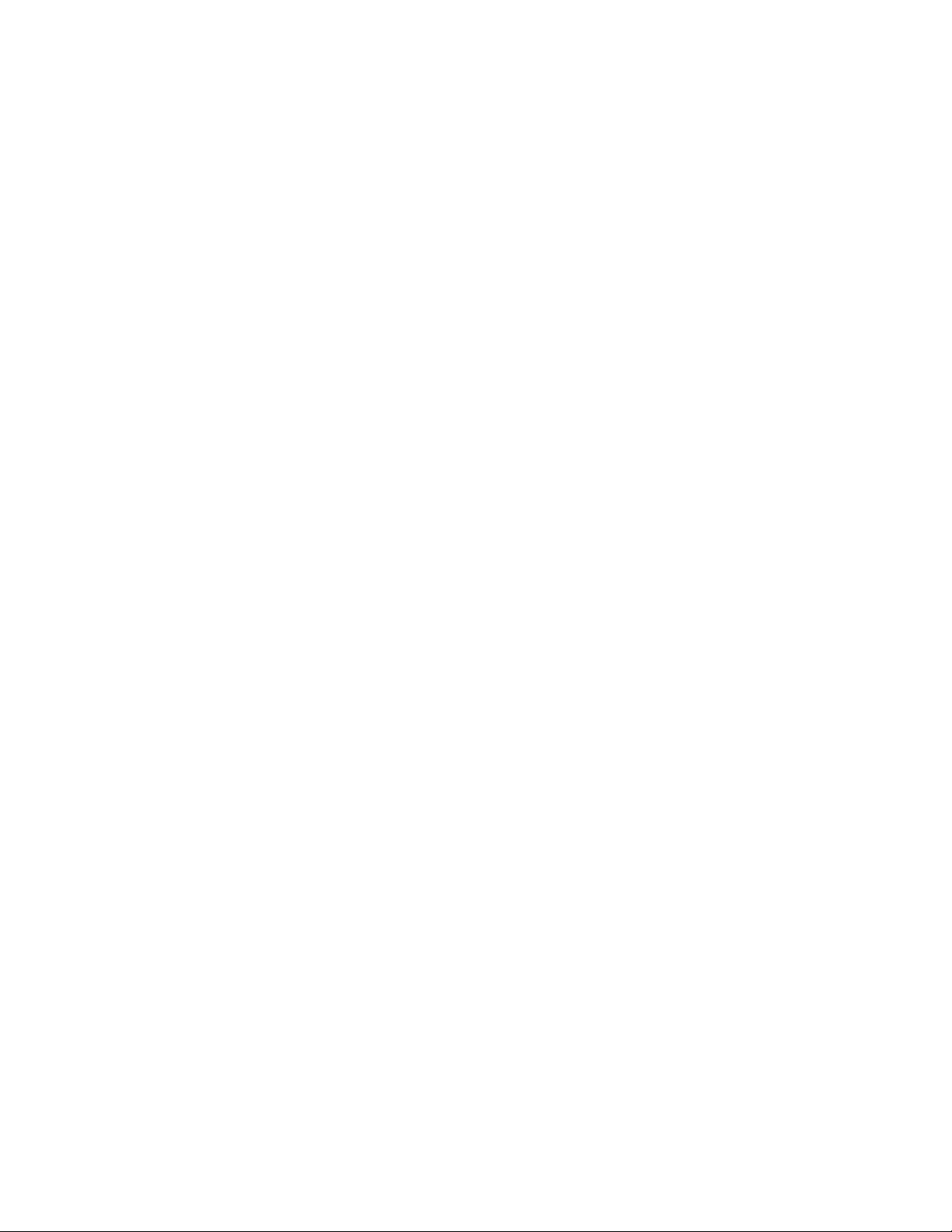
Figures
12
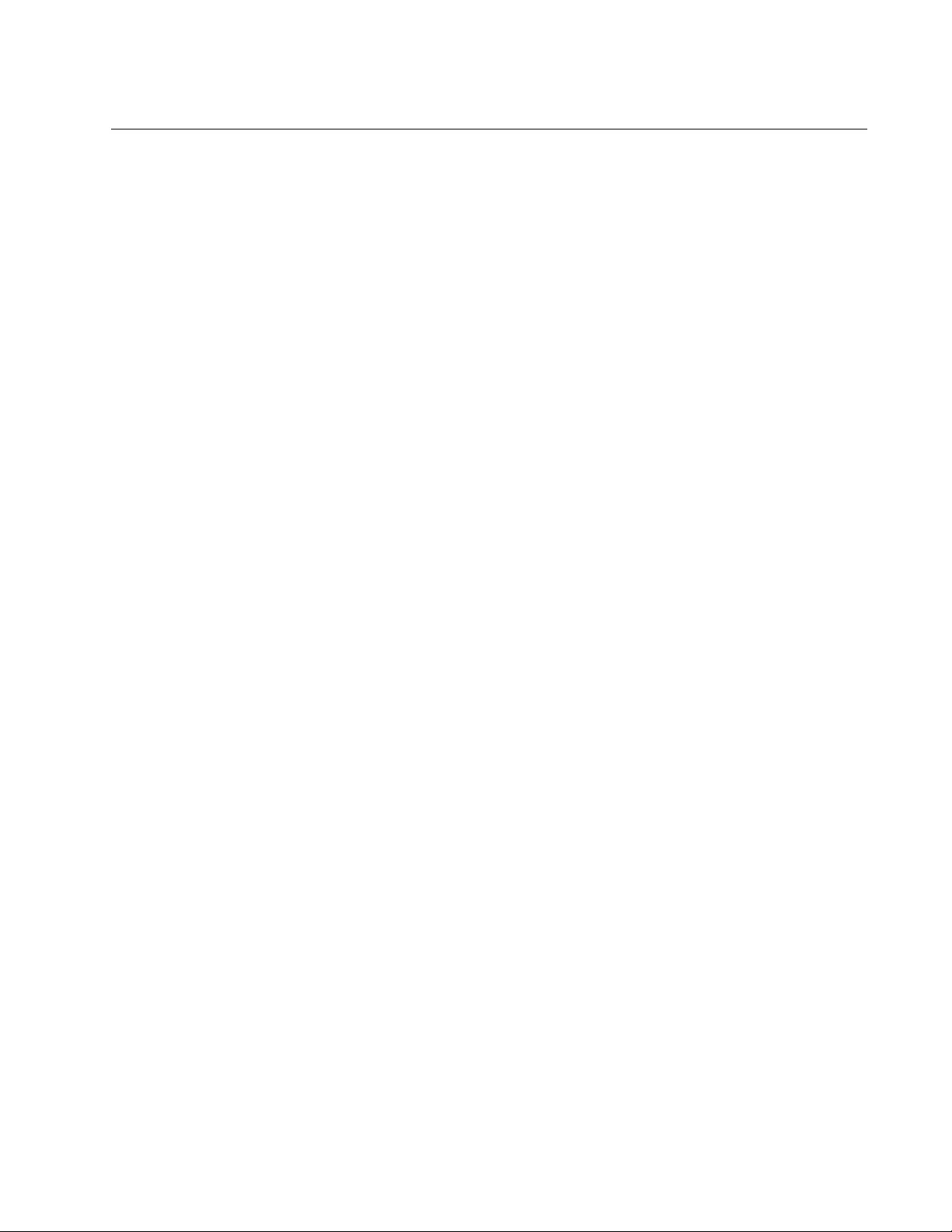
13
Tables
Table 1: Link and Activity Status LEDs for Ports for 1/2.5/5/10Gbps SFP/SFP+ Transceivers ...........................................26
Table 2: Twisted Pair Ports 1 to 24 on the x950-28XTQm Switch .......................................................................................27
Table 3: Link and Activity LEDs for Ports 1 to 24 on the x950-28XTQm Switch .................................................................28
Table 4: Ports for QSFP ......................................................................................................................................................29
Table 5: Link and Activity Status LEDs for 40Gbps QSFP+ or 100Gbps QSFP28 Transceivers ........................................31
Table 6: Link and Activity Status LEDs for 10Gbps Breakout Cables .................................................................................32
Table 7: Port Numbering for Ports 25 to 37 .........................................................................................................................32
Table 8: Port Numbering for Ports 49, 53, 57, and 61 .........................................................................................................33
Table 9: NET MGMT Port LED ............................................................................................................................................36
Table 10: Optional Direct Attach Cables ..............................................................................................................................39
Table 11: LEDs on the PWR600 AC Power Supply ............................................................................................................42
Table 12: LEDs on the PWR600 DC Power Supply ............................................................................................................43
Table 13: PORT Parameter Format .....................................................................................................................................46
Table 14: Software and Hardware Releases ......................................................................................................................49
Table 15: XEM2 Ethernet Line Cards ..................................................................................................................................53
Table 16: Twisted Pair Ports on the XEM2-8XSTm Line Card ............................................................................................55
Table 17: Link and Activity LEDs for the Twisted Pair Ports on the XEM2-8XSTm Line Card ............................................56
Table 18: Link and Activity LEDs for the SFP Ports on the XEM2-8XSTm Line Card .........................................................57
Table 19: Twisted Pair Ports on the XEM2-12XT Line Card ...............................................................................................59
Table 20: Port Link and Activity LEDs on the XEM2-12XT Line Card .................................................................................60
Table 21: Twisted Pair Ports on the XEM2-12XTm Line Card ............................................................................................61
Table 22: Link and Activity LEDs on the XEM2-12XTm Line Card ......................................................................................62
Table 23: Port Link and Activity LEDs on the XEM2-12XS Line Card .................................................................................64
Table 24: Port Link and Activity Status LEDs on the XEM2-4QS Line Card .......................................................................67
Table 25: Link and Activity Status LEDs for 10Gbps Breakout Cables ...............................................................................67
Table 26: Port Link and Activity Status LED on the XEM2-1CQ Line Card .........................................................................68
Table 27: Maximum Number of Trunk Ports Per Switch ......................................................................................................82
Table 28: Stacking Worksheet .............................................................................................................................................93
Table 29: Stacking Worksheet Columns ..............................................................................................................................94
Table 30: Example of a Completed Stack Worksheet .........................................................................................................96
Table 31: Extension Bracket Parts ....................................................................................................................................178
Table 32: Configuring the Master Switch - Part I ...............................................................................................................200
Table 33: Configuring the Master Switch- Part II ...............................................................................................................203
Table 34: Verifying the Master Switch ...............................................................................................................................206
Table 35: Configuring a Member Switch - Part I ................................................................................................................212
Table 36: Configuring a Member Switch - Part II ...............................................................................................................215
Table 37: Verifying a Member Switch ................................................................................................................................218
Table 38: Transceivers for the Base Transceiver Slots .....................................................................................................228
Table 39: Transceivers for XEM2 Ethernet Line Cards .....................................................................................................229
Table 40: Product Dimensions ...........................................................................................................................................264
Table 41: Product Weights ................................................................................................................................................265
Table 42: Ventilation Requirements ...................................................................................................................................266
Table 43: Environmental Specifications .............................................................................................................................267
Table 44: Maximum Power Consumptions (Watts) for the x950-28XSQ Switch ...............................................................268
Table 45: Maximum Power Consumptions (Watts) for the x950-28XTQm Switch ............................................................270
Table 46: Maximum Power Consumptions (Watts) for the x950-52XSQ Switch ...............................................................271
Table 47: Typical Power Savings in eco-friendly Mode (Watts) for the x950-28XSQ Switch ............................................272
Table 48: Typical Power Savings in eco-friendly Mode (Watts) for the x950-28XTQm Switch .........................................272
Table 49: Input Voltages ....................................................................................................................................................273
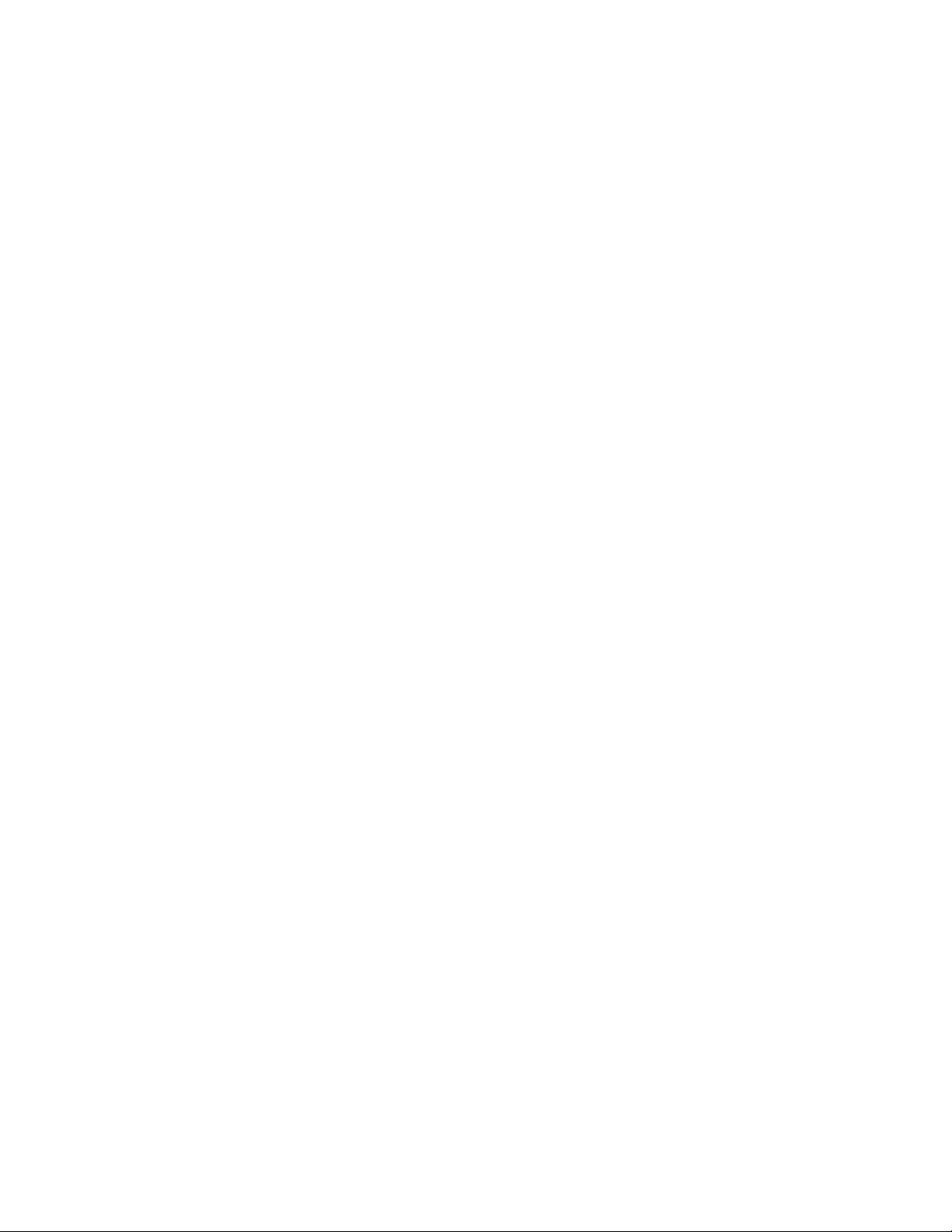
Tables
14
Table 50: Maximum Power Supply Efficiency (Based on 100V Input Voltage) ..................................................................273
Table 51: Heat Dissipations for the x950-28XSQ Switch ...................................................................................................273
Table 52: Heat Dissipations for the x950-28XTQm Switch ................................................................................................275
Table 53: Heat Dissipations for the x950-52XSQ Switch ...................................................................................................276
Table 54: Product Certifications .........................................................................................................................................277
Table 55: Pin Signals on RJ-45 Twisted Pair Ports at 100Mbps ......................................................................................278
Table 56: Pin Signals on Twisted Pair Ports at 1/2.5/5/10Gbps ........................................................................................279
Table 57: RJ-45 Style Serial Console Port Pin Signals .....................................................................................................280
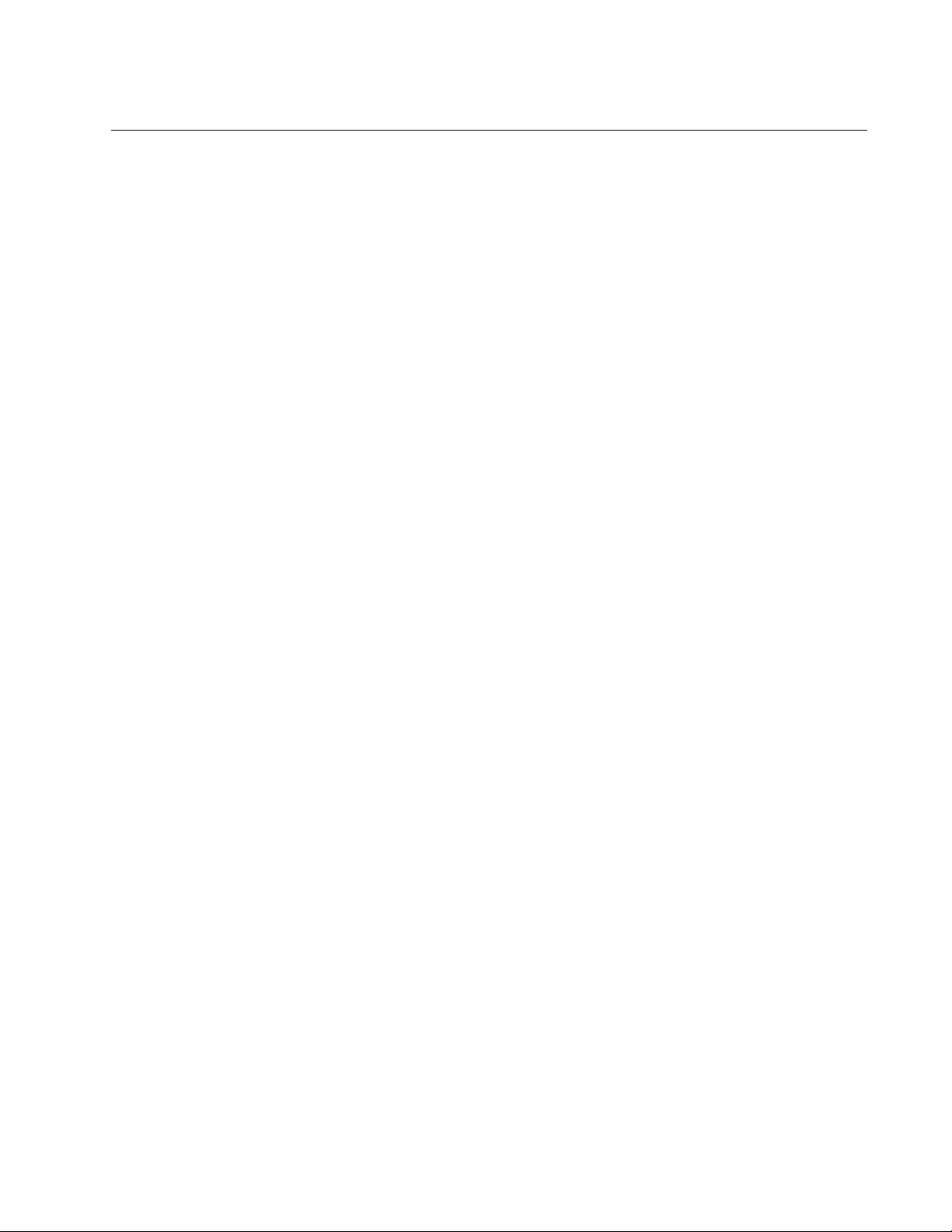
15
Preface
This guide contains the installation instructions for the x950 Series of
advanced Layer 3+ Ethernet switches. The instructions explain how to
build a virtual stack of up to four units with the Virtual Chassis Stacking
(VCStack) feature. For instructions on how to install the switches as stand-
alone devices, refer to the x950 Series Installation Guide for Stand-alone
Switches.
This preface contains the following sections:
“Document Conventions” on page 16
“Contacting Allied Telesis” on page 17
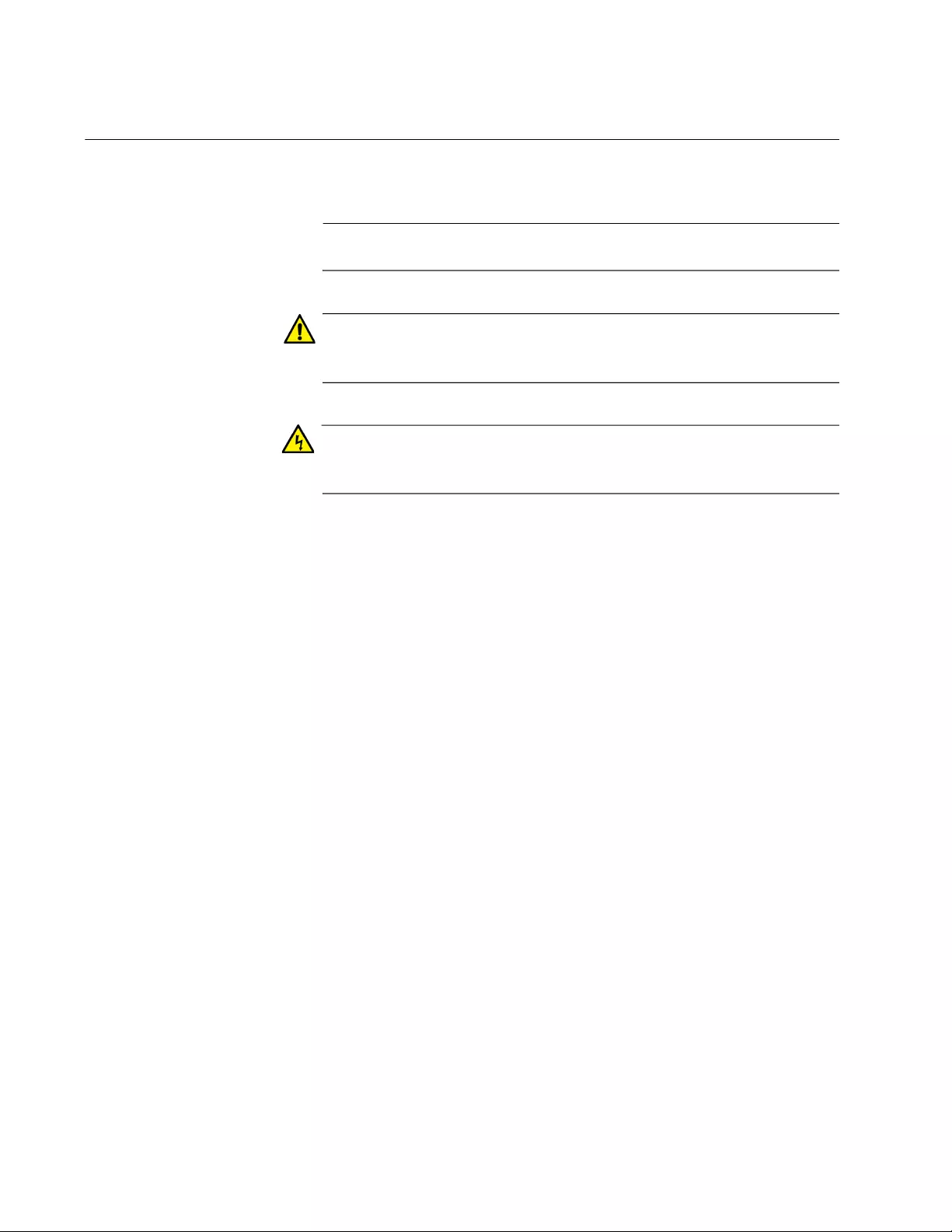
Preface
16
Document Conventions
This document uses the following conventions:
Note
Notes provide additional information.
Caution
Cautions inform you that performing or omitting a specific action
may result in equipment damage or loss of data.
Warning
Warnings inform you that performing or omitting a specific action
may result in bodily injury.
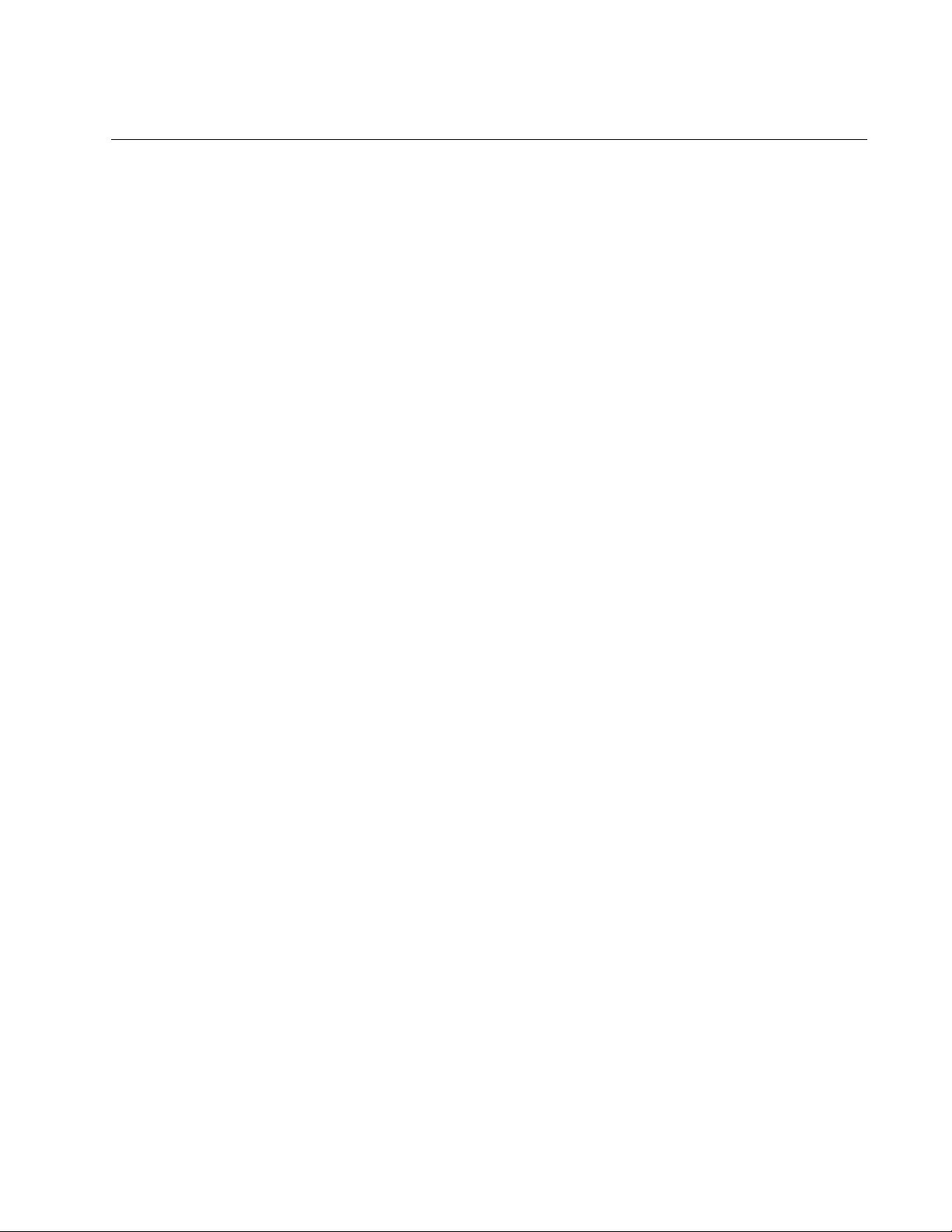
x950 Series Installation Guide for VCStack
17
Contacting Allied Telesis
For assistance with this product, you may contact Allied Telesis technical
support by going to the Support & Services section of the Allied Telesis
web site at www.alliedtelesis.com/support. The page has links to the
following services:
24/7 Online Support — Enter our interactive support center to
search for answers to your product questions in our knowledge
database, to check support tickets, to learn about RMAs, and to
contact Allied Telesis technical experts.
USA and EMEA phone support — Select the phone number that
best fits your location and customer type.
Hardware warranty information — Learn about Allied Telesis
warranties and register your product online.
Replacement Services — Submit a Return Merchandise
Authorization (RMA) request via our interactive support center.
Documentation — View the most recent installation and user
guides, software release notes, white papers, and data sheets for
your products.
Software Downloads — Download the latest software releases for
your managed products.
For sales or corporate information, go to www.alliedtelesis.com/contact
and select your region.
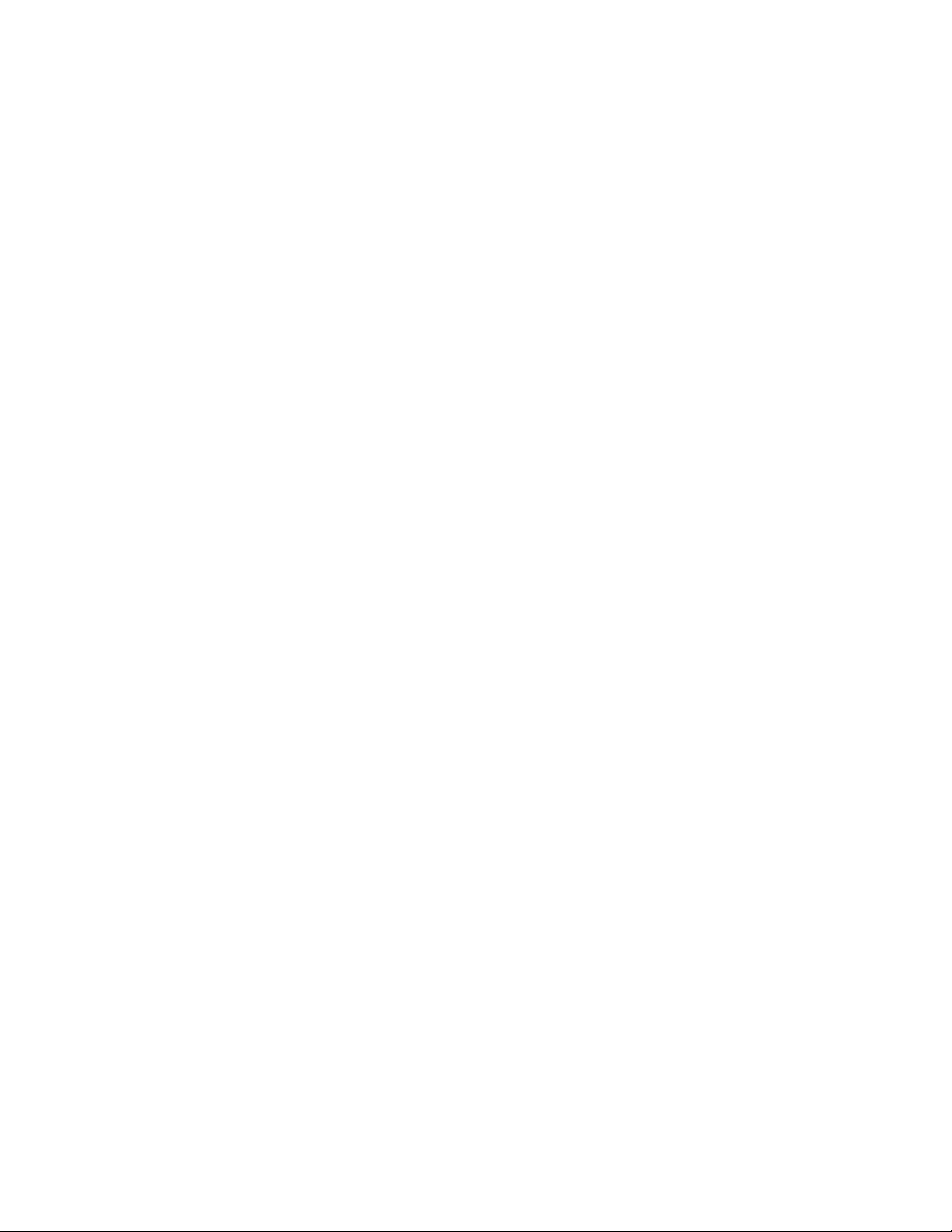
Preface
18

19
Chapter 1
Overview
The chapter contains the following sections:
“x950 Switches” on page 20
“Features” on page 22
“Ports for 1/2.5/5/10Gbps SFP/SFP+ Transceivers” on page 25
“Ports 1 to 24 on the x950-28XTQm Switch” on page 27
“Ports for 40Gbps QSFP+ or 100Gbps QSFP28 Transceiver, or
Breakout Cables” on page 29
“Management Panel” on page 34
“Optional Direct Attach Cables” on page 39
“PWR600 AC and DC Power Supplies” on page 40
“FAN05 Cooling Fan” on page 45
“Designating Ports in the Command Line Interface” on page 46
“Software and Hardware Releases” on page 49
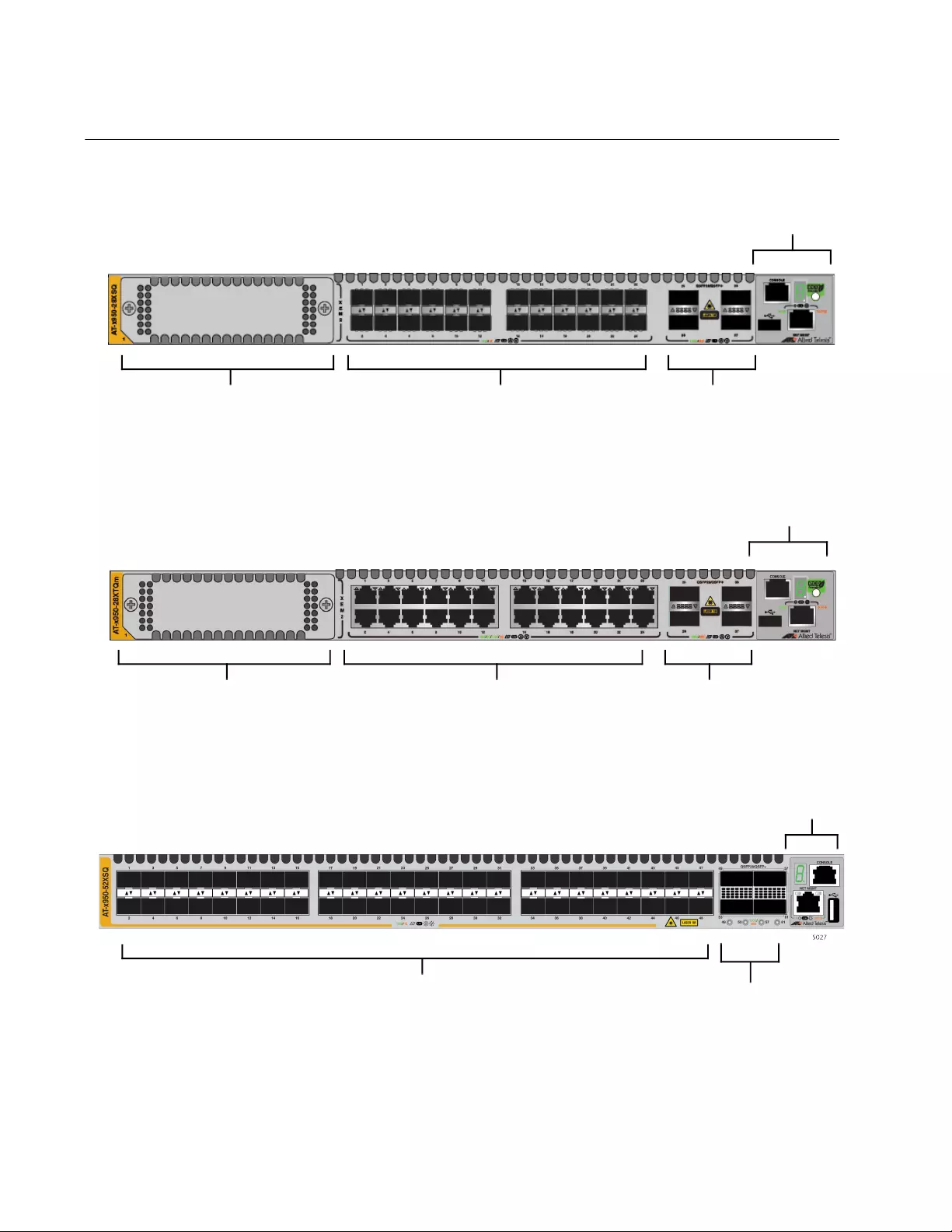
Chapter 1: Overview
20
x950 Switches
The front panels of the switches are shown in Figure 1.
Figure 1. Front Panels of the x950 Switches
XEM2 Line Card
Expansion Slot
Ports 25, 29, 33, 37:
40Gbps or 100Gbps
Transceivers, or
10Gbps Breakout Cables
Management Panel
Ports 1 to 24:
1/2.5/5/10 SFP/SFP+
Transceivers
XEM2 Line Card
Expansion Slot
Ports 25, 29, 33, 37:
40Gbps or 100Gbps
Transceivers, or
10Gbps Breakout Cables
Management Panel
Ports 1 to 24:
100Mbps, 1/2.5/5/10Gbps
Twisted Pair
x950-28XTQm Switch
x950-28XSQ Switch
x950-52XSQ Switch Management Panel
Ports 49, 53, 57, 61:
40Gbps or 100Gbps Transceivers,
or 10Gbps Breakout Cables
Ports 1 to 48:
1/2.5/5/10 SFP/SFP+
Transceivers
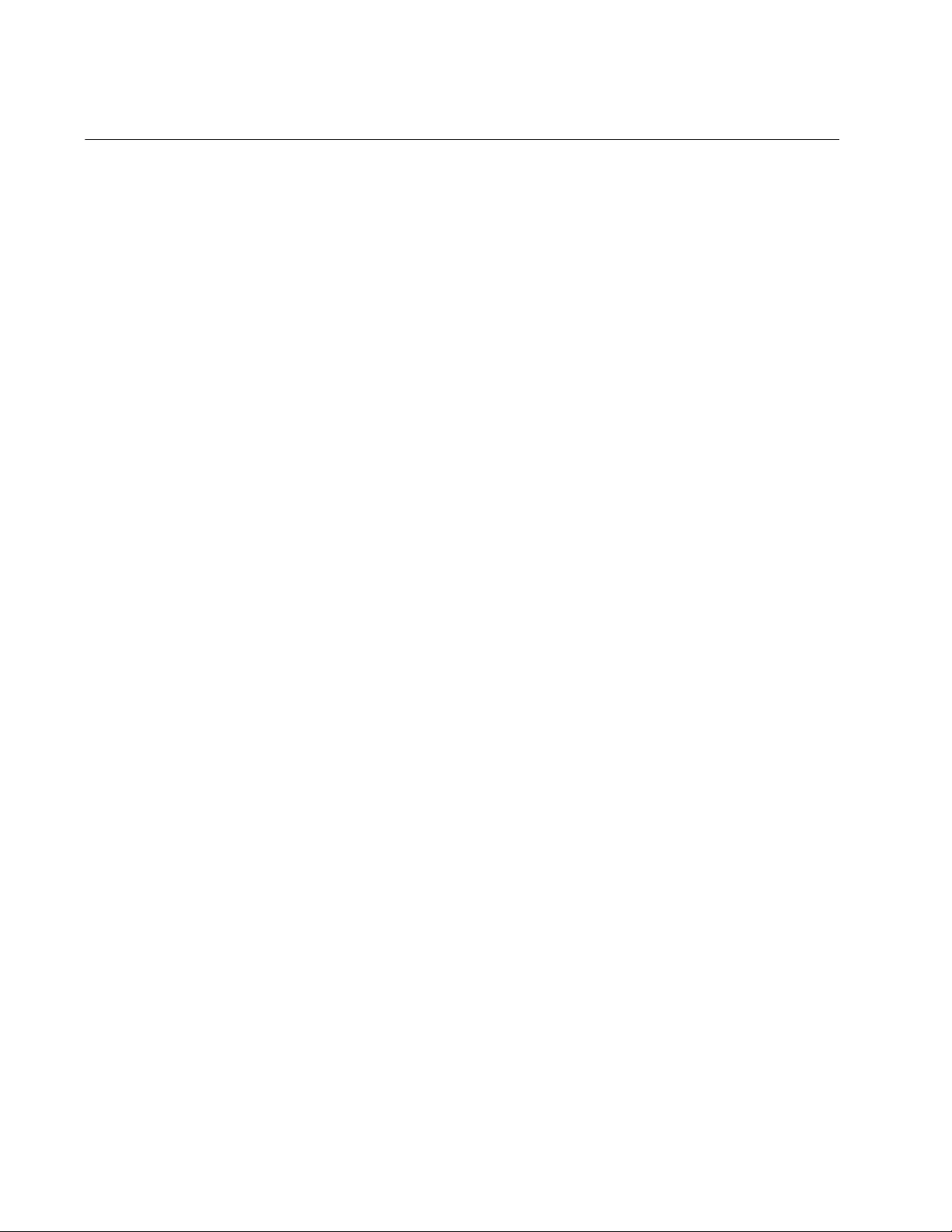
Chapter 1: Overview
22
Features
The main hardware features of the x950 Switches are listed here.
Hardware
Features
The switches have the following hardware features:
1RU height
24 ports on the x950-28XSQ Switch for 1Gbps SFP or 10Gbps
SFP+ transceivers. Refer to “Ports for 1/2.5/5/10Gbps SFP/SFP+
Transceivers” on page 25.
24 twisted pair ports on the x950-28XTQm Switch with speeds of
100Mbps and 1/2.5/5/10Gbps. Refer to “Ports 1 to 24 on the
x950-28XTQm Switch” on page 27.
48 ports on the x950-52XSQ Switch for 1Gbps SFP or 10Gbps
SFP+ transceivers. Refer to “Ports for 1/2.5/5/10Gbps SFP/SFP+
Transceivers” on page 25.
Four ports for 40Gbps QSFP+ or 100Gbps QSFP28 transceivers,
or 10Gbps breakout cables. Refer to “Ports for 40Gbps QSFP+ or
100Gbps QSFP28 Transceiver, or Breakout Cables” on page 29.
One expansion slot on the x950-28XSQ and x950-28XTQm
switches for an optional XEM2 Ethernet line card. Refer to Chapter
2, “XEM2 Ethernet Line Cards” on page 51.
The switches supports two power supplies for primary and
redundant power. Refer to “PWR600 AC and DC Power Supplies”
on page 40.
The units come with two pre-installed fan modules. Refer to
“FAN05 Cooling Fan” on page 45.
The switches come with brackets for standard 19-inch equipment
racks or wall installation.
The XEM2 Ethernet line cards, power supplies, and fan modules
are hot-swappable.
XEM2 Ethernet
Line Cards
The XEM2 Ethernet line cards are listed here:
XEM2-8XSTm Card features four 100Mbps and 1/2.5/5/10Gbps
twisted pair ports with RJ-45 connectors and four ports for 1Gbps
SFP or 10Gbps SFP+ transceivers. Refer to “XEM2-8XSTm Line
Card” on page 55.
XEM2-12XT Card features 12 twisted pair ports with speeds of
100Mbps and 1/10Gbps, and RJ-45 connectors. Refer to
“XEM2-12XT Line Card” on page 59.
XEM2-12XTm Card features 12 twisted pair ports with speeds of
100Mbps and 1/2.5/5/10Gbps, and RJ-45 connectors. Refer to
“XEM2-12XTm Line Card” on page 61.
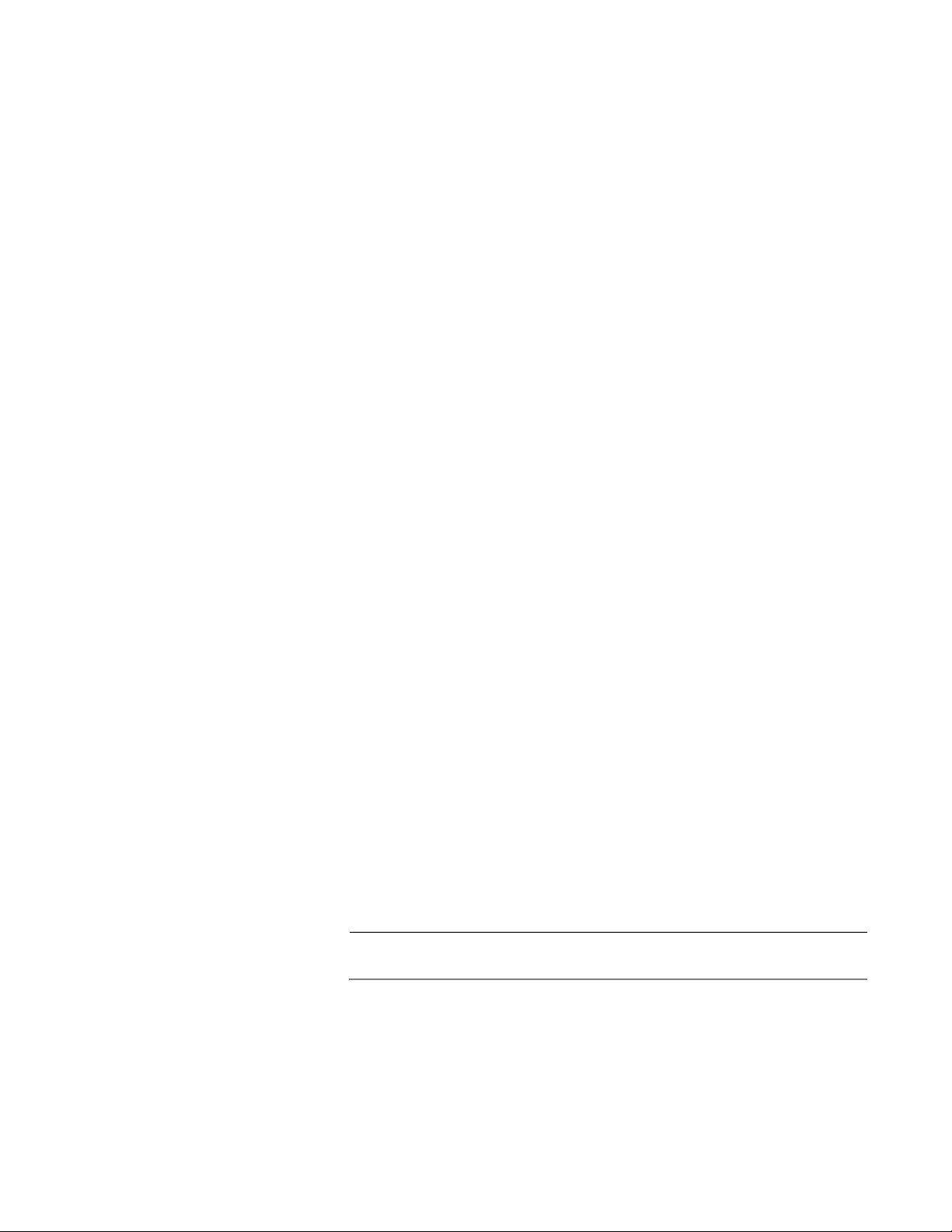
x950 Series Installation Guide for VCStack
23
XEM2-12XS and XEM2-12XS v2 Cards feature 12 ports for 1Gbps
SFP or 10Gbps SFP+ transceivers. Refer to “XEM2-12XS and
XEM2-12XS v2 Line Cards” on page 63.
XEM2-4QS Card features four ports for 40Gbps QSFP+
transceivers. Refer to “XEM2-4QS Line Card” on page 66.
XEM2-1CQ Card features one port for the 100Gbps QSFP28
transceiver. Refer to “XEM2-1CQ Line Card” on page 68.
Line cards are ordered separately. Refer to the product data sheet on the
Allied Telesis web site for a list of approved transceivers.
Management
Software and
Interfaces
Here are the management software and interfaces:
AlliedWare Plus management software.
Command line interface, available locally through the Console port
or remotely over the network.
Web browser interface available remotely over the network.
The AlliedWare Plus management software comes pre-installed on the
switch.
Management
Methods
You can manage the switch as follows:
Command line interface accessed locally through the Console port
or remotely using Telnet or Secure Shell.
Remote access using the web browser interface and HTTP.
Remote access with SNMPv1, v2c, or v3.
Management
Panel
The management panel has the following features:
Console RS-232 port for local management (no IP address
required).
USB 2.0 port for storing backup copies of system configuration
files, updating management software, and other management
functions.
An eco-friendly button for turning off the port and system LEDs to
reduce power consumption.
Note
The x950-52XSQ switch does not have the eco-friendly button.
Network management port for initial configuration and
maintenance access to the chassis.
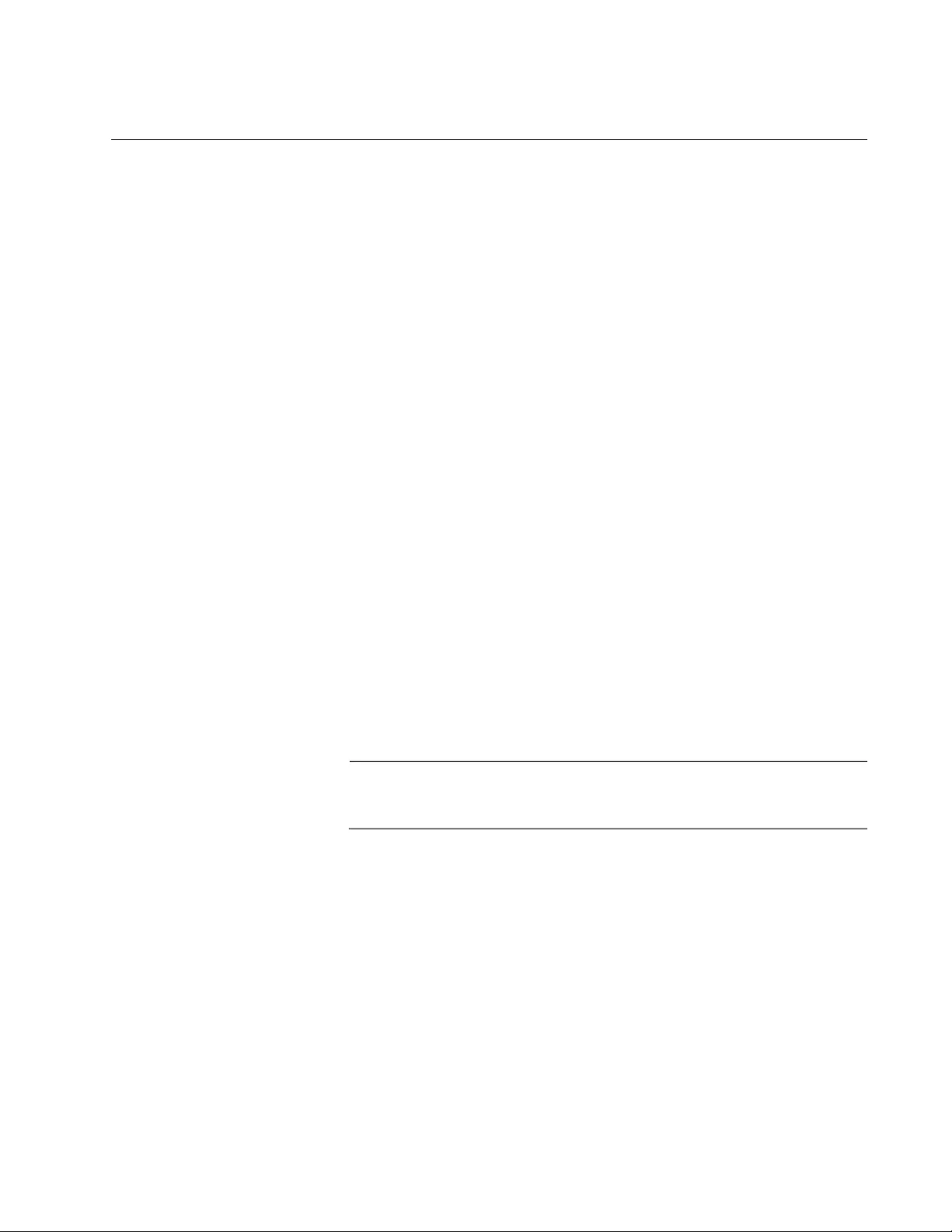
x950 Series Installation Guide for VCStack
25
Ports for 1/2.5/5/10Gbps SFP/SFP+ Transceivers
Ports 1 to 24 on the x950-28XSQ switch and ports 1 to 48 on the
x950-52XSQ switch support 1Gbps, 2.5Gbps, 5Gbps, and 10Gbps
SFP/SFP+ transceivers.
SFP and SFP+
Transceivers
Listed here are examples of 1Gbps SFP transceivers:
SPSX and LR short and long distance transceivers using
multi-mode or single mode fiber optic cable.
SPTX transceiver series with RJ-45 connector for twisted pair
cable.
SPEX transceivers with a maximum distance of two kilometers with
multi-mode fiber optic cable.
Listed here are examples of SFP+ 10Gbps transceivers:
SP10SR, LR, ER and ZR series of short or long distance
transceivers using multi-mode or single mode fiber optic cable.
SP10TW series of direct attach cables in lengths up to seven
meters.
SP10BD series of bidirectional transceivers for single mode fiber
optic cable with maximum distances of 10 to 40 kilometers
SP10T transceiver with RJ-45 connector for links up to 20 meters
at 10Gbps with Category 6a twisted pair cable, or 100 meters at
1Gbps.
SP10LRM Long Reach Multimode transceiver for OM1 multi-mode
fiber optic links up to 220 meters.
Note
Industrial (-40 to 85° C) and extended (-40 to 105° C) temperature
transceivers are available.
Here are transceiver guidelines:
The ports do not support 100Mbps-FX transceivers.
They support full-duplex mode only.
You can set the port speeds with Auto-Negotiation or manually.
The default is Auto-Negotiation.
Transceivers must be purchased separately. For a list of supported
transceivers, refer to the product data sheet on the Allied Telesis web site.
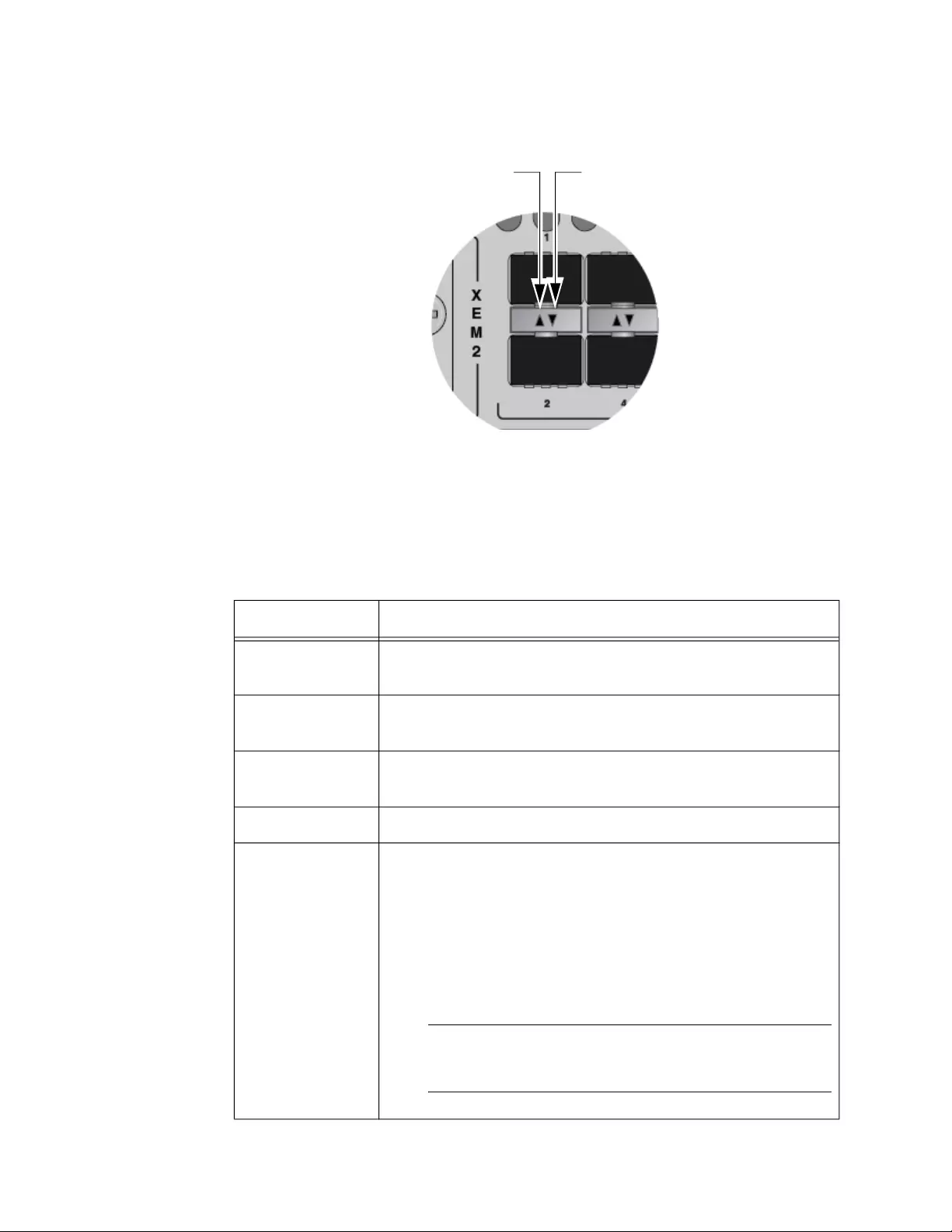
Chapter 1: Overview
26
LEDs The LEDs are located between the ports. Each port has one LED. Refer to
Figure 3.
Figure 3. Link and Activity LEDs for Ports for 1/2.5/5/10Gbps SFP/SFP+
Transceivers
The LEDs displays link and activity status. The possible LED states are
described in Table 1.
Top Transceiver Slot LED Bottom Transceiver Slot LED
Table 1. Link and Activity Status LEDs for Ports for 1/2.5/5/10Gbps SFP/SFP+
Transceivers
State Description
Solid Green The transceiver has established a 2.5Gbps, 5Gbps, or
10Gbps link to a network device.
Flashing Green The transceiver is transmitting or receiving data in
2.5Gbps, 5Gbps, or 10Gbps.
Solid Amber The transceiver has established a 1Gbps link to a network
device.
Flashing Amber The transceiver is transmitting or receiving data in 1Gbps.
Off Possible causes of this state are listed here:
- The slot is empty.
- The transceiver has not established a link to a network
device.
- The LEDs are turned off. To turn on the LEDs, use the
eco-friendly button in the management panel.
Note
The x950-52XSQ switch does not have the
eco-friendly button.
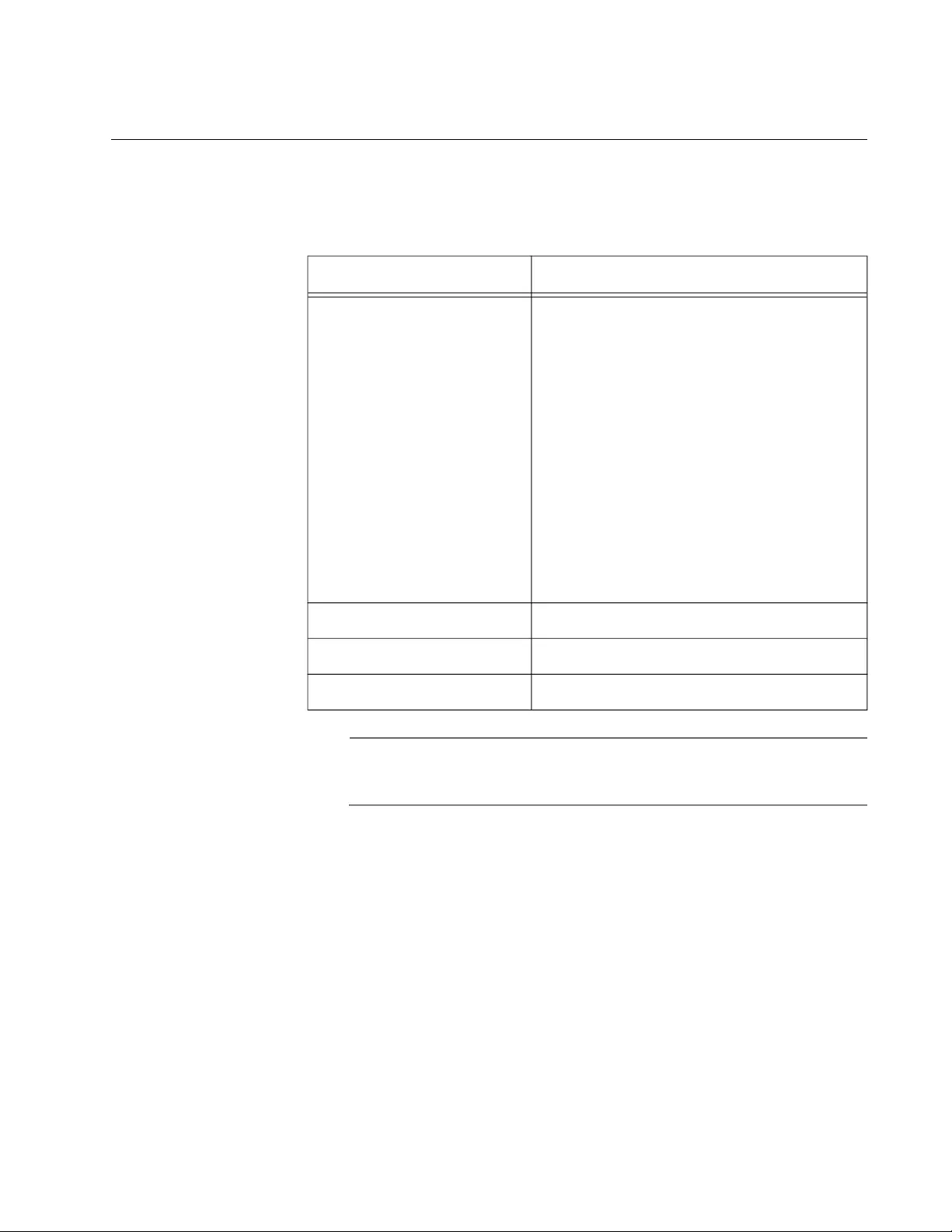
x950 Series Installation Guide for VCStack
27
Ports 1 to 24 on the x950-28XTQm Switch
The specifications for twisted pair ports 1 to 24 on the x950-28XTQm
Switch are listed in Table 2.
Note
Network devices connected to the ports must be IEEE 802.3u
compliant.
Cable
Requirements
The cable requirements are listed here:
100Mbps - Standard TIA/EIA 568-B-compliant Category 3
unshielded cabling.
1/2.5/5Gbps - Standard TIA/EIA 568-A-compliant Category 5 or
TIA/EIA 568-B-compliant Enhanced Category 5 (Cat 5e)
unshielded cabling.
10Gbps -Standard TIA/EIA 568-C-compliant Category 6a
unshielded cabling.
Table 2. Twisted Pair Ports 1 to 24 on the x950-28XTQm Switch
Specification Description
Port Speed Here are the supported speeds:
- 100Mbps
- 1/2.5/5/10Gbps
Here are the guidelines to setting port
speeds:
- 100Mbps can be set manually or with
Auto-Negotiation.
- 1/2.5/5/10Gbps require
Auto-Negotiation.
The default port setting is
Auto-Negotiation.
Duplex Mode Full-duplex only
Maximum Distance 100 meters (328 feet)
Connector 8-pin RJ-45
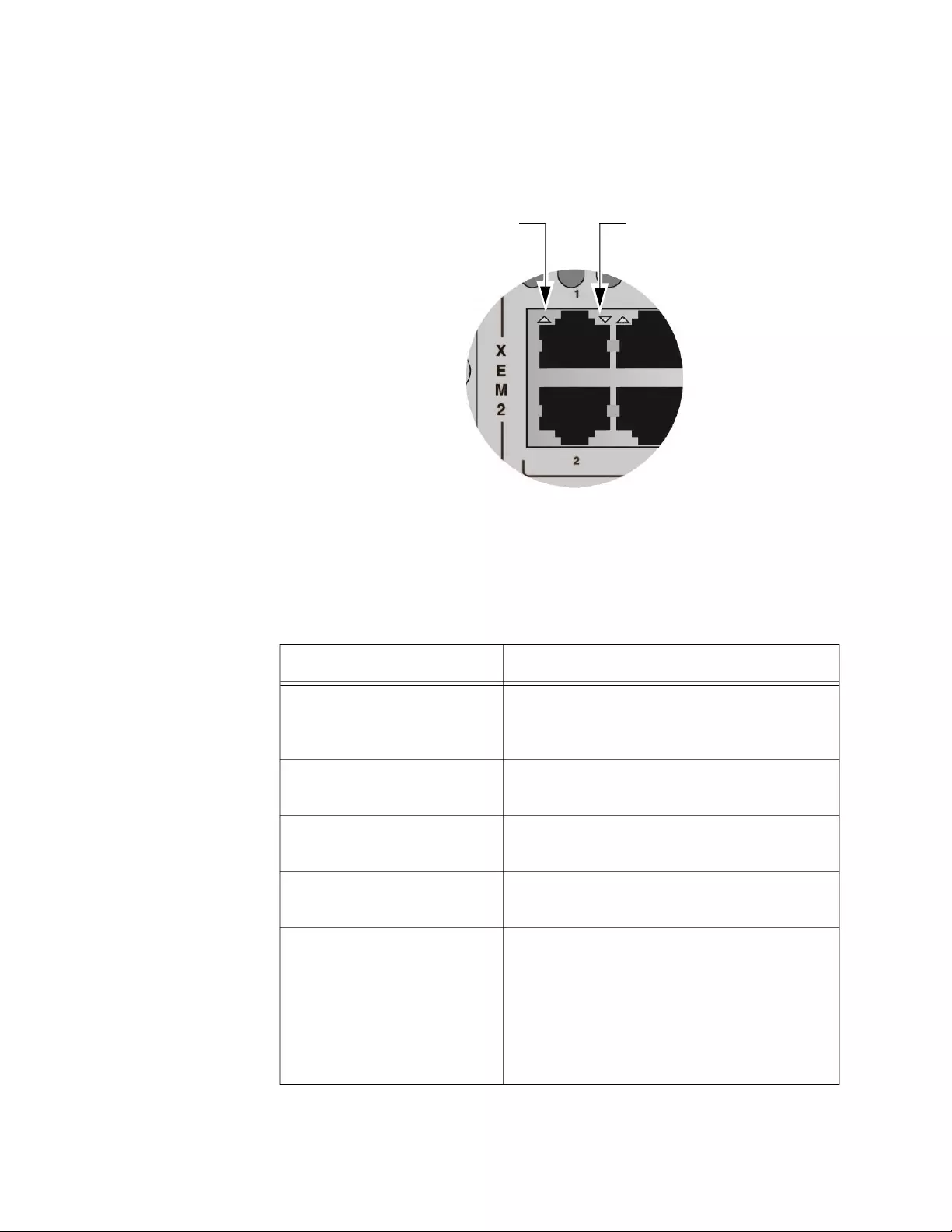
Chapter 1: Overview
28
LEDs This section explains the LEDs for the 100Mbps and 1/2.5/5/10Gbps
twisted pair ports on the x950-28XTQm Switch. Each port has one LED
that displays link and activity information. The LEDs are shown in
Figure 4.
Figure 4. Link and Activity LEDs for Ports 1 to 24 on the x950-28XTQm
Switch
The states of the link and activity LEDs are described in Table 3.
Table 3. Link and Activity LEDs for Ports 1 to 24 on the x950-28XTQm
Switch
State Description
Solid Green The port has established a 2.5Gbps,
5Gbps, or 10Gbps link to a network
device.
Flashing Green The port is transmitting or receiving data
at 2.5Gbps, 5Gbps or 10Gbps.
Solid Amber The port has established a 100Mbps or
1Gbps link to a network device.
Flashing Amber The port is transmitting or receiving data
at 100Mbps or 1Gbps.
Off Possible causes of this state are listed
here:
- The port has not established a link with
another network device.
- The LEDs are turned off. To turn on the
LEDs, use the eco-friendly button.
Top Port LED Bottom Port LED
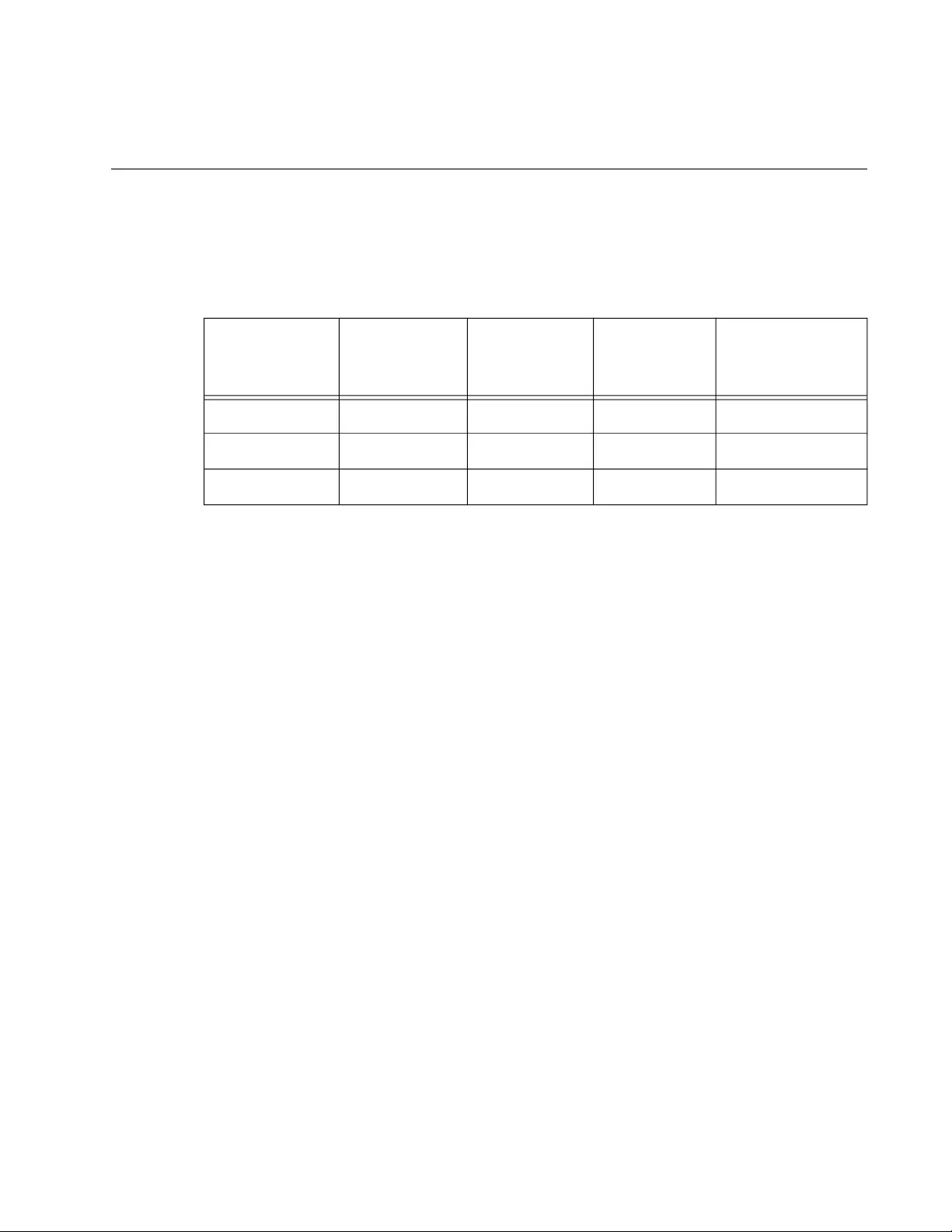
x950 Series Installation Guide for VCStack
29
Ports for 40Gbps QSFP+ or 100Gbps QSFP28 Transceiver, or
Breakout Cables
The x950 series switch has four ports that support the transceivers and
cables listed in Table 4.
QSFP28
Transceivers
The ports support the following 100Gbps QSFP28 transceivers:
QSFP28SR4 transceiver - Maximum operating distance of 70m
(230 ft) or 100m (328 ft) with 12-strand OM3 or OM4 fiber optic
cable, respectively. Requires an MPO pluggable optical connector.
QSFP28LR4 transceiver - Operating range of 2m (6.6 ft) to 10km
(6.2 mi) with single-mode fiber optic cable. Requires a duplex LC
connector.
QSFP28-1CU and QSFP28-3CU direct attach cables - Lengths of
one and three meters, respectively.
QSFP+
Transceivers
The ports support the following 40Gbps QSFP+ transceivers:
QSFPSR4 transceiver - Maximum operating distance of 150m (492
ft) with 12-strand OM4 fiber optic cable.
QSFPLR4 transceiver - Maximum operating distance of 2m (6.6 ft)
to 10km (6.2 mi) with single-mode fiber optic cable.
QSFP1CU and QSFP3CU direct attach cables - Lengths of 1 and 3
meters, respectively.
Breakout Cables The ports also support copper and fiber optic breakout cables. The cables
convert them from 40Gbps ports to four SFP+ 10Gbps ports. The model
names of the copper cables are QSFP-4SFP10G-3CU and
QSFP-4SFP10G-5CU. The cables are in lengths of 3 and 5 meters,
respectively. Refer to Figure 5 on page 30.
Table 4. Ports for QSFP
Port number
40Gbps
QSFP+
transceivers
100Gbps
QSFP28
transceivers
40Gbps to
10Gbps
breakout cables
x950-28XSQ 25, 29, 33, 37 Yes Yes Yes
x950-28XTQm 25, 29, 33, 37 Yes Yes Yes
x950-52XSQ 49, 53, 57, 61 Yes Yes Yes
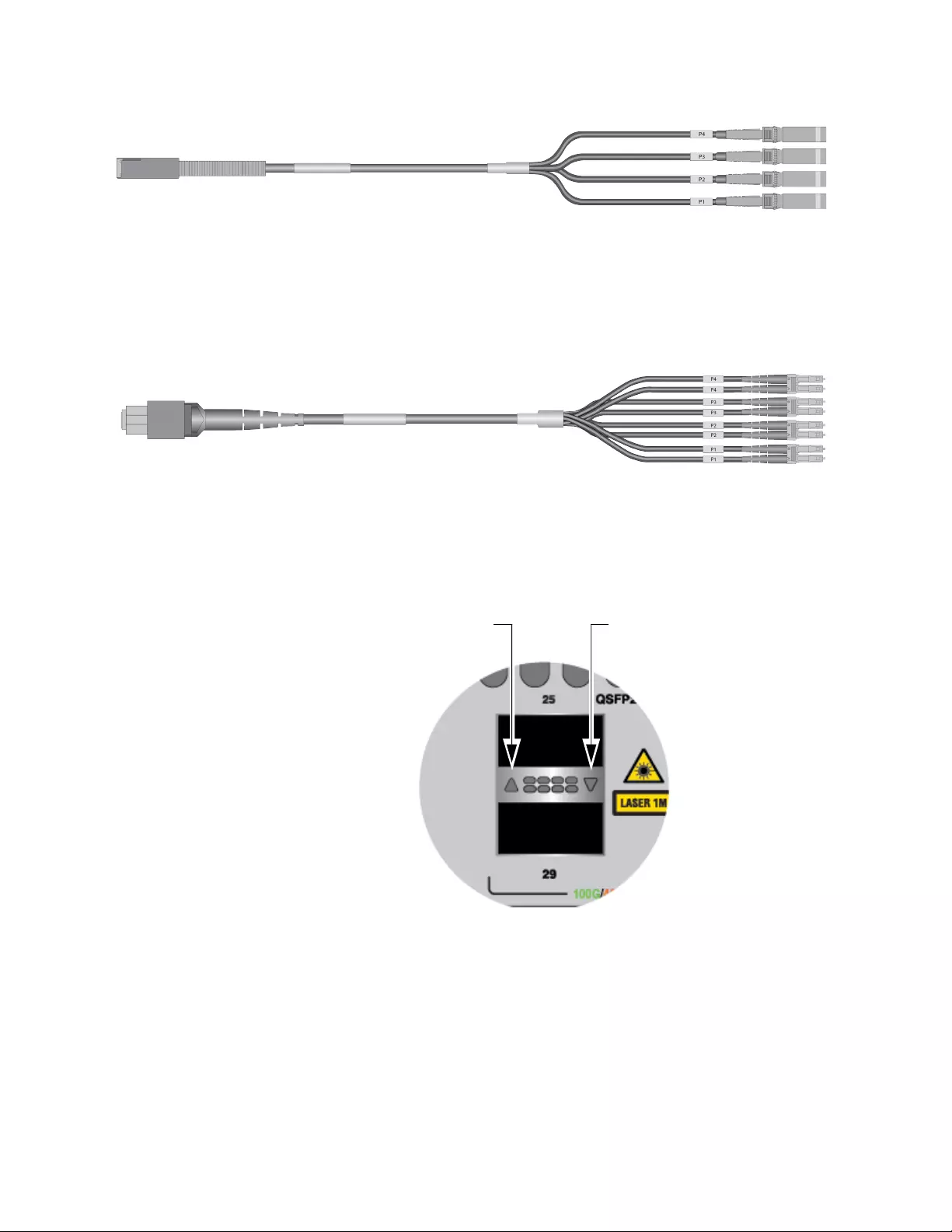
Chapter 1: Overview
30
Figure 5. QSFP-4SFP10G-3CU or QSFP-4SFP10G-5CU Copper
Breakout Cable
The fiber optic breakout cables are ET3-MPO08-4LC-5 and
ET3-MPO08-4LC-10, in lengths of 5 and 10 meters, respectively, with
duplex LC connectors. Refer to Figure 6.
Figure 6. ET3-MPO08-4LC-5 or ET3-MPO08-4LC-10 Fiber Optic
Breakout Cable
LEDs The ports for the QSFP28 and QSFP+ transceivers have one link and
activity status LED each. Refer to Figure 7.
Figure 7. LEDs for Ports 25, 29, 33, 37 on the x950-28XSQ and
x950-28XTQm Switches
Top Transceiver Slot
LED
Bottom Transceiver Slot
LED
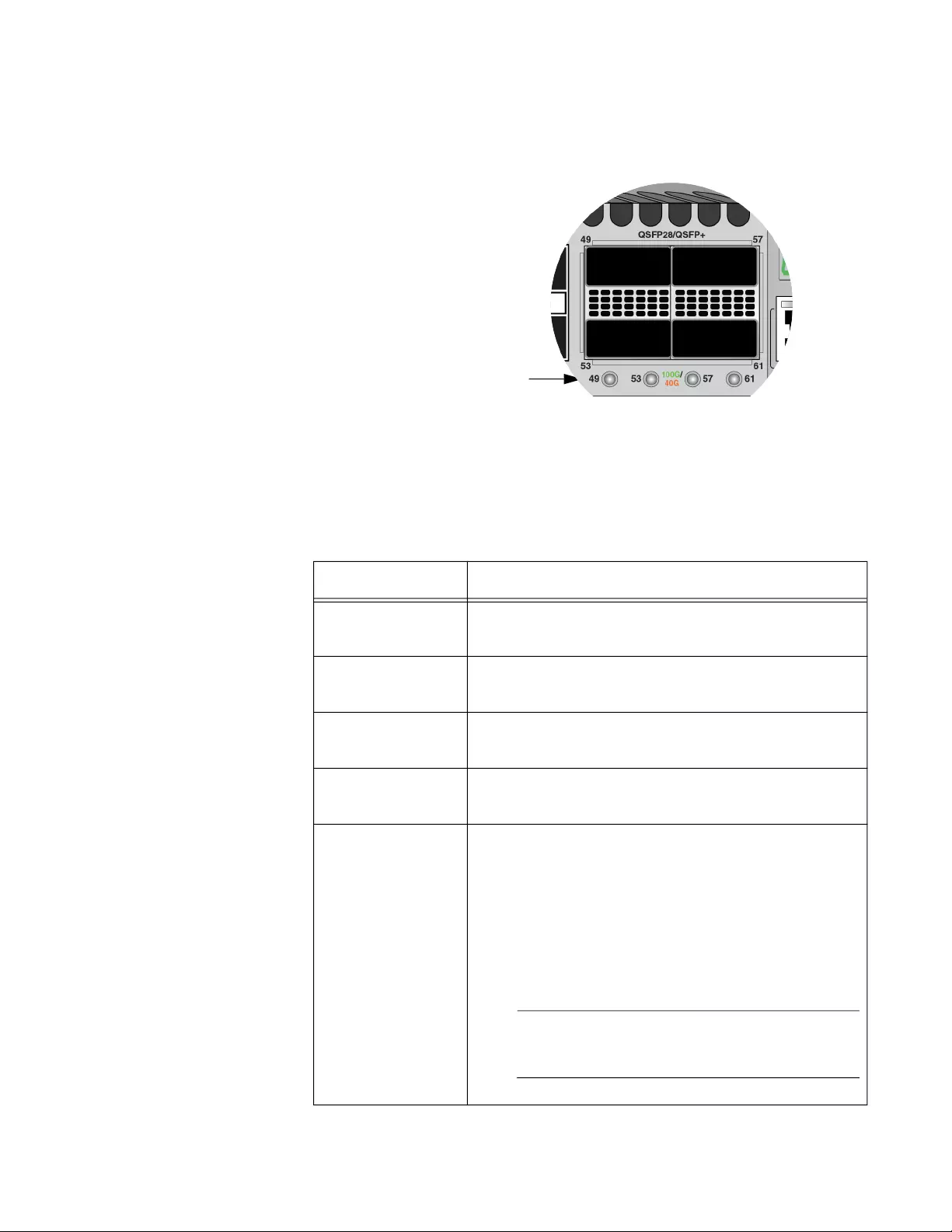
x950 Series Installation Guide for VCStack
31
Ports 49, 53, 57, and 61 on the x950-52XSQ switch have one link and
activity status LED each. Refer to Figure 8.
Figure 8. LEDs for Ports 49, 53, 57, 61 on x950-52XSQ Switch
The states of the LEDs for 40Gbps QSFP+ or 100Gbps QSFP28
transceivers are defined in Table 5.
Table 5. Link and Activity Status LEDs for 40Gbps QSFP+ or 100Gbps
QSFP28 Transceivers
State Description
Solid Green The transceiver has established a 100Gbps link to
a network device.
Flashing Green The transceiver is transmitting or receiving data at
100Gbps.
Solid Amber The transceiver has established a 40Gbps link to a
network device.
Flashing Amber The transceiver is transmitting or receiving data at
40Gbps.
Off Possible causes of this state are listed here:
- The transceiver slot is empty.
- The transceiver has not established a link to a
network device.
- The LEDs are turned off. To turn on the LEDs,
use the eco-friendly button.
Note
The x950-52XSQ switch does not have the
eco-friendly button.
Transceiver port LED
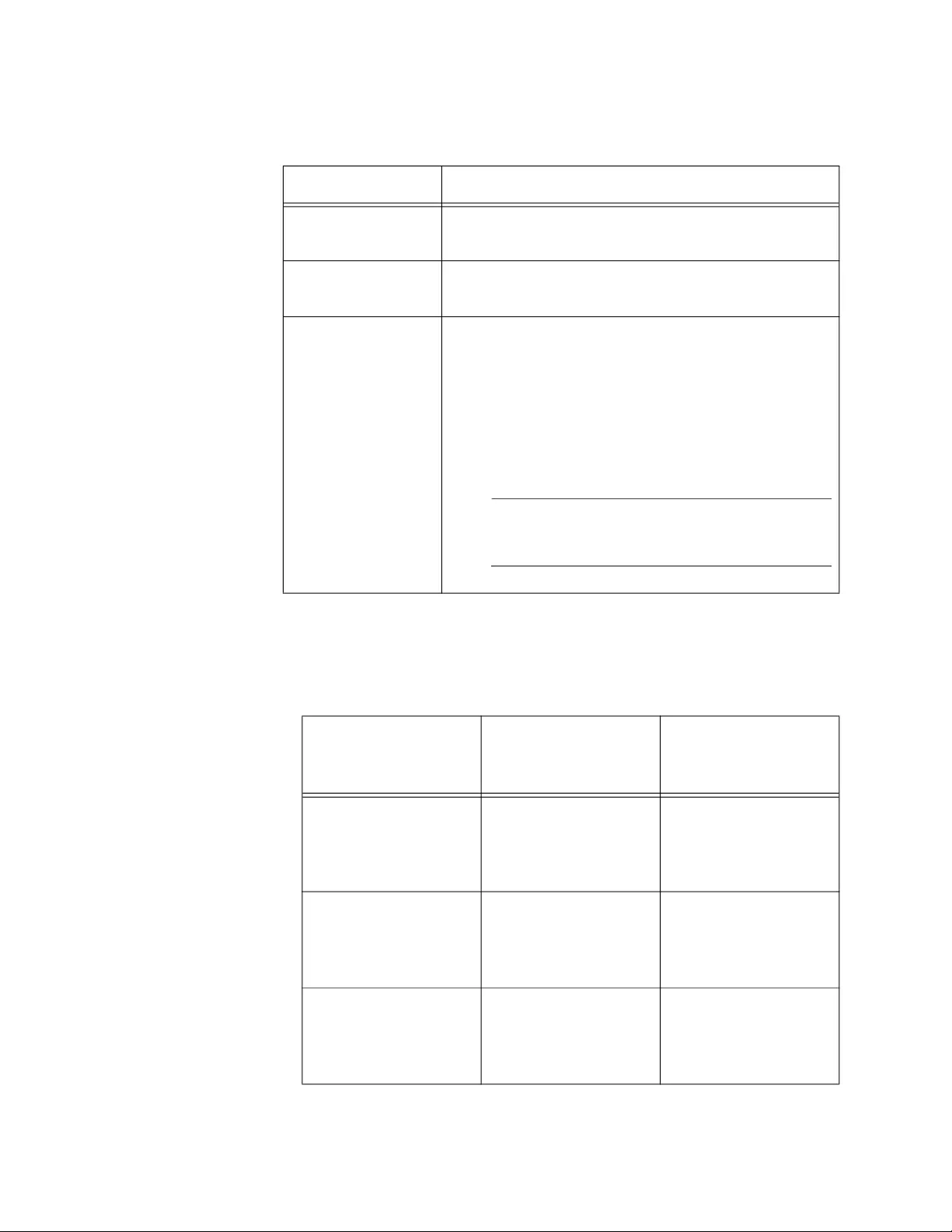
Chapter 1: Overview
32
The LED states for breakout cables are described in Table 6.
Port Numbering
for the
x950-28XSQ and
x950-28XTQm
Switches
Table 7 lists the port numbering system for ports 25, 29, 33, and 37 on the
x950-28XSQ and x950-28XTQm switches when the switch is operating in
a stack with the VCStack feature:
Table 6. Link and Activity Status LEDs for 10Gbps Breakout Cables
State Description
Solid Amber At least one of the four ports on the breakout cable
has established a 10Gbps link to a network device.
Flashing Amber At least one of the four ports on the breakout cable
is sending or receiving data.
Off Possible causes of this state are listed here:
- The transceiver slot is empty.
- None of the ports on the breakout cable have
established links to network devices.
- The LEDs are turned off. To turn on the LEDs,
use the eco-friendly button.
Note
The x950-52XSQ switch does not have the
eco-friendly button.
Table 7. Port Numbering for Ports 25 to 37
Port
With Fiber Optic
Transceiver or
Direct Attach Cable
With Breakout
Cable
25 portn.0.25 portn.0.25
portn.0.26
portn.0.27
portn.0.28
29 portn.0.29 portn.0.29
portn.0.30
portn.0.31
portn.0.32
33 portn.0.33 portn.0.33
portn.0.34
portn.0.35
portn.0.36
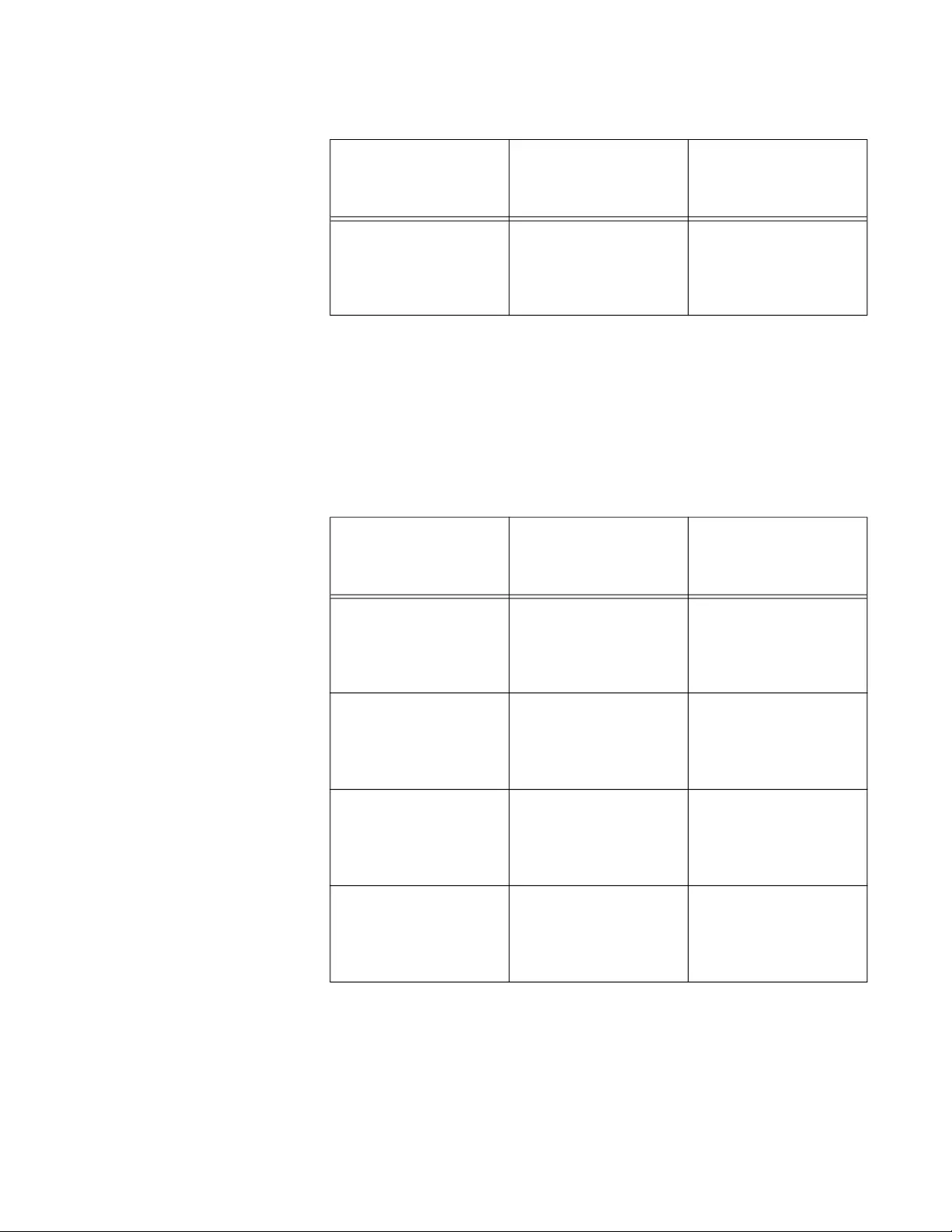
x950 Series Installation Guide for VCStack
33
The “n” variable is the switch’s ID number, displayed on the switch ID LED
on the front panel. For more information, refer to “Designating Ports in the
Command Line Interface” on page 46.
Port Numbering
for the
x950-52XSQ
Switch
Table 8 lists the port numbering system for ports 49, 53, 57, and 61 on the
x950-52XSQ switch when the switch is operating in a stack with the
VCStack feature:
The “n” variable is the switch’s ID number, displayed on the switch ID LED
on the front panel. For more information, refer to “Designating Ports in the
Command Line Interface” on page 46.
37 portn.0.37 portn.0.37
portn.0.38
portn.0.39
portn.0.40
Table 7. Port Numbering for Ports 25 to 37 (Continued)
Port
With Fiber Optic
Transceiver or
Direct Attach Cable
With Breakout
Cable
Table 8. Port Numbering for Ports 49, 53, 57, and 61
Port
With Fiber Optic
Transceiver or
Direct Attach Cable
With Breakout
Cable
49 portn.0.49 portn.0.49
portn.0.50
portn.0.51
portn.0.52
53 portn.0.53 portn.0.53
portn.0.54
portn.0.55
portn.0.56
57 portn.0.57 portn.0.57
portn.0.58
portn.0.59
portn.0.60
61 portn.0.61 portn.0.61
portn.0.62
portn.0.63
portn.0.64
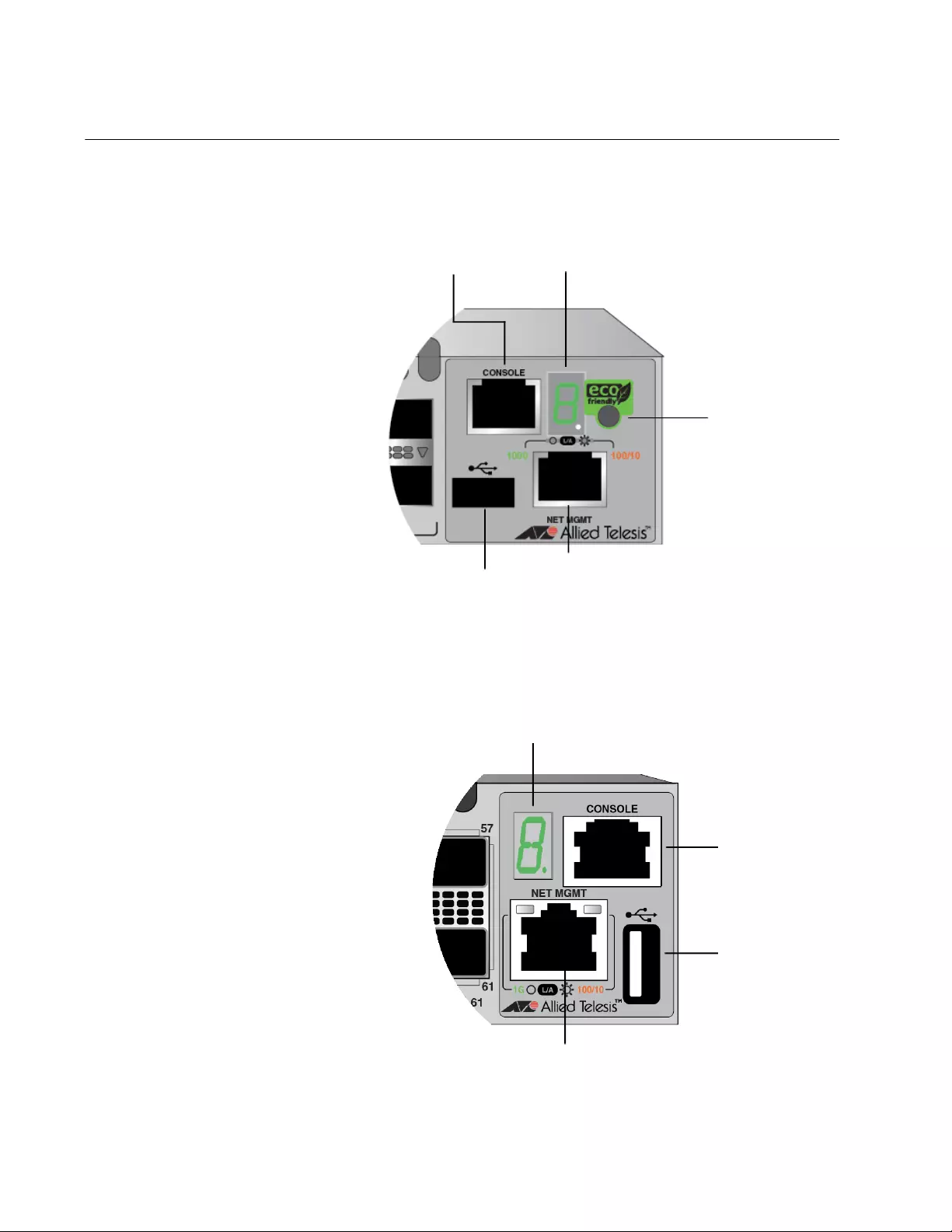
Chapter 1: Overview
34
Management Panel
The components on the management panel for x950-28XSQ and
x950-28XTQm switches are identified in Figure 9.
Figure 9. Management Panel for the x950-28XSQ and x950-28XTQm
Switches
The components on the management panel for and x950-52XSQ switch
are identified in Figure 10.
Figure 10. Management Panel for the x950-52XSQ Switch
USB Slot NET MGMT Port
CONSOLE
RS-232 Serial Port Switch ID LED
eco-friendly
Button
USB Slot
NET MGMT Port
CONSOLE
RS-232
Serial Port
Switch ID LED
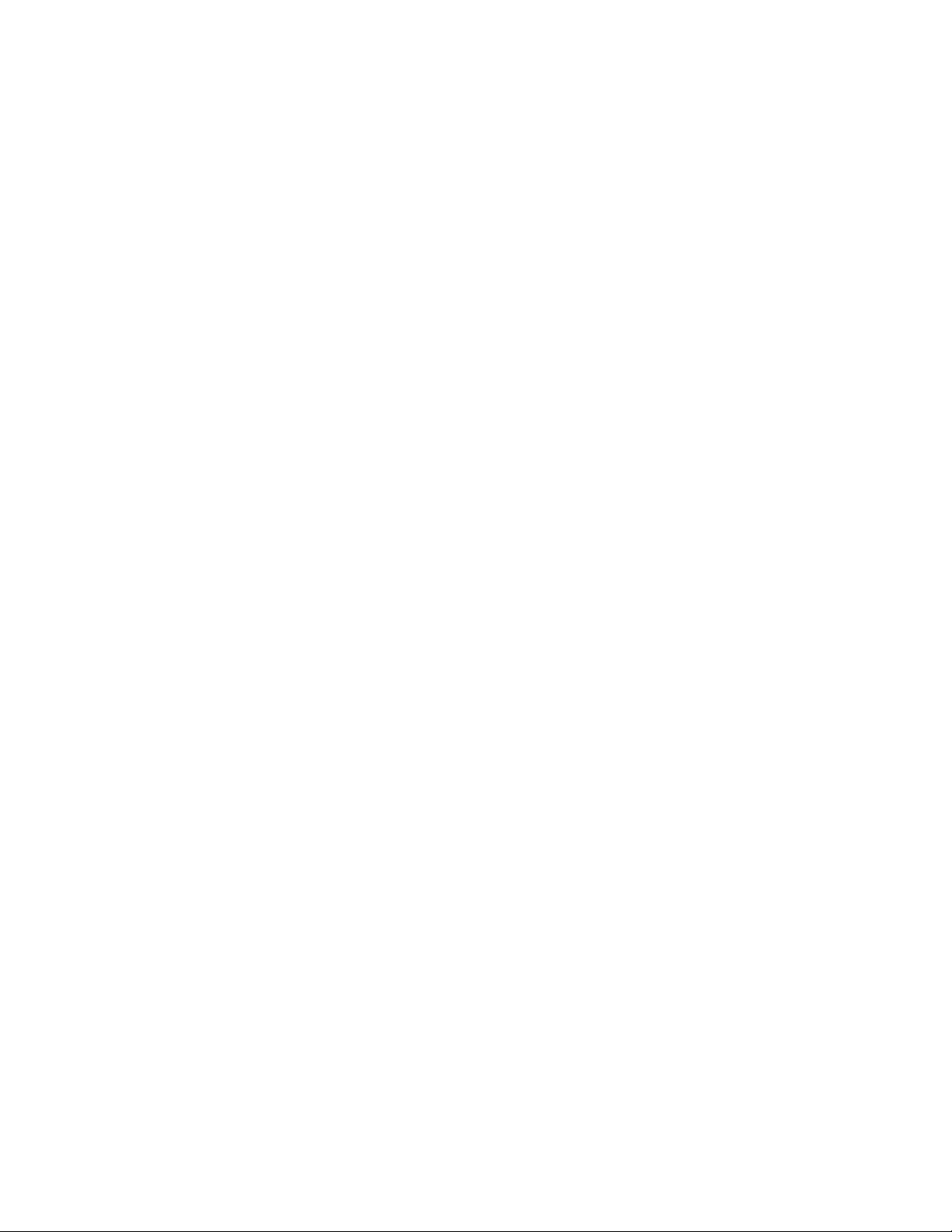
x950 Series Installation Guide for VCStack
35
USB Port You can use the USB port with a flash drive for the following functions:
Provide a centralized network backup location for Autonomous
Management Framework.
Store backup copies of configuration files.
Transfer configuration files between switches that are to have
similar configurations.
Store or transfer log files.
Store or transfer debug files (for example, the output of the SHOW
TECH-SUPPORT command).
Boot the AlliedWare Plus operating system and master
configuration file from flash drive.
Using a flash drive with the switch is optional.
NET MGMT
Ethernet
Management
Port
The switch uses the NET MGMT port as a separate routed eth0 interface.
The interface is not part of the switching matrix, but the switch can route
traffic in or out of the port from the network ports and Ethernet line card.
Here are the guidelines:
The port should only be used for initial configuration and
maintenance access to the chassis.
The NET MGMT port has a standard 8-pin RJ-45 connector and
operates at 10, 100, or 1000 Mbps in either half- or full-duplex
mode.
The default setting for the port is Auto-Negotiation, which sets the
speed and duplex mode automatically. You may disable
Auto-Negotiation and configure the port manually.
The wiring configuration of the NET MGMT port is set automatically
with automatic MDIX detection. You can disable automatic MDIX
detection and set the wiring configuration manually.
The port is referred to as eth0 in the management software.
The minimum cable requirements for the port are listed here.
10 or 100Mbps - Standard TIA/EIA 568-B-compliant Category 3
unshielded cabling.
1000Mbps - Standard TIA/EIA 568-A-compliant Category 5 or
TIA/EIA 568-B-compliant Enhanced Category 5 (Cat 5e)
unshielded cabling.
For instructions on how to configure the NET MGMT port, refer to the
Software Reference for x950 Switch, AlliedWare Plus Operating System.
The Network Management (NET MGMT) port has one Status LED,
described in Table 9.
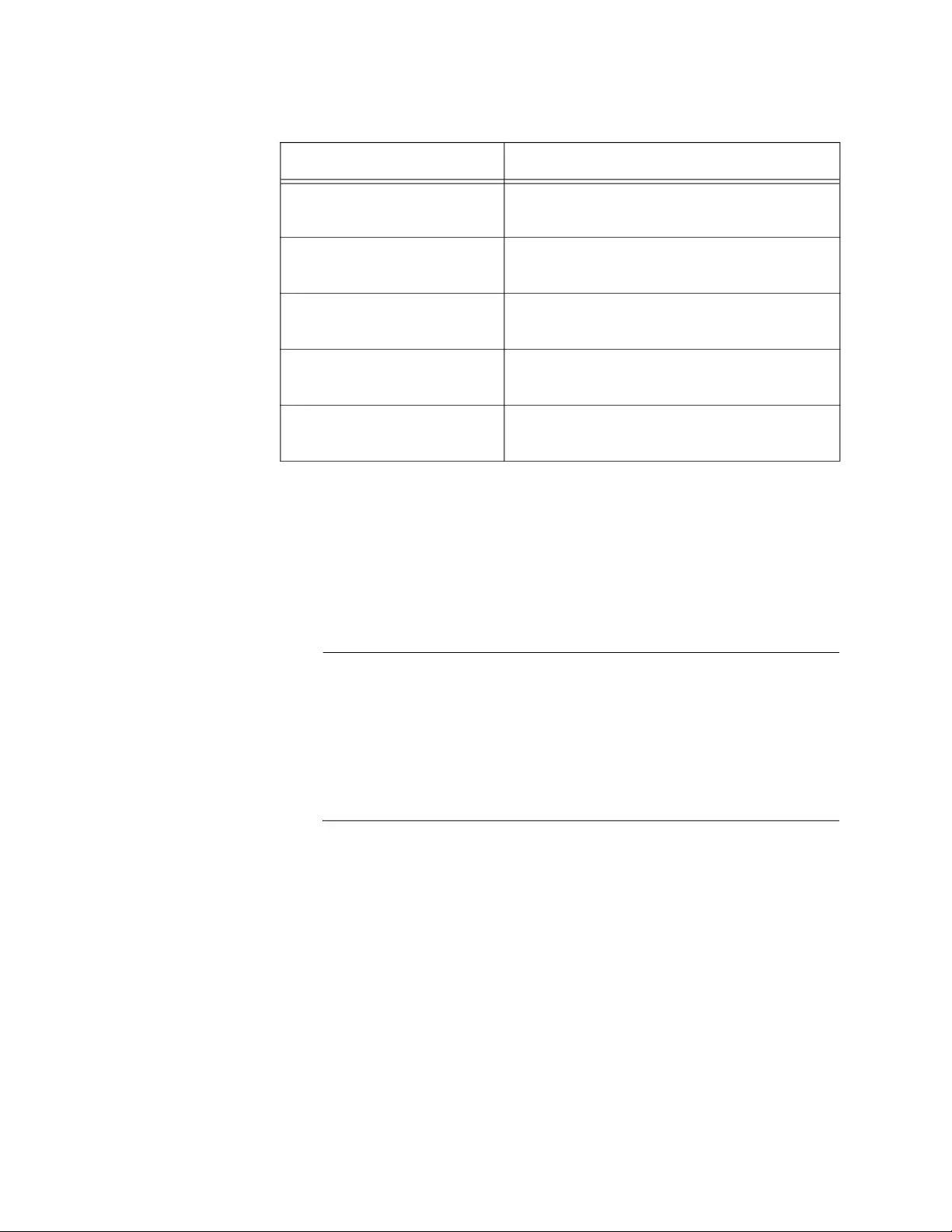
Chapter 1: Overview
36
Console (RS-232)
Port
You use the Console Port to conduct local management sessions with the
switch. Local management sessions require a terminal or PC with a
terminal emulation program, and the management cable that comes with
the switch. The switch does not need an Internet Protocol (IP) address for
local management sessions because they are not conducted over a
network. For instructions, refer to “Starting a Local Management Session”
on page 196.
Note
The first management session of the switch can be either a local
session or a remote session over your network through the NET
MGMT port. For remote management, the switch uses either its
default IP address 192.168.42.42 or an address assigned to it by a
DHCP server. For instructions on remote management sessions,
refer to the Software Reference for x950 Switches, AlliedWare Plus
Operating System.
Switch ID LED The Switch ID LED, shown in Figure 9 on page 34 or Figure 10 on page
34, displays a variety of information. Figure 11 on page 37 shows the
states of the LED when the eco-friendly mode is disabled.
Table 9. NET MGMT Port LED
State Description
Solid Green The port has established a 1000 Mbps link
with a network device.
Flashing Green The port is transmitting or receiving data
at 1000 Mbps.
Solid Amber The port has established a 10 or 100
Mbps link.
Flashing Amber The port is transmitting or receiving data
at 10 or 100 Mbps.
Off The port has not established a link to a
network device.
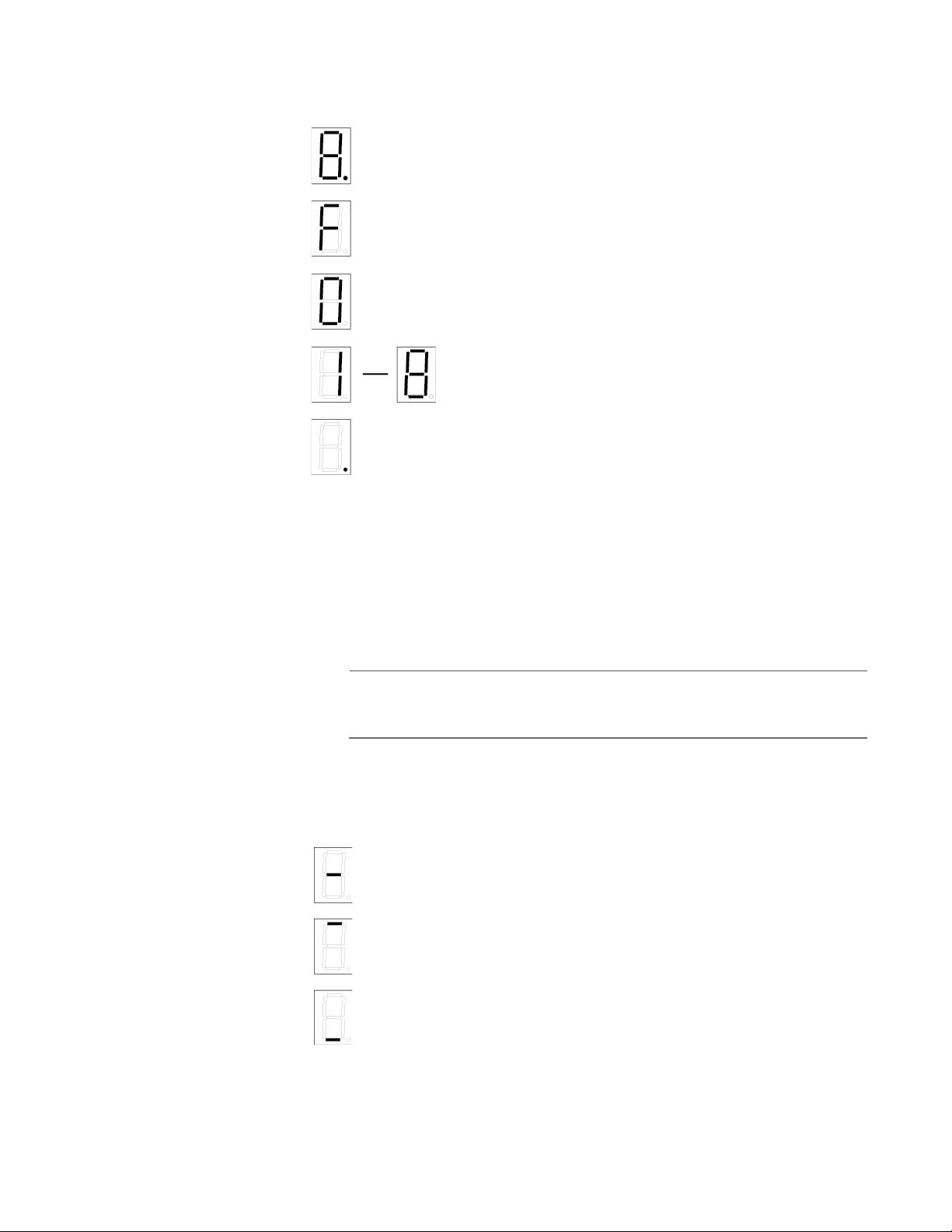
x950 Series Installation Guide for VCStack
37
Figure 11. Switch ID LED with the eco-friendly Mode Disabled
The switch displays the letter “F” for fault on the ID LED if it detects one of
the following problems:
A cooling fan has failed.
The switch is about to shut down because its internal temperature
is outside the normal operating range.
Note
You can use the SHOW SYSTEM ENVIRONMENT command in the
command line interface to identify the source of the problem.
Figure 12 illustrates the states of the LED when the eco-friendly mode is
enabled and the switch is operating in the low power mode.
Figure 12. Switch ID LED with the eco-friendly Mode Enabled
The switch is booting up.
The switch has encountered a fault condition.
The VCStack feature is disabled. The switch is operating
as a stand-alone unit, with the ID number 1.
The switch is a member of a VCStack and has
The dot in the lower right corner flashes when the switch
accesses USB memory.
an ID number in the range of 1 to 8.
The VCStack feature is disabled. The switch is operating
The switch is the master switch of a VCStack.
The switch is a member switch of a VCStack.
as a stand-alone device.
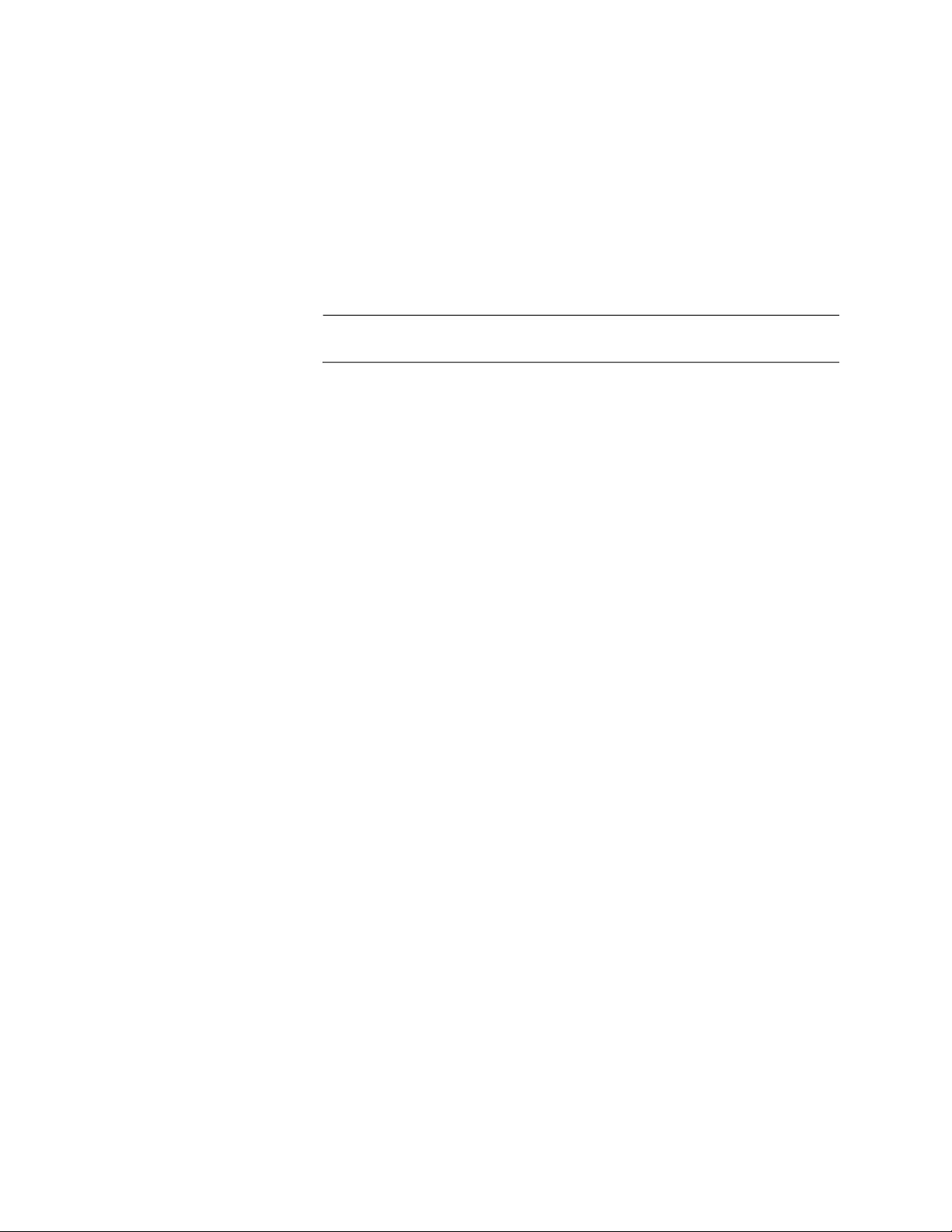
Chapter 1: Overview
38
eco-friendly
Button
You use the eco-friendly button on the management panel to turn the
LEDs on or off. You might turn off the LEDs when you are not using them
to monitor the control and Ethernet line cards, to conserve electricity.
When the LEDs are off, the overall power consumption of the chassis is
reduced by approximately 2 watts.
The button controls all the port LEDs, except for the L/A LED for the NET
MGMT port. Additionally, the button does not control the LEDs on the
power supplies.
Note
The x950-52XSQ switch does not have the eco-friendly button.
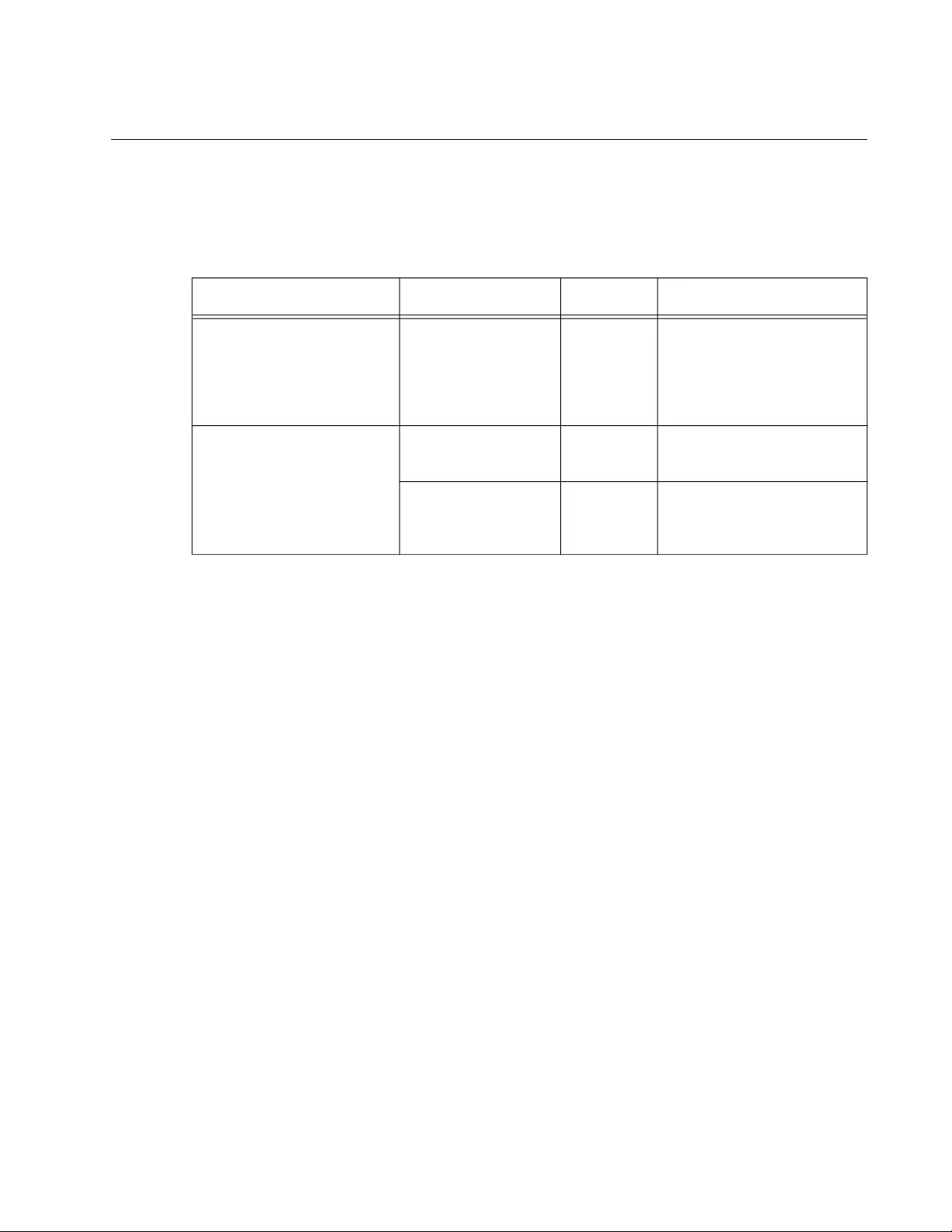
x950 Series Installation Guide for VCStack
39
Optional Direct Attach Cables
The optional direct attach cables listed in Table 10 offer an economical
way to add 10Gbps, 40Gbps, or 100Gbps connections over short
distances for switch ports or ports on XEM2 Line Cards.
Table 10. Optional Direct Attach Cables
Switch Ports XEM2 Line Card Speed Direct Attach Cable
Ports 1 to 24 on
x950-28XSQ
Ports 1 to 48 on
x950-52XSQ
XEM2-8XSTm
XEM2-12XS
XEM2-12XS v21
10Gbps SP10TW1 - 1 meter
SP10TW3 - 3 meters
SP10TW7 - 7 meters
Ports 25, 29, 33, and 37
on x950-28XSQ and
x950-28XTQm
Ports 49, 53, 57, and 61
on x950-52XSQ
XEM2-4QS 40Gbps QSFP1CU - 1 meter
QSFP3CU - 3 meters
XEM2-1CQ 100Gbps QSFP28-1CU - 1 meter
QSFP28-3CU - 3 meters
1. The XEM2-12XS v2 Card supports the SP10TW1 and SP10TW3 cables. It does not support the
SP10TW7 cable.
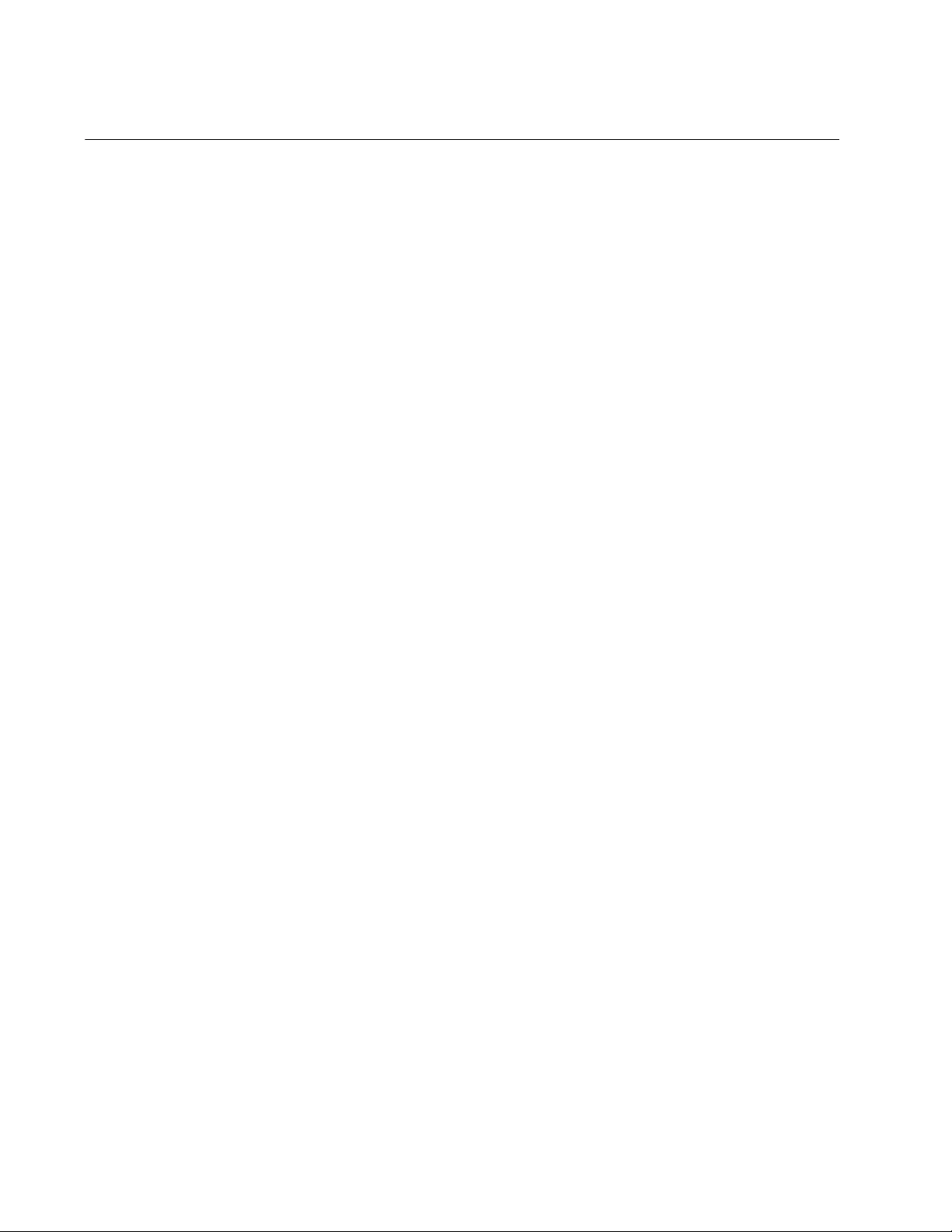
Chapter 1: Overview
40
PWR600 AC and DC Power Supplies
The x950 series switch supports the PWR600 AC and PWR600 DC power
supply units.
Here are power supply guidelines:
You can install either one or two power supplies in the switch.
A single power supply can power a fully equipped switch.
Installing two power supplies adds power redundancy.
You can install two PWR600 AC modules, two PWR600 DC
modules, or a combination of the PWR600 AC and PWR600 DC
modules on one switch.
The power supplies are installed in the PSU A and PSU B slots in
the rear panel of the chassis. If you are installing only one power
supply, Allied Telesis recommends installing it in PSU A slot
because that slot does not come with a blank slot cover.
The switch does not come with power supplies. They are
purchased separately.
The power supplies are field-replaceable and hot-swappable. If the
switch has two power supplies and one fails, you do not have to
power off the operational power supply to replace the failed unit.
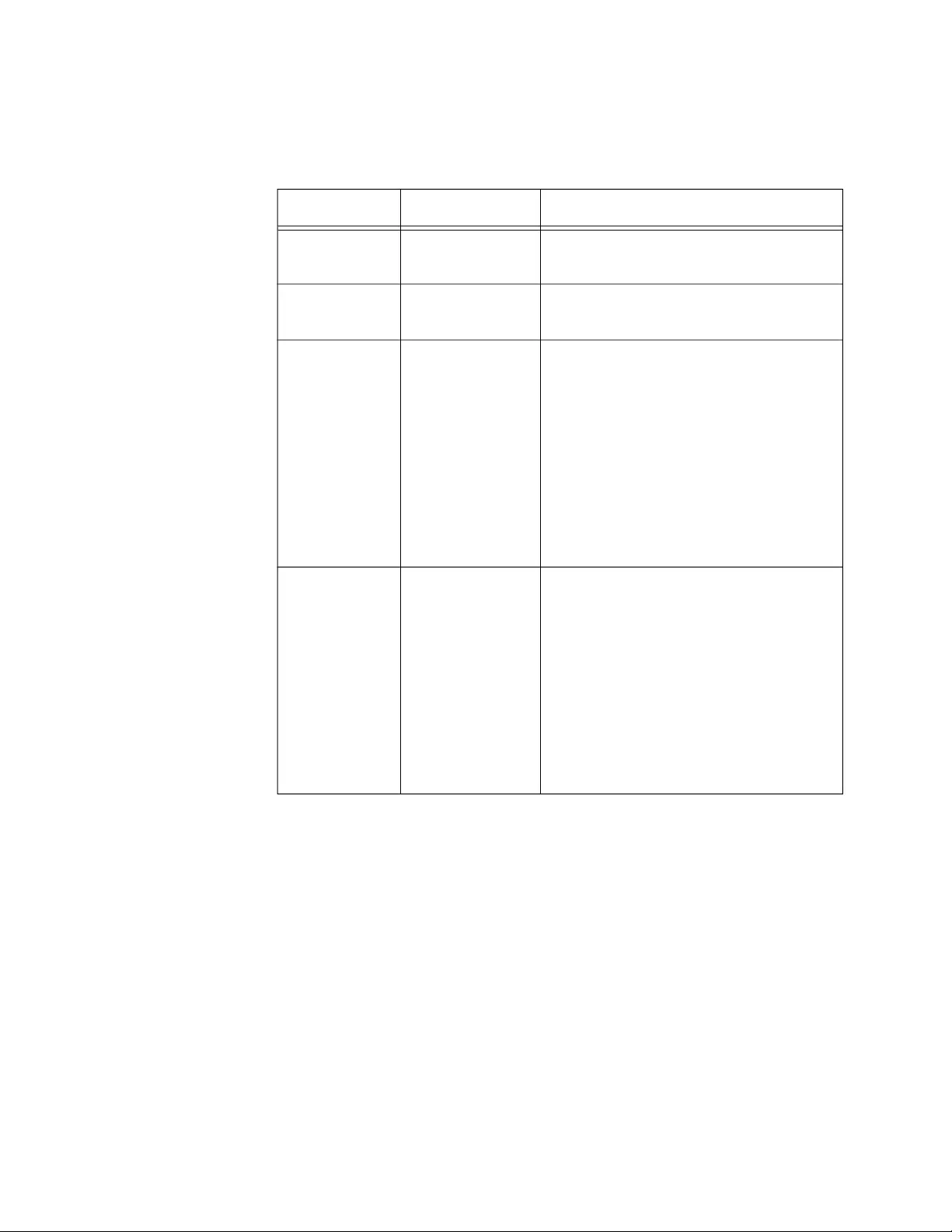
Chapter 1: Overview
42
LEDs The two LEDs on the front panel of the power supply are described in
Table 11.
Table 11. LEDs on the PWR600 AC Power Supply
Green LED Amber LED Description
Solid green Off The power supply is operating
normally.
Blinking
green
Off The power supply is in the standby
mode.
Solid green Blinking amber The power supply is experiencing a
warning condition, but is still
operating. Here are possible causes:
- The power supply is overheating.
- The speed of it’s fan is too low.
- Its output current is too high.
- The input voltage from the AC
power source is too low.
Off Solid amber The power supply shut down because
one of these fault conditions occurred:
- The power supply overheated.
- Its fan stopped or was too slow.
- Its output current to the switch was
too high.
- The input voltage from the AC
power source was too low.

x950 Series Installation Guide for VCStack
43
PWR600 DC
Power Supply
The PWR600 DC module is a DC power supply for the switch. Refer to
Figure 14.
Figure 14. PWR600 DC Power Supply
LEDs The PWR600 DC power supply has the two LEDs on the front panel as
shown in Figure 14. See Table 12 for the descriptions.
Figure 15. LEDs for PWR600 DC Power Supply
LEDs
Table 12. LEDs on the PWR600 DC Power Supply
Green LED Amber LED Description
Solid green Off The power supply is operating
normally.
Blinking
green
Off The power supply is in the standby
mode.
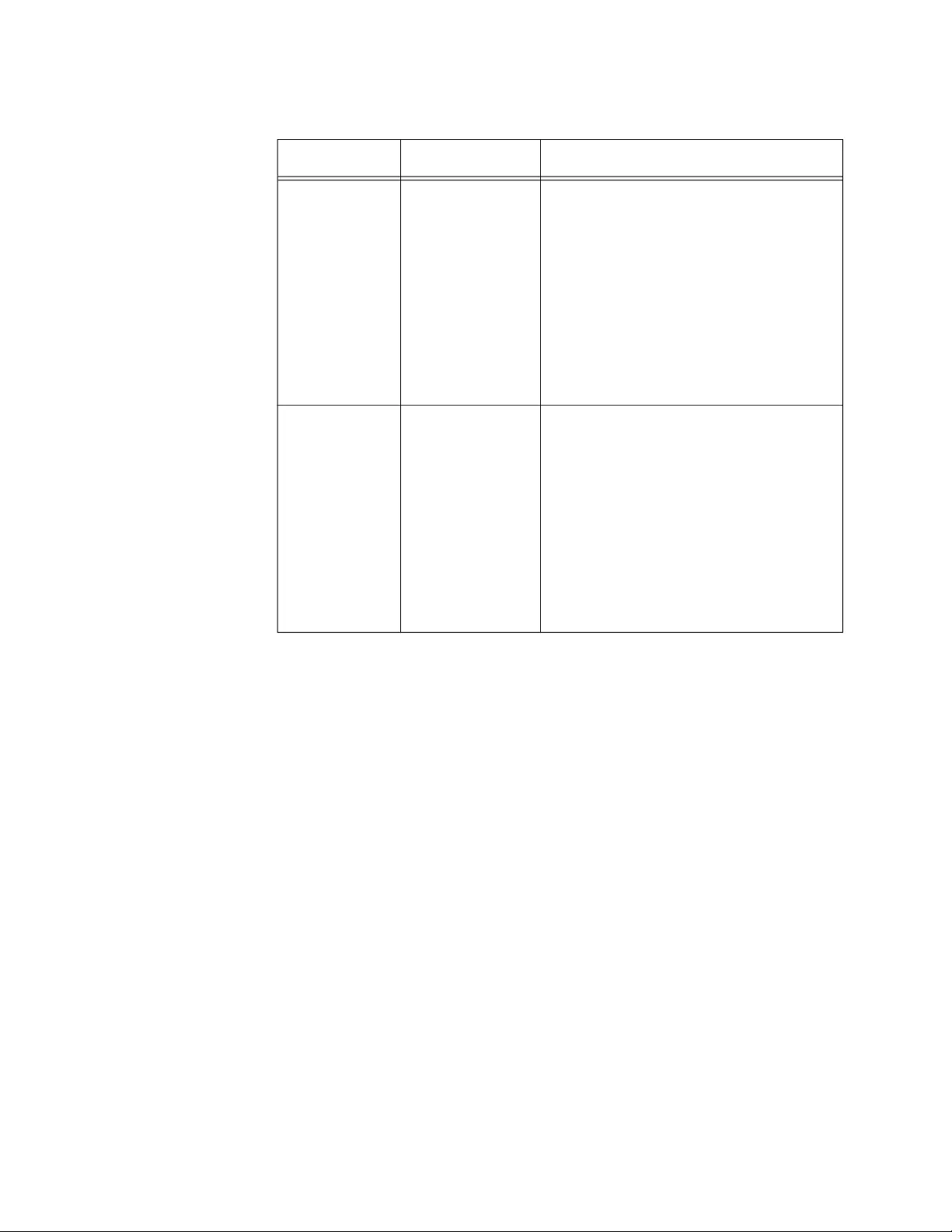
Chapter 1: Overview
44
Solid green Blinking amber The power supply is experiencing a
warning condition, but is still
operating. Here are possible causes:
- The power supply is overheating.
- The speed of it’s fan is too low.
- Its output current is too high.
- The input voltage from the DC
power source is too low.
Off Solid amber The power supply shut down because
one of these fault conditions occurred:
- The power supply overheated.
- Its fan stopped or was too slow.
- Its output current to the switch was
too high.
- The input voltage from the DC
power source was too low.
Table 12. LEDs on the PWR600 DC Power Supply
Green LED Amber LED Description
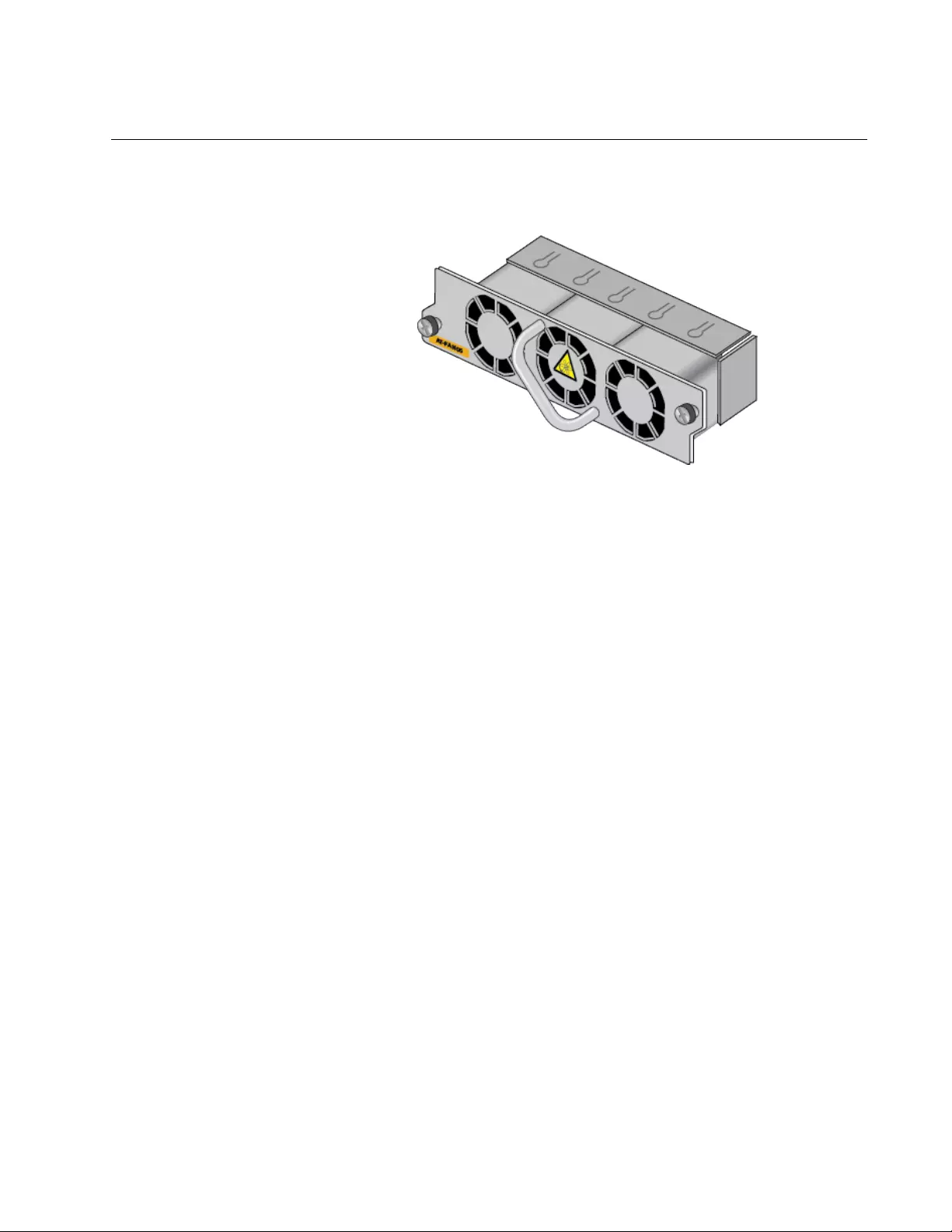
x950 Series Installation Guide for VCStack
45
FAN05 Cooling Fan
The cooling unit for the chassis is the FAN05 Fan module. Refer to
Figure 16.
Figure 16. FAN05 Fan Module
Here are the fan module guidelines:
The switch comes with two pre-installed fan modules in FAN A and
FAN B slots on the rear panel.
The fan modules are field-replaceable and hot-swappable. You do
not have to power off the switch to replace them.
The switch automatically adjusts the fan speeds according to its
internal temperature.
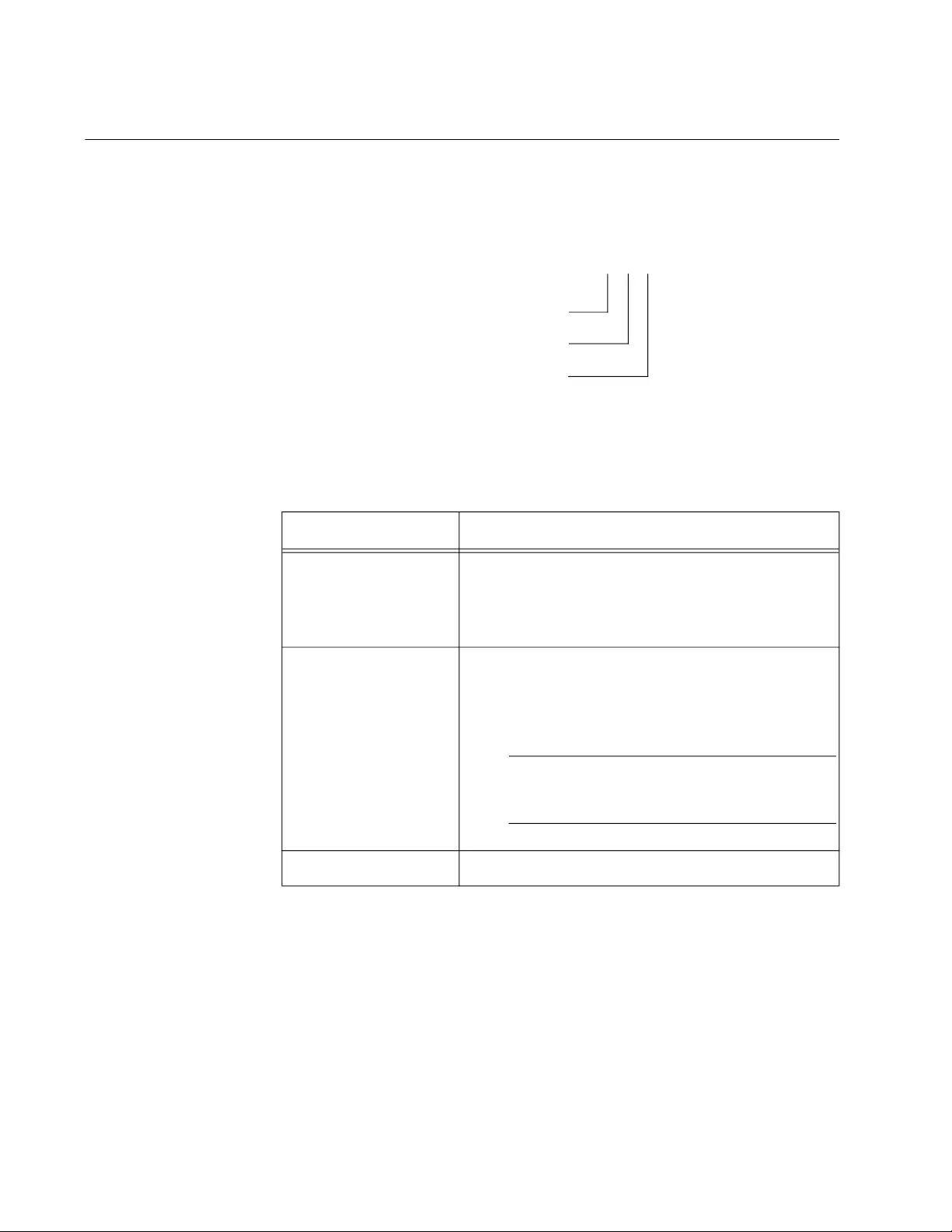
Chapter 1: Overview
46
Designating Ports in the Command Line Interface
The individual ports on the switch are identified with the PORT parameter
in the command line interface of the AlliedWare Plus management
software. The format of the parameter is shown in Figure 17.
Figure 17. PORT Parameter in the Command Line Interface
The three parts of the PORT parameter are described in Table 13.
Table 13. PORT Parameter Format
Number Description
Switch ID Number Identifies the switch’s unique ID number in the
stack. When the VCStack feature is enabled,
switches display their ID numbers on the Switch
ID LEDs on the front panels.
Slot Number Identifies whether ports are base ports or ports
on an XEM2 Line Card. Slot number 0 indicates
base ports and slot number 1 indicates ports on
a line card. Refer to Figure 18 on page 47.
Note
The x950-52XSQ switch has base ports
only.
Port Number Identifies a port number.
port
n.n.n
Slot Number
Port Number
Switch ID Number
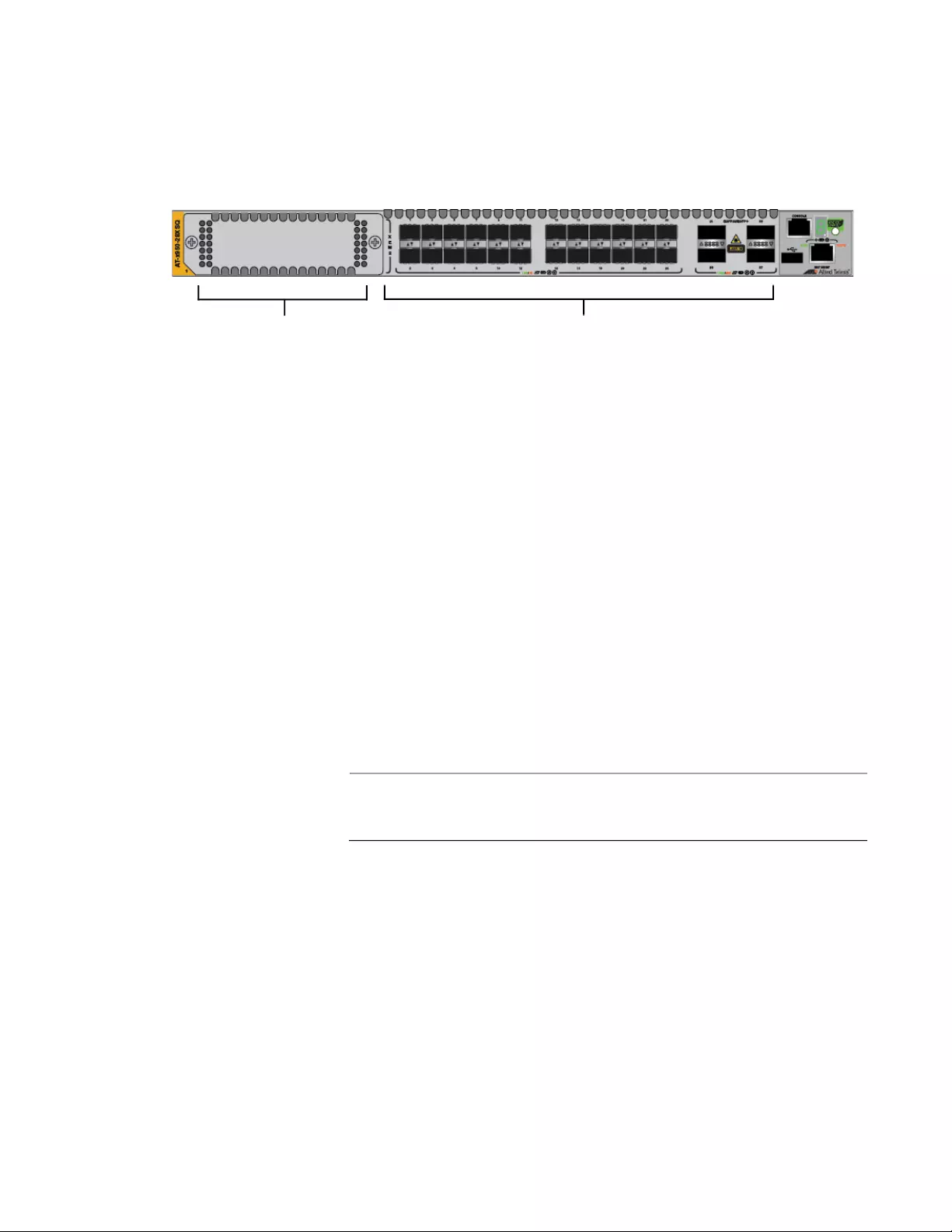
x950 Series Installation Guide for VCStack
47
Examples of Port
Numbering
You must include the PORT parameter when identifying individual ports,
and omit it from the last port when specifying ranges.
Figure 18 identifies the slot numbers for base ports and line card ports.
Figure 18. Slot Numbers for Port Numbering
Here are examples of the PORT parameter in the INTERFACE command
for switches in a stack.
PORT Parameter on Base Ports
Ports on the switch are called base ports to distinguish from ports on an
XEM2 line card.
The first example enters the port Interface mode for base port 11 in a
switch with ID 1:
awplus> enable
awplus# configure terminal
awplus(config)# interface port1.0.11
This example enters the port Interface mode for base port 4 to 7 in a
switch with ID 2:
Note
You have to include the PORT parameter when identifying individual
ports, and omit it from the last port when specifying ranges.
awplus(config)# interface port2.0.4-2.0.7
This example enters the port Interface mode for base port 10 in a switch
with ID 1 and base port 18 in a switch with ID 2:
awplus(config)# interface port1.0.10,port2.0.18
Slot Number 1 for XEM2 Line Card:
portn.1.n
Slot Number 0 for Base Ports:
portn.0.n
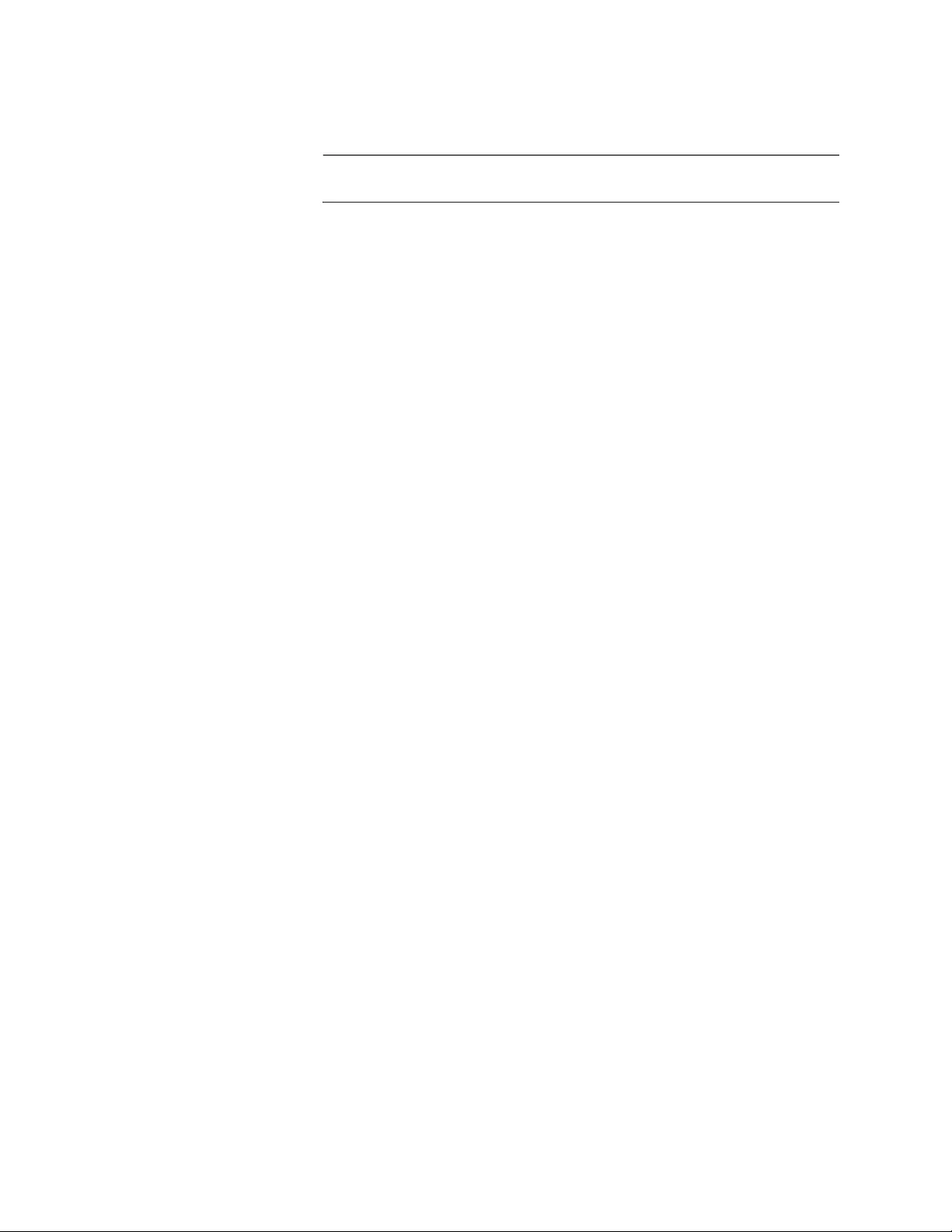
Chapter 1: Overview
48
PORT Parameter on an XEM2 Line Card
Note
The x950-52XSQ switch has base ports only.
This example enters the port Interface mode for ports 2 and 5 in an XEM2
line card in a switch with ID 1:
awplus(config)# interface port1.1.2,port1.1.5
This example enters the port Interface mode for base port 6 as well as port
5 on an XEM2 line card in a switch with ID 2:
awplus(config)# interface port2.0.6,port2.1.5
For further instructions, refer to the Software Reference for x950 Switch,
AlliedWare Plus Operating System.
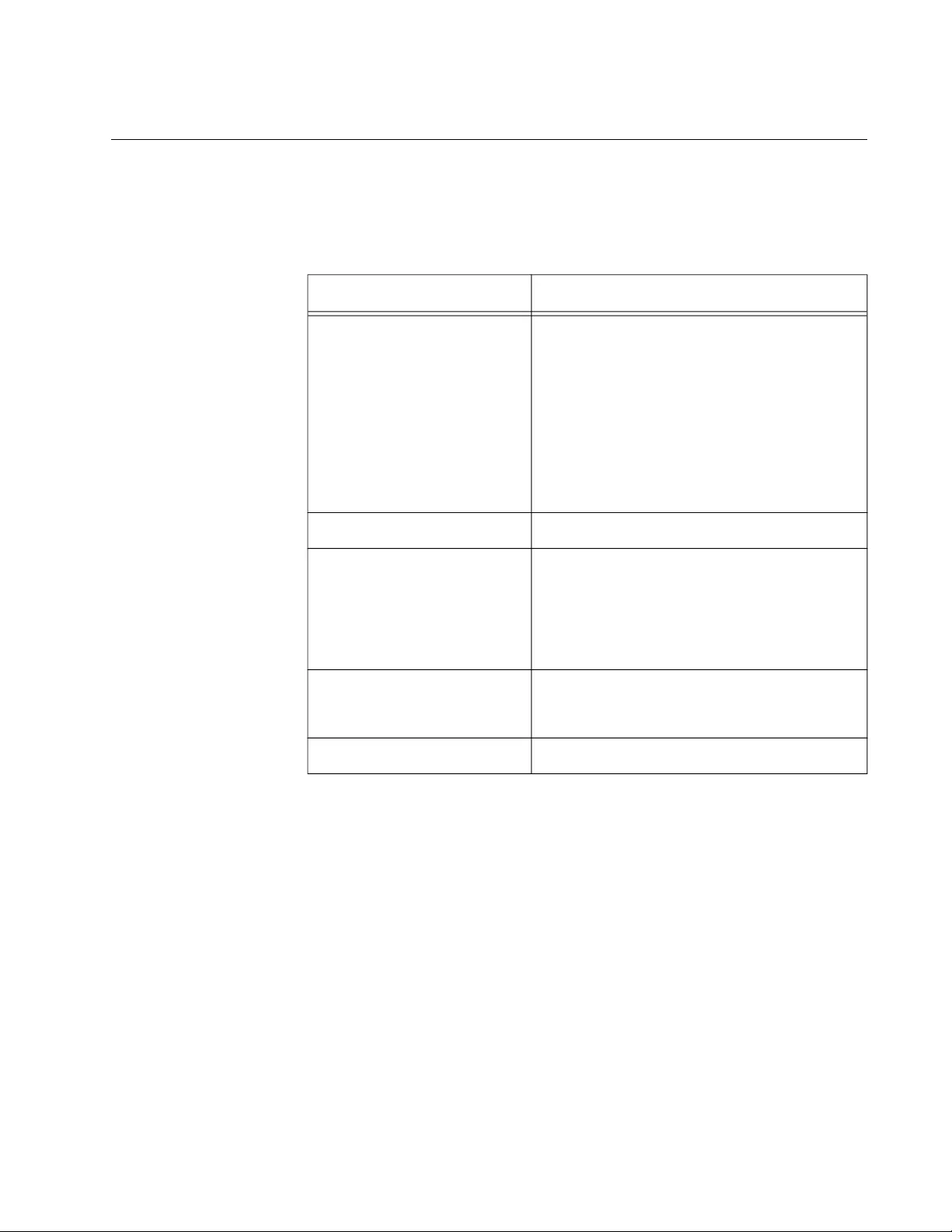
x950 Series Installation Guide for VCStack
49
Software and Hardware Releases
The software and hardware releases for the AlliedWare Plus operating
software and x950 Switches are listed in Table 14.
Table 14. Software and Hardware Releases
Software Version Hardware / VCStack
v5.4.8-2 x950-28XSQ Switch
XEM2-12XT Line Card
XEM2-12XS Line Card
XEM2-4QS Line Card
XEM2-1CQ Line Card
VCStack - Stacks up to two switches.
v5.4.9 VCStack - Stacks up to four switches.
v5.4.9-1 x950-28XTQm Switch
XEM2-12XTm Line Card
XEM2-12XT Line Card: Adds 100Mbps
port speed
v5.4.9-2 XEM2-8XSTm Line Card
XEM2-12XS v2 Line Card
v5.5.0-1 x950-52XSQ Switch
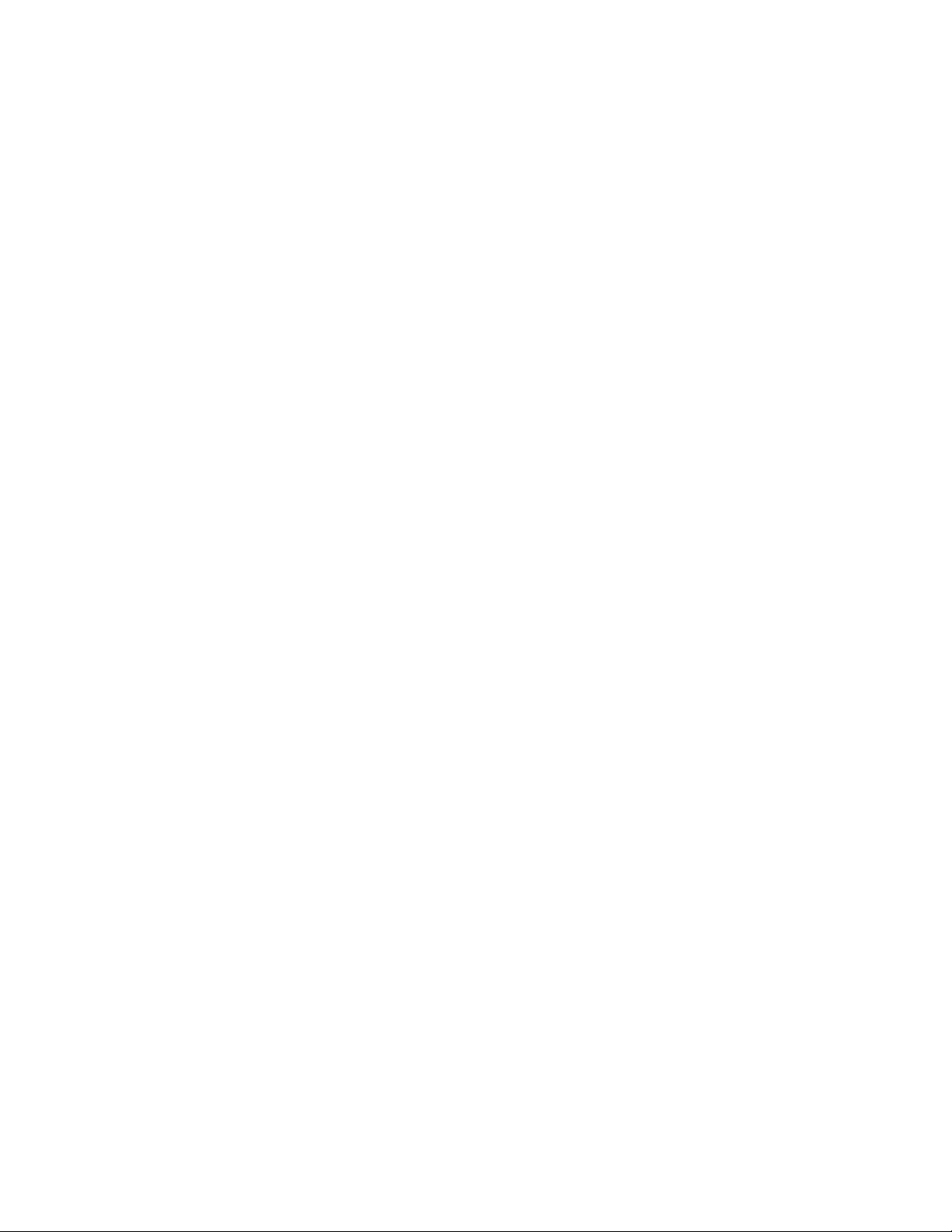
Chapter 1: Overview
50
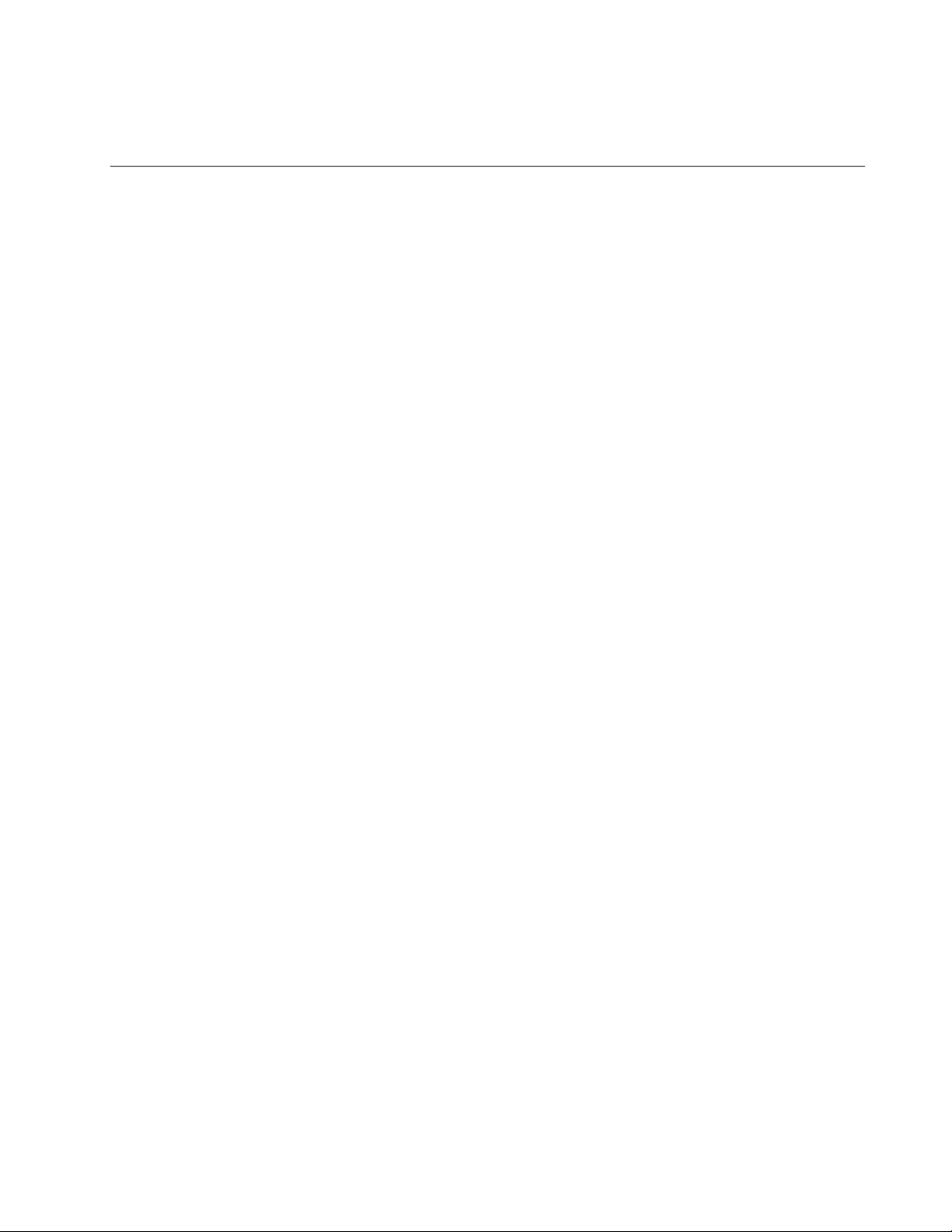
51
Chapter 2
XEM2 Ethernet Line Cards
The chapter contains the following sections:
“Overview” on page 52
“XEM2-8XSTm Line Card” on page 55
“XEM2-12XT Line Card” on page 59
“XEM2-12XTm Line Card” on page 61
“XEM2-12XS and XEM2-12XS v2 Line Cards” on page 63
“XEM2-4QS Line Card” on page 66
“XEM2-1CQ Line Card” on page 68
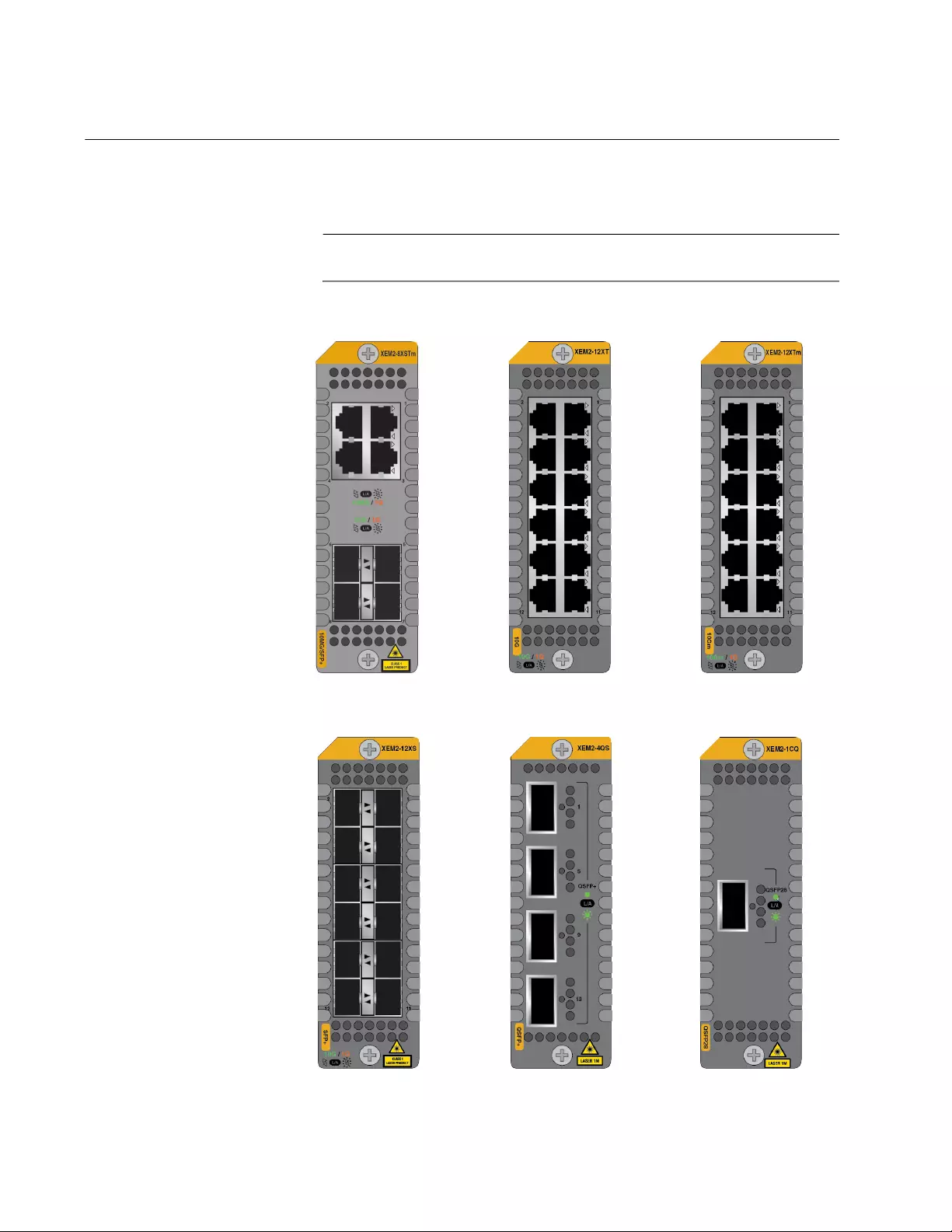
Chapter 2: XEM2 Ethernet Line Cards
52
Overview
The x950-28XSQ and x950-28XTQm switches have one expansion slot
on the front panel for an optional XEM2 Ethernet line card. See Figure 19.
Note
The x950-52XSQ switch does not support the XEM2 line cards.
Figure 19. XEM2 Ethernet Line Cards
XEM2-4QS XEM2-1CQ XEM2-12XS and v2
XEM2-12XT XEM2-12XTm
XEM2-8XSTm
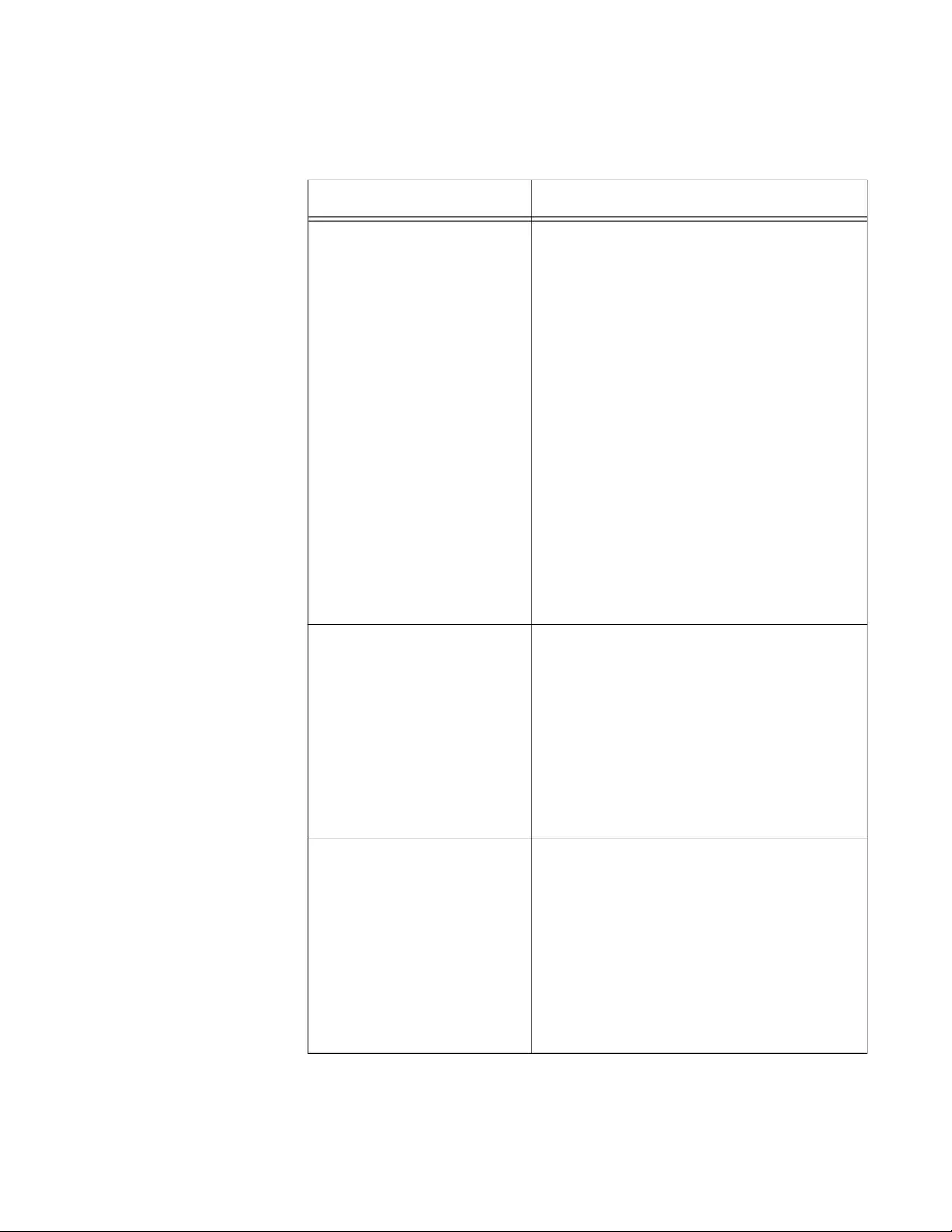
x950 Series Installation Guide for VCStack
53
The XEM2 Ethernet line cards are described in Table 15.
Table 15. XEM2 Ethernet Line Cards
Line Card Description
XEM2-8XSTm Four twisted pair ports (1-4) with RJ-45
connectors that support the following
speeds:
- 100Mbps
- 1/2.5/5/10Gbps
Four ports (5-8) that support the following
types of transceivers:
- 1Gbps SFP
- 10Gbps SFP+
- 10Gbps one meter SP10TW1 and three
meter SP10TW3 direct connect twinax
cables (The card does not support the
seven meter SP10TW7 cable.)
Refer to “XEM2-8XSTm Line Card” on
page 55.
XEM2-12XT 12 twisted pair ports with RJ-45
connectors that support the following
speeds:
- 100Mbps (requires AlliedWare Plus
v5.4.9-0 or later.)
- 1/10Gbps
Refer to “XEM2-12XT Line Card” on
page 59.
XEM2-12XTm 12 twisted pair ports with RJ-45
connectors that support the following
speeds:
- 100Mbps
- 1/2.5/5/10Gbps
Refer to “XEM2-12XTm Line Card” on
page 61.(This card requires AlliedWare
Plus v5.4.9-0 or later.)
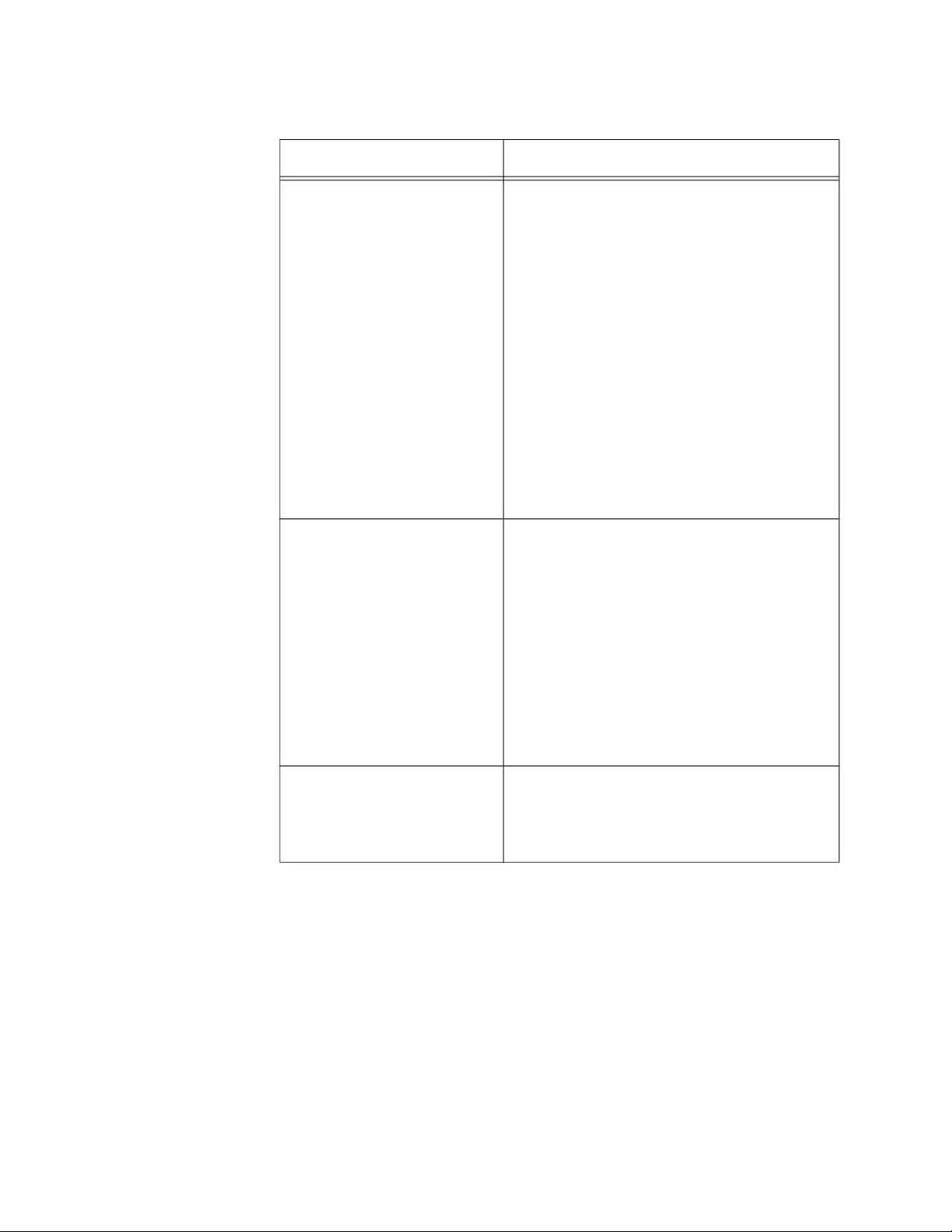
Chapter 2: XEM2 Ethernet Line Cards
54
The XEM2-8XSTm Card requires AlliedWare Plus v5.4.9-2 or later.
The 100Mbps port speed on the XEM2-12XT Card requires
AlliedWare Plus v5.4.9-0 or later.
The XEM2-12XTm Card requires AlliedWare Plus v5.4.9-0 or later.
For more information, refer to “Software and Hardware Releases” on
page 49.
XEM2-12XS and XEM2-
12XS v2
12 ports that support the following types of
transceivers:
- 1/2.5/5/10Gbps SP10TM transceivers
with RJ-45 connectors
- 1Gbps SFP
- 10Gbps SFP+
- 10Gbps one meter SP10TW1, three
meter SP10TW3, and seven meter
SP10TW7 direct connect twinax cables
(The XEM2-12XS v2 Card does not
support the SP10TW7 cable.)
Refer to “XEM2-12XS and XEM2-12XS v2
Line Cards” on page 63.
XEM2-4QS Four ports that support the following types
of transceivers
- 40Gbps QSFP+ transceivers
- 40Gbps QSFPCU direct connect cables
- QSFP-4SFP10G-3CU and QSFP-
4SFP10G-5CU 40Gbps to 10Gbps
breakout cables
Refer to “XEM2-4QS Line Card” on
page 66.
XEM2-1CQ One port for the 100Gbps QSFP28
transceiver or QSFP28-1CU or QSFP28-
3CU direct attach cable. Refer to “XEM2-
1CQ Line Card” on page 68.
Table 15. XEM2 Ethernet Line Cards (Continued)
Line Card Description
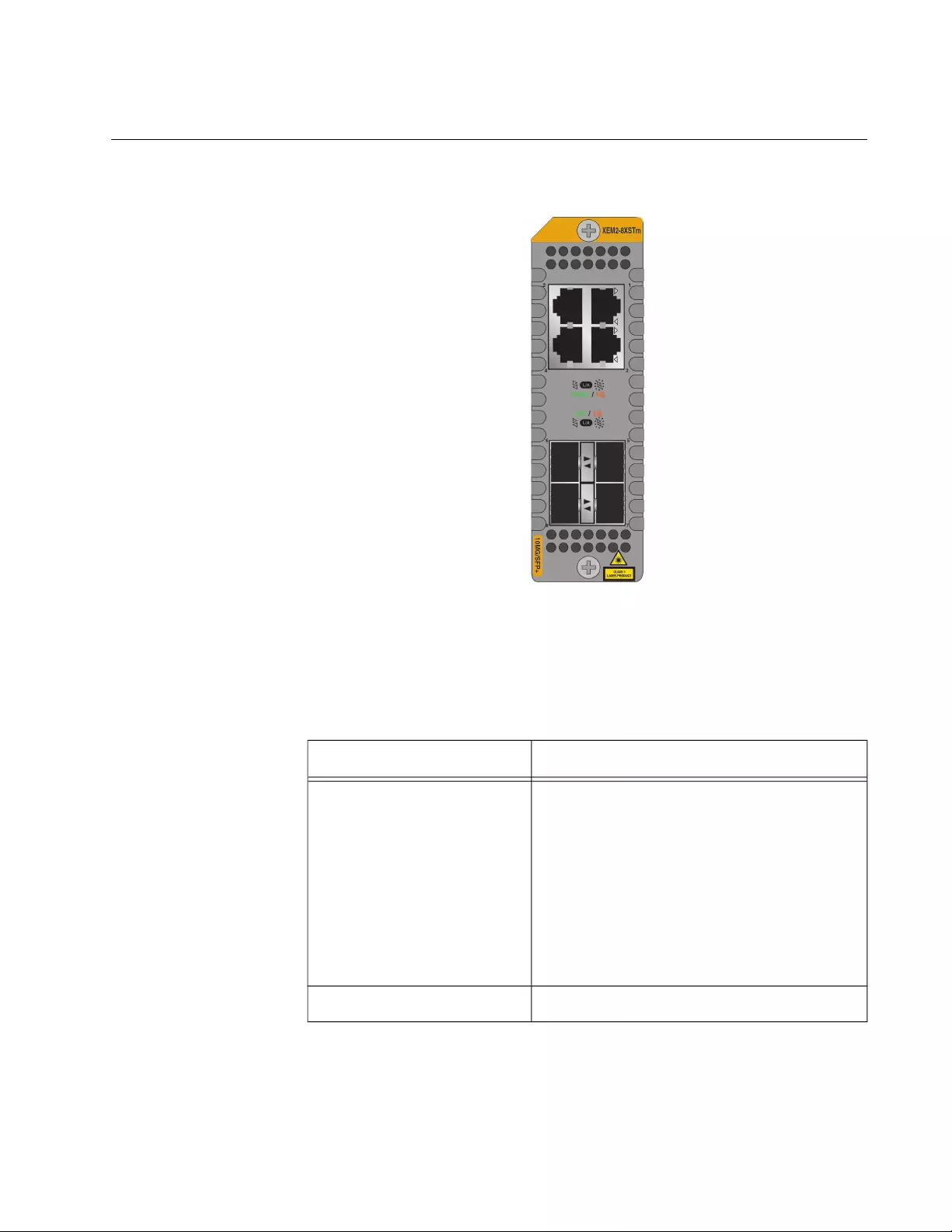
x950 Series Installation Guide for VCStack
55
XEM2-8XSTm Line Card
The XEM2-8XSTm Line Card is shown in Figure 20.
Figure 20. XEM2-8XSTm Line Card
Twisted Pair
Ports
The XEM2-8XSTm Card has four twisted pair ports and four SFP ports.
The specifications for the twisted pair ports are listed in Table 16.
Table 16. Twisted Pair Ports on the XEM2-8XSTm Line Card
Specification Description
Port Speed The ports support the following speeds:
- 100Mbps
- 1/2.5/5/10Gbps
The ports do not support 10Mbps.
You can set port speed with Auto-
Negotiation or manually. The default is
Auto-Negotiation.
Duplex Mode Full-duplex only.
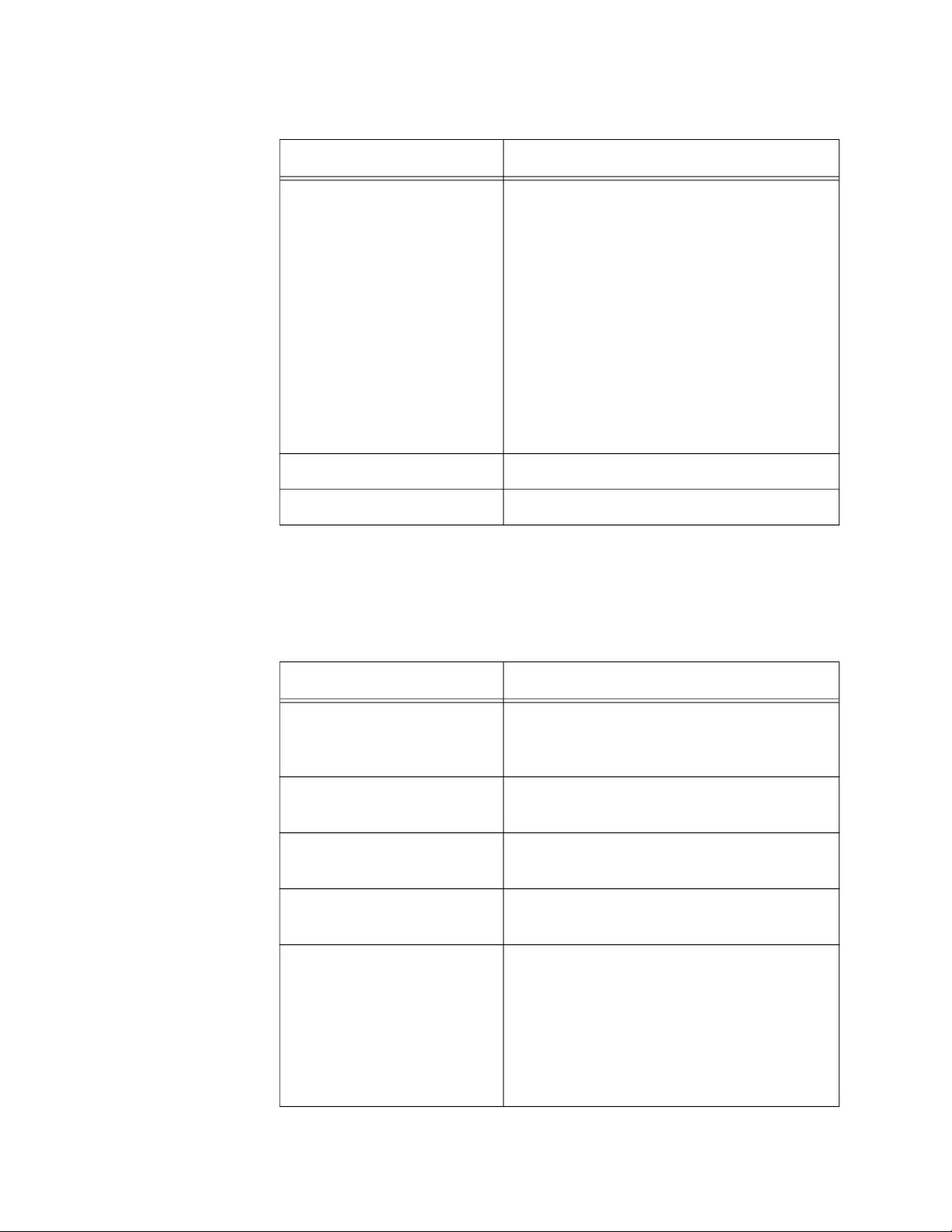
Chapter 2: XEM2 Ethernet Line Cards
56
Twisted Pair Port
LEDs
Each port has a single LED that displays link and activity information. The
states of LEDs are described in Table 17.
Cabling Minimum cable requirements are:
- 100Mbps - Standard TIA/EIA 568-B-
compliant Category 3 unshielded
cabling.
- 1/2.5/5Gbps - Standard TIA/EIA 568-A-
compliant Category 5 or TIA/EIA 568-B-
compliant Enhanced Category 5 (Cat
5e) unshielded cabling.
- 10Gbps -Standard TIA/EIA 568-C-
compliant Category 6a unshielded
cabling.
Maximum Distance 100 meters (328 feet)
Connector 8-pin RJ-45
Table 16. Twisted Pair Ports on the XEM2-8XSTm Line Card (Continued)
Specification Description
Table 17. Link and Activity LEDs for the Twisted Pair Ports on the XEM2-
8XSTm Line Card
State Description
Solid Green The port has established a 2.5Gbps,
5Gbps, or 10Gbps link to a network
device.
Flashing Green The port is transmitting or receiving data
at 2.5Gbps, 5Gbps, or 10Gbps.
Solid Amber The port has established a 100Mbps or
1Gbps link to a network device.
Flashing Amber The port is transmitting or receiving data
at 100Mbps or 1Gbps.
Off Possible causes of this state are listed
here:
- The port has not established a link with
another network device.
- The LEDs are turned off. To turn on the
LEDs, use the eco-friendly button.
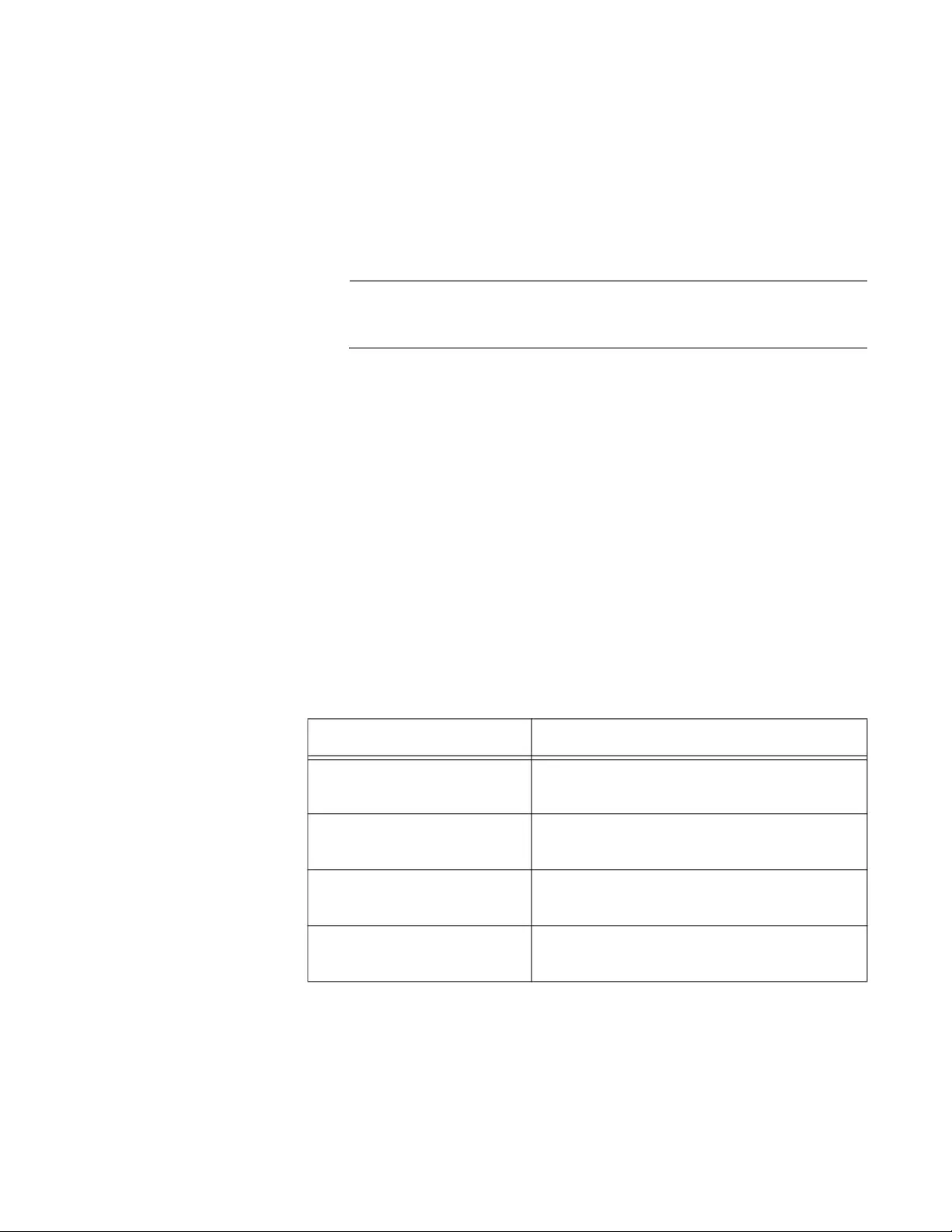
x950 Series Installation Guide for VCStack
57
Transceivers
Ports
The XEM2-8XSTm Card also has four transceiver ports that support the
following types of 1Gbps SFP or 10Gbps SFP+ transceivers:
1Gbps SX or LX SFP fiber optic transceivers
10Gbps SR or LR SFP+ fiber optic transceivers
10Gbps one meter SP10TW1 and three meter SP10TW3 direct
connect twinax cables, with SFP+ transceiver-style connectors
Note
The XEM2-8XSTm Card does not support the seven meter
SP10TW7 direct connect cable.
Guidelines about the SFP+ transceiver ports are listed here:
The ports do not support 100Mbps transceivers.
The ports support full-duplex mode only.
You can set the port speeds with Auto-Negotiation or manually.
The default is Auto-Negotiation.
SFP and SFP+ transceivers are purchased separately. For a list of
supported transceivers, refer to the SBx908 GEN2 Series data sheet on
the Allied Telesis web site.
Transceivers Port
LEDs
The ports have link and activity LEDs. The states of the LEDs are
described in Table 18.
Table 18. Link and Activity LEDs for the SFP Ports on the XEM2-8XSTm
Line Card
State Description
Solid Green The transceiver in the slot has established
a 10GBase link to a network device.
Flashing Green The transceiver is transmitting or receiving
data at 10GBase.
Solid Amber The transceiver has established a 1GBase
link to a network device.
Flashing Amber The transceiver is transmitting or receiving
data at 1GBase.
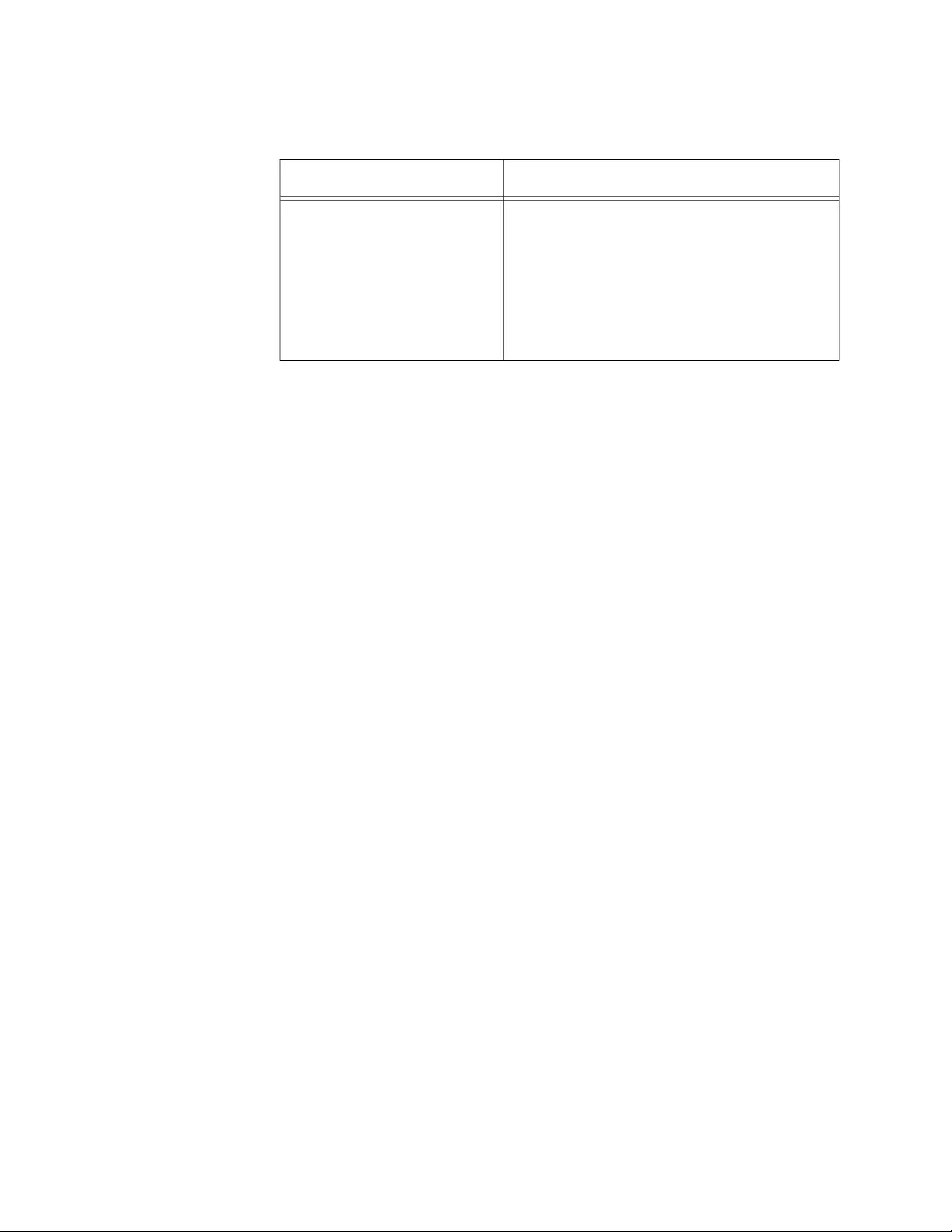
Chapter 2: XEM2 Ethernet Line Cards
58
Off Possible causes of this state are listed
here:
- The transceiver has not established a
link with another network device.
- The LEDs are turned off. To turn on the
LEDs, use the eco-friendly button.
Table 18. Link and Activity LEDs for the SFP Ports on the XEM2-8XSTm
Line Card (Continued)
State Description
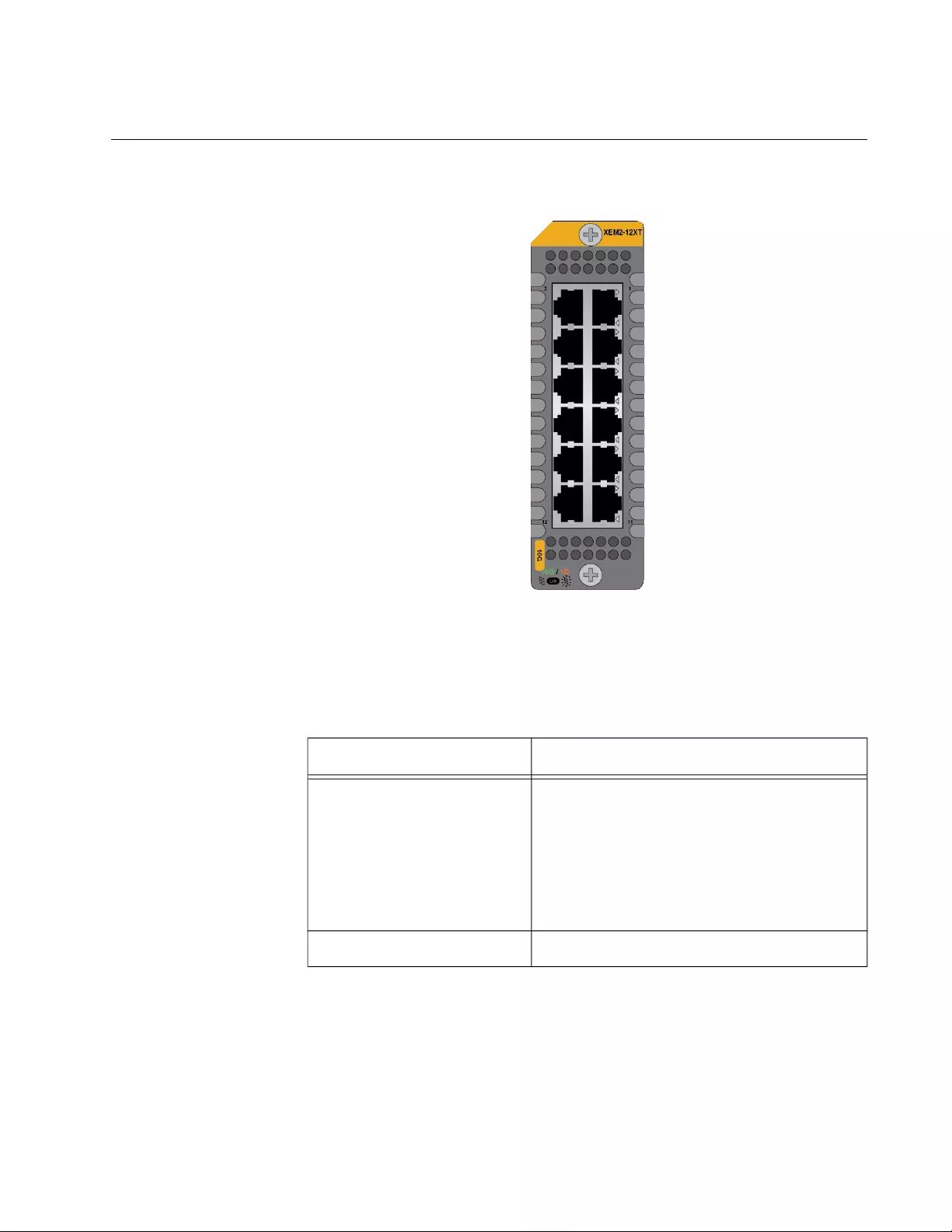
x950 Series Installation Guide for VCStack
59
XEM2-12XT Line Card
The XEM2-12XT Line Card is shown in Figure 21.
Figure 21. XEM2-12XT Line Card
Twisted Pair
Ports
The card has 12 twisted pair ports with standard 8-pin RJ-45 ports. The
specifications of the ports are listed in Table 19.
Table 19. Twisted Pair Ports on the XEM2-12XT Line Card
Specification Description
Port Speed The ports support the following speeds:
- 100Mbps (Requires AlliedWare Plus
v5.4.9-0 or later)
- 1/10Gbps
The ports do not support 10Mbps.
Duplex Mode Full-duplex only
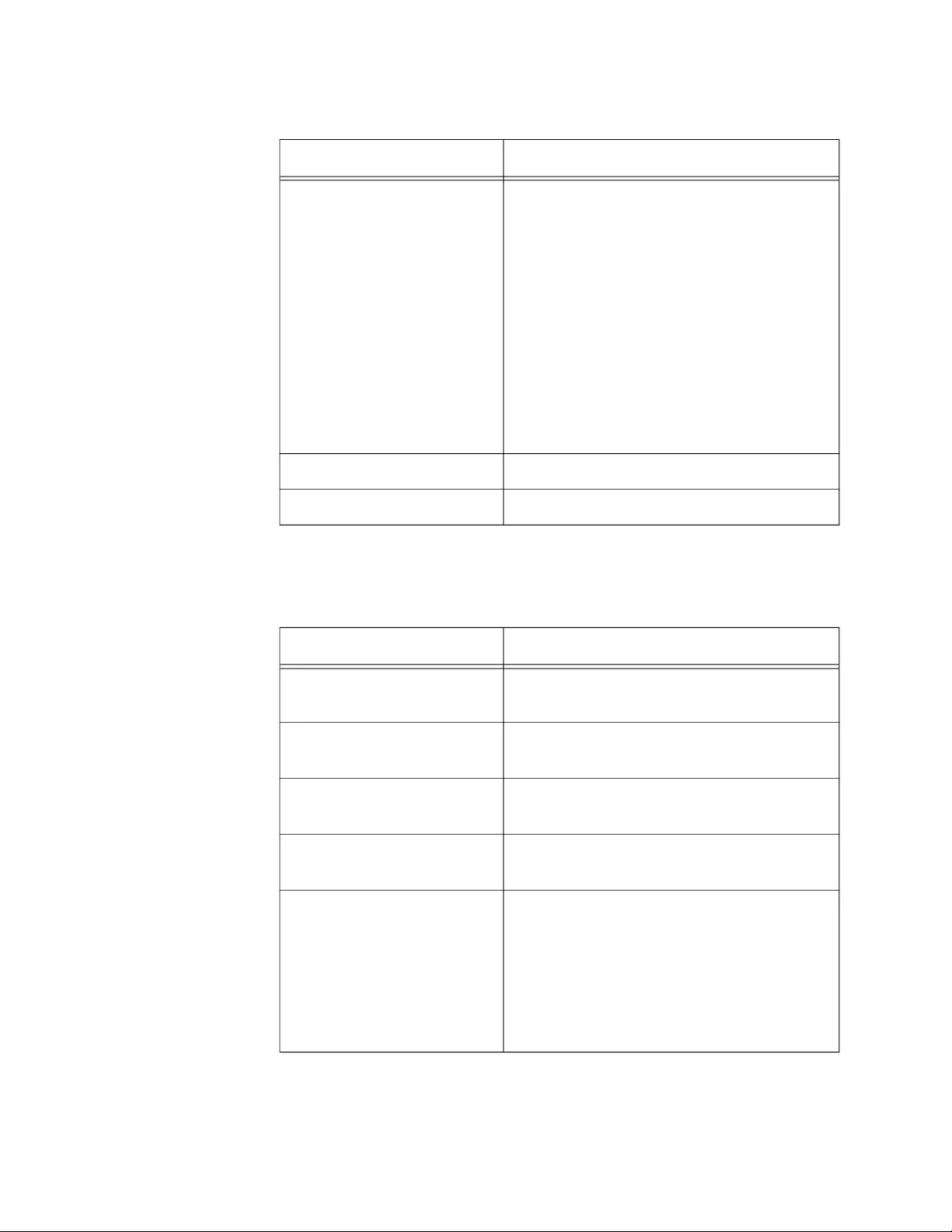
Chapter 2: XEM2 Ethernet Line Cards
60
LEDs Each port has a single LED that displays link and activity information.
Refer to Table 20.
Cabling The minimum cable requirements are:
- 100Mbps - Standard TIA/EIA 568-B-
compliant Category 3 unshielded
cabling.
- 1Gbps - Standard TIA/EIA 568-A-
compliant Category 5 or TIA/EIA 568-B-
compliant Enhanced Category 5 (Cat 5e)
unshielded cabling.
- 10Gbps -Standard TIA/EIA 568-C-
compliant Category 6a unshielded
cabling.
Maximum Distance 100 meters (328 feet)
Connector 8-pin RJ-45
Table 19. Twisted Pair Ports on the XEM2-12XT Line Card (Continued)
Specification Description
Table 20. Port Link and Activity LEDs on the XEM2-12XT Line Card
State Description
Solid Green The port has established a 10GBase link
to a network device.
Flashing Green The port is transmitting or receiving data
at 10GBase.
Solid Amber The port has established a 100Mbps or
1GBase link to a network device.
Flashing Amber The port is transmitting or receiving data
at 100Mbps or 1GBase.
Off Possible causes of this state are listed
here:
- The port has not established a link with
another network device.
- The LEDs are turned off. To turn on the
LEDs, use the eco-friendly button.
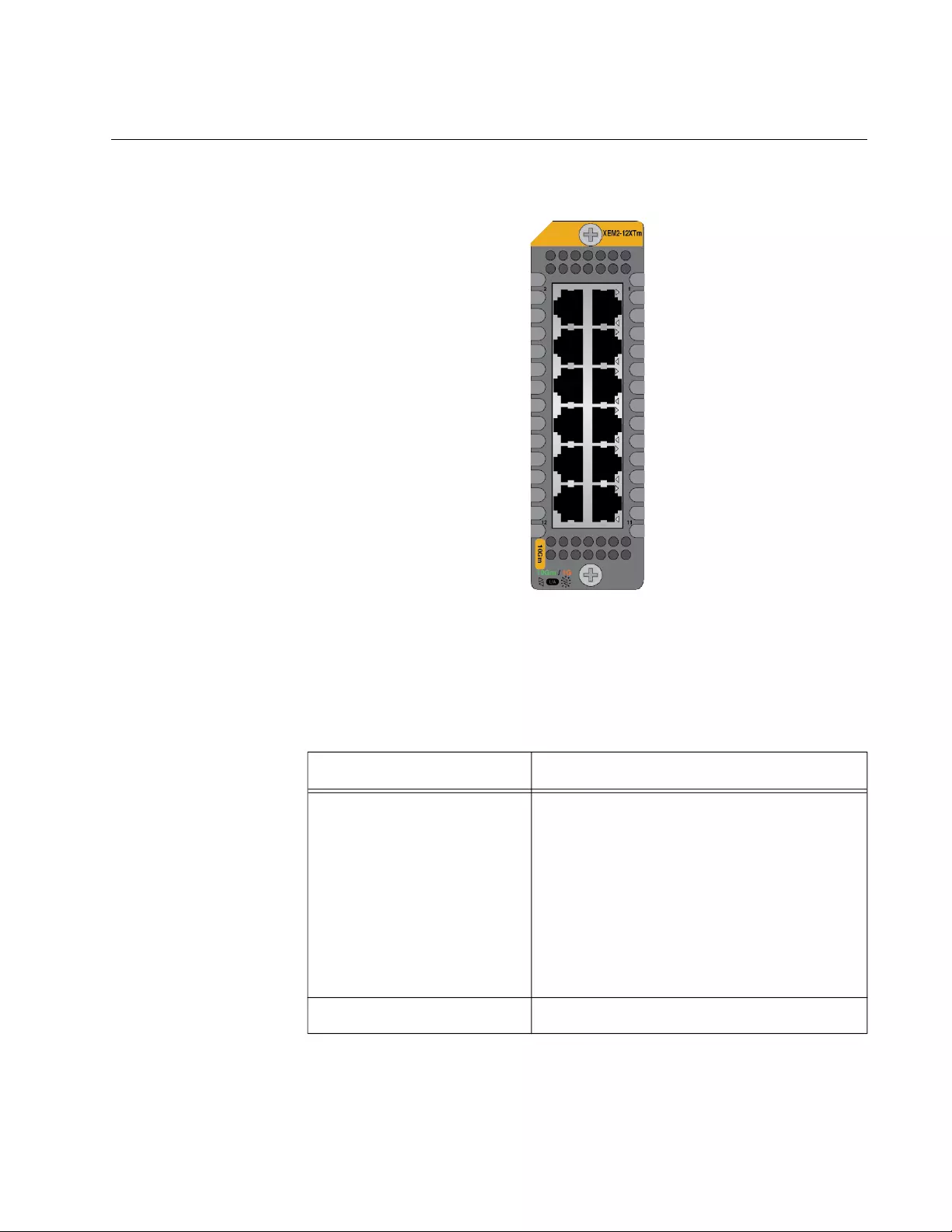
x950 Series Installation Guide for VCStack
61
XEM2-12XTm Line Card
The XEM2-12XTm Card is shown in Figure 22.
Figure 22. XEM2-12XTm Line Card
Twisted Pair
Ports
The XEM2-12XTm Card has 12 twisted pair ports with standard 8-pin RJ-
45 ports. The specifications of the ports are listed in Table 21.
Table 21. Twisted Pair Ports on the XEM2-12XTm Line Card
Specification Description
Port Speed The ports support the following speeds:
- 100Mbps
- 1/2.5/5/10Gbps
The ports do not support 10Mbps.
You can set port speed with Auto-
Negotiation or manually. The default is
Auto-Negotiation.
Duplex Mode Full-duplex only.
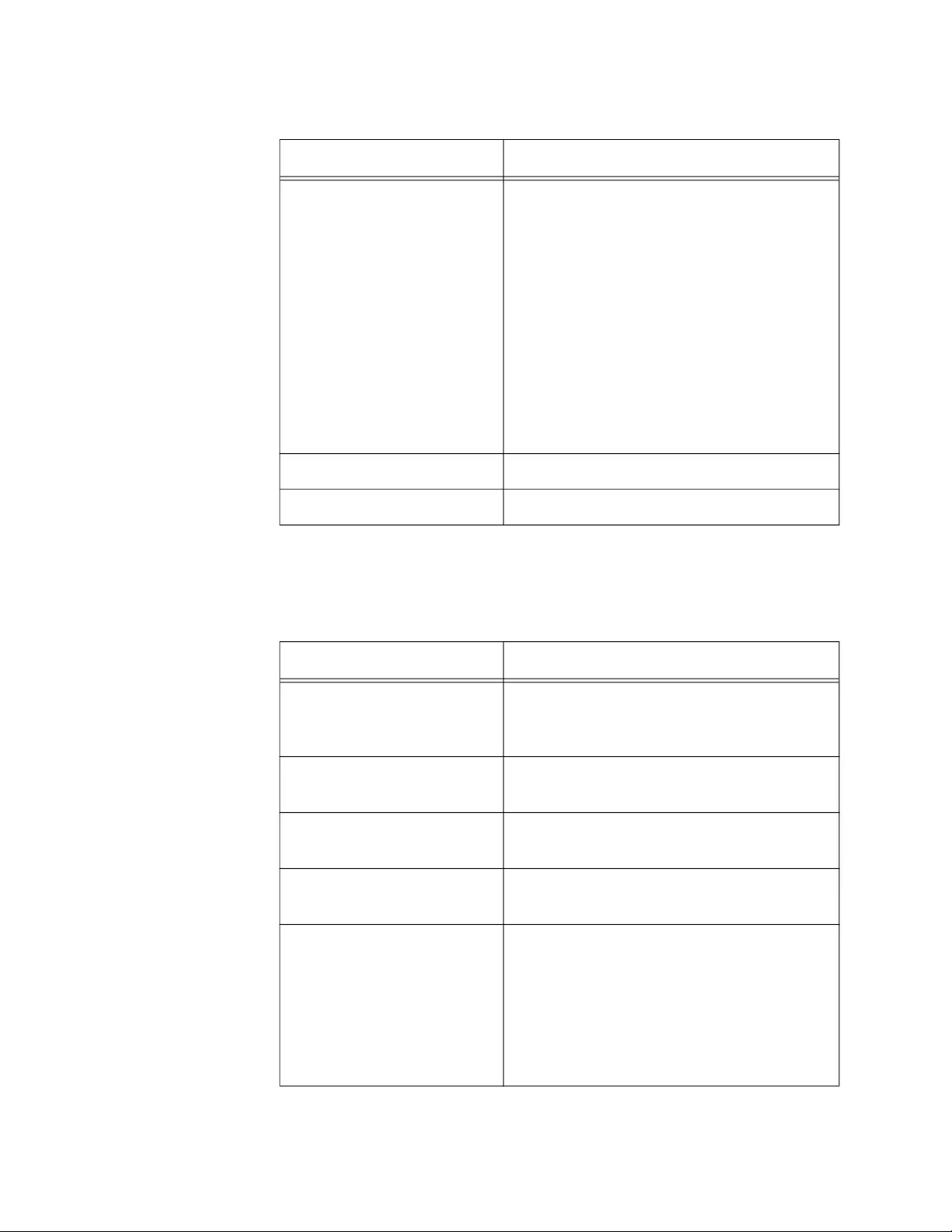
Chapter 2: XEM2 Ethernet Line Cards
62
LEDs Each port has a single LED that displays link and activity information. The
states of LEDs are described in Table 22.
Cabling Cable minimum requirements are:
- 100Mbps - Standard TIA/EIA 568-B-
compliant Category 3 unshielded
cabling.
- 1/2.5/5Gbps - Standard TIA/EIA 568-A-
compliant Category 5 or TIA/EIA 568-B-
compliant Enhanced Category 5 (Cat
5e) unshielded cabling.
- 10Gbps -Standard TIA/EIA 568-C-
compliant Category 6a unshielded
cabling.
Maximum Distance 100 meters (328 feet)
Connector 8-pin RJ-45
Table 21. Twisted Pair Ports on the XEM2-12XTm Line Card (Continued)
Specification Description
Table 22. Link and Activity LEDs on the XEM2-12XTm Line Card
State Description
Solid Green The port has established a 2.5Gbps,
5Gbps, or 10Gbps link to a network
device.
Flashing Green The port is transmitting or receiving data
at 2.5Gbps, 5Gbps, or 10Gbps.
Solid Amber The port has established a 100Mbps or
1GBase link to a network device.
Flashing Amber The port is transmitting or receiving data
at 100Mbps or 1GBase.
Off Possible causes of this state are listed
here:
- The port has not established a link with
another network device.
- The LEDs are turned off. To turn on the
LEDs, use the eco-friendly button.
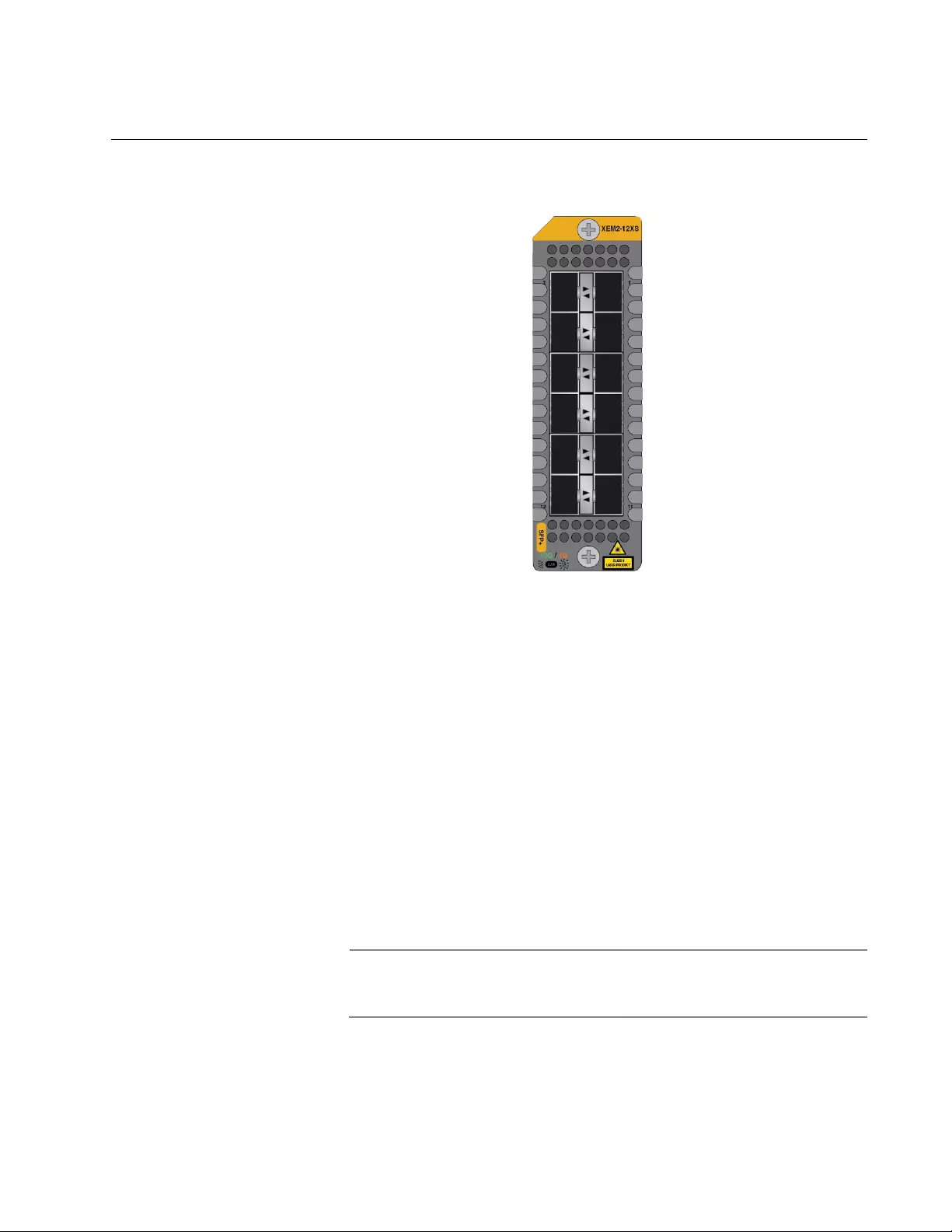
x950 Series Installation Guide for VCStack
63
XEM2-12XS and XEM2-12XS v2 Line Cards
The XEM2-12XS Line Card is shown in Figure 23.
Figure 23. XEM2-12XS Line Card
Transceiver Ports The card has twelve ports that support the following types of 1Gbps SFP,
10Gbps SFP+, and 1/2.5/5/10Gbps transceivers with RJ-45 connectors:
1Gbps SX or LX SFP transceivers
10Gbps SR or LR fiber optic transceivers
10Gbps one meter SP10TW1, three meter SP10TW3, and seven
meter SP10TW7 direct connect twinax cables with SFP+
transceiver-style connectors
1Gbps SPTX transceivers with RJ-45 ports for twisted pair cable
1Gbps/10Gbps SP10T transceivers with RJ-45 ports for twisted
pair cable
1Gbps/2.5Gbps/5Gbps/10Gbps SP10TM transceivers with RJ-45
ports for twisted pair cable
Note
The XEM2-12XS v2 Card does not support the seven meter
SP10TW7 cable.
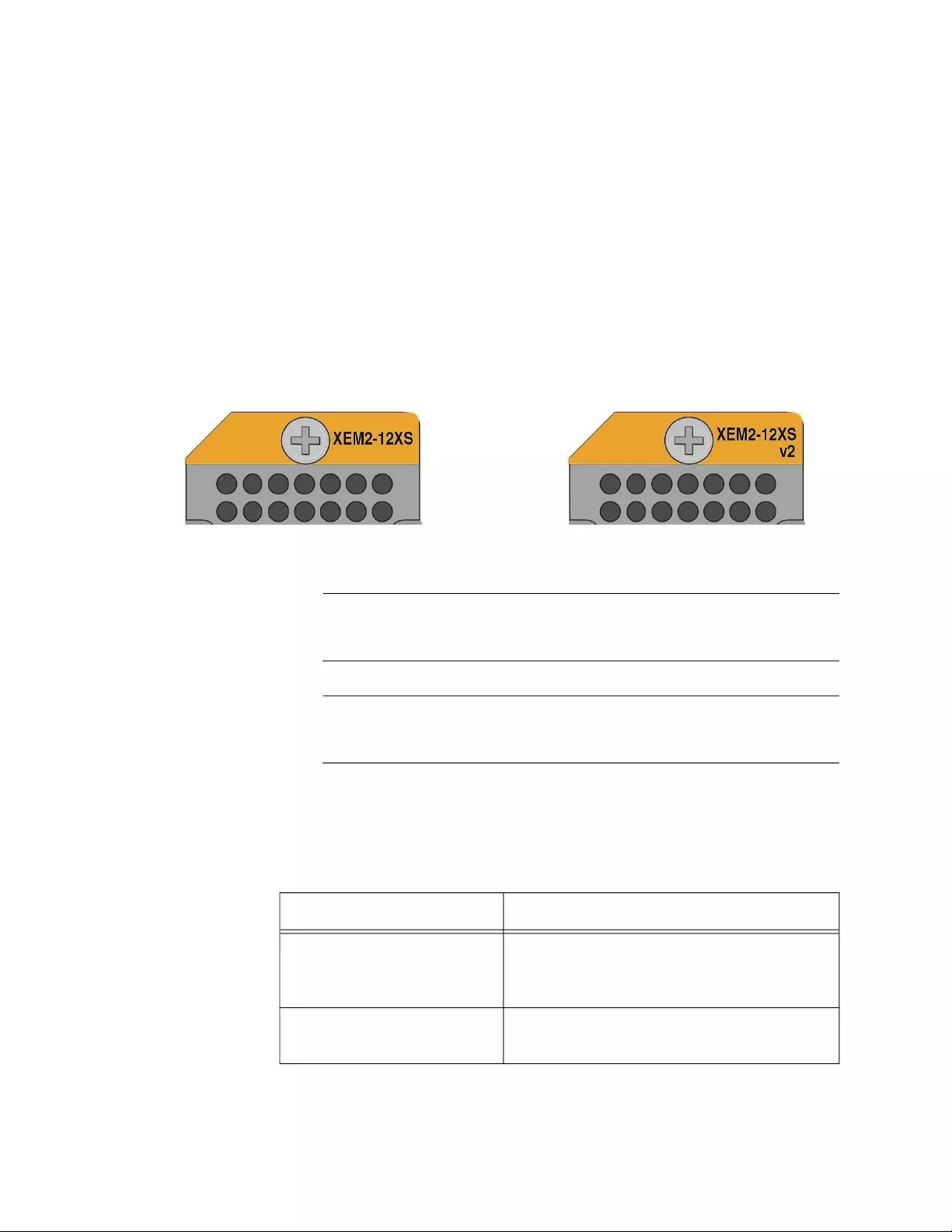
Chapter 2: XEM2 Ethernet Line Cards
64
Guidelines about the ports are listed here:
They do not support 100Mbps transceivers.
They support full-duplex mode only.
You can set the port speeds with Auto-Negotiation or manually.
The default is Auto-Negotiation.
SFP or SFP+ transceivers are purchased separately. For a list of
supported transceivers, refer to the x950 Switches data sheet on the Allied
Telesis web site.
Card Versions There are two versions of the XEM2-12XS Line Card. Their names are
“XEM2-12XS” and “XEM2-12XS v2.” Refer to Figure 24.
Figure 24. XEM2-12XS and XEM2-12XS v2 Line Cards
Note
The XEM2-12XS v2 Line Card requires AlliedWare Plus v5.4.9-2 or
later.
Note
Unless stated otherwise, the “XEM2-12XS” model name in this
manual refers to both cards.
LEDs The ports have link and activity LEDs. The LED states are described in
Table 23.
Table 23. Port Link and Activity LEDs on the XEM2-12XS Line Card
State Description
Solid Green The transceiver has established a
2.5Gbps, 5Gbps, or 10GBase link to a
network device.
Flashing Green The transceiver is transmitting or receiving
data at 2.5Gbps, 5Gbps, or 10Gbps.
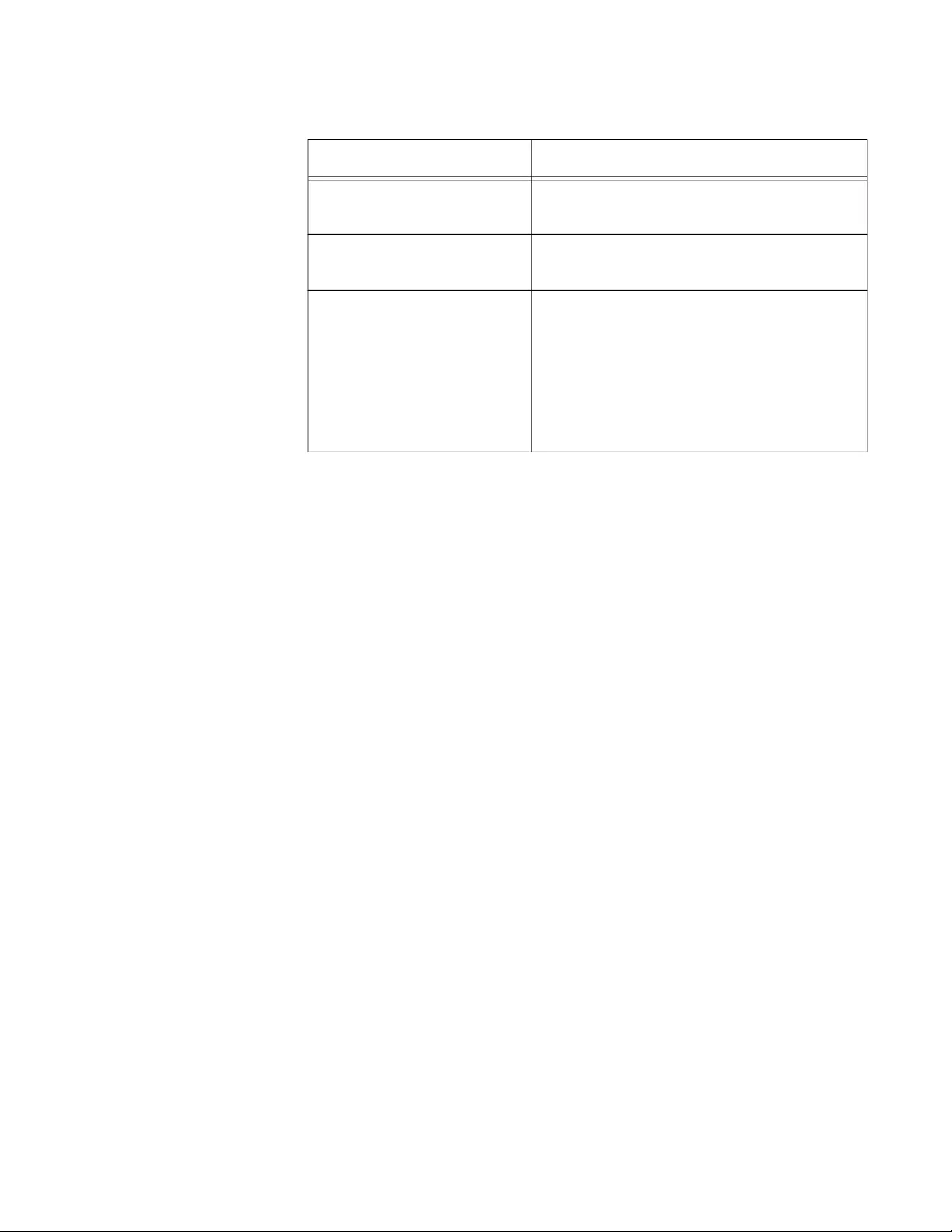
x950 Series Installation Guide for VCStack
65
Solid Amber The transceiver has established a 1GBase
link to a network device.
Flashing Amber The transceiver is transmitting or receiving
data at 1GBase.
Off Possible causes of this state are listed
here:
- The transceiver has not established a
link with another network device.
- The LEDs are turned off. To turn on the
LEDs, use the eco-friendly button.
Table 23. Port Link and Activity LEDs on the XEM2-12XS Line Card
State Description
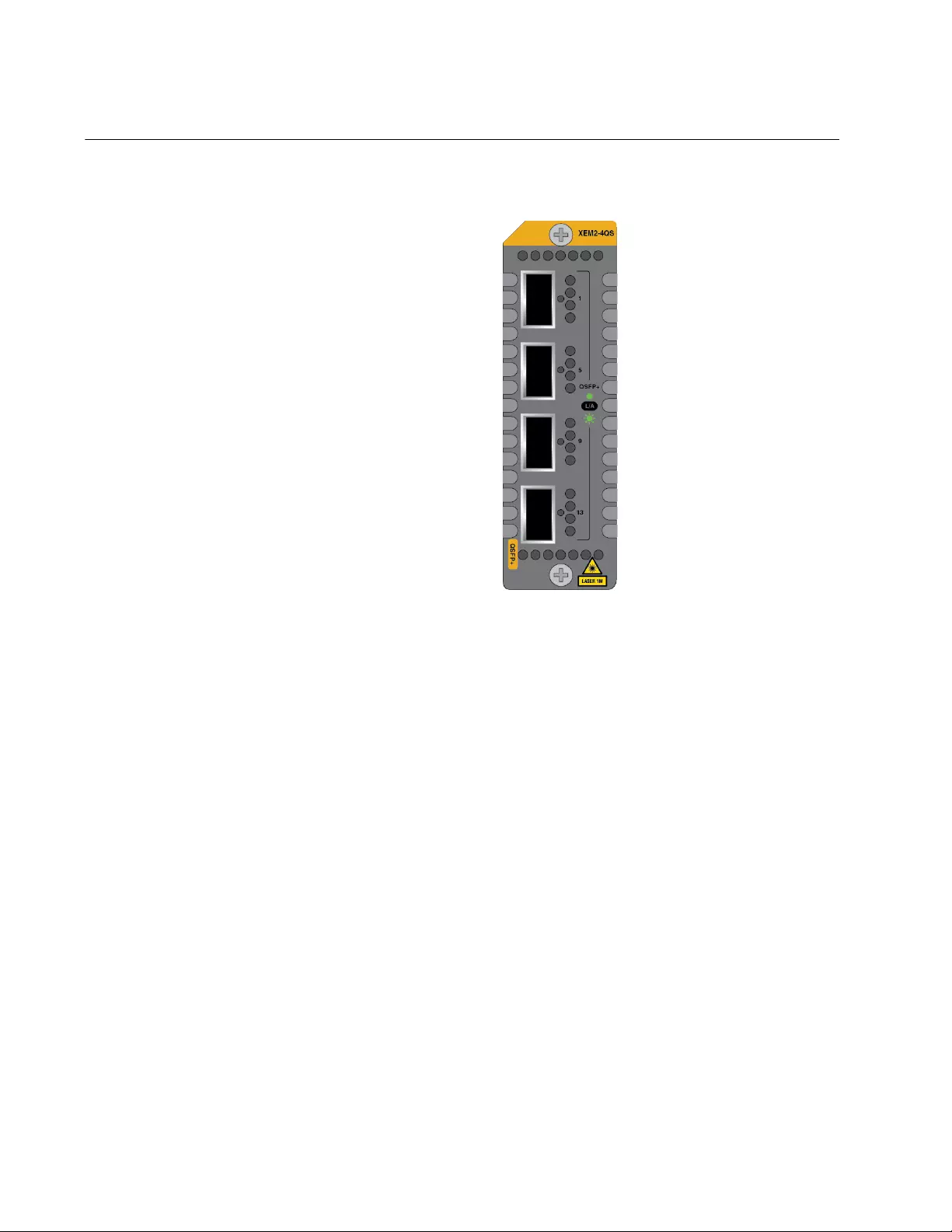
Chapter 2: XEM2 Ethernet Line Cards
66
XEM2-4QS Line Card
The XEM2-4QS Line Card is shown in Figure 25.
Figure 25. XEM2-4QS Line Card
Transceiver Ports The card supports the following types of 40Gbps QSFP+ transceivers in
its four ports:
QSFPSR4 transceiver - Maximum operating distance of 150
meters (492 feet) with 12-strand OM4 fiber optic cable.
QSFPLR4 transceiver - Operating range of 2 meters (6.6 feet) to
10 kilometers (6.2 miles) with single-mode fiber optic cable.
QSFP1CU and QSFP3CU direct attach cables - Lengths of 1 and
3 meters, respectively.
QSFP-4SFP10G-3CU and QSFP-4SFP10G-5CU 40Gbps to
10Gbps breakout cables in lengths of 3 and 5 meters, respectively.
Refer to “Breakout Cables” on page 29 for more information.
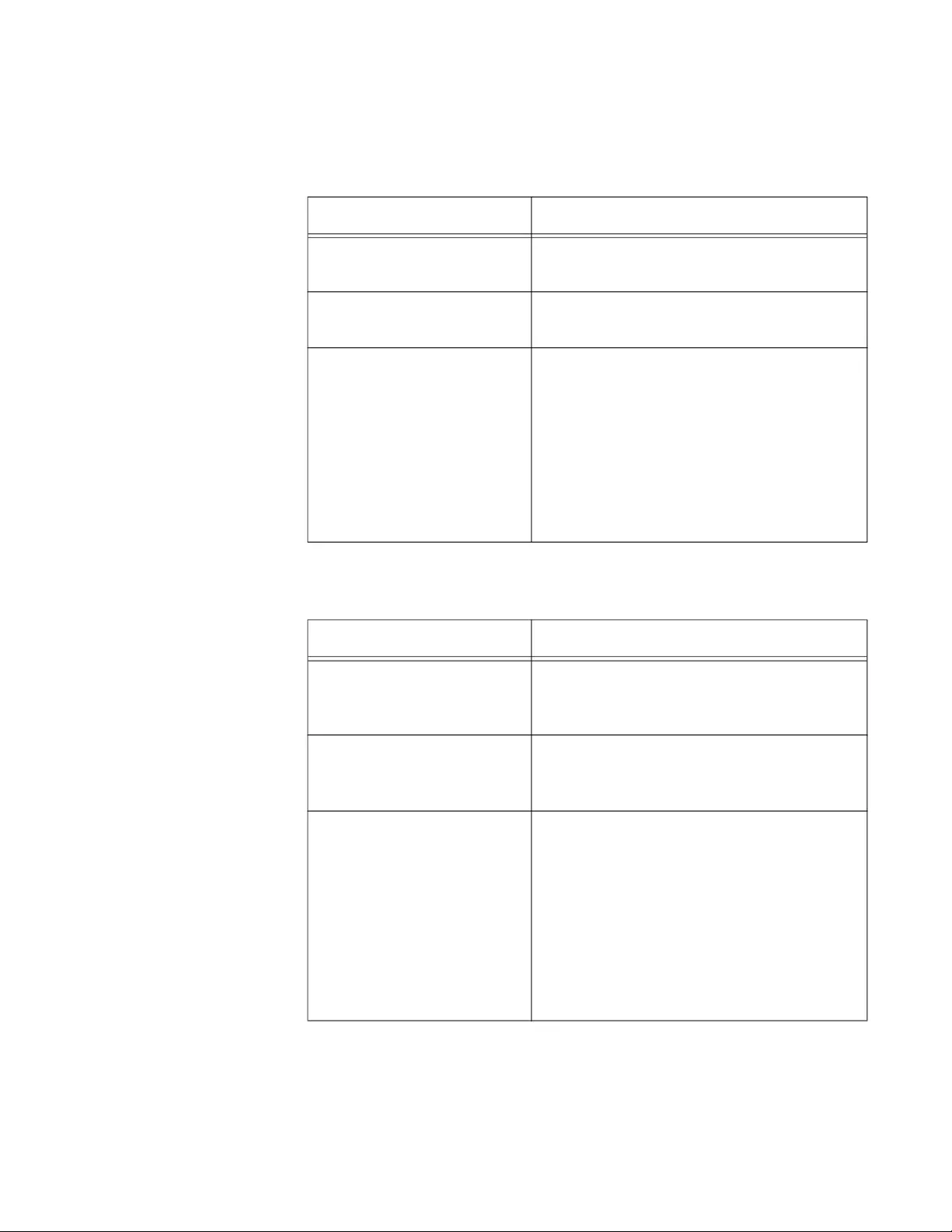
x950 Series Installation Guide for VCStack
67
LEDs The LED states for transceivers or direct attach cables in ports on the
XEM2-4QS Line Card are described in Table 24.
The LED states for breakout cables are described in Table 25.
Table 24. Port Link and Activity Status LEDs on the XEM2-4QS Line Card
State Description
Solid Green The transceiver has established a
40GBase link to a network device.
Flashing Green The transceiver is transmitting or receiving
data.
Off Possible causes of this state are listed
here:
- The transceiver slot is empty.
- The transceiver has not established a
link to a network device.
- The LEDs are turned off. To turn on the
LEDs, use the eco-friendly button.
Table 25. Link and Activity Status LEDs for 10Gbps Breakout Cables
State Description
Solid Amber At least one of the four ports on the
breakout cable has established a 10Gbps
link to a network device.
Flashing Amber At least one of the four ports on the
breakout cable is sending or receiving
data.
Off Possible causes of this state are listed
here:
- The transceiver slot is empty.
- None of the ports on the breakout cable
have established a link to a network
device.
- The LEDs are turned off. To turn on the
LEDs, use the eco-friendly button.
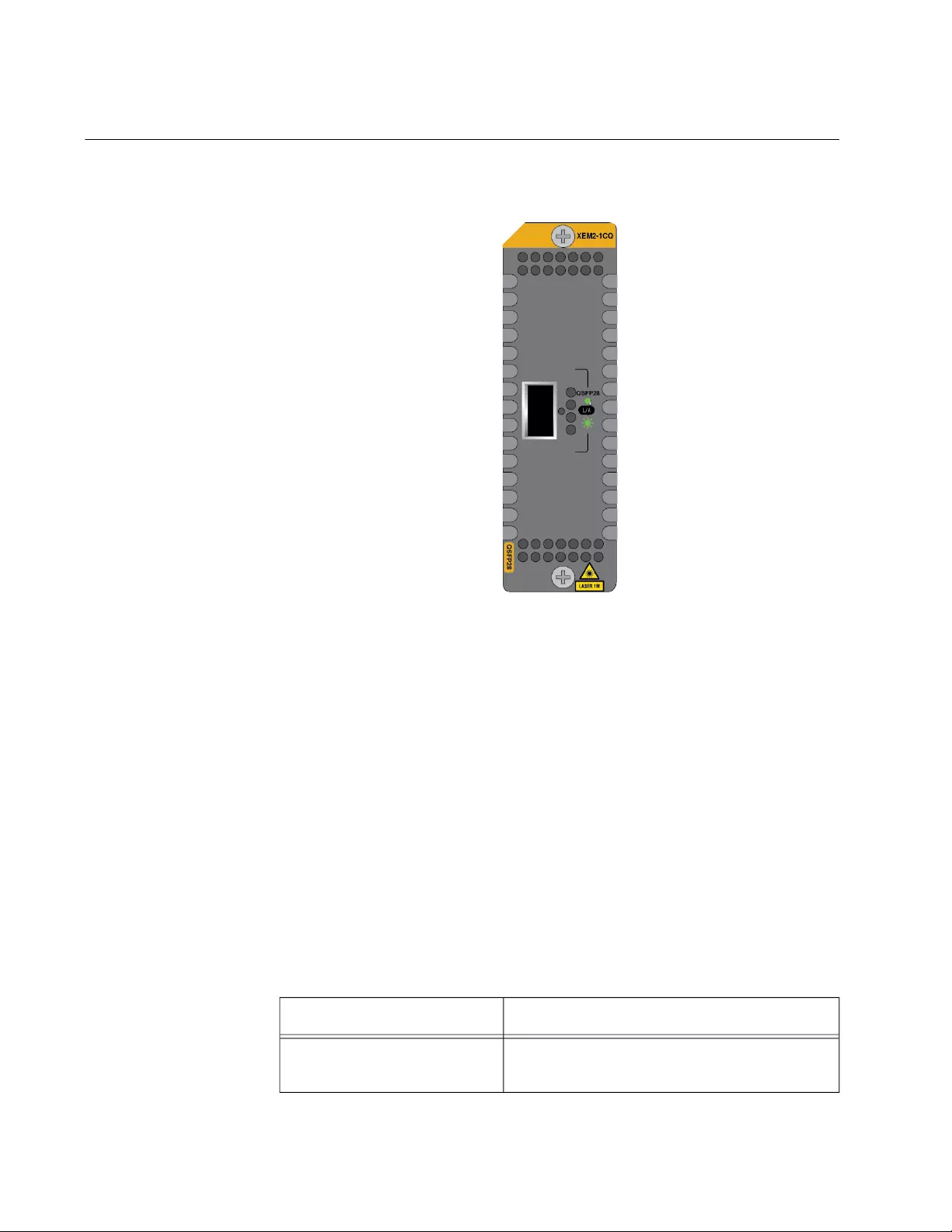
Chapter 2: XEM2 Ethernet Line Cards
68
XEM2-1CQ Line Card
The XEM2-1CQ Line Card is shown in Figure 26.
Figure 26. XEM2-1CQ Line Card
Transceiver Port The one port on the card supports the following 100Gbps QSFP28
transceivers:
QSFP28SR4 transceiver - Maximum operating distance of 70m
(230 ft) or 100m (328 ft) with 12-strand OM3 or OM4 fiber optic
cable, respectively. Requires a MPO pluggable optical connector.
QSFP28LR4 transceiver - Operating range of 2m (6.6 ft) to 10km
(6.2 mi). Requires single-mode fiber optic cable with a duplex LC
connector.
QSFP28-1CU and QSFP28-3CU direct attach cables - Lengths of
one and three meters, respectively.
LED The LED states for the port in the XEM2-1CQ Line Card are described in
Table 26.
Table 26. Port Link and Activity Status LED on the XEM2-1CQ Line Card
State Description
Solid Green The transceiver has established a link to a
network device.
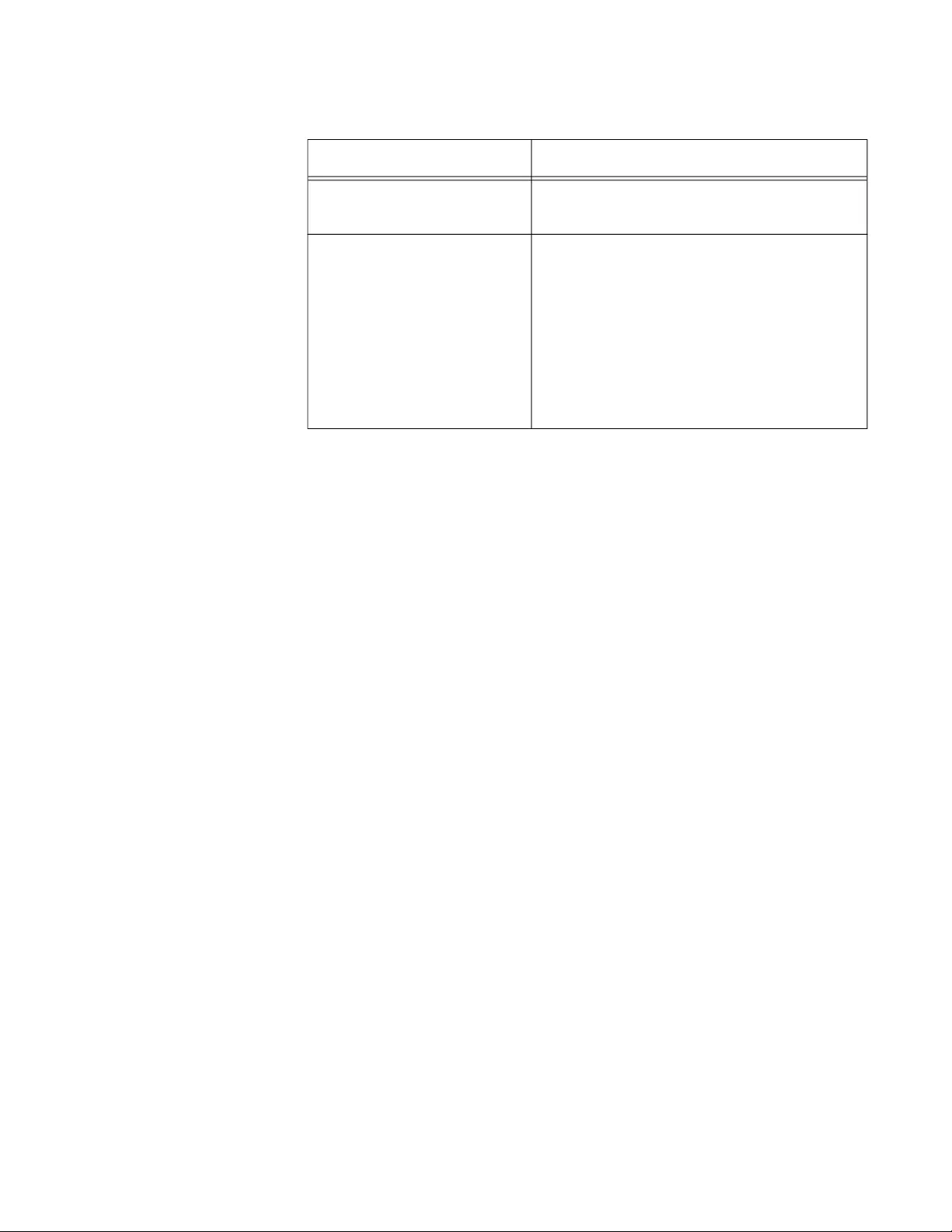
x950 Series Installation Guide for VCStack
69
Flashing Green The transceiver is transmitting or receiving
data.
Off Possible causes of this state are listed
here:
- The transceiver slot is empty.
- The transceiver has not established a
link to a network device.
- The LEDs are turned off. To turn on the
LEDs, use the eco-friendly button.
Table 26. Port Link and Activity Status LED on the XEM2-1CQ Line Card
State Description
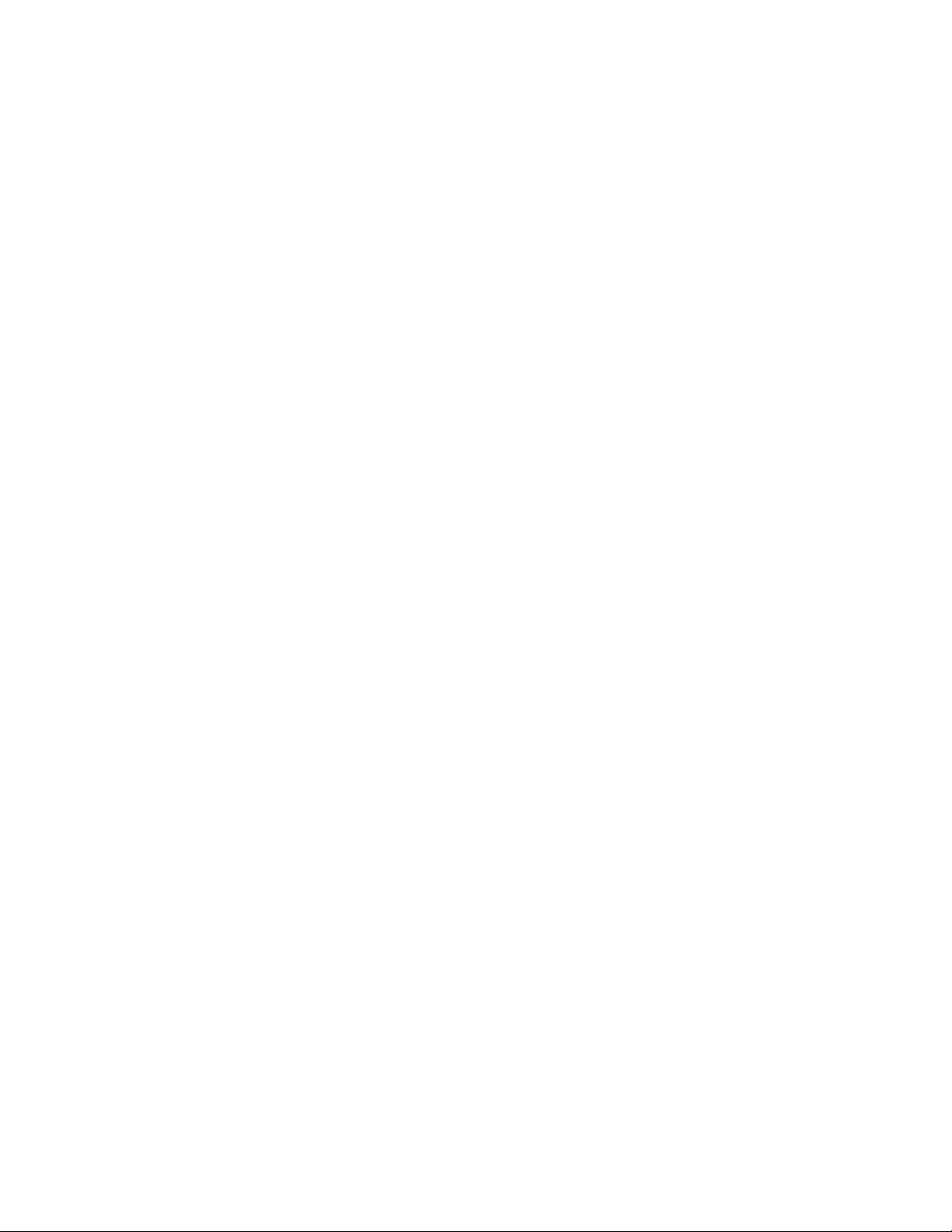
Chapter 2: XEM2 Ethernet Line Cards
70
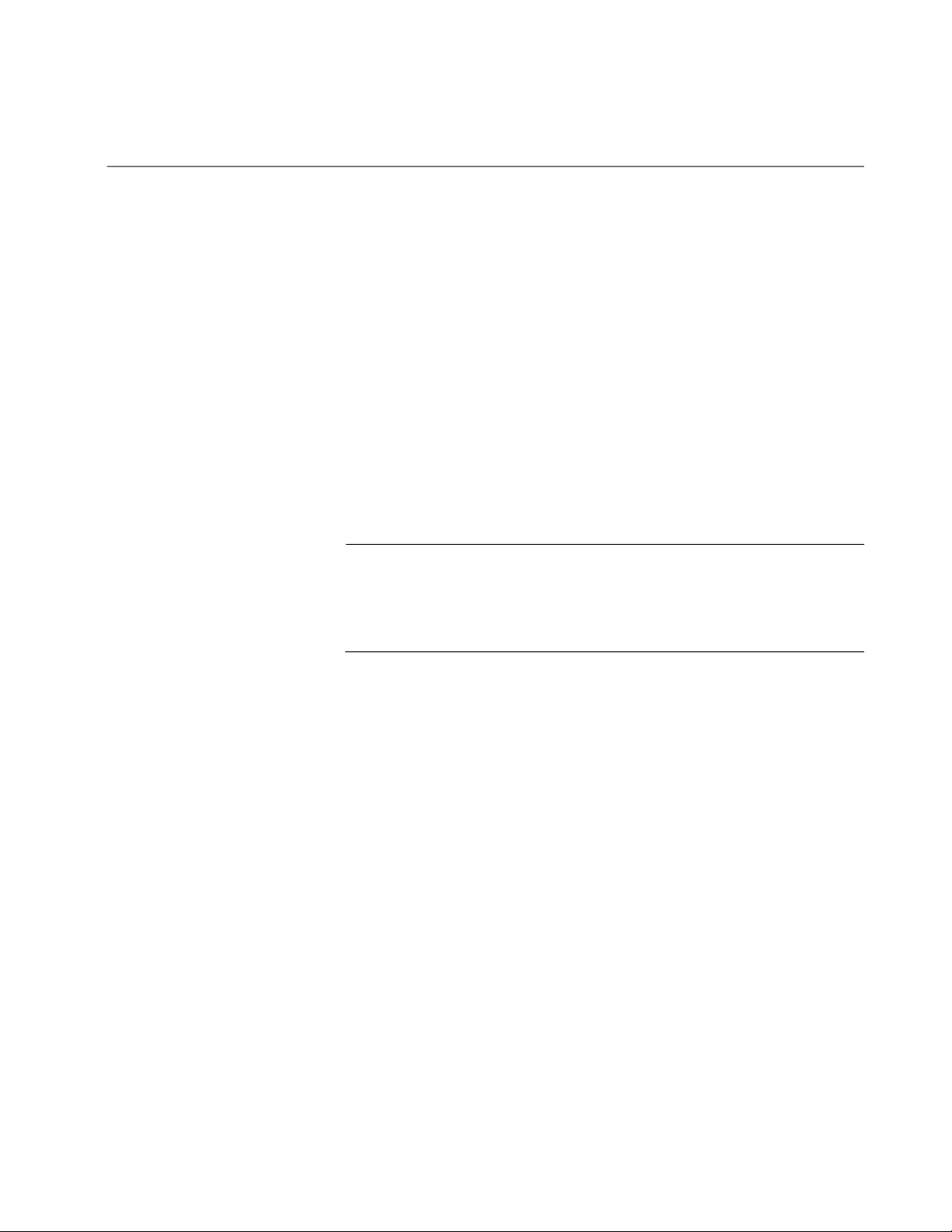
71
Chapter 3
Virtual Chassis Stacking
The sections in this chapter are listed here:
“Overview” on page 72
“Stacking Guidelines” on page 73
“Stack Trunks” on page 74
“Master and Member Switches” on page 89
“Switch ID Numbers” on page 90
“Optional Feature Licenses” on page 91
“Planning a Stack” on page 92
“Stacking Worksheet” on page 93
Note
For more information on VCStack, refer to the Stacking Introduction
and Stacking Commands chapters in the Software Reference for
x950 Series Switches, AlliedWare Plus Operating System from
www.alliedtelesis.com/support.
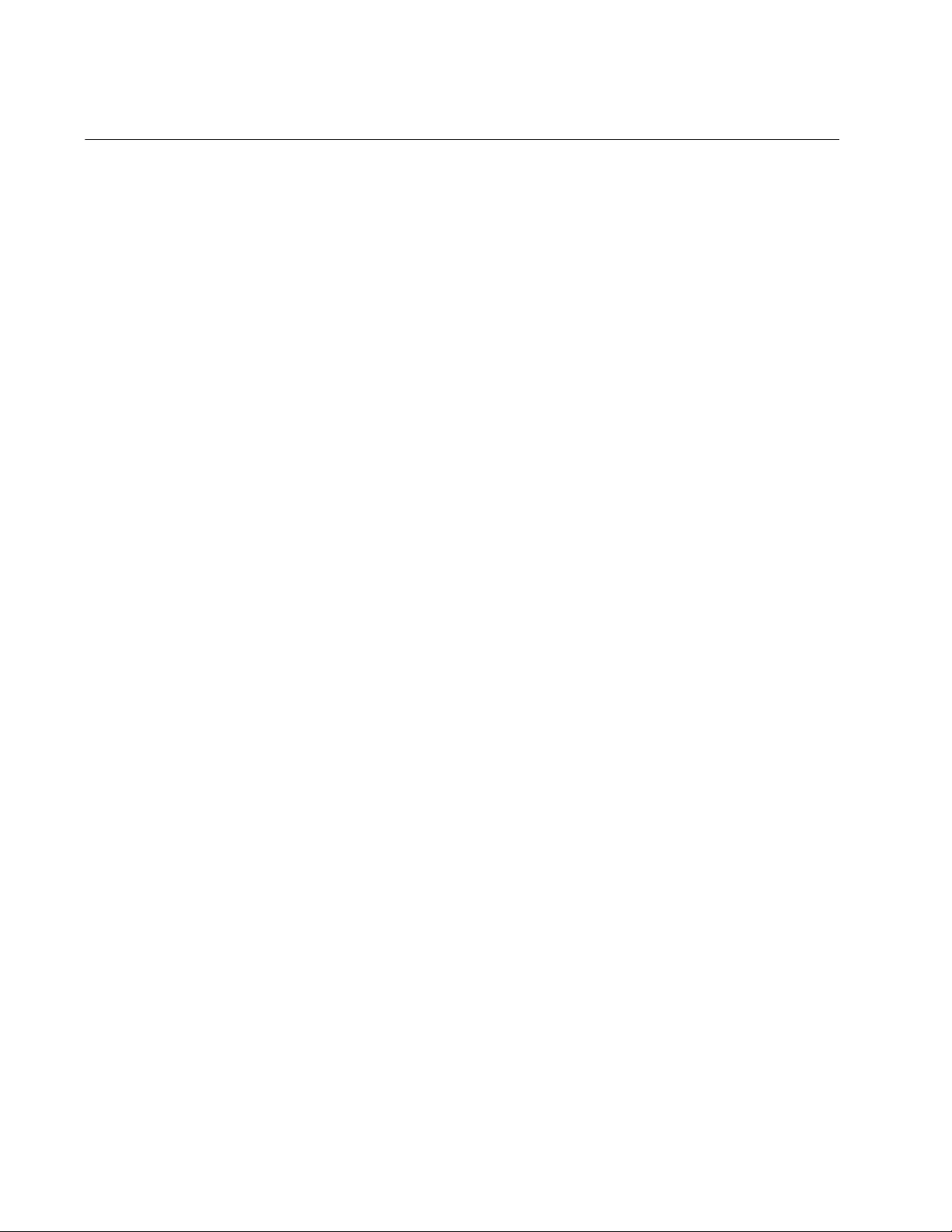
Chapter 3: Virtual Chassis Stacking
72
Overview
The Virtual Chassis Stacking (VCStack) feature enables you link together
up to four x950 Switches into a virtual stack so that they function as a
single networking unit. The feature provides the following benefits:
Simplifies management - You can manage the devices as a single
unit, rather than individually. Your local and remote management
sessions automatically give you management access to all the
switches.
Reduces IP addresses - A stack requires only one IP address for
remote management access, reducing the number of IP addresses
you have to assign to network devices. The one address gives you
management access to all the stack units.
Adds feature flexibility and resiliency - Stacking gives you more
flexibility in how you can configure some features. For instance,
you can create port aggregations using ports from different
switches, rather than ports from only one switch. By distributing the
ports of an aggregation across multiple switches, you increase its
resiliency because the aggregation can continue to function,
though at a reduced bandwidth, even if a switch in a stack stops
functioning.
Reduces protocol requirements - Creating a stack might eliminate
the need to configure some protocols, such as the Virtual Router
Redundancy Protocol or Spanning Tree Protocol.
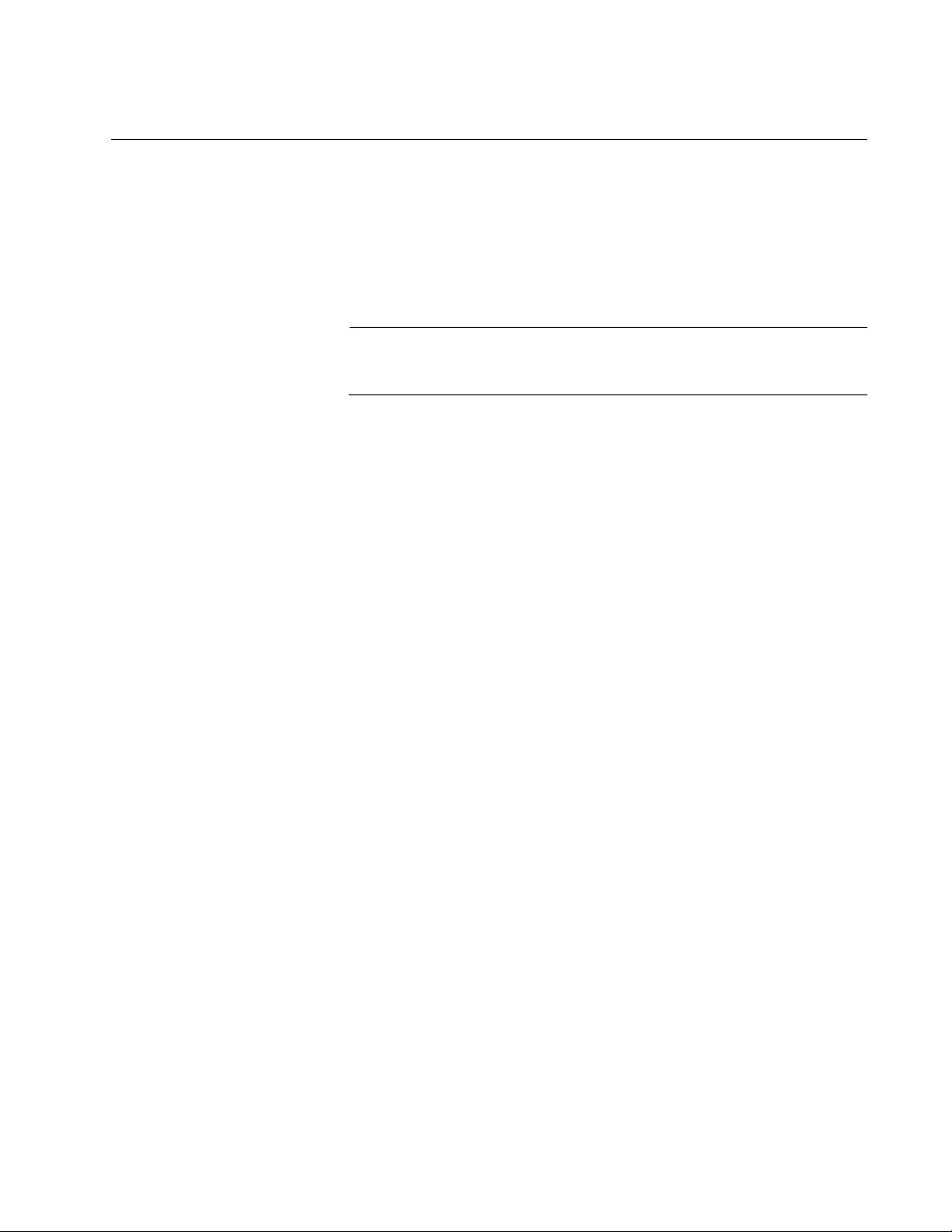
x950 Series Installation Guide for VCStack
73
Stacking Guidelines
Here are general stacking guidelines:
AlliedWare Plus v5.4.8-2 or later supports stacks of two switches.
AlliedWare Plus v5.4.9 or later supports stacks up to four switches.
AlliedWare Plus v5.4.9-2.3, v5.5.0 or later supports stacks up to
eight switches.
Note
Instructions later in this guide explain how to view the version
number of the operating software on the switches.
The VCStack feature comes standard with the AlliedWare Plus
operating software. No additional software or license is required.
The default setting for the VCStack feature on x950 Switches is
disabled. Enabling it requires rebooting the switch. Instructions
later in this guide explain how to enable the feature and reboot the
unit.
A stack can have x950-28XSQ, x950-28XTQm, and x950-52XSQ
switches.
The switches must have the same optional features licenses. If you
purchased optional features for the switches, you should install
them before assembling the stack.
The switches of a stack have to be connected together with a
network link called a stack trunk. As explained in “Stack Trunks” on
page 74, you can choose any ports on the switches to be the trunk.
Once ports are designated as members of the trunk, they cannot
be used as regular networking ports.
You should not pre-configure the features of the switches, such as
virtual LANs and spanning tree, before building the stack. The
configuration settings are likely to be discarded once the switches
begin operating as a stack.
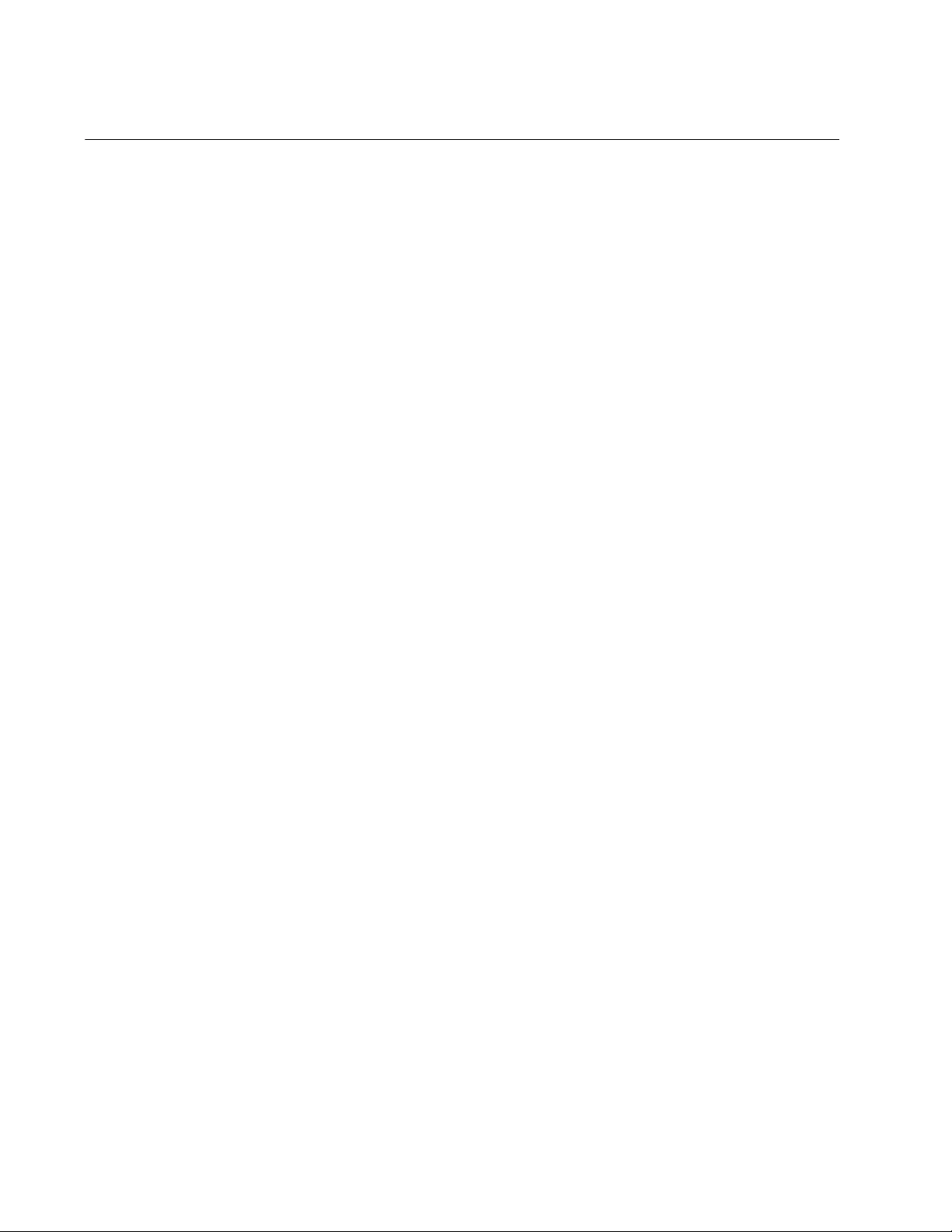
Chapter 3: Virtual Chassis Stacking
74
Stack Trunks
The switches of a stack are connected with a physical network link called
the stack trunk. Here are general trunk guidelines:
The ports of a trunk can be 10Gbps, 40Gbps, or 100Gbps.
A stack can have only one trunk.
A trunk can have multiple physical links between switches, for
added bandwidth and resiliency.
All the ports in the trunk must be the same speed.
There are no default trunk ports.
You designate trunk ports with the STACKPORT command in the
AlliedWare Plus operating system.
Once ports are designated as trunk ports, you cannot view or
change their parameter settings.
The fiber optic transceivers or direct attach cables of a trunk must
be from Allied Telesis. Transceivers or cables from other network
equipment providers might not perform properly as trunks. For a
list of supported transceivers, refer to the Allied Telesis web site.
A stack of x950 Switches cannot include other stacking products,
such as x600 Switches.
In most cases, a trunk should have a minimum of two physical links
between switches.
If a trunk fails for any reason, the switches operate as stand-alone
devices.
You can choose the ports of a trunk from the following groups on the x950
Switches:
“Ports 1 to 24 and Ports 1 to 48,” next
“Ports 25 to 37 and Ports 49 to 61 with 40Gbps Transceivers” on
page 79
“Ports 25 to 37 and Ports 49 to 61 with 100Gbps Transceivers” on
page 80
“XEM2 Line Cards” on page 82
Ports 1 to 24 and
Ports 1 to 48
Ports 1 to 24 on the x950-28XSQ switch and ports 1 to 48 on the
x950-52XSQ switch support 1/2.5/5/10Gbps SFP/SFP+ transceivers,
while ports 1 to 24 on the x950-28XTQm switch are twisted pair ports that
support 1/2.5/5/10Gbps. Even though the ports are different on these
switches, the rules to using them as a stack trunk are mainly the same.
Here are the guidelines:
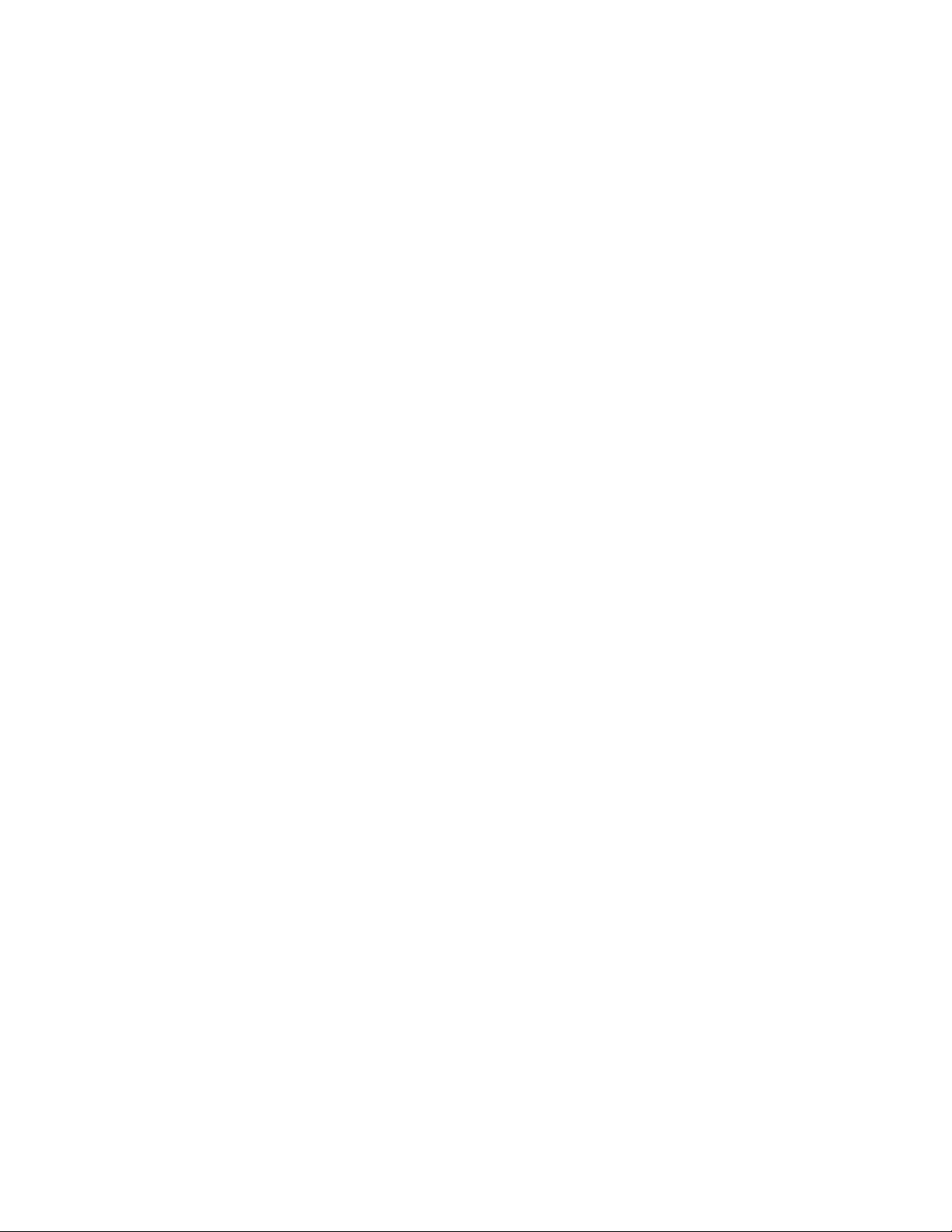
x950 Series Installation Guide for VCStack
75
The trunk can have up to eight ports per switch. The more ports in
the trunk, the greater its bandwidth and resiliency.
You can use any of the ports for the trunk.
There are no default trunk ports.
For the x950-28XTQm model, all the switches in the stack must be
the same x950-28XTQm model. To build stacks with the
x950-28XTQm model and the other two models, use ports 25, 29,
33, 37 or XEM2 Line Cards on the x950-28XSQ and
x950-28XTQm switches, or ports 49, 53, 57, 61 on the
x950-52XSQ switch.
For the x950-28XSQ and x950-52XSQ models, any combination of
two models can be in the stack.
Ports 1 to 24 in the x950-28XSQ switch and ports 1 to 48 on
x950-52XSQ switch support 1Gbps, 2.5Gbps, 5Gbps, and 10Gbps
transceivers. However, the transceivers for the trunk must be
10Gbps.
For a stack of x950-28XSQ and x950-52XSQ switches, the trunk
can consist of either 10Gbps fiber optic transceivers or, if the
switches are in the same or adjacent equipment racks, SP10TW
direct attach cables.
Ports 1 to 24 on the x950-28XTQm switch support 1/2.5/5/10Gbps.
Ports used in a trunk must operate at 10Gbps, in Auto-Negotiation.
In stacks of three of four switches, you have to connect the end
switches together to form a ring.
The following guidelines are not mandatory but they are recommended
because they can make managing or troubleshooting a trunk easier:
Use the same ports for the trunk on all the switches.
Choose consecutive ports (for example, ports 6 to 9).
When cabling the trunk links, connect together the same ports in
the switches, if possible.
Figure 27 on page 76 has examples of stacks of two, three, and four
x950-28XSQ Switches, with trunks of 10Gbps links. Here are the general
properties:
The trunks consist of four 10Gbps ports on each switch. (10Gbps
trunks can have up to eight ports per switch.)
The switches use the same consecutive ports, 1 to 4. As
mentioned earlier, the trunk ports do not have to be consecutive,
nor do they have to be the same ports on all switches. But following
the recommendations can make trunk management easier.
In stacks of three or four switches, the top and bottom switches are
connected together.so that the trunk forms a ring.
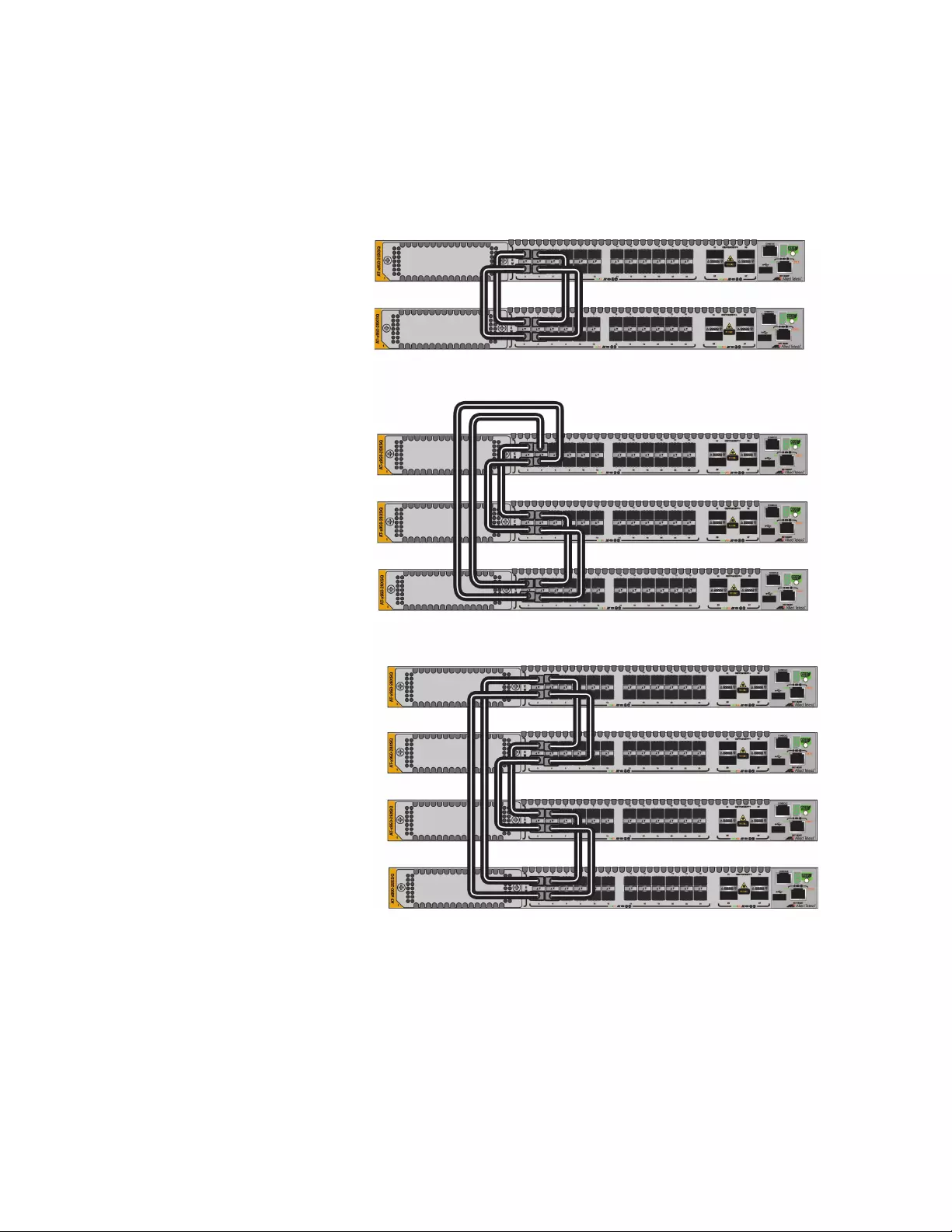
Chapter 3: Virtual Chassis Stacking
76
When possible, try cabling the same trunk ports together. For
example, if you select ports 6 to 9 as trunk ports, cable port 6 on
one switch to port 6 on the next, port 7 to port 7, and so on. Again,
this is not mandatory, but it can make managing or troubleshooting
the stack easier.
Figure 27. Example Stacks of x950-28XSQ Switches with Trunks of
10Gbps Ports
Stack of Two Switches
Stack of Three Switches
Stack of Four Switches
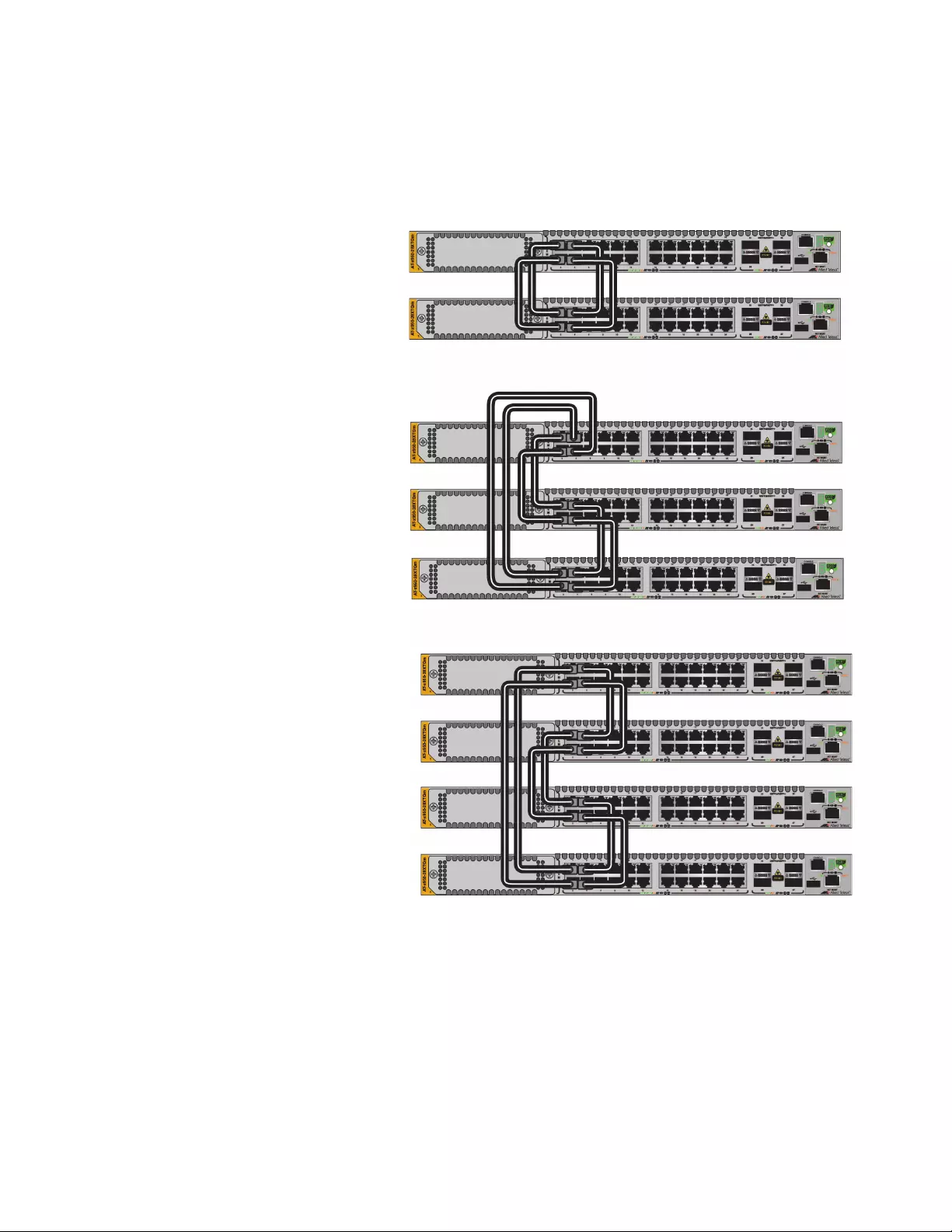
x950 Series Installation Guide for VCStack
77
Figure 28 has examples of stacks with 10Gbps trunks for two, three, or
four x950-28XTQm Switches. The examples use ports 1 to 4 for the
trunks. As a reminder, a trunk of ports 1 to 24 can have up to eight ports
per switch and you can use any of the ports.
Figure 28. Example Stacks of x950-28XTQm Switches with Trunks of
10Gbps Ports
Stack of Two Switches
Stack of Three Switches
Stack of Four Switches
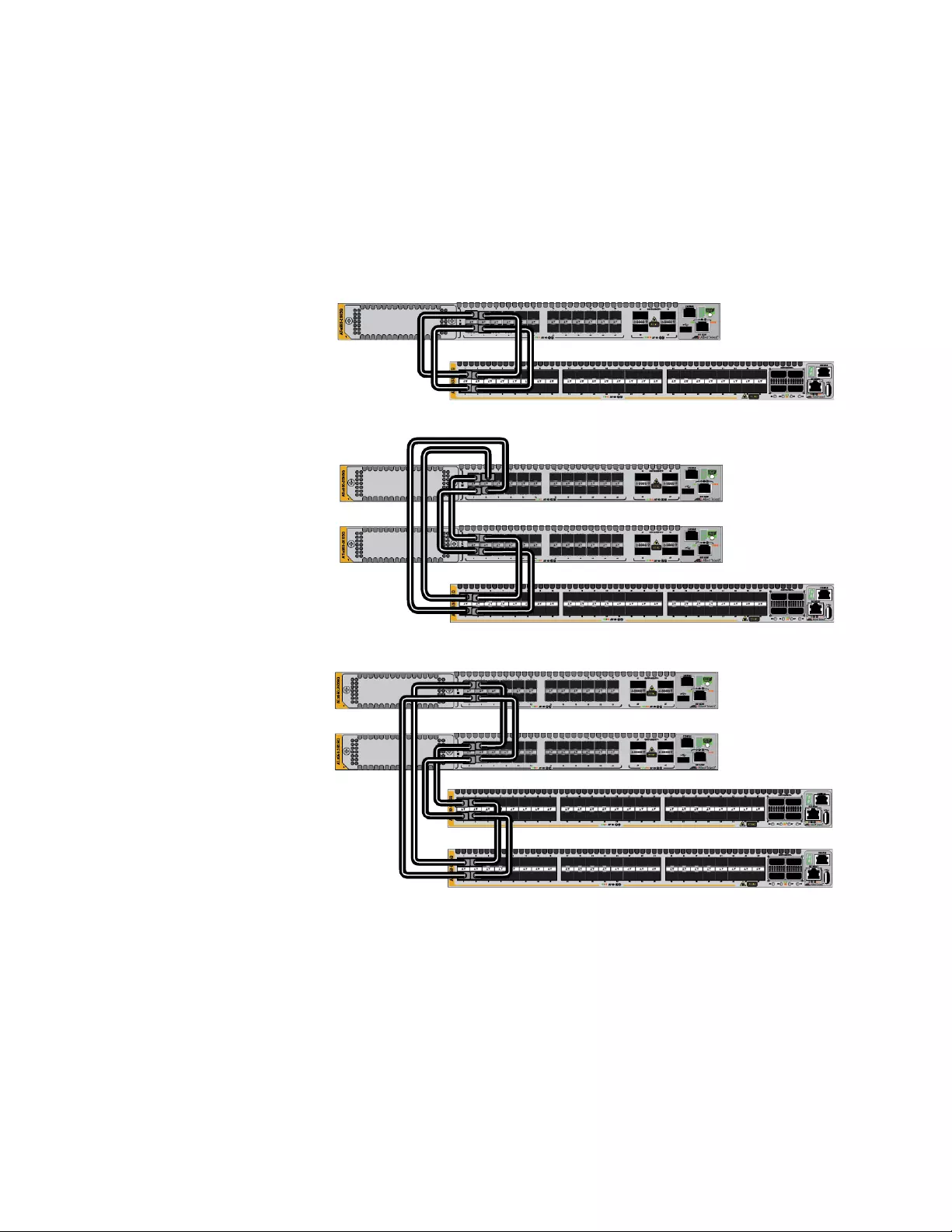
Chapter 3: Virtual Chassis Stacking
78
Figure 29 has examples of stacks with 10Gbps trunks with combinations
of two, three, or four x950-28XSQ and x950-52XSQ switches. The
examples use ports 1 to 4 for the trunks. As a reminder, a trunk of ports 1
to 24 on the x950-28XSQ switch and ports 1 to 48 on the x950-52XSQ
switch can have up to eight ports per switch and you can use any of the
ports.
Figure 29. Example Stack Trunks of 10Gbps Links on x950-28XSQ and
x950-52XSQ Switches
Stack of Two Switches
Stack of Three Switches
Stack of Four Switches
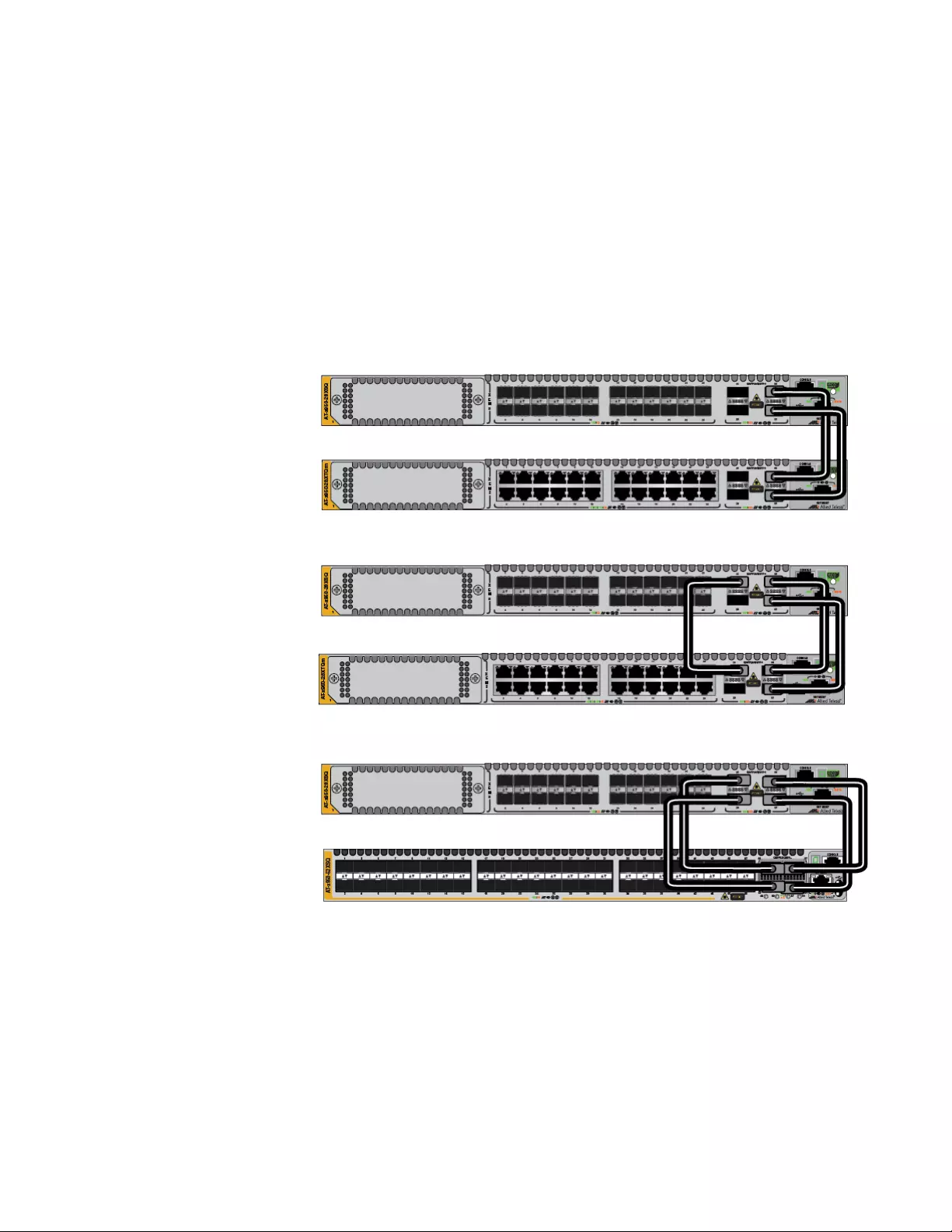
x950 Series Installation Guide for VCStack
79
Ports 25 to 37 and
Ports 49 to 61
with 40Gbps
Transceivers
You can also use ports 25 to 37 on the x950-28XSQ or x950-28XTQm
switch and ports 49 to 61 on the x950-52XSQ switch for stack trunks.
These ports support both 40Gbps and 100Gbps transceivers. You can use
either type of transceivers for the trunk, but the rules are slightly different.
Here are the guidelines to using 40Gbps transceivers for the trunk:
The trunk links can consist of fiber optic transceivers or QSFP1CU
or QSFP3CU direct attach cables.
Stacks can have any combination of x950-28XSQ, x950-28XTQm,
or/and x950-52XSQ switches.
For stacks of two switches, you can use two, three, or four ports
per switch for trunks. Examples are show in Figure 30.
Figure 30. Stack Trunk Examples of Two Switches with Trunk 40Gbps
Links
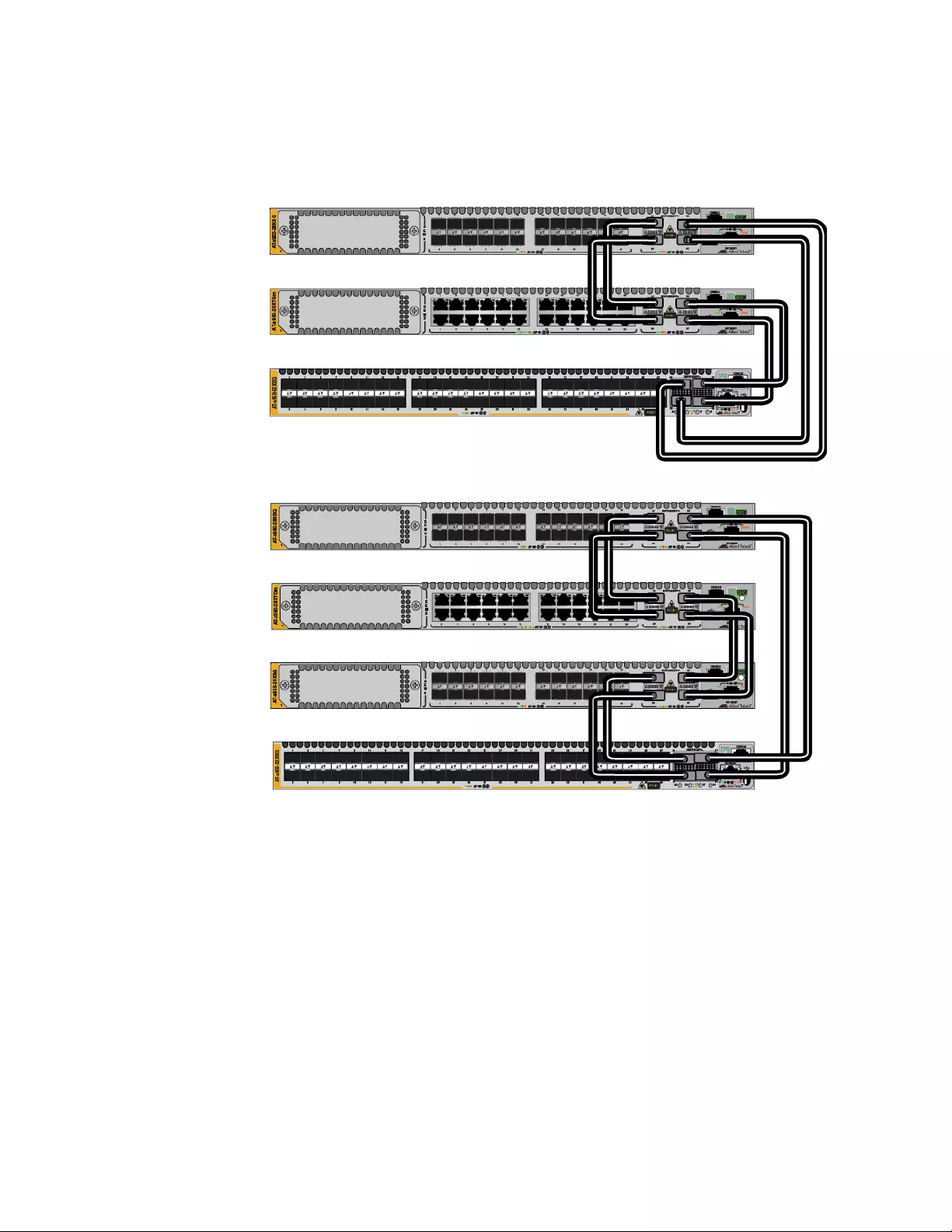
Chapter 3: Virtual Chassis Stacking
80
To build stacks of three or four switches, Allied Telesis
recommends using all four ports. Examples are shown in
Figure 31. Please note how the top and bottom switches are
connected to form a loop in the trunk.
Figure 31. Stack Trunk Examples of Three or Four Switches with 40Gbps
Links
Ports 25 to 37 and
Ports 49 to 61
with 100Gbps
Transceivers
Here are the guidelines to using ports 25 to 37 for the x950-28XSQ or
x950-28XTQm switch and ports 49 to 61 for the x950-52XSQ switch with
100Gbps transceivers for trunks:
You can use either fiber optic transceivers or QSFP28-1CU or
QSFP28-3CU direct attach cables for the trunk links.
The trunk can have a maximum of two ports per switch.
You can use any two of the four 100Gbps ports for the trunk.
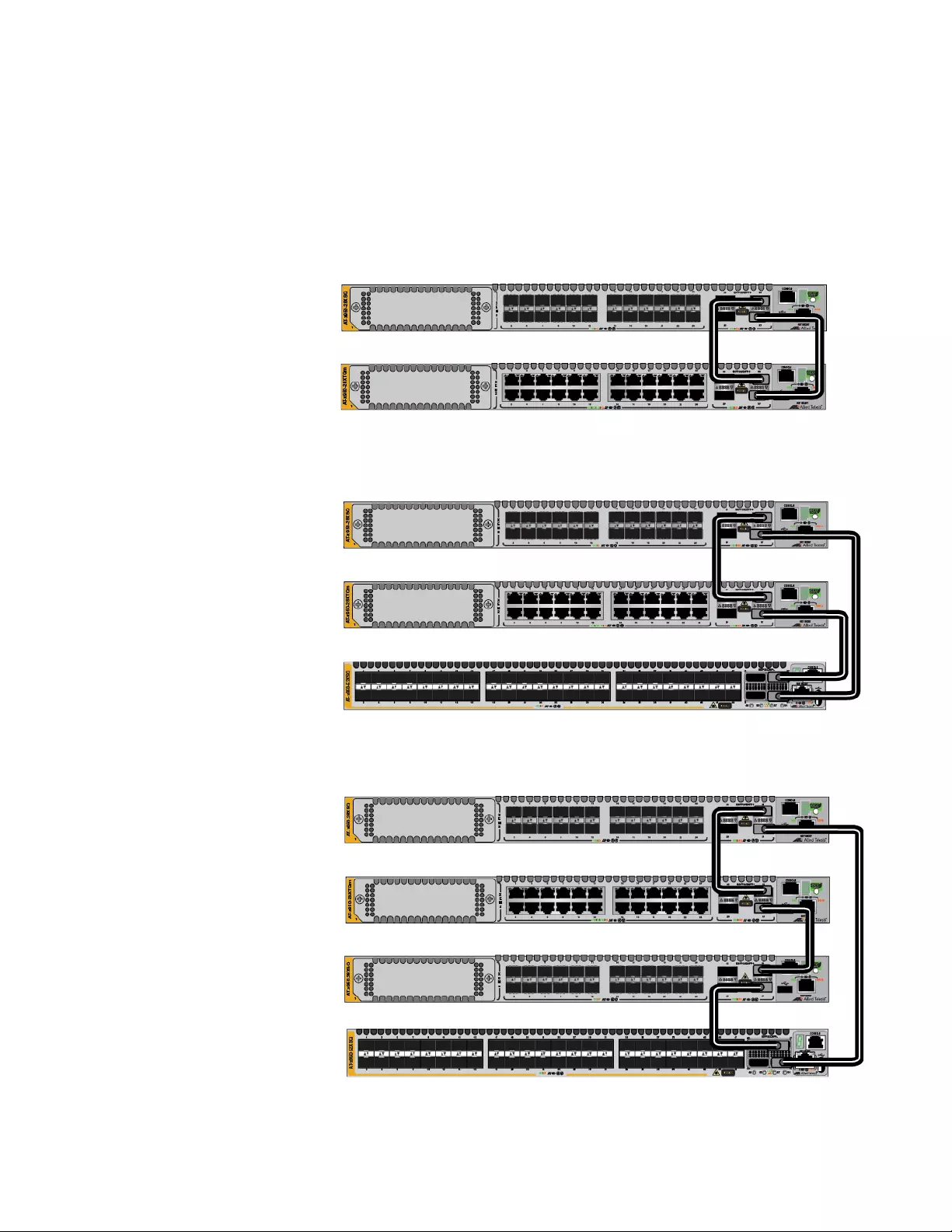
x950 Series Installation Guide for VCStack
81
Because the trunk cannot have more than two 100Gbps ports per
switch, stacks of three or four switches can have only one link
between switches.
Stacks can have any combination of x950-28XSQ, x950-28XTQm,
or/and x950-52XSQ switches.
Figure 32 illustrates stacks of two, three, and four switches, with
ports 33, 37, 57and 61 and 100Gbps links as the trunks.
Figure 32. Stack Trunk Examples with 100Gbps Links
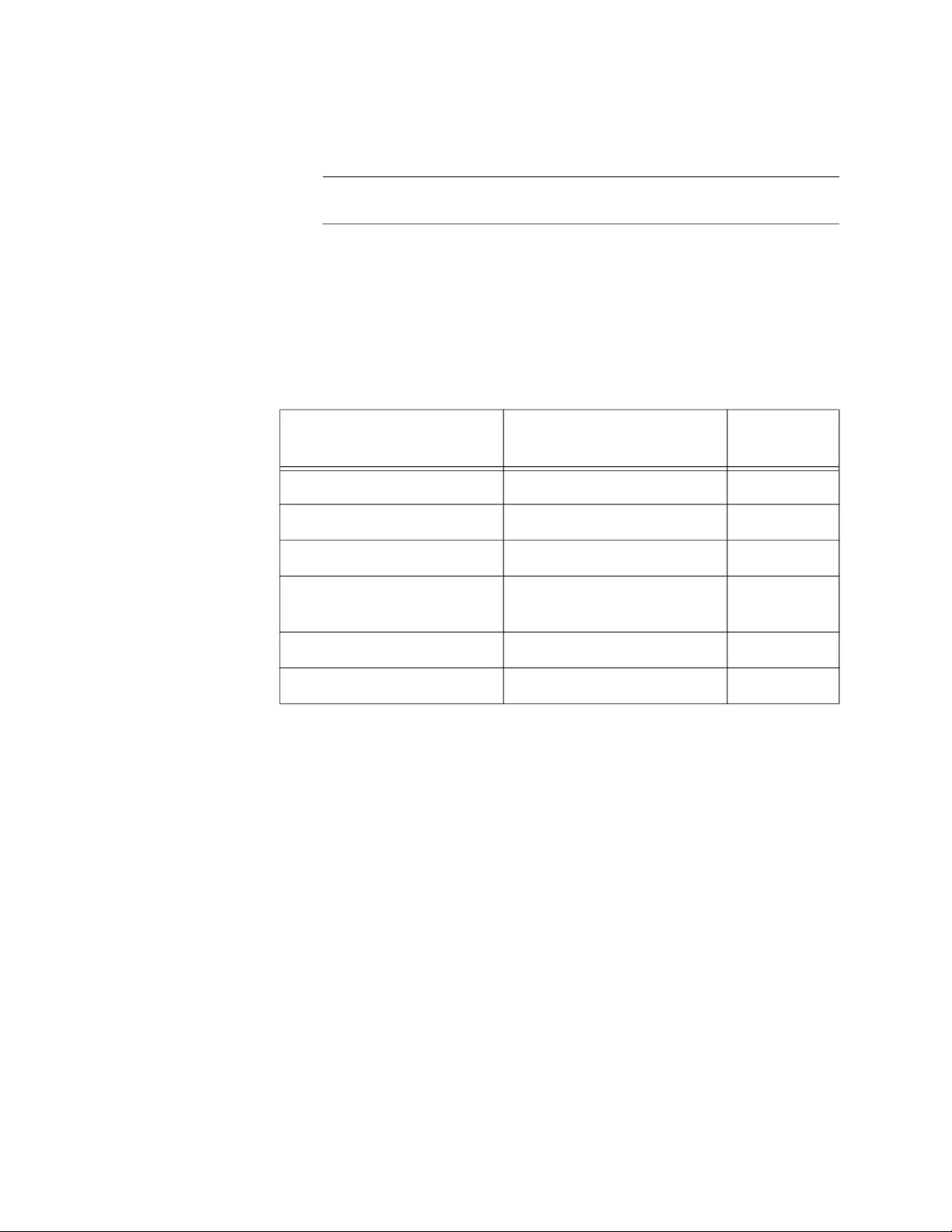
Chapter 3: Virtual Chassis Stacking
82
XEM2 Line
Cards
Here are the guidelines for using ports on XEM2 Line Cards in the
expansion slots for trunks:
Note
The x950-52XSQ switch does not support XEM2 line cards.
Stacks can have up to four switches.
Stacks can have both x950-28XSQ and x950-28XTQm Switches.
The maximum number of links in the trunk varies by line card.
Refer to Table 27. For example, a trunk using XEM2-12XT or
XEM2-12XS Line Cards can have up to eight ports per card.
The guidelines are listed here:
1. Trunks of twisted pair ports on XEM2-8XSTm, XEM2-12XT, or
XEM2-12XTm Line Cards have to operate at 10Gbps. They cannot
be used as trunk ports at lower speeds.
2. Trunks of SFP+ ports on XEM2-8XSTm, XEM2-12XS, or XEM2-
12XS v2 Line Cards have to use 10Gbps SFP+ transceivers. They
cannot be used as trunk ports at lower speeds.
3. Allied Telesis does not recommend using the XEM2-1CQ Line Card
for a stack trunk.
Figure 33 on page 83 is an example of a stack of two switches with
a trunk of six 10Gbps links on XEM2-12XT Line Cards.
Table 27. Maximum Number of Trunk Ports Per Switch
Ethernet Line Card Maximum Number of
Trunk Ports Per Switch Guidelines
XEM2-8XSTm 4 1, 2
XEM2-12XT 8 1
XEM2-12XTm 8 1
XEM2-12XS and
XEM2-12XS v2
8 2
XEM2-4QS 4
XEM2-1CQ 1 3
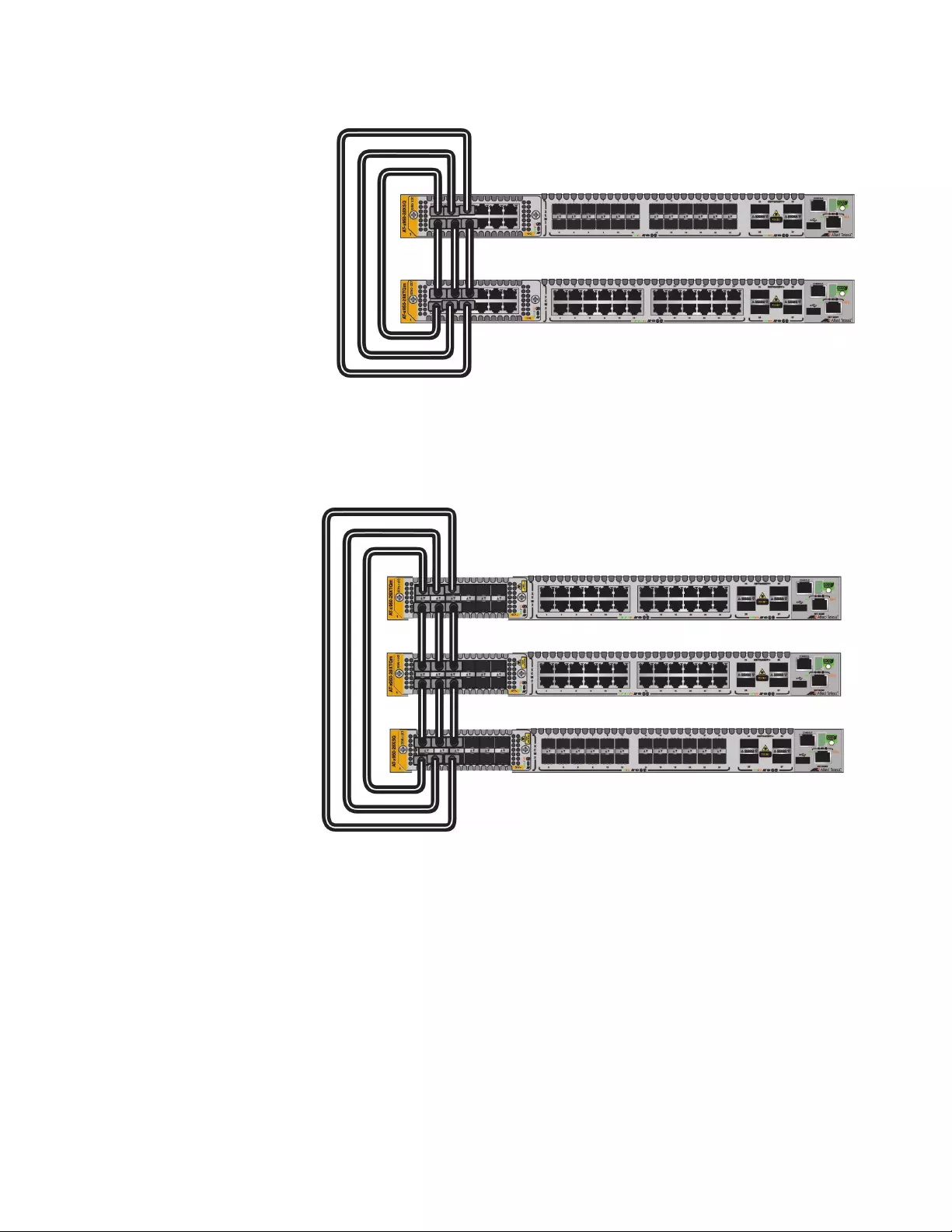
x950 Series Installation Guide for VCStack
83
Figure 33. Example Trunk Using XEM2-12XT Line Cards
Figure 34 is an example of a stack of three switches with a trunk
from ports on XEM2-12XS Line Cards.
Figure 34. Example Trunk Using XEM2-12XS Line Cards
Figure 35 on page 84 is an example of a stack of four switches with
a trunk of ports on XEM2-4QS Line Cards.
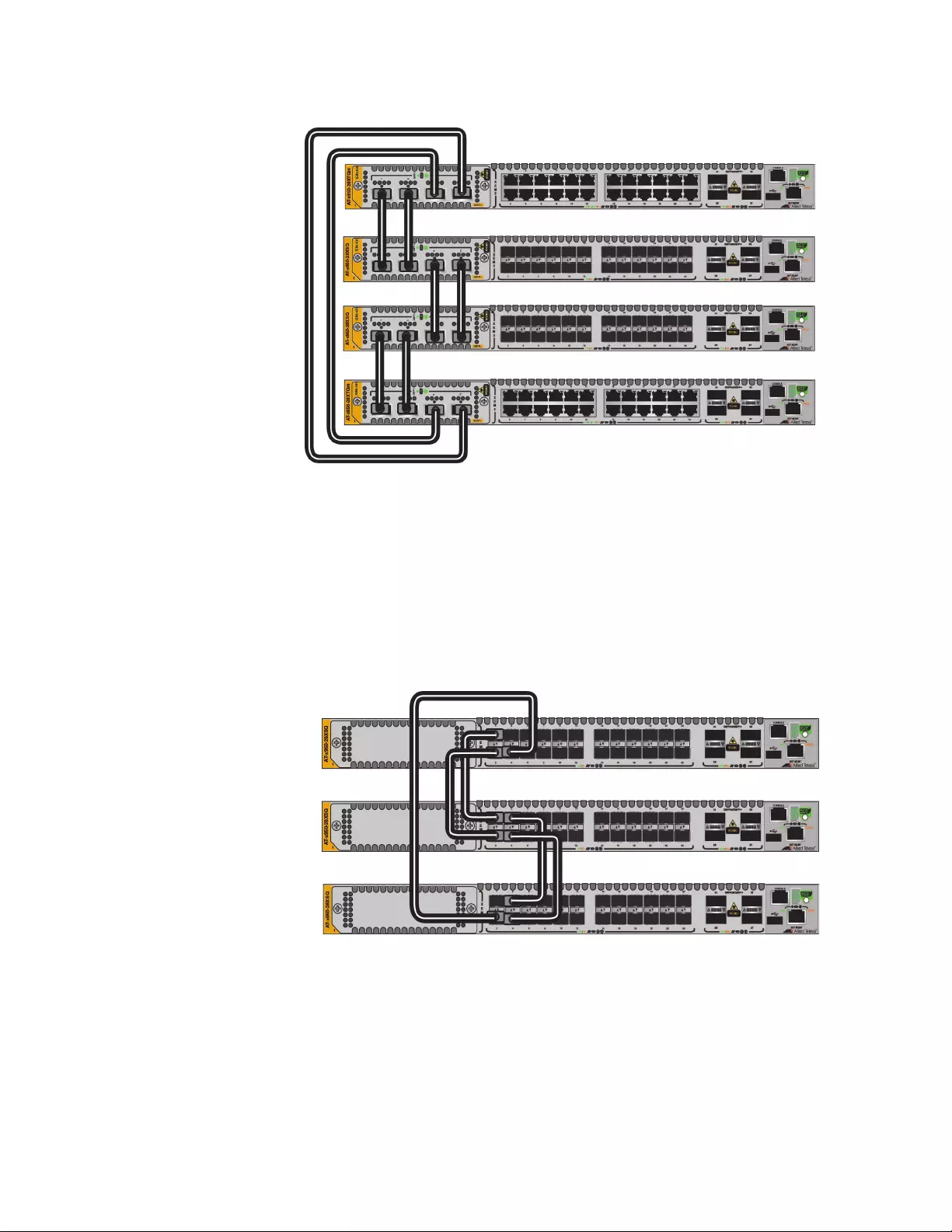
Chapter 3: Virtual Chassis Stacking
84
Figure 35. Example Trunk Using XEM2-4QS Line Cards
Unsupported
Trunks
The following are examples of unsupported trunks.
In stacks of three or four switches, the number of links in the trunk
has to be the same on all switches. The trunk in Figure 36 is
unsupported because the middle switch is connected to the top
and bottom switches with two links each, while the top and bottom
switches are connected with only one link.
Figure 36. Unsupported Trunk with Different Numbers of Links Between
Switches
The cables in a trunk must be all the same type: They can be all
fiber optic cables, direct attach cables, or twisted pair cables.
Trunks cannot contain different types of cables. The trunk in Figure
37 on page 85 is unsupported because it has both fiber optic and
direct attach cables.
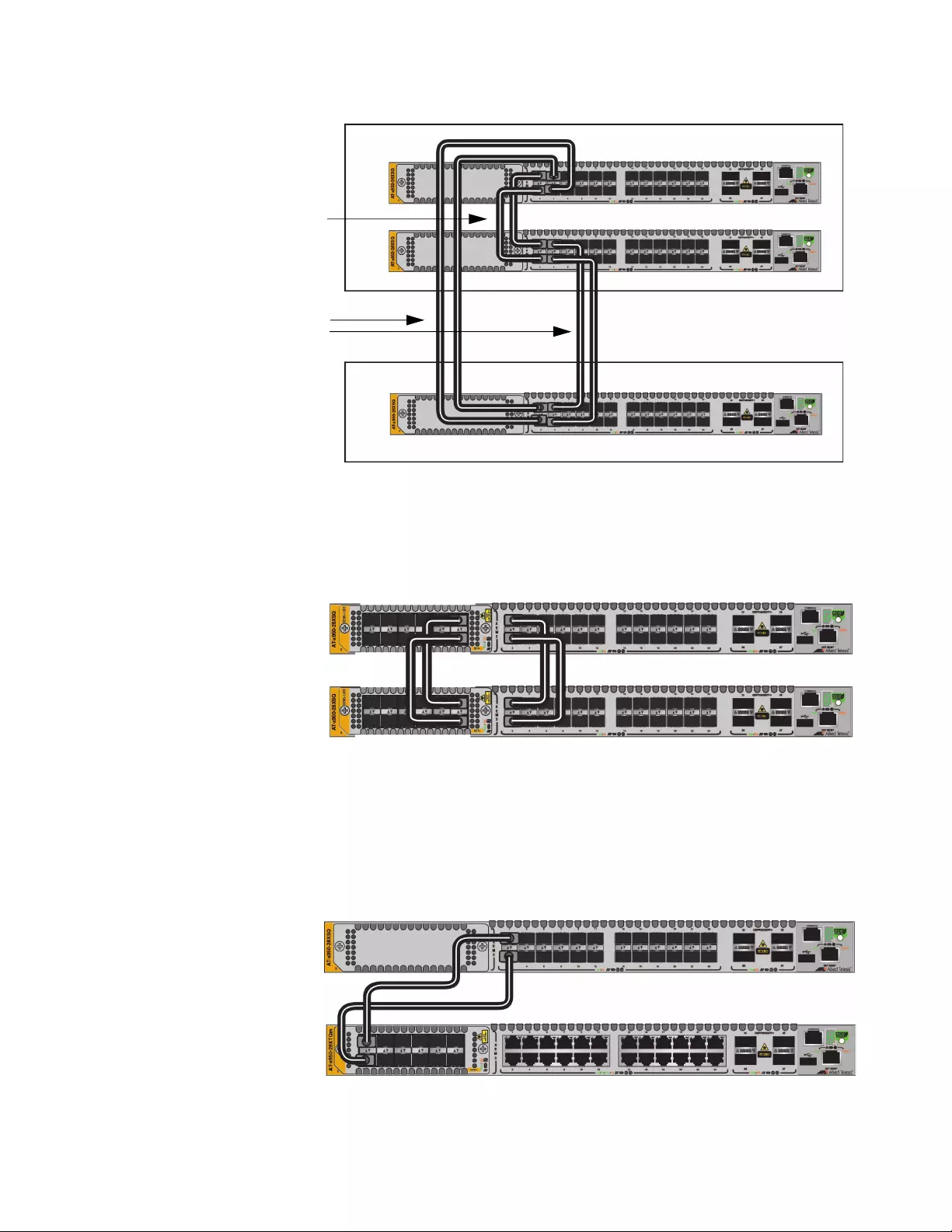
x950 Series Installation Guide for VCStack
85
Figure 37. Unsupported Trunk with Mixed Cables
Trunks cannot have both base ports and XEM2 Line Card ports.
The unsupported trunk in Figure 38 consists of base 10Gbps ports
and ports on XEM2-12XS Line Cards.
Figure 38. Unsupported Trunk with Both Base and XEM2 Line Card Ports
Trunks cannot have links that interconnect base ports and XEM2
Line Card ports. The example trunk in Figure 39 is unsupported
because base 10Gbps ports 1 and 2 in the top switch are
connected to ports 1 and 2 on the XEM2-12XS Line Card in the
bottom switch.
Figure 39. Unsupported Trunk of Connected Base and Line Card Ports
Wiring Room 1
Wiring Room 2
Fiber Optic Cables
SP10TW Direct
Attach Cables
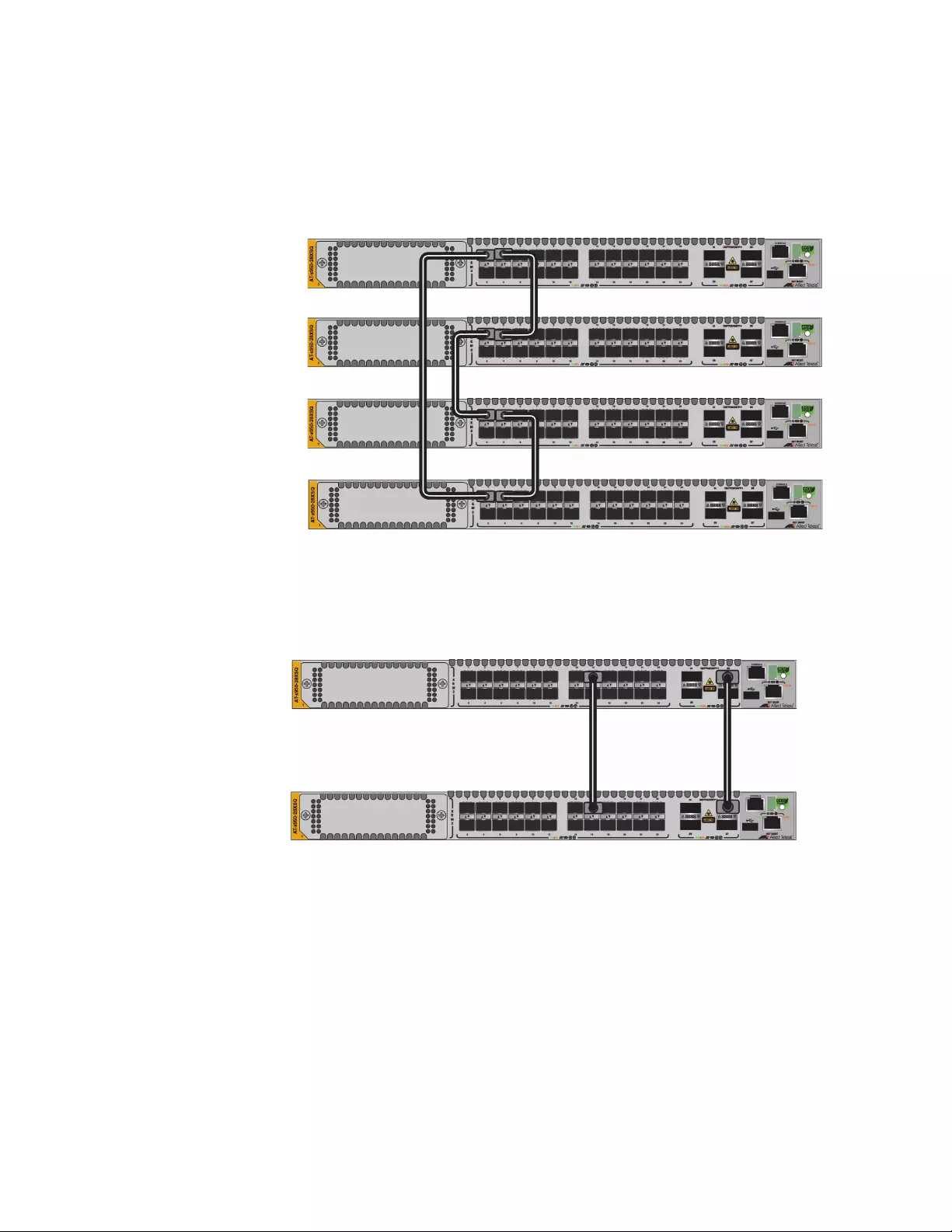
Chapter 3: Virtual Chassis Stacking
86
In most cases, trunks should have a minimum of two links between
switches. The trunk in Figure 40 is not recommended because
there is only one link between switches. The exceptions to this are
stacks of three or four switches with trunks of base 100Gbps ports.
Refer to Figure 32 on page 81.
Figure 40. Unsupported Trunk with Only One Link Between Switches
Trunk links must be the same speed. The example in Figure 41 is
unsupported because the links are different speeds.
Figure 41. Unsupported Trunk with Different Port Speeds
Allied Telesis does not recommend using the XEM2-1CQ Line
Card for a stack trunk because it has only one transceiver port and
the switch has only one expansion port. Refer to Figure 42 on page
87. Instead, use two base 40/100Gbps transceiver ports, as shown
in Figure 32 on page 81, to build a 100Gbps trunk.
10Gbps 40Gbps or
100Gbps
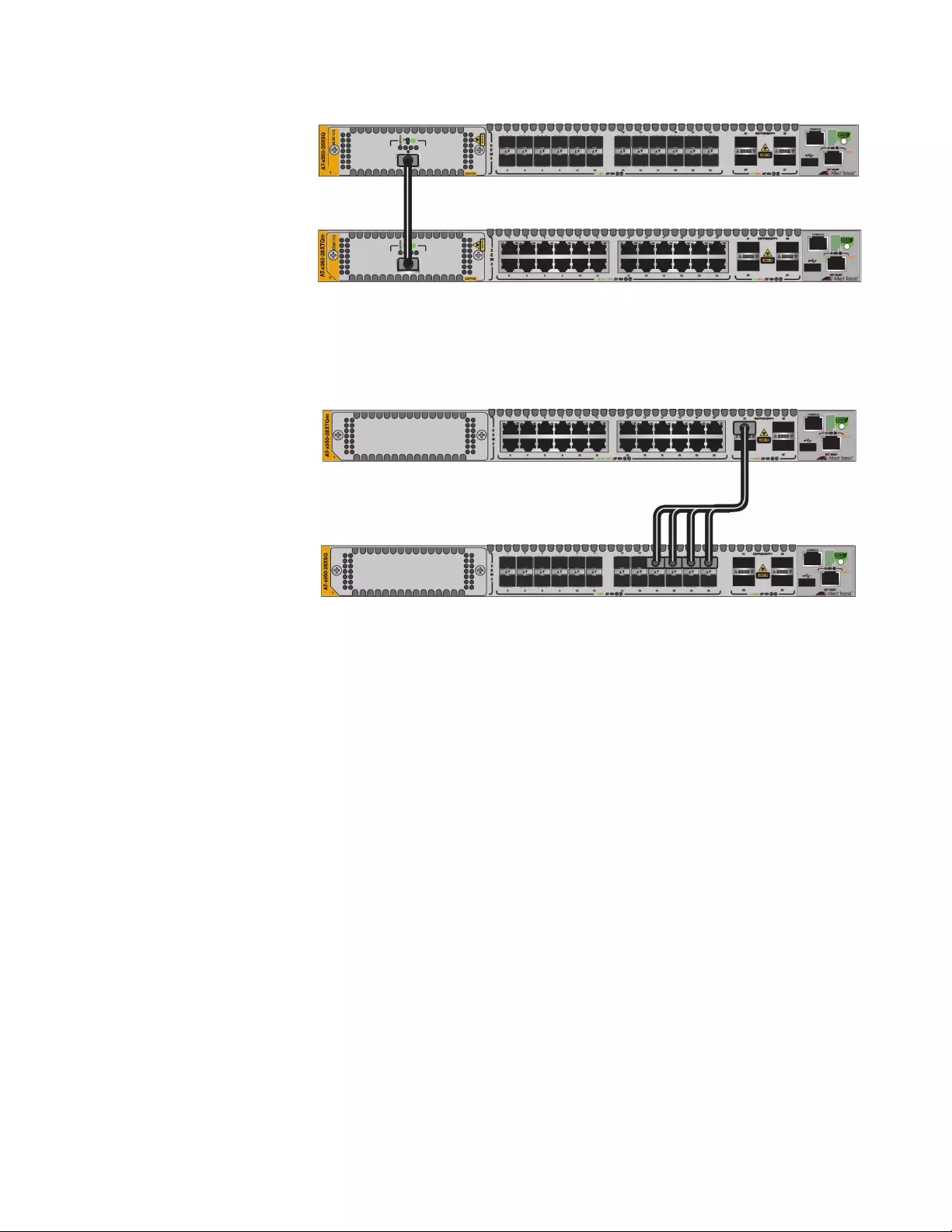
x950 Series Installation Guide for VCStack
87
Figure 42. Not Recommended Stack Trunk of XEM2-1CQ Line Cards
You cannot use a 10Gbps breakout cable for a trunk. Refer to
Figure 43.
Figure 43. Unsupported Trunk with a 10Gbps Breakout Cable
The base 10Gbps transceiver ports and XEM2-12XS Line Card
support 1Gbps transceivers. However, you cannot use 1Gbps
transceivers for a stack trunk.
Trunk links must be direct connections between ports on the
switches, without any intermediary network devices, such as media
converters, routers, or other Ethernet switches. Figure 44 on page
88 is an example of an unsupported trunk because it contains
media converters.
100Gbps
Breakout
Cable
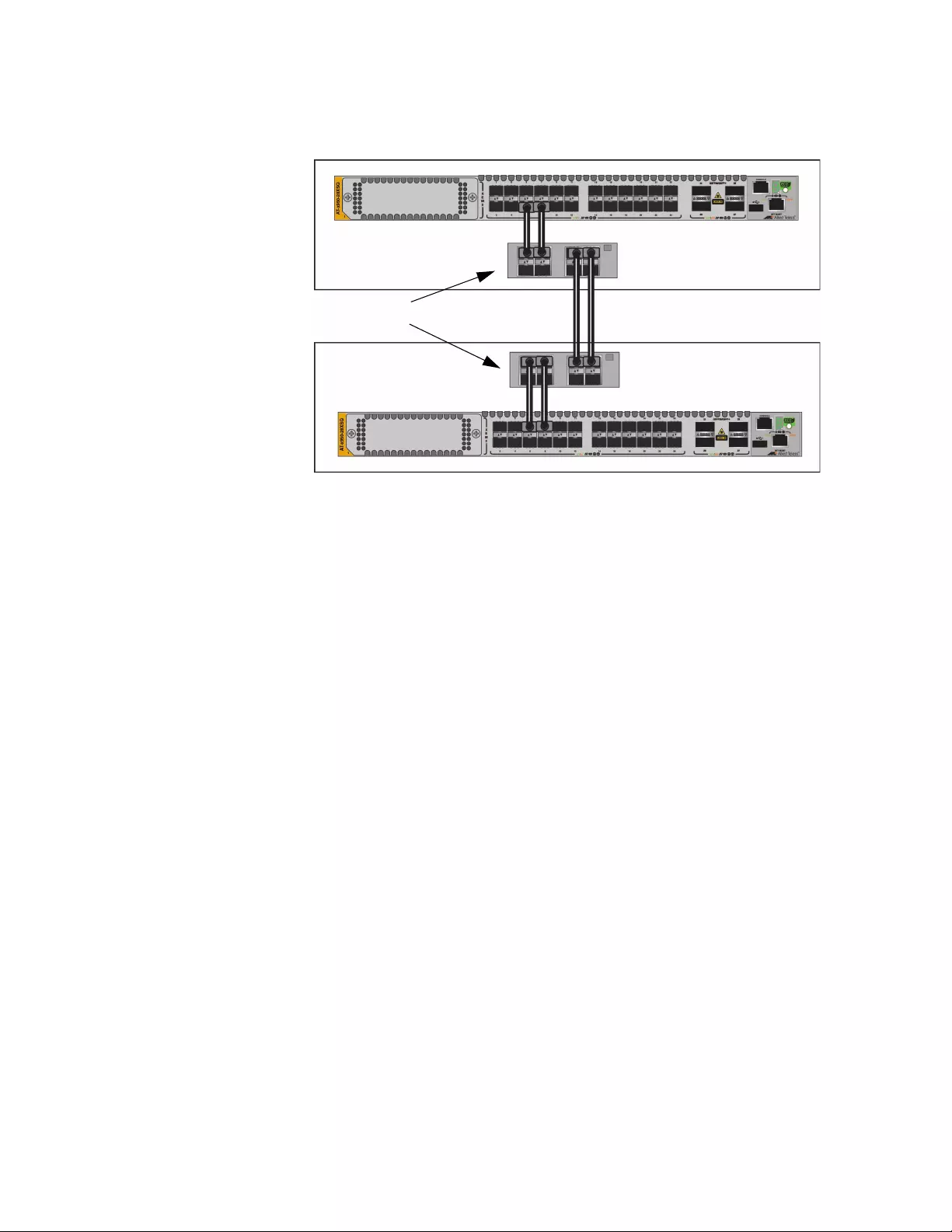
Chapter 3: Virtual Chassis Stacking
88
Figure 44. Unsupported Trunk with Intermediary Network Devices
Media
Converters
Wiring closet 1
Wiring closet 2
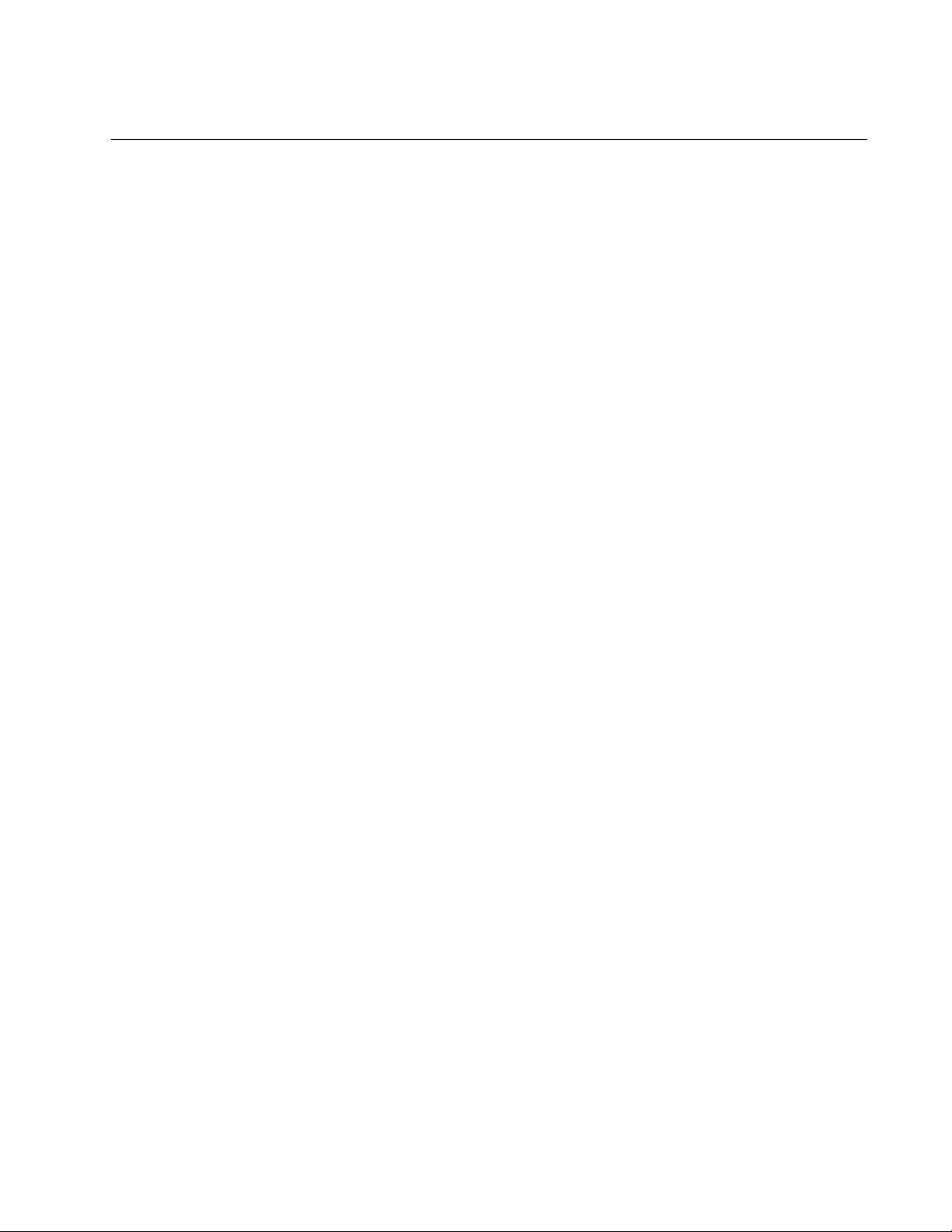
x950 Series Installation Guide for VCStack
89
Master and Member Switches
One switch of a stack functions as a master switch. Its main functions are
listed here:
Coordinate and monitor stack operations.
Verify that the switches are using the same version of
management software. It automatically downloads its management
software over the stacking cables to switches with different
software versions.
Verify that the switches have different ID numbers. It automatically
assigns new ID numbers to resolve conflicts where two or more
switches have the same ID number.
The other switches are called member switches.
Selection of the
Master Switch
The switches of the stack designate the master switch during the
initialization process, when they are powered on or reset. They base the
selection of the master switch on the following parameters:
Stack priority numbers
MAC addresses
The stack priority number is an adjustable value of 0 to 255, where the
lower the number, the higher the priority. Typically, the switch with the
lowest priority number (highest priority) becomes the master switch of a
stack. The default priority value is 128.
If the switches have the same priority values, the selection of the master
switch is based on their MAC addresses. As with the priority value, the
lower the MAC address, the higher the priority. The switch with the lowest
MAC address becomes the master switch.
If you power on the stack without adjusting the priority values, the master
switch is selected based on the MAC addresses if the units are powered
on simultaneously. If you power on the switches one at a time, the master
switch is the first switch powered on.
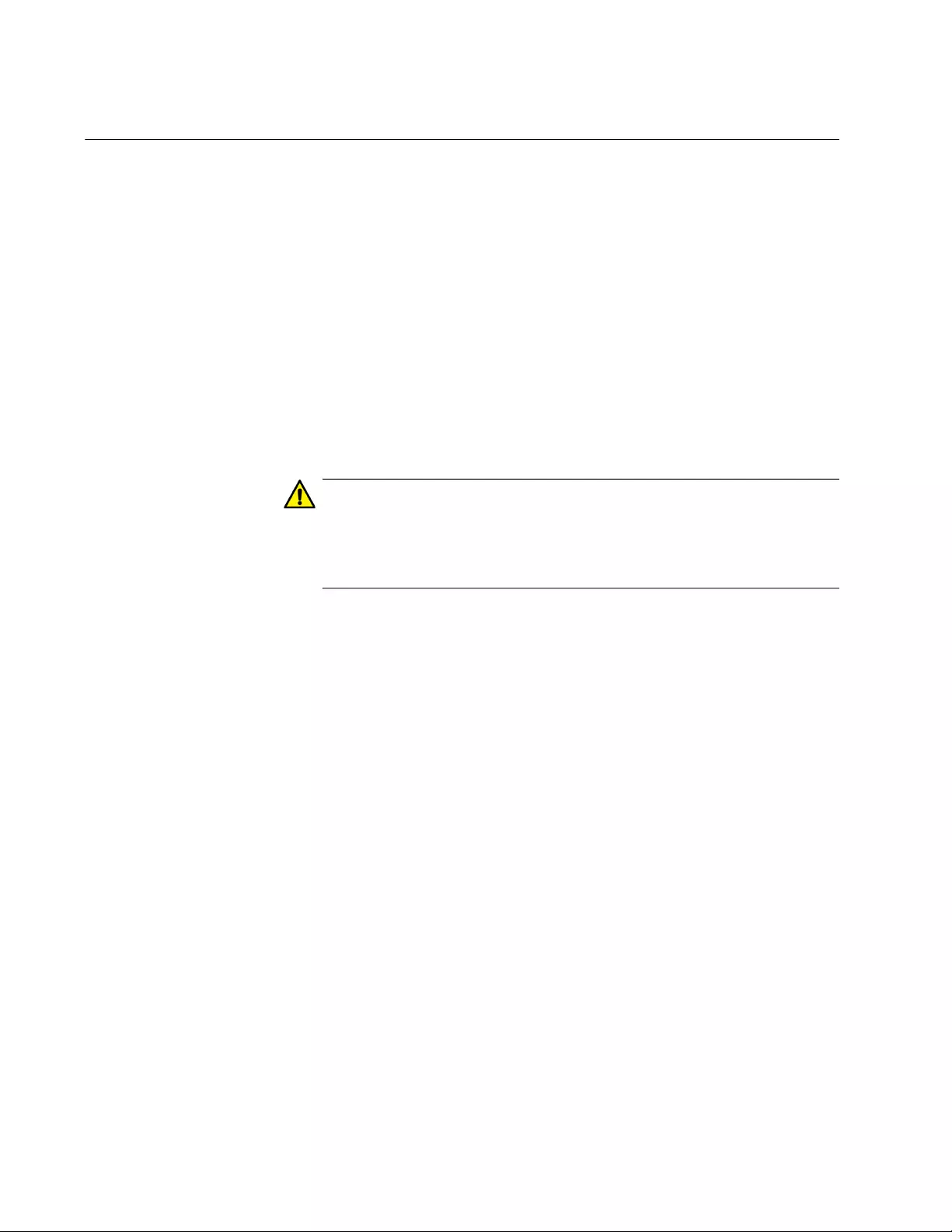
Chapter 3: Virtual Chassis Stacking
90
Switch ID Numbers
Each switch must have an ID number. The range is 1 to 4. The default is 1.
The ID numbers are displayed on the ID LEDs on the front panels of the
units. You can assign the numbers yourself or let the master switch assign
the numbers automatically when you first power on the stack.
You use the ID numbers to identify the individual ports and switches when
configuring the devices with the commands in the management software.
For further information, refer to “Designating Ports in the Command Line
Interface” on page 46.
The ID numbers are also used to identify the parameter settings that are
stored in the configuration file. When the stack is reset or power cycled,
the switches uses the ID numbers in the commands in the configuration
file to determine which parameter settings belong to which switch.
Caution
You should not change the ID numbers of the switches after you
begin configuring the parameter settings. Otherwise, the stack might
apply parameter settings to the wrong devices when you reset or
power cycle it. E79
The switches do not use the ID numbers to select the master switch. The
selection of the master switch is based on the priority numbers and MAC
addresses, as previously explained.
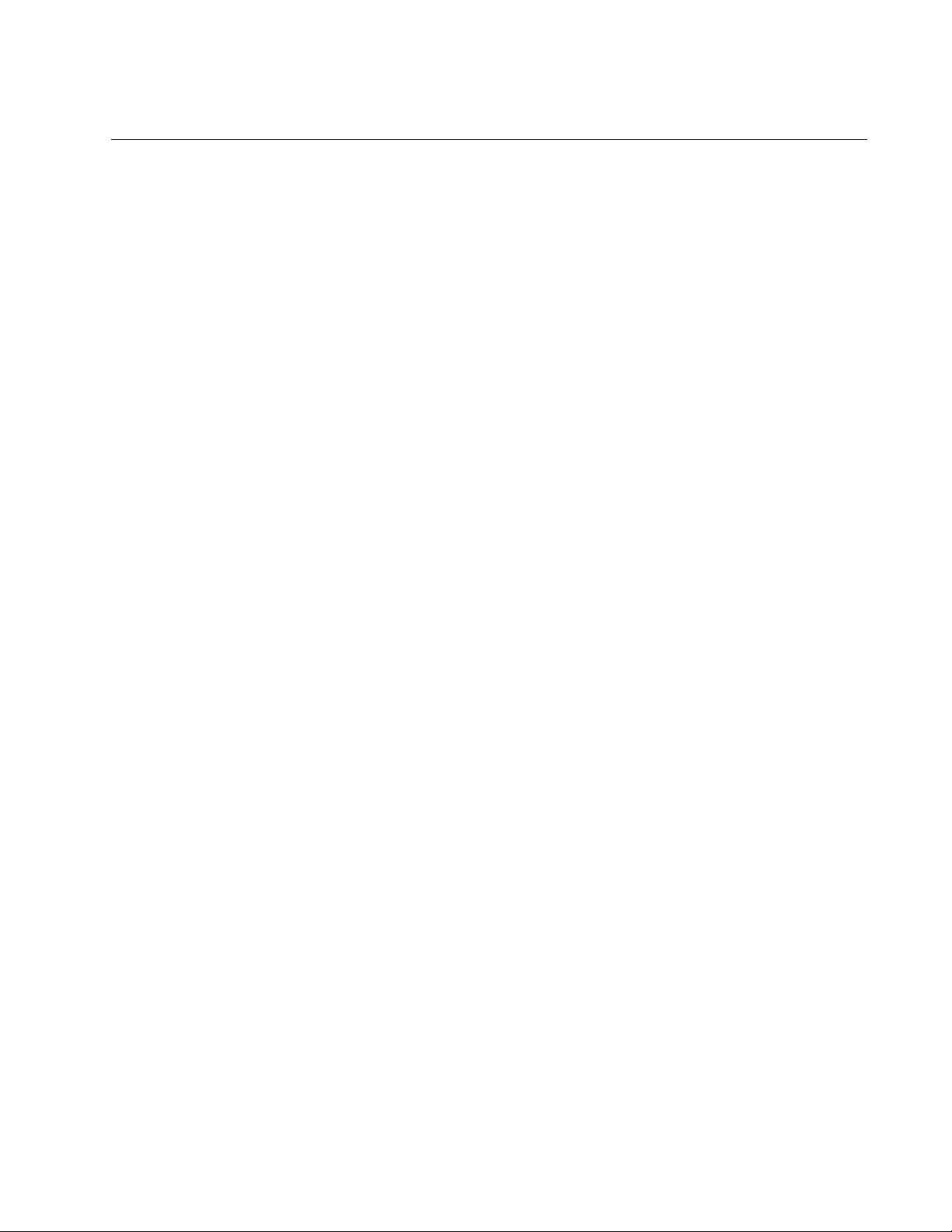
x950 Series Installation Guide for VCStack
91
Optional Feature Licenses
The x950 Switch comes with the AlliedWare Plus management software
and a base set of features that are available as soon as you install the
device. Additional features and capabilities might be included with the
operating system, but can be access only after they are unlocked with
optional feature licenses from Allied Telesis. Contact your authorized
reseller or distributor for a list of optional features licenses for this product.
Here are the guidelines to feature licenses for a stack of x950 Series
switches:
The VCStack feature is part of the base features of the switch. It
does not require an optional feature license.
You can install feature licenses while the switches are operating as
stand-alone units or as a stack.
When ordering feature licenses for the switches of a stack, you
must order one license for each switch.
Switches can form a stack even if they have different feature
licenses. However, the additional features are only available on
those switches with the licenses. The stack generates a warning
message if it detects that the switches do not have the same
optional feature licenses.
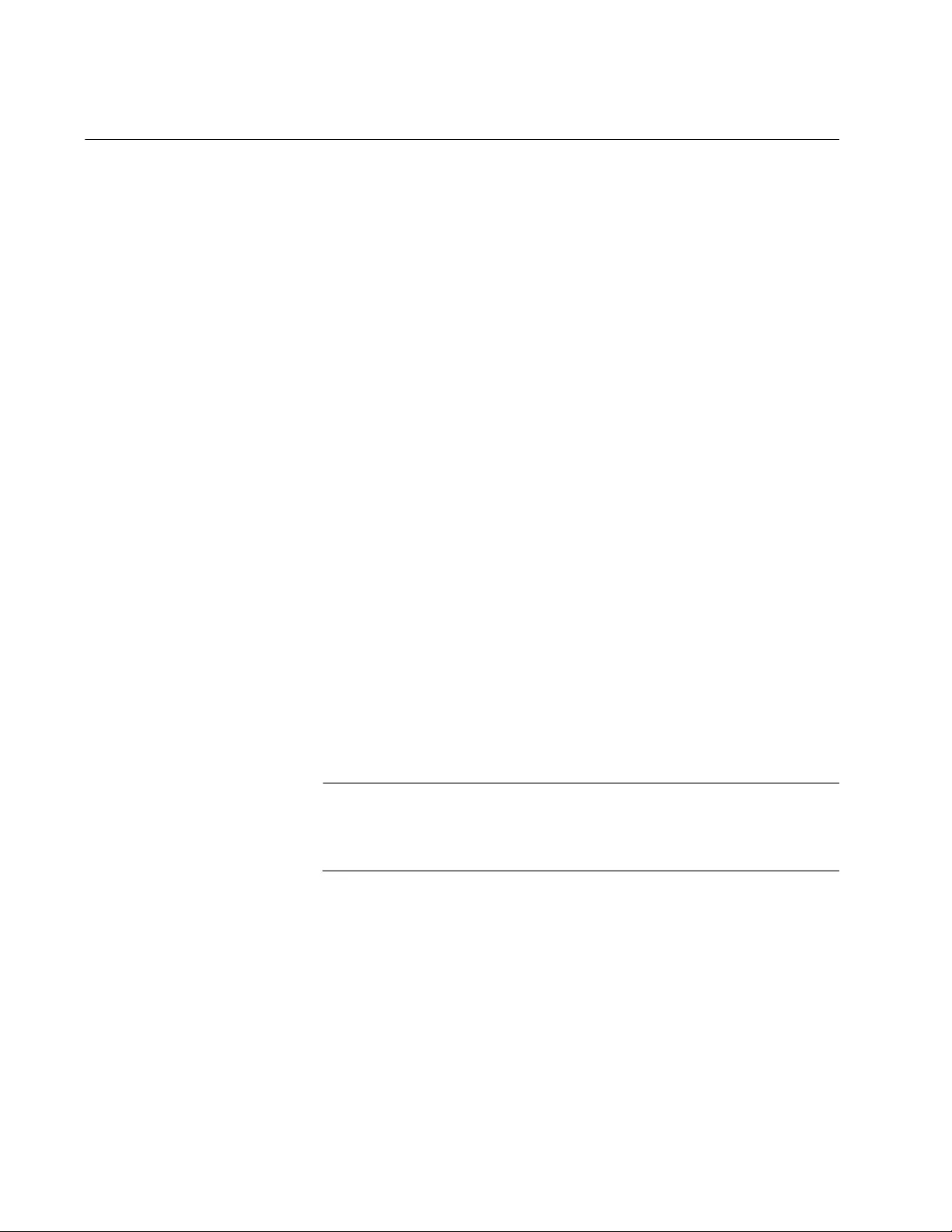
Chapter 3: Virtual Chassis Stacking
92
Planning a Stack
Here are questions you need to answer before building or configuring a
stack:
How many switches will be in the stack? AlliedWare Plus v5.4.8-2
supports stacks of two switches. AlliedWare Plus v5.4.9 or later
supports stacks up to four switches.
Which switch will be the master switch? Refer to “Master and
Member Switches” on page 89. It can be any switch.
Which ports will be the trunk ports on the switches? Refer to “Stack
Trunks” on page 74.
What will be the ID numbers of the member switches? Refer to
“Switch ID Numbers” on page 90. The master switch should be
given ID 1, the default value. Member switches should be assigned
IDs in the range of 2 to 4.
If you are planning to use ports on XEM2 Line Cards for the stack
trunk, have you already installed the cards in the switches? Refer
to “Installing an Optional XEM2 Ethernet Line Card” on page 130.
What types of transceivers will be used in ports 25, 29, 33, and 37
on the x950-28XSQ or x950-28XTQm switch, or ports, 49, 53, 57,
and 61 on the x950-52XSQ switch in the master and member
switches? Refer to “Ports for 40Gbps QSFP+ or 100Gbps QSFP28
Transceiver, or Breakout Cables” on page 29. You may install the
transceivers (but not cable them) before configuring the switches
for stacking.
Have you already connected network cables to the trunk ports? If
so, you should disconnect them before configuring the switches for
stacking.
Note
Cabling the trunk ports before activating and configuring the
VCStack feature may result in loops in your network topology, which
can cause poor network performance.

x950 Series Installation Guide for VCStack
93
Stacking Worksheet
The worksheet in Table 28 is here to assist you in configuring and
maintaining a stack.
Table 28. Stacking Worksheet
Switch Switch/
Location
Switch
ID
Prior-
ity
Firmware
Version
Number1
Trunk
Ports
Transceivers in
Slots 25 to 37 or
Slot 49 to 612
XEM2
Card
Master 1 1 25 or 49:
29 or 53:
33 or 57:
37 or 61:
Member 2 2 25 or 49:
29 or 53:
33 or 57:
37 or 61:
Member 3 3 25 or 49:
29 or 53:
33 or 57:
37 or 61:
Member 4 4 25 or 49:
29 or 53:
33 or 57:
37 or 61:
1. AlliedWare Plus version number.
2. Use slots 25 to 37 for the x950-28XSQ and x950-28XTQm switches, or slots 49 to 61 for the x950-52XSQ
switch.
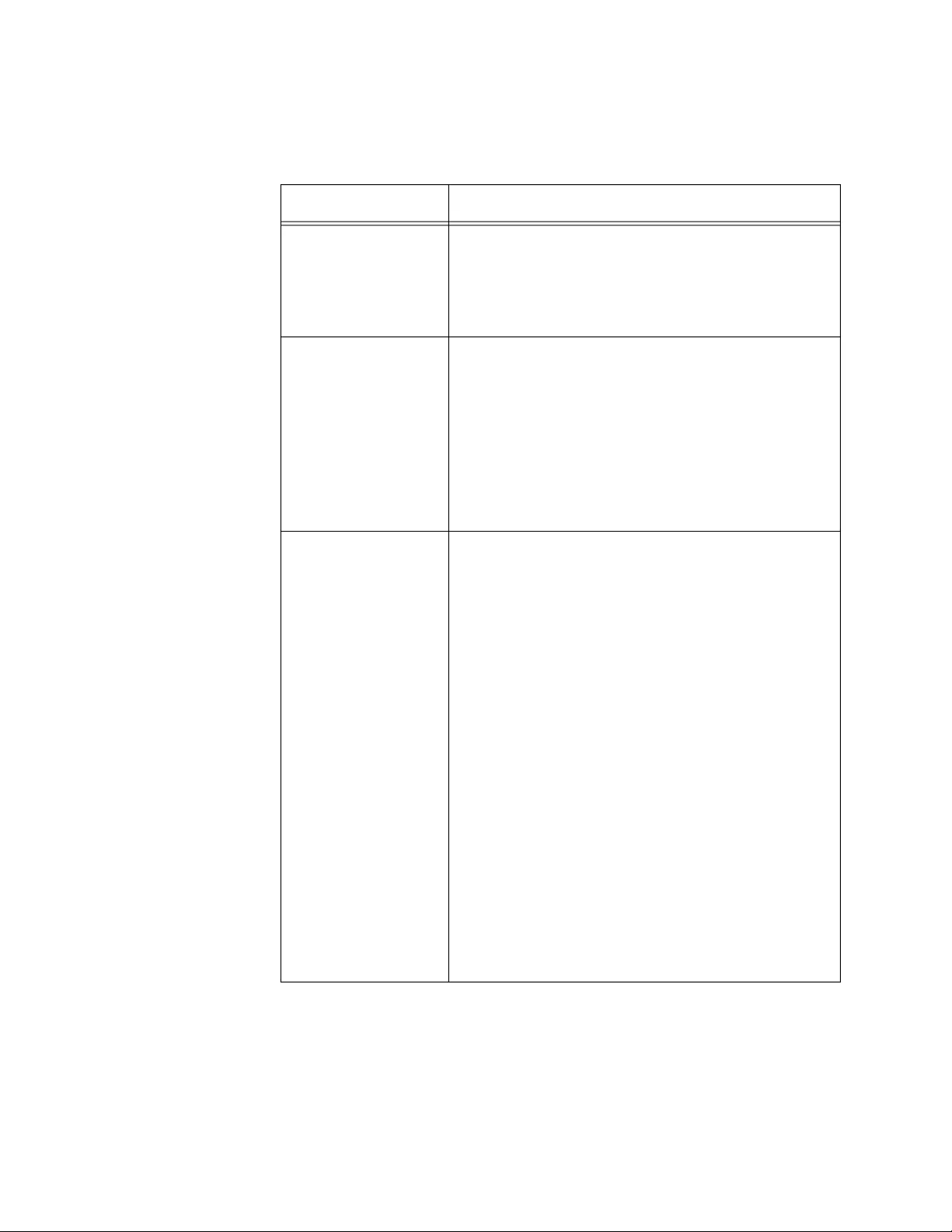
Chapter 3: Virtual Chassis Stacking
94
The worksheet columns are described in Table 29.
Table 29. Stacking Worksheet Columns
Column Description
Location Use this column to record the model names and
physical locations of the switches, such as their
buildings or equipment rooms. The information
can be useful in identifying and locating the
switches if they are in different locations.
ID Each switch in a stack has to have a unique ID
number, in the range of 1 to 4. They display the
numbers on the ID LEDs on the front panels and
you use the numbers to configure the individual
ports. Allied Telesis recommends assigning the
ID 1, the default value, to the master switch. You
should decide on the ID assignments of the
switches before beginning the configuration
procedures.
Priority When the switches of a stack are reset or
powered on, they perform an initialization process
that involves, in part, choosing the master switch.
The selection is based on their priority numbers
and MAC addresses. The former is an adjustable
parameter with a range of 0 to 255 and a default
value of 128. The lower the value, the higher the
priority. Thus, the switch with the lowest value
becomes the stack master.
If switches have the same priority number, the
master is selected based on their MAC
addresses. Again, as with priority numbers, the
lower the MAC address, the higher the priority.
Allied Telesis recommends setting each switch’s
priority value to match its ID value. This is to
ensure that the switch you have chosen to be the
master unit will indeed function in that role. It will
also make it possible for you to know the order in
which the switches assume the master role if the
primary master should fail or be powered off.
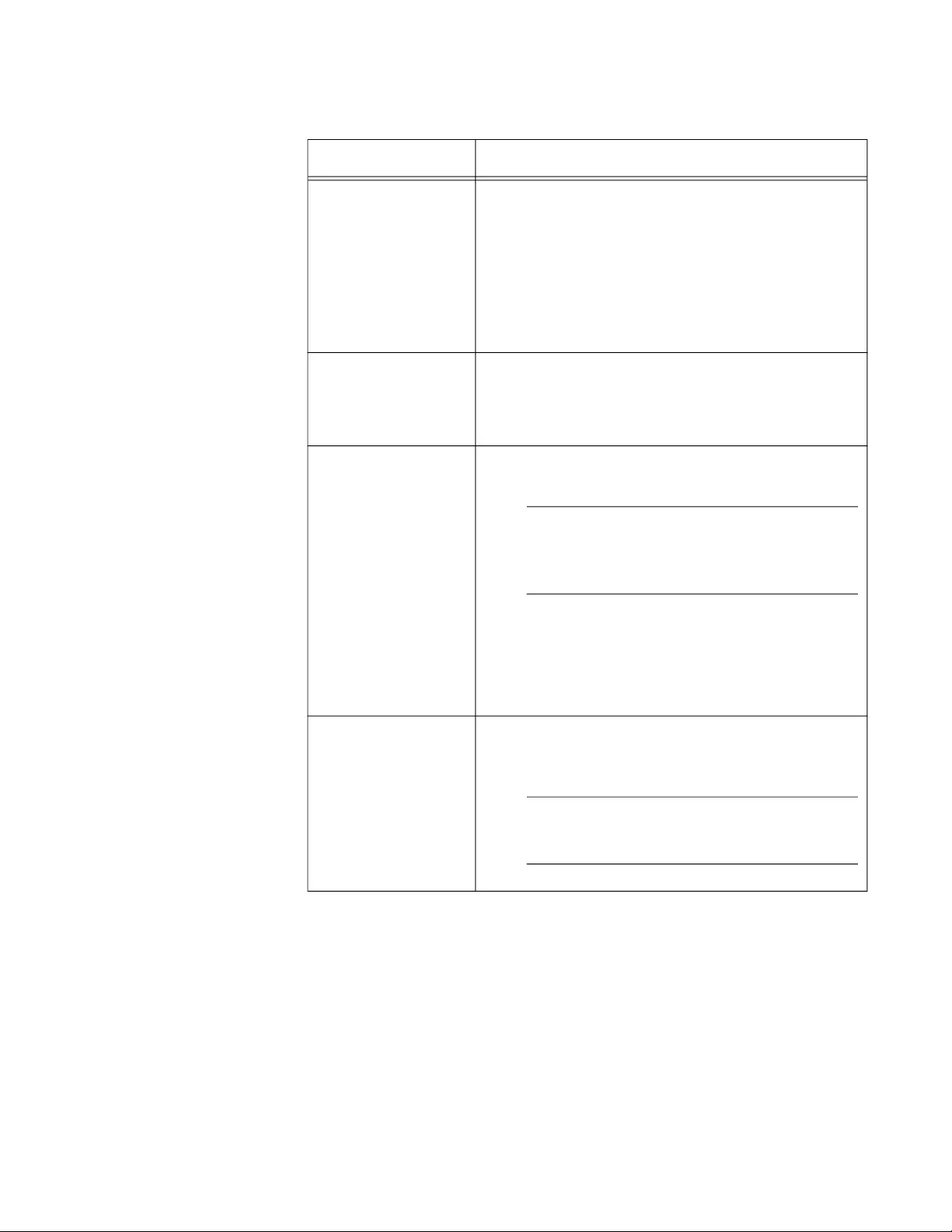
x950 Series Installation Guide for VCStack
95
Firmware Version
Number
Use this column to record the version numbers of
the AlliedWare Plus management software on
the switches. The switches might not be able to
form the stack if they have different versions.
Switches that have different versions should be
updated to the most recent release before you
build the stack. The configuration instructions
explain how to view the version numbers.
Trunk Ports Use this column to enter the trunk ports. You
should choose the ports before beginning the
configuration procedures. Refer to “Stack Trunks”
on page 74.
Transceivers in
Slots 25 to 37 or
Slots 49 to 61
Used this column to record the transceiver
speeds for slots 25 to 37 or 49 to 61.
Note
Use slots 25 to 37 for the x950-28XSQ and
x950-28XTQm switches, or slots 49 to 61
for the x950-52XSQ switch
The possible speeds are listed here:
- 40Gbps
- 100Gbps
- 10Gbps breakout cable
XEM2 Slot Use this column to enter the model names of the
XEM2 Line Cards, if present, in the expansion
slots.
Note
The x950-52XSQ does not support XEM2
line cards.
Table 29. Stacking Worksheet Columns (Continued)
Column Description
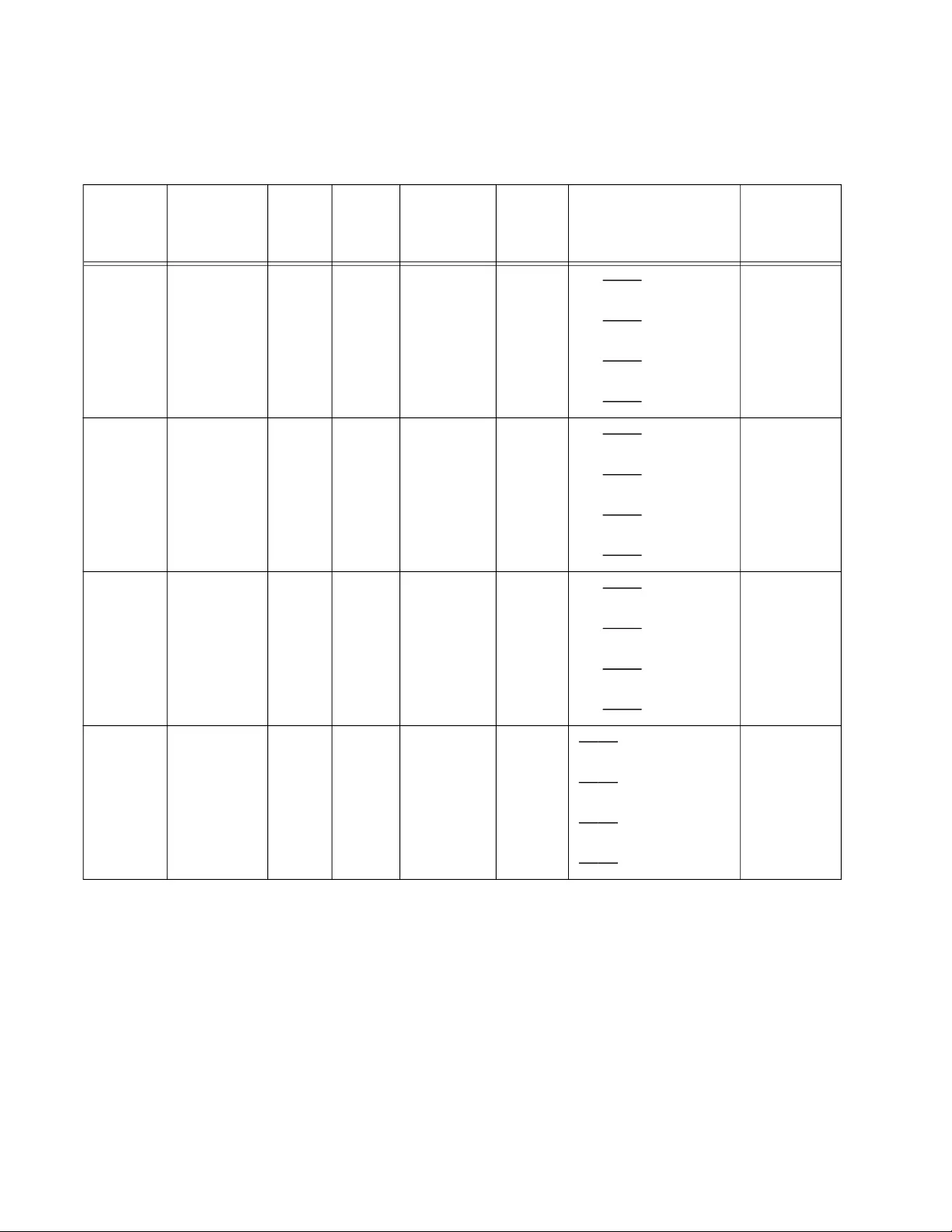
Chapter 3: Virtual Chassis Stacking
96
Table 30 is an example of a completed worksheet.
Table 30. Example of a Completed Stack Worksheet
Switch Switch/
Location
Switch
ID
Prior-
ity
Firmware
Version
Number
Trunk
Ports
Transceivers in
Slots
25 to 37
XEM2
Card
Master x950-
28XSQ
Bldg 2A
rm:304
1 1 v5.4.9-0 33, 37 25 or 49: empty
29 or 53: 40Gbps
33 or 57: 100Gbps
37 or 61: 100Gbps
none
Member x950-
28XTQm
Bldg 2A
rm:304
2 2 v5.4.9-0 33, 37 25 or 49: 40Gbps
29 or 53: 40Gbps
33 or 57: 100Gbps
37 or 61: 100Gbps
XEM2-
12XS
Member x950-
28XTQm
Bldg 2A
rm:304
3 3 v5.4.9-0 33, 37 25 or 49: 10Gbps
Breakout
29 or 53: Empty
33 or 57: 100Gbps
37 or 61: 100Gbps
XEM2-
4QS
Member x950-
52XSQ
Bldg 2A
rm:304
4 4 v5.5.0-1 57, 61 25 or 49: 10Gbps
Breakout
29 or 53: 100Gbps
33 or 57: 100Gbps
37 or 61: 100Gbps
none1
1. The x950-52XSQ switch does not support XEM2 line cards.
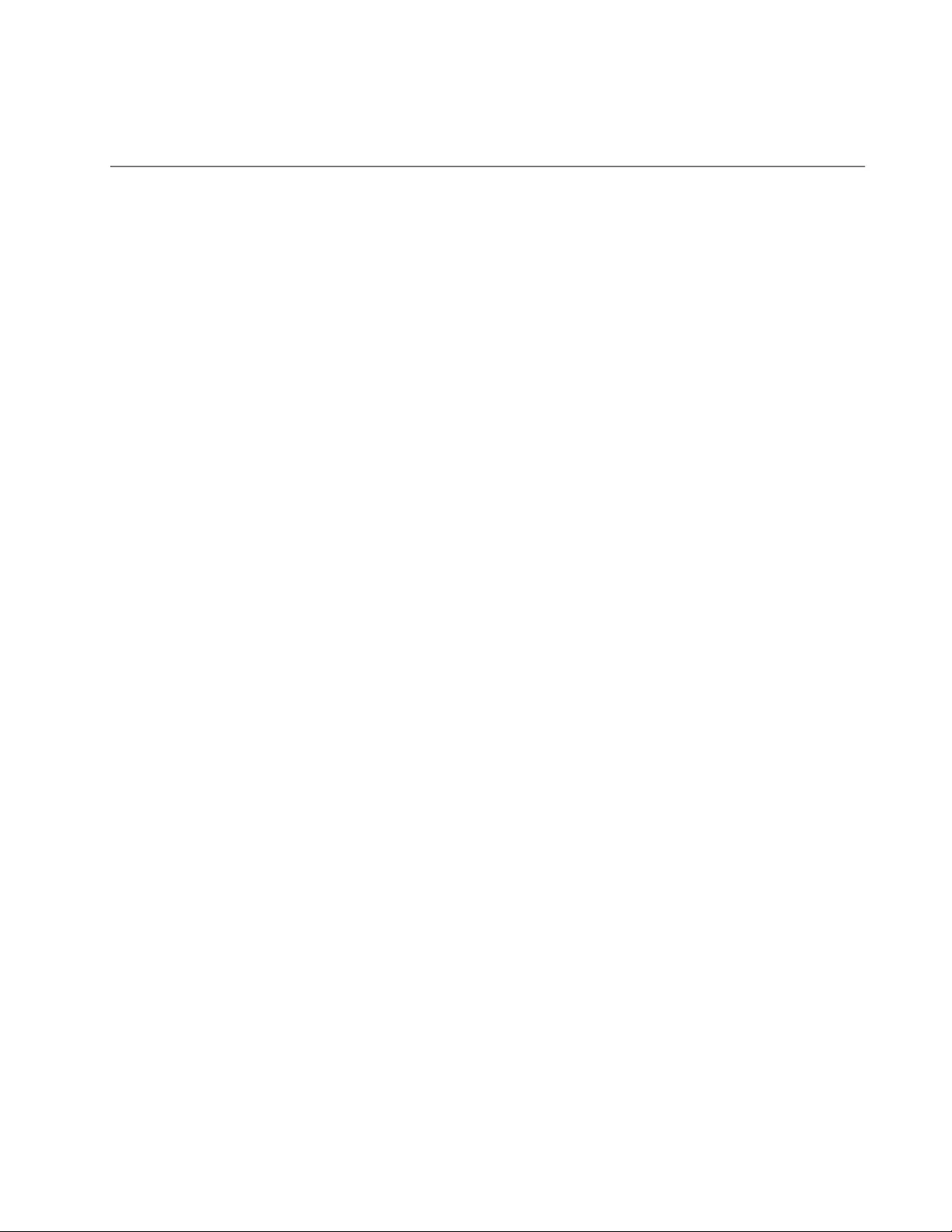
97
Chapter 4
Beginning the Installation
The chapter contains the following sections:
“Reviewing Safety Precautions” on page 98
“Installation Options” on page 103
“Choosing a Site for the Chassis” on page 104
“Unpacking the Switch” on page 105
“Verifying the Accessory Kit” on page 109
“Unpacking the PWR600 AC Power Supply” on page 111
“Unpacking the PWR600 DC Power Supply” on page 114
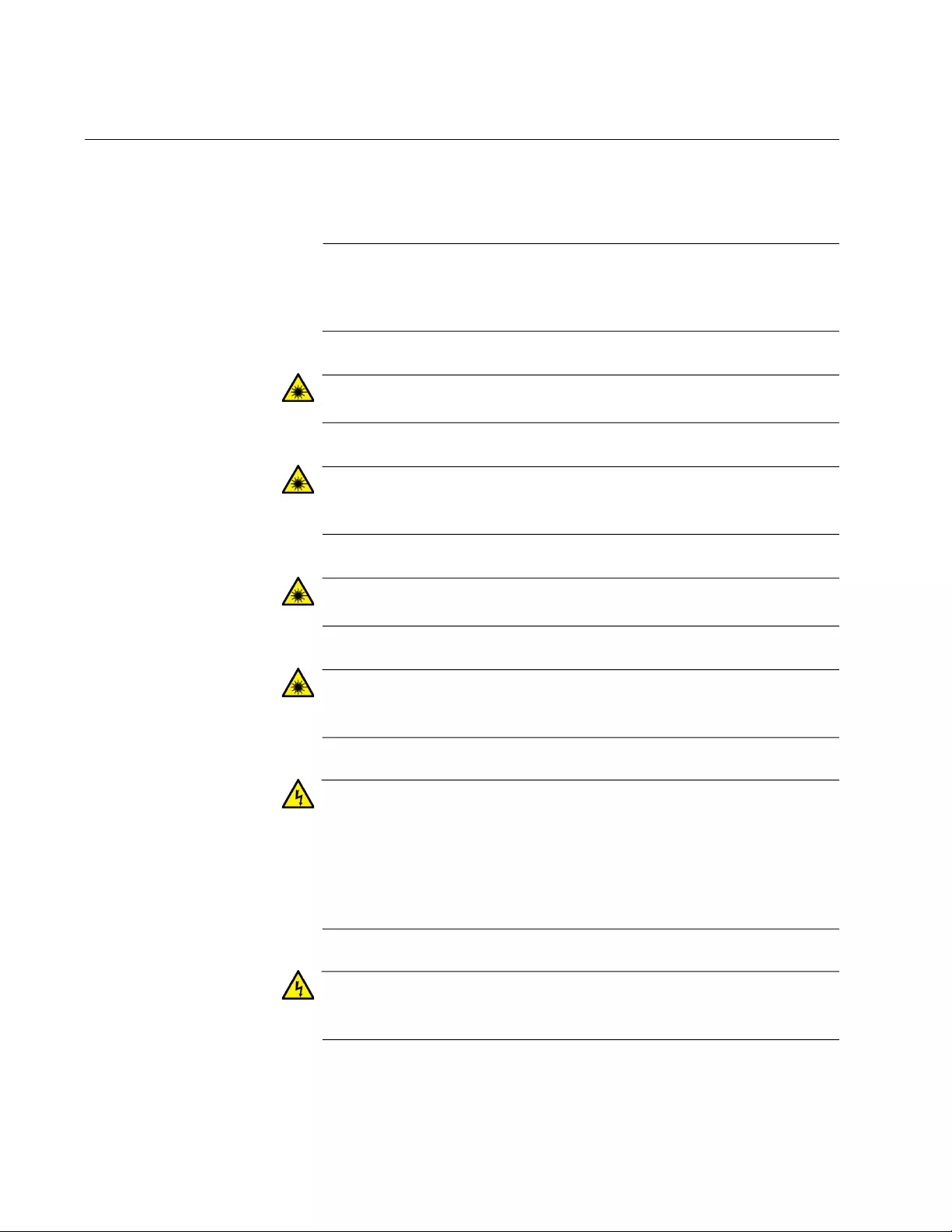
Chapter 4: Beginning the Installation
98
Reviewing Safety Precautions
Please review the following safety precautions before beginning the
installation procedure.
Note
Safety statements that have the symbol are translated into
multiple languages in the Translated Safety Statements document at
www.alliedtelesis.com/support.
Warning
Class 1 Laser product. L1
Warning
Laser Radiation.
Class 1M Laser product.
Warning
Do not stare into the laser beam. L2
Warning
Do not look directly at the fiber optic ends or inspect the cable ends
with an optical lens. L6
Warning
To prevent electric shock, do not remove the cover. No user-
serviceable parts inside. This unit contains hazardous voltages and
should only be opened by a trained and qualified technician. To
avoid the possibility of electric shock, disconnect electric power to
the product before connecting or disconnecting the LAN cables.
E1
Warning
Do not work on equipment or cables during periods of lightning
activity. E2
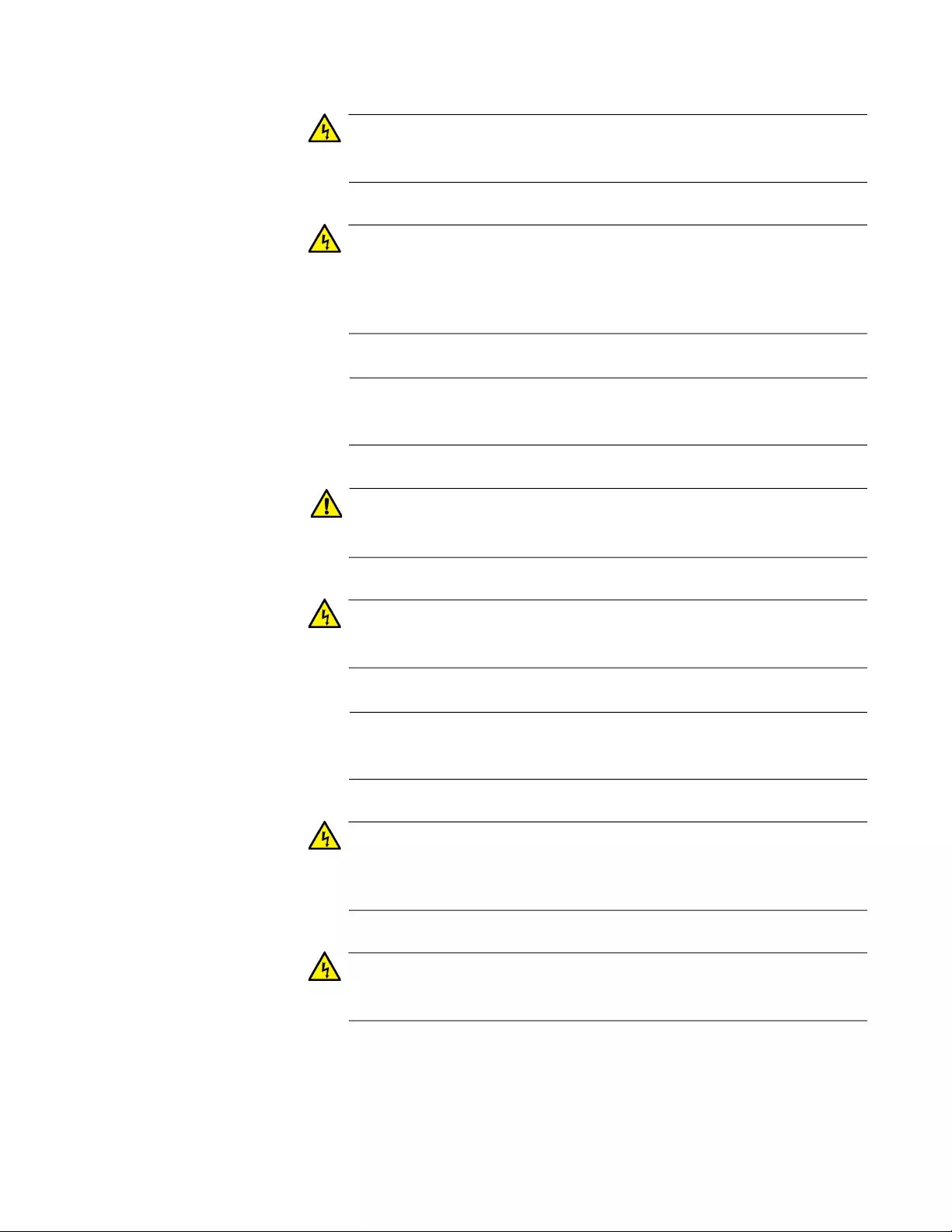
x950 Series Installation Guide for VCStack
99
Warning
Power cord is used as a disconnection device. To de-energize
equipment, disconnect the power cord. E3
Warning
Class I Equipment. This equipment must be earthed. The power
plug must be connected to a properly wired earth ground socket
outlet. An improperly wired socket outlet could place hazardous
voltages on accessible metal parts. E4
Note
Pluggable Equipment. The socket outlet shall be installed near the
equipment and shall be easily accessible. E5
Caution
Air vents must not be blocked and must have free access to the
room ambient air for cooling. E6
Warning
Operating Temperatures. This product is designed for a maximum
ambient temperature of 50° degrees C. E52
Note
All Countries: Install product in accordance with local and National
Electrical Codes. E8
Warning
Do not strip more than the recommended amount of wire. Stripping
more than the recommended amount can create a safety hazard by
leaving exposed wire on the terminal block after installation. E10
Warning
When installing this equipment, always ensure that the frame ground
connection is installed first and disconnected last. E11
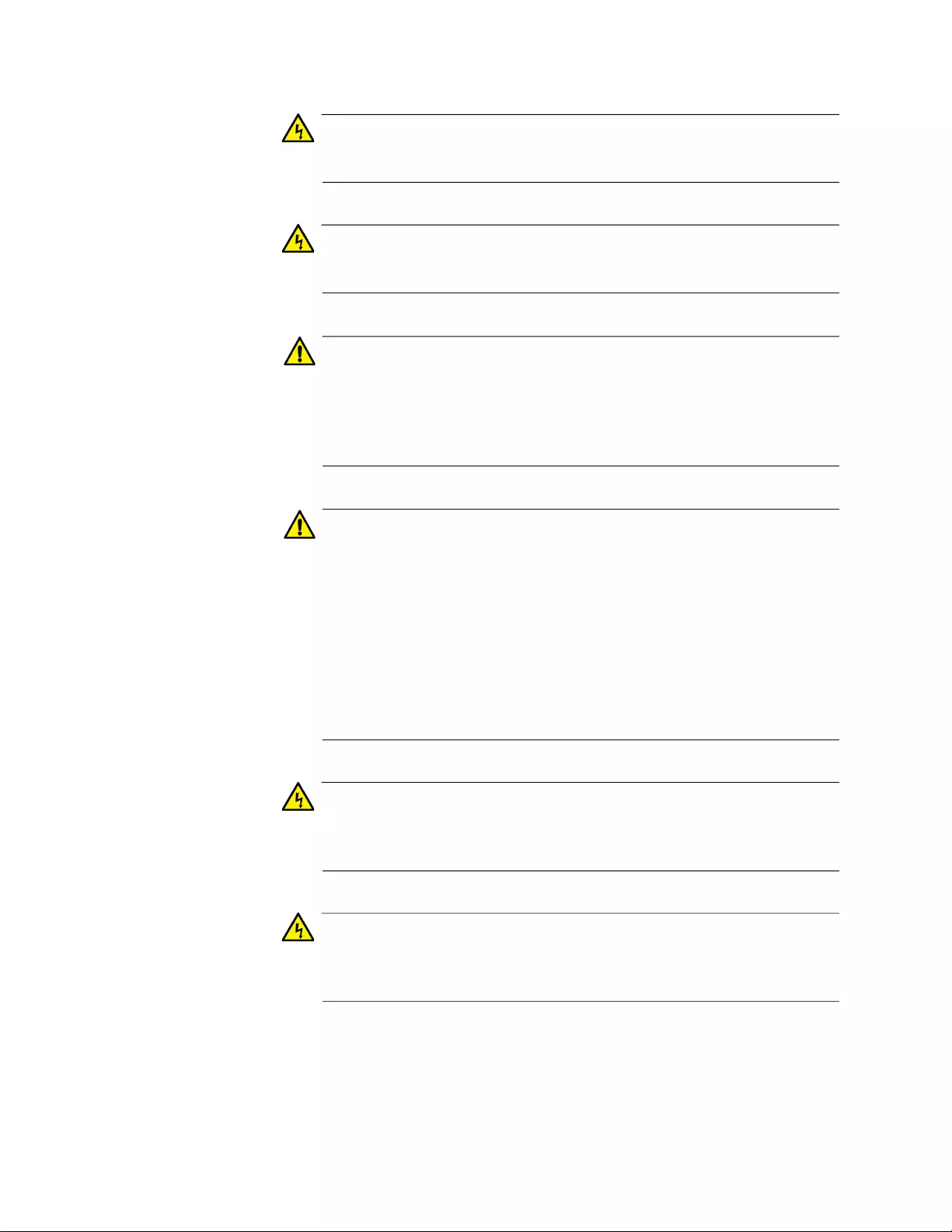
Chapter 4: Beginning the Installation
100
Warning
Only trained and qualified personnel are allowed to install or replace
this equipment. E14
Warning
The equipment must be earthed. The ground screw on the unit must
be connected to a properly earthed bonding point. E120
Caution
Circuit Overloading: Consideration should be given to the
connection of the equipment to the supply circuit and the effect that
overloading of circuits might have on overcurrent protection and
supply wiring. Appropriate consideration of equipment nameplate
ratings should be used when addressing this concern. E21
Caution
Risk of explosion if battery is replaced by an incorrect type. Replace
only with the same or equivalent type recommended by the
manufacturer. Dispose of used batteries according to the
manufacturer’s instructions.
Attention: Le remplacement de la batterie par une batterie de type
incorrect peut provoquer un danger d’explosion. La remplacer
uniquement par une batterie du même type ou de type équivalent
recommandée par le constructeur. Les batteries doivent être
éliminées conformément aux instructions du constructeur. E22
Warning
Mounting of the equipment in the rack should be such that a
hazardous condition is not created due to uneven mechanical
loading. E25
Warning
The chassis may be heavy and awkward to lift. Allied Telesis
recommends that you get assistance when mounting the chassis in
an equipment rack. E28
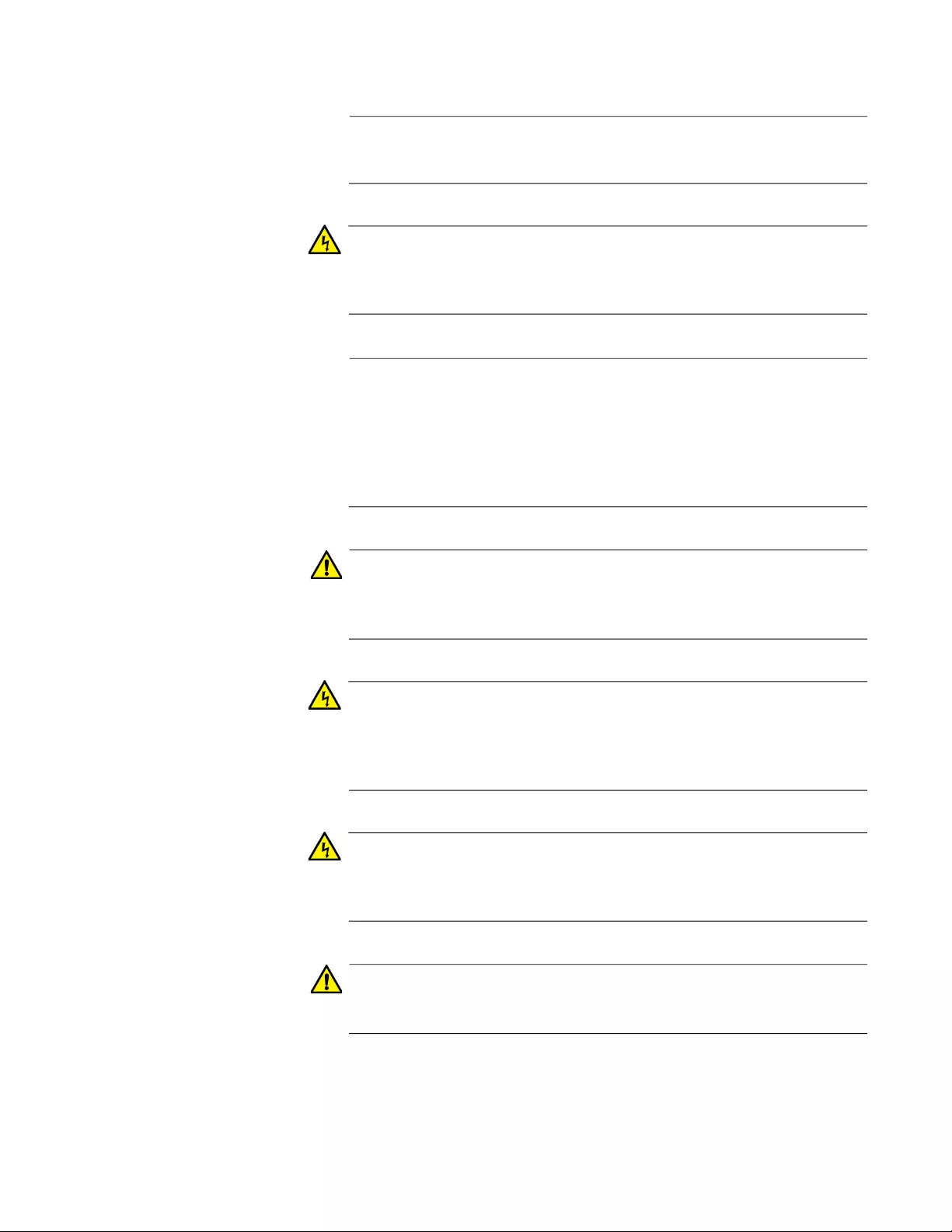
x950 Series Installation Guide for VCStack
101
Note
Use dedicated power circuits or power conditioners to supply
reliable electrical power to the device. E27
Warning
This unit might have more than one power cord. To reduce the risk
of electric shock, disconnect all power cords before servicing the
unit. E30
Note
If installed in a closed or multi-unit rack assembly, the operating
ambient temperature of the rack environment may be greater than
the room ambient temperature. Therefore, consideration should be
given to installing the equipment in an environment compatible with
the manufacturer’s maximum rated ambient temperature (Tmra).
E35
Caution
Installation of the equipment in a rack should be such that the
amount of air flow required for safe operation of the equipment is not
compromised. E36
Warning
Reliable earthing of rack-mounted equipment should be maintained.
Particular attention should be given to supply connections other than
direct connections to the branch circuits (e.g., use of power strips).
E37
Warning
This product may have multiple AC power cords installed. To de-
energize this equipment, disconnect all power cords from the device.
E41
Caution
An Energy Hazard exists inside this equipment. Do not insert hands
or tools into open chassis slots or plugs. E44
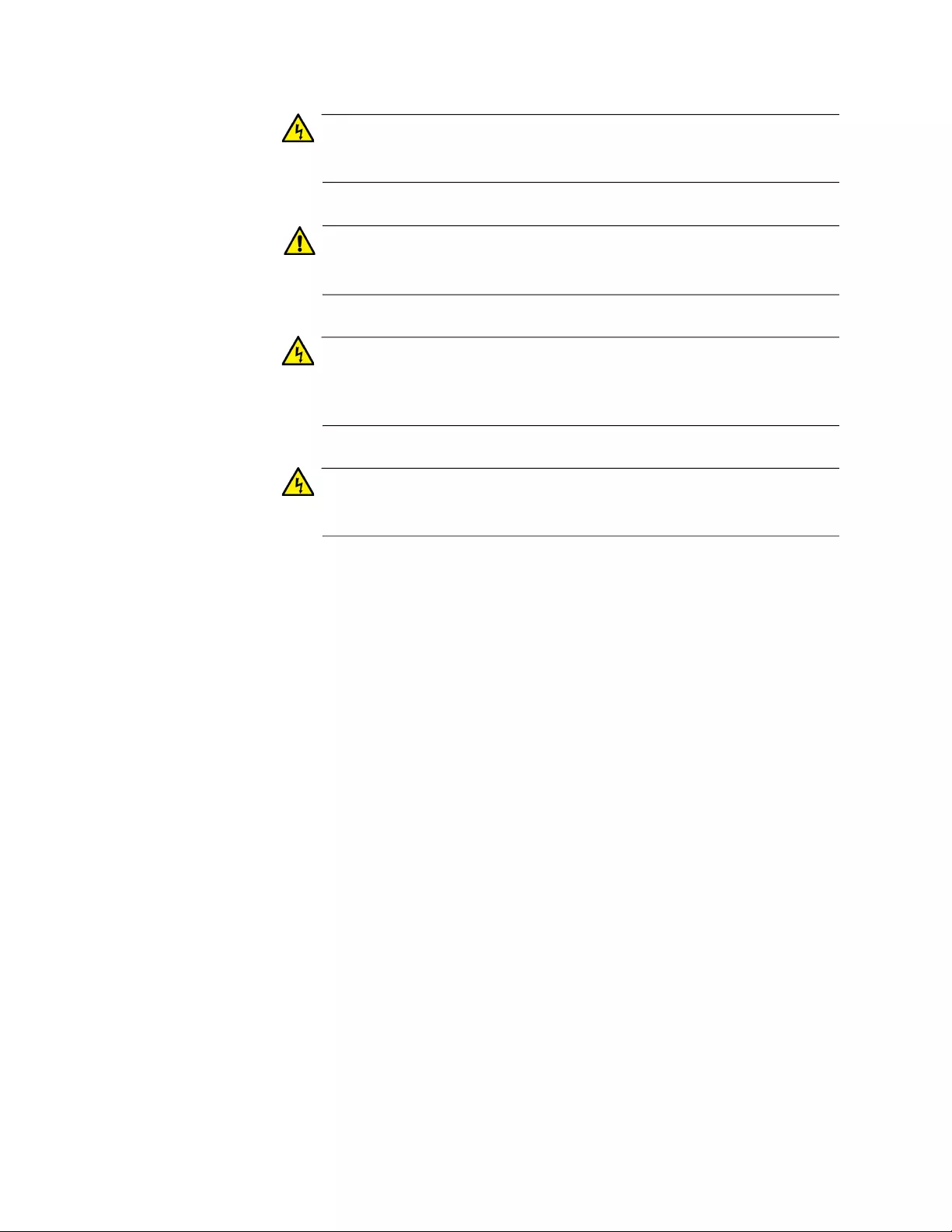
Chapter 4: Beginning the Installation
102
Warning
This equipment shall be installed in a Restricted Access location.
E45
Caution
The unit does not contain serviceable components. Please return
damaged units for servicing. E42
Warning
The temperature of an operational SFP or SFP+ transceiver may
exceed 70° C (158° F). Exercise caution when removing or handling
transceivers with unprotected hands. E43
Warning
The chassis must be supplied by a grounded three wire AC source
through the power supply cord.
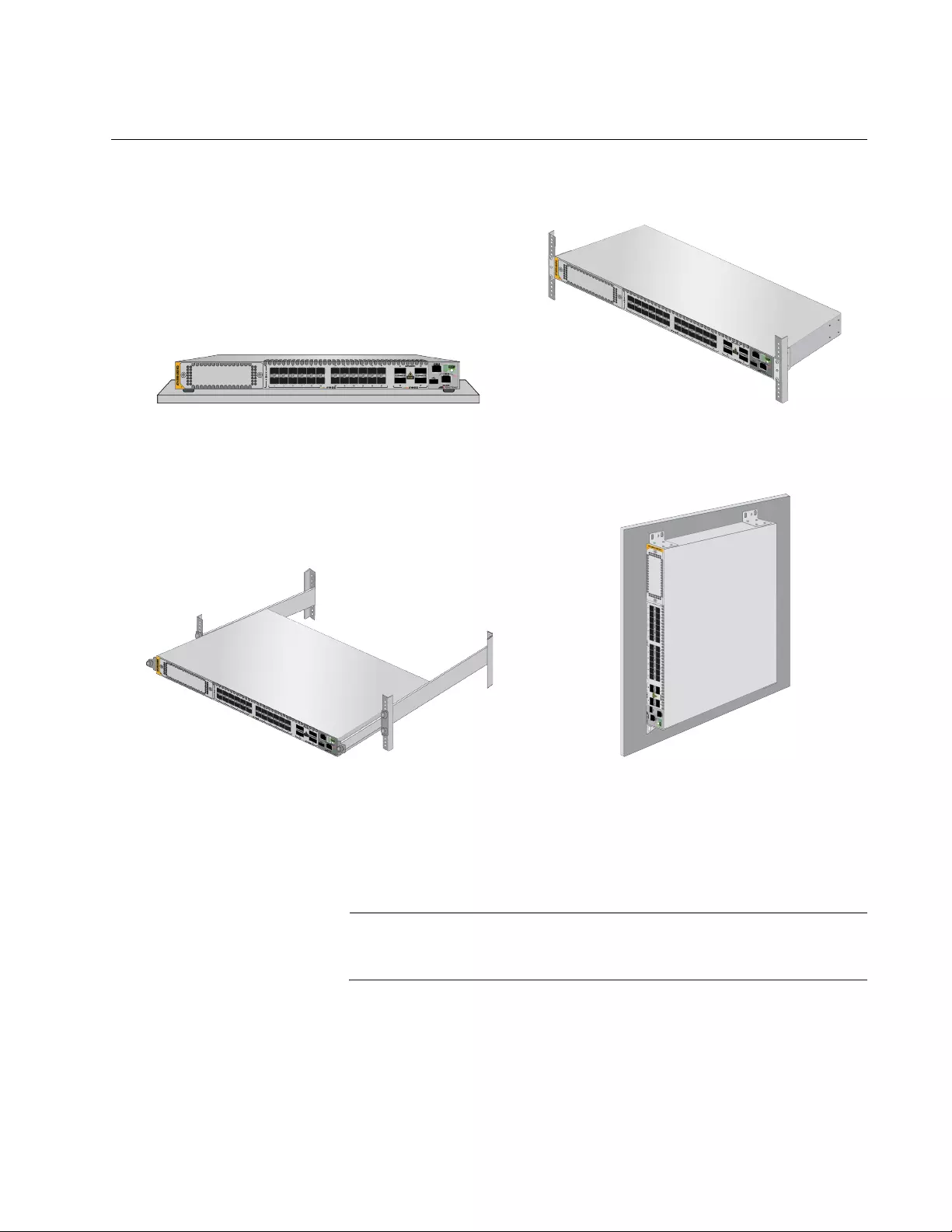
x950 Series Installation Guide for VCStack
103
Installation Options
Figure 45 illustrates the four installation options.
Figure 45. Installation Options
Note
The standard brackets are included with the switch, The optional
RKMT-SL01 Sliding Shelf is purchased separately.
This guide contains instructions for all installation options, except the
RKMT-SL01 Sliding Rack Mount Kit. Instructions for the latter are provided
in the RKMT-SL01 Sliding Rack Mount Kit Installation Guide on the Allied
Telesis web site,
19-inch Equipment Rack with
Optional RKMT-SL01 Sliding
Rack Mount Kit
19-inch Equipment Rack
with Standard Brackets
Wall Installation with
Standard Brackets
Tabletop
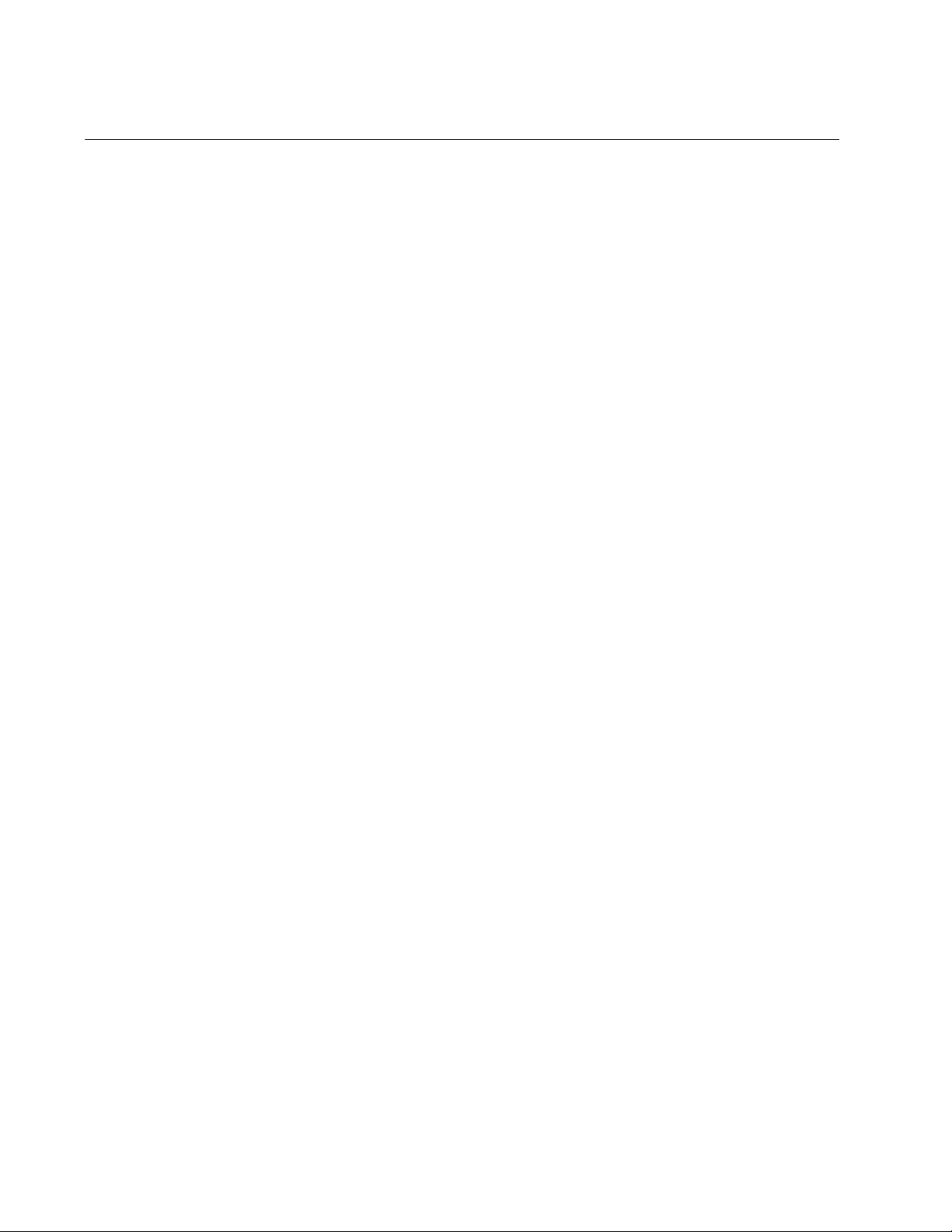
Chapter 4: Beginning the Installation
104
Choosing a Site for the Chassis
Observe these site requirements.
If you are installing the device in an equipment rack, check that the
rack is safely secured so that it will not tip over. Devices should be
installed in the rack starting at the bottom, with the heavier devices
near the bottom of the rack.
The power outlet should be located near the chassis and be easily
accessible.
The site should allow for easy access to the ports on the front of
the switch, so that you can easily connect and disconnect cables,
and view the port LEDs.
The site should allow for adequate air flow around the unit and
through the cooling vents on the front and rear panels. (The
ventilation direction is from front to back, with the fans on the back
panel drawing the air out of the unit.)
The site should not expose the switch to moisture or water.
The site should be a dust-free environment.
The site should include dedicated power circuits or power
conditioners to supply reliable electrical power to the network
devices.
Twisted pair cabling should not be exposed to sources of electrical
noise, such as radio transmitters, broadband amplifiers, power
lines, electric motors, or fluorescent fixtures.
Switch ports are suitable for intra-building connections, or where
non-exposed cabling is required.
Do not install the device in a wiring or utility box that has
inadequate airflow because it might overheat and fail.
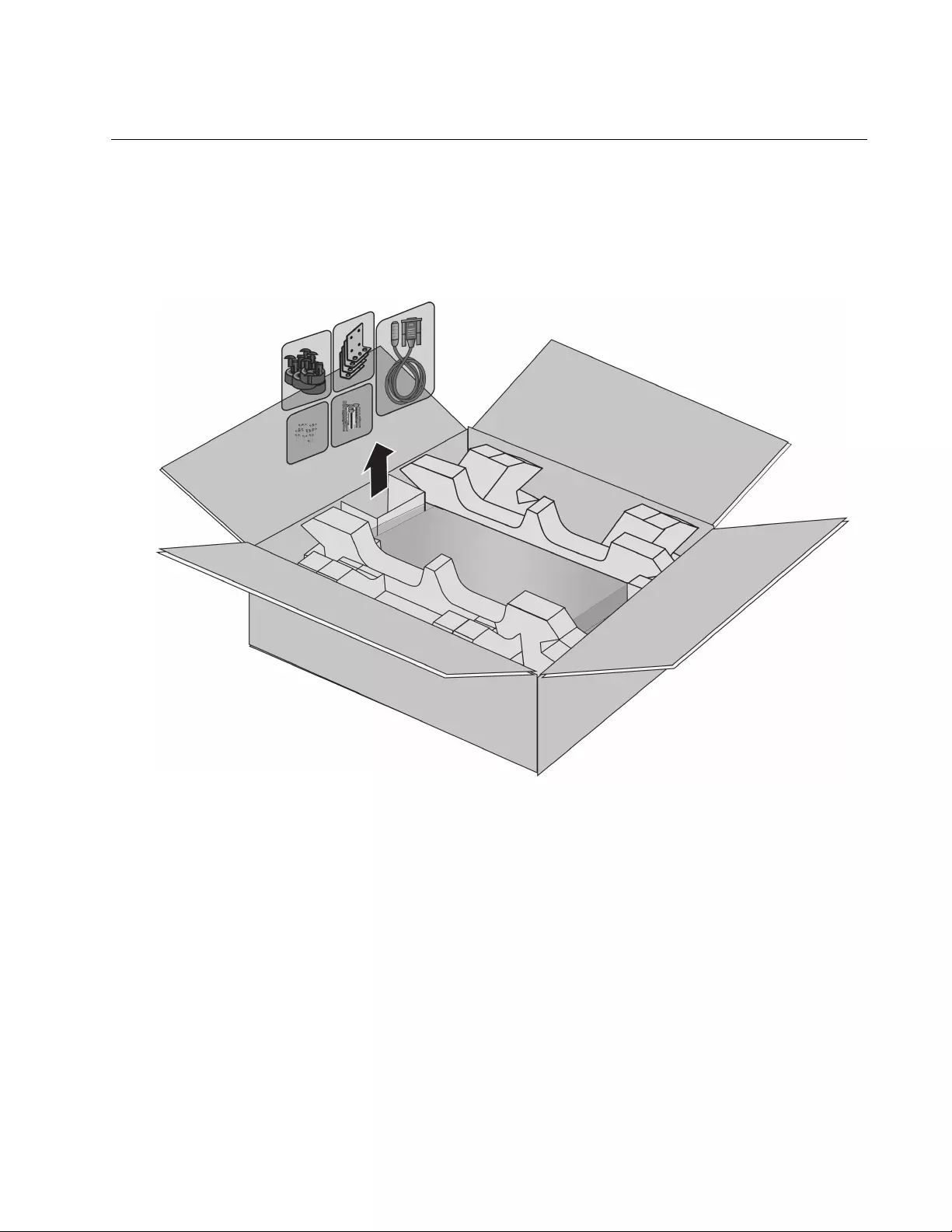
x950 Series Installation Guide for VCStack
105
Unpacking the Switch
To unpack the switch from its shipping box, perform the following
procedure:
1. Remove the accessories and documents from the accessory partition.
Refer to Figure 46.
Figure 46. Removing Accessories
2. Remove the accessory partition. Refer to Figure 47 on page 106.
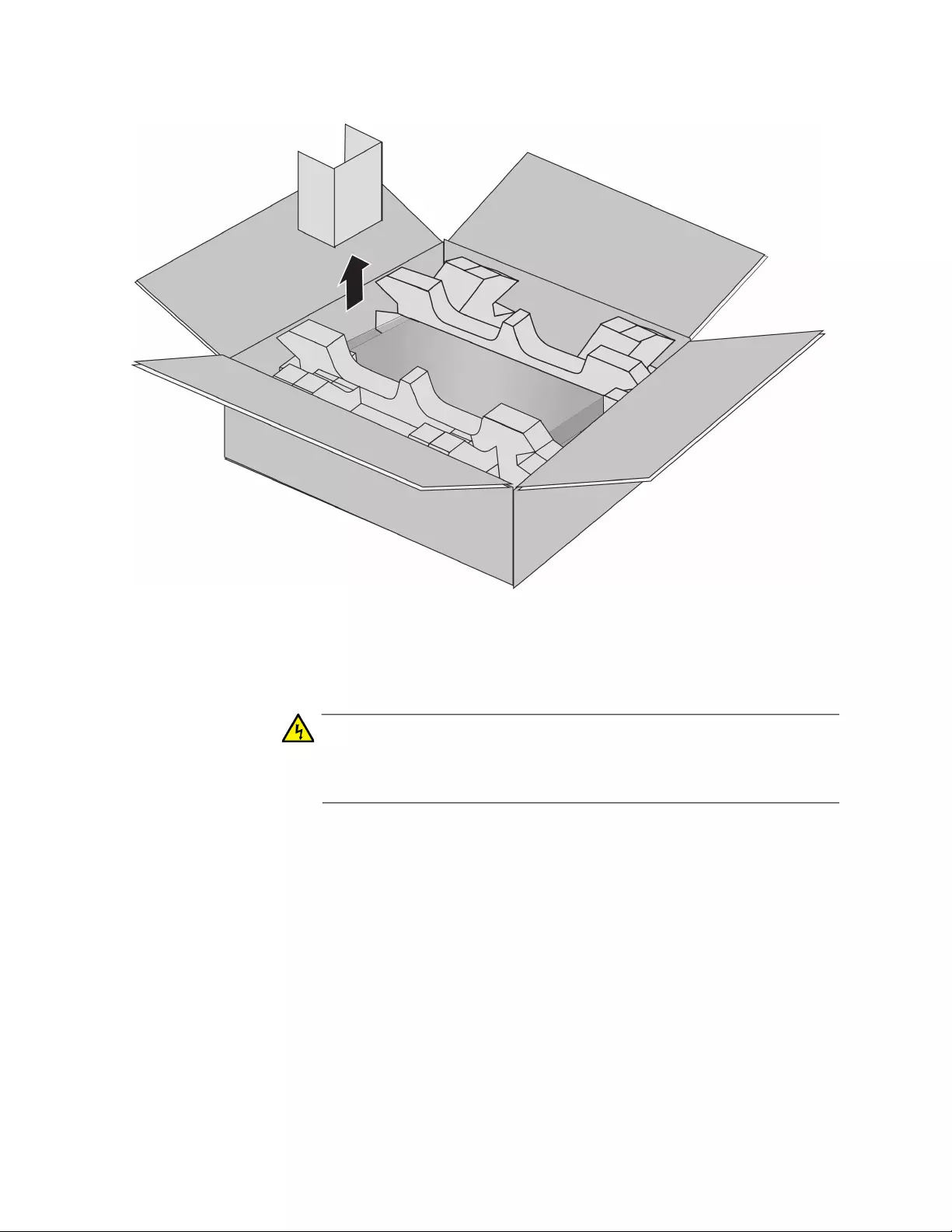
Chapter 4: Beginning the Installation
106
Figure 47. Removing the Shipping Partition
3. Lift the switch from the shipping box and place it on a level, secure
table. Refer to Figure 48 on page 107.
Warning
The switch is heavy. Ask for assistance lifting the device out of the
shipping box. You might injure yourself or damage the device if you
lift it without assistance.
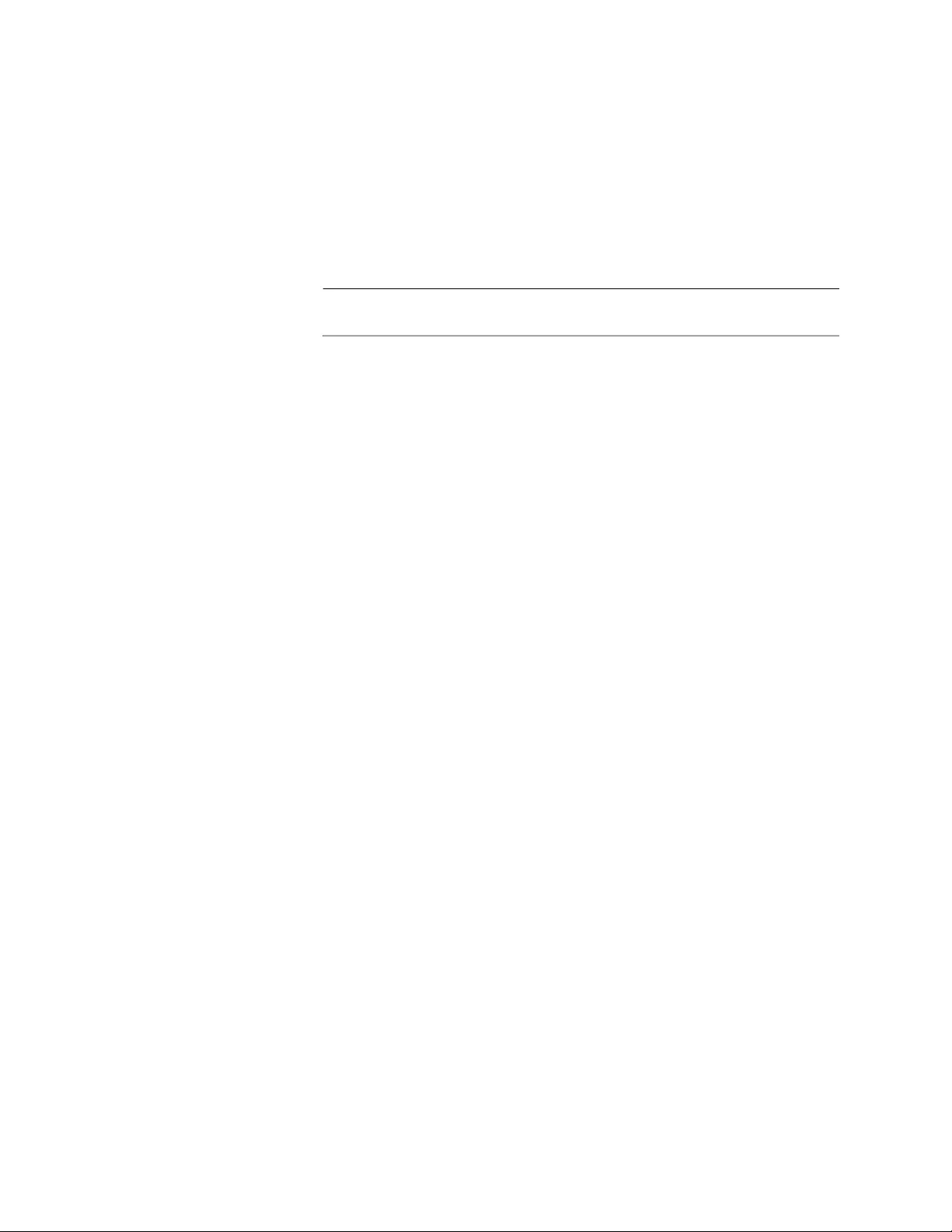
Chapter 4: Beginning the Installation
108
5. Visually inspect the product for damage.
6. Visually inspect the front panel for the components shown in Figure 1
on page 20.
7. Verify that there are two pre-installed fan modules in FAN A and FAN
B slots on the rear panel. Refer to Figure 2 on page 21 and “FAN05
Cooling Fan” on page 45.
Note
Do not power on the switch if it is missing a fan module.
8. Go to “Verifying the Accessory Kit” on page 109.
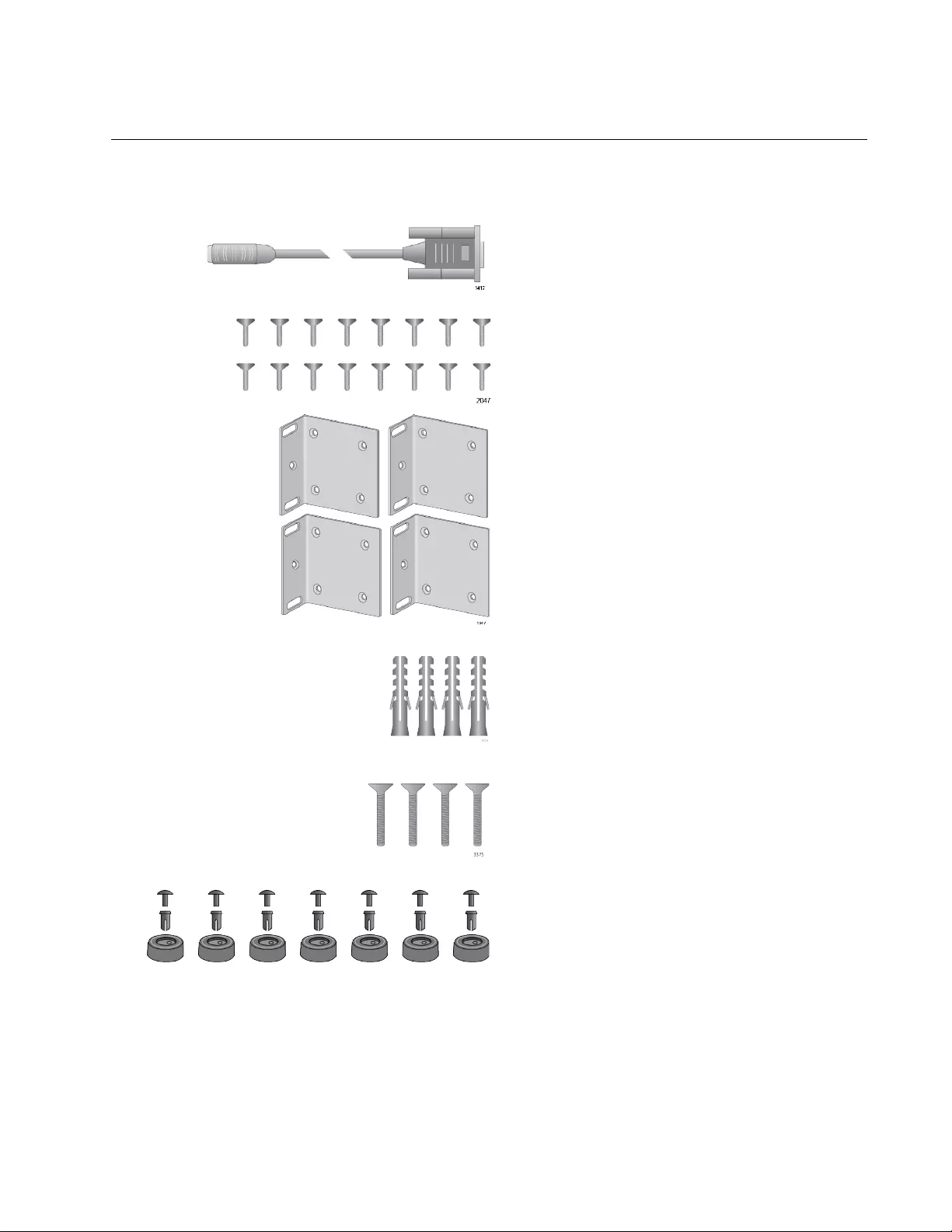
x950 Series Installation Guide for VCStack
109
Verifying the Accessory Kit
Figure 50 lists the accessory items that are included with the switch.
Figure 50. Accessory Kit
Four standard equipment rack
or wall mounting brackets
One 2 m (6.6 ft) local management
cable with RJ-45 (8P8C) and DB-9
(D-sub 9-pin) connectors.
Sixteen bracket screws
Four anchors for concrete
walls:
Length: 29.6mm (1.2 in.)
Diameter: 4mm (0.2 in.)
Four screws for wood or
concrete walls:
Length: 32.6mm (1.3 in.)
Diameter: 4mm (0.2 in.)
Seven bumper feet
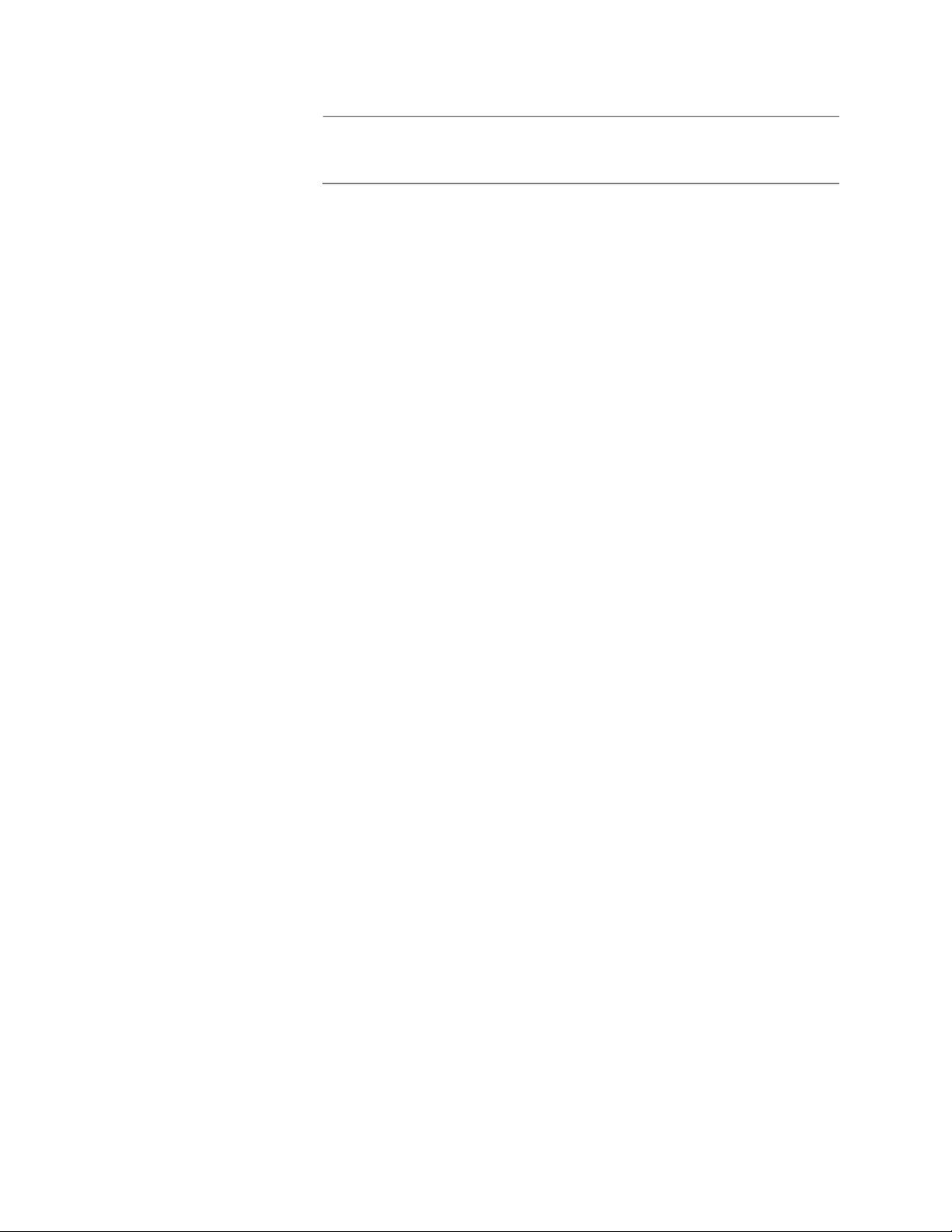
Chapter 4: Beginning the Installation
110
Note
If any item is missing or damaged, contact your Allied Telesis sales
representative for assistance.
After unpacking the switch and verifying the accessory kit, go to
“Unpacking the PWR600 AC Power Supply” on page 111 or “Unpacking
the PWR600 DC Power Supply” on page 114.
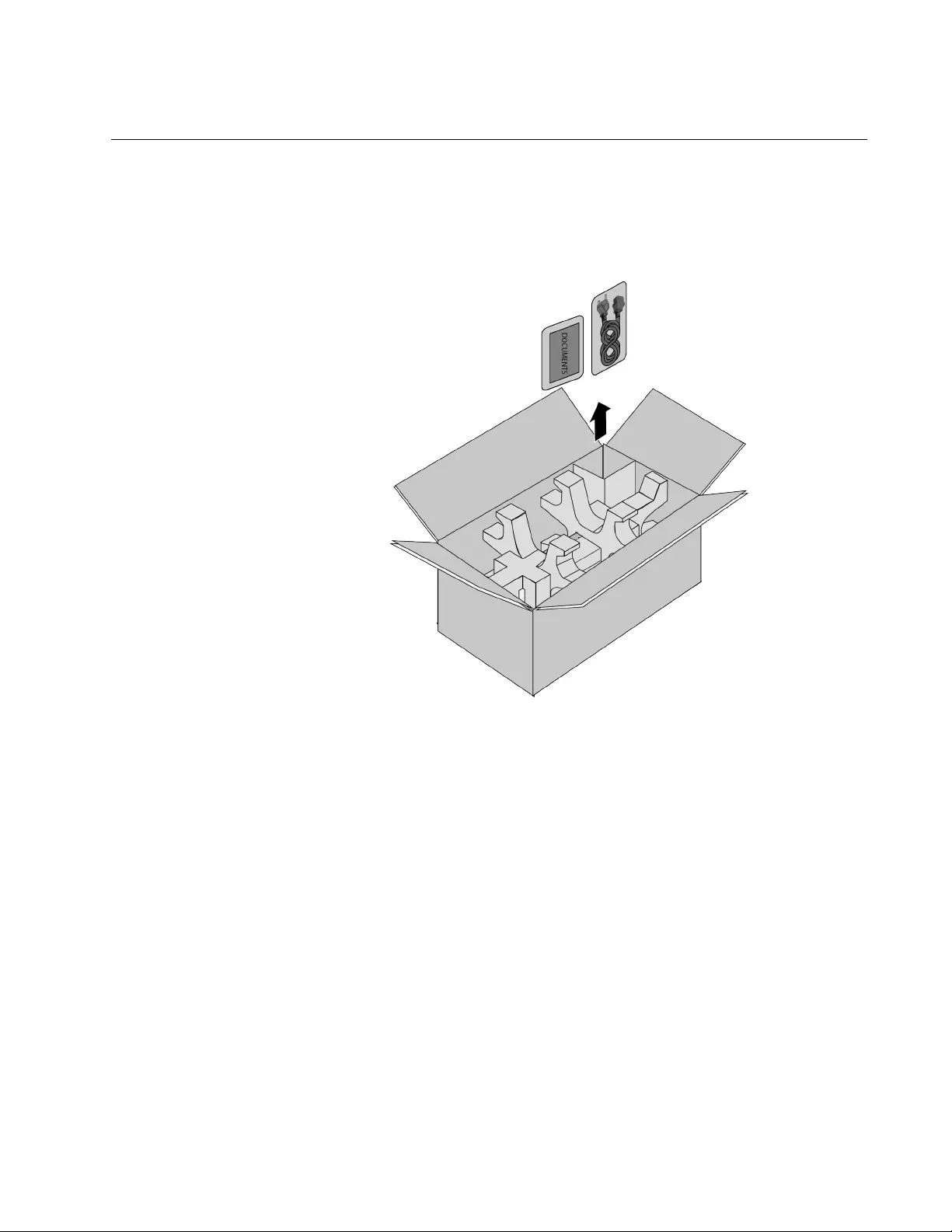
x950 Series Installation Guide for VCStack
111
Unpacking the PWR600 AC Power Supply
To unpack the PWR600 Power Supply, perform the following procedure:
1. Remove the power cord and any documents from the accessory
partition. Refer to Figure 51.
Figure 51. Removing the Power Cord and Documents from the PWR600
AC Power Supply
2. Remove the partition from the shipping box. Refer to Figure 52 on
page 112.
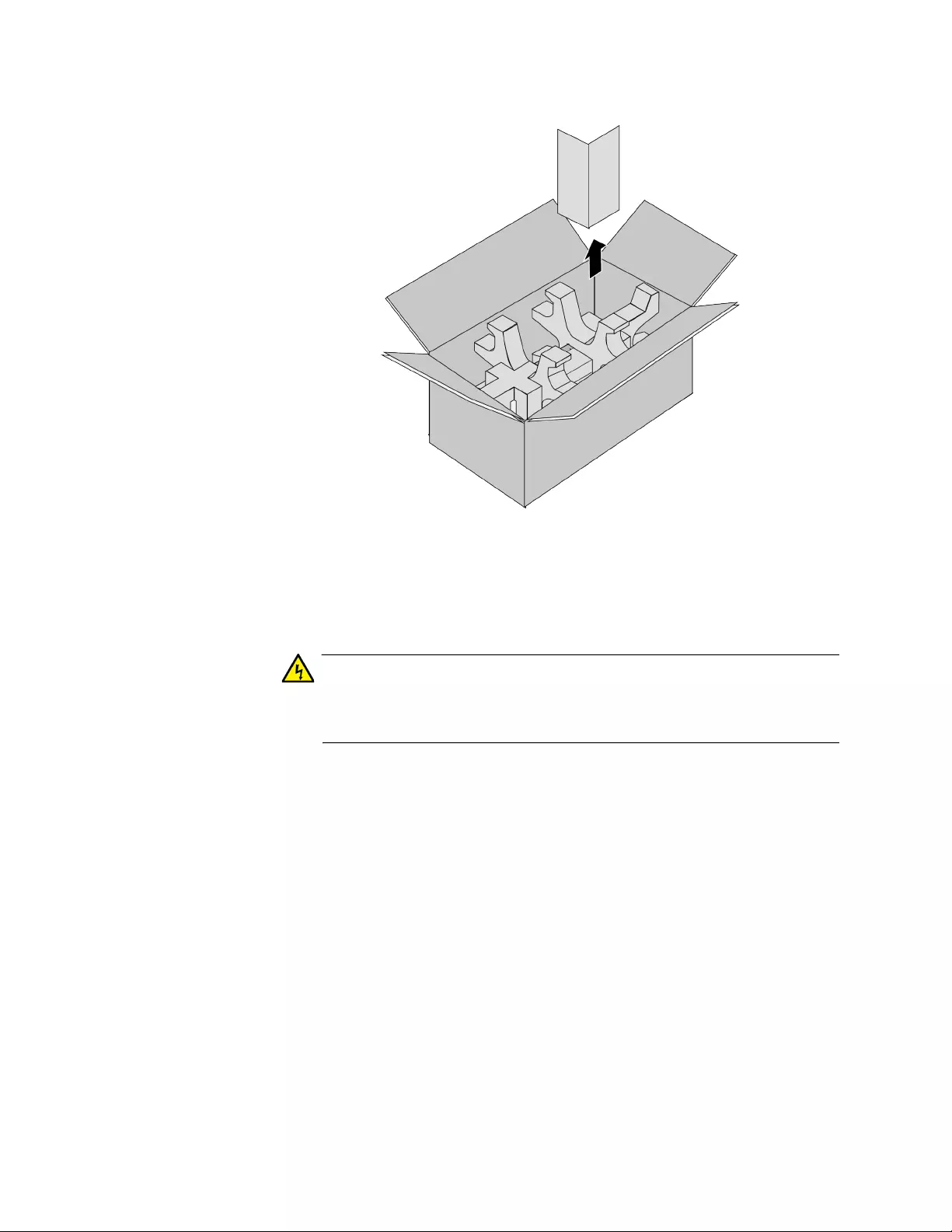
Chapter 4: Beginning the Installation
112
Figure 52. Removing the Partition from the PWR600 AC Power Supply
Shipping Box
3. Lift the power supply from the shipping box and place it on a level,
secure table. Refer to Figure 53 on page 113.
Warning
The power supply is heavy. Ask for assistance lifting the device out
of the shipping box. You might injure yourself or damage the device
if you lift it without assistance.
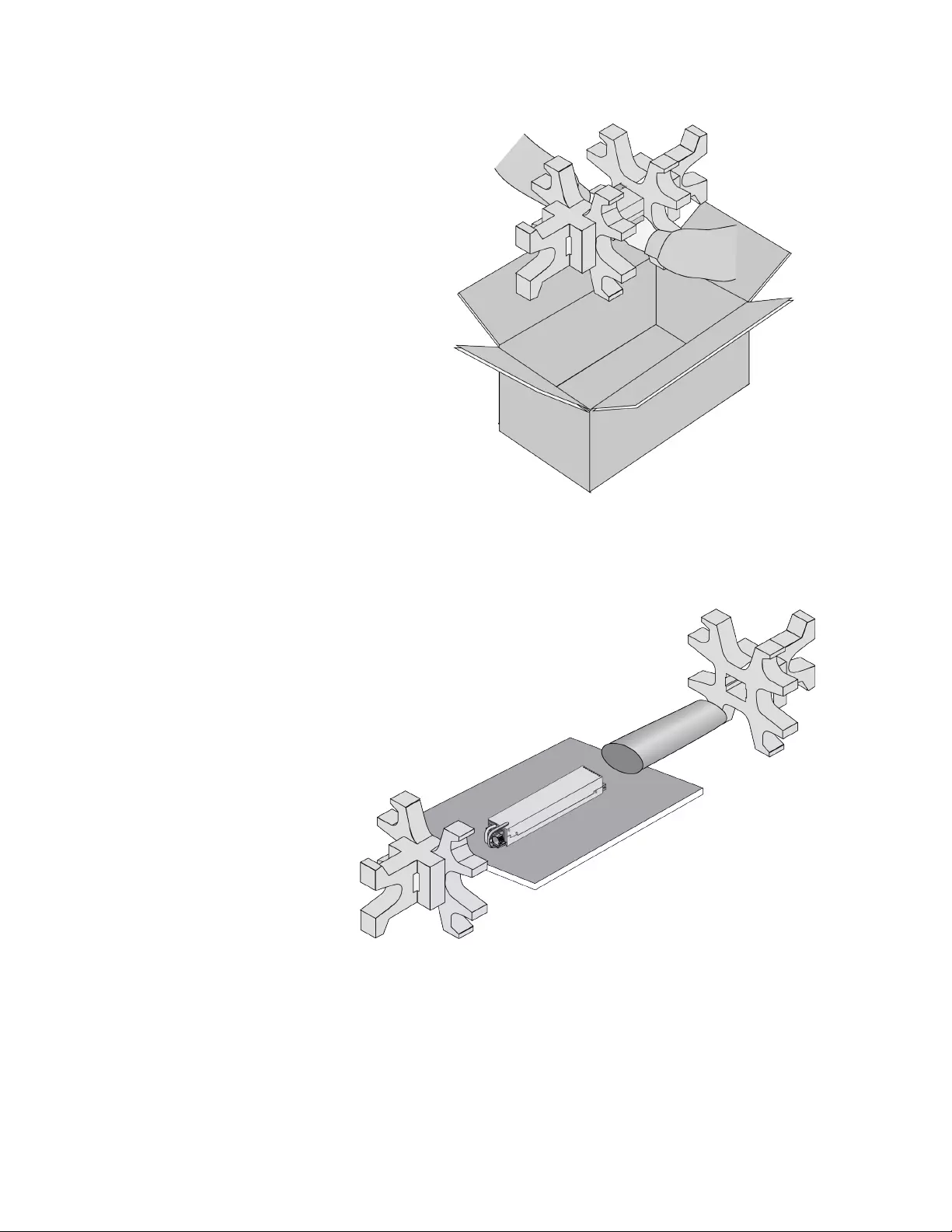
x950 Series Installation Guide for VCStack
113
Figure 53. Removing the Power Supply from the Shipping Box
4. Remove the power supply from the shipping end-caps and protective
shipping bag. Refer to Figure 54.
Figure 54. Removing the Power Supply from the Shipping End-caps and
Protective Bag
5. Visually inspect the product for damage.
6. After unpacking the switch and power supplies, go to Chapter 5,
“Installing Power Supplies and Optional XEM2 Line Card” on page
115.
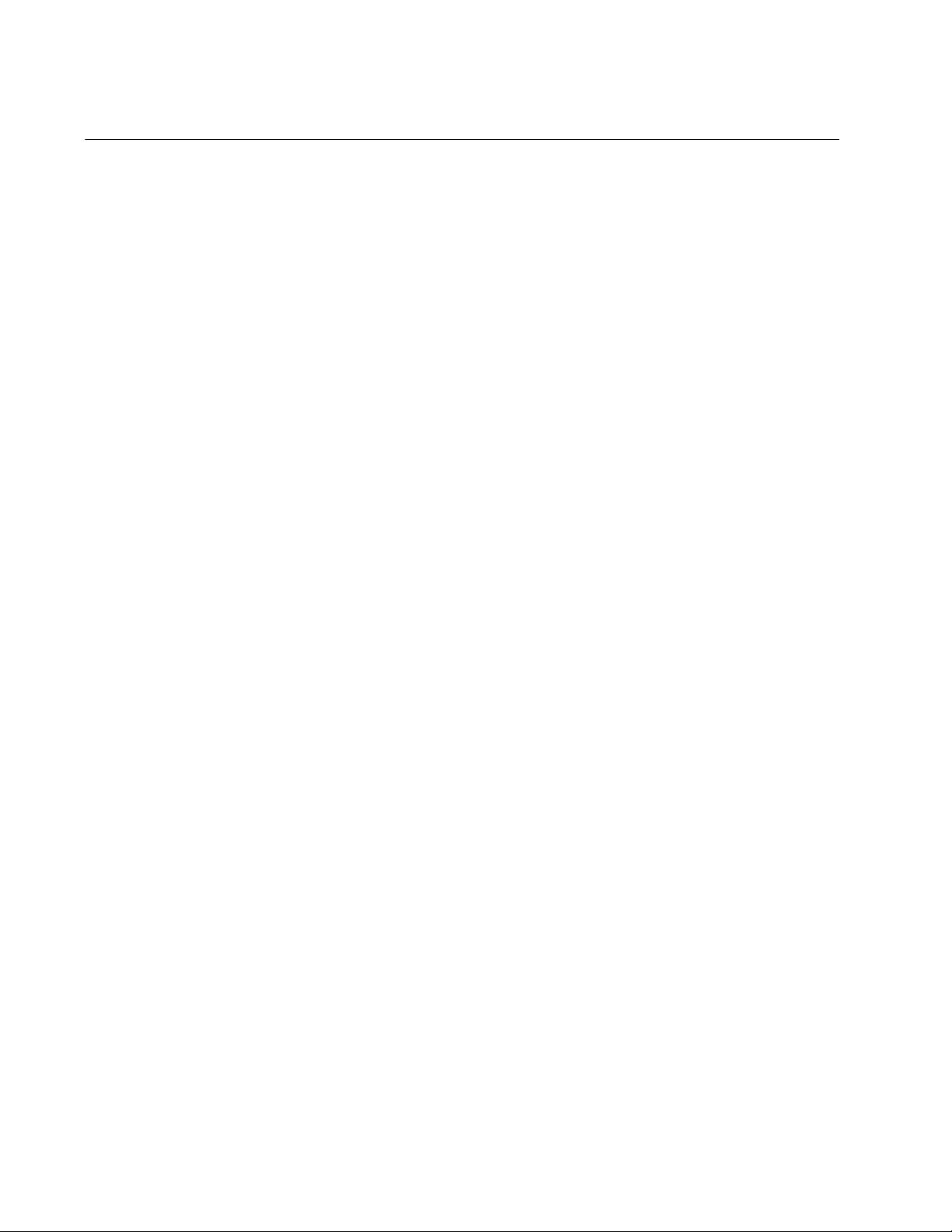
Chapter 4: Beginning the Installation
114
Unpacking the PWR600 DC Power Supply
To unpack the PWR600 DC Power Supply, perform the following
procedure:
1. Open the box and remove the PWR600 DC power supply.
2. Visually inspect the product for damage.
3. After unpacking the switch and power supplies, go to Chapter 5,
“Installing Power Supplies and Optional XEM2 Line Card” on page
115.
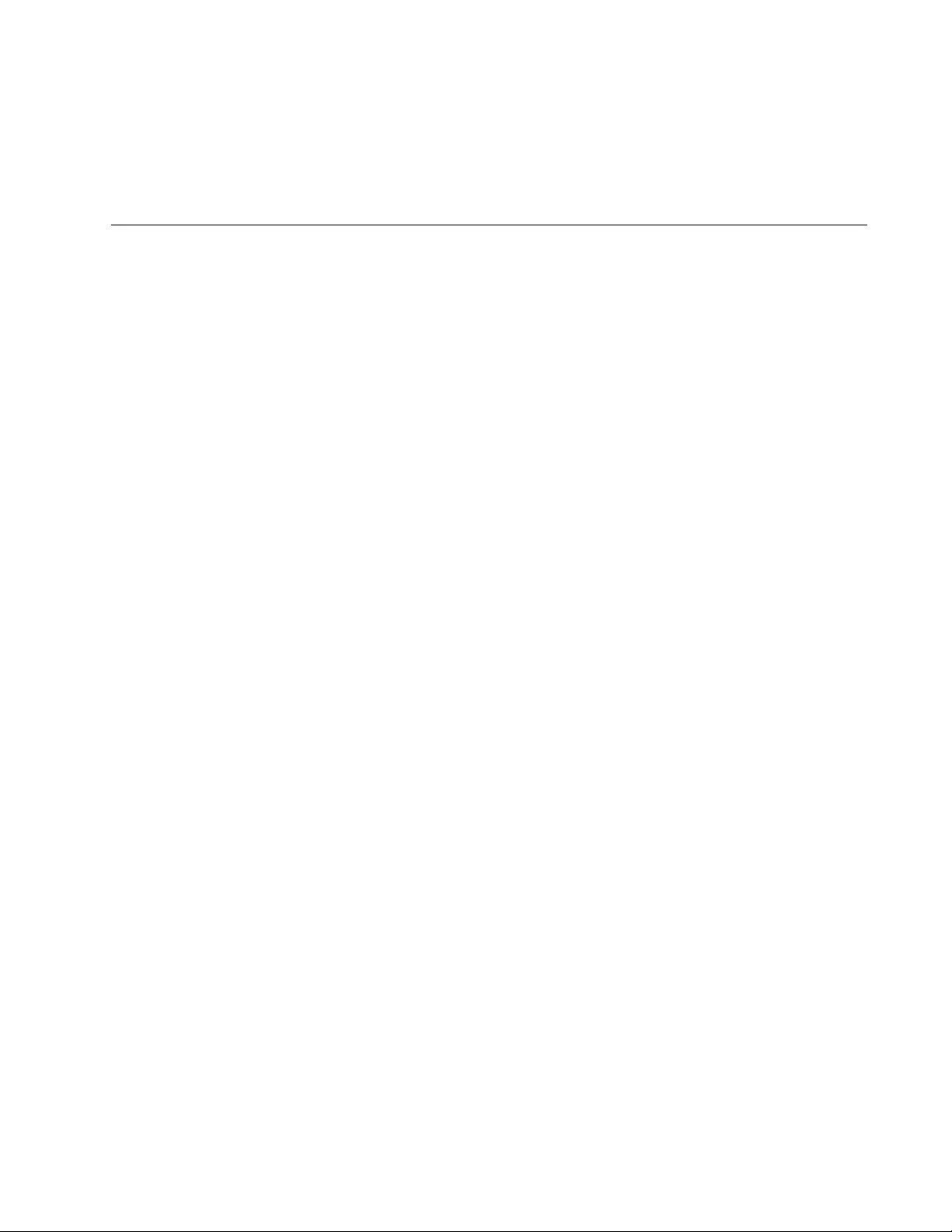
115
Chapter 5
Installing Power Supplies and Optional
XEM2 Line Card
This chapter has the following procedures:
“Installing PWR600 AC Power Supplies” on page 116
“Installing PWR600 DC Power Supplies” on page 120
“Connecting the Grounding Wire” on page 123
“Connecting the DC Power Wires” on page 126
“Installing an Optional XEM2 Ethernet Line Card” on page 130
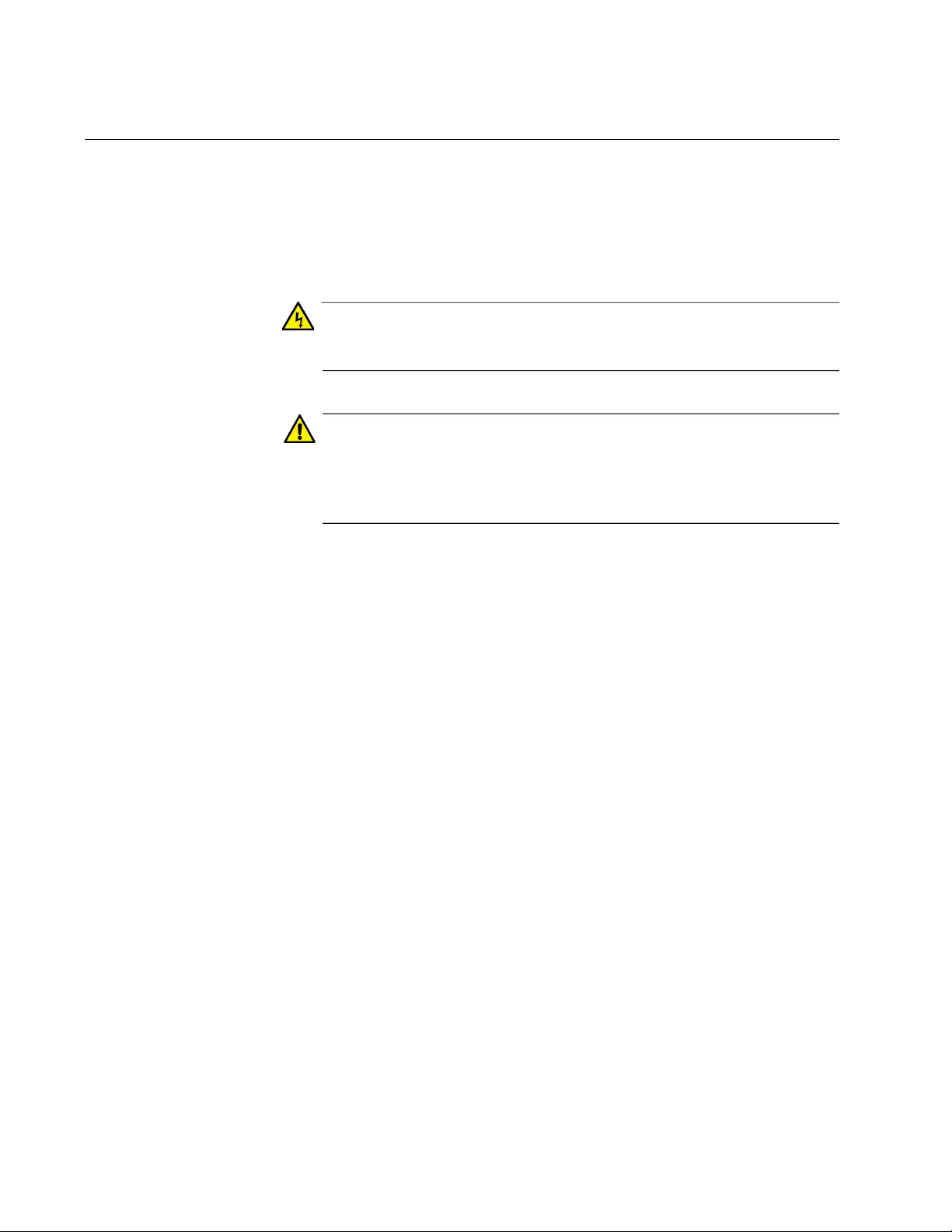
Chapter 5: Installing Power Supplies and Optional XEM2 Line Card
116
Installing PWR600 AC Power Supplies
This section contains the procedure for installing PWR600 AC Power
Supplies in the switch. For background information, refer to “PWR600 AC
and DC Power Supplies” on page 40. For a list of power supply
components, refer to “Unpacking the PWR600 AC Power Supply” on
page 111.
Warning
The power supply is heavy. Use both hands to lift it. You might injure
yourself or damage the device if you drop it.
Caution
The device can be damaged by static electricity. Be sure to follow
proper anti-static precautions when installing the device. Allied
Telesis recommends using a properly grounded wrist strap or other
personal anti-static device and an anti-static mat.
To install a PWR600 AC power supply, perform the following procedure:
1. Choose a slot for the power supply. The two power supply slots are
labeled PSU A and PSU B on the left side of the rear panel.
If you are installing only one power supply, you can install it in either
slot. Allied Telesis recommends PSU A because that slot does not
come with a blank power supply panel.
2. If there is already a power supply in PSU A, remove the blank panel
from PSU B slot by pressing the release tab to the right and sliding the
panel from the switch. Refer to Figure 55 on page 117.

x950 Series Installation Guide for VCStack
117
Figure 55. Removing the Blank Power Supply Panel from Slot PSU B
Release Tab
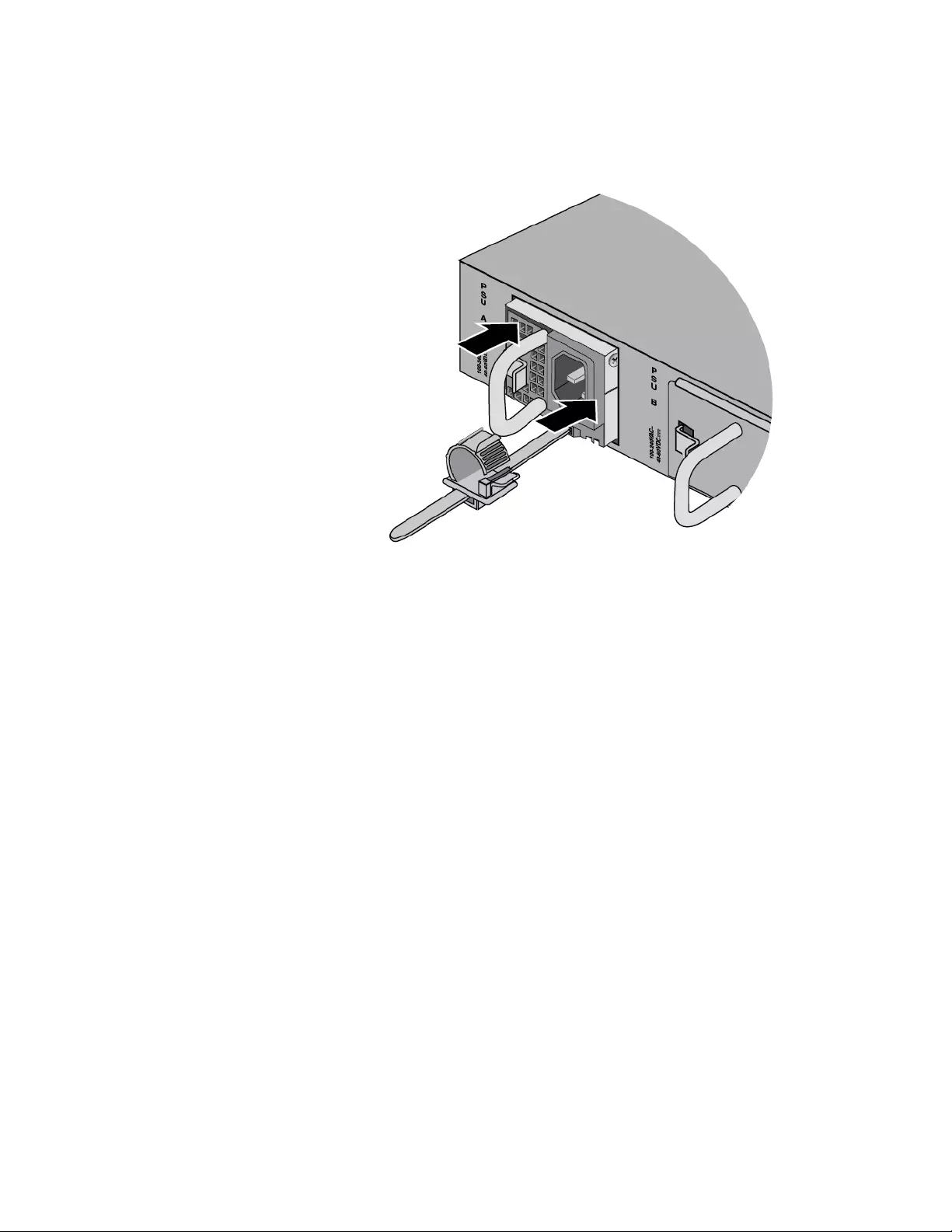
x950 Series Installation Guide for VCStack
119
4. When the power supply makes contact with the connector inside the
switch, gently press on its faceplate to seat it on the connector. Refer
to Figure 57.
Figure 57. Seating the Power Supply on the Internal Connector
5. Visually inspect the power supply to be sure that its faceplate is flush
against the rear panel of the chassis.
6. If you purchased two AC power supplies for the switch, repeat this
procedure to install the second unit.
7. If you purchased a DC power supply as the second power supply, go
to “Installing PWR600 DC Power Supplies” on page 120.
8. To install an optional XEM2 Ethernet Line Card, go to “Installing an
Optional XEM2 Ethernet Line Card” on page 130.
9. After installing the power supplies and optional XEM2 Line Card, go to
one of the following chapters:
Chapter 6, “Installing the Switch on a Table” on page 135
Chapter 7, “Installing the Switch in an Equipment Rack” on page 139
Chapter 8, “Installing the Switch on a Wall” on page 147
Chapter 9, “Installing the Switch in the RKMT-SL01 Sliding Rack” on
page 163
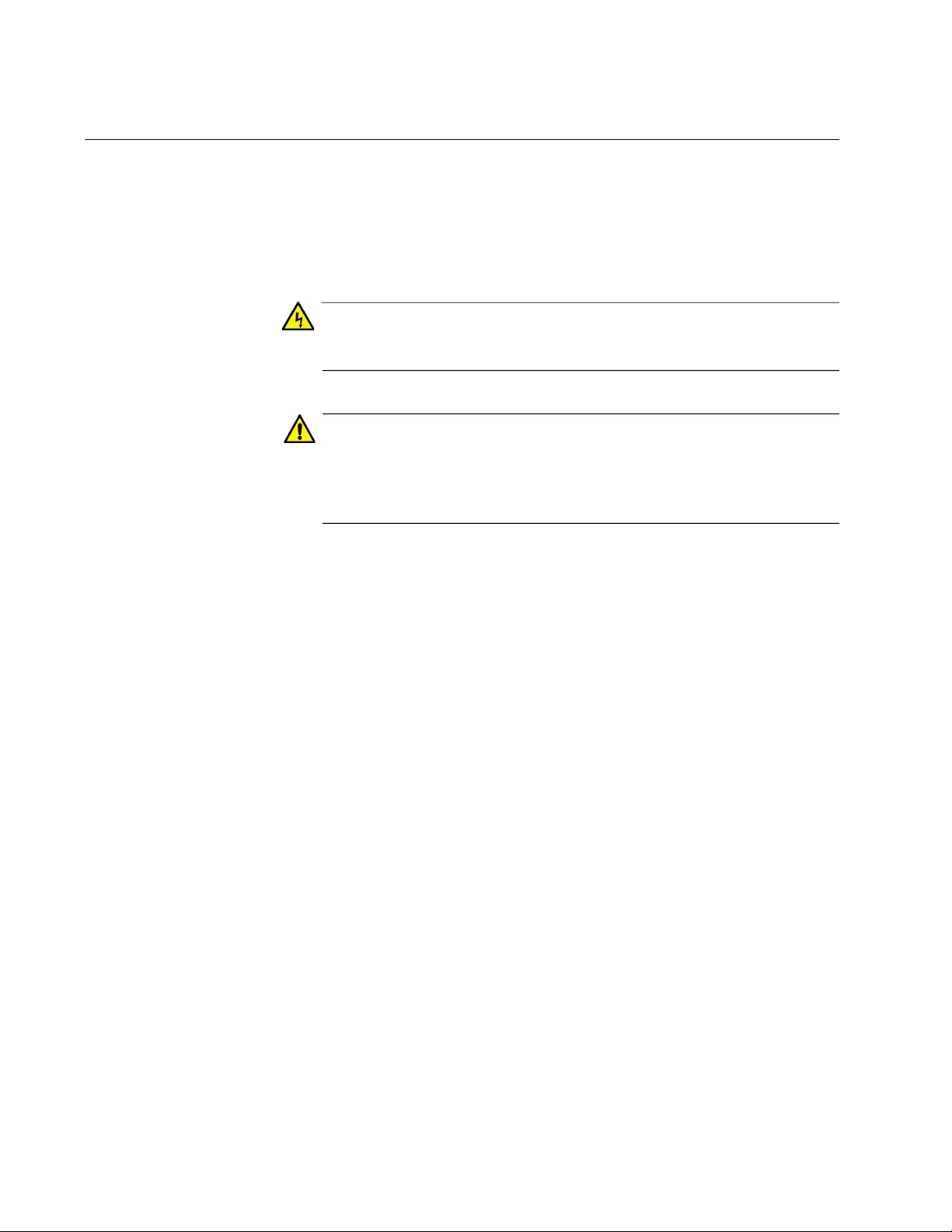
Chapter 5: Installing Power Supplies and Optional XEM2 Line Card
120
Installing PWR600 DC Power Supplies
This section contains the procedure for installing PWR600 DC Power
Supplies in the switch. For background information, refer to “PWR600 AC
and DC Power Supplies” on page 40. For a list of power supply
components, refer to “Unpacking the PWR600 DC Power Supply” on
page 114.
Warning
The power supply is heavy. Use both hands to lift it. You might injure
yourself or damage the device if you drop it.
Caution
The device can be damaged by static electricity. Be sure to follow
proper anti-static precautions when installing the device. Allied
Telesis recommends using a properly grounded wrist strap or other
personal anti-static device and an anti-static mat.
To install a PWR600 DC power supply, perform the following procedure:
1. Choose a slot for the power supply. The two power supply slots are
labeled PSU A and PSU B on the left side of the rear panel.
If you are installing only one power supply, you can install it in either
slot. Allied Telesis recommends PSU A because that slot does not
come with a blank power supply panel.
2. If there is already a power supply in PSU A, remove the blank panel
from PSU B slot by pressing the release tab to the right and sliding the
panel from the switch. Refer to Figure 55 on page 117.
3. Carefully align the power supply in the slot and slide it into the slot.
Figure 58 on page 121 shows the module aligned for the PSU A slot.
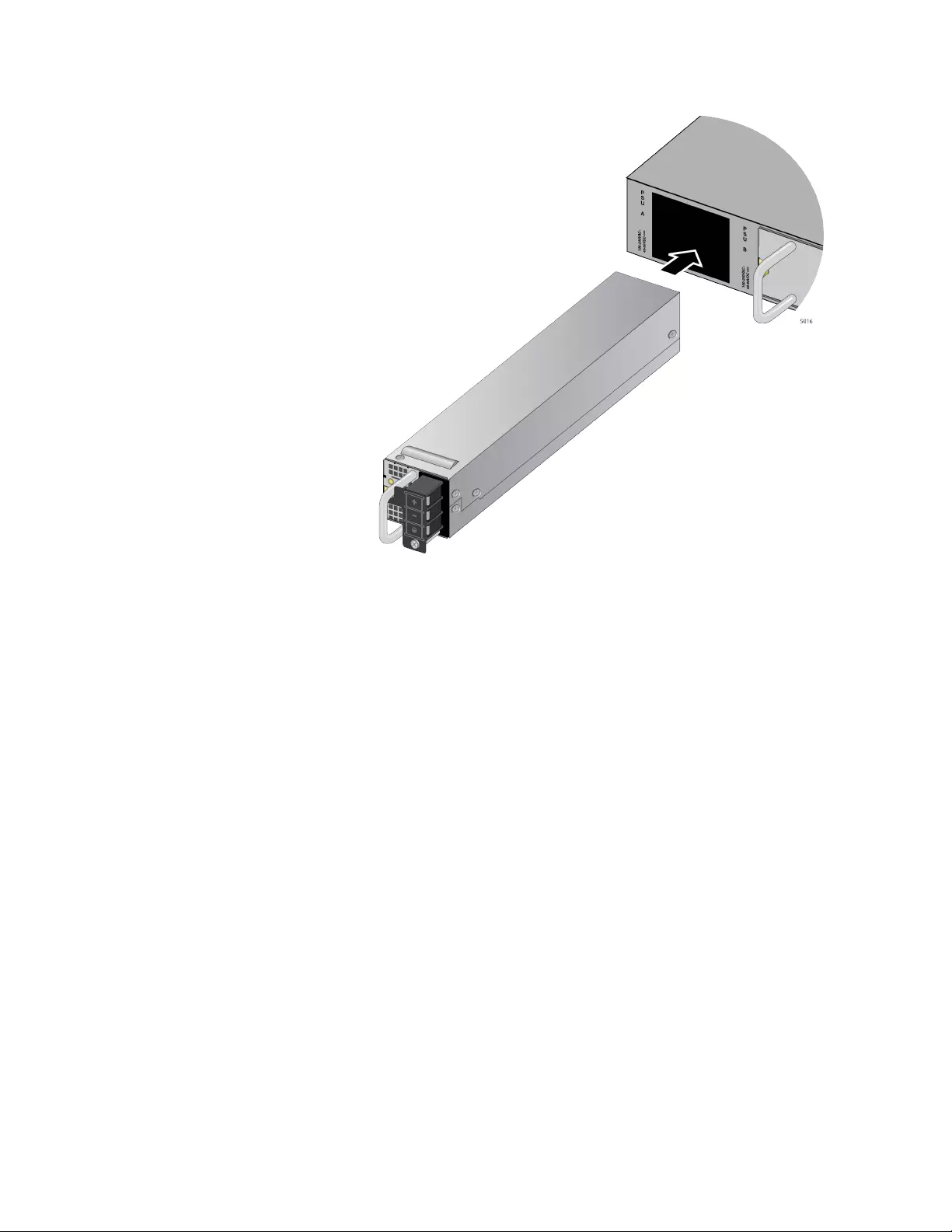
x950 Series Installation Guide for VCStack
121
Figure 58. Sliding the PWR600 DC Power Supply into the Chassis
4. When the power supply makes contact with the connector inside the
switch, gently press on its faceplate to seat it on the connector.
5. Visually inspect the power supply to be sure that its faceplate is flush
against the rear panel of the chassis.
6. If you purchased two DC power supplies for the switch, repeat this
procedure to install the second unit.
7. After installing the PWR600 DC power supply, go to the following
sections:
“Connecting the Grounding Wire” on page 123
“Connecting the DC Power Wires” on page 126
8. If you purchased an AC power supply as the second power supply, go
to “Installing PWR600 AC Power Supplies” on page 116.
9. To install an optional XEM2 Ethernet Line Card, go to “Installing an
Optional XEM2 Ethernet Line Card” on page 130.
10. After installing the power supplies and optional XEM2 Line Card, go to
one of the following chapters:
Chapter 6, “Installing the Switch on a Table” on page 135
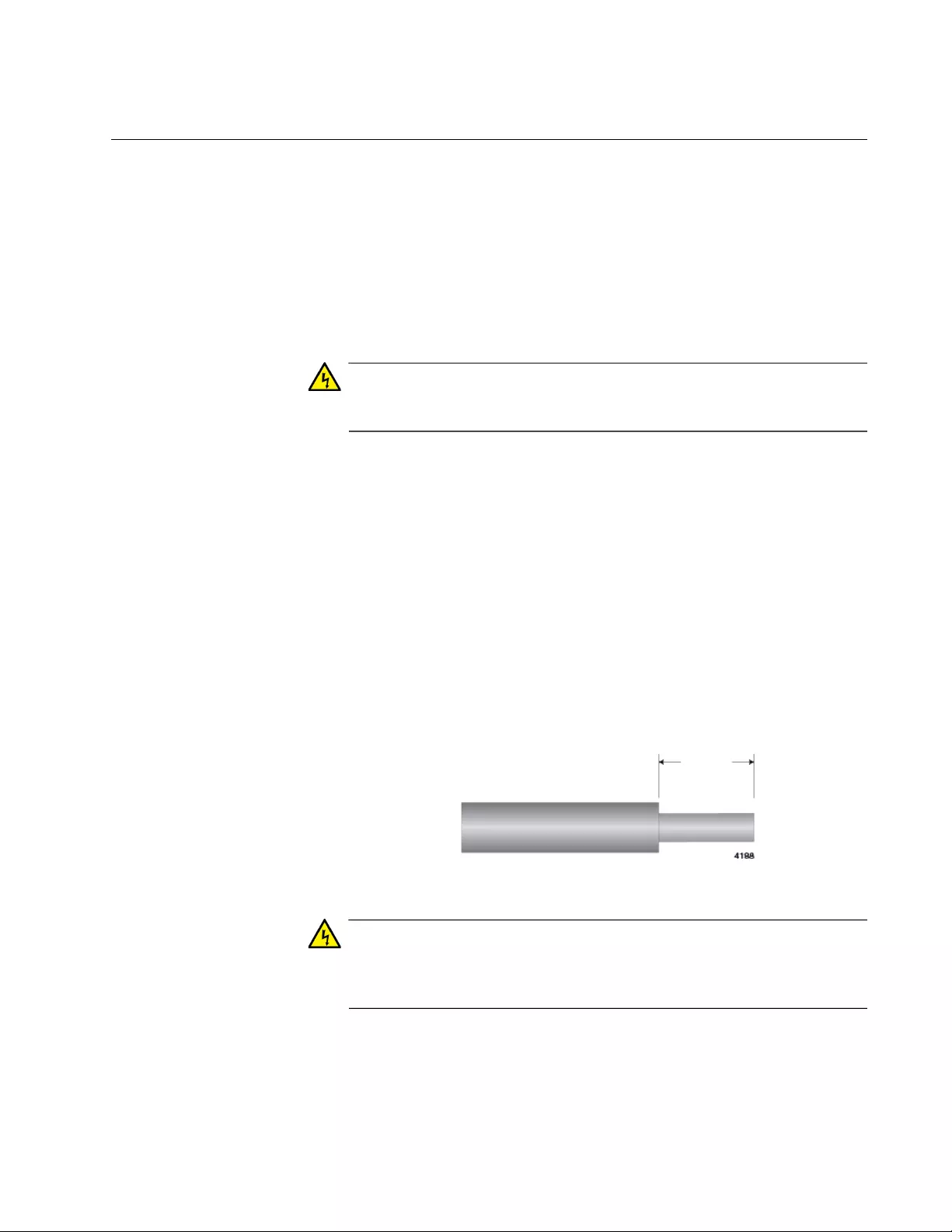
x950 Series Installation Guide for VCStack
123
Connecting the Grounding Wire
Here are the guidelines for the grounding wire:
The wire should be minimum #16 AWG solid wire.
The wire length should be as short as possible.
Continuity from the grounding screw to the earth ground must be
less than 0.05 ohms.
If a terminal is used, it should be double crimped.
Warning
The equipment must be earthed. The ground screw on the unit must
be connected to a properly earthed bonding point. E120
The material and tools you need for connecting the ground wire:
Minimum #16 AWG solid wire
Wire insulation stripper
Phillips-head screwdriver
To connect the grounding wire with bare wire, perform the following
procedure:
1. Strip 2.54cm (1.0 in.) of insulation from the end of the solid grounding
wire with a wire insulator stripper. Refer to Figure 59.
Figure 59. Stripping the Grounding Wire
Warning
Do not strip more than the recommended amount of wire. Stripping
more than the recommended amount can create a safety hazard by
leaving exposed wire on the terminal block after installation. E10
2. Loosen the screw for the connector panel several turns with a Phillips-
head screwdriver. Refer to Figure 60 on page 124.
2.54cm
(1.0 in.)
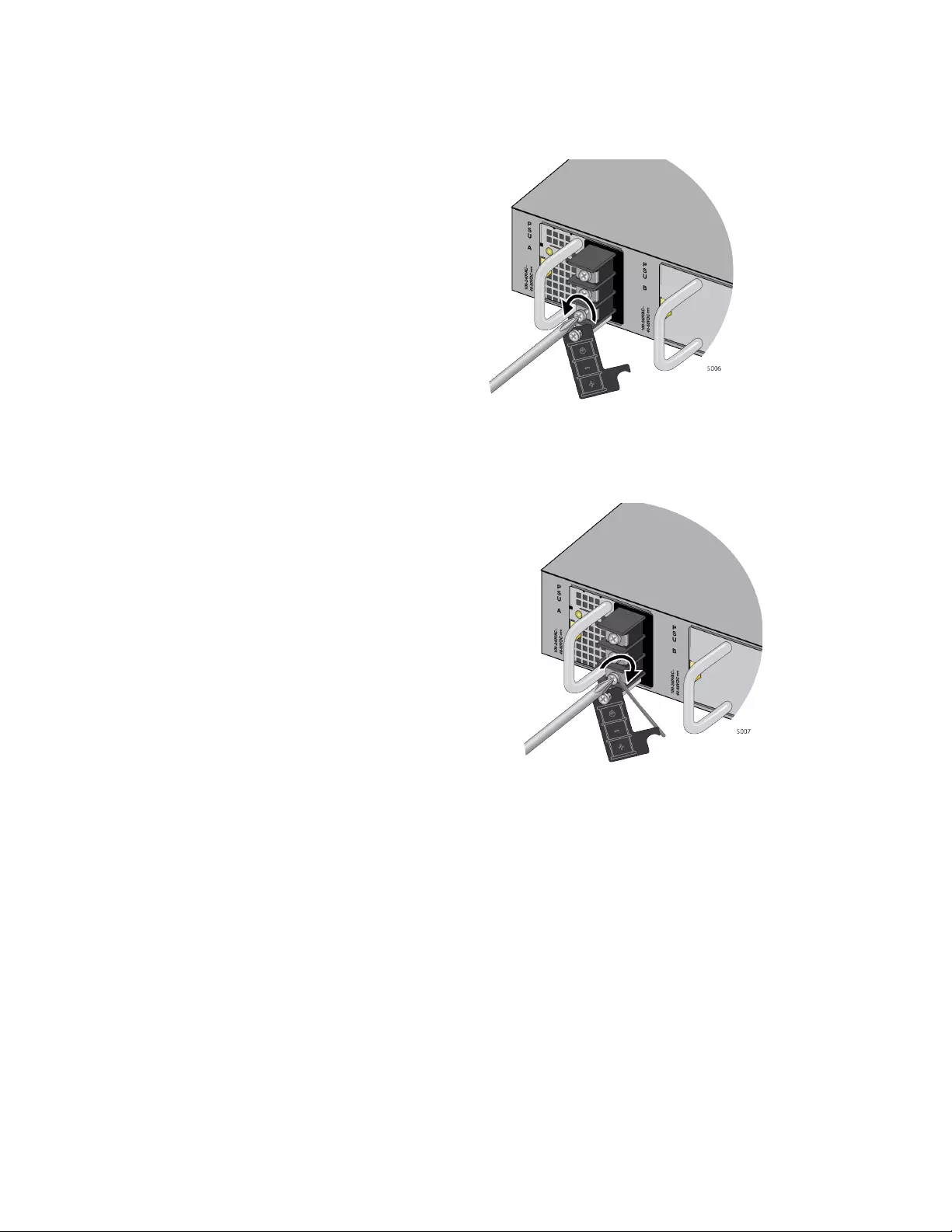
x950 Series Installation Guide for VCStack
125
4. Loosen the ground screw with a Phillips-head screwdriver. Refer to
Figure 62.
Figure 62. Loosening the Ground Screw
5. Wind the grounding wire clockwise around the base of the grounding
screw. Refer to Figure 63 on page 125.
Figure 63. Wrapping the Grounding Wire and Tightening the Screw
6. Tighten the ground screw.
7. Connect the other end of the ground wire to a ground point at the
installation site.
8. Go to “Connecting the Grounding Wire” on page 123.
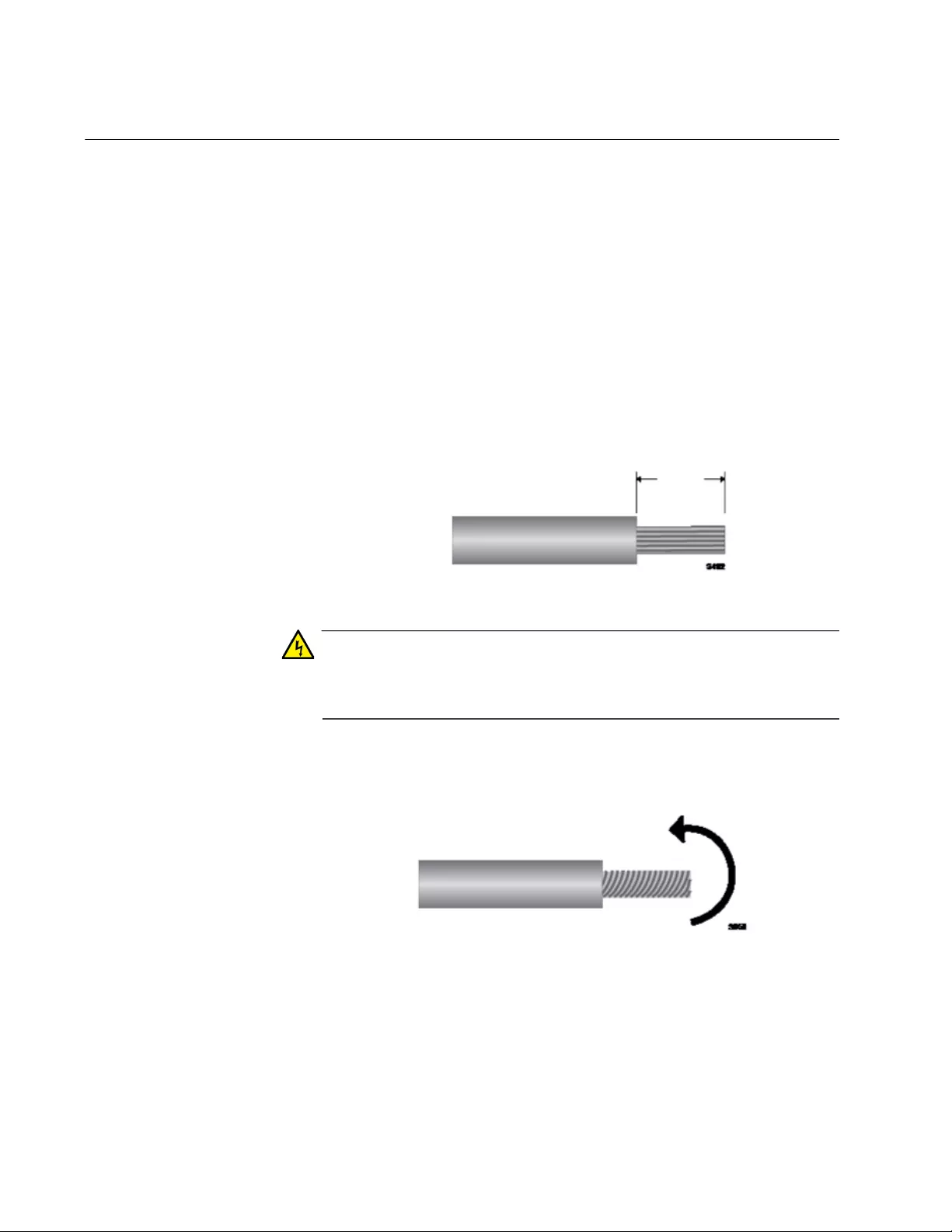
Chapter 5: Installing Power Supplies and Optional XEM2 Line Card
126
Connecting the DC Power Wires
Here are the materials and tools for connecting the DC power cables:
18 AWG stranded wires. Do not use wire heavier than 16 AWG.
solid wire.
Wire insulation stripper
Phillips-head screwdriver
To connect the DC power cables, perform the following procedure:
1. Strip 6.5mm (0.25 in.) of insulation from the end of the stranded power
wires with a wire insulator stripper. Refer to Figure 61.
Figure 64. Stripping the Power Wire
Warning
Do not strip more than the recommended amount of wire. Stripping
more than the recommended amount can create a safety hazard by
leaving exposed wire on the terminal block after installation. E10
2. Tightly wrap the wire strands with your finger tips.
Figure 65. Wrapping the Wire Strands
This step is to prevent loose strands from touching other wires and
causing an electrical short.
6.5mm
(0.25 in.)
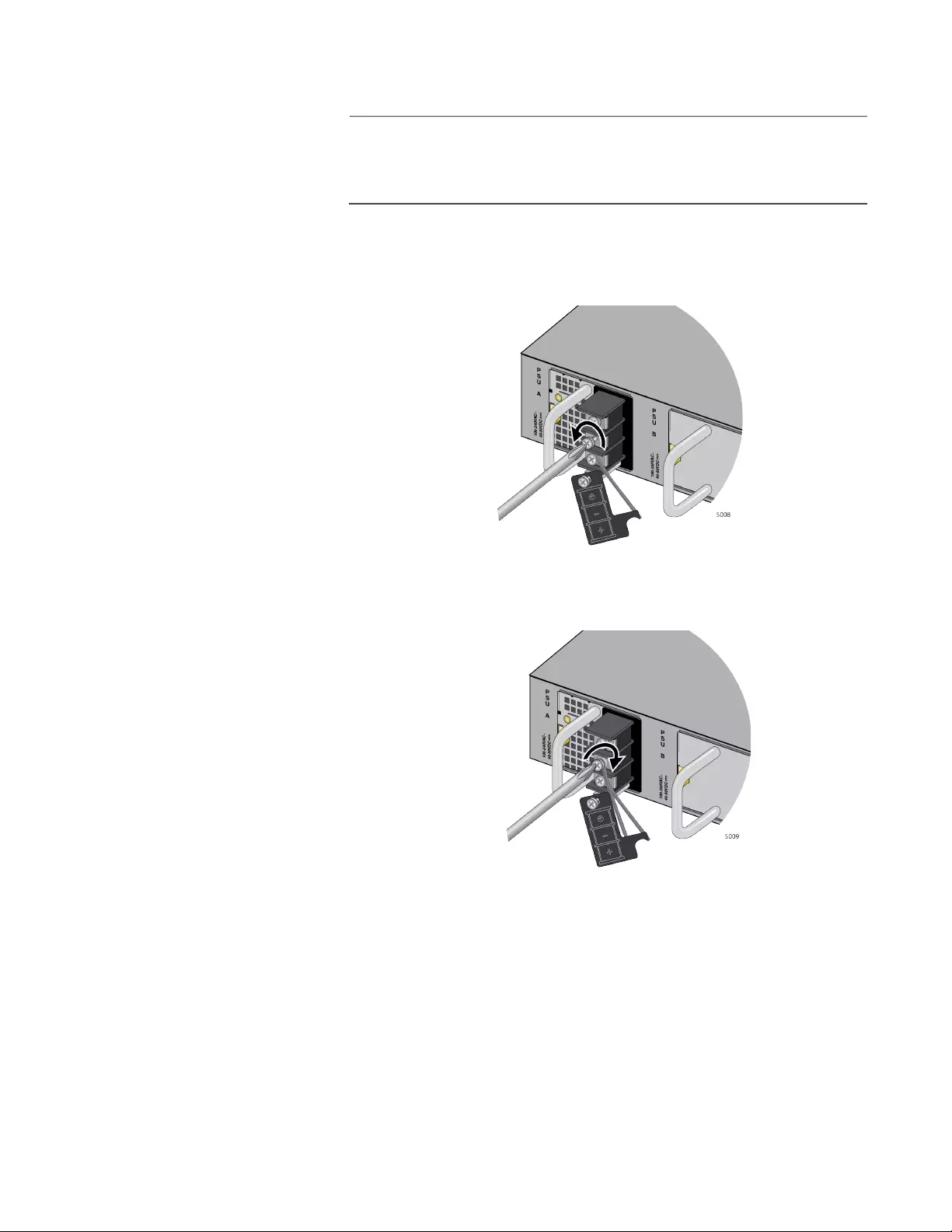
x950 Series Installation Guide for VCStack
127
Note
Allied Telesis recommends tinning the wires with solder for added
protection against loose strands. This guide does not provide
instructions on how to tin wires.
3. Loosen the middle screw for the negative (-) with a Phillips-head
screwdriver. Refer to Figure 66.
Figure 66. Loosening the Screw for the Negative (-)
4. Wind the power wire and tighten the screw. Refer to Figure 67.
Figure 67. Tightening the Screw for the Negative (-)
5. Loosen the top screw for the positive (+) with a Phillips-head
screwdriver. Refer to Figure 68 on page 128.
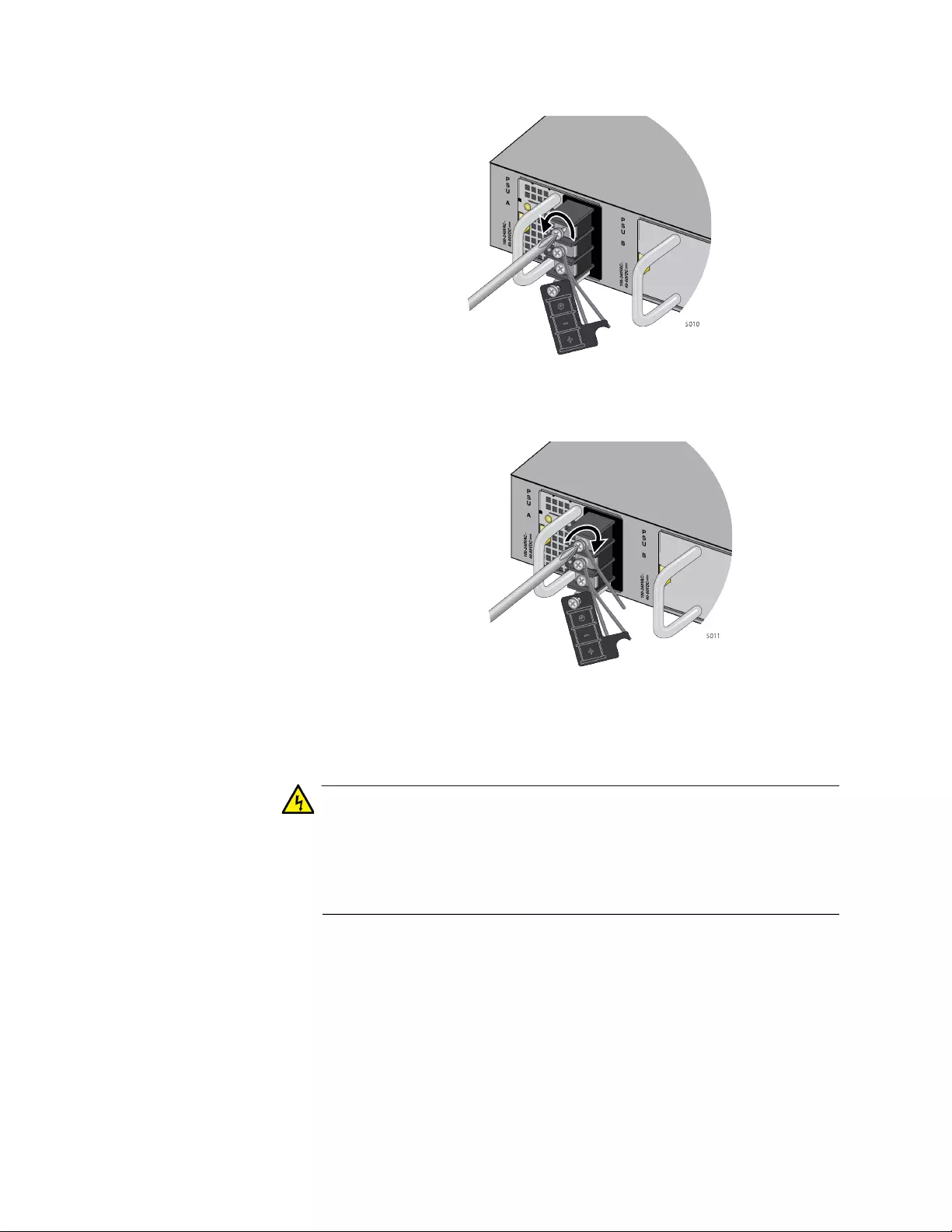
Chapter 5: Installing Power Supplies and Optional XEM2 Line Card
128
Figure 68. Loosening the Screw for the Negative (+)
6. Wind the power wire and tighten the screw.Refer to Figure 69.
Figure 69. Tightening the Screw for the Negative (+)
7. After attaching the wires to the screws, verify that there are no
exposed wires or loose wire strands.
Warning
Check to see if there are any exposed copper strands coming from
the installed wires. When this installation is done correctly there
should be no exposed copper wire strands extending from the
terminal block. Any exposed wiring can conduct harmful levels of
electricity to persons touching the wires. E12
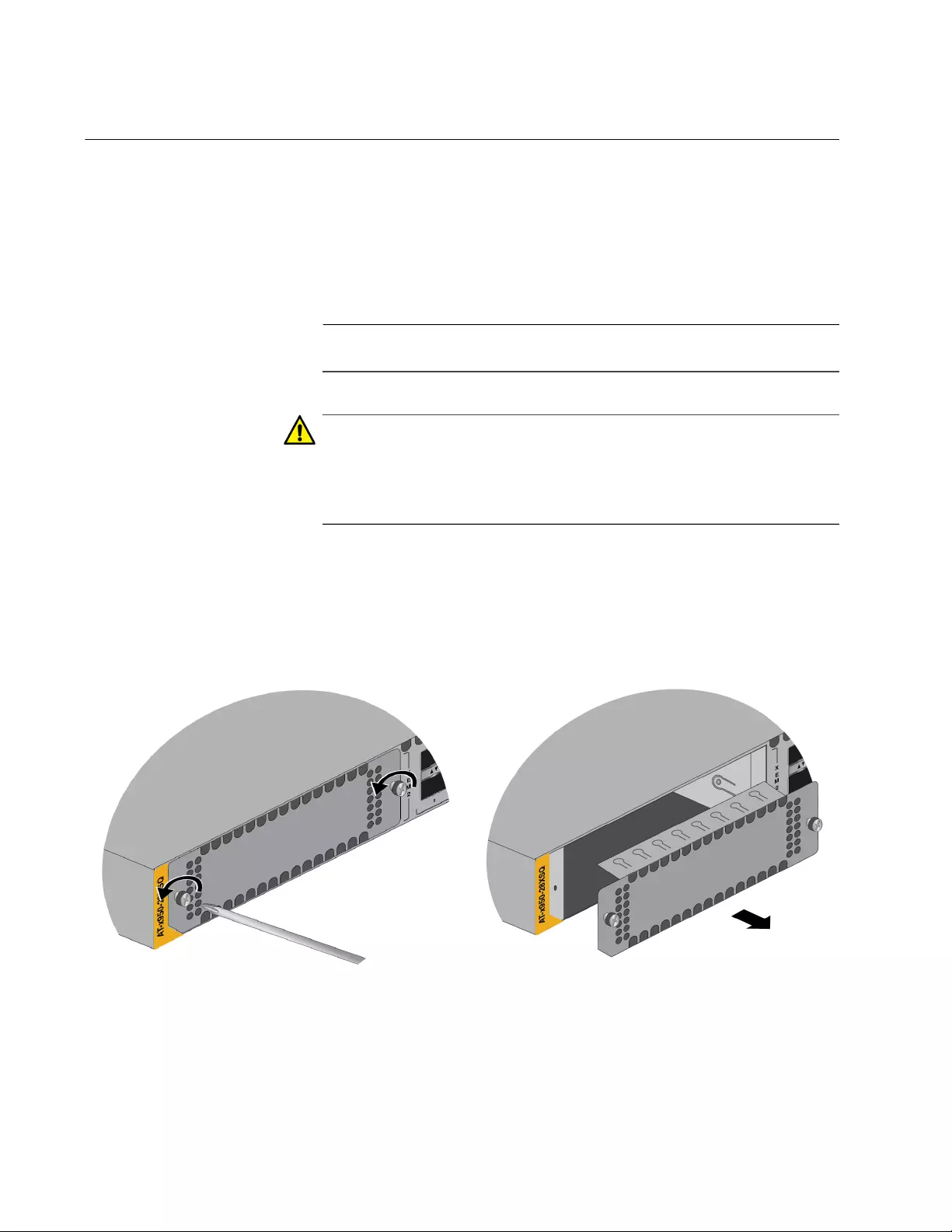
Chapter 5: Installing Power Supplies and Optional XEM2 Line Card
130
Installing an Optional XEM2 Ethernet Line Card
This section contains the procedure for installing an optional XEM2
Ethernet line card in the expansion slot in the front panel of the
x950-28XSQ and x950-28XTQm switches. For background information,
refer to Chapter 2, “XEM2 Ethernet Line Cards” on page 51. The
illustrations show the XEM2-12XT Line Card. The procedure is the same
for all line card models.
Note
The x950-52XSQ switch does not support the XEM2 line cards.
Caution
The device can be damaged by static electricity. Be sure to follow
proper anti-static precautions when installing the device. Allied
Telesis recommends using a properly grounded wrist strap or other
personal anti-static device and an anti-static mat.
To install an XEM2 Ethernet line card, perform the following procedure:
1. Using a #2 Phillips-head screwdriver, loosen the two captive screws
on the blank expansion slot panel and remove it from the switch. Refer
to Figure 72.
Figure 72. Removing the Blank Line Card Cover
2. Carefully remove the new Ethernet line card from its shipping
container and anti-static bag. Refer to Figure 73 on page 131.
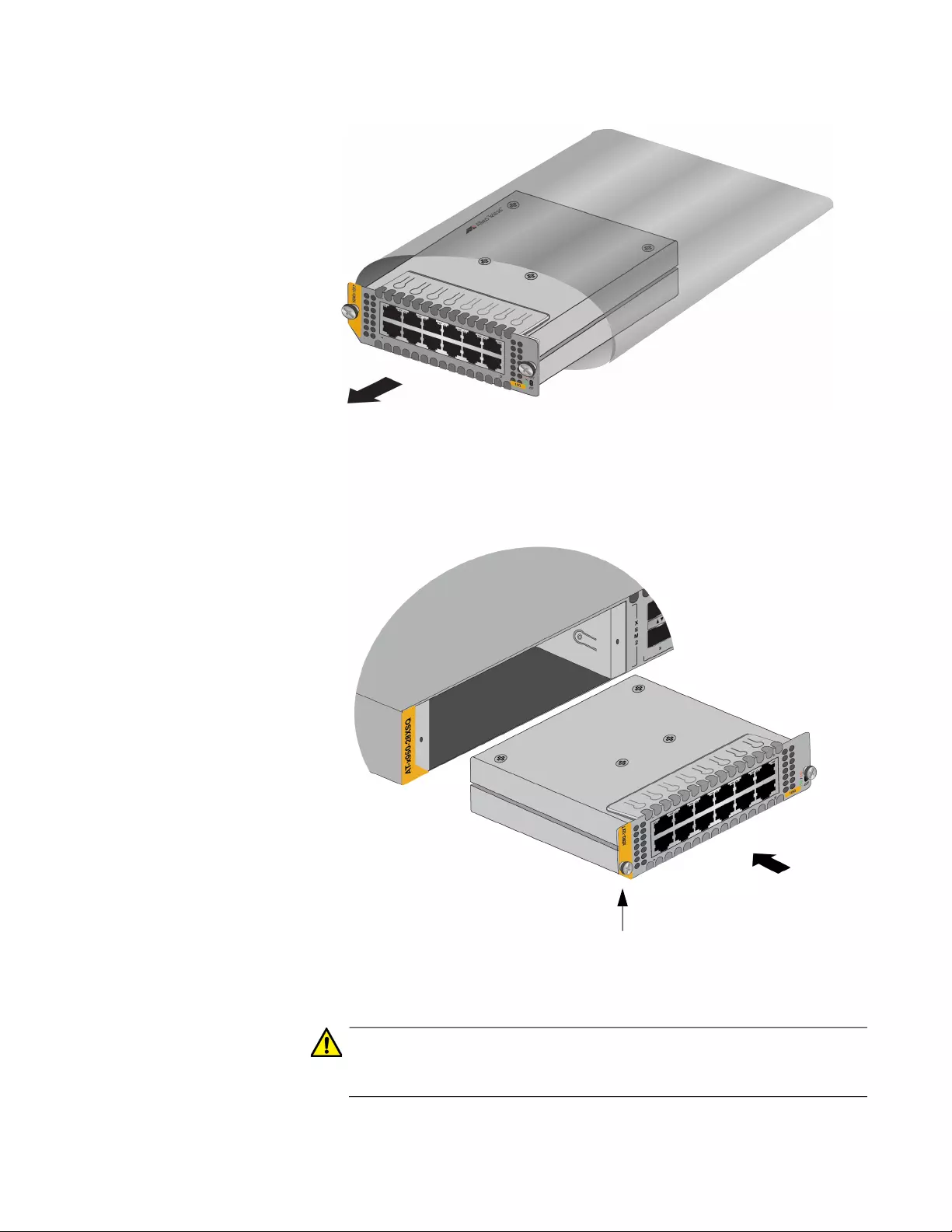
x950 Series Installation Guide for VCStack
131
Figure 73. Removing the Ethernet Line Card from the Anti-static Bag
3. Position the line card with the notch on the faceplate in the bottom left
corner, as shown in Figure 74, and carefully slide it into the slot.
Figure 74. Sliding the Ethernet Line Card into the Slot
Caution
Do not force the card into the slot. If you feel resistance, remove it
and try again.
Notch
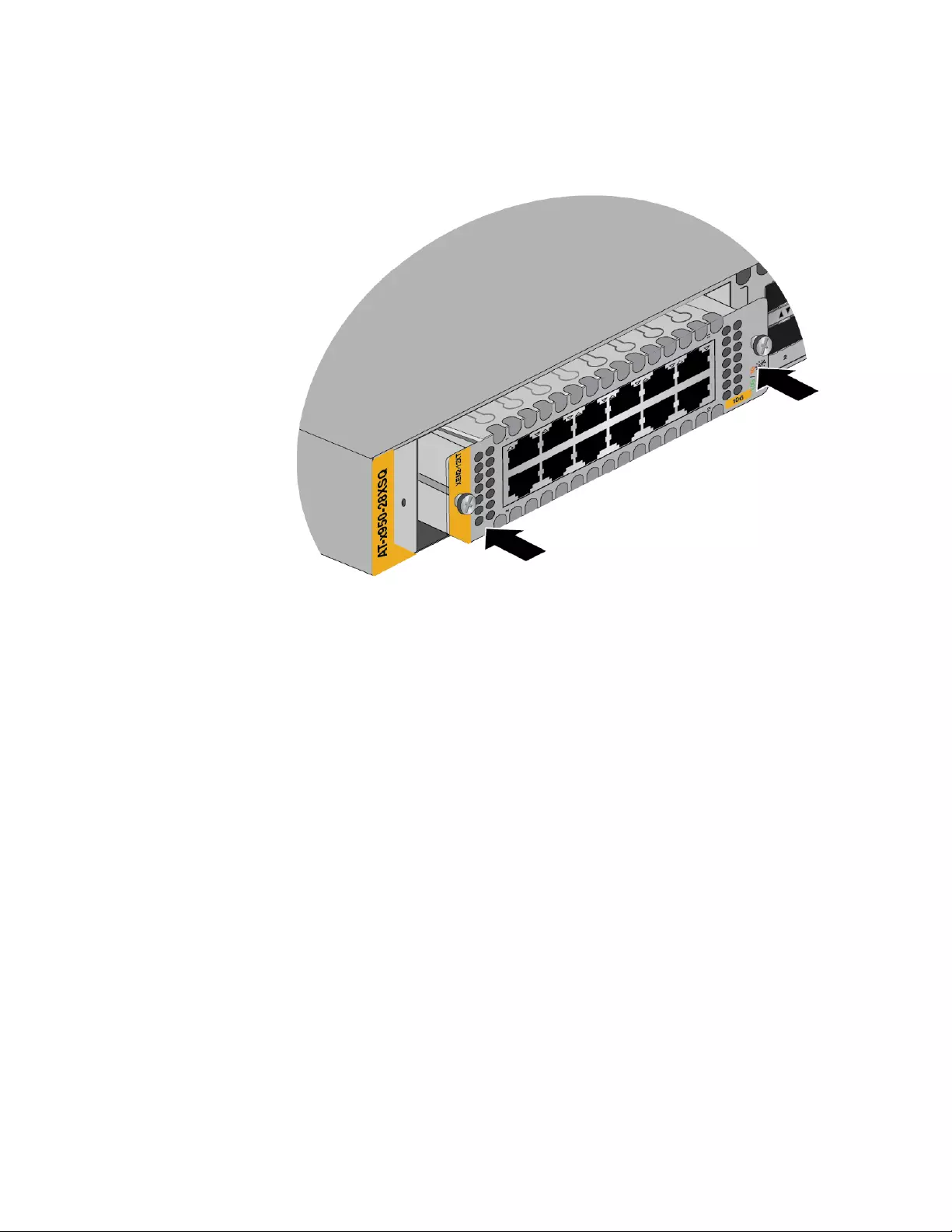
Chapter 5: Installing Power Supplies and Optional XEM2 Line Card
132
4. When the line card makes contact with the internal connector in the
switch. gently press on the sides of its faceplate to seat it on the
connector. Refer to Figure 75.
Figure 75. Seating the Ethernet Line Card in the Expansion Slot
5. Visually inspect the line card to verify that its faceplate is flush against
the front panel of the chassis.
6. Tighten the two captive screws on the card to secure it in the switch.
Refer to Figure 76 on page 133.
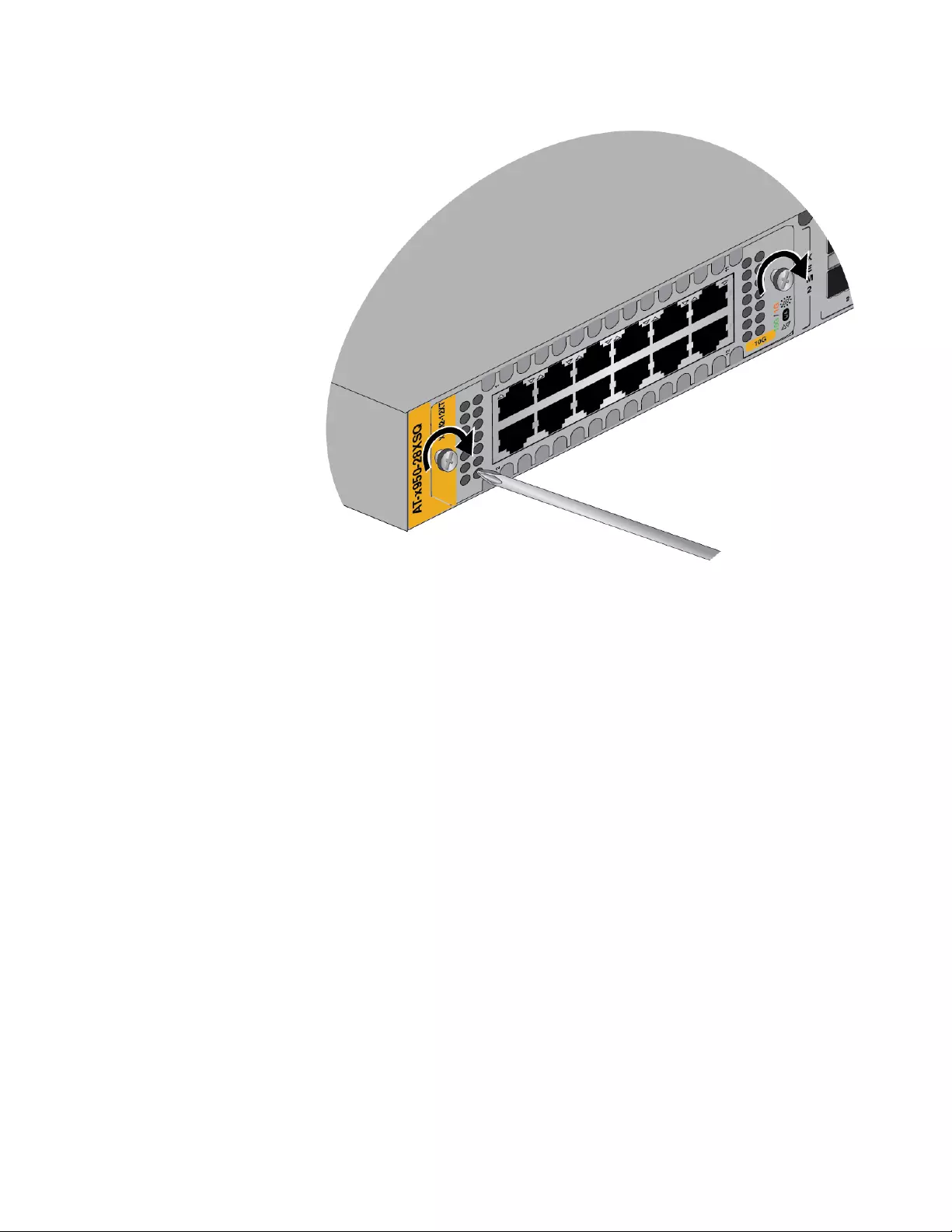
x950 Series Installation Guide for VCStack
133
Figure 76. Tightening the Two Captive Screws on the Ethernet Line Card
7. After installing the power supplies and optional XEM2 Line Card, go to
one of the following chapters:
Chapter 6, “Installing the Switch on a Table” on page 135
Chapter 7, “Installing the Switch in an Equipment Rack” on page
139
Chapter 8, “Installing the Switch on a Wall” on page 147
Chapter 9, “Installing the Switch in the RKMT-SL01 Sliding Rack”
on page 163
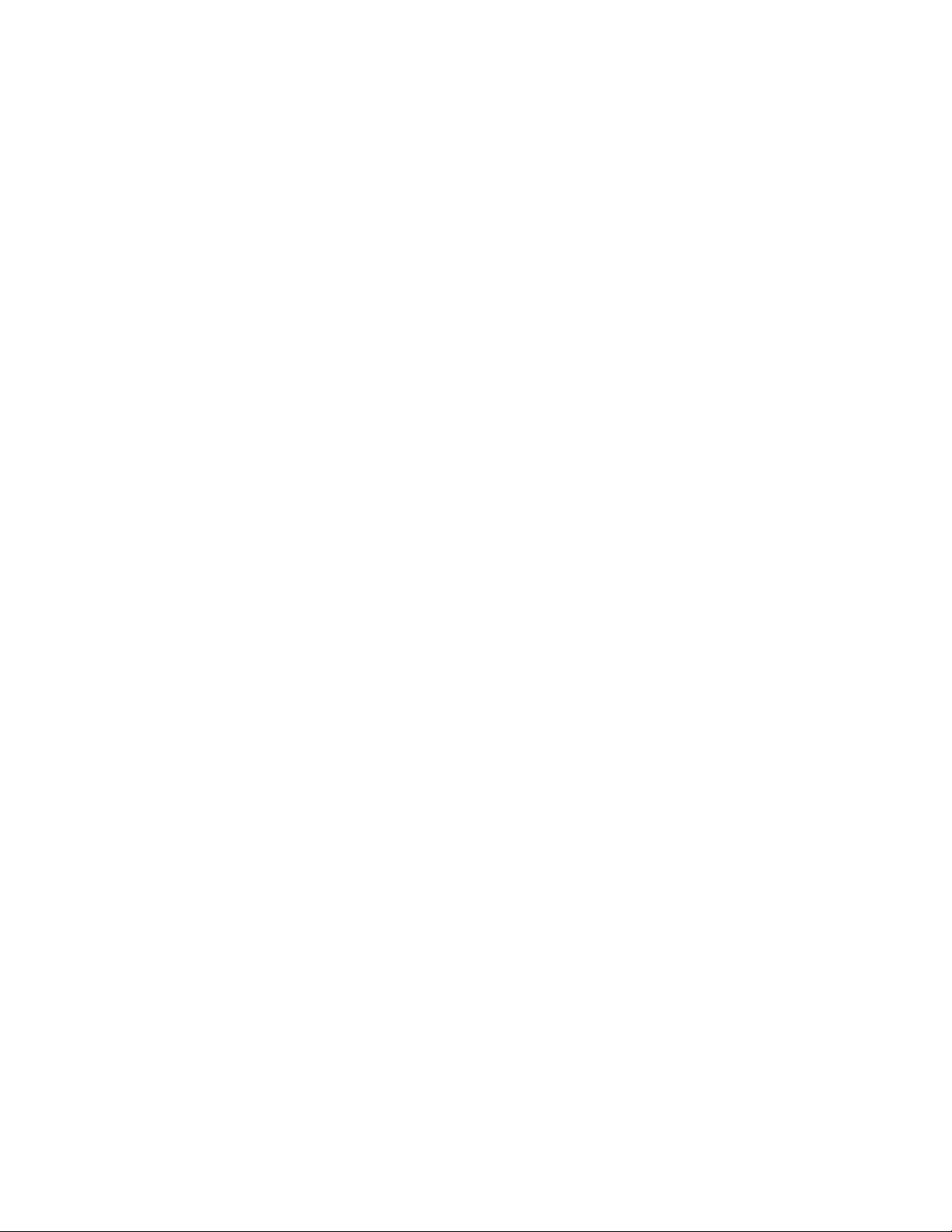
Chapter 5: Installing Power Supplies and Optional XEM2 Line Card
134
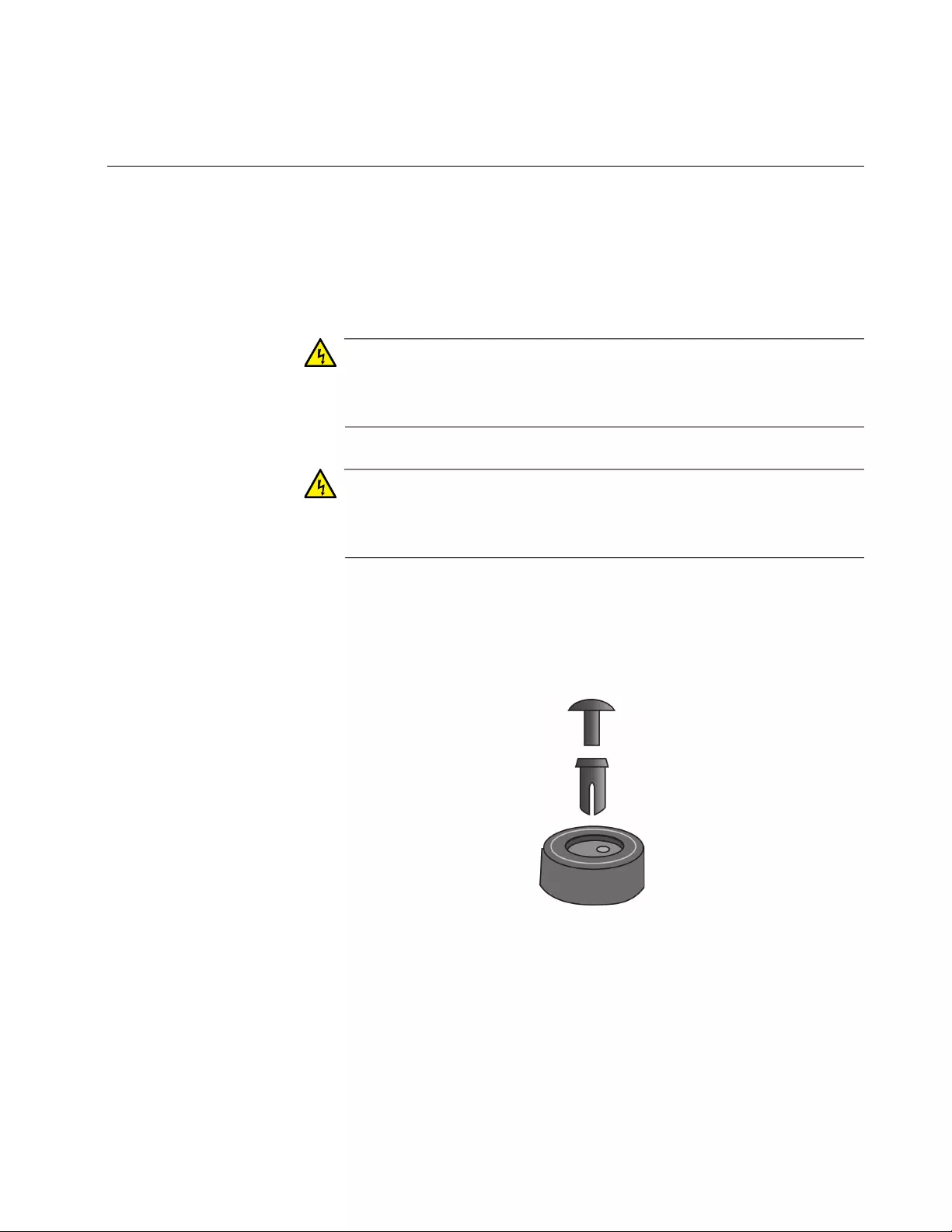
135
Chapter 6
Installing the Switch on a Table
This chapter contains the instructions for installing the switch on a table or
desktop.
Warning
Switches should not be stacked on a table or desktop. They could
present a physical safety hazard if you need to move or replace
switches. E91
Warning
The switch is heavy. Always ask for assistance when moving or
lifting the device so as to avoid injuring yourself or damaging the
equipment.
The switch comes with seven bumper feet in the accessory kit. The feet,
which are reusable, are used when installing the switch on a table. If they
are already assembled, disassemble them by removing the rivets and rivet
housings from the bumper feet. Refer to Figure 77.
Figure 77. Parts of the Bumper Feet
The holes in the base of the switch for the bumper feet are shown in Figure
78 on page 136.
Rivet
Rivet Housing
Bumper Foot
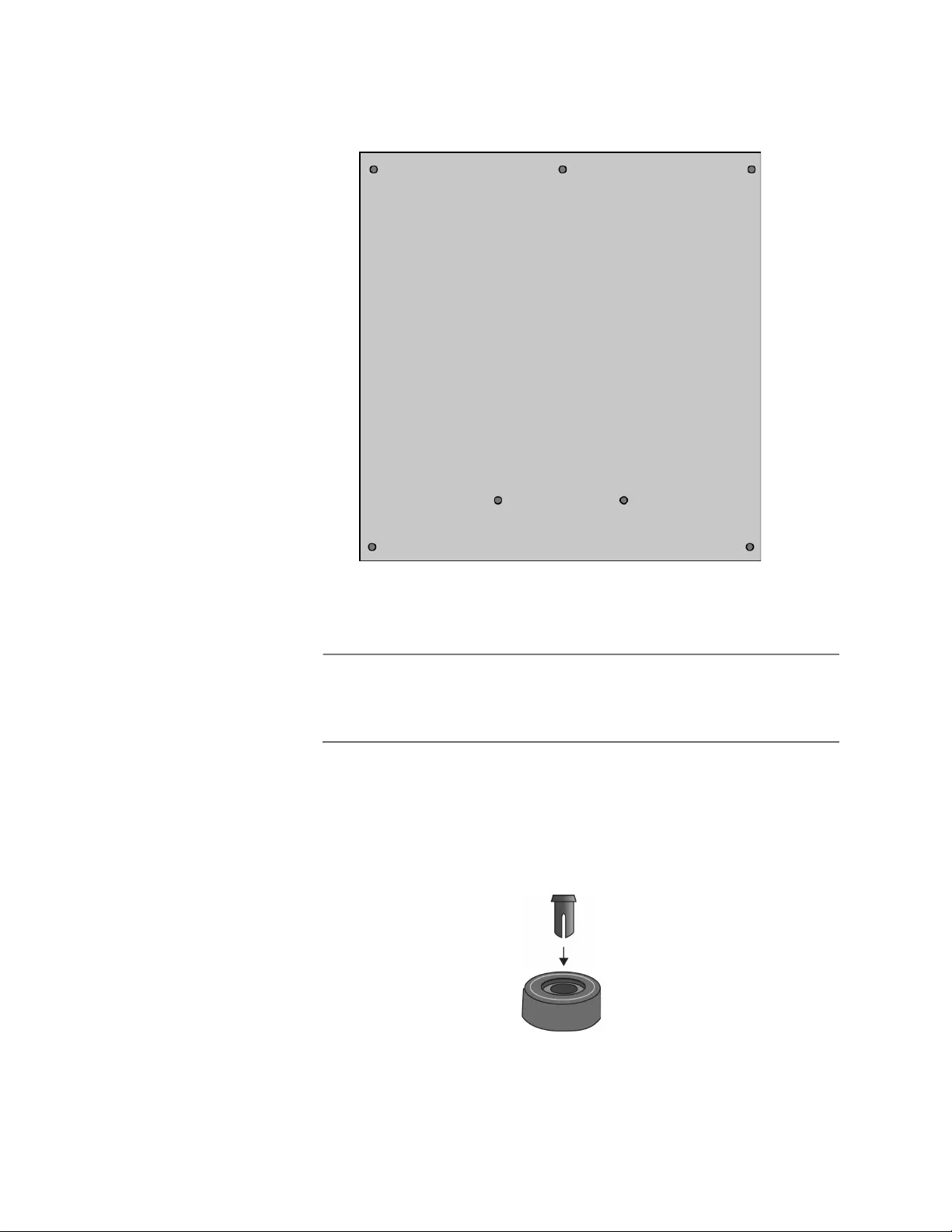
Chapter 6: Installing the Switch on a Table
136
Figure 78. Holes for Bumper Feet
Note
The following procedure assumes that you have already reviewed
the information and performed the procedures in Chapter 4,
“Beginning the Installation” on page 97.
To install the switch on a table, perform the following procedure:
1. Place the switch upside down on a table.
2. Inset a rivet housing into a bumper foot. Refer to Figure 79.
Figure 79. Inserting the Rivet Housing into the Bumper Foot
Rear of Chassis
Front of Chassis
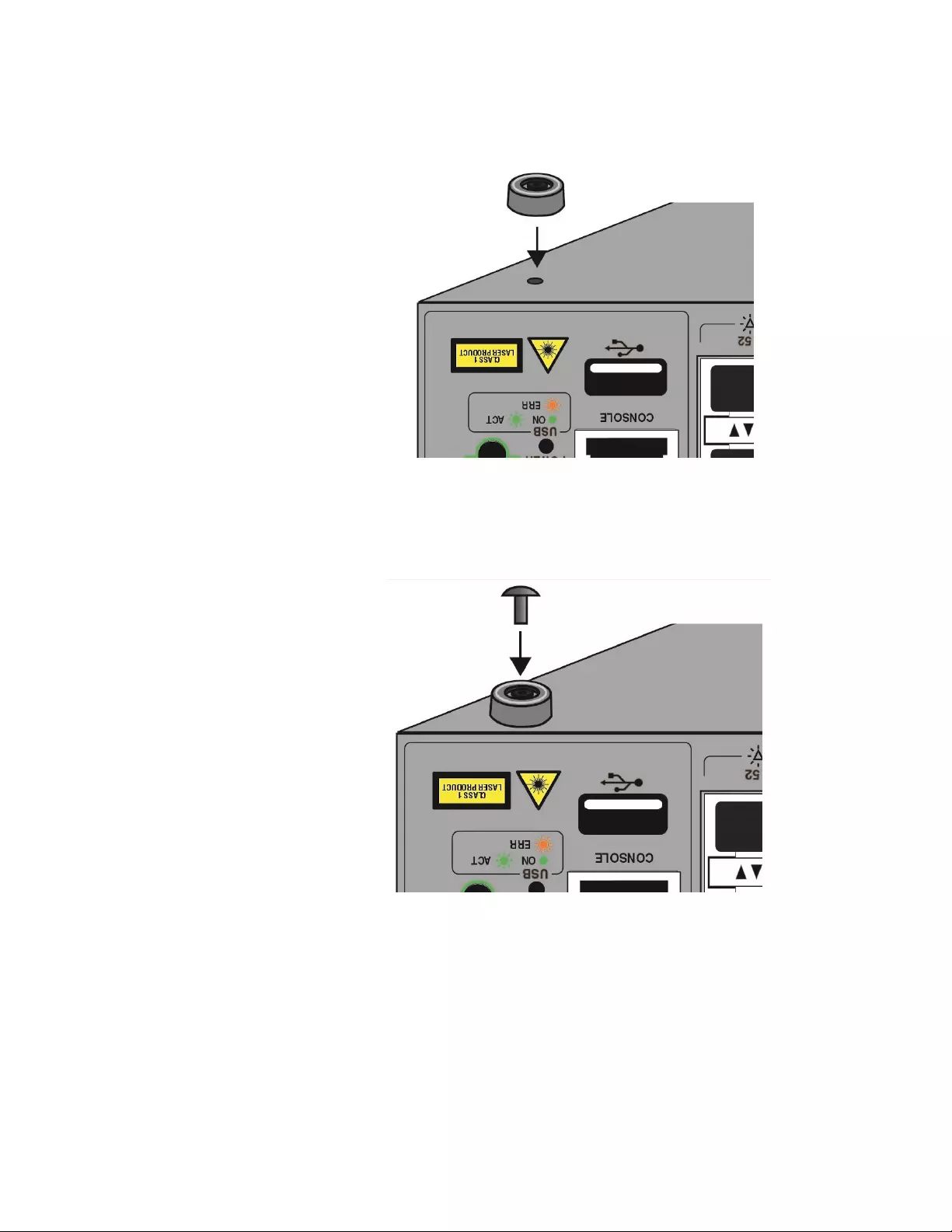
x950 Series Installation Guide for VCStack
137
3. Place the bumper foot onto one of the holes in the base of the switch.
Refer to Figure 80.
Figure 80. Placing the Bumper Foot on a Base Corner Hole
4. Insert the rivet to secure the bumper foot to the base. Refer to
Figure 81.
Figure 81. Inserting the Rivet into the Bumper Foot
5. Repeat steps 2 to 4 to install the remaining bumper feet.
6. Turn the switch over and place it on a flat, secure desk or table, leaving
ample space around it for ventilation.
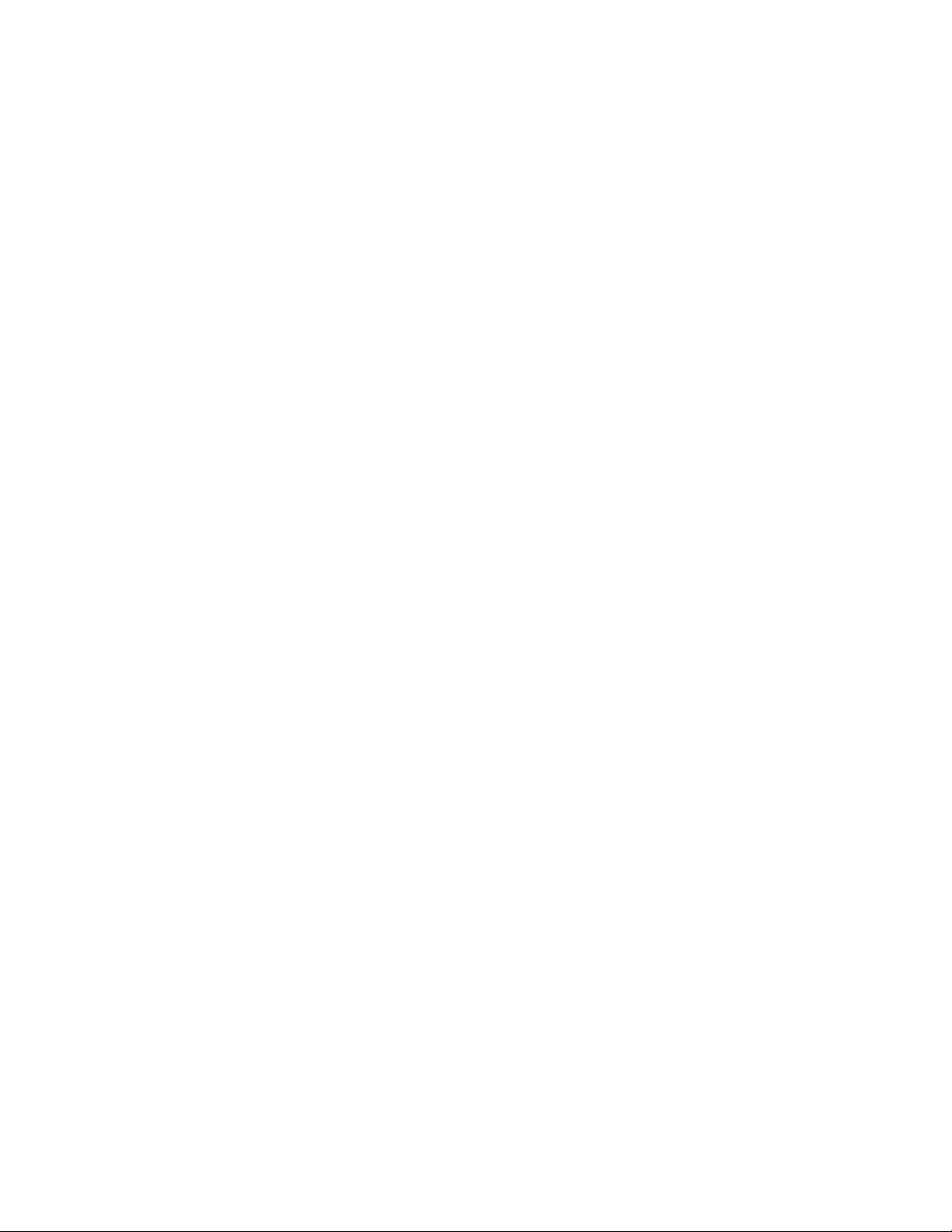
Chapter 6: Installing the Switch on a Table
138
7. Do one of the following:
To install power supplies, go to “Installing PWR600 AC Power
Supplies” on page 116 or “Installing PWR600 DC Power Supplies”
on page 120.
To install an optional XEM2 Ethernet Line Card, go to “Installing an
Optional XEM2 Ethernet Line Card” on page 130.
After installing the switches of the stack, go to Chapter 10,
“Configuring the Master Switch” on page 187.
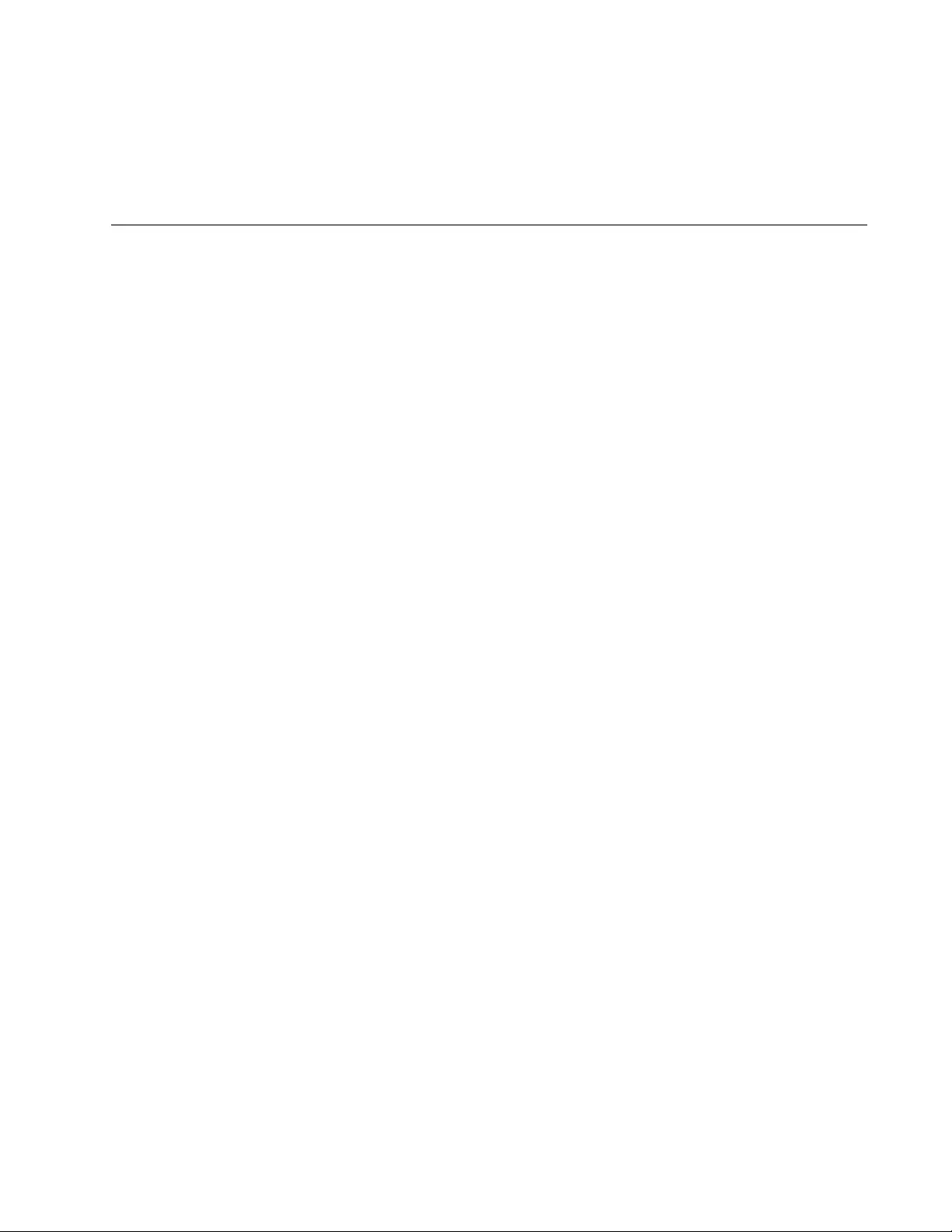
139
Chapter 7
Installing the Switch in an Equipment
Rack
This chapter contains instructions for installing the switch in a standard 19-
inch equipment rack. The procedures in this chapter are listed here:
“Beginning the Installation” on page 140
“Removing the Bumper Feet” on page 142
“Installing the Switch” on page 143
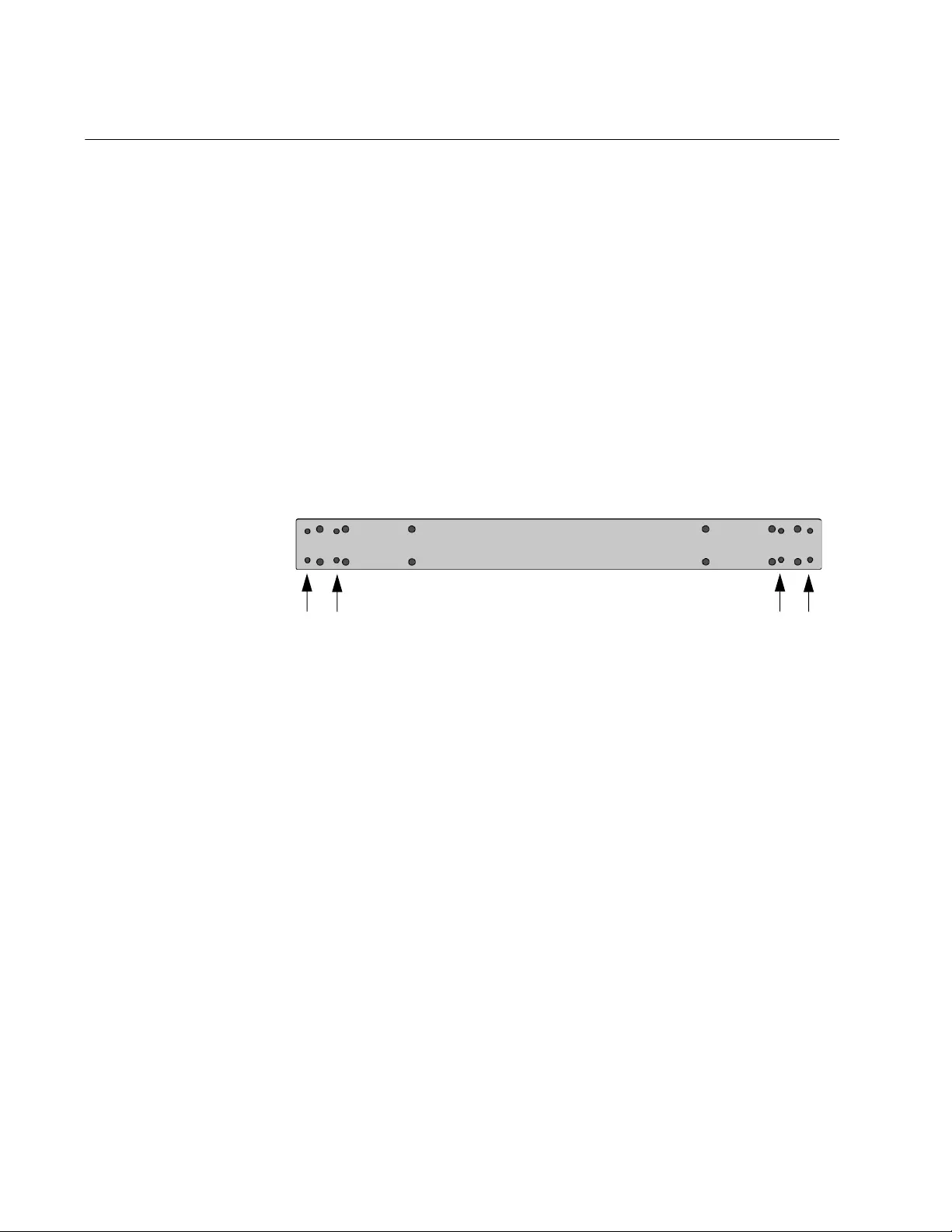
Chapter 7: Installing the Switch in an Equipment Rack
140
Beginning the Installation
This chapter contains the procedure for installing the switch in a standard
19-inch equipment rack, with the brackets included with the unit.
Required Items The following items are required to install the switch in an equipment rack:
Two equipment rack brackets (included with the switch)
Eight M4x6mm bracket screws (included with the switch)
Cross-head screwdriver (not provided)
Four standard equipment rack screws (not provided)
Switch
Orientations in
the Equipment
Rack
The switch has two sets of screw holes on the left and right sides, for the
standard brackets included with the switch and the optional RKMT-SL01
Sliding Rack Mount Kit. Figure 82 identifies the holes for the standard
brackets.
Figure 82. Bracket Holes on the Switch
You can install the switch with its front panel flush with or extending in
front of the equipment rack. The illustrations in Figure 83 on page 141
show the possible switch orientations in the equipment rack.
Holes for
Standard Brackets
Holes for
Standard Brackets
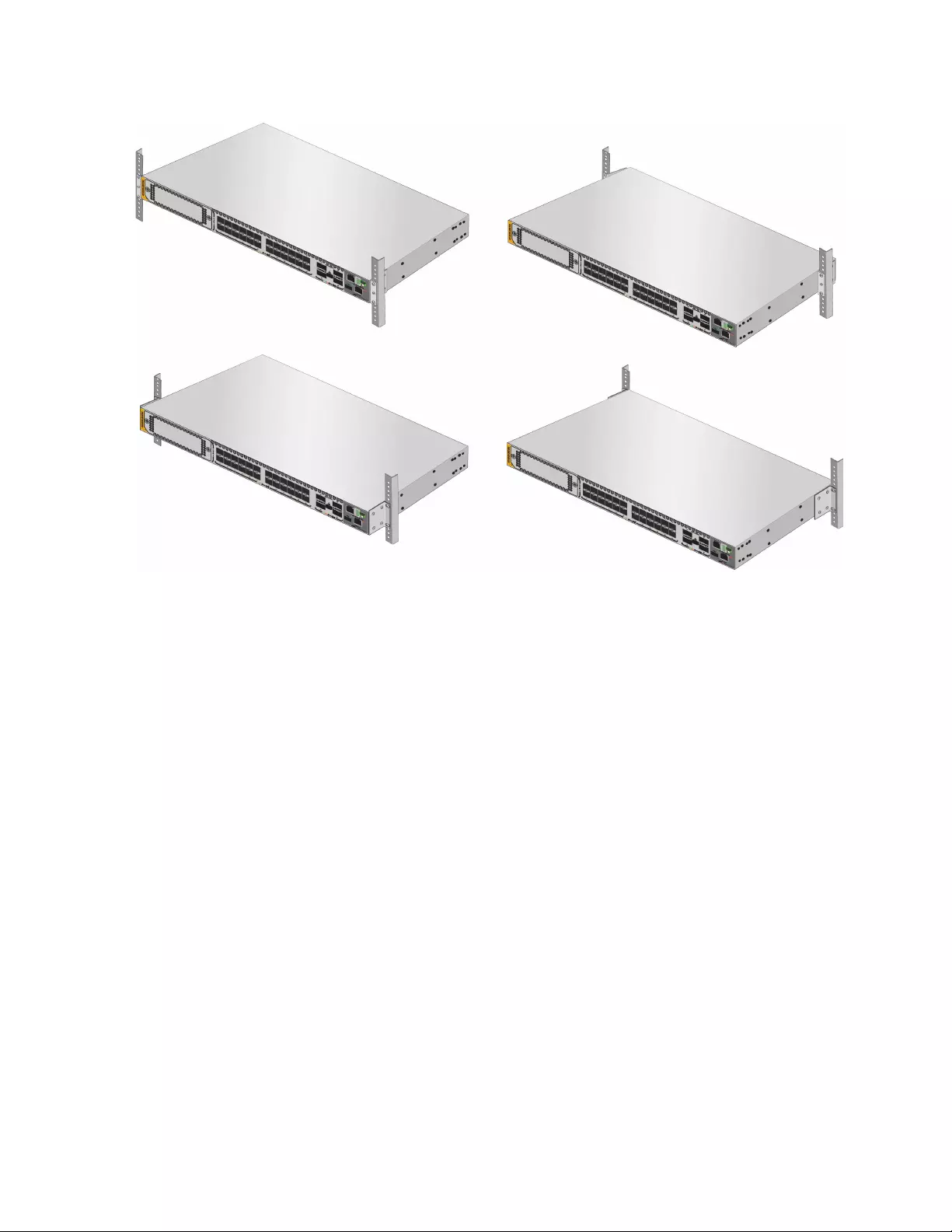
x950 Series Installation Guide for VCStack
141
Figure 83. Switch Orientations in an Equipment Rack
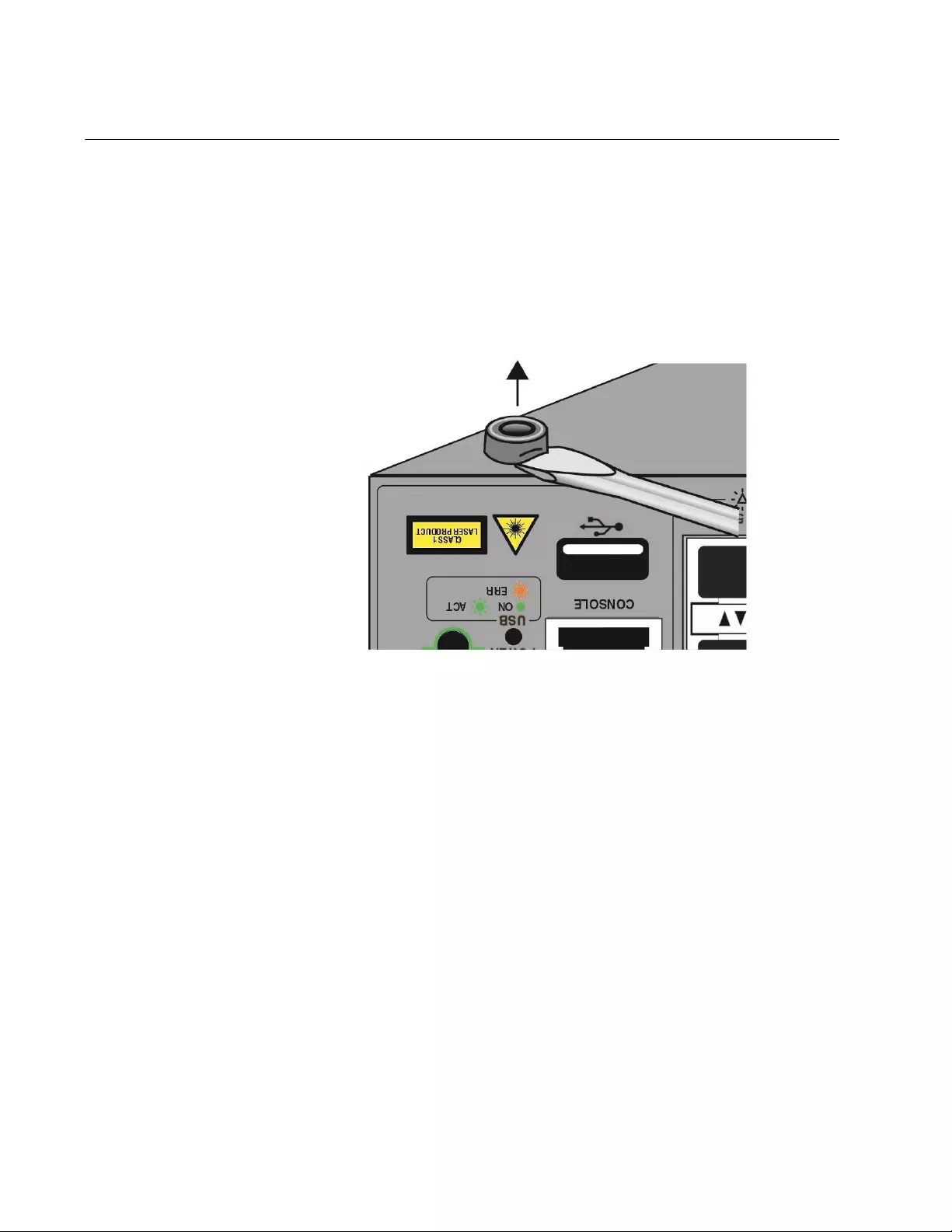
Chapter 7: Installing the Switch in an Equipment Rack
142
Removing the Bumper Feet
The bumper feet included with the switch should not be used when
installing the device in an equipment rack. If they are already installed,
perform the following procedure to remove them:
1. Place the switch upside down on a level, secure surface.
2. Use a small flat-head screwdriver to gently pry the feet from the
bottom of the switch. Refer to Figure 84.
Figure 84. Removing the Bumper Feet
3. Turn the switch back over.
4. Go to“Installing the Switch” on page 143.
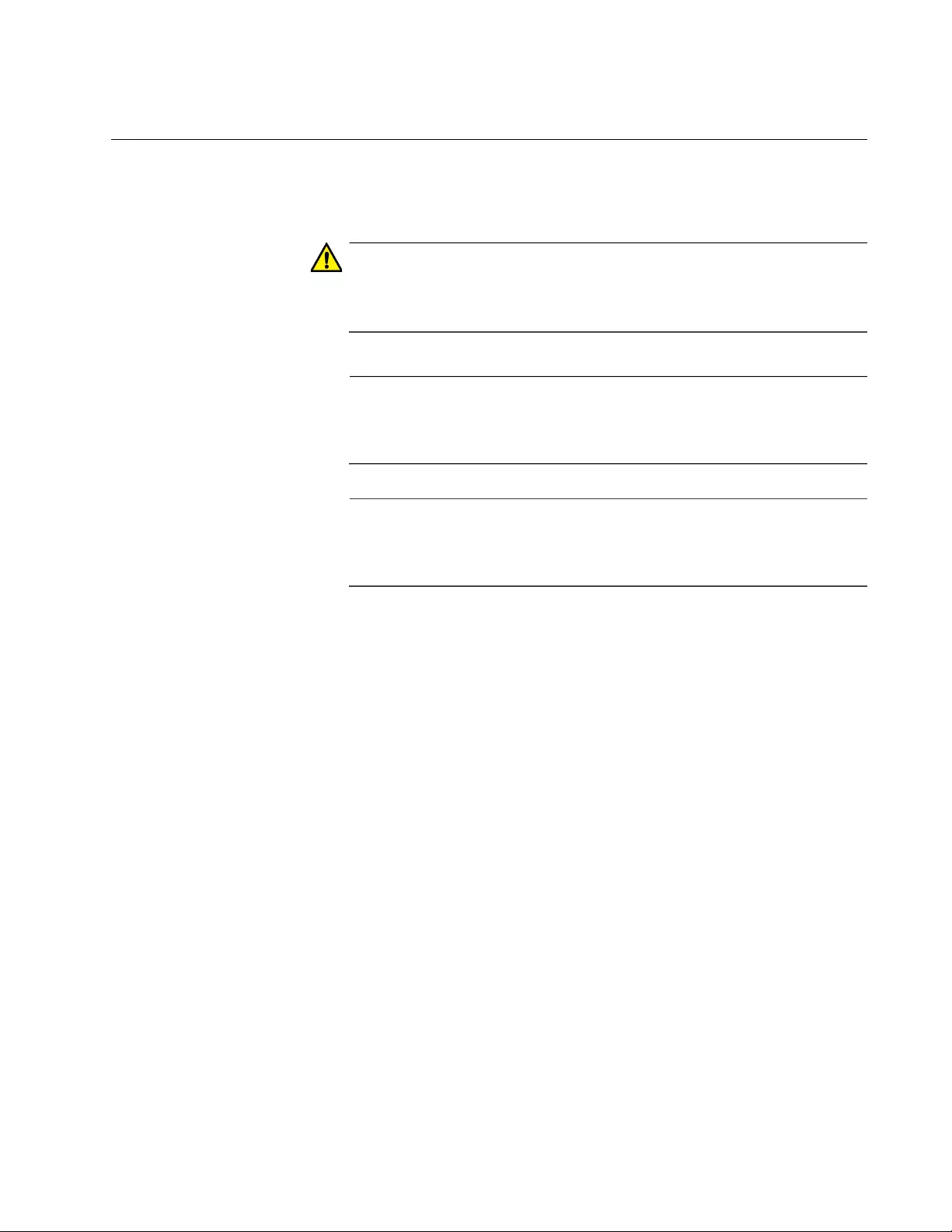
x950 Series Installation Guide for VCStack
143
Installing the Switch
Please review the information and perform the procedures in Chapter 4,
“Beginning the Installation” on page 97 before installing the switch.
Caution
The chassis may be heavy and awkward to lift. Allied Telesis
recommends that you get assistance when mounting the chassis in
an equipment rack. E28
Note
The switch can be installed in an equipment rack with the optional
RKMT-SL01 Sliding Rack Mount Kit. For instructions, refer to the
RKMT-SL01 Sliding Rack Mount Kit Installation Guide.
Note
The switch comes with four brackets. Installing the device in an
equipment rack requires only two brackets. All four brackets are
used to install the switch on a wall.
To install the switch in a 19-inch equipment rack, perform the following
procedure:
1. Place the unit on a level, secure surface.
2. If you have not chosen an orientation for the switch in the equipment
rack, review “Switch Orientations in the Equipment Rack” on page 140.
3. Attach two of the four rack mount brackets to the sides of the switch in
the selected positions, with eight of the M4x6mm screws included with
the unit. The illustration in Figure 85 on page 144 shows the
installation of the brackets so that the front panel is even with the front
of the equipment rack.
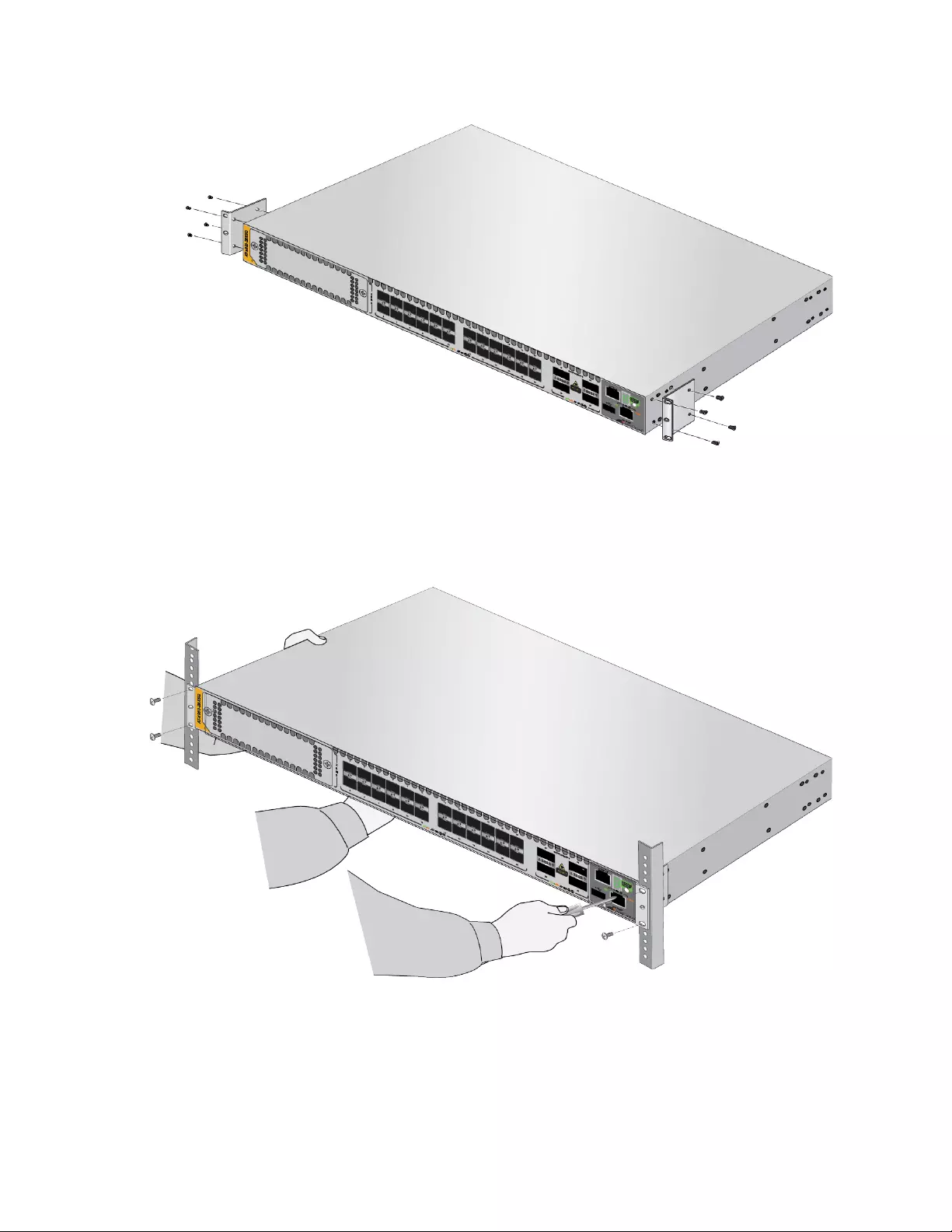
Chapter 7: Installing the Switch in an Equipment Rack
144
Figure 85. Attaching the Equipment Rack Brackets
4. Have another person hold the switch in the equipment rack while you
secure it using standard equipment rack screws (not provided). Refer
to Figure 86.
Figure 86. Installing the Switch in an Equipment Rack
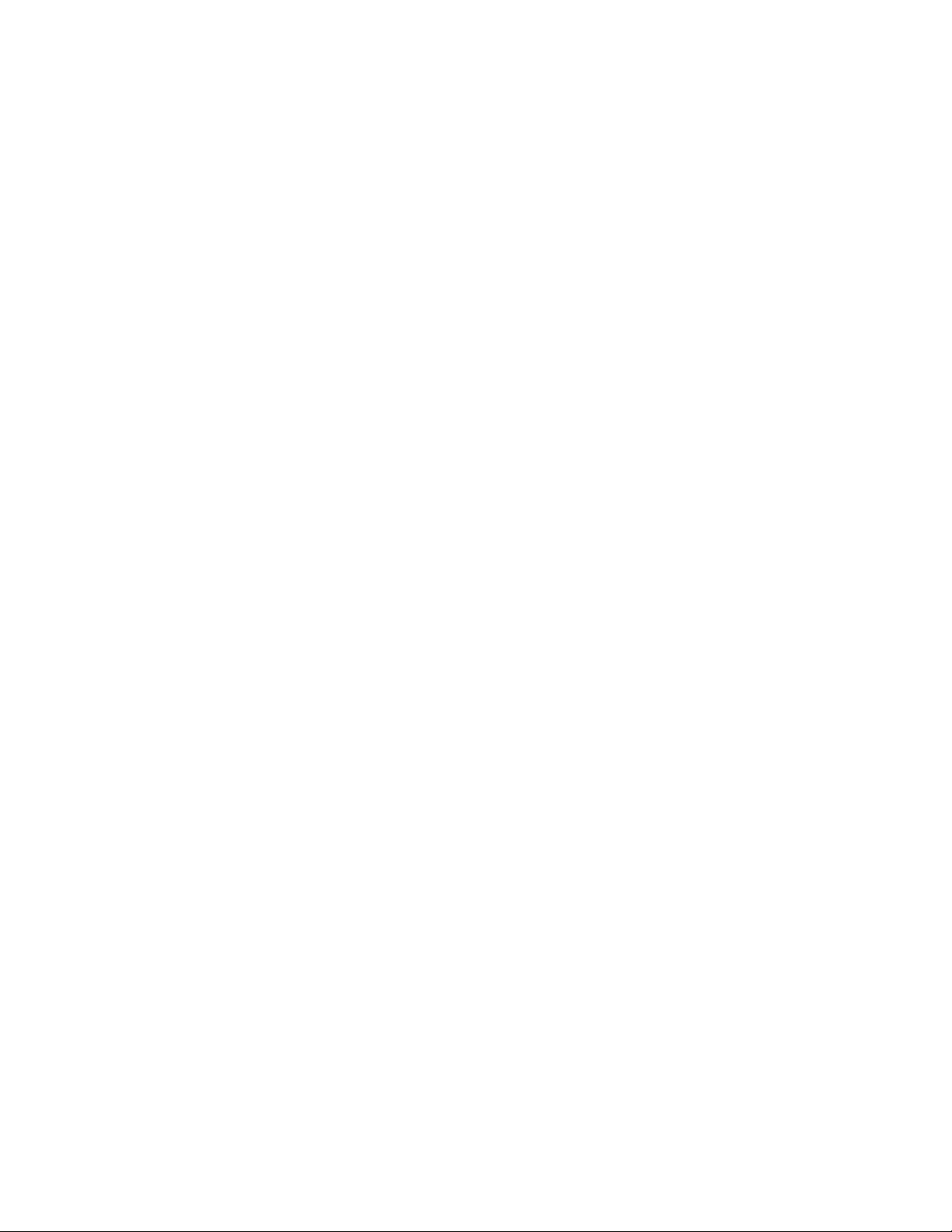
x950 Series Installation Guide for VCStack
145
5. Do one of the following:
To install power supplies, go to “Installing PWR600 AC Power
Supplies” on page 116.
To install an optional XEM2 Ethernet Line Card, go to “Installing an
Optional XEM2 Ethernet Line Card” on page 130.
After installing both switches of the stack, go to Chapter 10,
“Configuring the Master Switch” on page 187.
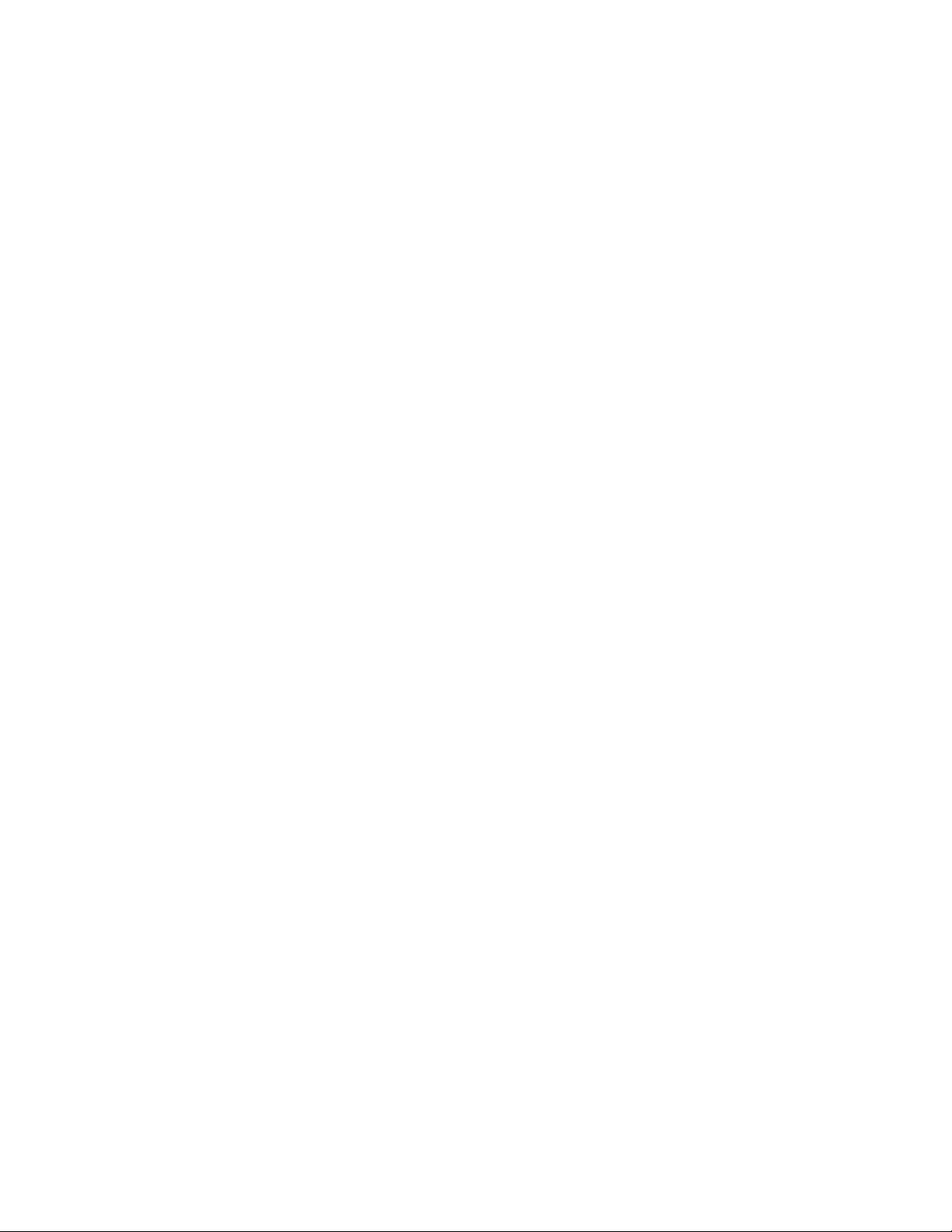
Chapter 7: Installing the Switch in an Equipment Rack
146
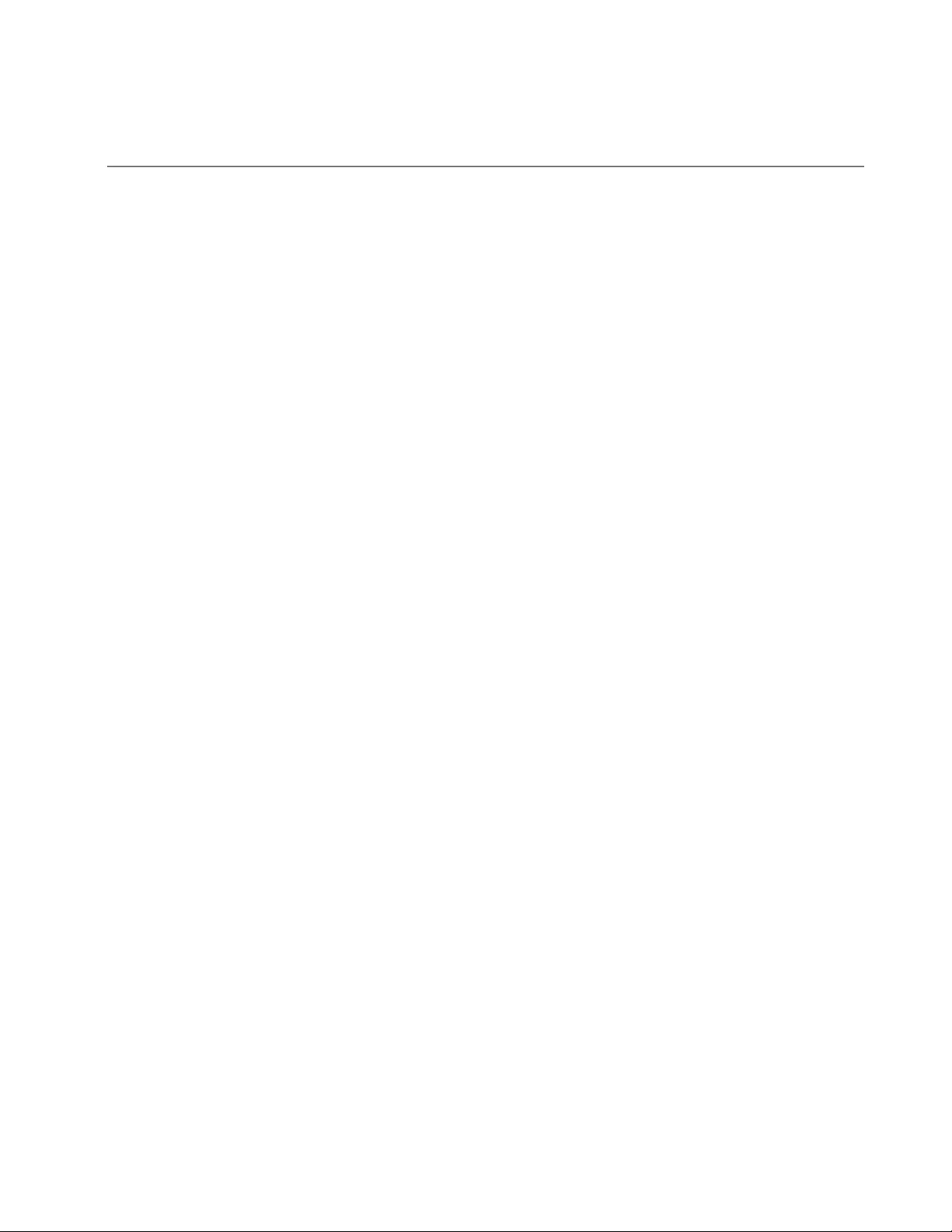
147
Chapter 8
Installing the Switch on a Wall
The procedures in this chapter are listed here:
“Switch Orientations on a Wall” on page 148
“Recommended Minimum Wall Area Dimensions” on page 149
“Plywood Base for a Wall with Wooden Studs” on page 151
“Installation Guidelines” on page 153
“Installing the Plywood Base” on page 155
“Installing the Switch on the Plywood Base” on page 156
“Installing the Switch on a Concrete Wall” on page 159
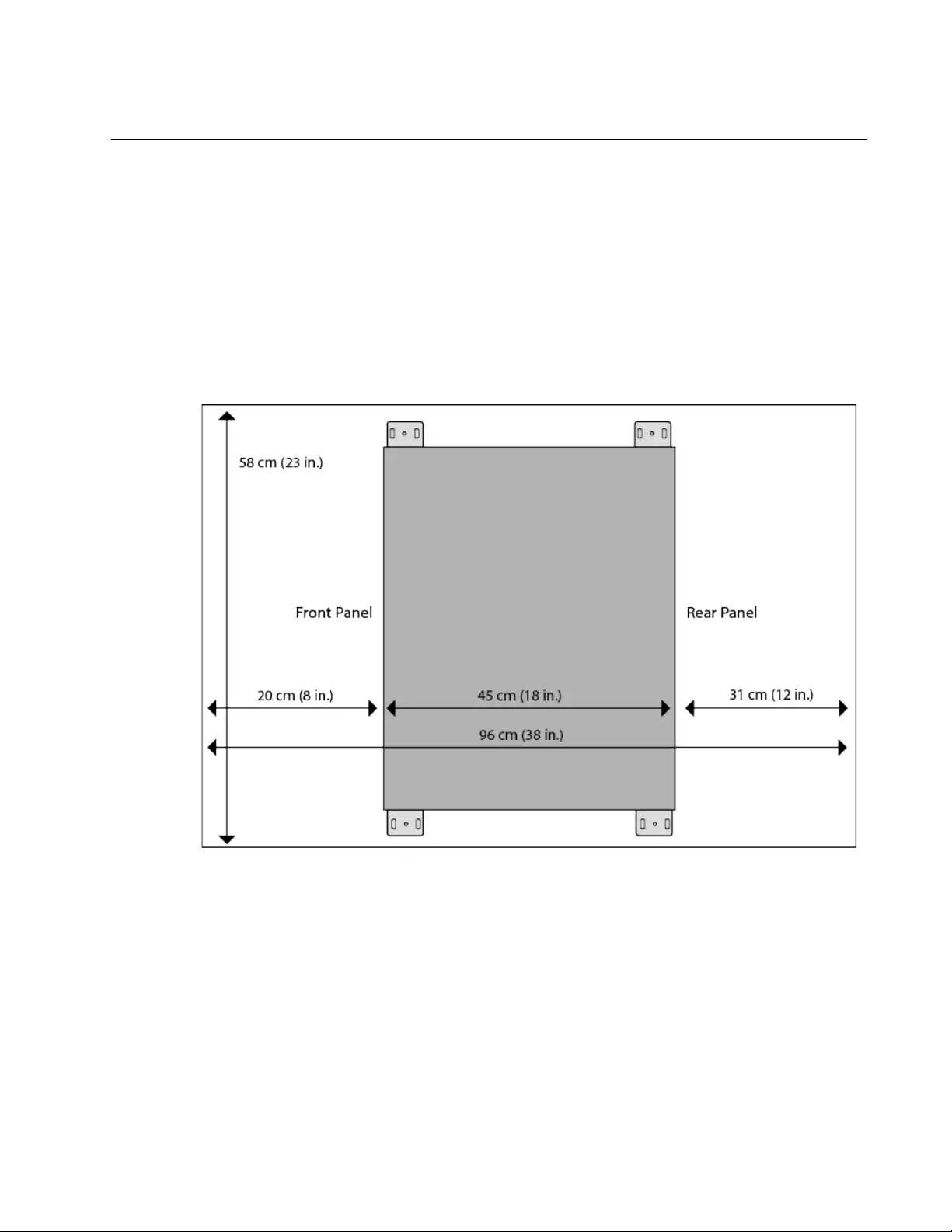
x950 Series Installation Guide for VCStack
149
Recommended Minimum Wall Area Dimensions
The recommended minimum dimensions for the reserved wall area for the
switch are listed here:
Width: 77.4 centimeters (31 inches)
Height: 58.4 centimeters (23 inches)
Figure 88 and Figure 89 on page 150 illustrate the recommended
positions of the switch in the reserved area when the front panel is on the
left and right, respectively. Be sure to leave sufficient space on the rear
panel so that you can replace power supplies or fan modules, if necessary.
Figure 88. Minimum Wall Area Dimensions with the Front Panel on the
Left
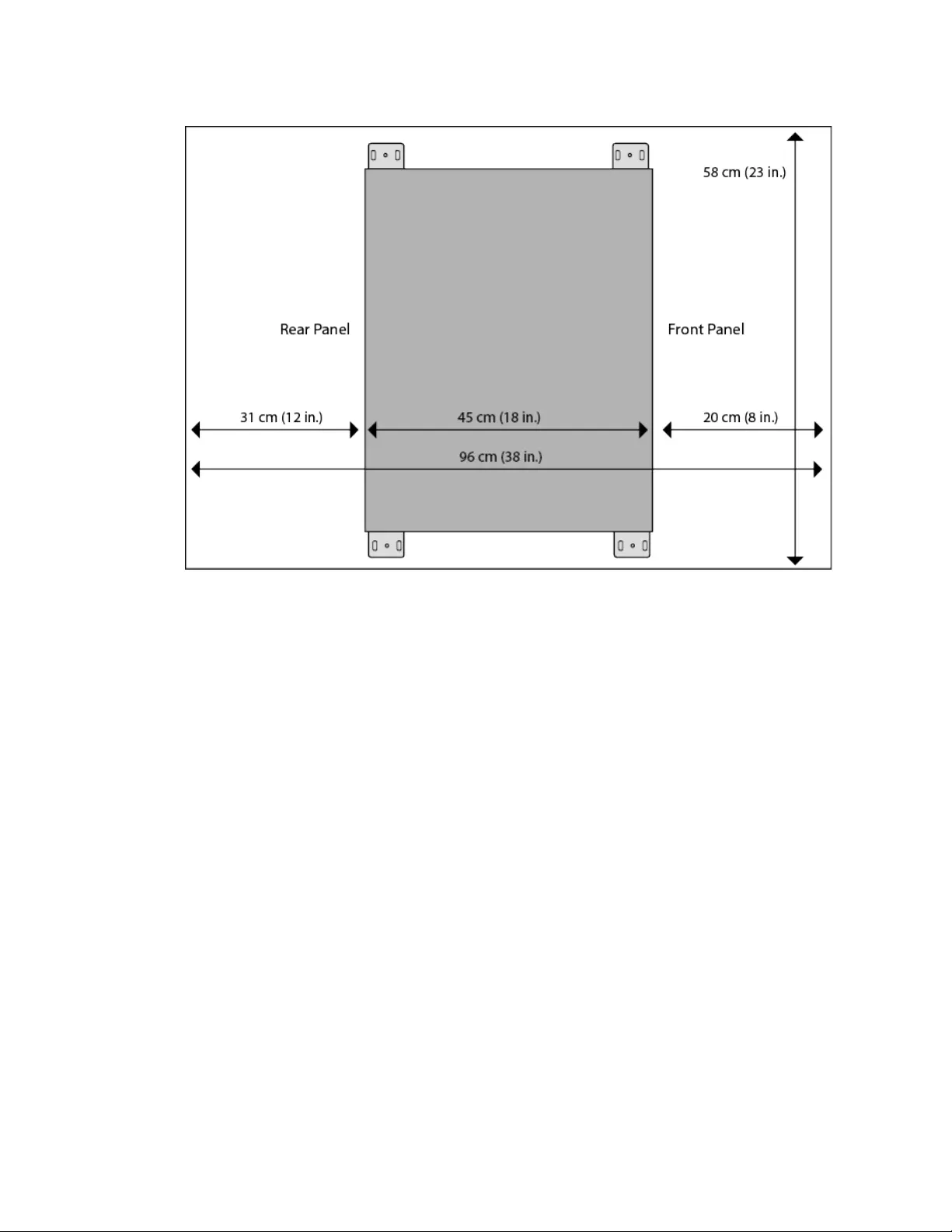
Chapter 8: Installing the Switch on a Wall
150
Figure 89. Minimum Wall Area Dimensions with the Front Panel on the
Right
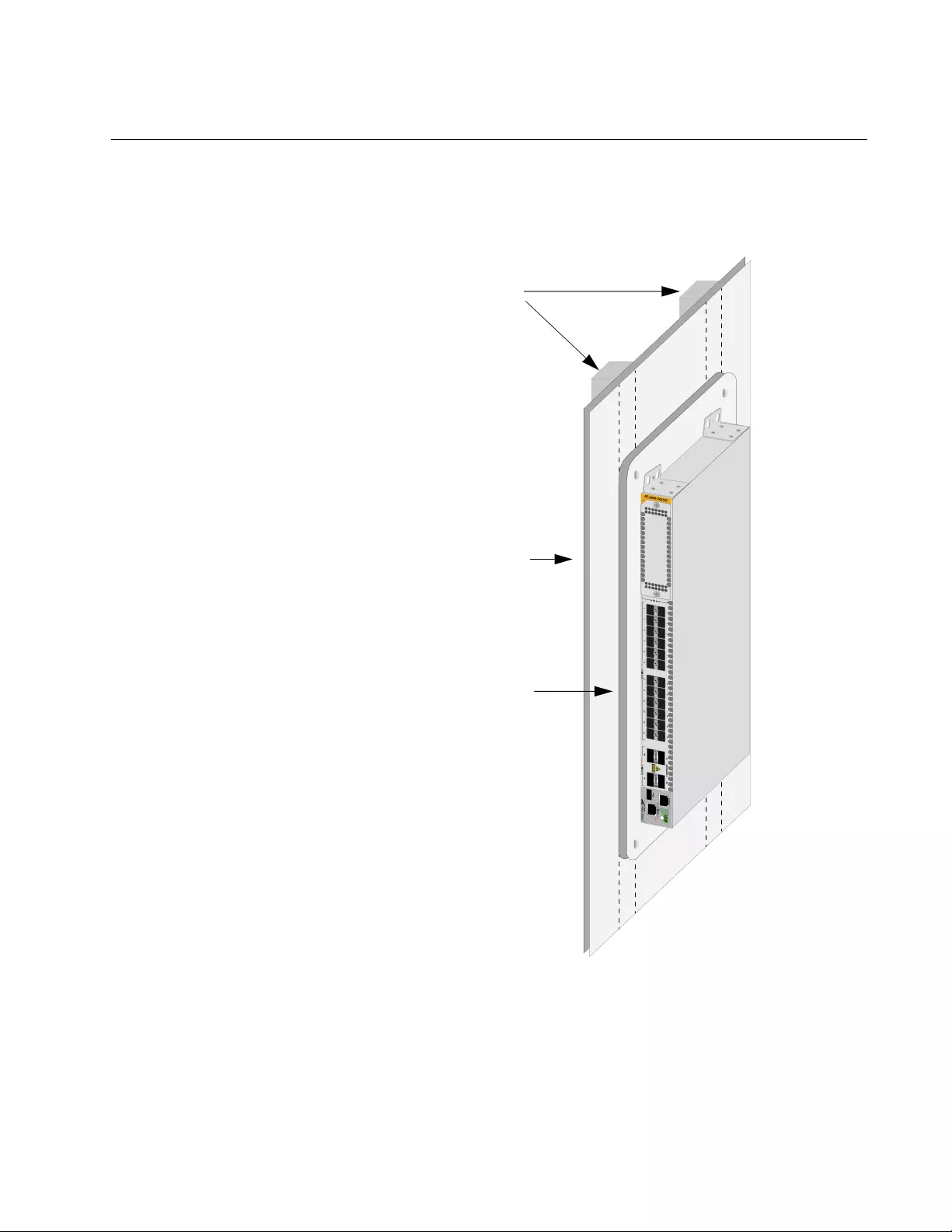
x950 Series Installation Guide for VCStack
151
Plywood Base for a Wall with Wooden Studs
If you are installing the switch on a wall that has wooden studs, Allied
Telesis recommends using a plywood base for the device. (A plywood
base is not required for a concrete wall.) Refer to Figure 90.
Figure 90. Switch on the Wall with a Plywood Base
The plywood base allows you to mount the switch on two wall studs.
Without the base, only one side of the switch would be attached to a stud.
This is because the standard distance between two studs in a wall is 41
centimeters (16 inches) while the distance between the left and right
brackets on the switch is 37 centimeters (14 1/2 inches).
Wall Studs
Wall
Plywood Base
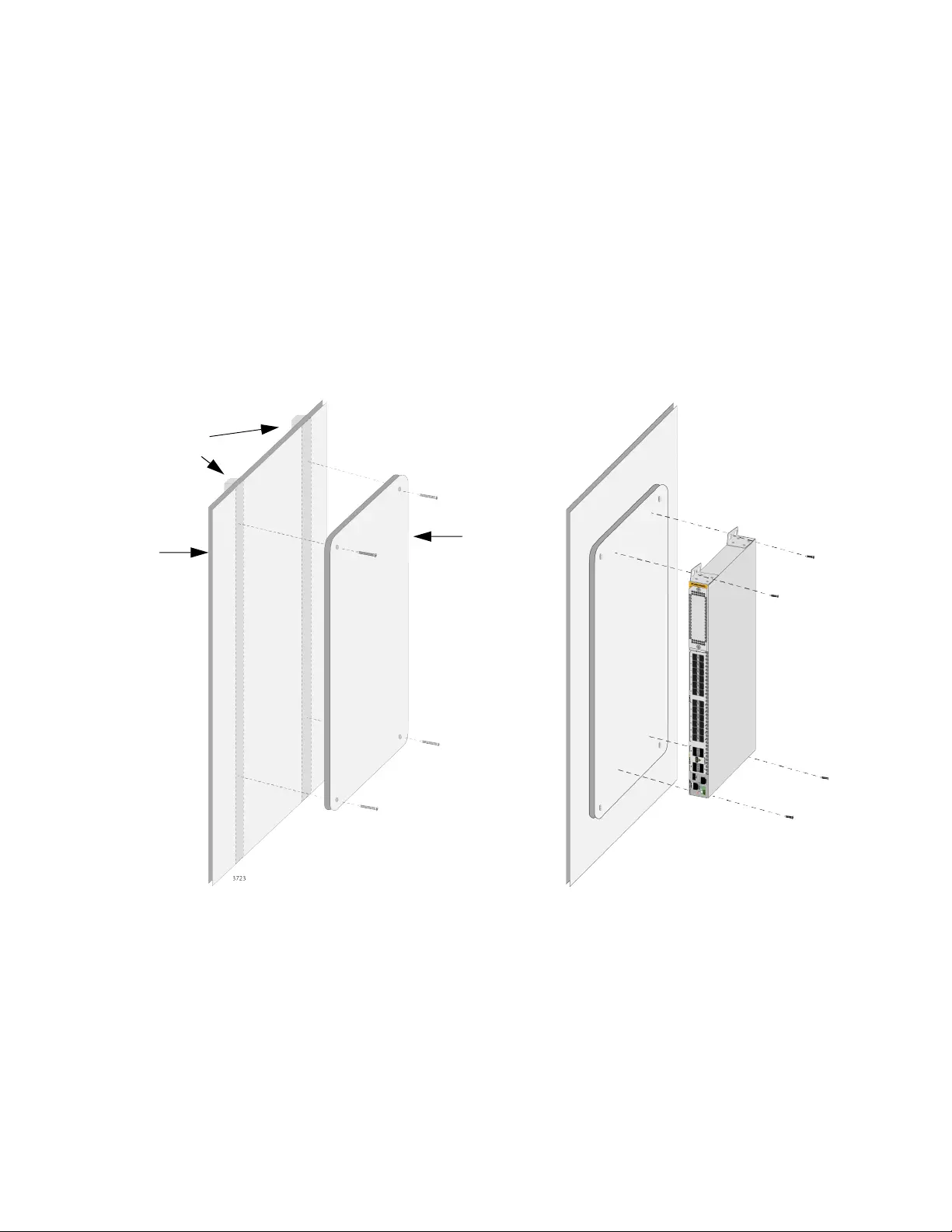
Chapter 8: Installing the Switch on a Wall
152
The recommended minimum dimensions of the plywood base are listed
here:
Width: 58.4 centimeters (23 inches)
Height: 55.9 centimeters (22 inches)
Thickness: 5.1 centimeters (2 inches)
The dimensions assume the wall studs are 41 centimeters (16 inches)
apart. You may need to adjust the width of the base if the distance
between the studs in your wall is different than the industry standard.
You should install the plywood base to the wall and then install the switch
on the base. Refer to Figure 91.
Figure 91. Steps to Installing the Switch with a Plywood Base
Step 1: Install the
plywood base on
the wall.
Step 2: Install the
switch on the
plywood base.
Wall
Plywood
Base
Wall Studs
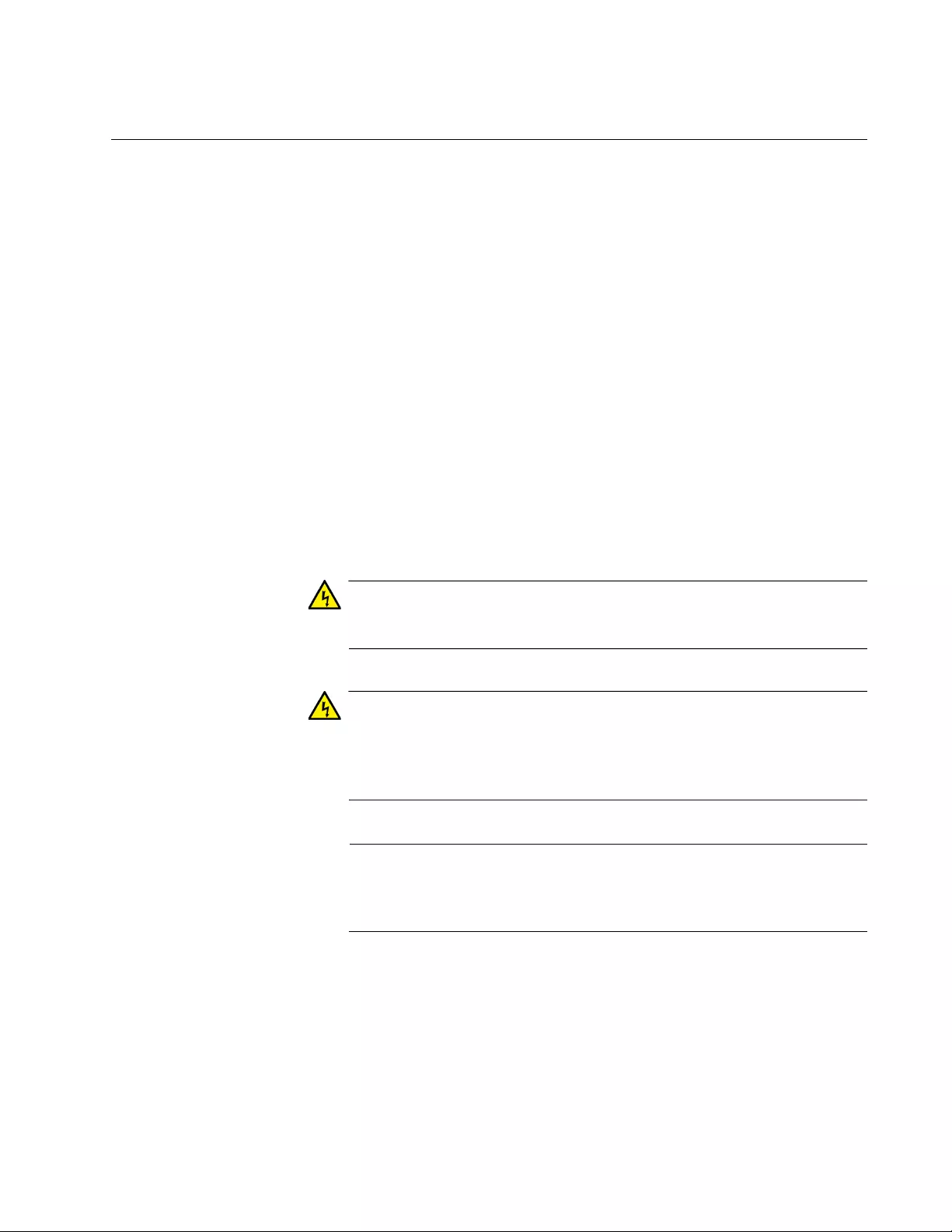
x950 Series Installation Guide for VCStack
153
Installation Guidelines
Here are the guidelines to installing the switch on a wall:
You may install the switch on a wall that has wooden studs.
You may install it on a concrete wall.
If you are installing the switch on a wall with wooden studs, you
should use a plywood base to support the switch. For more
information, refer to “Plywood Base for a Wall with Wooden Studs”
on page 151. A plywood base is not required for a concrete wall.
You should not install the switch on a wall that has metal studs.
Metal studs may not be strong enough to safely support the device.
You should not install the switch only on sheetrock or similar
material. Sheetrock is not strong enough to safely support the
device.
You should install the power supplies and optional XEM2 Line
Card before installing the switch on a wall. For instructions, refer to
“Installing PWR600 AC Power Supplies” on page 116 and
“Installing an Optional XEM2 Ethernet Line Card” on page 130.
Warning
The device is heavy. Always ask for assistance before moving or
lifting it to avoid injuring yourself or damaging the equipment.
Warning
The device should be installed on a wall by a qualified building
contractor. Serious injury to yourself or others or damage to the
equipment may result if it is not properly fastened to the wall.
E105
Note
Depending on your installation, it may be easier to install the power
supplies and optional XEM2 Line Card before installing the switch on
the wall.
Tools and
Material
Here are the required tools and material for installing the switch on a wall:
Four wall/equipment rack brackets and sixteen screws (included
with the switch)
Four wood or concrete wall screws (included with the switch)
Four concrete wall anchors (included with the switch)
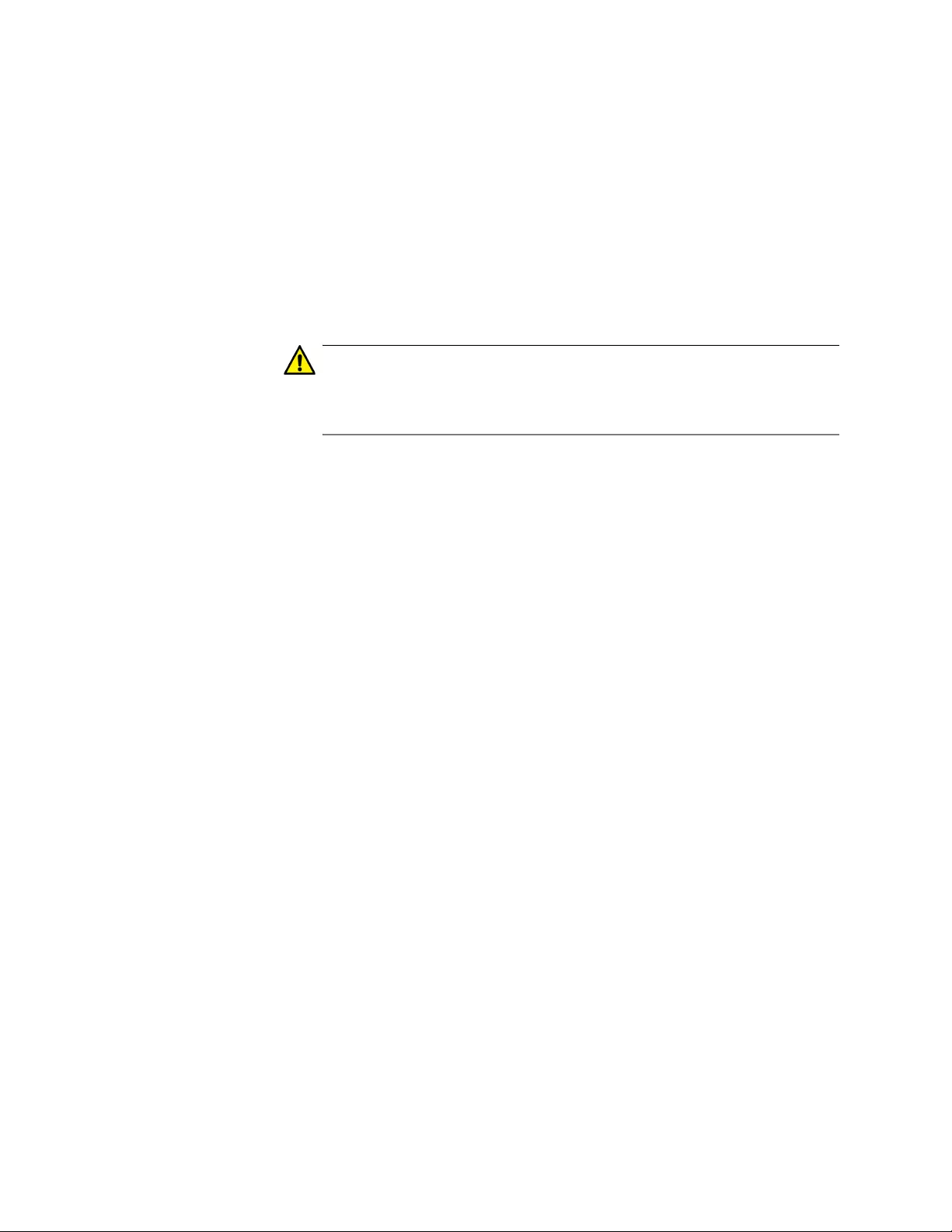
Chapter 8: Installing the Switch on a Wall
154
Cross-head screwdriver (not provided)
Stud finder for a wooden wall, capable of identifying the middle of
wall studs and hot electrical wiring (not provided)
Drill and 1/4” carbide drill bit for a concrete wall (not provided)
Plywood base if you are installing the switch on a wall with wooden
studs (not provided.) Refer to “Plywood Base for a Wall with
Wooden Studs” on page 151 for illustrations.
Four screws and anchors for attaching the plywood base to the
wall (not provided)
Caution
The supplied screws and anchors may not be appropriate for all
walls. A qualified building contractor should determine the hardware
requirements for your wall before installing the switch. E88
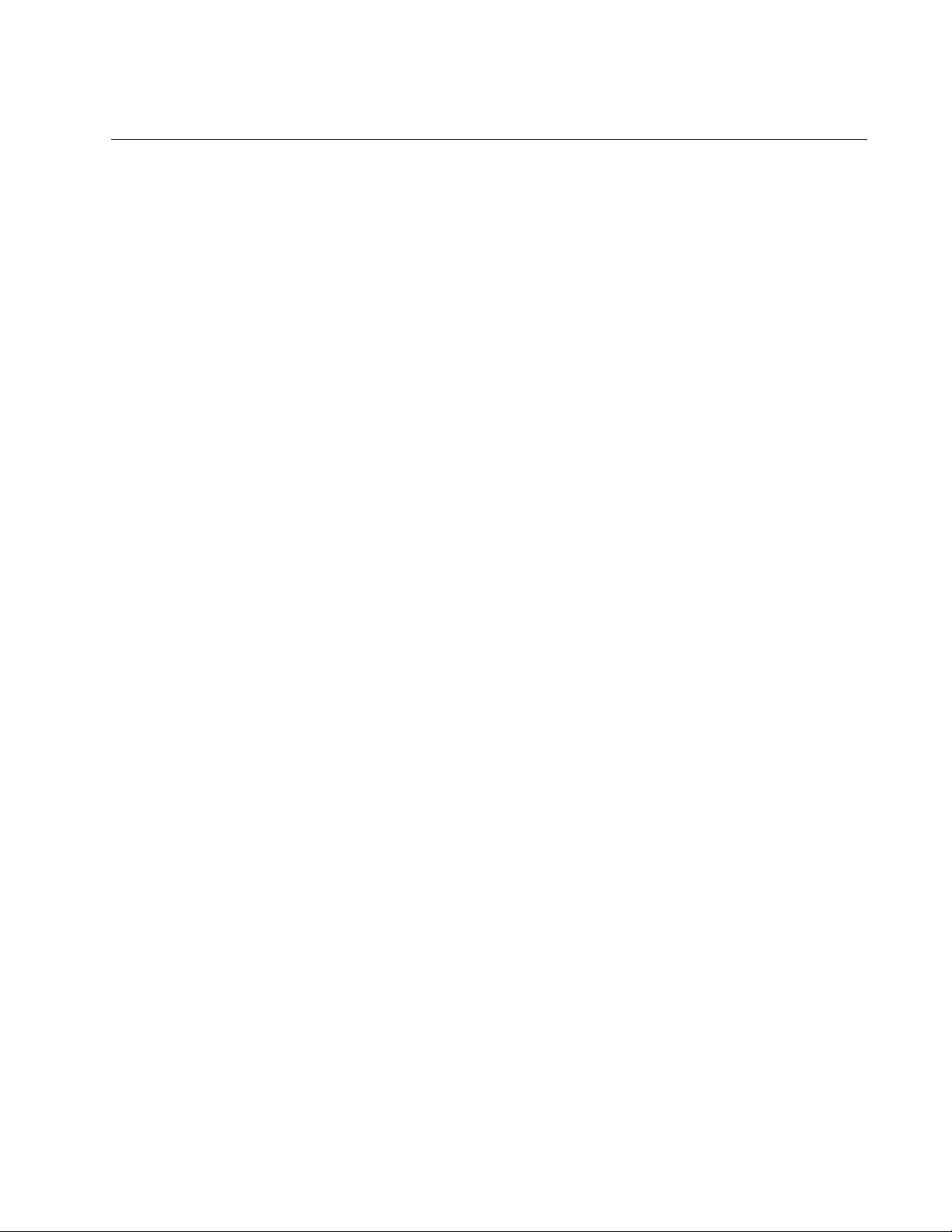
x950 Series Installation Guide for VCStack
155
Installing the Plywood Base
A plywood base is recommended when installing the switch on a wall that
has wooden studs. Refer to “Plywood Base for a Wall with Wooden Studs”
on page 151. Consult a qualified building contractor for installation
instructions for the plywood base. The installation guidelines are listed
here:
You should use a stud finder to identify the middle of studs and hot
electrical wiring in the wall.
You should attach the base to two wall studs with a minimum of
four screws.
The selected wall location for the base should adhere to the
recommendations in “Choosing a Site for the Chassis” on
page 104 and “Recommended Minimum Wall Area Dimensions” on
page 149.
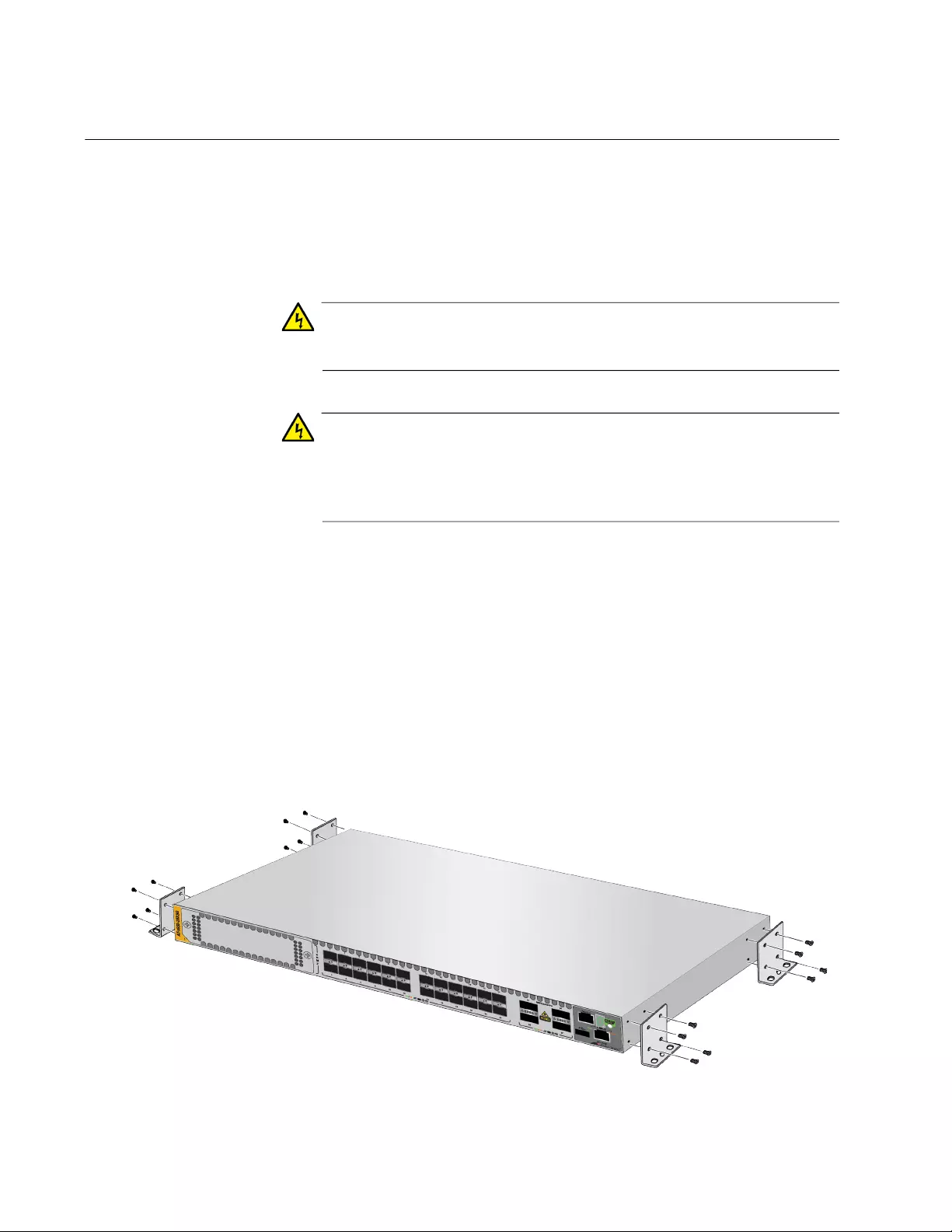
Chapter 8: Installing the Switch on a Wall
156
Installing the Switch on the Plywood Base
This procedure assumes that the plywood base for the switch is already
installed on the wall. Please review “Reviewing Safety Precautions” on
page 98 and “Choosing a Site for the Chassis” on page 104 before
performing this procedure. Allied Telesis recommends a minimum of three
people for this procedure.
Warning
The device is heavy. Always ask for assistance before moving or
lifting it to avoid injuring yourself or damaging the equipment.
Warning
The device should be installed on the wall by a qualified building
contractor. Serious injury to yourself or others or damage to the
equipment may result if it is not properly fastened to the wall.
E105
Allied Telesis recommends installing the power supplies and optional
XEM2 Line Card before installing the switch on a wall. For instructions,
refer to “Installing PWR600 AC Power Supplies” on page 116 and
“Installing an Optional XEM2 Ethernet Line Card” on page 130.
To install the switch on the plywood base, perform the following
procedure:
1. Place the switch in a table.
2. Install the four brackets with the sixteen screws that come with the
switch to the sides of the unit, as shown in Figure 92.
Figure 92. Installing the Brackets to the Switch for Wall Installation
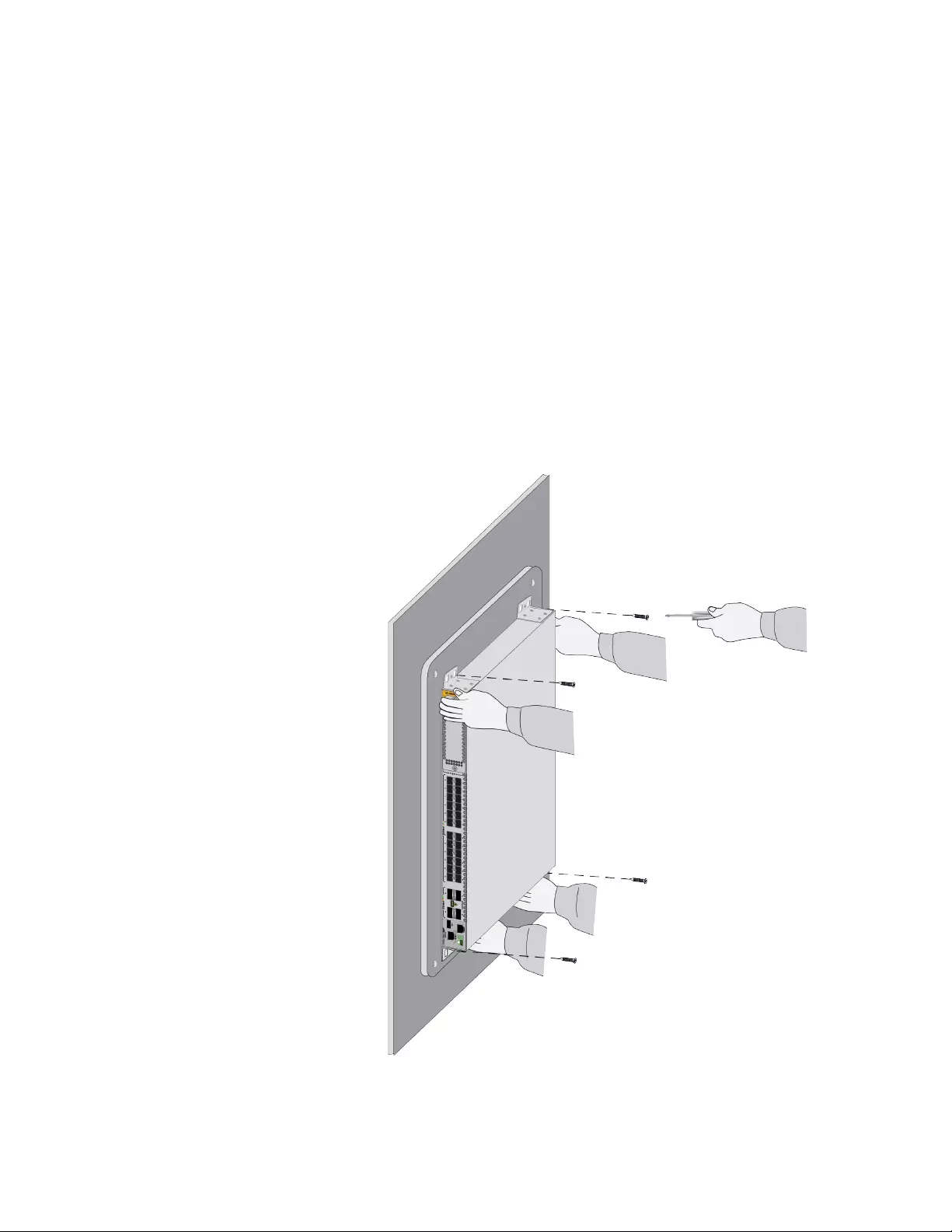
x950 Series Installation Guide for VCStack
157
The sides of the switch have two sets of holes. One set is for installing
the switch on a wall with the brackets and the other is for the RKMT-
SL01 Rack Mounting Kit. For this procedure, you need to use the
bracket holes, identified in Figure 82 on page 140.
3. After attaching the brackets to the side of the switch, have two people
hold the switch on the plywood base on the wall while you secure it
with the four provided screws. Refer to Figure 93.
Please follow these guidelines as you position the switch on the wall:
Position the switch so that the front panel is either on the left or the
right. Refer to Figure 87 on page 148. You may not install the
switch with the front panel facing up or down.
Leave sufficient space from other devices or walls so that you can
access the front and back panels. Refer to “Recommended
Minimum Wall Area Dimensions” on page 149.
Figure 93. Attaching the Switch to the Plywood Base
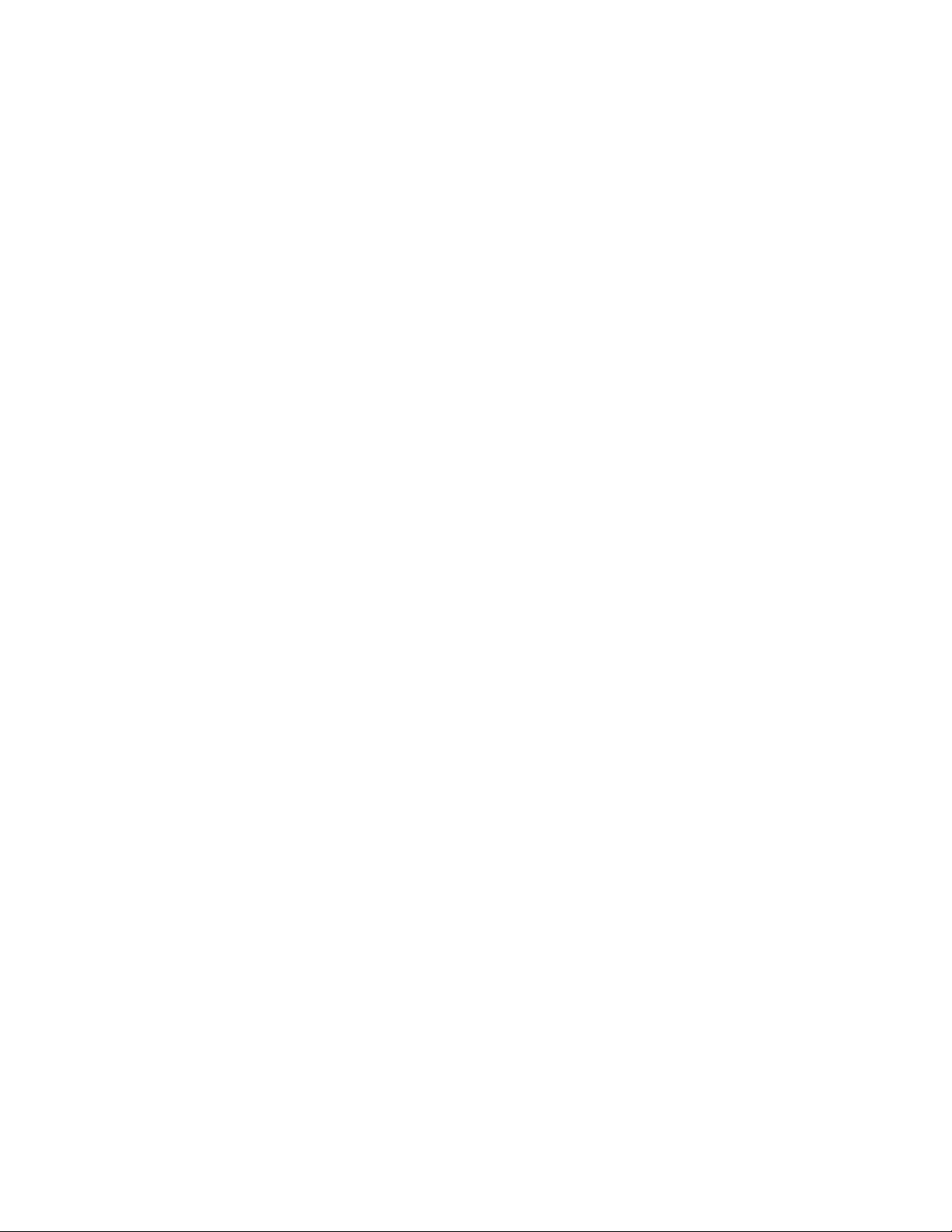
Chapter 8: Installing the Switch on a Wall
158
4. Do one of the following:
To install the power supplies, go to “Installing PWR600 AC Power
Supplies” on page 116.
To install an optional XEM2 Ethernet Line Card, go to “Installing an
Optional XEM2 Ethernet Line Card” on page 130.
After installing the switches of the stack, go to Chapter 10,
“Configuring the Master Switch” on page 187.
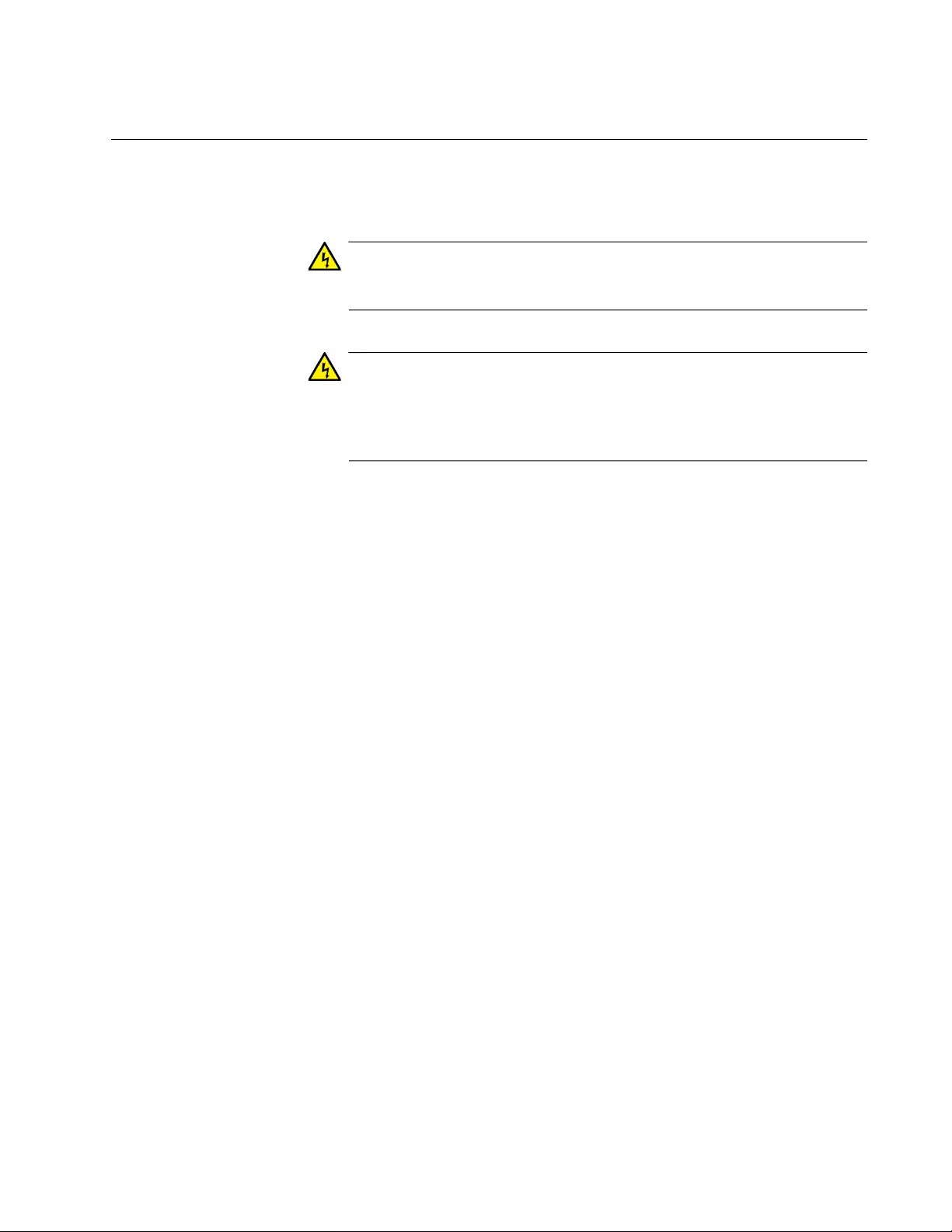
x950 Series Installation Guide for VCStack
159
Installing the Switch on a Concrete Wall
Allied Telesis recommends a minimum of three people for this procedure.
To install the switch on a concrete wall, perform the following procedure:
Warning
The device is heavy. Always ask for assistance before moving or
lifting it to avoid injuring yourself or damaging the equipment.
Warning
The device should be installed on a wall by a qualified building
contractor. Serious injury to yourself or others or damage to the
equipment may result if it is not properly fastened to the wall.
E105
Allied Telesis recommends installing the power supplies and optional
XEM2 Line Card before installing the switch on a wall. For instructions,
refer to “Installing PWR600 AC Power Supplies” on page 116 and
“Installing an Optional XEM2 Ethernet Line Card” on page 130.
1. Place the switch in a table.
2. Install the four brackets with sixteen screws that come with the switch
to the sides of the unit, as shown in Figure 92 on page 156.
3. Have two people hold the switch on the concrete wall at the selected
location for the device while you use a pencil or pen to mark the wall
with the locations of the four screw holes in the four brackets. Refer to
Figure 94 on page 160.
Please follow these guidelines as you position the switch on the wall:
Position the switch so that the front panel is either on the left or the
right. Refer to Figure 87 on page 148. You may not install the
switch with the front panel facing up or down.
Leave sufficient space from other devices or walls so that you can
access the front and back panels. Refer to “Recommended
Minimum Wall Area Dimensions” on page 149.
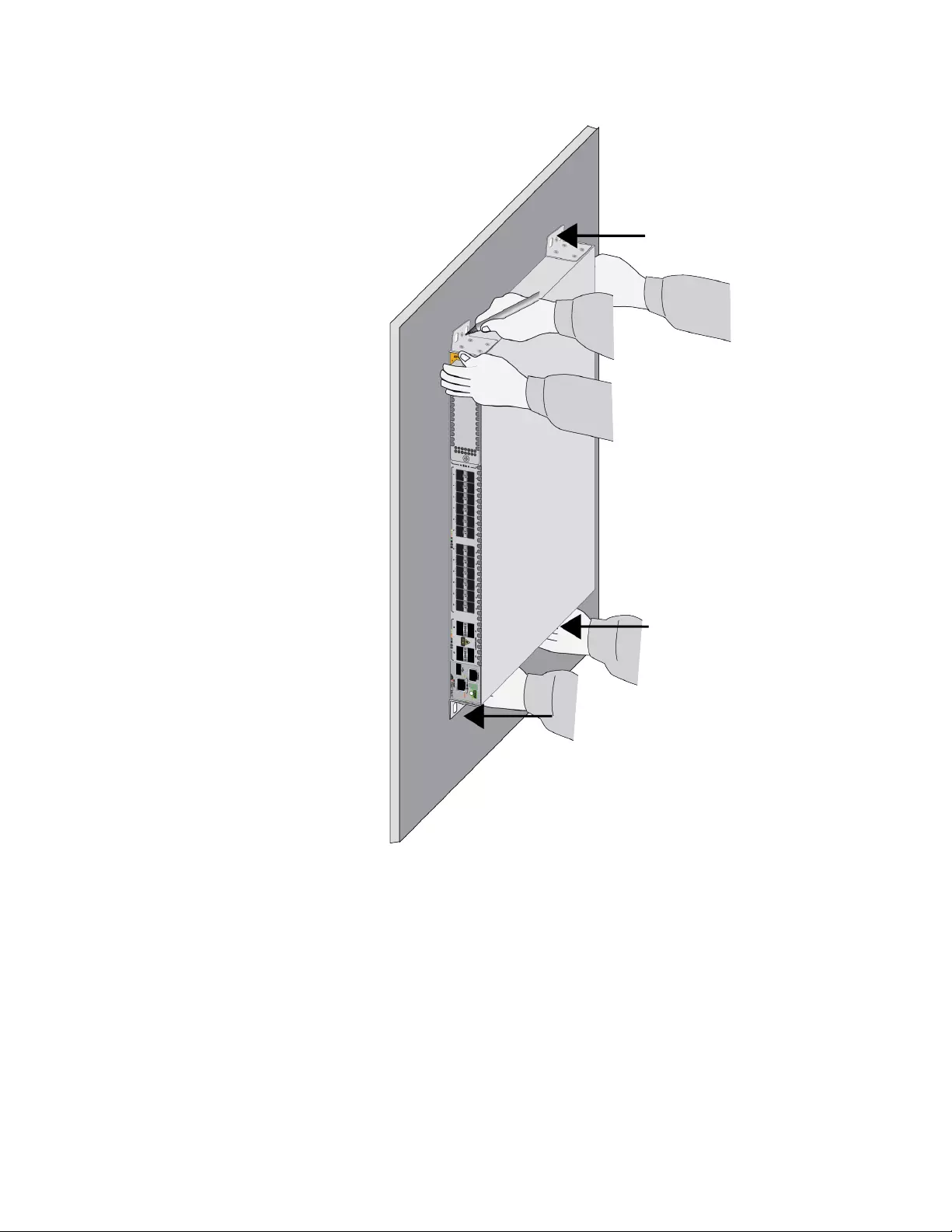
Chapter 8: Installing the Switch on a Wall
160
Figure 94. Marking the Locations of the Bracket Holes on a Concrete Wall
4. Place the switch on a table or desk.
5. Use a drill and 1/4” carbide drill bit to pre-drill the four holes you
marked in step 3. Please review the following guidelines:
Prior to drilling, set the drill to hammer and rotation mode. The
modes break up the concrete and clean out the hole.
Allied Telesis recommends cleaning out the holes with a brush or
compressed air.
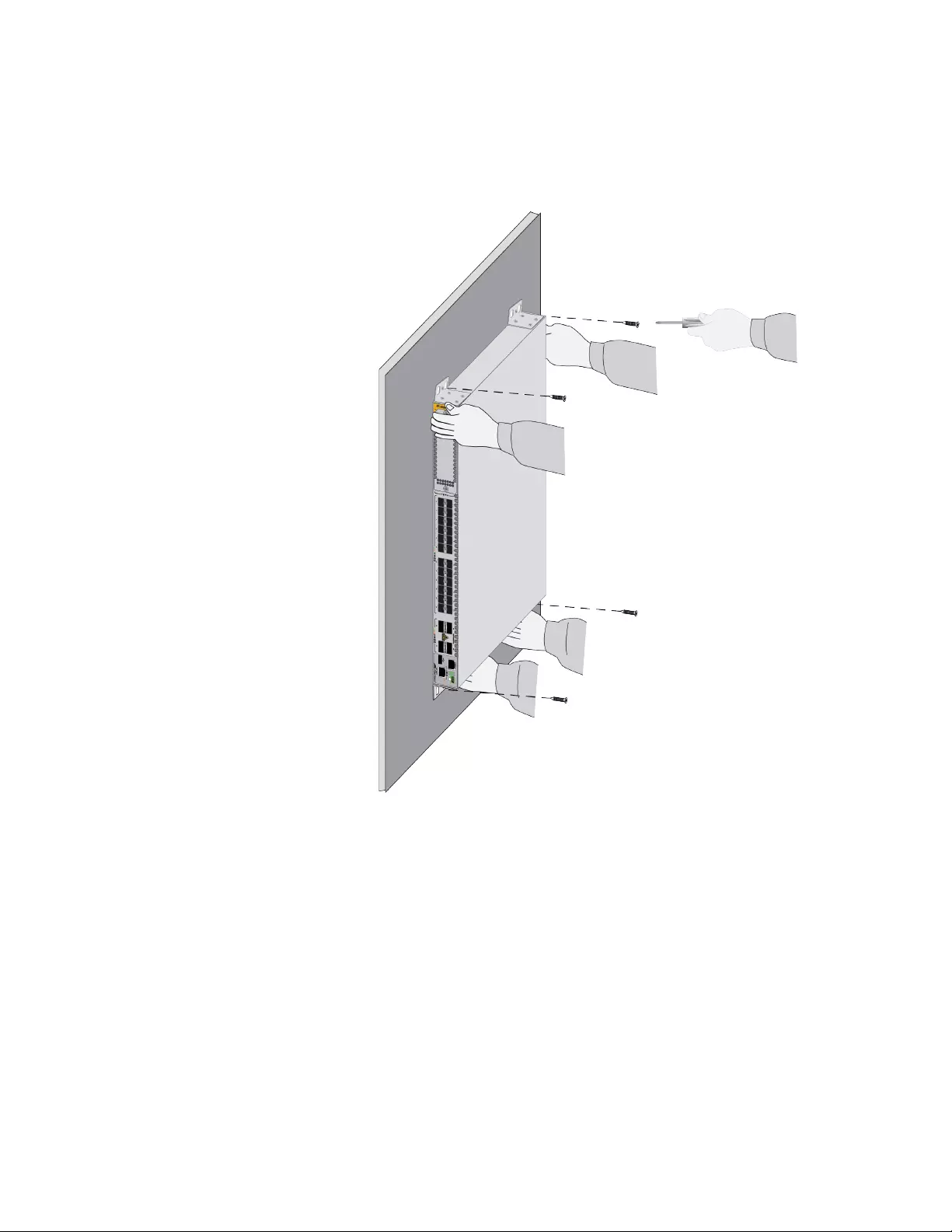
x950 Series Installation Guide for VCStack
161
6. Insert the four anchors into the holes.
7. Have two people hold the switch at the selected wall location while you
secure it to the wall with the four provided screws. Refer to Figure 95.
Figure 95. Installing the Switch on a Concrete Wall
8. Do one of the following:
To install the power supplies, go to “Installing PWR600 AC Power
Supplies” on page 116.
To install an optional XEM2 Ethernet Line Card, go to “Installing an
Optional XEM2 Ethernet Line Card” on page 130.
After installing the switches of the stack, go to Chapter 10,
“Configuring the Master Switch” on page 187.
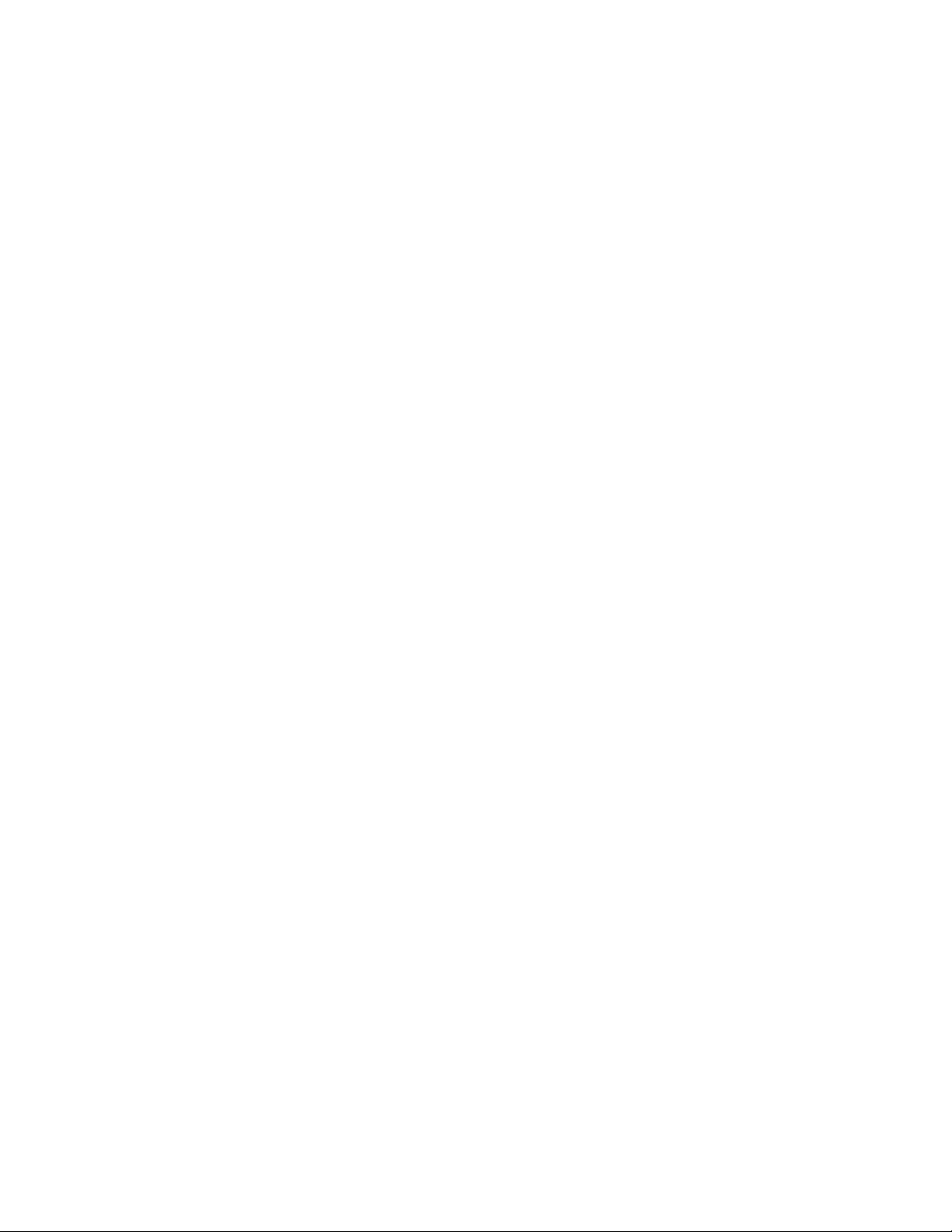
Chapter 8: Installing the Switch on a Wall
162
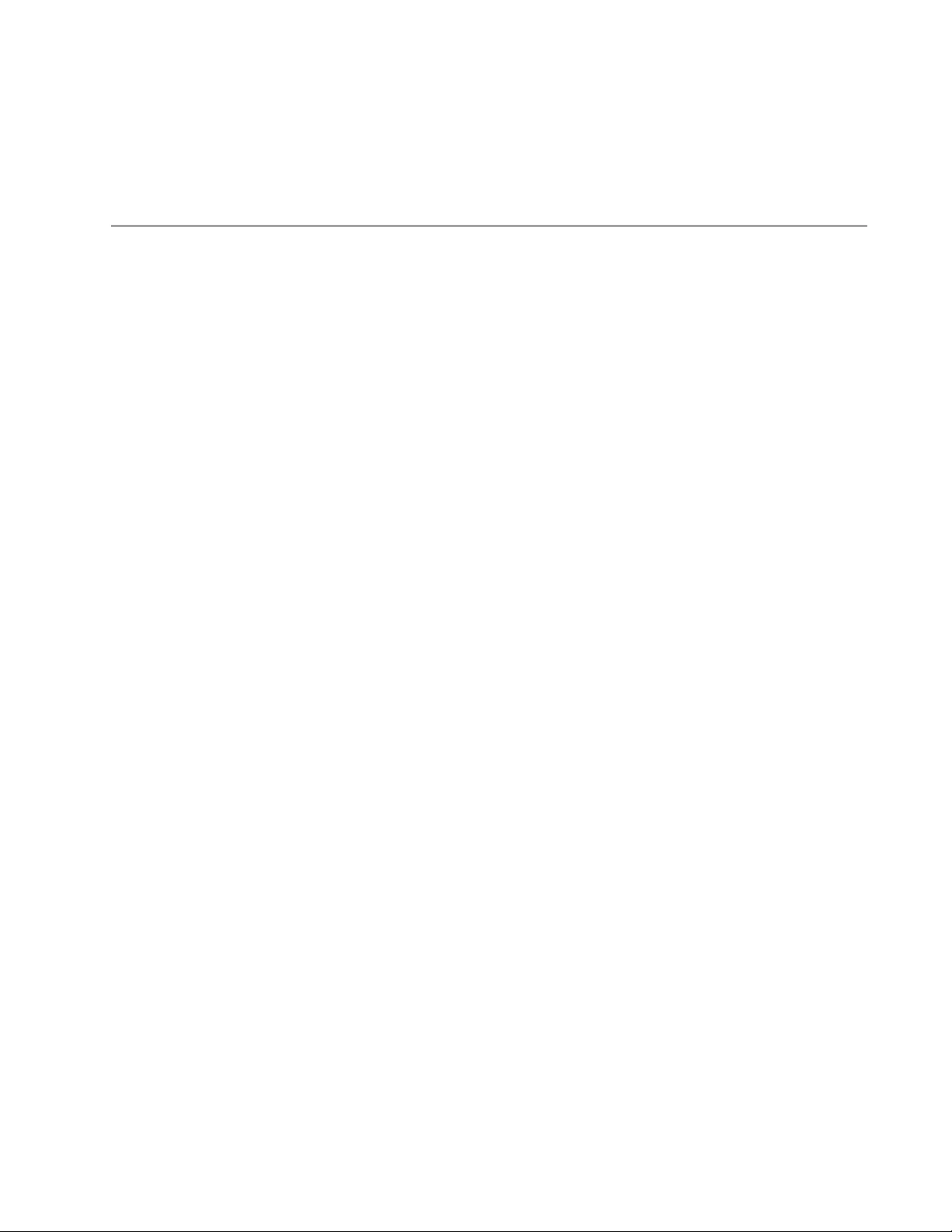
163
Chapter 9
Installing the Switch in the RKMT-SL01
Sliding Rack
This appendix contains the following sections:
“Introduction” on page 164
“Rack Mount Kit Components” on page 165
“Equipment Rack Requirements” on page 167
“Reviewing Safety Precautions” on page 168
“Installation Overview” on page 171
“Unpacking the Shipping Container” on page 172
“Installing the Outer Rails on the Equipment Rack” on page 174
“Installing the Extension Brackets on the Inner Rails” on page 176
“Installing the Inner Rails on the Switch” on page 182
“Installing the Switch in the Equipment Rack” on page 184
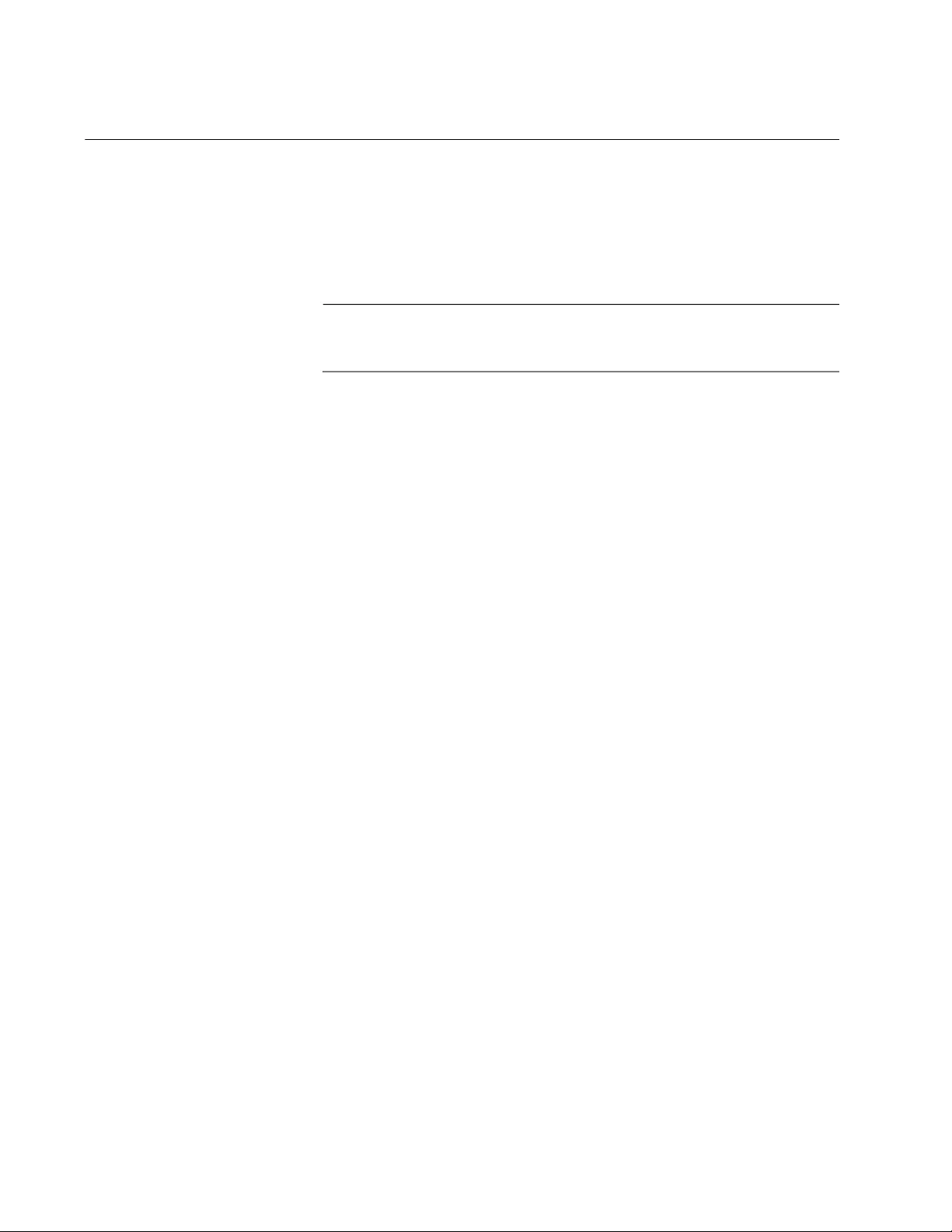
Chapter 9: Installing the Switch in the RKMT-SL01 Sliding Rack
164
Introduction
The RKMT-SL01 Rack Mount Kit is a slide-rail type rack-mount kit for
Allied Telesis switches in EIA standard 19-inch equipment racks. The kit
makes installation and maintenance of network equipment easier by
letting you slide switches into or out of equipment racks, including server
racks with deep dimensions.
Note
The RKMT-SL01 Kit should only be used with approved Allied
Telesis products.
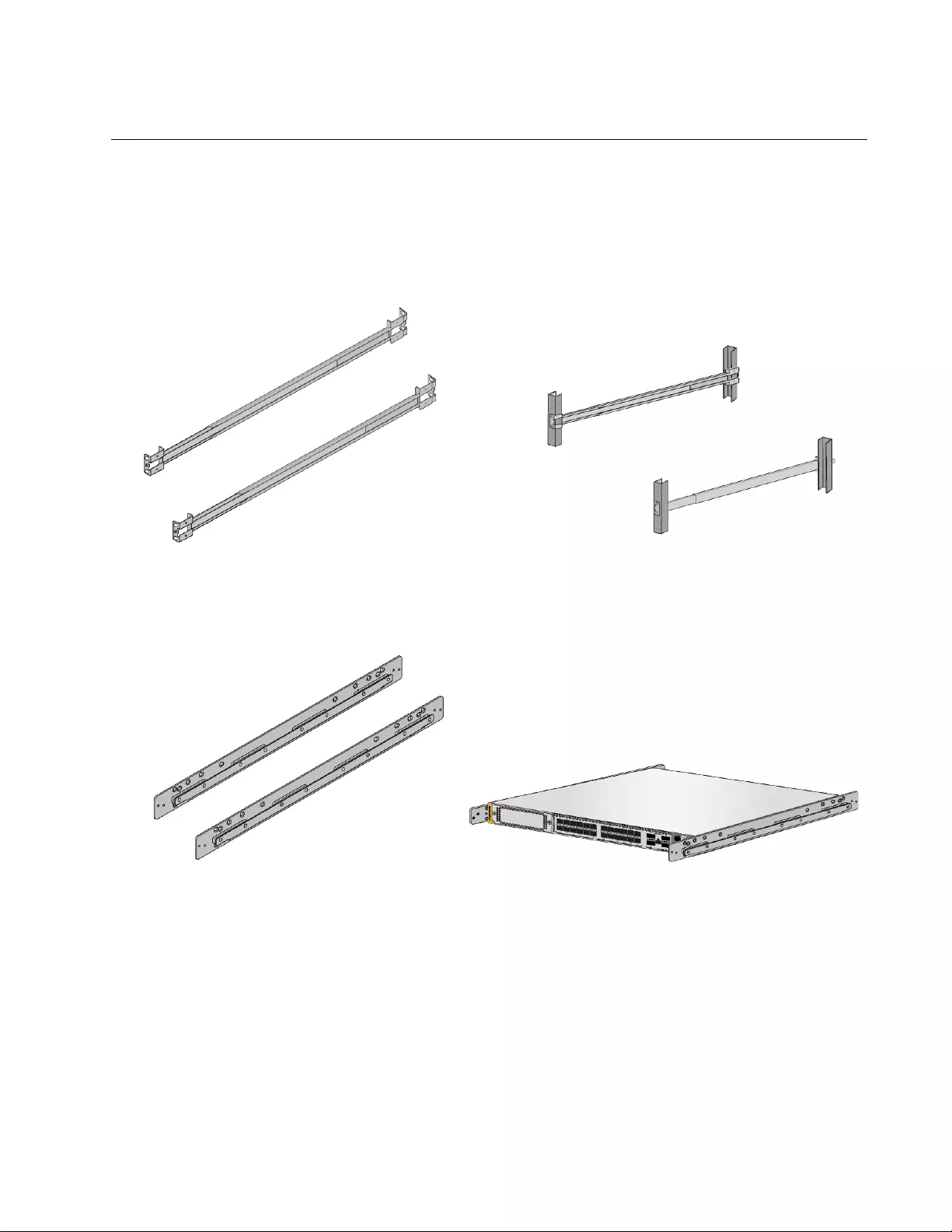
x950 Series Installation Guide for VCStack
165
Rack Mount Kit Components
The kit has three main components.
Adjustable Outer
Rails
Two adjustable outer rails attach to the equipment rack. They are suitable
for racks with depths of 600 mm (23.6 in) to 900 mm (35.4 in). Refer to
Figure 96.
Figure 96. Outer Rails
Inner Rails Two Inner rails attach to the sides of the switch. Refer to Figure 97.
Figure 97. Inner Rails
Extension
Brackets
Two extension brackets attach to the front of the inner rails and control the
amount the switch is recessed in the equipment rack. The brackets also
have a captive screw for securing the switch in the equipment rack. Refer
to Figure 98 on page 166.
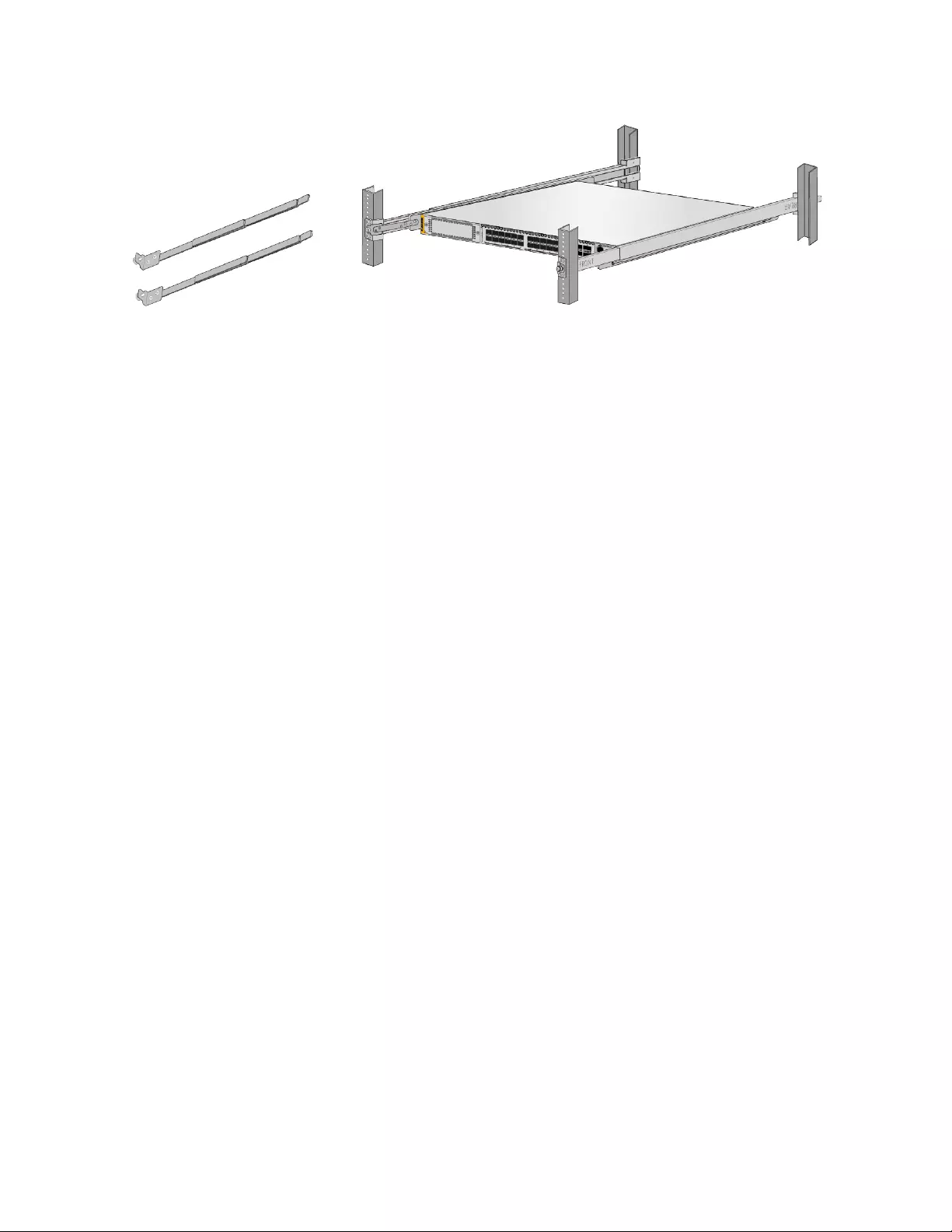
Chapter 9: Installing the Switch in the RKMT-SL01 Sliding Rack
166
Figure 98. Extension Brackets
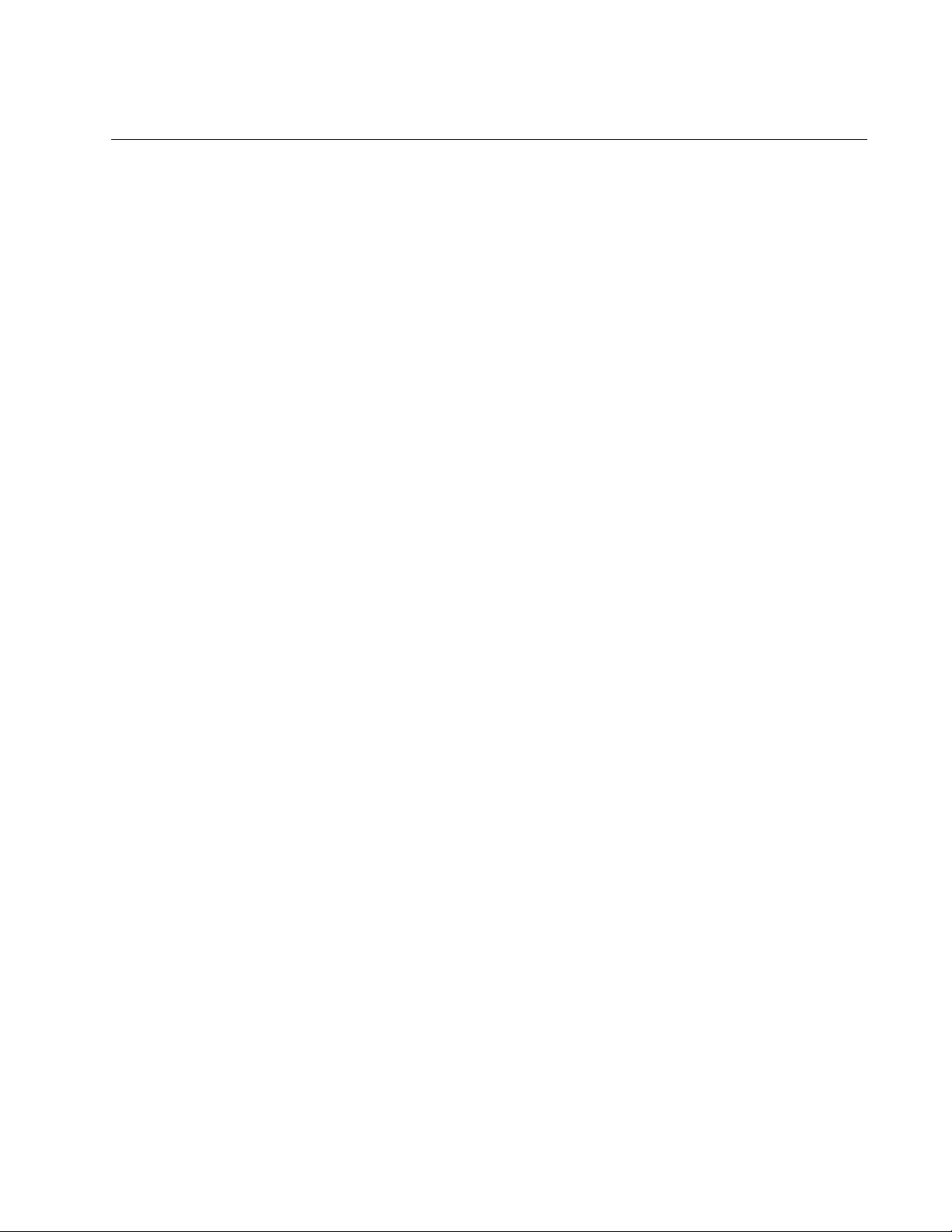
x950 Series Installation Guide for VCStack
167
Equipment Rack Requirements
The Rack Mount Kit is designed for equipment racks that meet the
following requirements:
The depth can be from 600 mm (23.6 in) to 900 mm (35.4 in).
The width should be a minimum of 452 mm (17.8 in).
There should be 35 mm (1.4 in) depth within the rack post for the
outer rail mounting.
The distance between the left and right wall (for the outer rail
mounting) should be a minimum of 10 mm (0.4 in) from the screw
hole in the center of the rack posts.
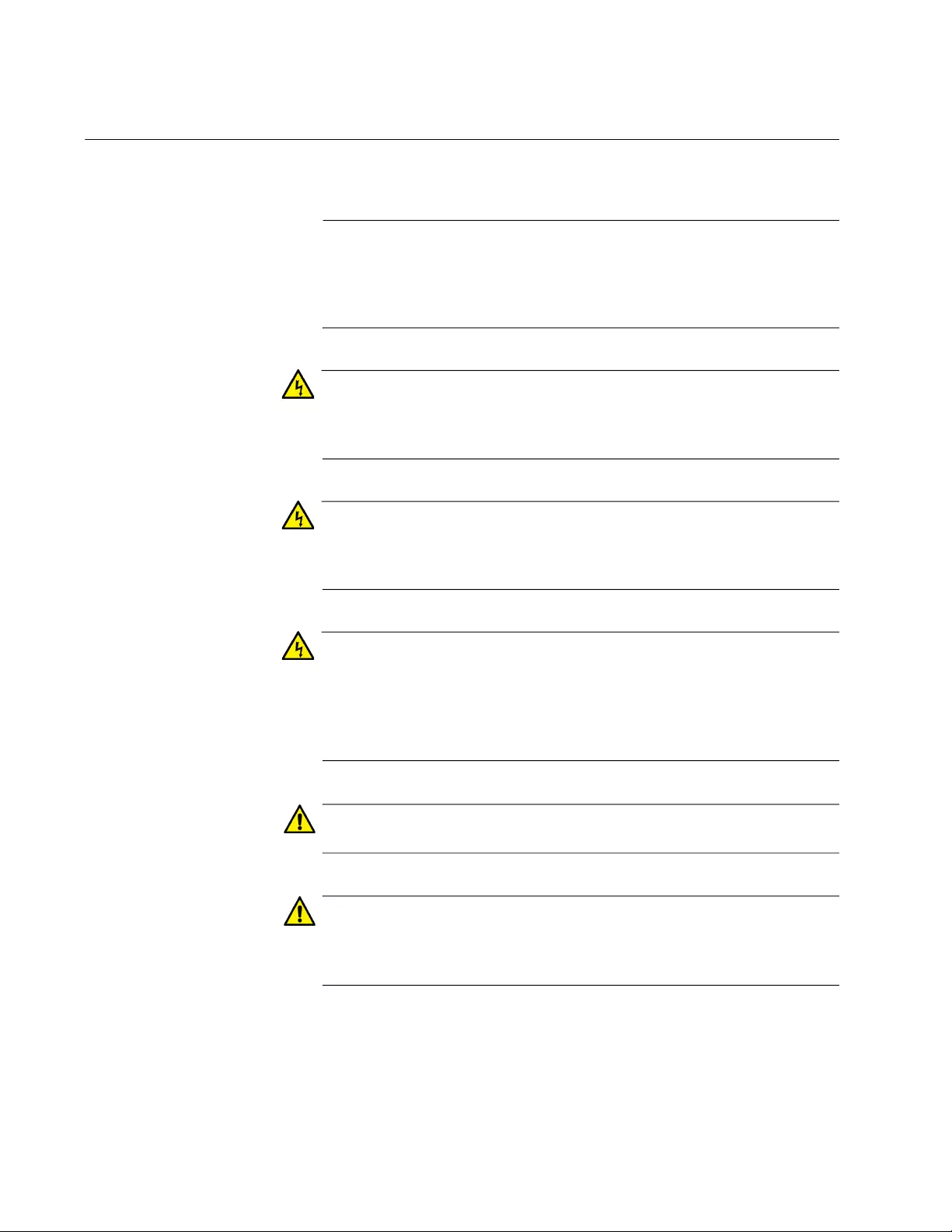
Chapter 9: Installing the Switch in the RKMT-SL01 Sliding Rack
168
Reviewing Safety Precautions
Review these safety precautions before installing the RKMT-SL01 Kit.
Note
The indicates that a translation of the safety statement is
available in a PDF document titled Translated Safety Statements
posted on the Allied Telesis website at www.alliedtelesis.com/
support.
Warning
Mounting of the equipment in the rack should be such that a
hazardous condition is not created due to uneven mechanical
loading. E25
Warning
Do not pull the rear of the switch out past the front rack posts. If you
need to position the rear of the switch out past the front of the rack,
you should remove it completely from the rack. E58
Warning
Pull the switch out slowly if you must remove it from the rack for
maintenance. If you pull the switch out past the front of the rack
posts, or if you pull it out too quickly, there is a risk that the weight of
the switch will cause the sliding rail assemblies to fail and cause the
switch to fall out. E59
Caution
Avoid applying excessive force to the cables. E60
Caution
If using long extension bracket(s), secure between the fixed bracket
and short extension bracket - the long extension bracket(s) cannot
be attached directly to the inner rail. E61
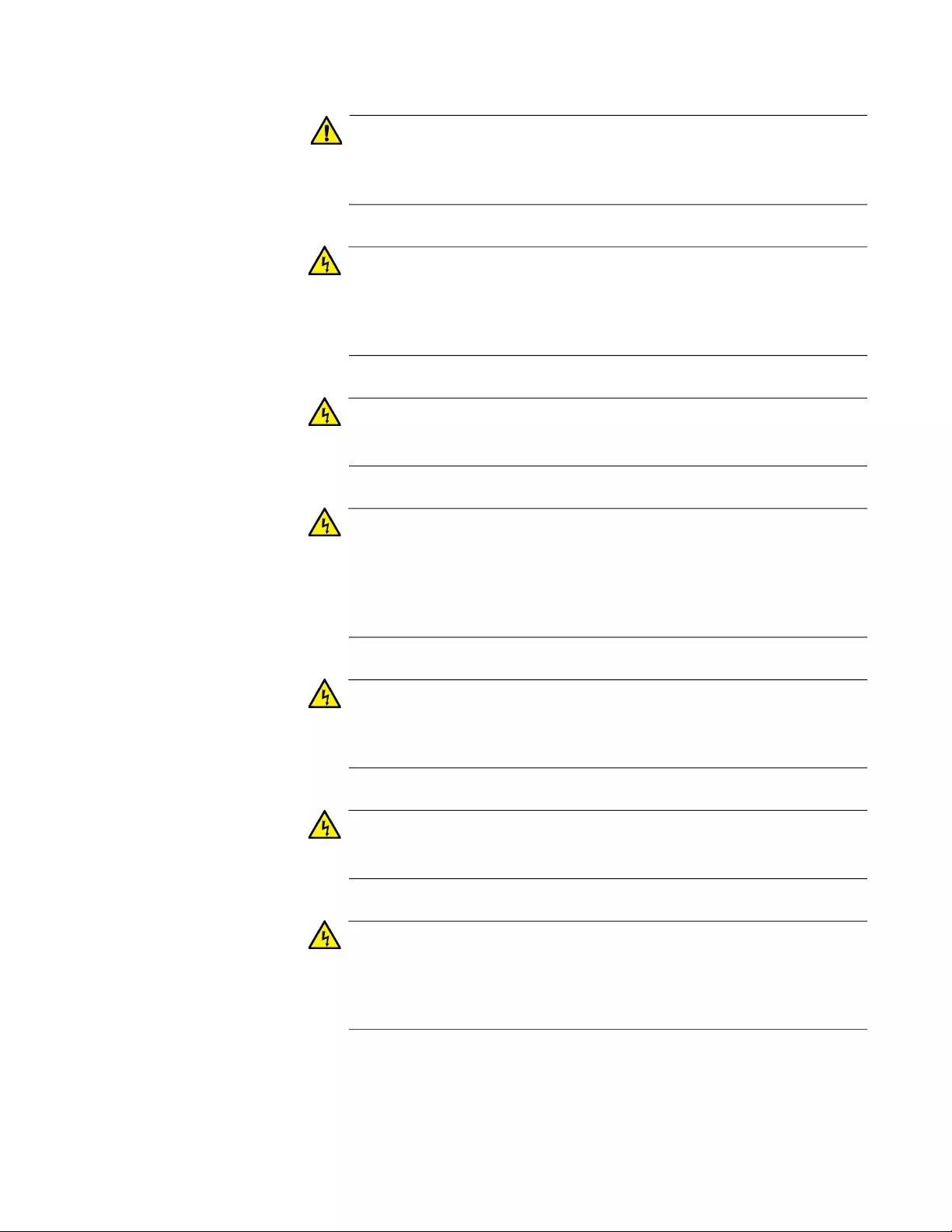
x950 Series Installation Guide for VCStack
169
Caution
Use the adjustment bracket screws supplied with the inner rail.
Using screws other than those supplied may result in equipment
damage. E62
Warning
When installing the outer and inner rails, and adjustment bracket,
ensure the components are securely attached with the appropriate
screws. If not securely attached, a serious accident may occur due
to falling equipment. E63
Warning
When installing and removing the switch from the rack, disconnect
the media and power cables. E64
Warning
A built-in stopper prevents the outer rail from extending beyond its
maximum length of 960 mm (37.8 in). Do not extend the rail by force
beyond this point, otherwise, the outer bracket will be weakened,
and the switch may fall from the rack; equipment could be damaged.
E65
Warning
Ensure the front and rear of both outer rails are attached at the same
distance from the floor, otherwise the switch may fall from the rack.
E66
Warning
Be careful to not drop the switch when lifting and not to pinch your
fingers when inserting the switch into the rack. E67
Warning
Other than maintenance work, secure the switch to the outer rail (via
the adjustment bracket): If the switch is not secured properly, there
is a risk of the switch falling out during movement caused by an
earthquake. E68
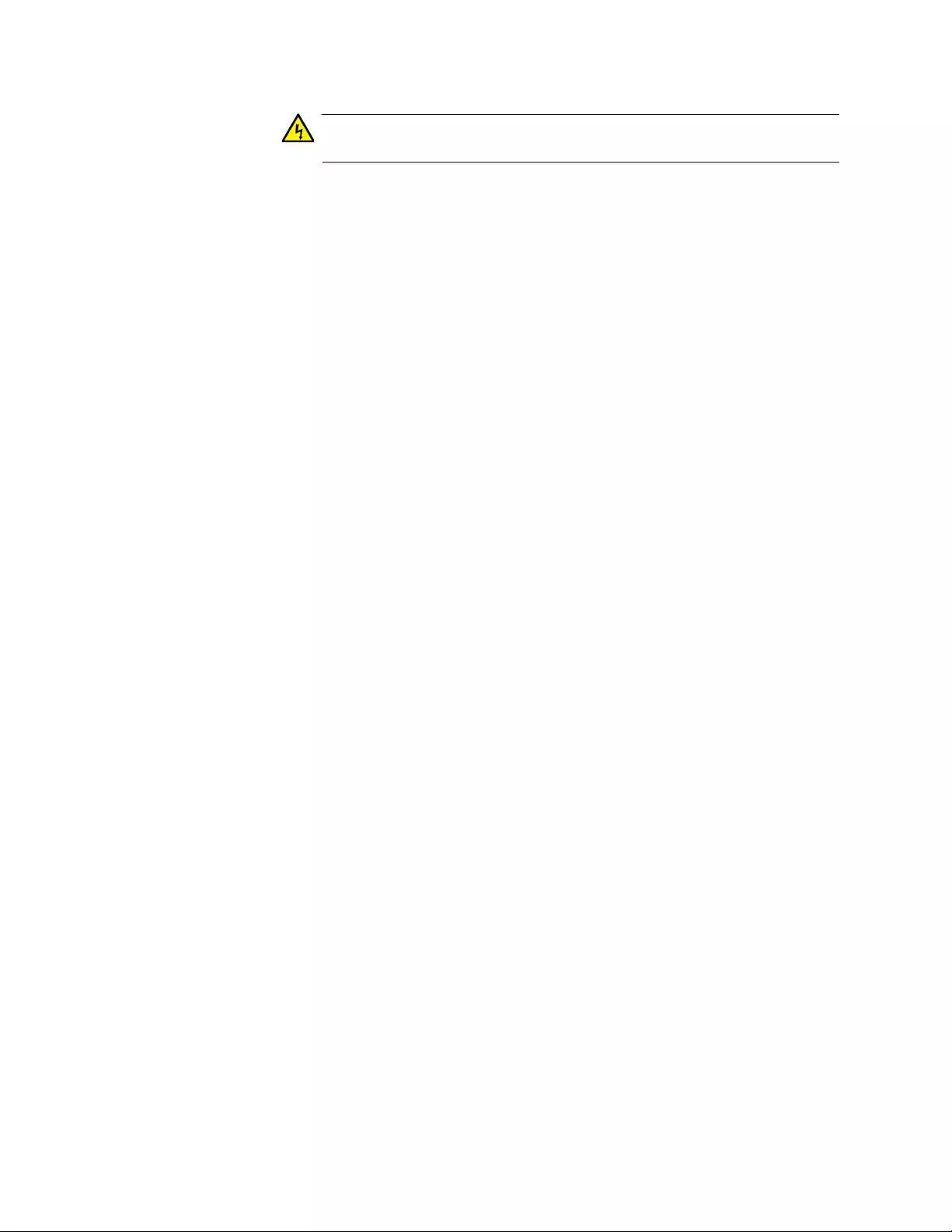
Chapter 9: Installing the Switch in the RKMT-SL01 Sliding Rack
170
Warning
Do not pull the switch out past the front rack posts. E69
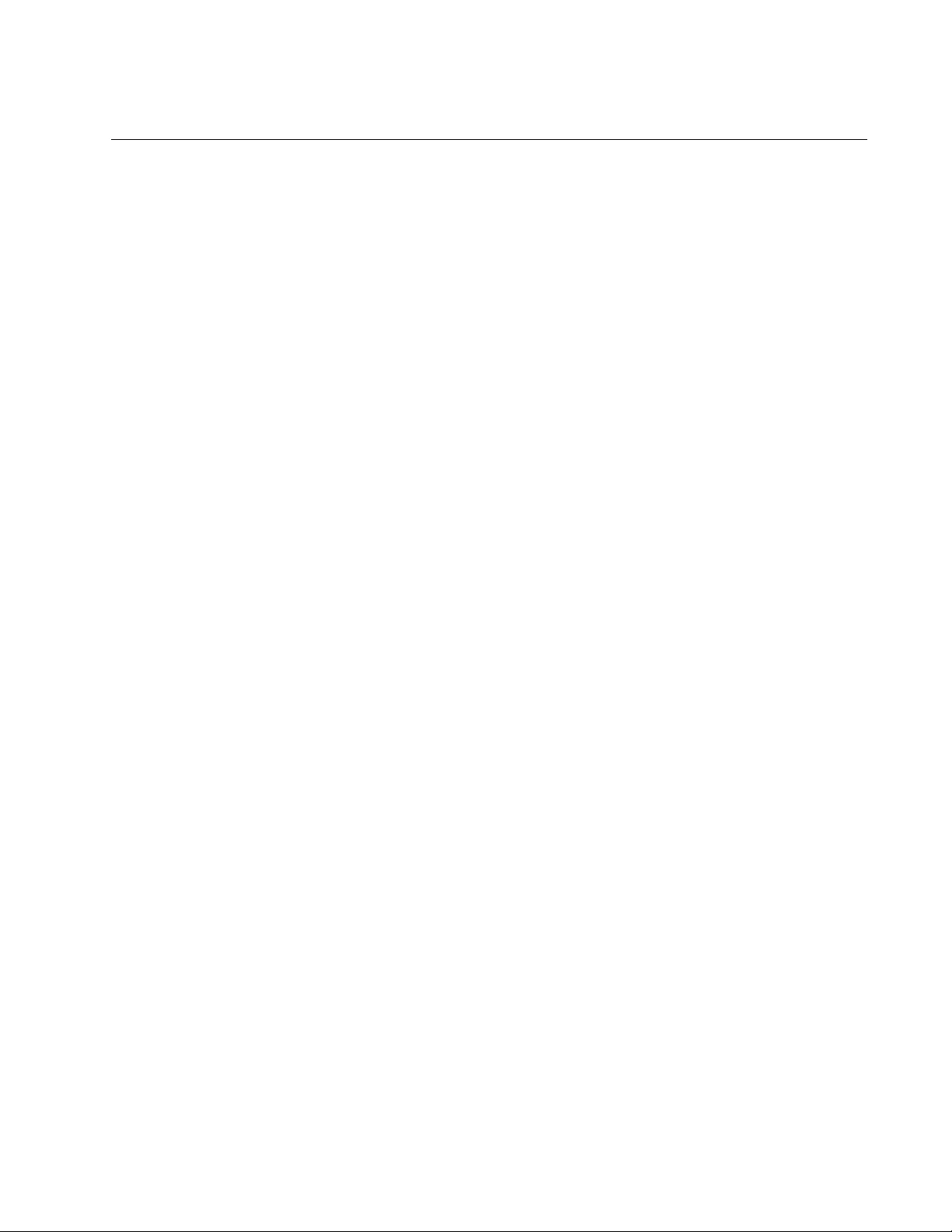
x950 Series Installation Guide for VCStack
171
Installation Overview
The following steps summarize the installation procedure for the RKMT-
SL01 Rack Mount Kit:
1. Verify the contents of the shipping box. Refer to “Unpacking the
Shipping Container” on page 172.
2. Attach the outer rails to the equipment rack. Refer to “Installing the
Outer Rails on the Equipment Rack” on page 174.
3. Determine the lengths of the extension brackets and install the
brackets on the inner rails. Refer to “Installing the Extension Brackets
on the Inner Rails” on page 176.
4. Attach the inner rails to the switch. Refer to “Installing the Inner Rails
on the Switch” on page 182.
5. Slide the switch into the outer rails. Refer to “Installing the Switch in the
Equipment Rack” on page 184.
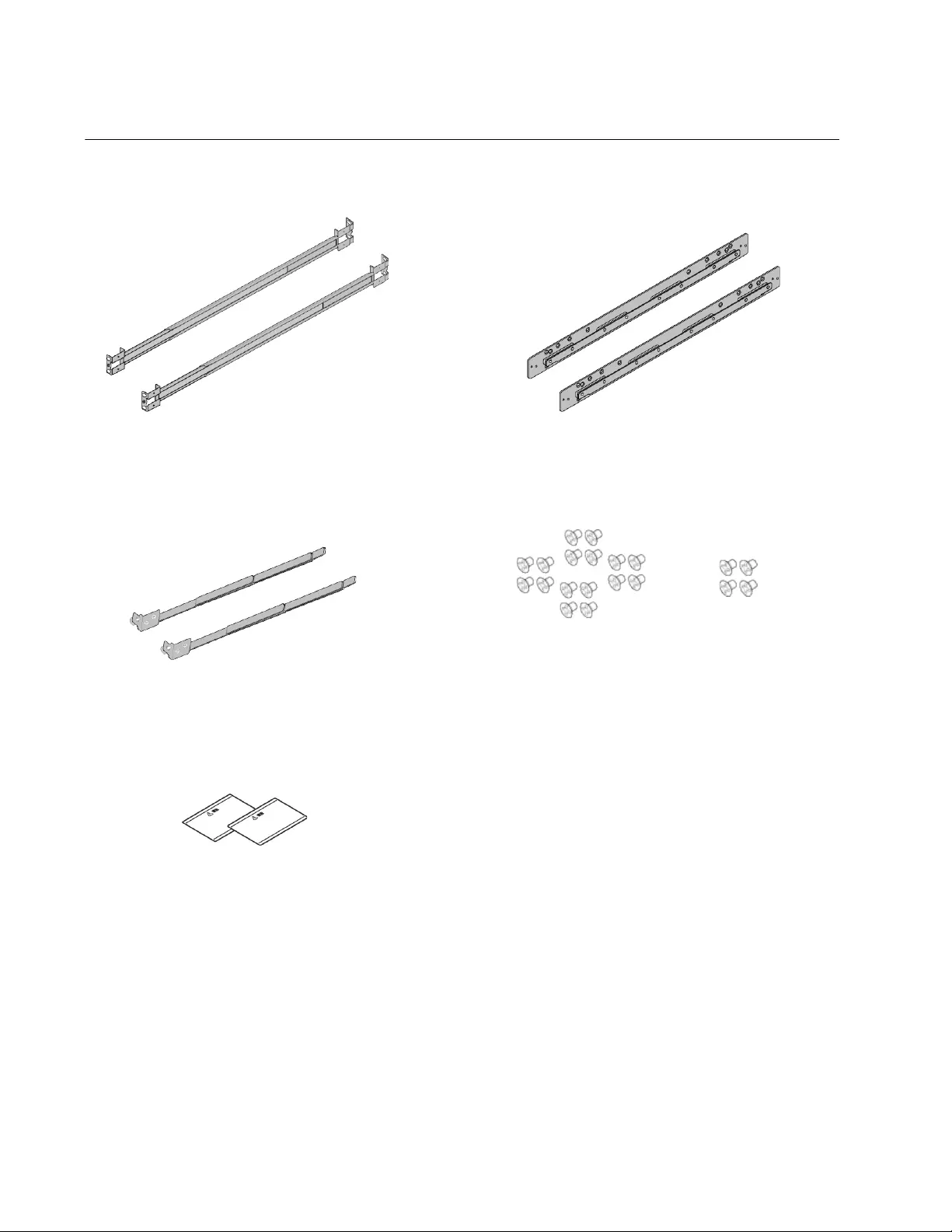
Chapter 9: Installing the Switch in the RKMT-SL01 Sliding Rack
172
Unpacking the Shipping Container
The contents of the shipping container are shown in Figure 99.
Figure 99. Shipping Container Contents
16 inner rail screws (M4 x 8
countersunk) - They attach the inner
rails to the switch. Screw holes and
number of screws vary depending on
the switch.
Four extension bracket screws (M3 x
4 countersunk) - They attach the
extension brackets to the inner rails.
Two outer rails - They attach to the
equipment rack. Their lengths are
adjustable from 600 to 960 mm
(23.6 - 37.8 in).
Two inner rails - They attach to
the sides of the switch.
Two extension brackets - They set
the distance the switch is recessed
in the equipment rack and secure
the switch to the rack.
Two warning labels - They are
affixed to the top and bottom of the
switch and warn against pulling the
switch out past the equipment rack
posts.
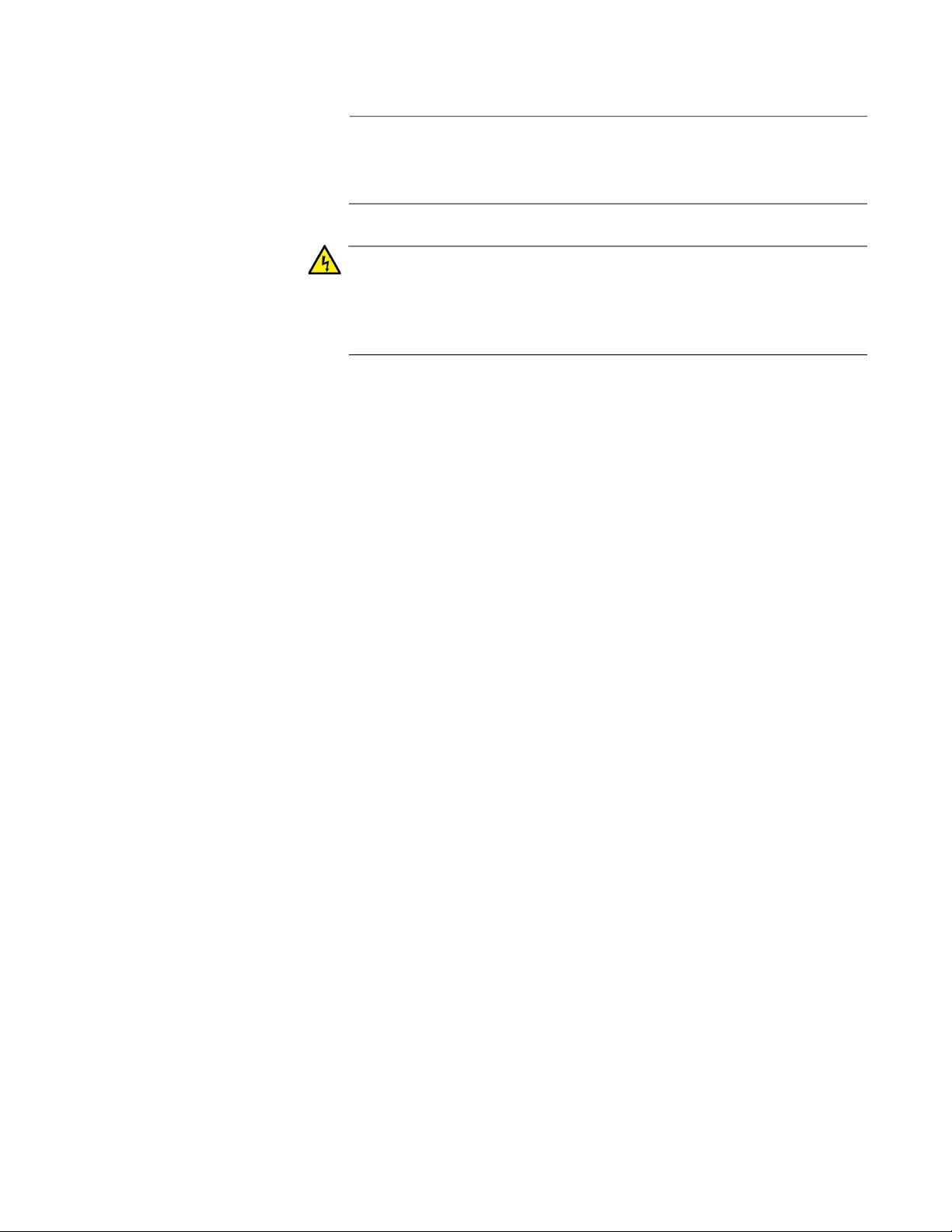
x950 Series Installation Guide for VCStack
173
Note
Store the packaging material in a safe location. You should use the
original shipping material if you need to return the kit to Allied
Telesis.
Warning
When installing the outer and inner rails, and extension brackets,
ensure the components are securely attached with the appropriate
screws. If not securely attached, a serious accident may occur due
to falling equipment. E63

Chapter 9: Installing the Switch in the RKMT-SL01 Sliding Rack
174
Installing the Outer Rails on the Equipment Rack
To install the outer rails to the equipment rack, perform the following
procedure.
1. Locate the FRONT and REAR labels on the sides of the rails. You
have to install the rails with the FRONT labels at the front of the
equipment rack and the REAR Labels at the back. Refer to Figure 100.
Figure 100. FRONT and REAR Labels on the Outer Rails
2. Attach the outer rails to the equipment rack using the supplied screws.
Use four screws per rail. Refer to Figure 101 on page 175. Installing
the switch can be easier if you leave the screws slightly loosened now
and fully tightened them after the switch is installed.
Warning
Built-in stoppers prevent the outer rails from extending beyond their
maximum length of 960 mm (37.8 in). Do not force the rails beyond
the maximum length. Otherwise, the brackets will be weakened, and
the switch may fall from the rack and be damaged. E65
Warning
Verify that the front and rear of both outer rails are attached at the
same distance from the floor, otherwise the switch may fall from the
rack. E66
3. Go to “Installing the Extension Brackets on the Inner Rails” on
page 176.
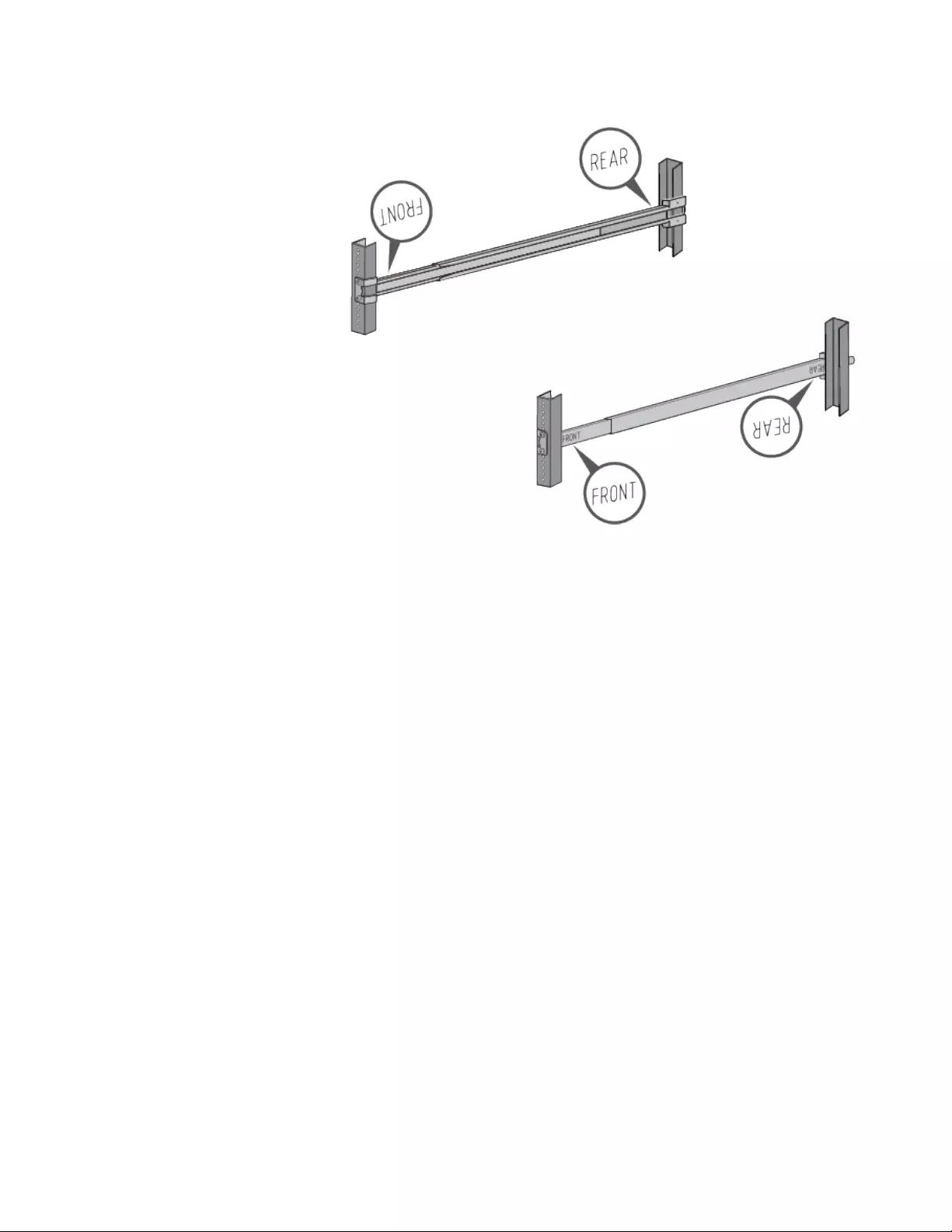
x950 Series Installation Guide for VCStack
175
Figure 101. Installing the Outer Rails on the Equipment Rack
Front of
Equipment Rack
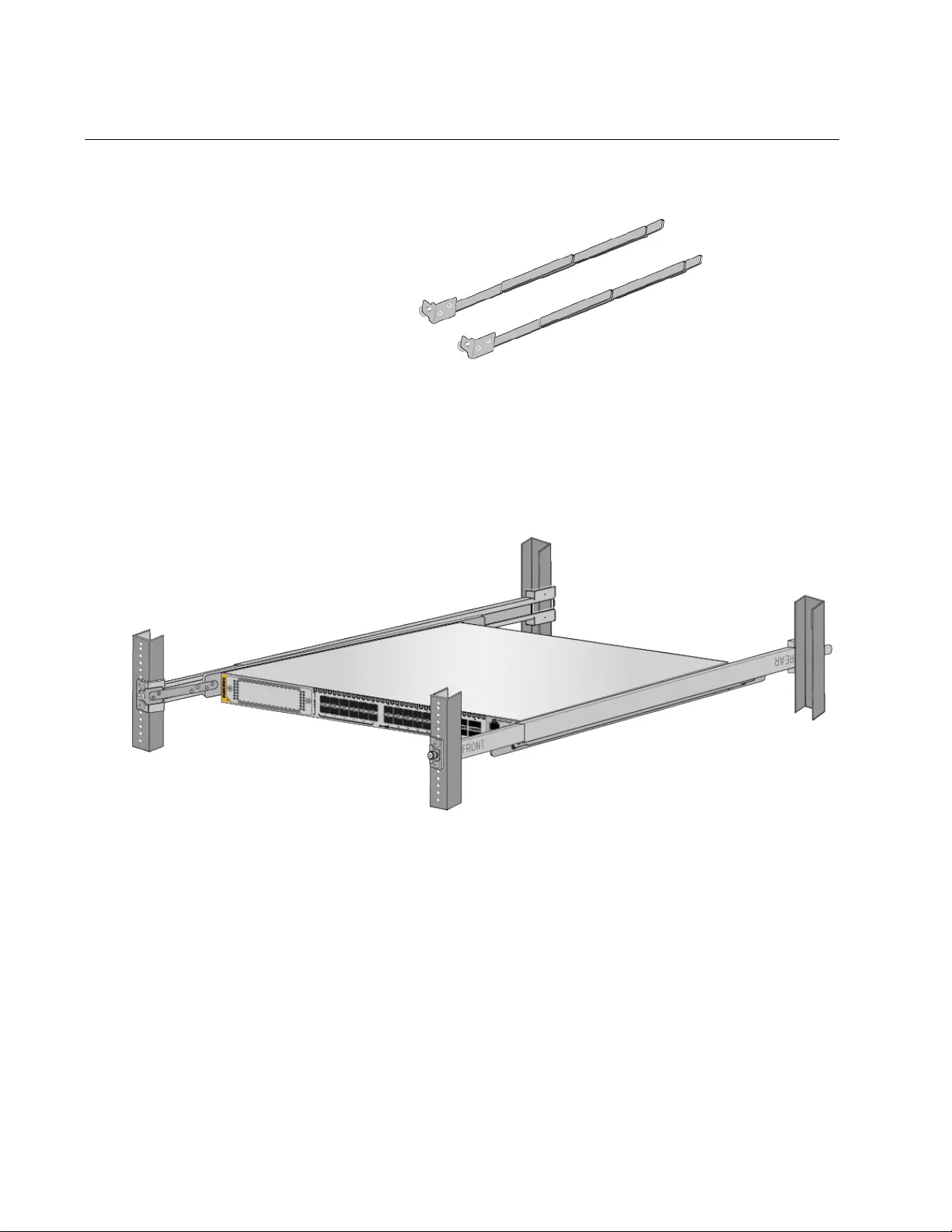
Chapter 9: Installing the Switch in the RKMT-SL01 Sliding Rack
176
Installing the Extension Brackets on the Inner Rails
The kit comes with two extension brackets. Refer to Figure 102.
Figure 102. Extension Brackets
You use the brackets to recess the switch in the equipment rack. The
maximum distance will depend on the depth of the rack. The deeper the
equipment rack, the more the switch can be recessed. The range is
approximately 40mm (1.6 in.) to 453mm (17.8 in.). Figure 103 is an
example.
Figure 103. Example of a Switch Recessed in an Equipment Rack
Measuring the
Extension
Bracket Lengths
The first step is to decide how much you want to recess the front panel of
the switch in the rack and then measure the distance. That will tell you the
approximate lengths of the extension brackets. Perform the following
procedure:
1. Slide one of the inner rails into an outer rail. Be sure that the UP arrow
on the inner rail is pointing up. Refer to Figure 104 on page 177.
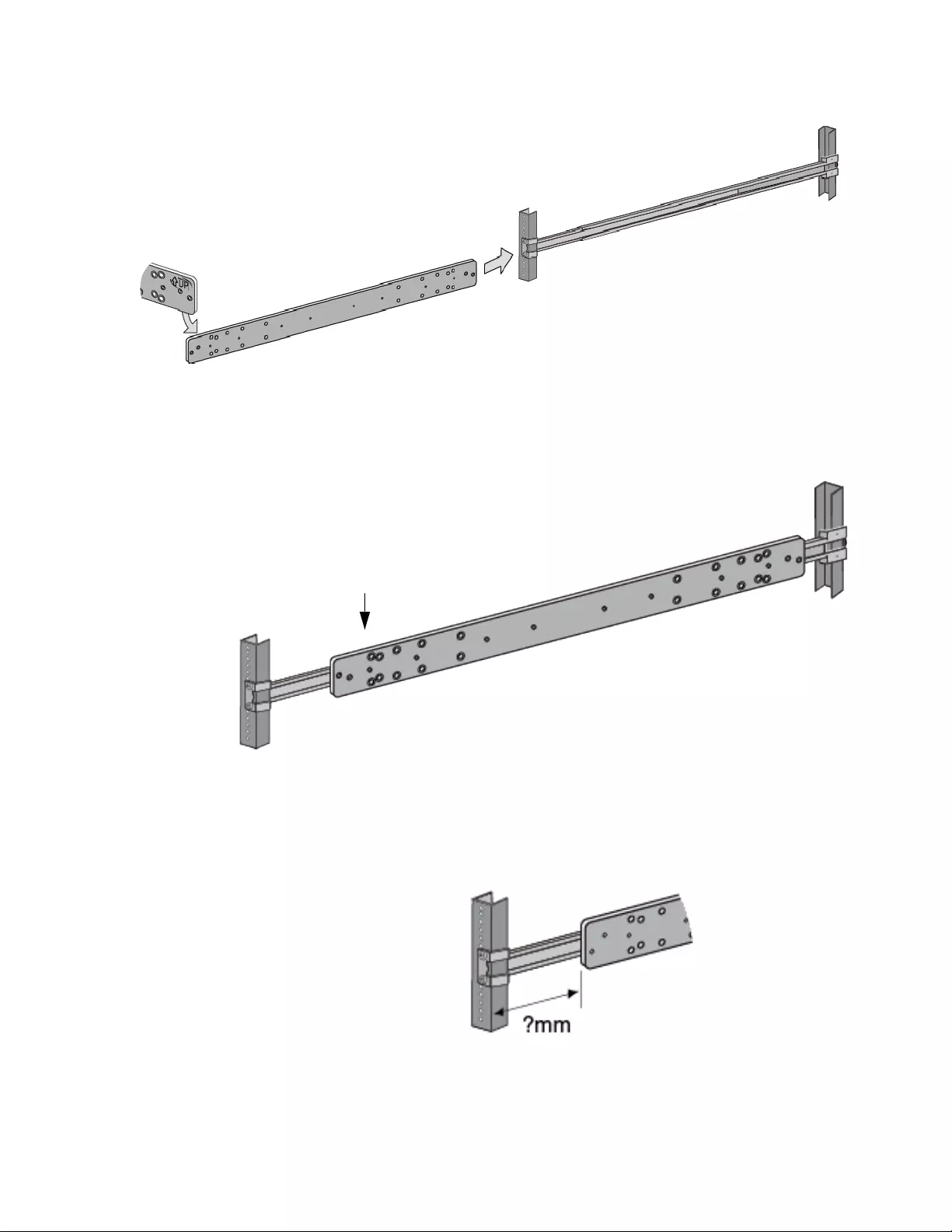
x950 Series Installation Guide for VCStack
177
Figure 104. Inserting an Inner Rail into an Outer Rail
2. Position the inner rail at the planned location for the front panel of
switch in the sliding rack. Refer to Figure 105.
Figure 105. Example of Positioning the Inner Rail
3. Measure the distance from the front of the equipment rack to the front
of the inner rail. This will be the approximate length of the extension
brackets. Refer to Figure 106.
Figure 106. Measuring for the Extension Brackets
Location of Front
Panel of Switch
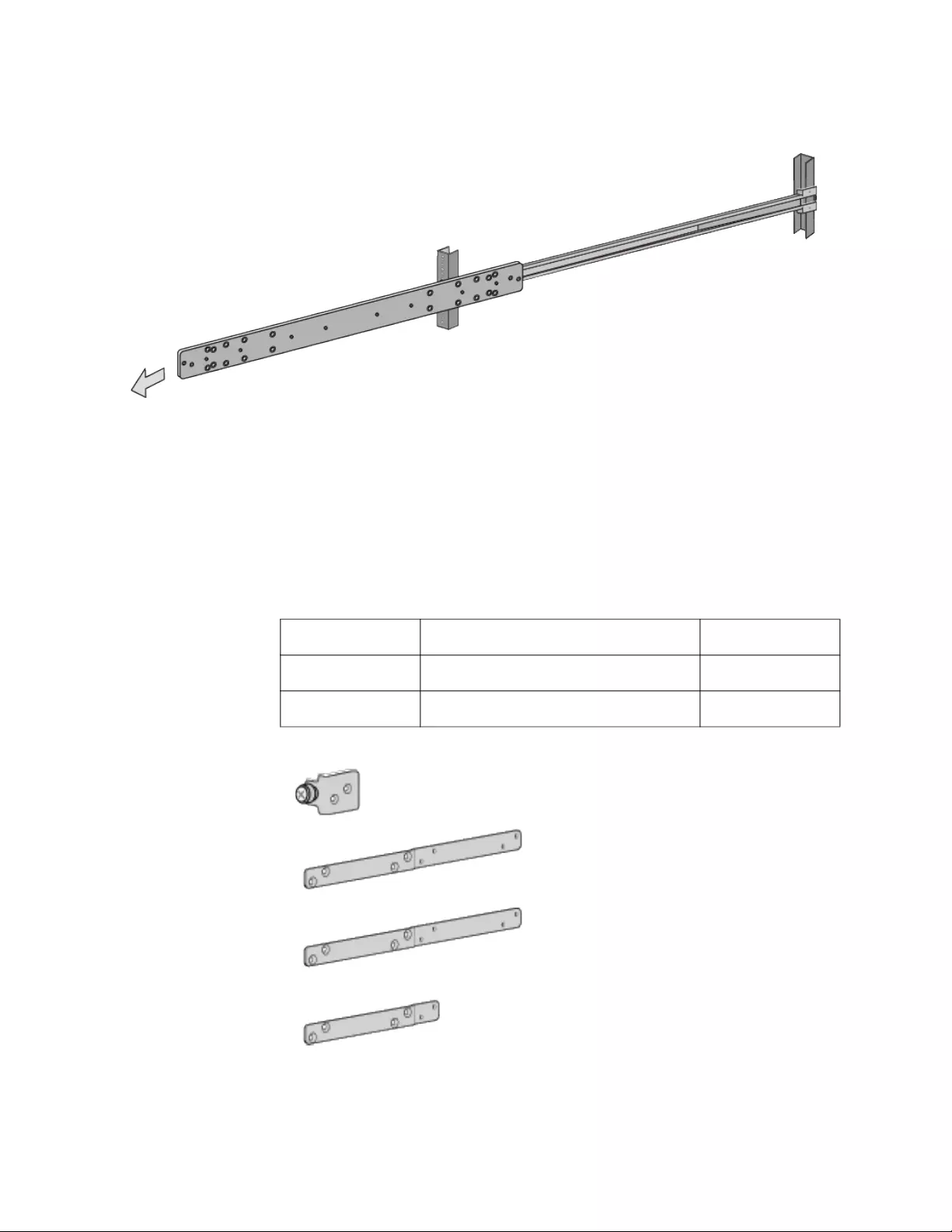
Chapter 9: Installing the Switch in the RKMT-SL01 Sliding Rack
178
4. Remove the inner rail from the outer rail. Refer to Figure 107.
Figure 107. Removing the Inner Rail
5. Go to “Assembling the Extension Brackets,” next.
Assembling the
Extension
Brackets
Now that you know the approximate length for the extension brackets, you
are ready to assemble them. The brackets consist of four parts. Refer to
Table 31 and Figure 108.
Figure 108. Extension Bracket Parts
Table 31. Extension Bracket Parts
AFixed Bracket 1 ea
BLong Extension Brackets 2 ea
CShort Extension Bracket 1 ea
A - Fixed Bracket
B - Long Extension Bracket
B - Long Extension Bracket
C - Short Extension Bracket
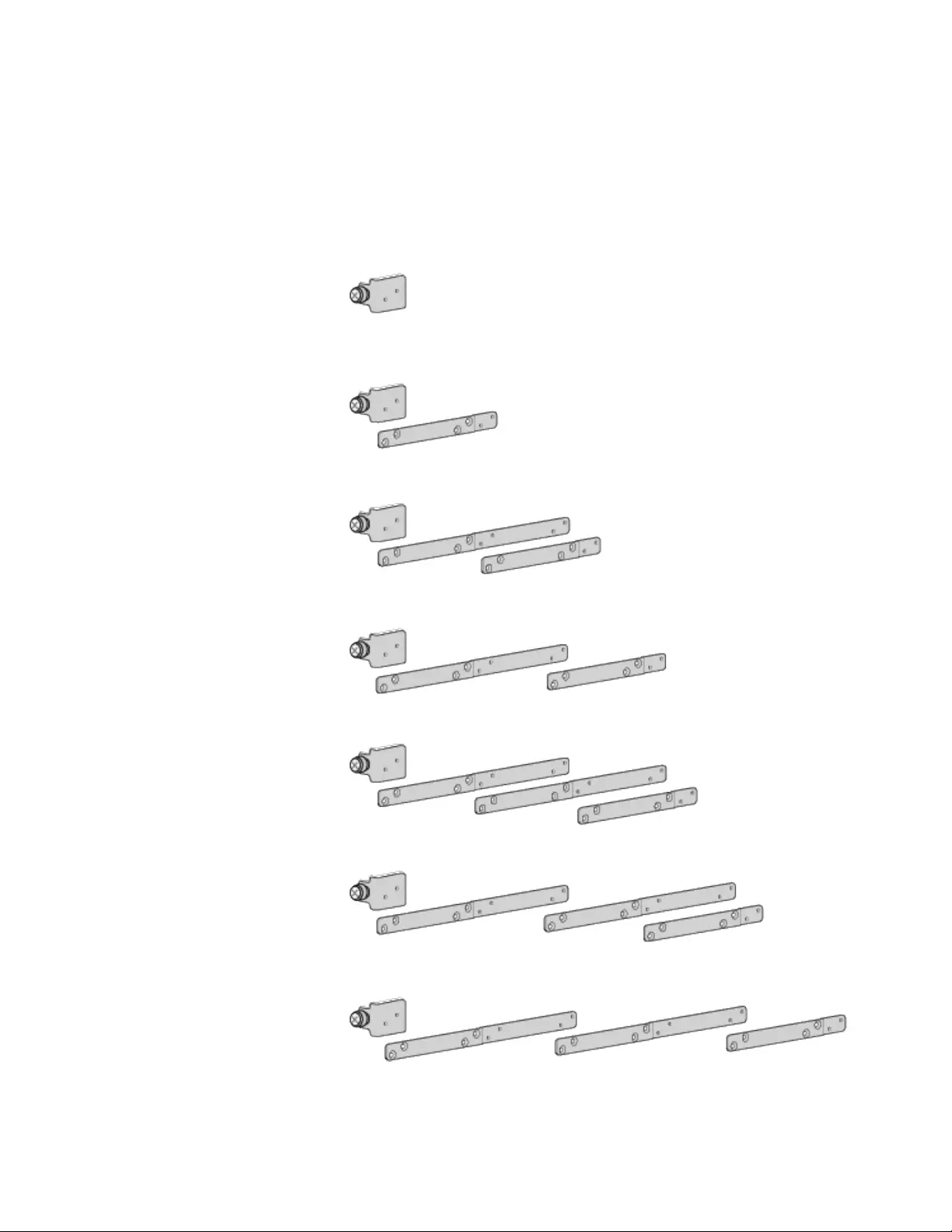
x950 Series Installation Guide for VCStack
179
You adjust the lengths of the brackets by connecting them in different
combinations. There are seven possible configurations. Refer to
Figure 109. The default configuration is number 5. To adjust the extension
brackets, perform the following procedure:
1. Review Figure 109 to find the bracket length that most closely matches
the measurement taken in step 3 in the previous procedure.
Figure 109. Extension Bracket Configurations
#1
#2
Length:101mm (3.8 in.)
#3
Length:202mm (8.0 in.)
#4
Length:277mm (10.9 in.)
#5
Length:303mm (11.9 in.)
(Factory default)
#6
Length:378mm (14.9 in.)
#7
Length:453mm (17.8 in.)
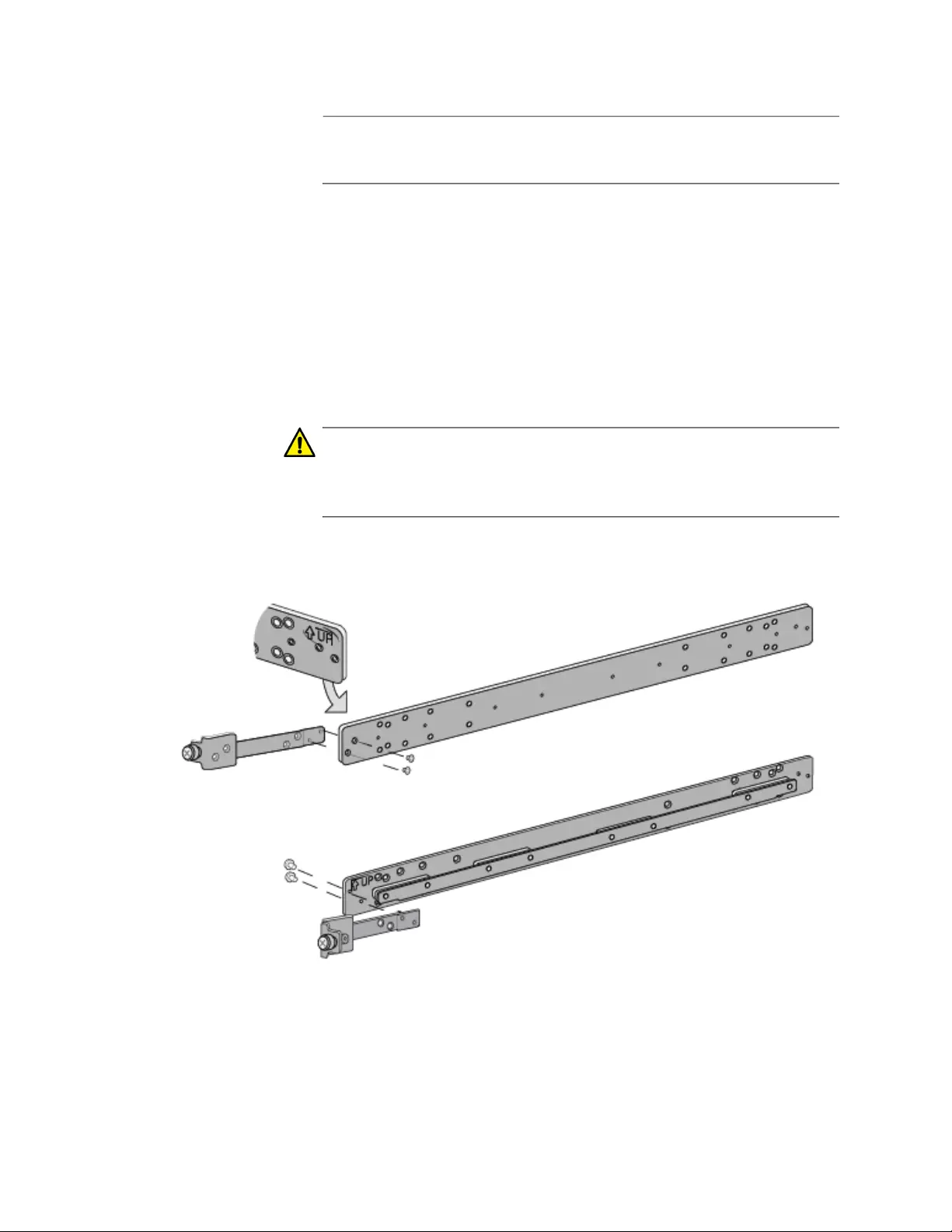
Chapter 9: Installing the Switch in the RKMT-SL01 Sliding Rack
180
Note
The long brackets have to be used between the fixed and short
brackets. You cannot connect them directly to the inner rails.
2. Assemble the extension brackets to match the selected length in the
table.
3. Attach the extension brackets to the inner rails. Observe the following:
Attach the brackets to the sides of the inner rails with the UP
arrows.
Attach the screws through the holes on the sides opposite the
sides with the UP arrows.
Caution
Use the extension bracket screws supplied with the inner rail. Using
screws other than those supplied may result in equipment damage.
E62
Figure 110 on page 180 shows an example.
Figure 110. Example of Attaching the Extension Brackets to the Inner
Rails
4. To test the lengths of the extension brackets, slide the inner rails into
the outer rails in the equipment rack. Refer to Figure 111.
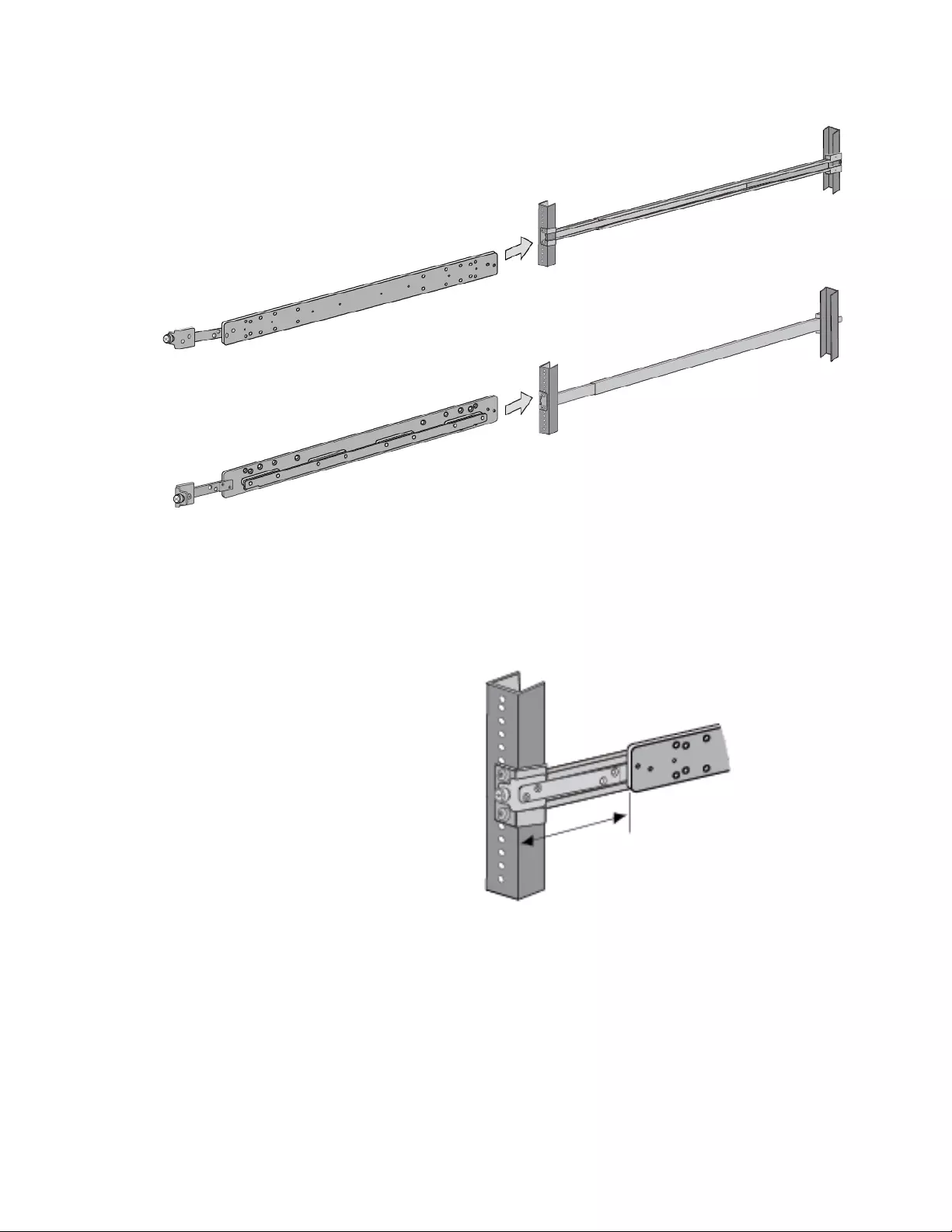
x950 Series Installation Guide for VCStack
181
Figure 111. Testing the Inner Rails with the Extension Brackets
5. Measure the distance from the front of the equipment rack to the front
of the inner rail. Refer to Figure 112. This should approximately match
the value you measured in “Measuring the Extension Bracket Lengths”
on page 176.
Figure 112. Verifying the Length of the Extension Bracket
6. If the extension brackets are the correct length, remove the inner
brackets from the outer brackets and go to “Installing the Inner Rails on
the Switch” on page 182.
7. If the brackets are not the correct length, repeat this procedure.
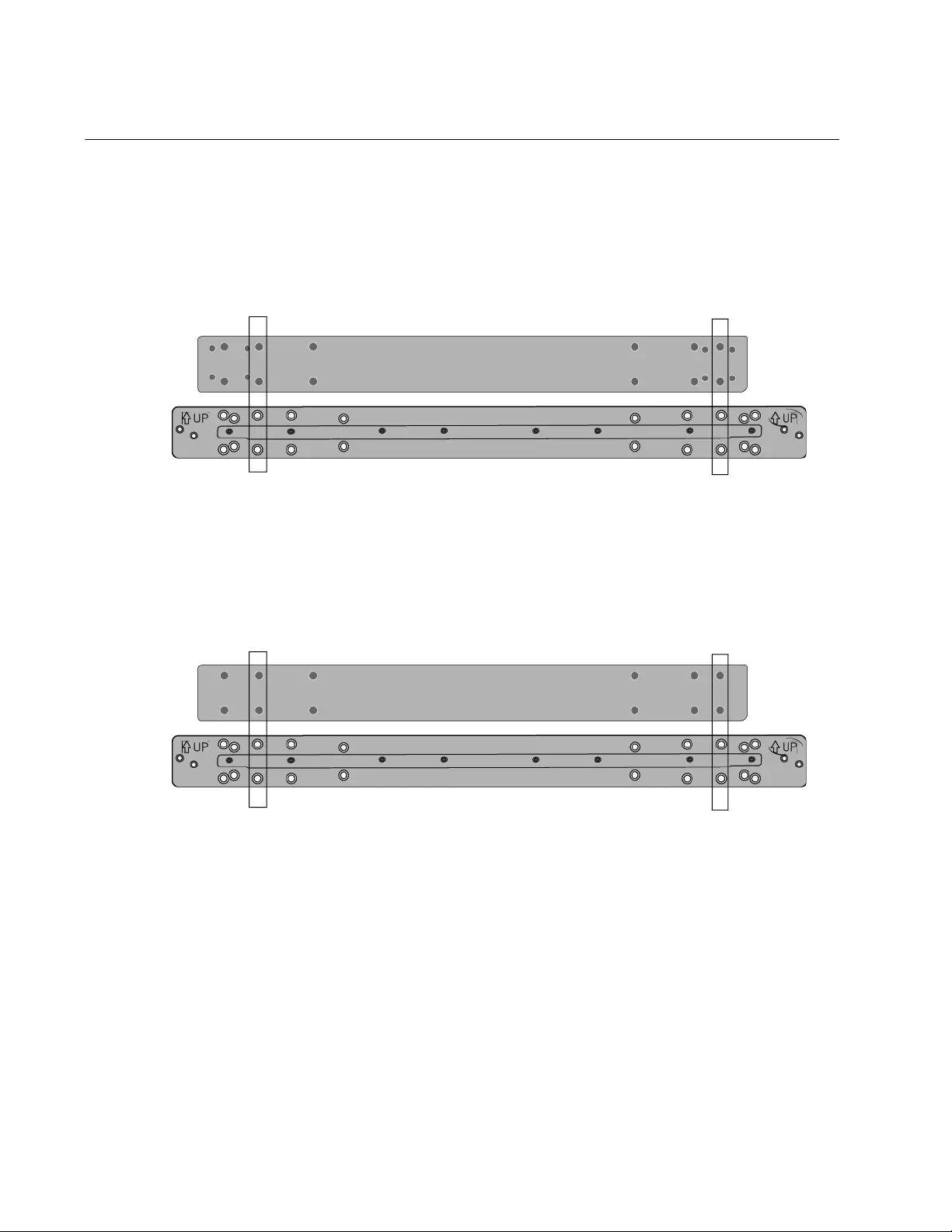
Chapter 9: Installing the Switch in the RKMT-SL01 Sliding Rack
182
Installing the Inner Rails on the Switch
The sides of the x950-28XSQ and x950-28XTQm switches have two sets
of bracket screw holes. The smaller M3 holes are for the standard
brackets that come with the switch and the larger M4 screw holes are for
the inner rails of the RKMT-SL01 sliding rack. The inner rails are attached
to the switch with four M4 screws on each side. Figure 113 identifies the
respective screw holes on the sides of the switch and inner rails.
Figure 113. Inner Rail Screw Holes for the x950-28XSQ and x950-
28XTQm Switches
The x950-52XSQ switch has only M4 holes on its two sides. The holes are
used for both the standard brackets included with the device and the rails
for the sliding equipment rack. Figure 114 identifies the screw holes for
attaching the inner rails to the switch.
Figure 114. Inner Rail Screw Holes for the x950 Switch
Attach the inner rails to the switch using eight M4 screws included with the
sliding rack. Be sure that the UP arrows on the rails are pointing up and
that the extension brackets extend in front of the switch. Refer to Figure
115 on page 183.
Front of
Switch
Front of
Switch
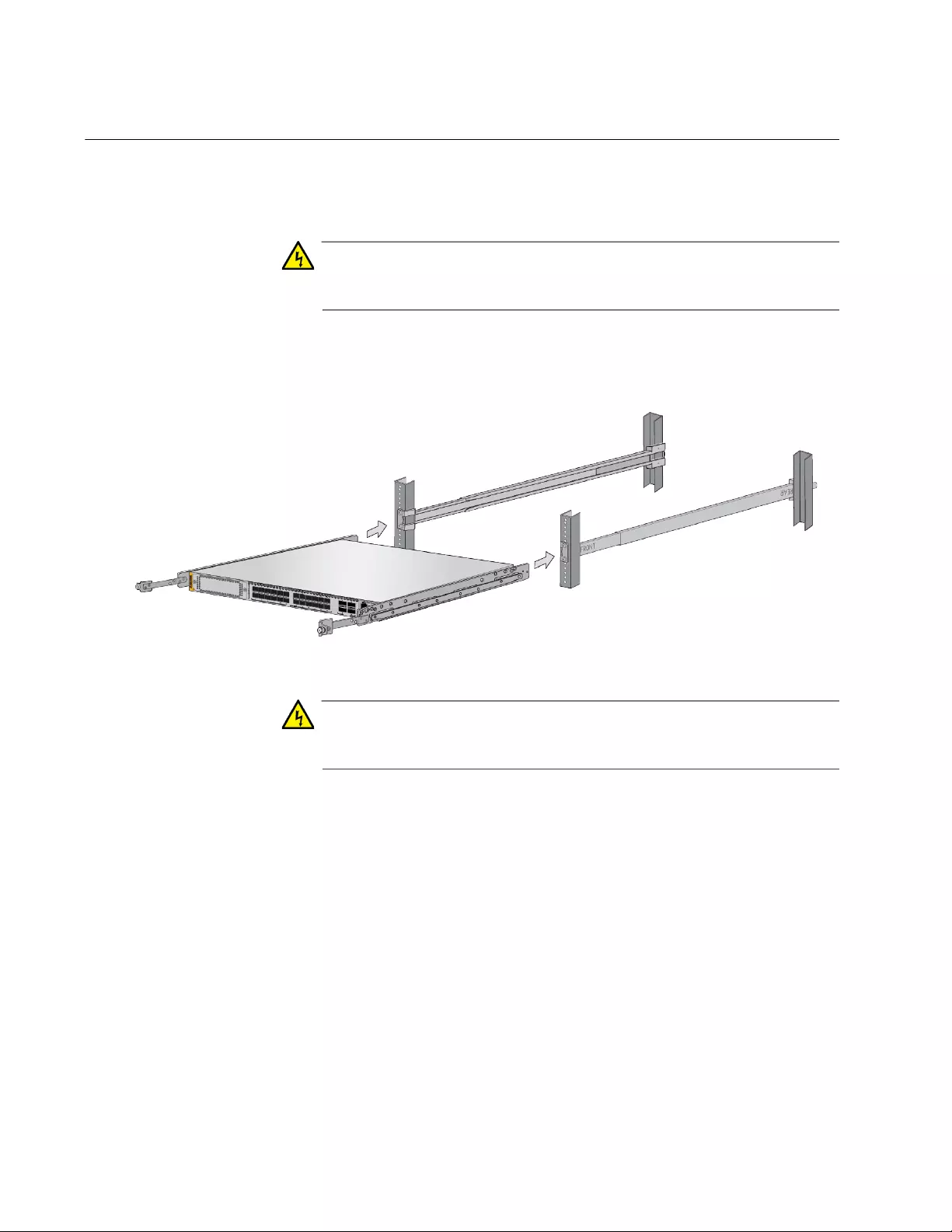
Chapter 9: Installing the Switch in the RKMT-SL01 Sliding Rack
184
Installing the Switch in the Equipment Rack
After attaching the inner rails and extension brackets to the switch,
perform the following procedure to install the switch in the sliding rack:
Warning
When installing or removing the switch from the rack, disconnect the
media and power cables. E64
1. Install the switch in the sliding rack by sliding the inner rails into the
outer rail grooves. Refer to Figure 116.
Figure 116. Sliding the Inner Rails on the Switch into the Outer Rails
Warning
Be careful to not drop the switch or pinch your fingers when inserting
it into the sliding rack. E67
2. Affix the provided warning labels to the top and bottom of the switch, in
locations immediately visible when removing the device from the rack.
Refer to Figure 117 on page 185.
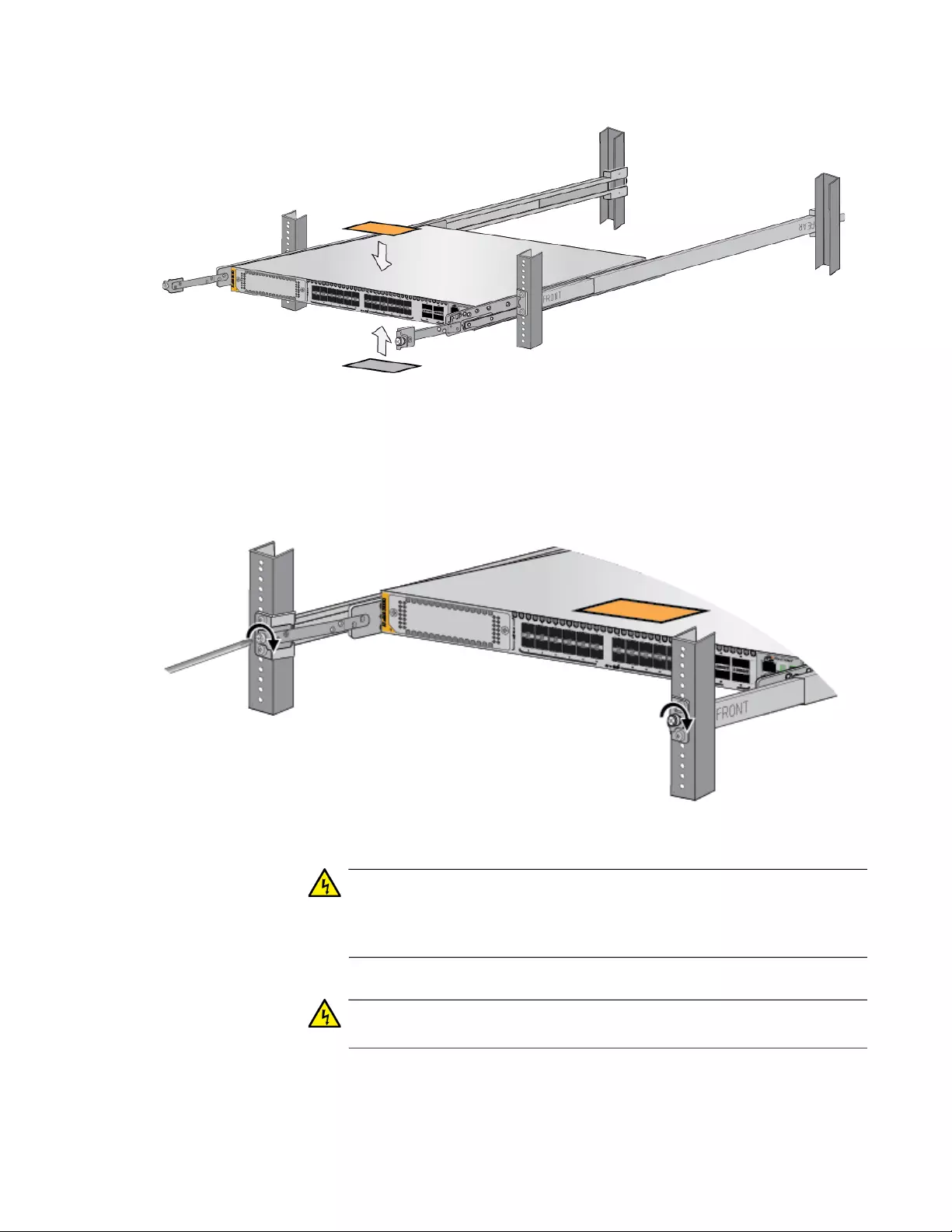
x950 Series Installation Guide for VCStack
185
Figure 117. Affixing the Warning Labels
3. Slide the switch fully into the rack.
4. Tighten the two screws on the fixed brackets to secure the switch to
the equipment rack. Refer to Figure 118.
Figure 118. Tightening the Two Screws on the Fixed Brackets
Warning
Always be sure to secure the switch to the outer rail (via the
adjustment bracket). If the switch is not secured properly, there is a
risk of it falling out during an earthquake. E68
Warning
Do not pull the switch out past the front rack posts. E69
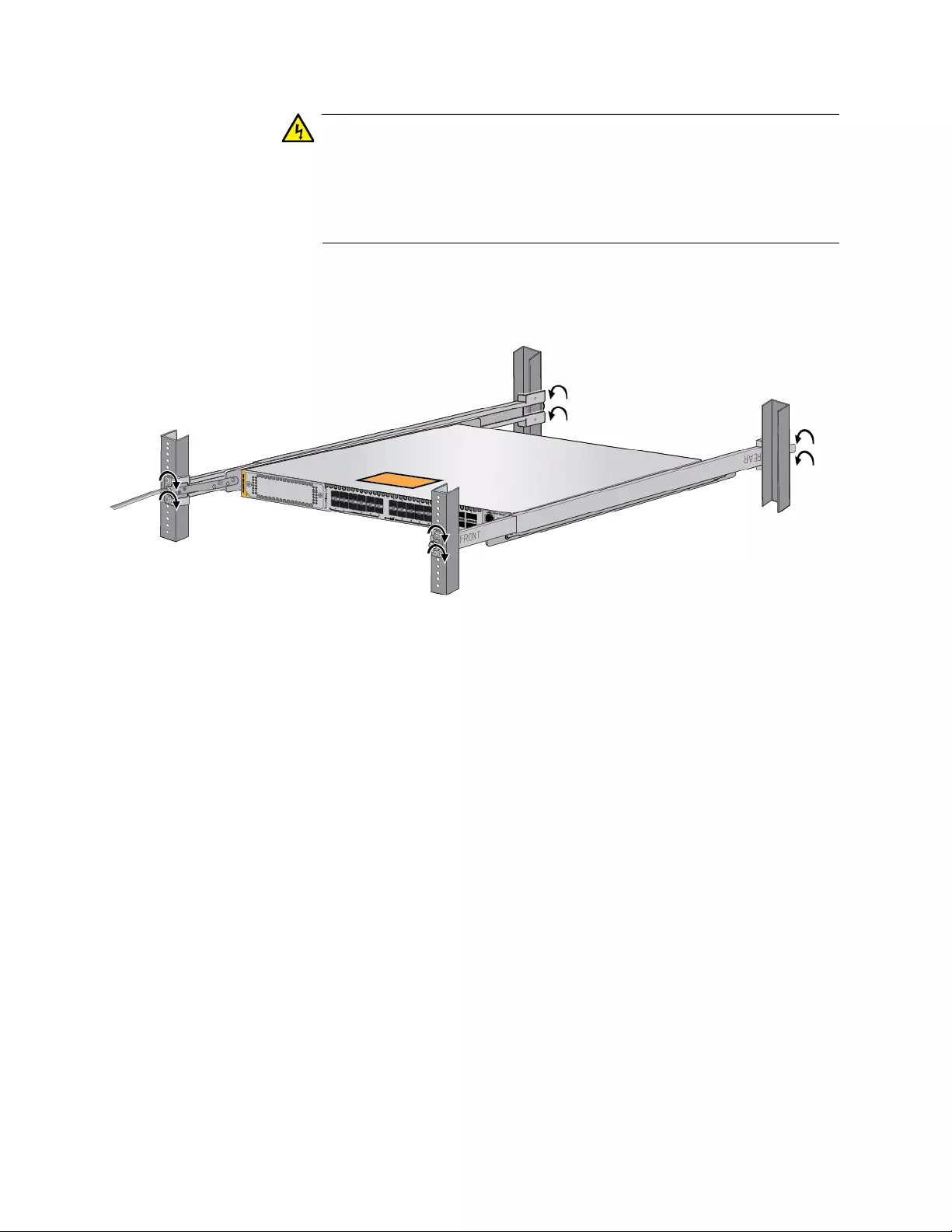
Chapter 9: Installing the Switch in the RKMT-SL01 Sliding Rack
186
Warning
Pull the switch out slowly if you must remove it from the rack for
maintenance. If you pull the switch out past the front of the rack
posts, or if you pull it out too quickly, there is a risk that the weight of
the switch will cause the sliding rail assemblies to fail and cause the
switch to fall out. E59
5. Finish tightening the eight screws on the outer rails to secure the rails
to the equipment rack. See Figure 119.
Figure 119. Tightening the Screws on the Outer Rails
This completes the installation procedure.
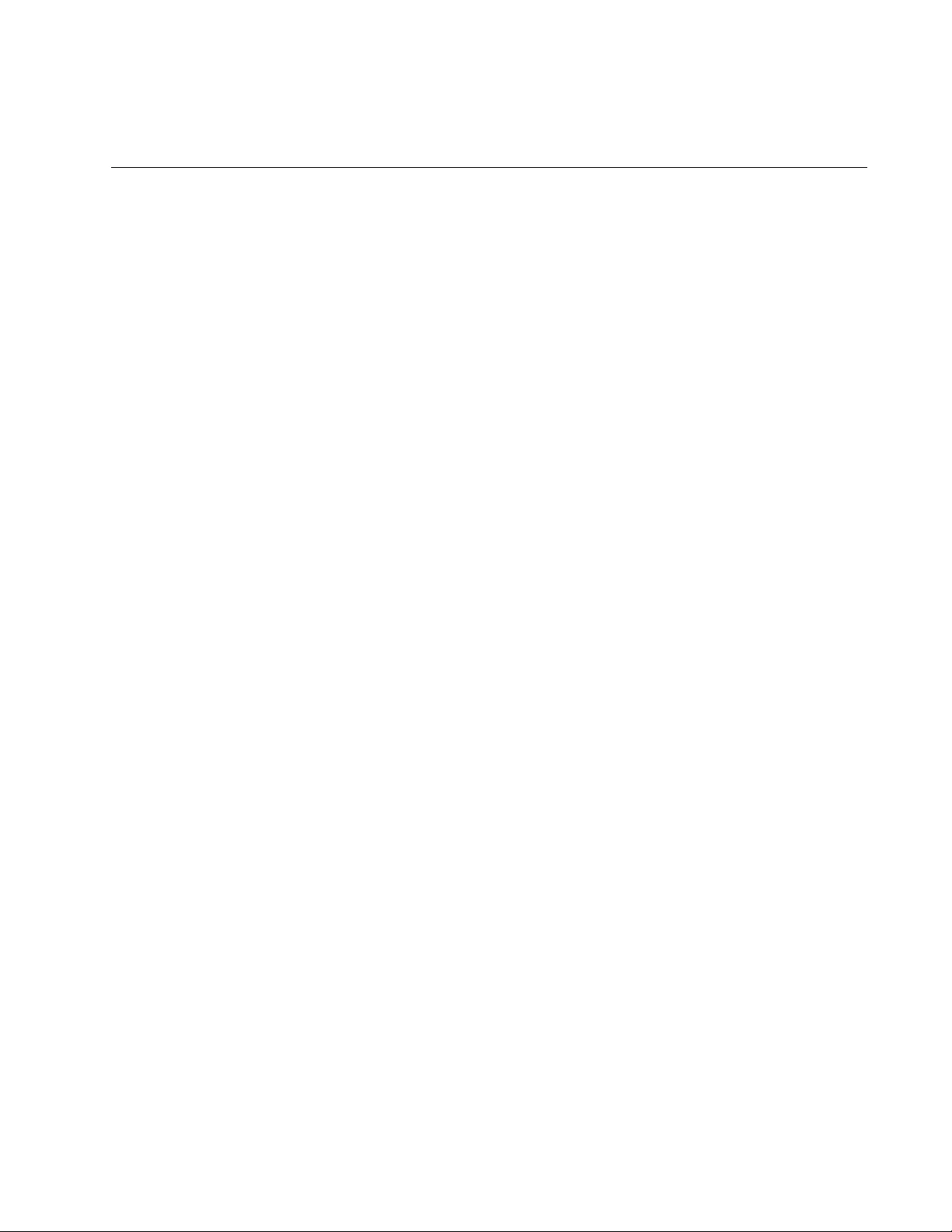
187
Chapter 10
Configuring the Master Switch
This chapter contains the following sections:
“Command Summary” on page 188
“Powering On a Switch” on page 192
“Starting a Local Management Session” on page 196
“General Steps for the Master Switch” on page 198
“Configuring the Master Switch - Part I” on page 200
“Configuring the Master Switch - Part II” on page 203
“Verifying the Master Switch” on page 206
“What to Do Next” on page 208
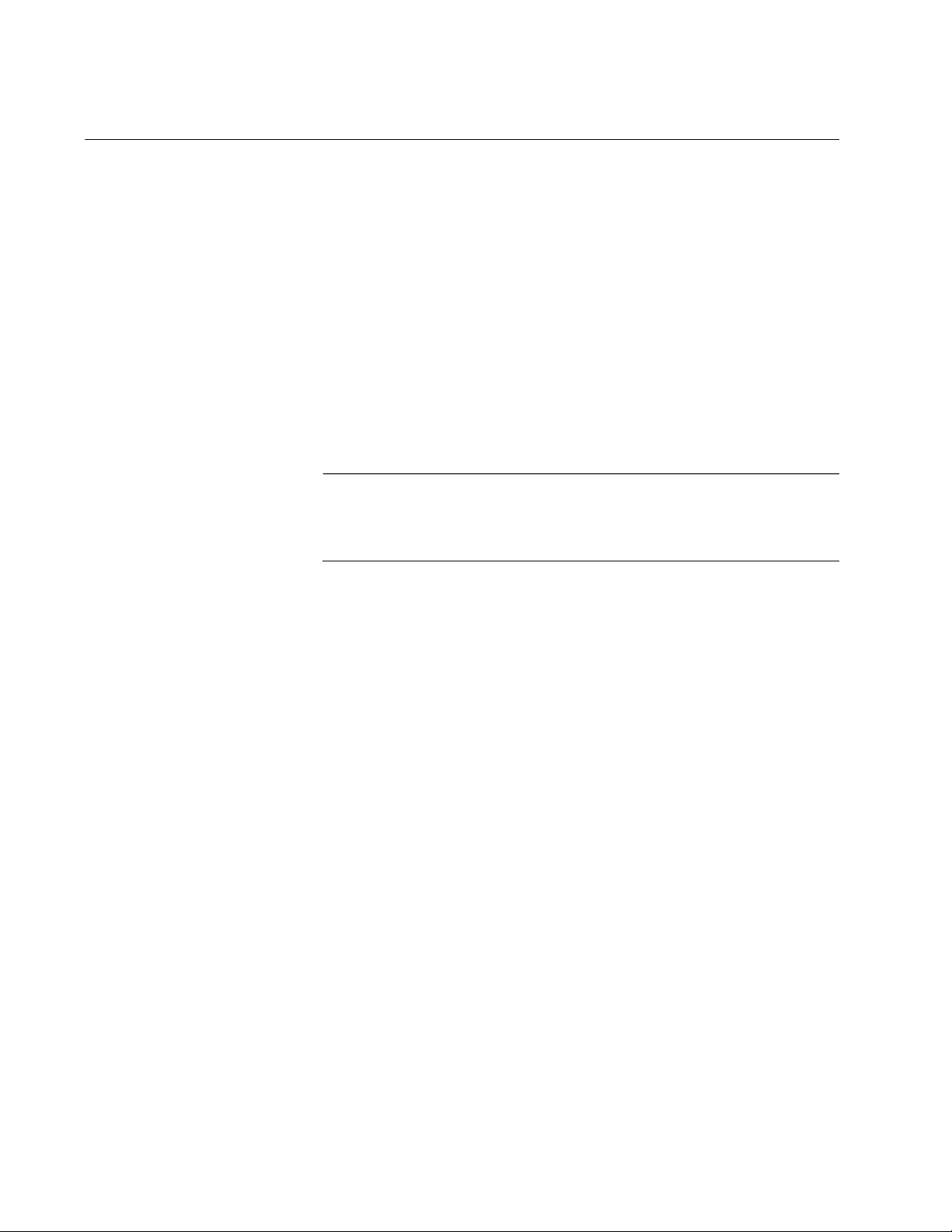
Chapter 10: Configuring the Master Switch
188
Command Summary
The following sections briefly describe the commands for configuring the
master and member switches for stacking. For further instructions, refer to
the Software Reference for x950 Switch, AlliedWare Plus Operating
System. After reviewing the commands, go to “General Steps for the
Master Switch” on page 198 to begin the configuration procedures.
PLATFORM
PORTMODE
INTERFACE
This command is used to configure ports 25, 29, 33, 37 on the
x950-28XSQ and x950-28XTQm switches and port 49, 53, 57, 61 on the
x950-52XSQ switch for the following types of transceivers and cables:
40Gbps QSFP+ transceivers
100Gbps QSFP28 transceivers
40Gbps to 10Gbps breakout cables
Note
You must reset the switch after designating ports for 100Gbps
transceivers or after replacing 100Gbps transceivers with 40Gbps
transceivers or breakout cables.
Allied Telesis recommends configuring these ports during the initial
configuration procedure even if they will not be used for the stack trunk.
The command format is shown here:
platform portmode interface ports 40g|100g|10gx4
The variables are defined here:
The PORTS variable specifies the ports to be configured. The
values are PORTn.0.25, PORTn.0.29, PORTn.0.33, PORTn.0.37,
PORTn.0.49, PORTn.0.53, PORTn.0.57, and PORTn.0.61. The
“n” variable is the switch’s ID. You can configure more than one
port at a time.
The “40g” parameter configures ports for 40Gbps QSFP+
transceivers. This is the default setting.
The “100g” parameter configures ports for 100Gbps QSFP28
transceivers.
The “10gx4” parameter configures ports for 10Gbps breakout
cables.
This example configures ports 33 and 37 for 100Gbps QSFP28
transceivers:
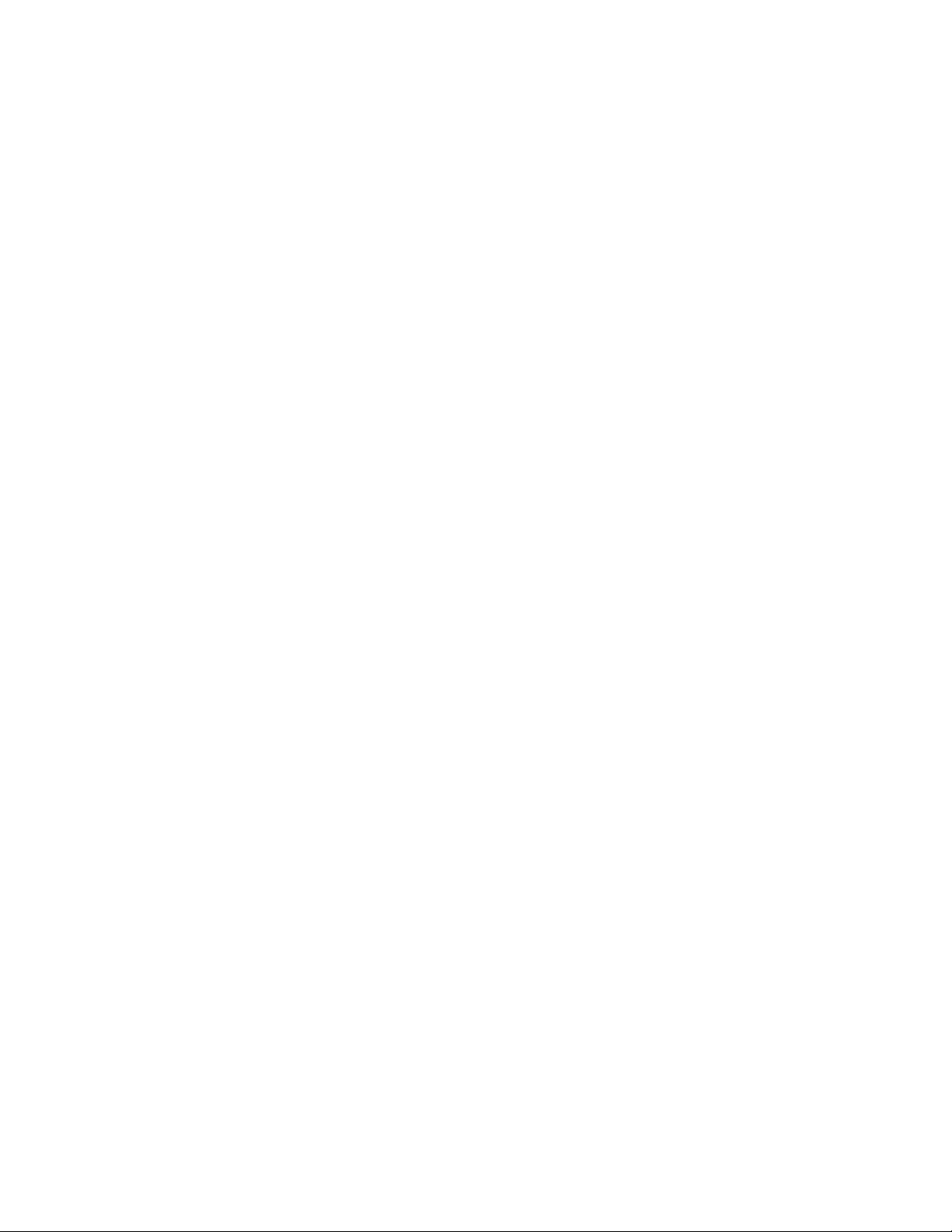
x950 Series Installation Guide for VCStack
189
awplus(config)# platform portmode interface
port1.0.33,port1.0.37 100g
This example configures port 25 for a breakout cable:
awplus(config)# platform portmode interface port1.0.25
10gx4
This example restores the default settings for ports 49 and 53 to 40Gbps
QSFP+ transceivers:
awplus(config)# platform portmode interface
port1.0.49,port1.0.53 40g
For background information on port numbering, refer to “Designating Ports
in the Command Line Interface” on page 46.
STACKPORT You use this command to designate the ports of the stack trunk. The
command has to be performed after you have enabled the stacking feature
with the STACK ENABLE command. Additionally, it has to be performed
from the Interface mode of the selected ports. In this example, ports 1 to 4
on the switch are designated as ports of the stack trunk:
awplus(config)# interface port1.0.1-1.0.4
awplus(config-if)# stackport
The command for removing the stacking function from ports is the NO
STACKPORT command. You might perform the command if you assign
the stacking function to the wrong ports or decide to change the trunk
ports. Like the STACKPORT command, it has to be performed from the
Interface mode, This example removes the stacking function from ports 6
and 8:
awplus(config)# interface port1.0.6,port1.0.8
awplus(config-if)# no stackport
As explained in “Designating Ports in the Command Line Interface” on
page 46, you need to adjust the PORT parameter depending on the ID
number of the switch. This example designates ports 33 and 37 as the
trunk ports on a switch with the ID number 2:
awplus(config)# interface port2.0.33,port2.0.37
awplus(config-if)# stackport
STACK
ENABLE
This command, which is located in the Global Configuration mode, is used
to activate the VCStack feature. Activating the VCStack feature requires
resetting the switch. You must perform this command before designating
the ports of the stack trunk with the STACKPORT command. Here is the
command:
awplus(config)# stack enable
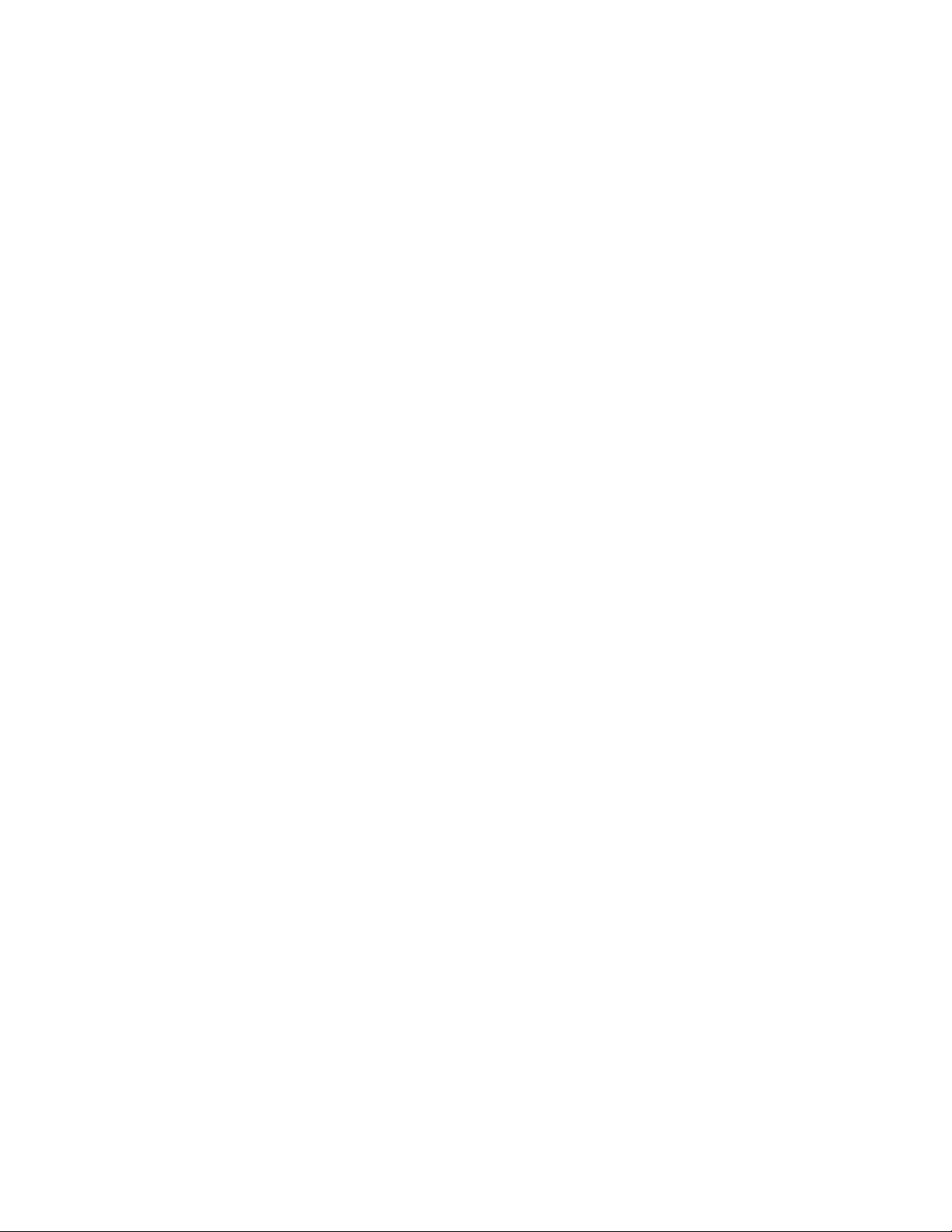
Chapter 10: Configuring the Master Switch
190
STACK
PRIORITY
This command is used to assign priority numbers to switches.Switches
use the numbers to select the master switch. The lower the number the
higher the priority. The unit with the lowest number becomes the master. If
they have the same priority value, they use their MAC addresses to
determine the master. As with priority numbers, the lower the MAC
address, the higher the priority. A switch can have only one priority
number.
Allied Telesis recommends making a switch’s priority and ID numbers the
same. This is not required, but it can make managing and troubleshooting
a stack easier.
The format of the command, which is in the Global Configuration mode, is
shown here:
stack switch_ID priority priority_number
The variables are defined here:
switch_ID - This is the ID number of the switch. The range is 1 to 8.
You can specify only one ID number.
priority_number - This is the new priority number for the switch.
You can specify only one number. The range is 0 to 255. The
default is 128.
This example assigns the priority 1 to the switch with ID 1:
awplus(config)# stack 1 priority 1
STACK
RENUMBER
Every switch in a stack has to have a unique ID number assigned with this
command. Here is the format.
stack current_switch_ID renumber new_switch_ID
The variables are defined here:
current_switch_ID - This is the current ID number of the switch.
You can specify only one ID number.
new_switch_ID - This is the new ID number for the switch. You can
specify only one number. The range is 1 to 8. The default is 1.
Changing the ID number requires resetting the switch.
This example changes the switch’s ID from the default 1 to 2:
awplus(config)# stack 1 renumber 2
SWITCH
PROVISION
To ensure that the first power-on of the stack is successful, Allied Telesis
recommends configuring the units such that each unit knows about the
others prior to forming the stack. This involves using the SWITCH
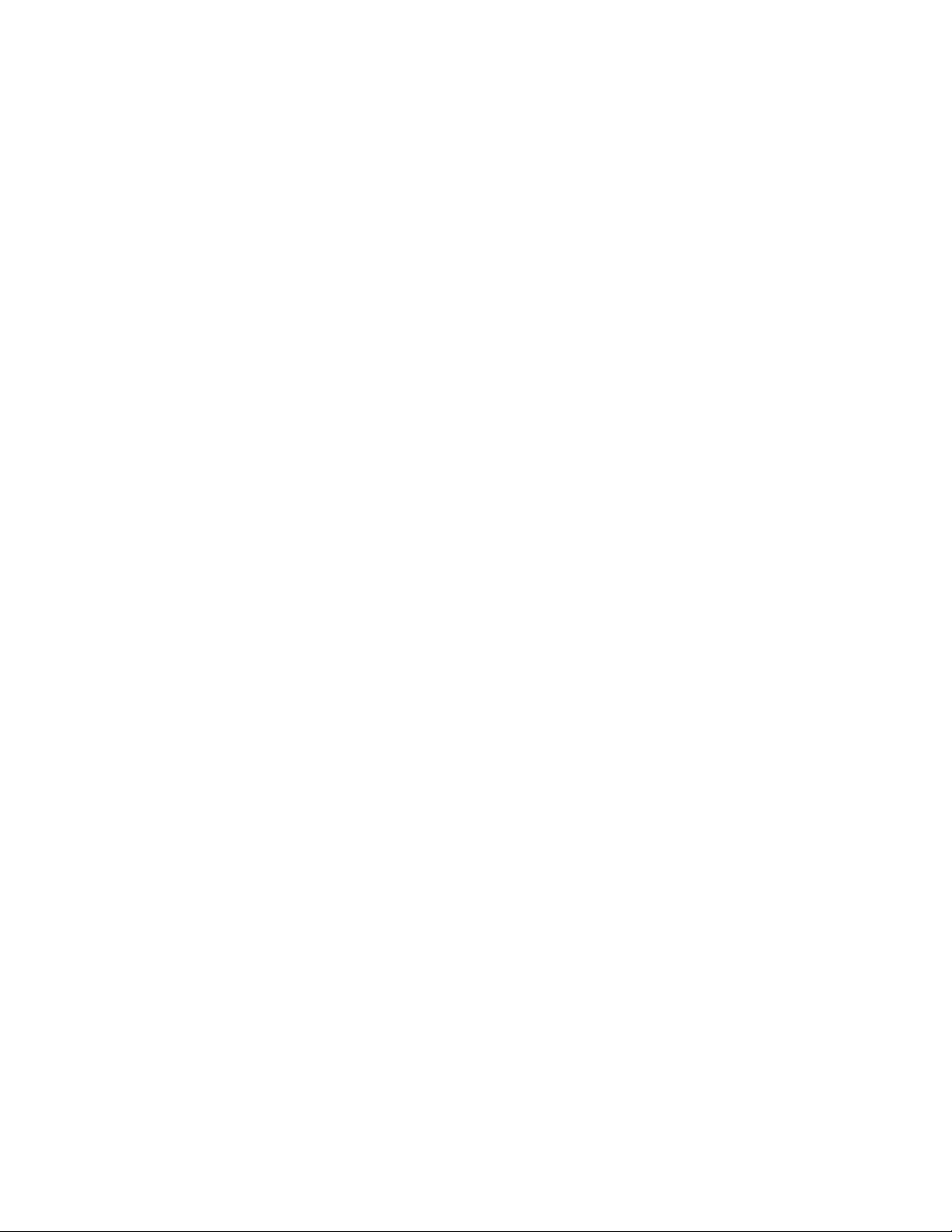
x950 Series Installation Guide for VCStack
191
PROVISION command to add the switches as provisioned units on all the
devices. Here is the format of the command:
switch switch_ID provision x950-28
This example adds a provisioned switch with the ID 2 to the current switch:
awplus(config)# switch 2 provision x950-28
This example adds a provisioned switch with the ID 3 to the current switch:
awplus(config)# switch 3 provision x950-28
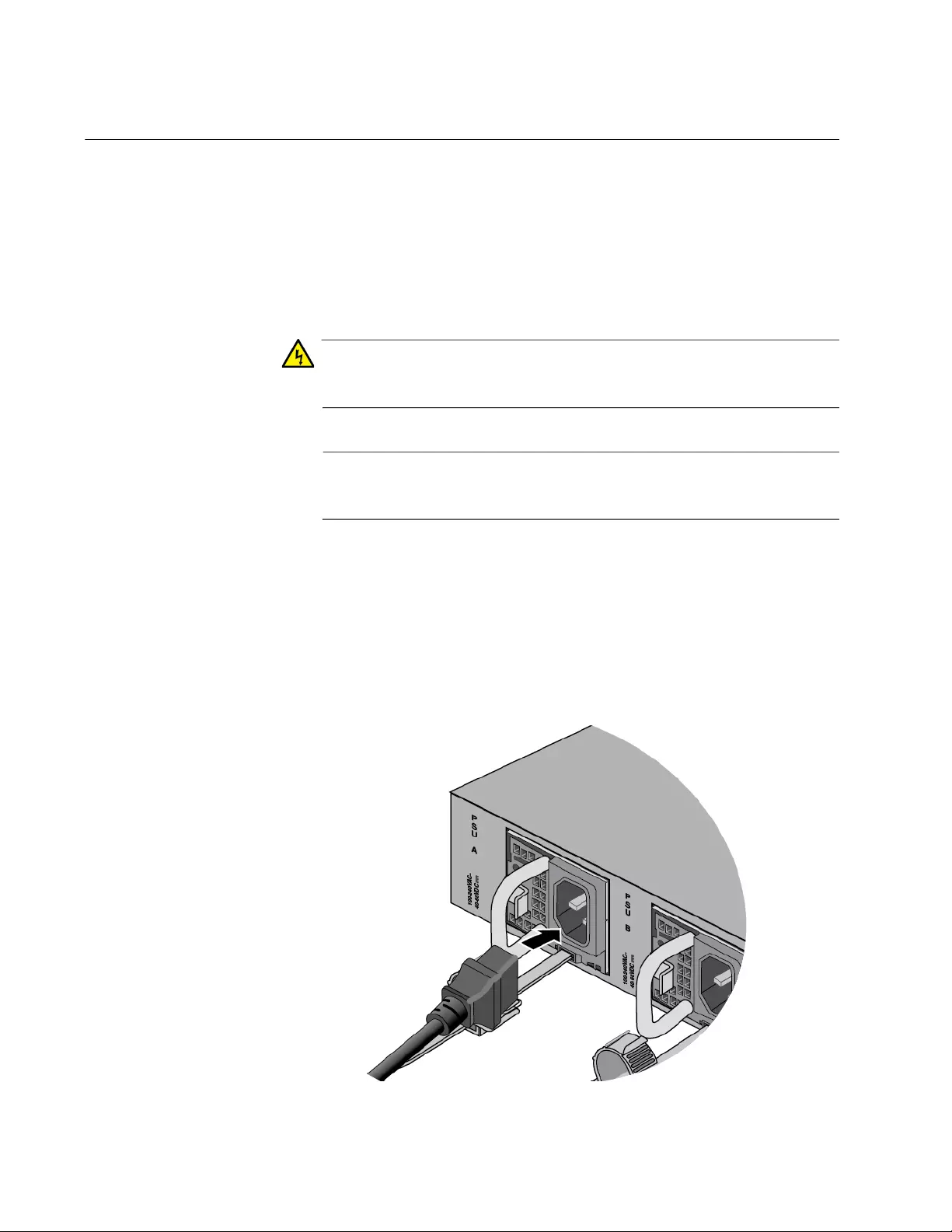
Chapter 10: Configuring the Master Switch
192
Powering On a Switch
The procedure in this section explains how to power on the switch. If you
have not installed the power supplies, refer to “Installing PWR600 AC
Power Supplies” on page 116 or/and “Installing PWR600 DC Power
Supplies” on page 120 for instructions.
Before powering on the chassis, review the information in “Power
Specifications” on page 268.
Warning
Power cord is used as a disconnection device. To de-energize
equipment, disconnect the power cord. E3
Note
Pluggable Equipment. The socket outlet shall be installed near the
equipment and shall be easily accessible. E5
Powering on the
PWR600 AC
Power Supply
To power on the switch with the PWR600 AC power supply, perform the
following procedure:
1. Connect the AC power cord included with the power supply to the AC
power connector on the rear panel of the chassis. If the switch has two
power supplies, you only need to power on one of them to configure
the switch. Refer to Figure 120.
Figure 120. Connecting the AC Power Cord
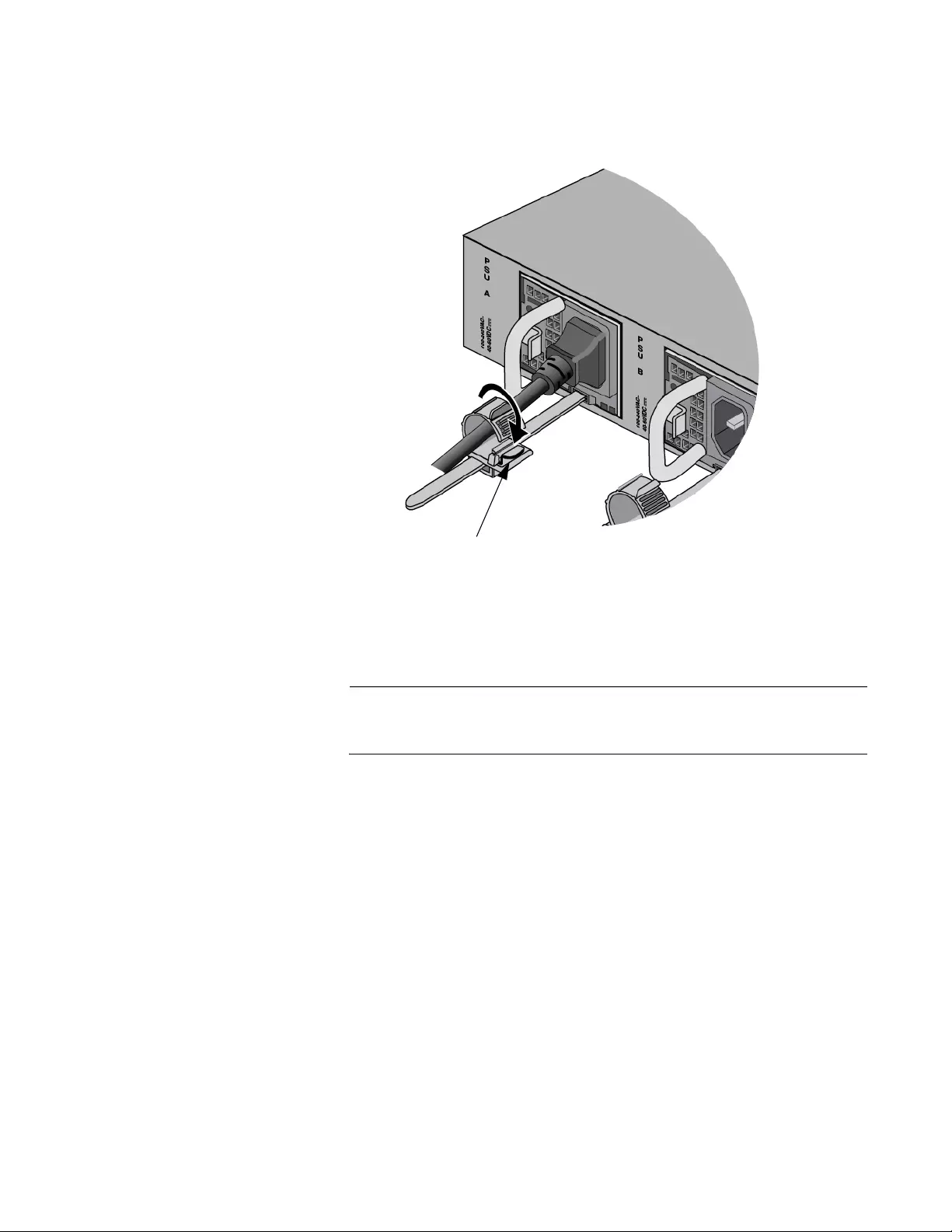
x950 Series Installation Guide for VCStack
193
2. Move the power cord into the restraining strap and secure the strap by
feeding it into the tab slot. Refer to Figure 121 on page 193.
Figure 121. Securing the Power Cord with the Restraining Strap
3. Connect the power cord to an appropriate AC power source. Refer to
Figure 122.
Note
The illustration shows the North American power cord. Your power
cord may be different.
Tab Slot
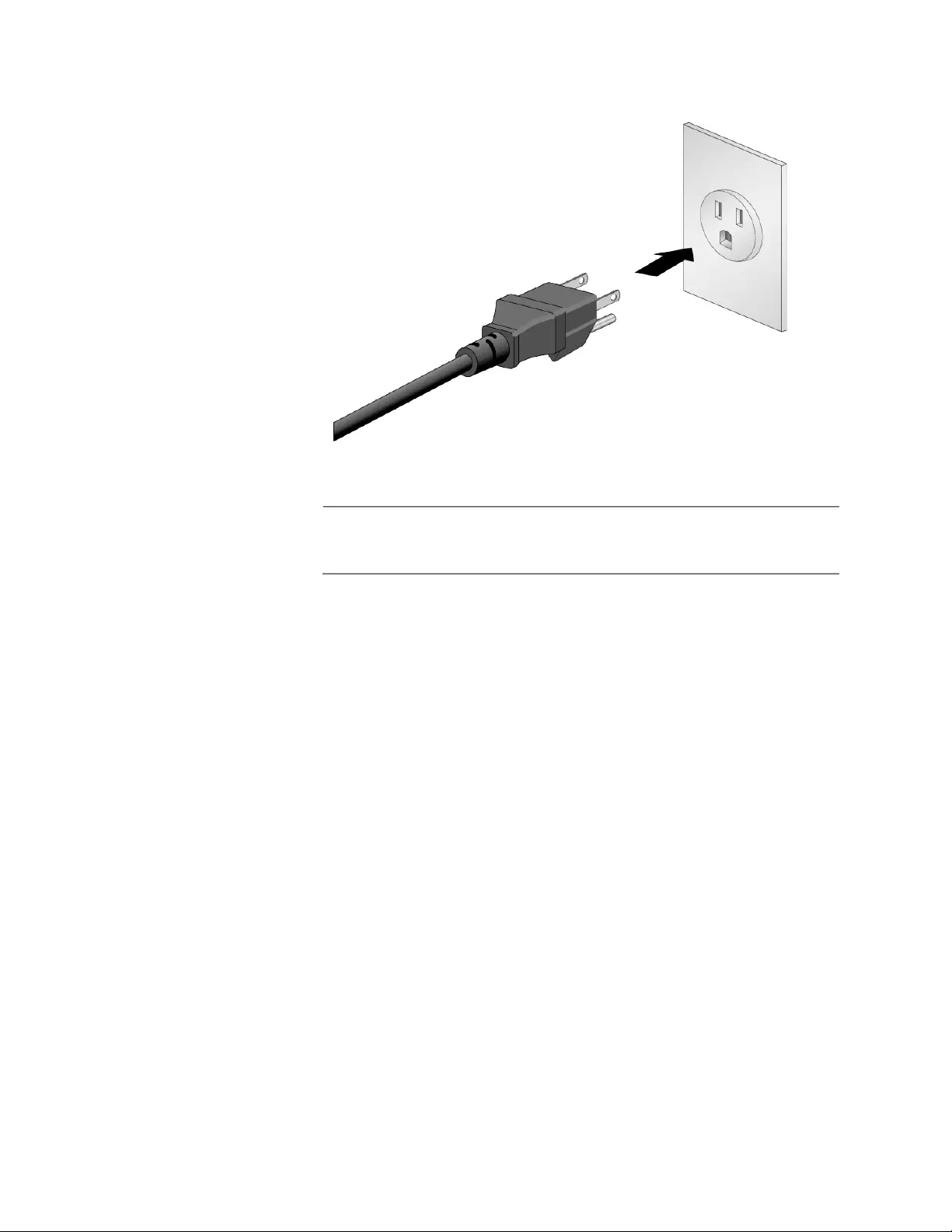
Chapter 10: Configuring the Master Switch
194
Figure 122. Connecting the Power Cord to an AC Power Source
Note
If the switch has two power supplies, you do not have to power on
both of them to perform the procedures in this chapter.
4. If the switch has two AC power supplies, repeat this procedure to
connect a power cord to the second power supply.
5. If you have the PWR600 DC power supply installed on the switch, go
to “Powering on the PWR600 DC Power Supply” on page 194.
6. Wait two minutes for the switch to initialize its management software.
7. Go to “Starting a Local Management Session” on page 196.
Powering on the
PWR600 DC
Power Supply
To power on the switch with the PWR600 DC power supply, perform the
following procedure:
1. Verify that the DC power source unit that provides power to the switch
is powered off. If there are two DC power supplies, verify that both
units are powered off.
2. Verify that the DC power wires are connected to the PWR600 DC
supply.
3. Connect the other end of the power wire to the DC power source unit.
Refer to the documentation included with the unit for instructions.
4. Power on the DC power source unit.
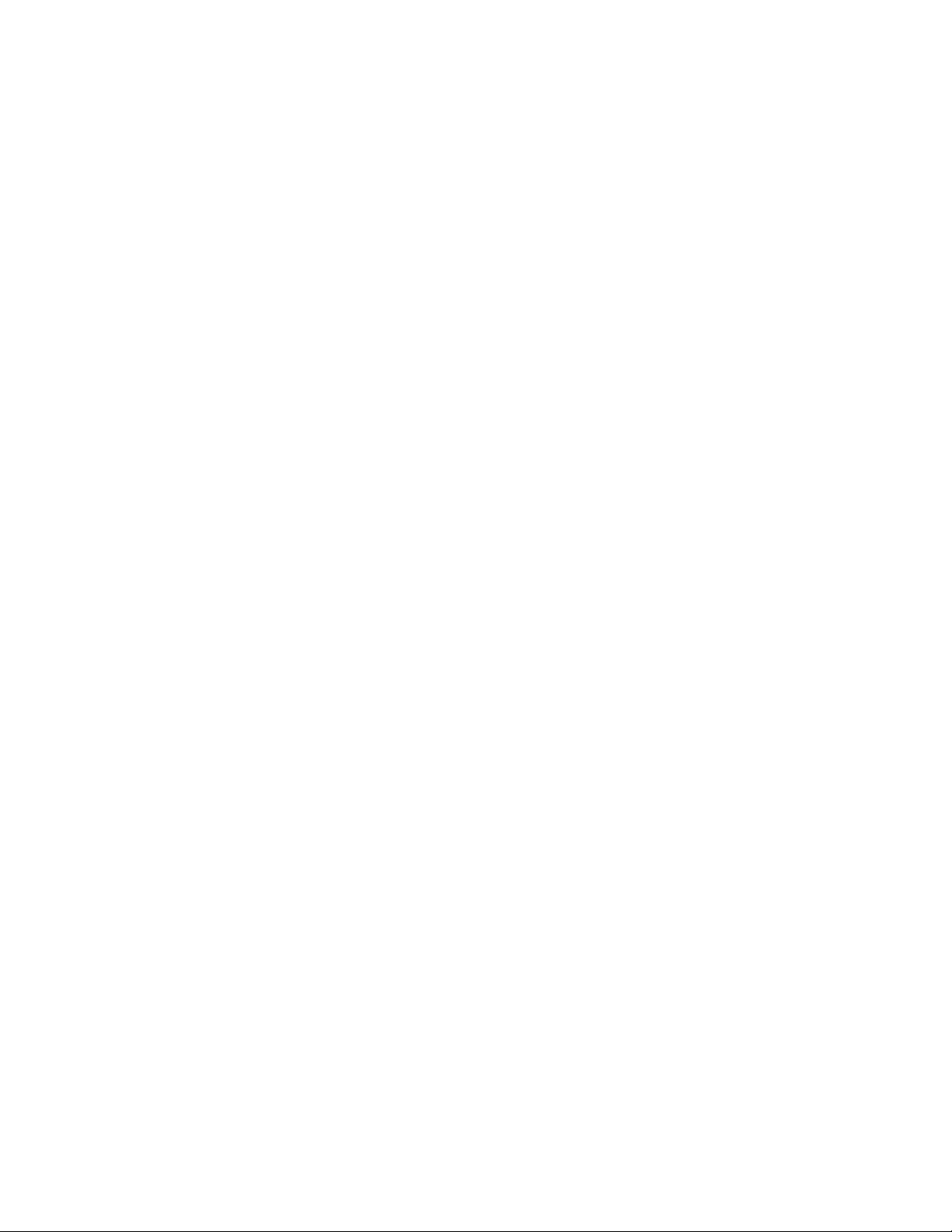
x950 Series Installation Guide for VCStack
195
5. If the switch has two DC power supplies, repeat this procedure to
power on the second DC power supply.
6. If you have the PWR600 AC power supply installed on the switch, go
to “Powering on the PWR600 AC Power Supply” on page 192.
7. Wait two minutes for the switch to initialize its management software.
8. Go to “Starting a Local Management Session” on page 196.
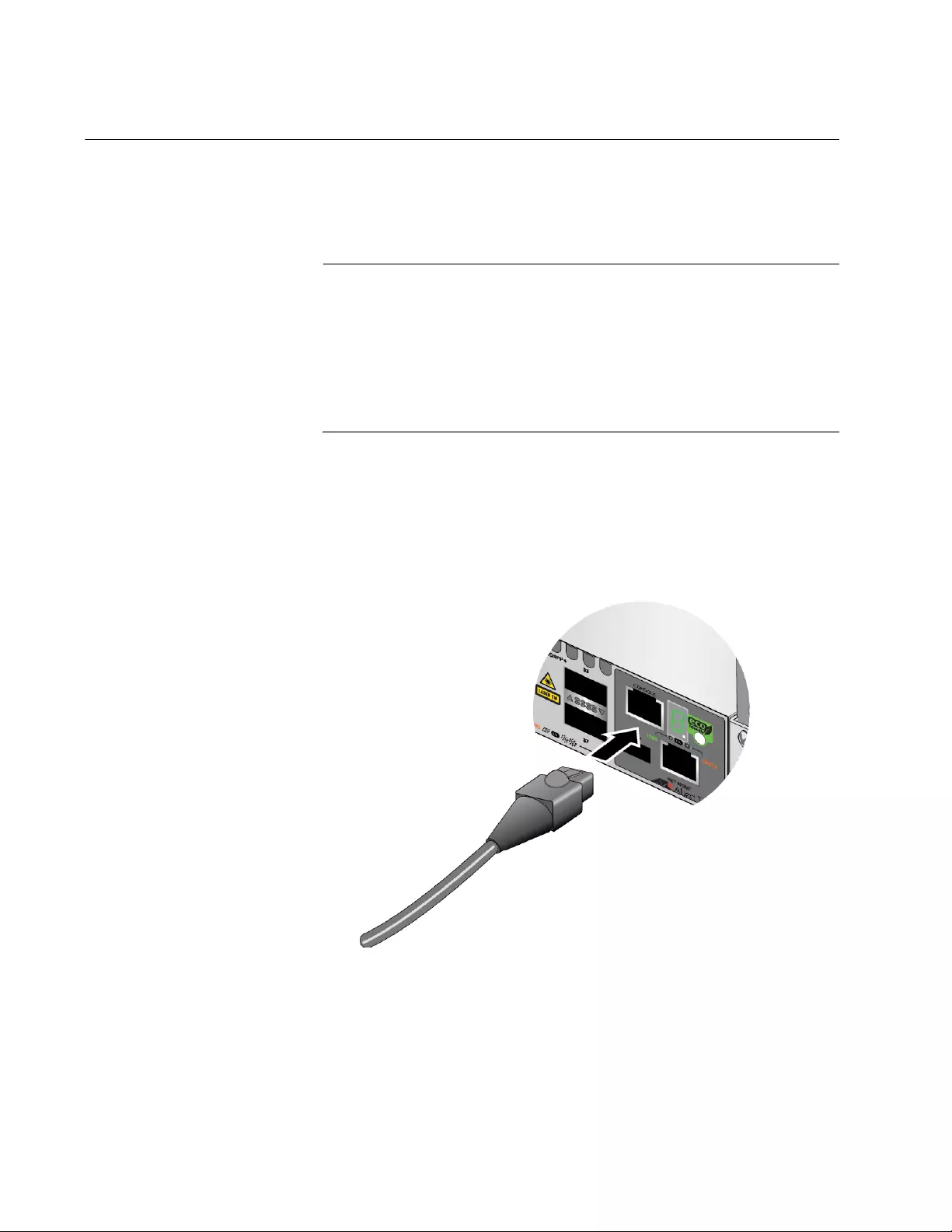
Chapter 10: Configuring the Master Switch
196
Starting a Local Management Session
This procedure explains how to start a local management session on the
switch. It assumes that you powered on the device and waited two
minutes for it to initialize its operating software.
Note
The first management session of the switch can be either a local
session, as explained in this section, or a remote session over your
network through the NET MGMT port. For remote management, the
switch uses either its default IP address 192.168.42.42 or an
address assigned to it by a DHCP server. For instructions on how to
start a remote management session, refer to the Software
Reference for x950 Switches, AlliedWare Plus Operating System.
To start a local management session, perform the following procedure:
1. Connect the RJ-45 end of the management card included with the
switch to the Console RS-232 port on the management panel. Refer to
Figure 123.
Figure 123. Connecting the Management Cable to the Console RS-232
Port
2. Connect the other end of the cable to an RS-232 port on a terminal or
personal computer with a terminal emulation program.
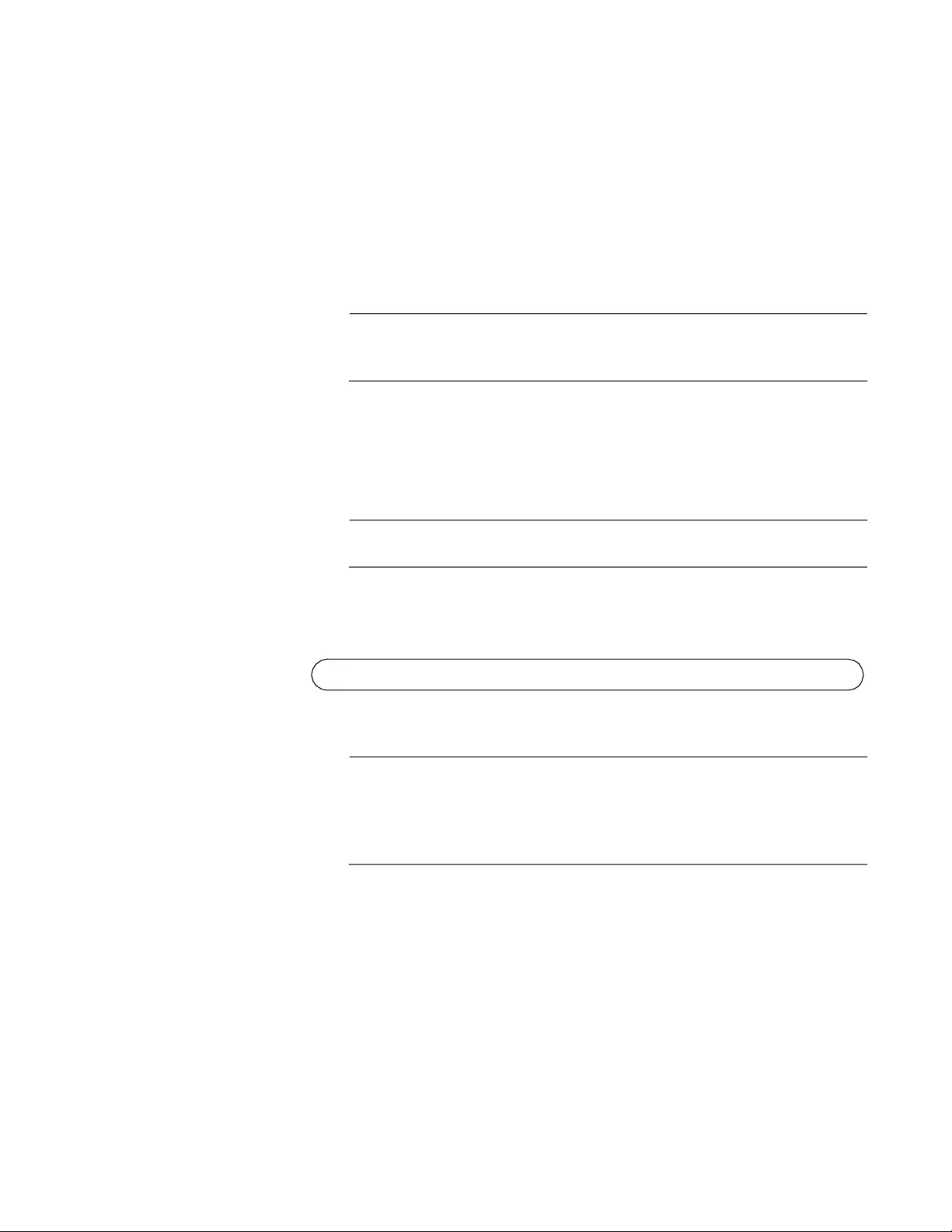
x950 Series Installation Guide for VCStack
197
3. Configure the VT-100 terminal or terminal emulation program as
follows:
Baud rate: 9600 bps
Data bits: 8
Parity: None
Stop bits: 1
Flow controller: None
Note
The port settings are for a DEC VT100 or ANSI terminal, or an
equivalent terminal emulator program.
4. Press Enter. You are prompted for a user name and password.
5. Enter the default user name and password. They are “manager” and
“friend” (without the quotes), respectively
Note
User names and passwords are case sensitive.
The local management session starts when the User Exec mode
prompt, shown in Figure 124. is displayed.
Figure 124. User Exec Mode Prompt
Note
The User Exec mode is the first level in the command mode
interface. For complete information on the modes and commands,
refer to the Software Reference for x950 Series Switches,
AlliedWare Plus Operating System from www.alliedtelesis.com.
6. Do one of the following:
To begin configuring the master switch, go to “Configuring the
Master Switch - Part I” on page 200.
If you have already configured the master switch, go to Chapter 11,
“Configuring Member Switches” on page 209.
awplus>
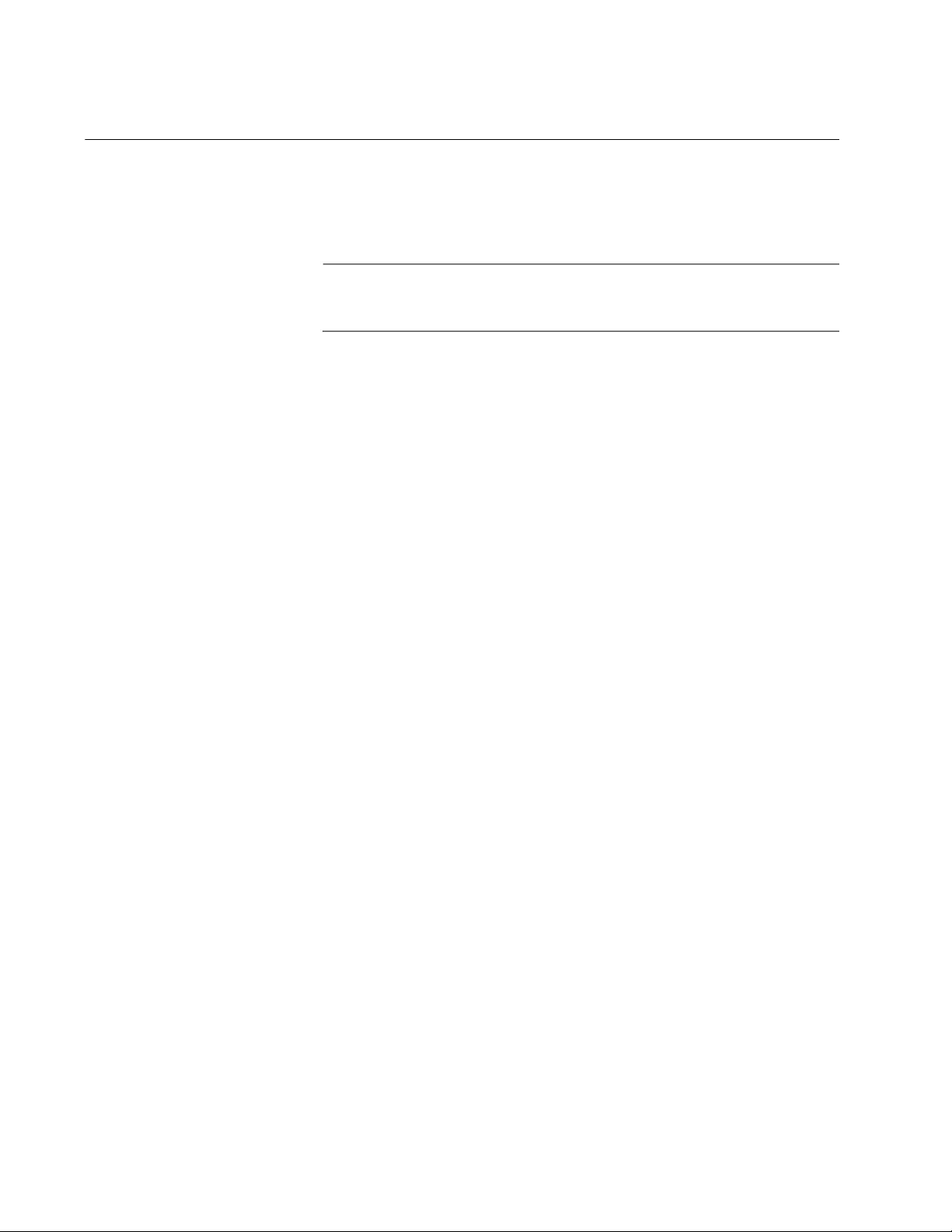
Chapter 10: Configuring the Master Switch
198
General Steps for the Master Switch
The procedure for configuring the master switch is divided into two parts.
Here are the general steps to “Configuring the Master Switch - Part I” on
page 200.
Note
The procedures require reseting the switch. Some network traffic will
be lost if the unit is already connected to an active network.
1. Start a local management session on the switch.
2. Verify the hardware with the SHOW SYSTEM ENVIRONMENT
command in the Privilege Exec mode.
3. Display the firmware version number with the SHOW VERSION
command.
4. Enable the VCStack feature with the STACK ENABLE command in the
Global Configuration mode.
5. Assign the master switch the priority 1 with the STACK PRIORITY
command in the Global Configuration mode. This is to ensure that it
acts as the master switch during the first power-on of the stack.
6. Add the member switches as provisioned units to the master switch,
with the SWITCH PROVISION command. This step is to ensure that
the master switch knows about the member switch during the first
power-on of the stack.
7. Save your changes with the WRITE command in the Privilege Exec
mode.
8. Reboot the switch with the REBOOT command.
Here are the general steps to “Configuring the Master Switch - Part II” on
page 203:
1. Start a new local management session.
2. Designate the types of transceivers to be used in ports 25 to 37 for the
x950-28XSQ and x950-28XTQm switch and in ports 49 to 61 for the
x950-52XSQ switch with the PLATFORM PORTMODE INTERFACE
command, on the master and provisioned member switches. Allied
Telesis recommends performing this task at this time even if you are
not using those ports as the stack trunk.
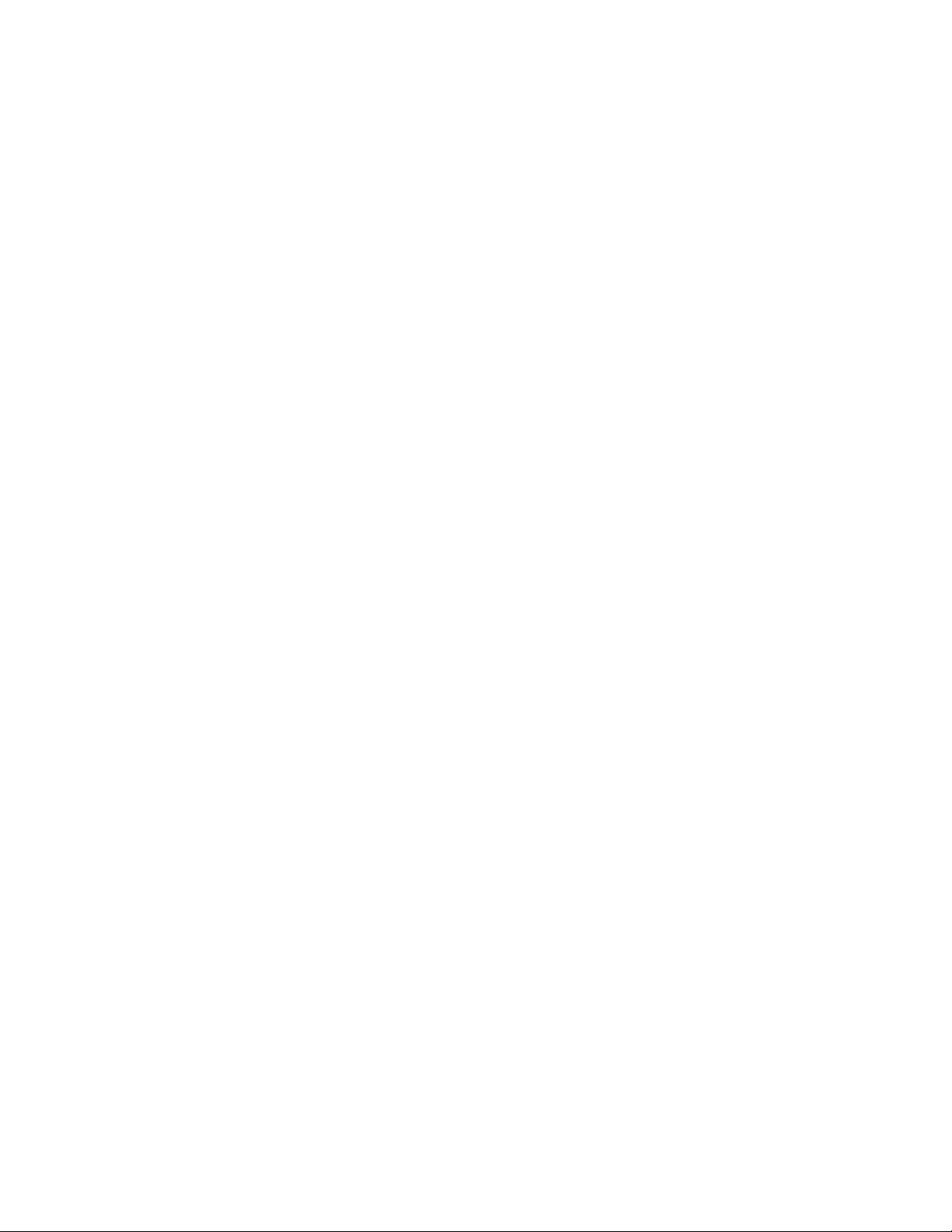
x950 Series Installation Guide for VCStack
199
3. Designate the ports of the stack trunk on the master and provisioned
member switches with the STACKPORT command in the port
Interface mode.
4. Save your changes with the WRITE command in the Privilege Exec
mode.
5. Reboot the switch with the REBOOT command.
6. Verify the changes with the SHOW STACK and SHOW RUNNING-
CONFIG commands.
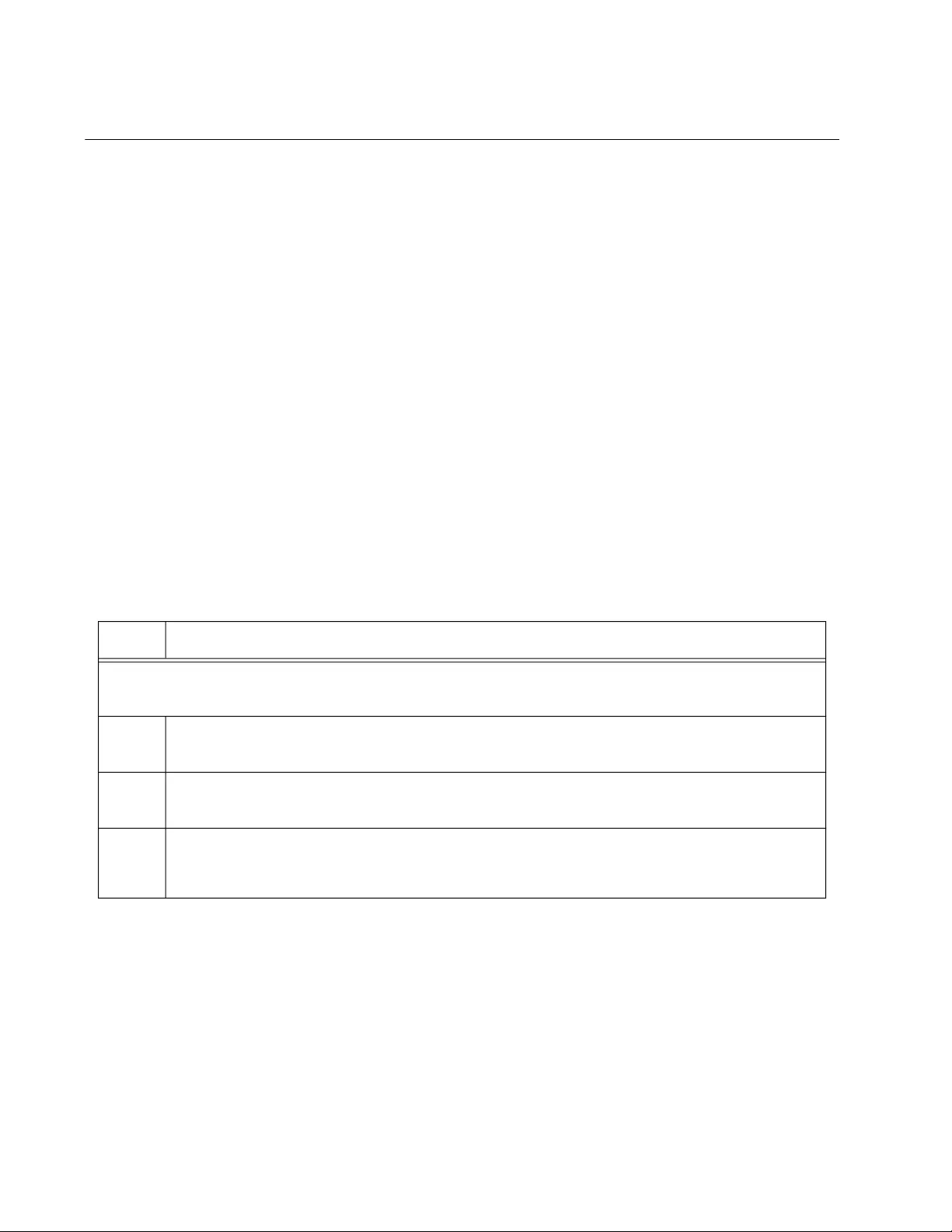
Chapter 10: Configuring the Master Switch
200
Configuring the Master Switch - Part I
This section contains Part I for configuring the master switch for stacking.
In this procedure you do the following:
Verify the hardware status with the SHOW SYSTEM
ENVIRONMENT command.
Display the firmware version number with the SHOW VERSION
command.
Enable VCStack with the STACK ENABLE command.
Assign the master switch the priority 1 with the STACK PRIORITY
command in the Global Configuration mode.
Add the member switches as provisioned switches with the
SWITCH PROVISION command.
Save the configuration and reboot the switch with the WRITE and
REBOOT commands.
Allied Telesis recommends filling out the worksheet in “Stacking
Worksheet” on page 93 before performing this procedure.
To configure the master switch, perform the procedure in Table 32.
Table 32. Configuring the Master Switch - Part I
Step Description and Command
Steps 1 to 4 power on the switch, start a local management session, and verify the hardware
operations of the unit.
1 Power on the master switch and wait two minutes for it to initialize the management
software. Refer to “Powering On a Switch” on page 192.
2 Start a local management session. Refer to “Starting a Local Management Session”
on page 196.
3 Move to the Privileged Exec mode with the ENABLE command.
awplus> enable
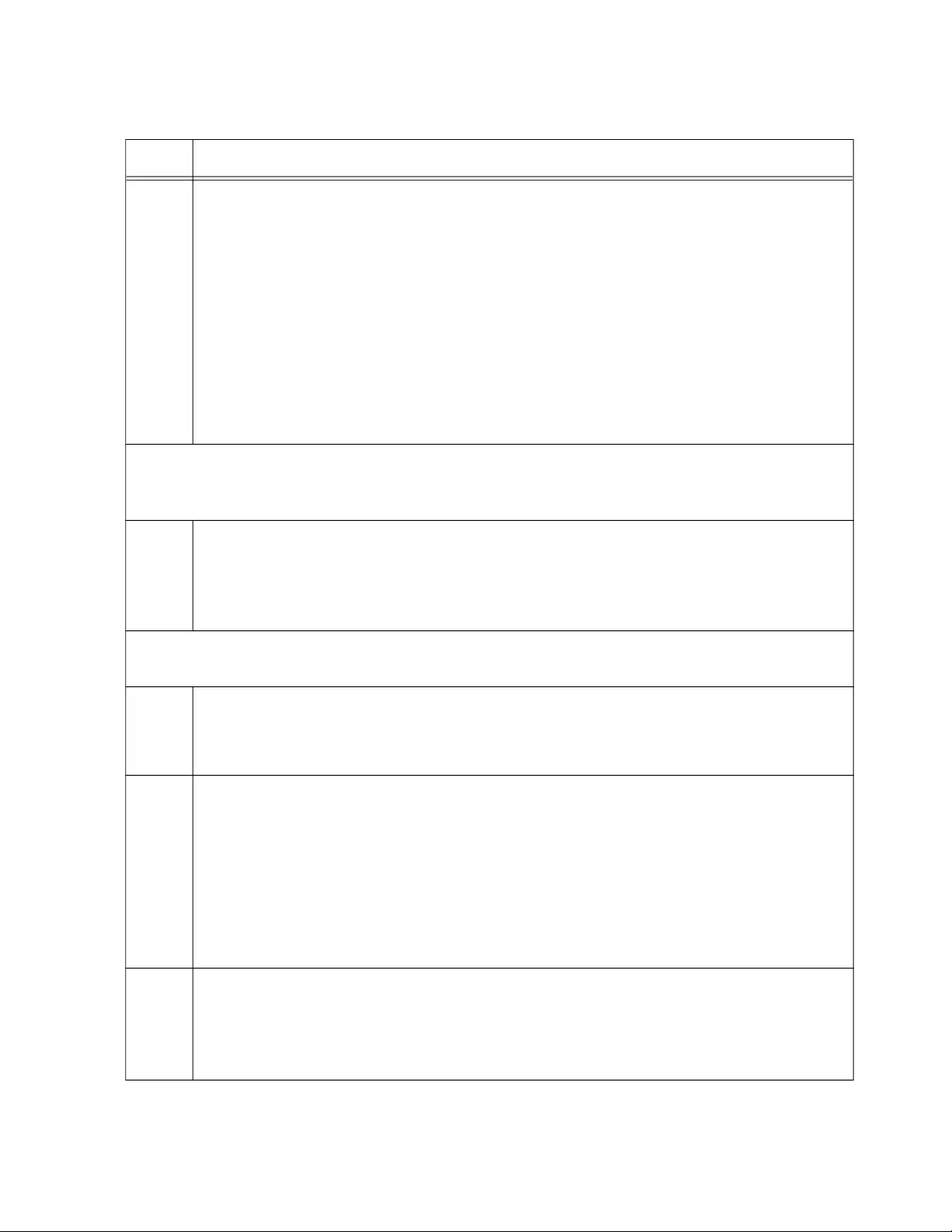
x950 Series Installation Guide for VCStack
201
4 Verify that the switch hardware is operating correctly with the SHOW SYSTEM
ENVIRONMENT command. The status of all components should be Ok.
awplus# show system environment
Environment Monitoring Status
Overall Status: Normal
Resource ID: 1 Name: PSU Bay A (AT-PWR600)
ID Sensor (Units) Reading Low Limit High Limit Status
1 Device Present Yes - - Ok
2 Fan/Temperature Fault Yes - - Ok
.
.
Step 5 displays the version number of the AlliedWare Plus operating software on the switch.
After viewing the version numbers on all the switches, you will compare them to confirm they all
have the same version. Switches with different versions will have to be updated.
5 Display the version number of the AlliedWare Plus operating software on the switch
by entering the SHOW VERSION command and write it down in the worksheet in
“Stacking Worksheet” on page 93 for the master switch.
awplus# show version
Steps 6 to 8 activate VCStack on the switch and assign it the priority 1 so that it becomes the
master switch when the stack is powered on for the first time.
6 Move to the Global Configuration mode with the CONFIGURE TERMINAL command.
awplus# configure terminal
Enter configuration commands, one per line. End with CNTL/Z.
7 Activate VCStack on the switch with the STACK ENABLE command.
awplus(config)# stack enable
% Automatically enabling ‘stack virtual-mac’ to minimize disruption
form failovers.
% Please check that the new MAC 0000.cd37.0431 is unique within the
network.
% Save the config and restart the system for this change to take
effect.
8Assign priority 1 to the switch with the STACK PRIORITY to ensure that it is selected
as the master switch during the first power-on of the stack.
awplus(config)# stack 1 priority 1
% Warning: Stacking is currently disabled.
Table 32. Configuring the Master Switch - Part I (Continued)
Step Description and Command
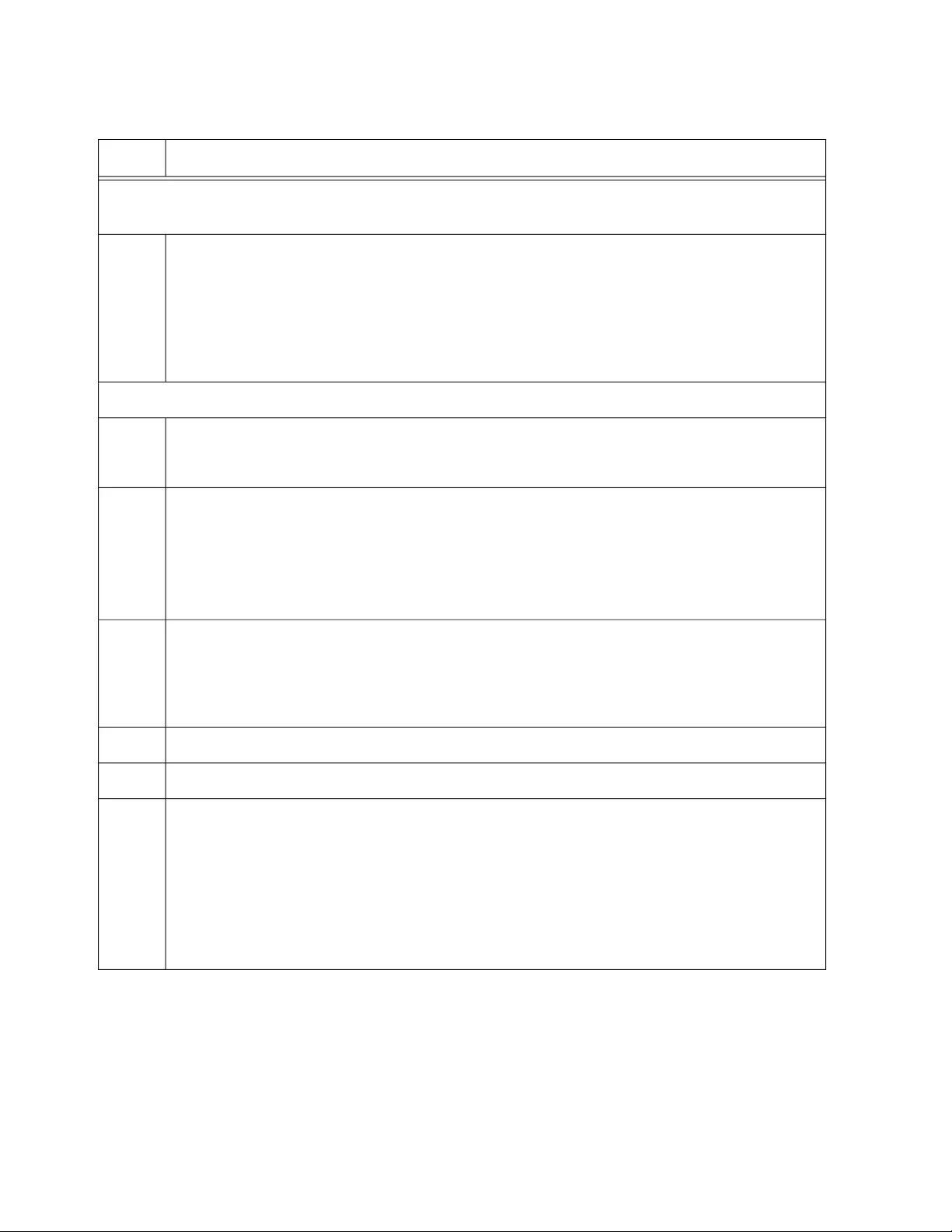
Chapter 10: Configuring the Master Switch
202
Step 9 adds the member switches as provisioned switches to the master switch. You need to
add one provisioned switch for each member switch to be in the stack.
9Add the member switches as provisioned switches to the master switch, with the
SWITCH PROVISION command. Assign them unique IDs in the range of 2 to 4. This
example assumes the stack will have three member switches.
awplus(config)# switch 2 provision x950-28
awplus(config)# switch 3 provision x950-28
awplus(config)# switch 4 provision x950-28
Steps 10 to 15 save your changes and reboot the switch.
10 Return to the Privileged Exec mode.
awplus(config)# exit
11 Enter the WRITE command to save your change. If this is the first management
session, the switch adds the configuration file DEFAULT.CFG to flash memory.
awplus# write
Building configuration ...
[OK]
12 Restart the switch with the REBOOT command.
awplus# reboot
reboot system? (y/n):
awplus#
13 Type “Y” for yes.
14 Wait two minutes for the switch to initialize its management software.
15 Check the ID LED in the management panel on the front panel and do one of the
following:
- If the ID LED is displaying the number 1, VCStack is now enabled on the switch. Go
to “Configuring the Master Switch - Part II” on page 203.
- If the ID LED is displaying “0,” VCStack is still disabled. Repeat this procedure,
being sure to issue the WRITE command to save your change before resetting the
switch.
Table 32. Configuring the Master Switch - Part I (Continued)
Step Description and Command
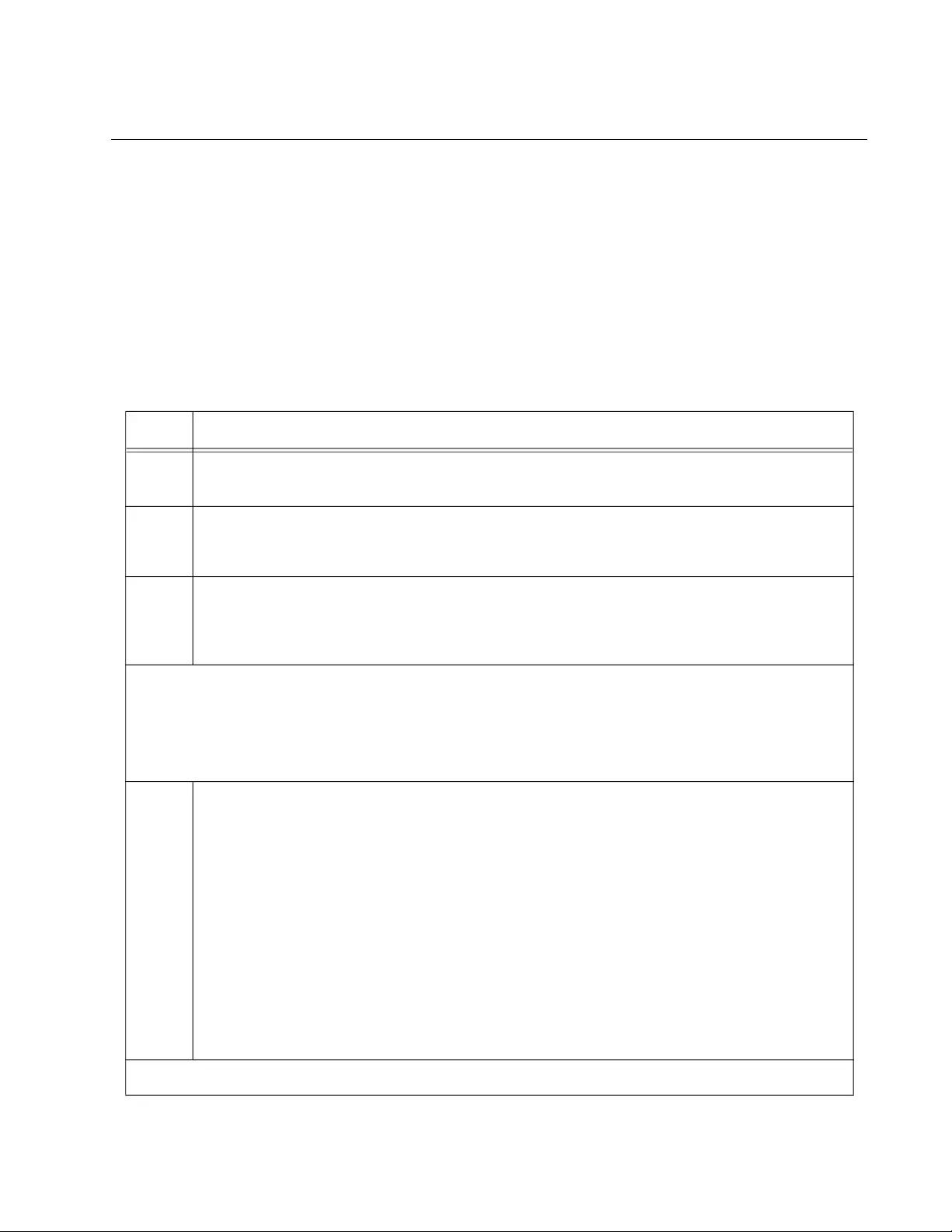
x950 Series Installation Guide for VCStack
203
Configuring the Master Switch - Part II
This section contains Part II for configuring the master switch. In this
procedure you do the following:
Designate the types of transceivers to be used in ports 25, 29, 33,
and 37 for the x950-28XSQ and x950-28XTQm switches or ports
49, 53, 57, 61 for the x950-52XSQ switch on the master and
provisioned member switches.
Designate the trunk ports.
To perform Part II, perform the procedure in Table 33.
Table 33. Configuring the Master Switch- Part II
Step Description and Command
1 Start a new local management session. Refer to “Starting a Local Management
Session” on page 196.
2 Move to the Privileged Exec mode with the ENABLE command.
awplus> enable
3 Move to the Global Configuration mode with the CONFIGURE TERMINAL command.
awplus# configure terminal
Enter configuration commands, one per line. End with CNTL/Z.
Steps 4 designates the types of transceivers to be used in ports 25, 29, 33, and 37 for the
x950-28XSQ and x950-28XTQm switches or in ports 49, 53, 57, and 61 for the x950-52XSQ
switch on the master switch. The ports support 40Gbps QSFP+ transceivers, 100Gbps
QSFP28 transceivers, and 40Gbps to 10Gbps breakout cables. The default is 40Gbps QSFP+
transceivers.
4 Designate the types of transceivers to be used in ports 25, 29, 33, and 37 for the
x950-28XSQ and x950-28XTQm switches or in ports 49, 53, 57, and 61 for the
x950-52XSQ switch on the master switch with the PLATFORM PORTMODE
INTERFACE command in the Global Configuration mode. You can skip this step for
ports that will be using 40Gbps QSFP+ transceivers because that is the default
setting. You can also skip this step and configure the ports later if you are not using
100Gbps transceivers for the stack trunk. For more information, refer to “Ports for
40Gbps QSFP+ or 100Gbps QSFP28 Transceiver, or Breakout Cables” on page 29
and “PLATFORM PORTMODE INTERFACE” on page 188.
This example configures ports 33 and 37 for 100Gbps transceivers on the master
switch:
awplus(config)# platform portmode interface port1.0.33-1.0.37 100g
Steps 5 to 7 designate the stack ports on the master switch with the STACKPORT command.
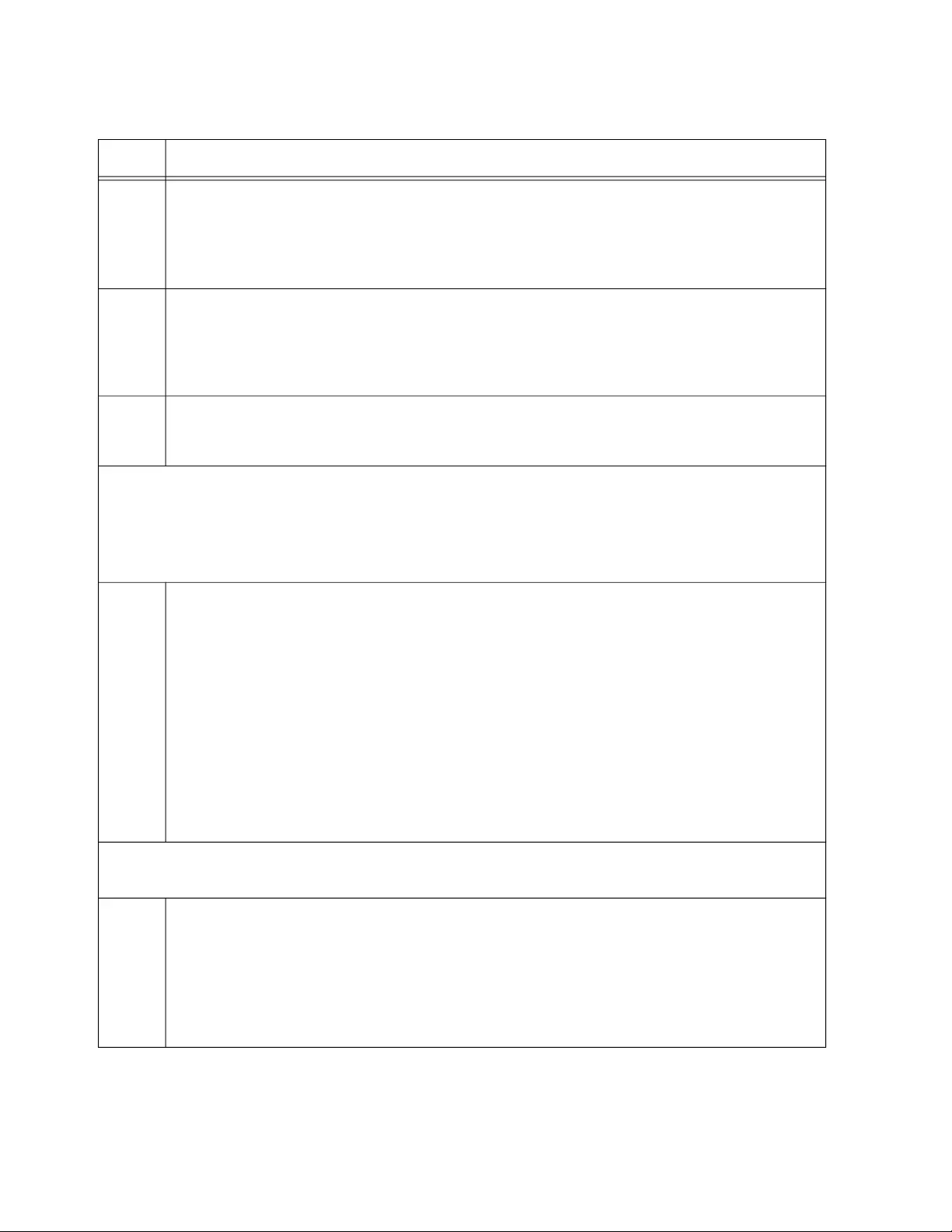
Chapter 10: Configuring the Master Switch
204
5Enter the port Interface modes of the ports that will be the stack trunk on the master
switch. This example assumes the master switch will use ports 33 and 37 as the stack
trunk. Be sure to modify the command to specify the ports for your stack trunk.
awplus(config)# interface port1.0.33-1.0.37
6Designate the ports as trunk ports with the STACKPORT command.
awplus(config-if)# stackport
% Save the config and restart the system for this change to take
effect.
7Return to the Global Configuration mode.
awplus(config-if)# exit
Steps 8 designates the types of transceivers to be used in ports 25, 29, 33, and 37 for the
x950-28XSQ and x950-28XTQm switches or in ports 49, 53, 57, and 61 for the x950-52XSQ
switch on the provisioned member switches. The ports support 40Gbps QSFP+ transceivers,
100Gbps QSFP28 transceivers, and 40Gbps to 10Gbps breakout cables. The default is
40Gbps QSFP+ transceivers.
8Configure ports 25, 29, 33, and 37 for the x950-28XSQ and x950-28XTQm switches
or in ports 49, 53, 57, and 61 for the x950-52XSQ switch on the provisioned member
switches for the appropriate transceivers, with the PLATFORM PORTMODE
INTERFACE command. For more information, refer to “Ports for 40Gbps QSFP+ or
100Gbps QSFP28 Transceiver, or Breakout Cables” on page 29 and “PLATFORM
PORTMODE INTERFACE” on page 188.
This example assumes a stack with three member switches (port2 to port4) that will
use 100Gbps transceivers in ports 33 and 37:
awplus(config)# platform portmode interface port2.0.33-2.0.37 100g
awplus(config)# platform portmode interface port3.0.33-3.0.37 100g
awplus(config)# platform portmode interface port4.0.33-4.0.37 100g
Steps 9 and 10 designate the stack ports on the provisioned switches with the STACKPORT
command.
9Enter the port Interface modes of the ports that will be the stack trunk on the
provisioned member switches. This example assumes the stack will have three
member switches and the stack ports are 33 and 37. Be sure to modify the command
to specify the ports for your stack trunk.
awplus(config)# interface port2.0.33-2.0.37,port3.0.33-3.0.37,
port4.0.33-4.0.37
Table 33. Configuring the Master Switch- Part II (Continued)
Step Description and Command
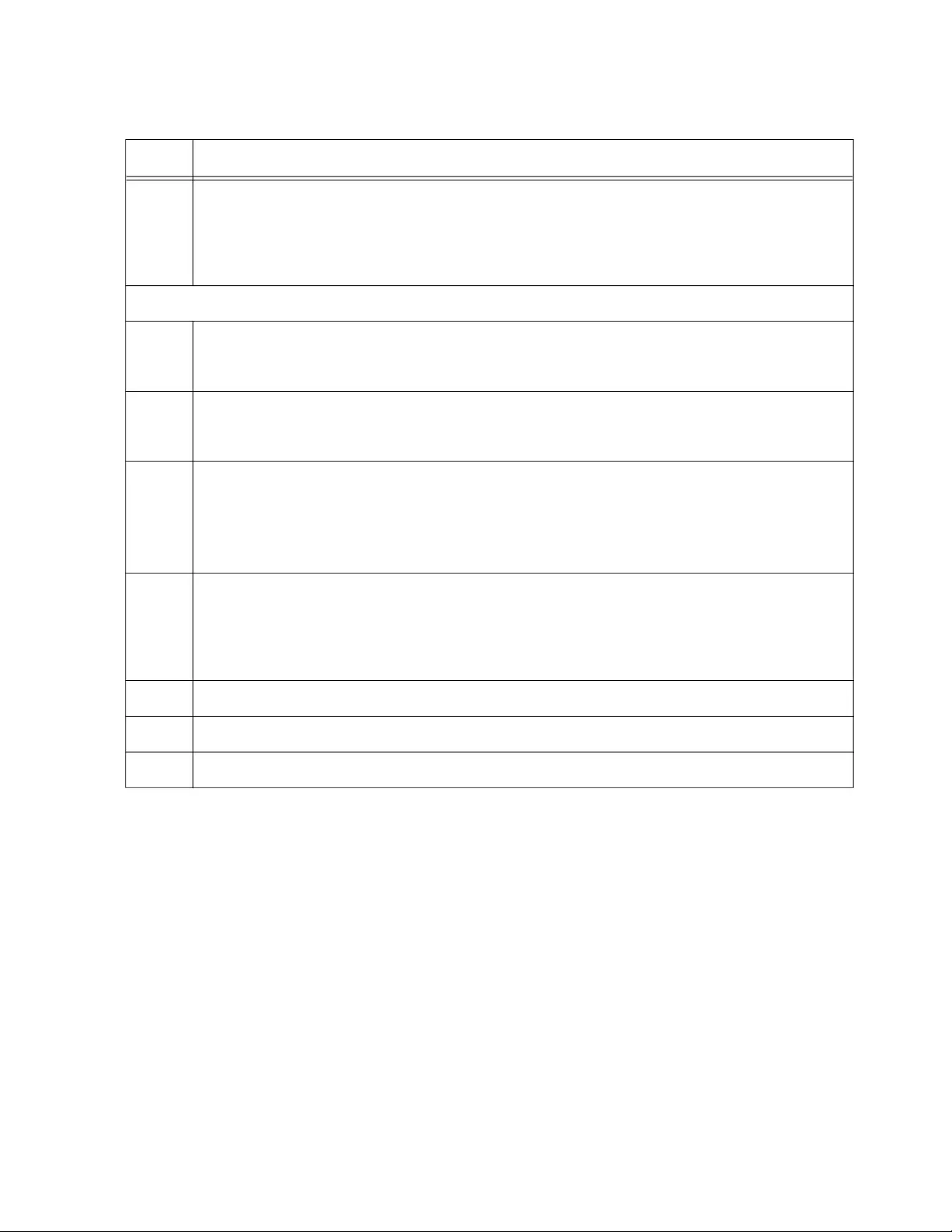
x950 Series Installation Guide for VCStack
205
10 Designate the ports as trunk ports with the STACKPORT command.
awplus(config-if)# stackport
% Save the config and restart the system for this change to take
effect.
Steps 11 to 17 save your changes and reboot the switch.
11 Return to the Global Configuration mode.
awplus(config-if)# exit
12 Return to the Privileged Exec mode.
awplus(config)# exit
13 Enter the WRITE command to save your change.
awplus# write
Building configuration ...
[OK]
14 Restart the switch with the REBOOT command.
awplus# reboot
reboot system? (y/n):
awplus#
15 Type “Y” for yes.
16 Wait two minutes for the switch to initialize its management software.
17 Go to “Verifying the Master Switch” on page 206.
Table 33. Configuring the Master Switch- Part II (Continued)
Step Description and Command
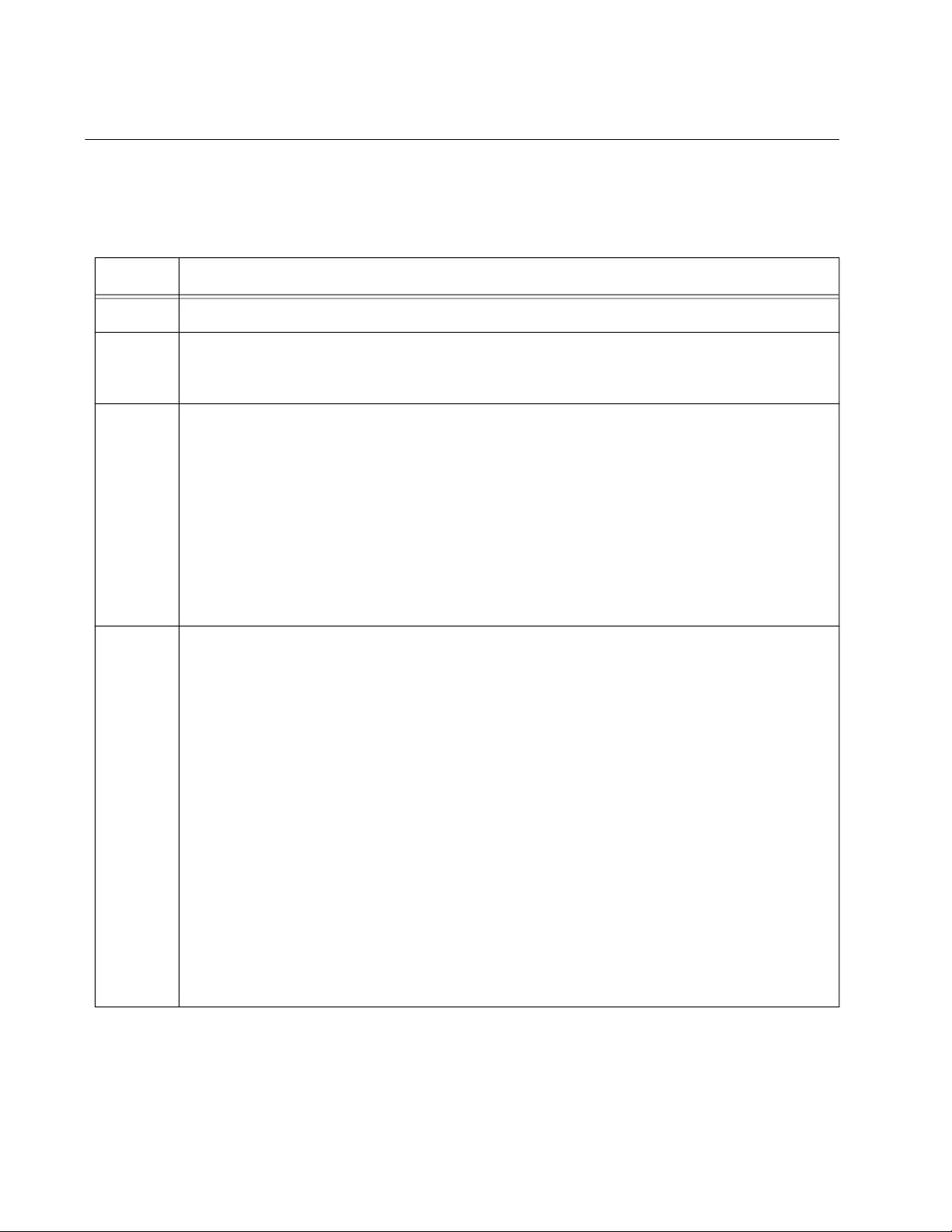
Chapter 10: Configuring the Master Switch
206
Verifying the Master Switch
Perform the steps in Table 34 to confirm the configuration of the master
switch.
Table 34. Verifying the Master Switch
Step Description and Command
1 Start a new local management session.
2 Move to the Privileged Exec mode with the ENABLE command.
awplus> enable
3 Enter the SHOW STACK command. Here is an example for a stack of four switches:
awplus# show stack
Virtual Chassis Stacking summary information
ID Pending ID MAC address Priority Status Role
1 - e01a.ba56.c208 1 Ready Active Master
2 - - - - Provisioned
3 - - - - Provisioned
4 - - - - Provisioned
Operational Status Standalone unit
Stack MAC address 0000.ab56.d4a8 (Virtual MAC)
4 Verify the display for the following:
- The table should have one entry for the master switch (ID 1).
- The table should have one entry for each provisioned member switch (IDs 2 to 4). If
the table is missing a member switch, repeat the SWITCH PROVISION command in
“Configuring the Master Switch - Part I” on page 200.
- The master switch should have the priority 1. If the priority number is incorrect,
repeat the STACK PRIORITY command in “Configuring the Master Switch - Part I”
on page 200.
- The Operational Status should be Standalone Unit, indicating that stacking is
enabled and that the unit is operating as a stack of one switch. If the status is
Stacking Hardware Disabled, the stacking feature is disabled and needs to be
enabled. Repeat the STACK ENABLE command in “Configuring the Master Switch -
Part I” on page 200.
- Always remember to perform the WRITE command to save your configuration
changes.
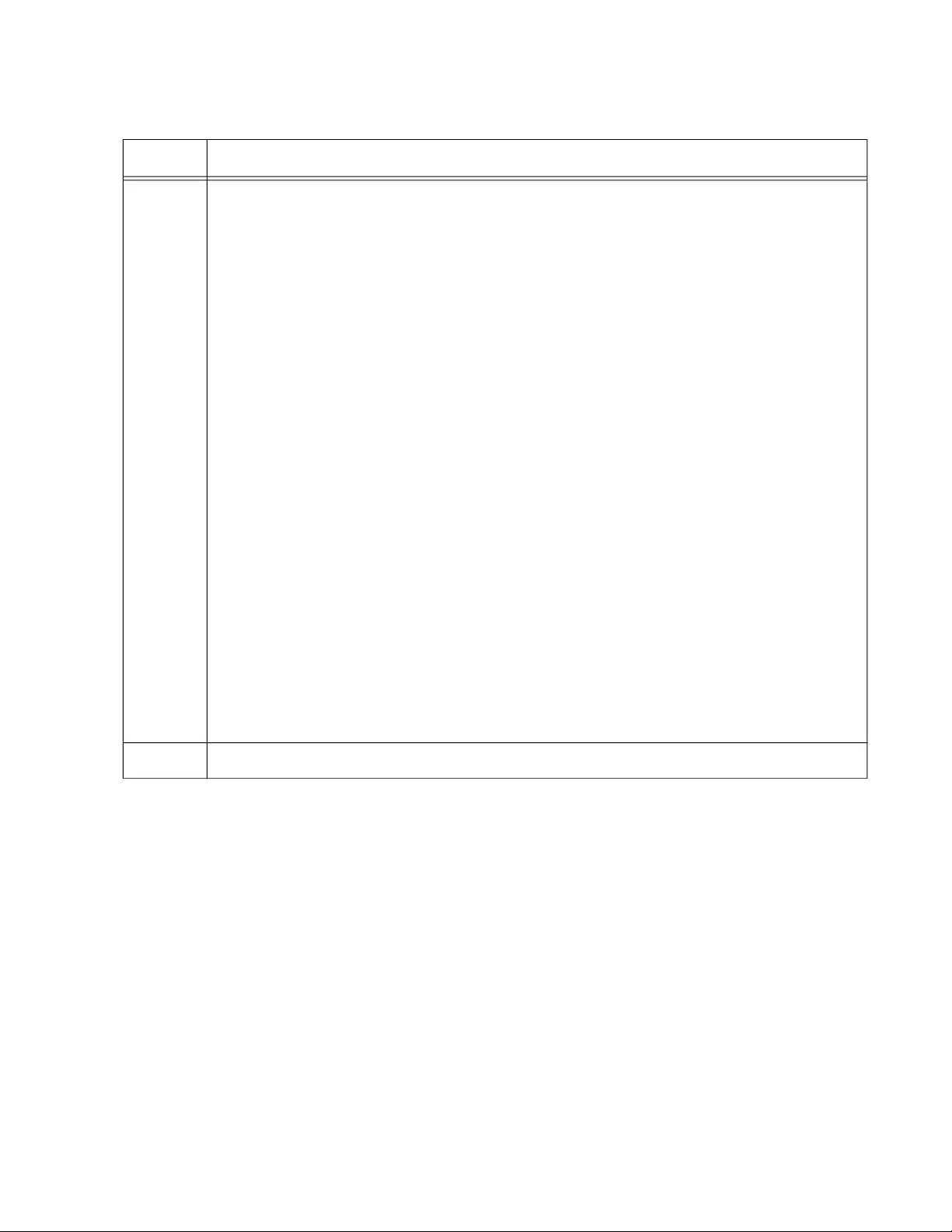
x950 Series Installation Guide for VCStack
207
5 Enter the SHOW RUNNING-CONFIG command and verify the following:
- Check the running configuration for SWITCH PROVISION commands. There
should be one command for each switch and the commands should designated
x950 switches. Here are examples for a stack of four switches:
switch 1 provision x950-28
switch 2 provision x950-28
switch 3 provision x950-28
switch 4 provision x950-28
- Check the running configuration for STACKPORT commands. There should be one
command for each switch and the commands should designate the trunk ports.
Here are examples:
.
interface port1.0.33-1.0.37
stackport
.
interface port2.0.33-2.0.37
stackport
.
interface port3.0.33-3.0.37
stackport
.
interface port4.0.33-4.0.37
stackport
6Go to “What to Do Next” on page 208.
Table 34. Verifying the Master Switch (Continued)
Step Description and Command
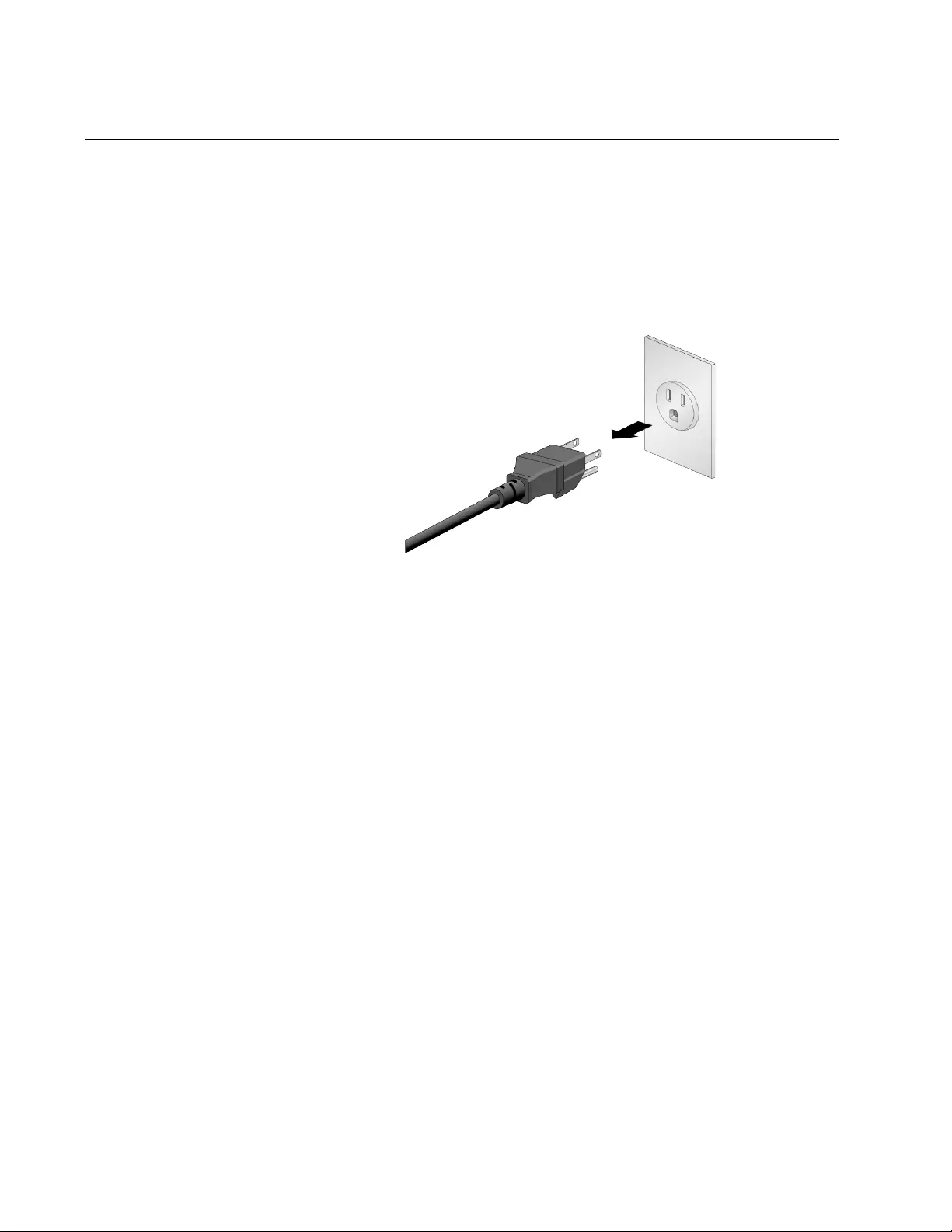
Chapter 10: Configuring the Master Switch
208
What to Do Next
After configuring the master switch, do the following:
1. Power off the switch by performing the following:
For the DC power supply, power off the DC power source units.
For the AC power supply, disconnect the AC power cords from the
AC power sources. Refer to Figure 125.
Figure 125. Powering Off the AC Power Supply
2. Configure the member switches, as explained in Chapter 11,
“Configuring Member Switches” on page 209.
3. After configuring the master and member switches, verify that all the
units are powered off.
4. Cable the ports of the stack trunk. Refer to Chapter 13, “Cabling the
Networking Ports” on page 225.
5. Power on the switches of the stack. Refer to “Powering on the Stack”
on page 222.
6. Verify that the switches formed the stack. Refer to “Verifying the Stack”
on page 223.
7. Cable the networking ports. Refer to Chapter 13, “Cabling the
Networking Ports” on page 225.
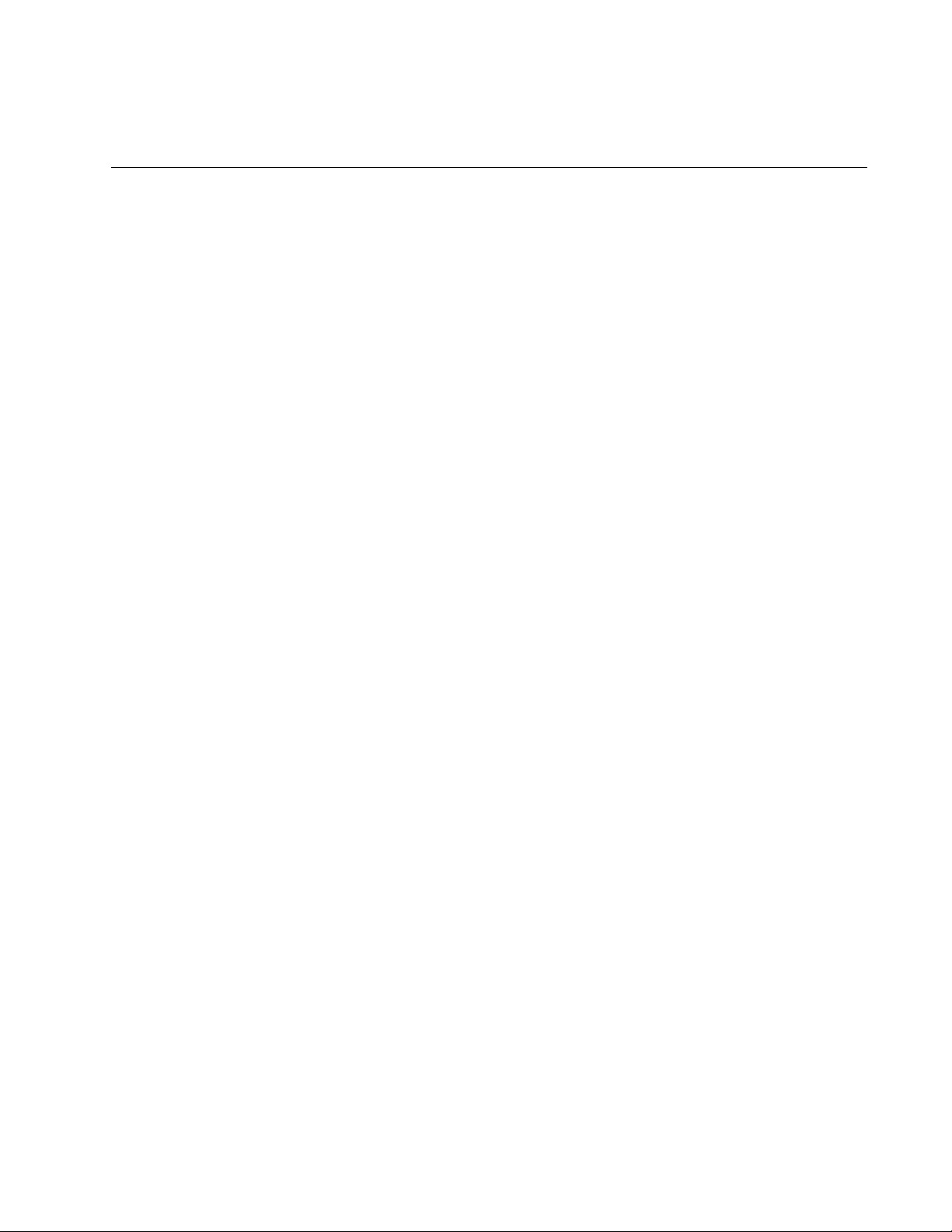
209
Chapter 11
Configuring Member Switches
This chapter contains the following sections:
“General Steps for Member Switches” on page 210
“Configuring a Member Switch - Part I” on page 212
“Configuring a Member Switch - Part II” on page 215
“Verifying a Member Switch” on page 218
“What to Do Next” on page 220
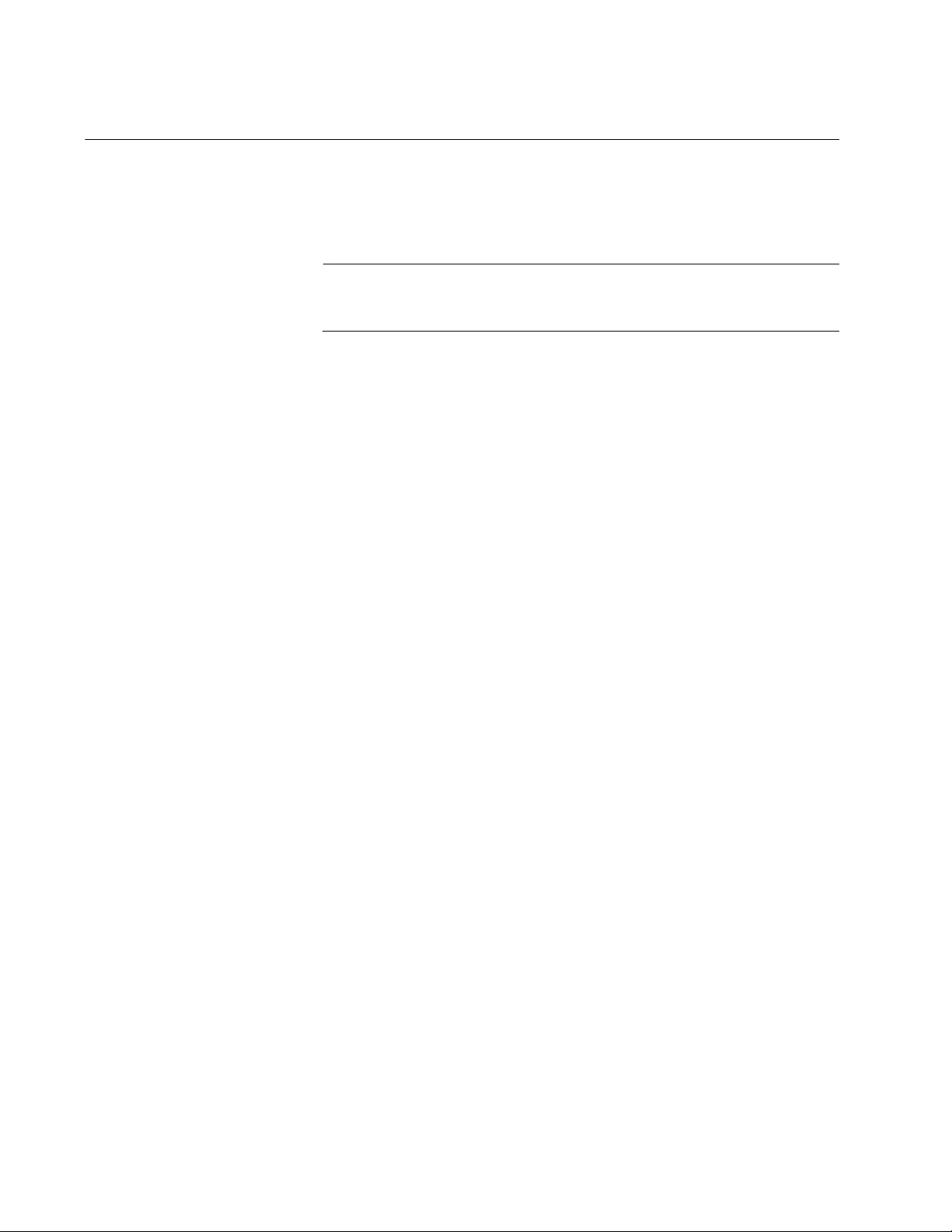
Chapter 11: Configuring Member Switches
210
General Steps for Member Switches
The procedure for configuring a member switch is divided into two parts.
Here are the general steps to “Configuring a Member Switch - Part I” on
page 212I:
Note
The procedures require resetting a member switch twice. Network
traffic will be lost if it is already connected to an active network.
1. Start a local management session on a member switch.
2. Verify the hardware with the SHOW SYSTEM ENVIRONMENT
command in the Privilege Exec mode.
3. Enable the VCStack feature with the STACK ENABLE command in the
Global Configuration mode.
4. Assign the member switch its unique ID number in the range 2 to 4,
with the STACK RENUMBER command in the Global Configuration
mode.
5. If the stack will have three or four switches, add the other member
switches as provisioned switches, with the SWITCH PROVISION
command.
6. Save your changes with the WRITE command in the Privilege Exec
mode.
7. Restart the switch with the REBOOT command.
Here are the general steps to “Configuring a Member Switch - Part II” on
page 215:
1. Start a new local management session.
2. Change the switch’s priority number to match its ID number, with the
STACK PRIORITY command in the Global Configuration mode.
3. Specify the types of transceivers to be used in slots 25, 29, 33, and 37
for the x950-28XSQ and x950-28XTQm switches, or in slots 49, 53,
57, 61 for the x950-52XSQ switch on the master and member switches
with the PLATFORM PORTMODE INTERFACE command.
4. Designate the ports of the stack trunk on the master and member
switches with the STACKPORT command in the port Interface mode.
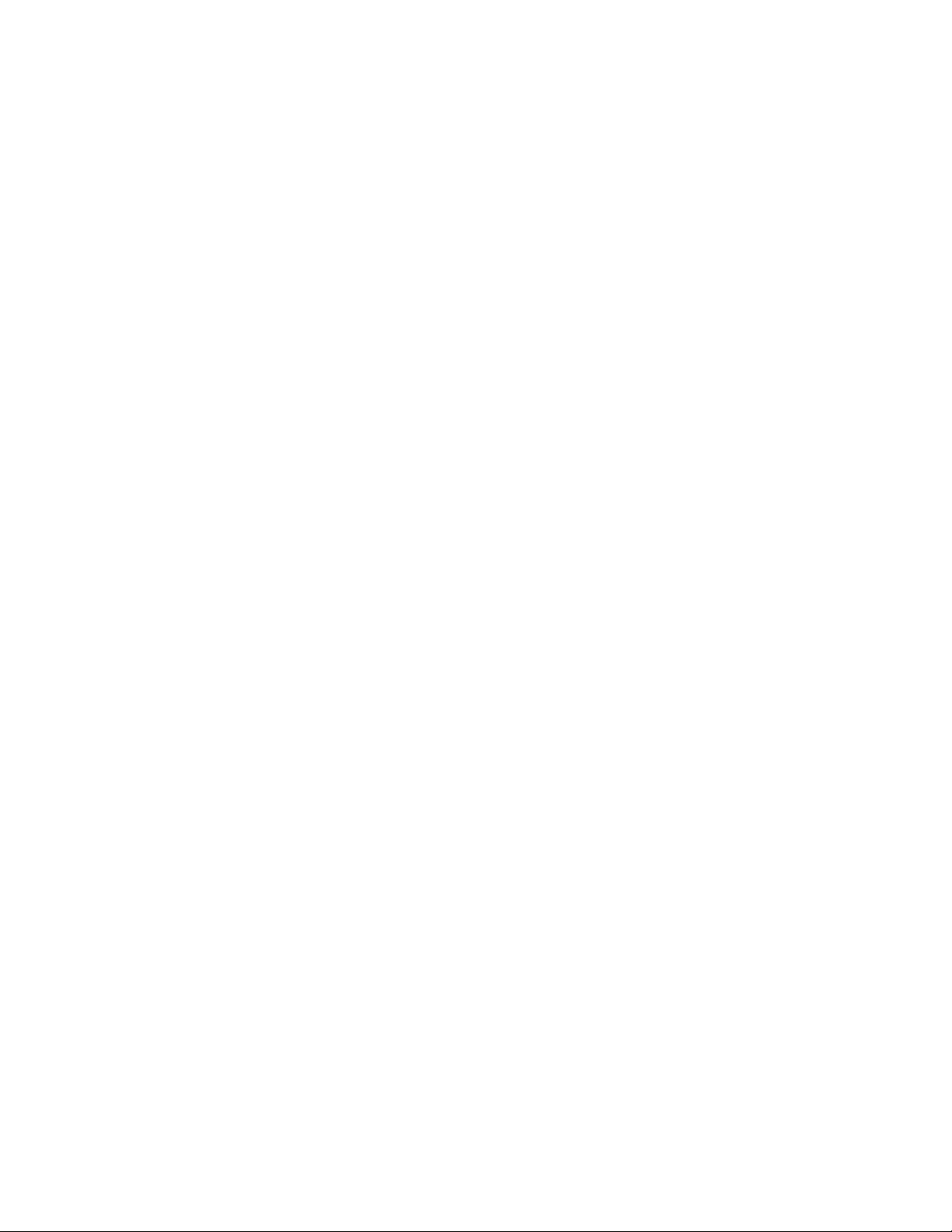
x950 Series Installation Guide for VCStack
211
5. Save your changes with the WRITE command in the Privilege Exec
mode.
6. Restart the switch with the REBOOT command.
7. Start a new local management session.
8. Verify the changes with the SHOW STACK and SHOW RUNNING-
CONFIG command.
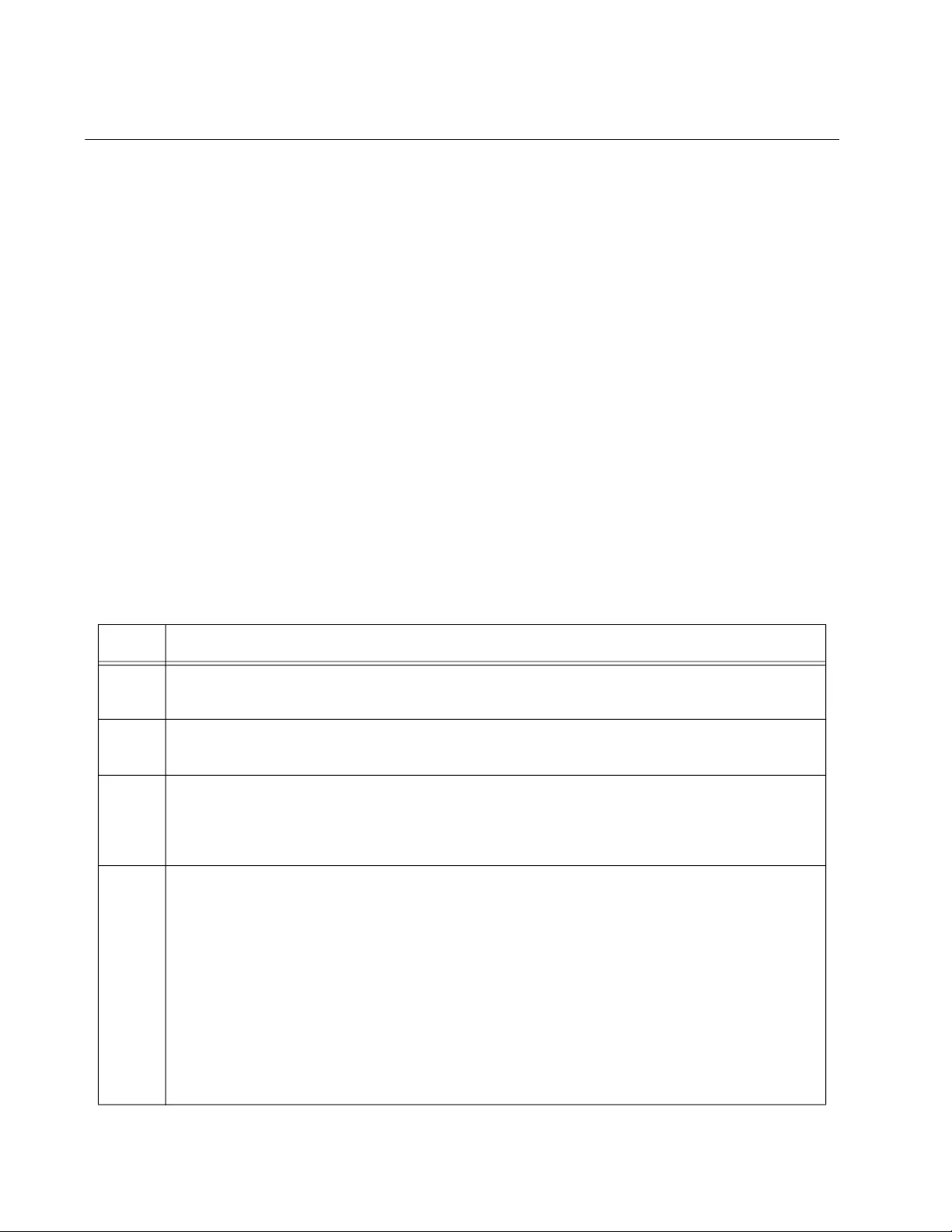
Chapter 11: Configuring Member Switches
212
Configuring a Member Switch - Part I
The instructions for configuring a member switch are divided into two
parts. In Part I you do the following:
Display the hardware status with the SHOW SYSTEM
ENVIRONMENT command.
Display the firmware version number with the SHOW VERSION
command.
Enable VCStack with the STACK ENABLE command.
Set the switch ID number with the STACK RENUMBER command.
Add other member switches with the SWITCH PROVISION
command.
Save the configuration and reboot the switch with the WRITE and
REBOOT commands.
Allied Telesis recommends filling out the worksheet in “Stacking
Worksheet” on page 93 before performing the procedures.
To configure a member switch, perform the procedure in Table 35.
Table 35. Configuring a Member Switch - Part I
Step Description and Command
1 Power on the member switch and wait two minutes for it to initialize the management
software. Refer to “Powering On a Switch” on page 192.
2 Start a local management session. Refer to “Starting a Local Management Session”
on page 196.
3 Enter the ENABLE command to move from the User Exec mode to the Privileged
Exec mode.
awplus> enable
4 Verify that the switch hardware is operating correctly, with the SHOW SYSTEM
ENVIRONMENT command. All components should have a status of Ok.
awplus# show system environment
Environment Monitoring Status
Overall Status: Normal
Resource ID: 1 Name: PSU Bay A (AT-PWR600)
ID Sensor (Units) Reading Low Limit High Limit Status
1 Device Present Yes - - Ok
2 Fan/Temperature Fault Yes - - Ok
.
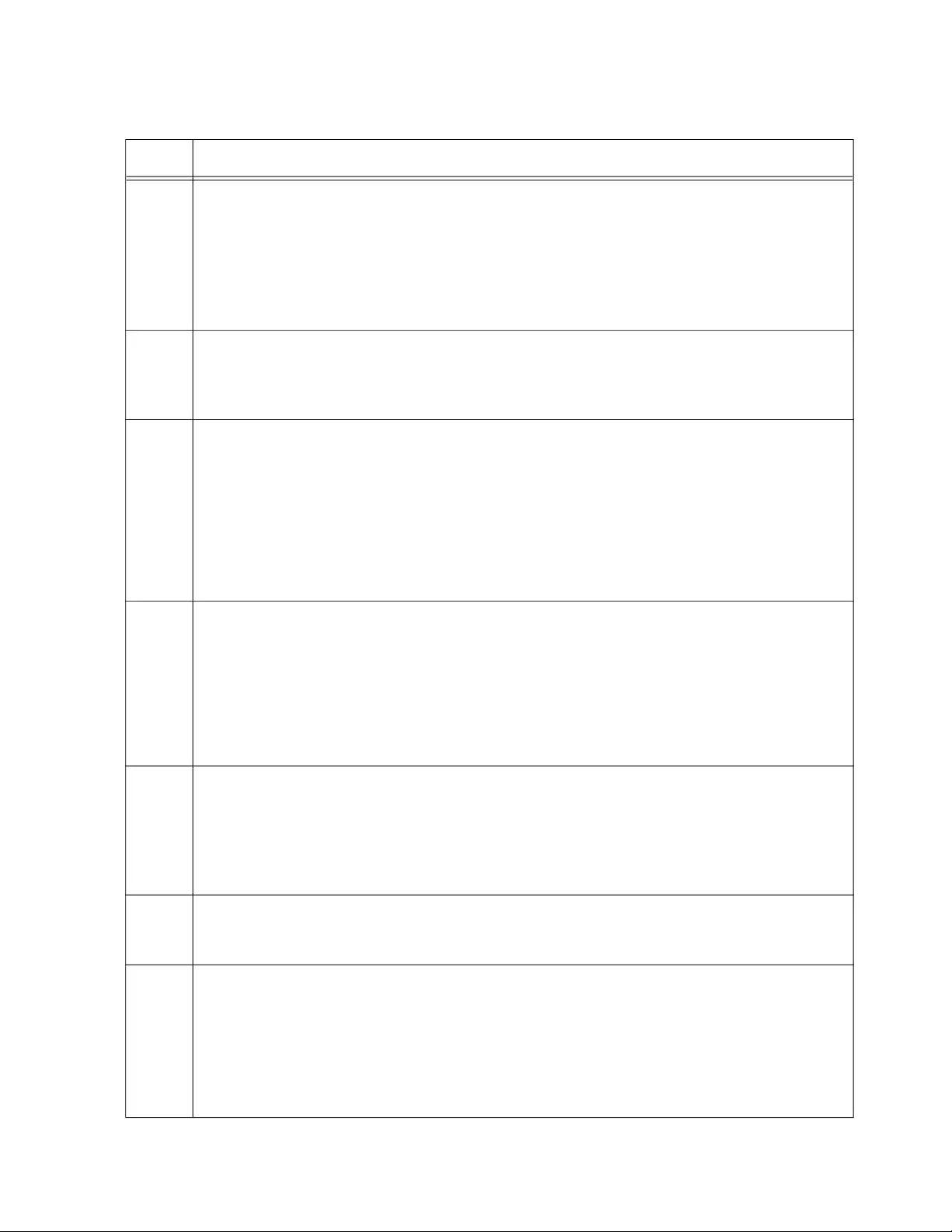
x950 Series Installation Guide for VCStack
213
5 Display the version number of the AlliedWare Plus operating software on the switch
by entering the SHOW VERSION command. Write down the version number in the
worksheet in “Stacking Worksheet” on page 93. After viewing the version numbers on
all the switches, you will compare them to confirm they all have the same version.
Switches with different versions will have to be updated.
awplus# show version
6 Move to the Global Configuration mode with the CONFIGURE TERMINAL command.
awplus# configure terminal
Enter configuration commands, one per line. End with CNTL/Z.
7 Activate VCStack on the switch with the STACK ENABLE command.
awplus(config)# stack enable
% Automatically enabling ‘stack virtual-mac’ to minimize disruption
form failovers.
% Please check that the new MAC 0000.cd37.0431 is unique within the
network.
% Save the config and restart the system for this change to take
effect.
8 Assign a unique ID number in the range of 2 to 4 to the member switch with the
STACK RENUMBER command. This example assigns the ID number 2 to the switch.
awplus(config)# stack 1 renumber 2
% Warning: Stacking is currently disabled.
% Warning: the new ID will not become effective until the stack-
member reboots.
% Warning: the boot configuration may now be invalid.
9Add the other member switches as provisioned switches to the member switch, with
the SWITCH PROVISION command, assigning them their unique IDs in the range of
2 to 4. This example adds two provisioned switches, with the IDs 3 and 4:
awplus(config)# switch 3 provision x950-28
awplus(config)# switch 4 provision x950-28
10 Return to the Privileged Exec mode.
awplus(config)# exit
11 Enter the WRITE command to save your change. If this is the first management
session, the switch adds the configuration file DEFAULT.CFG to flash memory, for
storing your configuration changes.
awplus# write
Building configuration ...
[OK]
Table 35. Configuring a Member Switch - Part I (Continued)
Step Description and Command
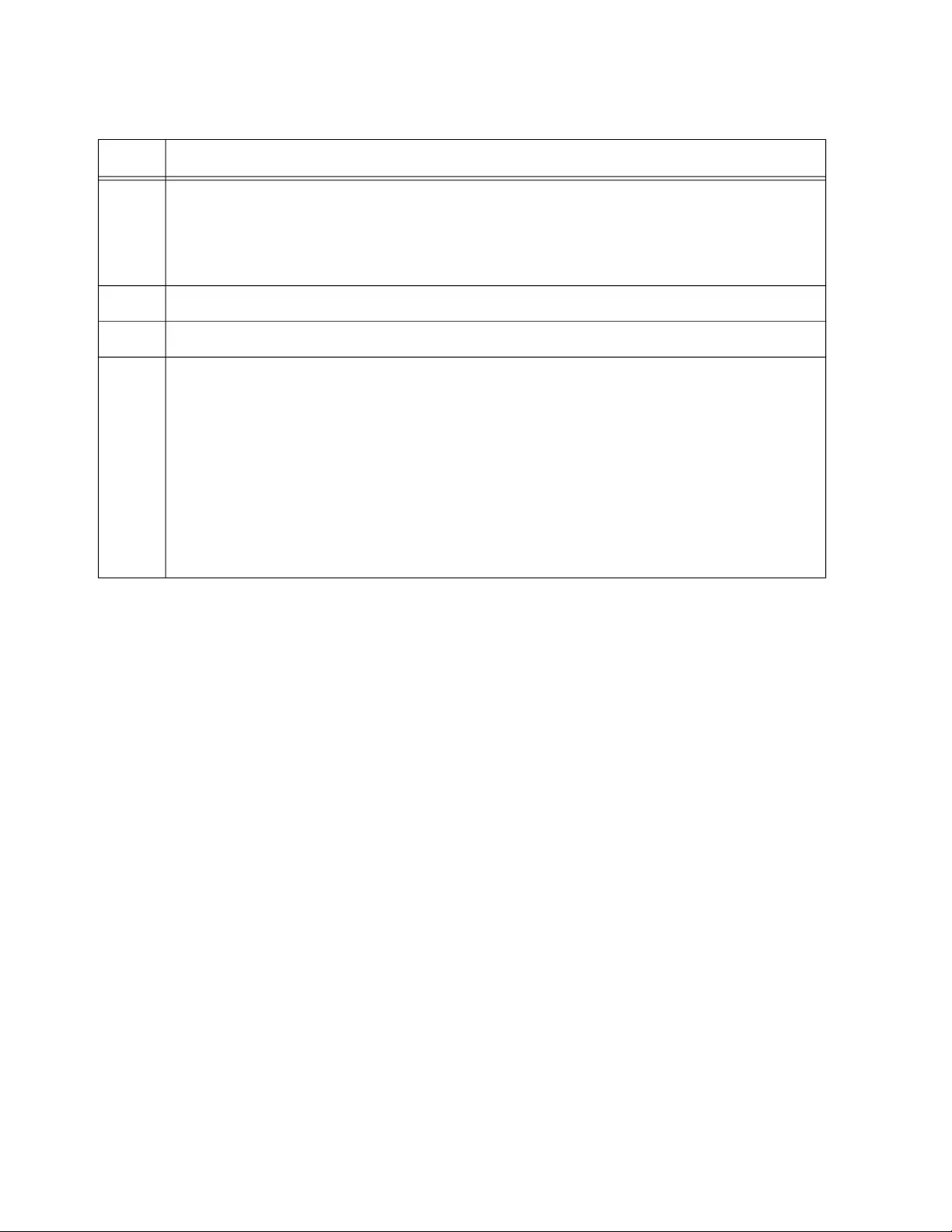
Chapter 11: Configuring Member Switches
214
12 Restart the switch with the REBOOT command.
awplus# reboot
reboot system? (y/n):
awplus#
13 Type “Y” for yes.
14 Wait two minutes for the switch to initialize its management software.
15 Check the ID LED on the front panel and do one of the following:
- If the ID LED is displaying the ID number you assigned to the switch, VCStack is
now enabled on the switch. Go to “Configuring a Member Switch - Part II” on
page 215.
- If the ID LED is displaying the wrong ID number for the switch, repeat this
procedure. Be sure to correctly enter the STACK RENUMBER command and to
save your changes with the WRITE command.
- If the ID LED is displaying “0,” VCStack is still disabled. Repeat this procedure. Be
sure to perform the STACK ENABLE command and to issue the WRITE command.
Table 35. Configuring a Member Switch - Part I (Continued)
Step Description and Command
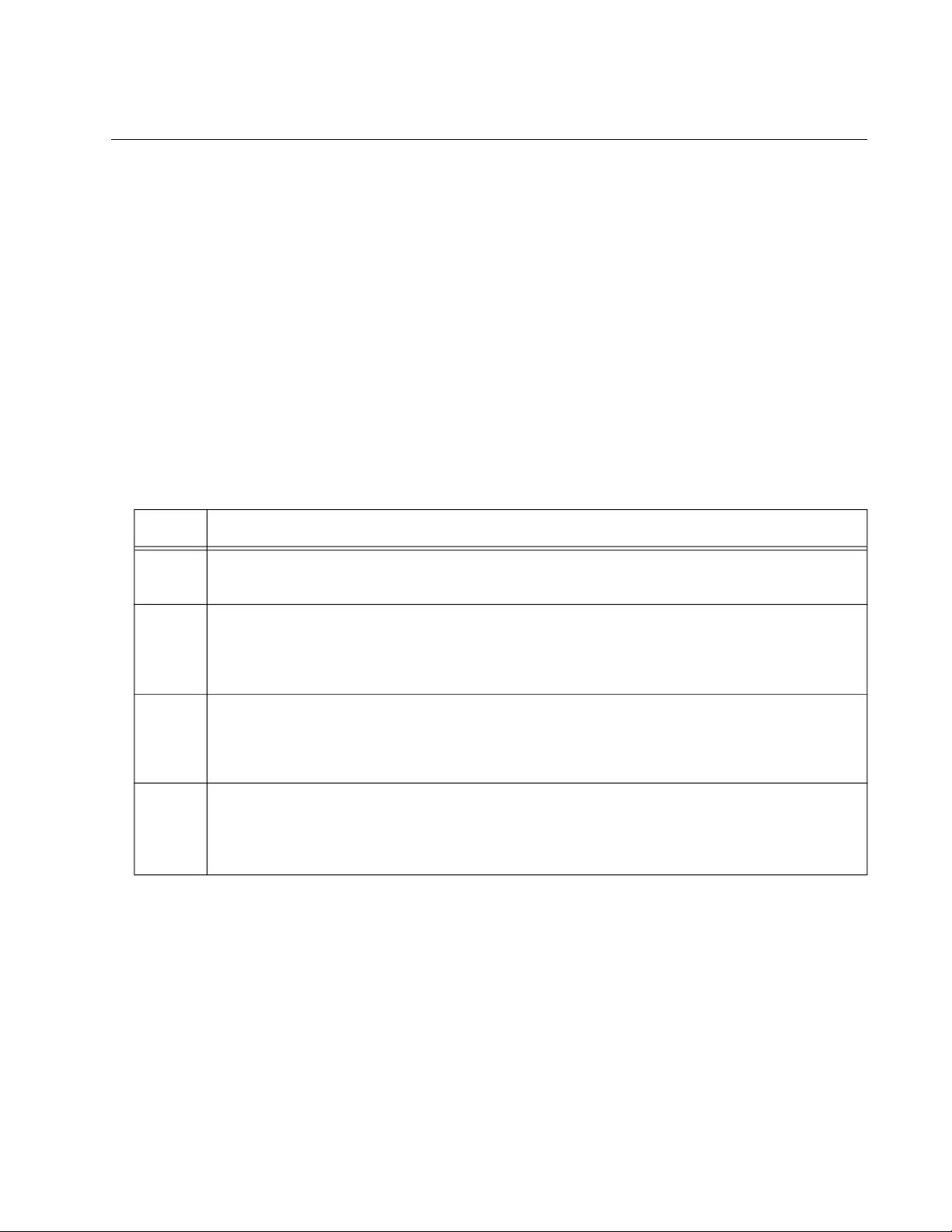
x950 Series Installation Guide for VCStack
215
Configuring a Member Switch - Part II
This section contains the second part to configuring member switches.
The steps show how to configure the following parameters:
Set the priority number of the switch to match its ID number, with
the STACK PRIORITY command.
Specify the types of transceivers to be used in slots 25, 29, 33, and
37 for the x950-28XSQ and x950-28XTQm switches, or in slots 49,
53, 57, 61 for the x950-52XSQ switch on the master and member
switches with the PLATFORM PORTMODE INTERFACE
command.
Designate the ports of the stack trunk with the STACKPORT
command. Refer to “Stack Trunks” on page 74.
To configure a member switch, perform the procedure in Table 36.
Table 36. Configuring a Member Switch - Part II
Step Description and Command
1 Start a new local management session on the member switch. Refer to “Starting a
Local Management Session” on page 196.
2 Enter the ENABLE command to move from the User Exec mode to the Privileged
Exec mode.
awplus> enable
3 Move to the Global Configuration mode with the CONFIGURE TERMINAL command.
awplus# configure terminal
Enter configuration commands, one per line. End with CNTL/Z.
4Change the switch’s priority to match its ID number, with the STACK PRIORITY
command. This example sets priority to 2 on a member switch with the ID 2:
awplus(config)# stack 2 priority 2
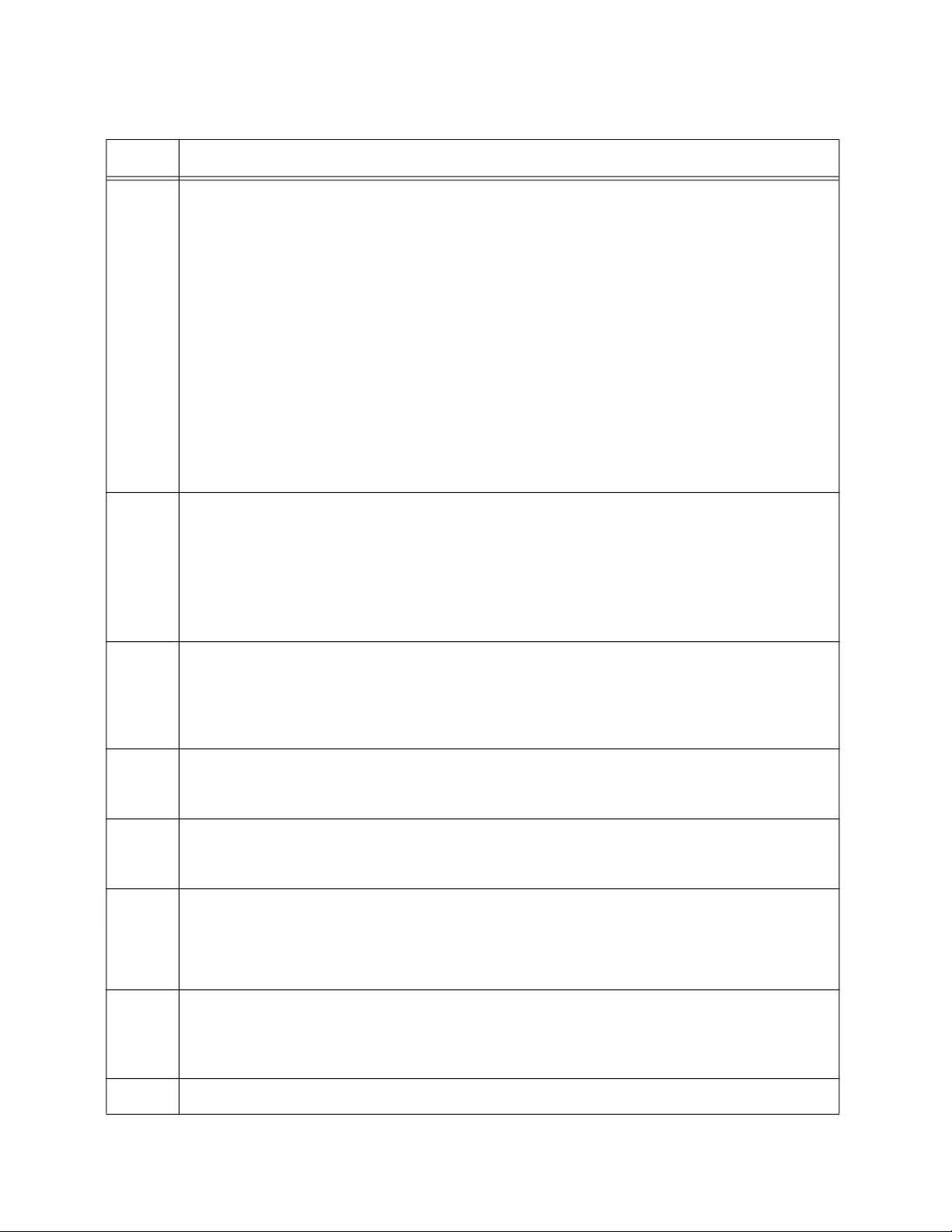
Chapter 11: Configuring Member Switches
216
5 Specify the types of transceivers to be used in slots 25, 29, 33, and 37 for the
x950-28XSQ and x950-28XTQm switches, or in slots 49, 53, 57, 61 for the x950-
52XSQ switch on the master (port1) and member switches with the PLATFORM
PORTMODE INTERFACE command. This step is very important if you will be using
100Gbps transceivers for the stack trunk. You can skip this step and configure the
ports after the stack is operating if you are not using 100Gbps transceivers for the
stack trunk. For more information, refer to “PLATFORM PORTMODE INTERFACE”
on page 188.
This example configures slots 33 and 37 for 100Gbps transceivers on a stack of four
switches.
awplus(config)# platform portmode interface port1.0.33-1.0.37 100g
awplus(config)# platform portmode interface port2.0.33-2.0.37 100g
awplus(config)# platform portmode interface port3.0.33-3.0.37 100g
awplus(config)# platform portmode interface port4.0.33-4.0.37 100g
6 Enter the port Interface modes of the ports to be the stack trunk on the master and
member switches with the INTERFACE command. The example command here
assumes a stack of four switches and that the switches will be using ports 33 and 37
for the stack trunk. Be sure to modify the command for you selected trunk ports.
awplus(config)# interface port1.0.33-1.0.37,port2.0.33-2.0.37,
port3.0.33-3.0.37,port4.0.33-4.0.37
7 Designate the ports as the stack trunk with the STACKPORT command.
awplus(config-if)# stackport
% Save the config and restart the system for this change to take
effect.
8 Return to the Global Configuration mode.
awplus(config-if)# exit
9 Return to the Privileged Exec mode.
awplus(config)# exit
10 Save your changes with the WRITE command.
awplus# write
Building configuration ...
[OK]
11 Restart the switch.
awplus# reboot
reboot system? (y/n):
12 Type “Y” for yes.
Table 36. Configuring a Member Switch - Part II (Continued)
Step Description and Command
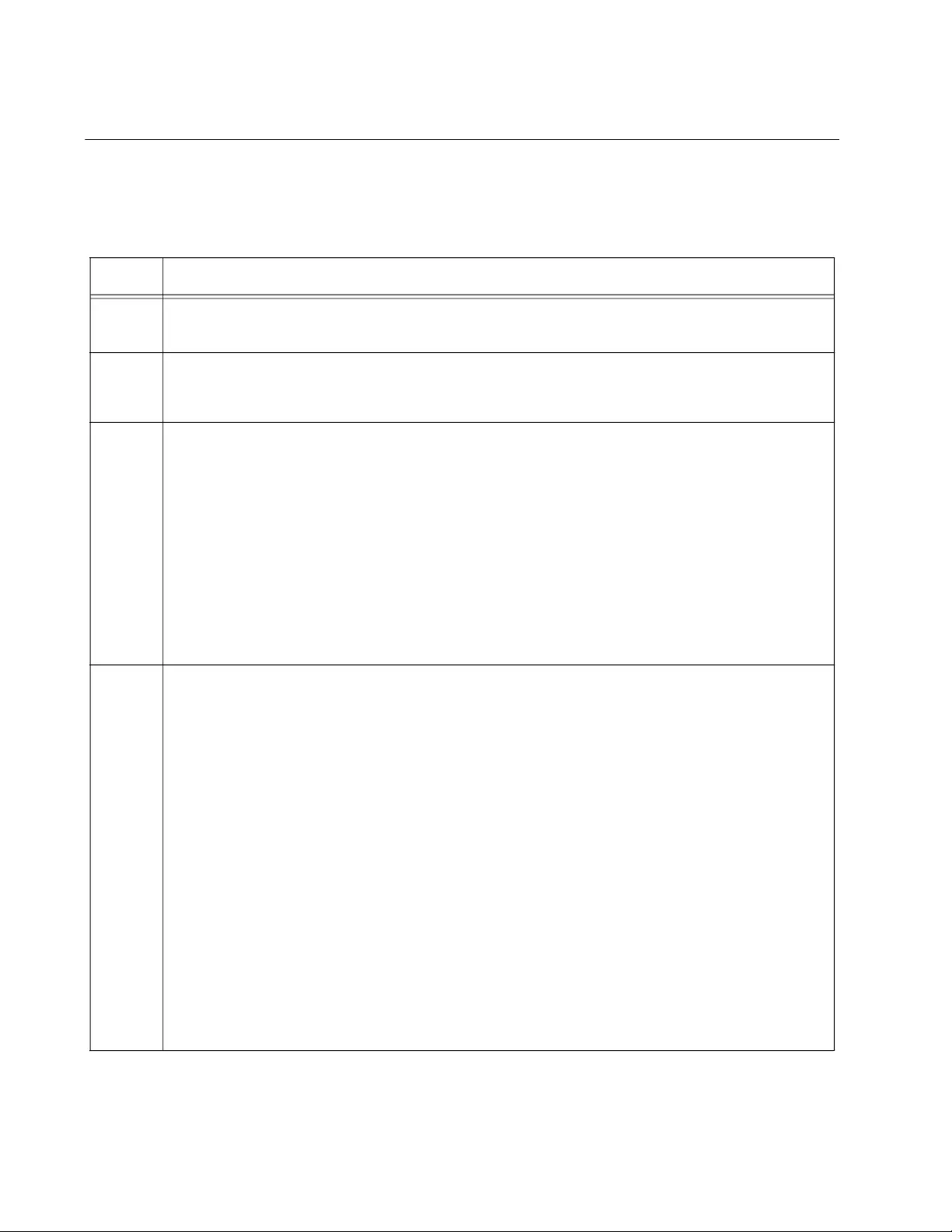
Chapter 11: Configuring Member Switches
218
Verifying a Member Switch
Perform the steps in Table 37 to confirm the configuration of a member
switch.
Table 37. Verifying a Member Switch
Step Description and Command
1 Start a local management session. Refer to “Starting a Local Management Session” on
page 196.
2 Move to the Privileged Exec mode.
awplus> enable
3 Enter the SHOW STACK command. The example here is for a member switch with the
ID 2, that will be in a stack of four switches:
awplus# show stack
Virtual Chassis Stacking summary information
ID Pending ID MAC address Priority Status Role
1 - - - - Provisioned
2 - e01a.ba56.c112 2 Ready Active Master
3 - - - - Provisioned
4 - - - - Provisioned
Operational Status Standalone unit
Stack MAC address 0000.ab56.478c (Virtual MAC)
4 Verify the display for the following:
- The table should have from two to four entries, depending on the number of switches
to be in the stack.
- Switch ID 1 will be for the master switch.
- The other entries are for the member switches. There should be one entry for each
member switch that will be in the stack. To add more entries, perform the SWITCH
PROVISION command in “Configuring a Member Switch - Part I” on page 212.
- The entry with the Ready status and Active Master role is the switch you are currently
managing. Its role will change to member after the stack is functioning.
- The switch’s priority should match its ID number. If it does not, perform the STACK
PRIORITY command in “Configuring a Member Switch - Part II” on page 215.
- The Operational Status should be Standalone Unit. This indicates that stacking is
enabled and the unit is operating as a stack of one switch. If the status is Stacking
Hardware Disabled, the stacking feature is disabled. Perform the STACK ENABLE in
“Configuring a Member Switch - Part I” on page 212. Be sure to save your changes
with the WRITE command.
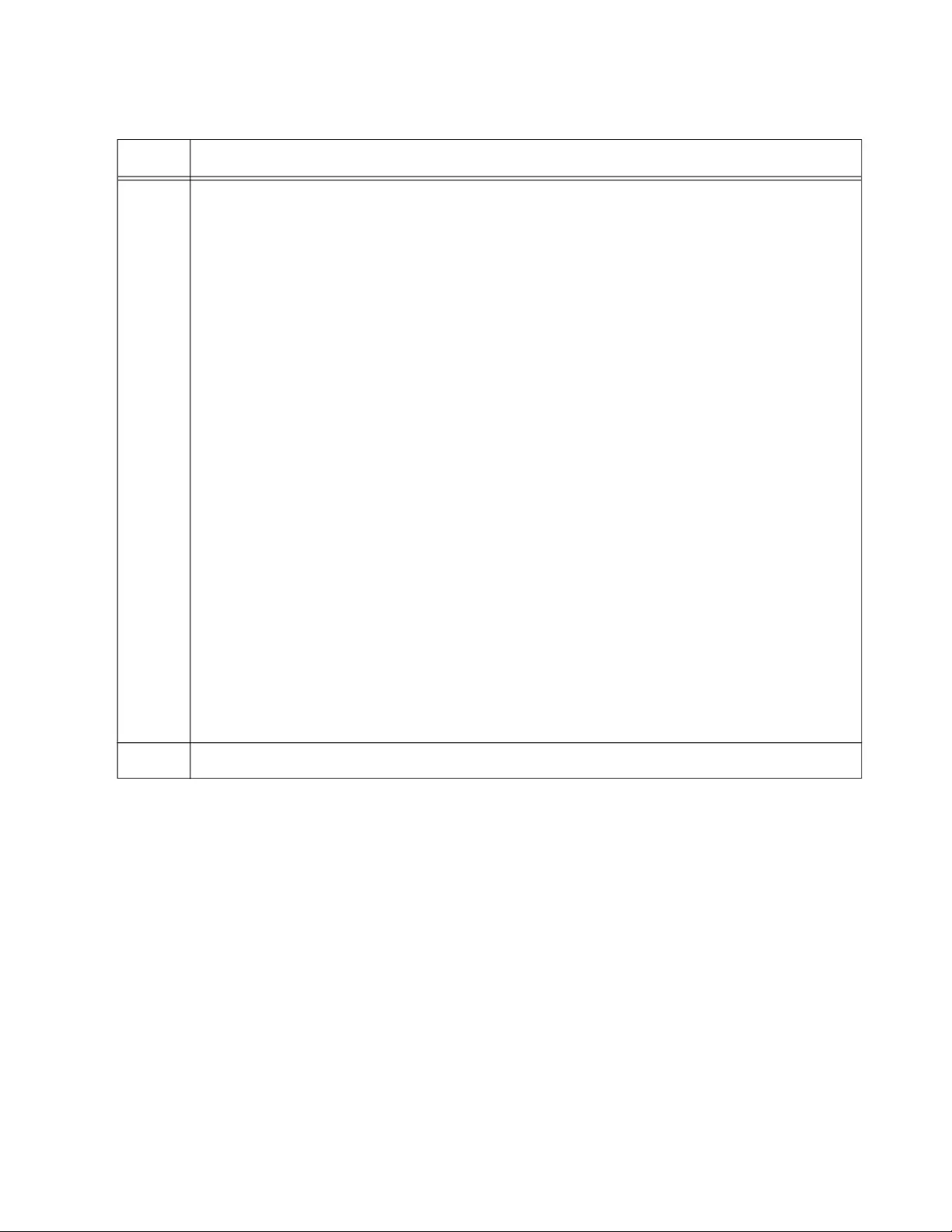
x950 Series Installation Guide for VCStack
219
5 Enter the SHOW RUNNING-CONFIG command and verify the following:
- Check the running configuration for SWITCH PROVISION commands. There should
be one command for each switch and the commands should designate x950
switches. Here are examples for a stack of four switches:
switch 1 provision x950-28
switch 2 provision x950-28
switch 3 provision x950-28
switch 4 provision x950-28
- Check the running configuration for STACKPORT commands. There should be one
command for each switch and the commands should designate the trunk ports. In this
example, ports 33 and 37 are designated as the trunk ports:
.
interface port1.0.33-1.0.37
stackport
.
interface port2.0.33-2.0.37
stackport
.
interface port3.0.33-3.0.37
stackport
.
interface port4.0.33-4.0.37
stackport
6Go to “What to Do Next,” next.
Table 37. Verifying a Member Switch (Continued)
Step Description and Command
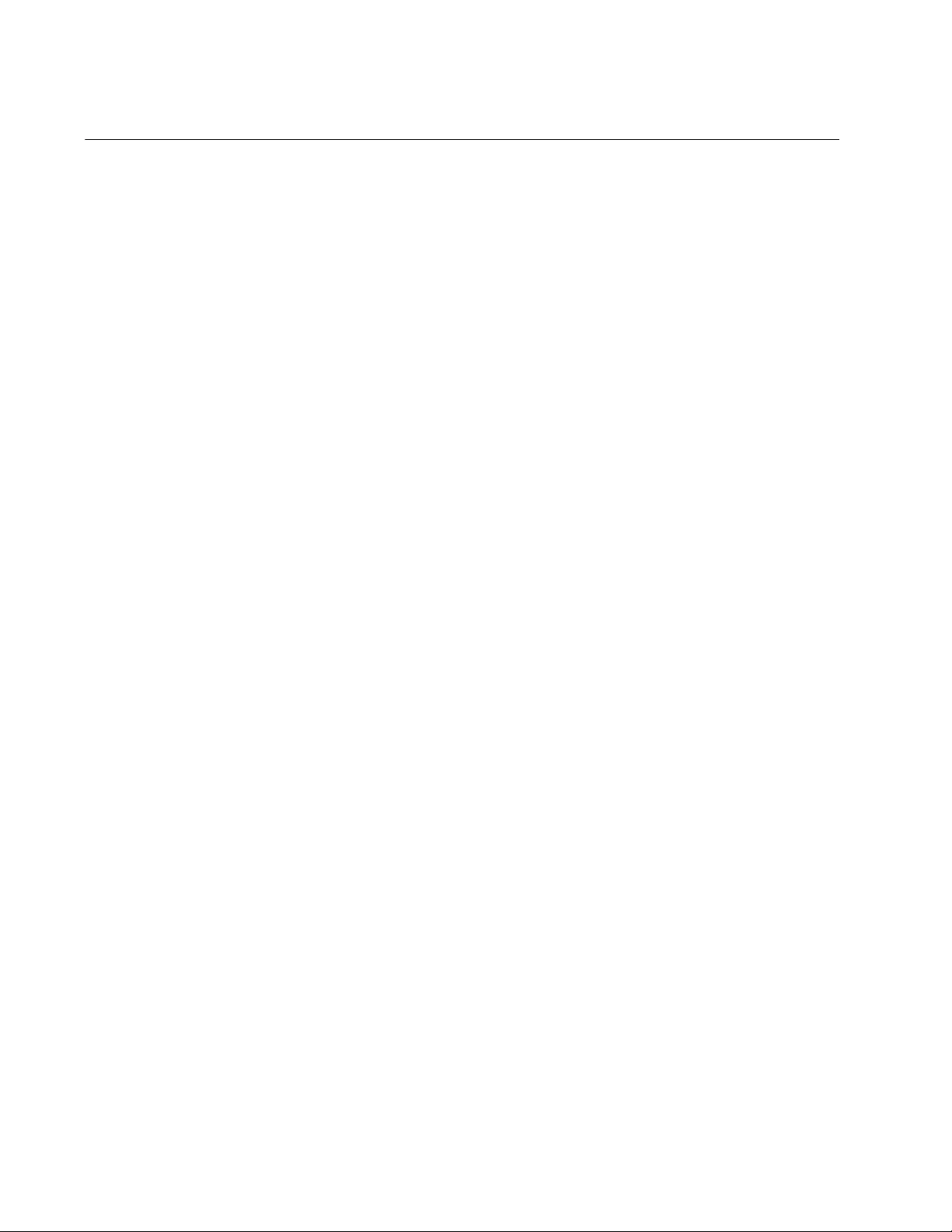
Chapter 11: Configuring Member Switches
220
What to Do Next
After configuring a member switch, do the following:
1. Power off the switch by performing the following:
For the DC power supply, power off the DC power source units.
For the AC power supply, disconnect the AC power cords from the
AC power sources. Refer to Figure 125 on page 208.
2. Repeat the procedures in this chapter to configure any additional
member switches.
3. If you have not already configured the master switch, perform
“Configuring the Master Switch - Part I” on page 200.
4. After configuring the master and member switches, verify that all the
units are powered off.
5. Cable the stacking ports on the master and member switches. Refer to
Chapter 13, “Cabling the Networking Ports” on page 225.
6. Power on the switches of the stack, as explained in “Powering on the
Stack” on page 222.
7. Verify that the switches have successfully formed the stack by
performing “Verifying the Stack” on page 223.
8. Cable the networking ports, as explained in Chapter 13, “Cabling the
Networking Ports” on page 225.
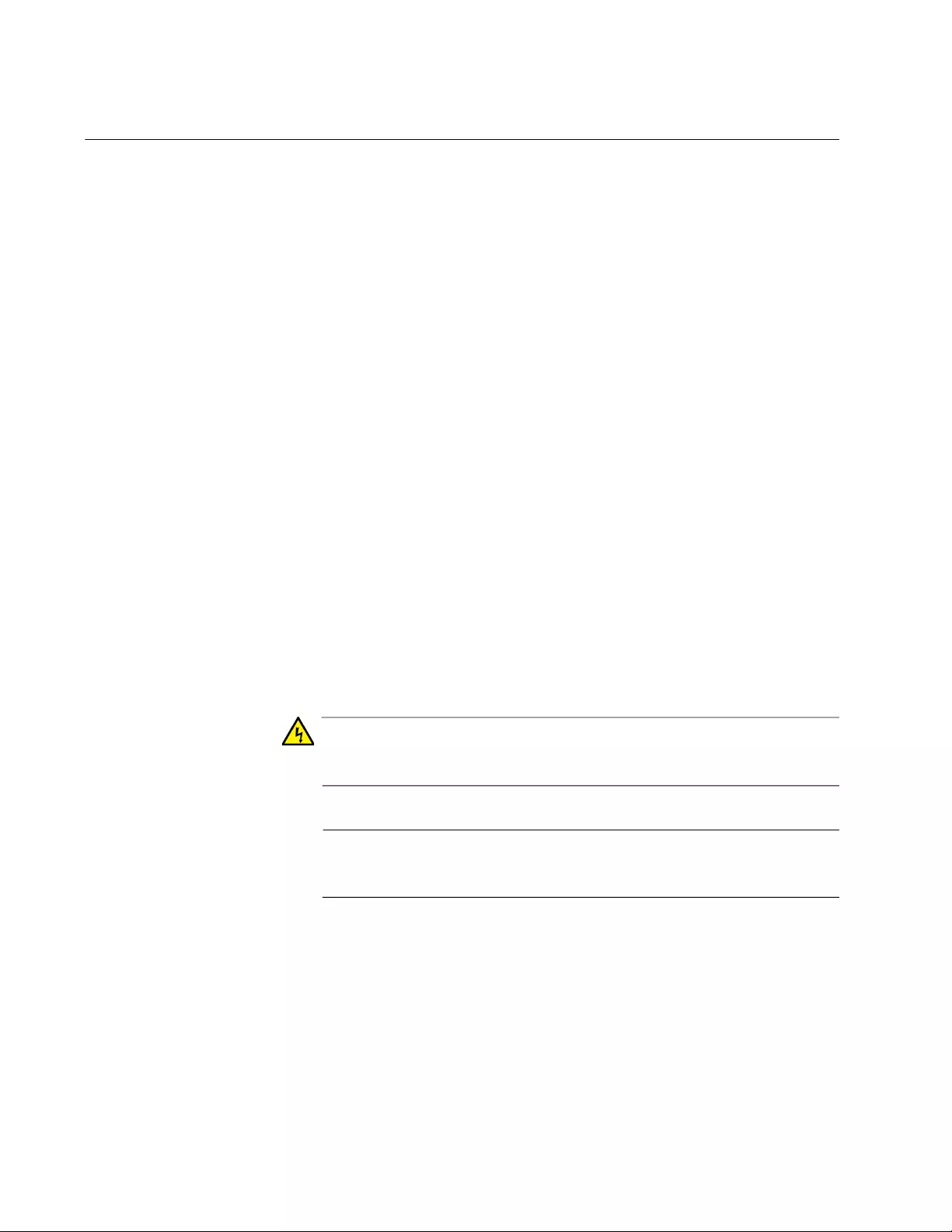
Chapter 12: Powering On and Verifying the Stack
222
Powering on the Stack
After configuring the master and member switches for stacking and
cabling the trunk ports, you are ready to power on the stack for the first
time. (If you want to monitor the power-on sequence, connect a terminal or
PC with a terminal emulator program to the Console port on any of the
switches).
To power on the stack for the first time, perform the following procedure:
1. Verify that all switches are powered off.
For the AC power supply, disconnect the AC power cord for the
power supply from the AC power source
For the DC power supply, power off the DC power source.
2. If you have not already cabled the trunk ports, do so now. Refer to
Chapter 13, “Cabling the Networking Ports” on page 225.
3. Power on all the switches at the same time.
For the AC power supply, see“Powering on the PWR600 AC
Power Supply” on page 192.
For the DC power supply, “Powering on the PWR600 DC Power
Supply” on page 194.
Refer to “Power Specifications” on page 268 for the power
specifications of the switches.
Warning
Power cord is used as a disconnection device. To de-energize
equipment, disconnect the power cord. E3
Note
Pluggable Equipment. The socket outlet shall be installed near the
equipment and shall be easily accessible. E5
4. Wait three minutes for the switches to form the stack.
5. Go to “Verifying the Stack” on page 223.
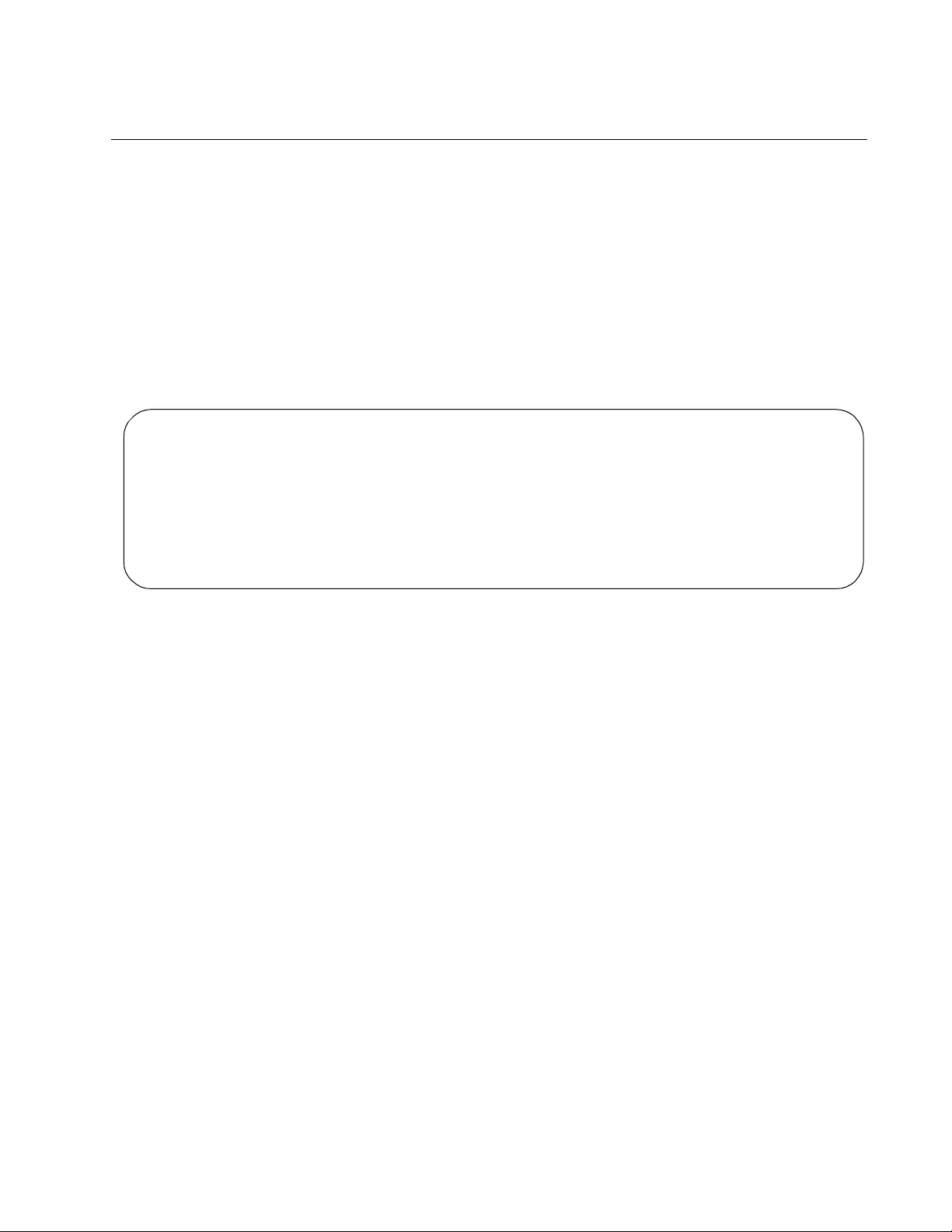
x950 Series Installation Guide for VCStack
223
Verifying the Stack
To verify the stack, perform the following procedure:
1. Start a local management session on any switch in the stack. Refer to
“Starting a Local Management Session” on page 196.
2. From the User Exec mode, enter the SHOW STACK command:
awplus> show stack
An example of the command for a stack of four switches is shown in
Figure 126.
Figure 126. SHOW STACK Command
Review the following items:
The command should list all the switches. If the list is incomplete,
refer to Chapter 15, “Troubleshooting” on page 257.
The Operational Status field should be “Normal operations” to
indicate that all the trunk ports are operating normally.
If the Operational Status field is displaying “Not all stack ports are
up,” one or more trunk ports are not being used or cannot establish
links with their counterparts. For more information, refer to Chapter
15, “Troubleshooting” on page 257.
3. Go to Chapter 13, “Cabling the Networking Ports” on page 225, to
complete the installation.
awplus> show stack
Virtual Chassis Stacking summary information
ID Pending ID MAC address Priority Status Role
1 - e01a:ea20:8011 1 Ready Active Master
2 - e01a:ea20:ee45 2 Ready Member
3 - e01a:ea20:8a98 3 Ready Member
4 - e01a:ea20:1b67 4 Ready Member
Operational Status Normal operations
Stack MAC address 0015:774f:ed30
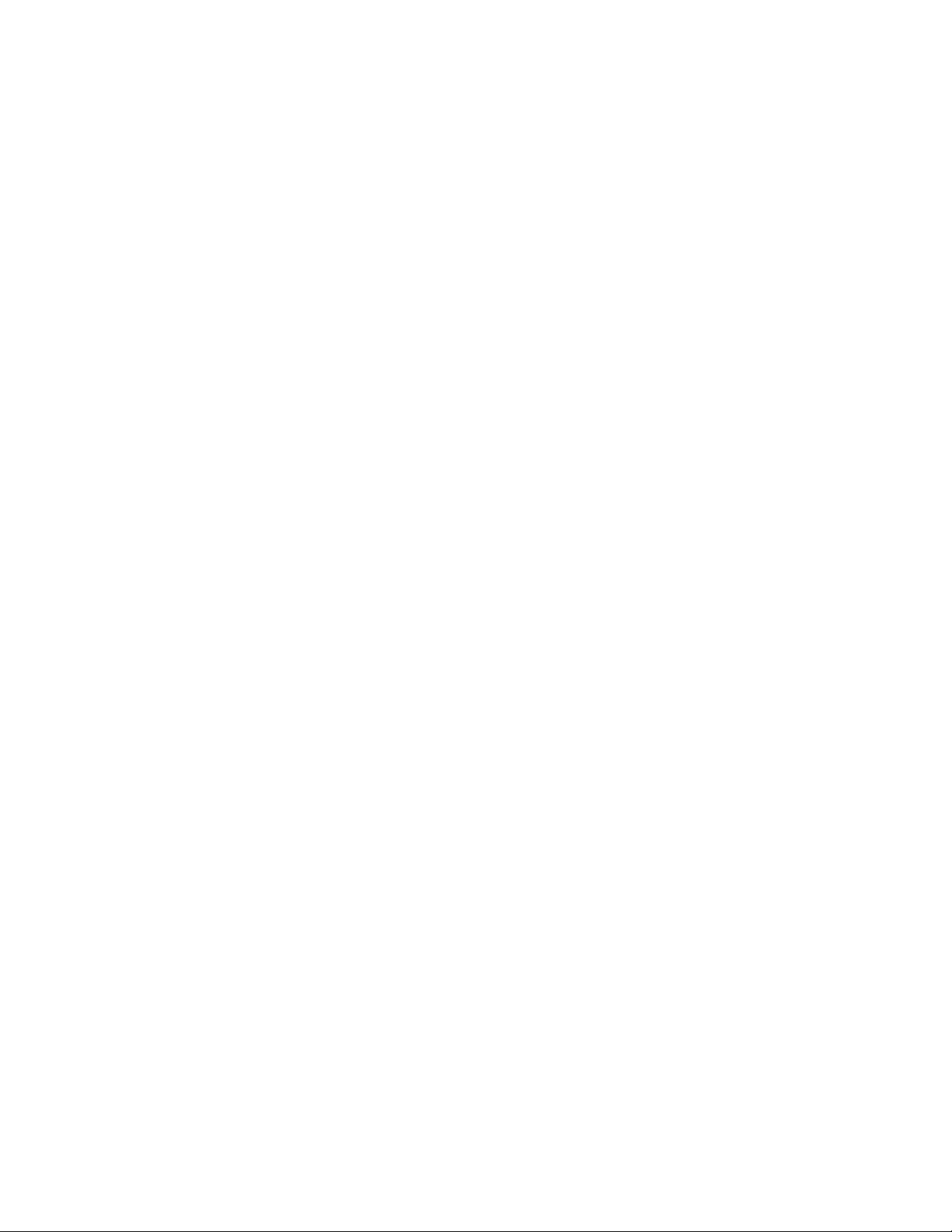
Chapter 12: Powering On and Verifying the Stack
224
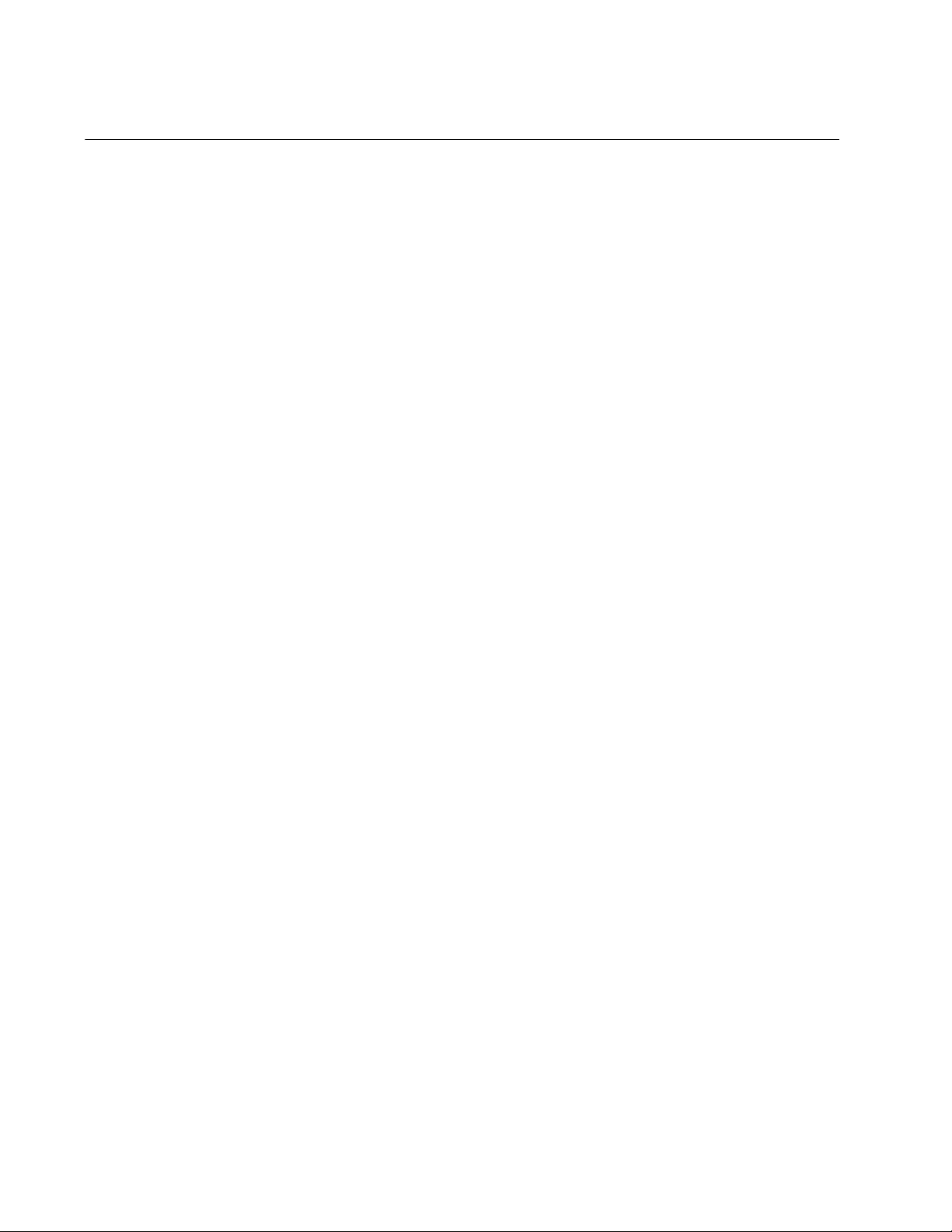
Chapter 13: Cabling the Networking Ports
226
Cabling Twisted Pair Ports
This section applies to the twisted pair ports on the following products:
x950-28XTQm Switch
XEM2-8XSTm Line Card
XEM2-12XT Line Card
XEM2-12XTm Line Card
Here are the cabling guidelines:
Here are the minimum cable requirements:
– 100Mbps - Standard TIA/EIA 568-B-compliant
Category 3 unshielded cabling.
– 1/2.5/5Gbps - Standard TIA/EIA 568-A-compliant
Category 5 or TIA/EIA 568-B-compliant Enhanced
Category 5 (Cat 5e) unshielded cabling.
– 10Gbps -Standard TIA/EIA 568-C-compliant
Category 6a unshielded cabling.
The connectors on the cables should fit snugly into the ports, and
the tabs should lock the connectors into place.
The default speed setting for the ports is Auto-Negotiation. This
setting is appropriate for ports connected to network devices that
also support Auto-Negotiation.
The ports must be set to Auto-Negotiation, the default setting, to
operate at 1Gbps or higher speeds.
The ports support full-duplex only.
Do not attach cables to ports of static or LACP port trunks until
after you have configured the ports on the switch. Otherwise, the
ports will form network loops that can adversely affect network
performance.

x950 Series Installation Guide for VCStack
227
Guidelines to Handling Twisted Pair or Fiber Optic Transceivers
Please review the following guidelines before installing twisted pair or fiber
optic transceivers:
Transceivers are hot-swappable. You can install them while the
chassis is powered on.
For a list of supported transceivers, refer to the product data sheet
on the Allied Telesis web site.
The operational specifications and fiber optic cable requirements
are provided in the documents included with the transceivers.
You should install transceivers in XEM2 line cards before
connecting their fiber optic cables.
Fiber optic transceivers are dust sensitive. Always keep the plug in
the optical bores when a fiber optic cable is not installed, or when
you store the transceiver. When you do remove the plug, keep it for
future use.
Repetitive removal or insertion of transceivers can lead to
premature failures.
100Gbps transceivers for XEM2-1CQ Line Cards have handles.
Use the handles when installing or removing transceivers. An
example is shown in Figure 127.
Figure 127. Handle on 100Gbps Transceivers for XEM2-1CQ Line Cards
Caution
Transceivers can be damaged by static electricity. Be sure to
observe all standard electrostatic discharge (ESD) precautions,
such as wearing an antistatic wrist strap, to avoid damaging the
devices. E92
Handle
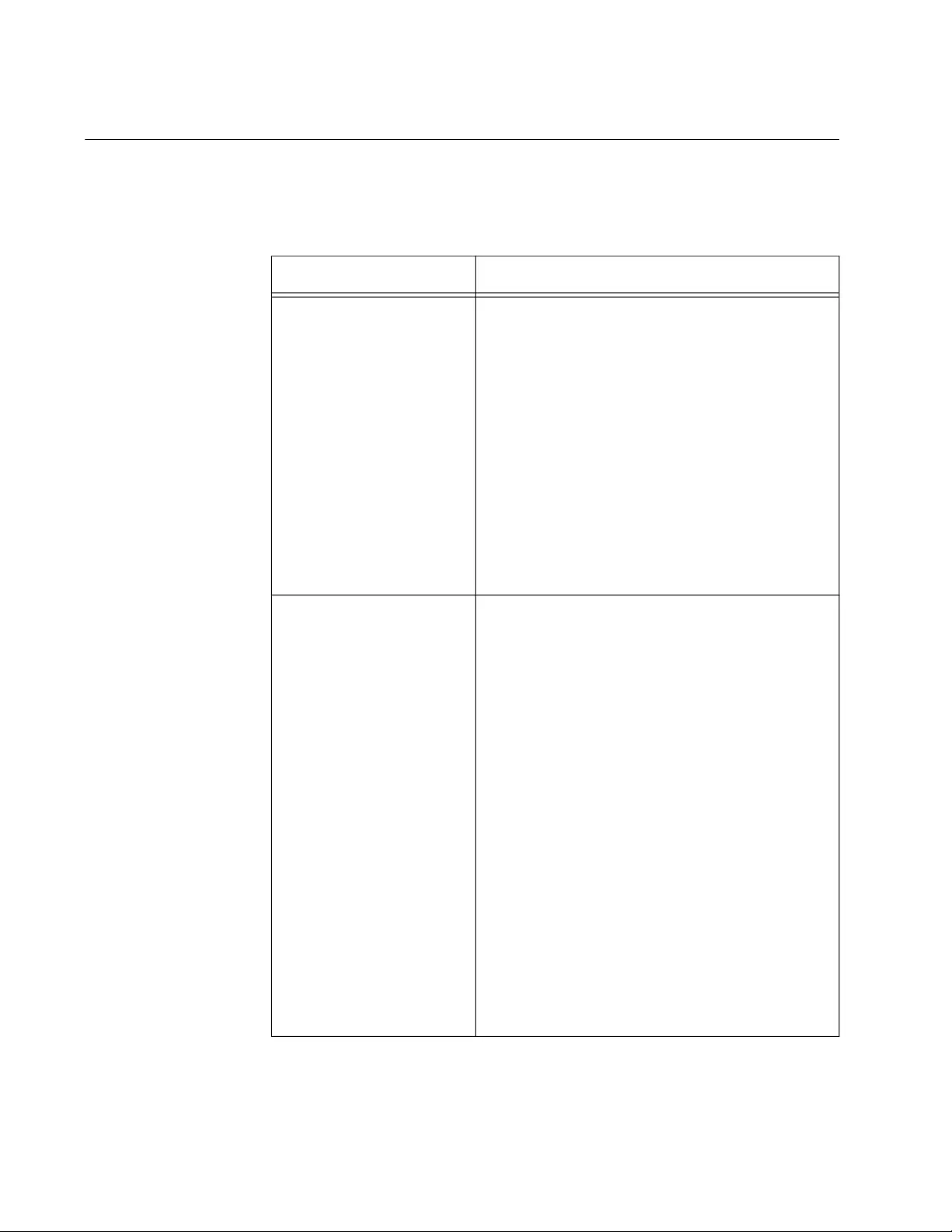
Chapter 13: Cabling the Networking Ports
228
Installing Transceivers
Table 38 lists the types of transceivers supported by the base transceiver
slots. Refer to the product data sheet for a list of approved transceivers.
Table 38. Transceivers for the Base Transceiver Slots
Base Ports Fiber Optic Transceiver
Ports 1 to 24 on the
x950-28XSQ switch
Ports 1 to 48 on the
x950-52XSQ switch
1Gbps SFP or 10Gbps SFP+ transceivers:
- 1Gbps SX/LX SFP transceivers
- 10Gbps SR/LR SFP+ fiber optic
transceivers
- 1/10Gbps SP10T transceiver with RJ-45
connector
- 10Gbps SP10TW direct attach twinax
cables with SFP+ transceiver-style
connectors
- 1/2.5/5/10Gbps SP10TM transceivers with
RJ-45 connectors
Ports 25, 29, 33, and 37
on the x950-28XSQ and
x950-28XTQm switches
Ports 49, 53, 57, and 61
on the x950-52XSQ
switch
100Gbps QSFP28 transceivers:
- QSFP28SR4 transceiver - Maximum
operating distance of 70m (230 ft) or 100m
(328 ft) with 12-strand OM3 or OM4 fiber
optic cable, respectively. Requires a MPO
pluggable optical connector.
- QSFP28LR4 transceiver - Operating range
of 2m (6.6 ft) to 10km (6.2 mi). Requires
single-mode fiber optic cable with a duplex
LC connector.
40Gbps QSFP+ transceivers, direct attach
cables, and breakout cables:
- QSFPSR4 transceiver - requires 12-strand
OM4 fiber optic cable and has a maximum
operating distance of 150m (492 ft).
- QSFPLR4 transceiver - requires single-
mode fiber optic cable and has an operating
range of 2 meters (6.6 ft) to 10km (6.2 mi).
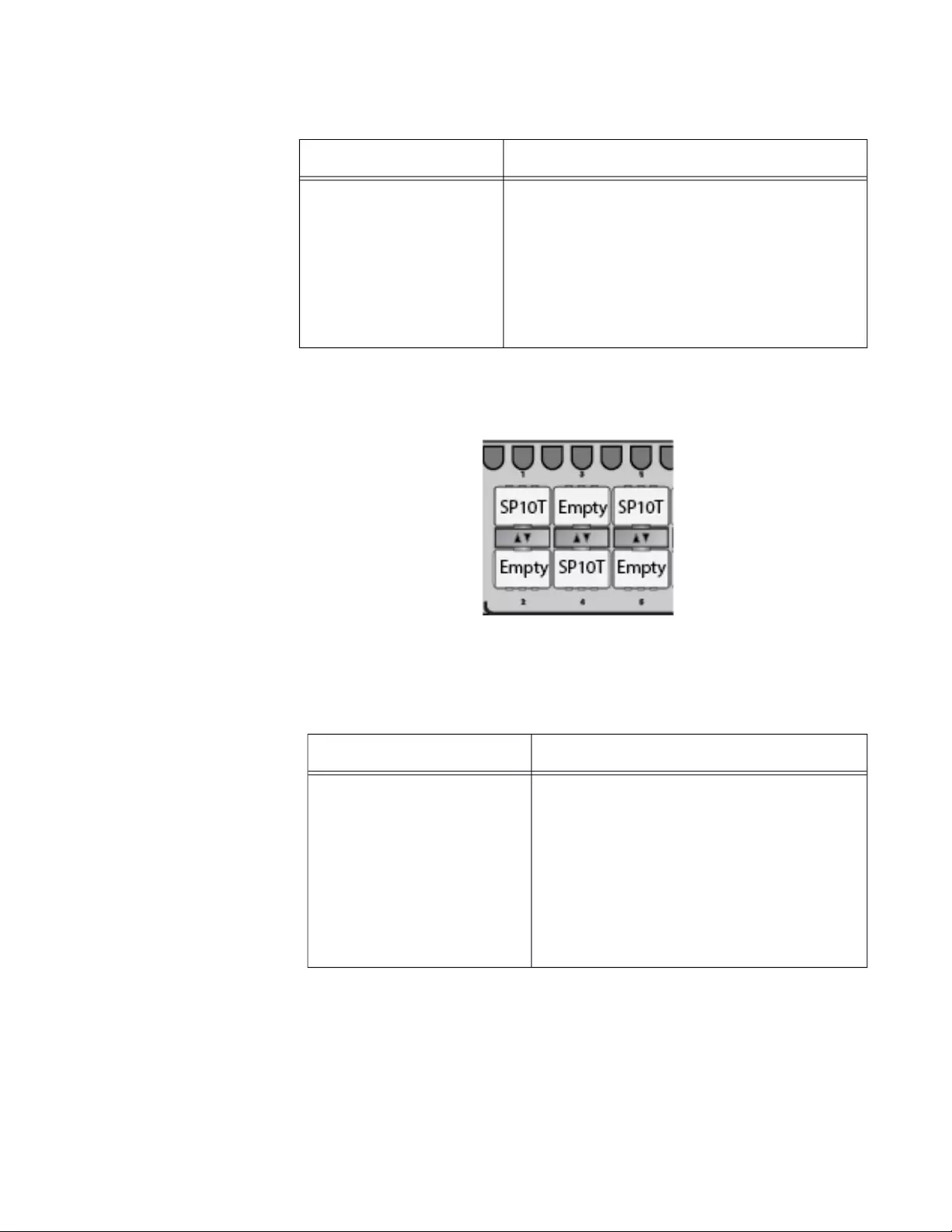
x950 Series Installation Guide for VCStack
229
SP10T transceivers with RJ-45 connections require that adjacent ports be
left empty to prevent overheating. Refer to Figure 128.
Figure 128. SP10T Transceivers
Table 39 lists the types of transceivers supported by XEM2 Line Cards.
Base ports 25, 29, 33,
and 37 on the
x950-28XSQ and
x950-28XTQm switches
Base ports 49, 53, 57,
and 61 on the
x950-52XSQ switch
- QSFP1CU and QSFP3CU direct attach
cables in lengths of 1 and 3 meters,
respectively.
--QSFP-4SFP10G-3CU and
QSFP-4SFP10G-5CU breakout cables in
lengths of 3 and 5 meters, respectively.
Table 39. Transceivers for XEM2 Ethernet Line Cards
Ethernet Line Card Transceiver
XEM2-8XSTm 1Gbps SFP or 10Gbps SFP+ transceivers:
- 1Gbps SX or LX SFP
- 10Gbps SR or LR SFP+
- 10Gbps one meter SP10TW1, three
meter SP10TW3, and seven meter
SP10TW7 direct attach twinax cables,
with SFP+ transceiver-style connectors
Table 38. Transceivers for the Base Transceiver Slots (Continued)
Base Ports Fiber Optic Transceiver
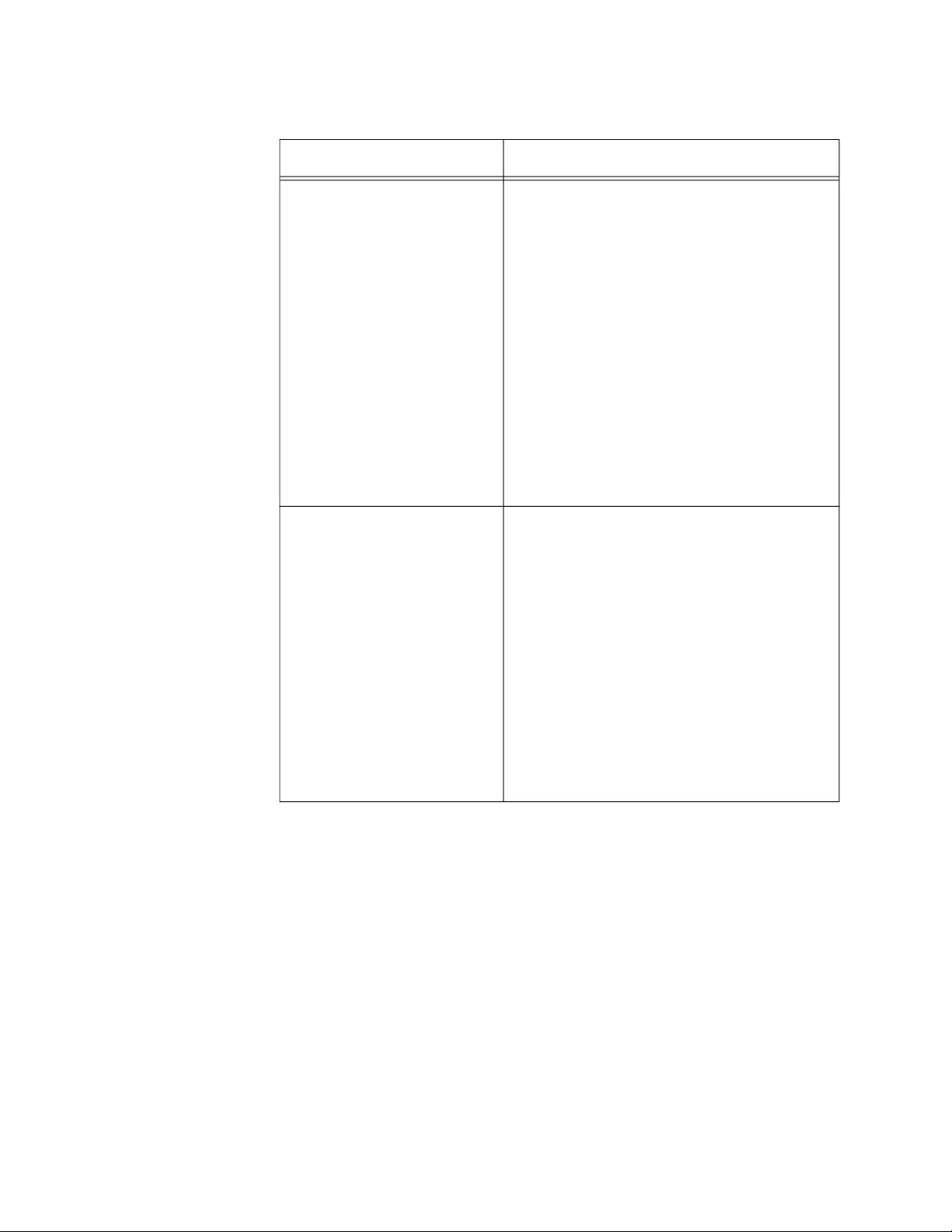
Chapter 13: Cabling the Networking Ports
230
XEM2-12XS 1Gbps SFP or 10Gbps SFP+ transceivers:
- 1Gbps SX or LX SFP fiber optic
transceivers
- 10Gbps SR or LR SFP+ fiber optic
transceivers
- 10Gbps one meter SP10TW1, three
meter SP10TW3, and seven meter
SP10TW7 direct attach twinax cables
with SFP+ transceiver-style connectors
(The XEM2-12XS v2 Card does not
support the SP10TW7 cable.)
- 1/2.5/5/10Gbps SP10TM transceivers
with RJ-45 connectors
XEM2-4QS 40Gbps QSFP+ transceivers:
- QSFPSR4 fiber optic transceiver -
Maximum operating distance of 150
meters (492 feet) with 12-strand OM4
fiber optic cable.
- QSFPLR4 fiber optic transceiver -
Operating range of 2 meters (6.6 feet) to
10 kilometers (6.2 miles) with single-
mode fiber optic cable.
- QSFP1CU and QSFP3CU direct attach
cables - Lengths of 1 and 3 meters,
respectively.
Table 39. Transceivers for XEM2 Ethernet Line Cards (Continued)
Ethernet Line Card Transceiver
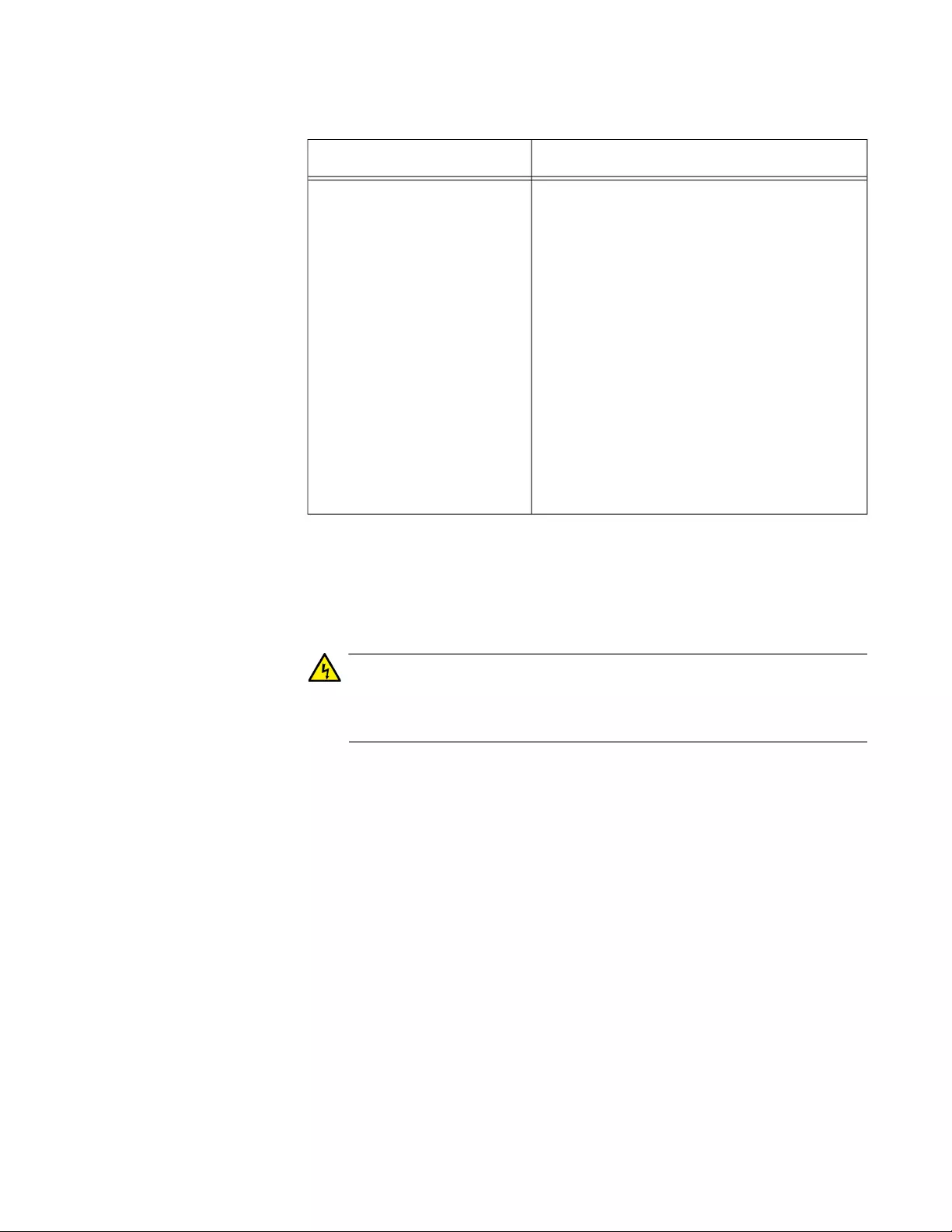
x950 Series Installation Guide for VCStack
231
Please review “Guidelines to Handling Twisted Pair or Fiber Optic
Transceivers” on page 227 before performing the procedure.
Your transceivers may look different than those shown in the following
illustrations.
Warning
The temperature of an operational transceiver can exceed 70° C
(158° F). Exercise caution when removing or handling transceivers
with unprotected hands. E43
To install a fiber optic transceiver, perform the following procedure:
1. Select a port for the transceiver.
2. If the selected port has a dust cover, remove it.
3. Remove the transceiver from its shipping container and store the
packaging material in a safe location.
4. Orient the transceiver and slide it into the port until it clicks into place.
The correct orientation depends on the line card and transceiver:
Base ports 1 to 24 and XEM2-8XSTm and XEM2-12XS Line Cards
- To install a transceiver in an odd numbered port, position it with
its handle on top. To install a transceiver in an even numbered
port, position it with its handle on the bottom. Refer to Figure 129
on page 232.
XEM2-1CQ 100Gbps QSFP28 transceivers:
- QSFP28SR4 fiber optic transceiver -
Maximum operating distance of 70m
(230 ft) or 100m (328 ft) with 12-strand
OM3 or OM4 fiber optic cable,
respectively. Requires a MPO pluggable
optical connector.
- QSFP28LR4 fiber optic transceiver -
Operating range of 2m (6.6 ft) to 10km
(6.2 mi). Requires single-mode fiber
optic cable with a duplex LC connector.
- QSFP28-1CU and QSFP28-3CU direct
attach cables in lengths of one and three
meters, respectively.
Table 39. Transceivers for XEM2 Ethernet Line Cards (Continued)
Ethernet Line Card Transceiver
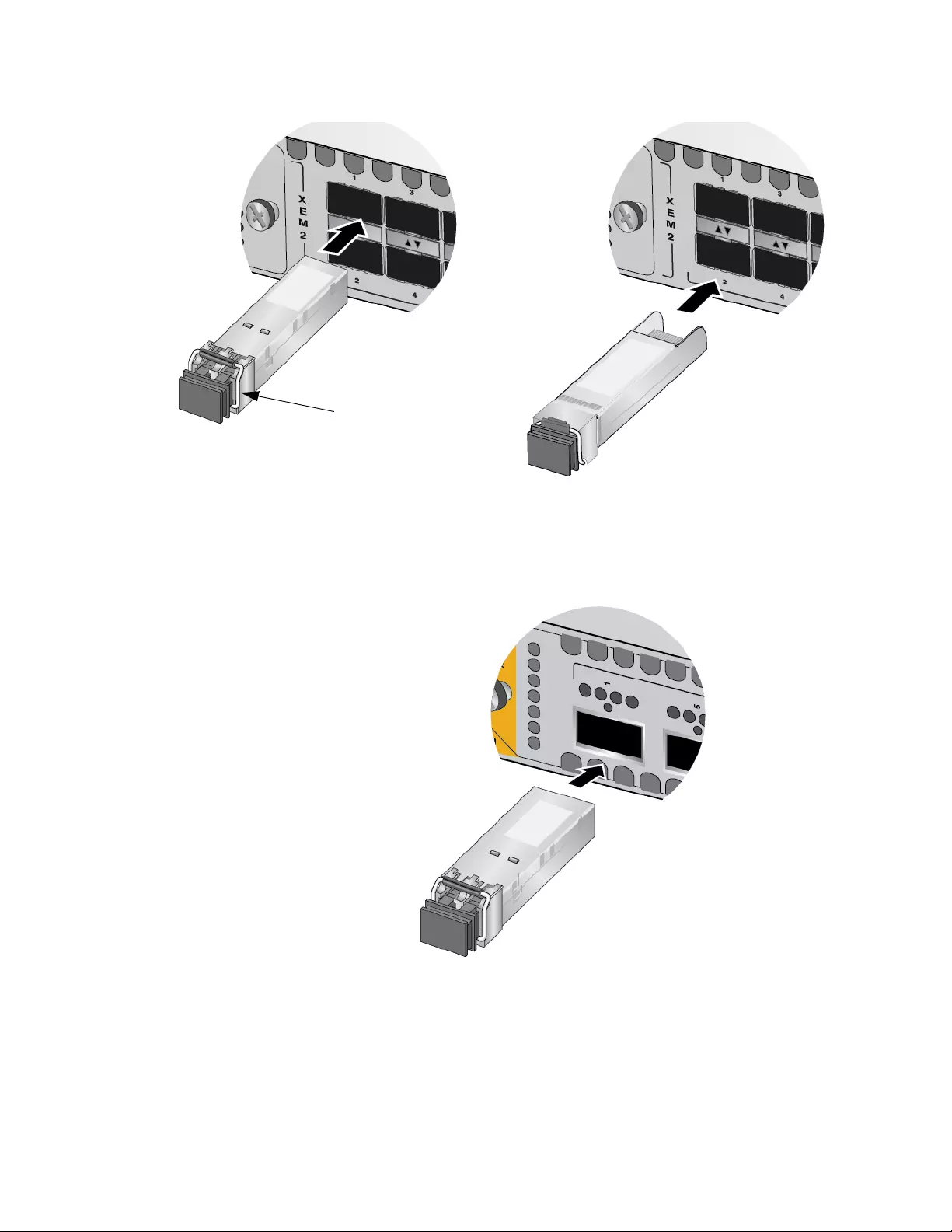
Chapter 13: Cabling the Networking Ports
232
Figure 129. Installing an SFP or SFP+ Transceiver
40Gbps transceivers in XEM2-4QS Line Cards - refer to Figure
130 on page 232.
Figure 130. Installing 40Gbps Fiber Optic Transceivers in XEM2-4QS Line
Cards
100Gbps QSFP28 transceivers for ports 25 to 37: refer to
Figure 131.
Handle
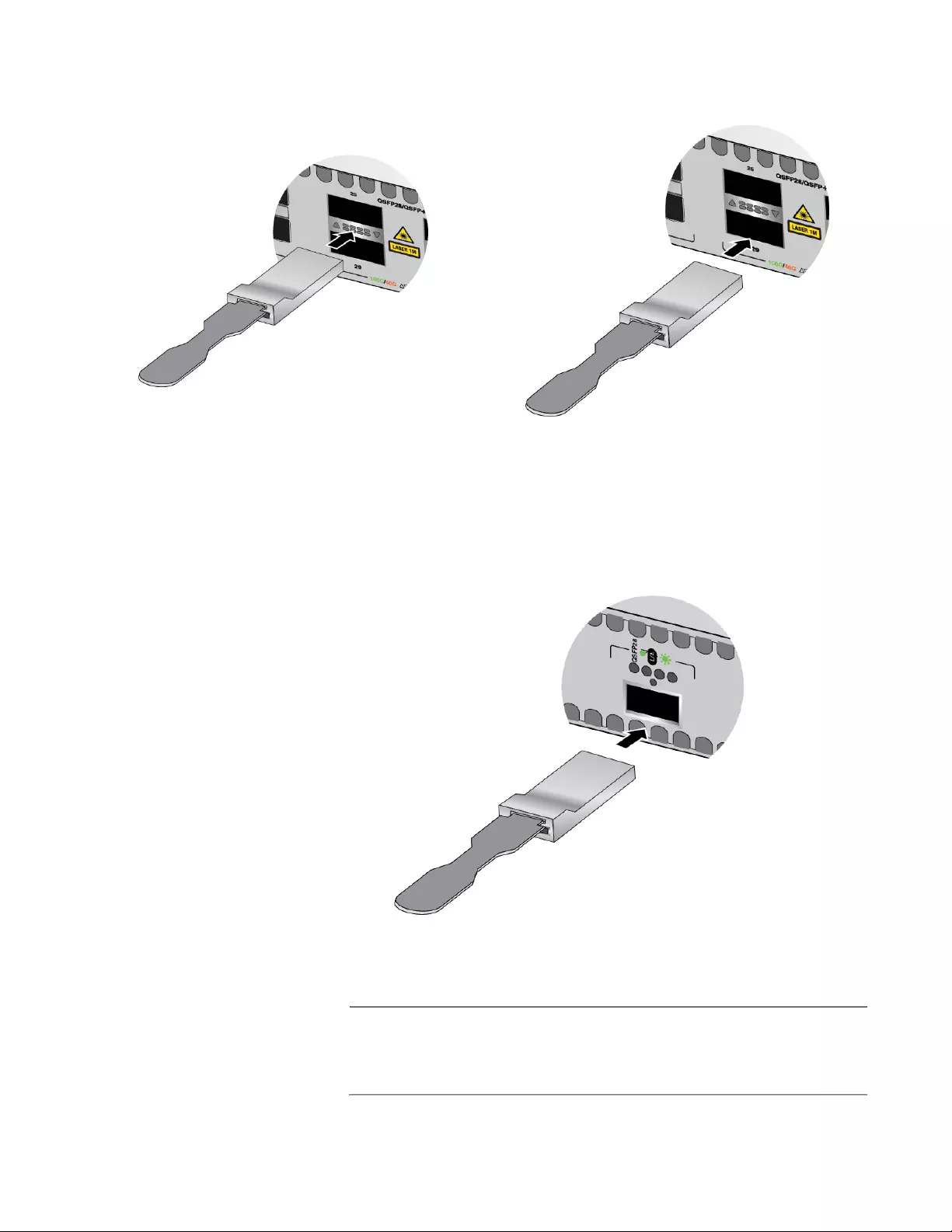
x950 Series Installation Guide for VCStack
233
Figure 131. Installing 100Gbps QSFP28 Transceivers in Base Ports 25,
29, 33, 37
100Gbps QSFP28 transceivers for XEM2-1CQ Line Card: refer to
Figure 132 on page 233.
Figure 132. Installing 100Gbps QSFP28 Transceivers in XEM2-1CQ Line
Cards
Note
If you are ready to attach the fiber optic cable to the transceiver,
continue with the next step. Otherwise, repeat steps 1 to 4 to install
additional transceivers.
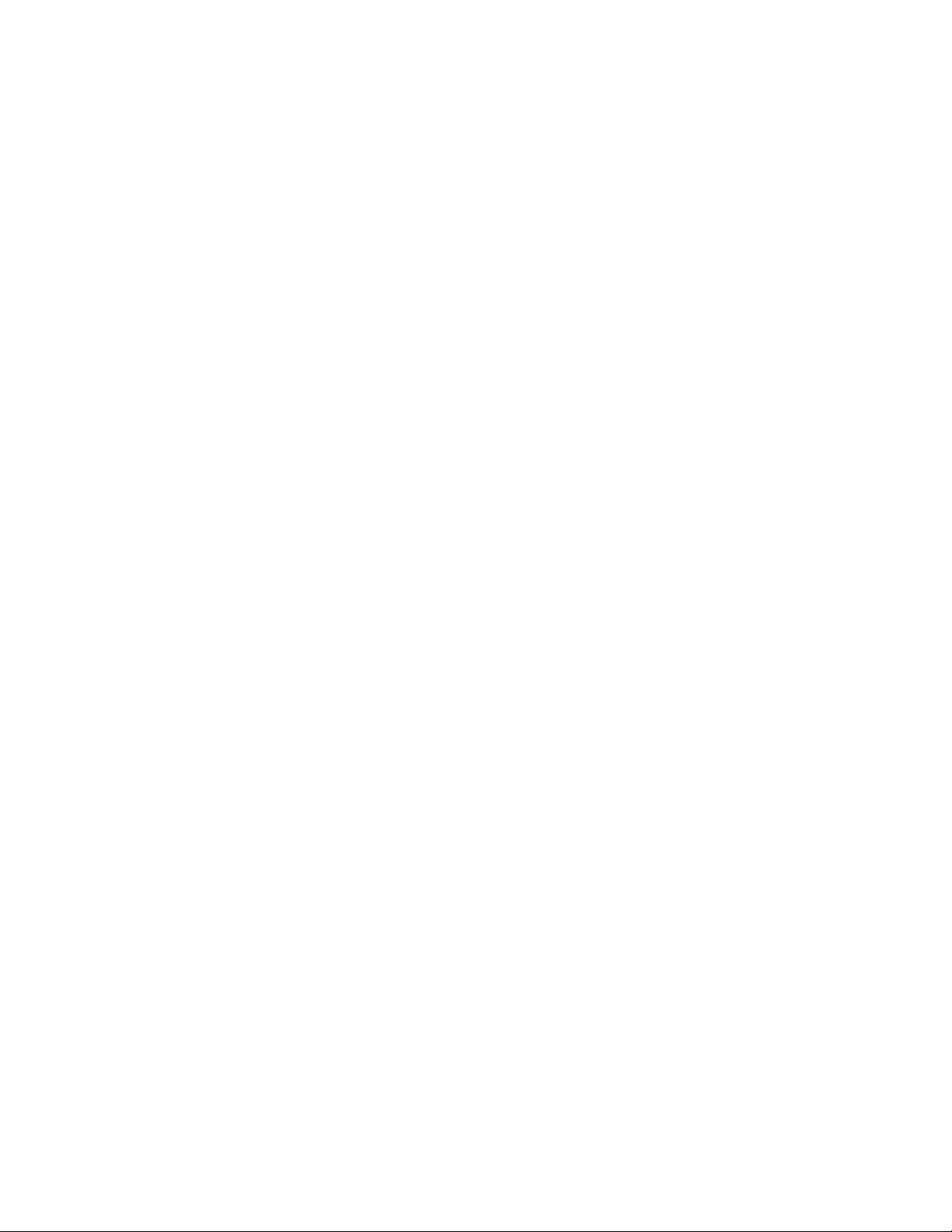
Chapter 13: Cabling the Networking Ports
234
5. If the fiber optic connector on the transceiver has a dust cover, remove
the cover.
6. Connect the fiber optic cable to the connector on the transceiver. The
cable is keyed such that it can connect to the transceiver only one
way.
7. Repeat this procedure to install additional transceivers.
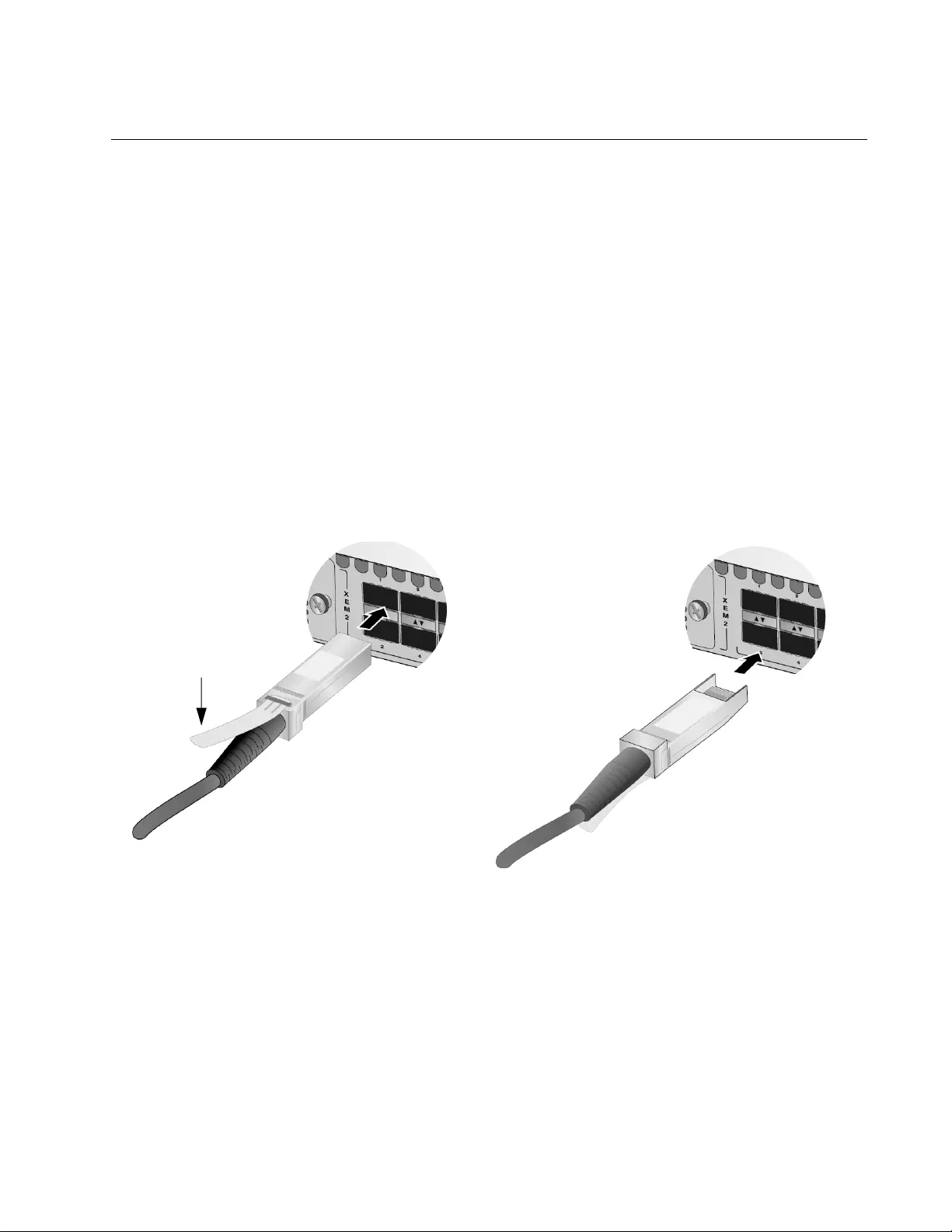
x950 Series Installation Guide for VCStack
235
Installing Direct Attach Cables
Table 10 on page 39 lists the direct attach cables for the base ports and
XEM2 Line Cards. They offer an economical way to add 10Gbps, 40Gbps,
or 100Gbps connections over short distances. To install direct attach
cables, perform the following procedure:
1. Select a port for the direct attach cable.
2. If the selected port has a dust cover, remove the cover.
3. Remove the transceiver from its shipping container and store the
packaging material in a safe location.
4. Orient the transceiver and slide it into the port until it clicks into place.
The correct orientation depends on the cable:
Figure 133 shows the orientations for SP10TW direct attach cables
installed in base ports 1 to 24 and XEM2-8XSTm and XEM2-12XS
Cards.
Figure 133. Installing SP10TW Direct Attach Cables
Figure 134 on page 236 shows the orientations for QSFPCU
Cables installed in base ports 25 to 37.
Release Tab
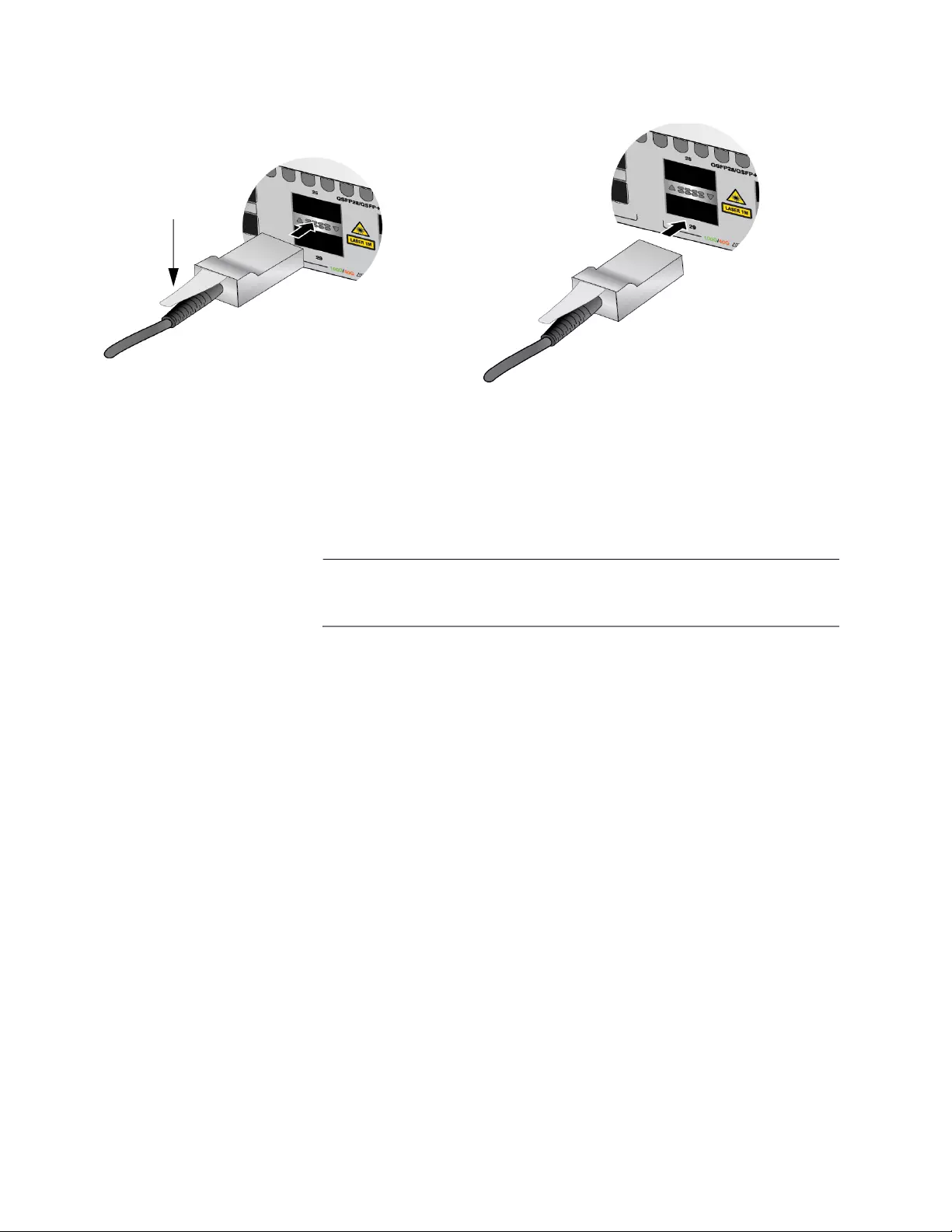
Chapter 13: Cabling the Networking Ports
236
Figure 134. Attaching QSFPCU Cables
5. Connect the other end of the cable into a compatible port on another
network device.
6. Repeat this procedure to install additional direct attach cables.
Note
To remove a cable from the port, gently push on the connector, pull
on the release tab, and slide the connector from the port.
Release Tab
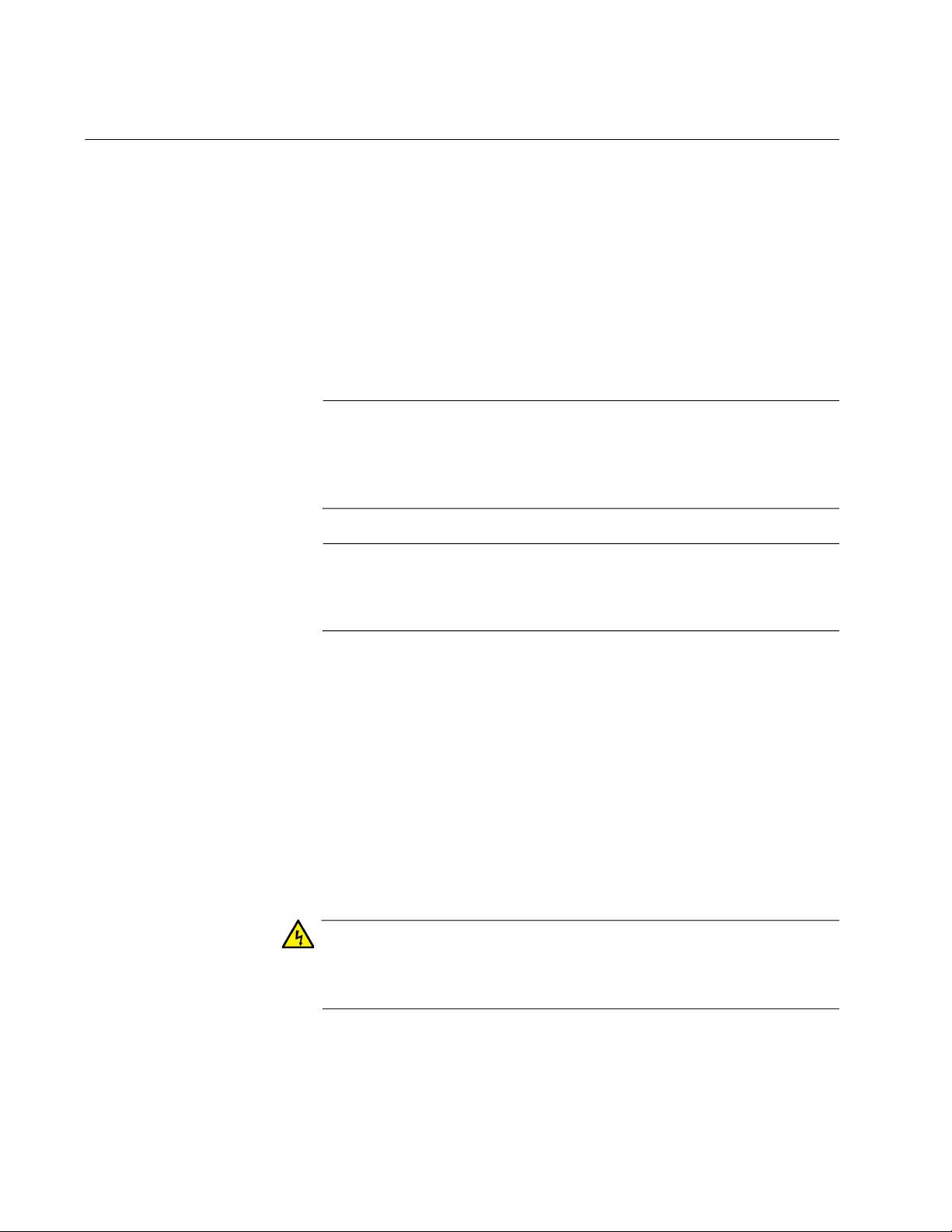
Chapter 14: Replacing Modules
238
Replacing XEM2 Ethernet Line Cards
This section contains the procedure for replacing an XEM2 Ethernet line
card in the x950 Switch. The illustrations in the procedure show the XEM2-
12XT line card. The procedure is the same for all cards. Please review the
following guidelines before performing the procedure:
All XEM2 line cards are hot-swappable. You do not have to power
off or reboot the switch when installing or replacing a line card.
When powered on, an XEM2 line card might require up to thirty
seconds to initialize its management software and begin
forwarding network traffic.
Note
Allied Telesis recommends saving a backup copy of the
configuration file in the switch before removing or replacing line
cards. For instructions, refer to the Software Reference for x950
Switches.
Note
The XEM2 Line Cards are also used in the SBx908 GEN2 Switch.
Please note that you have to reboot that switch when hotswapping
the XEM2-1CQ Line Card.
This procedure requires a #2 Phillips-head screwdriver (not provided).
To remove an XEM2 line card from the switch, perform the following
procedure:
1. Label and remove all cables from the line card.
2. If the line card has fiber optic transceivers, install dust covers on the
ports.
3. If the line card has transceivers or direct attach cables, label and
remove the transceivers or cables.
Warning
The temperature of an operational transceiver may exceed 70° C
(158° F). Exercise caution when removing or handling transceivers
with unprotected hands. E43
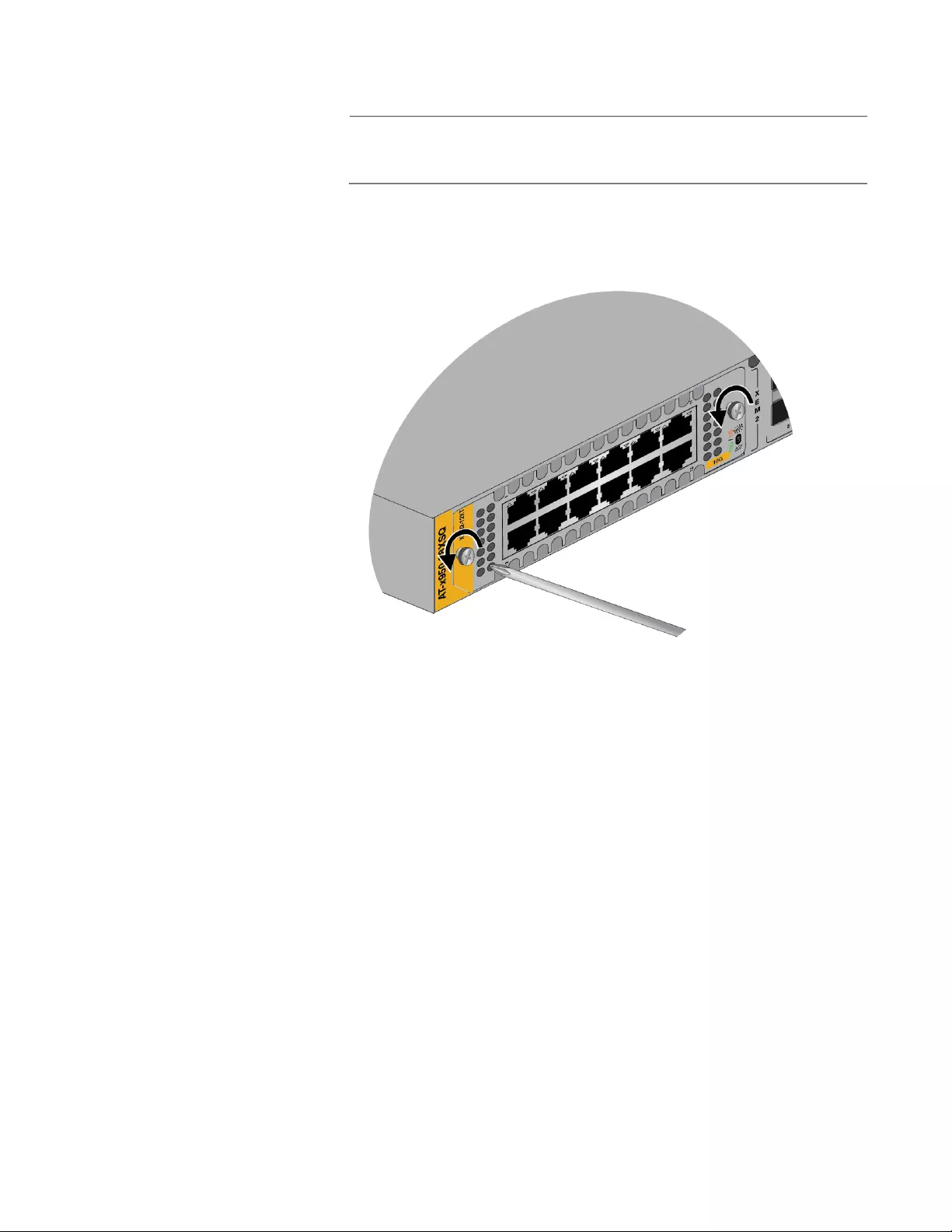
x950 Series Installation Guide for VCStack
239
Note
100Gbps transceivers for the XEM2-1CQ Line Card have handles.
Always use the handles when installing or removing transceivers.
4. Use a #2 Phillips-head screwdriver to loosen the two screws on the
faceplate of the card. Refer to Figure 135.
Figure 135. Loosening the Screws on the Ethernet Line Card
5. Carefully pull on the screws on the faceplate to disconnect the line
card from the internal connector in the switch. Refer to Figure 136 on
page 240.
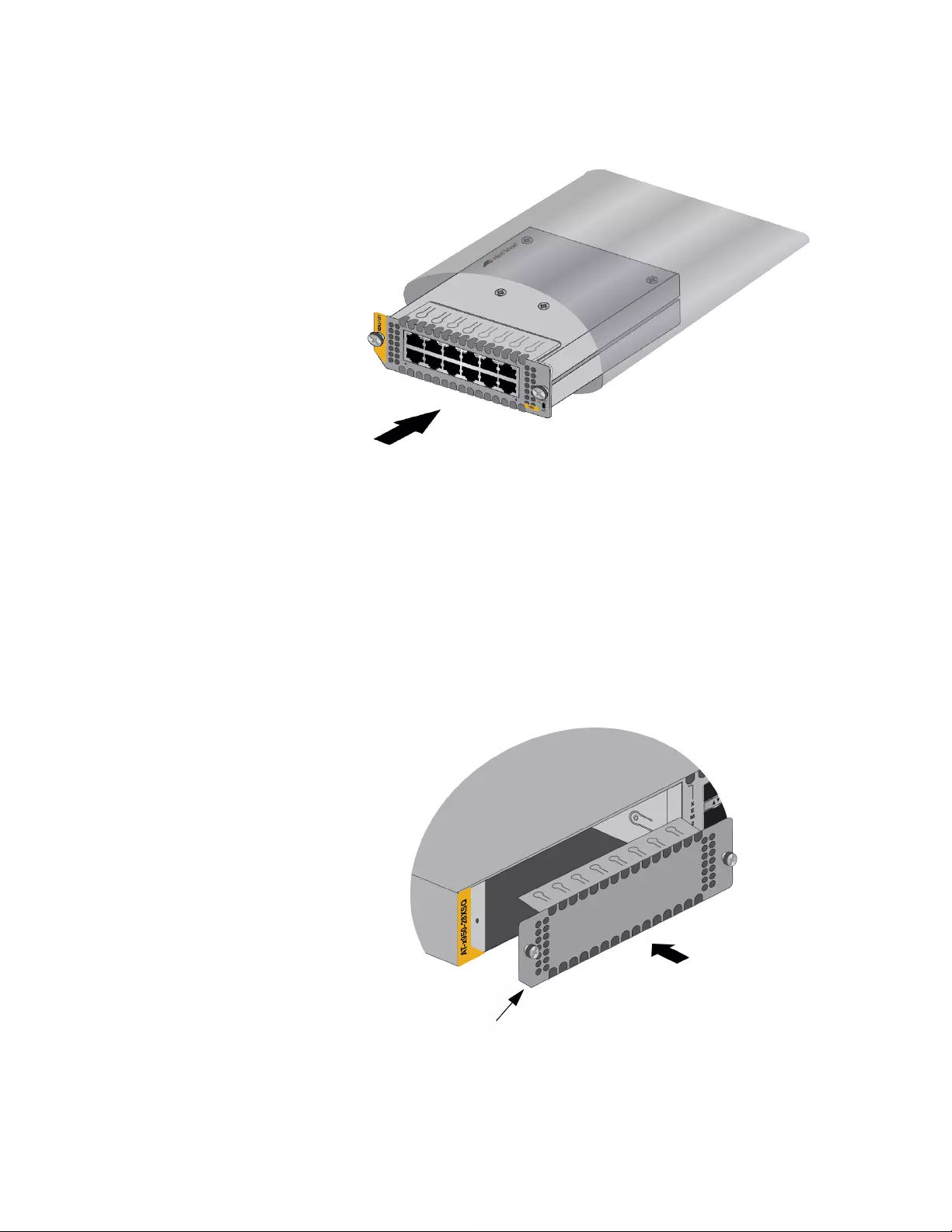
x950 Series Installation Guide for VCStack
241
7. If you are not installing the line card in another switch, store it in its
anti-static bag and shipping container. Refer to Figure 138.
Figure 138. Placing the Ethernet Line Card in its Anti-static Bag
8. Do one of the following:
For instructions on how to install another card in the slot, start with
step 2 in “Installing an Optional XEM2 Ethernet Line Card” on
page 130.
If you are not installing another line card in the slot now, continue
with the next step to install the blank cover.
9. Orient the blank cover as shown in Figure 139, with the notch on the
bottom left, and slid it into the slot.
Figure 139. Installing the Line Card Blank Cover
Notch
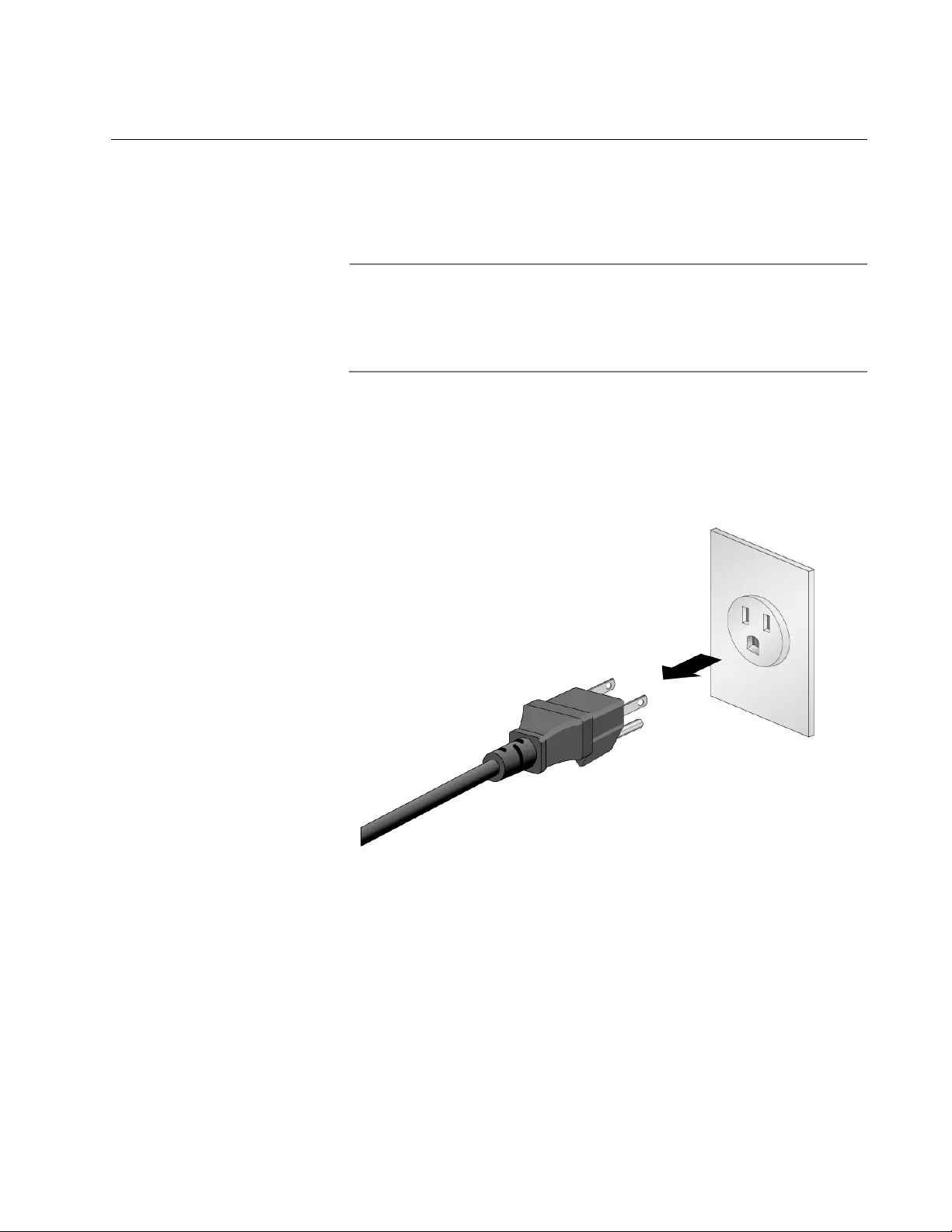
x950 Series Installation Guide for VCStack
243
Replacing PWR600 AC Power Supplies
This section contains the procedure for removing or replacing PWR600
AC Power Supplies.The following illustrations show the removal of a
power supply from slot PSU A. The procedure is the same for slot PSU B.
Note
Allied Telesis recommends saving a backup copy of the
configuration file in the switch before removing or replacing power
supplies. For instructions, refer to the Software Reference for x950
Switches.
To remove power supplies from the switch, perform the following
procedure:
1. Disconnect the AC power cord for the power supply from the AC power
source. Refer to Figure 141.
Figure 141. Disconnecting the AC Power Cord from the Power Source
2. Open the restraining strap on the power cord by pressing down on the
release tab and pulling out the strap. Refer to Figure 142 on page 244.
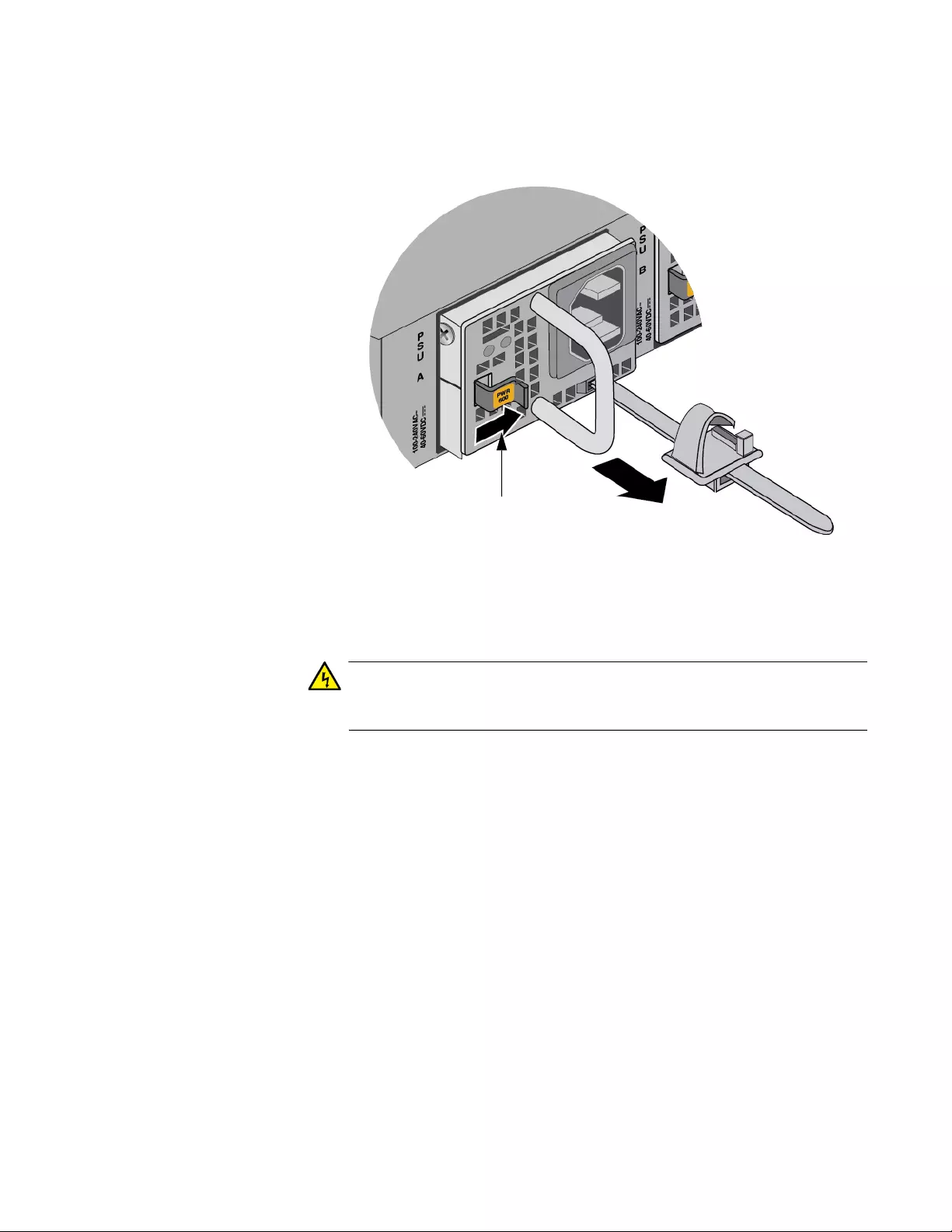
x950 Series Installation Guide for VCStack
245
4. Press the release lever to the right and pull on the handle to release
the power supply from the internal connector in the switch. Refer to
Figure 144.
Figure 144. Removing the Power Supply
5. Carefully slide the power supply from the switch. Refer to Figure 145
on page 246.
Warning
The power supply is heavy. Use both hands to hold it when
removing it from the switch.
Release Lever
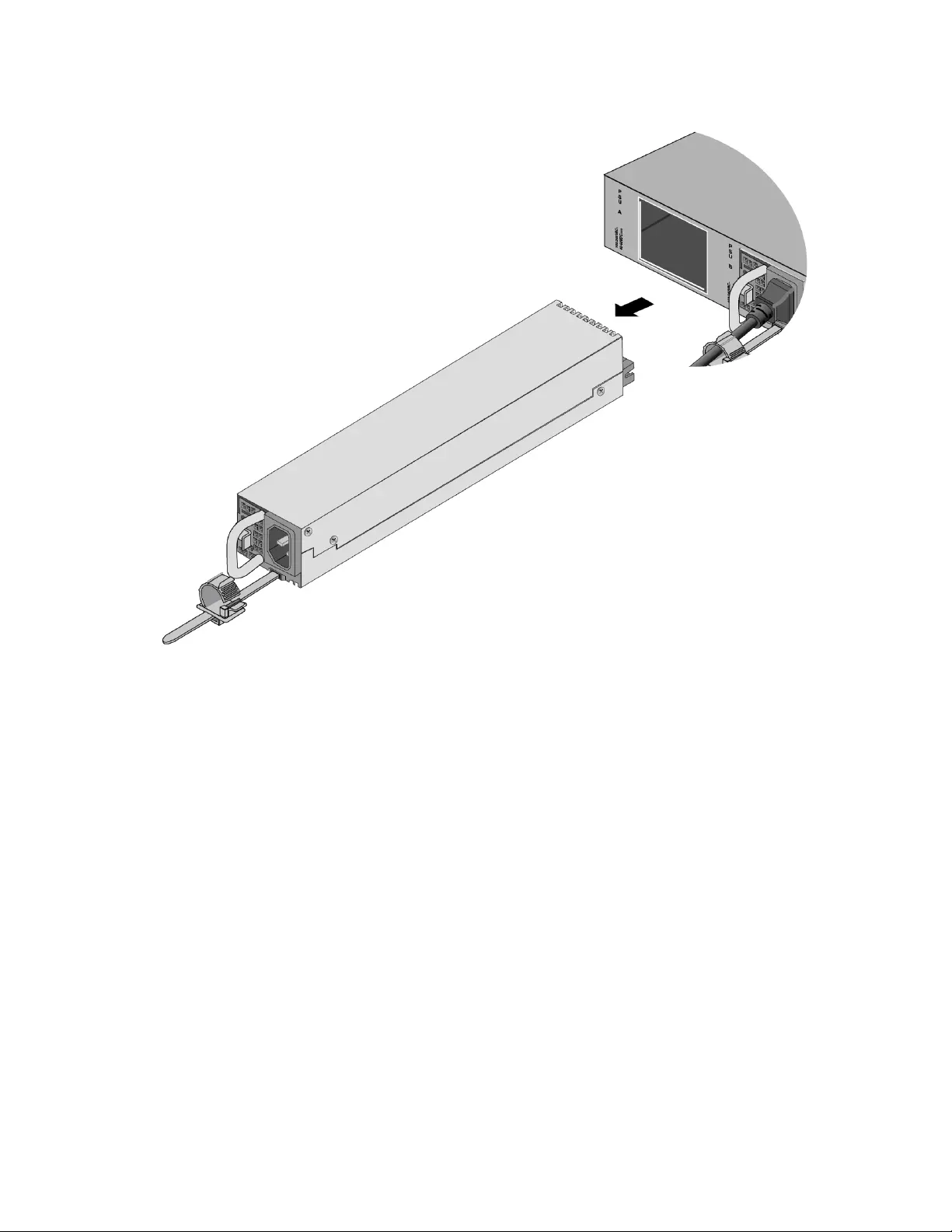
Chapter 14: Replacing Modules
246
Figure 145. Removing a Power Supply
6. Do one of the following:
To install a new power supply, refer to “Installing PWR600 AC
Power Supplies” on page 116 or “Installing PWR600 DC Power
Supplies” on page 120 for instructions.
If you are not installing a new power supply, continue with the next
step to install the blank panel
7. Orient the blank power supply cover as shown in Figure 146 on page
247 and slide it into the slot until it clicks into place.
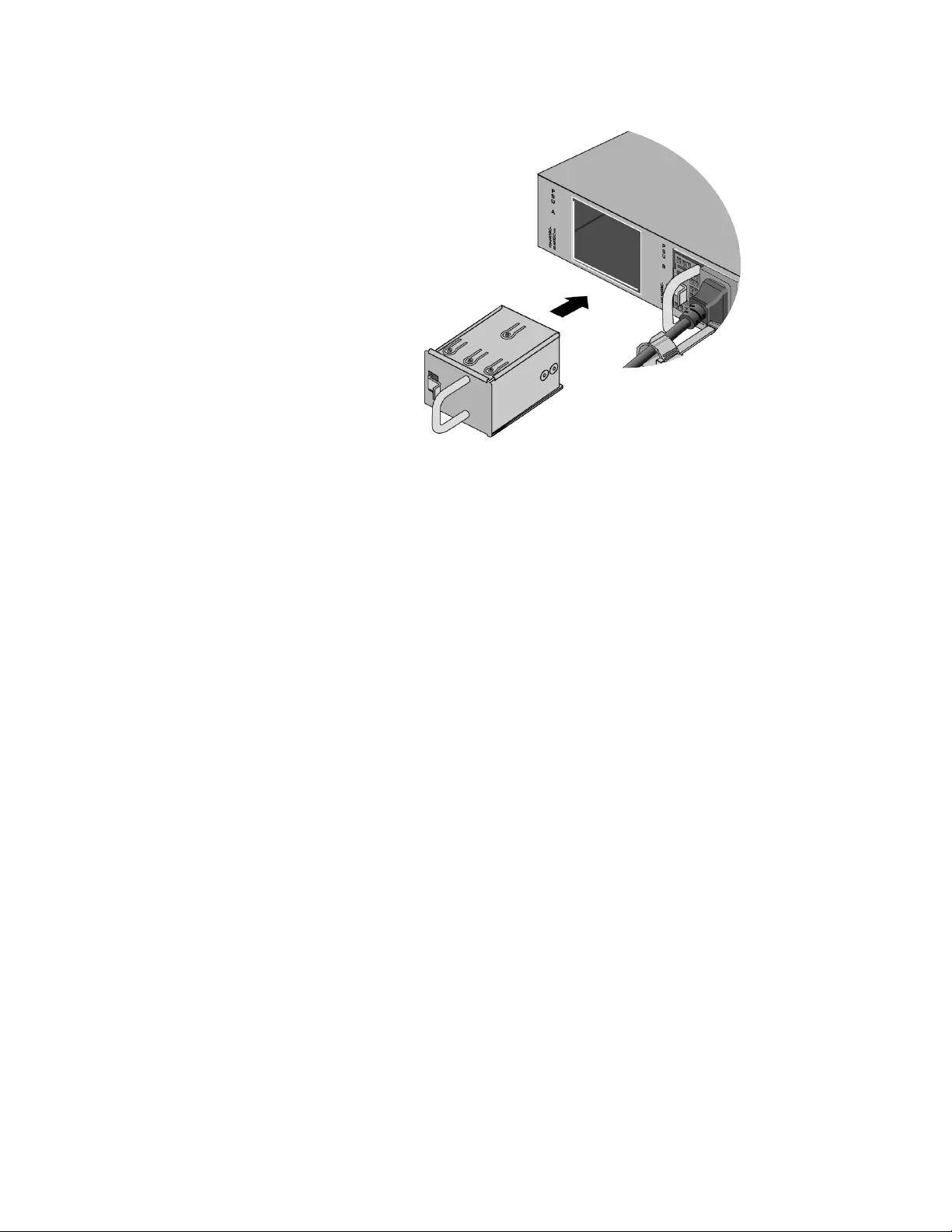
x950 Series Installation Guide for VCStack
247
Figure 146. Installing the Blank Power Supply Cover
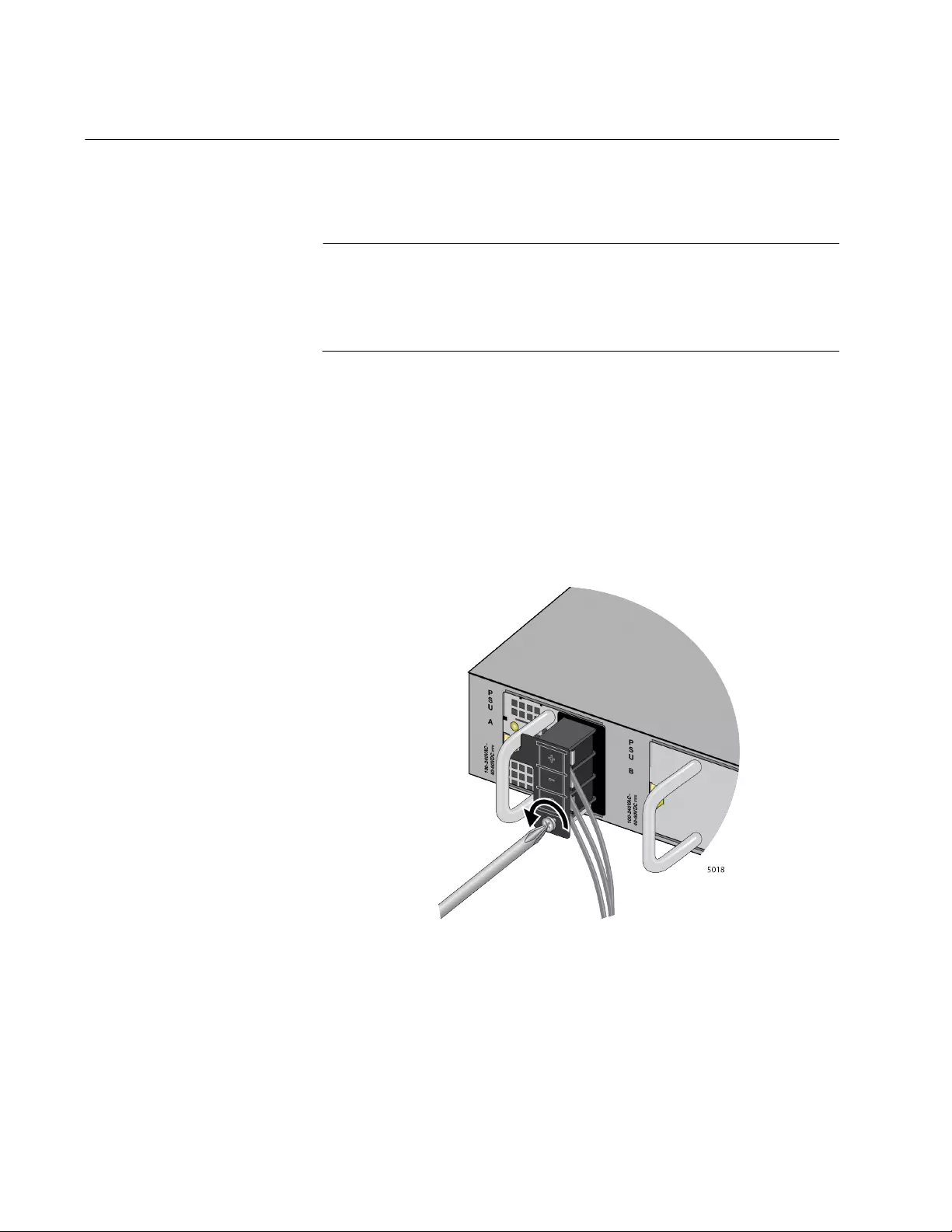
Chapter 14: Replacing Modules
248
Replacing PWR600 DC Power Supplies
This section contains the procedure for removing or replacing PWR600
DC Power Supplies.
Note
Allied Telesis recommends saving a backup copy of the
configuration file in the switch before removing or replacing power
supplies. For instructions, refer to the Software Reference for x950
Switches.
To remove DC power supplies from the switch, perform the following
procedure:
1. Power off the DC power supply.
2. Remove the ground wire from the ground point at the installation site.
3. Loose the screw for the connector panel with a Phillips-head
screwdriver. Refer to Figure 147.
Figure 147. Loosening the Screw for the Panel
4. Press the panel to the right to access the connecting screws as shown
in Figure 148 on page 249.
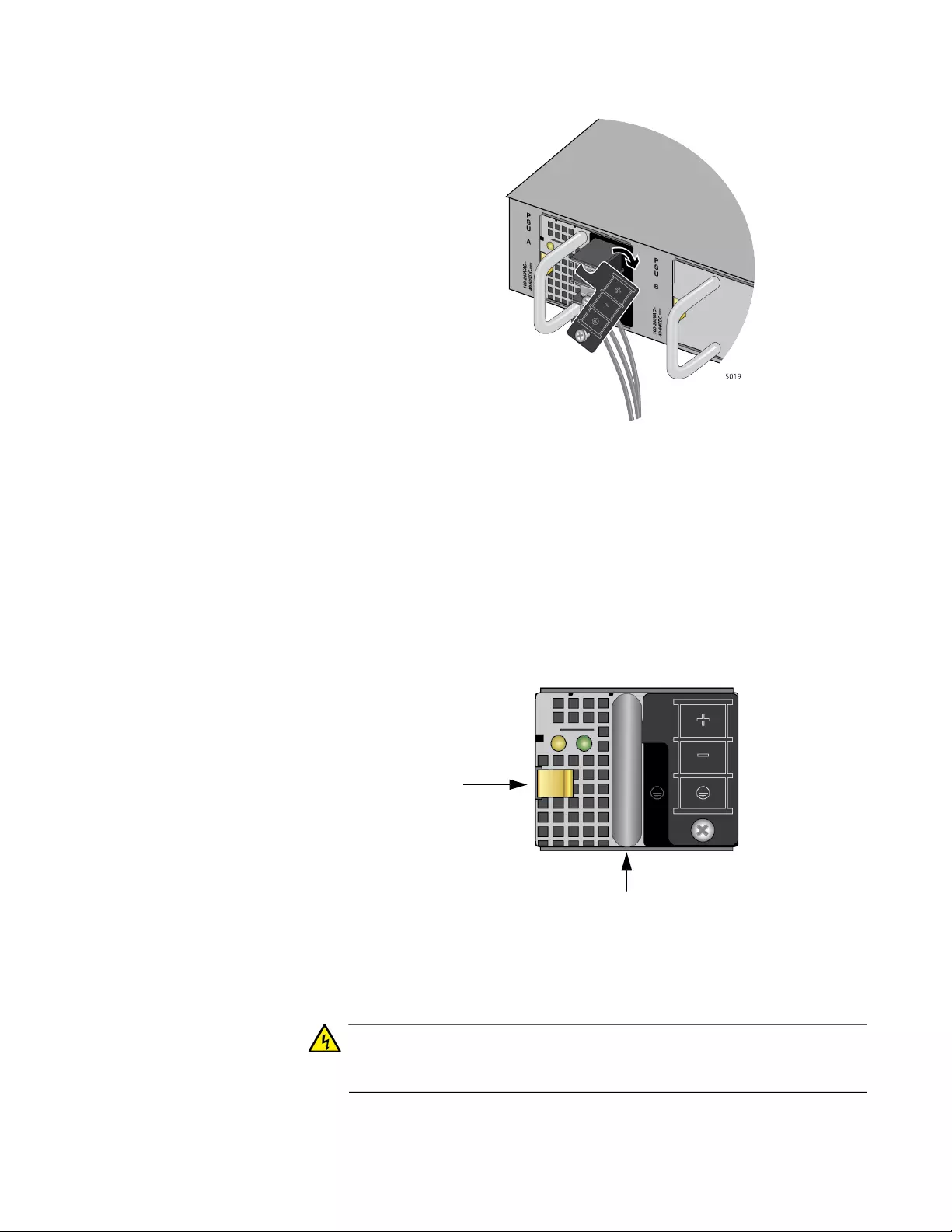
x950 Series Installation Guide for VCStack
249
Figure 148. Accessing the Connecting Screws
5. Loosen all three screws for the ground wire, positive(+) and
negative(-) wires.
6. Remove all three wires.
7. Press the release lever to the right and pull on the handle to release
the power supply from the internal connector in the switch. Refer to
Figure 131 on page 191.
The release lever and handle are shown in Figure 149.
Figure 149. Front Panel of the PWR600 DC Power Supply
8. Carefully slide the power supply from the switch. Refer to Figure 150
on page 250.
Warning
The power supply is heavy. Use both hands to hold it when
removing it from the switch.
Release Lever
Handle
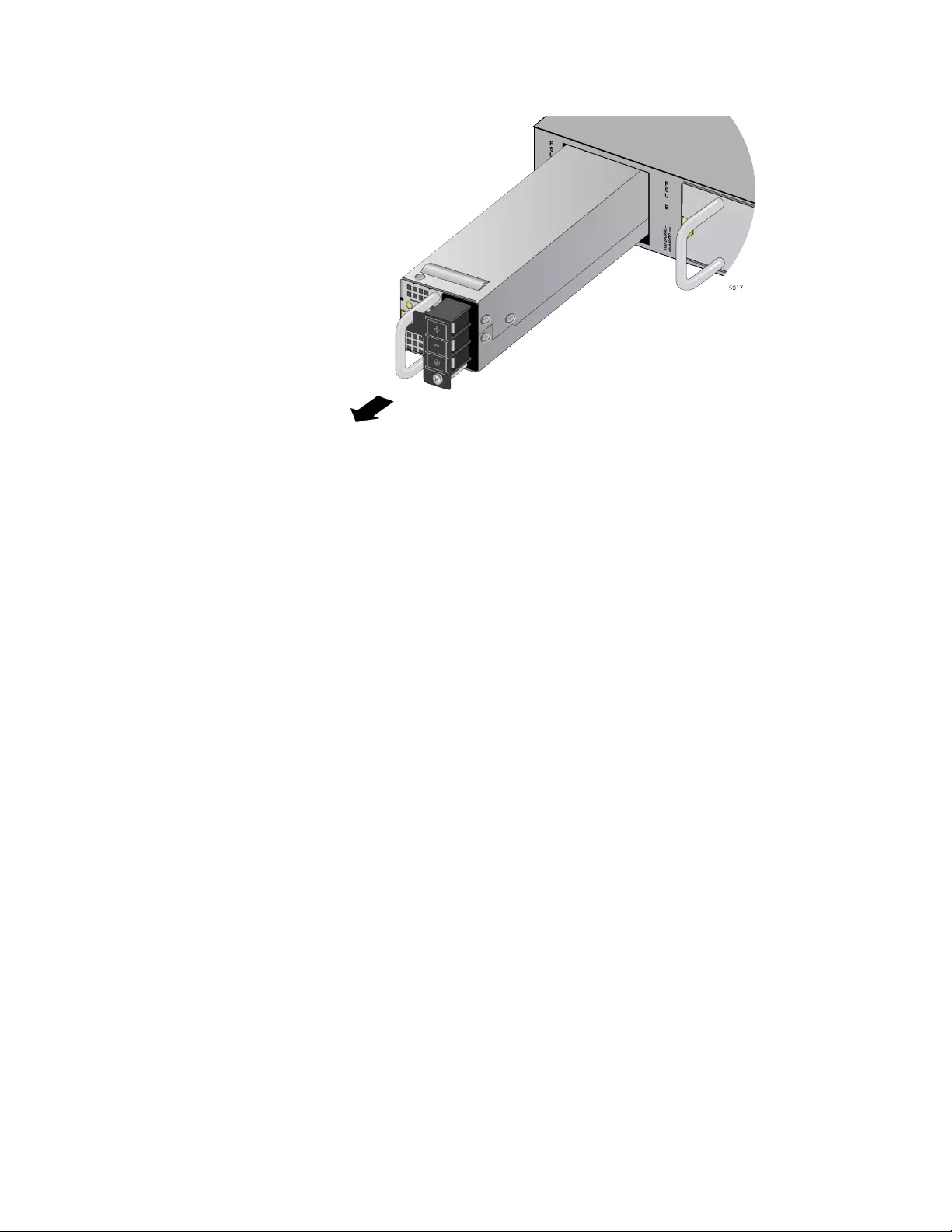
Chapter 14: Replacing Modules
250
Figure 150. Front Panel of the PWR600 DC Power Supply
9. Do one of the following:
To install a new power supply, refer to “Installing PWR600 AC
Power Supplies” on page 116 or “Installing PWR600 DC Power
Supplies” on page 120 for instructions.
If you are not installing a new power supply, continue with the next
step to install the blank panel
10. Orient the blank power supply cover as shown in Figure 146 on page
247 and slide it into the slot until it clicks into place.
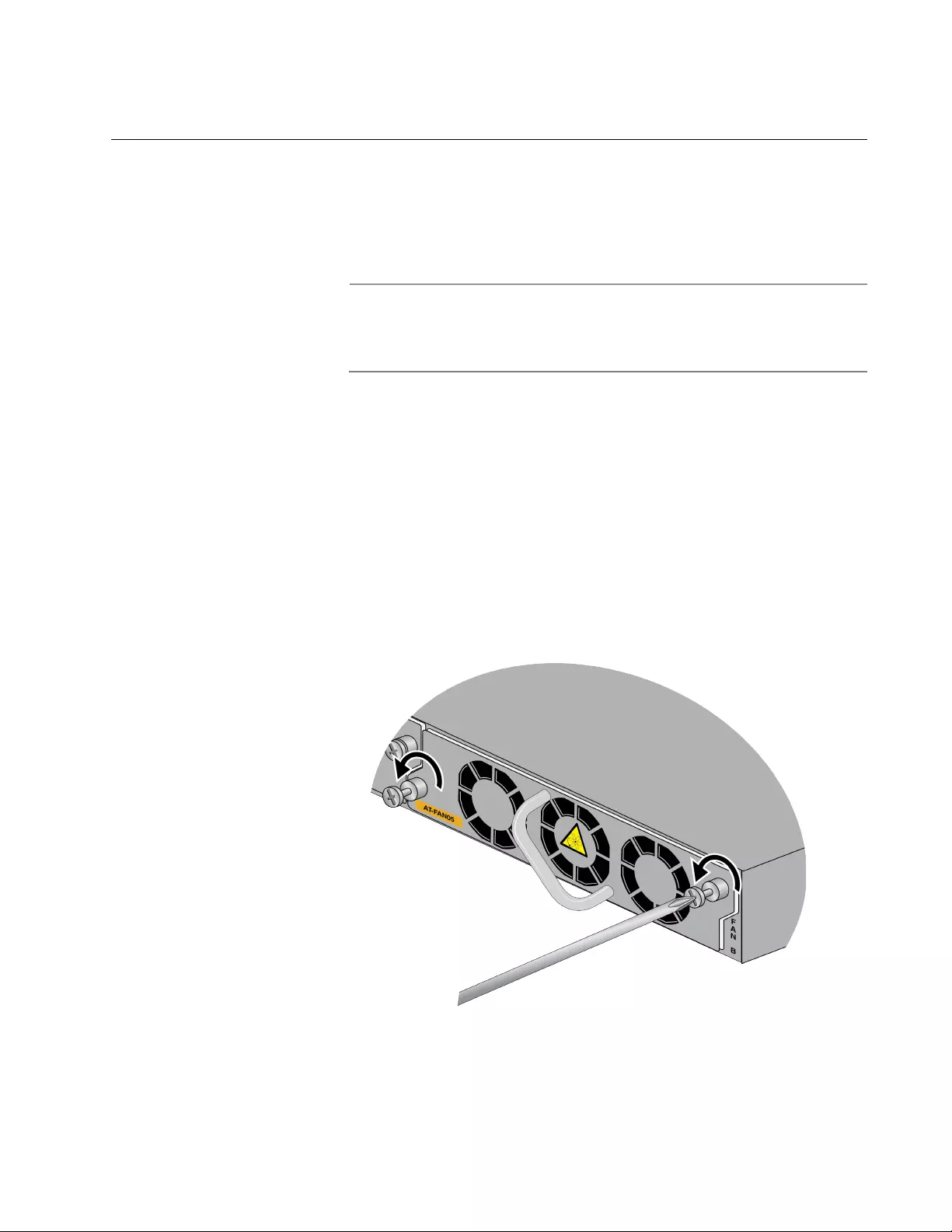
x950 Series Installation Guide for VCStack
251
Replacing FAN05 Modules
This section contains the procedure for replacing FAN05 Modules. Fan
modules are hot swappable. You can replace them without having to
power off the switch. For background information, refer to “FAN05 Cooling
Fan” on page 45.
Note
Allied Telesis recommends saving a backup copy of the
configuration file in the switch before replacing a fan module. For
instructions, refer to the Software Reference for x950 Switches.
Removing Fan
Modules
This procedure requires the following tool:
#2 Phillips-head screwdriver (not provided)
The illustrations show the removal of the fan module from FAN B slot on
the back panel. The procedure is the same for removing a module from
FAN A slot.
To remove a fan module from the switch, perform the following procedure:
1. Use a #2 Phillips-head screwdriver to loosen the two screws on the
faceplate of the fan module. Refer to Figure 151.
Figure 151. Loosening the Screws on the Fan Module
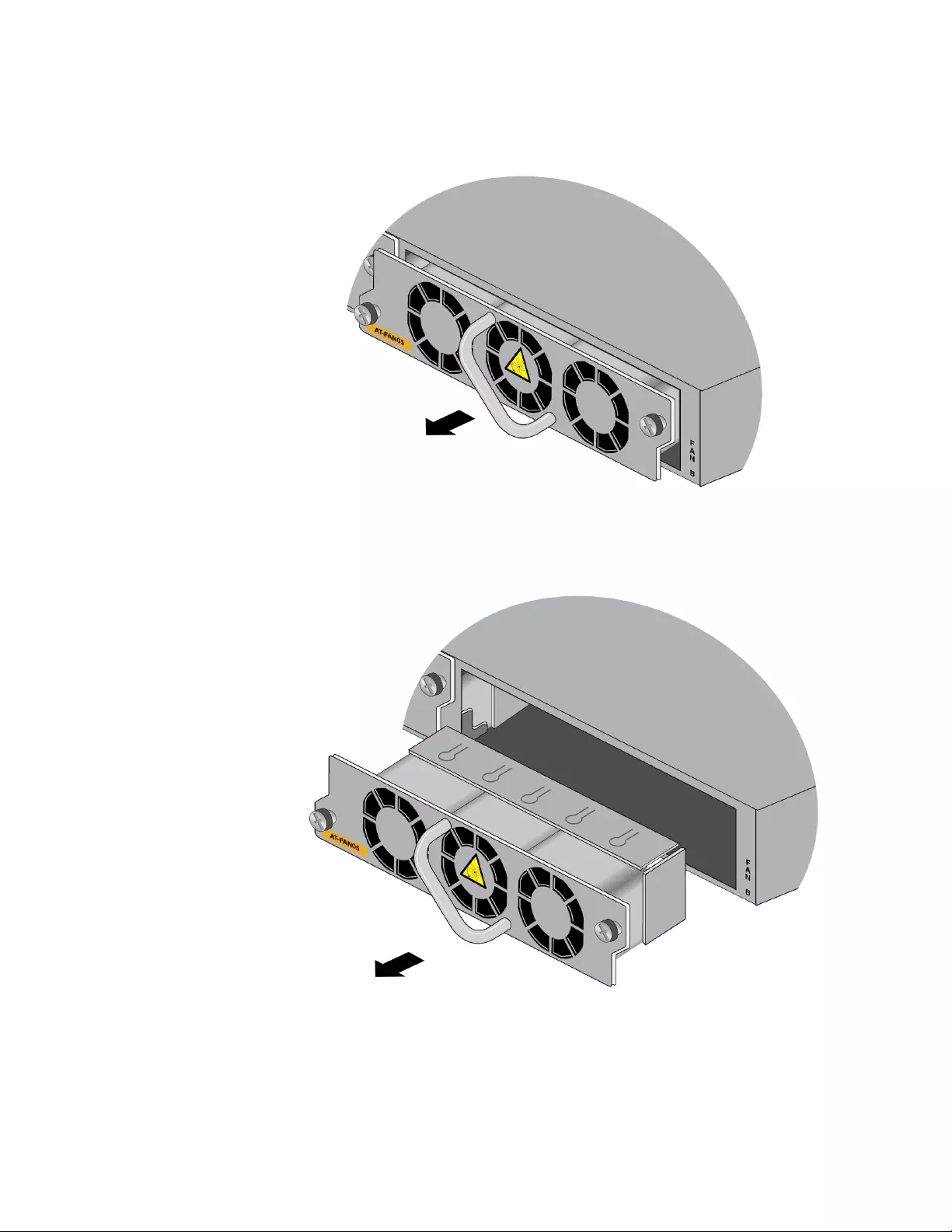
Chapter 14: Replacing Modules
252
2. Carefully pull on the handle to disconnect the line card from the
internal connector in the switch. Refer to Figure 152.
Figure 152. Disconnecting the FAN05 Module from the Switch
3. Slide the fan module out of the switch. Refer to Figure 153.
Figure 153. Sliding the Fan Module from the Switch
4. Continue with the next procedure to install a new FAN05 Module.
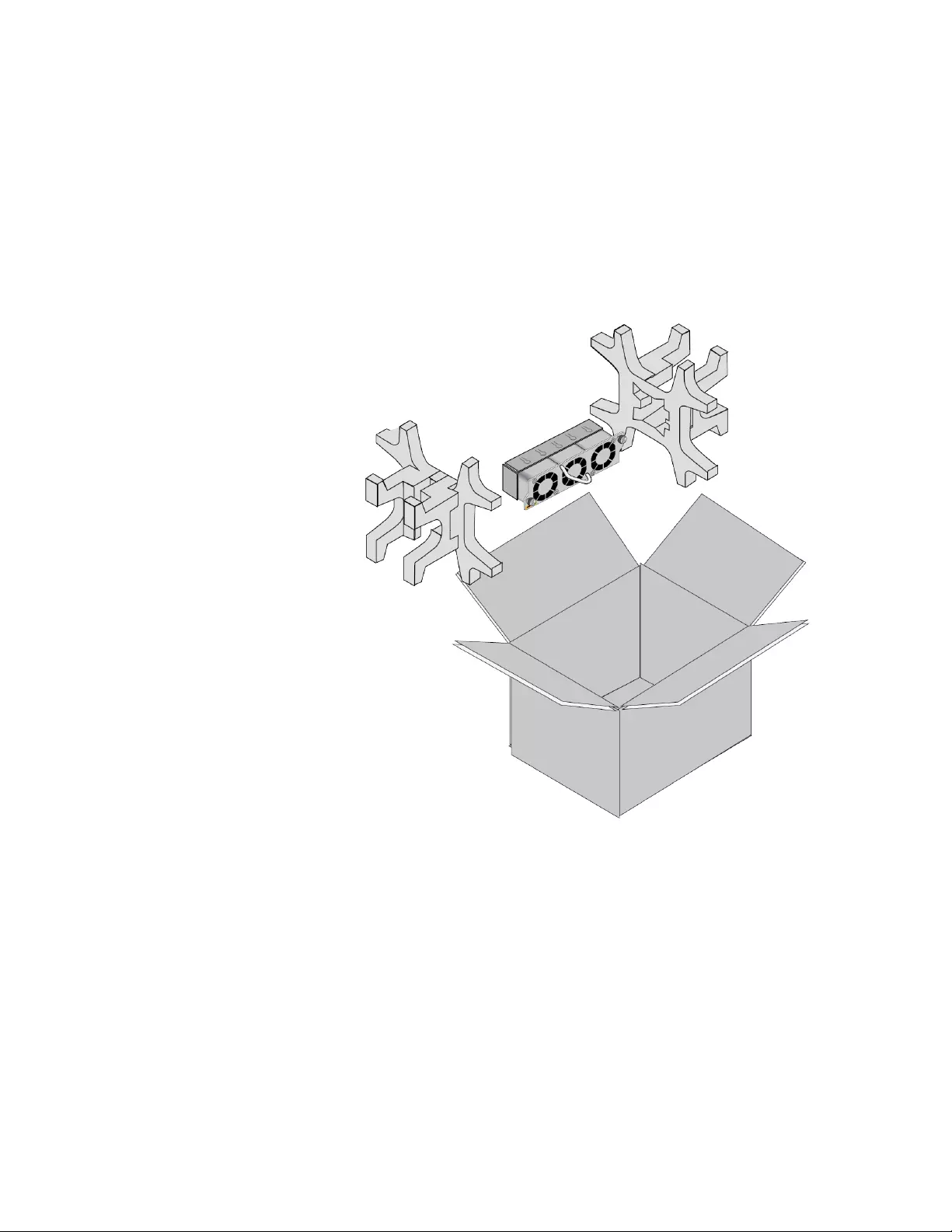
x950 Series Installation Guide for VCStack
253
Installing Fan
Modules
This procedure requires a #2 Phillips-head screwdriver (not provided).
The illustrations show the installation of a fan module in FAN B slot on the
back panel. The procedure is the same for installing a module in FAN A
slot.
To install a fan module, perform the following procedure:
1. Remove the new fan module form its shipping box. Refer to
Figure 154.
Figure 154. Removing the Fan Module from the Shipping Container
2. Align the fan module in the slot. Refer to Figure 155 on page 254.
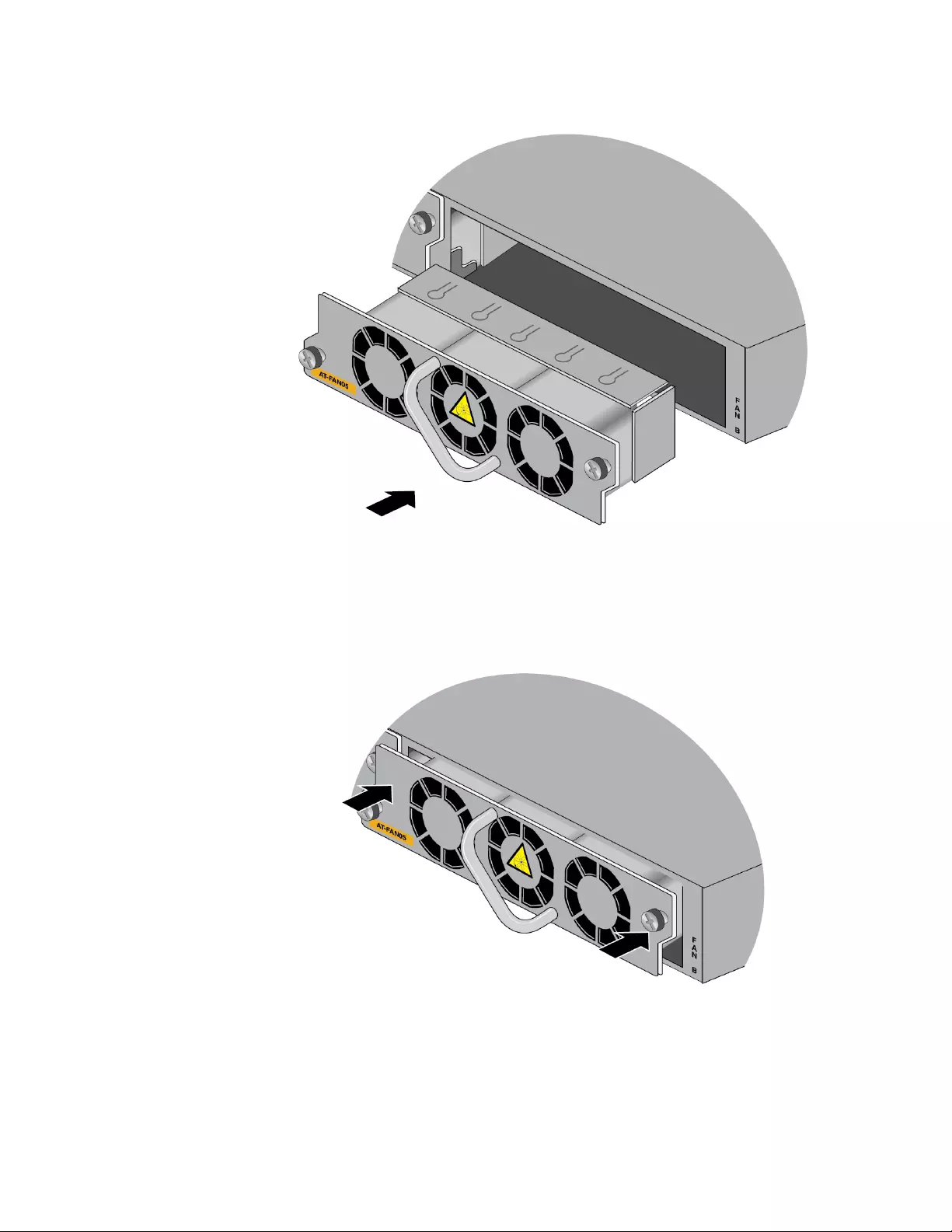
Chapter 14: Replacing Modules
254
Figure 155. Aligning the FAN05 Module in the Switch Slot
3. When you feel the module make contact with the internal connector,
gently press on both sides to seat the module on the connector. Refer
to Figure 156.
Figure 156. Seating the FAN05 Module on the Internal Connector
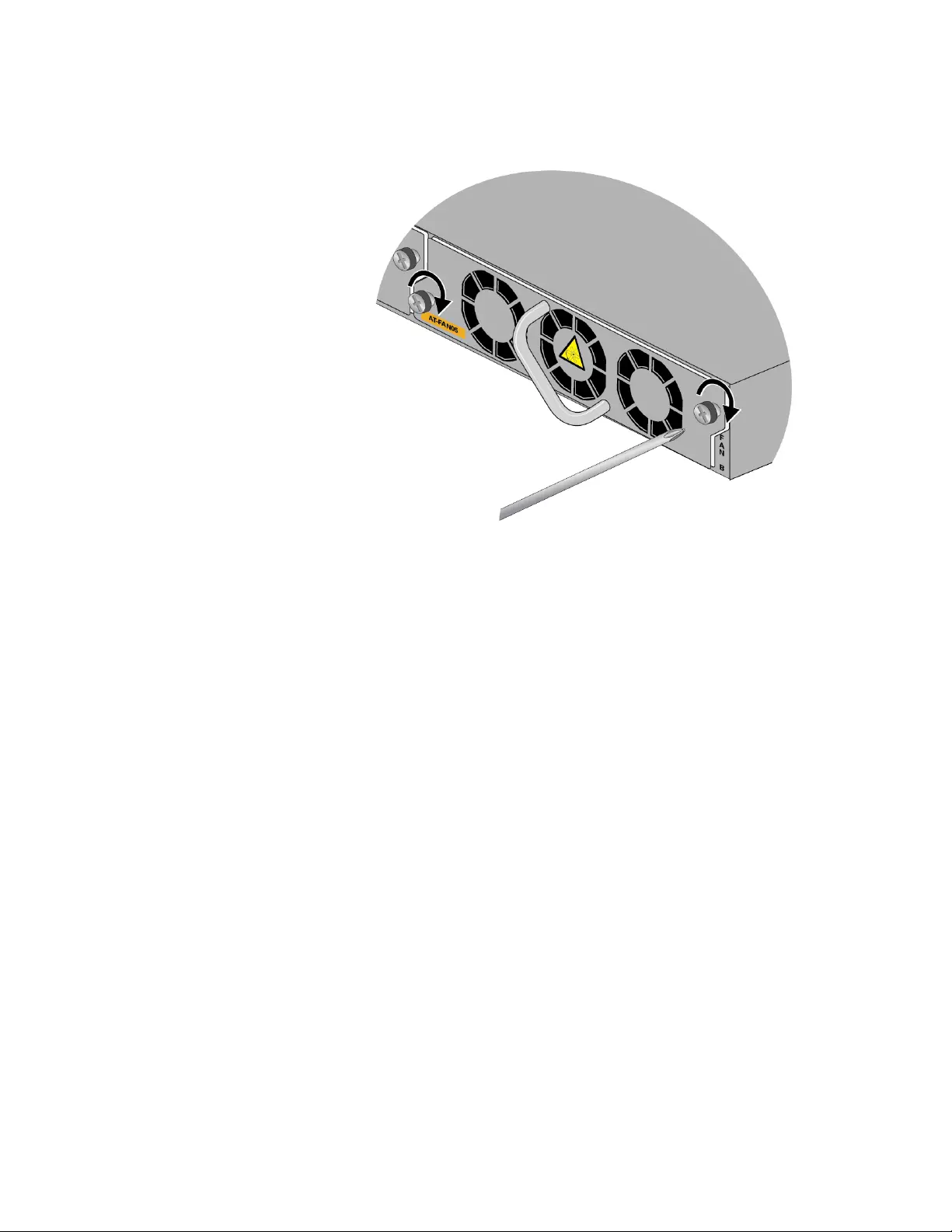
x950 Series Installation Guide for VCStack
255
4. Tighten the two screws on the module to secure it to the switch. Refer
to Figure 157.
Figure 157. Tightening the Two Captive Screws on the FAN05 Module
5. To confirm the operations of the new fan module, start a local or
remote management session and enter the SHOW SYSTEM
ENVIRONMENT command in the User Exec or Privileged Exec mode.
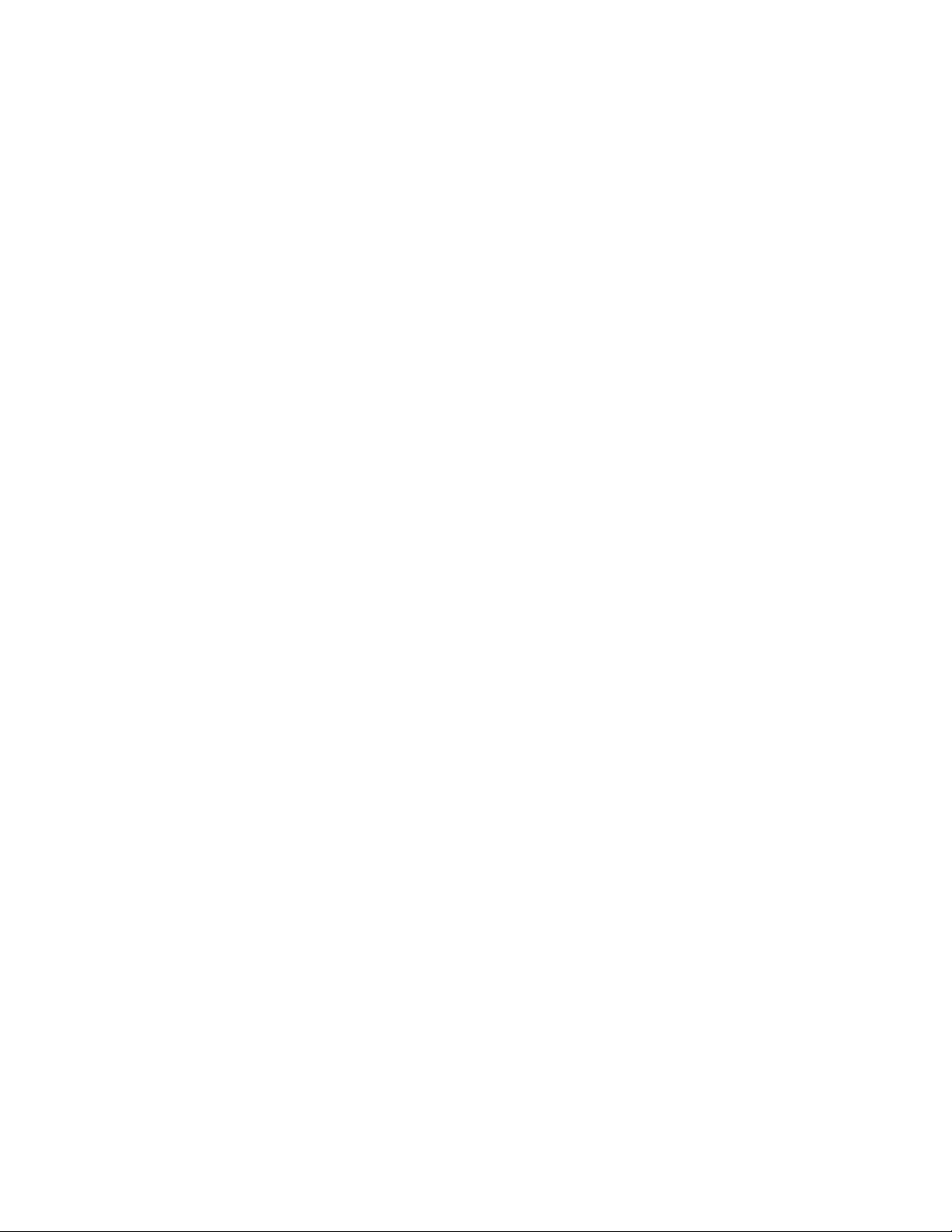
Chapter 14: Replacing Modules
256
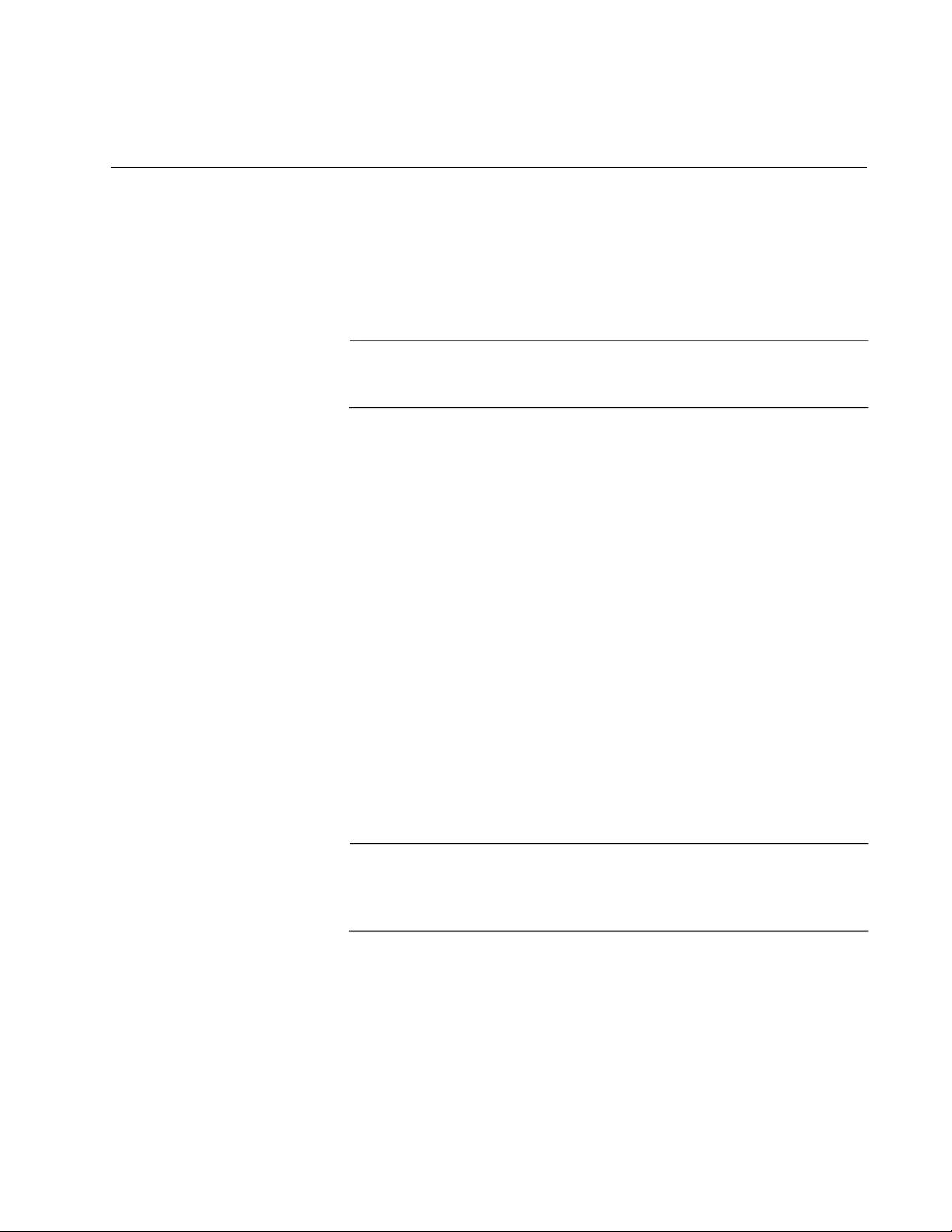
257
Chapter 15
Troubleshooting
This chapter contains suggestions on how to troubleshoot problems with
the switch.
Note
For further assistance, please contact Allied Telesis Technical
Support at www.alliedtelesis.com/support.
Problem 1: The unit is not receiving power. All the port LEDs and Switch
ID LED are off, and the fans are not operating.
Solutions: Try the following:
Verify that the power cord is securely connected to the power
source and AC connector on the back panel of the switch.
Verify that the DC power wires are securely connected to the
screws on the front panel and to the DC power source unit.
Verify that the power outlet has power by connecting another
device to it.
Try connecting the unit to another power source.
Try a different power cord.
Verify that the voltage from the power source is within the required
levels for your region. The power requirements for the switch are
listed in “Power Specifications” on page 268.
Try replacing the power supply.
Note
Power supplies are hot swappable. If the chassis has two power
supplies and one fails, you can replace the failed unit without having
to power off the operational power supply.
Problem 2: All the port LEDs are off even though the ports are connected
to active network devices.
Solution: The switch might be operating in the low power mode. To toggle
on the LEDs, press the eco-friendly button on the front panel of the switch.
You can also toggle the LEDs off and on with the ECOFRIENDLY LED and
NO ECOFRIENDLY LED commands in the command line interface.
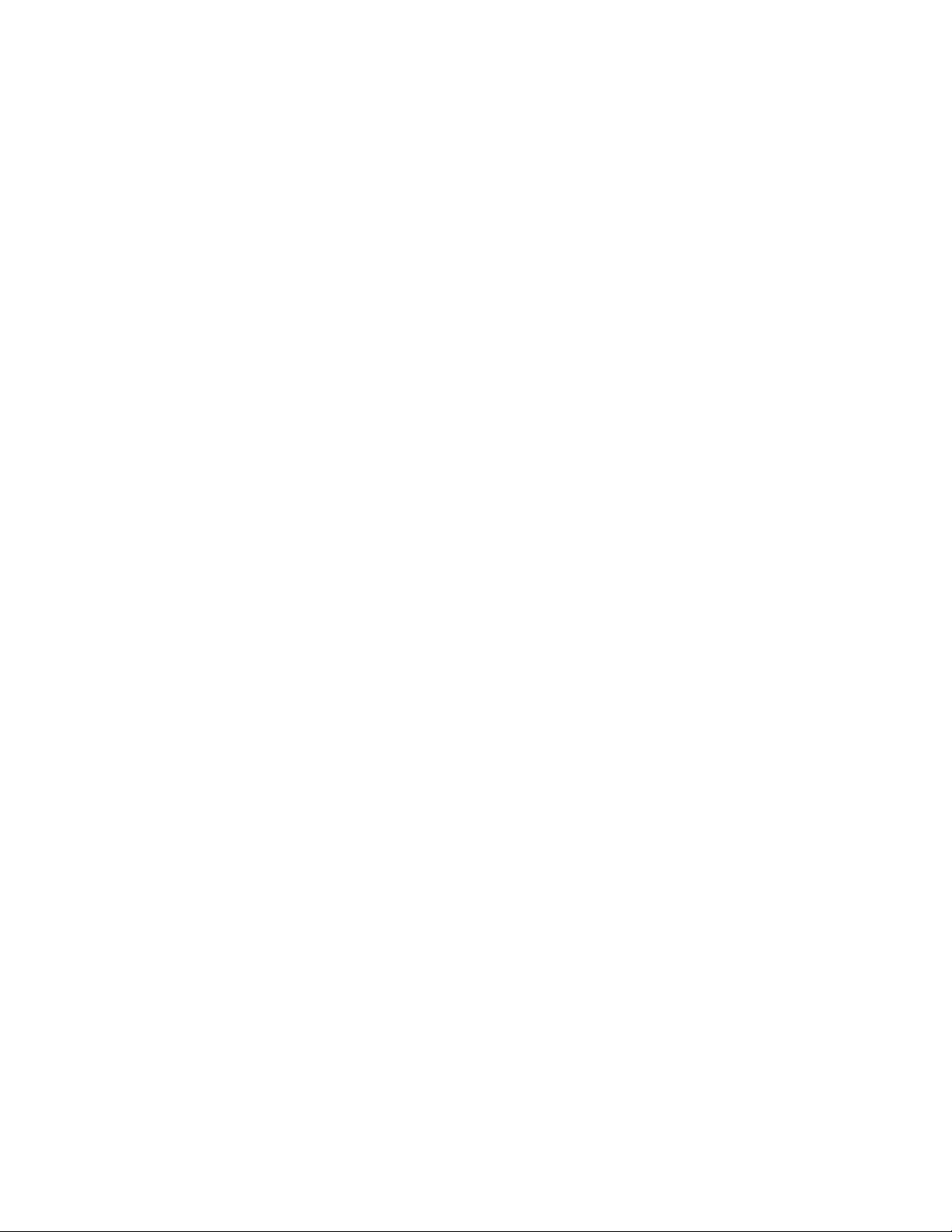
Chapter 15: Troubleshooting
258
Problem 3: A 1Gbps or 10Gbps fiber optic transceiver in a base port
(ports 1 to 24) of the x950-28XSQ switch or a base port of the
x950-52XSQ switch (ports 1 to 48) is unable to establish a link to a
network device.
Solutions: Try the following:
Check that the transceiver is fully inserted in the port.
Verify that the fiber optic cable is securely connected to the port on
the transceiver and the remote network device.
Verify that the remote network device is operating properly.
Verify that the operating specifications of the fiber optic ports on
the transceiver and remote network device are compatible.
Verify that the correct type of fiber optic cabling is being used.
Verify that the port is connected to the correct fiber optic cable.
Try connecting another network device to the fiber optic port using
a different cable. If the port is able to establish a link, then the
problem is with the cable or with the other network device.
Use the switch’s management software to verify that the port is
enabled.
If the remote network device is a managed device, use its
management firmware to determine whether its port is enabled.
If the problem is with two BiDi (bi-directional) transceivers, refer to
their data sheets to verify that their transmission and reception
frequencies are opposite each other. For instance, a BiDi
transceiver that transmits and receives at 1310nm and 1550nm,
respectively, has to be connected to a transceiver that transmits
and receives at 1550nm and 1310nm, respectively. Two BiDi
transceivers will not establish a link if they transmit and receive at
the same frequencies.
Test the attenuation of both directions on the fiber optic cable with
a fiber optic tester to determine whether the optical signal is too
weak or strong.
Problem 4: A 40Gbps or 100Gbps fiber optic transceiver in port 25, 29,
33, or 37 on the x950-28XSQ or x950-28XTQm switch, or in port 49, 53,
57, or 61 on the x950-52XSQ switch cannot establish a link with a network
device.
Solutions: Try the following:
Review the solutions to Problem 3.
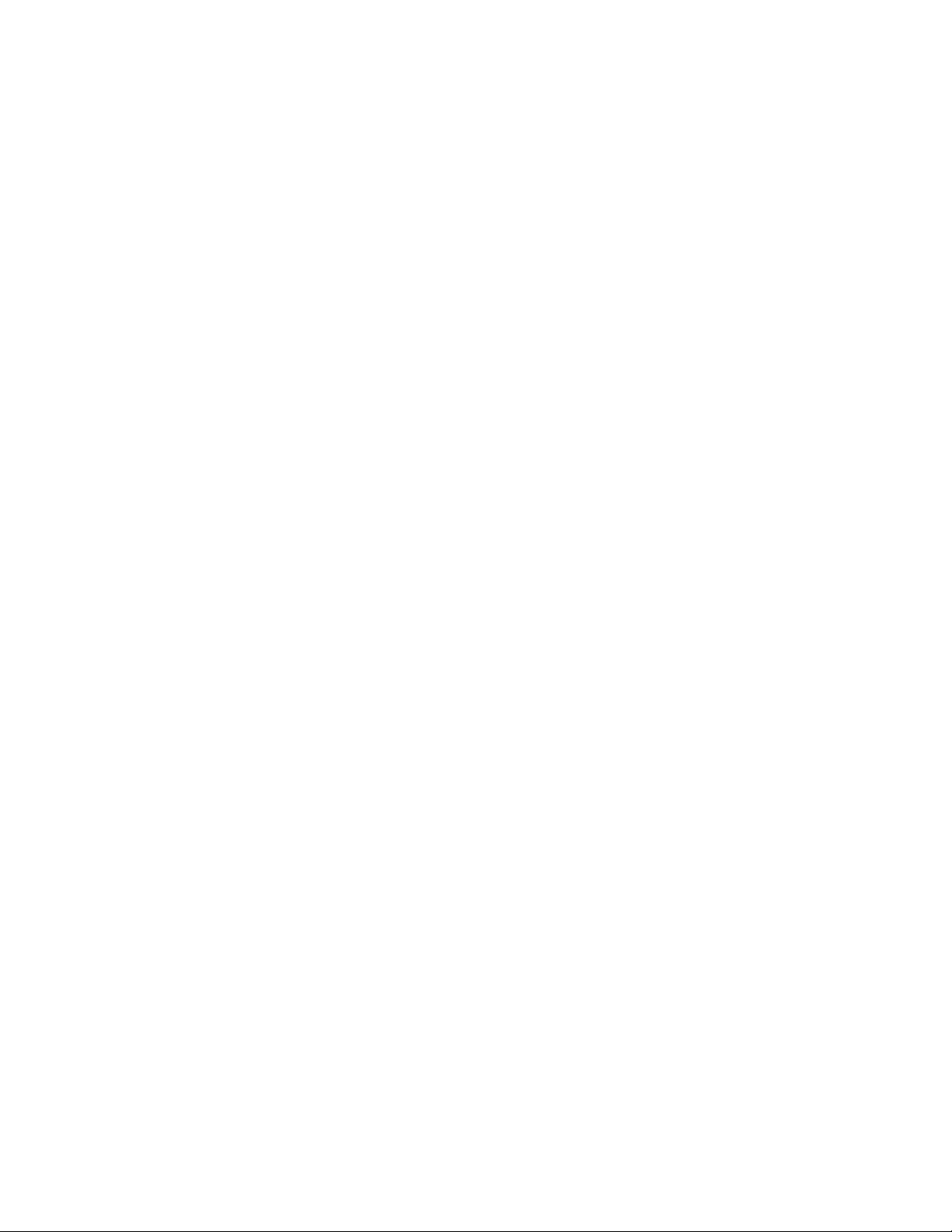
x950 Series Installation Guide for VCStack
259
Use the SHOW PLATFORM command to confirm that the port is
configured correctly for the transceiver. If necessary, use the
PLATFORM PORTMODE INTERFACE command to configure the
port. For more information, refer to “PLATFORM PORTMODE
INTERFACE” on page 188.
Changing a port from a 40Gbps transceiver or breakout cable to a
100Gbps transceiver requires resetting the switch. The same is
also true when replacing a 100Gbps transceiver with a 40Gbps
transceiver or breakout cable.
If the problem is with an 100Gbps transceiver, you might need to
adjust the Forward Error Correction (FEC) parameter on the port,
with the FEC command. Refer to the Software Reference for x950
Switch, AlliedWare Plus Operating System.
Problem 5: A 4x10Gbps breakout cable in port 25, 29, 33, or 37 on the
x950-28XSQ or x950-28XTQm switch, or in port 49, 53, 57, or 61 on the
x950-52XSQ switch cannot establish links with network devices.
Solutions: Try the following:
Check that the cable is fully inserted in the port.
Verify that the breakout cables are securely connected to the ports
on the network devices.
Use the SHOW PLATFORM command to confirm that the port is
configured for a breakout cable. If necessary, use the PLATFORM
PORTMODE INTERFACE command to configure the port. For
more information, refer to “PLATFORM PORTMODE INTERFACE”
on page 188.
If the port previously had a 100Gbps transceiver, you must reset
the switch after configuring it for a breakout cable.
Problem 6: An XEM2 line card in the expansion slot is not functioning.
Solutions: Try the following:
Visually inspect the card to verify that it is fully inserted into the
expansion slot.
If the problem is with an XEM2-12XTm Card, the switch might have
an earlier version of the AlliedWare Plus software that does not
support the card. The card requires v5.4.9-1 or later. Use the
SHOW VERSION command to display the version number.
Try installing the card in a different switch. If it still does not work,
the problem is probably with the card. Replace the card.
Try installing a different card in the switch. If the replacement card
fails to work, the problem is probably with the switch. Contact your
Allied Telesis sales representative for assistance.
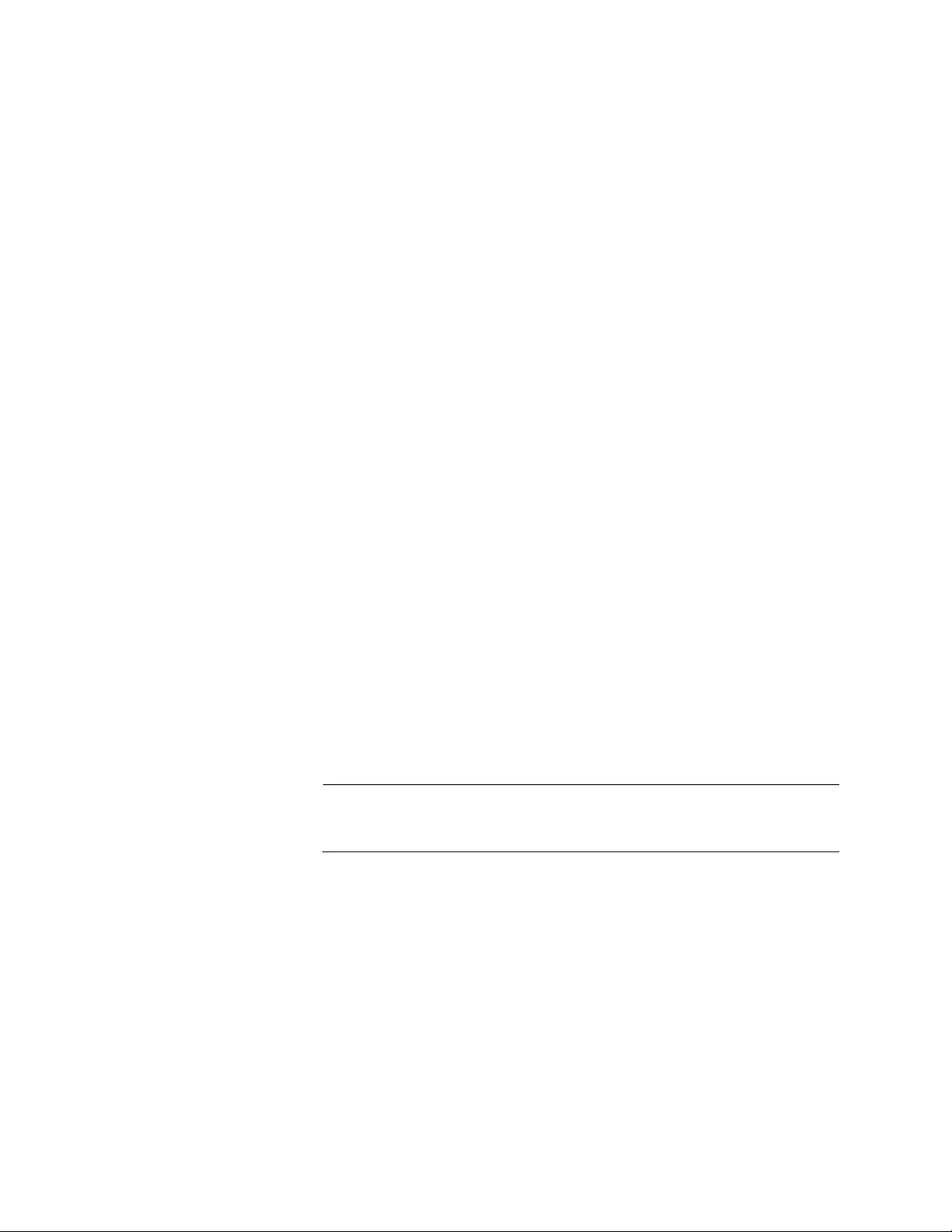
Chapter 15: Troubleshooting
260
Problem 7: An SFP, SFP+, or QSFP+ transceiver in an XEM2 line card is
unable to establish a link to another network device.
Solutions: Try the solutions to Problem 3.
Problem 8: A twisted pair port on the x950-28XTQm switch or an XEM2
line card cannot establish a link with a network device.
Solutions: Try the following:
Verify that the network device connected to the twisted pair port is
powered on and is operating properly.
Verify that the network device operates at a speed supported by
the card. The ports on the XEM2-12XT Card support 100Mbps and
1/10Gbps. The ports on the x950-28XTQm switch and
XEM2-8XSTm and XEM2-12XTm Cards support 100Mbps and
1/2.5/5/10Gbps. The ports do not support 10Mbps devices.
If the XEM2-12XT Card cannot establish links with 100Mbps
devices, the switch might have an earlier version of the AlliedWare
Plus management software. Support for 100Mbps devices on the
XEM2-12XT Card was added in version 5.4.9-1. Use the SHOW
VERSION command to display the version number. If necessary,
update the management software.
Try connecting another network device to the twisted pair port with
a different cable. If the twisted pair port is able to establish a link,
then the problem is with the cable or the other network device.
Verify that the twisted pair cable does not exceed 100 meters (328
feet).
Verify that you are using the appropriate category of twisted pair
cable. Refer to “Cabling Twisted Pair Ports” on page 226.
Verify that the port is connected to the correct twisted pair cable.
Note
1GBase/10GBase connections may require five to ten seconds to
establish links.
Problem 9: The SHOW STACK command is not displaying all the
switches in the stack.
Solutions: The switches are unable to form the stack. Try the following:
The switches might have an earlier version of the management
software that does not support VCStack, or they might have
different versions. The version must be 5.4.8-2 or later. You can
view the version number with the SHOW VERSION command.
Review the information in “Stack Trunks” on page 74 to verify that
the trunk complies with all rules and restrictions.
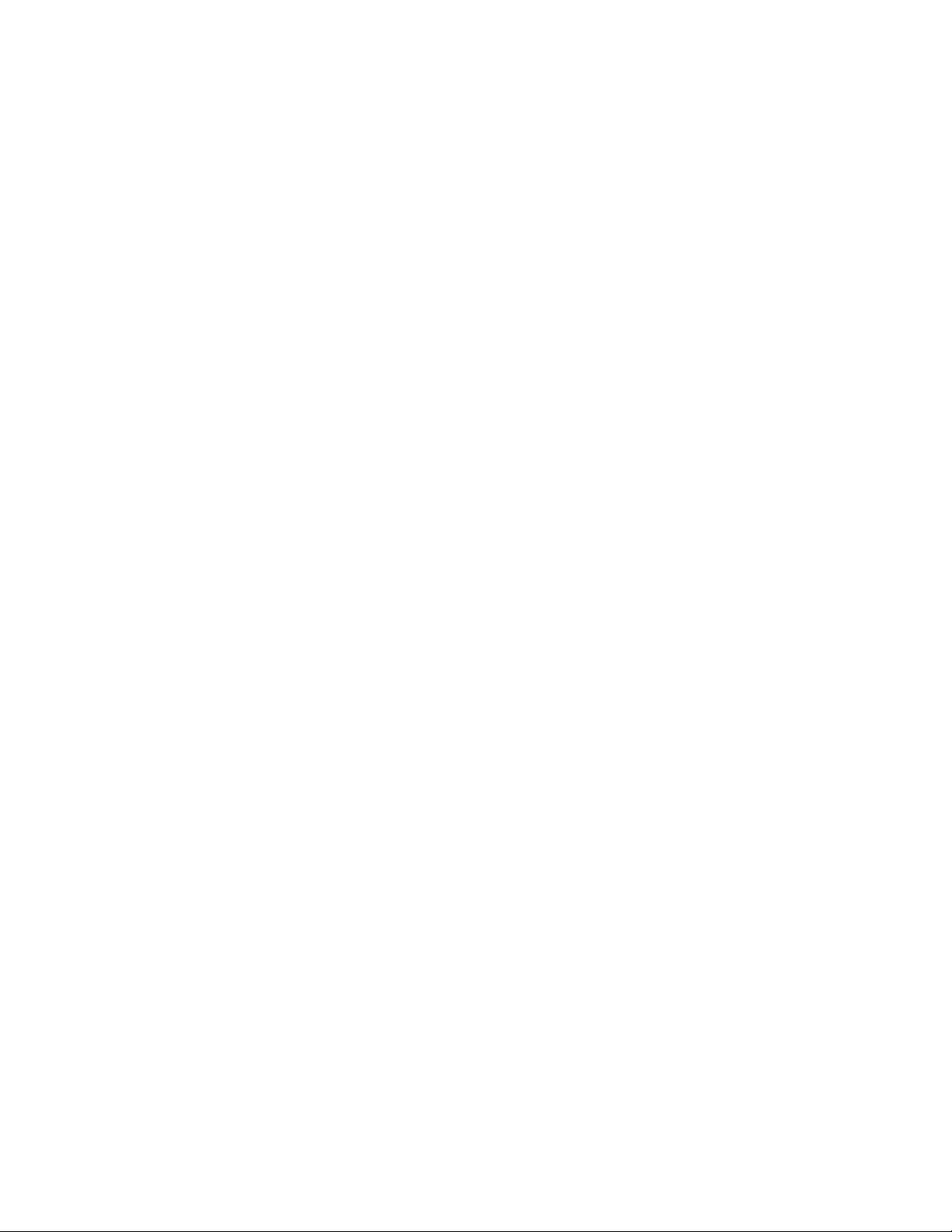
x950 Series Installation Guide for VCStack
261
If the trunk is using fiber optic transceivers, verify that they are fully
inserted into the ports.
Verify that the transceivers are from Allied Telesis.
Verify that the fiber optic cables are securely connected to the
ports on the transceivers.
Display the running configurations and confirm the ports of the
stack trunk. They are identified by the STACKPORT command. In
this example from a running configuration, ports 1 to 4 are the
stack trunk:
interface port1.0.1-1.0.4
stackport
If necessary, repeat the STACKPORT command. For information,
refer to “STACKPORT” on page 189. Afterwards, save your
changes and reboot the switch.
Problem 10: You removed a port from a stack trunk with the NO
STACKPORT command, but the port is still not forwarding regular
Ethernet traffic.
Display the running configuration to verify that the port is no longer
part of the stack trunk.
You have to reboot the switch whenever you add or remove ports
from stack trunks with the STACKPORT and NO STACKPORT
commands. Be sure to save the change to the configuration file
with the WRITE command before rebooting the unit.
Problem 11: The switch overheats and shuts down.
Solutions: Try the following:
Verify that the location of the switch allows for adequate airflow.
If the switch is operating, use the SHOW SYSTEM
ENVIRONMENT command in the Privileged Exec mode to verify
that the power supplies and fan modules are operating properly.
Problem 12: The switch functions intermittently.
Solutions: Try the following:
Use the SHOW SYSTEM ENVIRONMENT command in the
Privileged Exec mode to verify that the input voltage from the
power source to the switch is stable and within the approved
operating range. The unit will shut down if the input voltage
fluctuates above or below the approved operating range.
Use the SHOW SYSTEM ENVIRONMENT command in the
Privileged Exec mode to verify that the fan modules are operating
correctly.
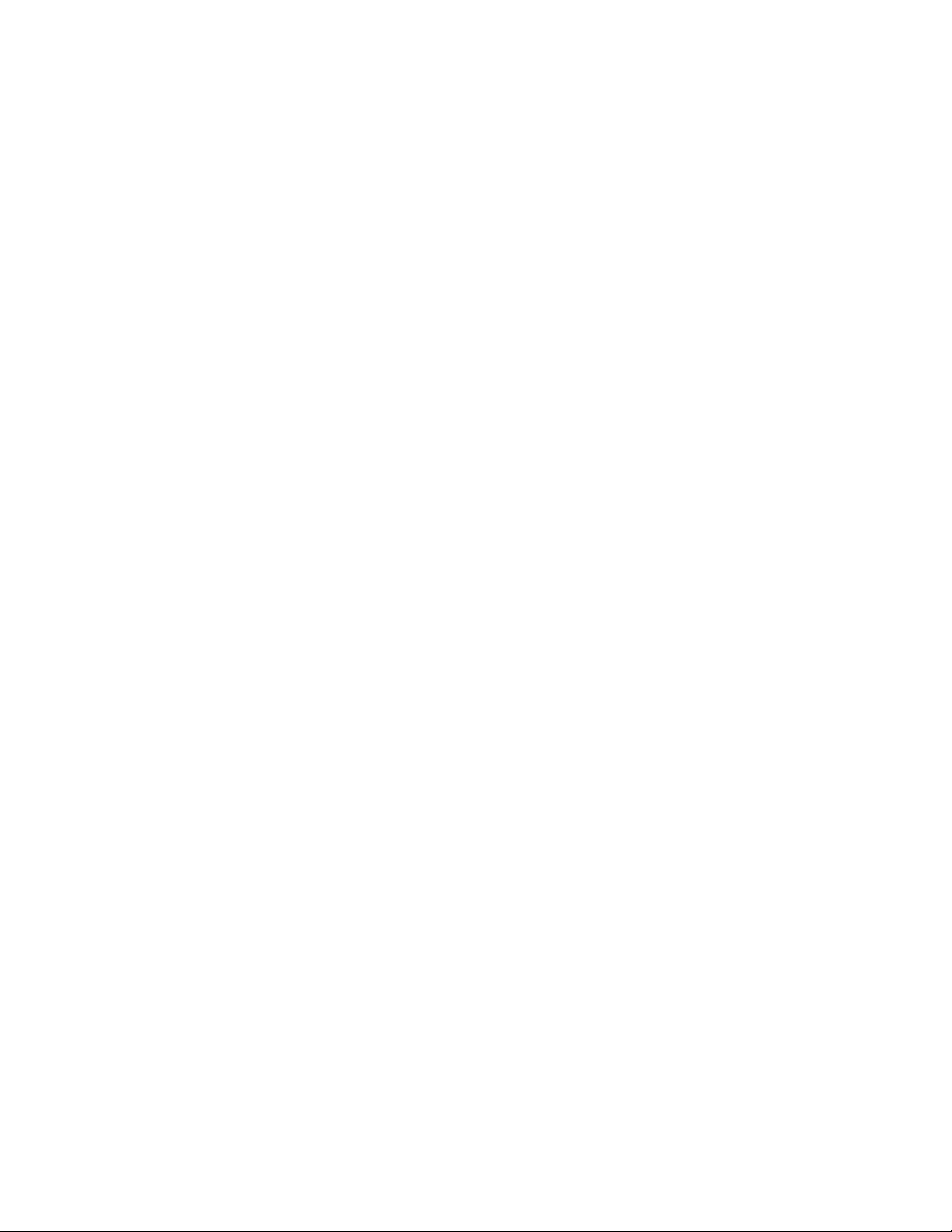
Chapter 15: Troubleshooting
262
Verify that the location of the switch allows for adequate airflow.
The unit will shut down if it overheats.
Problem 13: The Switch ID LED in the management panel is flashing “F.”
Solutions: One of the following problems has occurred:
A cooling fan has failed.
The internal temperature of the switch is outside the normal
operating range and the unit might shut down.
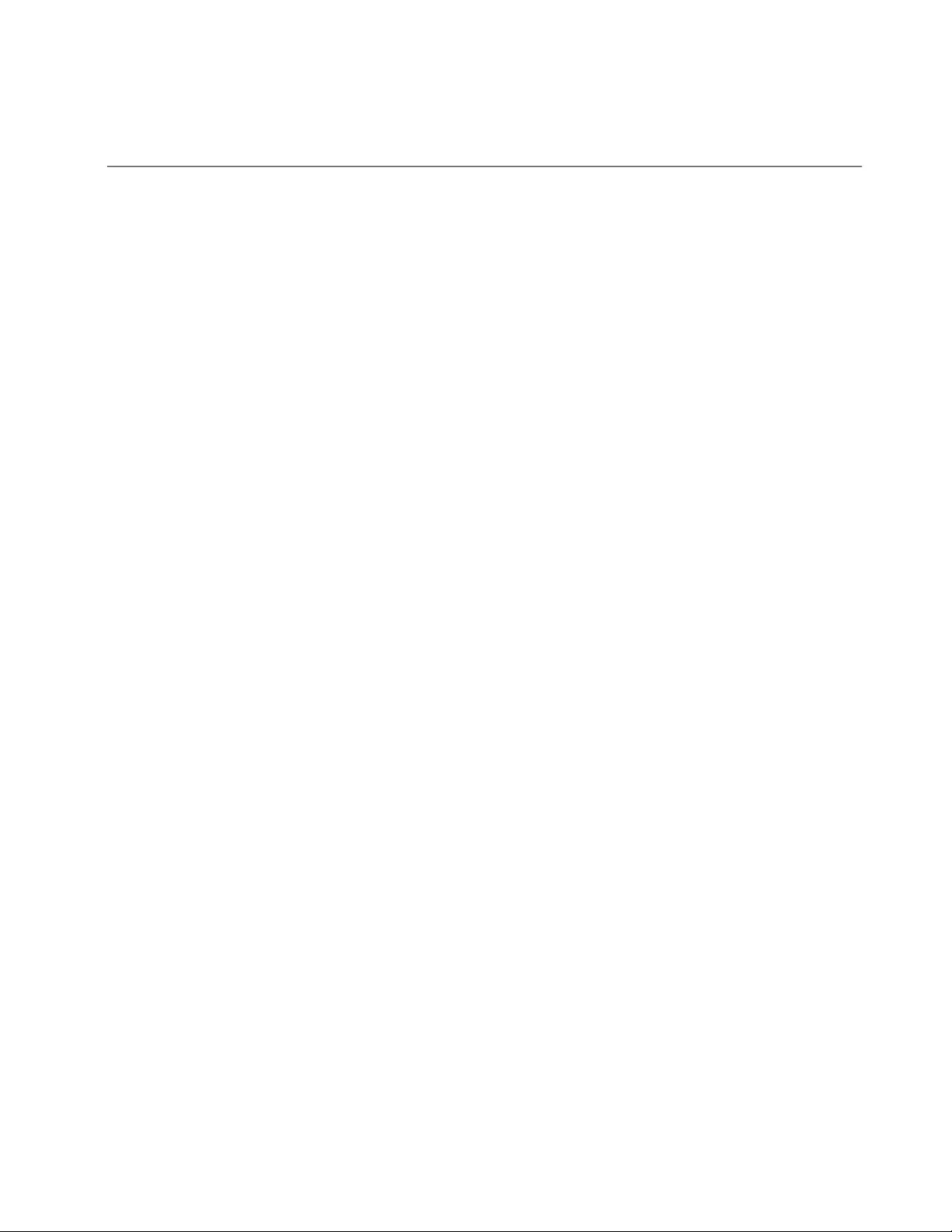
263
Appendix A
Technical Specifications
This appendix contains the following sections:
”Physical Specifications” on page 264
”Environmental Specifications” on page 267
”Power Specifications” on page 268
”Certifications” on page 277
”RJ-45 Twisted Pair Port Pinouts” on page 278
”RJ-45 Style Serial Console Port Pinouts” on page 280
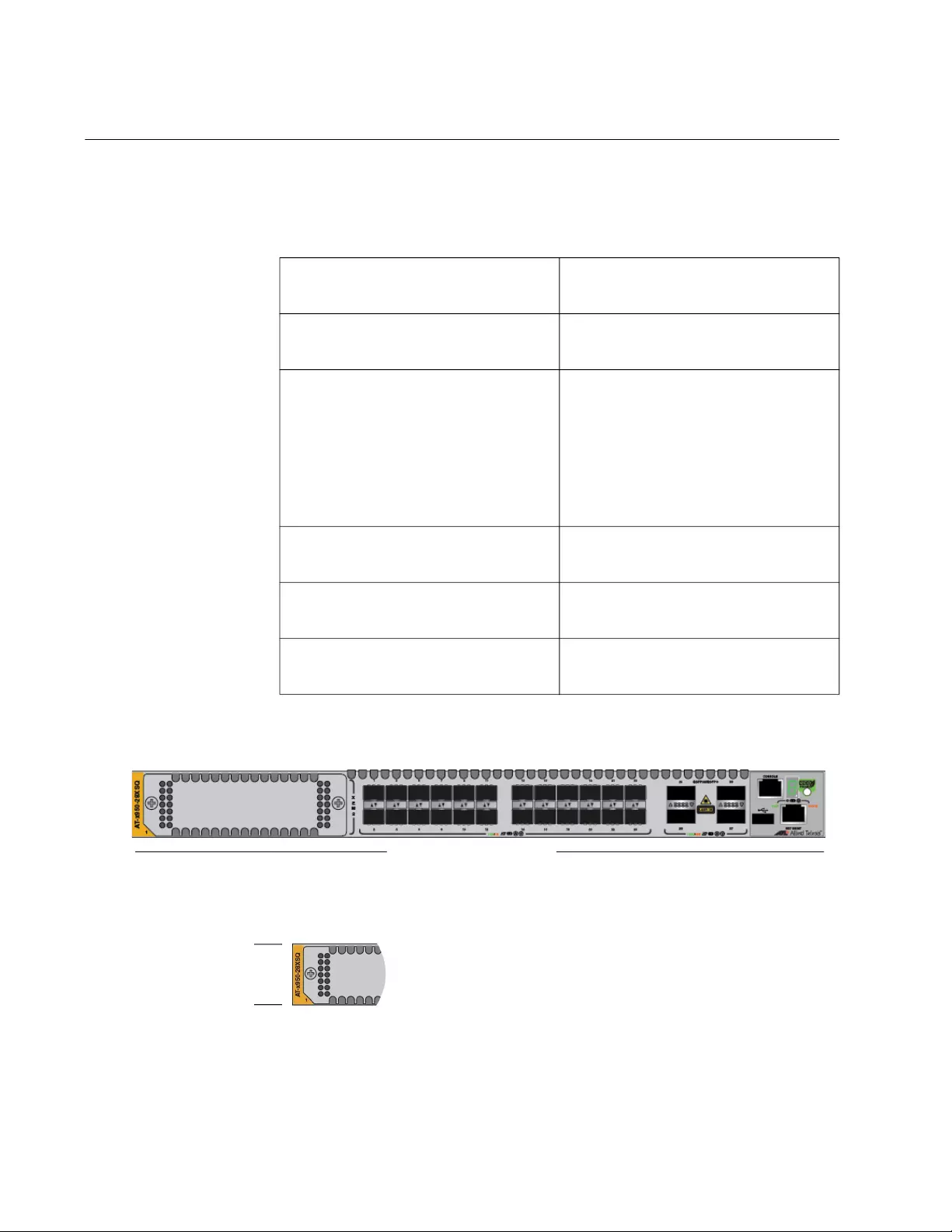
Appendix A: Technical Specifications
264
Physical Specifications
Dimensions (H x W x D)
Table 40 lists the dimensions of the switches and power supplies.
Figure 158. Switch Width and Height
Table 40. Product Dimensions
x950-28XSQ 4.4 cm x 44.0 cm x 44.5 cm
(1.7 in. x 17.3 in. x 17.5 in.)
x950-28XTQm 4.4 cm x 44.0 cm x 44.5 cm
(1.7 in. x 17.3 in. x 17.5 in.)
XEM2-8XSTm Line Card
XEM2-12XT Line Card
XEM2-12XTm Line Card
XEM2-12XS Line Card
XEM2-12XS v2 Line Card
XEM2-4QS Line Card
XEM2-1CQ Line Card
4.0 x 13.0 x 16.6 cm
(1.57 x 5.11 x 6.53 in.)
PWR600 AC 5.1 cm x 4.0 cm x 24.5 cm
(2.0 in. x 1.6 in. x 9.6 in.)
PWR600 DC 5.1 cm x 4.0 cm x 24.5 cm
(2.0 in. x 1.6 in. x 9.6 in.)
FAN05 4.3 cm x 15.2 cm x 10.0 cm
(1.7 in. x 6.0 in. x 3.9 in.)
44.0 cm (17.3 in.)
Width (Both Models)
4.4 cm (1.7 in.)
Height (Both Models)
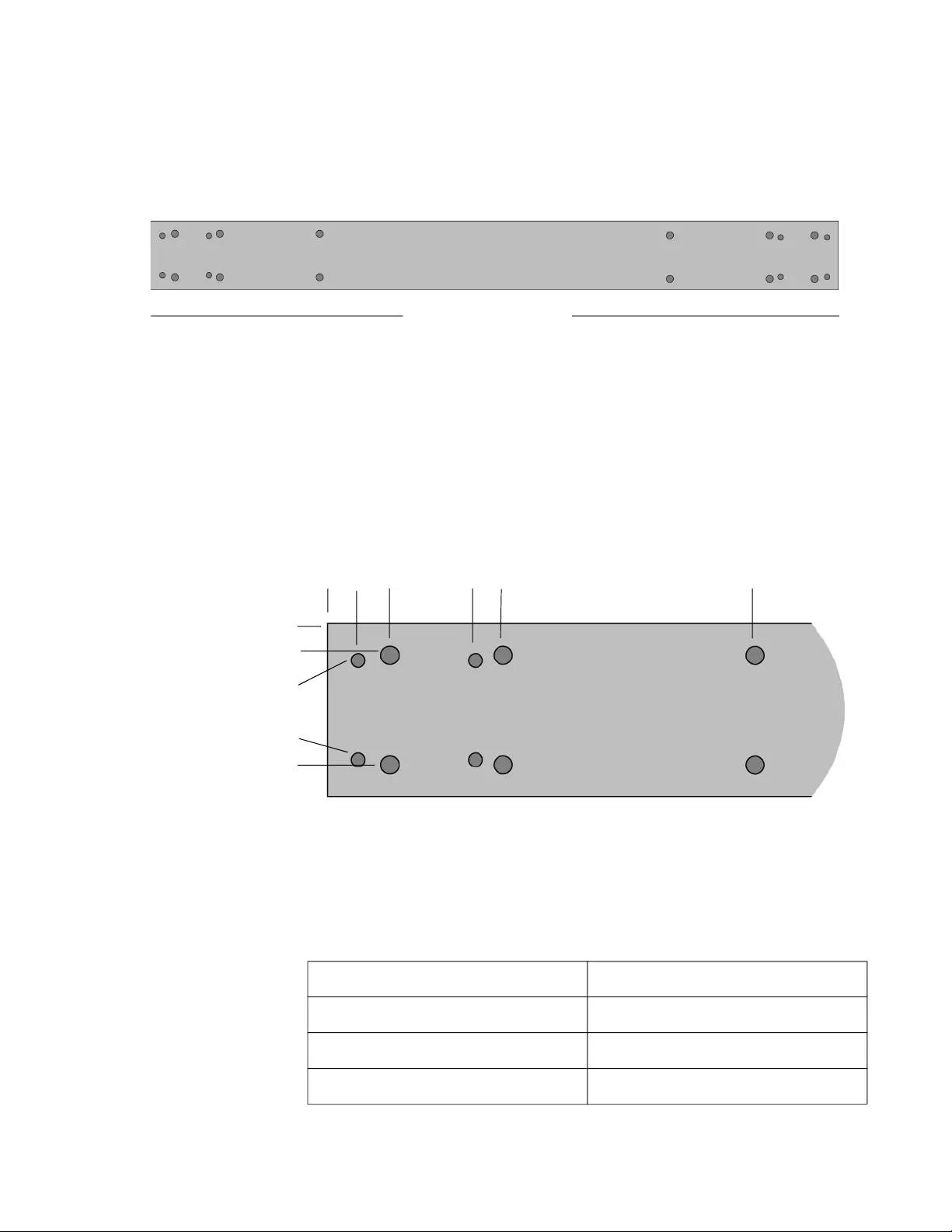
x950 Series Installation Guide for VCStack
265
The side dimension and locations of the bracket holes are shown in
Figure 159.
Figure 159. Switch Depth and Locations of Bracket Holes
Weights
Table 41 lists the weights of the switch and components.
0.00 mm (0.00 in.)
44.5 cm (17.5 in.)
Depth (Both Models)
7.85 mm (0.309 in.)
9.78 mm (0.385 in.)
35.84 mm (1.411 in.)
33.83 mm (1.332 in.)
Bracket Hole Locations (Both Models)
0.00 mm (0.000 in.)
10.16 mm (0.400 in.)
20.50 mm (0.807 in.)
34.21 mm (1.347 in.)
42.00 mm (1.654 in.)
97.98 mm (3.858 in.)
Table 41. Product Weights
x950-28XSQ Switch 7.21 kg (15.90 lb.)
x950-28XTQm Switch 7.33 kg (16.15 lb.)
x950-52XSQ Switch 7.35 kg (16.2 lb.)
XEM2-8XSTm Line Card 0.70 kg (1.54 lb.)
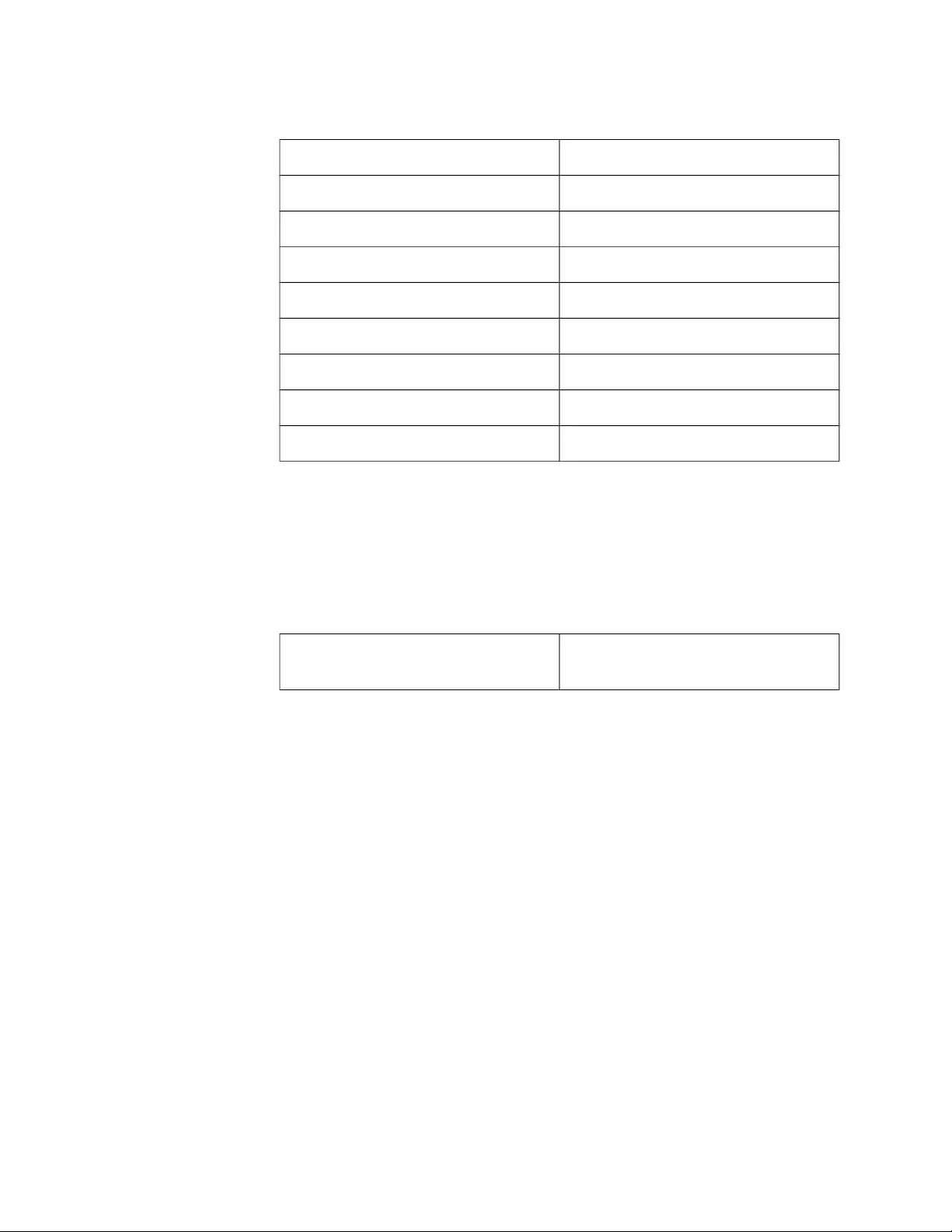
Appendix A: Technical Specifications
266
The weights of the switches include two cooling fan modules. They do not
include power supplies or line card.
Ventilation
Table 42 lists the ventilation requirements.
XEM2-12XT Line Card 0.75 kg (1.65 lb.)
XEM2-12XTm Line Card 1.04 kg (2.3 lb.)
XEM2-12XS Line Card 0.75 kg (1.65 lb.)
XEM2-12XS v2 Line Card 0.73 kg (1.60 lb)
XEM2-4QS Line Card 0.66 kg (1.45 lb.)
XEM2-1CQ Line Card 0.62 kg (1.37 lb.)
PWR600 AC 0.68 kg (1.5 lb.)
PWR600 DC 0.77 kg (1.7 lb.)
FAN05 0.34 kg (0.75 lb.)
Table 42. Ventilation Requirements
Recommended Minimum
Ventilation on All Sides
10 cm (4.0 in)
Table 41. Product Weights (Continued)
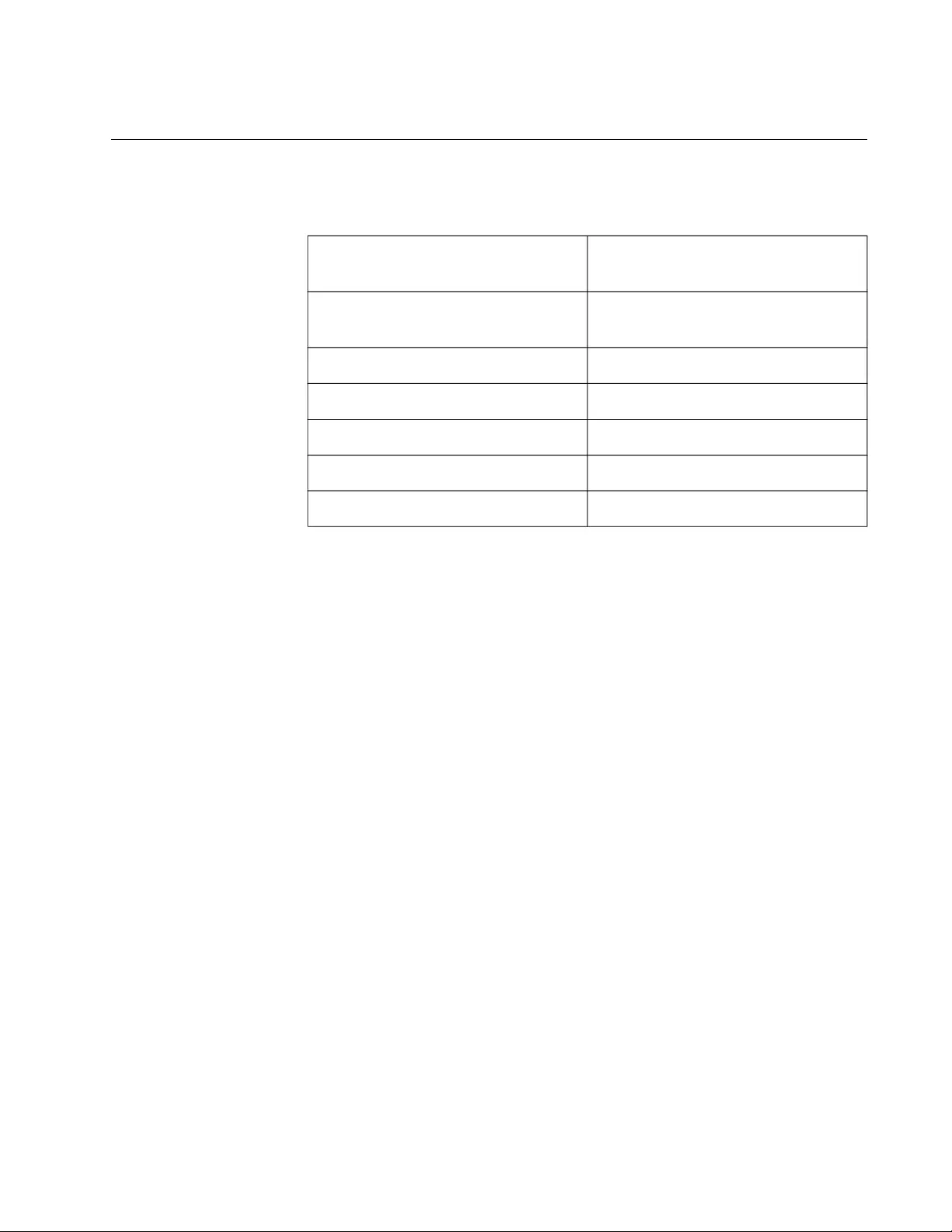
x950 Series Installation Guide for VCStack
267
Environmental Specifications
Table 43 lists the environmental specifications of the switches.
Table 43. Environmental Specifications
Operating Temperature
(with QSFP28 transceivers)
0° C to 45° C (32° F to 113° F)
Operating Temperature
(without QSFP28 transceivers)
0° C to 50° C (32° F to 122° F)
Storage Temperature -25° C to 70° C (-13° F to 158° F)
Operating Humidity 5% to 90% noncondensing
Storage Humidity 5% to 95% noncondensing
Maximum Operating Altitude 3,000 m (9,842 ft)
Maximum Nonoperating Altitude 4,000 m (13,100 ft)
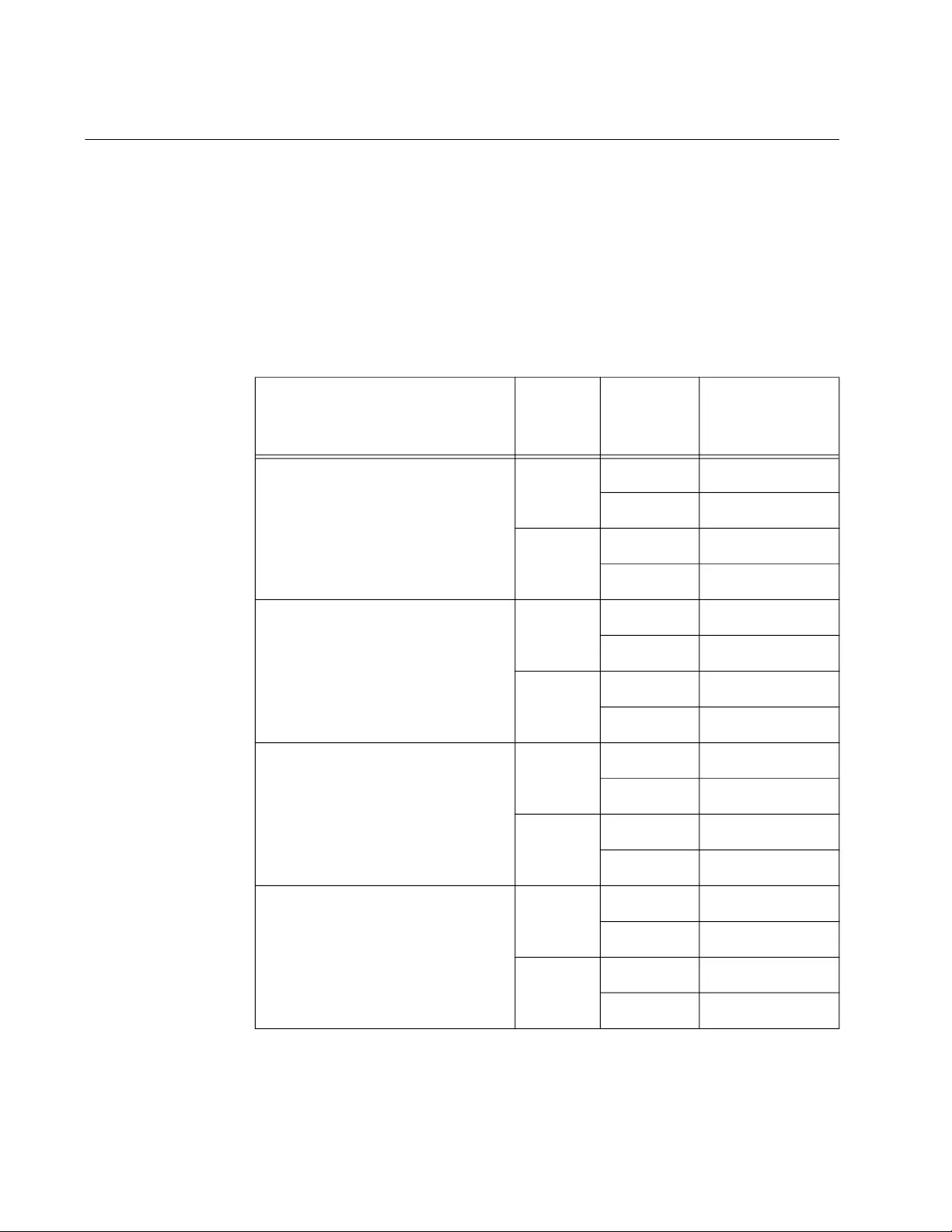
Appendix A: Technical Specifications
268
Power Specifications
This section contains the maximum power consumption values and input
voltages.
Maximum Power Consumptions
Table 44 list the maximum power consumptions for the x950-28XSQ
Switch.
Table 44. Maximum Power Consumptions (Watts) for the x950-28XSQ
Switch
x950-28XSQ Switch and Line
Card PWR600
Number of
Power
Supplies
Maximum
Power
Consumption
Switch - No card AC 1 206.08 W
2 231.22 W
DC 1 201.85 W
2 218.66 W
Switch plus XEM2-4QS Card AC 1 224.55 W
2 248.04 W
DC 1 219.80 W
2 236.11 W
Switch plus XEM2-12XT Card AC 1 251.07 W
2 271.85 W
DC 1 246.27 W
2 261.69 W
Switch plus XEM2-12XS Card AC 1 240.40 W
2 262.30 W
DC 1 235.66 W
2 251.44W
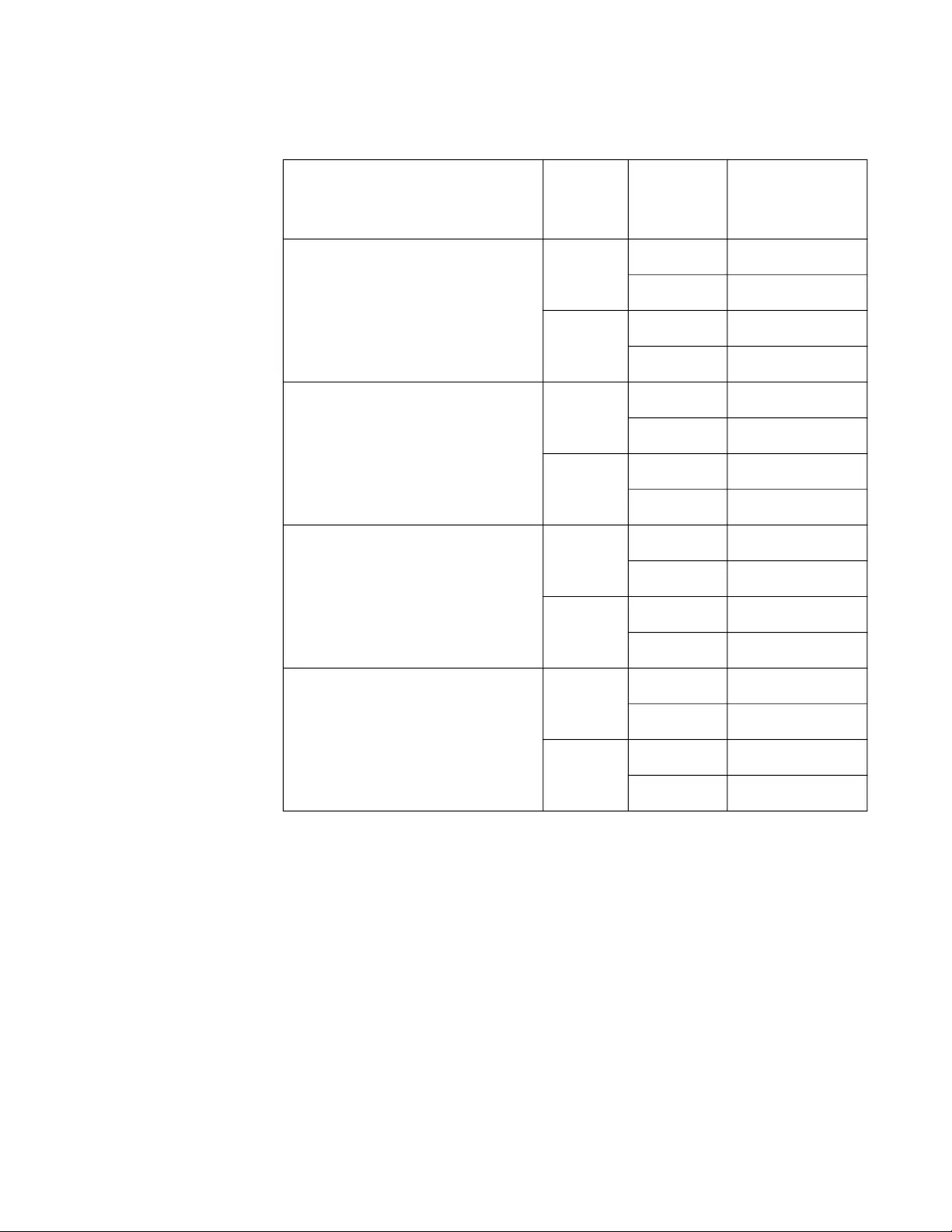
x950 Series Installation Guide for VCStack
269
Switch plus XEM2-1CQ Card AC 1 213.63 W
2 238.19 W
DC 1 209.36 W
2 226.04 W
Switch plus XEM2-12XTm Card AC 1 239.96 W
2 261.64 W
DC 1 233.73 W
2 249.67 W
Switch plus XEM2-12XS v2 Card AC 1 233.38 W
2 256.32 W
DC 1 227.97 W
2 244.19 W
Switch plus XEM2-8XSTm Card AC 1 226.71 W
2 250.27 W
DC 1 221.56 W
2 237.91 W
Table 44. Maximum Power Consumptions (Watts) for the x950-28XSQ Switch
(Continued)
x950-28XSQ Switch and Line
Card PWR600
Number of
Power
Supplies
Maximum
Power
Consumption
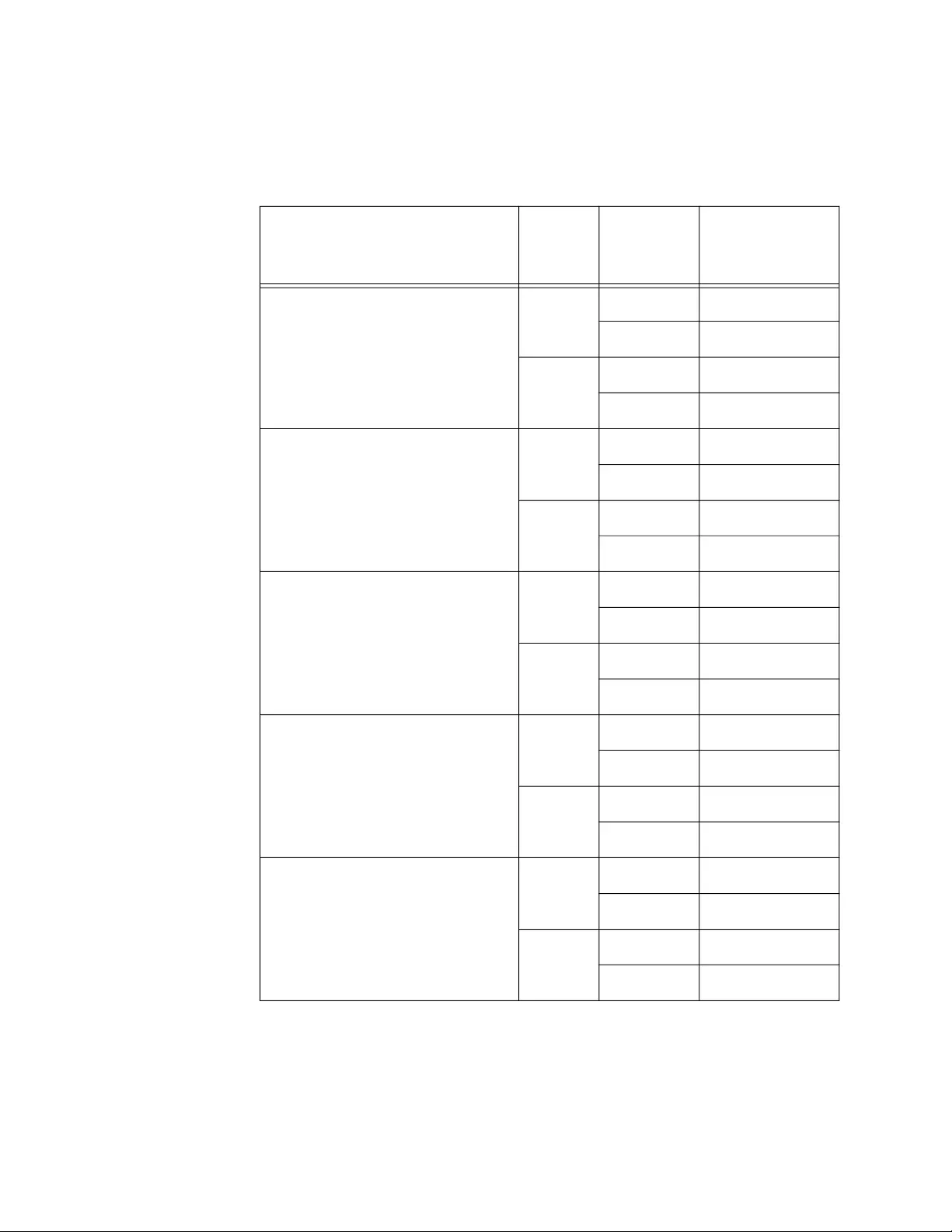
Appendix A: Technical Specifications
270
Table 45 list the maximum power consumptions for the x950-28XTQm
Switch.
Table 45. Maximum Power Consumptions (Watts) for the x950-28XTQm
Switch
x950-28XTQm Switch and Line
Card PWR600
Number of
Power
Supplies
Maximum
Power
Consumption
Switch - No card AC 1 234.55 W
2 255.26 W
DC 1 222.55 W
2 238.80 W
Switch plus XEM2-4QS Card AC 1 253.19 W
2 271.68 W
DC 1 240.59 W
2 256.15 W
Switch plus XEM2-12XT Card AC 1 280.51 W
2 295.82 W
DC 1 267.19 W
2 281.79 W
Switch plus XEM2-12XS Card AC 1 269.62 W
2 286.18 W
DC 1 256.71 W
2 271.49 W
Switch plus XEM2-1CQ Card AC 1 241.95 W
2 261.74 W
DC 1 230.07 W
2 246.02 W
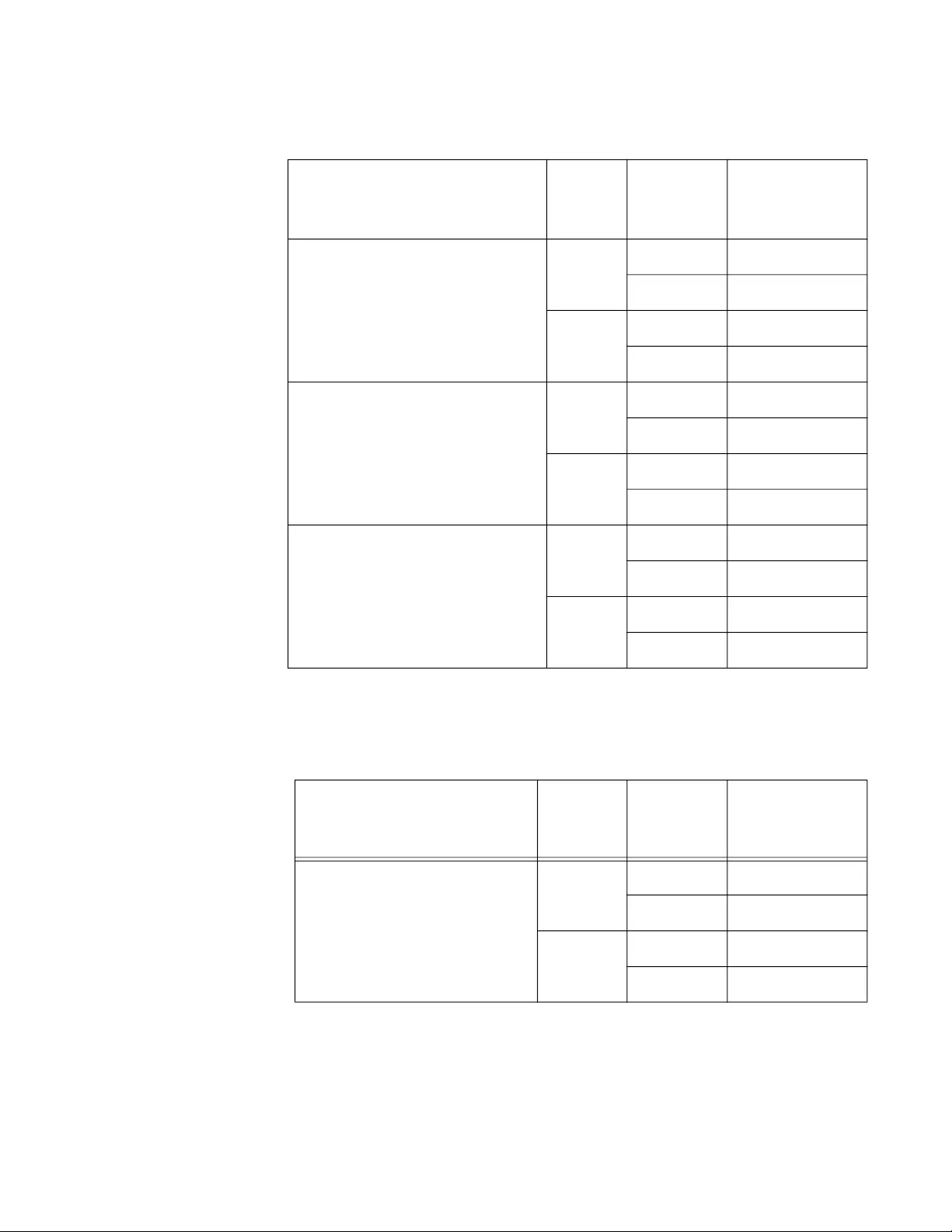
x950 Series Installation Guide for VCStack
271
Table 46 lists the maximum power consumptions for the x950-52XSQ
Switch.
Switch plus XEM2-12XTm Card AC 1 267.89 W
2 284.63 W
DC 1 254.83 W
2 269.90 W
Switch plus XEM2-12XS v2 Card AC 1 261.97 W
2 280.37 W
DC 1 248.92 W
2 264.26 W
Switch plus XEM2-8XSTm Card AC 1 255.31 W
2 273.90 W
DC 1 242.46 W
2 258.15 W
Table 46. Maximum Power Consumptions (Watts) for the x950-52XSQ
Switch
PWR600
Number of
Power
Supplies
Maximum
Power
Consumption
x950-52XSQ Switch
AC 1 246.26 W
2 266.12 W
DC 1 229.90 W
2 247.40 W
Table 45. Maximum Power Consumptions (Watts) for the x950-28XTQm
Switch (Continued)
x950-28XTQm Switch and Line
Card PWR600
Number of
Power
Supplies
Maximum
Power
Consumption
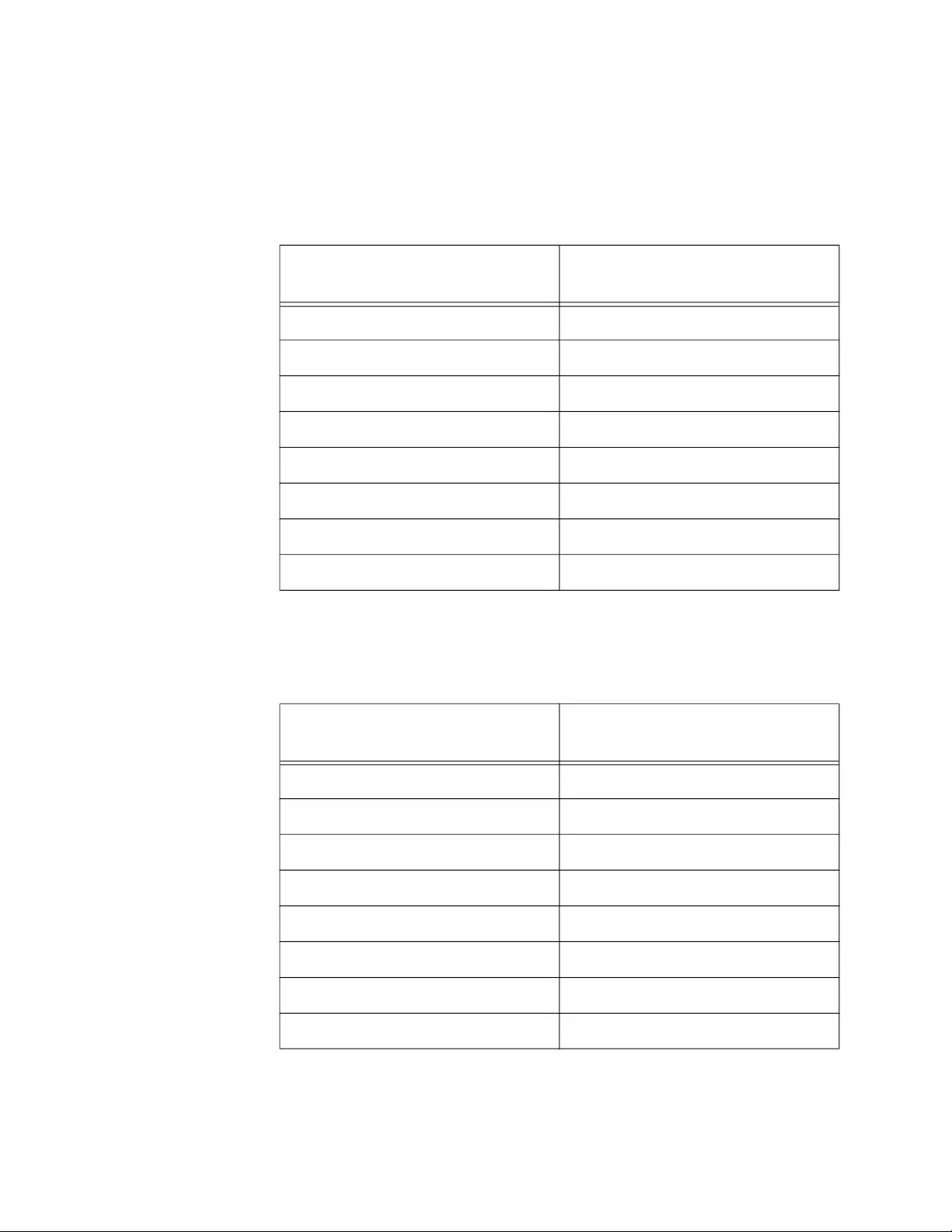
Appendix A: Technical Specifications
272
Typical Power Savings in eco-friendly Mode
Table 47 lists the typical power savings in eco-friendly mode for the
x950-28XSQ Switch.
Table 48 lists the typical power savings in eco-friendly mode for the x950-
28XTQm Switch.
Table 47. Typical Power Savings in eco-friendly Mode (Watts) for the
x950-28XSQ Switch
x950-28XSQ Switch and Line
Card Power Savings
Switch - No card 0.53 W
Switch plus XEM2-4QS Card 0.64 W
Switch plus XEM2-12XT Card 0.64 W
Switch plus XEM2-12XS Card 0.66 W
Switch plus XEM2-1CQ Card 0.55 W
Switch plus XEM2-12XTm Card 0.64 W
Switch plus XEM2-12XS v2 Card 0.84 W
Switch plus XEM2-8XSTm Card 0.81 W
Table 48. Typical Power Savings in eco-friendly Mode (Watts) for the
x950-28XTQm Switch
x950-28XTQm Switch and Line
Card Power Savings
Switch - No card 0.73 W
Switch plus XEM2-4QS Card 0.84 W
Switch plus XEM2-12XT Card 0.84 W
Switch plus XEM2-12XS Card 0.86 W
Switch plus XEM2-1CQ Card 0.75 W
Switch plus XEM2-12XTm Card 0.84 W
Switch plus XEM2-12XS v2 Card 0.84 W
Switch plus XEM2-8XSTm Card 0.81 W
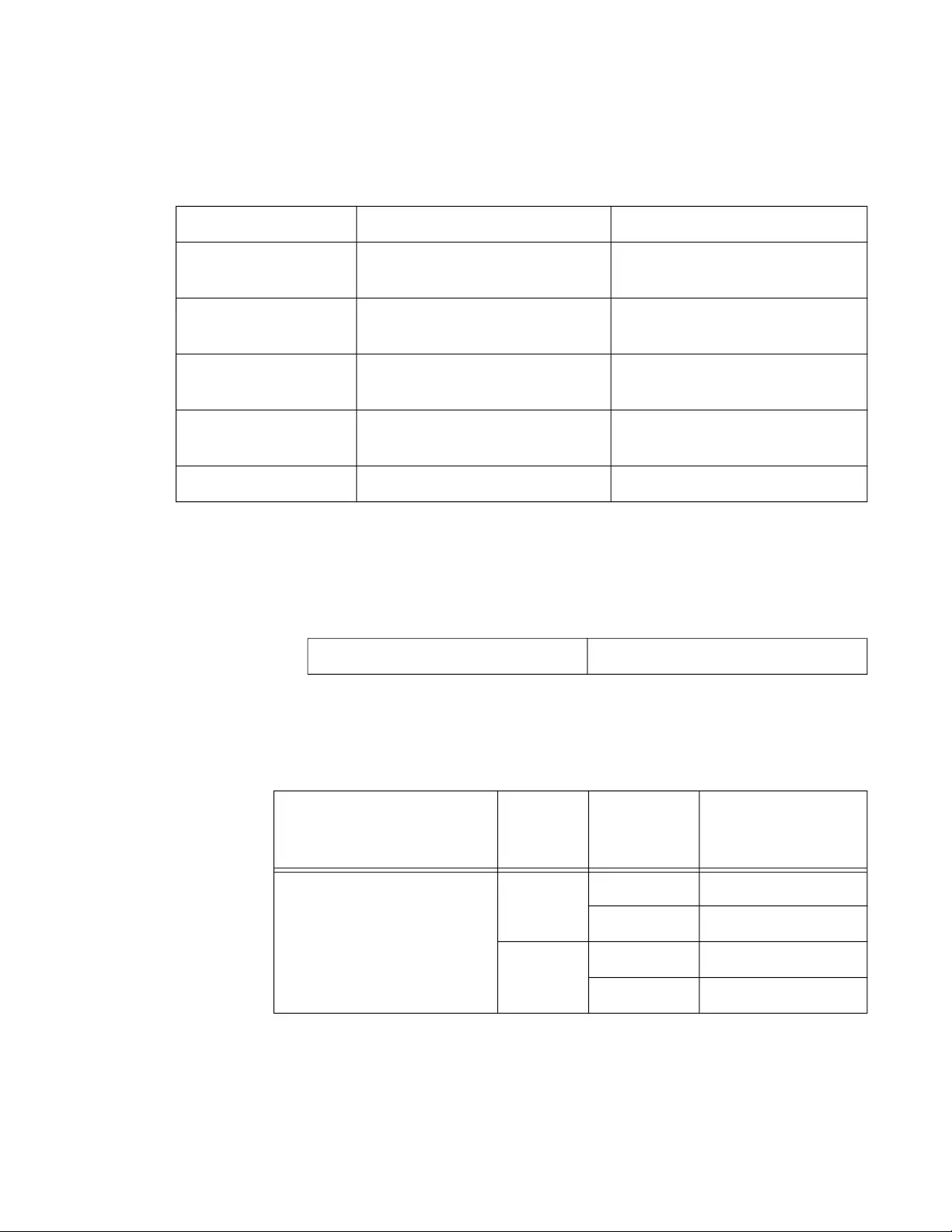
x950 Series Installation Guide for VCStack
273
Input Voltage
Table 49 lists the input voltage for the power supply.
Maximum Power Supply Efficiency
Table 50 lists the maximum power supply efficiency.
Heat Dissipations
Table 51 lists the heat dissipations for the x950-28XSQ Switch.
Table 49. Input Voltages
AC DC
x950-28XSQ Switch 100-240 VAC~, 4A maximum,
50/60 Hz (per inputx2)
40-60V DC, 6.0A (per Input x2)
x950-28XTQm Switch 100-240 VAC~, 4A maximum,
50/60 Hz (per inputx2)
40-60V DC, 6.0A (per Input x2)
x950-52XSQ Switch 100-240 VAC~, 4A maximum,
50/60 Hz (per inputx2)
40-60V DC, 6.0A (per Input x2)
PWR600 AC 100-240 VAC~, 8.7A maximum,
50/60 Hz (per input) N/A
PWR600 DC N/A 40-72 VDC, 6.0A maximum
Table 50. Maximum Power Supply Efficiency (Based on 100V Input
Voltage)
PWR600 AC Power Supply Up to 85%
Table 51. Heat Dissipations for the x950-28XSQ Switch
x950-28XSQ Switch and
Line Card PWR600
Number of
Power
Supplies
Heat Dissipation
(British Thermal
Units/Hour)
Switch - No card AC 1 703.24 BTU/hr
2 789.03 BTU/hr
DC 1 688.80 BTU/hr
2 746.16 BTU/hr
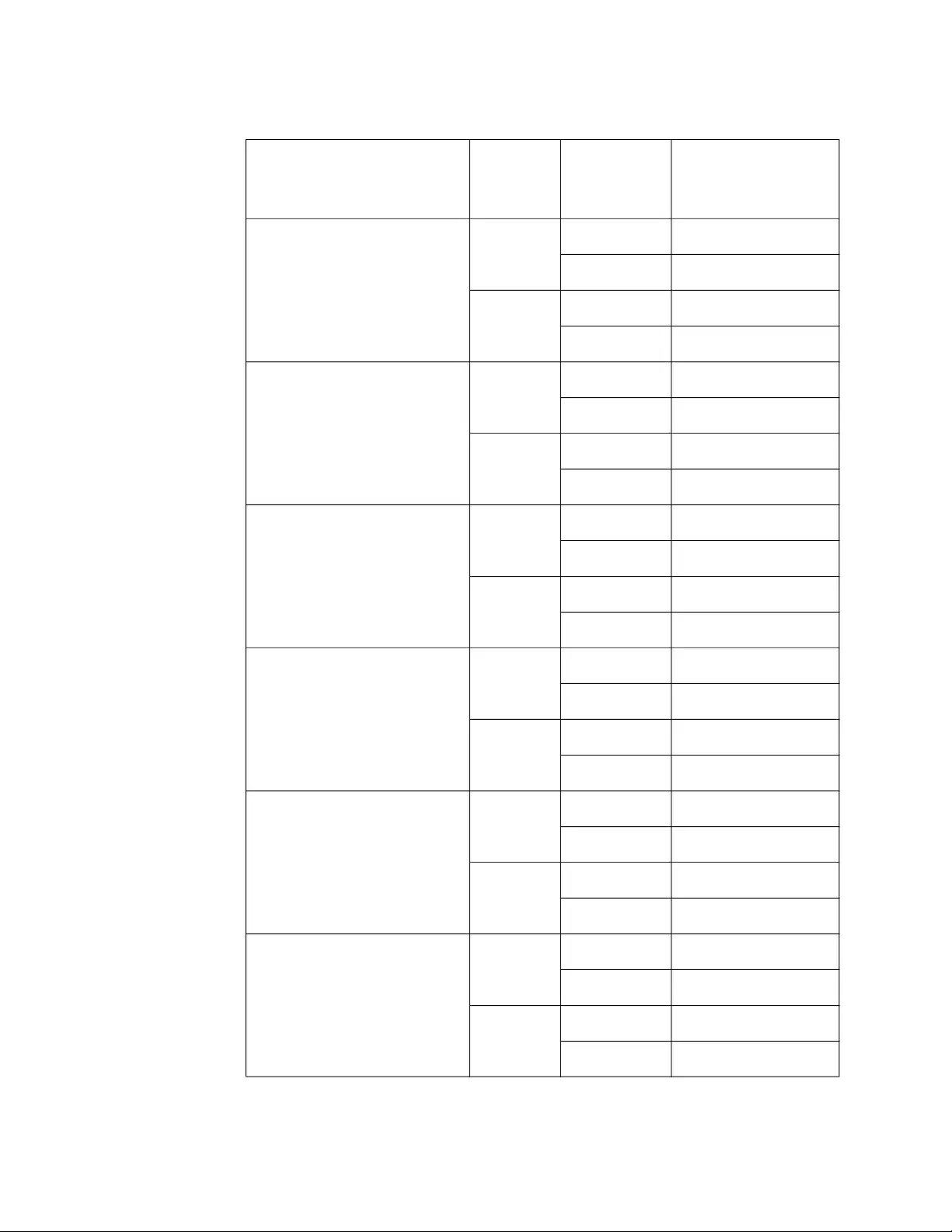
Appendix A: Technical Specifications
274
Switch plus XEM2-4QS
Card
AC 1 766.27 BTU/hr
2 846.43 BTU/hr
DC 1 750.05 BTU/hr
2 805.71 BTU/hr
Switch plus XEM2-12XT
Card
AC 1 856.77 BTU/hr
2 927.68 BTU/hr
DC 1 840.40 BTU/hr
2 893.01 BTU/hr
Switch plus XEM2-12XS
Card
AC 1 820.36 BTU/hr
2 895.09 BTU/hr
DC 1 804.17 BTU/hr
2 858.03 BTU/hr
Switch plus XEM2-1CQ
Card
AC 1 729.01 BTU/hr
2 812.82 BTU/hr
DC 1 714.43 BTU/hr
2 771.36 BTU/hr
Switch plus XEM2-12XTm
Card
AC 1 818.86 BTU/hr
2 892.84 BTU/hr
DC 1 797.61 BTU/hr
2 851.99 BTU/hr
Switch plus XEM2-12XS v2
Card
AC 1 796.40 BTU/hr
2 874.69 BTU/hr
DC 1 777.95 BTU/hr
2 833.31 BTU/hr
Table 51. Heat Dissipations for the x950-28XSQ Switch (Continued)
x950-28XSQ Switch and
Line Card PWR600
Number of
Power
Supplies
Heat Dissipation
(British Thermal
Units/Hour)
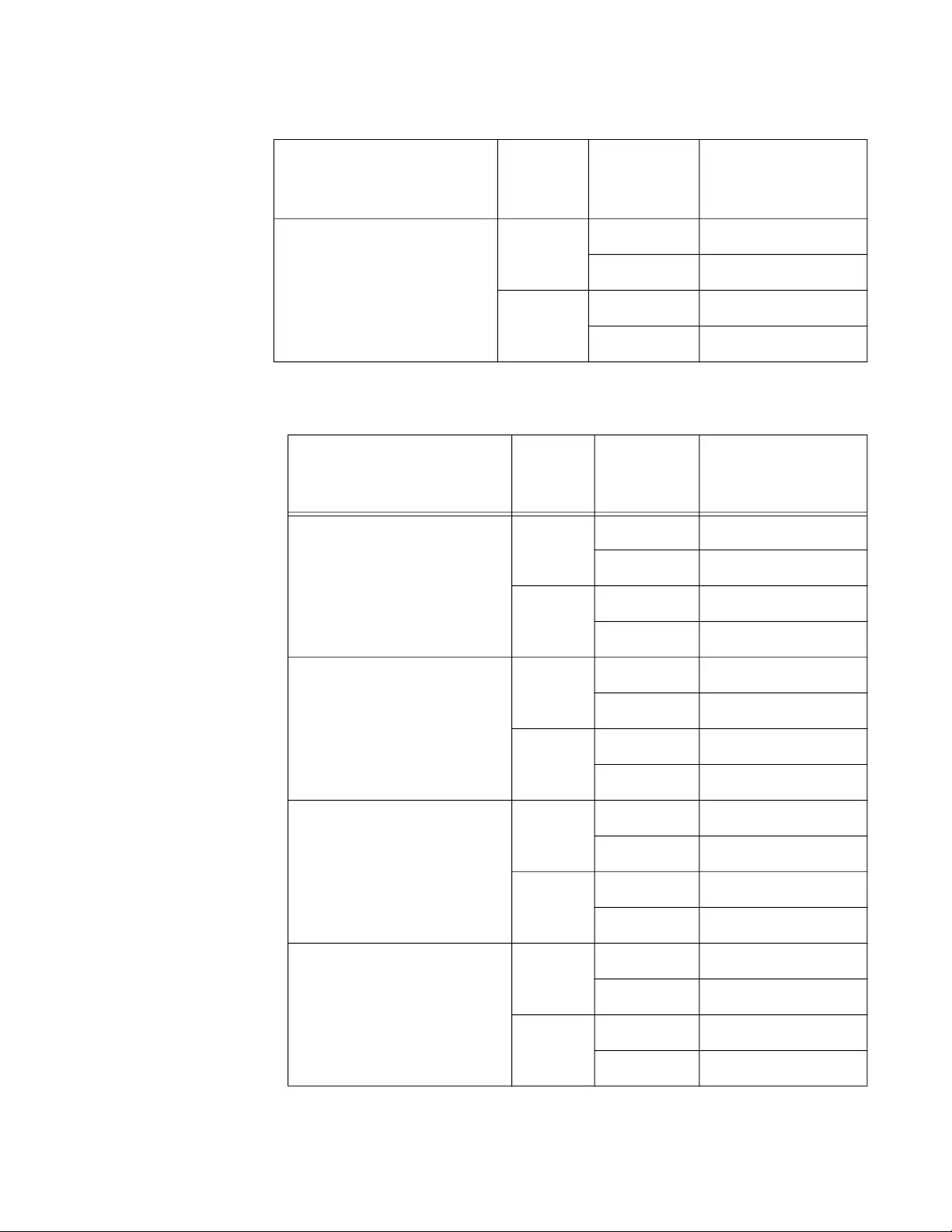
x950 Series Installation Guide for VCStack
275
Table 52 lists the heat dissipations for the x950-28XTQm Switch.
Switch plus XEM2-8XSTm
Card
AC 1 773.64 BTU/hr
2 854.04 BTU/hr
DC 1 756.07 BTU/hr
2 811.85 BTU/hr
Table 51. Heat Dissipations for the x950-28XSQ Switch (Continued)
x950-28XSQ Switch and
Line Card PWR600
Number of
Power
Supplies
Heat Dissipation
(British Thermal
Units/Hour)
Table 52. Heat Dissipations for the x950-28XTQm Switch
x950-28XTQm Switch and
Line Card PWR600
Number of
Power
Supplies
Heat Dissipation
(British Thermal
Units/Hour)
Switch - No card AC 1 800.40 BTU/hr
2 871.07 BTU/hr
DC 1 759.43 BTU/hr
2 814.90 BTU/hr
Switch plus XEM2-4QS
Card
AC 1 864.01 BTU/hr
2 927.10 BTU/hr
DC 1 821.00 BTU/hr
2 874.12 BTU/hr
Switch plus XEM2-12XT
Card
AC 1 957.23 BTU/hr
2 1009.48 BTU/hr
DC 1 911.79 BTU/hr
2 961.62 BTU/hr
Switch plus XEM2-12XS
Card
AC 1 920.07 BTU/hr
2 976.58 BTU/hr
DC 1 876.02 BTU/hr
2 926.45 BTU/hr
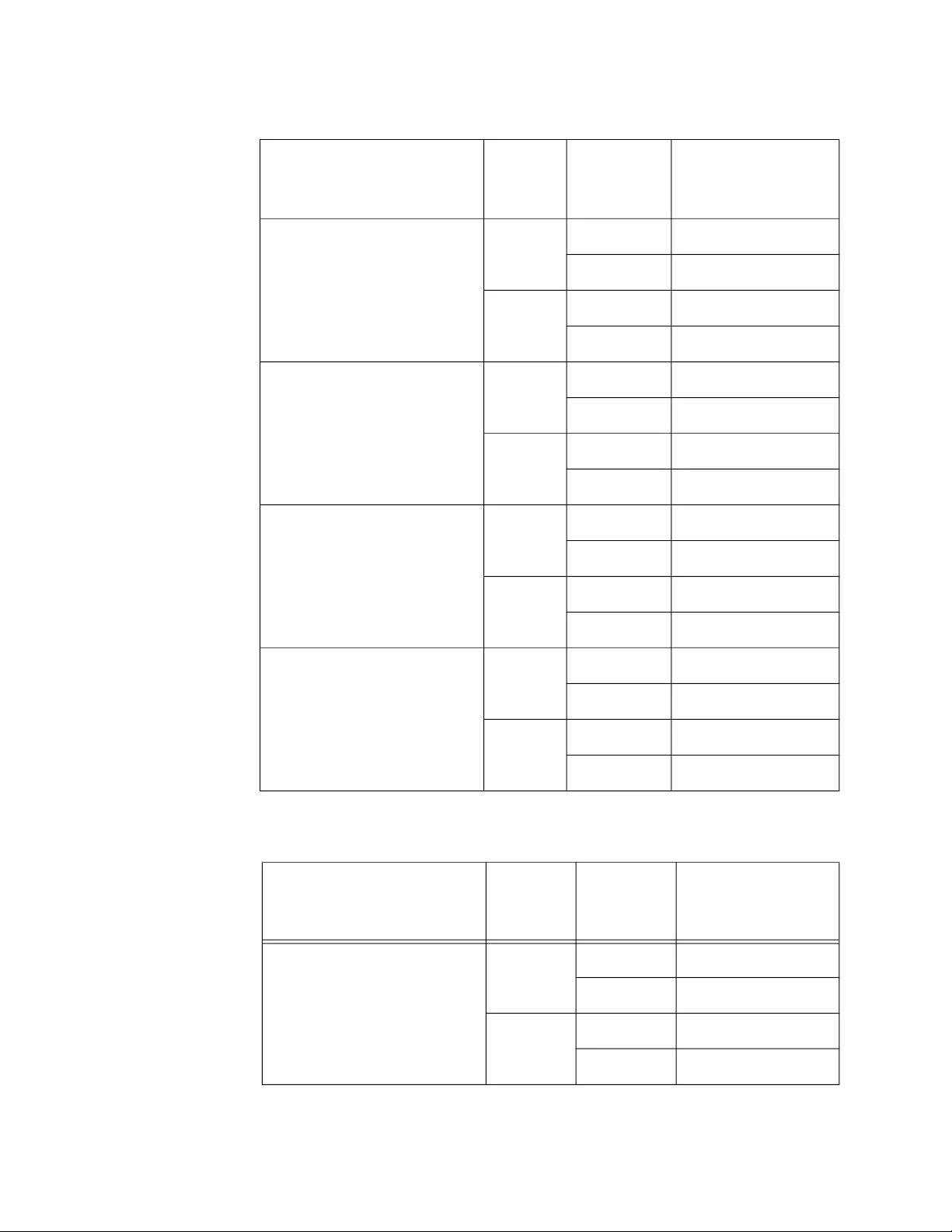
Appendix A: Technical Specifications
276
Table 53 list the heat dissipations for the x950-52XSQ Switch.
Switch plus XEM2-1CQ
Card
AC 1 825.65 BTU/hr
2 893.18 BTU/hr
DC 1 785.09 BTU/hr
2 839.52 BTU/hr
Switch plus XEM2-12XTm
Card
AC 1 914.17 BTU/hr
2 971.29 BTU/hr
DC 1 869.62 BTU/hr
2 921.01 BTU/hr
Switch plus XEM2-12XS v2
Card
AC 1 893.97 BTU/hr
2 956.76 BTU/hr
DC 1 849.44 BTU/hr
2 901.77 BTU/hr
Switch plus XEM2-8XSTm
Card
AC 1 871.24 BTU/hr
2 934.68 BTU/hr
DC 1 827.40 BTU/hr
2 880.92 BTU/hr
Table 53. Heat Dissipations for the x950-52XSQ Switch
PWR600
Number of
Power
Supplies
Heat Dissipation
(British Thermal
Units/Hour)
x950-52XSQ Switch
AC 1 840.36 BTU/hr
2 908.13 BTU/hr
DC 1 784.53 BTU/hr
2 844.25 BTU/hr
Table 52. Heat Dissipations for the x950-28XTQm Switch (Continued)
x950-28XTQm Switch and
Line Card PWR600
Number of
Power
Supplies
Heat Dissipation
(British Thermal
Units/Hour)
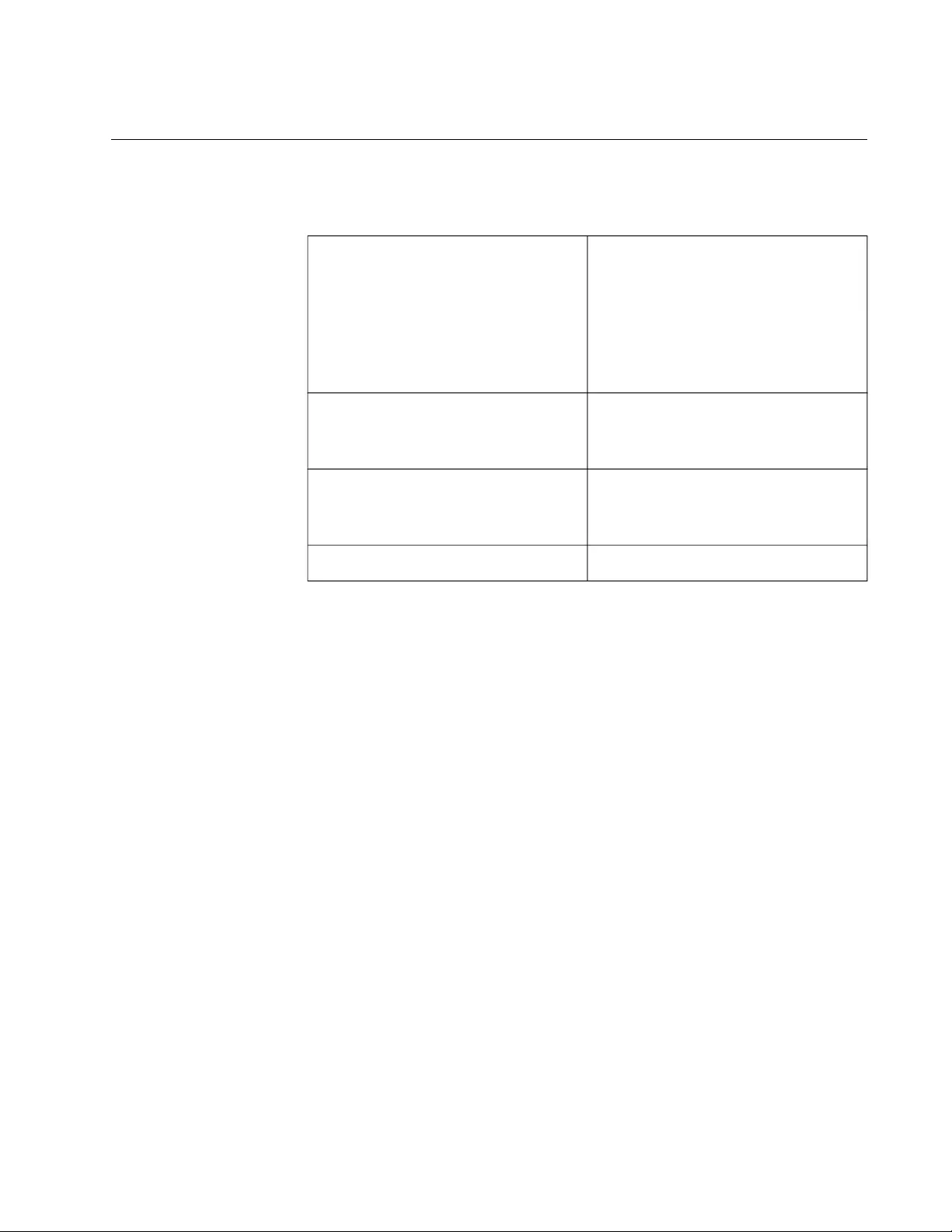
x950 Series Installation Guide for VCStack
277
Certifications
Table 54 lists the product certificates.
Table 54. Product Certifications
EMI (Emissions) FCC Class A
CISPR 22 Class A
EN 55032 Class A
VCCI Class A
ICES-003 Class A
RCM
EAC Certification
EMC (Immunity) EN 55024
EN 61000-3-2
EN 61000-3-3
Electrical and Laser Safety UL 60950-1 (CULUS)
EN 62368-1 (TUV)
EN 60825-1
RoHS RoHS6
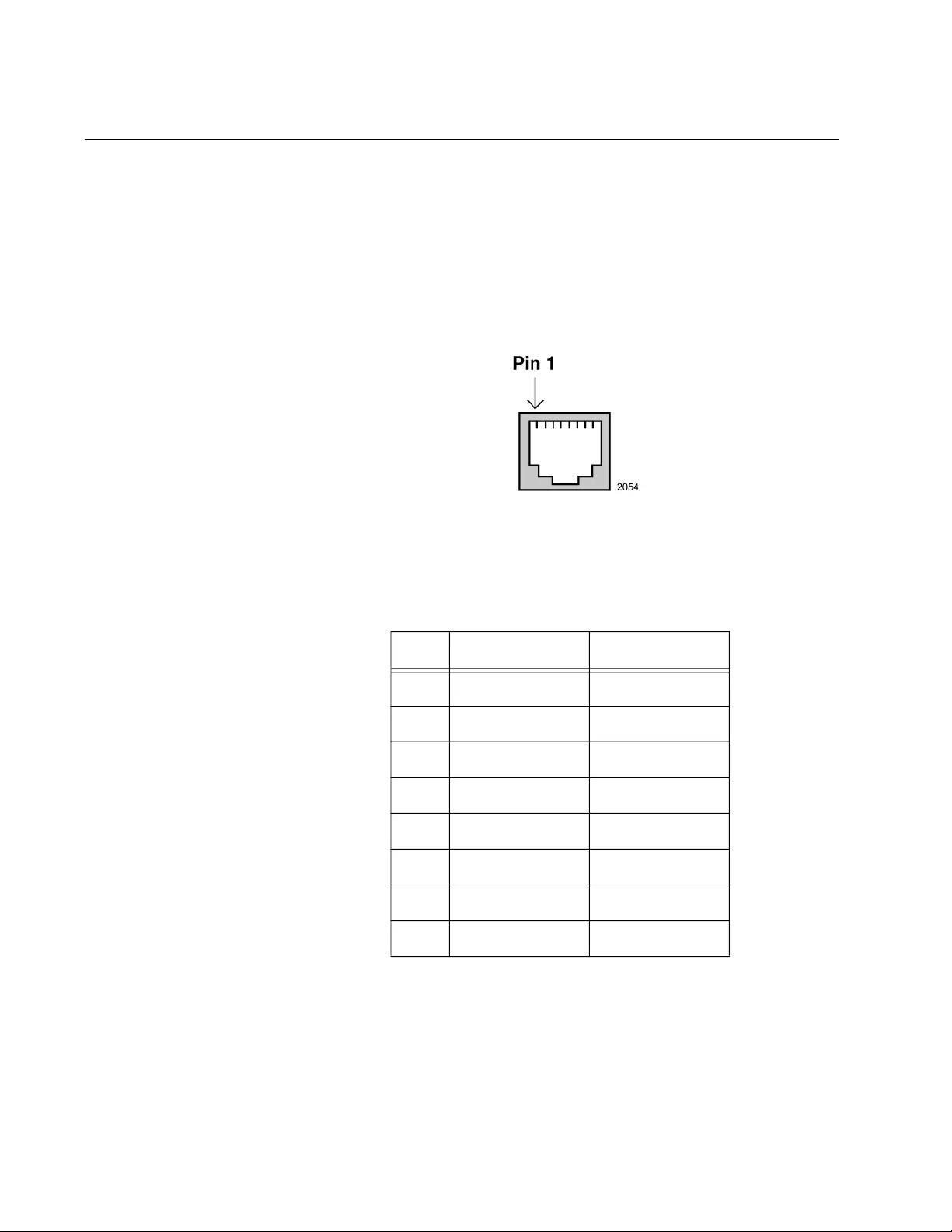
Appendix A: Technical Specifications
278
RJ-45 Twisted Pair Port Pinouts
Figure 160 illustrates the pin layout of the RJ-45 connectors on the
following products:
x950-28XTQm Switch
XEM2-8XSTm Line Card
XEM2-12XT Line Card
XEM2-12XTm Line Card
Figure 160. Pin Layout (Front View) of Twisted Pair Ports
Table 55 lists the pin signals at 100Mbps.
Table 55. Pin Signals on RJ-45 Twisted Pair Ports at 100Mbps
Pin MDI Signal MDI-X Signal
1 TX+ RX+
2 TX- RX-
3 RX+ TX+
4 Not used Not used
5 Not used Not used
6 RX- TX-
7 Not used Not used
8 Not used Not used
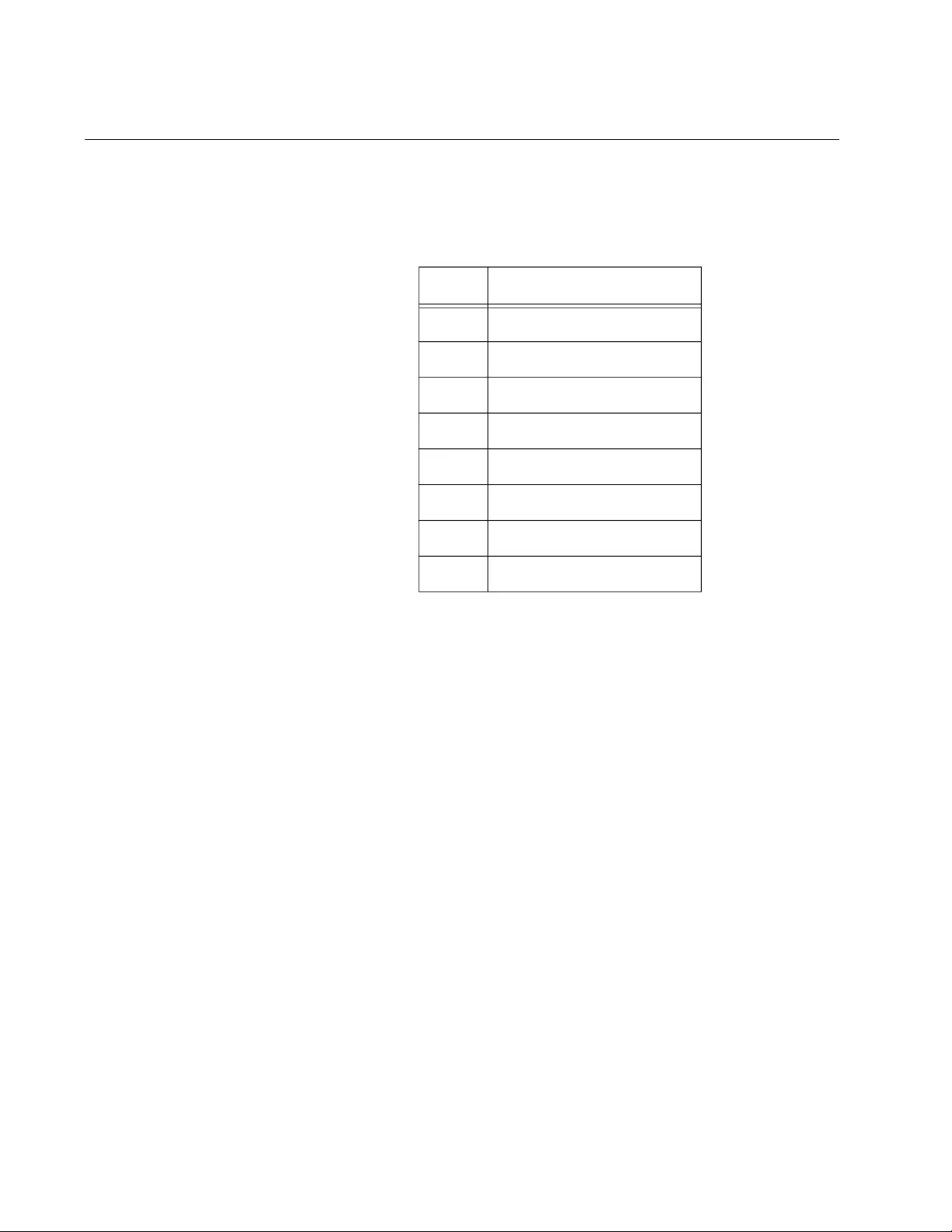
Appendix A: Technical Specifications
280
RJ-45 Style Serial Console Port Pinouts
Table 57 lists the pin signals of the RJ-45 style serial Console port.
Table 57. RJ-45 Style Serial Console Port Pin Signals
Pin Signal
1 Looped to pin 8.
2 Looped to pin 7.
3 Transmit Data
4 Ground
5 Ground
6 Receive Data
7 Looped to pin 2.
8 Looped to pin 1.